催化反应动力学数据测定
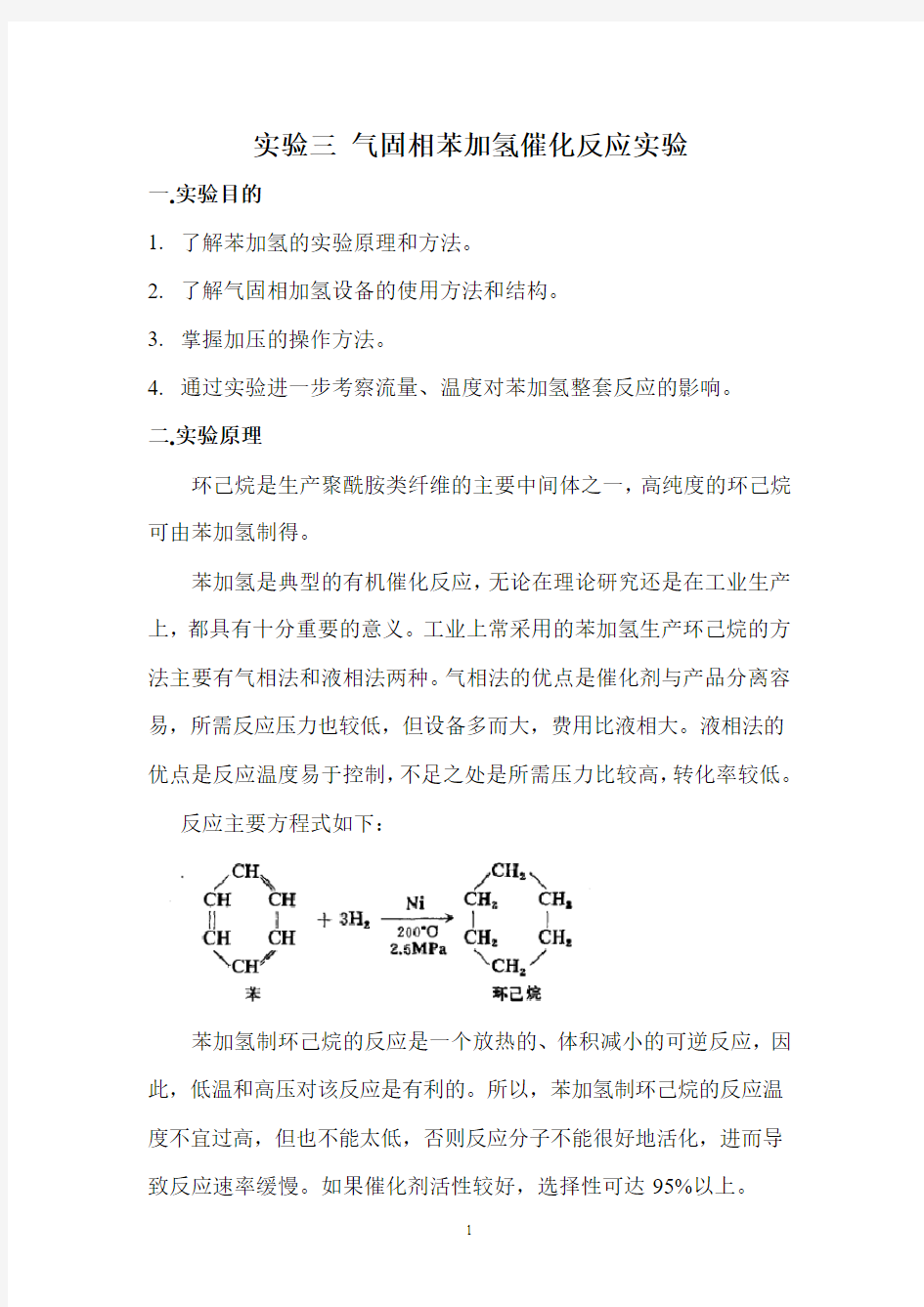

实验三气固相苯加氢催化反应实验
一.实验目的
1.了解苯加氢的实验原理和方法。
2.了解气固相加氢设备的使用方法和结构。
3.掌握加压的操作方法。
4.通过实验进一步考察流量、温度对苯加氢整套反应的影响。
二.实验原理
环己烷是生产聚酰胺类纤维的主要中间体之一,高纯度的环己烷可由苯加氢制得。
苯加氢是典型的有机催化反应,无论在理论研究还是在工业生产上,都具有十分重要的意义。工业上常采用的苯加氢生产环己烷的方法主要有气相法和液相法两种。气相法的优点是催化剂与产品分离容易,所需反应压力也较低,但设备多而大,费用比液相大。液相法的优点是反应温度易于控制,不足之处是所需压力比较高,转化率较低。
反应主要方程式如下:
苯加氢制环己烷的反应是一个放热的、体积减小的可逆反应,因此,低温和高压对该反应是有利的。所以,苯加氢制环己烷的反应温度不宜过高,但也不能太低,否则反应分子不能很好地活化,进而导致反应速率缓慢。如果催化剂活性较好,选择性可达95%以上。
本实验选择在加压固定床中进行催化反应,催化剂采用r-Al 2O 3
载Ni 或Cu 。
原料:苯,氢气,氮气(吹扫用),环己烷
三、流程示意图与面板布置图
1、流程示意图
V -截止阀,S -三通转换阀,T C I -控温,T I -测温,P I -测压
气体钢瓶, 过滤器, 稳压阀
, 干燥器, 质量流量计,止逆阀缓冲器, 预热器, 预热炉,
反应炉,
反应器
,
冷却
器
气
液分离器背压阀, 取样器,湿式流量计, 加料泵
2、面板布置图
四.实验步骤
1、装填20ml催化剂
打开反应加热炉,卸下反应器的上下盖法兰的连接口接头,从炉内取出反应器(拆卸时先将热电偶插件拔出)。在设备外部将上下法兰压紧螺栓松开,旋转推出,若反应器内上部有玻璃棉,用带有倒钩的不锈钢丝将它取出,并倒出催化剂,再取出反应器下部的玻璃棉,最后用镊子夹住沾有丙酮的脱脂棉擦拭一下,同样擦拭反应器内部,用吸耳球吹干。这时要注意,反应器内有测温套管,不能将它碰歪。若感到不方便,可将下法兰也卸下来,这样就很好清洗了。装填催化剂时要先将下法兰装好,后装好支撑架测好位置,装玻璃棉,倒入催化剂,最后再装入玻璃棉。上好上法兰,拧紧螺栓放回反应炉内支撑好,再次连接出入口接头,插入热电偶(其底端位置应根据装在反应器内催化剂的高度而定。催化剂的加入量以实验的要求而定,单位的取舍是根据空速单位而定,由此选择称量重量还是测量体积。装催化剂要通过小漏斗装入反应器。装填时要轻轻震动反应器使催化剂均匀分布,催化剂上部再放入少许玻璃棉。
注意:安装反应器和上开启炉子一定要轻轻操作,拧紧接头时要用力适当不能过力,以免损坏接口螺纹。
2、系统试漏
<1>确定操作压力,关闭尾气出口阀门、背压阀。
<2>检查气体和液体进口连接点是否紧密,确定反应物是气体还是液体,如果使用可燃性液体或气体,要用氮吹扫后再进气充压(打开气体钢瓶阀门,调节调压阀,开质量流量计电源,给定流量才能使气体进入系统),通过下列方法可初步确定是否泄漏:关闭系统排气阀门,打开进气阀,顺时针方向调节稳压阀,质量流量计有流量显示,如果没有泄漏则流量逐渐下降直到接近于零,否则一定有泄漏的地方。这时要用肥皂水检查各个接口点。注意!质量流量计使用要开机预热十分钟,详见质量流量计使用说明书。试漏工作应很仔细的进行。
