镀镍优点
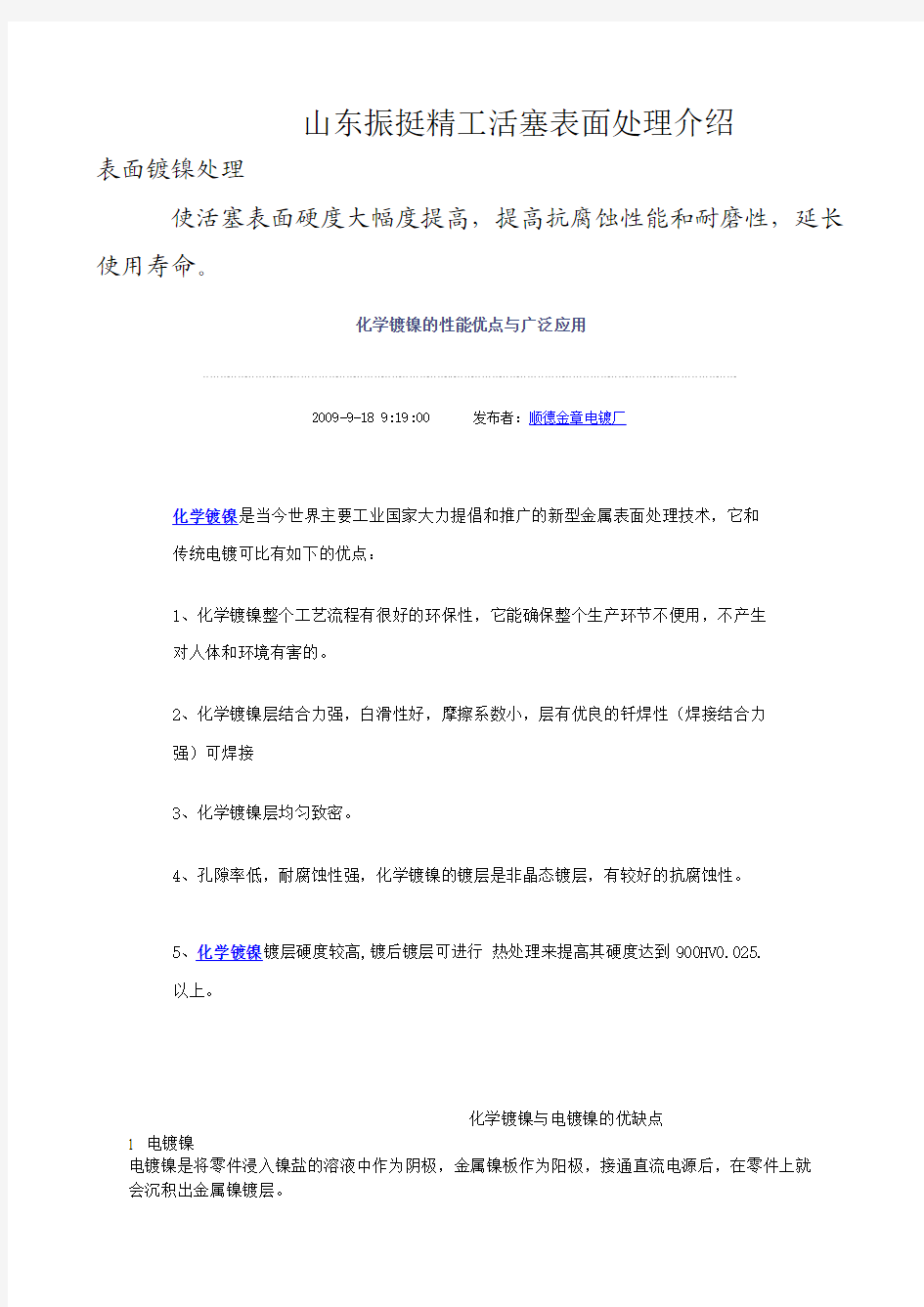

山东振挺精工活塞表面处理介绍
表面镀镍处理
使活塞表面硬度大幅度提高,提高抗腐蚀性能和耐磨性,延长使用寿命。
化学镀镍的性能优点与广泛应用
2009-9-18 9:19:00 发布者:顺德金章电镀厂
化学镀镍是当今世界主要工业国家大力提倡和推广的新型金属表面处理技术,它和
传统电镀可比有如下的优点:
1、化学镀镍整个工艺流程有很好的环保性,它能确保整个生产环节不便用,不产生
对人体和环境有害的。
2、化学镀镍层结合力强,白滑性好,摩擦系数小,层有优良的钎焊性(焊接结合力
强)可焊接
3、化学镀镍层均匀致密。
4、孔隙率低,耐腐蚀性强,化学镀镍的镀层是非晶态镀层,有较好的抗腐蚀性。
5、化学镀镍镀层硬度较高,镀后镀层可进行热处理来提高其硬度达到900HV0.025.
