超高强度螺栓断裂失效分析
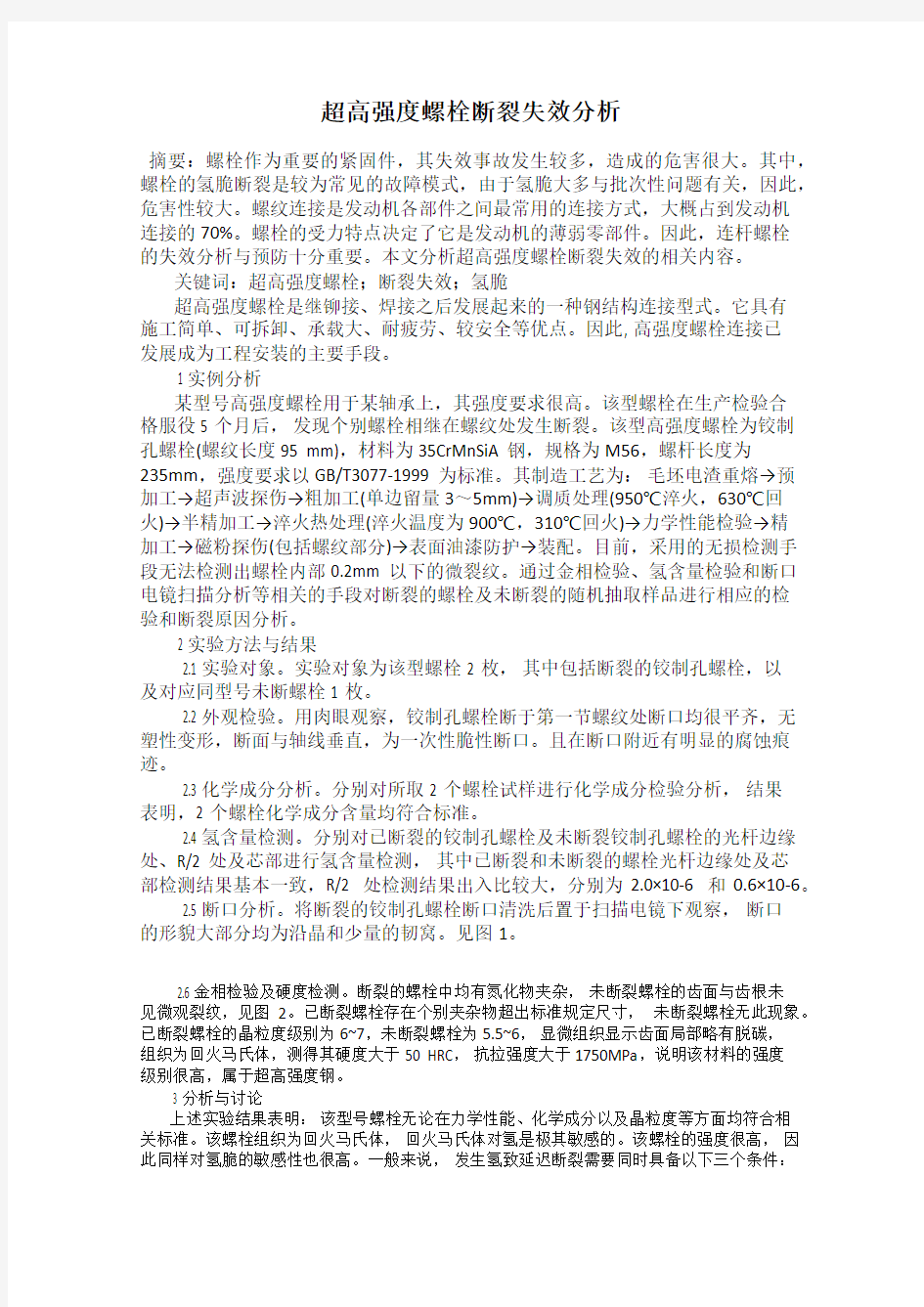

超高强度螺栓断裂失效分析
摘要:螺栓作为重要的紧固件,其失效事故发生较多,造成的危害很大。其中,螺栓的氢脆断裂是较为常见的故障模式,由于氢脆大多与批次性问题有关,因此,危害性较大。螺纹连接是发动机各部件之间最常用的连接方式,大概占到发动机
连接的70%。螺栓的受力特点决定了它是发动机的薄弱零部件。因此,连杆螺栓
的失效分析与预防十分重要。本文分析超高强度螺栓断裂失效的相关内容。
关键词:超高强度螺栓;断裂失效;氢脆
超高强度螺栓是继铆接、焊接之后发展起来的一种钢结构连接型式。它具有
施工简单、可拆卸、承载大、耐疲劳、较安全等优点。因此, 高强度螺栓连接已
发展成为工程安装的主要手段。
1 实例分析
某型号高强度螺栓用于某轴承上,其强度要求很高。该型螺栓在生产检验合
格服役5 个月后,发现个别螺栓相继在螺纹处发生断裂。该型高强度螺栓为铰制
孔螺栓(螺纹长度95 mm),材料为35CrMnSiA 钢,规格为M56,螺杆长度为
235mm,强度要求以GB/T3077-1999 为标准。其制造工艺为:毛坯电渣重熔→预
加工→超声波探伤→粗加工(单边留量3~5mm)→调质处理(950℃淬火,630℃回火)→半精加工→淬火热处理(淬火温度为900℃,310℃回火)→力学性能检验→精
加工→磁粉探伤(包括螺纹部分)→表面油漆防护→装配。目前,采用的无损检测手段无法检测出螺栓内部0.2mm 以下的微裂纹。通过金相检验、氢含量检验和断口电镜扫描分析等相关的手段对断裂的螺栓及未断裂的随机抽取样品进行相应的检
验和断裂原因分析。
2 实验方法与结果
2.1 实验对象。实验对象为该型螺栓2 枚,其中包括断裂的铰制孔螺栓,以
及对应同型号未断螺栓1 枚。
2.2 外观检验。用肉眼观察,铰制孔螺栓断于第一节螺纹处断口均很平齐,无
塑性变形,断面与轴线垂直,为一次性脆性断口。且在断口附近有明显的腐蚀痕迹。
2.3 化学成分分析。分别对所取2 个螺栓试样进行化学成分检验分析,结果
表明,2 个螺栓化学成分含量均符合标准。
2.4 氢含量检测。分别对已断裂的铰制孔螺栓及未断裂铰制孔螺栓的光杆边缘处、R/2 处及芯部进行氢含量检测,其中已断裂和未断裂的螺栓光杆边缘处及芯
部检测结果基本一致,R/2 处检测结果出入比较大,分别为2.0×10-6 和0.6×10-6。
2.5 断口分析。将断裂的铰制孔螺栓断口清洗后置于扫描电镜下观察,断口
的形貌大部分均为沿晶和少量的韧窝。见图1。
2.6 金相检验及硬度检测。断裂的螺栓中均有氮化物夹杂,未断裂螺栓的齿面与齿根未
见微观裂纹,见图2。已断裂螺栓存在个别夹杂物超出标准规定尺寸,未断裂螺栓无此现象。已断裂螺栓的晶粒度级别为6~7,未断裂螺栓为5.5~6,显微组织显示齿面局部略有脱碳,
组织为回火马氏体,测得其硬度大于50 HRC,抗拉强度大于1750MPa,说明该材料的强度
级别很高,属于超高强度钢。
3 分析与讨论
上述实验结果表明:该型号螺栓无论在力学性能、化学成分以及晶粒度等方面均符合相
关标准。该螺栓组织为回火马氏体,回火马氏体对氢是极其敏感的。该螺栓的强度很高,因
此同样对氢脆的敏感性也很高。一般来说,发生氢致延迟断裂需要同时具备以下三个条件:
金属--断裂与失效分析报告 刘尚慈
金属断裂与失效分析(尚慈编) 第一章概述 失效:机械装备或机械零件丧失其规定功能的现象。 失效类型:表面损伤、断裂、变形、材质变化失效等。 第二章金属断裂失效分析的基本思路 §2—1 断裂失效分析的基本程序 一、现场调查 二、残骸分析 三、实验研究 (一)零件结构、制作工艺及受力状况的分析 (二)无损检测 (三)材质分析,包括成分、性能和微观组织结构分析 (四)断口分析 (五)断裂力学分析 以线弹性理学为基础,分析裂纹前沿附近的受力状态,以应力强度因子K作为应力场的主要参量。 K I=Yσ(πα)1/2 脆性断裂时,裂纹不发生失稳扩展的条件:K I<K IC 对一定尺寸裂纹,其失稳的“临界应力”为:σc=K IC / Y(πα)1/2 应力不变,裂纹失稳的“临界裂纹尺寸”为:αc=(K IC / Yσ)2/π 中低强度材料,当断裂前发生大围屈服时,按弹塑性断裂力学提出的裂纹顶端开位移[COD(δ)]作为材料的断裂韧性参量,当工作应力小于屈服极限时: δ=(8σsα/πE)ln sec(πσ/2σs) 不发生断裂的条件为:δ<δC(临界开位移) J积分判据:对一定材料在大围屈服的情况下,裂纹尖端应力应变场强度由形变功差率J来描述。开型裂纹不断裂的判据为:
J<J IC K IC——断裂韧性;K ISCC——应力腐蚀门槛值 (六)模拟试验 四、综合分析 分析报告的涵:①失效零部件的描述;②失效零部件的服役条件;③失效前的使用记录;④零部件的制造及处理工艺;⑤零件的力学分析;⑥材料质量的评价;⑦失效的主要原因及其影响因素;⑧预防措施及改进建议等。 五、回访与促进建议的贯彻 §2—2 实效分析的基本思路 一、强度分析思路 二、断裂失效的统计分析 三、断裂失效分析的故障树技术 第三章金属的裂纹 §3—1 裂纹的形态与分类 裂纹:两侧凹凸不平,偶合自然。裂纹经变形后,局部磨钝是偶合特征不明显;在氧化或腐蚀环境下,裂缝的两侧耦合特征也可能降低。 发纹:钢中的夹杂物或带状偏析等在锻压或轧制过程中,沿锻轧方向延伸所形成的细小纹缕。发纹的两侧没有耦合特征,两侧及尾端常有较多夹杂物。 裂纹一般是以钢中的缺陷(发纹、划痕、折叠等)为源发展起来的。 一、按宏观形态分为: (1)网状裂纹(龟裂纹),属于表面裂纹。产生的原因,主要是材料表面的化学成分、金相组织、力学性能、应力状态等与中心不一致;或者在加工过程中发生过热与过烧,晶界性能降低等,导致裂纹沿晶界扩展。如: ①铸件表面裂纹:在1250~1450℃形成的裂纹,沿晶界延伸,
超高强度螺栓断裂失效分析