3、打开温度控制电源,将预热器温度控制仪温度给定在200℃并通入氢气进入催化剂加氢还原,氢气的流速控制在80ml/min,一段时间后温度会上升,调节给定温度使其不超过250℃为宜,还原活化2个小时后降温,在150℃时开启苯的加料泵,观察在三通阀通大气的一侧有液体流出后,转动三通阀进液至预热器并观察预热器和反应器的温度有无变化。苯的进料流量0.4ml/hr,转子流量计流量:50-100 ml/min,反应时间30min。进料后要调节背压阀,使反应压力维持在2.0MPa。当反应结束后,可取样分析产物,最后取出液体称量,分析含量。
五、气相色谱仪检测条件
GC类型:热导池;填充柱1.5m
柱前压:0.1MPa;气化温度:120℃;柱箱温度:100℃;检测器温度:120℃;桥电流:100mA;色谱柱类型:620n1(担体载癸二酸二异辛
酯20%)
六、实验数据及分析方法
根据实验内容自行设计记录表格,记录实验数据: 1、原始记录:
2、分析结果
3、按下式处理数据
00100 原料中苯量量
原料中苯量-产物中苯苯转化率=
00100mol)
mol)
反应的苯量(生成环己烷量(环己烷选择性=
环己烷收率=转化率x 选择性 七、 思考题: 1、实验中如何进行系统试漏? 2、实验中如何进行升温?
催化反应动力学
催化反应动力学研究小报告 催化反应大致可以分为三大类: (1)均相催化:催化剂与反应物处于同一相种,均为气相或均为液相; (2)复相催化:催化剂与反应物处于不同相中,如Fe 对合成氨的催化作用; (3)生物催化:即酶催化,如制酒过程中的发酵作用。酶是蛋白质或核酸分子组成,而分子很大,因此它既不属于均相也不属于复相,而是兼备二者的某些特性。本文将对这三种催化反应的反应动力学进行具体文献分析。 1.均相催化反应动力学研究 在均相催化反应中,催化剂和反应物同处于液相或者气相。其机理为首先反应物和催化剂生成不稳定的中间化合物,然后中间化合物又分解生成产物,使催化剂再生。 陈荣悌[1]等人以H g C I 2为催化剂时乙炔氢氯化制氯乙烯均相反应的动力学。 反应方程如下: 设速率方程为: 因为在一次实验中, 催化剂浓度是不变的, 而且当〔H +〕、〔Cl -〕均远大于〔C H ≡C H 〕时, 则速率方程可写成: 第一步:确定反应对乙炔的级数 当反应为一级或假一级反应时,可推导出如下公式: 本反应以)ln(P P -∞对t 线性回归, 其相关系数在0.99 以上。表明反应对乙炔为一级。 第二步:消除扩散影响的实验
为了消除扩散的影响,作者作了改变搅拌速度对速率常数影响的实验。当转速在1 3 85 转/ 分以上时,k′′值趋于稳定, 即扩散影响基本消除。全部实验中皆控制搅拌速度在1 3 8 5 转/分以上进行。 第三步:确定反应对催化剂H g CI2的级数 改变H g CI 2的浓度, 分别求出k′′值, 以l g k′′对lg〔H g C I2〕线性回归, 相关系数R =0 . 9 9 6 , 斜率为1 . 0 4 6 , 即m为1, 说明反应对催化剂H g C I2为一级。 