人工挖孔桩施工工艺及流程

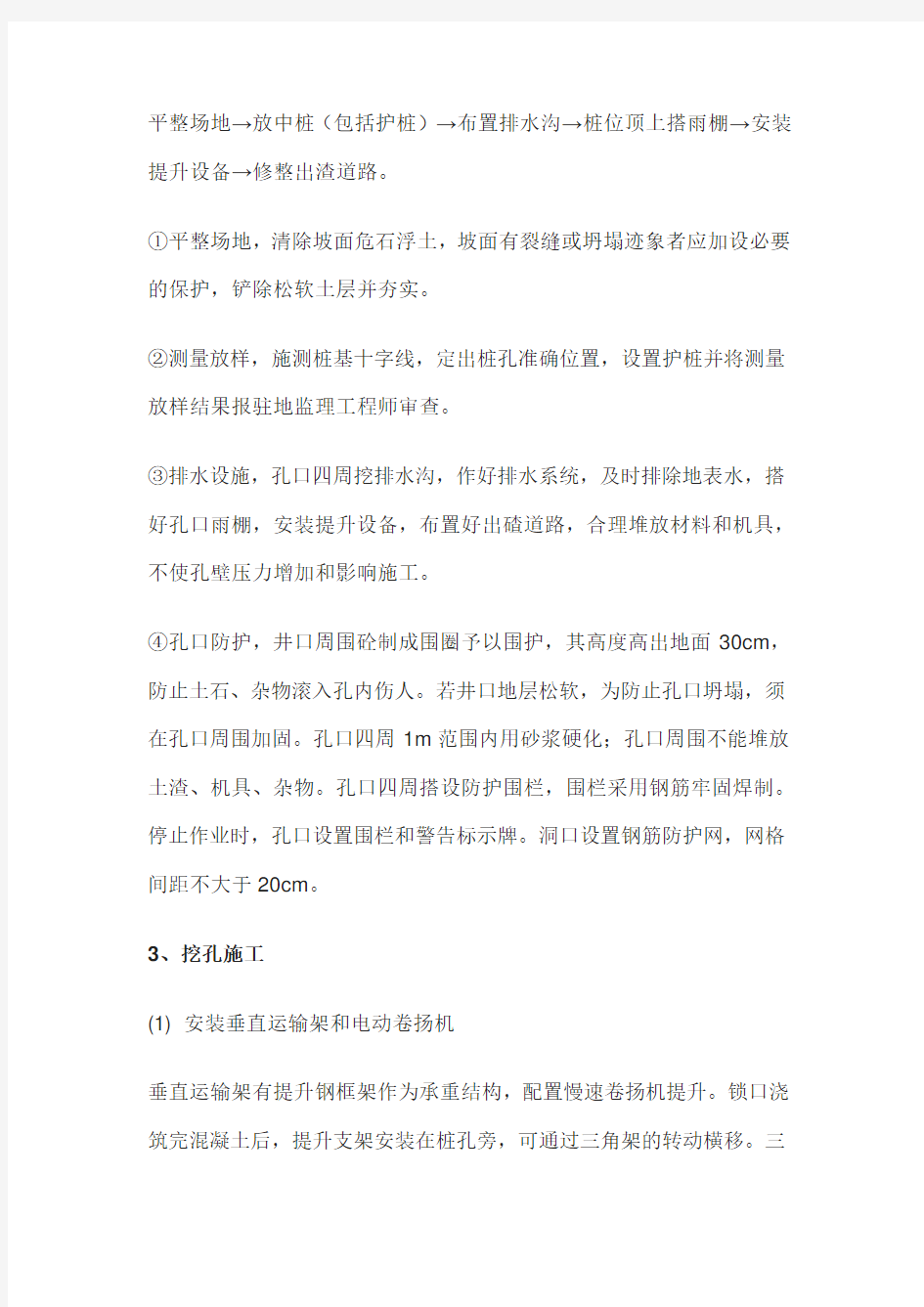
人工挖孔桩施工工艺及流程
尽管现在大型机械发展很迅速,但是在落差比较大的地形,机械总有上不去的地方,所以最原始的方法人工挖孔就不得不被用到施工去,人工挖孔危险系数特别大,所以,一个好的施工工艺和流程是非常重要的。话不多说,直奔正题。
1、总体施工工艺
挖孔桩施工工艺
2、施工准备
平整场地→放中桩(包括护桩)→布置排水沟→桩位顶上搭雨棚→安装提升设备→修整出渣道路。
①平整场地,清除坡面危石浮土,坡面有裂缝或坍塌迹象者应加设必要的保护,铲除松软土层并夯实。
②测量放样,施测桩基十字线,定出桩孔准确位置,设置护桩并将测量放样结果报驻地监理工程师审查。
③排水设施,孔口四周挖排水沟,作好排水系统,及时排除地表水,搭好孔口雨棚,安装提升设备,布置好出碴道路,合理堆放材料和机具,不使孔壁压力增加和影响施工。
④孔口防护,井口周围砼制成围圈予以围护,其高度高出地面30cm,防止土石、杂物滚入孔内伤人。若井口地层松软,为防止孔口坍塌,须在孔口周围加固。孔口四周1m范围内用砂浆硬化;孔口周围不能堆放土渣、机具、杂物。孔口四周搭设防护围栏,围栏采用钢筋牢固焊制。停止作业时,孔口设置围栏和警告标示牌。洞口设置钢筋防护网,网格间距不大于20cm。
3、挖孔施工
(1) 安装垂直运输架和电动卷扬机
垂直运输架有提升钢框架作为承重结构,配置慢速卷扬机提升。锁口浇筑完混凝土后,提升支架安装在桩孔旁,可通过三角架的转动横移。三
角形脚架安装在桩孔正上方,能过电动卷扬机提升渣桶,三角架沿主轴可横向移动。架底可压石头以增加其稳定性。
在运输架上安装滑轮组,穿上卷扬机钢丝绳,在架底位置安装卷扬机,地面运土用手推车或小翻斗车。
在地面按护壁处理挖深1m,安放护壁模板,浇筑C30砼形成井圈,井圈上口即井台座比周围地面或桩基顶标高(两者以高标高为准)高出30cm,以避免井口进水或掉落杂物。
圈顶通过测量准确测设四个控制点以铁钉做标记,通过这四个控制点校核孔中心位置和垂直度。在井圈内壁用油漆做水准标记,以便控制桩底高程。
(2) 安装活底吊桶、活动盖板、照明、水泵及通风机
在安装滑轮组和吊桶时,保持吊桶与孔壁之间留有适当距离,防止施工过程中吊桶碰撞孔壁,预防安全事故,井底照明必须用低压电源(36V)、防破电线、带罩的防水、防爆照明灯。孔口四周设置围护栏。当桩孔深度大于10m时,应进行井下机械通风,加强空气的流动,必要时向井下输送氧气,防止有毒气体对人体的危害,操作时上下人员轮流作业,桩孔上方人员必须密切观测桩孔下人员的情况,互相呼应,预防安全事故的发生。
当地下渗水量不大时,随挖随将泥水用吊桶运出,当地下水量较大时,在桩孔底先挖集水坑,用高扬程水泵抽水,边降水边挖土,水泵的规格