以上。
化学镀镍与电镀镍的优缺点
1 电镀镍
电镀镍是将零件浸入镍盐的溶液中作为阴极,金属镍板作为阳极,接通直流电源后,在零件上就会沉积出金属镍镀层。
电镀镍的优点是镀层结晶细致,平滑光亮,内应力较小,与陶瓷金属化层结合力强。
电镀镍的缺点是:
①受金属化瓷件表面的清洁和镀液纯净程度的影响大,造成电镀后金属化瓷件的缺陷较多,例如
起皮,起泡,麻点,黑点等;
②极易受电镀挂具和在镀缸中位置不同的影响,造成均镀能力差,此外金属化瓷件之间的相互遮
挡也会造成瓷件表面有阴阳面的现象;
③对于形状复杂或有细小的深孔或盲孔的瓷件不能获得较好的电镀表面;
④需要用镍丝捆绑金属化瓷件,对于形状复杂、尺寸较小、数量多的生产情况下,需耗费大量的
人力。
2 化学镀镍
化学镀镍是一种不加外在电流的情况下,利用还原剂在活化零件表面上自催化还原沉积得到镍层,当镍层沉积到活化的零件表面后由于镍具有自催化能力,所以该过程将自动进行下去。一般化学镀镍得到的为合金镀层,常见的是Ni-P合金和Ni-B合金。
化学镀镍的优点是不需要电流电源设备,厚度均匀致密,针孔少,均镀性好,仿真能力强,能在复杂零件表面沉积,深镀能力强,抗蚀性能好,镀镍的速度快,镀层厚度可达10~50,um,镀层在烧氢后无起皮、镍泡等缺陷。
化学镀镍的缺点是
①镀层为非晶态的层状结构,虽然进行热处理后,镀层结晶化,其层状结构逐渐消失,但是对陶
瓷一金属封接件的抗拉强度有所降低;
②镀液的成本高,寿命短,耗能大;
③镀液对杂质敏感,需经常处理,因而使工艺的可操作性变的相对复杂。
化学镀镍的优点和如何进行化学镀镍:
化学镀镍与电镀比较,具有如下优点:
①不需要外加直流电源设备。
②镀层致密,孔隙少。
③不存在电力线分布不均匀的影响,对几何形状复杂的镀件,也能获得厚度均匀的镀层;
④可在金属、非金属、半导体等各种不同基材上镀覆。
化学镀与电镀相比,所用的溶液稳定性较差,且溶液的维护、调整和再生都比较麻烦,材料成本费较高。
化学镀工艺在电子工业中有重要的地位。由于采用的还原剂种类不同,使化学镀所得的镀层性能有显著的差异,因此,在选定镀液配方时,要慎重考虑镀液的经济性及所得镀层的特性。
目前,化学镀镍、铜、银、金、钴、钯、铂、锡以及化学镀合金和化学复合镀层,在工业生产中已被采用。
如何进行化学镀镍
化学镀镍是化学镀应用最为广泛的一种方法,所用还原剂有次磷酸盐、肼、硼氢化钠和二甲基胺硼烷等。目前国内生产上大多采用次磷酸钠作还原剂,硼氢化钠和二甲基胺硼烷因价格较贵,只有少量使用。
1.镀层的用途
化学镀镍层的结晶细致,孔隙率低,硬度高,镀层均匀,可焊性好,镀液深镀能力好,化学稳定性高,目前已广泛用于电子、航空、航天、机械、精密仪器、日用五金、电器和化学工业中。
非金属材料上应用化学镀镍越来越多,尤其是塑料制品经化学镀镍后即可按常规的电镀方法镀上所需的金属镀层,获得与金属一样的外观。塑料电镀产品已广泛用于电子元件、家用电器、日用工业品等。
化学镀镍在原子能工业,如生产核燃料系统中的零件和容器以及火箭、导弹、喷气式发动机的零部件上已采用。
化工设备中压缩机等的零部件为防腐蚀、抗磨,而用化学镀镍层是很有利的。
化学镀镍层还能改善铝、铜、不锈钢材料的焊接性能,减少转动部分的磨耗,减少不锈钢与钛合金的应力腐蚀。
对镀层尺寸要求精确的精密零件和几何形状复杂的零件的深孔、盲孔、腔体的内表面,用化学镀镍能得到与外表面同样厚度的镀层。
对要求高硬度、耐磨的零件,可用化学镀镍代替镀硬铬。
化学镀镍在表面处理技术中占有重要的地位。随着表面处理技术的不断发展,化学镀镍会越来越得到广泛的应用。
化学镀的特点、原理及应用
化学镀的特点、原理及应用 一、特点 化学镀就是在不通电的情况下,利用氧化还原反应在具有催化表面的镀件上,获得金属合金的方法。它是新近发展起来的一门新技术。美、英、日、德等国,其工业产值正以每年15%的速度递增。它广泛地应用于机械、电子、塑料、模具、冶金、石油化工、陶瓷、水力、航空航天等工业部门,是一项很有发展前途的高新技术之一。其特点如下: 1、表面硬度高,耐磨性能好: 其表面硬度可在Hv0.1 =550-1100kg/mm2(相当于HRc =55-72)的范围内任意控制选择。处理后的机械部件,耐磨性能好,使用寿命长,一般可提高3-4倍,有的可达8倍以上。 2、硬化层的厚度极其均匀,处理部件不受形状限制,不变形。 特别适用于形状复杂、深盲孔及精度要求高的细小及大型部件的表面强化处理。 3、具有优良的抗腐蚀性能: 它在许多酸、碱、盐、氨和海水中具有很好的耐蚀性,其耐蚀性比不锈钢要优越得多,如表(1)所示。 表(1)Ni-12P合金镀层在下列介质中的腐蚀速率
腐蚀介质温度℃腐蚀速率(mm/年) 不锈钢1Cr18Ni9Ti Ni-12P合金 锈钢 42%NaOH 沸腾<0.048 >1.5 45%NaOH 20℃没有0.5 37%HCl 30℃0.14 1.5-1.8 10%H2 SO430℃0.031 >1.5 10% H2 SO470℃0.048 >1.5 水(海水)3.5%盐95℃没有0.5-1.4 40%HF 30℃0.0141 >1.5 4、处理后的部件,表面光洁度高,表面光亮,不需重新机械加工和抛光,即可直接装机使用。 5、镀层与基体的结合力高,不易剥落,其结合力比电镀硬铬和离子镀 要高。 6、可处理的基体材料广泛: 可处理材料有各种模具合金钢、不锈钢、铜、铝、锌、钛、塑料、尼龙、玻璃、橡胶、粉末、木头等。 二、化学镀镍的分类
化学镀镍缺陷介绍、分析及解决