第四步:确定反应对C l-的级数 在盐酸浓度为5.37 M 的基础上分别加入H C I O 4,使〔H C I〕+ 〔H C IO4〕= 6.2 7M 和7.16M , 并与单纯的〔H C I〕= 6.2 7M 和7.1 6M 的实验相比较发现当〔C l -〕足够大时( 因为生成H g C I2需足够的C l-) , 反应对C I-零级。 第五步:确定反应对H +的级数 由于反应对Cl-为零级, 因此可以通过改变盐酸浓度来确定反应对H+ 的级数以lgk′′对lg 〔H + 〕线性回归, 相关系数R = 0 .98 1 , 斜率为3 .07, 即n=3 , 说明反应对H+为三级。 第六步:求反应的表观活化能 在相同的条件下, 改变温度进行实验, 分别求出k′′值。以lnk′′对l/ T 线性回归, 相关系数R =0 . 9 9 7, 斜率为-6 8 21 , 从斜率求出表观活化能E =1 3 . 6千卡/ 摩尔。 最后该反应速率方程为: 2.复相催化反应动力学研究 复相催化主要是用固体酸催化气相反应或者液相反应。催化作用是通过表面来实现的,目前理论都不能完善解释其中机理,但活性中心的性质的解释是各种理论的共同点。 祁喜旺[2]等人采用经巯基乙胺改性的大孔磺酸型离子交换树脂作催化剂,在60-80℃, 原料酚/酮( mol比)为4:1-12:1的范围内研究了由苯酚与丙酮合成双酚A的催化反应动力学。 反应方程为:
催化反应动力学数据测定
实验三气固相苯加氢催化反应实验 一.实验目的 1.了解苯加氢的实验原理和方法。 2.了解气固相加氢设备的使用方法和结构。 3.掌握加压的操作方法。 4.通过实验进一步考察流量、温度对苯加氢整套反应的影响。 二.实验原理 环己烷是生产聚酰胺类纤维的主要中间体之一,高纯度的环己烷可由苯加氢制得。 苯加氢是典型的有机催化反应,无论在理论研究还是在工业生产上,都具有十分重要的意义。工业上常采用的苯加氢生产环己烷的方法主要有气相法和液相法两种。气相法的优点是催化剂与产品分离容易,所需反应压力也较低,但设备多而大,费用比液相大。液相法的优点是反应温度易于控制,不足之处是所需压力比较高,转化率较低。 反应主要方程式如下: 苯加氢制环己烷的反应是一个放热的、体积减小的可逆反应,因此,低温和高压对该反应是有利的。所以,苯加氢制环己烷的反应温度不宜过高,但也不能太低,否则反应分子不能很好地活化,进而导致反应速率缓慢。如果催化剂活性较好,选择性可达95%以上。
本实验选择在加压固定床中进行催化反应,催化剂采用r-Al 2O 3 载Ni 或Cu 。 原料:苯,氢气,氮气(吹扫用),环己烷 三、流程示意图与面板布置图 1、流程示意图 V -截止阀,S -三通转换阀,T C I -控温,T I -测温,P I -测压 气体钢瓶, 过滤器, 稳压阀 , 干燥器, 质量流量计,止逆阀缓冲器, 预热器, 预热炉, 反应炉, 反应器 , 冷却 器 气 液分离器背压阀, 取样器,湿式流量计, 加料泵
2、面板布置图
