基于UG的注塑模浇注系统构建与分析
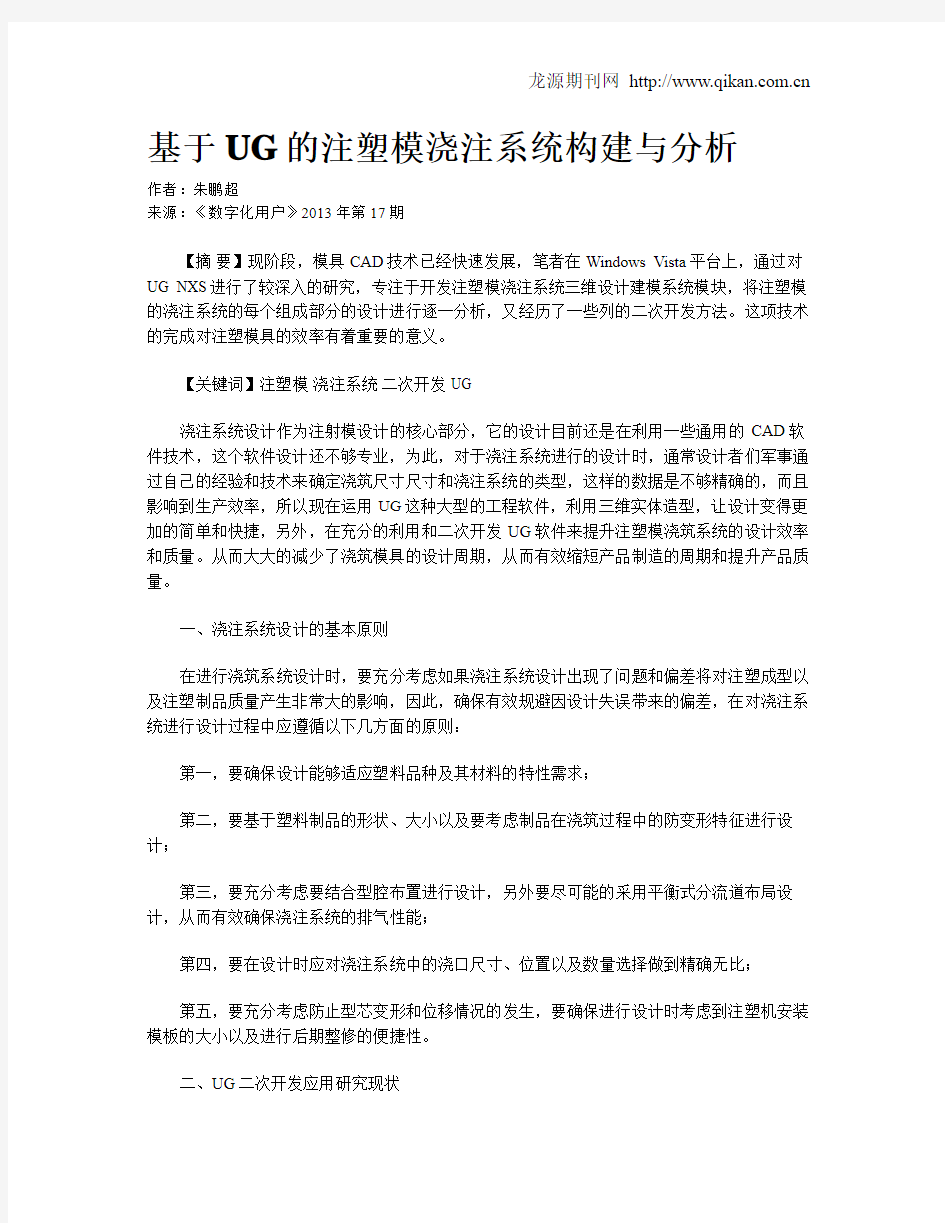

龙源期刊网 https://www.360docs.net/doc/143754473.html,
基于UG的注塑模浇注系统构建与分析
作者:朱鹏超
来源:《数字化用户》2013年第17期
【摘要】现阶段,模具CAD技术已经快速发展,笔者在Windows Vista平台上,通过对UG NXS进行了较深入的研究,专注于开发注塑模浇注系统三维设计建模系统模块,将注塑模的浇注系统的每个组成部分的设计进行逐一分析,又经历了一些列的二次开发方法。这项技术的完成对注塑模具的效率有着重要的意义。
【关键词】注塑模浇注系统二次开发UG
浇注系统设计作为注射模设计的核心部分,它的设计目前还是在利用一些通用的CAD软件技术,这个软件设计还不够专业,为此,对于浇注系统进行的设计时,通常设计者们军事通过自己的经验和技术来确定浇筑尺寸尺寸和浇注系统的类型,这样的数据是不够精确的,而且影响到生产效率,所以现在运用UG这种大型的工程软件,利用三维实体造型,让设计变得更加的简单和快捷,另外,在充分的利用和二次开发UG软件来提升注塑模浇筑系统的设计效率和质量。从而大大的减少了浇筑模具的设计周期,从而有效缩短产品制造的周期和提升产品质量。
一、浇注系统设计的基本原则
在进行浇筑系统设计时,要充分考虑如果浇注系统设计出现了问题和偏差将对注塑成型以及注塑制品质量产生非常大的影响,因此,确保有效规避因设计失误带来的偏差,在对浇注系统进行设计过程中应遵循以下几方面的原则:
第一,要确保设计能够适应塑料品种及其材料的特性需求;
第二,要基于塑料制品的形状、大小以及要考虑制品在浇筑过程中的防变形特征进行设计;
第三,要充分考虑要结合型腔布置进行设计,另外要尽可能的采用平衡式分流道布局设计,从而有效确保浇注系统的排气性能;
第四,要在设计时应对浇注系统中的浇口尺寸、位置以及数量选择做到精确无比;
第五,要充分考虑防止型芯变形和位移情况的发生,要确保进行设计时考虑到注塑机安装模板的大小以及进行后期整修的便捷性。
二、UG二次开发应用研究现状
模流分析
模具厂所接的订单的和一般公司还有所不同,我们所接的模具订单各种各样,工程师的经验有时毕竟有限,所以借助MOLDFLOW软件的分析功能,对我们设计模 具帮助很大。 案例一,CLIP设计: 此产品为一固定U盘的回行夹。如下图所示,标示处变形量要求较严格,以往生产出来的产品此处变形常常偏大,我们的工程师考虑先在模具设计时设定一方向的预变形,与产品变形相互抵消,保证产品符合要求的。 问题是此预变形量多大,方向如何,设计前并不知道,如果预变形做的太大, 将来产品可能就会反向变形。 借助MOLDFLOW软件的FLOW COOL WARP 模块,我们先分析出产品可能的变形量,在此基础上,给模具设计一合理的预变形量,从而一次试模成功,获得 了合格的产品。 案例二,memorex-bottom-top 设计:[/ALIGN]
此套模具为2+2 模穴,设计为自然平衡流道,如果不经过分析,模具设计者很难想到要在标示处加强排气,只能等试模时才能发现问题,必然会提高整 个产品上市周期。 经过 MOLDFLOW 软件的FLOW 模块分析后,我们在模具设计前就已经知道此问题,所以模具设计时特意在此处加强排气,保证一次试模成功。 还有一些案例解决流道平衡的问题,一模多腔的设计,通过控制流道尺寸,保证流动平衡,从而控制产品品质。避免由于流动不平衡带来过保压现象,导致产品翘曲变形。同时优化流道尺寸设计还有一个很大的益处就是减小循环周期。因为很多情况下,产品最后凝固在流道处,如果流道尺寸偏大,必然提高整个循 环周期,同时还会产生较多的废料。 电池盖部件是我们运用MOLDFLOW软件的又一成功案例。此产品是薄壁件, 难以填充。 在分析之前,解决它的方法是加大注射压力,提高注射速度,强制成型。这样一方面机器磨损较大,另外高压高速注射后的产品内部残余应力较大,产品品质仍然无法保证。采用MOLDFLOW分析后,采用局部加厚的方法,改善了产品的流动,从而使公司可以利用较小的压力和较低的注射速度成型。提高了成型参数 的选择范围,改善了产品品质。 [/ALIGN] [/TD][/TR
NTFS文件系统结构分析
NTFS文件系统结构分析 在NTFS文件系统中,文件存取是按簇进行分配,一个簇必需是物理扇区的整数倍,而且总 是2的整数次方。NTFS文件系统并不去关心什么是扇区,也不会去关心扇区到底有多大(如是不是512字节),而簇大小在使用格式化程序时则会由格式化程序根据卷大小自动的进行 分配。 文件通过主文件表(MFT)来确定其在磁盘上的存储位置。主文件表是一个对应的数据库, 由一系列的文件记录组成--卷中每一个文件都有一个文件记录(对于大型文件还可能有多个记录与之相对应)。主文件表本身也有它自己的文件记录。 NTFS卷上的每个文件都有一个64位(bit)称为文件引用号(File Reference Number,也称文件索引号)的唯一标识。文件引用号由两部分组成:一是文件号,二是文件顺序号。文 件号为48位,对应于该文件在MFT中的位置。文件顺序号随着每次文件记录的重用而增加, 这是为NTFS进行内部一致性检查而设计的。 NTFS使用逻辑簇号(Logical Cluster Number,LCN)和虚拟簇号(Virtual Cluster Number,VCN)来进行簇的定位。LCN是对整个卷中所有的簇从头到尾所进行的简单编号。卷因子乘 以LCN,NTFS就能够得到卷上的物理字节偏移量,从而得到物理磁盘地址。VCN则是对属于特定文件的簇从头到尾进行编号,以便于引用文件中的数据。VCN可以映射成LCN,而不必 要求在物理上连续。
