不锈钢的切削加工
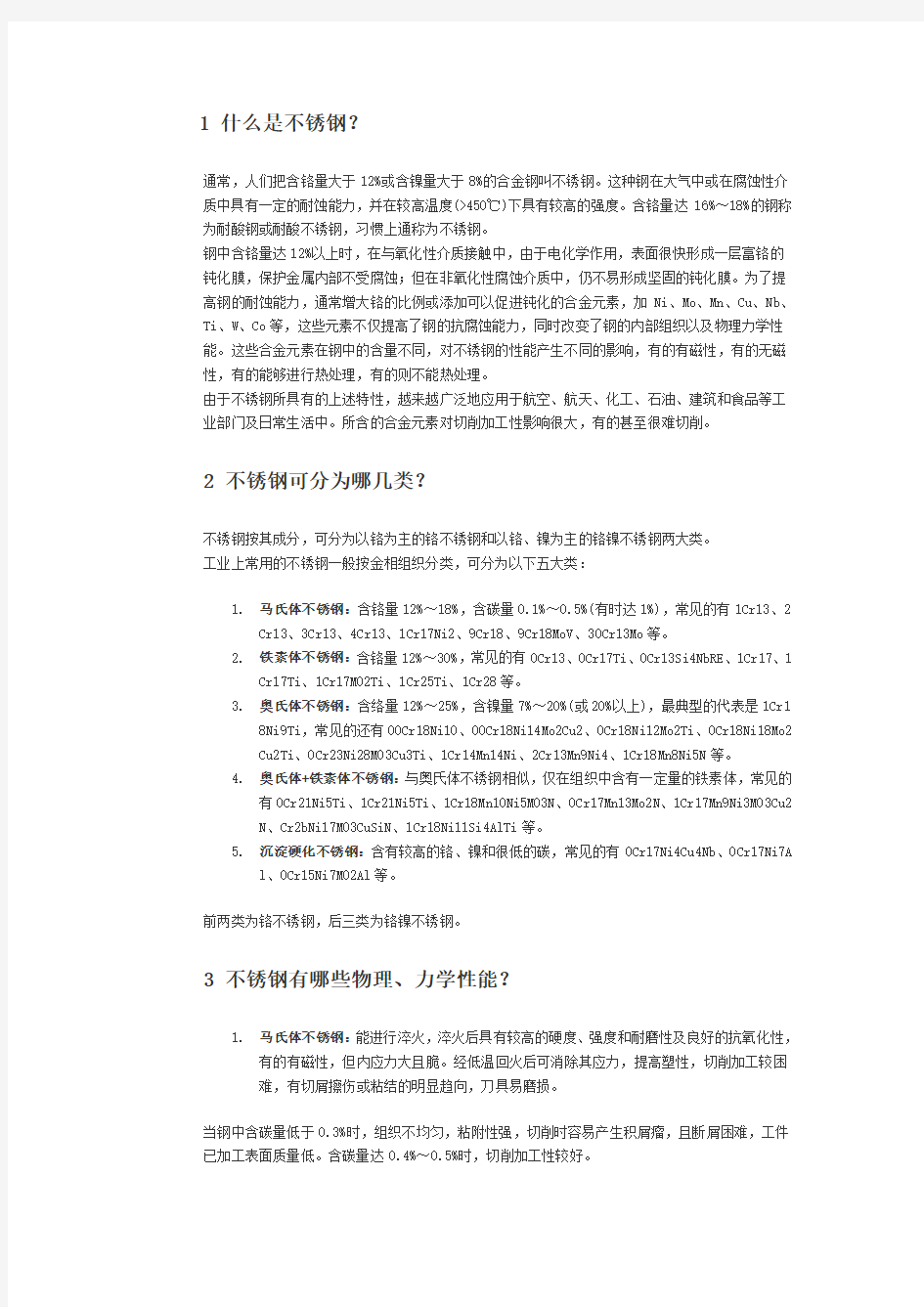

1 什么是不锈钢?
通常,人们把含铬量大于12%或含镍量大于8%的合金钢叫不锈钢。这种钢在大气中或在腐蚀性介质中具有一定的耐蚀能力,并在较高温度(>450℃)下具有较高的强度。含铬量达16%~18%的钢称为耐酸钢或耐酸不锈钢,习惯上通称为不锈钢。
钢中含铬量达12%以上时,在与氧化性介质接触中,由于电化学作用,表面很快形成一层富铬的钝化膜,保护金属内部不受腐蚀;但在非氧化性腐蚀介质中,仍不易形成坚固的钝化膜。为了提高钢的耐蚀能力,通常增大铬的比例或添加可以促进钝化的合金元素,加Ni、Mo、Mn、Cu、Nb、Ti、W、Co等,这些元素不仅提高了钢的抗腐蚀能力,同时改变了钢的内部组织以及物理力学性能。这些合金元素在钢中的含量不同,对不锈钢的性能产生不同的影响,有的有磁性,有的无磁性,有的能够进行热处理,有的则不能热处理。
由于不锈钢所具有的上述特性,越来越广泛地应用于航空、航天、化工、石油、建筑和食品等工业部门及日常生活中。所含的合金元素对切削加工性影响很大,有的甚至很难切削。
2 不锈钢可分为哪几类?
不锈钢按其成分,可分为以铬为主的铬不锈钢和以铬、镍为主的铬镍不锈钢两大类。
工业上常用的不锈钢一般按金相组织分类,可分为以下五大类:
1.马氏体不锈钢:含铬量12%~18%,含碳量0.1%~0.5%(有时达1%),常见的有1Cr13、2
Cr13、3Cr13、4Cr13、1Cr17Ni2、9Cr18、9Cr18MoV、30Cr13Mo等。
2.铁素体不锈钢:含铬量12%~30%,常见的有0Cr13、0Cr17Ti、0Cr13Si4NbRE、1Cr17、1
Cr17Ti、1Cr17M02Ti、1Cr25Ti、1Cr28等。
3.奥氏体不锈钢:含络量12%~25%,含镍量7%~20%(或20%以上),最典型的代表是1Cr1
8Ni9Ti,常见的还有00Cr18Ni10、00Cr18Ni14Mo2Cu2、0Cr18Ni12Mo2Ti、0Cr18Ni18Mo2
Cu2Ti、0Cr23Ni28M03Cu3Ti、1Cr14Mn14Ni、2Cr13Mn9Ni4、1Cr18Mn8Ni5N等。
4.奥氏体+铁素体不锈钢:与奥氏体不锈钢相似,仅在组织中含有一定量的铁素体,常见的
有0Cr21Ni5Ti、1Cr21Ni5Ti、1Cr18Mn10Ni5M03N、0Cr17Mn13Mo2N、1Cr17Mn9Ni3M03Cu2
N、Cr2bNi17M03CuSiN、1Cr18Ni11Si4AlTi等。
5.沉淀硬化不锈钢:含有较高的铬、镍和很低的碳,常见的有0Cr17Ni4Cu4Nb、0Cr17Ni7A
l、0Cr15Ni7M02Al等。
前两类为铬不锈钢,后三类为铬镍不锈钢。
3 不锈钢有哪些物理、力学性能?
1.马氏体不锈钢:能进行淬火,淬火后具有较高的硬度、强度和耐磨性及良好的抗氧化性,
有的有磁性,但内应力大且脆。经低温回火后可消除其应力,提高塑性,切削加工较困
难,有切屑擦伤或粘结的明显趋向,刀具易磨损。
当钢中含碳量低于0.3%时,组织不均匀,粘附性强,切削时容易产生积屑瘤,且断屑困难,工件已加工表面质量低。含碳量达0.4%~0.5%时,切削加工性较好。
马氏体不锈钢经调质处理后,可获得优良的综合力学性能,其切削加工性比退火状态有很大改善。
2.铁素体不锈钢:加热冷却时组织稳定,不发生相变,故热处理不能使其强化,只能靠变形强化,
性能较脆,切削加工性一般较好。切屑呈带状,切屑容易擦伤或粘结于切削刃上,从而增大切削力,切削温度升高,同时可能使工件表面产生撕裂现象。
3.奥氏体不锈钢:由于含有较多的镍(或锰),加热时组织不变,故淬火不能使其强化,可略改善其
加工性。通过冷加工硬化可大幅度提高强度,如果再经时效处理,抗拉强度可达2550~2740 MPa。
奥氏体不锈钢切削时的带状切屑连绵不断,断屑困难,极易产生加工硬化,硬化层给下一次切削
带来很大难度,使刀具急剧磨损,刀具耐用度大幅度下降。
奥氏体不锈钢具有优良的力学性能,良好的耐蚀能力,较突出的是冷变形能力,无磁性。
4.奥氏体+铁素体不锈钢:有硬度极高的金属间化合物析出,强度比奥氏体不锈钢高,其切削加工性
更差。
5.沉淀硬化不锈钢:含有能起沉淀硬化的铊、铝、钼、钛等合金元素,它们在回火时时效析出,产
生沉淀硬化,使钢具有很高的强度和硬度。由于含碳量低保证了足够的含铬量,因此具有良好的耐腐蚀性能。
4 不锈钢有哪些切削特点?
不锈钢的切削加工性比中碳钢差得多。以普通45号钢的切削加工性作为100%,奥氏体不锈钢1C
r18Ni9Ti的相对切削加工性为40%;铁素体不锈钢1Cr28为48%;马氏体不锈钢2Cr13为55%。其
中,以奥氏体和奥氏体+铁素体不锈钢的切削加工性最差。不锈钢在切削过程中有如下几方面特点:
1.加工硬化严重:在不锈钢中,以奥氏体和奥氏体+铁素体不锈钢的加工硬化现象最为突出。
如奥氏体不锈钢硬化后的强度σb达1470~1960MPa,而且随σb的提高,屈服极限σs升高;
退火状态的奥氏体不锈钢σs不超过的σb30%~45%,而加工硬化后达85%~95%。加工硬
化层的深度可达切削深度的1/3或更大;硬化层的硬度比原来的提高1.4~2.2倍。因为
不锈钢的塑性大,塑性变形时品格歪扭,强化系数很大;且奥氏体不够稳定,在切削应
力的作用下,部分奥氏体会转变为马氏体;再加上化合物杂质在切削热的作用下,易于
分解呈弥散分布,使切削加工时产生硬化层。前一次进给或前一道工序所产生的加工硬
化现象严重影响后续工序的顺利进行。
2.切削力大:不锈钢在切削过程中塑性变形大,尤其是奥氏体不锈钢(其伸长率超过45号
钢的1.5倍以上),使切削力增加。同时,不锈钢的加工硬化严重,热强度高,进一步增
大了切削抗力,切屑的卷曲折断也比较困难。因此加工不锈钢的切削力大,如车削1Cr1
8Ni9Ti的单位切削力为2450MPa,比45号钢高25%。
3.切削温度高:切削时塑性变形及与刀具间的摩擦都很大,产生的切削热多;加上不锈钢
的导热系数约为45号钢的?~?,大量切削热都集中在切削区和刀—屑接触的界面上,散
热条件差。在相同的条件下,1Cr18Ni9Ti的切削温度比45号钢高200℃左右。
4.切屑不易折断、易粘结:不锈钢的塑性、韧性都很大,车加工时切屑连绵不断,不仅影
响操作的顺利进行,切屑还会挤伤已加工表面。在高温、高压下,不锈钢与其他金属的
亲和性强,易产生粘附现象,并形成积屑瘤,既加剧刀具磨损,又会出现撕扯现象而使
已加工表面恶化。含碳量较低的马氏体不锈钢的这一特点更为明显。
5.刀具易磨损:切削不锈钢过程中的亲和作用,使刀—屑间产生粘结、扩散,从而使刀具
产生粘结磨损、扩散磨损,致使刀具前刀面产生月牙洼,切削刃还会形成微小的剥落和
缺口;加上不锈钢中的碳化物(如TiC)微粒硬度很高,切削时直接与刀具接触、摩擦,
擦伤刀具,还有加工硬化现象,均会使刀具磨损加剧。
6.线膨胀系数大:不锈钢的线膨胀系数约为碳素钢的1.5倍,在切削温度作用下,工件容
易产生热变形,尺寸精度较难控制。
5 切削不锈钢时怎样选择刀具材料?
