中英文文献翻译-仓库管理系统( WMS )

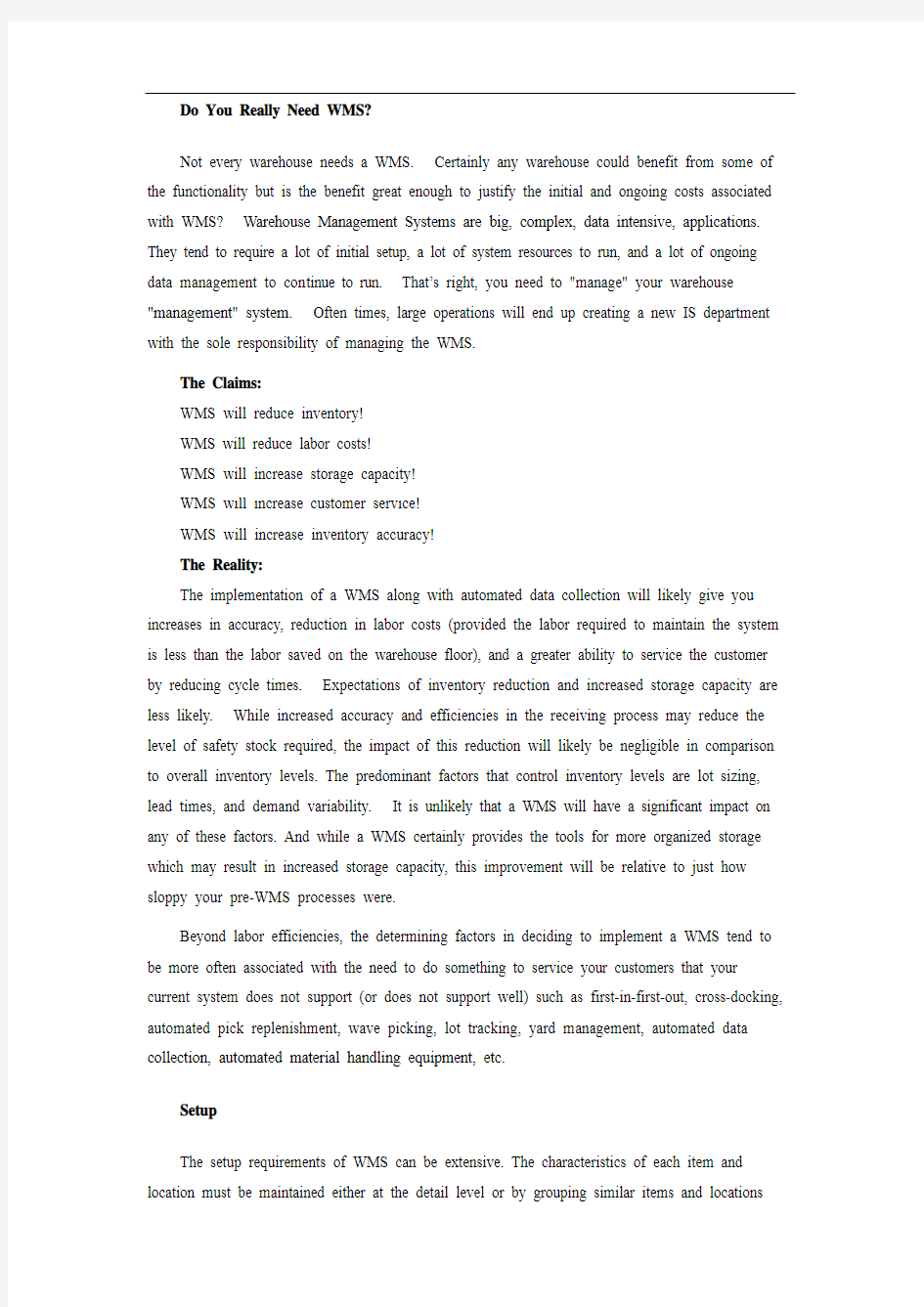
英文原文
Warehouse Management Systems (WMS).
The evolution of warehouse management systems (WMS) is very similar to that of many other software solutions. Initially a system to control movement and storage of materials within a warehouse, the role of WMS is expanding to including light manufacturing, transportation management, order management, and complete accounting systems. To use the grandfather of operations-related software, MRP, as a comparison, material requirements planning (MRP) started as a system for planning raw material requirements in a manufacturing environment. Soon MRP evolved into manufacturing resource planning (MRPII), which took the basic MRP system and added scheduling and capacity planning logic. Eventually MRPII evolved into enterprise resource planning (ERP), incorporating all the MRPII functionality with full financials and customer and vendor management functionality. Now, whether WMS evolving into a warehouse-focused ERP system is a good thing or not is up to debate. What is clear is that the expansion of the overlap in functionality between Warehouse Management Systems, Enterprise Resource Planning, Distribution Requirements Planning, Transportation Management Systems, Supply Chain Planning, Advanced Planning and Scheduling, and Manufacturing Execution Systems will only increase the level of confusion among companies looking for software solutions for their operations.
Even though WMS continues to gain added functionality, the initial core functionality of a WMS has not really changed. The primary purpose of a WMS is to control the movement and storage of materials within an operation and process the associated transactions. Directed picking, directed replenishment, and directed put away are the key to WMS. The detailed setup and processing within a WMS can vary significantly from one software vendor to another, however the basic logic will use a combination of item, location, quantity, unit of measure, and order information to determine where to stock, where to pick, and in what sequence to perform these operations.
Have a flexible location system.
Utilize user-defined parameters to direct warehouse tasks and use live
Have some built-in level of integration with data collection devices.
Do You Really Need WMS?
Not every warehouse needs a WMS. Certainly any warehouse could benefit from some of the functionality but is the benefit great enough to justify the initial and ongoing costs associated with WMS? Warehouse Management Systems are big, complex, data intensive, applications. They tend to require a lot of initial setup, a lot of system resources to run, and a lot of ongoing data management to con tinue to run. That’s right, you need to "manage" your warehouse "management" system. Often times, large operations will end up creating a new IS department with the sole responsibility of managing the WMS.