NTFS的目录只是一个简单的文件名和文件引用号的索引,如果目录的属性列表小于一个记 录的长度,那么该目录的所有信息都存储在主文件表的记录中,对于大于记录的目录则使用 B+树进行管理。
模具毕业设计69鼠标外壳注塑模毕业设计论文
目录 前言 摘要 第一章零件的工艺分析 (4) 1.1 材料的选择 (4) 1.2 产品工艺性与结构分析 (5) 第二章模具结构设计 (6) 2.1 型腔数量以及排列方式 (6) 2.2 初选注射机。 (6) 2.3 分型面的设计 (7) 2.4 浇注系统与排溢系统的设计 (9) 2.5 成型零件的设计 (15) 1. 凹模的设计 (15) 2. 型心尺寸的计算 (21) 3. 模具型腔侧壁和底版厚度的计算 (26) 2.6 推出机构的设计 (29) 2.7 侧向分型与抽芯机构的设计 (32) 2.8 注射机参数的较核 (34) 前言 毕业设计是在修完所有课程之后,我们走向社会之前的一次综合性设计。在此次设计中,主要用到所学的注射模设计,以及机械设计等方面的知识。着重说明了一副注射模的一般流程,即注射成型的分析、注射机的选择及相关参数校核、模具的结构设
计、注射模具设计的有关计算、模具总体尺寸的确定与结构草图的绘制、模具结构总装图和零件工作图的绘制、全面审核投产制造等。其中模具结构的设计既是重点又是难点,主要包括成型位置的及分型面的选择,模具型腔数的确定及型腔的排列和流道布局和浇口位置的选择,模具工作零件的结构设计,侧面分型及抽芯机构的设计,推出机构的设计,拉料杆的形式选择,排气方式设计等。通过本次毕业设计,使我更加了解模具设计的含义,以及懂得如何查阅相关资料和怎样解决在实际工作中遇到的实际问题,这为我们以后从事模具职业打下了良好的基础。 本次毕业设计也得到了广大老师和同学的帮助,在此一一表示感谢!由于实践经验的缺乏,且水平有限,时间仓促。设计过程中难免有错误和欠妥之处,恳请各位老师和同学批评指正。 在编写说明书过程中,我参考了《塑料模成型工艺与模具设计》、《实用注塑模设计手册》和《模具制造工艺》等有关教材。引用了有关手册的公式及图表。但由于本人水平的有限,本说明书存在一些缺点和错误,希望老师多加指正,以达到本次设计的目的。 绪论 第一节塑料成型在工业生产中的重要性 一、塑料及塑料工业的发展 塑料是以树脂为主要成分的高分子有机化合物,简称高聚物。塑料其余成分包括增塑剂、稳定剂、增强剂、固化剂、填料及其它配合剂。 塑料制件在工业中应用日趋普遍,这是由于它的一系列特殊
模具浇注系统设计
浇注系统设计 9.1 浇注系统设计原则 9.1.1 浇注系统的组成 模具的浇注系统是指模具中从注塑机 喷嘴开始到型腔入口为止的流动动通道, 它可分为普通流道浇注系统和无流道浇注 系统两大类型。普通流道浇注系统包括主 流道、分流道、冷料井和浇口组成。如图 9-1所示。 9.1.2 浇注系统设计时应遵循如下原则: 1 . 结合型腔的排位,应注意以下三点: a .尽可能采用平衡式布置,以便熔融塑料能平衡地充填各型腔; b .型腔的布置和浇口的开设部位尽可能使模具在注塑过程中受力均匀; c .型腔的排列尽可能紧凑,减小模具外形尺寸。 2 . 热量损失和压力损失要小 a .选择恰当的流道截面; b .确定合理的流道尺寸; 在一定范围内,适当采用较大尺寸的流道系统,有助于降低流动阻力。但流道系统 上的压力降较小的情况下,优先采用较小的尺寸,一方面可减小流道系统的用料, 另一方面缩短冷却时间。 c .尽量减少弯折,表面粗糙度要低。 3 . 浇注系统应能捕集温度较低的冷料,防止其进入型腔,影响塑件质量; 4 . 浇注系统应能顺利地引导熔融塑料充满型腔各个角落,使型腔内气体能顺利排出; 5 . 防止制品出现缺陷; 避免出现充填不足、缩痕、飞边、熔接痕位置不理想、残余应力、翘曲变形、收 缩不匀等缺陷。 6 . 浇口的设置力求获得最好的制品外观质量 浇口的设置应避免在制品外观形成烘印、蛇纹、缩孔等缺陷。 7 . 浇口应设置在较隐蔽的位置,且方便去除,确保浇口位置不影响外观及与周围零件 发生干涉。 8 . 考虑在注塑时是否能自动操作 4 6 1 2 3 I I 局部放大 图9-1 浇注系统的组成 1 - 主流道 ; 2 - 一级分流道 ; 3 - 拉料槽兼冷料井 4 - 冷料井 ; 5 - 二级分流道 ; 6 – 浇口 5
注塑模具毕业设计
前言 光阴似梭,大学三年的学习一晃而过,为具体的检验这三年来的学习效果,综合检测理论在实际应用中的能力,除了平时的考试、实验测试外,更重要的是理论联系实际,即此次设计的课题为闹钟后盖的注塑模具。 本次毕业设计课题来源于生活,应用广泛,但成型难度大,模具结构较为复杂,对模具工作人员是一个很好的考验。它能加强对塑料模具成型原理的理解,同时锻炼对塑料成型模具的设计和制造能力。本次设计以注射闹钟后盖模具为主线,综合了成型工艺分析,模具结构设计,最后到模具零件的加工方法,模具总的装配等一系列模具生产的所有过程。能很好的学习致用的效果。在设计该模具的同时总结了以往模具设计的一般方法、步骤,模具设计中常用的公式、数据、模具结构及零部件。把以前学过的基础课程融汇到综合应用本次设计当中来,所谓学以致用。在设计中除使用传统方法外,同时引用了CAD、Pro/E等技术,使用Office软件,力求达到减小劳动强度,提高工作效率的目的。 本次设计中得到了戴老师的指点。同时也非常感谢邵阳学院各位老师的精心教诲。 由于实际经验和理论技术有限,设计的错误和不足之处在所难免,希望各位老师批评指正。 目录 前言. (1) 绪论 (2) 1 塑料的工艺分析 (4) 塑件成形工艺分析 (4) 闹钟后盖原料(ABS)的成型特性与工艺参数 (4) 2 注塑设备的选择 (7)