合理选择刀具材料是保证高效率切削加工不锈钢的重要条件。根据不锈钢的切削特点,要求刀具
材料应具有耐热性好、耐磨性高、与不锈钢的亲和作用小等特点。目前常用的刀具材料有高速钢
和硬质合金。
1.高速钢的选择:高速钢主要用来制造铣刀、钻头、丝锥、拉刀等复杂多刃刀具。普通高
速钢W18Cr4V使用时刀具耐用度很低已不符合需要,采用新型高速钢刀具切削不锈钢可
获得较好的效果。
在相同的车削条件下,用W18Cr4V和95w18Cr4V两种材料的刀具加工1Cr17Ni2工件,刀具刃磨一
次加工的件数分别为2~3件和12件,用95w18Cr4V的刀具耐用度提高了几倍。这是由于提高了
钢的含碳量,从而增加了钢中碳化物含量,常温硬度提高2HRC红硬性更好,600℃时由W18Cr4V
的HRC48.5上升到HRC51~52,耐磨性比W18Cr4V提高2~3倍。
应用高钒高速钢W12Cr4V4Mo制作型面铣刀加工1Cr17Ni2可以获得较高的刀具耐用度。因为含钒
量增加,可在钢中形成硬度很高的VC,细小的VC存在于晶介,可以阻止晶粒长大,提高钢的耐
磨性;W12Cr4V4Mo的红硬性很好,600℃时硬度可达HRC51.7,因此适合于制作切削不锈钢的各种
复杂刀具。但其强度(σb=3140 MPa)及冲击韧性(a k=2.5 J/cm3)略低于W18Cr4V,使用时要稍加注意。
随着刀具制作技术的不断发展,对于批量大的工件,采用硬质合金多刃、复杂刀具进行切削加工
效果会更好。
2.硬质合金的选择:YG类硬质合金的韧性较好,可采用较大的前角,刀刃也可以磨得锋利些,使切
削轻快,且切屑与刀具不易产生粘结,较适于加工不锈钢。特别是在振动的粗车和断续切削时,YG类合金的这一优点更为重要。另外,YG类合金的导热性较好,其导热系数比高速钢高将近两倍,比YT类合金高一倍。因此YG类合金在不锈钢切削中应用较多,特别是在粗车刀、切断刀、扩孔钻及铰刀等制造中应用更为广泛。
较长时期以来,一般都采用YG6、YG8、YG8N、YW1、YW2等普通牌号的硬质合金作为切削不锈钢的
刀具材料,但均不能获得较理想的效果;采用新牌号硬质合金如813、758、767、640、712、798、
YM051、YM052、YM10、YS2T、YD15等,切削不锈钢可获得较好的效果。而用813牌号硬质合金刀
具切削奥氏体不锈钢效果很好,因为813合金既具有较高的硬度(≥HRA91)、强度(σb=1570MPa),
又具有良好的高温韧性、抗氧化性、抗粘结性,其组织致密耐磨性好。
6 切削不锈钢时怎样选择刀具几何参数?
1.前角γ0:不锈钢的硬度、强度并不高,但其塑性、韧性都较好,热强性高,切削时切屑不易被切
离。在保证刀具有足够强度的前提下,应选用较大的前角,这样不仅能够减小被切削金属的塑性变形,而且可以降低切削力和切削温度,同时使硬化层深度减小。
车削各种不锈钢的前角大致为12°~30°。对马氏体不锈钢(如2Cr13),前角可取较大值;对奥氏体和奥氏体+铁素体不锈钢,前角应取较小值;对未经调质处理或调质后硬度较低的不锈钢,可取较大前角;直径较小或薄壁工件,宜采用较大的前角。
高速钢铣刀取γn=10°~20°,硬质合金铣刀取γn=5°~10°;铰刀一般取γ0=8°~12°;丝锥一般取γ0=15°~20°(机用)或γ0=20°(手用)。
2.后角α0:加大后角能减小后刀面与加工表面的摩擦,但会使切削刃的强度和散热能力降低。后角
的合理值取决于切削厚度,切削厚度小时,宜选较大后角。
不锈钢车刀或镗刀通常取α0=10°~20°(精加工)或α0=6°~10°(粗加工);高速钢端铣刀取α0=1 0°~20°,立铣刀取α0=15°~20°;硬度合金端铣刀取α0=5°~10°,立铣刀取α0=12°~16°;
铰刀和丝锥取α0=8°~12°。
3.主偏角κr、副偏角κ′r,和rε:减小主偏角可
增加刀刃工作长度,有利于散热,但在切削
过程中使径向力加大,容易产生振动,常取κ
r=45°~75°,若机床刚性不足,可适当加
大。副偏角常取κ′r=8°~15°。为了加强
刀尖,一般应磨出ε=0.5~1.0 mm的刀尖圆
弧。
4.刃倾角λs:为了增加刀尖强度,刃倾角一般
取λs=-8°~-3°,断续切削时取较大值λs=-
15°~-5°。
生产实践中,为了加大切屑变形,提高刀尖
图1 双刃倾角断屑车刀强度与散热能力,采用双刃倾角车刀,取得
了良好的断屑效果,也加宽了断屑范围,如图1所示。第一刃倾角λs1≥0°,第二刃倾角在接近刀尖部位,λs2≈-20°,第二刃倾角的刀刃长度lλs2。≈a p/3。
当双刃倾角车刀的γ0=20°、α0=6°~8°、κr=90°或75°、倒棱前角γ01=-10°、rε=0.15~0.2 mm 时,在V c=80~100 m/min、f=0.2~0.3 mm/r、a p=4~15 mm的条件下切削,断屑效果良好,刀具耐用度高。
要求刀具前后刀面的表面粗糙度值小,刀具磨钝标锥VB为加工一般材料的1/2
7 切削不锈钢时怎样选择刀具断(卷)屑槽和刃口形式?
切削不锈钢时还应选择合适的刀具断(卷)屑槽,以便控制连绵不断的切屑,通常采用全圆弧形或
直线圆弧形断(卷)屑槽。断(卷)屑槽的宽度Bn=3~5 mm,槽深h=0.5~1.3 mm,Rn=2~8 mm 。一
般情况下,粗车时a p、f大,断(卷)屑槽宜宽而浅;精车时a p、f小,应窄而深些。断(卷)屑槽的形式见图2。
切削加工过程中,如果发生切屑缠绕在工件或刀具上的现象,表示断(卷)屑槽过宽过浅,可加大进给量,使切屑折断;如果切屑挤轧在槽内,发出吱吱叫声,或切屑飞溅伤人,表示断(卷)屑槽太窄太深,这时可减小进给量。同时还要注意控制断(卷)屑槽的位置。断(卷)屑槽的尺寸见表3、表4和表5。
8 切削不锈钢时怎样选择切削用量?
切削用量对加工不锈钢时的加工硬化、切削力、切削热等有很大影响,特别是对刀具耐用度的影响较大。选择的切削用量合理与否,将直接影响切削效果。
1.切削速度V c:加工不锈钢
时切削速度稍微提高一
点,切削温度就会高出许
多,刀具磨损加剧,耐用
度则大幅度下降。
为了保证合理的刀具耐用度,就要降低切削速度,一般按车削普通碳钢的40%~60%选取。镗孔和
切断时,由于刀具刚性、散热条件、冷却润滑效果及排屑情况都比车外圆差,切削速度还要适当
降低。
不同种类的不锈钢的切削加工性各不相同,切削速度也需相应调整。一般1Cr18Ni9Ti等奥氏体不
锈钢的切削速度校正系数Kv为1.0,硬度在HRC28以下的2cr13等马氏体不锈钢的Kv为1.3~1.
5,硬度为HRC28~35的2Cr13等马氏体不锈钢的Kv为0.9~1.1,硬度在HRC35以上的2Cr13等
马氏体不锈钢的Kv为0.7~0.8,耐浓硝酸不锈钢的Kv为0.6~0.7。
2.切削深度a p:粗加工时余量较大,应选用较大的切深,可减少走刀次数,同时可避免刀尖与毛坯
表皮接触,减轻刀具磨损。但加大切深应注意不要因切削力过大而引起振动,可选a p=2~5 mm。精加工时可选较小的切削深度,还要避开硬化层,一般采用a p=0.2~0.5 mm。
3.进给量f:进给量的增大不仅受到机床动力的限制,而且切削残留高度和积屑瘤高度都随进给量
的增加而加大,因此进给量不能过大。为提高加工表面质量,精加工时应采用较小的进给量。同时,应注意f不得小于0.1 mm/r,避免微量进给,以免在加工硬化区进行切削,并且应注意切削刃不要在切削表面停留。
9 切削不锈钢时怎样选择切削液和冷却方式?
由于不锈钢的切削加工性较差,对切削液的冷却、润滑、渗透及清洗性能有更高的要求,常用的
切削液有以下几类:
1.硫化油:是以硫为极压添加剂的切削油。切削过程中能在金属表面形成高熔点硫化物,
而且在高温下不易破坏,具有良好的润滑作用,并有一定的冷却效果,适用于一般车削、
钻孔、铰孔及攻丝。硫化豆油适用于钻、扩、铰孔等工序。
直接硫化油的配方是:矿物油98%,硫2%。
间接硫化油的配方是:矿物油78%~80%,植物油或猪油18%~20%,硫1.7%。
2.机油、锭子油等矿物油:其润滑性能较好,但冷却和渗透性较差,适用于外圆精车。
3.植物油:如菜油、豆油等,其润滑性能较好,适用于车螺纹及铰孔、攻丝等工序。
4.乳化液:具有较好的冷却和清洗性能。也有一定的润滑作用,可用于不锈钢粗车。
在切削加工过程中应使切削液喷嘴对准切削区,或最好采用高压冷却、喷雾冷却等冷却方式。
10 怎样对不锈钢进行铣削加工?
