一模一腔点浇口顶板顶出开水瓶盖模具设计
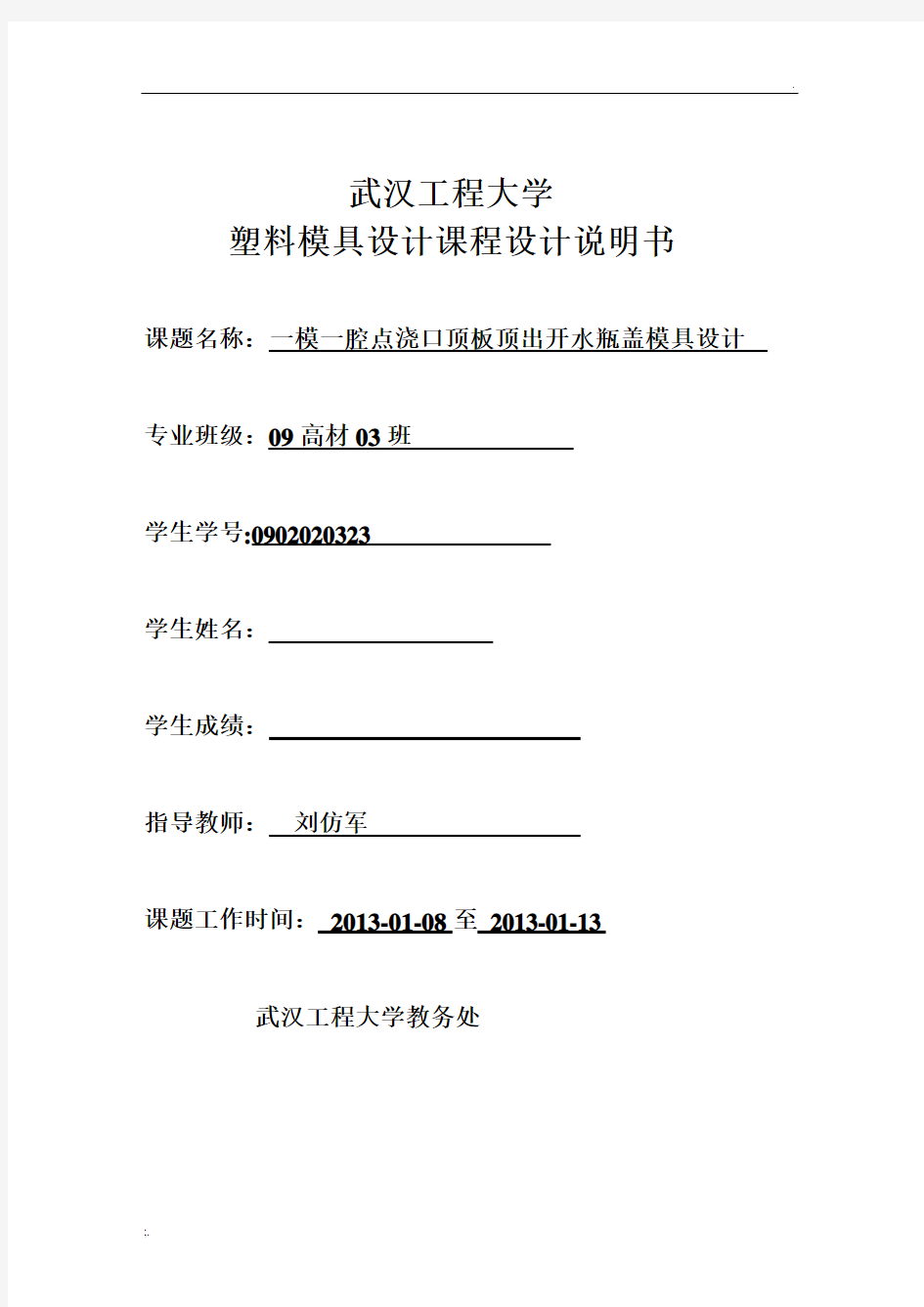

武汉工程大学
塑料模具设计课程设计说明书
课题名称:一模一腔点浇口顶板顶出开水瓶盖模具设计专业班级:09高材03班
学生学号:0902020323
学生姓名:
学生成绩:
指导教师:刘仿军
课题工作时间:2013-01-08至2013-01-13
武汉工程大学教务处
课程设计任务书
一、设计题目
小组同学(每组人数不超过4人)自己选定熟悉的塑料制品作为模具课程设计题目(控制题目难度在两周内完成)
二、课题条件
1、利用图书馆资料,进行必要的文献调研;
2、利用现有模具教具、生活现场取得的制品进行设计;
3、可提供计算机进行模具设计绘图、说明书编写等工作。
三、设计任务
1、根据选定的塑料件,确定制品的原材料品种,及制品的尺寸精度要
求。
2、小组讨论确定完成制品模具设计的程序,可以参照附件一。
3、小组讨论确定该制品模具的基本结构组成及时间进度安排。
4、电脑或手工绘制模具装配图,要求模具结构合理,功能完备。
(1)如果两视图不能表达清楚的,需附加三视图、局部剖视图等;
(2)模具装配图上应标注所有零件的件号、名称;
(3)模具装配图上应有明细表,内容:件号、数量、材料、热处理状态、硬度、规格、备注等内容。
5、绘制非标准零件图,尺寸标注完全合理(包括配合尺寸)
6、撰写设计说明书,应书写本设计过程中设计结果及参数选用等内容。
四、设计说明书内容
1、制品使用要求及原材料的工艺性和成型性能;
2、模腔数目确定,分型面的选择,成型零部件设计,合模导向机构,
浇注系统类型的确定及脱模方式的设计,温度调节系统的布排;
3、校核注射模与注射机规格的适应性;
4、标注参考资料。
目录
1.9 初步确定模腔数、浇注系统类型(主流道、分流道、浇口形式).. 错误!未定义书签。
1.10 制品分型面的确定................................................................................. 错误!未定义书签。
1.12 顶出机构的设计..................................................................................... 错误!未定义书签。
1.14 完成非标准零件图的绘制................................................................... 错误!未定义书签。摘要.. (6)
第一章塑料注射模具的设计步骤和结构组成 (7)
1.1塑料注射模具组成和应用 (7)
第二章开水瓶盖塑件 (8)
2.1塑件的结构和特点 (8)
2.2制品原材料的选择 (8)
2.3注射成型工艺条件 (11)
2.4塑件的主要参数 (12)
2.4.1设计的质量和体积 (12)
2.4.2塑件的投影面积 (12)