化学镀镍缺陷介绍、分析及解决 目录 序言 第一部分缺陷的分类 第二部分如何分析缺陷的类别 第三部分缺陷产生的原因 第四部分如何消除缺陷 第五部分(补充)研磨及其前工段来料缺陷分析 序言 作为一名电镀工作者,每天都会接触到各种各样的缺陷,学会分析这些缺陷对我们来说相当重要,不及时的分析出缺陷的成因,就难以找出消除缺陷的方法,那么缺陷就会继续产生,甚至危及生产。打个比方,缺陷好比病人,而你是医生,当病人来找你时,你首先要做的是通过望闻问切确定病人的病情(对于缺陷来说,就是观察缺陷的外观,确定缺陷产生的原因),然后对症下药(确定缺陷产生的原因后,找出产生缺陷的地方加以改正),不同的病情下不同的药(不同的缺陷用不同的方法解决),诊断错误不但不会解决病情,还会加重病情(没分析出缺陷产生的原因,那么缺陷就会继续产生,甚至危及生产),合格的电镀工作者应该能准确的判断出缺陷产生的根源并加以改正。 下文缺陷分析的方法不具有绝对性,例如A1,我们分析镀前还是镀后产生一般是看镀后缺陷处有无瘤状物,没有一般认为是镀前产生的,但一些比较轻微撞伤的铝片,镀后也看不见瘤状物。所以,在实际生产中,缺陷分析的方法只具有参考性。 第一部分缺陷的分类 总的说来,电镀产生的缺陷分为电镀前,电镀过程中,电镀后,共三大类,每大类下面有分有很多小类,下面一一介绍: ㈠:电镀前的缺陷 可细分成上工装、吊蓝和前处理三块。 1:上工装 上工装产生的缺陷主要是内径和外径,表面较少见,内径缺陷可由装挂臂,定位杆和挂杆产生。其中: 装挂臂可以产生内径B1,内径C9和表面B1。内径B1(图例1-1)为靠内径0.5CM内,一条或数条不超过0.5CM的不平行于圆周切线的直线擦伤。装挂臂产生的C9(图例1-2)位于盘片内径的两个点,该两点与圆心的夹角在90度左右。表面B1(图例1-3)为基本指向圆心的贯穿内外径的较长直线,
普通镀镍
普通镀镍(暗镍) 普通镀镍又称暗镍,是最基本的镀镍工艺。在镀暗镍的基础上,先后开发了半光亮镍、光亮镍、双层镍、三层镍、黑镍、缎面镍,等等。由于镍是铁族金属之一,所以其镀液在电镀过程中具有较大的阴极极化和阳极极化作用,在不加络合剂的镀液中,就能镀得结晶细小而致密的镀镍层。 根据镀液的性能和用途,普通镀镍液可以分为低浓度的预镀液、普通镀液、瓦特液和滚镀液等。 预镀液:经预镀后可保证镀层与铜铁基体和随后的镀铜层结合力良好。 普通液:该镀液的导电性好,可在较低温度下电镀、节省能源、使用比较方便。瓦特液:具有较快的沉积速度,成分简单,操作控制比较方便。 滚镀液:满足小零件的电镀,但镀液必须要有良好的导电性和覆盖能力。一、工艺规范(见表3—4—3) 表3—4—3 几种普通镀镍镀液的工艺规范 各种因素对用瓦特镀镍液获得的镀镍层的力学性能的影响,列于表3—4—4。 表3—4—4 各种因素对瓦特镀镍层力学性能的影响
二、镀液配制方法(以瓦特液为例) 根据容积计算好所需要的化学药品,分别用热水溶解,混合在一个容器中,加蒸馏水稀释到所需体积,静置澄清,用虹吸法或过滤法把镀液引入镀槽,再加入已经溶解的十二烷基硫酸钠溶液或其他类型湿润剂,搅拌均匀,取样分析,经调整试镀合格后,即可生产。 三、镀液成分和工艺规范的影响 1.镍盐 硫酸镍和氯化镍是供给镍离子的盐。虽然氯化镍溶液的导电性和覆盖能力较好,但因氯离子太多,镀层的内应力较大,成本也较高,因此当前普遍采用硫酸镍。工业用的硫酸镍有六水与七水两种结晶水规格,前者含镍22.3%,后者含镍20.9%,在国内,大都是含七份结晶水的硫酸镍。硫酸镍的含量范围较大,大致在100g/L~350g/L之间。低浓度的镀液其覆盖能力较好,镀层的结晶较细致,容易抛光,但是阴极电流效率较低,允许的阴极电流密度范围的上限值较小。含量在300g/L左右的高浓度的镀液,镀层色泽均匀,允许采用较高的电流密度,沉积速度快。 2.阳极活化剂 为了使阳极正常溶解,不断补充电镀时所消耗的镍量,在镀镍溶液中必须加入阳极活化剂,常用的是氯化钠或氯化镍。氯化钠含量在7g/L~20g/L,但钠离子会降低阴极电流密度的上限值,引起镀层晶格扭歪和硬度增高。因此,近几年来趋向用氯化镍作阳极活化剂。一方面氯离子可以活化阳极,另一方面,镍离子可以补充溶液中镍的浓度,两者都是有效成分,而且镀液组成简单、管理方便,但氯化镍成本较高。所以我国目前还有一部分工厂用氯化钠作阳极活化剂。采用结晶致密的镍阳极和使用较大的阳极电流密度时,需要相应地增加氯离子的浓度。其他卤素离子虽也能帮助阳极溶解,但价格较贵,很少使用。 3.缓冲剂 硼酸是最常用的缓冲剂,在镀镍溶液中具有稳定pH值的作用。在镀镍过程中,镀液的pH 值必需保持在一定的范围内,一般为3.8~5.6。pH值过低,H+易于放电,降低镀镍的电流效率,镀层容易产生针孔。pH值过高,镀液混浊,阴极周围的金属离子会以金属氢氧化物的形式夹入镀层中,使镀层的力学性能恶化,外观粗糙。硼酸添加量为30g/L~35g/L,低于20g/L时,缓冲作用较弱,pH值不够稳定,并易产生针孔,当含量达到31g/L以上时,才有显著作用,但不能过高,因为硼酸在常温下的溶解度约40g/L左右。 硼酸除了具有缓冲pH值效果外,还有使镀层结晶细致、不易烧焦。若采用高电流密度时,应该采用硼酸含量较高(40g/L)的镀液。 如果加入少量氟化物,它与硼酸形成氟硼酸,则缓冲作用更好。同时,氟化物对某些杂质(如铁)具有掩蔽作用,在这些杂质含量不大时能减轻其害,但不利于这些杂质的去除,氟化物对设备有腐蚀作l用,并且有毒。 4.防针孔
电镀镍故障的影响与原因分析1