铣削不锈钢的特点是:不锈钢的粘附性及熔着性强,切屑容易粘附在铣刀刀齿上,使切削条件恶化;逆铣时,刀齿先在已经硬化的表面上滑行,增加了加工硬化的趋势;铣削时冲击、振动较大,使铣刀刀齿易崩刃和磨损。
铣削不锈钢除端铣刀和部分立铣刀可用硬质合金作铣刀刀齿材料外,其余各类铣刀均采用高速钢,特别是钨—钼系和高钒高速钢具有良好的效果,其刀具耐用度可比W18Cr4V提高1~2倍。适宜制作不锈钢铣刀的硬质合金牌号有YG8、YW2、813、798、YS2T、YS30、YS25等。
铣削不锈钢时,切削刃既要锋利又要能承受冲击,容屑槽要大。可采用大螺旋角铣刀(圆柱铣刀、立铣刀),螺旋角β从20°增加到45°(γn=5°),刀具耐用度可提高2倍以上,因为此时铣刀的工作前角γ0e由11°增加到27°以上,铣削轻快。但β值不宜再大,特别是立铣刀以β≤35°为宜,以免削弱刀齿。
采用波形刃立铣刀加工不锈钢管材或薄壁件,切削轻快,振动小,切屑易碎,工件不变形。用硬质合金立铣刀高速铣削、可转位端铣刀铣削不锈钢都能取得良好的效果。
用银白屑(SWC)端铣刀铣削1Cr18Ni9Ti,其几何参数为γf=5°、γp=15°、αf=15°、αp=5°、κr=55°、κ′r=35°、γ01=-30°、bγ=0.4mm、rε=6mm,当V c=50~90 m/min、V f=630~750mm/min、a′p=2~6m m并且每齿进给量达0.4~0.8mm时,铣削力减小10%~15%,铣削功率下降44%,效率也大大提高。其原理是在主切削刃上磨出负倒棱,铣削时人为地产生积屑瘤,使其代替切削刃进行切削,积屑瘤的前角γb可达20~~302,由于主偏角的作用,积屑瘤受到一个前刀面上产生的平行于切削刃的推力作用而成为副屑流出,从而带走了切削热,降低了切削温度。
铣削不锈钢时,应尽可能采用顺铣法加工。不对称顺铣法能保证切削刃平稳地从金属中切离,切屑粘结接触面积较小,在高速离心力的作用下易被甩掉,以免刀齿重新切入工件时,切屑冲击前刀面产生剥落和崩刃现象,提高刀具的耐用度。
采用喷雾冷却法效果最为显著,可提高铣刀耐用度一倍以上;如用一般10%乳化液冷却,应保证切削液流量达到充分冷却。硬质合金铣刀铣削不锈钢时,取V c=70~150 m/min,V f=37.5~150 mm /min,同时应根据合金牌号及工件材料的不同作适当调整。
11 怎样对不锈钢进行钻孔?钻孔时应注意哪些问题?
在不锈钢工件上钻孔常采用麻花钻,对淬硬不锈钢,可用硬质合金钻头,有条件时可用超硬高速钢或超细晶粒硬质合金钻头。钻孔时扭矩和轴向力大,切屑易粘结、不易折断且排屑困难,加工硬化加剧,钻头转角处易磨损,钻头刚性差易产生振动。因此要求钻头磨出分屑槽,修磨横刃以减小轴向力,修磨成双顶角以改善散热条件。
钻削不锈钢的典型钻头(即不锈钢群钻)如图4所示。
图5 不锈钢断屑钻头
图4 不锈钢群钻
图
3
中
L
≈
.
3
2
d
0,
L
/
2
>
L
1
>
L
/
3
,
R
≈
.
2d 0,h=0.04d 0,b≈0.04d 0。使用这种钻头钻削1Cr18Ni9Ti 时,对?20 mm、?25 mm、呾 mm 三种
直径的钻头,采用n=105 r/min ,f=0.32 mm/r 、0.4 mm/r 、0.56 mm/r 、0.67 mm/r 四种不同的进
给量,均可顺利地断屑和排屑。
还可采用不锈钢断屑钻头(图5)、S 形硬质合金钻头(图6)、四刃带钻头(图7)及可转位硬质合金
浅孔钻。
用不锈钢断屑钻头(图5)加工马氏体不锈钢2Crl3时,只需磨出E-E 处断屑槽;而钻削加工lCrl
8Ni9Ti 奥氏体不锈钢时,还需加开A-A 处断屑槽。
S 形硬质合金钻头的特点是:无横刃,可减小轴向力50%;钻心处前角为正值,刃口锋利;钻心厚
度增大,提高了钻头刚性;有两个喷切削液孔;圆弧形切削刃及排屑槽分布合理,便于切屑成小
块,以利排出。
可转位硬质合金浅孔钻的特点是:钻头前端不对称装有两片凸三角形刀片,分屑切除孔的不同部
分,能自动定心,孔的直线性好,并且切入切出长度短;刀片前刀面上带有多个坑状断屑槽,切
削性能良好,尤其是断屑可靠,切屑呈一致的碎卷屑;内冷却使切削液直接喷向钻削加工表面,
改善冷却效果,排屑非常通畅;特别是可根据工件材料采用不同牌号的硬质合金刀片,切削速度
达80~120m/min ,钻削非常轻快。
钻削不锈钢时,经常发现钻头容易磨损、折断,孔表面粗糙,有时出现深沟而无法消除;孔径过
大,孔形不圆或向一边倾斜等现象。在操作时应注意下列事项: 图6 S 形硬质合金钻头
图7 四刃带钻头
1.几何形状必须刃磨正确,两切削刃要保持对称。钻头后角过大,会产生“扎刀”现象,
引起颤振,使钻出的孔呈多角形。应修磨横刃,以减小钻孔轴向力。
2.钻头必须装正,保持钻头锋利,用钝后应及时修磨。
用量,按钻孔深度要求,应尽量缩短钻头长度、加大钻心厚度以增加刚性。使用高速钢
钻头时,切削速度不可过高,以防烧坏刀刃。进给量不宜过大,以防钻头磨损加剧或使
孔钻偏,在切入和切出时进给量应适当调小。
3.充分冷却润滑,切削液一般以硫化油为宜,流量不得少于5~8 L/min,不可中途停止冷
却,在直径较大时,应尽可能采用内冷却方式。
4.认真注意钻削过程,应及时观察切屑排出状况,若发现切屑杂乱卷绕立即退刀检查,以
防止切屑堵塞。还应注意机床运转声音,发现异常应及时退刀,不能让钻头在钻削表面
上停留,以防钻削表面硬化加剧。
12 怎样解决耐酸不锈钢钻孔时的断屑问题?
耐酸不锈钢的塑性和韧性都很大,钻孔时存在的主要问题是不容易断屑,影响切削液的流入,切削区温度高,刀具耐用度低,生产率低。在钻孔时,切削负荷大,形成切屑要消耗很多的能量,再加上这类不锈钢的高温强度和硬度高,钻屑在切离时不易折断;同时冷作硬化现象非常严重,表面硬化程度可达100%以上,硬化层厚度达0.1~0.2mm。耐酸不锈钢的导热系数小,只有碳钢的1/3~1/4,切削区温度很高,与其他金属的亲和作用强以及材料中存在的硬质点,加剧了刀具的磨损。
为了解决耐酸不锈钢钻孔时的断屑问题,研制了新型钻耐酸不锈钢断屑群钻,用它钻孔时切屑长100mm左右呈“礼花”状从孔中排出,断屑效果十分理想。
在钻孔过程中要出这种切屑的关键是:一要使分屑点处于临界分屑状态;二要适当磨出钻尖高(h =0.05D~0.07D)和圆弧半径(R=0.2D);三是L1=1.7~3.3 mm位置应选择恰当,并配合适当大的进给量和较低的切削速度,使切屑在斜拧状态中折断。
使用耐酸不锈钢断屑群钻钻孔时,应选用较低的切削速度和较大的进给量,有利于实现断屑。
13 怎样对不锈钢进行铰孔?
对不锈钢铰孔时,经常遇到的问题是:孔表面容易划出沟槽,粗糙度差,孔径超差,呈喇叭口,铰刀易磨损等。不同种类不锈钢的切削加工性不同,在铰孔中所表现出的问题也不一样,如对1C r18Ni9Ti等奥氏体不锈钢和耐浓硝酸不锈钢铰孔时,主要是铰刀磨损问题;而对2Cr13等马氏体不锈钢铰孔时,主要是不容易保证铰孔的粗糙度和尺寸精度问题。为了避免这些问题,应注意以下事项:
1.合理选择铰刀和铰削用量,是保证铰孔顺利进行的关键。
2.(2)提高预加工工序质量,防止预加工孔出现划沟、椭圆、多边形、锥度或喇叭口、腰鼓
形状、轴心线弯曲、偏斜等现象。
3.保持工件材质硬度适中,尤其对2Cr13马氏体不锈钢,调质处理后的硬度在HRC28以下
为宜。
4.正确安装铰刀和工件,铰刀必须装正,铰刀轴线应和工件预加工孔的轴线保持一致,以
保证各刀齿均匀切削。
5.选用合适的切削液,可以解决不锈钢的切屑粘附问题,并使之顺利排屑,从而降低孔表
面粗糙度和提高刀具耐用度。一般以使用硫化油为宜,若在硫化油中添加10%~20%CCl4
或在猪油中添加20%~30%CCl4,对降低表面粗糙度有显著的效果。由于CCl4对人体有
害,宜采用硫化油85%~90%和煤油10%~15%的混合液。铰刀直径较大时,可采用内冷却
方式。
6.认真注意铰孔的过程,严格检查刀齿的跳动量,是获得均匀铰削的关键。在铰削过程中,
注意切屑的形状,由于铰削余量小,切屑呈箔卷状或呈很短的螺卷状。若切屑大小不一,有的呈碎末状、有的呈小块状,说明铰削不均匀。若切屑呈条的弹簧状,说明铰削余量
太大。若切屑呈针状、碎片状,说明铰刀已经磨钝。还要防止切屑堵塞,应勤于观察刀
齿有无粘屑,以避免孔径超差。使用硬质合金铰刀铰孔时,会出现孔收缩现象,为防止
退刀时将孔拉毛,可采取加大主偏角来改善这种情况。
14 怎样对不锈钢进行攻丝?
在不锈钢上攻丝比在普遍钢材上攻丝要困难得多。经常出现由于扭矩大,丝锥被“咬死”在螺孔中,崩齿或折断,螺纹表面不光,沟纹,尺寸超差,乱扣和丝锥磨损严重等现象。因此,攻制不锈钢螺纹时应采取相应的技术措施加以解决。
1.攻制不锈钢螺纹时,“胀牙”现象比较严重,丝锥容易“咬死”在孔中,所以螺纹底孔
应适当加大。一般情况下,螺距为1mm以下的螺纹底孔直径等于公称直径减去螺距;螺
距大于1mm时,螺纹底孔直径等于公称直径减去1.1倍螺距。
2.选择合适
的丝锥和
合理的切
削用量,是
关系到攻
丝质量的
关键。丝锥
材料,应选
含钴或铝
图10 加工不锈钢用的无槽丝锥超硬高速
钢;主偏角和螺距、丝锥把数有关,头锥κr=5°~7°,二锥、三锥为κr=10°~20°;校
准部分一般取3~4扣螺纹长度,并有0.05~0.1mm/100 mm的倒锥;容屑槽方向一般取β
=8°~15°,可以控制切屑流动方向,对于直槽丝锥,可以将丝锥前端改磨成螺旋形;
丝锥的前角一般为γp=15°~20°,后角为8°~12°。
3.可采用无槽丝锥对不锈钢攻丝,见图10。使用无槽丝锥挤丝前的底孔直径为:
d0=d w-(0.5-0.6)P
式中:d w——工件螺纹外径,mm;
P——螺距。
4.(4)不锈钢攻丝时,应保证有足够的冷却润滑液。通常可选用硫化油+15%~20%CCl4;白铅油+机油
或其他矿物油;煤油稀释氯化石蜡等。
5.在攻丝的过程中,万一丝锥折断,可将工件放在硝酸溶液中进行腐蚀,可以很快将高速钢丝锥腐
蚀,而不报废工件。
15 磨削不锈钢有哪些特点?