第三章注射机的选用 (12)
3.1选用注射机的方法和原则 (12)
3.1.1选用的方法和原则 (12)
3.1.2注射机的选用 (13)
3.1.3最大注射量的校核: (14)
第四章塑料注射模具设计 (15)
4.1型腔数目和分布 (15)
4.1.1确定型腔数目时要考虑的因素 (15)
4.1.2数目的确定 (16)
4.2分型面的选择 (16)
4.3型腔和型芯 (17)
4.3.1型腔和型芯的结构 (17)
4.3.2型腔和型芯的尺寸 (17)
第五章浇注系统设计 (19)
5.1浇注系统 (19)
5.2浇注系统的设计原则 (20)
5.3浇注系统的设计 (20)
第六章推出机构 (23)
6.1推出机构的作用和种类 (23)
6.2开水瓶盖推出机构的组成 (23)
6.3开水瓶盖推出机构的设计 (24)
第七章导向机构 (27)
7.1导向机构的作用和组成 (27)
7.2导向机构的设计 (28)
第八章模架的选用 (30)
8.1标准模架型号 (30)
8.2模架的长度和宽度 (31)
8.3模具标准零部件的设计 (33)
第九章模具的工作过程 (34)
第十章设计小结 (34)
参考文献 (35)
摘要
本次设计的是开水瓶盖, 主要介绍了开水瓶盖的设计思路、加工过程和开水瓶盖的注射模的设计。这种聚丙烯开水瓶盖无毒、无味,密度小,强度、刚度、硬度、耐热性都较好,是人们日常生活中常用的生活用品。
本次设计采用的是注射成型。在设计过程中,首先对进行原材料分析,比较不同塑料的物理和化学性质从而选定开水瓶盖的最佳原料为聚丙烯。然后介绍了不同形式的浇口的优缺点,接下来初步选定注射机和标准模架,再进一步设计模具各个结构,最后对注射机进行校核。
关键词:注塑成型注射机模具
第一章塑料注射模具的设计步骤和结构组成
1.1塑料注射模具组成和应用
塑料模具的种类很多,比较常见的有注射模、压缩模、压注模和挤出模。本文采用注射模。
注射模是安装在注射机上,完成注射成型工艺所使用的模具。注射模的种类很多,其结构与塑料的品种、塑件的结构和注射机的种类等很多因素有关.一般情况是由成形部件、浇注系统、导向机构、调温系统和支撑零部件组成,如果有侧向的孔或凸台,注射模还包括侧向分型和抽芯机构。
塑料注射模具一般由成形部件、浇注系统、导向机构、推出机构、调温系统、排气系统、支撑零部件、侧向分型和抽芯机构组成。
成形部件是指动、定模部分有关组成型腔的零件。
浇注系统是将熔融的塑料从注射机喷嘴进入模具型腔所经的通道,它包括主流道、分流道、浇口及冷料穴。
导向部分在注射模中,用导向部分对模具的定动模导向,以使模具和模时能准确对合。
推出机构是指分型后将塑件从模具中推出的装置。
调温系统是为了满足注射工艺对模具温度的要求,需要有条文系统对模具的温度进行调整。一般热塑性塑料的注射模主要是设计模具的冷却系统。
排气系统是为了将成形时的塑件本身挥发的气体排出模外,常常在分型面上开设排气槽。对于小塑件的模具,可直接利用分型面或推杆等与模具的间隙排气。支撑零部件是用来安装固定或支撑成形零部件及前述的各部分机构的零部件。