电镀镍故障的影响与原因分析 2009-8-12 1.镀镍层表面针孔 镀镍层(包括电镀镍和化学镀镍)表面出现针孔是镀镍中最常见的故障之一,对于镀镍层来说,有针孔就不能有效的防护基体材料,环境中的水分子或其他腐蚀介质就会通过镀层针孔发生腐蚀(图4-1)。针孔大多是镀镍过程中气体(氢气)在镀件表面上停留造成的。针孔既属于麻点,但又不同于麻点,它像流星一样,往往带有向上的"尾巴",而麻点仅仅是镀层上微小的凹坑,一般没有向上的"尾巴",针孔有深有浅,有人把针孔分为三种类型:①基体缺陷型(非圆形凹孔),与基体材料表面缺陷状态有关;②氢气析出型(蝌蚪式针孔),是零件表面析氢痕迹造成的;③氢气停留型(针孔较大,像无柄的梨),是阴极析出氢气停留造成的,一般是镀镍液中表面活性剂太少的原因。图4-1镀镍层表面出现的针孔 造成镀镍层表面针孔原因主要有:零件镀前处理不良,镀液中有油或有机杂质过多,镀液中含有固体微粒,镀液中没有加防针孔剂或防针孔剂太少,镀液中铁等杂质过多,镀液的pH 值太高或阴极电流密度过大,镀液中硼酸含量太少和镀液温度太低等。这些因素都有可能导致镀镍层表面产生针孔缺陷。 由于不同原因引起的针孔现象略有不同,所以在分析故障时,首先要观察故障现象。如镀前处理不良,它仅仅使镀件局部表面上的油或锈未彻底除去,造成这些部位上气体容易停留而产生针孔,所以这种因素造成的针孔现象是局部密集的,无规则的;镀液中有油或有机杂质过多引起的针孔往往出现在零件的向下面和挂具上部的零件上;镀液中固体微粒产生的镀镍层针孔较多出现在零件的向上面;镀液中防针孔剂太少造成的针孔在零件的各个部位都有;镀液中铁杂质过多、pH值过高和阴极电流密度较大引起的针孔较多地出现在零件的尖端和边缘(即高电流密度处),硼酸含量太少产生的针孔较多地出现在零件的下部,镪液温度过低造成的针孔是稀少的,在零件的各个部位都有可能出现。硼酸作为镀镍液中的缓冲剂,含量过低时pH值容易升高,导致形成金属氢氧化物或碱式盐夹杂于镀镍层内,从而使镀层产生针孔、粗糙和发雾等故障,所以镀镍液中硼酸含量,一般不应低于309/L。
电镀脱脂废水处理
废水来源: 电镀行业废水主要分为5类:脱脂废水、含金属离子废水、混合废水、槽脚废水和酸洗综合废水等等。脱脂废水主要来自于电镀工艺的预处理阶段,是对镀件进行刨光、清洗和除油等处理。 排出的废水中主要含有油、酸、碱和部分表面活性剂等物质,一般不含有重金属,处理主要是去除废水中的COD。苏州毅达机电工程有限公司可根据您的需求提供废水低温蒸发浓缩解决方案。 处理方案: 采用蒸发浓缩处理,废水进入低温真空蒸发器,在真空低温条件下蒸发,水蒸气在抽真空过程中冷凝形成蒸馏水,收集至清水储存罐中;剩余的微量废物做下一步处理。 经过废水处理系统真空蒸馏后残留物最低可减少到原有废水量的5%,水蒸气冷凝后几乎不含任何杂质,可作为工艺水送回到生产过程中。 蒸发处理优势: 1、相较于传统蒸发技术,热泵蒸发技术在能耗上可以节约90%以上;
2、其唯一的热源为电。无需任何蒸汽供热或者作为辅助热源,因而大大节省设备的配套设施的投资及消耗; 3、由于热泵其自身可以同时输出冷媒对物料产生的蒸汽进行冷凝,所以无需任何外部的冷却水供应,因而大大节省设备的配套设施及冷却水和电的消耗; 4、模块化设计。设备结构更加紧凑,占地面积小,组装运行快速方便; 5、超低温蒸发。真空度达45mbar,蒸发温度最低可达32℃。更加适合热敏性物料。对于腐蚀性物料对设备的腐蚀程度降到最低,延长设备的寿命; 6、全自动化控制及运行。相较于MVR蒸发器,其操作简单,控制点少,自动化程度更高,故障率低,运行稳定,维修及保养成本极低; 7、由于其规模效应,热泵蒸发器适用于蒸发量低于1000公斤/小时的工况。这很好的解决了中小型企业在污水处理方面投资大,运行维护成本高等的窘境,为我们中小型企业长远健康发展提供了一个非常经济有效的解决方案; 意大利废水浓缩系统应用广泛,包含: ●废水蒸馏 ●废水浓缩
化学镀镍配方成分,化学镀镍配方分析技术及生产工艺
化学镀镍配方成分分析,镀镍原理及工艺技术导读:本文详细介绍了化学镍的研究背景,分类,原理及工艺等,本文中的配方数据经过修改,如需更详细资料,可咨询我们的技术工程师。 禾川化学引进国外配方破译技术,专业从事化学镍成分分析、配方还原、研发外包服务,为化学镍相关企业提供一整套配方技术解决方案。 一、背景 化学镀镍也叫做无电解镀镍,是在含有特定金属盐和还原剂的溶液中进行自催化反应,析出金属并在基材表面沉积形成表面金属镀层的一种优良的成膜技术。化学镀镍工艺简便,成本低廉,镀层厚度均匀,可大面积涂覆,镀层可焊姓良好,若配合适当的前处理工艺,可以在高强铝合金和超细晶铝合金等材料上获得性能良好的镀层,因此在表面工程和精细加工领域得到了广泛应用。 禾川化学技术团队具有丰富的分析研发经验,经过多年的技术积累,可以运用尖端的科学仪器、完善的标准图谱库、强大原材料库,彻底解决众多化工企业生产研发过程中遇到的难题,利用其八大服务优势,最终实现企业产品性能改进及新产品研发。 样品分析检测流程:样品确认—物理表征前处理—大型仪器分析—工程师解谱—分析结果验证—后续技术服务。有任何配方技术难题,可即刻联系禾川化学技术团队,我们将为企业提供一站式配方技术解决方案! 二、化学镀工艺 化学镀工艺流程为:试样打磨-清洗-封孔-布轮抛光-化学除油-水洗-硝酸除锈-水洗-活化-化学镀-水洗-钝化-水洗-热水封闭-吹干。
图1 化学镀的工艺流程图 三、化学镀镍分类 化学镀镍的分类方法种类多种多样,采用不同的分类规则就有不同的分类法。 四、化学镀镍原理 目前以次亚磷酸盐为还原剂的化学镀镍的自催化沉积反应,已经提出的理论有羟基-镍离子配位理论、氢化物理论、电化学理论和原子氢态理论等,其中以原子氢态理论得到最为广泛的认同。 该理论认为还原镍的物质实质上就是原子氢。在以次亚磷酸盐为还原剂还原Ni2+时,可以以下式子表示其总反应: 3NaH2PO2+3H2O+NiSO4→3NaH2PO3+H2SO4+2H2+Ni(1) 也可表达为: Ni2++H2PO2-+H2O→H2PO3-+2H++Ni(2)
