马钢三钢厂50t电弧炉自动控制系统毕业设计

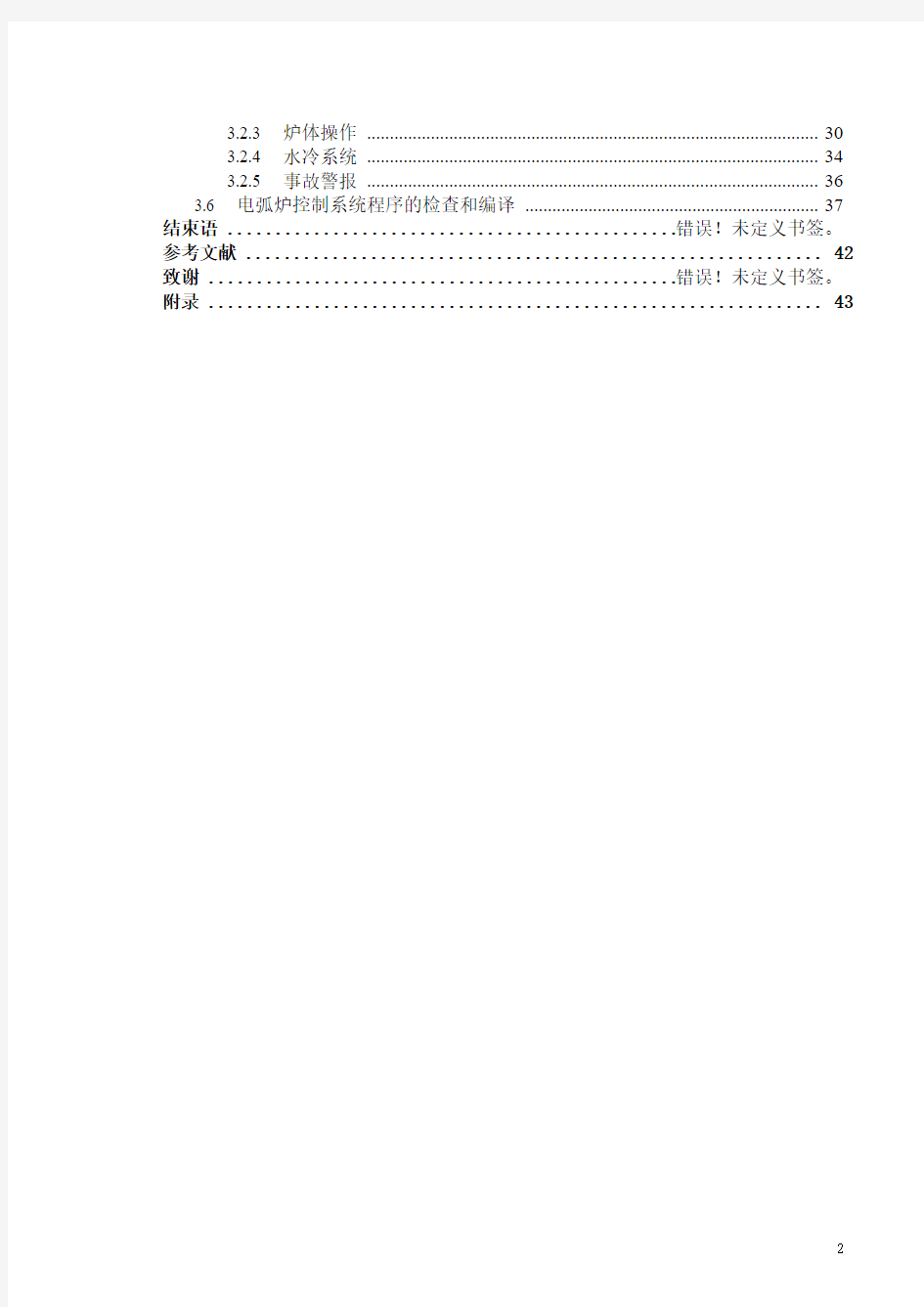
马钢三钢厂50t电弧炉自动控制系统毕
业设计
目录
1. 概述 (1)
1.1 引言 (1)
1.2 电弧炉系统 (1)
1.2.1电弧炉炼钢发展概况 (1)
1.2.2 电弧炉炼钢的特点 (2)
1.3 电弧炉工艺发展概况 (3)
1.3.1 电弧炉的历史发展 (4)
1.3.2 电弧炉在国内的发展 (4)
1.4 电弧炉自动化技术的发展趋势 (5)
1.4.1 电弧炉控制方法理论研究 (5)
1.4.2 电弧炉自动化发展趋势 (6)
1.5 电弧炉炼钢设备概括 (7)
1.5.1 电弧炉炼钢的机械设备 (7)
1.5.2 电弧炉炼钢的电气设备 (9)
1.6 电弧炉炼钢过程及工艺简介 (10)
1.6.1 电弧炉炼钢过程 (10)
1.6.2 电弧炉工艺简述 (11)
1.6.3 电弧炉工艺对控制系统的要求 (12)
1.6.4 电弧炉炼钢工艺对电极调节器的要求 (12)
2. 电弧炉炼钢控制系统 (14)
2.1 电极升降自动控制系统 (14)
2.1.1 电极调节器的特点 (15)
2.1.2 电极调节控制原理 (16)
2.2 液压、水冷、气动控制系统 (18)
2.2.1 液压控制系统 (18)
2.2.2 水冷控制系统 (18)
2.2.3 气动控制系统 (19)
2.3 计算机在电弧炉炼钢过程中的应用 (19)
2.4 PLC控制系统 (20)
2.4.1 电弧炉PLC控制系统的构成 (21)
2.4.2 电弧炉PLC控制系统的功能 (21)
3. 电弧炉控制系统的软硬件设计 (23)
3.1 电弧炉控制系统硬件设计 (23)
3.1.1 系统硬件选型 (23)
3.2 电弧炉控制系统软件设计 (24)
3.2.1 变压器保护系统 (24)
3.2.2 液压站控制 (26)
3.2.3 炉体操作 (30)
3.2.4 水冷系统 (34)
3.2.5 事故警报 (36)
3.6 电弧炉控制系统程序的检查和编译 (37)
结束语 ............................................... 错误!未定义书签。参考文献 (42)
致谢 ................................................. 错误!未定义书签。附录 . (43)
1. 概述
1.1 引言
据统计,近40年来,世界电弧炉炼钢得到迅速发展,电炉钢产量占钢总产量的比例逐年增长,目前全世界粗钢产量的56%由电炉生产,我国电炉钢也约占总钢产量的45%左右。电弧炉电气运行是电炉冶炼生产最基本的保障,它关系到冶炼工艺、原料、电气、设备等诸多方面的问题,直接影响电炉炼钢生产的各项技术和经济指标,因此对其进行最佳化的研究意义重大,不但可保障冶炼工艺的顺行和充分发挥设备资源的作用,还能提高生产率,节能降耗。
可编程控制器是在继电器控制和计算机控制发展的基础上开发出来的,并逐渐发展为以微处理器为核心,把自动化技术,计算机技术,通讯技术融为一体的新型工业自动控制装置。随着位处理器、计算机、网络和数字通信技术的飞速发展,工业生产自动化控制技术已扩展到了几乎所有的工业领域。应用计算机网络技术来解决工业自动化任务已逐渐成为普通的技术。可编程序控制器是应用面最广、功能强大、使用方便的通用工业控制装置,它已经成为当代工业自动化的主要实现工具,无论是国外引进的自动化生产线,还是自行设计的自动控制系统,普遍把可编程序控制器作为控制系统的核心器件。可编程序控制器在取代传统电气控制方面有着不可比拟的优点,在自动化领域已经形成了一种工业控制趋势。电气设备能否方便可靠的实现自动化,很大程度上取决于我们对可编程序控制器的应用水平。
可编程序控制器是一种专为在工业环境下应用而设计的计算机控制系统。它采用可编程序的存储器,能够执行逻辑控制,顺序控制,定时,计数和算术运算等操作功能,并通过开关量,模拟量的输入和输出完成各种机械或生产过程的控制。它具有丰富的输入、输出接口,并且具有较强的驱动能力,其硬件需根据实际需要来选配,其软件则需根据控制要求进行设计。
1.2 电弧炉系统
1.2.1电弧炉炼钢发展概况
近年来世界电弧炉的生产发展很快,随着二步炼钢法的兴起和20世纪70-80年代电炉自身采用了诸如超高功率技术、水冷炉壁、水冷炉顶、偏心炉底出钢、氧燃烧嘴、吹氧、喷碳、泡沫渣工艺等新技术,使得电炉钢生产不仅在传统的合金钢领域中继续保持优势,而且在普通钢范围内也表现了强大的竞争力。自20世纪80年代初世界上第一座直流电弧炉问世以来,电炉钢的生产突飞猛进。2000年,电炉钢约将占世界钢产量的34.4%,2004年世界粗钢产量达10.548亿t,其中转炉钢66452万t,占33.8%,我国钢产量27470万t,其中转炉钢23271万t,占85.72%,电炉钢4167.1万t,仅占15.17%。
目前,我国仍以交流电弧炉生产电炉钢为主,这种趋势目前仍不会改变。交流电弧炉在受到新兴直流电弧炉冲击的同时,在提高生产率和改善各种单耗方面也不断取
得进展;而直流电弧炉的诸多优点使其在未来的电弧炉炼钢中具有广阔的发展前景。
1.2.2 电弧炉炼钢的特点
电弧炉炼钢是以电能为热源,利用电极与炉料间产生的电弧的高温来加热和熔化炉料。电弧炉炼钢是以废钢铁料为主要原料,以各种微量合金和造渣料为辅料,以电能为热源,利用电极与炉料间产生的电弧的高温来加热和熔化炉料,经过一系列的物理化学反应,最后形成成分和温度合格的钢产品。
电弧炉炼钢有一系列的优点[1]
(1)能灵活掌握温度。电弧炉中电弧区温度高达4000℃以上,远远高于炼钢所需的温度,因而可以熔化各种高熔点的合金,通过电弧加热,钢液的温度可达1600℃以上。在冶炼过程中通过对电流和电压的控制,可以灵活掌握冶炼温度,以满足不同钢种冶炼的需要。
(2)热效率高。电弧炉炼钢没有大量高温炉气带走的热损失,因而热效率高,一般可达60%以上,比转炉炼钢和平炉炼钢的热效率高。
(3)炉内气氛可以控制。氧气转炉吹入大量氧气是熔炼得以进行的必要条件,平炉熔炼过程中为了保证燃料(煤气或重油)完全燃烧,必须在熔炼室中保持一定的过剩空气系数,因而在这些炉子中,熔炼自始至终是在不同程度的氧化性气氛下进行的。在电弧炉中没有可燃气体,根据工艺要求,既可造成炉内的氧化性气氛,也可造成还原性气氛,这是转炉和平炉无法达到的。因而在电弧炉炼钢过程中能够大量地去除钢中的磷、硫、氧和其他杂质,提高钢的质量,合金的回收率高且稳定,钢的化学成份比较容易控制,冶炼的钢种也较多。