The Claims:
WMS will reduce inventory!
WMS will reduce labor costs!
WMS will increase storage capacity!
WMS will increase customer service!
WMS will increase inventory accuracy!
The Reality:
The implementation of a WMS along with automated data collection will likely give you increases in accuracy, reduction in labor costs (provided the labor required to maintain the system is less than the labor saved on the warehouse floor), and a greater ability to service the customer by reducing cycle times. Expectations of inventory reduction and increased storage capacity are less likely. While increased accuracy and efficiencies in the receiving process may reduce the level of safety stock required, the impact of this reduction will likely be negligible in comparison to overall inventory levels. The predominant factors that control inventory levels are lot sizing, lead times, and demand variability. It is unlikely that a WMS will have a significant impact on any of these factors. And while a WMS certainly provides the tools for more organized storage which may result in increased storage capacity, this improvement will be relative to just how sloppy your pre-WMS processes were.
Beyond labor efficiencies, the determining factors in deciding to implement a WMS tend to be more often associated with the need to do something to service your customers that your current system does not support (or does not support well) such as first-in-first-out, cross-docking, automated pick replenishment, wave picking, lot tracking, yard management, automated data collection, automated material handling equipment, etc.
Setup
The setup requirements of WMS can be extensive. The characteristics of each item and location must be maintained either at the detail level or by grouping similar items and locations
into categories. An example of item characteristics at the detail level would include exact dimensions and weight of each item in each unit of measure the item is stocked (each, cases, pallets, etc) as well as information such as whether it can be mixed with other items in a location, whether it is rack able, max stack height, max quantity per location, hazard classifications, finished goods or raw material, fast versus slow mover, etc. Although some operations will need to set up each item this way, most operations will benefit by creating groups of similar products. For example, if you are a distributor of music CDs you would create groups for single CDs, and double CDs, maintaining the detailed dimension and weight information at the group level and only needing to attach the group code to each item. You would likely need to maintain detailed information on special items such as boxed sets or CDs in special packaging. You would also create groups for the different types of locations within your warehouse. An example would be to create three different groups (P1, P2, P3) for the three different sized forward picking locations you use for your CD picking. You then set up the quantity of single CDs that will fit in a P1, P2, and P3 location, quantity of double CDs that fit in a P1, P2, P3 location etc. You would likely also be setting up case quantities, and pallet quantities of each CD group and quantities of cases and pallets per each reserve storage location group.
If this sounds simple, it is…well… sort of. In reality most operations have a much more diverse product mix and will require much more system setup. And setting up the physical characteristics of the product and locations is only part of the picture. You have set up enough so that the system knows where a product can fit and how many will fit in that location. You now need to set up the information needed to let the system decide exactly which location to pick from, replenish from/to, and put away to, and in what sequence these events should occur (remember WMS is all about “directed” movement). You do this by assigni ng specific logic to the various combinations of item/order/quantity/location information that will occur.
Below I have listed some of the logic used in determining actual locations and sequences.
Location Sequence. This is the simplest logic; you simply define a flow through your warehouse and assign a sequence number to each location. In order picking this is used to sequence your picks to flow through the warehouse, in put away the logic would look for the first location in the sequence in which the product would fit.
Zone Logic. By breaking down your storage locations into zones you can direct picking, put away, or replenishment to or from specific areas of your warehouse. Since zone logic only designates an area, you will need to combine this with some other type of logic to determine exact location within the zone.
Fixed Location. Logic uses predetermined fixed locations per item in picking, put away, and replenishment. Fixed locations are most often used as the primary picking location in piece pick and case-pick operations, however, they can also be used for secondary storage.
Random Location. Since computers cannot be truly random (nor would you want them to be) the term random location is a little misleading. Random locations generally refer to areas where products are not stored in designated fixed locations. Like zone logic, you will need some additional logic to determine exact locations.
First-in-first-out (FIFO).Directs picking from the oldest inventory first.
Last-in-first-out (LIFO).Opposite of FIFO. I didn't think there were any real applications for this logic until a visitor to my site sent an email describing their operation that distributes perishable goods domestically and overseas. They use LIFO for their overseas customers (because of longer in-transit times) and FIFO for their domestic customers.
Pick-to-clear. Logic directs picking to the locations with the smallest quantities on hand. This logic is great for space utilization.
Reserved Locations. This is used when you want to predetermine specific locations to put away to or pick from. An application for reserved locations would be cross-docking, where you may specify certain quantities of an inbound shipment be moved to specific outbound staging locations or directly to an awaiting outbound trailer.
Maximize Cube. Cube logic is found in most WMS systems however it is seldom used. Cube logic basically uses unit dimensions to calculate cube (cubic inches per unit) and then compares this to the cube capacity of the location to determine how much will fit. Now if the units are capable of being stacked into the location in a manner that fills every cubic inch of space in the location, cube logic will work. Since this rarely happens in the real world, cube logic tends to be impractical.
Consolidate. Looks to see if there is already a location with the same product stored in it with available capacity. May also create additional moves to consolidate like product stored in multiple locations.
Lot Sequence. Used for picking or replenishment, this will use the lot number or lot date to determine locations to pick from or replenish from.
It’s very common to combine multiple logic methods to determine the best location. For example you may chose to use pick-to-clear logic within first-in-first-out logic when there are multiple locations with the same receipt date. You also may change the logic based upon current workload. During busy periods you may chose logic that optimizes productivity while during slower periods you switch to logic that optimizes space utilization.
Other Functionality/Considerations
Wave Picking/Batch Picking/Zone Picking. Support for various picking methods varies from one system to another. In high-volume fulfillment operations, picking logic can be a critical factor in WMS selection. See my article on Order Picking for more info on these methods.
Task Interleaving. Task interleaving describes functionality that mixes dissimilar tasks such as picking and put away to obtain maximum productivity. Used primarily in full-pallet-load operations, task interleaving will direct a lift truck operator to put away a pallet on his/her way to the next pick. In large warehouses this can greatly reduce travel time, not only increasing productivity, but also reducing wear on the lift trucks and saving on energy costs by reducing lift truck fuel consumption. Task interleaving is also used with cycle counting programs to coordinate a cycle count with a picking or put away task.