超高强度螺栓断裂失效分析 摘要:螺栓作为重要的紧固件,其失效事故发生较多,造成的危害很大。其中,螺栓的氢脆断裂是较为常见的故障模式,由于氢脆大多与批次性问题有关,因此,危害性较大。螺纹连接是发动机各部件之间最常用的连接方式,大概占到发动机 连接的70%。螺栓的受力特点决定了它是发动机的薄弱零部件。因此,连杆螺栓 的失效分析与预防十分重要。本文分析超高强度螺栓断裂失效的相关内容。 关键词:超高强度螺栓;断裂失效;氢脆 超高强度螺栓是继铆接、焊接之后发展起来的一种钢结构连接型式。它具有 施工简单、可拆卸、承载大、耐疲劳、较安全等优点。因此, 高强度螺栓连接已 发展成为工程安装的主要手段。 1 实例分析 某型号高强度螺栓用于某轴承上,其强度要求很高。该型螺栓在生产检验合 格服役5 个月后,发现个别螺栓相继在螺纹处发生断裂。该型高强度螺栓为铰制 孔螺栓(螺纹长度95 mm),材料为35CrMnSiA 钢,规格为M56,螺杆长度为 235mm,强度要求以GB/T3077-1999 为标准。其制造工艺为:毛坯电渣重熔→预 加工→超声波探伤→粗加工(单边留量3~5mm)→调质处理(950℃淬火,630℃回火)→半精加工→淬火热处理(淬火温度为900℃,310℃回火)→力学性能检验→精 加工→磁粉探伤(包括螺纹部分)→表面油漆防护→装配。目前,采用的无损检测手段无法检测出螺栓内部0.2mm 以下的微裂纹。通过金相检验、氢含量检验和断口电镜扫描分析等相关的手段对断裂的螺栓及未断裂的随机抽取样品进行相应的检 验和断裂原因分析。 2 实验方法与结果 2.1 实验对象。实验对象为该型螺栓2 枚,其中包括断裂的铰制孔螺栓,以 及对应同型号未断螺栓1 枚。 2.2 外观检验。用肉眼观察,铰制孔螺栓断于第一节螺纹处断口均很平齐,无 塑性变形,断面与轴线垂直,为一次性脆性断口。且在断口附近有明显的腐蚀痕迹。 2.3 化学成分分析。分别对所取2 个螺栓试样进行化学成分检验分析,结果 表明,2 个螺栓化学成分含量均符合标准。 2.4 氢含量检测。分别对已断裂的铰制孔螺栓及未断裂铰制孔螺栓的光杆边缘处、R/2 处及芯部进行氢含量检测,其中已断裂和未断裂的螺栓光杆边缘处及芯 部检测结果基本一致,R/2 处检测结果出入比较大,分别为2.0×10-6 和0.6×10-6。 2.5 断口分析。将断裂的铰制孔螺栓断口清洗后置于扫描电镜下观察,断口 的形貌大部分均为沿晶和少量的韧窝。见图1。 2.6 金相检验及硬度检测。断裂的螺栓中均有氮化物夹杂,未断裂螺栓的齿面与齿根未 见微观裂纹,见图2。已断裂螺栓存在个别夹杂物超出标准规定尺寸,未断裂螺栓无此现象。已断裂螺栓的晶粒度级别为6~7,未断裂螺栓为5.5~6,显微组织显示齿面局部略有脱碳, 组织为回火马氏体,测得其硬度大于50 HRC,抗拉强度大于1750MPa,说明该材料的强度 级别很高,属于超高强度钢。 3 分析与讨论 上述实验结果表明:该型号螺栓无论在力学性能、化学成分以及晶粒度等方面均符合相 关标准。该螺栓组织为回火马氏体,回火马氏体对氢是极其敏感的。该螺栓的强度很高,因 此同样对氢脆的敏感性也很高。一般来说,发生氢致延迟断裂需要同时具备以下三个条件:
案例一螺栓失效分析
案例一螺栓断裂失效分析 某螺栓生产厂家生产的螺栓在用户使用过程中发生断裂,为分析螺栓断裂原因,进行了化学成分测试、金相组织观察、螺栓断口观察、能谱测试以及硬度测试等,并对螺栓断裂做出了结论。 1、化学成分分析 螺栓成分分析采用成分分析仪,正常断裂、异常断裂螺栓成分见表1,从表中可以看出正常断裂螺栓与异常断裂螺栓成分都符合GB/T3077-1999《合金结构钢》中对45Mn2钢的要求。 表1 材料化学成分分析结果(质量分数,%) C Si Mn P S Cr Ni Fe 正常断裂螺栓0.421 0.250 1.498 0.011 0.001 0.078 0.021 余量 异常断裂螺栓0.425 0.269 1.534 0.011 <0.001 0.068 0.019 余量标准值0.42~0.49 0.17~0.37 1.4~1.8 2、金相组织分析 取平行于断裂截面的试样,打磨、抛光并观察其组织形貌。下图1(a)、1(b)所示为正常断裂螺栓与异常断裂螺栓的金相组织形貌,从图中可以看出螺栓金相组织均为回火马氏体。 (a)正常断裂螺栓;(b)异常断裂螺栓 图1 螺栓金相组织形貌 3、宏观断口形貌分析 正常断裂螺栓、异常断裂螺栓宏观断口形貌如图2(a)、2(b)所示。由图可知
两个螺栓均从中心起裂,裂纹向四周扩展。正常断裂螺栓与异常断裂螺栓断裂截面都具有裂纹源、扩展区、瞬断区三个部分,正常断裂螺栓扩展区面积比异常断裂螺栓大,瞬断区面积则比异常断裂螺栓小。这与异常断裂螺栓应力(165KN )比正常断裂螺栓断裂应力(215KN)小相吻合。同时正常断裂螺栓断裂截面较为平整,异常断裂螺栓在裂纹源附近呈凹陷状。 (a)正常断裂螺栓; (b)异常断裂螺栓 图2 螺栓断裂截面 4、 微观断口形貌分析 图3所示为正常断裂螺栓与异常断裂螺栓断裂截面裂纹源附近的微观形貌,从图中可以看出正常断裂螺栓组织较为平整,而异常断裂螺栓中心附近可见含有夹杂物的微孔。图4所示为夹杂物所在位置,图5为夹杂物能谱分析图,表2为其对应的元素分析表,从表中可以看出夹杂物中主要元素为O 、Si ,并存在少量的Mg 、Al 、Ca 元素,其中O 元素的含量很大,故较杂物主要为SiO 2,存在少量的MgO 、Al 2O 3、CaO 。 裂纹源 扩展区 裂纹源 扩展区 瞬断区 瞬断区 a) b)
弹簧失效的原因分析