(4)设备简单,工艺流程短。电弧炉的主要设备为变压器和炉体两大部分,因而基建费用低,投产快。电弧炉以废钢为原料,不象转炉那样以铁水为原料,所以不需要一套庞大的炼铁和炼焦系统,因而流程短。由于电弧炉炼钢法具有上述一系列优点,所以世界各国都在稳步地发展电炉炼钢。多年以来,世界电炉钢产量的增长速度一直高于世界钢总产量的增长速度。随着科技的发展,炼钢技术研究水平的不断进步,炼钢方法由以前的一炉直接出钢发展为炉内初炼和炉外精炼两步炼钢。目前这种以超高功率电炉炼钢、炉外精炼和连铸组成的工艺路线被称为最佳工艺流程。电炉炼钢主要指电弧炉炼钢,其他电炉如感应电炉、电渣炉等所炼钢数量很小,因此电弧炉炼钢在冶炼工艺中的地位是十分重要的。电弧炉是实现炉内初炼、生产粗钢的重要冶炼设备。冶炼过程在电弧炉内进行,靠电极和炉料间放电产生的电弧,使电能在弧光中转变为热能,并借助辐射和电弧的直接作用加热并熔化废钢料和炉渣,冶炼出各种成分的钢和合金的一种炼钢方法。电炉炼钢一般是以从各处搜集的废钢铁作为固体炉料,
所以电弧炉利用电极把电能转化为热能使炉料熔化并使之升温,然后在本炉或精炼炉中进行精炼,去除钢水中的气体﹑有害元素及杂质,测定并检验化学成分,调整到成品规格范围,同时使钢液在出钢时达到适合浇铸的温度。炼钢电弧炉根据炉衬的性质不同,可以分为碱式电弧炉和酸式电弧炉。由于炉衬性质不同,炼钢过程中所采用的造渣材料也不一样,碱式电弧炉用碱性材料造碱性渣,以石灰为主,而酸式电弧炉则是以石英砂为主材料造酸性渣。碱式电弧炉和酸式电弧炉各有其优缺点。碱式电弧炉能利用碱性炉渣有效去除钢中的有害元素磷、硫,适用于以钢锭和连铸坯为产品的电炉钢厂。而酸式电弧炉渣阻止气体透过的能力要大于碱性渣,因此使钢液升温快,比较适合异型铸造车间。电弧炉炼钢用电能加热能精确地控制温度。因为炉内没有可燃烧气体,所以可以根据工艺要求在各种不同的气氛中进行加热,也可以在任何压力或者真空中进行加热。
综上,由于电弧炉的上述特点,能保证冶炼含磷、硫、氧低的优质钢,能使用各种元素(包括铝、钛等易氧化的元素)来使钢合金化,冶炼出各种类型的优质钢和合金钢。电弧炉炼钢由于要将电能转化为热能,在炼钢过程中需要消耗大量的电能,是工矿企业中大的电能用户。在生产到销售的整个环节中,节省电能成为降低生产成本的重要环节,因此如何节约电能、提供最佳的供电曲线、给定一个最佳的电弧电流设定值成为许多国内外专家学者的研究方向。
1.3 电弧炉工艺发展概况
电弧炉炼钢技术发展至今已有近 100 年的历史,其钢产量在世界钢总产量的比例逐年上升。经过世界相关专家多年的研究使得电弧炉炼钢本体技术的不断完善,相关技术的不断涌现并不断充实到电弧炉炼钢工艺流程中,并且他吸取了其他炼钢方法的重要功能使电弧炉对原料适应性不断增强,能源的损耗不断减少,控制性能不断的完善。
表1-2 世界历年来电炉钢占钢总产量的比例
1.3.1 电弧炉的历史发展
电弧炉炼钢技术的发展大约可以追溯到 100 年前。
1899 年,赫劳特研制成三相交流电弧炉,成为现代炼钢电弧炉的雏形。1906年,德国人林登堡(R. Lindenberg)进行了第一炉钢水的铸锭,开创了电弧炉炼钢的先河。1926 年,德国德马格公司制造了炉盖开出式电弧炉,首次实现炉顶加料。以后电弧炉的发展就向着高效、节能、低消耗的方向发展,如水冷炉底、炉盖、底吹搅拌、长弧泡沫渣熔炼、无钢出渣、废钢预热和氧燃烧嘴等技术的应用。
1964 年,为提高电弧炉炼钢生产率,降低成本。在美国冶炼石油工程师协会的
电炉会议上,美国碳化物公司施瓦伯(W·E·Schwabe)和西北钢线材公司罗宾逊(C.G.Robinson)根据有关的实验结果,共同提出电弧炉超高功率概念(Ultra High Power,简称 UHP),并在两台 135t 的电弧炉上采用不同的功率水平进行进一步深入的运行试验。随后,瑞典、德国和日本等国也相继采用了这项技术,并取得了良好的效果。不久就在世界各国推广开来。
至此,超高功率电弧炉结合先进的控制技术,已经大大提高了设备的生产效率,使其能够以尽可能大的功率进行熔化、升温操作,进一步满足了熔液清洁度和严格的成分、温度要求。
为了克服交流超高功率电弧炉电弧不稳定、三相供电和熔化不平衡等问题,各国专家们开始了炼钢直流电弧炉的研究,并于 80 年代中期投入使用。
80 年代后期,从传统电弧炉系统及其流程本身和环境保护等方面综合考虑入手,开发出了新型的电弧炉,以提高电弧炉对原料的适应性,将低污染,优化供给电弧炉的能量的使用。其主要的特征表现为废钢预热竖炉化,原料灵活多样化,而炼钢过程追求连续化。开发出了如倾斜电极直流电弧炉(Comelt Process)、转炉型电弧炉(ConArc 炉和 Arcon 炉)及 ContiArc 电弧炉,这几种新型的电弧炉在设计上均各有其显著的特点。这些特点主要集中在:设备的高灵活性,其主要表现是炉子对原料的适应性上;改善能效的同时提高了生产率;改善了最终产品质量;在保证满足环保要求的基础上,充分降低了环保投资和运行成本。
90 年代初,为进一步完善超高功率电弧炉本身的设备和工艺,还相继出现了煤氧喷吹工艺、高阻抗电弧炉、CO 二次燃烧技术、连续炼钢技术、竖炉交/直流电弧炉、双炉壳电弧炉。这些工艺主要集中在废钢预热和减轻电弧炉的熔化负担上。这时,电弧炉炉型结构已出现了根本性的变化。对电弧炉原料类型已无多大的限制,电弧炉的炼钢过程逐渐转向封闭,电弧炉已不仅仅是一个主要用电能来冶炼的设备,甚至还将引入转炉的功能,集转炉和电弧炉功能于一体(ConArc 炉和 Arcon 炉)。可以肯定,高效、节能、环保型电弧炉将是钢的生产技术发展的新方向[2]。
1.3.2 电弧炉在国内的发展
解放前直到60 年代,我国钢铁工业非常薄弱,电弧炉钢产量极低。1966 年西安试制了我国第一台全液压传动、炉盖旋开式顶装料30t 电弧炉,结束仿制的历史。
80 年代末,广州钢厂、抚顺钢厂、舞阳钢厂和天津无缝钢管厂陆续引进了4 台高功率、超高功率电弧炉,并先后进行了水冷炉壁、水冷电极、偏心底出钢、煤氧燃烧嘴、
泡沫渣操作、直流电弧炉等设备工艺技术的开发和工业试验工作。重大进展有[3]:
1) 1988 年原上钢五厂在10.5t 电弧炉上成功采用偏心底技术,实现无渣出钢。
2) 1988 年煤氧枪强化助熔技术在唐钢5t 电弧炉上试验成功。
3) 1988 年,电弧炉-连铸-热送轧制短流程在无锡钢铁厂34t-150m 方坯热轧带钢生产线上试验成功。
4) 1988 年在首钢、抚钢、重钢、上钢三厂等钢厂进行喂线技术试验。