Integration with Automated Material Handling Equipment. If you are planning on using automated material handling equipment such as carousels, ASRS units, AGNS, pick-to-light systems, or separation systems, you’ll wa nt to consider this during the software selection process. Since these types of automation are very expensive and are usually a core component of your warehouse, you may find that the equipment will drive the selection of the WMS. As with automated data collection, you should be working closely with the equipment manufacturers during the software selection process.
Advanced Shipment Notifications (ASN). If your vendors are capable of sending advanced shipment notifications (preferably electronically) and attaching compliance labels to the shipments you will want to make sure that the WMS can use this to automate your receiving process. In addition, if you have requirements to provide ASNs for customers, you will also want to verify this functionality.
Yard Management. Yard management describes the function of managing the contents (inventory) of trailers parked outside the warehouse, or the empty trailers themselves. Yard management is generally associated with cross docking operations and may include the management of both inbound and outbound trailers.
Labor Tracking/Capacity Planning. Some WMS systems provide functionality related to labor reporting and capacity planning. Anyone that has worked in manufacturing should be familiar with this type of logic. Basically, you set up standard labor hours and machine (usually lift trucks) hours per task and set the available labor and machine hours per shift. The WMS system will use this info to determine capacity and load. Manufacturing has been using capacity planning for decades with mixed results. The need to factor in efficiency and utilization to determine rated capacity is an example of the shortcomings of this process. Not that I’m necessarily against capacity planning in warehousing, I just think most operations don’t really need it and can avoid the disappointment of trying to make it work. I am, however, a big
advocate of labor tracking for individual productivity measurement. Most WMS maintain enough data to create productivity reporting. Since productivity is measured differently from one operation to another you can assume you will have to do some minor modifications here (usually in the form of custom reporting).
Integration with existing accounting/ERP systems. Unless the WMS vendor has already created a specific interface with your accounting/ERP system (such as those provided by an approved business partner) you can expect to spend some significant programming dollars here. While we are all hoping that integration issues will be magically resolved someday by a standardized interface, we isn’t there yet. Ideally you’ll want an integrator that has already integrated the WMS you chose with the business software you are using. Since this is not always possible you at least want an integrator that is very familiar with one of the systems.
WMS + everything else = ? As I mentioned at the beginning of this article, a lot of other modules are being added to WMS packages. These would include full financials, light manufacturing, transportation management, purchasing, and sales order management. I don’t see this as a unilateral move of WMS from an add-on module to a core system, but rather an optional approach that has applications in specific industries such as 3PLs. Using ERP systems as a point of reference, it is unlikely that this add-on functionality will match the functionality of
best-of-breed applications available separately. If warehousing/distribution is your core business function and you don’t want to have to deal with the integration issues of incorporating separate financials, order processing, etc. you may find these WMS based business systems are a good fit.
Implementation Tips
Outside of the standard “don’t underestimate”, “thoroughly test”, “train, train, train” implementation tips that apply to any business software installation ,it’s important to emphasize that WMS are very data dependent and restrictive by design. That is, you need to have all of the various data elements in place for the system to function properly. And, when they are in place, you must operate within the set parameters.
When implementing a WMS, you are adding an additional layer of technology onto your system. And with each layer of technology there is additional overhead and additional sources of potential problems. Now don’t take this as a condemnation of Warehouse Management Systems. Coming from a warehousing background I definitely appreciate the functionality WMS have to offer, and, in many warehouses, this functionality is essential to their ability to serve their customers and remain competitive. It’s just important to note that every solution has its downsides and having a good understanding of the potential implications will allow managers to make better decisions related to the levels of technology that best suits their unique environment.
中文译文
仓库管理系统( WMS )
仓库管理系统( WMS )的演变与许多其他软件解决方案是很像的。最初的系统用来控制物料在仓库内的流动和贮存,仓库的作用正在延伸到包括轻型制造业,交通运输管理,订单管理,和完整的会计制度中。利用与先前的业务有关的软件,制造资源计划,作为一个比较,材料需求计划( MRP )开始作为一个规划要求,原材料的生产环境的系统。物料需求计划很快演变成以MRP系统,补充调度和容量规划为基础的逻辑制造资源计划( MRPII系统)。最终MRPII系统演变成企业资源规划( ERP ),吸收所有的MRPII系统的功能包括充分的财务与客户和供应商管理功能。现在,无论仓库管理系统演变成一个以仓库为中心的ERP系统是一件好事或不可达的辩论。清楚的是,在仓库管理系统,企业资源规划,布局规划要求,交通运输管理系统,供应链计划,高级计划与排程,以及制造执行系统之间扩大重叠功能性只会增加那些寻找软件解决方案业务的公司混乱水平。
尽管仓库继续获得额外的功能,最初的仓库管理系统的核心功能还没有真正改变。其主要目的是控制管理系统在工艺操作相关联的交易中的流动和材料储存。定向采摘,定向补充,定向收集是仓库的关键。从一个软件供应商到另一个在一个管理系统中详细的安装和处理可以有一个很大的差别,但是其基本逻辑将使用相结合的项目,地点,数量,度量单位,并以收集信息以确定在哪里储存,在哪里挑选,以及以何种顺序执行这些操作。
最低限度,一个仓库管理系统应采取下列措施
有一个灵活的定位系统。
利用用户定义的参数,指导仓库任务和使用Live文件来执行这些任务。
有一些内置的一体化和数据收集设备结合体。
您是否真的需要仓库管理系统?
并非每一个仓库需要一个仓库管理系统。当然,任何仓库可受益于其中一些功能,但这些受益是否足以证明管理系统最初的和正在进行的相关费用是正确的?仓库管理系统是大的,复杂的,数据密集型的应用。他们往往需要大量的初始安装,很多系统资源的运行,很多正在进行的数据管理为继续运行。没错,你需要“管理”你的仓库“管理”制度。一般情况下,大规模的行动最终将建立一个新的IS部门用来唯一负责管理仓库管理系统。
声明
1仓库管理系统将减少库存!
