塑料排水管现场质量检验报告单
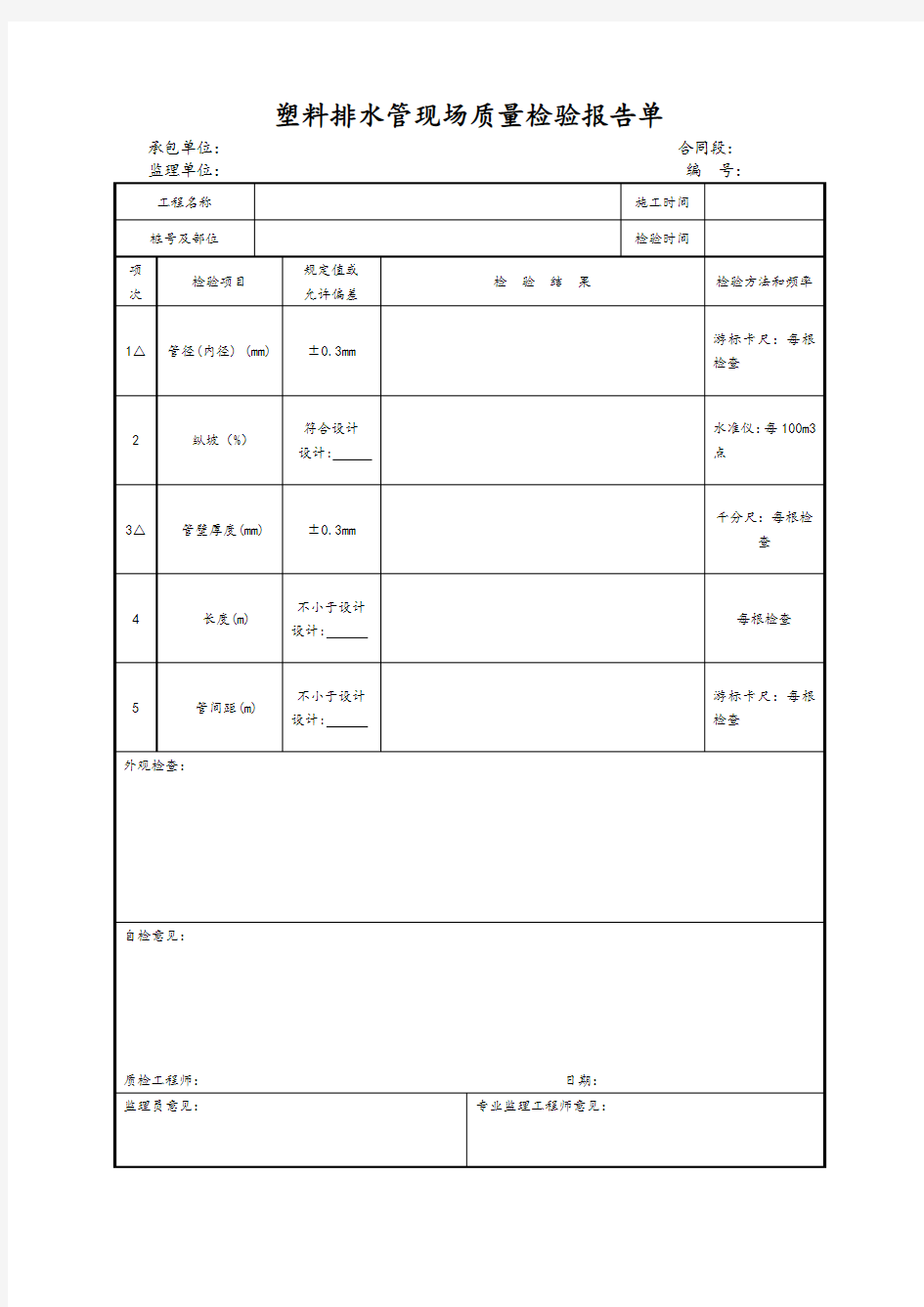

塑料排水管现场质量检验报告单
承包单位:合同段:
承包人技术负责人:日期:
钣金件检验作业指导书
钣金件检验作业指导书 文件编号 编制:刘桂强 审核: 批准: Xxxxxxxxxxxxxxx有限公司 发放范围:车间、生产部、技术部、档案室各一份
一、目的 规范钣金结构件的检验标准,以使各过程的产品质量得以控制,保证本公司的产品质量,从而使我公司的产品让顾客满意。。 二、适用范围 本标准适用于各种钣金结构件的检验,图纸和技术文件并同使用。当有冲突时,以技术规范和客户要求为准。 三、引用标准 本标准的尺寸未注单位皆为mm,未注公差按以下国标IT13级执行 GB/T1800.3-1998 极限与配合标准公差和基本偏差数值表 GB/T1800.4 -1998 极限与配合标准公差等级和孔、轴的极限偏差表 GB/1804-2000 一般公差未注公差的线性和角度尺寸的公差 未注形位公差按GB/T1184 –1996 形状和位置公差未注公差值执行。 四、原材料检验标准 1.金属材料 1.1钣材厚度及质量应符合国标,采用的钣材需出示性能测试报告及厂商明。 1.2材料外观:平整无锈迹,无开裂与变形。 1.3 尺寸:按图纸或技术要求执行,本司未有的按现行国标执行。 2.塑粉
2.1塑粉整批来料一致性良好,有出厂证明与检验报告,包含粉号、色号以及各项检验参数。 2.2试用后符合产品要求(包括颜色、光泽、流平性、附着力等)。3通用五金件、紧固件 3.1外观:表面无绣迹、无毛刺批锋,整批来料外观一致性良好。3.2尺寸:按图纸与国标要求,重要尺寸零缺陷。 3.3性能:试装配与使用性能符合产品要求。 五、工序质量检验标准 1.冲裁检验标准 1.1对有可能造成伤害的尖角、棱边、粗糙要做去除毛刺处理。 1.2图纸中未明确标明之尖角(除特别注明外)均为R1.5。 1.3冲压加工所产生的毛刺,对于门板、面板等外露可见面应无明显凸起、凹陷、粗糙不平、划伤、锈蚀等缺陷。 1.4毛刺:冲裁后毛刺高L≤5%t(t为板厚)。 1.5划伤、刀痕:以用手触摸不刮手为合格,应≤0.1。 1.6平面公差度要求见表一。 附表一、平面度公差要求 表面尺寸(mm) 变形尺寸(mm) 3以下±0.2以下 大于3小于30 ±0.3以下 大于30小于315 ±0.5以下
油漆件表面质量检验规范
1.目的: 对油漆件质量进行有效控制,确保完工的零件符合图纸的指标,满足规定的使用要求。2.适用范围: 本规范适用于表面要求油漆的零件的检验; 3.职责: 凯麦公司油漆件表面质量检验员负责检验; 4.检验要求: 按公司Q/YX40101-2002《外观质量技术条件》中规定的油漆件要求分为1级、2级和3级进行检验。客户有特殊要求的按客户要求检验。 4.1 1级要求; 4.1.1烘烤形光漆表面; a. 漆膜表面应颜色均匀、光泽一致、平整、纹理清晰、符合样板、样品要求。 b.在100mmX100mm范围内允许有1~2个直径不大于0.1mm的疵病,其间距大于80mm。 c.非主要面允许有微细隐暗的桔纹,局部轻微的厚薄不均,微小流边线、隐暗的流边痕 迹,不太顺丝而细暗的砂纹印。 4.1.2烘烤形桔形漆表面。 a. 漆膜颜色、光泽、纹理须与样板、样品相符。 b.在100mmX100mm范围内允许有1~3个直径不大于0.2mm疵病。 c.桔形点允许有不太明显的大小结合。 d.非主要表面允许不太明显的纹理不清和桔形不均。 4.2 2级要求: 4.2.1烘烤型光漆表面; a.漆膜颜色、光泽、纹理必须符合样板、样品。 b. 在100mmX100mm范围内允许有1~3个直径不大于0.2mm疵病,其间距大于 80mm。 b.非主要表面允许有不太明显的隐暗桔纹,局部厚薄不匀,小流边线和微乱细砂纹印。