化学镀镍的一般操作规范
化学镀镍的一般操作规范 简介 成形的化学镀镍工艺是在1946年被发现及发展的,1955年美国通用运输公司(GA TC)建成了第一条化学镀镍生产线和第一个商品化学镀镍溶液。20世纪80年代,化学镀镍工艺有了巨大的发展,研究和应用达到一个新的水平。按照合金成分分类,化学镀镍可以分为镍-磷合金和镍-硼合金两大类。从应用领域来讲,镍-磷合金使用更为普遍。 化学镀镍-磷合金按照溶液的pH可以分为碱性和酸性化学镀镍,碱性化学镀镍主要用于预镀的打底层,以提高电镀层与基体的结合力,在铝轮毂的电镀中有较成功的应用。酸性化学镀镍工艺是目前化学镀镍中应用最为广泛的工艺,按镀层中的磷含量又可分为低磷(2%~5%)、中磷(6%~9%)和高磷(10%以上)。化学镀镍工艺因为镀层均匀,亮度好,耐蚀性及耐磨性优良而被广泛应用于多个领域。 1. 化学镀镍的周期定义 化学镀镍溶液在使用中的管理与维护非常重要,它与电镀液的管理与维护不同,化学镀镍液中的镍离子等多种成分时刻在不断变化,均需要外加补充,否则溶液不能正常进行。化学镀镍溶液的好坏一般通过能够获得质量稳定镀层的周期(循环系数MTO)来评判。目前市场销售的化学镀镍溶液多数分为A、B、C三种组份,周期数可以做到6~8,对镀层质量要求不严格的可以做到12个周期甚至以上。1个周期的定义是,当溶液中主盐的添加量达到了开缸剂量时为一个周期,以1L溶液为例,开缸量一般为60毫升/升,在使用过程中,当A剂的补充量达到了60毫升时,该化学镀镍溶液就已使用一个周期。 2. 化学镀镍溶液的过程控制 2.1应准确计算槽体容积和零件的表面积 看似再简单不过的问题,但很多时候都难以做到。化学镀镍溶液的消耗及补充与装载量有直接的关系,因此,溶液的装载量应得到重视。装载量就是所要施镀零件的表面积与溶液体积之比值。一般控制在1~1.5 dm2/L为最佳,过大(>2.5 dm2/L)或过小(<0.5 dm2/L)对溶液的稳定性都不好。 首先在配槽前,应准确的测量槽体的容积以及计算所配溶液的合理体积(一般取10的倍数)。 2.2 分析补加记录要全,补加量要准确 溶液补加等数据记录,能够较好的掌握所记录溶液的使用情况,并有针对性的对后续所发生的问题提供信息。化学镀镍溶液的补加应按照说明书的方法进行分析检测,并根据要求比例补加,量取应用带有刻度的量杯或量筒进行,不能随意量取。补加时应搅拌均匀,补加后要注意调整溶液的pH。 补加经验:补加的次数及补加量因不同溶液配方而不同。若镀速在20微米/小时的化学镀镍溶液,在正常操作时,装载量为1 dm2/L,大约每隔30分钟就应进行补加0.6~0.8g金属镍。因此,在施镀25分钟左右时应当进行分析检测。 2.3 随时测量溶液的pH和温度 稳定的溶液pH和工作温度,对镀层质量和镀液的寿命都是有好处的。一般来说,pH
反渗透膜处理镀镍废水工艺设计
反渗透膜技术处理含镍废水 摘要:建立24m'/d电镀镶漂洗水膜法闭路循环回收系统,采用两级反渗透(RO)膜分离技术对电镀废水浓缩50倍以上,23.6m'/d透过液回用到电镀生产线作为漂洗用水,浓缩液再用蒸发器进一步浓缩后直接回到镀槽,废水处理实现闭路循环。从2005年4月到2007年4月,共运行了2年,整个系统运行良好。通过回用水和回收镍等资源,产生较显著的经济、社会和环境效益,实现清洁生产,基本上实现了电镀含镍废水的零排放。 关健询:电镀含镶废水;反渗透膜分离技术;回用水;回收镍 一.电镀 电镀是利用化学或电化学的方法对金属和非目前,电镀废水的治理把握住无害化的原则,金属表面进行装饰、防护及获取某些新性能的一种但是如何更好地实现电镀废水的资源化,回收利用工艺过程,在工业上通用性强,使用面广,几乎所有有用资源,国内外学者进行了广泛深入的研究。本的工业部门( 如机械、机电、交通、电子、仪表、纺织、文重点对各种处理技术进行较为详细的分析,对螯轻工等) 都有电镀厂( 车间) 。但由于电镀厂分散而合沉淀法和NMSTA 天然矿物污水处理剂在电镀废面广,镀件功能要求各异,镀种、镀液组分、操作方水治理中的应用进行了简单介绍,并结合新的排放式及工艺条件等种类繁多,相应带入电镀废水中的标准,对电镀废水处理技术的发展趋向进行展望。 二. 电镀废水来源及特点 电镀废水水质成分不易控制,常见的铬、铜、镍、锌、锡、铅、镉及铁等各种重金 属离子危害性更大,因此被列为当今全球三大污一般的电镀生产工艺由前处理、电镀和后处理工艺三部分组成,每个工艺一定程度上都有废水产生,其中,电 镀生产过程中的镀件漂洗废水是电镀废水的主要来源之一,约占车间废水排放 量的80%以上,废水中大部分的污染物质是由镀件表面的附着液在漂洗时带 入的; 镀液过滤废水是指在镀液过滤过程中,滴漏的镀液以及在过滤前后冲洗
钢铁的化学镀镍磷