2仓库管理系统将减少劳动力成本!
3仓库管理系统将增加存储容量!
4仓库管理系统将提高客户服务!
5仓库管理系统将增加库存的准确性!
现实
实施一个仓库管理系统用来自动的数据收集将可能使你的准确性增加,减少劳动力成本(提供需要维持系统的劳动力少于物品保存在仓库楼需要的劳动力)和更好地来服务客户以降低周期。预期库存减少和增加存储容量的可能性较小。虽然在接收过程中增加了准确性和效率可能降低库存安全水平,但这种降低产生的影响与整体库存水平相比可以忽略不计。控制库存水平批量最主要的因素是多种尺寸,交货时间和需求的变化,仓库管理系统将对任何因素有重大影响是不可能。而且同时仓库管理系统确实的为更多的有组织的存储提供工具,因为这种存储可能会导致更多的存储容量,相对于这种改善您之前的仓库管理系统是多么草率啊。除了劳动效率,决定实施仓库管理系统的决定因素,往往与一些能满足您的客户的需求有更多关联,比如您目前的系统不支持(或不太支持)像先进先出,交叉对接,自动挑选补充,波采摘,多种跟踪,停车场管理,自动数据采集,自动材料处理设备等。
设置
仓库管理系统的设置需求是广泛的,每个项目和地点都必须保持在详细或分组类似项目和地点分类。一个例子,项目详细程度的特点将包括确切尺寸和重量,每个项目在每个单位的项目储备(项目,案件,托盘等),以及信息,如是否可以与其他物品混在一个位置,无论是的最高层次,最大堆叠高度,最高量的位置,危险性分类,半成品或原材料,快与慢动,等。尽管一些行动将需要用这种方式设立每个项目,但大多数业务将有利于创造群体的类似产品。例如,如果你是一个音乐CD分销商,您将创建集团单一CD和双张CD ,保持详细的尺寸和重量的资料在组一级,只需要对每个项目附上组代码。您可能会需要对特殊物品保持详细的资料,如盒装套或CD的特别包装。您也可以为地域的不同类型在您的仓库里创造群组。一个例子是,为您用于CD采摘的三种不同大小前瞻性采摘地点建立3个不同群体(小一,二,三)。然后,您可以建立单一的光盘数量,将适合P1,P2和P3的位置,多种双张CD适合在小一,二,小三的位置等。您可能还设立案件的数量,每个CD组光盘数量,货箱的数量和光盘的每个后备存储位置组。
如果这听起来很简单,但在现实中很多业务有更多元化的产品组合,将需要更多的系统设置。而且建立产品的物理特性和产品的位置只是蓝图的部分。你设定的使系统知道产品可以适合哪里并且多少产品将满足这个地方已经足够了。您现在需要建立必要的信息,以让系统决定从哪些位置选择,补充,并采集,并在这些事件应该出现这些序列中(记得仓库管理就是“指示”流动)。你分配具体逻辑的的做法使各种组合项目/订单/数量/位置信息将出现。
下面我列出一些用于确定实际位置和序列的逻辑
1)位置顺序。这是最简单的逻辑;您只需确定流经你的仓库和为每一个地点分配序列编号。
为了挑选这是把您选择的在流经的仓库排序,在采集逻辑将寻求在第一位置的顺序适合的产品。
2)区逻辑。由于把你的储存地点分到区,您可以直接采摘,收集,或补充或特定地区的
仓库。自区逻辑唯一指定的一个地区,则需要再加上一些其他类型的逻辑,以确定确切位置在禁区内。
3)固定的位置。逻辑使用预先确定的固定地点,每一项目中分拣,采集,和补充。固定
地点是一块采摘挑选和个案选择的行动最常用的首要位置,但是,它们也可用于二级存储。
4)随机地点。由于电脑不能真正随机(也不想要他们)的任期随机位置有点误导。随机
地点一般指的是产品不会储存在指定的固定地点的地方。如Zone逻辑,您将需要一些额外的逻辑,以确定确切位置。
5)先入先出( FIFO的)。首先指示挑选最古老的库存。
6)最后,先出( LIFO )。我不认为这种逻辑有任何实际应用,直到我的网站访问者发送
一封电子邮件,说明自己在国内和海外销售易腐货物的行动。他们为海外客户使用LIFO(因为长期在途中)和为国内客户使用FIFO。
7)挑选到清楚。用最少的人手挑选逻辑指示的地点。这种逻辑是巨大的空间利用率。
8)预留位置。这个是在预约具体地点采集时使用。从申请预留位置将交叉对接,在那里你
可以指定一定数量的入境货物转移到具体的举办地点外,或直接到等待出境拖车。
9)最大限度地立方。立方体逻辑中是在WMS系统发现最多的,尽管它很少使用。立方体逻
辑基本上使用单位面积计算立方体(立方英寸每单位)。然后比较这个位置的立方体能力,以确定有多少适合。现在,如果这些单位能堆叠成的位置,以填补每立方英寸的空间中的位置,立方体逻辑将工作。由于这很少发生在现实世界,立方体的逻辑往往是不切实际的。10)巩固。查询看是否有一个以现有性质存放相同产品的位置。还可以创造更多的行动,以
巩固同类产品存放在多个位置。
11)很多序列。用于采摘或补充,这将使用大量批号或日期,以确定位置,以选择或补充。
这是非常常见的逻辑结合多种方法,以确定最佳的位置。例如您可以选择使用挑选到清晰的逻辑内先入先出逻辑当有多个地点以同样的收据的日期。您也可能会根据目前的工作量改变的逻辑。在繁忙时段内您可以选择的逻辑,优化生产力,同时在速度较慢时期您切换到逻辑,优化空间利用率。
其他功能/思考
1)波拾取/批次拣货/区拣货。支持各种不同选择方法从一个系统到另一个。在高销量的
完成作业,可采摘逻辑中的一个关键因素韦氏选择。见我的文章的订单欲知有关这些方法。
2)任务交织。工作交织介绍混合不同的功能,任务,如挑选和采集获得最大的生产力。
主要用于全货负荷运作,任务交织将指示叉车经营者抛弃托盘上他/她的方式在未来选秀权。
在大型仓库这可以大大减少旅行时间,不仅提高生产力,而且还减少磨损叉车和节约的能源成本,减少燃料消耗叉车。工作交织也使用周期计算程序,以协调的循环计数与采摘或采集任务。
3)集成自动材料处理设备。如果你计划使用自动材料处理设备,如传送带,ASRS 单位,
AGVS,挑选到照明系统,或分拣系统,您需要考虑在软件选择过程考虑它们。由于这些类型的自动化是非常昂贵,通常是一个核心组成仓库的部分,您可能会发现,这些设备将驱动WMS的选择作用,你应该与设备制造商在软件选择过程密切合作。
4)先进的装运通知(ASN)。如果您的供应商有能力向先进装运通知(最好以电子方式),
并附加遵守标签的出货量您会希望以确保仓库可以使用这个自动化您接受过程。此外,如果您需要向客户提供ASNS,你也将要验证此功能。循环计数。大多数仓库将有一些循环计数功能。修改循环计数系统是常见的,以满足特定的业务需求。
5)堆场管理。堆场管理描述了管理职能的内容(库存)的拖车停在仓库,或空拖车本身。
堆场管理通常与交叉对接,并可能包括管理入站和出站拖车。
6)劳动跟踪/容量规划。有的WMS系统提供的功能有关的劳动报告和容量规划。任何人
都一直在制造业应该熟悉这种类型的逻辑。基本上,您设定标准工时和机器(通常叉车)小时以上的任务,并设置可劳动和机时数的转变。该仓库系统将利用这一信息,以确定能力和负载。制造能力已使用了几十年规划的结果好坏参半。需要因素的效率和利用率,以确定额定容量就是一个例子中存在的缺点这一进程。不是说我一定对规划的仓储能力,我想大多数业务并不真的需要它,并能够避免的失望试图使它发挥作用。然而,我一个大倡导的个别劳动生产率的跟踪测量。大多数仓库保持足够的数据来创建生产力报告。由于生产力是衡量从一个不同的行动,另一个你可以假设你将不得不做一些小的改动这里(通常的形式是自定义的报告)。
7)整合现有的会计/ ERP系统。除非仓库管理系统供应商已经建立了一个特定的接口与您
的会计/ ERP系统(如所提供的经批准的商业合作伙伴)您可以预期花费一些重大编程美元这里。虽然我们大家都希望这种融合的问题将得到解决,有一天奇迹般地由一个标准的接口,但是我们还没有。理想您需要一个积分,已经集成了仓库管理系统您选择与商业软件您使用。
systems. 由于这并非总是可能你至少需要一个积分,这是非常熟悉的系统。
8)仓库+一切= ?正如我前面提到在本文开头,还有很多其他模块被添加到仓库管理系统
软件包。这将包括全面的财务,轻型制造业,交通运输管理,采购和销售订单管理。我不认为这是一个单方面行动的仓库管理系统由一个附加模块,核心系统,而是一个可选的办法,已应用在具体行业,如3PLs。用ERP系统作为一个参照点,这是不太可能,这个附加的功能,将匹配的功能,最佳的应用软件可单独购买。如果仓储/分销的核心业务职能和你不想必须处理一体化问题纳入单独的财务,订单处理,等您可能会发现这些仓库管理系统基础的业务系统是一个良好的生长。
执行小贴士
标准以外的“不低估”,“彻底的测试”,“火车,火车,火车”执行情况提示,适用于任何商业软件的安装,尤其要强调的是,WMS的设计非常依赖数据和限制性。也就是说,您需要使系统正常运行的所有适合的不同的数据元素。此外,当他们已到位,您必须在规定的参数操作。
中英文文献翻译
毕业设计(论文)外文参考文献及译文 英文题目Component-based Safety Computer of Railway Signal Interlocking System 中文题目模块化安全铁路信号计算机联锁系统 学院自动化与电气工程学院 专业自动控制 姓名葛彦宁 学号 200808746 指导教师贺清 2012年5月30日
