主减速器设计课程设计说明书-毕设论文
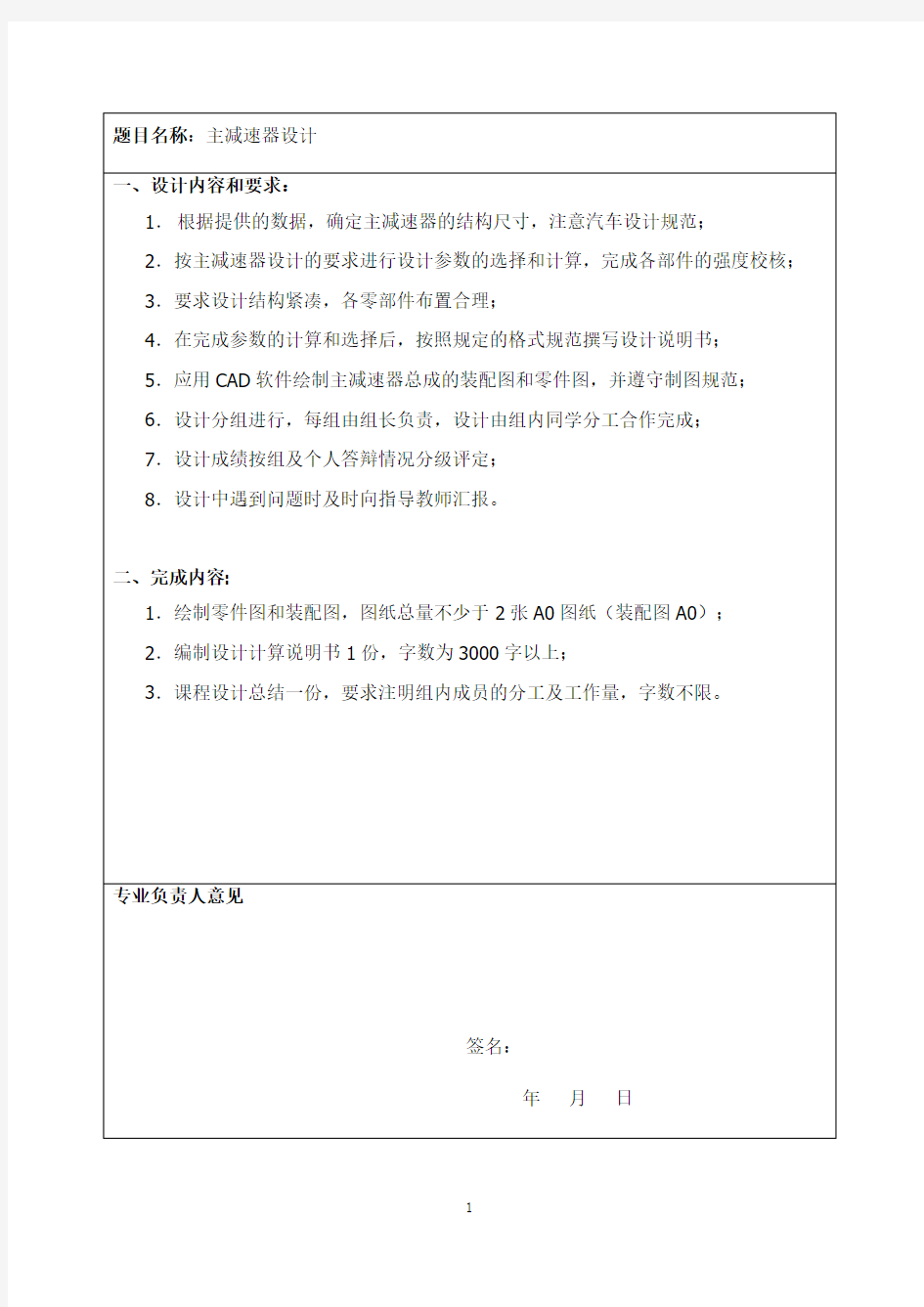
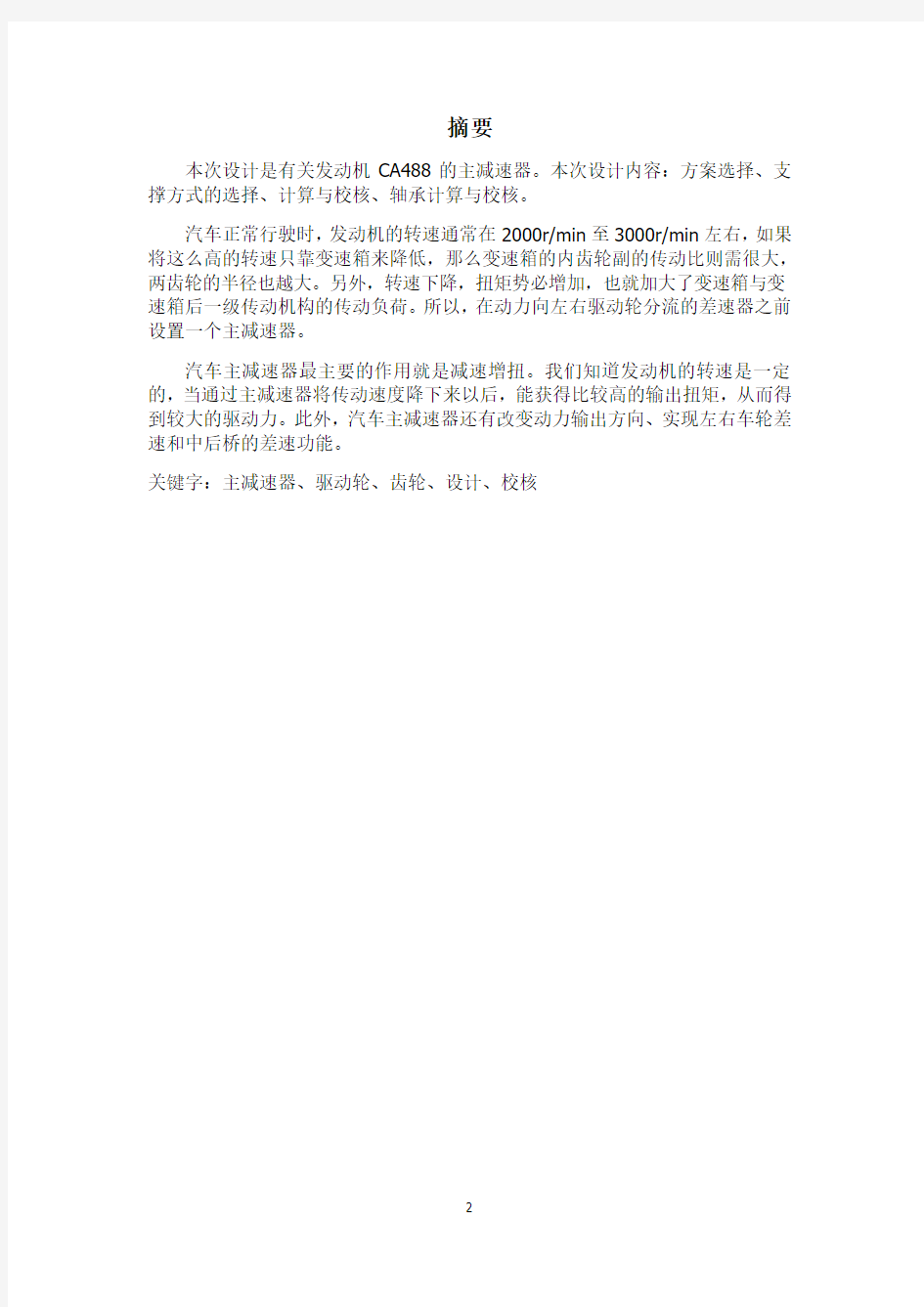
题目名称:主减速器设计
一、设计内容和要求:
1.根据提供的数据,确定主减速器的结构尺寸,注意汽车设计规范;
2.按主减速器设计的要求进行设计参数的选择和计算,完成各部件的强度校核;
3.要求设计结构紧凑,各零部件布置合理;
4.在完成参数的计算和选择后,按照规定的格式规范撰写设计说明书;
5.应用CAD软件绘制主减速器总成的装配图和零件图,并遵守制图规范;
6.设计分组进行,每组由组长负责,设计由组内同学分工合作完成;
7.设计成绩按组及个人答辩情况分级评定;
8.设计中遇到问题时及时向指导教师汇报。
二、完成内容:
1.绘制零件图和装配图,图纸总量不少于2张A0图纸(装配图A0);
2.编制设计计算说明书1份,字数为3000字以上;
3.课程设计总结一份,要求注明组内成员的分工及工作量,字数不限。
专业负责人意见
签名:
年月日
本次设计是有关发动机CA488的主减速器。本次设计内容:方案选择、支撑方式的选择、计算与校核、轴承计算与校核。
汽车正常行驶时,发动机的转速通常在2000r/min至3000r/min左右,如果将这么高的转速只靠变速箱来降低,那么变速箱的内齿轮副的传动比则需很大,两齿轮的半径也越大。另外,转速下降,扭矩势必增加,也就加大了变速箱与变速箱后一级传动机构的传动负荷。所以,在动力向左右驱动轮分流的差速器之前设置一个主减速器。
