聚酯缩聚的工艺综述
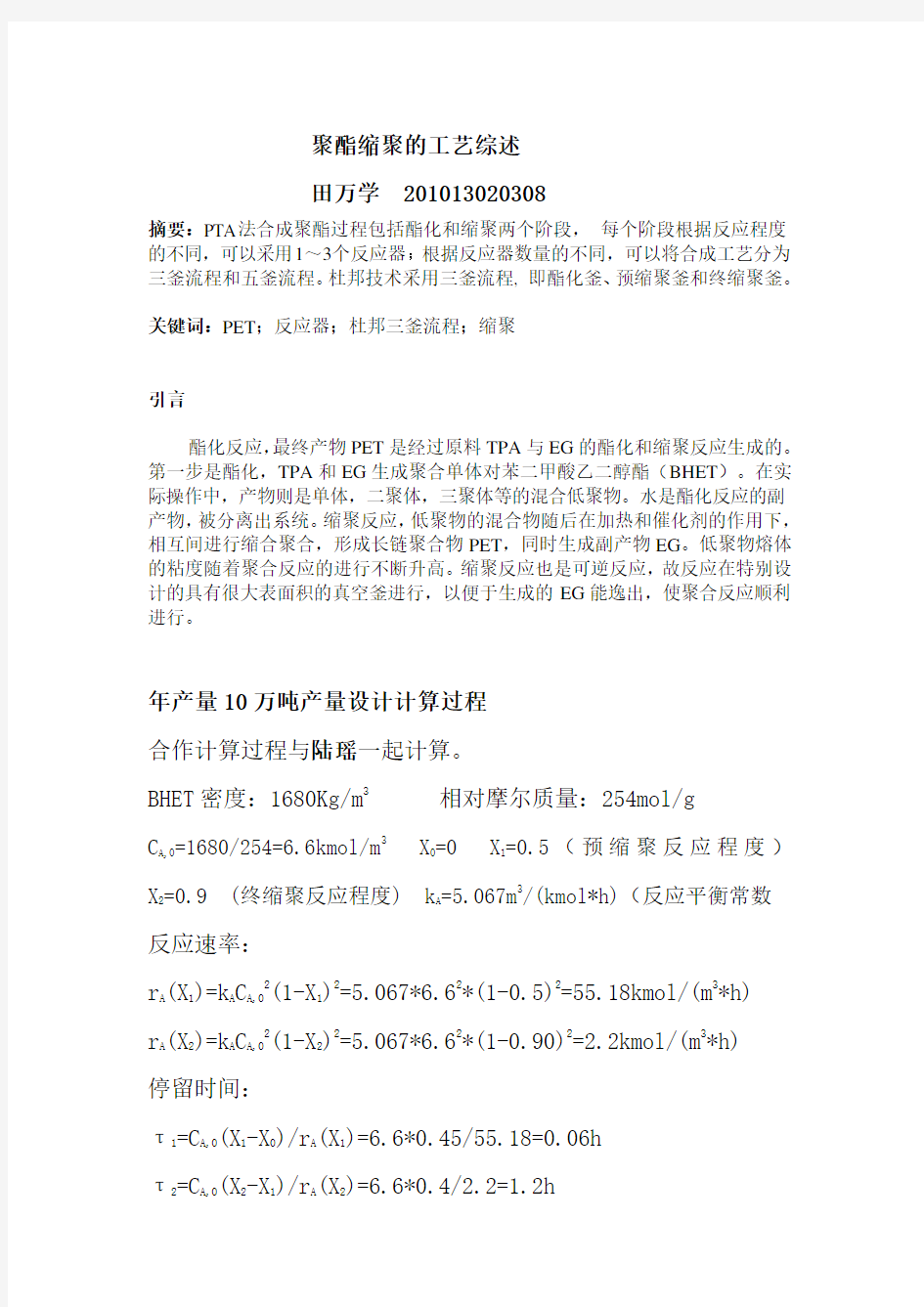
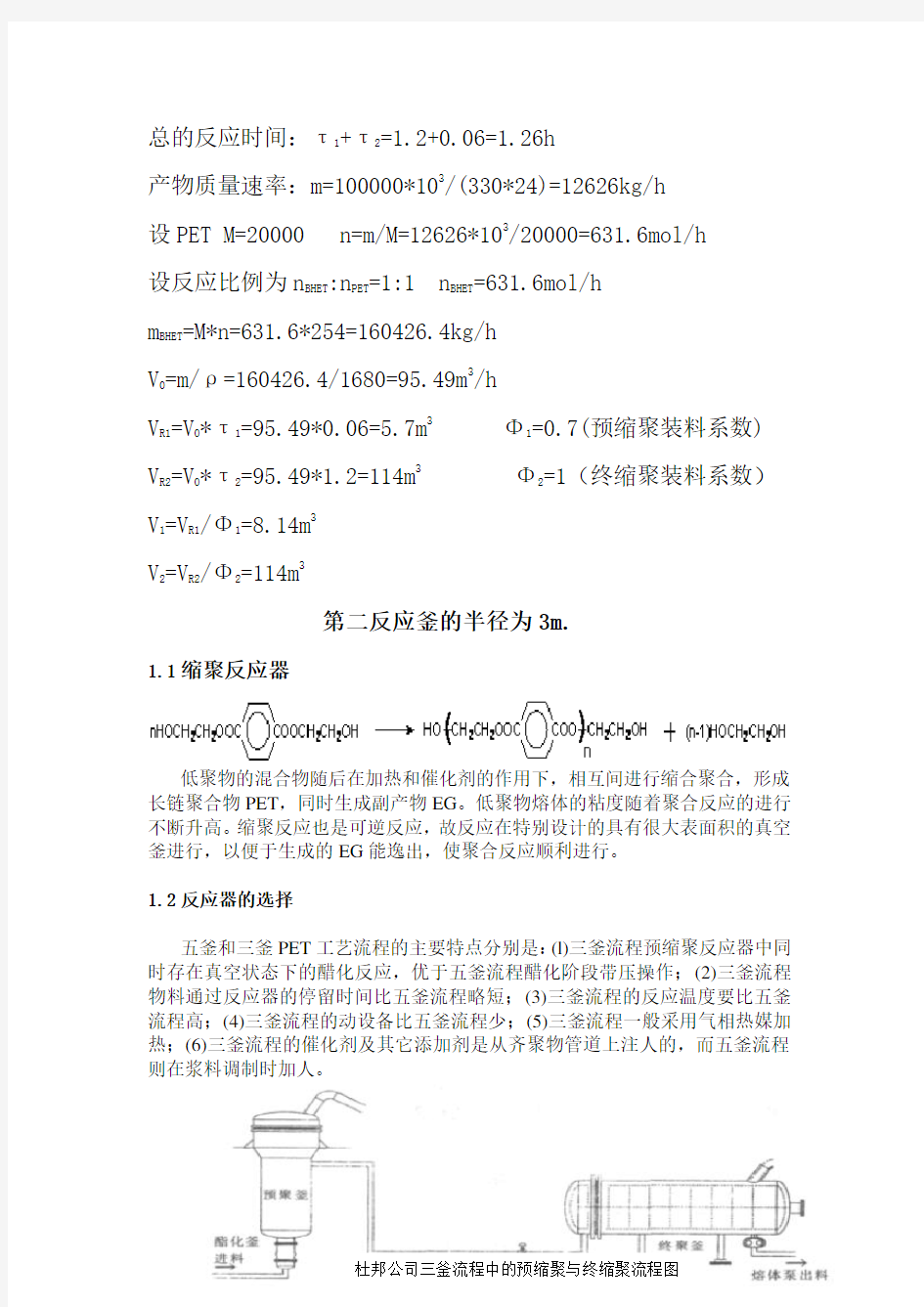
聚酯缩聚的工艺综述
田万学 201013020308
摘要:PTA法合成聚酯过程包括酯化和缩聚两个阶段,每个阶段根据反应程度
的不同,可以采用1~3个反应器;根据反应器数量的不同,可以将合成工艺分为
三釜流程和五釜流程。杜邦技术采用三釜流程, 即酯化釜、预缩聚釜和终缩聚釜。
关键词:PET;反应器;杜邦三釜流程;缩聚
引言
酯化反应,最终产物PET是经过原料TPA与EG的酯化和缩聚反应生成的。
第一步是酯化,TPA和EG生成聚合单体对苯二甲酸乙二醇酯(BHET)。在实
际操作中,产物则是单体,二聚体,三聚体等的混合低聚物。水是酯化反应的副
产物,被分离出系统。缩聚反应,低聚物的混合物随后在加热和催化剂的作用下,
相互间进行缩合聚合,形成长链聚合物PET,同时生成副产物EG。低聚物熔体
的粘度随着聚合反应的进行不断升高。缩聚反应也是可逆反应,故反应在特别设
计的具有很大表面积的真空釜进行,以便于生成的EG能逸出,使聚合反应顺利
进行。
年产量10万吨产量设计计算过程
合作计算过程与陆瑶一起计算。
BHET密度:1680Kg/m3相对摩尔质量:254mol/g
C A,0=1680/254=6.6kmol/m3X0=0 X1=0.5(预缩聚反应程度)
X2=0.9 (终缩聚反应程度) k A=5.067m3/(kmol*h)(反应平衡常数
反应速率:
r A(X1)=k A C A,02(1-X1)2=5.067*6.62*(1-0.5)2=55.18kmol/(m3*h) r A(X2)=k A C A,02(1-X2)2=5.067*6.62*(1-0.90)2=2.2kmol/(m3*h)
停留时间:
τ1=C A,0(X1-X0)/r A(X1)=6.6*0.45/55.18=0.06h
τ2=C A,0(X2-X1)/r A(X2)=6.6*0.4/2.2=1.2h
总的反应时间:τ1+τ2=1.2+0.06=1.26h
产物质量速率:m=100000*103/(330*24)=12626kg/h
设PET M=20000 n=m/M=12626*103/20000=631.6mol/h
设反应比例为n BHET:n PET=1:1 n BHET=631.6mol/h
m BHET=M*n=631.6*254=160426.4kg/h
V0=m/ρ=160426.4/1680=95.49m3/h
V R1=V0*τ1=95.49*0.06=5.7m3 Φ1=0.7(预缩聚装料系数)
V R2=V0*τ2=95.49*1.2=114m3 Φ2=1(终缩聚装料系数)V1=V R1/Φ1=8.14m3
V2=V R2/Φ2=114m3
第二反应釜的半径为3m.