4.2.2 烘烤形桔形漆表面 a.漆膜颜色、光泽、纹理必须符合样板、样品。 b.在100mmX100mm范围内允许有1~3个直径不大于0.3mm疵病,其间距大于 80mm疵病。 c. 桔形点允许有不大明显的不均,大小结合。 4.3 3级要求: 4.3.1 烘烤形光漆和烘烤型桔形漆表面; a. 漆面各处必须喷到,厚薄一致。 b.喷漆面无明显液挂,无损伤性缺陷或碎裂。 4.4 油漆件检验时必须以图纸或样品为基准,对非漆面及保护面和油漆件上的孔、槽等必须清理干净,保护漆去掉后的表面必须用清洗剂擦干净,不允许有保护漆残留渍。4.5 平台油漆件用刀口尺和塞尺进行检验,刀口尺测量平面时不应有蹋边和不规则形状,中凹部份≤0.10mm。客户有特殊要求的按客户要求检验。 4.6 漆膜的附着力检验应合格。 4.7 漆膜的表面硬度检验应合格。 4.8 漆膜的耐溶剂实验应合格。 4.9 油漆零件的分级原则: 4.9.1 平台工作面属于1级要求检验。 4.9.2 内置零件喷漆按3级要求检验。 4.9.3 其余按2级要求检验(有特殊要求除外)。 5.工作程序: 5.1 检验条件: 喷漆件外观质量的检验应该在由两盏40W(最小)荧光灯或等效照明物照明下,并在45o角从检查人员后面射向被检表面,被检物应放置在中性背景前。 5.2 1级要求检验方法: 满足5.1条要求,在大约250 mm处(但不得超过300 mm)按4.1条和4.4、4.5条要求目视检验。
钣金件检验标准
钣金件检验标准 一、适用范围: 公司产品钣金件的尺寸、外观检验。 二、检验项目及验收标准: A. 尺寸验收标准:尺寸按图纸要求及钣金加工公差表执行,特殊情况以实际装配并提交研发部工程师协同解决。 B. 表面处理验收标准: a. 表面烤漆检验标准: 1. 颜色及纹路:由承制方按要求制作样板,双方确认。验收按样板,不得有明显色差(不得大于3度),纹路符合样板。 2. 密着检验:用百格刀划一面100方格到底材后,用3M胶布贴上,60度方向瞬间用力拉开,不得脱落40/100格。 3. 溶剂检验:酒精擦拭后,不能有变色、掉色、无光泽等现象。 4. 硬度检验:以H铅笔将笔芯前端切齐,铅笔与待测物成45度推出,表面无划伤。 5. 钣金件表面烤漆前须作前道电着处理,达到双重保护的目的。根据实际的使用效果,允许厂商使用双面镀锌材质加工,以替代电着工艺。 6. 厂商在每次送货时须提供材质报告,有表面处理要求的须提供表面处理检验合格报告 7. 外观判定标准,如下表: 判定标准 外观 1. 表面不得有任何碰伤、开裂、刮伤等严重表面缺陷。如加工过程中有此缺陷,喷涂前须补腻子处理。表面各边、角、焊接部位毛刺均须去除。 2. 表面污点、颗粒、气泡检验:
A面: 整个表面内允许3点,每点直径1mm以下,点与点距离20mm以上。 B面: 整个表面内允许5点,每点直径1mm以下,点与点距离20mm以上。 C面: 整个表面内允许7点,每点直径1mm以下,点与点距离20mm以上 3. 箱体内表面检验: 各面允许8点气泡或污点, 每点直径1mm以下,点与点距离20mm以上。 4. 烤漆厚度30μm-60μm。 5. 表面处理后,各螺柱及螺孔表面不允许有漆层覆盖,影响装配。 包装: 1. 每箱数量固定。 2. 包装袋内不得有残留毛屑及杂物。 3. 包装箱不得有破损现象。 4. 每箱须标明料号、品名、数量等资料。 b. 表面镀层检验标准: 镀层外观质量要求i. 镀层颜色检查 A、花锌:镀锌层经钝化后带有绿色、黄色和紫色的不亮或半光亮彩虹色; B、五彩:镀锌层经钝化后带有绿色、黄色和紫色光亮彩虹色; C、白锌:镀锌层经钝化后稍带有浅兰色调的银白色; D、镀铬:工程图无特别说明均为镀亮铬(3级—2级); E、镀镍:工程图无特别说明均为镀亮铬(3级—2级)。化学镀镍层应为稍带浅黄色的银白色或带黄色色彩的钢灰色,抛光后为光泽的钢灰色。ii. 镀层结晶 镀层结晶应是均匀、细致、光滑。iii. 允许缺陷镀层允许以下缺陷存在: A、轻微的水印(非主视面主要表面);
钣金件检验规程