四.实验步骤 1、装填20ml催化剂 打开反应加热炉,卸下反应器的上下盖法兰的连接口接头,从炉内取出反应器(拆卸时先将热电偶插件拔出)。在设备外部将上下法兰压紧螺栓松开,旋转推出,若反应器内上部有玻璃棉,用带有倒钩的不锈钢丝将它取出,并倒出催化剂,再取出反应器下部的玻璃棉,最后用镊子夹住沾有丙酮的脱脂棉擦拭一下,同样擦拭反应器内部,用吸耳球吹干。这时要注意,反应器内有测温套管,不能将它碰歪。若感到不方便,可将下法兰也卸下来,这样就很好清洗了。装填催化剂时要先将下法兰装好,后装好支撑架测好位置,装玻璃棉,倒入催化剂,最后再装入玻璃棉。上好上法兰,拧紧螺栓放回反应炉内支撑好,再次连接出入口接头,插入热电偶(其底端位置应根据装在反应器内催化剂的高度而定。催化剂的加入量以实验的要求而定,单位的取舍是根据空速单位而定,由此选择称量重量还是测量体积。装催化剂要通过小漏斗装入反应器。装填时要轻轻震动反应器使催化剂均匀分布,催化剂上部再放入少许玻璃棉。 注意:安装反应器和上开启炉子一定要轻轻操作,拧紧接头时要用力适当不能过力,以免损坏接口螺纹。 2、系统试漏 <1>确定操作压力,关闭尾气出口阀门、背压阀。
催化反应动力学报告
催化裂化集总反应动力学模型研究进展 摘要:分析和介绍了国内外催化裂化装置建模和稳态模拟方面的研究和进展。对催化裂化反应集总方法及相应的反应网络进行归纳,并讨论其优缺点;推导了动力学模型方程并着重探讨方程求解算法以及模型中动力学参数、催化剂失活因子和装置因素的估计方法。对催化裂化集总反应动力学模型的研究进展进行了综述,从中可见复杂反应体系集总反应动力学模型的发展历程。 1.引言 催化裂化是炼油工业最重要的二次加工工艺之一,其目的是将重质油转化成更有价值的轻端产品。由于油品组成复杂,很难用常规的动力学方法研究该高度偶联的反应体系,集总(1umping)理论的出现为催化裂化反应动力学的研究开辟了新的途径。近些年来,催化裂化在新技术、新工艺等方面取得了很大的进展,同时在集总动力学模型的开发和应用研究上也取得了引人注目的成绩。如蜡油的三集总、四集总、五集总、十集总、十一集总和渣油的六集总、十一集总、十三集总等动力学模型的开发,其中有些模型已经成功地应用于工业装置并取得明显的经济效益。本论文将综合评述催化裂化集总动力学模型的研究现状,为模型的进一步开发和研究提供指导。 1963年由Aris 等和We i 等创立的反应速率常数矩阵法,解决了复杂反应体系内反应强耦联这一难题,使对复杂的耦联反应体系进行解耦成为了可能。但由于复杂反应体系内原料与产物组分繁多,且每一组分又能进行不止一种的反应,故而建立详细描述每一组分反应行为的动力学模型是不可能的,必须进行一定的简化处理。所谓集总即是将反应系统中众多的单一化合物,按其动力学特性相似的原则,归并为若干个虚拟的单一组分(集总),然后去开发这些虚拟的集总组分间的反应网络,建立简化了的集总反应网络的动力学模型。集总反应动力学模型是在深刻认识反应机理的基础上将复杂的反应网络简化处理,从而开辟了一条动力学研究的新途径。集总理论最早应用于催化裂化过程,其后又应用于催化重整、延迟焦化、渣油加氢等其它过程。本文将通过回顾、总结催化裂化集总反应动力学模型的发展来见证集总理论及集总反应动力学模型的发展历程。 2 催化裂化集总反应动力学模型集总划分原则的发展 从集总划分原则的角度,可将催化裂化集总反应动力学模型的发展分为三个阶段。 2.1 第一阶段 20世纪60年代后期,Week man 等最早将集总理论成功运用于催化裂化过程,建立了催化裂化三集总反应动力学模型。该模型根据馏程的不同将反应物和产物归并为未转化的原料油、汽油和气体+ 焦炭三个集总。结果表明该模型能够较准确地预测给定原料油的转化率、生成汽油的选择性和最佳操作条件等。由于该模型参数少,计算简便,预测结果准确,在指导工业装置设计操作优化等方面显示出了强大的作用。催化裂化三集总反应动力学模型开创了集总理论在催化裂化反应动力学领域应用的先河,它肯定了将集总方法运用于复杂