汽车主减速器最主要的作用就是减速增扭。我们知道发动机的转速是一定的,当通过主减速器将传动速度降下来以后,能获得比较高的输出扭矩,从而得到较大的驱动力。此外,汽车主减速器还有改变动力输出方向、实现左右车轮差速和中后桥的差速功能。
关键字:主减速器、驱动轮、齿轮、设计、校核
1 课程设计的目的 (5)
2 单级主减速器结构方案分析 (6)
2.1 主减速器的功用 (6)
2.2 主减速器的结构形式 (6)
2.2.1 主减速器的齿轮类型选择 (6)
2.2.2 主减速器的减速形式选择 (6)
2.3 主减速器主、从动锥齿轮的支撑方案 (6)
2.3.1 主动锥齿轮的支撑 (6)
2.3.2 从动锥齿轮的支撑 (7)
3 主减速器的基本参数选择与设计计算 (8)
3.1 主减速器计算载荷的确定 (8)
3.2 主动锥齿轮的计算转矩 (9)
3.3 主减速器锥齿轮的主要参数选择 (9)
3.3.1 主、从动锥齿轮齿数Z1和Z2的确定 (9)
3.3.2 从动锥齿轮大端分度圆直径D2和端面模数m s (10)
3.3.3 主、从动锥齿轮齿面宽1b和2b的计算 (11)
3.3.4 中点螺旋角β的选择 (11)
3.3.5 双曲面齿轮副偏移距E (11)
3.3.6 双曲面齿轮的偏移方向 (12)
3.3.7 螺旋方向的确定 (12)
3.3.8 法向压力角α (13)