侧向分型与抽芯机构是当有些塑件有侧向的凹凸形状的孔或凸台时,须先把侧向的凹凸形状的瓣合模或侧向的型芯从塑件上脱开或抽出。
第二章开水瓶盖塑件
2.1塑件的结构和特点
本次模具设计的制品是一个开水瓶盖,开水瓶盖在生活中较常见,它结构简单,轻便易拿。
2.2制品原材料的选择
1. 聚苯乙烯PS
性能:电绝缘(尤其高频绝缘性)性优良,无色透明,透光率仅次于有机玻璃,着色性、耐水性、化学稳定性良好,力学强度一般,刚性好,但性脆,易产生应力碎裂,不耐笨、汽油等有机溶剂。
用途:适于制作绝缘透件、透明件、装饰件日用品、泡沫包装材料及建筑隔热材料等。
2. 聚乙烯PE
性能:耐腐蚀性、电绝缘(尤其高频绝缘性)性优良,可以氯化、辐照改性,可用玻璃纤维增强。
高密度聚乙烯(HDPE)熔点、刚性、硬度和强度较高、耐应力开裂性好,吸水性小,有突出的绝缘性能和良好的耐辐照性。
低密度聚乙烯(LDPE)柔软性、伸长率、冲击强度和透明性较好。
线性低密度聚乙烯(LLDPE)的性能介于LDPE和HDPE之间。
茂金属聚乙烯(mPE)主要用于薄膜,薄膜强度、柔软性、热封性和透明性极好。
超高分子量聚乙烯(UHMWPE)冲击强度高,耐疲劳,耐磨,用冷压烧结成型。
用途:高密度聚乙烯适于制作管材、中空瓶、注射制品、重包装膜、编织袋、撕裂膜、大包带、周转箱及丝类等。
低密度聚乙烯用于制作地膜、大棚膜、保鲜膜、电缆及注射件等。
线性低密度聚乙烯主要用于薄膜、注射制品、编织袋、打包带等。
超高分子量聚乙烯适于制作减磨、耐磨及传动零件。
3. 聚氯乙烯PVC
(1)硬聚氯乙烯(HPVC)
性能:力学强度高,硬度大,绝缘性优良,耐酸碱力极强,化学稳定性好,阻燃性好,印刷及焊接性好,但软化点低。
用途:适于制造型材、管材、棒材、板材、片材、丝类、中空瓶、焊条及注射制品(管件和阀门等),代替木材和金属材料。
(2)软聚氯乙烯(SPVC)
性能:制品柔软,断裂伸长率大,力学强度大、耐腐蚀性、电绝缘性均低于硬聚氯乙烯,且易老化。
用途:适于制作大棚薄膜、盐膜、日用膜、电线电缆绝缘层、革类、鞋类、软管、软片及密封材料等。
4. 聚丙烯PP
性能:性对密度小,强度、刚性、耐热性均优于低压聚乙烯,可在100℃左右使用。具有优良的耐腐蚀性,耐疲劳性好,良好的高频绝缘性,不受湿度影响,但低温变脆,不耐磨,易光老化。用玻璃纤维增强后,强度接近工程塑料。聚丙烯的共聚物(PP-C)可改善其冲击性能,其中无轨共聚物(PP-R)主要用于管材,嵌段共聚物(PP-B)主要用于大型容器、周转箱等。
用途:PP适于制作注射制品、汽车配件、壳体、日用品、打包带、编织袋、双向拉伸膜(烟膜、黏胶带基膜等)、电容器膜、上水管材、地热管、片材(吸塑成保证盒、一次性水杯等)及中空瓶等。
经查阅[2],由张维合主编《注塑模具设计使用教程》书中表1-1以及表1-4可知PP的计算收缩率及其他性能如表1-1。
表1-1 PP的计算收缩率及其他性能