弹簧失效的原因分析 弹簧失效的原因分析 一、佛山弹簧分解弹簧永久变形及其影响因素 弹簧的永久变形是弹簧失效的主要原因之一 弹簧的永久变形,会使弹簧的变形或负荷超出公差范围,而影响机器设备的正常工作。 检查弹簧永久变形的方法 1.快速高温强压处理检查弹簧永久变形:是把弹簧压缩到一定高度或全部并紧,然后放在开水中或温箱保持10~60分钟,再拿出来卸载,检查其自由高度和给定工作高度下的工作载荷。 2.长时间的室温强压处理检查弹簧永久变形:是在室温下,将弹簧压缩或压并若干天,然后卸载,检查其自由高度和给定工作高度下的工作载荷。 二、弹簧断裂及其影响因素 弹簧的断裂破坏也是弹簧的主要失效形式之一 弹簧断裂形式可分为;疲劳断裂,环境破坏(氢脆或应力腐蚀断裂)及过载断裂。 弹簧的疲劳断裂: 弹簧的疲劳断裂原因:属于设计错误,材料缺陷,制造不当及工作环境恶劣等因素。 疲劳裂纹往往起源于弹簧的高应力区,如拉伸弹簧的钩环、压缩弹簧的内表面、压缩弹簧(两端面加工的压缩弹簧)的两端面。 受力状态对疲劳寿命的影响 (a)恒定载荷状态下工作的弹簧比恒定位移条件下工作的弹簧,其疲劳寿命短得多。 (b)受单向载荷的弹簧比受双向载荷的弹簧的疲劳寿命要长得多。 (c)载荷振幅较大的弹簧比载荷振幅较少的弹簧的疲劳寿命要短得多。 腐蚀疲劳和摩擦疲劳 腐蚀疲劳:在腐蚀条件下,弹簧材料的疲劳强度显著降低,弹簧的疲劳寿命也大大缩短。 摩擦疲劳:由于摩擦磨损产生细微的裂纹而导致破坏的现象叫摩擦疲劳。 弹簧过载断裂 弹簧的外加载荷超过弹簧危险截面所有承受的极限应力时,弹簧将发生断裂,这种断裂称为过载断裂。 过载断裂的形式 (a)强裂弯曲引起的断裂; (b)冲击载荷引起的断裂; (c)偏心载荷引起的断裂 佛山弹簧后处理的缺陷原因及防止措施 缺陷一:脱碳 对弹簧性能影响:疲劳寿命低 缺陷产生原因:1、空气炉加热淬火未保护气2、盐浴脱氧不彻底 防止措施:1、空气炉加热淬火应通保护气或滴有机溶液保护:盐浴炉加热时,盐浴应脱氧,杂质BAO质量分数小于0.2%。2、加强对原材料表面质量检查 缺陷二:淬火后硬度不足
高强度螺栓断裂失效分析
高强度螺栓断裂失效分析 韩志良 (常州机电职业技术学院机械系,常州213012) 马红卫,丁燕君 (常柴股份有限公司理化室,常州213002) 摘要:针对装配现场发生的几起高强度螺栓断裂失效事故,采用金相分析、化学成分分析和力学性能测试等方法进行检测。分析结果认为螺栓失效的原因有:(1)螺纹成形时产生裂纹,螺栓因之而脆断;(2)杆部与头部交接处表面脱碳、使局部强度降低而断裂;(3)装配时扭矩过大,螺栓明显缩颈而断裂;(4)原材料中心存在裂纹。 关键词:螺栓;裂纹;扭转;脱碳 高强度螺栓是发动机紧固件中最重要的零件之一,如连杆螺栓、缸盖螺栓、主轴承盖螺栓,要求强度等级为10.9级,有的甚至达12.9级。但在实际使用中,高强度螺栓(简称螺栓)断裂失效也时有发生。笔者就发生在装配过程中的四起高强度螺栓断裂失效逐一进行分析。 1 195连杆螺栓断裂失效分析 195连杆螺栓装配时断裂于螺纹处。从断口上看,断口平直,无缩颈,几乎没有裂纹萌生区,全部为最后瞬断区。零件供应商进行了失效分析,认为装配时连杆螺纹内夹入异物,阻碍了螺纹的拧紧,导致装配扭矩过大而断裂。 1.1 断口分析 由于断口表现出极大的脆性,如果是基于扭紧力矩过大而断裂,断口应表现出良好的塑性,因为拧紧时螺栓主要受扭转应力,而扭转试验的应力状态的柔性系数较大(大于拉伸试验),材料易于塑性变形,而失效的螺栓并未表现出塑性。另外,断裂源也不在齿根部,而是有所偏离。 1.2 化学成分和显微组织分析 螺栓材料牌号为40Cr钢,强度等级10.9级,硬度要求32~38HRC,金相组织要求1~3级(JB/T8837-2000)。经检验,螺栓化学成分(质量分数)符合GB/T3077-1988之规定,见表1。显微组织为细的回火索氏体,按JB/T8837-2000评定为1级,其硬度值为34HRC和35HRC,硬度和显微组织均符合技术条件规定。经磁粉探伤未发现磁痕。 将螺栓从杆部与头部交接处纵向剖开,经金相制样、观察,结果在大部分螺纹的根部均有裂纹,即在断口附近和远离断口的螺纹处均存在裂纹,裂纹位置偏离“真正的”齿根部,裂纹的两侧无贫碳和脱碳,说明裂纹的形成与调质处理无关,见图1和图2。由于裂纹细小且位于螺纹根部,常规磁粉探伤未发现磁痕。
HT200试棒脆性断裂失效分析
HT200试棒脆性断裂失效分析 过程装备与控制工程2013-2刘凯(22)李阔(16) 摘要:在机电装备的各类失效分析中以断裂失效最主要,危害最大,往往造成严重的后果及巨大的经济损失。试棒脆性断裂失效分析从断口的宏观外观、微观组织、受力状态等方面综合分析,解释断裂失效的原因。 关键字:HT200试棒脆性断裂失效分析 断裂是金属构件在应力作用下材料分离为互不相连的两个或两个以上部分的现象,是金属构件常见的失效形式之一,特别是脆性断裂,它是危害性甚大的失效形式。脆性断裂前构件的变形量很小,没有明显可以觉察出来的宏观变形量。断裂过程中材料吸收的能量很小,一般是在低于允许应力条件下的低能断裂。通过对HT200拉力试棒断裂失效分析包括力学性能、化学成分、金相组织、其他相关性能;断口分析、表面分析,包括金相组织、电镜分析各种分析;失效现象及原因分析等综合学习掌握关于脆性断裂的相关知识 一、试样收集与观察 HHT200拉力试棒 图示拉力试棒为液压万能试验机拉断后的试棒,其原始尺寸如下图。 HT200拉力试棒尺寸图 试棒装在液压万能试验机后,开动试验机缓慢加载。在拉伸过程中,没有肉眼可见的颈缩、屈服现象,,随着“砰”一声,试棒被拉断。拉断前的应变很小,伸长率也很小,十分典型的脆性断裂过程。 二、化学成分 脆性断裂实验所用拉力试棒为HT200材料,具体含义为灰口铸铁抗拉强度为200MPa,硬度范围为163~255HB,抗拉强度和塑性低,但铸造性能和减震性能好,主要用来铸造汽车发动机汽缸、汽缸套、车床床身等承受压力及振动部件。其具体化学成分如下表。