1.不锈钢的韧性大,热强度高,而砂轮磨粒的切削刃具有较大的负前角,磨削过程中磨屑不容易被
切离,切削阻力大,挤压、摩擦剧烈。单位面积磨削力很大,磨削温度可达1000℃~1500℃。同
时,在高温高压的作用下,磨屑易粘附在砂轮上,填满磨粒问的空隙,使磨粒失去切削作用。不
锈钢的类型不同,产生砂轮堵塞的情况也不相同,如磨削耐浓硝酸不锈钢及耐热不锈钢,粘附、
堵塞现象比1Cr18NiTi严重,而1Cr13、2Cr13等马氏体不锈钢就比较轻。
2.不锈钢的导热系数小,磨削时的高温不易导出,工件表面易产生烧伤、退火等现象,退火层深度
有时可达0.01~0.02 mm。磨削过程中产生严重的挤压变形,导致磨削表面产生加工硬化,特别
是磨削奥氏体不锈钢时,由于奥氏体组织不够稳定,磨后易产生马氏体组织,使表面硬化严重。
3.不锈钢的线膨胀系数大,在磨削热的作用下易产生变形,其尺寸难以控制。尤其是薄壁和细长的
零件,此现象更为严重。
4.多数类型的不锈钢不能被磁化,在平面磨削时,只能靠机械夹固或专用夹具来夹持工件,利用工
件侧面夹紧工件,产生变形和造成形状或尺寸误差,薄板工件更为突出。同时也会引起磨削过程
中的颤振而出现鳞斑状的波纹。
16 磨削不锈钢时怎样选择砂轮?
1.磨料:白刚玉具有较好的切削性能和自锐性,适于磨削马氏体及马氏体+铁素体不锈钢;单晶刚玉
磨料适用于磨削奥氏体和奥氏体+铁素体不锈钢;微晶刚玉磨料是由许多微小的晶体组成的,强度
高、韧性和自锐性好,其自锐的特点是沿微晶的缝隙碎裂,从而获得微刃性和微刃等高性,可以
减少烧伤、拉毛等现象,并可以降低磨削表面粗糙度,适于磨削各种不锈钢;立方氮化硼磨料的
硬度很高,热稳定性好,化学惰性高,在1300℃~1500℃不氧化,磨粒的刃尖不易变钝,产生的
磨削热也少,适用于磨削各种不锈钢。为了减少粘附现象,也可采用碳化硅和人造金刚石为磨料
的砂轮。
2.粒度:磨削不锈钢时,一般以采用36号、46号、60号中等粒度的砂轮为宜,其中粗磨时,采用
36号、46号粒度,精磨用60号粒度。为了同时适用于粗磨和精磨,则采用46号或60号粒度。
3.结合剂:磨削不锈钢要求砂轮具有较高的强度,以便承受较大的冲击载荷。陶瓷结合剂耐热、抗
腐蚀,用它制成的砂轮能很好地保持切削性能,不怕潮湿,且有多孔性,适合于制作磨削不锈钢
砂轮的结合剂。磨削耐浓硝酸不锈钢等材料内孔时,可采用树脂结合剂制造砂轮。
4.硬度:应选用硬度较低的砂轮,以提高自锐性。一般选用G~N硬度的砂轮,其中以K~L使用最
为普遍,使用微晶刚玉作磨料的内圆磨砂轮,则以J硬度为宜。
5.组织:为了避免磨削过程中砂轮堵塞,砂轮组织应选较疏松的,一般选用5号~8号较为合适。
17 磨削不锈钢时怎样选择磨削用量?
陶瓷结合剂砂轮的速度为30~35 m/s;树脂结合剂的砂轮速度为35~50 m/s。当发现表面烧伤时,应将砂轮速度降至16~20 m/s。
工件速度,当工件直径小于50 mm时,n=120~150 r/min;大于50 mm时,n=40~80 r/min。用砂轮外圆进行平面精磨时,工作台运动速度一般为15~20 m/min,粗磨时为5~50 m/min。磨削深度和横向进给量小时取大值,横向进给量大时取小值。粗磨深度为0.04~0.08 mm,精磨深度为0.01 mm。修整砂轮后应减小磨削深度。
外圆磨削时纵向进给量,粗磨时为(0.2~0.7)B mm/r,精磨时为(0.2~0.3)B mm/r;内圆磨削时纵向进给量,粗磨时为(0.4~0.7)B mm/r,精磨时为(0.25~0.4)B mm/r;砂轮外圆平面磨横向进给量,粗磨时(0.3~0.7)B mm/dst,精磨时为(0.05~0.1)B mm/dst。
18 磨削不锈钢时应注意什么?
1.应及时修整砂轮,粗磨时砂轮要修整粗一些,精磨时砂轮要始终保持锋利,以免过热烧
伤。修整后的砂轮两侧转角处,不允许有毛刺存在。
2.低表面粗糙度磨削时,粗精磨应分别进行,精磨余量一般留0.05 mm为宜,工件装夹误
差大时可留0.1 mm。
3.磨削过程中必须充分冷却,以带走大量的磨削热和进行冲刷,防止砂轮堵塞和工件表面
烧伤。冷却液必须清洁,不能混入磨屑或砂粒,以免将工件拉毛。磨削不锈钢的冷却液,一般选用冷却性能较好的乳化液,或用含有极压添加剂且表面张力小的冷却液。流量为
20~40 L/min,砂轮直径大时为80 L/min。
4.不锈钢磨削余量应取小一些,外圆磨削时,直径上的磨削余量为0.15~0.3 mm,精磨余
量为0.05 mm。内圆磨削的余量与外圆磨削基本相同。平面磨削时,对面积小、刚性好
的零件,单边留余量为0.15~0.2 mm,刚性差、面积大的零件,单边留磨削余量0.25~
0.3 mm。
19 加工不锈钢的实例有哪些?
不锈钢的用途很广,切削加工的实例也很多,在这里仅举几个切削加工的实例,以供参考。
1.车削:工件材料为1Cr18Ni9Ti,工件尺寸为?900 mm×720 mm。原用YG8硬质合金车刀,
刀具几何参数γ0=15°~18°,α0=6°~8°,κr=75°,λs=-5°~-8°;切削用量为Vc=2
8 m/min,a p=0.3~0.5 mm,f=0.16mm/r,精车一刀需刃磨28次车刀,且工件表面接刀
痕十分明显。后改用YG8N硬质合金车刀,除将切削速度提高到42.4m/min外,其他条件
相同,精车一刀外圆,仅需磨刀5次,工件表面粗糙度Ra为3.2μm,接刀痕也不明显。
2.车螺纹:工件材料为1Cr18Ni9Ti,螺纹规格为M20×2.5。原用YG8硬质合金,Vc=10 m
/min,f=2.5 mm/r,a p=0.3~0.4 mm,刀具刃磨一次加工不了一件。改用813硬质合金,在Vc=36 m/min的条件下,可加工两件以上,效率和刀具耐用度可提高两倍以上。
3.铣削:工件材料为Cr17Ni2,铣削平面,切削用量为Vc=90~100 m/min,a p=3~4 mm,a
f=0.15 mm/z。刀具为可转位端铣刀,刀具材料为YW4,刀具几何参数为γ0=5°,α0=8°,κr=75°,λs=5°。刀具耐用度为41 min。
4.镗孔:工件材料为1Cr18Ni9Ti,刀具材料原用YG6和YG10H硬质合金,刀具几何参数为
γ0=20°,α0=8°,κr=75°,λs=-3°。切削用量为Vc=20 m/min,a p=3 mm,f=0.32mm/r。
在相同的条件下,YG6的刀具耐用度为15 min,且不断屑而粘刀,YG10H的刀具耐用度为60 min,而且切削质量良好。
不锈钢加工刀具选择
不锈钢加工刀具选择 1.引言 随着航空、航天、石油、化工、冶金和食品等工业的蓬勃发展,不锈钢材料已得到广泛应用,而不锈钢材料由于韧性大、热强度高、导热系数低、切削时塑性变形大、加工硬化严重、切削热多、散热困难等原因,造成刀尖处切削温度高、切屑粘附刃口严重、容易产生积屑瘤,既加剧了刀具的磨损,又影响加工表面粗糙度。此外,由于切屑不易卷曲和折断,也会损伤已加工表面,影响工件的质量。为提高加工效率和工件质量,正确选择刀具材料、车刀几何参数和切削用量至关重要。 2.刀具材料的选择 正确选用刀具材料是保证高效率加工不锈钢的决定因素。根据不锈钢的切削特点,刀具材料应具备足够的强度、韧性、高硬度和高耐磨性且与不锈钢的粘附性要小。常用的刀具材料有硬质合金和高速钢两大类,形状复杂的刀具主要采用高速钢材料。由于高速钢切削不锈钢时的切削速度不能太高,因此影响生产效率的提高。对于较简单的车刀类刀具,刀具材料应选用强度高、导热性好的硬质合金,因其硬度、耐磨性等性能优于高速钢。常用的硬质合金材料有:钨钴类(YG3、YG6、YG8、YG3X、YG6X),钨钴钛类(YT30、YT15、YT14、YT5),通用类(YW1、YW2)。YG类硬质合金的韧性和导热性较好,不易与切屑粘结,因此适用于不锈钢粗车加工;而YW类硬质合金的硬度、耐磨性、耐热性和抗氧化性能以及韧性都较好,适合于不锈钢的精车加工。加工1Cr18Ni9Ti奥氏体不锈钢时,不宜选用YT类硬质合金,由于不锈钢中的Ti和YT类硬质合金中的Ti 产生亲合作用,切屑容易把合金中的Ti带走,促使刀具磨损加剧。 〕 3.刀具几何角度的选择 刀具切削部分的几何角度,对于不锈钢切削加工的生产率、刀具耐用度、被加工表面粗糙度、切削力以及加工硬化等方面都有很大的影响,合理选择和改进刀具几何参数是保证加工质量、提高效率、降低成本的有效途径。 (1)车刀前角γ0的选择 前角的大小决定刀刃的锋利与强度。增大前角可以减小切屑的变形,从而减小切削力和切削功率,降低切削温度,提高刀具耐用度。但是增大前角会使楔角减小,降低刀刃强度,造成崩刃,使刀具耐用度下降。车削不锈钢时,在不降低刀具强度的条件下,应把前角适当取大一些。在刀具前角大时其塑性变形小,切削力和切削热降低,减轻加工硬化趋势,提高刀具耐用度,一般刀具前角宜取12°~20°。
2205双相不锈钢和它地机械的性能
2205双相不锈钢和它的机械性能 浏览次数:3087 添加时间:2008-9-9 14:41:47 2205 合金( UNS S32305/S31803 )是由22%铬,3%钼及5-6%镍氮合金构成的复式不锈钢。它具有高强度、良好的韧性以及良好的整体和局部的抗协强腐蚀能力。 与316L 和317L 奥氏体不锈钢相比,2205 合金在抗蚀损斑及裂缝方面的性能更优越,它具有很高的抗腐蚀能力,与体相比,它的热膨胀系数更低,导热性更高。 与奥氏体不锈钢相比,它的耐压强度是其两倍,与316L 和317L 相比,设计者可以减轻其重量,其成本也更低。 General Properties 2205复式不锈钢2205合金是由22%铬,3%钼及5-6%镍氮合金构成的复式不锈钢。它具有高强度、良好的冲击韧性以好的整体和局部的抗应力腐蚀能力。 与316L和317L奥氏体不锈钢相比,2205合金在抗斑蚀及裂隙腐蚀方面的性能更优越,它具有很高的抗腐蚀能力,与奥氏体它的热膨胀系数更低,导热性更高。 与奥氏体不锈钢相比,它的耐压强度是其两倍,与316L和317L相比,设计者可以减轻其重量,故其成本也更低。这种合金特用于—50?F/+600?F温度范围内,在严格限制的情况下(尤其对于焊接结构),也可以用于更低的温度. 应用领域 压力器皿、高压储藏罐、高压管道、热交换器(化学加工工业)。 石油天然气管道、热交换器管件。 污水处理系统。 纸浆和造纸工业分类器、漂白设备、贮存处理系统。 高强度耐腐蚀环境下的回转轴、压榨辊、叶片、叶轮等。 轮船或卡车的货物箱 食品加工设备