1.1缩聚反应器
低聚物的混合物随后在加热和催化剂的作用下,相互间进行缩合聚合,形成长链聚合物PET,同时生成副产物EG。低聚物熔体的粘度随着聚合反应的进行不断升高。缩聚反应也是可逆反应,故反应在特别设计的具有很大表面积的真空釜进行,以便于生成的EG能逸出,使聚合反应顺利进行。
1.2反应器的选择
五釜和三釜PET工艺流程的主要特点分别是:(l)三釜流程预缩聚反应器中同时存在真空状态下的醋化反应,优于五釜流程醋化阶段带压操作;(2)三釜流程物料通过反应器的停留时间比五釜流程略短;(3)三釜流程的反应温度要比五釜流程高;(4)三釜流程的动设备比五釜流程少;(5)三釜流程一般采用气相热媒加热;(6)三釜流程的催化剂及其它添加剂是从齐聚物管道上注人的,而五釜流程则在浆料调制时加人。
1.2.1预缩聚反应器的选择
缩聚过程主要进行聚合物之间的缩聚反应。缩聚反应也是可逆平衡反应,它的平衡常数小,所以要把反应生成的小分子脱除,才能使反应向缩聚方向进行。缩聚过程是化学反应和小分子脱挥的耦合过程,过程速率从受反应速率控制过渡到受反应速率和脱挥速率共同控制。所谓”预缩聚”是受反应速率控制的过程,而“后缩聚”是从反应速率控制过渡到受反应速率和脱挥速率共同控制的过程。
反应器中物料的比表面积(m2/ kg) 是决定过程速率控制步骤以及决定脱挥速率大小的关键参数。为使得过程能处于反应速率控制,为提高脱挥速率,都要求反应器提供尽可能大的物料比表面积。缩聚过程是在真空条件下进行,所以小分子物的脱除速率相当高。随小分子从物料中脱除会产生雾沫夹带,这些夹带物堵塞真空系统管路是影响聚酯装置稳定运转的首害。雾沫夹带多少与物料的黏度高低、操作压力高低以及反应器中气相空间体积大小直接相关。所以每个反应器工况条件的确定和几个缩聚反应器之间负荷分配,直接影响装置能否长期稳定运转。聚合物在高温下会产生热降解而影响熔体的可纺性。有实验数据表明,高于285 ℃,热降解速率明显加剧。高质量产品的聚合度分布是均匀的,因此要求反应器中物料停留时间分布要均匀。
1.2.2圆盘转子式反应器
圆盘转子式反应器作为预缩聚反应器使用。物料在圆盘反应器中的流动相当于多个全混釜的串联,物料的特性黏度从进口的~0. 15 提高到出口的~0. 25 以上。在上述黏度范围,虽然物料并不能在盘面上完全成膜,但是通过圆盘转子的搅动,它可以较槽式反应器提供大得多的比表面积,从而使过程处于反应速率控制。
1.2.3物料流动型式
在预缩聚段,一方面发生的醋化反应和缩聚反应均为可逆平衡反应,为使酷化、缩聚反应深入进行,必须移走醋化反应产生的小分子水和缩聚反应产生的小分子乙二醇,移走小分子要有足够的传质面积和蒸发空间,搅拌釜较适合;另一方面,分子量的增长过程是一系列链增长的串联反应过程,液相返混不利于链增长,并且不同分子量的齐聚物相互反应产生不同分子量的产物,造成产物分子堂存在一定分布,为了得到较窄分子量分布的缩聚产物,也要求反应器物料停留时间要均一,预缩聚段物料流动为平推流较佳。
1.2.4搅拌型式
PET预缩聚反应器搅拌目的主要是强化传质,促进小分子的脱出,同时也满足混合、传热需要。搅拌任务除可用叶轮搅拌器完成外,还有气流搅拌、射流混合、管道混合等方法。无机械搅拌的装置减少了故障出现的可能性,可延长设备运转周期。
1.2.5 反应动力学关系式的建立
对于PET合成来说,通过直接酷化法制得单体BHET后,在加热、减压、和缩聚催化剂的作用下,进行缩聚反应,生成聚对苯二甲酸乙二醇酷(PET)。其反应方程式如下:
除此以外,下面的反应也是导致链增长的重要反应之一:
另外还有降解副反应(热降解、热氧化降解、链端降解、链间降解、水解等等),但在动力学研究和实际生产上,在温度不特别高、真空度较好的情况下,可以不考虑副反应。缩聚反应的动力学比较重要的是开放体系中催化剂作用下的缩聚反应动力学,相关的报道文献上有很多。G.Rafler等人通过实验确定金属离子催化下的BHET的缩聚属于二级反应,在只考虑缩聚中的主要链增长反应(上述的ECI式)的情况下得出:
将上式积分得如下方程:
式中:C t一一在t时刻反应物(经基)的浓度;
C。一一起始反应物(经基)的浓度;
k一一反应速度常数:t一一反应时间。
在聚醋缩聚反应动力学研究中上述G.Rafler所得动力学方程是最
简单、也是最常用的。、
1.3终聚反应器的选择
终聚反应的聚醋产品,必须具有高度的聚合度的均匀性,也就是说要达到一定的聚合度分布,这就要求通过终聚反应器的每一单元质量(dm)的反应物,在规定的温度和压力的前提下,都能停留相同的时间(τ),达到相同的聚合度。聚合物在终聚反应器中的停留时间是完成缩聚的重要因素。停留时间不够,达不到要求的聚合度;停留时间过长,会造成聚合物的过热降解。而且如前所述终聚反应器的设计应保证聚合物每微元质量(dm)在终聚反应器内均停留相同时间(t)。为了达到上述要求终聚反应器的设计应避免聚合物流动的死角和滞流区。综上所述聚酷终聚反应器的结构设计主要应满足以下诸项工艺要求:
(1)保证物料在反应器内所必需的停留时间;
(2)使物料的运动呈活塞流,避免返混、死角与滞流区;
(3)保证在反应同时能够迅速排出生成的EG,使缩聚得以顺利进行;
(4)提供缩聚时所需要的温度并使同一物流切面内的温度梯度保持在允许范围之内;
(5)在保证上述条件下反应器结构应尽量简单可靠,具有足够的强度与刚度,便于安装、维护与检修;
(6)具有合理的经济性减少占地面积及空间。
1.3.1反应装置图
为了保证反应器内物料的温度,反应器体及盖均须设置热媒夹套。同时热媒夹套本身也增强了做为真空容器的反应器体与盖的刚度。
1.3.2反应器热负荷
缩聚反应是放热的。后缩聚过程外界输入的搅拌功转化为热能使熔体温度升高。而为了避免出现聚合物的热降解影响可纺性,对熔体的温升要控制的。与其他几个反应器有区别,后缩聚反应器夹套热媒主要起保温作用,而对传热并没有特殊要求。与气相热媒比较,液相热媒的温度更易于控制。采用”半管”夹套可以满足工艺要求,与“L”形夹套相比,它的加工费用低。
1.3.3反应所需的添加剂
二氧化钛
二氧化钛亦称钛白粉,白色粉末,无毒、化学性质稳定,聚酯生产中用作消光剂。加入量为0.1~0.3%(mt)时为半消光PET,如加入量为0.5~2% 时为全消光。
催化剂
在直接酯化法的PET 生产中,酯化过程一般不需要催化剂,而缩聚过程必需催化剂。选择催化剂时,应符合下列要求:
1.能促进主反应,力求减少副反应。
2.易在原料或产物中溶解,便于均匀分布。
3.所得产品在粘度、熔点、色相、热稳定性等方面,不得因使用催化剂而降低质量指标。4.价廉、容易取得。
缩聚催化剂
缩聚催化剂有锑、钛、锡、锗等四个体系。其中锑系催化剂在聚酯生产中用得较普遍。常用的有三氧化二锑(Sb2O3)和三醋酸锑[Sb(AC)3],两者的差异在于:
1.Sb(AC)3 易溶于EG 中,在20℃时溶解度为47 g/l,在60℃时,可达150 g/l,所以配制时不需要加热。要求配制浓度为0.035~0.043%(对PTA 浆料)时,一般在1~2 小时内即可完成,而Sb2O3 在EG 中的溶解度较低,50℃时仅30g/l(该温度下Sb(AC)3 的溶解度为122g/l)。所以Sb2O3 的配制时间不长,配制温度高达140℃。
2.与Sb2O3 相比较,Sb(AC)3 对缩聚反应具有更强的催化能力。
3.Sb(AC)3 一般有Sb2O3 制成,在制备过程中已除去所有不溶性杂质,所以配成的EG 溶液不需过滤。而Sb2O3-EG 溶液,则需要设置过滤器加以过滤。
4.Sb2O3 和Sb(AC)3 对人体有一定的毒性,长期接触时对肝脏有明显损害。而Sb(AC)3 还有醋酸蒸汽逸出,还是一种腐蚀性的介质。
1.3.4物料浓度对酯化平衡反应的影响