Component-based Safety Computer of Railway Signal Interlocking System 1 Introduction Signal Interlocking System is the critical equipment which can guarantee traffic safety and enhance operational efficiency in railway transportation. For a long time, the core control computer adopts in interlocking system is the special customized high-grade safety computer, for example, the SIMIS of Siemens, the EI32 of Nippon Signal, and so on. Along with the rapid development of electronic technology, the customized safety computer is facing severe challenges, for instance, the high development costs, poor usability, weak expansibility and slow technology update. To overcome the flaws of the high-grade special customized computer, the U.S. Department of Defense has put forward the concept:we should adopt commercial standards to replace military norms and standards for meeting consumers’demand [1]. In the meantime, there are several explorations and practices about adopting open system architecture in avionics. The United Stated and Europe have do much research about utilizing cost-effective fault-tolerant computer to replace the dedicated computer in aerospace and other safety-critical fields. In recent years, it is gradually becoming a new trend that the utilization of standardized components in aerospace, industry, transportation and other safety-critical fields. 2 Railways signal interlocking system 2.1 Functions of signal interlocking system The basic function of signal interlocking system is to protect train safety by controlling signal equipments, such as switch points, signals and track units in a station, and it handles routes via a certain interlocking regulation. Since the birth of the railway transportation, signal interlocking system has gone through manual signal, mechanical signal, relay-based interlocking, and the modern computer-based Interlocking System. 2.2 Architecture of signal interlocking system Generally, the Interlocking System has a hierarchical structure. According to the function of equipments, the system can be divided to the function of equipments; the system
物流外文文献翻译(DOC)
外文文献原稿和译文 原稿 Logistics from the English word "logistics", the original intent of the military logistics support, in the second side after World War II has been widely used in the economic field. Logistics Management Association of the United States is defined as the logistics, "Logistics is to meet the needs of consumers of raw materials, intermediate products, final products and related information to the consumer from the beginning to the effective flow and storage, implementation and control of the process of . " Logistics consists of four key components: the real flow, real storage, and management to coordinate the flow of information. The primary function of logistics is to create time and space effectiveness of the effectiveness of the main ways to overcome the space through the storage distance. Third-party logistics in the logistics channel services provided by brokers, middlemen in the form of the contract within a certain period of time required to provide logistics services in whole or in part. Is a third-party logistics companies for the external customer management, control and operation of the provision of logistics services company. According to statistics, currently used in Europe the proportion of third-party logistics services for 76 percent, the United States is about 58%, and the demand is still growing; 24 percent in Europe and the United States 33% of non-third-party logistics service users are actively considering the use of third-party logistics services. As a third-party logistics to improve the speed of material flow, warehousing costs and financial savings in the cost effective means of passers-by, has become increasingly attracted great attention.