综上所述:根据以上制品性能,综合参考,特别是聚丙烯具有很好的耐热性,正是开水瓶盖需要的性能,所以选择PP作为开水瓶盖的原材料。
2.3注射成型工艺条件
干燥处理:如果储存适当则不需要干燥处理。
熔化温度:220~275℃,注意不要超过275℃。
模具温度:40~80℃,建议使用50℃。结晶程度主要由模具温度决定。注射压力:1500-1800bar。
注射速度:通常,使用高速注塑可以使内部压力减小到最小。如果制品表面出现了缺陷,那么应使用较高温度下的低速注塑。
流道和浇口:对于冷流道,典型的流道直径范围是4~7mm。建议使用通体为圆形的注入口和流道。所有类型的浇口都可以使用。典型的浇口直径范围是1~1.5mm,但也可以使用小到0.7mm的浇口。对于边缘浇口,最小的浇口深度应为壁厚的一半;最小的浇口宽度应至少为壁厚的两倍。PP材料完全可以使用热流道系统。
成型时间:注射时间 20s~60s
高压时间 0s~3s
冷却时间 20s~90s
总周期 50s~160s
2.4塑件的主要参数 2.4.1设计的质量和体积
此次设计的开水瓶盖的半径50mm ,碗壁厚2mm ,高50mm 。估算其体积和质量(聚丙烯密度取0.905 g/cm 3) 塑件体积:
2223333.14(5048)48 3.1425045.241045.24V mm cm =?-?+??=?=
塑件质量:
0.90545.2440.94M V g ρ==?=
2.4.2塑件的投影面积
塑件成形的最大正面投影面积:S=πR2=78.50 cm 2
第三章 注射机的选用
3.1选用注射机的方法和原则 3.1.1选用的方法和原则 1.使用现有设备
2.根据每次成型件数安排最大注射量、锁模力、经济性等要求选择合适的注射机。
3.1.2注射机的选用
选PP为材料,注射压力取80MPa。根据塑件的大小和实际中常用的注射机,选用XS—ZY—125/90型螺杆式注射机,并采用一模一腔点浇口。
①XS—ZY—125型螺杆式注射机的主要参数:
额定注射量/cm3 125
注射重量/g 114
螺杆直径/mm Φ42
注射压力/MPa 116
注射行程/mm 115
注射速率/(g/s) 72
塑化能力/(kg.h-1) 35
锁模力/kN 900
注射方式螺杆式
最大开模行程/mm 300
模具最大厚度/mm 300
模具最小厚度/mm 200
合模方式肘杆
顶出行程/mm 180
结构形式卧式
拉杆间距/mm 260×290
定位圈直径/ mm Φ100
电动机功率/kW 15
喷嘴球半径/mm Φ10
喷嘴孔直径/mm Φ4
最大注射成型面积/cm3 320
②注射机的顶出方式:机械式顶板顶出
3.1.3最大注射量的校核:
1、注射压力的校核
2、锁模力的校核
3、最大成形面积的校核
当上述四个校核都满足要求时,才能确定注射机选用的合适。
注射机的参数校核
1、最大注射量的校核
注射机的额定注射量为125cm3
塑件体积:3.14×(5×5-4.8×4.8)×4.8+5×5×3.14×2=45.24cm3 (取整46cm3) ,每次成型1个塑件。