4 主减速器双曲面锥齿轮的强度计算 (14)
4.1 单位齿长圆周力的计算 (14)
4.2 轮齿的弯曲强度计算 (14)
4.2.1 主动锥齿轮强度校核 (14)
4.2.2 从动锥齿轮强度校核 (15)
4.3 轮齿的表面接触强度计算 (15)
4.4主减速器锥齿轮的材料选择 (15)
5 主减速器轴承计算及选择 (17)
5.1 锥齿轮齿面上的作用力 (17)
5.1.1 齿宽中点处的圆周力F (17)
5.1.2 锥齿轮的轴向力和径向力 (18)
5.2 主减速器轴承载荷的计算 (19)
5.3 锥齿轮型号的确定 (21)
结论 (23)
参考文献 (23)
1 课程设计的目的
本课程设计是在学完“汽车设计”课程之后进行的,旨在对车辆设计的学习进行总结,对所学知识加以巩固。通过设计过程,要求学生能够全面掌握《汽车设计》课程中的基本理论知识,试验方法,并能够分析和评价汽车及其各总成的结构与性能,合理选择设计方案及有关参数,掌握汽车主要零部件设计与计算方法和总体设计的一般方法。
2 单级主减速器结构方案分析
2.1 主减速器的功用
(1) 使发动机传给驱动轮的转速降低,转矩增大。
(2) 改变发动机传动驱动轮转矩短的传递方向(采用纵置发动机)。
2.2 主减速器的结构形式
主减速器可根据齿轮类型,减速形式以及主、从动齿轮的安装及支承方式的不同分类。
2.2.1 主减速器的齿轮类型选择