试验过程中观察不到拉力试棒明显的应变过程及颈缩现象,在较小的拉应力作用下就被拉断了,没有屈服和颈缩现象,拉断前的应变很小,伸长率也很小。其拉伸时的应力-应变关系是一段微弯的曲线,没有明显的直线部分,也没有明显的屈服阶段。 铸铁在拉断时的最大应力即为其强度极限。因为没有屈服现象,强度极限σ b是衡量强度的唯一指标。σ b =Fb Ao 。 灰口铸铁σ-ε图 四、断裂试棒断口宏观形貌及其微观金相组织观察 脆性断裂是从金属构件内部原本存在的微小裂纹为裂纹源而开始的。因此,脆性断裂往往是突然发生的,断裂前基本没有肉眼可见的变形量。脆性断裂一般沿低指数晶面穿晶解理,解理是金属在正应力作用下沿解理面发生的一种低能断裂。由于解理是通过破坏原子间的键合来实现的,而密排面之间的原子间隙最大,键合力最弱,故绝大多数解理面是原子密排面。但也有一些脆性材料断裂是沿晶断裂,如晶界上有脆性物或有晶间腐蚀是,就有可能产生沿晶断裂。该拉力试棒为沿解理面断裂,故其断口的宏观形貌具有两个明显特征。一、其断口表面是明亮结晶状的,表面存在小刻面。一个多晶体金属材料的解理断口,由于其每个晶体的取向不同,所以其解理面与断裂面所取的位向也就不同,若把断口放在手中旋转时,将闪闪发亮,像存在许多分镜面。二、存在“山形”条纹。脆性材料在断裂时会从断裂源点形成“山形”裂纹。随着裂纹的发展,条纹会变粗,因此,根据断口“山形”裂纹的图形可以判断脆性断裂的裂纹扩展方向和寻找断裂起源点。综上并观察试棒断口分析可知HT200拉力试棒为典型的脆性断裂。 脆性解理断裂的电子显微断口形态的一个特征是呈现河流花样。由于金属是多晶体,取向又是无序的,解理在某一晶粒内进行时以及穿过一个晶粒向相邻晶粒传播时,均会造成解理裂缝在不同的结晶面上断开,这些解理裂缝相交处即会形成台阶。在电子显微镜中这些解理台阶呈现出形似地球上的河流状形貌,故名河流状花样。沿着解理断裂的方向河流可以合并为“主流”。解理穿越晶界时,不仅河流花样的“流向”要发生变化,而且有可能加粗或部分消失由于实际晶体内部存在许多缺陷(位错、析出物、夹杂物等),所以在一个晶粒内的解理并不
螺栓断裂原因分析
螺栓断裂原因分析 螺栓的抗拉强度比想象中强得多,以一只M20×80的8.8级高强螺栓为例,它的重量只有0.2公斤,而它的最小拉力载荷是20吨,高达它自身重量的十万倍,一般情况下,我们只会用它紧固几十公斤的部件,只使用它最大能力的千分之一。即便是设备中其它力的作用,也不可能突破部件重量的千倍,因此螺栓的抗拉强度是足够的,不可能因为螺栓的强度不够而损坏。 很多螺栓断裂的最终分析认为是超过螺栓的疲劳强度而损坏,但是螺栓在横向振松实验中只需一百次即可松动,而在疲劳强度实验中需反复振动一百万次才会损坏。换句话说,螺栓在使用其疲劳强度的万分之一时即松动了,我们只使用了螺栓能力的万分之一,所以说螺栓的损坏也不是因为螺栓疲劳强度。 静态紧固用螺栓很少会自行松动,也很少出现断裂情况。但是在冲击,振动,变载荷情况下使用的螺栓就会出现松动和断裂的情况。 所以我认为螺栓损坏的真正原因是松动。螺栓松动后,螺纹和连接件之间产生微小间隙,冲击和振动会产生巨大的动能mv^2,这种巨大的动能直接作用于螺栓,受轴向力作用的螺栓可能会被拉断。受径向力作用的螺栓可能会被剪断。 因此设计时,对于关键的运动部位的连接紧固要注意防松设计。 自锁螺母尼龙锁紧螺母以上为两种形式的锁紧螺母。 对于弹簧垫片的放松效果,一直存在争议。 弹簧垫圈的放松原理是在把弹簧垫圈压平后,弹簧垫圈会产生一个持续的弹力,使螺母和螺栓连接副持续保持一个摩擦力,产生阻力矩,从而防止螺母松动。同时弹簧垫圈开口处的尖角分别嵌入螺栓和被连接件的表面,从而防止螺栓相对于被连接件回转。
以M16螺栓连接为例,实验显示用约10N.m的螺栓预紧力矩就可以将16弹簧垫圈完全压平。弹簧垫圈只能提供10N.m的弹力,而10N.m的弹力对于280N.m的螺栓预紧力矩来说可以忽略,其次,这么小的力,不足以使弹簧垫圈切口处的尖角嵌入螺栓和被连接件表面。折卸后观察,螺栓和被连接件表面都没有明显的嵌痕。所以,弹簧垫圈对螺栓的防松作用可以忽略。另外,在螺栓与被连接件之间增加一个垫圈,如果垫圈质量有问题,相当于给螺栓连接又增加了一个安全隐患。
断裂分析报告
M10-45H 内六角紧定螺钉 断裂分析 据客户反映,由本公司供应的M10-45H 紧定螺钉,安装过程中发生故障。 现状:M10-45H 内六角紧定螺钉,在密封锁紧螺母安装过程中发生断裂; 安装过程:在部件上指定部位使用43~48N.m 扭矩旋入紧定螺钉(作为限位螺钉使用),然后,在紧定螺钉露出端使用43~48N.m 的终拧扭矩旋入密封锁紧螺母并拧紧,防止螺钉与基体之间的间隙造成介质渗漏。 一,失效件检测分析: 1,断口形貌宏观观察: 断面基本与轴线垂直,颜色灰色,颗粒细小均匀;放大10倍进行观测,未见目测可见原始裂纹。 2,机械性能检测: 3,金相检测分析: 沿轴线使用线切割方式制样,检测了纵向剖面的金相组织。如下图图1和图2。 图1 芯部金相x500 芯部金相组织:回火马氏体+回火屈氏体 图2 螺纹金相x200 螺纹部位金相:无脱碳层或渗碳层 4,化学成分分析: 合金钢SCM435: 0.35%C, 0.21%Si, 0.70%Mn, 0.013%P, 0.007%S, 1.04%Cr, 0.185%Mo 符合GB3098.3对45H 级螺钉的材质要求。 失效件检测分析表明,该产品机械性能和使用材料完全符合GB3098.3标准要求 二,断裂原因分析: 对失效件的机械性能检测、金相组织检测、化学成分检测结果表明,产品完全符合标准规范。 对照标准GB/T 3098.3-2000,在标准条文内第一章,标准范围,对该产品的描述,第一段有明确:本标 准 规 定了由碳钢或合金钢制造的、在环境温度为10-35℃条件下进行试验时,螺纹公称直径为1.6- 24m m 的紧定螺钉及类似的不受拉应力的紧固件机械性能。如下截图:
失效分析