假设浇道凝料为30cm3。
实际注射量=46+30=76cm3<125×80%=100cm3。
最大注射量满足要求。
2、注射压力的校核
PP塑料的注射成型时的压力为70~140MPa,取80MPa;
SX —ZY —125注射机的注射压力为116MPa 。P P 注成型 注射机的注射压力满足要求。 3、锁模力的校核
注射机的锁模压力为1800KN ;
锁模力为模具型腔内塑料熔体平均压力(MPa )一般为注射压力的0.3~0.65倍。PP 塑料成型时的注射压力取80MPa ,我们选择塑料熔体平均压力(MPa )P=0.5×80=40MPa
塑料成型时型腔压力40MPa,塑件在分型面上的投影面积为78.50cm 2 锁模力=78.50×40=314KN<900KN 锁模力满足要求。
4、最大注射成型面积的校核
SX —ZY —125注射机的最大注射成型面积为320cm 2; 塑件在分型面上的投影面积为78.50cm 2; 注射时模具的成型面积=78.5cm 2<320cm 2 最大注射成型面积满足要求。
第四章 塑料注射模具设计
4.1型腔数目和分布
4.1.1确定型腔数目时要考虑的因素
1 按注射机的最大注射量确定型腔数量
n ≤(0.8V g -V j [3] )/V z =(0.8×125-30)/46=1.52----------
V g (mg)—注射机最大注射量(cm3或g),取125cm3
V j (mj)—浇注系统凝料量(cm3或g),假设浇道凝料为30cm3
V z (mz)—单个制品的容积或质量(cm3或g),单个塑件为 46cm3。
2 按注射机的额定合模力确定型腔数。
n≤(F-P m Aj[3])/P m A z=(900×103-40×106×8×10-4)/(40×106×78.5×10-4)=2.76--------
F—注射机的额定合模力,查手册为900KN,
P m—塑料熔体对型腔的平均压力(MPa),取40MPa;
A j—浇注系统在分型面上的投影面积(mm2),取8cm2;
A z—单个制品在分型面上的投影面积(mm2).由计算得78.5cm2。
偏差标注。
4.1.2数目的确定
根据开水瓶盖的尺寸选用一模一腔。
4.2分型面的选择
塑件的分型面设计原则为:
1、分型面应选择在塑件外形的最大轮廓处;
2、分型面的选取应有利于塑件的留模方式,便于塑件顺利脱模;
3、保证塑件的精度要求;
4、便于模具制造;
5、减小成型面积;
6、增强排气效果。
综合考虑诸多因素,本设计中塑件的分型面选用单分型面,模具中有定模(或上模)、动模(或下模)以及推件板,为了使制品及流道内的物料可以取出来,因此需要两个分型面,故称双分型面注射模。
定模:安装在注射机定模安装板上的部分,图中的蓝色部分;
动模:安装在注射机动模移动板上的部分,图中的其余部分;
分型面:模具上用以取出塑件和(或)浇注系统凝料的可分离的接触表面。如图所示。
4.3型腔和型芯
4.3.1型腔和型芯的结构