化工动力学
1、CO在钯催化剂上的抵押氧化动力学 从该反应速率方程式中可以看出, 反应速率与TiO2表面吸附的O浓度和Pt 表面吸附的CO浓度呈正比
2、合成氨催化反应动力学 氨合成为气固相催化反应,它的宏观动力学过程包括以下几个步骤。 ①氮氢气体从气流主体扩散到催化剂颗粒的外表面----外扩散②反应物从外表面向催化剂的孔道内部扩散----内扩散 ③反应物被催化剂吸附----吸附④在催化剂内部孔道内组成的内表面上进行催化反应----化学反应⑤产物从催化剂表面脱附----脱附⑥产物从催化剂内表面扩散到外表面----内扩散⑦产物从外表面扩散到气流主体----外扩散 氮、氢气在催化剂表面反应机理,可表示为: N2(g)+催化剂—→2N(催化剂) H2(g)+催化剂—→2H(催化剂) N(催化剂) + H(催化剂) —→NH(催化剂) NH(催化剂) + H(催化剂) —→NH2(催化剂) NH2(催化剂) + H(催化剂) —→NH3(催化剂) NH3(催化剂)—→NH3(g) + 催化剂 实验结果证明,N2活性吸附是最慢的一步,即为表面反应过程的控制步骤。 对整个气固相催化反应过程,是表面反应控制还是扩散控制,取决于实际操作条件。低温时可能是动力学控制,高温时可能是内扩散控制; 大颗粒的催化剂内扩散路径长,小颗粒的路径短,所以在同样温度下大颗粒可能是内扩散控制,小颗粒可能是化学动力学控制。 1、温度 变换反应是放热反应,存在反应最佳温度。从热力学上看,T↑,Kp↓;但从动力学因素看,T↑,Kp ↑。使变换率最大的温度为最佳温度, 2.压力 从速度方程可看出,提高压力可使正反应速度增加大于逆反应速度增加,所以一般选择较高压力。同时必须在较高压力下才有可观的速度。 3、甲烷蒸汽转化反应动力学
均相反应动力学基础
第二章 均相反应的动力学基础 2.1 基本概念与术语 均相反应:是指在均一的液相或气相中进行的反应。 均相反应动力学是研究各种因素如温度、催化剂、反应物组成和压力等对反应速率反应产物分布的影响,并确定表达这些因素与反应速率间定量关系的速率方程。 2.1-1 化学计量方程 它是表示各反应物、生成物在反应过程的变化关系的方程。如 N 2+3H 2===2NH 3 一般形式为: 2NH 3- N 2-3H 2== 0 有S 个组分参与反应,计量方程: 02211=+++S S A A A ααα 或 ∑==S i i i A 1 α 式中: A i 表示i 组分 αi 为 i 组分的计量系数 反应物αi 为负数,产物为正值。 注意: 1. 化学计量方程仅是表示由于反应而引起的各个参与反应的物质之间量的变化关系,计量方程本身与反应的实际历程无关。 2. 乘以一非零的系数λ i 后,可得一个计量系数不同的新的计量方程: ∑==S i i i i A 1 αλ 3. 