1.目的:规范钣金结构件的检验标准,以使各过程的产品质量得以控制。 2.适用范围: 本标准适用于各种钣金结构件的检验,图纸和技术文件同时使用。当有冲突时,以技术规范和客户要求为准。 3.引用标准: 本标准的尺寸未注单位皆为mm,未注公差按以下国标IT13级执行 GB/T1800.1-2009产品几何技术规范极限与配合第1部分:公差、偏差、和配合的基础 GB/T1800.2 -2009产品几何技术规范极限与配合第2部分:标准公差等级和孔、轴极限偏差表 GB/1804-2000 一般公差未注公差的线性和角度尺寸的公差 未注形位公差按GB/T1184 -1996 形状和位置公差未注公差值执行。 4。原材料检验标准 4.1金属材料: 4.1.1钣材厚度及质量应符合国标,采用钣材需出示性能测试报告及厂商证明。 4.1.2材料外观:平整无锈迹,无开裂与变形。 4.1.3 尺寸:按图纸或技术要求执行,本司未有的按现行国标执行。 4.2通用五金件、紧固件 4.2.1外观:表面无绣迹、无毛刺批锋,整批来料外观一致性良好。 4.2.2尺寸:按图纸与国标要求,重要尺寸零缺陷。 4.2.2性能:试装配与使用性能符合产品要求。
5、工序质量检验标准 5.1冲裁检验标准 5.1.1 对有可能造成伤害的尖角、棱边、粗糙要做去除毛刺处理。 5.1.2 图纸中未明确标明之尖角(除特别注明外)均为R1.0。 5.1.3 冲压加工所产生的毛刺,对于门板、面板等外露可见面应无明显凸起、凹陷、粗糙不平、划伤、锈蚀等缺陷。 5.1.4毛刺:冲裁后毛刺高L≤5%t(t为板厚)。 5.1.5 划伤、刀痕:以用手触摸不刮手为合格,应≤0.1mm。 5.1.6平面度公差要求见表一。 附表一、未注平面度公差要求 5.2 折弯检验标准 5.2.1 毛刺:折弯后挤出毛刺高L≤10%t(t为板厚)。 5.2.2 压印:看得到有折痕,但用手触摸感觉不到。(有特殊表面要求和镜面除外) 5.2.3 折弯变形标准按照《表二》及《表三》。 【附表二:对角线公差要求】
钣金检验分析报告
深圳浦菲特机电技术有限公司 作业指导书文件编号 版次A0 修改状态 文件名称钣金产品检验报告页次 1 of 1 1.目的:为了便于控制钣金产品质量以及给检验员提供检验时的准确依据。 2. 适用范围:此标准适用于对钣金产品的检验。 3.检验要求 3.1 工件形状、材料种类符合图纸设计要求。 3.2 工件尺寸应符合要求: 3.2.1 基本尺寸、公差范围应符合图纸标注尺寸。 3.3对盛装液体的工件检验:向工件内加入水如不发生渗漏则为合格。 4..检验内容 产品类别钣金类抽样计划:正常单次抽样检验结果 序号检验 项目 检验内容、标准 检验 手段标准合格不合格 1 外观A.焊缝平整光滑,无裂纹,凹凸等缺陷。 B.工件成型后边角分明,切边无毛刺,表面无划伤,不 钢保护膜无破损。 目 测、 手试 2 尺寸 A.直线度:1000以内≤±1㎜,1000~3000≤±3㎜ B.平行度:1000以内≤0.5㎜,1000~3000≤0.8㎜ C.焊接符合图纸设计要求,图纸未标注要求的工件: 1.厚度1~2mm时,焊缝高度1~4mm,焊缝宽度2~ 2.厚度3~4mm时,焊缝高度3~5mm,焊缝宽度3~ D.剪板符合图纸要求,图纸未标注要求的工件: 1.厚度≤1.2 mm,公称尺寸≤200 mm时,允许偏差 ±0.5 mm 2.厚度≤1.2~4 mm,公称尺寸≤200 mm时,允许偏 差±1 mm。 2.厚度≤1.2~4 mm,公称尺寸200~1000 mm时, 许偏差±1.5 mm。 4. 厚度≤1.2~4 mm,公称尺寸1000~3000 mm时, 许偏差±2.0 mm. 卷尺、 卡 尺、 直角 尺、 表面处 理 A.护罩类钣金件焊缝必须打磨抛光打磨面要求平整 、光滑、相接边倒圆角; B.不锈钢件,不要有毛刺,焊缝打磨光滑。 C.焊缝打磨拉丝的宽带不允许15㎜,拉丝后的表面 原表面无明显差别,光泽纹理一致。 目测、 手试
现场质量检验报告单