5) 1985 年世界上第一台双电极磁镜式炼钢生产用10t/7MV·A 直流电弧炉在太原重型机械厂投产,此年稳定运行。
6) 1993 年自行设计第一台出钢量为12t,变压器容量为6.3KV·A 的单电极直流电弧炉在上钢五厂投产,取得良好效果。
进入90 年代后,我国电弧炉装备进入了大发展阶段。目前我国设计制造75t
以下的普通功率电弧炉、50t 以下的超高功率电弧炉和150t 以下的钢包精炼炉技术已基本成熟,并具备制造100-130t 电弧炉的能力。能制造50t 以下的直流电弧炉。
1.4 电弧炉自动化技术的发展趋势
在电弧炉熔炼工艺不断发展的同时,电弧炉过程自动化技术也随着整个工业自动化技术的不断进步而发展。电弧炉过程自动化技术的发展始终和计算机技术和控制理论的发展密不可分,大致经历了基础自动化、两级计算机控制系统、分布式计算机控制系统等几个阶段,目前正朝计算机集成自动化方向发展。
1.4.1 电弧炉控制方法理论研究
60、70 年代国外一些学者在电弧炉过程控制理论研究方面作了大量而集中的研究,提出了一些控制算法,从不同的角度对电弧炉控制难点作了深入的分析。
1972 年 Billings 和 Nichilson 提出了电弧炉电极调节温度加权自适应控制算法2[4],该算法以电弧炉中熔池温度能连续检测为前提,以炉温为时变参数的可测辅助变量,其基本思想是认为电弧特性参数的时变性主要是由冶炼过程中炉温变化造成的,其结果导致电极调节系统的开环增益在冶炼过程中的不同时刻有一定的差异。如果对此问题加以考虑,则必然使电极调节系统的调节特性不断地在过阻尼和不稳定状态两个极端之间变化,为了消除这种现象,Billings 等人在文中假设炉温可测的条件下,事先确定了一个以炉温为自变量的权函数,在系统实际运行时用此权函数与取得的控制作用相乘,再作用于被控对象。这样由于炉温不同,相应求得的权函数值也不同,从而使系统的调节特性在整个冶炼过程中保持不变。
这种方法的问题所在是要决定加权函数,由于不能连续直接测试炉温,就需要有可靠性高的状态观测器,目前还无法满足这一要求。
1979 年,Billings 提出了采用弧流/阻抗控制的双模型控制方案[5],即通过检测电流,当电流值达到短路电流值时采用电流控制策略,否则就采用阻抗控制策略。这两种控制方法相结合的优点在于:电流控制策略能够保证短路时对电极进行快速调节,阻抗控制策略则能保持三相互不干扰,自动调节的特点。H.Nicholson 等人提出了电弧炉阻抗在线最优控制方案,该控制方案通过对液压式电极调节器进行分析研究
后,首先给出了系统 11 阶非线性模型,经过线性化及降阶处理后得到了 6 阶的线性模型,并用通常的向量微分方程表示为:X(t)=Ax(t)+Bu(t),然后利用基于二次型的性能指标,求出其最优控制 u(t)。实施在线控制的结果表明,在瞬态特性方面在线最优控制方案要优于模拟控制方案,也优于 PID 控制,只是在求解 Riccti 方程时,加权阵 Q、R 初值的选择尤为重要。
80 年代末,国外一些学者借助于智能控制原理对电弧炉过程控制方法和技术进行了系统的研究。这方面工作具有代表性的应首推美国 Standford 大学的W.E.Staib 等人,他们于 1990 年,成功地将人工神经网络学习技术应用到电弧炉炼钢过程控制中,开发出了“智能电弧炉—IAF”。这是一项创造性的工作,该项专利产品已经在世界上几十座不同吨位的交流电弧炉上得到了实际应用。国内对电弧炉炼钢过程控制理论方面的研究虽然起步较晚,但发展很快。在80 年代初,顾兴源、毛志忠等人提出了电弧炉电极调节自校正控制方案与辨识方法。1985 年张殿华等人提出具有可变遗传因子的电弧炉电极调节自校正控制方案,并且证明了,当被控系统满足确定性、时不变和最小相等条件时,该控制算法具有全局收敛性。1993 年王顺幌等人根据电弧炉炼钢过程特点,在分析其机理的基础上,针对电极升降调节在不同冶炼过程中不同的控制性能要求,提出了电弧炉炼钢过程电极升降智能复合控制方案
[6],为电弧炉冶炼过程节能提供了一个可行方案。1996 年毛志忠、李健提出一种具有前馈环节的电弧炉电极升降自适应控制方案,通过引入前馈控制环节来减小三相电极间的相互影响 ,并在线通过累计实际输入炉内的能量值来间接地估算电弧放大系数 ,从而校正控制器参数。
由以上分析可见,我国在控制理论的方法上,研究水平同国外一些先进国家相比,差距不大,特别是在现代控制方法的研究上(如自适应控制,最优化控制,预测控制等)具有一定的先进水平,但在将这些先进的控制方法转化为生产力的实际控制技术方面的能力与国外先进国家相比,差距比较明显。
1.4.2 电弧炉自动化发展趋势
从电弧炉的控制技术角度来看,把电弧炉控制系统仅仅作为孤立系统的观点已经向将电弧炉冶炼过程控制系统与相关车间(连铸、连轧等)的生产过程控制子系统一起集成起来的方向改变,并和整个企业的商业信息系统等高层次的计算机相连,组成计算机集成制造系统(CIMS)。这不仅要求把整个企业生产流程作为一个整体实现生产自动化,还必须向上级调度管理子系统传送数据并接受生产调度命令,这就对承担基础级生产控制任务的现场仪表和 DCS 提出了新的控制要求,即开放性和可互相操作性。
这样,冶炼过程计算机可从高层管理机上获得订货数据文件和生产调度命令,快速、准确的做出正确的生产、经营决断,合理安排短期内的各个冶炼炉次,从而加快生产节奏、提高经济效益,以使包括所有生产环节在内的整个企业活动能够满足市场多变的需求。
如果想实现以上任务,必须把过程控制集成到整个企业运行的管理系统中。即在控制结构上,将电弧炉的冶炼控制与企业经营管理系统相结合,由多级计算机来进行
全面的协调管理控制,实现综合管理系统功能。
这种计算机集成制造系统的分级控制管理结构,如图 1-1 所示,电弧炉自动化控制系统处于控制层即 1、2、3 级。
综上,电弧炉过程控制技术由常规基础自动化和一般监控功能向计算机人工智能、专家系统操作指导及管理优化方向发展[7]。
尽管我国在控制技术方面的发展同国外先进国家相比,差距还很大,所以要使我国的电弧炉熔炼产品在世界市场具有竞争力,就必须尽最大可能提高产品质量、降低产品成本。要达到这一目的,必须采取先进的过程控制技术,只靠人工手动操作或一般常规控制策略是无法实现的。
图1-4 企业自动化分级控制管理结构
1.5 电弧炉炼钢设备概括
1.5.1 电弧炉炼钢的机械设备
电弧炉的构造主要由炼钢工艺决定,同时与电弧炉的容量大小、装料方式、传动方式等有关[8]。电弧炉的基本结构如图1-5.