只用一个计量方程即可唯一的给出各反应组分之间的变化关系的 反应体系——单一反应;必须用两个(或多个)计量方程方能确定各反应组分在反应时量的变化关系的反应,成为复合反应。 CO+2H 2=CH 3OH CO+ 3H 2=CH 4+ H 2O 2.1-2 化学反应速率的定义 化学反应速率是以单位时间,单位反应容积内着眼(或称关键)组分K 的物质量摩尔数变化来定义K 组分的反应速率。 R S B A R S B A αααα+=+ ))((单位时间单位体积的摩尔数) (由于反应而消耗的A Vdt dn r A A =- =- dt dn V r A A 1- =- dt dn V r B B 1-=- dt dn V r S S 1= dt dn V r R R 1=
化学反应工程习题-第五章:非均相反应动力学
第五章 非均相反应动力学 1.工业催化剂所必备的三个主要条件是:_______、_______、_______。(活性好、选择性高、寿命长) 2.气体在固体表面上的吸附中物理吸附是靠_______结合的,而化学吸附是靠_______结合的。(范德华力、化学键力) 3.气体在固体表面上的吸附中物理吸附是_______分子层的,而化学吸附是_______分子层的。(多、单) 4.气体在固体表面上发生吸附时,描述在一定温度下气体吸附量与压力的关系式称为_______。(吸附等温方程) 5. _______吸附等温方程式是假定吸附热是随着表面覆盖度的增加而随幂数关系减少的。(Freundlich ) 6._______吸附等温方程式是按吸附及脱附速率与覆盖率成指数函数的关系导出的。(Temkin ) 7.固体催化剂的比表面积的经典测定方法是基于_______方程。(BET ) 8.在气—固相催化反应中,反应速率一般是以单位催化剂的重量为基准的,如反应A →B ,A 的反应速率的定义为_______。( dt dn W r A A ?-=-1) 9.对于气—固相催化反应,要测定真实的反应速率,必须首先排除_______和_______的影响。(内扩散、外扩散) 10.测定气固相催化速率检验外扩散影响时,可以同时改变催化剂装量和进料流量,但保持_______不变。(0A F W ) 11.测定气固相催化速率检验外扩散影响时,可以同时改变_______和_______,但保持0A F W 不变。(催化剂装量、进料流量) 12.测定气固相催化速率检验内扩散影响时,可改变催化剂的_______,在恒定的0A F W 下测_______,看二者的变化关系。[粒度(直径p d )、转化率] 13.测定气固相催化速率检验内扩散影响时,可改变催化剂的粒度(直径 p d ),在恒定的 _______下测转化率,看二者的变化关系。(0A F W ) 14.催化剂回转式反应器是把催化剂夹在框架中快速回转,从而排除_______影响和达到气相_______及反应器_______的目的。(外扩散、完全混合、等温) 15.流动循环(无梯度)式反应器是指消除_______、_______的存在,使实验的准确性提高。(温度梯度、浓度梯度) 16.对于多孔性的催化剂,分子扩散很复杂,当孔径较大时,扩散阻力是由_______所致。(分子间碰撞) 17.