主减速器齿轮有弧齿锥齿轮,双曲面齿轮,圆柱齿轮和涡轮蜗杆等形式,运用最为广泛的是弧齿锥齿轮好双曲面齿轮,一般情况下,当主减速器比大于4.5而轮廓尺寸又有限时,采用双曲面齿轮传动更为合理,而当传动比小于2.0时,双曲面齿轮传动的主动齿轮相对于弧齿锥齿轮传动的主动齿轮显的过大,此时选用弧齿锥齿轮更合理,因为后者具有较大的差速器可利用空间,对于中等传动比,两种齿轮传动均可采用,本次设计的主减速器传动比为4.55,故采用双曲面轮齿。
2.2.2 主减速器的减速形式选择
本次设计主要考虑汽车的动力性和经济性,所以根据主减速器比i0可选用单级主减速器和双级主减速器。
单级主减速器具有结构简单、质量小、尺寸紧凑、制造成本低等优点,因而广泛应用于主传动比i0≤7的汽车上。
双级主减速器于单级主减速器相比,双级主减速器在保持离地间隙相同时,可得到大的传动比,i0一般为7~12;但其尺寸、质量均较大,结构复杂,制造成本也显著增加,因此主要应用在总质量较大的商用车上。本次设计的主减速器的传动比为4.55,故采用单级主减速器。
2.3 主减速器主、从动轮的支承方案
2.3.1 主锥齿轮的支承
主锥齿轮的支承形式可分为悬臂式支承和跨置式支承,悬臂式支承结构简单,支承刚度较差,用于传递转矩较小的主减速器上,在需要传递较大转矩情况下,最好采用跨置式。本次设计发动机的最大转矩为157N·m,故采用悬臂式支承。
2.3.2 从动锥齿轮支承
从动锥齿轮的支承刚度与轴承的形式,支承间的距离及载荷在轴承之间的分布比例有关,从动锥齿轮多采用圆锥滚子轴承支承。
3 主减速器的基本参数选择与设计计算.