增加反应物的浓度或减少生成物的浓度,可使酯化平衡向生成酯化物的方向移动。但实际的生产中往往采用增大原料中的EG 的摩尔比和减少体系中的水含量这两种方法来促进酯化反应。例如,在封闭体系中T=EG/PTA(摩尔比)=10 时,温度为235℃,转化率就可达90%(按羟基减少量计算)。所得的平衡常数Kv=1.09/1.10。这一平衡常数是在封闭体系中测定的,前述的Kv=2.0 是在敞开体系中测定的。敞开体系中,酯化反应生成的水将不断被蒸发排出系统,导致平衡向生成物方向移动,所以Kv 值大。
平衡时体系中各物料的浓度
按反应的当量的投料,在酯化反应达到平衡(封闭体系):
所以反应达到平衡时,转化率最多只能达到58.6%,因此,实际生产中往往采用敞开体系,及时除去水可适当增加原料的EG 浓度、使反应达到较高的转化率。
1.3.5聚酯生产的副产物
聚酯生产中的副产物按其形态可分气相副产物、液相副产物和固相副产物
气相副产物主要是指乙醛等不凝性气体,分别在酯化过程的EG-H2O 分离塔和缩聚过程的真空系统中排出。除此之外,在污EG 贮罐、粗WG预蒸发罐等处也可排出大量乙醛气体。聚酯生产中的液相副产物主要有EG、DEG 和TEG 等,固相副产物主要是指聚酯废块。
1.3.7预缩聚段的工艺操作条件
最终缩聚
1.3.8缩聚过程的温度控制
由于缩聚过程是微放热反应,所以反应所需的热量较少,大部分需要只是用来保温。因此缩聚温度的控制比较容易,可采用一般的简单调节回路。例如,仪化聚酯中,预缩聚的两个反应釜合同一个二次热媒温控系统,各自的反应釜段分别构成本系统的温度调节回路。对于最终缩聚,则只考虑一个二次热媒的温度调节回路,就可以满足生产的要求。
结论
综合以上,聚酯的合成分为两个部分,酯化和缩聚的两个过程,在缩聚里面又分为预缩聚和终缩聚两个部分,在预缩聚中是进一步的提高酯化过来的缩聚程度,最终在终缩聚中达到我们需要的缩聚度。以设计的工艺流程参考的是杜邦公司的三釜流程,想对五釜流程来说,起码在能源上面,节省了不少。在预缩聚中为了小分子的挥发,需要很大的面积来提供挥发的场所。在预缩聚中为了分子量分布的均匀需要在反应釜中停留的时间一样。再设计上要考虑到流动的均匀性。
聚酯装置流程与聚酯生产概述
聚酯装置流程与聚酯生产概述-----------------------作者:
-----------------------日期:
第一章 聚酯装置流程介绍 18万吨/年聚酯装置是中国纺织设计院设计的国产化生产线, 在工艺上以精对苯二甲酸(PTA)和乙二醇(EG)为原料,采用直接酯化连续缩聚的五釜工艺流程,装置设计负荷为日产500吨。该聚酯装置具有单系列生产能力大、生产弹性大、化工料品种少、原料消耗低、三废少等特点。在控制系统上,聚酯装置采用了先进的集中分散DCS 控制系统,具有操作控制方便、人机联系好、功能齐全、可靠性高等特点。 本聚酯装置的产品为半消光纤维级聚酯熔体及切片,可用于直接纺制涤纶长丝或短纤。 聚酯生产装置包括主生产装置和辅助生产装置两大部分。主生产装置包括以下生产工序: (一)PTA 卸料及输送(设PTA 库房两座,两座库房面积共9800m 2,贮存周期约25天) (二)浆料制备 (三)酯化(第一、二酯化及工艺塔) (四)预缩聚(第一、二预缩聚,预聚物过滤及输送) (五)终缩聚(终缩聚、熔体输送及过滤) (六)切片生产、输送及包装 (七)尾气淋洗 (八)催化剂制备 (九)消光剂制备 辅助生产装置包括以下部分: (一)热媒站(配备单台热负荷800万大卡的热媒炉三台,两用一备) (二)罐区(设容积5000m 3的乙二醇贮罐两个,贮存周期约52天;设容积1000m 3的燃料油贮罐两个,贮存周期约32天。) (三)过滤器清洗 (四)化验室 聚酯装置主工艺流程图如下: 终缩聚 预缩Ⅱ预缩Ⅰ酯化Ⅱ酯化Ⅰ浆料配制EG动力蒸汽
外购原料PTA通过叉车将PTA贮存于PTA仓库,人工将PTA投入链板输送前的小料仓后,用链板输送方式将PTA送到聚酯大楼的日料仓。另一主要原料乙二醇贮存在罐区,用泵通过管线送入车间。催化剂三醋酸锑(或乙二醇锑)用桶装、消光剂二氧化钛用袋装运入聚酯大楼四楼。 聚酯装置主要由催化剂配制、二氧化钛配制、浆料配制、酯化、缩聚、切片生产及包装等几个工序组成。酯化缩聚设置了五个反应器,其中两个是酯化反应器,两个是预缩聚反应器,一个后缩聚反应器。两个酯化反应器为立式搅拌釜,设内盘管加热,两台反应器共用一个分离乙二醇和水的工艺塔。第一预缩聚反应器为立式槽,不设搅拌装置,用液环真空泵产生真空。第二预缩聚反应器和后缩聚反应器为圆盘转子式,两个反应器共用一套三级乙二醇蒸汽喷射泵系统(它用液环泵作排气的),在每个缩聚反应器和它的真空装置间设刮板冷凝器。在第二预缩聚反应器和后缩聚反应器之后分别设有熔体过滤器。从终缩聚反应器出来的熔体每天300吨供应长丝八条生产线,每天200吨供应另外的长丝四条生产线,其余大约有每天20--40吨熔体通过水下切粒机生产半消光切片,本装置配有两台切粒机,切出的切片通过干燥装置后,用气相脉冲输送方式将切片送至切片料仓,打包后出厂。 辅助装置有:热媒(HTM)系统(主要由三台800万大卡的热媒炉组成)、过滤器清洗等辅助设施。本装置用液相热媒作反应器等设备、管线的加热和保温,共设置了十一个二次热媒回路,分别服务不同的使用点。 聚酯生产中的每一段工序其作用分别简要说明如下: 1、浆料配制 原料PTA自PTA储存料仓采用星型给料器出料,通过振动筛去除夹带的异状物,质量流量计连续计量后,送入浆料调配槽。原料PTA和MEG以及催化剂溶液按规定比例连续送入浆料配制槽中,由特殊设计的搅拌器使之充分混合并配制为恒定摩尔比(MEG/PTA)的浆料,经浆料输送泵连续送入酯化反应器中。 2、酯化反应 酯化反应系统共设置两台酯化反应器。在第一酯化反应器中酯化率可以达到91%;第二酯化反应器后控制酯化率在96.5%左右。通过调节反应器的温
聚酯装置生产过程危险性分析
聚酯装置生产过程危险性分析 1 装置概况 1.1 概述 聚酯装置是某石油化工总厂的主要生产装置之一。该装置采用美国杜邦(DUPONT)连续缩聚聚酯生产专利技术,美国康泰斯(CHEMTEX)公司为工程承包商。1997年1月30日由中国石油化工总公司国际事业部与美国康泰斯公司签定《某石油化工总厂化纤工程年产20万吨聚酯装置成套设备和技术合同》。装置由两套聚合生产线和辅助系统组成,由美国康泰斯公司负责基础设计,中国纺织工业设计院承担初步设计和详细设计。合同于1997年5月生效,1998年2月动工,1999年12月单机试运行,2000年5月投产。项目占地69000平方米,总投资97565万元(其中外汇4929.3万元)人民币,建筑面积28352平方米。 装置的设计生产能力为20万吨/年,日产熔体606吨。全年开工330天,即7920小时。装置设计有两条连续酯化
缩聚生产线,每条生产线的设计能力为日产熔体303吨。生产纤维级聚酯切片时,生产弹性可在50~100%范围内调整。 1.2 装置工艺概况 1.2.1工艺流程简述 原料PTA经大料仓,用压缩氮气分别送至两个PTA日料仓,用于两条生产线。日料仓的PTA与EG经计量(EG/PTA 的摩尔比2:1)后进入浆料混合槽中混合成浆料。经浆料泵送至浆料供给槽,密度合格的浆料再经过泵送至浆料注入喷嘴进入酯化反应器,进行酯化反应。在酯化反应器中,PTA 浆料从热交换器底部自下而上通过列管加热(反应温度295℃、压力0.1MPa)后,物料上升至热交换器顶部溢流至蒸汽分离器,完成酯化反应。总反应时间90分钟,酯化率92%。 蒸汽分离器中的液态酯化料在热虹吸作用下进行循环,一部分齐聚物经齿轮泵、冷却器,温度降至275℃左右送至预缩聚釜反应。循环抽出比为100:1。在送往预缩聚釜的齐聚物管线上,催化剂、稳定剂等通过装在管线上的喷嘴进入