第三章(2)现场质量检验报告单 质报单1、开挖基坑现场质量检验报告单 质报单2、基础工程现场质量检验报告单 质报单3、混凝土浇注申请报告单 质报单4、模板安装现场质量检验报告单 质报单5、拱架、支架现场质量检验报告单 质报单6、分层压实度现场质量检验报告单 质报单7、分层压实度现场质量检验报告单 质报单8、分层压实度现场质量检验报告单 质报单9、路基压实度现场质量检验报告单 质报单10、路面底基层压实度现场质量检验报告单 质报单11、路面基层压实度现场质量检验报告单 质报单12、路面面层压实度现场质量检验报告单 质报单13、无机结合料稳定抗压强度现场质量检验报告单质报单14、弯沉值检测现场质量检验报告单 质报单15、弯沉值检测现场质量检验报告单 质报单16、路面结构层厚度现场质量检验报告单 质报单17、路面结构层厚度现场质量检验报告单 质报单18、路面结构层厚度现场质量检验报告单 质报单19、水泥混凝土抗弯强度现场质量检验报告单 质报单20、水泥混凝土抗压强度现场质量检验报告单 质报单21、砂浆抗压强度现场质量检验报告单 质报单22、水泥混凝土抗压强度现场质量检验报告单 质报单23、砌筑砂浆施工现场质量检验报告单 质报单24、结构物回填现场质量检验报告单 质报单25、无机结合料稳定抗压强度现场质量检验报告单质报单26、隧道喷射混凝土抗压强度现场质量检验报告单质报单27、冲击压实路堤现场质量检验报告单 质报单28、强夯片(砾)石桩柱现场质量检验报告单
质报单29、土工织物铺设现场质量检验报告单 质报单30、坡体排水(仰斜排水孔)现场质量检验报告单质报单31、预应力锚索现场质量检验报告单 质报单32、锚碇板挡土墙现场质量检验报告单 质报单33、柱板式锚杆挡土墙现场质量检验报告单 质报单34、单元格锚杆框架防护现场质量检验报告单 质报单35、预应力锚杆框架现场质量检验报告单 质报单36、SNS柔性防护网现场质量检验报告单 另加:(通用)现场质量检验报告单 (编号说明:表ZBD-01即质报单1,其他相似。)
塑料管材检测项目及标准.doc
. 塑料管材检测项目及标准 塑料管材作为化学建材的重要组成部分,以其优越的性能,卫生、环保、低耗等为广大 用户所广泛接受,主要有UPVC排水管,UPVC给水管,铝塑复合管,聚乙烯(PE )给水 管材这几种。青岛科标检测研究院有限公司拥有多年的塑料管材检测和分析经验,是权威第 三方检测机构。并可根据检测和分析结果,出具权威检测和分析报告! 检测产品: 塑料管材:发泡管材、丙烯酸共聚聚氯乙烯管材、排水管材、PP 管材、农用管材、PVC 塑料管、五孔管、七孔管、双壁波纹管、HDPE双壁波纹管、通信管材、电力管、梅花管、透水管、硅芯管、HDPE硅芯管、高压电力管、碳素管、光缆管、方孔栅格管、电缆护套管、 碳素管、三色光缆管、PVC 格栅管、PVC 塑料线管 塑料管件:VC-U管件、双壁波纹管件、PVC 管件、铝塑管、多孔管、PVC-U加筋管塑料软管:机油软管、喷雾软管、焊接软管、增强软管、液压软管、冷却系统软管、内 燃机软管、压缩空气软管、耐酸碱软管、织物增强软管、喷砂软管、汽车制动软管 检测项目: 重点评估项目:☆强度和刚性☆水力性能☆密封性能☆寿命评估☆耐腐蚀性 力学性能:拉伸强度、弯曲强度、摩擦系数、蠕变性能、撕裂强度、剪切性能、冲击性 能、压缩性能、疲劳强度、断裂韧度、拉伸性能、弯曲性能、电性能、耐磨性能、低温性能、回弹性能、撕裂性能 燃烧性能检测:垂直燃烧点燃温度氧指数水平燃烧炽热棒 热性能检测:热变形温度、热分解温度、维卡软化点、高低温冲击、玻璃化转变温度、 熔融温度、热稳定性、尺寸热稳定性、负荷热变形温度、马丁耐热、总体积收缩量、线性收
缩率、维卡软化点、线性热膨胀率、流动性、熔点、软化点、熔体流动速率、热导率、玻璃化转变温度、脆化温度、失强温度 适用性:导热性能耐腐蚀性能耐低温性能耐液压性能绝缘性能透湿性能 检测标准: GB/T 20674.2-2006塑料管材和管件聚乙烯系统熔接设备第2部分:电熔对接 GB/T 21300-2007塑料管材和管件不透光性的测定 GB/T 23241-2009灌溉用塑料管材和管件基本参数及技术条件 GB/T 4217-2008流体输送用热塑性塑料管材公称外径和公称压力 .