钢铁的化学镀镍磷 金属1002 陈浩 3100702039 摘要:本文简要介绍了钢铁化学镀镍磷的原理与工艺流程,简述了镀层的性能及技术指标,随之分析了影响镀层性能的主要因素,并据此给出了工艺中的除锈配方和镀液配方,最后对试验参数进行了测定与比较,得出了一定的结论。 关键词:化学镀镀镍磷表面强化耐磨耐腐蚀性 一.前言 化学镀镍磷工艺是近年来迅速发展起来的一种新型表面保护和表面强化技术手段,具有广泛的应用前景。目前化学镀镍磷合金已广泛地应用在石油化工、石油炼制、电子能源、汽车、化工等行业。石油炼制和石油化工是其最大的市场,并且随着人们对这一化学镀特性的认识,它的应用也越来越广泛,主要用在石油炼制、石油化工的冷换设备上,化学镀镍磷能够显著提高设备的耐磨、耐蚀性能,延长其寿命,性能优于目前使用的有机涂料,而且适用于碳钢、铸铁、有色金属等不同基材。 二.实验原理 化学镀镍磷合金是一种在不加电流的情况下,利用还原剂在活化零件表面上自催化还原沉积得到镍磷镀层的方法。其主要反应为应用次亚磷酸钠还原镍离子为金属镍,即在水溶液中镍离子和次亚磷酸根离子碰撞时,由于镍触媒作用析出原子态氢,而原子态氢又被催化金属吸附并使之活化,把水溶液中的镍离子还原为金属镍形成镀层,另外次亚磷酸根离子由于在催化表面析出原子态氢的作用,被还原成活性磷,与镍结合形成Ni-P合金镀层。 以次磷酸钠为还原剂的化学镀镍磷工艺,其反应机理,现普遍被接受的是“原子氢态理论”和“氢化物理论”。下面介绍“原子氢态理论”,其过程可分为以下四步: 1、化学沉积镍磷合金镀液加热时不起反应,而是通过金属的催化作用,次亚磷酸根在水溶液中脱氢而形成亚磷酸根,同时放出初生态原子氢。 H 2PO 2 -+H 2 O→HPO 3 -+2H+H-
镀镍
镀镍 一:什么是镀镍? 通过电解或化学方法在金属或某些非金属上金上一层镍的方法,称为镀镍。镀镍分电镀镍和化学镀镍。 电镀镍是在由镍盐(称主盐)、导电盐、pH缓冲剂、润湿剂组成的电解液中,阳极用金属镍,阴极为镀件,通以直流电,在阴极(镀件)上沉积上一层均匀、致密的镍镀层。从加有光亮剂的镀液中获得的是亮镍,而在没有加入光亮剂的电解液中获得的是暗镍。 化学镀镍是在加有金属盐和还原剂等的溶液中,通过自催化反应在材料表面上获得镀镍 层的方法。 二:镀镍的特点、性质、用途 (一)电镀镍的特点、性能、用途: 1 电镀镍层在空气中的稳定性很高,由于金属镍具有很强的钝化能力,在表面能迅速生成一层极薄的钝化膜,能抵抗大气、碱和某些酸的腐蚀。 2 电镀镍结晶极其细小,并且具有优良的抛光性能。经抛光的镍镀层可得到镜面般的光泽外表,同时在大气中可长期保持其光泽。所以,电镀层常用于装饰。 3 镍镀层的硬度比较高,可以提高制品表面的耐磨性,在印刷工业中常用镀媒层来提高铅表面的硬度。由于金属镍具有较高的化学稳定性,有些化工设备也常用较厚的镇镀层,以防止被介质腐蚀。镀镍层还广泛的应用在功能性方面,如修复被磨损、被腐蚀的零件,采用刷镀技术进行局部电镀。采用电铸工艺,用来制造印刷行业的电铸版、唱片模以及其它模具。厚的镀镍层具有良好的耐磨性,可作为耐磨镀层。尤其是近几年来发展了复合电镀,可沉积出夹有耐磨微粒的复合镍镀层,其硬度和耐磨性比镀镍层更高。若以石墨或氟化石墨作为分散微粒,则获得的镍-石墨或镍-氟化石墨复合镀层就具有很好的自润滑性,可用作为润滑镀层。黑镍镀层作为光学仪器的镀覆或装饰镀覆层亦都有着广泛的应用。 4 镀镍的应用面很广,可作为防护装饰性镀层,在钢铁、锌压铸件、铝合金及铜合金表面上,保护基体材料不受腐蚀或起光亮装饰作用;也常作为其他镀层的中间镀层,在其上再镀一薄层铬,或镀一层仿金层,其抗蚀性更好,外观更美。在功能性应用方面,在特殊行业的零件上镀镍约1~3mm厚,可达到修复目的。特别是近年来在连续铸造结晶器、电子元件表面的模具、合金的压铸模具、形状复杂的宇航发动机部件和微型电子元件的制造等方应用越来越广泛。 5 在电镀中,由于电镀镍具有很多优异性能,其加工量仅次于电镀锌而居第二位,其消耗量占到镍总产量的10%左右。 (二)化学镀镍的特点、性能、用途: 1 厚度均匀性厚度均匀和均镀能力好是化学镀镍的一大特点,也是应用广泛的原因之一,化学镀镍避免了电镀层由于电流分布不均匀而带来的厚度不均匀。化学镀时,只要零件表面和镀液接触,镀液中消耗的成份能及时得到补充,镀件部位的镀层厚度都基本相同,即使凹槽、缝隙、盲孔也是如此。 2. 镀件不会渗氢,没有氢脆,化学镀镍后不需要除氢。 3. 很多材料和零部件的功能如耐蚀、抗高温氧化性等比电镀镍好。 4. 可沉积在各种材料的表面上,例如:钢镍基合金、锌基合金、铝合金、玻璃、陶瓷、塑料、半导体等材料的表面上,从而为提高这些材料的性能创造了条件。 5. 不需要一般电镀所需的直流电机或控制设备。 6 热处理温度低,只要在400℃以下经不同保温时间后,可得到不同的耐蚀性和耐磨性,因此,特别适用于形状复杂,表面要求耐磨和耐蚀的零部件的功能性镀层等 三:镀镍溶液的类型 镀镍液的类型主要有硫酸盐型、氯化物型、氨基磺酸盐型、柠檬酸盐型、氟硼酸盐型等。其中以硫酸盐型(低氯化物)即称之谓Watts(瓦特)镀镍液在工业上的应用最为普遍。几
国内电镀废水处理现状
国内电镀废水处理现状 国内电镀行业屑于劳动密集型的“三来一补”企业,耗能高、排污量大、产品附加值相对较低,对环境的污染危害性较大,属重污染行业,已不符合现今发展循环经济的理念,因此,政府对这类工艺落后、污染严重的企业态度明确,以政策法规和技术支撑为保障,实施生态化改造,强化管理、逐步淘汰,对超标排放而又治理无望的企业,注册期到,一律终止,工商部门不再续期办理营业执照。执行“严格管理、提高效益、保护环境、实现资源有效利用”的策略。 珠三角电镀品种有印制电路板、电子元器件、电脑配件、汽车部件、眼镜、卫生洁具、摩托车配件、家电、灯具、门锁、五金件、首饰、钟表等。电镀工艺有普通电镀、化学镀、复合电镀、脉冲电镀、电铸、机械镀、真空蒸镀、离子镀。单一金属有锌、铜、镍、铬、锡、金、银、铀、铑、钯、铟等。二元合金有铜基的铜镍、铜锌、铜锡;锌基的锌铜、锌镍、锌铁、锌钴;镍基的镍磷、镍钴;锡基的锡锌、锡镍、锡钴。