3.1 主减速器计算载荷的确定
采用格里森齿制齿轮计算载荷的三种确定方法
(1) 按发动机最大转矩和最低档传动比确定从动锥齿轮的计算转矩T ce m N 82.2711n
······0f 1emax d ce
?==
η
i i i T k k T (3-1)
式中:
i 0——主减速器传动比,i 0=4.55; i 1——主减速器一档传动比,i 1=4.218; i f ——分动器传动比,i f =1;
η——发动机到万向传动轴之间的传动效率,η=0.9; k d ——接离合器所产生的动载系数,16195
.0emax
a j ≥=T g
m f 得k d =1; k ——液力变矩器变矩系数,k =[(k 0-1)/2]+1,k 0为最大变矩系数(k 0=1); n ——驱动桥数,n =1; T emax ——发动机最大转矩。
(2) 按驱动轮打滑转矩确定从动锥齿轮转矩T cs
m N 5.4292m
m r
22cs
?==
ηφi r m G T
(3-2)
式中:
G 2——满载状态下一个驱动桥的静载荷,G 2=m a *9.8*0.55=11346N ; r r ——车轮滚动半径,r r =195*80%+14*25.4/2 mm=333.8mm ; m 2——汽车最大加速度时的后轴负载荷转移系数,m 2=1.2; Φ——轮胎与路面间的附着系数,Φ=0.85; i m ——主减速器从动轮之间的传动比,i m =1; ηm ——主减速器到车轮间的传动效率,ηm =1。
(3) 按汽车日常行驶平均转矩确定从动锥齿轮的计算转矩T cf
)
(i H R m m r
a ef f f
f n
i r G T +
+
=
η (3-3)
式中:
G a ——汽车满载总质量;
f R ——道路滚动阻力系数(轿车f R =0.010~0.015); f H ——平均爬坡能力系数(轿车取0.08); f i ——汽车性能系数,
16)
(195
.0max
≥+e r a T G G 时,f i =0。
代入公式可得:T cf =782.11N·m
当计算锥齿轮最大应力时T c =min[T ce ,T cs ]; 当计算锥齿轮的疲劳寿命时T c =T cf 。
3.2 主动锥的计算转矩T z
G
0c z ηi T T =
(3-4)
T z ——主动齿轮的计算转矩; i 0——主减速比;
ηG ——主、从动锥齿轮间的传动效率,双曲面齿轮副取0.9。
(1) 按发动机的最大转矩T ce 和传动系最低档速比确定的主动锥齿轮的计算转矩 T ze =622.23N·m
(2) 按驱动轮打滑转矩T cs 确定的主动锥齿轮的计算转矩 T zs =1143.46N·m
(3) 按汽车日常行驶平均转矩T cf 确定的主动锥齿轮的计算转矩 T zf =190.57 N·m
3.3主减速器锥齿轮的主要参数选择 3.3.1 主、从动锥齿轮齿数Z 1和Z 2的确定
选择主、从动锥齿轮齿数时应考虑如下因素: ① 为了磨合均匀,Z 1、Z 2之间应避免有公约数。
② 为了的到理想的齿面重合度和高的轮齿弯曲强度,主、从动齿轮齿数 应不少于40 。
③ 为了啮合平稳、噪声小和具有高的疲劳强度,对于乘用车,Z 1一般不少于9;对于商用车,Z 1一般不少于6。
④ 主传动比i 。较大时,Z 1尽量取的少些,以便得到满意的离地间隙。 ⑤ 对于不同的主传动比,Z 1、Z 2之间应避免有公约数。
为了啮合平稳、噪声小和具有高的疲劳强度,大小齿轮的齿数和不少于40在轿车主减速器中,小齿轮齿数不小于9,主减速器的传动比为4.55,初定主动齿轮齿数Z 1=9,从动齿轮齿数Z 2=41。 重新计算传动比i 0
56.41
2
0==Z Z i (3-5)
3.3.2 从动锥齿轮大端分度圆直径D 2和端面模数m s
对于单级主减速器,增大尺寸
D 2会影响驱动桥壳的离地间隙,减小又会