图1-5 炼钢电弧炉示意图
1-倾炉用液压缸;2-倾炉摇架;3-炉门;4-熔池;5-炉盖;6-电极;7-电极夹持器;8-炉体;9-电弧;10-出钢槽。
电弧炉的主要机械设备由炉体、电极夹持器、电极升降装置、炉体倾动装置、炉盖提升、旋转装置和炉顶装料系统等以及液压系统、水冷系统、气动系统等辅助系统组成。
炉体:是电弧炉的主要装置,用来熔化炉料和进行各种冶金反应。电弧炉的炉体由金属构件和耐火材料砌筑成的炉衬两部分组成。电弧炉的金属构件包括炉壳、炉门、出钢槽、炉盖圈和电极密封圈。炉壳由钢板焊成,上部有加固圈。炉门可以用来观测炉内情况及进行扒渣等操作,炉盖的上方一有三个呈正三角形不知的电极孔,在孔与电极之间设有电极密封圈。炉壳的上部、炉盖和电极密封圈都通水冷却,炉壳内部、炉盖及出钢槽内部都是用耐火砖砌成的。
电极夹持器及电极升降装置:电极夹持器可以用来夹紧和放松电极,还可以把电流传送到电极上。在熔炼过程中,由于炉料不断熔化,不冈的熔炼阶段要求给出不同的电能。同时,电极自身的长度也会存在自消耗。因此,需要随时升降电极以调整电弧的长度。电极通过电极夹持器固定在电极升降装置上。电极升降装置由导电横臂、立柱和传动装置组成。导电横臂由铜钢复合板制成,作为支持用的机械结果部分,用来固定电极夹头。立柱和导电横臂连接成“厂”形支架,一起在固定的框架内升降,框架固定在炉体的摇架上,框架内装有滚轮,立柱沿滚轮升降。电极夹头、导电横臂都是内部通水冷却。传动方一式为液压传动。电极升降机构包括电极升降液压缸、电极升降立柱、电极喷林环、夹头喷吹等部分。
炉体倾动装置:为底倾机构,传动形式为液压传动。炉子装在专门的摇架上,摇架两侧的扇形板支撑在底座上,倾动时摇架的扇形板沿底座摆动,出钢槽末端的运动轨迹为摆线。倾动时工作液进入液压缸,使液压活塞杆推动摇架,摇架沿水平底座滚动,带动炉体倾动,为防止摇架和水平底座发生相对滑动,在它们的整个接触面上,
分别加工上导钉孔和导钉。倾炉机构包括倾动摇架、倾动轨道、倾动液压缸、水平支撑机构与炉盖旋转轴承和旋转锁定等。倾动摇架下部为弧形结构,在轨道平面上进行滚动,定位准确、可靠。两个活塞式倾动炉液压缸下支座固定在水泥基础上。上支座固定在摇架平台的底部。倾动油路上安装有液压锁,以保证炉子在任何倾动位置失压时,停止不动。水平支撑状态,不得向出渣侧倾动。
炉盖提升及旋转装置:该机构包括炉盖旋转架、炉盖提升缸、提升连杆机构、炉盖旋转机构及锁定机构等。旋转架通过旋转轴承连接在倾动摇架平台上。当固定在平台上的液压缸活塞杆伸出时,可使炉盖旋开。液压缸活塞杆缩回时,炉盖即可复位。旋转架伸出臂下通水冷却,以防止高温变形。
液压系统:液压系统包括液压源、控制阀门、蓄液箱、蓄能器等。液压源有三台恒匿变量泵并配备一定数量的蓄能器。以保证事故状态的应急操作。电极升降采用比例阀,以保证在穿井塌料时电极能快速提升,防止电极碰断和提高灵敏度。炉体倾动采用比例阀,使倾动速度在0-3/s之间随意控制,以满足出钢和快速回倾的要求。炉盖旋转采用比例阀控制,以保证在旋转过程平稳、快速。
水冷系统:为了延长电弧炉的使用寿命以及改善炉前操作条件,电弧炉的许多部位通水冷却,如前所述的炉盖、炉壳等、水冷系统主要包括三部分:水冷炉壁、水冷炉盖和水冷导电横臂、炉体为双层结构,中间为水冷夹层,炉壁匕有入水口和出水口,冷却水不断从夹层中流过,使炉壁冷却。冷却水的进口压力要求一般在1. 45个大气压以上。电炉主体的水冷系统供给水冷炉壁、水冷炉盖、炉门、炉门框、导电横臂电极夹头、电极喷林水冷电缆和铜管等。
气动系统:气动装置为电极夹头清灰,为加料斗气缸、炉门气缸等供气,系统由主阀架气动三大件、气阀等组成,系统压力0. 3Mpa。
1.5.2 电弧炉炼钢的电气设备
电弧炉的电气设备主要分为主电路和电极升降自动调节系统。主电路的任务是将高压电转变为低压大电流输往电弧炉,并以电弧的形式将电能转变为热能。电弧炉的主电路如图1.2,主要由高匿断电器、电抗器、电炉变压器及低压短网等组成[9]。
电弧炉采用三相交流电供电,电气设备主要包括以下几个部分:高压供电系统、二次回路、电炉变压器、电抗器、短网、低压供电系统和控制系统。
高压系统:一股由35Kv电,经高压隔离开关、高压真空断路器、电抗器送至电弧炉变压器,在高压供电系统中设有氧化锌避雷器、阻容吸收器,作为电压吸收装置,吸收操作电压和浪涌过电压,以保证变压器正常运行。高压测二次计量回路设有高压侧电压、高压侧电流、功率因数、有功功率、有功电度及无功电度的计量,二次保护回路设有过电流保护、欠压保护、缺相保护、变压器温度保护、变压器瓦斯保护及冷却器保护等完善的保护回路。
电炉变压器:采用高阻抗电弧炉专用变压器,变压器采用有载电动调压,低压二次侧采用铜管侧出线、内封口,采用强油循环水冷却器进行冷却。变压器配套强油循环冷却器及其电气控制台。
电抗器:电抗器为外附电抗器,无载调节可连续过载20%,配有隔离开关,接地
开关。
短网:也称大电流线路,是指从电弧炉变压器低压出线到电极(包括电极)之间的各种形式导体的总和。电流经短网送入炉内,产生电流,将电能变成热能,把炉料熔化。
低压动力及控制电源:由系统动力柜接收车间馈电,进线电压380/220V,三相四线制。主要是给液压站、高压泵、加热器、闸整流电源、电炉变压器调压控制器、油水冷却器、仪表电源、控制电源、稳压电源等供电。
图1-6 电弧炉主电路简图
1-高压电缆;2-隔离开关;3-高压断路器;4-电抗器;5-电抗器短炉开关; 6-电炉变压器;7一电板;8-电弧;9-金属。
1.6 电弧炉炼钢过程及工艺简介
1.6.1 电弧炉炼钢过程
电弧炉是以电弧为主要热源的电炉,分为直流电弧炉和交流电弧炉两种。在电弧炉炼钢过程中,电弧产生于专用的电极棒和被熔化的炉料之间,炉料受到电弧的直接加热。
电弧炉是继转炉、平炉之后出现的又一种炼钢方法,已有百年历史。目前世界上
电炉钢产量95%以上都是由交流电弧炉生产的,已成为主要的炼钢方法之一。
如图1.3三相电弧炉构造简图。它由一台特种变压器的三相交流电供电,三相交流电流通过3个上下移动的电极直接加热炉内金属。[10]
图 1-7 三相电弧炉构造简图
1-炉底;2-钢液;3-渣层;4-流钢嘴:5-炉顶;6-电极;7-电极夹持器;8-短网;9-电炉变压器;10-炉门。
电弧炉整个炼钢过程一般分为熔化期、氧化期和还原期三个时期,各个时期对冶炼温度和功率的要求各不相同。
熔化期的任务是将固体炉料熔化为钢液,这个时期要求尽可能地向炉内输入最大电功率以保证炉料在最短的时间内熔为金属液。氧化期主要是通过脱碳反应而造成钢液沸腾,从而达到除磷、除杂、均匀等目的。还原期的主要任务是:(l)使钢和炉渣还原;(2)去除钢液中的氧和硫,使其舍量达到规定的要求;(3)调整钢液的化学成分,使其达到要求;(4)加热钢液至正常出钢温度。电弧炉炼钢过程工艺如图1-8所示。
图 1-8 电弧炉炼钢工艺过程
1.6.2 电弧炉工艺简述
电弧炉炼钢的工艺方法归纳起来有三种,即氧化法、不氧化法和返回吹氧法。氧化法是电弧炉炼钢工艺的最基本的方法,不氧化法和返回吹氧法都是在氧化法的基础
上发展起来的[11]。
传统的氧化法冶炼工艺由补炉、装料、熔化期、氧化期、还原期和出钢六个阶段组成。在炉内即要完成熔化、脱磷、脱碳、升温,又要进行脱氧、脱硫、去气、去除夹杂物、合金化以及温度成分的调整,因而冶炼周期很长。这即难保证对钢材越来越严格的质量要求,又限制了电弧炉生产率的提高。工艺上的改进大大提高了电弧炉设备能力,使其能够以尽可能大的功率进行熔化、升温操作,而把那些只需要较低功率的操作转移到钢包精练炉内进行。并且越来越完善的电弧技术能进一步满足钢液纯度和严格的成分、温度控制的要求。同时,在现代电弧炉炼钢工艺中,在熔化初期就对炉内进行吹氧,因此熔化期和氧化期己无明显的区分,所以现代电弧炉炼钢工艺包括补炉、装料、熔氧期和出钢四个阶段。
补炉:补炉是指当上炉出钢完后,霈要迅速将炉体损坏的部位进行维修,以保证下一炉钢的正常冶炼。
装料:装料是指将固体炉料装入炉膛内。目前多数电弧炉采用炉盖上升,炉体开出,或者炉盖升起旋开,用吊车吊起炉料一次加入炉膛内。
熔氧期:从通电开始到出钢阶段称为熔氧期。熔氧期的主要任务是迅速熔化全部炉料,去除钢液中的磷、气体和夹杂物,将钢液温度加热到高于出钢温度10-20℃。为了加速熔化和节约电能,在熔氧期一般采用吹氧助熔,有条件的也可以采川煤氧助熔。
出钢:钢液脱碳、脱磷良好,化学成分符合要求,温度达到出钢要求,炉渣合乎出钢要求,即可出钢。
1.6.3 电弧炉工艺对控制系统的要求
由于炼钢工艺在电弧炉炼钢上采用了多种提高冶炼效果,缩短炼钢时间,节能降耗的技术,从而使电弧炉的控制系统更为复杂。例如在电弧炉上采用吹氧技术之后,对计算机控制系统的要求是:在炼钢过程中如何达到最佳的脱碳效果,同时要控制化学反应中产生的一氧化碳在炉内进行充分二次燃烧。控制吹氧的效果,确保浮渣的厚度足以去覆盖电弧,从而保证电能效率得以最大限度地发挥,提高钢水的搅拌效果,迅速把热能传递给需熔化的废钢,扩大氧和钢水之间反应的有效区域,允许电弧炉进行长弧操作。综合各种因素的控制,达到最大功率的冶炼效果[12]。
1.6.4 电弧炉炼钢工艺对电极调节器的要求