抗腐蚀能力 一般腐蚀由于其较高的铬 钼及氮含量,2205的抗腐蚀特性在大多数环境下优于316L和317L 局部抗腐蚀 2205中铬、钼及氮的含量使其在腐蚀性及酸性的溶液中, 对锈斑及裂隙腐蚀具有很强的抵抗能力。 在含2000ppm 氯化物的硫磺酸溶液中等腐蚀曲线4 mpy (0.1 mm/yr) 抗应力腐蚀 不锈钢的复式微观结构有助于提高其抗应力裂隙腐蚀的能力。 在一定的温度、压强、氧气及氯化物存在的情况下,氯化物应力腐蚀的现象会发生。因为这些条件不宜控制。304L、31 317L的使用在这方面受到限制。 疲劳强度腐蚀 2205 合金的高强度及抗腐蚀能力使其具有很高的抗腐蚀抗疲劳强度。主要应用于具有较强腐蚀性的环境中。 采用AvestaPolarit 蚀损电池测得1M NaCl 中蚀损临界温度。
双相不锈钢的优点和缺点
双相不锈钢的分析 班级学号姓名 摘要双相不锈钢是在18-8奥氏体不锈钢的基础上,提高C r含量或者加入其他铁素体元素形成的,使钢具有奥氏体加铁素体双向组织,又节约了Ni合金。由于双向不锈钢两相组织的特点,通过正确控制化学成分和热处理工艺,使双相不锈钢兼有铁素体不锈钢和奥氏体不锈钢的优点。文章主要介绍双相不锈钢的性能、双相不锈钢的类型以及双相不锈铜的应用领域。 关键词双相不锈钢;性能;加工;热处理工艺;铁素体不锈钢;奥氏体不锈钢 双相不锈钢的基本优点如下: (1)含铬量为18%—22%的双相不锈钢在低应力下有良好的耐中性氯化物应力腐蚀性能。一般应用在70Y以上中性氯化物溶液中的18—8型奥氏体不锈钢容易发生应力腐蚀破裂,在微量氯化物及硫化氢的工业介质中用这类不锈钢制造的热交换器、蒸发器等设备都存在着产生应力腐蚀破裂的倾向,而双相不锈钢却有良好的抵抗能力。 (2)含钥双相不锈钢有良好的耐孔蚀性能。在具有相同的孔蚀当量值(PR5=cr%*3.3%Moll6%N)时,双相不锈钢与奥氏体不锈钢的临界孔蚀电位相近。含18%cr的双相不 锈钢耐孔蚀性能与AIsl316L相当。含25%Cr的尤其是含氮的高铬双相不锈钢的耐孔蚀和缝隙腐蚀性能超过了AISI 316L。 (3)有良好的耐腐蚀疲劳和磨损腐蚀性能,在某些腐蚀介质条件下被用于泵、阀等设 备中。 (4)综合力学性能好,有较高的强度和疲劳强度,屈服强度是18—8型奥氏体不锈钢的2倍。双相不锈钢由于具有奥氏体+铁素体双相组织,且两个相组织的含量基本相当,故兼有奥氏体不锈钢和铁素体不锈钢的特点。屈服强度可达400Mpa ~ 550MPa,是普通奥氏体不锈钢的2倍。与铁素体不锈钢相比,双相不锈钢的韧性高,脆性转变温度低,耐晶间腐蚀性能和焊接性能均显着提高;同时又保留了铁素体不锈钢的一些特点,如475℃脆性、热导率高、线膨胀系数小,具有超塑性及磁性等。与奥氏体不锈钢相比,双相不锈钢的强度高,特别是屈服强度显着提高,且耐孔蚀性、耐应力腐蚀、耐腐蚀疲劳等性能也有明显的改善。 (5)可焊性良好,热裂倾向小。一般焊前不需预热,焊后不需热处理,可与18—8型奥氏体不锈钢或碳钢等异种钢焊接。 (6)台低铬(18%cr)的双相不锈钢热加工温度范围比18—8型奥氏体不锈钢宽,抗力小,可不经过锻造,直接轧制开坯生产钢板”肯高铬(25%c)的钢则比奥氏休不锈钢热加r 困难。 (7)与奥氏体不锈钢相比,导热系数大,线膨胀系数小板,也适用丁制造热交换器的管芯。与奥氏体不锈钢相比,双相不锈钢(DSS)的强度和耐局部腐蚀性能结合良好, DSS的金相组织通常为50%的铁素体和50%的奥氏体,但二者的比例也可以在35%/65%到55%/45%之间变化。由于其高强度及长期使用中的高可靠性,目前国外开始考虑把它作为“基体材料”,以代替碳钢应用到大型储罐及设备制造方面。在炼油行业中经常使用的DSS有22%cr和25%Cr两个级别,后者与前者相比包含更多的钼和氮,具有更高的耐蚀性能双相不锈钥处存在如下缺点: (1)与奥氏休不锈钢比较,耐热性较低,一般控制在300Y以下的工作环境中使用。 (2)冷加r比18—8型奥氏体不锈钢的加丁硬化效应大,在管、板承受变形初期,需施
不锈钢材料加工难点分析
不锈钢材料加工难点分析 不锈钢材料加工难点主要有以下几个方面: 1. 切削力大,切削温度高 该类型材料强度大,切削时切向应力大、塑性变形大,因而切削力大。此外材料导热性极差,造成切削温度升高,且高温往往集中在刀具刃口附近的狭长区域内,从而加快了刀具的磨损。 2. 加工硬化严重 奥氏体不锈钢以及一些高温合金不锈钢均为奥氏体组织,切削时加工硬化倾向大,通常是普通碳素钢的数倍,刀具在加工硬化区域内切削,使刀具寿命缩短。 3. 容易粘刀 无论是奥氏体不锈钢还是马氏体不锈钢均存在加工时切屑强韧、切削温度很高的特点。当强韧的切屑流经前刀面时,将产生粘结、熔焊等粘刀现象,影响加工零件表面粗糙度。 4. 刀具磨损加快 上述材料一般含高熔点元素、塑性大,切削温度高,使刀具磨损加快,磨刀、换刀频繁,从而影响了生产效率,提高了刀具使用成本。 主要是降低切削线速度,进给。采用专门加工不锈钢或者高温合金的刀具,钻孔攻丝最好内冷。 不锈钢零件加工工艺
通过上述加工难点分析,不锈钢的加工工艺及相关刀具参数设计与普通结构钢材料应具有较大的不同,其具体加工工艺如下: 1.钻孔加工 在钻孔加工时,由于不锈钢材料导热性能差,弹性模量小,孔加工起来也比较困难。解决此类材料的孔加工难题,主要是选用合适的刀具材料,确定合理的刀具的几何参数以及刀具的切削用量。钻削上述材料时,钻头一般应选用W6Mo5Cr4V2Al、W2Mo9Cr4Co8等材质的钻头,这些材质钻头缺点是价格比较昂贵,而且难以采购。而采用常用的W18Cr4V普通标准高速钢钻头钻孔时,由于存在顶角较小、切屑太宽而不能及时排出孔外、切削液不能及时冷却钻头等缺点,再加上不锈钢材料导热性差,造成集中在刀刃上的切削温度升高,容易导致两个后刀面和主刃烧伤及崩刃,使钻头的使用寿命降低。 1)刀具几何参数设计在采用W18Cr4V普通高速钢钻头钻孔时,切削力及切削温度均集中在钻尖上,为提高钻头切削部位的耐用度,可以适当增大顶角角度,顶角一般选135°~140°,顶角增大也将使外缘前角减小,钻屑变窄,以利于排屑。但是加大顶角后,钻头的横刃变宽,造成切削阻力增大,因而必须对钻头横刃进行修磨,修磨后横刃的斜角为47°~55°,横刃前角为3°~5°,修磨横刃时,应将切削刃与圆柱面转角处修磨成圆角,以增加横刃强度。由于不锈钢材料弹性模量较小,切屑层下的金属弹性恢复大,加之加工过程中加工硬化严重,后角太小会加快钻头后刀面的磨损,而且增加了切削温度,降低钻头的寿命。因此须适当加大后角,但后角太大,将使钻头的主刃变得单薄,减小了
不锈钢的切削加工
1 什么是不锈钢? 通常,人们把含铬量大于12%或含镍量大于8%的合金钢叫不锈钢。这种钢在大气中或在腐蚀性介质中具有一定的耐蚀能力,并在较高温度(>450℃)下具有较高的强度。含铬量达16%~18%的钢称为耐酸钢或耐酸不锈钢,习惯上通称为不锈钢。 钢中含铬量达12%以上时,在与氧化性介质接触中,由于电化学作用,表面很快形成一层富铬的钝化膜,保护金属内部不受腐蚀;但在非氧化性腐蚀介质中,仍不易形成坚固的钝化膜。为了提高钢的耐蚀能力,通常增大铬的比例或添加可以促进钝化的合金元素,加Ni、Mo、Mn、Cu、Nb、Ti、W、Co等,这些元素不仅提高了钢的抗腐蚀能力,同时改变了钢的内部组织以及物理力学性能。这些合金元素在钢中的含量不同,对不锈钢的性能产生不同的影响,有的有磁性,有的无磁性,有的能够进行热处理,有的则不能热处理。 由于不锈钢所具有的上述特性,越来越广泛地应用于航空、航天、化工、石油、建筑和食品等工业部门及日常生活中。所含的合金元素对切削加工性影响很大,有的甚至很难切削。 2 不锈钢可分为哪几类? 不锈钢按其成分,可分为以铬为主的铬不锈钢和以铬、镍为主的铬镍不锈钢两大类。 工业上常用的不锈钢一般按金相组织分类,可分为以下五大类: 1.马氏体不锈钢:含铬量12%~18%,含碳量0.1%~0.5%(有时达1%),常见的有1Cr13、2 Cr13、3Cr13、4Cr13、1Cr17Ni2、9Cr18、9Cr18MoV、30Cr13Mo等。 2.铁素体不锈钢:含铬量12%~30%,常见的有0Cr13、0Cr17Ti、0Cr13Si4NbRE、1Cr17、1 Cr17Ti、1Cr17M02Ti、1Cr25Ti、1Cr28等。 3.奥氏体不锈钢:含络量12%~25%,含镍量7%~20%(或20%以上),最典型的代表是1Cr1 8Ni9Ti,常见的还有00Cr18Ni10、00Cr18Ni14Mo2Cu2、0Cr18Ni12Mo2Ti、0Cr18Ni18Mo2 Cu2Ti、0Cr23Ni28M03Cu3Ti、1Cr14Mn14Ni、2Cr13Mn9Ni4、1Cr18Mn8Ni5N等。 4.奥氏体+铁素体不锈钢:与奥氏体不锈钢相似,仅在组织中含有一定量的铁素体,常见的 有0Cr21Ni5Ti、1Cr21Ni5Ti、1Cr18Mn10Ni5M03N、0Cr17Mn13Mo2N、1Cr17Mn9Ni3M03Cu2 N、Cr2bNi17M03CuSiN、1Cr18Ni11Si4AlTi等。 5.沉淀硬化不锈钢:含有较高的铬、镍和很低的碳,常见的有0Cr17Ni4Cu4Nb、0Cr17Ni7A l、0Cr15Ni7M02Al等。 前两类为铬不锈钢,后三类为铬镍不锈钢。 3 不锈钢有哪些物理、力学性能? 1.马氏体不锈钢:能进行淬火,淬火后具有较高的硬度、强度和耐磨性及良好的抗氧化性, 有的有磁性,但内应力大且脆。经低温回火后可消除其应力,提高塑性,切削加工较困 难,有切屑擦伤或粘结的明显趋向,刀具易磨损。 当钢中含碳量低于0.3%时,组织不均匀,粘附性强,切削时容易产生积屑瘤,且断屑困难,工件已加工表面质量低。含碳量达0.4%~0.5%时,切削加工性较好。