对于多孔性的催化剂,分子扩散很复杂,当孔径较大时,扩散阻力是由分子间碰撞所致,这种扩散通常称为_______。[分子扩散(容积扩散)] 18.对于多孔性的催化剂,分子扩散很复杂,当微孔孔径在约_______时,分子与孔壁的碰撞为扩散阻力的主要因素。(0.1um ) 19.对于多孔性的催化剂,分子扩散很复杂,当微孔孔径在约0.1um 时,_______为扩散阻力的主要因素。(分子与孔壁的碰撞) 20.对于多孔性的催化剂,分子扩散很复杂,当微孔孔径在约0.1um 时,分子与孔壁的碰撞为扩散阻力的主要因素,这种扩散称为_______。(努森扩散) 21.等温催化剂的有效系数η为催化剂粒子的______________与催化剂内部的_______________________________之比。(实际反应速率、浓度和温度与其外表面上的相等时的反应速率) 22.气—固相催化反应的内扩散模数=S φ_______,它是表征内扩散影响的重要参数。
化学反应工程习题(word版)第二章 均相反应动力学
第二章 均相反应动力学 1. 均相反应是指___________________________________。(参与反应的物质均处于同一相) 2. aA + bB pP + sS 对于反应,则=P r _______)(A r -。(a p ) 3.着眼反应组分K 的转化率的定义式为_______。(0 0K K K K n n n -= χ) 4.当计量方程中计量系数的代数和等于零时,这种反应称为_______,否则称为_______。(等 分子反应、非等分子反应) 5. 化学反应速率式为β α B A C A C C K r =-,用浓度表示的速率常数为C K ,假定符合理想气体状 态方程,如用压力表示的速率常数P K ,则C K =_______P K 。() () (βα+RT ) 6. 化学反应的总级数为n ,如用浓度表示的速率常数为C K ,用逸度表示的速率常数f K ,则C K =_______f K 。(n RT )() 7. 化学反应的总级数为n ,如用浓度表示的速率常数为C K ,用气体摩尔分率表示的速率常数y K ,则C K =_______y K 。(n p RT ???? ??) 8.在构成反应机理的诸个基元反应中,如果有一个基元反应的速率较之其他基元反应慢得多,他的反应速率即代表整个反应的速率,其他基元反应可视为处于_______。(拟平衡常态) 9.当构成反应机理的诸个基元反应的速率具有相同的数量级时,既不存在速率控制步骤时,可假定所有各步基元反应都处于_______。(拟定常态) 10. 活化能的大小直接反映了______________对温度的敏感程度。(反应速率) 11. 一个可逆的均相化学反应,如果正、逆两向反应级数为未知时,采用______________法来求反应级数。(初始速率法) 12.生成主产物的反应称为_______,其它的均为_______。(主反应、副反应) 13. 平行反应 A P(主) S(副)均为一级不可逆反应,若主 E >副E ,选择性S p 与_______无关, 仅是_______的函数。 (浓度、温度) 14. 如果平行反应A P(主) S(副)均为一级不可逆反应,若 主 E >副E ,提高选择性P S 应 _______。(提高温度) 15. 一级连串反应A S P 在全混流釜式反应器中,则目的产物P 的最大浓 度=max ,P C ______、= opt τ______。(2 2/1120 ] 1) /[(+K K C A 、 2 11 K K )