估算塑件体积 (7) 选择注射机 (7) 模架的选定 (7) 最大注射压力的校核 (8) 3 塑料件的工艺尺寸的计算 (10) 型腔的径向尺寸 (10) 型芯的计算 (10) 模具型腔壁厚的计算 (11) 4 浇注系统的设计 (12) 主流道的设计 (12) 冷料井的设计 (13) 分流道的设计 (13) 浇口的选择 (14) 5 分型面的选择与排气系统的设计 (17) 分型面的选择 (17) 排气槽的设计 (17) 6 合模导向机构的设计 (18) 7 脱模机构的设计 (20) 8 温度调节系统的设计 (21) 模具冷却系统的设计 (22) 模具加热系统的设计 (22) 9 模具的装配 (23) 模具的装配顺序 (23) 开模过程分析 (24) 设计总结 (25) 参考资料 (26) 致谢 (27) 绪论 {一} 【模具在加工工业中的地位】 模具是利用其特定形状去成型具有一定的形状和尺寸制品的工具。在各种材料加工工
MOLDFLOW模流分析结果解释
MOLDFLOW模流分析结果解释 解释结果的一个重要部分是理解结果的定义,并知道怎样使用结果。下面将列出常用结果的定义及怎样使用它们的建议,越常用的结果将越先介绍。 屏幕输出文件(screen output)和结果概要(results summary) 屏幕输出文件和结果概要都包含了一些分析的关键结果的总结性信息。屏幕输出文件还包含如图169所示的附加输出,表明分析正在进行,同时还提供重要信息。从它可以看出分析使用的压力和锁模力的大小、流率的大小和使用的控制类型。
图169. 充模分析的屏幕输出文件 屏幕输出文件和结果概要都有与图170相似的部分。它同时包含了分析过程中(第一部分)和分析结束时的关键信息。使用这些信息可以快速查看这些变量,从而判断是否需要详细分析某一结果,以发现问题。
图170. 结果概要输出 充模时间(Fill Time) 充模时间显示的是熔体流动前沿的扩展情况,其默认绘制方式是阴影图,但使用云纹图可更容易解释结果。云纹线的间距应该相同,这表明熔体流动前沿的速度相等。制件的填充应该平衡。当制件平衡充模时,制件的各个远端在同一时刻充满。对大多数分析,充模时间是一个非常重要的关键结果。 压力(Pressures) 有几种不同的压力图,每种以不同的方式显示制件的压力分布。所有压力图显示的都是制件某个位置(一个节点)、或某一时刻的压力。 使用的最大压力应低于注射机的压力极限,很多注射机的压力极限为140 MPa (~20,000 psi)。模具的设计压力极限最好为100 MPa (~14,500 psi)左右。如果所用注塑机的压力极限高于140MPa,则设计极限可相应增大。模具的设计压力极限应大约为注射机极限的70%。假如分析没有包括浇注系统,设计压力极限应为注射机极限的50%。 象充模时间一样,压力分布也应该平衡。压力图和充模时间图看起来应该十分相似,如果相似,则充模时制件内就只有很少或没有潜流。 具体的压力结果定义如下: ?压力(Pressure) 压力是一个中间结果,每一个节点在分析时间内的每一时刻的压力值都记录了下来。默认的动画是时间动画,因此,你可以通过动画观察压力随时间变化的情况。压力分布应该平衡,或者在保压阶段应保证均匀的压力分布和几乎无过保压。 ?压力(充模结束时)(Pressure (end of filling)) 充模结束时的压力属于单组数据,该压力图是观察制件的压力分布是否平衡的有效工具。因为充模结束时的压力对平衡非常敏感,因此,如果此时的压力图分布平衡,则制件就很好地实现了平衡充模。 ?体积/压力控制转换时的压力(Pressure at V/P switchover ) 体积/压力控制转换时的压力属于单组数据,该压力图同样是观察制件的压力分布是否平衡的有效工具。通常,体积/压力控制转换时的压力在整个注塑成型周期中是最高的,此时压力的大小和分布可通过该压力图进行观察。同时,你也可以看到在控制转换时制件填充了多少,未填充部分以灰色表示。 ?注射位置压力:XY图(Pressure at injection location: XY Plot )
文件系统结构分析
文件系统结构分析 1嵌入式文件系统 1.1嵌入式文件系统体系结构 在嵌入式系统中,文件系统是嵌入式系统的一个组成模块,它是作为系统的一个 可加载选项提供给用户,由用户决定是否需要加载它。同时,它还需要满足结构紧 凑、代码量小、支持多种存储设备、可伸缩、可剪裁、可移植等特点。基于上面的要 求,嵌入式文件系统在设计和实现时就要把它作为一个独立的模块来整体考虑。特别 是对文件系统内部资源的管理要做到独立性。 由于嵌入式文件系统是作为嵌入式系统的一个可选加载项提供给用户的,当 用户针对其应用的特殊要求对嵌入式系统进行配置时没有选择加载文件系统,但 是用户还是需要使用到系统I/O。由于这种情况的出现就决定了嵌入式系统中的文件 系统不再具有I/O设备的管理功能。系统I/O的管理和使用接口的提供将由 I/O管理 模块完成,文件系统作为一个独立的自包含模块存在。 基于以上考虑,嵌入式文件系统的体系结构如图1所示。 1卩 硬件 图1嵌入式文件系统体系结构 在嵌入式文件系统的最上层是文件系统 API。文件系统的一切功能都是通过这一层提供给用户的。同时,在整个文件系统中也只有这一层对用户是可见的。 在这一层中所提供的所有功能接口都将严格的遵循 POSIX标准。 文件系统核心层是实现文件系统主要功能的模块。在这一层中,文件系统要把