失效分析 第三章失效分析的基本方法 1.按照失效件制造的全过程及使用条件的分析方法:(1)审查设计(2)材料分析(3)加工制 造缺陷分析(4)使用及维护情况分析 2.系统工程的分析思路方法:(1)失效系统工程分析法的类型(2)故障树分析法(3)模糊故 障树分析及应用 3.失效分析的程序:调查失效时间的现场;收集背景材料,深入研究分析,综合归纳所有信息 并提出初步结论;重现性试验或证明试验,确定失效原因并提出建议措施;最后写出分析报告等内容。 4.失效分析的步骤:(1)现场调查①保护现场②查明事故发生的时间、地点及失效过程③收集 残骸碎片,标出相对位置,保护好断口④选取进一步分析的试样,并注明位置及取样方法⑤询问目击者及相关有关人员,了解有关情况⑥写出现场调查报告(2)收集背景材料①设备的自然情况,包括设备名称,出厂及使用日期,设计参数及功能要求等②设备的运行记录,要特别注意载荷及其波动,温度变化,腐蚀介质等③设备的维修历史情况④设备的失效历史情况⑤设计图样及说明书、装配程序说明书、使用维护说明书等⑥材料选择及其依据⑦设备主要零部件的生产流程⑧设备服役前的经历,包括装配、包装、运输、储存、安装和调试等阶段⑨质量检验报告及有关的规范和标准。(3)技术参量复验①材料的化学成分②材料的金相组织和硬度及其分布③常规力学性能④主要零部件的几何参量及装配间隙(4)深入分析研究(5)综合分析归纳,推理判断提出初步结论(6)重现性试验或证明试验 5.断口的处理:①在干燥大气中断裂的新鲜断口,应立即放到干燥器内或真空室内保存,以防 止锈蚀,并应注意防止手指污染断口及损伤断口表面;对于在现场一时不能取样的零件尤其是断口,应采取有效的保护,防止零件或断口的二次污染或锈蚀,尽可能地将断裂件移到安全的地方,必要时可采取油脂封涂的办法保护断口。②对于断后被油污染的断口,要进行仔细清洗。③在潮湿大气中锈蚀的断口,可先用稀盐酸水溶液去除锈蚀氧化物,然后用清水冲洗,再用无水酒精冲洗并吹干。④在腐蚀环境中断裂的断口,在断口表面通常覆盖一层腐蚀产物,这层腐蚀产物对分析致断原因往往是非常重要的,因而不能轻易地将其去掉。 6.断口分析的具体任务:①确定断裂的宏观性质,是延性断裂还是脆性断裂或疲劳断裂等。② 确定断口的宏观形貌,是纤维状断口还是结晶状断口,有无放射线花样及有无剪切唇等。③查找裂纹源区的位置及数量,裂纹源的所在位置是在表面、次表面还是在内部,裂纹源是单个还是多个,在存在多个裂纹源区的情况下,它们产生的先后顺序是怎样的等。④确定断口的形成过程,裂纹是从何处产生的,裂纹向何处扩展,扩展的速度如何等。⑤确定断裂的微观机理,是解理型、准解理型还是微孔型,是沿晶型还是穿晶型等。⑥确定断口表面产物的性质,断口上有无腐蚀产物,何种产物,该产物是否参与了断裂过程等。 7.断口的宏观分析(1)最初断裂件的宏观判断①整机残骸的失效分析;②多个同类零件损坏的 失效分析;③同一个零件上相同部位的多处发生破断时的分析。(2)主断面(主裂纹)的宏观判断①利用碎片拼凑法确定主断面;②按照“T”形汇合法确定主断面或主裂纹;③按照裂纹
钢锭_坯_在轧制过程中出现翘皮及断裂等常见缺陷的原因分析和防止途径
甘肃冶金 2001年3月 第1期钢锭(坯)在轧制过程中出现翘皮及断裂等常见缺陷的原因分析和防止途径 贾 静 (兰州钢铁公司 甘肃省 兰州市 730020) 摘 要 分析了钢锭(坯)轧制过程中出现翘皮、裂纹、断裂等常见缺陷的原因,并且提出了解决问题的途径。 关键词 分析解决 缺陷 途径 1 前言 钢锭(坯)在轧制过程中会出现翘皮、裂缝、断裂等多种缺陷而致废。由于种种原因,90年代初以来,特别是近几年里,钢锭(坯)轧裂和翘皮的数量骤然上升并有居高不下之势。为此,我们将近几年来发生的钢锭(坯)轧废情况统计分析结果列于表1(数据以每年退换钢锭的数量为依据)。 表1 钢锭(坯)轧裂退换统计表 年 份钢 种废品数量致 废 原 因小 时(t) 1995 1996 1997 1998 1999Q195—Q235沸钢258钢锭重接19.08t,翘皮、断裂Q235镇静钢— Q195—Q235沸钢118翘皮、断裂 150220M nSi连铸坯70夹杂、断裂 20M nSi钢47断裂 Q195—Q235沸钢44翘皮、断裂 150220M nSi连铸坯80夹杂、断裂 1502Q235连铸坯40脱方 Q235镇静钢100纵裂纹、发纹 Q195—Q235沸钢220翘皮、断裂 Q235镇静钢110裂纹、断裂 Q195—Q235沸钢20断裂、裂口 Q235镇静钢240纵裂纹、裂口、断裂 258 235 264 330 260 9 收稿日期:2000-12-28
表1的统计结果表明: 早期镇静钢锭质量比沸腾钢锭的好,但近两年来质量有下滑趋势。 钢锭(坯)在轧制过程中退废的主要缺陷是翘皮、裂纹和断裂。平均每年退换钢锭293t ,由此造成的经济损失30余万元。 根据金属学和钢的热塑性变形原理,结合现场生产的实际情况,作者对这些缺陷的成因从炼钢工艺和轧钢工艺两方面进行分析。2 炼钢工艺对钢锭质量的影响2.1 化学成分的影响 对于碳素结构钢来讲,就元素影响而言造成轧制过程中出现裂纹、断裂极为有关的元素有S 、M n 、P 、Cu 。2.1.1 元素S 、M n 的影响及S 的“ 热脆”缺陷对大量轧裂钢锭化学成分的分析结果表明,元素S 的超标准上限及元素Mn 的低标准下限是钢锭轧裂的重要原因。 高硫钢锭经轧制后通身四面都有严重裂缝,有时只经过粗轧几道就断成碎块。其致废的机理是:S 是生铁或燃料中天然存在的杂质,由于S 在固态Fe 中的溶解度很小,几乎不能溶解。它在钢中以FeS 的形式存在,而FeS 和Fe 易形成熔点较低(仅有985℃)的共晶体,当钢在1100~1200℃进行热加工时,分布于晶界的低熔点共晶体固熔化而导致开裂,这就是通常所说的S 的“热脆”现象。在冶炼中为了清除S 的有害作用,必须增加钢中的含M n 量,使Mn 与S 优先形成高熔点的M nS,其熔点高达1620℃而且呈粒状分布于晶粒中,从而可以有效地防止或避免S 在钢中的“热脆”现象。2.1.2 元素P 的影响及P 的“冷脆”缺陷 通常,元素P 超标的钢锭在热轧过程中不出现裂纹或断裂,但成品坯(材)冷却至室温就会发生“冷脆”现象,在远远小于钢材力学指标力的作用下就发生脆断。 