PET聚酯
聚酯(PET)市场分析和技术进展 聚酯(聚对苯二甲酸乙二醇酯,PET)由聚对苯二甲酸(PTA)和乙二醇聚合而成,聚酯(PET)主要用于瓶级聚酯(广泛用于各种饮料尤其是碳酸饮料的包装)、聚酯薄膜(主要用于包装材料、胶片和磁带等)以及化纤用涤纶。 发展现状 聚酯(PET)发明于1944年,1949年率先在英国实现工业化生产,因其有优良的服用和高强度等性能,成为合成纤维中产量最大的品种。聚酯在20世纪70年代以前一直保持高速发展,其生产增长率为:1960年200%、1965年50%、1970年60%,此后增速减缓并呈周期性发展趋势,1975年增速为30%、1982年为10%、1987年为12.6%、1992年为6%、1999年为4.3%、2001年为4.8%,预计2004年为8%。上个世纪90年代后,聚酯工业的发展重心开始转向亚洲,至90年代中期,因产能扩充过多,除中国外已出现供大于求的局面。到1999年,聚酯工业又迎来新的发展阶段,主要由于瓶用和膜用、复合等非纤用聚酯的用量增加,衣用涤纶需求也达到高峰。据聚酯世界大会分析,从1999~2005年,聚酯产能还可以增长33~40%,年均增长率为6.6~8%。从2000年开始,世界聚酯工业又进入新一轮的快速发展期。 在聚酯产品上,非纤聚酯的发展速度很快。1996年,世界聚酯包装树脂和薄膜产量分别为451.9万吨和138.2万吨,占世界聚酯总产量的20.7%和6.3%,1998年则分别为699.5万吨和163.1万吨,占世界聚酯总产量的24.6%和5.7%。2000年分别达到823.6万吨和176.9万吨,年均增长率分别为17.6%和6.2%,各占世界聚酯总产量的26.0%和5.59%。预计到2003年,非纤聚酯产量约占聚酯总产量的1/3。 PET的用途不再主要局限于纤维,而是进一步拓展到各类容器、包装材料、薄膜、胶片、工程塑料等领域,目前,PET正在越来越多地取代铝、玻璃、陶瓷、纸张、木材、钢铁和其他合成材料,聚酯的家庭也在持续扩大。 发泡PET:近年来不断探索PET的新用途,PET挤出发泡工艺及其应用逐渐引起关注,在包装材料及许多需要较高温度的应用上,PET发泡体有突出的性能。采用发泡的方式可减轻聚酯材料的质量,可节省成本,发泡产品比未发泡产品有更好的热绝缘性能。发泡PET 还具有极好的耐热性能,并且经发泡后的PET板具有优异的性能成本比,再加上PET本身就具有耐油、耐化学腐蚀性、易回收等优异性能,符合食品卫生要求,因此发泡在食品包装、微波容器、冰箱内板、屋顶绝热、电线绝缘、微电子电路板绝缘、运动器材、汽车、航天工业等方面将有很大的市场。 PET工程塑料:PET具有良好的力学性能、电绝缘性、耐化学药品性、耐蠕变性能、耐疲劳性能及耐磨擦性能等,其缺点是结晶速率低、抗冲击能力差。国内外工作者对其进行大量的研究工作,研制出了可用于轿车用的PET工程塑料,也可作为工程塑料用于电子、电器领域,如仪表壳、热风口罩等。
PET的生产工艺介绍
聚酯切片的生产工艺介绍 百科名片 聚酯切片 聚酯切片聚酯工艺路线有直接酯化法(PTA法)和酯交换法(DMT法)。PTA法具有原料消耗低、反应时间短等优势,自80年代起己成为聚酯的主要工艺和首选技术路线。大规模生产线的为连续生产工艺,半连续及间歇生产工艺则适合中、小型多种生产装置。聚酯PET 的用途不再主要局限于纤维,而是进一步拓展到各类容器、包装材料、薄膜、胶片、工程塑料等领域。 简介 聚酯切片 PET 学名:聚对苯二甲酸乙二醇酯英文简称:PET由精对苯二甲酸(PTA)和乙二醇(EG)聚合而成. 分类
1、按组成和结构可分为:共混、共聚、结晶、液晶、环形聚酯切片等; 2、按性能可分为:着色、阻燃、抗静电、吸湿、抗起球、抗菌、增白、低熔点、增粘(高粘)聚酯切片等; 3、按用途可分为:纤维级聚酯切片、瓶级聚酯切片、膜级聚酯切片(主要是工艺指标不同)。纤维级聚酯切片按其中消光剂tio2的含量不同又可以分为:超有光(大有光)、有光、半消光、(全)消光聚酯切片。另外还有阳离子聚酯切片。 发现与发展 目前,主要用于瓶级聚酯(广泛用于各种饮料尤其是碳酸饮料的包装)、聚酯薄膜(主要用于包装材料、胶片和磁带等)以及化纤用涤纶. 聚酯系列产品的最早历史,可以说,1928年美国杜邦公司的卡罗瑟斯(Carothers)对脂肪族二元酸和乙二醇的缩聚进行了研究,并最早用聚酯制成了纤维。1931年秋天,卡罗瑟斯(Carothers)在美国化学会正式发表其研究成果。该纤维具有丝的光泽,强力和弹性均可和蚕丝媲美,但是由于其熔点低、易水解不耐碱,而无实用价值。但这项研究最早证实了聚酯可以制成纤维。1941年英国卡利科印染工作者协会(以下简称CPA)的温菲尔德和迪克森在卡罗瑟斯(Carothers)工作的启发下,继续研究聚酯,1942年CPA取得了专利权。可以说,聚酯(PET)是在1949年率先在英国实现工业化生产,因其有优良的服用和高强度等性能,成为合成纤维中产量最大的品种。 生产方法 PTA法连续工艺主要有德国吉玛(Zimmer)公司、美国杜邦公司、瑞士伊文达(Inventa)公司和日本钟纺(Konebo)公司等几家技术。其中吉玛、伊文达、钟纺技术为5釜流程,杜邦则开发了3釜流程(目前正在开发2釜流程),两者缩聚工艺基本相似,区别在于酯化工艺。如5釜流程采用较低温度及压力酯化,而3釜流程则采用高乙二醇(EG)/PTA摩尔比和较高的酯化温度,以强化反应条件,加快反应速度,缩短反应时间。总的反应时间为5釜流程10小时,3釜流程3.5小时。目前世界大型聚酯公司都采用集散型(DCS)控制系统进行生产控制和管理,并对全流程或单釜流程进行仿真计算。 2003年初,伊文达-费希尔(Inventa-Fisher)(I-F)公司公布了其聚酯生产流程和能耗。该工艺从PTA或DMT与乙二醇(EG)反应生产树脂级或纺织级聚酯。采用4釜(4R)工艺,由PTA和EG或熔融DMT和EG组成的浆液,进入第一酯化/酯交换反应器,反应在较高压力和温度(200~270℃)下进行,生成的低聚物进入第二串级搅拌式反应器,在较低压力和较高温度下进行反应,反应转化率大于97%。然后在低于常压和较高温度下,藉第3台串级反应器预聚合,缩聚程度大于20,经第4台DISCAGE精制器后,使最终缩聚物的特性粘度(i.V.)提高到0.9。能耗为:电力55.0 kwh/t,燃料油
聚酯装置简介和重点部位及设备
编号:SM-ZD-87342 聚酯装置简介和重点部位 及设备 Organize enterprise safety management planning, guidance, inspection and decision-making, ensure the safety status, and unify the overall plan objectives 编制:____________________ 审核:____________________ 时间:____________________ 本文档下载后可任意修改
聚酯装置简介和重点部位及设备 简介:该安全管理资料适用于安全管理工作中组织实施企业安全管理规划、指导、检查和决策等事项,保证生产中的人、物、环境因素处于最佳安全状态,从而使整体计划目标统一,行动协调,过程有条不紊。文档可直接下载或修改,使用时请详细阅读内容。 一、装置简介 (一)装置发展及类型 1.装置发展 聚酯工艺产生于20世纪40年代,在50年代实现了工业化,是利用基础化工原料生产合成纤维的工艺技术。20世纪70年代以后,各国针对聚酯存在的吸水率低、不易染色、易产生静电等缺点进行了改性研究,取得了较多成果,使聚酯工业有了飞速的发展。70年代末,我国从前西德引进了第一套直接酯化连续缩聚生产涤纶树脂的工业化生产装置。经过几十年的发展,聚酯在我国三大合成纤维工业中已占有举足轻重的地位。截止到20xx年底,我国聚酯装置的产能已经达到1115X10的4次方(原多次方位置应该标在右上位置,但word格式不支持)t/a,占世界总产量的三分之一左右。进入21世纪,随着工艺技术的不断发展,我国聚酯装置正向工艺技术更先进、经济效益更好的方向发展。