三元合金有铜镍铬、锡钴锌。在色彩方面有黑镍、沙丁镍、黑铬、沙丁铬、枪色、古铜、光亮铜、光亮镍、彩色钝化膜、蓝白色。基体材料有金属、铝、工程塑料等。 (一)管理现状 随着经济的发展,环境保护的工作越来越得到重视,国家成立了环境保护部,2009年,各省相继成立环境保护厅,从组织上给予开展该项工作的保证。政府对电镀企业进行强制管理是从2002年正式开始,从这时起,电镀废水的处理有了较快的发展,人们由不认识到较熟练地掌握废水处理技术,设备由简单的几个池子,发展到今天的半自动控制的连续处理,技术、设备、管理上都取得了很大的成绩,一些难处理、多年难以解决的技术问题都已克服,政府倡导的环保意识已普及,企业界接受了“严格管理、提高效益、保护环境、实现资源有效利用”这个理念,并逐渐自觉接受强制管理。 1.政策管理 (1)国家出台了《中华人民共和国固体废物污染环境防治法》,各省市也出台了相应的文件,对产生工业固体废物(电镀废水厂产生大量污泥)的单位强行建立、健全污染环境治理赍任制度:①电镀企业成立时要经过严格审批,要备齐一系列资料,如环保审批批文,污染防治设施的评估报告书和验收资料,生产工艺流程图,投资生产规模,产品种类和数量、原辅材料种类及数量、产生的工业固体废物特别是危险废物种类数量及其收集、忙存、转移、处理情况等;②执法人员采取现场监测、采集样品、拍摄现场等措施进行监管;③重视电镀企业布局,在深圳等经济发达地区已不允许再新建电镀厂,已有的集中到工业园区,按环保局的标准进行整改,达不到要求的强制关闭。 (2)国家实行工业固体废物申报登记制度,要求有关单位如实向环保主管部门申报工业固体废物的种类、产生量、把存、流向、处置等有关资料,如有重大改变,应当及时办理变更申报登记,产生危险废物的单位必须按照国家有关规定制定危险废物管理计划、意外事故的防范措施和应急预案,并向环保主管部门备案。
化学镀镍
化学镀镍 1 化学镀的定义 化学镀是在无电流通过(无外界动力)时借助还原剂在同一溶液中发生的氧化还原作用,从而使金属离子还原沉积在零件表面上的一种镀覆方法. M n+ + ne(由还原剂提供的) 催化表面M0 2 化学镀与电镀的区别 电镀是利用外电流将电镀液中的金属离子在阴极上还原成金属的过程。而化学镀是不外加电流,在金属表面的催化作用下经化学还原法进行的金属沉积过程。 3 化学镀的优缺点 优点: (1)可以在由金属,半导体和非导体等各种材料制成的零件上镀覆金属。 (2)无论零件的几何形状如何复杂,凡能接触到溶液的地方都能获得厚度均匀的镀层。 (3)可以获得较大厚度的镀层,甚至可以电铸。 (4)无需电源。 (5)镀层致密,孔隙小。 (6)镀层往往具有特殊的化学,机械或磁性能。 缺点: (1)溶液稳定性差,溶液维护,调整和再生等比较麻烦,成本比电镀高。 (2)镀层常显示出较大的脆性。 4 化学镀镍和电镀镍制品性能比较
5 化学镀能获得镀层的构成 (1)纯金属镀层,如C u Sn Ag Au Ru Pd (2)二元合金镀层,如Ni—P Ni—B C o—P C o—B (3)三元及四元合金镀层,如Ni—Co—P Ni—W—Sn—P (4)化学复合镀层 6 化学镀镍的定义 化学镀镍,又称为无电解镀镍,是在金属盐和还原剂共同存在的溶液中靠自催化的化学反应而在金属表面沉积了金属镀层的成膜技术. 7 化学镀镍的基本工艺 如同其他湿法表面处理一样,化学镀镍包括镀前处理、施镀操作、镀后处理各部分工艺序列组成,正确地实施工艺全过程才能获得质量合格的镀层。然而,与电镀工艺比较,化学镀镍工艺全过程应格外仔细。化学镀取决于在工件表面均匀一致的、迅速成的初始状态(起镀过程),化学镀镍并无外力启动和帮助克服任何表面缺陷;于是,工件一进入镀液即形成均匀一致的沉积界面,这一点很重要,因为化学镀是靠表面条件启动的,即异相表面自催化反应,而不是电力。一般来说,化学镀镍液比较电镀液更加敏感娇弱。其中各项化学成份的平衡、工艺参数的可操作范围比较狭窄;对于污染物的耐受能力较差,甚至ppm级的重金属离子就可能造成镀层性能恶化或漏镀、停镀;考虑到化学镀液的寿命,比较电镀液而言,十分有限,需要给予更多的维护,尽可能延长化学镀液寿命是十分重要的。 8 化学镀镍的简单原理 第一步溶液中的次磷酸根在催化表面上催化脱氢,同时氢化物离子转移到催化表面,而本身氧化成亚磷酸根。 [H 2PO 2]—+ H 2O 催化表面[HPO3] 2—+ H++ 2[H]—(吸附于催化表面) 第二步吸附于催化表面上的活性氢化物与镍离子进行还原反应而沉积镍,而本身氧化成氢气。 Ni2++ 2[H]—Ni0 + H2 总反应式为 2H 2PO 2—+ 2H 2O + Ni2+ Ni0 + H2 + 4 H++ 2HPO32— 部分次磷酸根被氢化物还原成单质磷,同时进入镀层 H 2PO 2—+ [H]—(催化表面)P + H 2O + OH— 上述还原反应是周期地进行的,其反应速度取决于界面上的pH值。pH值较高时,镍离子还原容易;而pH值较低时磷还原变得容易,所以化学镀镍层中含磷量随pH值升高而降低。 除上述反应外,化学镀中还有副反应发生,即 H 2PO 2—+ H 2O 催化表面H++ [H PO 3]2—+ H2 Ni 加入槽中的次磷酸盐最终约90%转化为亚磷酸盐, 亚磷酸镍溶解度低,当有络合剂存在,游离镍离子少时,不产生沉淀物.当有亚磷酸镍固体沉淀物存在时,将触发溶液的自分解.在化学镀中不可避免地会有微量的镍在槽壁和镀液中析出,容易导致自催化反应在均相中发生,需要用稳定剂加以控制.反应中生成的氢离子将降低镀液pH值,从而降低沉积速度,所以需加pH值缓冲剂及时调整pH值.