用户的功能操作转化成对文件系统的抽象对象的操作。这些操作将通过下面的功能模块最终落实到物理介质上面。如果文件系统需要支持多种具体的文件系统格式的话,这一层还可以进一步细分成虚拟文件系统和逻辑文件系统。 块高速缓存的存在是为了提高文件系统的性能。在这一层中缓存着以前访问过的块设备数据。文件系统通过一定的算法来高效的管理这些数据,以提高缓冲的性能。同时,它的存在使下层的数据操作对上层的文件操作透明,提高了文件系统的模块性。 1.2 嵌入式文件系统体系的功能与特点 文件系统是操作系统的重要组成部分,用于控制对存储设备的存取。它提供对文件和目录的分层组织形式、数据缓冲(对于实时系统,允许绕过缓冲)以及对文件存取权限的控制。 嵌入式系统所使用的文件系统除了要提供通用文件系统的功能外,还由于嵌入式操作系统的特殊性而具有其自身的一些特点。嵌入式文件系统的设计应该满足如下目标: 1.实现按名存取。和桌面操作系统类似,用户对文件的操作是通过其“文件名”来完成的。因此,用户只需知道待操作文件的文件名,就可以方便的访问数据,而不必关心文件在物理设备上是如何存放的,以及如何对文件的打开、关闭操作进行处理等细节。所有与文件相关的管理工作都由文件系统组件隐式完成。 2.与实时系统相适应。嵌入式应用大多数都具有实时性需求。实时系统不仅 要求计算结果地准确无误,而且要求特定的指令要在限定的时间内完成,这就对文件系统提出了很高的要求。在通用操作系统中,往往采取分页和虚拟存储器管理的机制来满足规定的指令时间。然而嵌入式实时操作系统一般都不具有虚拟存储器管理机制,且各种外部设备的性能差异较大,控制文件系统的实时性变得非常困难。为了尽可能提高文件系统的实时性,除了选取高速存储介质作为嵌入式系统的外设外,还应该根据设备的特点设置一定大小的高速缓冲,以提高数据存取的相应速度。 3.支持多任务环境。面对日益复杂的计算环境,应用常常采取“分而治之” 的方法,将解决方案划分为多个任务,每个任务完成相对单一的功能。实时操作系统的设计目标之一就是对多任务的支持。从应用的层面上看,多任务可以对文件进行并发读操作,在实时内核进程间同步与通信机制支持下进行写操作。此外,文件系统内部实现也应该具备较好的可重入性,即利用同步机制对全局数据结构 进行必要的保护。 4.支持多种逻辑文件系统标准。随着操作系统技术的发展,出现了多种成熟的桌面文件系统标准,如 Windows下的FAT系列,Linux中的ext系列等。将这些成熟标
FAT32文件系统的存储组织结构
FAT32文件系统的存储组织结构(一) (2012-05-19 16:57) 标签: FAT32 文件系统分类:文件系统 对磁盘的物理结构,逻辑结构和存储结构有了比较深入的了解后,我们来仔细探讨FAT32文件系统的存储组织结构。说到文件系统的组织结构,我们应该马上意识到,这指的是文件系统在同一个分区内的组织结构,在这个话题上,我们完全可以不管分区之外的所有事情。 为了分析FAT32文件系统的存储组织结构,我们来建立一个实实在在的文件系统:将U盘插入电脑,将U盘格式化成FAT32分区格式: 以建好的U盘FAT32文件系统为基础,下面从文件系统的各个组成来分别加以介绍。 分区引导扇区DBR 用winhex打开U盘显示如下:
这是FAT32分区引导记录,定义如下: 偏移00H: 3字节的跳转指令 EB 58 90,跳过下面的BPB和扩展BPB部分 偏移03H:8字节的硬盘分区类型文本字符名:4D 53 44 4F 53 35 2E 30 即:MSDOS5.0 偏移0BH: 25字节的分区参数块(BPB),细分如下: 偏移0BH:扇区字节数 00 02 即0X0200,512字节 偏移0DH:每簇扇区数 08即每簇包括8个扇区
偏移0EH:保留扇区数 24 00即保留36个扇区 偏移10H:FAT表份数 02即两个FAT表 偏移11H:未用 00 00 偏移13H:未用 00 00 偏移15H:介质类型 F8即本地硬盘 偏移16H:未用 00 00 偏移18H:每磁道扇区数 3F 00 即每磁道63扇区 偏移1AH:磁头数 FF 00即255个磁头 偏移1CH:隐藏扇区数 80 1F即8064个隐藏扇区 偏移20H:磁盘总扇区数 80 F0 77 00即总共7860352个扇区 (7860352*512=4024500224,因为我的U盘是4G) 偏移24H:52字节的扩展分区参数块(扩展BPB),细分如下: 偏移24H:FAT表占用扇区数 EE 1D 00 00即FAT表占7662个扇区 偏移28H:未用 00 00 00 00 偏移2CH:根目录入口簇号 02 00 00 00即根目录从02号簇开始 偏移30H:文件系统信息扇区号 01 00即扇区1 偏移32H:备份引导扇区的位置 06 00即6号扇区(第7个扇区),从WINHEX中我们也可以看到,6号扇区的内容和0号引导扇区内容是一样的 偏移34H:未用 00 00 00 00 00 00 00 00 00 00 00 00 偏移40H:物理磁盘号 00 偏移41H:未用 00 偏移42H:扩展引导标志 29即0X29 偏移43H:磁盘序列号F1 2A 27 04通常为一随机数 偏移47H:卷标ASCII 4E 4F 20 4E 41 4D 45 20 20 20 20 即NO NAME
模具毕业设计3灯盖的注塑模设计
本科毕业设计题目:灯盖的注塑模设计 学院:工学院 姓名: 学号: 专业:机械设计制造及其自动化年级: 指导教师:职称:高级实验师 二0 一四年五月
目录 摘要 (1) Abstract (2) 1 绪论 (3) 1.1 模具和模具工业 (3) 1.2 塑料成型模具的分类 (3) 1.3塑料的基本组成与分类 (3) 2 塑件设计及分析 (4) 2.1 制品材料性能 (4) 2.1.1 ABS的成型特性与工艺参数 (4) 2.1.2 收缩率 (4) 2.2 制件分析 (5) 2.2.1 制品形状 (5) 2.2.2 尺寸精度 (6) 2.2.3 表面质量 (6) 3 注塑模结构 (7) 3.1注塑模具结构组成及典型结构 (7) 3.2 热塑性塑料注塑模的特点 (7) 4 注塑成型原理及工艺分析 (8) 4.1注塑成型原理 (8) 4.2 注塑成型工艺 (8) 4.3 注塑成型的工艺参数 (8) 5 注塑机的选择 (9) 5.1 注塑机简述 (9) 5.2 注塑机的类型 (9) 5.3 注塑机的组成 (9) 5.4 最大注塑量的确定 (9) 5.5注塑压力的确定 (10) 5.6 所需锁模力的确定 (10)