其机理是:室温下钢中的P 可全部溶于钢的铁素体中,使钢的强度、硬度增加,塑性、韧性显著降低。这种钢坯(材)的“冷脆”现象在我厂的生产中偶有发生。2.1.3 元素Cu 的影响及富Cu 轧制的网状裂纹 1997年10月,我厂轧制的Q 235镇静钢68方坯有两批总重量101.36t 成品钢坯表面出现了严重的裂纹,其症状如图1所示,可见钢坯通身有网状裂纹。经取样做成分分析发现Cu 含量在0.6%~0.8%,严重超标。 图1 富铜轧制的网状裂纹 元素Cu 超标造成钢锭热轧开裂的原因是:由于西域废钢资源的特点,含Cu 量有时较高。当钢中含Cu 量超过0.4%且它在加热炉中的氧化性气氛中较长时间加热时,由于选择性氧化的结果,在钢的表面氧化铁皮下会富集一薄层熔点低于1100℃的富Cu 合金,这层合金在约1100℃时熔化并浸蚀钢的表层,使钢在热加工时开裂并多形成网状裂纹。 因此,在技术标准中对碳素结构钢中残余铜元素的含量有明确规定,应该不高于0.3%。2.2 炼钢脱氧操作及浇注工艺的影响 我厂轧制钢锭从脱氧方式上分沸腾钢和镇静钢。由于钢液脱氧方式及结晶热力学的条件10
高强螺栓脆性断裂研究及实例分析
高强螺栓脆性断裂研究及实例分析 摘要:本文简要回顾了高强螺栓的发展历程,介绍了当前高强螺栓研究的现状及动态,总结了钢材脆性断裂理论、脆性断裂的影响因素及高强螺栓的断裂分析。 关键词:高强螺栓;脆性断裂; Research on Brittle Fracture of High Strength Bolt and Analysis by Example Abstract:The article briefly reviewed the development course of high strength bolt, introduced the current status and trends of high strength bolt, and summarized the theory of brittle fracture and influenced factors and the fracture Analysis of strength bolt. Keywords: high strength bolt;brittle fracture; 0 引言 我国从1957年起开始研究高强度螺栓及其连接,并首先运用于桥梁。这为我国钢结构采用高强螺栓连接奠定了基础。在以后修建成昆铁路时推广了此项新技术,使高强螺栓连接技术得到了提高和发展。在材料使用方面,我国高强度螺栓制作从开始时使用45号钢和40硼钢材料逐步转变到使用具有更好力学性能和工艺性能的20MnTiB钢。高强度螺栓的应用范围也逐渐广泛,从原来的桥梁结构扩展到各种钢结构、机械结构设备,甚至宇宙飞船、海洋钻井平台的使用。大量各种连接形式的静力试验和疲劳试验,为高强度螺栓连接合理设计提供了可靠的参数。 1高强螺栓的研究现状 1.1国外现状:美国伊利偌斯大学的Rajasekhaaran S.Hair等对单螺栓连接和T字型双螺栓连接进行了试验和理论分析,得出了高强度螺栓的撬力作用会大大降低T字型双螺栓连接的极限承载力和疲劳强度的结论。荷兰的Stark J WB和Bijlaard FSK对由高强度螺栓构成的钢框架节点的弯矩一曲率关系进行了研究。意大利学者Giro Faena等对T字型螺栓连接进行了试验分析。并总结了影响高强度螺栓预拉力的主要因素。另外,美国的Yang Jun和DewoIf John.T则对高强度螺栓预拉力的松弛现象进行了探索。
螺纹紧固件失效分析案例(第1部分)
螺纹紧固件失效分析案例 全国紧固件标准化技术委员会 机械工业通用零部件产品质量监督检测中心 二〇〇八年6月
序 机械产品失效是一门关于研究机械产品质量的综合性技术学科,主要研究失效的规律与机理。机械零件的失效是在特定的工作条件下,当其所具备的失效抗力指标不能满足工作条件的要求时发生的。导致零件失效的本质原因可能是材料本身的失效抗力不足,也可能是零件存在与设计或制造等过程有关的缺陷。产品的早期失效往往是产品质量低劣或质量管理不善及科学技术水平不高的直接反映。失效发生后能否尽快作出正确的判断,确定失效原因,制定防止失效的措施,则是衡量有关科技人员技术水平的重要标志。加入WTO后,我国的产品将参与国际市场的竞争,于是提高产品质量成为提高竞争力的关键因素。失效分析则是定量评定产品质量的重要基础,也是保证产品可靠性的重要手段。 机械科学研究总院、机械工业通用零部件产品质量监督检测中心在进行大量失效分析的基础上(包括对断裂、腐蚀和磨损的深入研究,特别是断口、裂纹和痕迹分析),分析了可能出现失效的形式和类型,以供大家在生产中借鉴,在生产工艺中加以避免出现失效的可能;同时,在今后的质量纠纷中维护自己的正当权益。 机械工业通用零部件产品质量监督检测中心熊学端研究员从事了几十年失 效分析研究工作,有很深的理论造诣,积累了丰富的失效分析经验,本文中列举了部分螺纹紧固件失效分析案例,希望能够为生产企业及用户提供良好的参考和借鉴;同时,中心愿为生产企业和用户在今后的失效分析中提供技术咨询和指导。 全国紧固件标准化技术委员会
目 录 第一部分 失效分析概述 (1) 1. 失效定义 (1) 2. 失效分析的意义、目的 (1) 3. 失效的来源 (1) 4. 失效分析的思路、方法 (1) 5. 断口分析 (2) 6. 断口分析部分名词术语 (3) 第二部分 失效分析案例 (7) 1. 汽车上臂螺栓断裂原因分析 (7) 2. 溜冰鞋螺钉、螺母断裂原因分析 (12) 3. 紧定螺钉断裂原因分析报告 (20) 4. 连杆螺栓断裂原因分析 (25) 5. 汽车轮毂螺栓断裂原因分析 (29) 6. M8×55高强度螺栓断裂原因分析 (33) 7. 高压开关螺栓断裂原因分析报告 (37) 8. 沟槽刚性接头紧固螺栓断裂原因分析报告 (42) 9. 定位螺钉断裂原因分析 (47) 10. M36×280高强度螺栓断裂原因分析 (53) 11. 高压线塔联结螺栓断裂原因分析 (59) 12. 中压电器用螺栓断裂原因分析报告 (64) 13. 网架螺栓断裂原因分析 (66) 14. 螺钉断裂原因分析 (69) 15. 吊环螺钉断裂失效分析 (73) 16. 螺栓失效原因分析 (79)