涤纶长丝生产工艺简介
涤纶长丝生产工艺简介 1. 预结晶 切片干燥过程中需要加热到140℃以上,而普通切片的软化点很低,在80℃以下即软化 发粘,容易粘结成块堵塞干燥装置或输料管(俗称结块),为了提高切片的软化点,必须提高切片的结晶度,使其软化点达到200℃左右,这样干燥工序才能顺利进行。 预结晶采用120~170℃左右的热空气对切片加热,为了防止切片粘结成块(俗称结块),一般采取以下三种方式: 1.利用沸腾床等装置,将热空气从下往上吹向切片,使得切片呈现沸腾状,切片粒子之间的位置一直处 于快速波动之中,有效防止了切片之间的粘结。一般将这种方式称为BM 式。 2.利用搅拌装置,对处于预结晶过程中的切片不断搅拌,使得切片粒子之间无法粘结或者粘结后随即被打散。一般将这种方式称为KF 式。 利用震动装置,使得处于预结晶过程中的切片高频震动,粒子之间的位置快速变化,从而无法相互粘结。一般与BM 式结合使用。 熔体直纺没有预结晶流程。 2.干燥 涤纶生产过程中,PET 切片需要在290℃左右的高温下熔融,在此高温下,如果切片的含水率达到一定程度(比如100ppm 以上),熔体会发生水解现象使得熔体质量下降,从而使纺丝工序难以顺利进行甚至导致成品丝品质下降。 将经过脱湿处理的干燥空气(露点降到-20 ℃以下)加热到160℃左右,从干燥塔底部输送到干燥塔中与切片逆向接触使切片迅速脱水,干空气将水分从干燥塔顶部带出。切片一般在干燥塔中停留4~8 小时,当工艺条件(干燥温度、干空气露点、干空气流量、切片在干燥塔中的停留时间)合适时,切片的含水率可以降低到50ppm 以下,满足纺丝要求。不同的生产工艺和品种对切片的含水率要求有明显差异: UDY-DT : 目标含水率≤100ppm POY-DTY: 目标含水率≤50ppm FDY : 目标含水率≤30ppm 常规品种含水率可以偏高一点,但是异型丝和细旦、超细旦丝对含水率要求很高,一般要求含水率≤20ppm 。 切片含水率偏高时,熔融后熔体降解程度大,纺丝工段容易出现毛丝、断头、飘丝等异常现象,丝的强度会降低,断裂伸长率升高。 干燥工序分连续干燥和间歇干燥两种方式。 连续干燥采用干燥塔(一般需要加上预结晶装置),干燥介质为除湿干空气,采用电加热方式,这种方式干燥效率高,干燥效果好,操作简便可以自动控制,工艺调整方便,是目前普遍采用的干燥方式; 间歇干燥采用转鼓装置(无需额外的预结晶装置),加热方式为蒸汽,用抽真空的方式使切片脱水。这种方式干燥效率很低,干燥效果不理想,操作麻烦且多为手动控制方式,工艺调整不方便,除了在一些老式UDY 生产线上还有少量存在以外,已经基本被淘汰。 目前,随着熔体直接纺技术的成熟,越来越多的厂家采用了熔体直纺技术,采用这项技术,省去了切片造粒、切片包装、切片运输、切片筛选、切片输送、切片干燥、切片熔融等很多过程,因而使生产成本大大降低。 3.纺丝纺丝是整个化纤生产中的关键工序,纺丝状况如何,直接影响到“产、质、耗”等生产指标能否顺利完成。 纺丝就是将熔融状态下或呈溶液状态下的高聚物纺成丝束的过程。对于切片法纺丝而言还包括了将切片由颗粒状固体熔融成熔体的过程。 纺丝设备包括熔体过滤器、纺丝箱体、计量泵、组件(包括海砂或金属砂、过滤网、分配板、喷丝
最新国产三釜聚酯装置介绍
最新国产三釜聚酯装置介绍 咨询电话:(0086)571 82718253 转 773 【作者:未知】【发布时间:2006/10/24 14:36:32】【字体:大中小】【关闭】 该技术为中国聚酯技术的一个重大进步,作为聚酯技术的管理人员有必要向各位同行介绍一下,加强一下各位朋友对聚酯发展的新动向的了解。 新三釜聚酯装置是中国纺织机械(集团)有限公司(CTMC)北京英诺威逊聚合技术有限公司自主开发的拥有完整知识产权的新技术。该装置包含新型双区酯化釜、新型多层预缩聚釜和原创性栅缝降膜终缩聚塔各一台,三者均不设机械搅拌。双区酯化釜和多层预缩聚釜已成功用于宜兴市明阳化纤厂470吨/日聚酯工程。栅缝降膜终缩聚塔中试结果令人耳目一新,不仅聚合速度显著高于传统的卧式圆盘或鼠笼搅拌釜,还能直接生产圆盘或鼠笼釜无法得到的高粘聚酯产品,取消SSP。目前已有数家世界著名聚酯生产企业希望北京英诺威逊聚合技术有限公司向其授权或与其合作完成栅缝降膜塔直接生产高粘聚酯技术 商品化。 新型双区酯化釜 理想型酯化反应器优化设计原则: ◇酯化前期物料全混型流动,用酯化物溶解PTA粉末,避免非均相反应麻烦;酯化后期保持平推流动,提高酯化反应速度; ◇强化传热,以合理的方式满足酯化巨大的热量需求; ◇简化结构,降低建设投资和运行成本。 酯化反应器现状: 目前,国内外酯化反应器主要有两类: Zimmer和Inventa配置两台搅拌釜串联,第二酯化釜采用内外室或多层结构向平推流靠近。这种配置酯化率可达97%,能满足工艺要求,但占用空间大,制造维修运行成本较高。 DuPont采用单台自然循环酯化釜,无机械搅拌,结构简单,维修及运行成本较低。该釜为外置循环,占用空间较大。浆料注入外循环管后和回流的酯化物混合升温,浆料中水份和部分EG迅速蒸发,两相混合流体从下封头进入列管换热器。与浮力相比,气泡水平运动的推动力十分微弱,较多气泡垂直上升进入进料管口上方区域列管,其余列管气泡含量较低,部分含气泡较少的列管内物料密度较高,可能向下倒流,影响传热和酯化速率。 DuPont单釜酯化率不足94%,必须与其特有的上流式预缩聚反应器(UFPP)配套,在UFPP中加入大量EG继续提高酯化率。 新型双区酯化釜简介: 遵循理想型酯化反应器优化设计原则并针对现行酯化反应器缺陷,北京英诺威逊聚合技术有限公司发明了新型双区酯化釜。该釜由釜体、列管换热器、釜内区域分隔板及各区域内构件组成,其结构及釜内物料和蒸汽流动途径示意见图1。
影响聚酯工艺过程的主要因素
影响聚酯工艺过程的主要因素 1、EG/PTA摩尔比 原料EG/PTA的摩尔比对反应过程和产品PET的聚合度有重要影响。据反应可知,只有EG与PTA在等物质的量配比条件下才能得到高聚合度的PET。当PTA与EG的物质的量比趋近1时,PET的聚合度(DP)为一极限值。 PTA与EG酯化反应中,EG/PTA摩尔比为2:1。但是在反应体系中,EG/PTA酯化产物BHET的缩合又放出EG,为防止EG自身缩合成DEG影响PET质量,通常使EG摩尔含量小于EG/PTA摩尔比,EG/PTA的摩尔比为1.7-1.8 :1。EG/PTA的摩尔比也不宜过低,否则酯化产物的羧基含量增高。 随着EG/PTA的摩尔比提高,酯化反应加速、时间缩短,但同时也使体系中DEG含量增加,最终导致产品PET中的DEG含量提高。据此在继续降低EG/PTA摩尔比的同时,开发了适当提高EG/PTA摩尔比的工艺。其核心问题是,在充分发挥EG/PTA摩尔比的条件下反就优势的同时,有效控制体系中DEG含量的增加。 在连续工艺中,酯化过程基醒在接近“清晰点”的条件下进行的,缩聚反应脱出的EG 经回收再循环到系统中,以补充少量EG的过程损失,通常采用的EG/PTA加料摩尔比为1.1-1.2:1,而近年开发的高配比工艺,EG/PTA摩尔比已达2左右。 2、催化剂 PTA法生产聚酯,酯化过程中PTA溶于EG后释放后释放出的H+具有自催化作用, 可以不用催化剂。 