物流外文文献及翻译
文献出处: Mahpula A、The Research of Regional Logistics Competitiveness [J]、Journal of Transport Geography, 2015, 15(2): 30-34、 原文 The Research of Regional Logistics Competitiveness Mahpula A Abstract At present, the development of logistics is the logistics demand rapid increase, the expanding market capacity, accelerates the construction of logistics infrastructure, third-party logistics fast growth the tendency, the whole logistics industry is developing in the direction of the information, globalization and specialization、At the same time, with the rapid increase of logistics demand, the development of the regional logistics more rapidly、Regional logistics is an important part of regional economy, the existence and development of regional logistics is the premise of existence and development of regional economy, no regional economy there would be no regional logistics、Regional logistics and regional economic development level, is closely related to the scale and the level of the different regional economic shape, size and industry, determines the level of regional logistics, the scale and structure form、Regional economic integration can make the area and regional logistics incline to reasonable, adapt to reasonable layout of industrial structure, to reduce logistics cost, promote the development of regional logistics、On the other hand, the regional economic development is inseparable from the development of regional logistics and regional logistics to provide support and guarantee for the development of regional economy, the development of the regional logistics will drive and promote the further development of regional economy、Therefore, the development of the regional logistics has become to improve the regional investment environment and industry development environment, expanding the scope of the regional influence, the key to enhancing regional competitiveness、 Keywords: Regional logistics; Regional logistics competitiveness; Evaluation index 1 Introduction The rapid development of world economy and the progress of modern science and technology, the logistics industry as an emerging service industry, is developing rapidly in the global scope、Internationally, logistics industry is considered to be the economic development of the artery and basic industry, its development degree
文献翻译英文原文
https://www.360docs.net/doc/2a7727810.html,/finance/company/consumer.html Consumer finance company The consumer finance division of the SG group of France has become highly active within India. They plan to offer finance for vehicles and two-wheelers to consumers, aiming to provide close to Rs. 400 billion in India in the next few years of its operations. The SG group is also dealing in stock broking, asset management, investment banking, private banking, information technology and business processing. SG group has ventured into the rapidly growing consumer credit market in India, and have plans to construct a headquarters at Kolkata. The AIG Group has been approved by the RBI to set up a non-banking finance company (NBFC). AIG seeks to introduce its consumer finance and asset management businesses in India. AIG Capital India plans to emphasize credit cards, mortgage financing, consumer durable financing and personal loans. Leading Indian and international concerns like the HSBC, Deutsche Bank, Goldman Sachs, Barclays and HDFC Bank are also waiting to be approved by the Reserve Bank of India to initiate similar operations. AIG is presently involved in insurance and financial services in more than one hundred countries. The affiliates of the AIG Group also provide retirement and asset management services all over the world. Many international companies have been looking at NBFC business because of the growing consumer finance market. Unlike foreign banks, there are no strictures on branch openings for the NBFCs. GE Consumer Finance is a section of General Electric. It is responsible for looking after the retail finance operations. GE Consumer Finance also governs the GE Capital Asia. Outside the United States, GE Consumer Finance performs its operations under the GE Money brand. GE Consumer Finance currently offers financial services in more than fifty countries. The company deals in credit cards, personal finance, mortgages and automobile solutions. It has a client base of more than 118 million customers throughout the world
英文文献翻译