5.7 初选注塑机 (10) 6 成型零部件设计 (11) 6.1 成型零部件的结构设计 (11) 6.1.1 凹模和凸模的结构设计 (11) 6.2 成型零部件的材料选择 (11) 6.3 成型零部件钢材的热处理要求 (13) 6.4 型腔、型芯工作部位尺寸的确定 (14) 6.5成型零部件配合尺寸的公差要求 (15) 7 分型面的设计 (17) 7.1 塑料制件在模具中的位置 (17) 7.1.1型腔数目的确定 (17) 7.1.2塑件在模具中的位置 (17) 7.2 分型面的形式 (17) 7.3 分型面的设计原则 (17) 7.4 分型面的选择 (18) 8 浇注系统的设计 (19) 8.1 普通浇注系统的组成及设计原则 (20) 8.2 主流道设计 (20) 8.3 分流道设计 (20) 8.3.1 分流道的形状与尺寸 (20) 8.3.2分流道的长度 (20) 8.3.3分流道在分型面上的布置 (21) 8.4浇口的设计 (21) 8.4.1 浇口的形式及选择 (21) 8.4.2 浇口位置选择 (21) 8.5冷料穴和拉料杆的设计 (22) 9 推出结构的设计 (23) 9.1 合模导向机构的设计 (23) 9.2 推出机构的结构组成 (23) 9.3 推出零件尺寸的计算 (23) 9.4 推出机构的设计要求 (24) 9.5 推出力的计算 (24) 9.6 确定推出方式及推杆位置 (24) 9.7 复位杆的设计 (24) 10 冷却系统的设计 (25) 10.1 模温对制品质量和生产效率的影响 (25) 10.1.1 温度对制品质量的影响 (25)
注塑模流分析实施报告
. .. . . 华东交通大学 螺丝刀盒moldflow实训说明书 QZ 2015/11/30 课程:材料成型计算机仿真 学校:华东交通大学 学院:机电工程学院 专业:材料成型及控制工程 班级:2012模具2班 姓名:覃钊
学号: 指导老师:匡唐清
1、三维造型 利用UG8.0设计出模型如下图1.1、1.2表示 图1.1 实物图图1.2三维图 模型参数长宽高为143*85*19.5,主壁厚为1.5mm。二维图如图1.3 图1.3二维图 壁厚均匀,但在盖钩和挂处厚度和壁厚相差较大,体积收缩率在这两个地应该会出现一些问题。主分型面在上表面,侧面有卡勾及圆,需要做侧抽芯。材料选用普通PP材料。
模型建好之后导出为IGES格式。 2、模型修复与简化 打开CAD Doctor后导入IGES模型,检查并修复,直到所有错误都为0,修复 完成之后将模型导出,格式为udm格式。 3、moldflow模流分析 3.1网格划分 (1)新建工程,输入工程名称,导入模型,在导入窗口选择双层面。 (2)网格划分,网格变长取壁厚的3倍,为4.5mm,合并容差默认为0.1,启用弦高控制0.1mm,立即划分网格,划分之后打开网格统计,看到网格的基本情况,不存在自由边和多个连通区域的问题后进行下一步。一般来说初始划分的网格纵横比都比较大,所以要进行修复。纵横比诊断结果如图3.1.1:最大纵横比达到了45.57。 图3.1.1初次纵横比诊断 3.2网格诊断与修复 点击【网格】——【网格修复向导】,前进到选择目标纵横比,输入6,点击修复。之后在进行手动修复,通过合并节点移动节点等式进行,直到得到满意的结果。如下图3.2.1:
Linux文件系统相关数据结构及相互间的关系案例分析
文件系统相关数据结构及相互间的关系 一.详细关系: 1.进程要访问文件,就要首先与文件系统中要访问的文件建立连接,在进程数据结构task_struct中,有两个指针fs和files,一个指向fs_struct数据结构,是关于文件系统的信息;另一个指向files_struct数据结构,是关于已打开文件的信息。 2.fs_struct数据结构中有dentry结构指针,dentry结构中有inode结构指针。Dentry结构所代表的是逻辑意义上的文件,记录的是其逻辑上的属性,而inode 结构所代表的是物理意义上的文件,记录的是物理上的属性。它们之间的关系是多对一的关系。Inode结构中定义union数据结构用于大致反应Linux内核目前所支持的各种文件系统。 2.1.dentry结构中有一个d_inode指针指向相应的inode结构,dentry结构代表的是逻辑意义上的文件,描述文件的逻辑属性,因此目录项在磁盘上并没有对应的映像;而inode结构代表的是物理意义上的文件,记录其物理属性,对与一个具体的文件系统,inode结构在磁盘上有对应的映像。由此可见,一个索引节点对象可能对应多个目录项对象。一个有效的dentry结构必定对应一个inode 结构,这是因为一个目录项要么代表一个文件,要么代表一个目录,而目录实际上也是文件。所以只要dentry结构是有效的,则其指针d_inode必定指向一个inode结构。反之则不成立,因为一个inode可以对应多个dentry结构,即一个文件可以有不止一个文件名或路径名。因为一个已经建立的文件可以被链接到其他文件名。所以inode结构中有一个i_dentry,凡是代表着同一个文件的所有目录项都通过其dentry结构体中的d_alias域挂入相应的inode结构体中的
注塑模设计-毕业设计说明书