酯化和缩聚也可以选用单一催化剂Sb(AC)3进行综合催化,吉玛工艺即用Sb(AC)3作为催化剂。由于Sb(AC)3在EG和反应体系中具有良好的溶解性和较高的催化活性,而且所得产品PET质量也较好,因此在工业生产中应用已久。根据工艺试验结果,得出催化剂用量与PET平均聚合度关系的经验式:Δ[η]=F·C0.5Δτ 式中:Δ[η]为产品PET的特性粘度[η] 与[η0]之差;Δτ为相应的反应时间;C为催化剂浓度,ppm(Sb,Sb=80-320ppm);F为工艺参数,包括温度、真空度、搅拌速度等。在连续缩聚中,一般选用催化剂浓度为[Sb]=170-220ppm,当浓度高于300ppm时,会使粘度下降。 3、温度 温度是影响EG/PTA酯化的重要因素。提高温度不仅加速反应,同时也增大了PTA在EG体系中的溶解度,从而进一步促进了酯化反应和提高酯化率。当然升高温度也加速了副反应,从而使反应产物DEG和CH3CHO增多,EG蒸发量加大,能耗提高。 BHET缩聚虽然不是放热反应,而热效应(-ΔH)甚微,仅为8.4kJ/mol左右,因此温度对平衡影响不大。根据力学规律,温度升高必将加速反应速度,所以加速反应趋向平衡,必须恰当地控制升温速度。达到平衡后,后期则要严格控制温度不能超温,防止PET热降解等副反应。 因缩聚反应为微放热反应,ΔH为负值,显然平衡常数随温度升高而减小;但升高又利于缩聚超向平衡,并促使生成的小他子产物EG等排出,反应向高聚物方向移动。 由于温度对BHET缩聚反应影响的多重性,在反应过程中,要严格依据温度操作曲线进行控制,确保达到PET的质量标准。 4、压力 因为EG的常压沸点为196℃,而PTA与EG酯化温度要远高于此,所以通常酯化过程
直接酯化法聚酯生产工艺原理
直接酯化法聚酯生产工艺原理 §1-1 反应机理 用PTA 和EG 为原料合成PET 的主要化学反应包括酯化反应和缩聚反应。 一、酯化反应: 想象一下这样的化学实验:将一定MR 比的EG/PTA 浆料加入到带有搅拌器、分馏塔的反应器中,开始搅拌、逐步升温,则PTA 和EG 开始发生化学反应。在所发生的化学反应中,固态粉末状的PTA 和液态EG 之间所发生的酯化反应反应速率很慢,一般忽略部不计。在酯化反应的初始阶段,固态PTA 和EG 之间进行的酯化反应分为如下两步:固态粉末状的PTA 溶解于EG/酯化物的混合物中,已溶解的PTA 在高温下与EG 发生酯化反应,生成酯化物;其中主要的酯化物是对苯二甲酸双羟乙酯(简称BHET )。反应的方程式如下: PTA (固体) PTA (液体) (包括2~5聚体) 由于PTA 在EG 中的溶解度很小,在酯化反应的开始阶段,反应体系是一个固液非均相体系。因为PTA 的溶解速度远大于已溶解的PTA 和EG 之间的反应速度,溶液中的PTA 总是处于饱和状态,所以在酯化反应的初始阶段,化学反应是控制步骤,此时的反应速率与PTA 和EG 的浓度无关,只是依赖于反应温度,该化学反应是零级反应。 由于PTA 在反应混合物中的溶解度远比在纯EG 中的溶解度大,随着反应的进行,PTA 的溶解度逐渐增大。当达到一定的反应程度时,PTA 完全溶解,反应进入均相酯化反应阶段,这时的酯化率就称为“清晰点”(Es 约为89%)。至此,酯化反应速率将随着PTA 和EG 浓度的改变而变化;这阶段的酯化反应可近视看作二级反应。 酯化反应是一个微放热的可逆反应,其化学平衡常数比较小,必须将反应产生的水不断除去,才能使酯化反应不断地向正反应方向进行下去。因此,在酯化反应阶段,都设有用于分离和去除水的工艺塔。酯化反应时由于PTA 上的羧基电+2CH 2OH 2OH COOH COOH +2 H 2O HOCH 2CH 2O C O CH 2CH 2OH O C O
聚酯装置说明危险因素以及防范措施
聚酯装置说明危险因素以及防范措施 集团企业公司编码:(LL3698-KKI1269-TM2483-LUI12689-ITT289-
聚酯装置说明、危险因素以及防范措施 一、装置简介 (一)装置发展及类型 1.装置发展 聚酯工艺产生于20世纪40年代,在50年代实现了工业化,是利用基础化工原料生产合成纤维的工艺技术。20世纪70年代以后,各国针对聚酯存在的吸水率低、不易染色、易产生静电等缺点进行了改性研究,取得了较多成果,使聚酯工业有了飞速的发展。70年代末,我国从前西德引进了第一套直接酯化连续缩聚生产涤纶树脂的工业化生产装置。经过几十年的发展,聚酯在我国三大合成纤维工业中已占有举足轻重的地位。截止到2003年底,我国聚酯装置的产能已经达到1115×104t/a,占世界总产量的三分之一左右。进入21世纪,随着工艺技术的不断发展,我国聚酯装置正向工艺技术更先进、经济效益更好的方向发展。 2.生产工艺路线 聚酯通常是由二元酸和二元醇经酯化和缩聚反应而制得的一种高分子缩聚物。目前用途最广的聚酯是由对苯二甲酸和乙二醇经酯化和缩聚反应所生成的聚对苯二甲酸乙二醇酯。生产聚酯的工艺技术主要取决于精对苯二甲酸、对苯二甲酸二甲酯及乙二醇的生产发展。用于合成聚对苯二甲酸乙二醇酯中间体的主要原料路线有以下几种:一种是酯交换法
(简称DMT法);另一种是直接酯化法(简称PTA法);第三种是环氧乙烷酯化缩聚路线(简称环氧乙烷法)。 酯交换法(DMT法):是将以对苯二甲酸与甲醇反应生成易于精制提纯的对苯二甲酸二甲酯,或采用对二甲苯合并氧化、酯化制成对苯二甲酸二甲酯,再将提纯的对苯二甲酸二甲酯与乙二醇进行酯交换反应制得聚酯。该方法在聚酯工业化的初期,未找到有效提纯对二甲苯的方法的时候得以广泛应用。 直接酯化法(PTA法):是以精对苯二甲酸与乙二醇为原料,进行直接酯化连续缩聚的反应制得聚酯。到90年代初期,PTA法的产量已经超过了DMT法,成为聚酯工业的主流生产工艺。 环氧乙烷法因为使用环氧乙烷代替乙二醇(EG),可省去环氧乙烷水解工序,合成反应生成物为单一的对苯二甲酸双β—羟乙酯(BHET),不需要回收设备,工艺流程短,成本低,所以是较有前途的生产方法。 从工艺流程上来看,PTA法连续化生产以前以六釜流程为主,即三段酯化,二段预缩,一段后缩,该流程技术较落后,物耗、能耗较高,已经基本被淘汰。现在的生产流程是以吉玛公司、钟纺公司、伊文达公司为代表的五釜流程,或以杜邦公司、莱茵公司为代表的三釜流程为主。五釜流程即二段酯化,二段预缩,一段后缩,三釜流程即一段酯化,一段预缩,一段后缩。他们共同的特点是技术先进、工艺流程简化、生产控制先进、装置操作弹性大。 二、重点部位及设备 (一)聚酯装置主要原料危险性分析
聚酯生产培训资料
第1章聚酯生产基础知识 聚脂我们通常称为涤纶,"涤纶"是我国的商品名,其主要成分为PET(聚对苯二甲酸乙二醇酯),由PET切片或熔体纺丝而成,主要生产工艺有PET熔体直接纺丝和PET切片纺丝两种,前者因具有步骤少、成本低等诸多优点, 目前许多大型生产装置都采用此法。 八十年代后开始兴建的PET生产装置,尤其是大规模单品种装置,大都采用PTA法直接酯化连续缩聚生产工艺。PTA法连续生产工艺主要有德国吉玛公司(Zimmer)、美国杜邦公司(DuPont)、瑞士伊文达公司(Inventa)和日本钟纺公司(Konebo)等几家技术。其中德国吉玛、瑞士伊文达和日本钟纺的技术都是“五釜流程”,美国杜邦公司的技术是“三釜流程”。、 PET是由PTA(精对苯二甲酸)与EG(乙二醇)缩聚而成,每生产1吨PET 需要消耗PTA和EG分别为0.86吨和0.34吨。 工程例:采用直接酯化、连续聚合的五釜流程技术,设计生产能力为年产180000吨聚酯。
EG动力蒸汽 短纤 浆料配制 酯化Ⅰ 酯化Ⅱ 预缩Ⅰ 预缩Ⅱ 终缩聚 切粒 长丝