中等分辨率制备分离的 快速色谱技术 W. Clark Still,* Michael K a h n , and Abhijit Mitra Departm(7nt o/ Chemistry, Columbia Uniuersity,1Veu York, Neu; York 10027 ReceiLied January 26, 1978 我们希望找到一种简单的吸附色谱技术用于有机化合物的常规净化。这种技术是适于传统的有机物大规模制备分离,该技术需使用长柱色谱法。尽管这种技术得到的效果非常好,但是其需要消耗大量的时间,并且由于频带拖尾经常出现低复原率。当分离的样本剂量大于1或者2g时,这些问题显得更加突出。近年来,几种制备系统已经进行了改进,能将分离时间减少到1-3h,并允许各成分的分辨率ΔR f≥(使用薄层色谱分析进行分析)。在这些方法中,在我们的实验室中,媒介压力色谱法1和短柱色谱法2是最成功的。最近,我们发现一种可以将分离速度大幅度提升的技术,可用于反应产物的常规提纯,我们将这种技术称为急骤色谱法。虽然这种技术的分辨率只是中等(ΔR f≥),而且构建这个系统花费非常低,并且能在10-15min内分离重量在的样本。4 急骤色谱法是以空气压力驱动的混合介质压力以及短柱色谱法为基础,专门针对快速分离,介质压力以及短柱色谱已经进行了优化。优化实验是在一组标准条件5下进行的,优化实验使用苯甲醇作为样本,放在一个20mm*5in.的硅胶柱60内,使用Tracor 970紫外检测器监测圆柱的输出。分辨率通过持续时间(r)和峰宽(w,w/2)的比率进行测定的(Figure 1),结果如图2-4所示,图2-4分别放映分辨率随着硅胶颗粒大小、洗脱液流速和样本大小的变化。
物流规划中英文对照外文翻译文献
物流规划中英文对照外文翻译文献(文档含英文原文和中文翻译)
设施规划 引言 设施规划在过去的十年间已经被赋予了全新的意义。在过去,设施规划一般被认为是一门科学。而在当今竞争激烈的全球市场,设施规划成为了一种策略。政府、教育机构和企业已经不再单独相互竞争,现在这些实体或企业将彼此联合为合作企业、组织协会,并最终合成为供应链,将客户纳入到整个供应链过程以保持竞争力。 这些年来设施规划问题一直是一个热门话题。尽管它已拥有很悠久的历史,但在目前的出版物、会议以及研究中,设施规划仍是最受欢迎的科目之一。设施规划的处理已经从清单式或者菜单式的方法发展到了高度复杂的数学建模。在本文中,我们使用了一个实用的设施规划方法,其利用了实证以及同时包含传统和现代概念的分析方法。值得提及的是,在本文中拥有很广泛的设施规划应用示例。例如,这本书的内容可以适用于一个新医院,一个装配部门,一个已有的仓库,或者一个机场的行李部的规划。无论问题是发生在医院、生产工厂、配送中心、机场、零售商店、学校、银行、还是办公室或者这些设施的任何部分;无论是在一个发达国家的现代化设施还是在一个发展中国家的过时设施中,本文给出的材料在进行规划时都非常有用。重要的是要认识到现代设施规划中将设施当作是一个动态的实体,一个成功的设施规划方案的关键因素是其适应性以及适合全新应用的能力。 设施规划的定义 当今的设施规划必须能够帮助组织实现供应链的优越性。实现供应链的优越性是一个有六个步骤、或者说六个等级的过程。一如既往,这些步骤与优越性、可见性、协同性、综合性、敏捷性等联系在一起。 当一家公司最大化供应链的各个功能(采购-制造-运输-储存-销售),个体部门(如金融、市场营销、销售、采购、信息技术、研发、生产、分配和人力资源等部门)的目标就是要成为公司最好的部门。组织的有效性不是重点,每个组
第三方物流外文文献(原文与翻译)
我国第三方物流中存在的问题、原因及战略选择 熊卫 【摘要】我国物流业发展刚刚起步,第三方物流的理论和实践等方面都比较薄弱。本文指出我国第三方物流存在的问题在于国内外第三方物流企业差距、物流效率不高、缺乏系统性管理、物流平台构筑滞后、物流管理观念落后等。分析了产生上述问题的原因,并提出了精益物流、中小型第三方物流企业价值链联盟、大型第三方物流企业虚拟化战略等三种可供选择的第三方物流企业发展战略。 【关键词】第三方物流;精益物流战略;价值链联盟;虚拟化战略 1引言 长期以来,我国国内企业对采购、运输、仓储、代理、包装、加工、配送等环节控制能力不强,在“采购黑洞”、“物流陷井”中造成的损失浪费难以计算。因此,对第三方物流的研究,对于促进我国经济整体效益的提高有着非常重要的理论和实践意义。本文试图对我国策三方物流存在的问题及原因进行分析探讨,并提出第三方物流几种可行的战略选择。 2我国第三方物流业存在的主要问题 (一)我国策三方物流企业与国外第三方物流企业的差距较大,具体表现在以下几个方面: 1、规模经济及资本差距明显。由于国外的大型第三方物流企业从全球经营的战略出发,其规模和资本优势是毫无疑问的,尤其初创时期的我国策三方物流业,本身的规模就很小,国外巨头雄厚的资本令国内企业相形见绌。 2、我国策三方物流业企业提供的物流服务水准及质量控制远不如国外同行。当国内一些企业还在把物流理解成“卡车加仓库“的时候,国外的物流企业早已完成了一系列标准化的改造。同时,国外的物流组织能力非常强大,例如德国一家第三方物流公司,公司各方面的物流专家遍布欧洲各地。如果有客户的货物需要经达不同的国家,那么欧洲各地的这些专家就在网上设计出一个最佳的物流解决方案。这种提供解决方案的能力就是这第三方物流公司的核心能力,而不像国内公司号称拥有多少条船,多少辆车。 3、我国加入WTO后物流产业的门槛降低。在物流服务业方面:我国承诺所有的服务行业,在经过合理过渡期后,取消大部分外国股权限制,不限制外国服务供应商进入
英文文献及中文翻译
毕业设计说明书 英文文献及中文翻译 学院:专 2011年6月 电子与计算机科学技术软件工程
https://www.360docs.net/doc/2a7727810.html, Overview https://www.360docs.net/doc/2a7727810.html, is a unified Web development model that includes the services necessary for you to build enterprise-class Web applications with a minimum of https://www.360docs.net/doc/2a7727810.html, is part of https://www.360docs.net/doc/2a7727810.html, Framework,and when coding https://www.360docs.net/doc/2a7727810.html, applications you have access to classes in https://www.360docs.net/doc/2a7727810.html, Framework.You can code your applications in any language compatible with the common language runtime(CLR), including Microsoft Visual Basic and C#.These languages enable you to develop https://www.360docs.net/doc/2a7727810.html, applications that benefit from the common language runtime,type safety, inheritance,and so on. If you want to try https://www.360docs.net/doc/2a7727810.html,,you can install Visual Web Developer Express using the Microsoft Web Platform Installer,which is a free tool that makes it simple to download,install,and service components of the Microsoft Web Platform.These components include Visual Web Developer Express,Internet Information Services (IIS),SQL Server Express,and https://www.360docs.net/doc/2a7727810.html, Framework.All of these are tools that you use to create https://www.360docs.net/doc/2a7727810.html, Web applications.You can also use the Microsoft Web Platform Installer to install open-source https://www.360docs.net/doc/2a7727810.html, and PHP Web applications. Visual Web Developer Visual Web Developer is a full-featured development environment for creating https://www.360docs.net/doc/2a7727810.html, Web applications.Visual Web Developer provides an ideal environment in which to build Web sites and then publish them to a hosting https://www.360docs.net/doc/2a7727810.html,ing the development tools in Visual Web Developer,you can develop https://www.360docs.net/doc/2a7727810.html, Web pages on your own computer.Visual Web Developer includes a local Web server that provides all the features you need to test and debug https://www.360docs.net/doc/2a7727810.html, Web pages,without requiring Internet Information Services(IIS)to be installed. Visual Web Developer provides an ideal environment in which to build Web sites and then publish them to a hosting https://www.360docs.net/doc/2a7727810.html,ing the development tools in Visual Web Developer,you can develop https://www.360docs.net/doc/2a7727810.html, Web pages on your own computer.