高强度螺栓断裂研究分析
高强度螺栓断裂分析
————————————————————————————————作者:————————————————————————————————日期:
高强度螺栓断裂分析 作者:上海交通大学曾振鹏 摘要:采用断口分析、金相检验和硬度 测定等方法,对高强度螺栓断裂原因进行了分析。断口分析结果表明,断口平坦,呈放射状花样,微观形态主要为准解理花样,表明螺栓的断裂是脆性断裂;同时发现,在断口附近还存在横向内裂纹,内裂纹的断口形态与断裂断口一样。金相分析表明,材料棒中存在严重的中心碳偏析,而中心碳偏析是引起断裂的主要原因。 关键词:高强度螺栓;准解理;横向内裂纹;中心碳偏析 某厂生产的一批规格为M30×160mm的高强度大六角头螺栓,在进行验收试验时发生断裂。螺栓材料为35CrMoA,采用常规工艺生产,硬度要求为35~39HRC。 1检验 1.1材料的化学成分 用VD25直读光谱仪进行了材料化学成分分析,分析结果(质量分数)列于表1。从表1可以看出,材料的化学成分符合标准要求。 1.2硬度测定 硬度测定结果列于表2。由表可见,螺栓材料硬度虽符合技术要求,但已接近上限。 1.3材料的显微组织 (1)在抛光态下,可见材料中含有较严重的夹杂物,其形态、分布见图1。对照标准[2],夹杂物级别为3~4级。
图1夹杂物形态及分布状况100× 图2螺栓的显微组织280× (2)显微组织见图2。组织为回火马氏体+粒状贝氏体,并有少量铁素体。从图2可明显看出,组织中存在严重偏析,出现回火马氏体和粒状贝氏体带,致使显微组织不均匀,而且在回火马氏体带中存在MnS夹杂。对样品螺纹根部附近的组织进行了观察,未发现脱碳现象。 1.4断口分析 (1)图3a为断口的宏观形貌,断口较平坦,表面呈灰色,有明显的撕裂脊,呈放射状花样,放射线从中心向四周发射。表明裂纹先在中心形成,然后向外扩展。当裂纹扩展至整个横截面时,螺栓断裂。 图3断口的宏观形貌 (2)断口的微观形态基本上以准解理花样为主,还有一些二次裂纹,如图4所示。
汽车悬置螺栓断裂失效分析
汽车悬置螺栓断裂失效分析 发表时间:2018-05-23T17:22:09.973Z 来源:《基层建设》2018年第6期作者:姚瑶 [导读] 摘要:本文分析了发动机安装支架和发动机支架的疲劳断裂问题。 江淮汽车集团股份有限公司乘用车制造公司安徽合肥 230601 摘要:本文分析了发动机安装支架和发动机支架的疲劳断裂问题。对螺栓的宏观、扫描电镜、化学成分和金相分析进行了分析,并对同一批次螺栓进行了力学性能试验。在各种物理化学试验的基础上,结合显微断裂和断裂机理,分析了螺栓的断裂原因。 关键词:汽车;悬置螺栓;失效分析 1前言 在开发多车发动机支架的过程中,将车辆用于发动机锻造钢悬架。在常规车辆的道路试验中,连接螺栓和螺栓断裂。本文从螺栓、螺柱断裂类型、螺栓连接强度计算和结构设计等方面分析了连接失效分析,并提出了改进建议。 2分析的内容 2.1分析样本 分析样品是一个完整的螺栓失效螺栓和失效螺栓。完整的螺栓是全新未使用的。 2.2分析内容 进行了断裂分析、化学成分分析、硬度测试、金相分析、扫描电镜和能谱测试。对完整的螺栓进行了化学成分分析、硬度测试、拉伸试验和金相分析。 2.2.1宏观断口分析。 断裂的连杆被分成两部分:螺纹部分的断裂部分留在连杆的深孔中,螺栓的另一部分暴露在外。打开螺丝孔后,将断头取出,螺孔内螺纹有外拉的痕迹。通过与相同模型的完全螺栓比较,发现螺栓的断裂位置位于螺纹的第一齿位置,螺纹部分没有明显的塑性变形。由于暴露螺钉的二次损伤,存在明显的多重冲击痕迹,杆体严重变形。虽然断裂具有一定的疲劳特性,但断裂边缘明显受到破坏。因此,暴露的螺杆部分没有断裂分析值。 2.2.2化学成分分析 样品采用螺栓,化学成分符合设计人员的技术要求。 2.2.3光学金相分析。 对失败螺栓基体的金相组织进行分析,组织相对均匀。在螺栓表面附近的组织形态学中未发现明显的脱碳。金相检查未发现异常。 2.2.4硬度分析。 结果表明,断裂螺栓的硬度与设计要求一致。 2.2.5SEM分析 采用扫描电子显微镜观察螺栓孔内的断裂情况,发现裂纹源位于断裂边缘。源区域面积较小,瞬时区域面积约为1/2。通过安装位置对准,线的螺纹有向外拉的位置。源区域的部分增大,疲劳阶段从断裂边缘开始,有许多与裂纹扩展方向垂直的小的疲劳条纹。 在源区没有明显的夹杂物和不均匀的冶金缺陷。随着裂纹扩展,疲劳条纹变得越来越长。在裂缝快速膨胀区,有一个明显的酒窝形状。扫描电镜(sem)在螺纹上观察,发现裂纹与断裂源部分平行。横截面的外表面有许多微裂纹。螺纹表面没有明显的加工缺陷。螺杆断裂为多个断口源,断裂源集中在截面的同一侧,锚杆和瞬态断裂带占整个断裂的比例(近1/2),这是典型的大应力低周疲劳断裂特征。通过对螺纹的观察,发现加工缺陷引起的应力集中,除了疲劳裂纹外,没有发现。因此,扫描电子显微镜(sem)的结果表明,连杆的断裂是在高单向弯曲循环加载作用下形成的。 3基于VDI2230方法的连接计算分析。 机械设计手册主要是指国家标准的螺栓连接计算方法。与VDI2230的计算方法相比,计算方法略粗糙,前考虑不全面。本文采用VD12230方法计算悬吊支架的连接,从表面处理、摩擦系数、结构尺寸、预紧力矩等方面分析了螺栓的连接强度。通过道路光谱采集,获得了悬吊支架的载荷和横向载荷,并得到了悬架的横向载荷。通过实验得到了连接结构的摩擦系数。 表一:摩擦系数 (1)使用VDI2230方法(MDESIGN分析软件)的帮助下,螺栓疲劳应力幅值是80mpa,电泳锻钢悬置支架的抗滑安全系数引擎联接螺栓底部SG=1.5,小于VDI2230SG1.8或更高的设计要求、安全系数;锻钢支架山经过电泳处理(相对结表面之间的摩擦系数是0.18),,通过嵌入预应力损失预紧的损失(VDI2230嵌入式)。