钣金质量检验标准
钣金质量检验标准 规范钣金结构件的检验标准,以使各过程的产品质量得以控制。 图纸和技术文件并同使用。当有冲突时,以技术规范和客户要求为准。 1.钣材厚度及质量应符合国标,采用的钣材需出示性能测试报告及厂商证明。 2.折弯检验标准 毛刺:折弯后挤出毛刺高L?10%t(t为板厚)。除特别注明外,折弯内圆角为 R1。 压印:看得到有折痕,但用手触摸感觉不到(可与限度样板相比较)。 3.折弯变形标准按照照 对角线公差要求 对角线尺寸(mm) 对角线的尺寸差(mm) 300以下 ?0.3以下 大于300小于600 ?0.6以下 大于600小于900 ?0.9以下 大于900小于1200 ?1.2以下 大于1200小于1500 ?1.5以下 大于1500小于1800 ?1.8以下 大于1800小于2100 ?2.1以下 大于2100小于2400 ?2.4以下 大于2400小于2700 ?2.7以下 折弯方向、尺寸与图纸一致。 4.钣金加工件检验标准 尺寸按图纸要求检验。
标准尺寸尺寸公差(mm) 3以下 ?0.2 大于3小于30 ?0.3 大于30小于315 ?0.5 大于315小于1000 ?1.0 大于1000小于2000 ?1.5 大于2000小于3150 ?2.0 5.压铆件 压铆螺母(柱)、压铆螺钉、涨铆螺母(柱)、拉铆螺母等,压上零部件后,螺纹不得变形(螺母或螺钉能自由进出,顺畅无卡滞现象),压铆件应与板面相平,不允许凸起或凹进(手感触摸应平滑),压铆件与板面垂直,压铆后压铆区无有变形、猪嘴现象,拉包的高度、壁厚应均匀一致,顶部不应有毛刺。 6.焊接 焊缝应牢固、均匀,不得有虚焊、裂纹、未焊透、焊穿、豁口、咬边等缺陷。焊缝长度、高度不均不允许超过长度、高度要求的10%。 焊点要求:焊点长度8,12mm,两焊点之间的距离200?20mm,焊点位置要对称,上下位置要统一。如加工图纸上对焊点有特殊要求,按图纸执行。 点焊间距小于50mm,焊点直径小于φ5,焊点布置均匀,焊点上压痕深度不超过板材实际厚度15%,且焊接后不能留有明显的焊疤。 焊接后,其它非焊接部位不允许有被焊渣、电弧损伤现象,表面焊渣、飞溅物需清除干净。 焊接后,零件外表面应无夹渣、气孔、焊瘤、凸起、凹陷等缺陷,内表面的缺陷应不明显 及不影响装配。门板、面板等重要零件还应去除焊后应力,防止工件变形。
排水管道及配件安装检验批质量验收记录
排水管道及配件安装检验批质量验收记录
填写说明 一、填写依据 1 《建筑给水排水及采暖工程施工质量验收规范》GB50242-2002。 2 《建筑工程施工质量验收统一标准》GB50300-2013。 二、检验批划分 可按设计系统、楼层、施工段、单元划分。 三、GB50242-2002规范摘要 主控项目 5.2.1 隐蔽或埋地的排水管道在隐蔽前必须做灌水试验,其灌水高度应不低于底层卫生器具的上边缘或底层地面高度。 检验方法:满水15min水面下降后,再灌满观察5min,液面不降,管道及接口无渗漏为合格。 5.2.2 生活污水铸铁管道的坡度必须符合设计或本规范表5.2.2的规定。 5.2.3 生活污水塑料管道的坡度必须符合设计或本规范表5.2.3的规定。 5.2.4 排水塑料管必须按设计要求及位置装设伸缩节。如设计无要求时,伸缩节间距不得大于4m。 高层建筑中明设排水塑料管道应按设计要求设置阻火圈或防火套管。 检验方法:观察检查。 5.2.5 排水主立管及水平干管管道均应做通球试验,通球球径不小于排水管道管径的2/3,通球率必须达到100%。 检查方法:通球检查。 一般项目 5.2.6 在生活污水管道上设置的检查口或清扫口,当设计无要求时应符合下列规定: 1 在立管上应每隔一层设置一个检查口,但在最底层和有卫生器具的最高层必须设置。如为两层建筑时,可仅在底层设置立管检查口;如有乙字弯管时,则在该层乙字弯管的上部设置检查口。检查口中心高度距操作地面一般为1m,允许偏差 ±20mm;检查口的朝向应便于检修。暗装立管,在检查口处应安装检修门。 2 在连接2个及2个以上大便器或3个及3个以上卫生器具的污水横管上应设置清扫口。当污水管在楼板下悬吊敷设时,可将清扫口设在上一层楼地面上,污水管起点的清扫口与管道相垂直的墙面距离不得小于200mm;若污水管起点设置堵头代替清扫口时,与墙面距离不得小于400mm。 3 在转角小于135°的污水横管上,应设置检查口或清扫口。 4 污水横管的直线管段,应按设计要求的距离设置检查口或清扫口。 检验方法:观察和尺量检查。 5.2.7 埋在地下或地板下的排水管道的检查口,应设在检查井内。井底表面标高与检查口的法兰相平,井底表面应有5%坡度,坡向检查口。 检验方法:尺量检查。 5.2.8 金属排水管道上的吊钩或卡箍应固定在承重结构上。固定件间距:横管不大于2m;立管不大于3m。楼层高度小于或等于4m,立管可安装1个固定件。立管底部的弯管处应设支墩或采取固定措施。 检验方法:观察和尺量检查。 5.2.9 排水塑料管道支、吊架间距应符合表5.2.9的规定。