双相不锈钢性能特点-力学性能特点
与不锈钢中其他四类相比,由于双相不锈钢具有α+γ双相组织结构,因此,其性能特点兼有奥氏体不锈钢和铁素体不锈钢的特性,是一类高强度与高耐蚀性最佳匹配的不锈钢。 与铁素体不锈钢相比,α+γ双相不锈钢的脆性转变温度低,室温韧性高,耐晶间腐蚀和焊接性能显著改善,同时仍保留铁素体不锈钢的一些特点,如457℃脆性,中温脆性和高温脆性及热导率高、线胀系数小何具有超塑性等。 与奥氏体不锈钢相比,双相不锈钢的强度,特别是屈服强度显著提高,耐晶间腐蚀、应力腐蚀、疲劳腐蚀及磨蚀等性能明显改善,但有磁性。 上述双相不锈钢的特性,随两相比例的不同而有所改变。例如,当铁素体相的比例较大时,则更易显示铁素体不锈钢的性能特点;反之,则更易显示奥氏体不锈钢的性能特点。
1.力学性能 高强度,存在脆性转变温度和三个脆性区。 由于双相不锈钢具有微细的显微组织以及钼、氮等的强化作用,双相不锈钢的强度远远高于铁素体不锈钢和奥氏体不锈钢,一些试验结果见表1和图2。 表1.铁素体(430)、奥氏体(304)和双相不锈钢代表性牌号室温力学性能的对比 图2.分别为超级铁素体不锈钢、超级双相不锈钢、超级奥氏体不锈钢的力学性能对比 但是,双相不锈钢中含高铬、钼的大量铁素体相的存在,使得铁素体不锈钢中所具有的脆性 转变温度和457℃脆性、中温脆性以及高温脆性三个脆性区的特征,在双相不锈钢中先也显 现了出来(图3~5)。但是由于双相不锈钢的晶粒细化且又存在大量奥氏体,所以双相不锈 钢的脆性转变温度明显低于普通铁素体不锈钢,一般均在-40℃或-50℃以下,而且室温冲击 韧性也足够高(表1),因此不影响双相不锈钢的工程应用。至于457℃脆性和中温脆性只 要不高于260℃,长期使用就不会有任何危险。
切削不锈钢时怎样选择切削用量
不锈钢的切削加工 核心提示:本文重点介绍分析了不锈钢的性能,切削特点,怎样选择刀具材料、刀具几何参数、切削用量,切削液和冷却方式,加工方式等等 1 什么是不锈钢? 通常,人们把含铬量大于12%或含镍量大于8%的合金钢叫不锈钢。这种钢在大气中或在腐蚀性介质中具有一定的耐蚀能力,并在较高温度(>450℃)下具有较高的强度。含铬量达16%~18%的钢称为耐酸钢或耐酸不锈钢,习惯上通称为不锈钢。 钢中含铬量达12%以上时,在与氧化性介质接触中,由于电化学作用,表面很快形成一层富铬的钝化膜,保护金属内部不受腐蚀;但在非氧化性腐蚀介质中,仍不易形成坚固的钝化膜。为了提高钢的耐蚀能力,通常增大铬的比例或添加可以促进钝化的合金元素,加Ni、Mo、Mn、Cu、Nb、Ti、W、Co等,这些元素不仅提高了钢的抗腐蚀能力,同时改变了钢的内部组织以及物理力学性能。这些合金元素在钢中的含量不同,对不锈钢的性能产生不同的影响,有的有磁性,有的无磁性,有的能够进行热处理,有的则不能热处理。 由于不锈钢所具有的上述特性,越来越广泛地应用于航空、航天、化工、石油、建筑和食品等工业部门及日常生活中。所含的合金元素对切削加工性影响很大,有的甚至很难切削。 2 不锈钢可分为哪几类? 不锈钢按其成分,可分为以铬为主的铬不锈钢和以铬、镍为主的铬镍不锈钢两大类。 工业上常用的不锈钢一般按金相组织分类,可分为以下五大类: 马氏体不锈钢:含铬量12%~18%,含碳量0.1%~0.5%(有时达1%),常见的有1Cr13、2Cr13、3Cr13、4Cr13、1Cr17Ni2、9Cr18、9Cr18MoV、30Cr13Mo等。 铁素体不锈钢:含铬量12%~30%,常见的有0Cr13、0Cr17Ti、0Cr13Si4NbRE、1Cr17、1Cr17Ti、1Cr17M02Ti、1Cr25Ti、1Cr28等。 奥氏体不锈钢:含络量12%~25%,含镍量7%~20%(或20%以上),最典型的代表是1Cr18Ni9Ti,常见的还有00Cr18Ni10、00Cr18Ni14Mo2Cu2、0Cr18Ni12Mo2Ti、0Cr18Ni18Mo2Cu2Ti、0Cr23Ni28M03Cu3Ti、1Cr14Mn14Ni、2Cr13Mn9Ni4、1Cr18Mn8Ni5N等。 奥氏体+铁素体不锈钢:与奥氏体不锈钢相似,仅在组织中含有一定量的铁素体,常见的有0Cr21Ni5Ti、1Cr21Ni5Ti、1Cr18Mn10Ni5M03N、0Cr17Mn13Mo2N、1Cr17Mn9Ni3M03Cu2N、Cr2bNi17M03CuSiN、1Cr18Ni11Si4AlTi等。 沉淀硬化不锈钢:含有较高的铬、镍和很低的碳,常见的有0Cr17Ni4Cu4Nb、0Cr17Ni7Al、0Cr15Ni7M02Al等。 前两类为铬不锈钢,后三类为铬镍不锈钢。 3 不锈钢有哪些物理、力学性能?切削不锈钢时怎样选择刀具断(卷)屑槽和刃口形式? 切削不锈钢时还应选择合适的刀具断(卷)屑槽,以便控制连绵不断的切屑,通常采用全圆弧形或直线圆弧形断(卷)屑槽。断(卷)屑槽的宽度Bn=3~5 mm,槽深h=0.5~1.3 mm,Rn=2~8 mm。一般情况下,粗车时ap、f大,断(卷)屑槽宜宽而浅;精车时ap、f小,应窄而深些。 断(卷)屑槽的形式见图2。
不锈钢加工参数
不锈钢切削加工 不锈钢切削加工摘要:螺纹类零件10的数控车床加工编程NUM公司力推新一代Axium Power 数控系统数控铣削的编程与工艺分析基于细胞神经网络刀具磨损图像处理的研究中国最大乙烯装置的裂解气压缩机试车成功发动机盲孔除切屑机的研制与应用在不断变化时代的工具钢加工什么是智能变送器?机械故障的形成及其特性分析数控车间(机床)集成管理技术及产品浅谈CAD的特征造型技术轴承钢的表面强化方法如何进行电话销售?拉刀齿距及同时工作齿数的确定大型水轮机叶片的多轴联动数控加工编程技术张晓静:计算机在冲压领域的应用 PLC位控单元在精密磨削控制中的应用硬质材料铣削技术 CAD技术发展趋势数控机床软件界面人的因素分析 [标签:tag] 1 什么是不锈钢?通常,人们把含铬量大于12%或含镍量大于8%的合金钢叫不锈钢。这种钢在大气中或在腐蚀性介质中具有一定的耐蚀能力,并在较高温度(450℃)下具有较高的强度。含铬量达16%~18%的钢称为耐酸钢或耐酸不锈钢,习惯上通称为不锈钢。钢中含铬量达12%以上时,. 1?什么是不锈钢? 通常,人们把含铬量大于12%或含镍量大于8%的合金钢叫不锈钢。这种钢在大气中或在腐蚀性介质中具有一定的耐蚀能力,并在较高温度(>450℃)下具有较高的强度。含铬量达16%~18%的钢称为耐酸钢或耐酸不锈钢,习惯上通称为不锈钢。 钢中含铬量达12%以上时,在与氧化性介质接触中,由于电化学作用,表面很快形成一层富铬的钝化膜,保护金属内部不受腐蚀;但在非氧化性腐蚀介质中,仍不易形成坚固的钝化膜。为了提高钢的耐蚀能力,通常增大铬的比例或添加可以促进钝化的合金元素,加Ni、Mo、Mn、Cu、Nb、Ti、W、Co等,这些元素不仅提高了钢的抗腐蚀能力,同时改变了钢的内部组织以及物理力学性能。这些合金元素在钢中的含量不同,对不锈钢的性能产生不同的影响,有的有磁性,有的无磁性,有的能够进行热处理,有的则不能热处理。 由于不锈钢所具有的上述特性,越来越广泛地应用于航空、航天、化工、石油、建筑和食品等工业部门及日常生活中。所含的合金元素对切削加工性影响很大,有的甚至很难切削。2?不锈钢可分为哪几类? 不锈钢按其成分,可分为以铬为主的铬不锈钢和以铬、镍为主的铬镍不锈钢两大类。 工业上常用的不锈钢一般按金相组织分类,可分为以下五大类: 马氏体不锈钢:含铬量12%~18%,含碳量0.1%~0.5%(有时达1%),常见的有1Cr13、2Cr13、3Cr13、4Cr13、1Cr17Ni2、9Cr18、9Cr18MoV、30Cr13Mo等。?铁素体不锈钢:含铬量12%~30%,常见的有0Cr13、0Cr17Ti、0Cr13Si4NbRE、1Cr17、1Cr17Ti、1Cr17M02Ti、1Cr25Ti、1Cr28等。?奥氏体不锈钢:含络量12%~25%,含镍量7%~20%(或20%以上),最典型的代表是1Cr18Ni9Ti,常见的还有00Cr18Ni10、00Cr18Ni14Mo2Cu2、0Cr18Ni12Mo2Ti、0Cr18Ni18Mo2Cu2Ti、0Cr23Ni28M03Cu3Ti、1Cr14Mn14Ni、2Cr13Mn9Ni4、1Cr18Mn8Ni5N等。?奥氏体铁素体不锈钢:与奥氏体不锈钢相似,仅在组织中含有一定量的铁素体,常见的有0Cr21Ni5Ti、1Cr21Ni5Ti、1Cr18Mn10Ni5M03N、0Cr17Mn13Mo2N、1Cr17Mn9Ni3M03Cu2N、Cr2bNi17M03CuSiN、1Cr18Ni11Si4AlTi等。?沉淀硬化不锈钢:含有较高的铬、镍和很低的碳,常见的有0Cr17Ni4Cu4Nb、0Cr17Ni7Al、0Cr15Ni7M02Al等。 前两类为铬不锈钢,后三类为铬镍不锈钢。 3?不锈钢有哪些物理、力学性能? 马氏体不锈钢:能进行淬火,淬火后具有较高的硬度、强度和耐磨性及良好的抗氧化性,有的有磁性,但内应力大且脆。经低温回火后可消除其应力,提高塑性,切削加工较困难,有切屑擦伤或粘结的明显趋向,刀具易磨损。 当钢中含碳量低于0.3%时,组织不均匀,粘附性强,切削时容易产生积屑瘤,且断屑困难,
双相不锈钢基本特性