因为螺栓利用率是72.3%,可以满足连接的安全系数增加扭矩。然而,螺栓的应力幅值很小,当扭矩接近屈服时,螺栓的应力幅值仍然高达71MPa。 (2)如果连接支撑面不进行电泳(螺栓的摩擦系数为0.23),则螺栓连接防滑的安全系数为SG=1.92,满足连接安全系数的要求;螺栓应力幅值为62MPa,不满足螺栓疲劳应力的要求。 (3)采用电导支架,然后螺栓扭矩增加,使螺栓计算利用率达到95%,螺栓疲劳应力幅值仍高达56mpa,仍然不能解决螺栓疲劳应力幅值过大的问题。结果表明,单纯增加预应力不能解决锚杆的疲劳破坏,表明锚杆应力幅值过大,导致螺栓疲劳断裂。 (4)通过增加基础凸集的3毫米直径,增加的面积的利用率95%结表面和螺栓,螺栓应力幅值明显降低,增加了底座直径的螺栓疲劳失效后问题解决了道路试验。指出零件结构的尺寸设计对螺栓连接的疲劳性能有重要影响,是提高螺栓连接在允许结构下的疲劳性能的一种方法。 (5)当然,在这种连接结构中,在弯矩作用下,3个紧固点分布,在弯矩作用下容易发生接触面积,在螺栓应力打开后会急剧增加,最终导致疲劳失效。如果你考虑在三角形分布中变化的扣分,可以有效地减少弯曲力,在三个螺栓上的载荷分布可以更均匀,防止单个螺栓发生早期疲劳断裂失效。然而,在发动机室空间中,很难进行有足够空间的三角形连接布置。
失效分析习题
填空: 1.常见的断裂分类有: 1)根据断裂时变形量的大小,将断裂失效分为两大类,即脆性断裂和延性断裂。 2)按裂纹走向与金相组织的关系,将断裂失效分为穿晶断裂和沿晶断裂。 3)按断裂机制与形貌将断裂失效分为:1)按断裂机制进行分类,分为微孔型断裂、解理型(准解理型)断裂、沿晶断裂及疲劳型断裂等。2)按断口的宏观形貌分类,分为纤维状、结晶状、细瓷状、贝壳状及木纹状,人字形、杯锥状等。3)按断口的微观形貌分类,分为微孔状、冰糖状、河流花样、台阶、舌状、扇形花样、蛇形花样、龟板状、泥瓦状及辉纹等。4)按加工工艺或产品类别对断裂进行分类:1)按加工下艺分类,有铸件断裂、锻件断裂、磨削裂纹、焊接裂纹及淬火裂纹等。2)按产品类别分类,有轴们断裂齿轮断裂、连接件断裂压力容器断裂和弹簧断裂等。 2.失效分析可分为:事前分析、事中分析和事后分析。 3.腐蚀产物的去除方法有化学法、电化学法及干剥法等。 4.解理断裂的微观形貌特征主要是:河流花样及解理台阶,除此之外尚有舌状花样、鱼骨状花样、扇形花样及羽毛花样等以及珠光体解理。 5.典型的疲劳断口的宏观形貌结构可分为疲劳核心、疲劳源区、疲劳裂纹的发展区、裂纹的快速扩展区及瞬时断裂区等五个区域。 二、判断 1.缩孔:由于金属从液态至固态的凝固期间,产生的收缩得不到充分补缩,使铸件在最后凝固部位形成具有粗糙的或粗晶粒表面的孔洞,一般呈倒锥形。 2.点腐蚀:只有在特定的介质中才能发生点腐蚀。当介质中的氯离子和氧化剂(如溶解氧)同时存在时,容易发生点腐蚀、大部分设备发生的点腐蚀失效都是氯化物和氯离子引起的。 3.晶间腐蚀:某种材料是否发生晶间腐蚀取决于材料/介质体系的特征。在这种体系中,材料的晶界区域比晶粒本体的溶解速度大,所发生的腐蚀即为晶间腐蚀。 只有那些能使不锈钢的晶界呈现活化状态,而晶粒呈现钝化状态的介质环境,才会发生晶间腐蚀。 金属发生晶间腐蚀后,在宏观上几乎看不到任何变化,几何尺寸及表面金属光泽不变,但其强度及延伸率显著降低。 4.在一般情况下,当应力较小、腐蚀介质较弱时,应力腐蚀裂纹多呈沿晶扩展;相反,当应力较大、腐蚀介质较强时,应力腐蚀裂纹通常是穿晶扩展。 5.微孔型断裂的宏观表现:宏观塑性的微孔断裂(提高材料的塑变抗力防止)、宏观脆性的微孔断裂(提高材料的断裂韧度)。 6.冷脆金属低温脆断断口的宏观特征:结晶状,并有明显的镜面反光现象。冷脆金属低温断裂断口的微观形貌具有典型的解理断裂特征:河流花样、台阶、舌状花样、鱼骨花样、羽毛状花样、扇形花样等。 7.准解理断裂:从材料方面考虑,必为淬火加低温回火的马氏体组织,回火温度低,易产生此类断裂。为了防止此类断裂,最有效的办法就是提高钢材的抗低温脆断的能力,即降低钢材的脆性转折温度。 三、名词解释
单趾弹簧扣件PR弹条断裂原因分析论文
单趾弹簧扣件PR弹条断裂原因分析摘要:采用化学分析、金相检验、硬度测定和受力分析方法,对单趾弹簧扣件pr弹条在使用过程中出现的断裂现象进行了分析。认为弹条断裂的原因是安装工艺不规范、导致弹条的工作弹程和应力超过设计状态引起的。 关键词:弹条断裂检验受力分析 abstract: the chemical analysis, metallographic examination, the hardness testing and stress analysis method, the single toe spring fastener pr play in use article appeared in the process of fracture is analyzed. think of the fracture reason is article installation process is not standard, lead to the work of the article cheng and stress caused by more than design state. key words: article the fracture inspection stress analysis 中图分类号:u213.2+1文献标识码:a文章编号: 1 前言 弹条是轨道结构的重要部件,其有效与否直接关系到行车的安全。它主要利用弹性变形时所储存的能量起到缓和机械上的震动和冲击作用,在动荷载下承受长期的、周期性的弯曲、扭转等交变应力。 某单位生产的弹条为单趾弹簧扣件pr弹条,其结构型式如图1