目录 目录 (1) 1. 绪论 (3) 1.1模具工业的概况 (3) 1.2 我国塑料模具现状及地区分布 (4) 1.3 塑料模具的发展趋势 (7) 1.4 注塑模具CAD发展概况及趋势 (8) 2.塑件分析 (10) 2.1 塑件的简介 (10) 2.2.注射工艺选择 (13) 2.3 计算塑件的体积和质量 计算塑件的体积和质量是为了选用注塑机,提高设备利用率,确定模具型腔数。经(Pro/E)计算塑件体积为: (14) 3. 注塑成型的准备 (15) 3.1 注塑成型工艺简介 (15) 3.2 注塑成型工艺条件 (16) 4. 拟定模具结构形式 (18) 4.1 确定型腔数量及排列方式 (18) 4.2 模具结构形式的确定 (18) 5. 注塑机选用 (19) 5.1 注塑机简介 (19) 5.2 注塑机基本参数 (19) 5.3注射机的选用原则 (20) 5.4选择注塑机 (20) 5.5 注射机及各个参数的校核 (21) 6.分型面的选择 (25) 6.1 分型面的设计原则 (25) 7.浇注系统设计 (26) 7.1浇注系统设计原则 (26) 7.2 主流道设计 (26) 7.3 分流道的设计 (28) 7.4浇口的设计 (30) 7.5浇注系统的平衡 (32) 7.6 冷料穴 (32) 7.7 拉料杆的设计 (32) 7.8 浇注系统凝料的脱出机构 (33) 7.9排气方式 (33) 8.成型零部件设计 (34) 8.1 凹模和凸模的结构设计 (34) 8.2 成型零部件的工作尺寸计算 (35) 8.3 成型零部件的工作尺寸计算 (38) 9.结构零部件的设计 (40) 9.1模架的确定和标准件的选用 (40)
注塑模流分析报告
华东交通大学 螺丝刀盒moldflow实训说明书 QZ 2015/11/30 课程:材料成型计算机仿真 学校:华东交通大学 学院:机电工程学院 专业:材料成型及控制工程 班级:2012模具2班 姓名:覃钊 学号:20120310040 指导老师:匡唐清
1、三维造型 利用UG8.0设计出模型如下图1.1、1.2表示 图1.1 实物图图1.2三维图 模型参数长宽高为143*85*19.5,主壁厚为1.5mm。二维图如图1.3 图1.3二维图 壁厚均匀,但在盖钩和挂孔处厚度和壁厚相差较大,体积收缩率在这两个地方应该会出现一些问题。主分型面在上表面,侧面有卡勾及圆孔,需要做侧抽芯。材料选用普通PP材料。 模型建好之后导出为IGES格式。
2、模型修复与简化 打开CAD Doctor后导入IGES模型,检查并修复,直到所有错误都为0,修复完 成之后将模型导出,格式为udm格式。 3、moldflow模流分析 3.1网格划分 (1)新建工程,输入工程名称,导入模型,在导入窗口选择双层面。 (2)网格划分,网格变长取壁厚的3倍,为4.5mm,合并容差默认为0.1,启用弦高控制0.1mm,立即划分网格,划分之后打开网格统计,看到网格的基本情况,不存在自由边和多个连通区域的问题后进行下一步。一般来说初始划分的网格纵横比都比较大,所以要进行修复。纵横比诊断结果如图3.1.1:最大纵横比达到了45.57。 图3.1.1初次纵横比诊断 3.2网格诊断与修复 点击【网格】——【网格修复向导】,前进到选择目标纵横比,输入6,点击修复。之后在进行手动修复,通过合并节点移动节点等方式进行,直到得到满意的结果。如下图
树形目录结构文件系统
操作系统课程设计 课程名称操作系统 题目名称树形目录结构文件系统学生学院 专业班级 学号 学生姓名 指导教师 2011 年1 月13 日
目录 一、课程设计目的 (3) 二、设计概要 (3) 三、详细设计 (3) 3.1数据结构设计 (4) 3.2程序功能模块图 (5) 3.2.1 文件管理系统主功能图示 (5) 3.2.2 用户界面管理图示 (5) 3.2.3 新建文件图示 (6) 3.2.4 复制、剪切文件图示 (6) 3.2.5 粘贴文件图示 (7) 3.2.6 删除文件图示 (7) 四、程序界面设计及运行结果分析 (8) 五、课程设计总结 (12) 六、参考文献 (12)
一、课程设计目的: 操作系统课程设计是配合操作系统课开设的专业基础必修课。本课程通过设计实现一个综合作业,培养学生程序设计的方法和技巧,提高学生编制清晰、合理、可读性好的系统程序的能力,加深对操作系统课程的理解。 二、设计概要: (1) 运行平台: Windows系列 (2) 设计平台: Microsoft Visual Studio 2008 (3) 存储系统:XML文件 (4) 运行需求: .NET Framework 2.0版本以上 (5) 软件简介: 文件管理系统 (6) 功能简介: A、提供用户登录注销功能 B、多用户管理,多级目录形式,文件可互相共享. C、智能化的树形和列表界面操作(包括图标、列表以及详细显示方 式,方便的菜单,右击菜单,工具栏等) D、模拟Windows多种实用功能 (7)本系统参照了windwos文件管理结构,实现了其大部分常用功能,采用多用户系统实现了文件夹与文件的创建,打开,读写,删除,关闭,剪切,复制,粘贴,重命名,刷新,查看,排列图标、属性设置、模糊搜索以及多用户文件共享功能。 三、详细设计: 3.1、数据结构设计: 本程序采用XML文件形式管理文件信息,XML文件适合小数据块的存储和传输,.NET为XML提供了丰富的类库,更加方便了操作使用,详细数据设计思路如下: XML文件编码声明: 首节点:
注塑模具毕业设计
(学校名称)毕业论文 题目:天线盖上盖模具设计 系别: 专业: 学号: 姓名: 指导老师: 2009年12月30日