影响跨置式主动轮的前支承座的安装空间和差速器的安装
D 2由经验公式初选
mm 33.2093c 2D 2==T K D (3-6)
D 2——从动锥齿轮的大端分度圆半径; K D2——直径系数,取15(一般为13.0~15.3); T c ——计算转矩, T c =T c =min[T ce ,T cs ]=2717.78N·m ;
m s 的选择:
11.52
2
==
Z D m s (3-7)
88.43c m s ==T K m (3-8)
式中:
K m ——模数系数,K m =0.35(取0.3~0.4);
T c ——计算转矩,T c =T c =min[T ce ,T cs ]=2717.78N·m 。
m s 取整5
3.3.3主、从动锥齿轮齿面宽b 1和b 2的计算
锥齿轮齿面过宽并不能增大的强度和寿命,反而会导致因锥齿轮轮齿小端齿沟变窄引起的切削刀头顶面过窄及刀尖圆角过小,这样不但会减小了齿根圆角半径,加大了集中应力,还降低了刀具的使用寿命。此外,安装时有位置偏差或由于制造、热处理变形等原因使齿轮工作时载荷集中于轮齿小端,会引起轮齿小端过早损坏和疲劳损伤。另外,齿面过宽也会引起装配空间减小。但齿面过窄,轮齿表面的耐磨性换入轮齿的强度会降低,汽车主减速器螺旋锥齿轮与双曲面齿轮的从动齿轮齿面宽b 2
b 2=0.155·D 2=31.78mm (3-9) 一般习惯使锥齿轮的小齿轮齿面宽比齿轮稍大,使其在大齿轮齿面两端都超出一些,通常小齿轮的齿面加大10%较为合适,在此取b 1=1.1b 2=34.96mm
3.3.4 中点螺旋角β的选择
双曲面齿轮副的中点螺旋角是不相等的,选β时应考虑它对齿面重和度εF ,
轮齿强度和轴向力的大小的影响,β越大,则εF 也越大,同时啮合的齿越多,传动越平稳,噪声越低,而且轮齿的强度越高,εF 应不小于1.25,在1.5~2.0之间时效果最好,但β过大,会导致轴向力增大
汽车主减速器双曲面齿轮副的平均螺旋角为??40~35,而乘用车选用较大
的β,应保证较大的εF ,使运转平稳,噪声低
“格里森”制推荐用下式来近似地预选主动齿轮螺旋角的名义值
?=?+?+?=67.4490525'2
121d E
Z Z β (3-10) 式中:
β1'——主动齿轮(名义)中心螺旋角的预选值; Z 1,Z 2——主、从动齿轮齿数; d 2——从动轮的节圆直径; E ——双曲面齿轮的偏移距。
预选β1'后,需用刀号来加以校正,首先要求近似刀号
近似刀号=
'sin 20
2
f 1f βθθ+
'34.1962723.305717.0arctan 05717.02
)(tan tan 2f 1f 2
1*a*2f 1f 1f 2f 22=?====++===
=θθθθZ Z m m
c h R h R h
选择标准刀号14
48.45)20arcsin(
'2
f 1f 1=+?=θθβ标准刀号
(3-11)
对于双曲面齿轮传动,当确定了主动齿轮的螺旋角之后,可用下式近似地确定从动轮的名义螺旋角
?=-=-=98.35506901.9483518.4512εββ
式中:
ε——双曲面齿轮传动偏移角。
)
22(si 12b d E
n +=
ε (3-12)
式中:
E ——双曲面齿轮的偏移距; d 2 ——双曲面从动齿轮的节圆直径; b 2——双曲面从动齿轮的齿面宽。
?=+=
73.402
2
1βββ (3-13)
3.3.5 双曲面齿轮副偏移距E
E 值过大将使齿面纵向滑动过大,从而引起齿面早期磨损和擦伤,E 值过过小则不能发挥双曲面齿轮传动的特点。E =0.1D 2=20.5mm 。 3.3.6 双曲面齿轮的偏移方向
双曲面齿轮的偏移可分为上偏移和下偏移两种。由从动齿轮的锥顶向其齿面看去,并使主动齿轮处于右侧,如果主动齿轮在从动齿轮中心线的上方,则为上偏移;在从动齿轮中心线下方,则为下偏移。如果主动齿轮处于左侧,则情况相反。