外购原料PTA通过叉车将PTA贮存于PTA仓库,人工将PTA投入链板输送前的小料仓后,用链板输送方式将PTA送到聚酯大楼的日料仓。另一主要原料乙二醇贮存在罐区,用泵通过管线送入车间。催化剂三醋酸锑(或乙二醇锑)用桶装、消光剂二氧化钛用袋装运入聚酯大楼四楼。 聚酯装置主要由催化剂配制、二氧化钛配制、浆料配制、酯化、缩聚、切片生产及包装等几个工序组成。酯化缩聚设置了五个反应器,其中两个是酯化反应器,两个是预缩聚反应器,一个后缩聚反应器。两个酯化反应器为立式搅拌釜,设内盘管加热,两台反应器共用一个分离乙二醇和水的工艺塔。第一预缩聚反应器为立式槽,不设搅拌装置,用液环真空泵产生真空。第二预缩聚反应器和后缩聚反应器为圆盘转子式,两个反应器共用一套三级乙二醇蒸汽喷射泵系统(它用液环泵作排气的),在每个缩聚反应器和它的真空装置间设刮板冷凝器。在第二预缩聚反应器和后缩聚反应器之后分别设有熔体过滤器。从终缩聚反应器出来的熔体每天300吨供应长丝八条生产线,每天200吨供应另外的长丝四条生产线,其余大约有每天20--40吨熔体通过水下切粒机生产半消光切片,本装置配有两台切粒机,切出的切片通过干燥装置后,用气相脉冲输送方式将切片送至切片料仓,打包后出厂。
聚酯装置流程与聚酯生产概述(doc 14页)(完美正式版)
第一章 聚酯装置流程介绍 18万吨/年聚酯装置是中国纺织设计院设计的国产化生产线, 在工艺上以精对苯二甲酸(PTA)和乙二醇(EG)为原料,采用直接酯化连续缩聚的五釜工艺流程,装置设计负荷为日产500吨。该聚酯装置具有单系列生产能力大、生产弹性大、化工料品种少、原料消耗低、三废少等特点。在控制系统上,聚酯装置采用了先进的集中分散DCS 控制系统,具有操作控制方便、人机联系好、功能齐全、可靠性高等特点。 本聚酯装置的产品为半消光纤维级聚酯熔体及切片,可用于直接纺制涤纶长丝或短纤。 聚酯生产装置包括主生产装置和辅助生产装置两大部分。主生产装置包括以下生产工序: (一)PTA 卸料及输送(设PTA 库房两座,两座库房面积共9800m 2,贮存周期约25天) (二)浆料制备 (三)酯化(第一、二酯化及工艺塔) (四)预缩聚(第一、二预缩聚,预聚物过滤及输送) (五)终缩聚(终缩聚、熔体输送及过滤) (六)切片生产、输送及包装 (七)尾气淋洗 (八)催化剂制备 (九)消光剂制备 辅助生产装置包括以下部分: (一)热媒站(配备单台热负荷800万大卡的热媒炉三台,两用一备) (二)罐区(设容积5000m 3的乙二醇贮罐两个,贮存周期约52天;设容积1000m 3的燃料油贮罐两个,贮存周期约32天。) (三)过滤器清洗 (四)化验室 聚酯装置主工艺流程图如下: 其余大约有每天20--40吨熔体通过水下切粒机生产半消光切片,本装置配有两台切粒机,切出的切片通过干燥装置后,用气相脉冲输送方式将切片送至切片料仓,打包后出厂。 终缩聚预缩Ⅱ 预缩Ⅰ酯化Ⅱ酯化Ⅰ浆料配制EG动力蒸汽
辅助装置有:热媒(HTM)系统(主要由三台800万大卡的热媒炉组成)、过滤器清洗等辅助设施。本装置用液相热媒作反应器等设备、管线的加热和保温,共设置了十一个二次热媒回路,分别服务不同的使用点。 聚酯生产中的每一段工序其作用分别简要说明如下: 1、浆料配制 原料PTA自PTA储存料仓采用星型给料器出料,通过振动筛去除夹带的异状物,质量流量计连续计量后,送入浆料调配槽。原料PTA和MEG以及催化剂溶液按规定比例连续送入浆料配制槽中,由特殊设计的搅拌器使之充分混合并配制为恒定摩尔比(MEG/PTA)的浆料,经浆料输送泵连续送入酯化反应器中。 2、酯化反应 酯化反应系统共设置两台酯化反应器。在第一酯化反应器中酯化率可以达到91%;第二酯化反应器后控制酯化率在96.5%左右。通过调节反应器的温度、压力和液位等,可以控制反应酯化率,同时保证装置的稳定运转。两个酯化反应器的汽相物采用一个工艺塔用于乙二醇回收。分离的重组分乙二醇回流到两个酯化反应器中。塔顶轻组分冷凝后,凝液用作塔的回流液,其余作为生产污水送污水预处理系统处理。 3、预缩聚反应 预缩聚反应系统共设置两台预缩聚反应器。第一预缩聚反应器的操作压力控制在100mbar左右,使用乙二醇蒸汽喷射泵和液环真空泵产生真空,并控制第二预缩聚反应器的操作压力在10mbar左右。并与终缩聚反应器共用乙二醇蒸汽喷射泵产生真空。在预缩聚反应器及其真空设备之间设置刮板冷凝器,采用乙二醇喷淋以捕集汽相中的乙二醇及夹带物。乙二醇凝液收集在液封槽中,以循环冷却水作为冷却介质,通过冷却器降低温度后循环使用。因乙二醇凝液中水含量较高,可送入酯化反应系统工艺塔中进行分离。第二预缩聚反应器采用齿轮泵出料,经预聚物熔体过滤器过滤后送入终缩聚反应器中。 4、终缩聚反应 设置一台终缩聚反应器,终缩聚反应器中的操作压力控制在1mbar左右。通过控制真空度使熔体的聚合度达到指标要求。为控制终缩聚系统真空度,采用冷冻水作为乙二醇喷淋液的冷却介质。新鲜乙二醇加入在终缩聚反应器的刮板冷凝器、乙二醇蒸发器和液环真空泵组中。终缩聚反应器和乙二醇蒸汽喷射泵组气相凝液水含量较低,无需分离即可直接回用。该部分乙二醇和预缩聚系统经工艺塔分离后的乙二醇混合,可直接送到浆料配制槽用作浆料调配用。采用乙二醇蒸汽喷射产生真空,用液环泵作为它的排气级。通过调节补加在喷射泵吸入口的乙二醇蒸汽量,控制操作真空度。喷射泵组的第一级混合冷凝器的真空度在6 mbar左右,第二予缩聚反应器的刮板冷凝器的未凝气引至这个混合冷凝器。设置乙二醇蒸发器,为喷射泵提供动力蒸汽。 5、熔体分配及切片生产 聚酯熔体采用齿轮泵出料和增压,经熔体过滤器过滤后,通过特殊设计的熔体分配系统,一部分送熔体直纺长丝装置,另一部分送切片生产系统铸带切粒。设置二条切粒生产线,当其中一台切粒机换刀维修时,另一台切粒机可承担全部负荷。聚酯熔体从铸带头挤出成型,采用除盐水作为冷却介质,通过换热器冷却循环使
涤纶聚酯生产装置的真空系统
涤纶聚酯生产装置的真空系统 摘要:文章介绍了聚酯生产中所使用的真空获得系统的发展过程;华达公司开发、设计、生产的真空系统的技术原理及特点。 关键词:聚酯;真空系统; 一、涤纶聚酯生产装置中真空泵发展历程概述 在上世纪最早的涤纶聚酯生产装置中,采用机械真空泵(滑罗机组)作为真空获得设备。由于机械真空泵存在缺点: A、不能抽除可凝性气体(今后干式螺杆泵发展情况怎样?); B、易受齐聚物堵塞,真空度波动大; C、随着单线产量规模增大,需要许多机械真空泵组并联,机构庞大复杂;维修复杂; 50年代(国外)~60年代(国内)开始,逐渐被水蒸汽喷射真空泵所取代(上海涤纶厂等)。 采用水蒸汽喷射真空泵产生新的问题: A、能耗大; B、产生大量废水; C、原料EG损耗大; 60年代开始,德国吉玛公司开始研制以涤纶聚酯原料的乙二醇蒸汽驱动的EG喷射真空泵——EG液体喷射真空泵和EG蒸汽喷射真空泵,国内于1977年由北京燕山长征化工厂首先引进使用。 整个80~90年代,我国引进的或国产的涤纶聚酯装置,大部分仍采用水蒸汽喷射真空泵,小部分采用EG蒸汽喷射真空泵(仪化)。 进入21世纪,我国引进的或国产的涤纶聚酯装置,大部分采用EG蒸汽喷射真空泵,小部分仍采用水蒸汽喷射真空泵。 实践证明,在涤纶聚酯生产中,EG蒸汽喷射真空泵具有能耗小,不损耗原料EG,不产生废水,真空度稳定等优点。 二、华达公司发展EG真空泵历程概述 华达公司(前身建华真空设备机械厂)创立时,生产的第一台设备——5级真空泵就是为涤纶聚酯生产服务的。