高考化学反应中的能量变化
2009年高考化学试题分类汇编——化学反应中的能量变化 1.(09全国卷Ⅱ11) 已知:2H 2(g )+ O 2(g)=2H 2O(l) ΔH= -571.6KJ · mol -1 CH 4(g )+ 2O 2(g)=CO 2(g)+2H 2O(l) ΔH= -890KJ · mol -1 现有H 2与CH 4的混合气体112L (标准状况),使其完全燃烧生成CO 2和H 2O(l),若实验测得反应放热3695KJ ,则原混合气体中H 2与CH 4的物质的量之比是 A .1∶1 B .1∶3 C .1∶4 D .2∶3 答案:B 解析: 设H 2、CH 4的物质的量分别为x 、ymol 。则x + y =5,571.6x/2 + 890y = 3695,解得x=1.25mol; y=3.75mol ,两者比为1:3,故选B 项。 2.(09天津卷6)已知:2CO(g)+O 2(g)=2CO 2(g) ΔH=-566 kJ/mol Na 2O 2(s)+CO 2(g)=Na 2CO 3(s)+ 21O (g)2 ΔH=-226 kJ/mol 根据以上热化学方程式判断,下列说法正确的是 A.CO 的燃烧热为283 kJ B.右图可表示由CO 生成CO 2的反应过程和能量关系 C.2Na 2O 2(s)+2CO 2(s)=2Na 2CO 3(s)+O 2(g) ΔH >-452 kJ/mol D.CO(g)与Na 2O 2(s)反应放出509 kJ 热量时,电子转移数为6.02×1023 答案:C 解析:A 项,燃烧热的单位出错,应为Kj/mol ,错;图中的量标明错误,应标为2molCO 和2molCO 2,故错。CO 2气体的能量大于固体的能量,故C 项中放出的能量应小于452KJ,而H 用负值表示时,则大于-452Kj/mol ,正 确;将下式乘以2,然后与上式相加,再除以2,即得CO 与Na 2O 2的反应热,所得热量为57KJ ,故D 项错。 3. (09四川卷9)25 ℃,101 k Pa 时,强酸与强碱的稀溶液发生中和反应的中和热为57.3 kJ/mol ,辛烷的燃烧热为5518 kJ/mol 。下列热化学方程式书写正确的是 A.2H +(aq) +24SO -(aq)+2Ba +(aq)+2OH -(aq)=BaSO 4(s)+2H 2O(1);?H=-57.3 kJ/mol B.KOH(aq)+ 12H 2 SO 4(aq)= 12K 2SO 4(aq)+H 2O(I); ?H=-57.3kJ/mol C.C 8H 18(I)+ 252 O 2 (g)=8CO 2 (g)+ 9H 2O; ?H=-5518 kJ/mol D.2C 8H 18(g)+25O 2 (g)=16CO 2 (g)+18H 2O(1); ?H=-5518 kJ/mol 答案:B
ASTM B-733-97 金属表面化学镀镍磷层规范标准
Designation:B733–97 Standard Speci?cation for Autocatalytic(Electroless)Nickel-Phosphorus Coatings on Metal1 This standard is issued under the?xed designation B733;the number immediately following the designation indicates the year of original adoption or,in the case of revision,the year of last revision.A number in parentheses indicates the year of last reapproval.A superscript epsilon(e)indicates an editorial change since the last revision or reapproval. This standard has been approved for use by agencies of the Department of Defense. 1.Scope 1.1This speci?cation covers requirements for autocatalytic (electroless)nickel-phosphorus coatings applied from aqueous solutions to metallic products for engineering(functional)uses. 1.2The coatings are alloys of nickel and phosphorus pro-duced by autocatalytic chemical reduction with hypophosphite. Because the deposited nickel alloy is a catalyst for the reaction, the process is self-sustaining.The chemical and physical properties of the deposit vary primarily with its phosphorus content and subsequent heat treatment.The chemical makeup of the plating solution and the use of the solution can affect the porosity and corrosion resistance of the deposit.For more details,see ASTM STP265(1)2and Refs(2)(3)(4)and(5) also refer to Figs.X1.1,Figs.X1.2,and Figs.X1.3in the Appendix of Guide B656. 1.3The coatings are generally deposited from acidic solu-tions operating at elevated temperatures. 1.4The process produces coatings of uniform thickness on irregularly shaped parts,provided the plating solution circu-lates freely over their surfaces. 1.5The coatings have multifunctional properties,such as hardness,heat hardenability,abrasion,wear and corrosion resistance,magnetics,electrical conductivity provide diffusion barrier,and solderability.They are also used for the salvage of worn or mismachined parts. 1.6The low phosphorus(2to4%P)coatings are microc-rystalline and possess high as-plated hardness(620to750HK 100).These coatings are used in applications requiring abra-sion and wear resistance. 1.7Lower phosphorus deposits in the range between1and 3%phosphorus are also microcrystalline.These coatings are used in electronic applications providing solderability,bond-ability,increased electrical conductivity,and resistance to strong alkali solutions. 1.8The medium phosphorous coatings(5to9%P)are most widely used to meet the general purpose requirements of wear and corrosion resistance. 1.9The high phosphorous(more than10%P)coatings have superior salt-spray and acid resistance in a wide range of applications.They are used on beryllium and titanium parts for low stress properties.Coatings with phosphorus contents greater than11.2%P are not considered to be ferromagnetic. 1.10The values stated in SI units are to be regarded as standard. 1.11The following precautionary statement pertains only to the test method portion,Section9,of this speci?cation.This standard does not purport to address all of the safety concerns, if any,associated with its use.It is the responsibility of the user of this standard to establish appropriate safety and health practices and determine the applicability of regulatory limita-tions prior to use. 2.Referenced Documents 2.1ASTM Standards: B368Test Method for Copper-Accelerated Acetic Acid-Salt Spray(Fog)Testing(CASS Testing)3 B374Terminology Relating to Electroplating3 B380Test Method of Corrosion by the Corrodkote Proce-dure3 B487Test Method for Measurement of Metal and Oxide Coating Thicknesses by Microscopical Examination of a Cross Section3 B499Test Method for Measurement of Coating Thick-nesses by the Magnetic Method:Nonmagnetic Coatings on Magnetic Basis Metals3 B504Test Method for Measurement of Thickness of Me-tallic Coatings by the Coulometric Method3 B537Practice for Rating of Electroplated Panels Subjected to Atmospheric Exposure3 B567Method for Measurement of Coating Thickness by the Beta Backscatter Method3 B568Method for Measurement of Coating Thickness by X-Ray Spectrometry3 1This speci?cation is under the jurisdiction of ASTM Committee B-08on Metal Powders and Metal Powder Products and is the direct responsibility of Subcom- mittee B08.08.01on Engineering Coatings. Current edition approved July10,1997.Published October1997.Originally published as B733–https://www.360docs.net/doc/179732336.html,st previous edition B733–90(1994). 2The boldface numbers given in parentheses refer to a list of references at the end of the text.3Annual Book of ASTM Standards,V ol02.05. 1 Copyright?ASTM International,100Barr Harbor Drive,PO Box C700,West Conshohocken,PA19428-2959,United States.