前言 毕业设计是在修完所有课程之后,我们走向社会之前的一次综合性设计。在此次设计中,主要用到所学的注射模设计,以及机械设计等方面的知识。着重说明了一副注射模的一般流程,即注射成型的分析、注射机的选择及相关参数校核、模具的结构设计、注射模具设计的有关计算、模具总体尺寸的确定与结构草图的绘制、模具结构总装图和零件工作图的绘制、全面审核投产制造等。其中模具结构的设计既是重点又是难点,主要包括成型位置的及分型面的选择,模具型腔数的确定及型腔的排列和流道布局和浇口位置的选择,模具工作零件的结构设计,侧面分型及抽芯机构的设计,推出机构的设计,拉料杆的形式选择,排气方式设计等。通过本次毕业设计,使我更加了解模具设计的含义,以及懂得如何查阅相关资料和怎样解决在实际工作中遇到的实际问题,这为我们以后从事模具职业打下了良好的基础。 在这个过程中,我学到了许多书本上学不到的知识,将理论知识运用到实际中去,进一步理解了注射模的结构、设计以及生产。 在完成大学三年的课程学习,我熟练地掌握了机械制图、机械设计、机械原理等专业基础课和专业课方面的知识,对机械制造、加工的工艺有了一个系统、全面的理解,达到了学习的目的。对于模具设计这个实践性非常强的设计课题,我们进行了大量的实训。经过一个月的毕业设计实训,我对于模具特别是塑料模具的设计步骤有了一个全新的认识,丰富了各种模具的结构和动作过程方面的知识,而对于模具的制造工艺更是实现了零的突破。在指导老师的协助和讲解下,同时在图书馆借阅了许多相关手册和书籍,设计中,我将充分利用和查阅各种资料,并与同学进行充分讨论,尽最大努力搞好本次毕业设计。 在设计的过程中,将有一定的困难,但有指导老师的悉心指导和自己的努力,相信会完满的完成毕业设计任务。由于学生水平有限,而且缺乏经验,设计中不妥之处在所难免,肯请各位老师指正。
注塑模具设计毕业答辩内容
一、首先是开场白:班的学生,我的毕业论文题目是对讲机注3各位老师,上午好!我叫金函绪,是08级机制在这里我向我的导师表示深深论文是在李章东导师的悉心指点下完成的,塑模具毕业设计。并对四年来我有机会聆听向各位老师不辞辛苦参加我的论文答辩表示衷心的感谢,的谢意,下面我将本论文设计的目的和主要内容向各位老师作一汇教诲的各位老师表示由衷的敬意。报,恳请各位老师批评指导。二、内容首先,我想陈述这个毕业论文设计的目的及意义。熟悉拟定塑料成型工艺和模具设计原则、)设计对讲机注塑模具,是基于一下几个目的:(1锻炼自己对步骤和方法。增加对注塑模具的认识,对塑料模具制作过程有一个大概的了解。未曾接触过的事物的分析问题和解决问题的能力。其次,我想谈谈这篇论文的结构和主要内容。. 本文分成10个部分第一部分是前言。这部分主要阐明了我国注塑模具的现状以及未来的发展方向并确定脱模斜第二部分是塑件工艺分析。这部分主要进行了塑料结构和材料成型工艺分析,度和模具的结构形式,同时完成浇注系统的设计。塑件和流道凝料在分型面上的投影第三部分是注射机型号的确定。这部分需要进行注射量、面积及锁模力的计算,并校核注射剂的工艺参数,确定注射机的型号。第四部分是模架的确定。主要确定模架的型号以及各板的尺寸。第五部分是合模导向及定位机构的设计。包括了导柱、导套以及斜导柱侧抽芯机构的设计。脱模阻力的计第六部分是脱模机构的设计和计算。主要囊括了脱模机构的设计原则及分类,算和脱模机构的选用。第七部分内侧抽芯机构的设计。主要完成内抽芯距的计算。第八部分是模具温度调节系统的设计和计算。包括了冷却系统的设计及冷却装置的设计要点,计算冷却参数和冷却时间。第九部分模具零件的选材和制造工艺。主要包括了模具各零件的选材及制造工艺。第十部分是模具的装配和工作过程。主要包括模具装配的步骤和模具工作过程校验和修改。不足之处:不能根据实没有实践经验,本次设计的不足之处是我对模具设计过程中思考问题有些简单,以及对塑料模具知识的缺乏,使该设计中有不足之处,请各位老师批评指正。际情况来修改,老师提问:掌握了塑料模具成本论文的优缺点:对塑料模具在成型过程中有了更深一层的理解,(10)解决对独立设计模具具有一次新的锻炼,学会了分析问题、型的机构特点及设计计算办法,模具中斜顶杆不能准问题的方法。本设计的不足之处在于:大量生产后,由于顶针板变形,确复位,并对型腔造成损害,使塑件上有磨伤,且侧凹位置发生变化,无法满足装配要求。)写作毕业论文的体会(9对我在大学阶段所学习的模具设计方面的知识做了一个很好的总结通过本次毕业设计,也发现了自己在学科内的和巩固,也对平时所学习的比较零散的知识做到了系统化的运用。对模具的设计和加工有了通过本次设计,做到了很好的复习和理解。某些方面知识的欠缺,但在李章东老师的热心指导下,.一个比较系统全面的认识和了解,同时也遇到了很多问题,终于圆满完成了设计任务,在此对给予我帮助的老师们及同学们表示真挚的感谢。 8()还有那些问题自己还没有搞清楚,在论文中论述的不够透彻?对于斜导柱的侧抽芯机构不甚了解,对斜导柱和滑块、导槽的配合过程中的整个动作过程 不太明白。对斜导柱的在模架上的安装位置还不太明白。 (7)论文虽未论及,但与其较密切相关的问题还有那些? 我对塑料的基本情况进行了了解。首先是塑料的组成和特性,塑料由合成树脂和添加剂组成,添加剂包括填充剂、稳定剂、增塑剂、润滑剂、固化剂、着色剂。其次是塑料的特性,包括质量轻、电气绝缘性好,强度刚度高、化学稳定性好。热导率低,耐磨性能优良。最后是塑料的分类,按合成树脂受热的状态可以分为热塑性塑料和热固性塑料,按应用范围分为通用塑料、工程塑料、特种塑料。 (6)在研究本课题的过程中发现了那些不同的见解?对这些不同的见解,自己是怎么逐步认识的?又是如何处理的? 对分流道设计过程中,由于分流道的截面有圆形、梯形、U型、矩形等,为了减少分流道内的压力损失,希望分流道的截面面积要大,同时,为了减小散热,又希望分流到表面积要小,对选用
模流分析解析(详细) by heyy