应按照抽水量选定。地下水位较高时,应先采用统一降水措施,然后再开挖。
桩孔口安装水平推移的活动安全盖板,当桩孔内挖孔时,应掩好安全盖板,防止杂物掉下砸伤人。吊运土时,才打开安全活动盖板一定面积,留一定宽度作为挖孔人员的安全空间。
井孔内搭设应急时的安全绳和软爬梯,并随桩孔深放长至作业面。不能用人工拉绳子运送作业人员和脚踩护壁凸缘上下桩孔。
(3) 桩基开挖
土层采用人工直接开挖,局部采用风镐配合,用小型卷扬机提升出渣,每开挖1米护壁1米,上口护壁厚30cm,下口厚20cm。强度低的中风化岩层采用风镐破碎挖出,强度高的弱风化岩层采用风钻钻孔,布置小剂量炸药爆破,风镐配合破碎。
岩石采用风钻钻炮眼,布置小药量电引爆的浅眼爆破法施工。护壁强度达到一定强度后才能爆破,防止震坍孔壁。爆破后利用空压机及时通风排出有害气体,再采用人工清凿继续开挖。以此种方式循环进行施工,直至桩底设计标高.爆破施工时严格按照爆破设计的警戒范围布置安全警戒(该爆破由于属孔内爆破,根据药量计算及经验判断,飞石横向散落范围很小,故警戒范围定为50米),警戒时,警戒人员从爆区由里向外清场,所有与爆破无关的人员、设备撤离到安全地点并警戒。确认人员设备全部撤离危险区,具备安全起爆条件时,爆破工作领导人才能发出起
爆信号。爆破员收到起爆信号后,才能进行爆破器充电并将主线接到起爆器上,充好电以后,进行起爆。爆破后,严格按照《爆破安全规程》规定的等待时间超过15min,方准许检查人员进入爆区进行检查,确认安全后,方准发出解除警戒信号。
孔桩入岩爆破的岩石为中、微风化,周边对所爆破岩石的约束力大。根据孔桩工程入岩的爆破参数类比、修正,得出单位用药量系数K如下表:
单位用药量系数表
孔桩入岩采用手持式气动凿岩机钻眼,炮眼直径d=32-42mm,间距按a=(15-20)d布置,即a=500-800mm。在小直径孔桩入岩爆破中,岩石的周边夹制力大,炮眼利用率低。
一般炮眼深度L取孔桩直径D的0.6-0.8倍,即L=(0.6-0.8)D。其中掏槽眼应比周边眼加深100-200mm。
孔桩爆破炮眼利用率η一般可以达到85-95%,则循环进尺Lˊ=ηL=(0.85-0.95)L。
在小直径孔桩爆破中,工作面通常按掏槽眼3-4个,辅助眼4-6个,周边眼7-13个。其中掏槽眼按照锥形布置,倾角10-15°;辅助眼和周边眼多用垂直眼,周边眼距孔桩护壁100-200mm均匀布置。
每循环进尺所需用药量Q=(π×D×D/4)×L×K
式中:
Q——每循环进尺用药量(g)
K——单位用药量系数(g/m3)
D——孔桩掘进直径,(m)
L——炮眼的平均深度,(m)
(2)单孔理论装药量q= Q/N
式中:
q——单孔理论装药量(g)
Q——每循环进尺用药量(g)
N——工作面炮眼数量(个)