给排水管材检验细则
塑料、铸铁给排水管材检验细则 塑料管道 一、检验目的: 及时、公正地出具有效检验数据。 二、检验项目: 检测产品几何尺寸的符合性,如壁厚、直径、长度、角度和垂直长等的测量。 三、检验评定依据: GB/T 8806-2008 《塑料管道系统塑料部件尺寸的测定》 四、仪器设备 1.游标卡尺 0~150mm 精度 0.01mm 0~300mm 精度 0.02mm 0~500mm 精度 0.02mm 2.光学显微镜 0~25mm 精度 0.001mm 3.钢直尺 0~500mm 精度0.5mm 0~1000mm 精度 0.5mm 4.钢卷尺 0~7.5m 精度 1mm 5.直径π尺Φ15~Φ55 mm 精度 0.05mm Φ50~Φ300 mm 精度 0.01mm Φ300~Φ600 mm 精度 0.01mm Φ600~Φ900 mm 精度 0.02mm Φ900~Φ1200 mm 精度 0.01mm 6.壁厚规 0~10mm 精度0.01 mm 7.微分筒 0~25mm 精度 0.001mm 8.直角尺。 五、试验步骤 测量要求 一般要求测量量具的准确度
7.3.3壁厚 7.3.3.1选择量具或仪器以及测量的相关步骤,使结果的准确度在下表3要求的范围内,除非其他标准另有规定,应使用光学显微镜、壁厚规或微分筒进行测量。 7.3.3.2最大和最小壁厚 在选定的被测截面上移动测量量具直至找出最大和最小壁厚,并记录测量值。 7.3.3.3平均壁厚 在每个选定的被测截面上,沿环向均匀间隔至少6点进行壁厚测量。由测量值计算算术平均值,按上表的规定修约并记录结果作为平均壁厚,em 7.3.4直径 7.3.4.1选择量具或仪器以及相关的步骤测量试样在选定截面处的直径(外径或内径),使结果的准确度在下表4要求的范围内,除非其他标准另有规定。 7.3.4.2按表A.2选择被测截面,测量部件的直径。 7.3.4.3最大和最小直径 在选定的每个被测截面上移动测量量具,直至找出直径的极值并记录测量值。 7.3.4.4平均外径 平均外径de,m可用以下任意方法测定 A)用π尺直接测量; B)按下表5的要求对每个选定截面上沿环向均匀间隔测量的一系列单个值计算算术平均值,按上表4的规定修约并记录结果作为平均外径de,m
钣金件检验作业指导书
钣金件检验作业指导书 一、目的 规范钣金结构件的检验标准,以使各过程的产品质量得以控制。 二、适用范围 本标准适用于各种钣金结构件的检验,图纸和技术文件并同使用。当有冲突时,以技术规范和客户要求为准。 三、引用标准 本标准的尺寸未注单位皆为mm,未注公差按以下国标IT13级执行 GB/T1800.3-1998 极限与配合标准公差和基本偏差数值表 GB/T1800.4 -1998 极限与配合标准公差等级和孔、轴的极限偏差表 GB/1804-2000 一般公差未注公差的线性和角度尺寸的公差 未注形位公差按GB/T1184 –1996 形状和位置公差未注公差值执行。 四、原材料检验标准 1.金属材料 1.1钣材厚度及质量应符合国标,采用的钣材需出示性能测试报告及厂商明。 1.2材料外观:平整无锈迹,无开裂与变形。 1.3 尺寸:按图纸或技术要求执行,本司未有的按现行国标执行。 2.塑粉 2.1塑粉整批来料一致性良好,有出厂证明与检验报告,包含粉号、色号以及各项检验参数。 2.2试用后符合产品要求(包括颜色、光泽、流平性、附着力等)。 3通用五金件、紧固件 3.1外观:表面无绣迹、无毛刺批锋,整批来料外观一致性良好。 3.2尺寸:按图纸与国标要求,重要尺寸零缺陷。 3.3性能:试装配与使用性能符合产品要求。 五、工序质量检验标准 1.冲裁检验标准 1.1对有可能造成伤害的尖角、棱边、粗糙要做去除毛刺处理。 1.2图纸中未明确标明之尖角(除特别注明外)均为R1.5。 1.3冲压加工所产生的毛刺,对于门板、面板等外露可见面应无明显凸起、凹陷、粗糙不平、划伤、锈蚀等缺陷。 1.4毛刺:冲裁后毛刺高L≤5%t(t为板厚)。 1.5划伤、刀痕:以用手触摸不刮手为合格,应≤0.1。 1.6平面公差度要求见表一。 附表一、平面度公差要求 表面尺寸(mm) 变形尺寸(mm) 3以下±0.2以下 大于3小于30 ±0.3以下 大于30小于315 ±0.5以下 大于315小于1000 ±1.0以下 大于1000小于2000 ±1.5以下 大于2000小于3150 ±2.0以下 2.折弯检验标准 2.1 毛刺:折弯后挤出毛刺高L≤10%t(t为板厚)。除特别注明外,折弯内圆角为R1。 2.2 压印:看得到有折痕,但用手触摸感觉不到(可与限度样板相比较)。