均相反应的动力学基础
§2 均相反应的动力学基础 §2.1 基本概念和术语 若参于反应的各物质均处同一个相内进行化学反应则称为均相反应。 均相反应动力学:研究各种因素如温度、催化剂、反应物组成和压力等对反应速率、反应产物分布的影响,并确定表达这些影响因素与反应速率之间定量关系的速率方程。 §2.1.1 化学计量方程 化学计量方程:表示各反应物、生成物在反应过程中量的变化关系的方程。 一个由S 个组分参予的反应体系,其计量方程可写成: ∑==S i i i A 1 0α 式中:Ai 表示i 组分,i α为i 组分的计量系数。通常反应物的计量系数为负数,反应产物的计量系数为正值。 注意: 1.计量方程本身与反应的实际历程无关,仅表示由于反应引起的各个参予反应的物质之间量的变化关系。 2.规定在计量方程的计量系数之间不应含有除1以外的任何公因子。这是为了消除计量系数在数值上的不确定性。 单一反应:只用一个计量方程即可唯一给出各反应组分之间量的变化关系的反应体系。 复杂反应:必须用两个或多个计量方程方能确定各反应组分之间量的变化关系的反应体系 例如,合成氨反应的计量方程通常写成:32223NH H N ?+ 写成一般化的形式为:023322=+--NH H N 而错误的形式有:0462322=+--NH H N
§2.1.2 反应程度和转化率 反应程度是各组分在反应前后的摩尔数变化与其计量系数的比值,用符号ξ来表示,即: k k k i i i n n n n n n αααξ0 1 10 1-= -= =-= 或写成: i i i i n n ξα=-0 1.不论哪一个组分,其反应程度均是一致的,且恒为正值。 2.如果在一个反应体系中同时进行数个反应,各个反应各自有自己的反应程度,则任一反应组分i 的反应量应等于各个反应所作贡献的代数和,即: ∑==-M j j ij i i n n 1 0ξα 其中:M 为化学反应数,ij α为第j 个反应中组分I 的化学计量系数。 转化率是指某一反应物转化的百分率或分率,其定义为: 0k k k n n n x -= = 该反应物的起始量某一反应物的转化量 1.如果反应物不只一种,根据不同反应物计算所得的转化率数值可能 是不一样的,但它们反映的都是同一个客观事实。 关键组分:通常选择不过量的反应物(常常也是反应物中价值较高的组分)来计算转化率,这样的组分称为关键(着眼)给分。 2.单程转化率和全程转化率:某些反应系统原料通过反应器膈的转化率很低(化学平衡的限制或其它的原因),为了提高原料利用率以降低产品成本,往往将反应器出口物料中的反应产物分离出来,余下的物料再送回反应器入口,与新鲜原料一起进入反应器再反应,然后再分离、再循环等等。有两种含义不同的转化率,新鲜原料通过反应器一次所达到的转化率,叫单程转化率,可以理解为以反应器进口物料为基准的转化率;新鲜原料进入反应系统起到离开系统为止所达到的转化率,称为全程转化率,或者说是以新鲜原料为计算的转化率。