第一类属低合金型,代表牌号UNS S32304(23Cr-4Ni-0.1N),钢中不含钼,PREN值为24-25,在耐应力腐蚀面可代替AISI304或316使用。 第二类属中合金型,代表牌号是UNS S31803(22Cr-5Ni-3Mo-0.15N),PREN值为32-33,其耐蚀性能介于AISI 316L和6%Mo+N奥氏体不锈钢之间。 第三类属高合金型,一般含25%Cr,还含有钼和氮,有的还含有铜和钨,标准牌号UNSS32550(25Cr-6Ni-3Mo-2Cu-0.2N),PREN值为38-39,这类钢的耐蚀性能高于22%Cr的双相不锈钢。 第四类属超级双相不锈钢型,含高钼和氮,标准牌号UNS S32750(25Cr-7Ni-3.7Mo-0.3N),有的也含钨和铜,PREN值大于40,可适用于苛刻的介质条件,具有良好的耐蚀与力学综合性能,可与超级奥氏体不锈钢相媲美。国外主要双相不锈钢牌号的近似对照见表2。 表1 双相不锈钢(DSS)代表牌号的主要化学成分和蚀抗力当量值 Representative Duplex Stainless Steel Types,Main Chemical Analysis and Pitting Resistance Equivalent Number - . -考试文档-
- . -考试文档-
- . -考试文档-
表2 各国主要双相不锈钢牌号的近似对照 Comparison of Main Duplex Stainless Steels Of Different Countries - . -考试文档-
不锈钢加工对刀具材质和参数的要求
不锈钢加工对刀具材质和参数的要求 1 不锈钢加工对刀具的基本要求 对刀具几何参数的要求加工不锈钢时,刀具切削部分的几何形状,一般应从前角、后角方面的选择来考虑。在选择前角时,要考虑卷屑槽型、有无倒棱和刃倾角的正负角度大小等因素。不论何种刀具,加工不锈钢时都必须采用较大的前角。增大刀具的前角可减小切屑切离和清出过程中所遇到的阻力。对后角选择要求不十分严格,但不宜过小,后角过小容易和工件表面产生严重摩擦,使加工表面粗糙度恶化,加速刀具磨损。并且由于强烈摩擦,增强了不锈钢表面加工硬化的效应;刀具后角也不宜过大,后角过大,使刀具的楔角减小,降低了切削刃的强度,加速了刀具的磨损。通常,后角应比加工普通碳钢时适当大些。 对刀具切削部分表面粗糙度的要求提高刀具切削部分的表面光洁度可减少切屑形成卷曲时的阻力,提高刀具的耐用度。与加工普通碳钢相比较,加工不锈钢时应适当降低切削用量以减缓刀具磨损;同时还要选择适当的冷却润滑液,以便降低切削过程中的切削热和切削力,延长刀具的使用寿命。 对刀杆材料的要求加工不锈钢时,由于切削力较大,故刀杆必须具备足够的强度和刚性,以免在切削过程中发生颤振和变形。这就要求选用适当大的刀杆截面积,同时还应采用强度较高的材料来制造刀杆,如采用调质处理的45号钢或50号钢。 对刀具切削部分材料的要求加工不锈钢时,要求刀具切削部分的材料具有较高的耐磨
性,并能在较高的温度下保持其切削性能。目前常用的材料有:高速钢和硬质合金。由于高速钢只能在600°C以下保持其切削性能,因此不宜用于高速切削,而只适用于在低速情况下加工不锈钢。由于硬质合金比高速钢具有更好的耐热性和耐磨性,因此用硬质合金材料制成的刀具更适合不锈钢的切削加工。 硬质合金分钨钴合金(YG)和钨钴钛合金(YT)两大类。钨钴类合金具有良好的韧性,制成的刀具可以采用较大的前角与刃磨出较为锋利的刃口,在切削过程中切屑易变形,切削轻快,切屑不容易粘刀,所以在一般情况下,用钨钴合金加工不锈钢比较合适。特别是在振动较大的粗加工和断续切削加工情况下更应采用钨钴合金刀片,它不象钨钴钛合金那样硬脆,不易刃磨,易崩刃。钨钴钛合金的红硬性较好,在高温条件下比钨钴合金耐磨,但它的脆性较大,不耐冲击、振动,一般作不锈钢精车用刀具。 2 刀具材料牌号的选择 刀具材料的切削性能关系着刀具的耐用度和生产率,刀具材料的工艺性影响着刀具本身的制造与刃磨质量。宜选择硬度高、抗粘结性和韧性好的刀具材料,如YG类硬质合金,最好不要选用YT类硬质合金,尤其是在加工1Gr18Ni9Ti奥氏体不锈钢应绝对避免选用YT类硬质合金,因为不锈钢中的钛(Ti)和YT类硬质合金中的Ti产生亲合作用,切屑容易把合金中的Ti带走,促使刀具磨损加剧。生产实践表明,选用YG532、YG813及YW2三种牌号材料加工不锈钢具有较好的加工效果(见附表)。 三种硬质合金牌号的性能比较
不锈钢加工难点分析及解决办法【全面分析】
不锈钢加工难点分析及解决办法【全面分析】 内容来源网络,由“深圳机械展(11万㎡,1100多家展商,超10万观众)”收集整理! 更多cnc加工中心、车铣磨钻床、线切割、数控刀具工具、工业机器人、非标自动化、数字化无人工厂、精密测量、数控系统、3D打印、激光切割、钣金冲压折弯、精密零件加工等展示,就在深圳机械展. 【摘要】新产品的不断涌现对零件的材料提出了更高的要求,所需材料有时必须满足高硬度、高耐磨性、高韧性等特殊要求,由此产生了一批难加工材料,对加工工艺提出了更高的要求。本文以不锈钢等难加工材料为对象,结合我所加工遇到的实际问题,分析不锈钢的加工难点,并提出了切实有效的解决方法。 【关键词】不锈钢;切削加工;加工方法 1.引言 与优质碳素结构钢相比,不锈钢材料加入了Cr、Ni、N、Nb、Mo等合金元素。这些合金元素的增加,不仅提高了钢的耐蚀性,对不锈钢的机械性能也有一定影响。如马氏体不锈钢4Cr13与45号中碳钢相比,具有相同的含碳量,但相对切削加工性只有45钢的58%;奥氏体不锈1Cr18Ni9Ti只有40%,而奥氏体—铁素体双相不锈钢韧性高、切削性更差。 2.不锈钢材料切削难点分析 在实际加工中,切削不锈钢往往伴随着断刀、粘刀现象的发生。由于不锈钢在切削时塑性变形大,产生的切屑不易折断、易粘结,导致在切削过程中加工硬
化严重,每一次走刀都对下一次切削产生硬化层,经过层层积累,不锈钢在切削过程中的硬度越来越大,需要的切削力也随之升高。 加工硬化层的产生、切削力的增高必然导致刀具与工件之间的摩擦增大,切削温度也随之升高。并且,不锈钢的导热系数较小,散热条件差,大量切削热集中刀具与工件之间,使已加工表面恶化,严重影响了已加工表面的质量。而且,切削温度的升高会加剧刀具磨损,使刀具前刀面产生月牙洼,切削刃产生缺口,从而影响工件表面质量,降低了工作效率,增加了生产成本。 3.提高不锈钢加工质量的方法 由上可以看出,不锈钢的加工比较困难,切削时易产生硬化层,容易断刀;产生的切屑不易折断,导致粘刀,会加剧刀具的磨损。针对不锈钢这些切削特点,结合生产实际,我们从刀具材料、切削参数及冷却方式三方面入手,找到提高不锈钢加工质量的方法。 3.1 刀具材料的选择 选择合适的刀具是加工出高质量零件的基础。刀具太差,加工不出合格的零件;选择过好的刀具,虽然能满足零件的表面质量要求,但容易造成浪费,提高了生产成本。结合不锈钢切削时散热条件差、产生加工硬化层、易粘刀等特点,选择的刀具材料应满足耐热性好、耐磨性高、与不锈钢亲和作用小的特点。 3.1.1 高速钢 高速钢是加入W、Mo、Cr、V、Go等合金元素的高合金工具钢,具有较好的工艺性能,强度和韧性配合好,抗冲击振动的能力较强。在高速切削产生高热情况下(约500℃)仍能保持高的硬度(HRC仍在60以上),高速钢红硬性好,适合制作铣刀、车刀等铣削刀具,可以满足不锈钢切削时产生的硬化层及散
不锈钢零件机加工工艺
不锈钢零件机加工工艺 1不锈钢材料加工难点 1.1切削力大,切削温度高 该类型材料强度大,切削时切向应力大、塑性变形大,因而切削力大。此外材料导热性极差,造成切削温度升高,且高温往往集中在刀具刃口附近的狭长区域内,从而加快了刀具的磨损。 1.2加工硬化严重 奥氏体不锈钢以及一些高温合金不锈钢均为奥氏体组织,切削时加工硬化倾向大,通常是普通碳素钢的数倍,刀具在加工硬化区域内切削,使刀具寿命缩短。 1.3容易粘刀 论是奥氏体不锈钢还是马氏体不锈钢均存在加工时切屑强韧、切削温度很高的特点。当强韧的切屑流经前刀面时,将产生粘结、熔焊等粘刀现象,影响加工零件表面粗糙度。 1.4刀具磨损加快 上述材料一般含高熔点元素、塑性大,切削温度高,使刀具磨损加快,磨刀、换刀频繁,从而影响了生产效率,提高了刀具使用成本。 2 不锈钢零件加工工艺 通过上述加工难点分析,不锈钢的加工工艺及相关刀具参数设计与普通结构钢材料应具有较大的不同,其具体加工工艺如下: 2.1钻孔加工 在钻孔加工时,由于不锈钢材料导热性能差,弹性模量小,孔加工起来也比较困难。解决此类材料的孔加工难题,主要是选用合适的刀具材料,确定合理的刀具的几何参数以及刀具的切削用量。钻削上述材料时,钻头一般应选用W6Mo5Cr4V2Al、W2Mo9Cr4Co8等材质的钻头,这些材质钻头缺点是价格比较昂贵,而且难以采购。而采用常用的W18Cr4V普通标准高速钢钻头钻孔时,由于存在顶角较小、切屑太宽而不能及时排出孔外、切削液不能及时冷却钻头等缺点,再加上不锈钢材料导热性差,造成集中在刀刃上的切削温度升高,容易导致两个后刀面和主刃烧伤及崩刃,使钻头的使用寿命降低。 (1)刀具几何参数设计在采用W18Cr4V普通高速钢钻头钻孔时,切削力及切削温度均集中在钻尖上,为提高钻头切削部位的耐用度,可以适当增大顶角角度,顶角一般选135°~140°,顶角增大也将使外缘前角减小,钻屑变窄,以利于排屑。但是加大顶角后,钻头的横刃变宽,造成切削阻力增大,因而必须对钻头横刃进行修磨,修磨后横刃的斜角为47°~55°,横刃前角为3°~5°,修磨横刃时,应将切削刃与圆柱面转角处修磨成圆角,以增加横刃强度。由于不锈钢材料弹性模量较小,切屑层下的金属弹性恢复大,加之加工过程中加工硬化严重,后角太小会加快钻头后刀面的磨损,而且增加了切削温度,降低钻头的寿命。因此须适当加大后角,但后角太大,将使钻头的主刃变得单薄,减小了主刃的刚性,所以后角应以12°~15°为宜。为使钻屑变窄,利于排屑,还需要在钻头两个后刀面上开交错分布的分屑槽。 (2)切削用量选择钻削时,切削用量的选择应从降低切削温度的基本点出发,因为高速切削将会使切削温度升高,而高的切削温度将加剧刀具磨损,因而切削用量中最重要的是选择切削速度。一般情况下,切削速度以12~15m/min较为合适。进给量对刀具寿命影响较小,但进给量选择太小将会使刀具在硬化层内切削,加剧磨损;而进给量如果太大,又会使表面粗糙度变差。综合上述两个因素,进给量选择为0.32~0.50mm/r为宜。 (3)切削液选择钻削时,为降低切削温度,可采用乳化液作为冷却介质。 2.2铰孔加工 (1)刀具几何参数设计不锈钢材料的铰削加工大部分使用硬质合金铰刀。铰刀的结构和几何参数与普通铰刀有所不同。为增强刀齿强度并防止铰削时产生切屑堵塞现象,铰刀齿数一般比较少。铰刀前角一般为8°~12°,但在某些特定情况,为了实现高速铰削,也可采用0°~