钣金件检验标准规范
\\ Q/XW Q/XW JXXXXX-2012 钣金件检验规范 (征求意见稿) 2012-XX-XX 发布 2012-XX-XX实施 发布
Q/XW JXXXXX-2012 1. 目的 本标准旨在明确制造过程中对各种钣金件质量的描述、检验方法、判定标准、及对钣金件固有缺陷记录和使用标准,为制造过程、入库的质量检验提供依据。 2. 适用范围 本标准适用于本公司范围内生产的冲压件半成品和成品的检验。 3. 引用标准 GB/T 2828 逐批检查计效抽样程序及抽样表 GB/T 13914-2002 冲压件尺寸公差 GB/T 700-2006 碳素结构钢 GB/T1800.3—1998 标准公差数值 GB/T1031—1995 表面粗糙度参数及其数值 GB/T 6583.1 质量管理和质量保证术语 GB/T 13915-92 冲压件角度公差 JB/T 8930-1999 冲压工艺质量控制规范 JB/T 4129-1999 冲压件毛刺高度 GB/T 15055-2007 冲压件未注公差尺寸极限偏差 GB/T 8923-2009 涂覆涂料前钢材表面处理表面清洁度的目视评定 GB/T 708-2006 冷轧钢板和钢带的尺寸、外形、重量及允许偏差 4.术语定义 4.1 关键钣金件 对整车的结构、装配、生产工艺、使用性能、安全等方面有重要影响的钣金件 将这一类钣金件作为过程质量的关键环节去加以控制,列为关键钣金件。 4.2 固有缺陷 针对前期产品开发过程中,因技术、工装及设计等原因导致的钣金件存在一些工艺上无法彻底整改的缺陷,制造过程对这些缺陷进行固化和稳定。 4.3 钣金件分类 4.3.1 根据钣金件在车身上功能尺寸等作用 分为:关键件和非关键件。
公路工程竣工资料全集(现场质量检验报告单)
第二章 公路工程检验使用表
目录施工测量放线 B-001 导线点测量报表 B-002 施工增加导线点测量报表 B-003 附合导线测量计算表 B-004 水准点测量报表 B-005 施工增加水准点测量报表 B-006 路线主点桩测量报表 B-007 施工放线测量记录表 B-008 施工放样测量报表 B-009 水准测量记录表 路基工程 B-010 清理与掘除检验报告单 B-011 土方路基现场质量检验报告单 B-012 石方路基现场质量检验报告单 B-013 砂垫层现场质量检验报告单 B-014 袋装砂井、塑料排水板现场质量检验报告单 B-015 碎石桩(砂桩)现场质量检验报告单 B-016 CFG现场质量检验报告单 B-017 粉喷桩现场质量检验报告单 B-018 加筋工程土工合成材料现场质量检验报告单 B-019 隔离工程土工合成材料现场质量检验报告单 B-020 过滤排水工程土工合成材料现场质量检验报告单B-021 防裂工程土工合成材料现场质量检验报告单 B-022 管节预制现场质量检验报告单 B-023 管道基础及管节安装现场质量检验报告单 B-024 检查(雨水)井砌筑现场质量检验报告单 B-025 土沟现场质量检验报告单 B-026 浆砌排水沟现场质量检验报告单 B-027 盲沟现场质量检验报告单 B-028 排水泵站(沉井)现场质量检验报告单
B-029 砌体挡土墙现场质量检验报告单 B-030 干砌挡土墙现场质量检验报告单 B-031 混凝土挡土墙现场质量检验报告单 B-032 筋带现场质量检验报告单 B-033 锚杆、拉杆现场质量检验报告单 B-034 面板预制现场质量检验报告单 B-035 面板安装现场质量检验报告单 B-036 锚杆、锚碇板和加筋土挡土墙总体现场质量检验报告单 B-037 锚杆、锚碇板和加筋土挡土墙墙背填土现场质量检验报告单B-038 抗滑桩现场质量检验报告单 B-039 挖方边坡锚喷防护现场质量检验报告单 B-040 锥、护坡现场质量检验报告单 B-041 浆砌砌体现场质量检验报告单 B-042 干砌片石现场质量检验报告单 B-043 导流工程现场质量检验报告单 B-044 石笼防护现场质量检验报告单 路面工程 B-045 水泥混凝土面层现场质量检验报告单 B-046 沥青混凝土面层和沥青碎(砾)石面层现场质量检验报告单B-047 