物流 外文翻译 外文文献 英文文献 中国快递行业研究报告
2011年中国快递行业研究报告——China Express Delivery Industry Report, 2011 Enterprise wide USD $ 3300 Release Date Dec.2011 Abstract In July, 2011, in the “Twelfth Five-Year (2011-2015)” plan on the development of postal industry issued by State Post Bureau of the Peo ple’s Republic of China, the following “twelfth five-year” development indicators were put forward for the express delivery industry: the network coverage of key express delivery enterprises came up to 98% in municipalities and provincial capitals, and over 90% in provincially administered municipalities; and the key express delivery enterprises realized the 72-hour inter-provincial capital and inter-key city express delivery rate of more than 90%, express delay rate of lower than 0.8%, damage rate of lower than 0.01%, and loss rate of lower than 0.005%. The express delivery business of China has witnessed rapid growth in 2011. Up to the end of September of 2011, Chinese express delivery companies (with annual sales of over RMB5 million) had made 2.52 billion deliveries, up 53.3% year-on-year, and harvested RMB53.14 billion, a 28.9% YoY rise, of which Chinese inner-city express business revenue was RMB4.67 billion, with the year-on-year increase of 58.1%; the cross regional express business revenue rose 37% year-on-year to RMB30.73 billion; and the international and Hong Kong, Macao and Taiwan business revenue was RMB13.57 billion, a slight rise of 4.9% from the same period of last year. From January to September of 2011, 1.125 billion deliveries were made in Guangdong, Zhejiang and Shanghai, accounting for 44.64% of the national business volume, and achieved RMB25.697 billion with a 48.36% share of the total business revenue in China. ‘Research report on the express delivery industry in China’ mainly covers the followings: The twelfth five-year plan of national express delivery industry and the twelfth five-year plan of express delivery industry in key provinces and cities;
仪表板外文文献翻译、中英文翻译、外文翻译
Dashboard From Wikipedia, the free encyclopedia This article is about a control panel placed in the front of the car. For other uses, see Dashboard (disambiguation). The dashboard of a Bentley Continental GTC car A dashboard (also called dash, instrument panel (IP), or fascia) is a control panel located directly ahead of a vehicle's driver, displaying instrumentation and controls for the vehicle's operation. Contents 1.Etymology 2.Dashboard features 3.Padding and safety 4.Fashion in instrumentation 5.See also 6.References Etymology Horse-drawn carriage dashboard Originally, the word dashboard applied to a barrier of wood or leather fixed at the front of a horse-drawn carriage or sleigh to protect the driver from mud or other debris "dashed up" (thrown up) by the horses' hooves.[1] Commonly these boards did not perform any additional function other than providing a convenient handhold for ascending into the driver's seat, or a small clip with which to secure the reins when not in use. When the first "horseless carriages" were constructed in the late 19th century, with engines mounted beneath the driver such as the Daimler Stahlradwagen, the simple dashboard was retained to protect occupants from debris thrown up by the cars' front wheels. However, as car design evolved to position the motor in front of the driver, the dashboard became a panel that protected vehicle occupants from the heat and oil of the engine. With gradually increasing mechanical complexity, this panel formed a convenient location for the placement of gauges and minor controls, and from this evolved the modern instrument panel,
英文文献及翻译
Research Article Mechanical Properties of Fiber Reinforced Lightweight Concrete Containing Surfactant Y oo-Jae Kim, Jiong Hu, Soon-Jae Lee, and Byung-Hee Y ou Department of Engineering Technology, Texas State University, San Marcos, TX 78666, USA Correspondence should be addressed to Y oo-Jae Kim, yk10@https://www.360docs.net/doc/2a7727810.html, Received 21 June 2010; Accepted 24 November 2010 Academic Editor: Tarun Kant Copyright ? 2010 Y oo-Jae Kim et al. This is an open access article distributed under the Creative Commons Attribution License, which permits unrestricted use, distribution, and reproduction in any medium, provided the original work is properly cited. Fiber reinforced aerated lightweight concrete (FALC) was developed to reduce concrete’s density and to improve its fire resistance, thermal conductivity, and energy absorption. Compression tests were performed to determine basic properties of FALC. The primary independent variables were the types and volume fraction of fibers, and the amount of air in the concrete. Polypropylene and carbon fibers were investigated at 0, 1, 2, 3, and 4% volume ratios. The lightweight aggregate used was made of expanded clay. A self-compaction agent was used to reduce the water-cement ratio and keep good workability. A surfactant was also added to introduce air into the concrete. This study provides basic information regarding the mechanical properties of FALC and compares FALC with fiber reinforced lightweight concrete. The properties investigated include the unit weight, uniaxial compressive strength, modulus of elasticity, and toughness index. Based on the properties, a stress-strain prediction model was proposed. It was demonstrated that the proposed model accurately predicts the stress-strain behavior of FALC. 1. Introduction In the last three decades, prefabrication has been applied to small housing and tall building construction, and precast concrete panels have become one of the widely used materials in construction system. Recently, much attention has been directed toward the use of lightweight concrete for precast concrete to improve the performances, such as dead load reduction, fire resistance, and thermal conductivity, of the buildings. Additionally, the structure of a precast building should be able to resist impact loading cases, particularly earthquakes, since resisting earthquakes of these buildings under the performances is becoming an important consideration [1, 2].Many efforts have been applied toward developing high performance concrete for building structures with enhanced performance and safety. V arious types of precast concrete products, such as autoclaved aerated lightweight concrete (AALC), fiber reinforced concrete (FRC), and lightweight concrete, have been developed and experimentally verified. A number of them have been applied in full-scale build-ing structures. AALC is well known and widely accepted, but its small size and weak strength limit its use instructural elements [3]. Lightweight aggregate concretes offer strength, deadload reduction, and thermal conductivity,