扬州惠通的第一条5000T/A线使用的也是我公司的5级泵。从1991年至2002年我们为间歇式提供了500多台(套)5级水蒸汽喷射真空泵(是中国聚酯工业发展的罪人,谢晓中语); 1999年,我公司开展EG真空泵的理论研究; 2000年,自费试制了1台EG真空泵在浙江超同安装,进行了性能测试; 2001年,在试验设备的基础上,为上海浦源免费制造2台,在间歇式生产中投入使用; 2002年,为上海石化CP-3提供第1台(与汪总、新良合作); 2003年到2008年,为近百条间歇式生产线提供了EG真空泵; 同时,从1994年开始为上海石化2号聚酯的6条钟纺线进行真空泵改造,1998年,随着改造进入到EG捕集器的改造阶段;我们开始接触涤纶聚酯生产装置中的整个真空系统。 2002年,我公司在加盟汪总——聚友公司团队后,使我们有机会参与了张家港新欣化纤的8万吨、新苏15万吨、上海石化的15万吨、埃及4+0.4万吨、新港15+3万吨、华特斯8万吨、,弘兴8+2万吨、金胜10万吨等涤纶聚酯项目工作; 同时,我们还参与了国内其他十几套涤纶聚酯装置真空系统的新建和改造工作:上海石化2号聚酯的6条钟纺线、3号聚酯的2条杜邦线、洛阳石化的2条杜邦线、三房巷的3条杜邦线、海南兴业的1条杜邦线、华西的1条吉玛线、华宏1条线、宜兴2条线、中捷1条线。 可以这么说,2003年之前,华达公司对EG真空泵及捕集器的开发实践好比一个人的儿童状态,2003年之后,在聚友公司的庇荫下逐步成年,为此,我在这里,谨代表华达公司对在座的和不在座的所有聚友公司的同仁们,表示衷心的感谢! 三、我公司真空系统的特点 通过以上提到的各项工作的实践,我们对涤纶聚酯生产装置中真空系统:捕集器和EG蒸汽喷射真空泵系统的设计、生产、调试积累了一定的经验,形成了一定的特点,特总结如下,供大家参考,并请斧正。 1、EG捕集器部分 在涤纶聚酯装置中,EG捕集器起到捕集缩聚釜中产生的大量可凝性气体和低分子齐聚物的作用,是真空系统的关键设备。 如果EG捕集器对可凝性气体捕集效果不好,可凝性气体得不到充分冷凝,将大大增加真空泵的负荷,造成系统真空度达不到要求。
国产化聚酯装置的现状和展望
国产化聚酯装置的现状和展望 【作者:郭兴永】 我国聚酯工业的现状 我国聚酯工业发展简况:最早的世界聚酯是由杜邦公司于1928年用脂肪族二酸与脂 肪族二醇合成的,但因其熔点低(~65 `}C )、易水解、不耐碱而无实用价值。1941年英国的温菲尔德(whinfield )选用对苯二甲酸(PTA)与乙二醇(EG)合成聚对苯二甲酸乙二酯,制成具有实用价值的聚酯,自此以后,聚酯工业逐渐发展起来。我国聚酯起步较晚,70年代初,金山、辽化和天化从国外成套引进了DMT生产工艺路线的聚酯生产装置。上世纪70年代中国内地开始在上海、辽宁、天津等地建设大型连续化聚酯生产装置。1985年,仪征化纤一期工程正式投产,标志着内地聚酯工业开始快速发展。到1990年,中国内地聚酯年产能力达到115万吨,占世界总产能的9%,居世界第四位。90年代前后,国家又相继批准引进十余套聚酯装置。但由于引进的先进连续缩聚技术和设备价格高昂,投资成本太大,1998年以前受资金、原料制约,中国内地聚酯产能和产量增速缓慢。1998年,中国内地聚酯年产能力为275万吨,排在美国、韩国及中国台湾省之后,位居世界第四位。在1999年到2000年期间,聚酯业的利润高起,当时每吨聚酯切片利润高达2000元左右,在高额利益的驱使下,吸引了大量民营资本,加之国产聚酯技术的日渐成熟投资下降,使聚酯发展迅速升温。随着市场发育逐步成熟,中国内地资源配置作用在纺织领域更加趋向明显。内地许多民营纺织企业在生产规模扩大后,直接感受到了来自原料的制约。为了延伸产业链,抵御市场风险,获取更大效益,这些企业想方设法上聚酯项目,致使国内东部地区在2000年前后形成一股兴建小聚酯装置(主要是间歇式聚合装置)热潮,其中江苏省局部地区几乎每个乡镇都建了聚酯厂。到2000年底,中国内地聚酯年产能力达到568万吨,产量512万吨,一跃成为世界第一。 进入21世纪后,中国内地聚酯工业发展又有重大突破。设备国产化的技术逐渐,聚酯投资成本也比上世纪90年代初下降七八成,进而掀起了新一轮聚酯投资热。2000~2002年,中国内地新增聚酯年产能力462万吨,占世界新增总产能的72%。2002年世界聚酯总年产能力达3944万吨,国内产能为1032万吨,中国内地占了1/4多。发展到2003年至1260多万吨,短短三年增加了一倍多。尤其是2001年产能增幅最大由2000年595万吨迅速增加为881万吨,年增长率达到了48%。民营企业已成为聚酯行业的生力军,占据半壁江山。 近几年来,世界其他国家几乎没有新的聚酯装置投产,在中国内地产能快速增长,2004年底时国内聚酯产能达1650万吨,2005年1-7月又有19条大聚酯线投产,共计299万吨产能。目前仍有390万吨在建聚酯产能,去除小聚酯长年闲置的约140万吨产能,预计到2005年底国内实际可能形成的有效聚酯产能约1950-2000万吨之间。目前中国聚酯能力已占全球总能力的近50%。在纺织工业强劲拉动下, 2005年中国内地聚酯需求量达到1300万吨。 聚酯技术方面的发展:20世纪70年代以前,只有零星小的间歇聚酯。70年代后期燕山石化公司及仪化公司又成套引进了PTA工艺技术,最大单线公称生产能力为200吨/天。以后全国许多省份也都陆续从吉玛、杜邦、英文塔等公司引进了聚酯装置。引进方式,也从70年代的成套引进,发展到设备部分国内分交,由国外承担基础设计,国内完成施工
聚酯装置说明、危险因素以及防范措施(正式)
编订:__________________ 单位:__________________ 时间:__________________ 聚酯装置说明、危险因素以及防范措施(正式) Deploy The Objectives, Requirements And Methods To Make The Personnel In The Organization Operate According To The Established Standards And Reach The Expected Level. Word格式 / 完整 / 可编辑
文件编号:KG-AO-8348-40 聚酯装置说明、危险因素以及防范 措施(正式) 使用备注:本文档可用在日常工作场景,通过对目的、要求、方式、方法、进度等进行具体、周密的部署,从而使得组织内人员按照既定标准、规范的要求进行操作,使日常工作或活动达到预期的水平。下载后就可自由编辑。 一、装置简介 (一)装置发展及类型 1.装置发展 聚酯工艺产生于20世纪40年代,在50年代实现了工业化,是利用基础化工原料生产合成纤维的工艺技术。20世纪70年代以后,各国针对聚酯存在的吸水率低、不易染色、易产生静电等缺点进行了改性研究,取得了较多成果,使聚酯工业有了飞速的发展。70年代末,我国从前西德引进了第一套直接酯化连续缩聚生产涤纶树脂的工业化生产装置。经过几十年的发展,聚酯在我国三大合成纤维工业中已占有举足轻重的地位。截止到20xx年底,我国聚酯装置的产能已经达到1115×10的4次方(原多次方位置应该标在右
上位置,但word格式不支持)t/a,占世界总产量的三分之一左右。进入21世纪,随着工艺技术的不断发展,我国聚酯装置正向工艺技术更先进、经济效益更好的方向发展。 2.生产工艺路线 聚酯通常是由二元酸和二元醇经酯化和缩聚反应而制得的一种高分子缩聚物。目前用途最广的聚酯是由对苯二甲酸和乙二醇经酯化和缩聚反应所生成的聚对苯二甲酸乙二醇酯。生产聚酯的工艺技术主要取决于精对苯二甲酸、对苯二甲酸二甲酯及乙二醇的生产发展。用于合成聚对苯二甲酸乙二醇酯中间体的主要原料路线有以下几种:一种是酯交换法(简称DMT法);另一种是直接酯化法(简称PTA法);第三种是环氧乙烷酯化缩聚路线(简称环氧乙烷法)。 酯交换法(DMT法):是将以对苯二甲酸与甲醇反应生成易于精制提纯的对苯二甲酸二甲酯,或采用对二甲苯合并氧化、酯化制成对苯二甲酸二甲酯,再将提纯的对苯二甲酸二甲酯与乙二醇进行酯交换反应制