沥青贯入式面层(或上拌下贯式面层)现场质量检验报告单B-048 沥青表面处治面层现场质量检验报告单 B-049 水泥土底基层现场质量检验报告单 B-050 水泥稳定粒料基层及底基层现场质量检验报告单 B-051 石灰土底基层现场质量检验报告单 B-052 石灰稳定粒料底基层现场质量检验报告单 B-053 石灰、粉煤灰土底基层现场质量检验报告单 B-054 石灰、粉煤灰稳定粒料基层和底基层现场质量检验报告单B-055 级配碎(砾)石基层和底基层现场质量检验报告单 B-056 填隙碎石(矿渣)底基层现场质量检验报告单 B-057 路缘石铺设现场质量检验报告单 B-058 路肩现场质量检验报告单 桥梁工程 B-059 桥梁总体现场质量检验报告单 B-060 钢筋安装现场质量检验报告单
公路工程现场质量检验报告单2017版
目录 现场质量检验表 (7) 表土清除现场质量检验报告单 (8) 土方路基现场质量检验报告单 (9) 石方路基现场质量检验报告单 (11) 砂(碎石)垫层现场质量检验报告单 (12) 垂直排水井(即袋装砂井、塑料排水板)处理软基 (14) 现场质量检验报告单 (14) 粒料桩现场质量检验报告单 (15) 加固土桩现场质量检验报告单 (16) 水泥粉煤灰碎石桩现场质量检验报告单 (17) 刚性桩现场质量检验报告单 (18) 加筋工程土工合成材料处置层现场质量检验报告单 (19) 隔离工程土工合成材料铺筑现场质量检验报告单 (20) 过滤排水工程土工合成材料现场质量检验报告单 (21) 防裂工程土工合成材料现场质量检验报告单 (22) 管节预制现场质量检验报告单 (23) 混凝土排水管安装现场质量检验报告单 (24) 检查(雨水)井砌筑现场质量检验报告单 (25) 土沟现场质量检验报告单 (26) 浆砌排水沟现场质量检验报告单 (28) 盲沟现场质量检验报告单 (29) 排水泵站(沉井)现场质量检验报告单 (30) 沉淀池现场质量检验报告单 (31) 浆砌挡土墙现场质量检验报告单 (32) 干砌挡土墙现场质量检验报告单 (34) 片石混凝土挡土墙现场质量检验报告单 (35) 悬臂式和扶臂式挡土墙现场质量检验报告单 (37) 加筋挡土墙筋带现场质量检验报告单 (38) 拉杆现场质量检验报告单 (39) 锚杆现场质量检验报告单 (40) 面板预制现场质量检验报告单 (41) 面板安装现场质量检验报告单 (43) 锚杆、锚碇板和加筋土挡土墙总体现场质量检验报告单 (45) 锚杆、锚碇板和加筋土挡土墙墙背填土现场质量检验报告单 (46) 锚杆、锚索现场质量检验报告单 (47) 坡面结构现场质量检验报告单 (48) 土钉现场质量检验报告单 (49)
水泥混凝土路面质量检验报告单
〖其他公路〗 水泥混凝土路面质量检验报告单 工程部位: 施工单位: 监理单位: 分项工程名称: 所属分部工程名称: 所属建设项目: 检测: 复核: 施工主管: 质检负责人: 施工技术负责人: 年 月 日 基本要求 1)基层必须符合规定要求,并应进行弯沉测定,验算的基层整体模量应满足设计要求。 2) 水泥强度、物理性能和化学性能和化学成份应符合国家标准及有关规范的规定。 3)粗细集料、水、外掺剂、接缝填缝料应符合设计和施工规范要求。 4)施工配合比应根据现场测定水泥的实际强度进行计算,并经试验,选择采用最佳配合比。 5)接缝位置、规格、尺寸及传力杆、拉力杆的设置应符合设计要求。 6)路面拉毛或机具压等抗滑措施,其构件深度应符合施工规范要求。 7)面层与其他构件物相接应平顺,检查井井盖顶面高程应高于周边路面1—3mm 。雨水口标高按设计比路面底5—8mm ,路面边缘无积水现象。 8)混凝土路面铺筑后按施工规范要求养生。 实测项目 项次 检查项目 规定值或允许偏差 实测值和实测偏差值 1 2 3 4 5 6 7 8 9 10 1Δ 抗压强度(MPa) 符合设计要求 见检查记录 2Δ 板厚度(mm) 代表值 -5 见检查记录 合格值 -10 见检查记录 3 平整度 IRI (m/Km ) 2.0 见检查记录 δ(mm ) 3.2 见检查记录 最大间隙h (mm ) 5 见检查记录 4 抗滑构造深度(mm) 一般不小于0.5,不大于1.0,特殊路段不小于0.6,不大于1.1。 见检查记录 5 相邻板高差(mm) 3 见检查记录 6 纵横缝顺直度(mm) 10 见检查记录 7 中线平面偏差(mm) 20 见检查记录 8 路面宽度(mm) +20 见检查记录 9 纵断高程(mm) +15 见检查记录 10 横坡(%) +0.25 见检查记录 外观鉴定 自检意见 签字: 日期 监理意见 签字 日期