电极调节器的调节条件和调节任务颇为复杂。在起弧熔化冷料时,长度为数毫米的电弧在不甚大的范围内,就能产生数千千瓦的功率,此时电弧温度高达数千度,被熔料在电极下面迅速而激烈的熔化、飞溅,时有短路和断弧现象发生,因此弧长、输入功率不断变化。当电弧电流小于额定值时,输入到炉内的电能减少,熔化时间拖长,电能及电极消耗均有增加:而当电流非常大时,虽仅数秒钟,就能使线路损耗大大增加,导致输入电弧妒内的电能减少,降低设备的各项指标,此时电弧长度非常短,特别使当电极同炽热或液态熔液接触时,会使熔液遭受增碳的危险,严重时可折断电极。可见,电弧炉电极调节器的调节任务非常关键,即在保证稳定调节的条件下,要求电
极调节器灵敏度高,快速性好,超调小。
具体的说,40吨电弧炉对自动调节器的要求如下:
(1) 高灵敏度。对电弧电流变化的反应要灵敏,可以用非灵敏区来衡量。非灵敏区指当电极调节被控量偏差发生变化时,电极仍保持静止的整个区间。通常用不感系数来代表调节器非灵敏区的大小。执行机构在开始向两个方向动作时的被调量之差与其算术平均值之比的百分数称为不感系数。
(2) 电极调节快速性好。电极提升速度要快,否则容易造成短路而使高压断路器自动跳闸;下降要慢,以免电极碰撞炉料而折断或插入熔液中。电极速度由零升至最大速度的90%所需时间不得大于0.3S,电极速度由最大速度降到10%所需的时间不得大于0.15S。
(3) 保证电弧电流能在额定值的30-125%的范围内平滑的整定。
(4) 电极同炉料短路时,在保证电弧稳定的情况下,应使电极以最大速度上升。
(5) 保证电极升降控制能迅速的从自动切换为手动,或由手动切换为自动。
(6) 屯弧炉通电时,电极调节器应能保证自动燃弧。
(7) 调节器应能保证调节工作高度可靠,操作简单。
上面的各项要求,最重要的是快速性、灵敏度和系统的超调量小。调节器的快速作用能够提高电弧功率平均值、功率因数COSQ和电效率r1,改善电气设备的工作条件,同时有利于减少电极对熔液增碳。足够高的灵敏度不但能以高准确度来维持每相电弧功率相等,而且能改善各项性能指标。如电弧功率平均值、功率因数COSQ 和电效率r1。除此以外,还能消除每个电弧周围的耐火砖受热不均匀的可能性。高灵敏度、快速性和整个系统的超调量控制之间的正确配合是设计性能优越调节器的决定性条件。
2. 电弧炉炼钢控制系统
2.1 电极升降自动控制系统
电弧炉炼钢应遵循高产、优质、低消耗的原则。因此,各类钢种的冶炼过程的供电制度应符合其工艺原则。
如图2-1为10t电弧炉,变压器容量为5500KVA的电力曲线控制实例。图中纵坐标为输入电流(A),曲线上标明输入电压值(V),输入功率即为二者乘积,图中阴影部分为电流可调节的范围,其值应根据刚液温度灵活掌握。表2-1为40t电弧炉,变压器容量16MVA的供电制度。
图2-1 10t电弧炉冶炼过程电力曲线控制图
表2-1 40t,16MAV电弧炉变压器的供电制度
电力曲线分析:
(1) 熔化期。在通电起弧5~l0min内,为了避免弧光损坏炉盖,此阶段输入中级电压,中级电流;l0min后,熔炼进入穿井和电极回升阶段,为促使炉料快速熔化,此阶段输入最大电压和最大电流,直到炉料熔化掉80%以上,熔池面逐渐上升平展,只剩下炉坡,渣线处和低温区附近的一些炉料。同时,电极也相应上升,电弧也暴露
在熔池面上,如果继续采用高电压、大电流,势必严重损坏炉体和炉盖,故改用中级电压、中级电流,减少输入功率,一直保持到炉料全熔,并将钢液加热到需要的温度为止。
(2) 氧化期。这个阶段的主要任务之一就是合理地把钢液温度加热到出钢温度或高于出钢温度。与熔化期相比,输入功率可适当减少,一般采用中级电压和中级电流送电。
(3) 还原期。加入稀薄渣料后,为了减少脱氧剂烧损及维护炉衬,应立即转为低级电压供电。在正常情况下,应输入小功率只需弥补炉子正常的散热损失。
电极自动调节系统必须适应炼钢的合理供电规则,使炉料熔化时间最短、电能消耗最小。炉料的熔化时间友下式确定:
ks
e P P G E t -=η0 (2-1)
式中 e η——熔化期内平均电效应;
P ——熔化期电弧炉变压器自电网取得平均功率,KW ;
ks P ——用来补充损失的功率,KW ;
G ——装入炉中的炉料重量,t ;
0E ——熔化1t 金属在理论上的电能消耗,KW ·h/t 。
式中说明:炼钢时间取决于输入炉膛的平均功率和炼钢中散热损失的功率。为了减少电能消耗,减少冶炼时间以便减小散热损失的电能,应视炼钢工艺过程情况合理调节输入到炉膛的功率。电路功率的调节实际上是通过调节变压器档位和电极电弧的长度来实现的。
2.1.1 电极调节器的特点
在电弧炉的生产过程中,由于钢水的沸腾,钢水表面起伏不定,必然导致电弧长度忽短忽长,时刻变化。虽然此时电弧的长度受到的扰动较其它时期要小得多,也平稳得多,但同样能使弧电压和弧电流不停地变动,供电电能很大比例地消耗在网络的变压器中,既提高了成本,又对电网不利。因此调节器的首要任务就是根据炉内的情况及时调节极棒的位置,进而达到调节电弧长度的目的,使电弧功率保持在一定数值。但是由于炼钢过程中炉内复杂多变的炉况和时变的电弧增益,要达到此目的并不容易,这就对电极调节器的功能提出了更高的要求。
首先,要选择一个比较好的控制原则,电极调节器对电弧长度的调节量是通过一些控制原则来进行的。一个好的控制原则是电极调节器控制性能的基本保证,控制原则的选择将在后面讨论。
其次,炉内钢水的沸腾对电弧长度产生干扰,且这种干扰是无确定的规律可循的,是一随机过程。若使电极调节器具有良好的调节功能,它必须具备一定的消除随机噪声干扰的能力。还有电极调节的快速性也是非常重要的,当电弧长度发生改变后,它
应尽快予以纠正,动作迟缓将达不到理想的控制效果。甚至当调节过分不灵敏时,会有断弧或短路发生。
最后,电弧的增益随着温度发生变化也是电极调节器所要考虑的一个问题,所以它要具有抗参数时变的能力,即鲁棒性好。另外,由于炉内废钢的放置不是均匀的,因而三相电极之间是不平衡的。同时,三相电极之间也存在相互间的影响。这些都是设计电极调节器时需要考虑的。
综上所述一个良好的电弧炉炼钢电极调节器应具有以下的特点:
① 保证电极在一定控制原则下点弧工作;
② 抗干扰性好;
③ 调节灵敏、迅速。
④ 良好的三相间的平衡性及相互间的尽可能小的影响。
2.1.2 电极调节控制原理
50吨电弧炉电极调节控制系统采用恒阻抗控制策略。
即:
()()()k I K k U K k E **21-= (2-2) ()()()k I K k U K i *21-=
式中:()k U —实测电弧电压 ()k I —实测电弧电流
1K — 由系统特性决定的电压系数
2K — 由系统特性决定的电流系数
i K 2— 等效电流系数
采用增量式 PID 算法得到增量公式:
()()()1--=?k U k U k U
()()[]()k E K k E k E K I P *1*+--=
()()()[]212*-+--+k E k E k E K d
(2-3)
式中:
()k E —当前偏差 ()1-k E —前一次偏差
()2-k E —前两次偏差 P K —比例系数
i K —积分系数 d K —微分系数
()k U —当前控制信号 ()1-k U —前一次控制信号
带有前馈环节的控制量输出公式为:
()()()C A A A A I f k U k U k U +?+-=1 (2-4)
()()()A B B B B I f k U k U k U +?+-=1 (2-5)
()()()B C C C C I f k U k U k U +?+-=1 (2-6) 式中:A f —A 相前馈系数
A I 、
B I 、
C I —分别为 A 、B 、C 相电流
采用非线性控制器的控制量输出公式:
()()[]()2
**k E k E sign K k U P = (2-7)
式中: P K —比例系数 U(k)、E(k)同上
()[]()()???-≥=0101< k ifE k ifE k E sign (2-8) 1)推导i K 2 计算公式 理想状况下:设定值和反馈值的偏差为零。即:
()()()02=?-=k I K k U k E i i n i (2-9) 所以推出
()()k I k U K i n i =2 (2-10)
式中:()k U n ——第n 档电压对应的数字量 (n=1~12) ()
k I i ——第i 相电弧电流的设定值对应的数字量 (i=A,B,C )
由于本系统选用的一次侧电流互感器变送器为(25000:5),电流变送器输入交流电流I max= 5A (额定值),输出直流电压V max=4~20mV 。且由于模拟量输出模板组态为:输出直流电压0~10V ,对应数字量0~27648。所以,可以推出电流(单位安培)与数字量之间的对应关系:
()()2500027648k I k I si i ?= (2-11)
式中:()k I si ——第i 相电弧电流的设定值 (i=A,B,C 单位:安培)
综上所述,推出i K 2计算公式:
()()27648250002??=k I k U K si n i (2-12)
式中:()k U n ——第n 档电压对应的数字量 (n=1~12)
()k I si ——第i 相电弧电流的设定值 (i=A,B,C 单位:安培)
2)推倒实际控制偏差()k E i
实际电极调节控制过程中,()k E i 不可能为零。通过(2-12)所给出的i K 2计算公式,可以按照下述公式计算电极条的实际偏差值 ()k E i 。即:
()()()k I K k U K E fi i fi i ?-=2 (2-13)
式中:()k U fi ——第i 相电弧电压反馈值 (i=A,B,C ) ()k I fi ——第i 相电弧电流反馈值 (i=A,B,C )
通过对计算得出的调节偏差,针对电弧炉不同熔炼阶段,采用(2-4)(2-6)的控制算法进行电极调节控制,来实现电极升降自动调节。 2.2 液压、水冷、气动控制系统
2.2.1 液压控制系统
电弧炉电极升降机构采用液压传动方式控制的,称为全液压传动电弧炉。由于电极升降的液压缸动作十分频繁,其工作时间几乎就是冶金时间,需要一个长时间供应压力液体的液压系统,故一般都设有液压力蓄势器(贮压罐)作为长期供应的压力源,整个液压系统比较复杂。而一般液压传动的电弧炉,其电极升降机构作为机械传动,在电炉冶炼工作时,只要其他机构不动作,液压系统的油泵可以停止工作,也不需要蓄势器,液压系统较为简单[13]。
电弧炉液压系统由四个部分组成:
(1) 驱动部分:即油泵,它的作用是将机械能转换为液体的压力能。
(2) 执行部分:即油缸,它的作用是将压力液体的压力能转换为工作部件运动的机械能。
(3) 控制部分:即控制液流的压力、流量和方向的各种阀件。它的作用是满足执行部件提出的推动要求、动作方向要求和动作速度要求等。
(4) 辅助部分:包括油管、邮箱、蓄能器、滤油管、管接头、压力表和液位计等。它的作用是将驱动部分、控制部分和执行部分连成一个系统,并具有连接、测量、贮液、蓄能和过滤等功能。
2.2.2 水冷控制系统
水冷系统包括短网的三相大截面水冷电缆、电极夹持器、导电横臂、炉体、炉门及水冷壁、水冷炉盖圈。
电弧炉操作规程标准范本
操作规程编号:LX-FS-A39247 电弧炉操作规程标准范本 In The Daily Work Environment, The Operation Standards Are Restricted, And Relevant Personnel Are Required To Abide By The Corresponding Procedures And Codes Of Conduct, So That The Overall Behavior Can Reach The Specified Standards 编写:_________________________ 审批:_________________________ 时间:________年_____月_____日 A4打印/ 新修订/ 完整/ 内容可编辑
电弧炉操作规程标准范本 使用说明:本操作规程资料适用于日常工作环境中对既定操作标准、规范进行约束,并要求相关人员共同遵守对应的办事规程与行动准则,使整体行为或活动达到或超越规定的标准。资料内容可按真实状况进行条款调整,套用时请仔细阅读。 本规程适用机型:ДC-5M;ДC-5MT 额定容量:5吨 1、遵守铸造设备通用操作规程。 2、检查行程开关和碰块的位置是否正确,如不正确,必须调整。 3、检查电极平衡锤,炉门平衡锤是否完全可靠,如不安全可靠,要及时修理。
4、检查电极升降齿轮齿条的啮合情况是否良好。 5、全面空运转试车,并进行以下检查: a、每相电极升降各两次,观察运动情况是否良好,电极升降不得超过1.8米; b、开动台车进出各两次,观看传动系统的运动是否正常,导轨是否平整。注意电炉水管在台车进出过程中不许被挂坏。 c、开动倾炉装置两次,观看传动系统的运动是否正常,行程开关是否灵敏可靠,包闸松紧是否合适。炉子前倾角度不和超过10°,后倾角度(出钢方
毕业设计(论文)文献综述模板
武汉理工大学 毕业设计(论文) 开题报告及文献综述 论文题目 学院(系):理学院 专业班级:电信科0802班 学生姓名:孙阳 指导教师:刘成国
本科生毕业设计(论文)任务书 学生姓名:孙阳专业班级:电信科0802 指导教师:刘成国工作单位:武汉理工大学 设计(论文)题目: 智能加温控制器的改进设计与实现 设计(论文)主要内容: (1) 研究已有智能温控系统,确定系统改进方案; (2) 设计各子系统电路,完成控制电路、显示电路和整机的设计与实现; (3) 研究改进的控制模式,形成代码,在单片机系统中运行; (4) 翻译与本题目有关的外文文献; (5) 撰写毕业论文。 要求完成的主要任务: (1) 查阅不少于15篇的相关资料,其中英文文献不少于2篇,完成开题报告; (2) 完成电路的设计、系统的联试和整机调式、安装; (3) 测试系统功能,完善系统样机功能; (4) 按要求完成不少于5000汉字的英文文献翻译; (5) 完成不少于12000字数的毕业论文。 必读参考资料: [1] 高峰. 单片微型计算机原理与接口技术.科学出版社[M].2009 [2] Zhang Huaguang, He Xiji, Fuzzy auto-adapting control and application[J], The publishing company of Beijing University of Aeronautics &Astronautics, 297-306,2002. [3] Li Zhuo, Xiao Deyun, He Shizhong, Fuzzy auto-adapting PID control method based on neural network[J], Control and decision-making, (3), 340-345, 1996. 指导教师签名:系主任签名: 院长签名(章)
大型炼钢电弧炉对电网及自身的影响和抑制方案
大型炼钢电弧炉对电网及自身的影响和抑制方案.txt26选择自信,就是选择豁达坦然,就是选择在名利面前岿然不动,就是选择在势力面前昂首挺胸,撑开自信的帆破流向前,展示搏击的风采。大型炼钢电弧炉对电网及自身的影响和抑制方案 翁利民,陈允平,舒立平 (武汉大学电气工程学院,湖北省武汉市430072) 摘要:详细分析了现代大型炼钢电弧炉对电网不利影响的4个方面:即电压波动、电压畸变、负序电压与电流、功率因数低,并结合实际从量的概念上认识其对自身在增加损耗、继电保护误动、增加网损、降低生产效益等方面的影响;介绍了抑制电弧炉的常规有效措施,得出了合理的结论。 关键词:电压闪变;电压波动;SVC;滤波器 1 引言 现代大型超高功率炼钢电弧炉,由于其容量大,是用电大户,对电网的影响具有举足轻重的作用。它具有功率因数低,无功波动负荷大且急剧变动,产生有害的高次谐波电流,三相负荷严重不平衡产生负序电流等对电网不利的因素,使得电网电能质量恶化,危及发配电和大量用户,也影响电炉自身的产量、质量,使电耗、电极消耗增大,从而成为电网的主要公害之一。现在有关大型电炉对电网公害抑制的研究也正在深入开展,有必要对其不利影响和抑制对策作一概述性的分析。 2 现代大型电炉对电网的影响 2.1 引起电网电压急剧波动 大型电炉在打孔期和熔化期电弧长度急剧变化,引起无功负荷急剧波动,其工作短路功率为电炉变压器额定功率的两倍左右,其最大波动无功为电炉变压器额定功率的1.5倍左右(具体倍数取决于短网阻抗、电炉变压器阻抗、供电系统阻抗之和的大小,总阻抗大则工作短路倍数小,反之则大)。无功的急剧波动,引起电网电压的急剧波动,其波动频率一般为1~15Hz,使灯光和电视机屏幕产生闪烁,使人视觉疲劳而感到烦躁,此外还影响到晶闸管设备和精密仪表等的稳定运行,甚至产生质量事故。国标GB12326-2000《电能质量电压允许波动和闪变》规定了电力系统公共供电点各级电压等级的电压波动和闪变允许值。 2.2 使电网电压波形产生畸变 电炉在熔化和打孔期,电弧电流是不规则的,且急剧变化,其电流波形不是正弦波,可分解为2次和2次以上的各次谐波电流,主要为2~7次,其中2次和3次最大,其平均值可达基波分量的5%~10%,最大可达15%~30%;4~7次平均值为2%~6%,最大值可达6%~15%。而电网中的铁磁元件也产生高次谐波,以3次和5次谐波电流较大,其中3次分量最大,而电炉刚好也是3次谐波电流很大,这对电网是极为不利的。谐波电流流入电网,使其电压波形发生畸变,引起电气设备发热、振动,增加损耗,干扰通信,使电力电缆局部放电绝缘损坏,电容器过载损坏等,国家标准GB/T14549-1993《电能质量公用电网谐波》规定了电压波形畸变率限值。 2.3 使电网电压产生负序分量 电炉在熔化期,特别是打孔期,各相电弧电压是独立变化的,三相电弧各自发生急剧无规则变化,故其三相电流是不对称的。在正常生产情况下,产生的负序电流约为电炉变压器额定电流的25%左右;在不正常情况下,如一相断弧时,可达56%左右,如两相短路的同时,第三相又断弧,此时可达86%左右。负序电流流入电网,使电网电压产生负序分量,影响发电机和用电设备使用效果,严重时可能造成损坏,还会使继电保护误动作,其严重程度一般用不平衡度(即负序电压与正序电压分量之比的百分数)表示,国标GB/T15543-1995《电能
水温自动控制系统毕业设计论文(DOC)
毕业设计论文 水温自动控制系统 钟野 院系:电子信息工程学系 专业:电气自动化技术 班级: 学号: 指导教师: 职称(或学位): 2011年5 月