3.3.7螺旋方向的确定
从锥齿轮锥顶看,齿形从中心线上平部向左倾斜为左旋,向右倾斜为右旋。主从动锥齿轮的螺旋方向是相反的。螺旋方向与锥齿轮的旋转方向影响其所受的轴向力的方向,当变速器挂前进挡时,应使主动锥齿轮的轴向力离开锥顶方向,这样可以使主、从动齿轮有分离的趋势,防止轮齿因卡死而损坏。所以主动锥齿轮选择为左旋,从锥顶看为向左倾斜,这样从动锥齿轮为右旋,从锥顶看向右倾斜,驱动汽车前进。
3.3.8 法向压力角α
加大压力角可以提高齿轮的强度,减少齿轮不产生根切的最小齿数。但对于尺寸小的齿轮,大压力角易使齿顶的变尖及刀尖宽度过小,并使齿轮的端面重叠系数下降。对于双曲面齿轮,从动齿轮轮齿两侧的压力角是相同的,但主动齿轮轮齿两侧的压力角是不等的。选取平均压力角时,乘用车为19°或者20°,本次设计取α=19°。
4 主减速器双曲面锥齿轮强度计算
4.1 单位齿长圆周力的计算
按发动机最大转矩计算
m N 893][m N 39.15610232
1f g emax d ?==?=
P b nD i ki T k P η
(4-1)
m N 30.11261023m
m 22r '22?=?=η?i b D r m G P 算
按驱动轮打滑的转矩计 (4-2)
4.2轮齿的弯曲强度计算
汽车主减速器锥齿轮的齿根弯曲应力为
3
w
s v m s 0c w 102?=bDJ m k k k k T σ (4-3)
式中:
T c ——所计算的齿轮计算转矩; K 0——过载系数,K 0=1;
K s ——载荷分配系数,K s =0.6661; K m ——尺寸系数,K m =1.1; K v ——质量系数,K v =1.0; m s ——齿轮端面模数; D 2——从动锥齿轮齿面宽;
J w1——主动齿轮弯曲应力综合系数,J w1=0.23; J w2——从动齿轮弯曲应力综合系数,J w2=0.26。 4.2.1 主动锥齿轮强度校核
(1) 以发动机最大转矩和传动系最低档速比所确定的主动锥齿轮的转矩T ze 为计算扭矩来计算校核
221w N/mm 700N/mm 00.504<=σ
(2) 以汽车日常行驶平均转矩所确定的主动锥齿轮转矩T zf 为计算扭转来校核
222w N/mm 210N/mm 36.154<=σ
4.2.2 从动锥齿轮强度校核
(1) 以发动机最大扭矩和传动系最低档速比所确定的从动锥齿轮的转矩T ce 为计算扭矩来计算校核
221w N/mm 700N/mm 21.469'<=σ
(2) 以汽车日常行驶平均转矩所确定的从动锥齿轮转矩T cf 为计算扭矩来校核 222w N/mm 210N/mm 33.135'<=σ
4.3轮齿的表面接触强度计算
锥齿轮的齿面接触应力为
2j
v 3
f m 0z 1
p
j N/mm 102bJ K K K K T D C ?=σ (4-4)
式中:
T z ——主动齿轮的计算转矩;
C p ——材料的弹性系数,对于钢制齿轮副取232.6N 0.5/mm ; K 0,K v ,K m ,K s ——与4-3相同;
K f ——表面质量系数,对于制造精确的齿轮取1.0; J j ——计算接触应力的综合系数,J j =0.175。
以发动机最大扭矩和传动系最低档速比所确定的主动锥齿轮的转矩T ze 为计算来校核
Mpa 2800][Mpa 49.1995102j j j
v 3
f s m 0c 1p f =<=?=σσbJ k k k k k T D C
以汽车日常行驶平均转矩所确定的主动锥齿轮转矩T zf 为计算转矩来校核
Mpa 1750][Mpa 33.1104102j j
v 3
f s m 0c 1
p
je =<=?=
∑σbJ k k k k k T D C
主、从动轮的齿面接触应力是相同的。
4.4主减速器锥齿轮的材料选择