确定型腔和型芯的结构形式
型腔、型芯可分别有整体式和组合式两种。由于塑件结构简单,型腔加工容易,所以选用整体式型腔和整体式型芯。在定模板上直接加工型腔。
4.3.2型腔和型芯的尺寸
计算成型零部件工作尺寸要考虑要素如下:
a塑件的收缩率波动;
b模具成形零件的误差;
c模具成形零件的磨损;
d模具安装配合的误差;
e塑件的总误差;
f考虑塑件尺寸和精度的原则。
综合以上的原则,本设计成形的零部件的具体计算如下:
1、型腔的内形尺寸
D M =[D+DS-△/2-δZ /2]+δZ 0 (mm)————--(1)
D M =[100+100×1.2%-1.2/2-0.3/2]δZ 0
=100.451.20
式中:D M —型腔内形尺寸(mm);
D—制品外形的基本或最大尺寸(mm);100mm △—制品公差或偏差(mm);取1.2mm
δZ—成型零件的制造公差或偏差(mm);
δZ =(1/5~1/3)△,取0.3mm
S—PP塑料的平均收缩率(%),取1.2%
2、型芯的外形尺寸
d m =[d+dS+△/2+δZ /2]0-δ(mm)————--(2)
d m =[96+96×1.2%+1.5/2+0.5/2]0-1.5
=98.150-1.5
式中:d m —型芯的外形尺寸(mm);
d —制品内形的基本尺寸或最小极限尺寸(mm);取96mm
3、型腔的深度尺寸
H M =[H+HS-△/2-δZ /2]]+δZ 0 (mm)————--(3)
H M =[50+50×1.2%-1.2/2-0. 4/2]+1.2 0
=49.801.20
式中:H M —型腔深度尺寸(mm);
H —制品高度的基本尺寸或最大极限尺寸(mm);取50mm
4、型芯的高度尺寸
h m =[h+hS+△/2+δZ /2]0-δ(mm)————--(4)
h m =[48+48×1.2%+1.0/2+0.25/2]0-1
=49.200-1
式中:h m—型芯高度尺寸(mm);
h —制品型孔深度的基本尺寸或最小极限尺寸(mm);取48mm 第五章浇注系统设计
5.1浇注系统
浇注系统:塑料熔体从注塑机喷嘴出来后,到达模腔之前在模具中流经的通道。
组成:主流道、分流道、浇口、冷料穴。
作用:将熔体平稳地引入型腔,使之充满型腔内各个角落,在熔体填充和凝固过程中,能充分地将压力传递到行腔的各个部位,获
得组织致密、外形清晰、尺寸稳定的塑件。
5.2浇注系统的设计原则:
1.确保塑料充满整个型腔
2.保证塑料熔体流动平稳
3.应尽量减短流程
4.流道表壁的粗糙度要低
5.防止制品变形和翘曲
6.防止型芯变形和嵌件位移
7.去除浇口应尽量方便,且不影响制品质量
8.合理设计冷却穴
5.3浇注系统的设计
(1)主流道设计
主流道是一端与注射机喷嘴相接触,可看作是喷嘴的通道在模具中的延续,另一端与分流道相连的一段带有锥度的流动通道。
根据《简明塑料模具实用手册》查得XS-ZY-250型注射机喷嘴的有关尺寸为:
喷嘴前端孔直径为Φ4mm;
喷嘴前端球面半径为10mm;