目录 1 引言 (2) 2 方案设计 (2) 2.1 总体系统的设计思路 (2) 2.2 部分外围系统的设计思路 (3) 3 硬件电路设计 (3) 3.1 单片机最小系统的设计 (3) 3.2 温度检测电路的设计与论证 (4) 3.3 显示功能电路的设计与论证 (5) 3.4 温度报警提示功能电路的设计与论证 (5) 3.5 外围电路控制设计 (6) 3.6 扩展部分方案设计 (7) 4 软件设计 (7) 4.1 控制主程序设计 (7) 4.2 温度设置程序设计 (8) 4.3 上下限报警程序设计 (8) 5 结论 (9) 结束语 (9) 致谢 (10) 参考文献 (10) 附录............................................................................................................... 错误!未定义书签。
水温自动控制系统 钟野 (XXXX电子信息工程学系指导教师:CXJ) 摘要:本文设计主要是采用A T89C51单片机为控制核心、以温度传感器(DS18B20)为温度采集元件, 外加温度设置电路、温度采集电路、显示电路、报警电路和加热电路来实现对水温的显示同时自动检测及线性化处理,其误差小于±0.5℃。本文重点介绍硬件设计方案的论证和选择,以及各部分功能控制的软件的设计。本次设计的目标在于:由单片机来实现水温的自动检测及自动控制,实现设备的智能化。 关键词:单片机;温度传感器;自动控制 Abstract: This paper is designed AT89C51 microcontroller as control core and temperature sensor DS18B20) for (temperature gathering element, plus the temperature setting circuit, temperature gathering electriccircuit, display circuit, alarm circuit and heating circuit to achieve water temperature display while automatically detecting and linearization, its error is less than 0.5 + ℃. This paper mainly introduces the hardware design argumentation and choice, and some functional control software design. This design goal is: by single-chip microcomputer to realize the automatic detection and automatic temperature control, realize the intellectualized equipment. Keywords: Microcontroller; Temperature sensors; Automatic control
电弧炉工艺操作流程
电弧炉工艺流程和注意事项 1、班长进行人员工作安排,设备巡检和辅料准备。 2、出钢时,有人专门联系行车吊料或换电极,出钢完后,清理EBT,保证出钢口通透,旋托盘的时候,要观察是否到位,不到位需要重新再打开,多次不到位必须联系钳工处理。填充料灌完形成馒头状,灌少不安全,灌多浪费成本。 3、专人摇平炉体(班长,副班长,配电工),打起支撑,若指示灯不亮,必须先亲自确认,再倾炉。根据炉底情况考虑是不是要加1-2吨石灰,提起电极到位,大炉盖到位,打开炉盖旋转锁,旋开炉盖到位。观察炉内情况,需要补炉时,要做到快补,薄补,高温补,提前检查喷补系统设备。 4、加料专人指挥,对讲机按着红灯亮再说话,保证一个加料过程中的电量,料罐到位小勾再起,指挥人员要站在既保证安全,又能看到行车操作的位置。 5、加完料之前,要观察是否调节电极长度,两人配合作业(优先班长和配电工),注意炉盖必须旋开到位,然后下电极挨着小平台,再看清是几号电极抱闸钥匙孔,打开钥匙,打开抱闸按钮。 6、配电操作根据炉料的情况分二种配电方式: A、好料,本厂情况基本为加工料(一级料和打碎料为主),以两次加料配电方式为:电压17或16档,电流50-55KA起
弧,电极穿井(3-6)分钟到位,提起电极,让其自己断弧,然后调节档位至(12-13-14)档化料,观察实际电流是否平稳,来不断的提升电流,电流根据目前的电极质量最大可以到65KA,超过65KA电极本身消耗过快。大档位二十分钟,然后档位调小至14-15档送电(5-10)分钟,在通电期间加石灰(2-3)吨,加料专人指挥料罐吊起,加料。第二次化料同上操作,注意后面料化至弧光快埋不住的时候,降低档位到15-16档,提高电流。 B、差料,本厂情况基本为返回料(渣包,钢渣,钢砂为主),埋弧效果不好,配电方式为,电压17或16档,电流50-55KA 起弧,观察电极穿井到位时间较长(8-12)分钟,提起电极,让其自己断弧,然后调节档位至(13-14-15)档化料,观察实际电流是否平稳,来不断的提高电流,在通电期间均匀的加石灰,注意后面料化至弧光快埋不住的时候,降低档位到15-16档,提高电流。配电前了解炉料情况,注意喷火、飞溅、塌料、翻腾等现象。 7、吹氧根据炉料配硅情况,硅高时早吹助熔,硅低时晚吹控制吹氧量,化掉炉门口的料或叉车推料,升温过程中准备喷碳化硅还原。 8、还原操作分两种情况: A、高硅料时,料罐加石灰2吨,炉底埋管一根,增加吹氧量,可以加快冶炼节奏,等温度上来,料化清的时候还原,喷
毕业设计(论文)材料归档要求
毕业设计(论文)材料归档要求 一、封面(红色) 论文全部完成经审核后填写 封面、论文正文、任务书、中期检查表、答辩记录表、成绩评定表等表格中的论文题目需与“选题汇总表”保持一致,不得更改。 二、论文 毕业设计(论文)用计算机打印,纸张一律使用A4复印纸 页眉:苏州大学本科生毕业设计(论文)(无论是做设计或是论文,页眉均照此编排) 毕业论文正文需不少于6000字。 毕业设计正文可写2000-3000字(上不封顶),必须配图(设计图请调整好格式大小),同一设计课题组的正文不能雷同。 1、目录 需含页眉:苏州大学本科生毕业设计(论文) 目录采用四号宋体字。如分章节的论文,则目录中每章题目用四号黑体字,每节题目用四号宋体字,并注明各章节起始页码,题目和页码用“……”相连,如下所示: 目录 第1章XXXX┈┈┈┈┈┈(1) 第1.1节XXXX┈┈┈┈┈(2) 2、中英文摘要、关键词(从本页开始编页码) 需含页眉:苏州大学本科生毕业设计(论文) 论文题目下面注明:学院、年级、专业、姓名、学号(署名均采用五号宋体字) 中文摘要、关键词采用小四号宋体字,外文摘要、关键词采用四号“Times New Roman”字型。 (论文题目无需进行外文翻译) 论文题目下面的格式示例如下: 关于河流的研究 金螳螂建筑与城市环境学院 2008级园林(城市园林) (备注:此段在同一行,居中) 张三 0841404090 指导教师:李四 (备注:此段在同一行,居中) 3、前言 含页眉:苏州大学本科生毕业设计(论文) 格式要求同“论文正文” 4、论文正文
含页眉:苏州大学本科生毕业设计(论文) (1)正文文字内容字型一律采用宋体,标题加黑.章节题目采用小三号字,正文中文内容采用小四号宋体,外文内容采用四号Times New Roman字型。 (2)章节题目间、每节题目与正文间空一个标准行。(章节不分大小,均采用小三号字,空行要求均相同。如:第1章***、1.1***、1.1.2***、“参考文献”、“致谢”等标题均为章节) (3)页面设置: 单面打印:上2cm,下2cm,左2.5cm,右1.5Cm,装订线0.5cm,选择“不对称页边距”, 页眉1.2cm,页脚1.5cm。页眉设置:居中,以小5号字宋体键入“苏州大学本科生毕业设计(论文)”。页脚设置:插入页码,居中。 正文选择格式段落为:固定值,22磅,段前、段后均为0磅。 标题可适当选择加宽。 5、结论 格式要求同“论文正文” 6、参考文献 (1)正文引用参考文献处应以方括号标注出。如“…效率可提高25%[1]。”表示此数据援引自文献1。(2)参考文献的编写格式的参考标准为《文后参考文献著录规则》(GB/T 7714-2005): ①专著 主要责任者.题名:其他题名信息[文献类型标志].其他责任者.版本项.出版地:出版者,出版年:引文页码[引用日期].获取和访问路径. ②专著中的析出文献 析出文献主要责任者.析出文献题名[文献类型标志].析出文献其他责任者//专著主要责任者.专著题名:其他题名信息.版本项.出版地:出版者,出版年:析出文献的页码[引用日期].获取和访问路径. ③连续出版物 主要责任者.题名:其他题名信息[文献类型标志].年,卷(期)-年,卷(期).出版地:出版者,出版年[引用日期].获取和访问路径. ④连续出版物中的析出文献 析出文献主要责任者.析出文献题名[文献类型标志].连续出版物题名:其他题名信息,年,卷(期):页码[引用日期].获取和访问路径. ⑤专利文献 专利申请者或所有者.专利题名:专利国别,专利号[文献类型标志].公告日期或公开日期[引用日期].获取和访问路径 ⑥电子文献 主要责任者.题名:其他题名信息[文献类型标志/文献载体标志].出版地:出版者,出版年(更新或修改日期)[引用日期].获取和访问路径. 7、致谢 格式要求同“论文正文” 8、附录(符号说明、原始材料等) 格式要求同“论文正文”