不锈钢切削加工及刀具
1. 刀具材料的选择............................................ 正确选用刀具材料是保证高效率加工不锈钢的决定因素。根据不锈钢的切削特点,刀具材料应具备足够的强度、韧性、高硬度和高耐磨性且与不锈钢的粘附性要小。常用的刀具材料有硬质合金和高速钢两大类。 由于高速钢切削不锈钢时的切削速度不能太高,因此影响生产效率的提高。对于铣刀类刀具,刀具材料应选用强度高、导热性好的硬质合金,因其硬度、耐磨性等性能优于高速钢。 常用的硬质合金材料有:钨钴类,钨钴钛类,通用类。钨钴类硬质合金的韧性和导热性较好,不易与切屑粘结,因此适用于不锈钢粗铣加工;而钨钴钛类硬质合金的硬度、耐磨性、耐热性和抗氧化性能以及韧性都较好,适合于不锈钢的精铣加工。 加工1Cr18Ni9Ti 奥氏体不锈钢时,不宜选用钨钴钛类硬质合金,由于不锈钢中的Ti 和钨钴钛类类硬质合金中的Ti 产生亲合作用,切屑容易把合金中的Ti 带走,促使刀具磨损加剧。 2. 刀具几何角度的选择............................................ 刀具切削部分的几何角度,对于不锈钢切削加工的生产率、刀具耐用度、被加工表面粗糙度、切削力以及加工硬化等方面都有很大的影响,合理选择和改进刀具几何参数是保证加工质量、提高效率、降低成本的有效途径。 (1)铣刀第一隙角的选择( Radius Angle ) 前角的大小决定刀刃的锋利与强度。增大前角可以减小切屑的变形,从而减小切削力和切削功率,降低切削温度,提高刀具耐用度。但是增大前角会使楔角减小,降低刀刃强度,造成崩刃,使刀具耐用度下降。 铣削不锈钢时,在不降低刀具强度的条件下,应把前角适当取大一些。在刀具前角大时其塑性变形小,切削力和切削热降低,减轻加工硬化趋势,提高刀具耐用度,一般刀具前角宜取12°~20°。 (2)铣刀第二隙角α0的选择( Secend Angle ) 在切削过程中,后角可以减小后刀面与切削表面的摩擦。若后角过大,则楔角减小,使散热条件恶化,刀具刃口强度下降,降低刀具耐用度;若后角过小,摩擦严重,则会使刃口变钝,增大切削力,增高切削温度,加剧刀具磨损。 在一般情况下,后角变化不大,但必须有一个合理的数值,以利于提高刀具的耐用度。铣削不锈钢时,由于不锈钢的弹性和塑性都比普通碳素钢大,所以刀具后角过小会使切断表面与铣刀后角的接触面积增大,摩擦产生的高温区集中于铣刀后角,加快铣刀磨损,降低被加工表面光洁度。
不锈钢的铣削加工参数
不锈钢的铣削加工 铣削不锈钢的特点是:不锈钢的粘附性及熔着性强,切屑容易粘附在铣刀刀 齿上,使切削条件恶化;逆铣时,刀齿先在已经硬化的表面上滑行,增加了加工硬化的趋势;铣削时冲击、振动较大,使铣刀刀齿易崩刃和磨损。 铣削不锈钢除端铣刀和部分立铣刀可用硬质合金作铣刀刀齿材料外,其余各类铣刀均采用高速钢,特别是钨—钼系和高钒高速钢具有良好的效果,其刀具耐用度可比W18Cr4V提高1~2倍。适宜制作不锈钢铣刀的硬质合金牌号有YG8、YW2、813、798、YS2T、YS30、YS25等。 铣削不锈钢时,切削刃既要锋利又要能承受冲击,容屑槽要大。可采用大螺旋角铣刀(圆柱铣刀、立铣刀),螺旋角b从20°增加到45°(g n =5°),刀具耐用度可 提高2倍以上,因为此时铣刀的工作前角g 0e 由11°增加到27°以上,铣削轻快。但b值不宜再大,特别是立铣刀以b≤35°为宜,以免削弱刀齿。 采用波形刃立铣刀加工不锈钢管材或薄壁件,切削轻快,振动小,切屑易碎,工件不变形。用硬质合金立铣刀高速铣削、可转位端铣刀铣削不锈钢都能取得良好的效果。 用银白屑(SWC)端铣刀铣削1Cr18Ni9Ti,其几何参数 采用波形刃立铣刀加工不锈钢管材或薄壁件,切削轻快,振动小,切屑易碎,工件不变形。用硬质合金立铣刀高速铣削、可转位端铣刀铣削不锈钢都能取得良好的效果。 用银白屑(SWC)端铣刀铣削1Cr18Ni9Ti,其几何参数为g f =5°、g p =15°、a f =15°、 a p =5°、k r =55°、k′ r =35°、g 01 =-30°、b g =0.4mm、r e =6mm,当V c =50~90 m/min、 V f =630~750mm/min、a′ p =2~6mm并且每齿进给量达0.4~0.8mm时,铣削力减小 10%~15%,铣削功率下降44%,效率也大大提高。其原理是在主切削刃上磨出负倒棱,铣削时人为地产生积屑瘤,使其代替切削刃进行切削,积屑瘤的前角g b 可达20~~302,由于主偏角的作用,积屑瘤受到一个前刀面上产生的平行于切削刃的推力作用而成为副屑流出,从而带走了切削热,降低了切削温度。 铣削不锈钢时,应尽可能采用顺铣法加工。不对称顺铣法能保证切削刃平稳地从金属中切离,切屑粘结接触面积较小,在高速离心力的作用下易被甩掉,以免刀齿重新切入工件时,切屑冲击前刀面产生剥落和崩刃现象,提高刀具的耐用度。 高速钢刀具加工参数: 直径:主轴转速(r/min)进给量mm/min 3~4 1100~750 10~15 5~6 750~ 550 15~20 8~10 600~350 20~30 12~14 350~270 30~37 16~18 270~230 37~47,5 20~22 250~200 47~55 硬制合金刀具:1500~2000 F120~150
双相不锈钢2205
双相不锈钢2205 2205双相不锈钢合金是由21%铬,2.5%钼及4.5%镍氮合金构成的复式不锈钢。它具有高强度、良好的冲击韧性以及良好的整体和局部的抗应力腐蚀能力。 2205双相不锈钢合金的屈服强度是奥氏体不锈钢的两倍,这一特性使设计者在设计产品时减轻重量,让这种合金比316,317L更具有价格优势。这种合金特别适用于-50°F/+600°F 温度范围内。超出这一温度范围的应用,也可考虑这种合金,但是有一些限制,尤其是应用于焊接结构的时候。 化学成分 C≤0.030 Mn≤2.00 Si≤1.00p≤0.030 S≤0.020 Cr 22.0~23.0 Ni 4.5~6.5 Mo3.0~3.5 N0.14~0.20(奥氏体-铁素体型) 2205双相钢应用领域 ·压力器皿、高压储藏罐、高压管道、热交换器(化学加工工业)。 ·石油天然气管道、热交换器管件。 ·污水处理系统。 ·纸浆和造纸工业分类器、漂白设备、贮存处理系统。 ·高强度耐腐蚀环境下的回转轴、压榨辊、叶片、叶轮等。 ·轮船或卡车的货物箱 ·食品加工设备 标准号:ASTM A240/A240M--01 ASTM/ASME...........A240 UNS S32205/S31803 EURONORM...........1.4462 X2CrNiMoN 22.5.3 AFNOR...................Z3 CrNi 22.05 AZ DIN.........................W. Nr 1.4462 抗腐蚀能力 均匀腐蚀由于铬含量(22%),钼(3%)及氮含量(0.18%),2205的抗腐蚀特性在大多数环境下优于316L和317L。 局部抗腐蚀 不锈钢的双相微观结构有助于提高不锈钢的抗应力腐蚀龟裂能力。在一定的温度、应张力、氧气及氯化物存在的情况下,奥氏体不锈钢会发生氯化物应力腐蚀。由于这些条件不易控制,因此304L、316L和317L的使用在这方面受到限制。 抗腐蚀疲劳 2205双相钢的高强度及抗腐蚀能力使其具有很高的抗腐蚀疲劳强度。加工设备易受腐蚀环境和加载循环的影响,2205的特性非常适合这样的应用。 结构
不锈钢车削方法
1切削过程中的难点及原因分析 在零件试生产时,我们按车削普通碳钢的工艺方法对3Cr13不锈钢进行了车削试验,结果是刀具磨损非常严重,生产率极低,零件表面质量达不到要求。 比较3Cr13钢与40钢、45钢等碳素结构钢的机械性能可知,3Cr1 3钢的强度比40钢和45钢高,它是一种强度高、塑性好的中碳马氏体不锈钢。由于切削时加工硬化严重,切削抗力大,切削温度高,导致刀具磨损严重,磨刀次数增多,增加了停机时间和机床调整时间,降低了生产率。同时又容易粘刀,产生积屑瘤,引起工件尺寸的变化并影响表面粗糙度,而且切屑不易卷曲和折断,易损伤工件已加工表面,影响零件质量。所以,不能用切削45钢的工艺来切削3Cr13,也不能把通用车床上的加工方法照搬到自动车床上来。因为一般自动车床装刀较少,要求最好一次走刀就能使被加工表面达到要求的尺寸和表面粗糙度,以保证较高的生产率。 2主要技术措施 1. 通过热处理,改变材料的硬度 马氏体不锈钢在热处理后的不同硬度,对车削加工的影响很大。表1是用YW2材料的车刀对热处理后不同硬度的3Cr13钢的车削情况。可见,退火状0.10.10.1态的马氏体不锈钢虽然硬度低,但车削性能差,这是因为材料塑性和韧性大,组织不均匀,粘附,熔着性强,切削过程易产生刀瘤,不易获得较好的表面质量。而调质处理后硬度在HRC30以下的3Cr13材料,车削加工性较好,易达到较好的表面质量。用硬度在HRC30以上的材料加工出的零件,表面质量虽然较好,但刀具易磨损。所以,在条件允许的情况下,可以在材料进厂后,先进行调质处理,硬度达到HRC25~HRC30,然后再进行切削加工。 表1 3Cr13钢材料切削用 量刀具 耐用 度 min 加工表 面粗糙 度 μm ν m/ mi n s m m /r HB240(退火)45 ~ 55 . 1 90~ 115 Ra6.3~ Ra3.2 HRC25~30(调质)45 ~ 55 . 1 95~ 110 Ra3.2 HRC35~38(调质)45 ~ 55 . 1 60~ 75 Ra3.2 2. 刀具材料的选择 在自动车床上车削不锈钢,一般使用的硬质合金的刀具材料有:YG6、YG8、YT15、YT30、YW1、YW2等材料。 常用的高速钢刀具有:W18Cr4V、W6M05Cr4V2AL等材料。我们在切削参数相同的条件