AMI 分析详解 7.1.1 1.直浇口 直浇口直接由主流道进入型腔。 2.侧浇口 侧浇口是叫口中最简单又最常用的浇口。侧浇口的深度尺寸的微小变化可使塑料熔体的流量发生较大变化。 3 . 护耳式浇口 使用侧浇口对于某些开阔的型腔,可能会产生喷射呵蛇形流等现象。护耳式浇口可将喷射、气纹控制在护耳上,需要的话,可用后加工手段去除护耳,使制品外观保持良好,常应用于高透明度平板类制件。 4 . 环形浇口 根据制件的几何形状可以分为对称和不对称两种类型。当需要设置多个浇口时,对称形状的制件要遵循每个浇口流长相等和填充体积相等的原则;不对称形状的制件由于本身就不能达到自然平衡,所以每个浇口的填充体积和压力降都不尽相同。不对称形状的制件可能需要较多的浇口数目以获得平衡流动或者产生何莉莉的熔接线位置,同时降低注塑压力。 5 . 隔膜浇口 通常在环状制件的内径中设置浇口,该制件通常具有薄壁区域。 7.1.3 分析结果解释 1 . 浇口位置日志 浇口位置日志给出了分析的一些日志,其中一条主要信息是给出了最佳浇口位置的节点。 2 . 流动阻力指示器 表示熔体的流动前沿离不同浇口位置的流动阻力。流动阻力的值从0到1的变化,阻值越高表明熔体流动越困难。 3 . 浇口匹配性 表示浇口位置合理性的因子分布图,因子值越小,浇口位于这个位置的成型合理性越小。 7.2充填分析 (必须)1 . 充填时间 充填时间显示了熔体填充随时间的变化而变化情况。从充填时间可以看出产品的 填充是否平衡。产品的两个末端的充填时间为****和****,相差****,效果****。 (必须)2 . 速度\压力切换时的压力 V\P转换时刻压力属于单组数据,通常,V\P转换时刻压力在整个注塑周期中时最
2020年注塑模具毕业设计论文参照模板
光阴似梭,大学三年的学习一晃而过,为具体的检验这三年来的学习效果,综合检测理论在实际应用中的能力,除了平时的考试、实验测试外,更重要的是理论联系实际,即此次设计的课题为闹钟后盖的注塑模具。 本次毕业设计课题来源于生活,应用广泛,但成型难度大,模具结构较为复杂,对模具工作人员是一个很好的考验。它能加强对塑料模具成型原理的理解,同时锻炼对塑料成型模具的设计和制造能力。 本次设计以注射闹钟后盖模具为主线,综合了成型工艺分析,模具结构设计,最后到模具零件的加工方法,模具总的装配等一系列模具生产的所有过程。能很好的学习致用的效果。在设计该模具的同时总结了以往模具设计的一般方法、步骤,模具设计中常用的公式、数据、模具结构及零部件。把以前学过的基础课程融汇到综合应用本次设计当中来,所谓学以致用。在设计中除使用传统方法外,同时引用了CAD、Pro/E 等技术,使用Office软件,力求达到减小劳动强度,提高工作效率的目的。 本次设计中得到了戴老师的指点。同时也非常感谢邵阳学院各位老师的精心教诲。 由于实际经验和理论技术有限,设计的错误和不足之处在所难免,希望各位老师批评指正。
前言. (1) 绪论 (2) 1 塑料的工艺分析 (4) 1.1塑件成形工艺分析 (4) 1.2闹钟后盖原料(ABS)的成型特性与工艺参数 (4) 2 注塑设备的选择 (7) 2.1 估算塑件体积 (7) 2.2 选择注射机 (7) 2.3 模架的选定 (7) 2.4 最大注射压力的校核 (8) 3 塑料件的工艺尺寸的计算 (10) 3.1 型腔的径向尺寸 (10) 3.2 型芯的计算 (10) 3.3 模具型腔壁厚的计算 (11) 4 浇注系统的设计 (12) 4.1 主流道的设计 (12) 4.2 冷料井的设计 (13) 4.3 分流道的设计 (13) 4.4 浇口的选择 (14) 5 分型面的选择与排气系统的设计 (17) 5.1 分型面的选择 (17)
浇注系统
《注塑模具理论》 浇注系统 中国模具设计网w w w .z g m j s j .c o m https://www.360docs.net/doc/143754473.html, 中国模具设计网https://www.360docs.net/doc/143754473.html,
前言 浇注系统是注塑模具里面特别重要的部分,它的主要作用是把注塑机里面可流动的塑料 引入到模具的型腔里面.就相当于人吃饭时的食管,灌水用的渠道. 中国模具设计网w w w .z g m j s j .c o m https://www.360docs.net/doc/143754473.html, 中国模具设计网https://www.360docs.net/doc/143754473.html,
中国模具设计网w w w .z g m j s j .c o m https://www.360docs.net/doc/143754473.html, 中国模具设计网https://www.360docs.net/doc/143754473.html,
第一节 浇注系统的构成 一、大水口浇注系统的构成:整个浇注系统又可以称为“废料”。1、主流道: 2、分流道:1)主分流道 2)次分流道3、胶口:4、冷料井: 中 国模具设计网w w w .z g m j s j .c o m https://www.360docs.net/doc/143754473.html, 中国模具设计网https://www.360docs.net/doc/143754473.html,
二、大水口浇注系统各部分的详解: 1、主流道:它的作用是把注塑机里面可流动的塑料引入到模具里面,是可流动的塑料经过模具的第一段通道,它一般在唧嘴里面成形。 注意:唧嘴是标准件,则主流道的大小尺寸由唧嘴来决定,为了减少“废料”,可以缩短唧嘴的长度,则保证上图当中的“M”不小于10即可.设计时,就算唧嘴选取错误了,也不要紧,可以直接更换. 中国模具设计网w w w .z g m j s j .c o m https://www.360docs.net/doc/143754473.html, 中国模具设计网https://www.360docs.net/doc/143754473.html,