一般情况下,掏槽眼的药量qt比周边眼及辅助眼药量qb多装20-25% qt=(1.2-1.25)q
qb=(0.85-0.95)q
式中:qt——掏槽眼装药量,(g)
qb——周边眼装药量,(g)
孔桩掘进爆破选用非电毫秒雷管网络电雷管起爆,禁止使用导火索、火雷管起爆网络。非电雷管起爆网络的接头一定要有良好的气密性,接点应离开泥水面。同时,为取得较好的爆破效果,保护护壁的稳定性,应选用微差爆破使用的非电毫秒雷管,辅助眼滞后掏槽眼起爆0.1s以上,周边眼滞后辅助眼起爆0.1s以上,按顺序依次起爆。
4、护壁施工
在桩基挖孔施工到位时,清理孔壁四周松散碎落体,支立护壁模板,护壁模板采用上小下大的梯形钢模,钢模拼装后保证护壁厚度,上口厚15cm,下口厚10cm,护壁模板内侧用钢筋或钢管加固,锁紧上口,固
定下口。护壁砼采用C30混凝土浇注,可将砂、石、水泥等材料运至孔口附近,用小型搅拌机拌合,用吊斗将拌合好的护壁混凝土运至桩底护壁待浇处,人工浇注护壁砼,用钢筋等将混凝土捣固密实。
人工挖孔桩砼护壁设计
为防止孔内大量渗水,上次护壁和下次护壁间的接缝要密实。孔壁渗水量大的地方预埋排水管,渗水量小的地方直接用砼填塞封堵。浇注护壁砼时要保证护壁砼振捣密实,下次护壁砼的上口超出上次护壁砼下口5cm,起到良好的防水作用,减小渗水量。
此外,桩孔注意每次砼护壁浇筑前都要将内模定位一次,以保证桩的垂直度和水平位置。
5、溶洞及裂隙处理
技术主管与作业队长首先要阅读地质资料,掌握溶洞出现的桩号,范围大小,对每个孔位的的地质柱状图技术人员及作业队长都要熟悉。挖孔桩开挖前,先查阅地质勘察报告,确认开挖桩位地底有无溶洞。有溶洞的桩孔,对溶洞位置、大小及埋深做好记录。对于有溶洞的桩孔,在第一节护壁顶面预埋2根Φ12钢筋作为孔内作业人员安全绳的锚固点,预埋置于护壁钢筋外侧,预埋深度为50cm,外露长度30cm,外露段末端做成180°U型环,预埋到护壁上。
溶洞现场图
人工挖孔桩桩基侧面溶洞图及处理图
孔内开挖至距溶洞顶板2m高度时,孔内人员必须套好安全带,扣好安全绳,安全绳末端扣在第一节护壁顶面预埋锚固筋上。安全绳长度应考虑孔内人员1.2m正常活动长度。当遇到孔内坍陷等情况时,由孔口工人收缩安全绳,将孔内工人提出桩孔。
当孔内开挖至距溶洞顶板1m高度时,放缓开挖进度,基岩采用人工机具开挖。接近溶洞顶板时,采取局部开挖贯穿顶板,并观察洞内填充情况。
(1)当填充物为满填时,用钎探法探测填充物的密实情况及溶洞深度,填充物较密实时按照正常情况开挖并按设计做好护壁。当填充物为虚土,溶洞直径小于桩基开挖孔径时,按正常情况开挖至溶洞底板,底板作为桩基持力层;溶洞直径大于桩基开挖孔径,溶洞深度小于3m,直接清除洞内虚土,对溶洞底板上桩孔位置凿平作为桩基持力层;溶洞直径大于桩基开挖孔径,溶洞深度大于3m时,沿孔周插打钢花管,间距