0.5吨电弧炉630KVA直流电炉(炼铁)主要参数
630 KV A 直流电炉(炼铁)主要参数 1 电源系统: 变压器容量630 KV A,油浸自冷,一次电压10 KV。六相十二脉整流,ZP5000A/1200V,直流电压75—110 V,分7级,低压3级恒电流,高压3级恒功率。 一次电流36.4 A,直流额定电流9545 A。 2 电极升降系统: 电极升降速度约1.2 米/分钟,行程约1500mm,钢丝绳卷扬系统。 紫铜电极夹持器,石墨电极直径250 mm,1根。 3 炉体系统: 炉体尺寸:外径X高度1800 mm X 1800 mm 炉膛尺寸:内径X深度800 mm X 1000 mm 炉底厚度:800 mm,炉衬厚度:500 mm 炉盖尺寸:外径X高度1600 mm X 400 mm 4 炉体倾转液压系统 5 短网: 连接铜排 水冷电缆 1000 mm2X 4.5(4.0) m,4根。 成套设备包括:
1 高压控制柜一台 具有过流、过压、防雷保护,功率显示,瓦斯报警,温度报警等功能。 2 低压操作柜一台(含自动化系统:PLC编程,变频器,触摸式操作屏等,无纸记录仪、水温显示,功率显示,高温、过流报警等) 3 电炉变压器一台 4 电极升降架一套 5 电极夹持器一套 5 炉体和炉盖一套 6 炉体倾转液压系统一套 7 短网铜排和水冷电缆四根 8 冷却水系统一套 合计40万。(包安装调试,但不含炉衬材料和砌筑) 2011-9-30 接电极高度约4.5米(吊钩高度) 炉体下部挖约1.5米地坑,炉体支撑轴离地面约0.5米 成套设备占地面积约8X8米 冷却水循环水量约8立方米。电缆和炉底电极冷却,筑炉材料6-7吨,熔池装水1.5吨
大型电弧炉冶炼作业炉内爆炸事故现场应急处置方案
编号:AQ-BH-00440 ( 应急管理) 单位:_____________________ 审批:_____________________ 日期:_____________________ WORD文档/ A4打印/ 可编辑 大型电弧炉冶炼作业炉内爆炸事故现场应急处置方案On site emergency disposal plan of explosion accident in large EAF smelting operation
大型电弧炉冶炼作业炉内爆炸事故 现场应急处置方案 备注:应急预案明确了应急救援的范围和体系,有利于做出及时的应急响应,当发生超过应急能力的重大事故时,便于与应急部门的协调,降低事故的危害程度。 大型电弧炉冶炼作业炉内爆炸事故现场应急处置方案 事故特征 事故类型和危险程度 灼烧伤事故:危险程度极高,炉体发生爆炸造成火灾、设备设施受损及人员伤亡事故。 事故征兆 冶炼时发生水冷板向炉内漏水,电弧声音异常,炉内气氛异常,白色烟尘较大。 事故发生区域 电弧炉冶炼炉台。 事故发生岗位
炉台冶炼班组、维修人员等。 事故发生季节 无季节性 应急组织与职责 应急小组 组长:主管安全生产领导 副组长:当班负责人 成员:现场作业人员 应急小组职责 1.在电弧炉冶炼前,做好生产前的各项准备工作,制定应急措施及检查应急物品准备。 2.现场组织指挥,实施救援行动。 3.向上级汇报事故情况或启动应急救援预案。 应急成员职责 1.组长负责全面协调指挥工作。 2.副组长负责现场全面指挥,负责人员疏散引导和安全防护救
护,逐级上报灾情,启动应急救援预案。 3.所有成员负责安全防护及负责协助事故应急领导小组组长对事故救援方案实施。 4.部门安全员负责协助副组长实施营救及后勤物资供应。 5.如有副组长因事不在现场,临时由组长指定负责人。 6.根据分工进行抢险、自救和避灾。 应急处置 处置程序: 1.发生冶炼炉内气氛异常或电弧声音异常,应立即停电检查。 2.若发生水冷件漏水较大时,严禁倾动炉体,立即疏散人员。 3.平时加强巡检,发现炉壳发红时应及时停电处理,当发红位置在炉前或炉后位置时,炉体向反向位置倾动,使发红位置脱离钢液面。当发红位置在炉体两侧时,应及时向渣道内倾倒钢水,以防炉体漏钢烧坏设备而引起较大的事故。 4.发生爆炸造成火灾事故,但无人员伤亡的情况下,及时拨打119等待专业消防救援。
温度自动控制系统的设计毕业设计论文
北方民族大学学士学位论文论文题目:温度自动控制系统的设计 北方民族大学教务处制
毕业设计(论文)原创性声明和使用授权说明 原创性声明 本人郑重承诺:所呈交的毕业设计(论文),是我个人在指导教师的指导下进行的研究工作及取得的成果。尽我所知,除文中特别加以标注和致谢的地方外,不包含其他人或组织已经发表或公布过的研究成果,也不包含我为获得及其它教育机构的学位或学历而使用过的材料。对本研究提供过帮助和做出过贡献的个人或集体,均已在文中作了明确的说明并表示了谢意。 作者签名:日期: 指导教师签名:日期: 使用授权说明 本人完全了解大学关于收集、保存、使用毕业设计(论文)的规定,即:按照学校要求提交毕业设计(论文)的印刷本和电子版本;学校有权保存毕业设计(论文)的印刷本和电子版,并提供目录检索与阅览服务;学校可以采用影印、缩印、数字化或其它复制手段保存论文;在不以赢利为目的前提下,学校可以公布论文的部分或全部内容。 作者签名:日期:
学位论文原创性声明 本人郑重声明:所呈交的论文是本人在导师的指导下独立进行研究所取得的研究成果。除了文中特别加以标注引用的内容外,本论文不包含任何其他个人或集体已经发表或撰写的成果作品。对本文的研究做出重要贡献的个人和集体,均已在文中以明确方式标明。本人完全意识到本声明的法律后果由本人承担。 作者签名:日期:年月日 学位论文版权使用授权书 本学位论文作者完全了解学校有关保留、使用学位论文的规定,同意学校保留并向国家有关部门或机构送交论文的复印件和电子版,允许论文被查阅和借阅。本人授权大学可以将本学位论文的全部或部分内容编入有关数据库进行检索,可以采用影印、缩印或扫描等复制手段保存和汇编本学位论文。 涉密论文按学校规定处理。 作者签名:日期:年月日 导师签名:日期:年月日
江苏大学毕业设计及论文基本要求
本科毕业设计要求: 1、英文文献翻译,文献的原文由老师提供,要求对英文文献中的题目、摘要、正文、图表 名称进行原意翻译,文献中的作者、公式、图表以及参考文献不需要翻译。翻译时不可通过翻译工具进行全文翻译,仅能使用翻译工具进行初步翻译再针对原文意思进行修改,必须保证译文具有一定的可读性和准确性。建议:通读全文,了解一定意思之后再进行翻译,专业词汇无法准确翻译,推荐使用CNKI翻译助手,网址为https://www.360docs.net/doc/2b1087802.html,/。 2、综述或读书笔记:即经过广泛阅读毕业设计相关资料、书籍和文献之后,针对毕业设计 内容的背景、发展现状、主要技术及应用、理论基础等做相应总结,撰写出一份综述或读书笔记。必须在最后给出阅读的参考文献,同样,内容的编排需要具备一定的可读性和准确性。要求篇幅8-10页。 3、任务书:由老师下达,学生提交正确的专业、班级和姓名。 4、针对毕业设计题目,进行一定的仿真、硬件设计或实验验证,每一个毕业设计必须要有 相应的结果,或是仿真模型和仿真波形结果,或者硬件系统设计原理图PCB,或者最终的实验平台搭建和实验结果,或者完成相应的软件代码编写,根据各自的题目,在毕业完成最后必须具有一定的结果呈出。 5、所有的英文文献翻译、综述以及毕业论文的撰写必须规范严谨,请参考下页给出的示意 图,所有的图表名称应比正文小一个字体,如正文为小四字体,则图表的名称为五号字体,并且要求图中和表中的文字尽量不要超过图表名称的字体大小。另:所有论文编写请统一采用office word,不要采用WPS,排版会有很大问题,所有的公式请采用公式编辑器MathType6.0及以上的安装版,画图和制图均使用office visio07或以上版本,软件请大家到网上下载,或者问老师拷贝安装。 6、请大家学会搜索和下载参考文献,进入学校图书馆网址https://www.360docs.net/doc/2b1087802.html,,在“常用资 源里面”的“CNKI知识网络数字平台”和“万方知识服务平台”两个数据库里面,可按照各自毕业设计题目中的关键词搜索相关期刊论文和硕士博士论文,进行阅读参考。如有疑问和不懂的地方,及时与老师沟通。 7、毕业设计期间纪律:(1)每周进行一次汇报,汇报各自研究进展和取得的阶段性成果; (2)请大家养成自觉和好问的习惯,有不会的地方及时沟通联系老师;(3)若要出去短暂实习或找工作,必须明确告知老师并请假,汇报可采用邮件或者电话或者QQ的形式;(4)原则情况下不接受全学期在外实习,如果需要毕业设计期间去工厂实习,必须办理相关手续,并且毕业设计由工厂提供,老师只负责监督和把关,由此造成的不良后果,请自行负责;(5)若出现不遵守纪律者,毕业设计出现不及格一概与老师无关!8、毕业设计具体和时间节点: (1)英文文献翻译,第4周周三前; (2)中期检查审核,第9-10周; (3)论文初稿,第13-14周; (4)论文定稿,第14-15周; (5)答辩时间,6月5日~6月10日。
马钢4号3200m3高炉开炉的实践经验
马钢4号3200m3高炉开炉的实践经验 2017-07-06 (伏明蒋裕聂长果) ●马钢通过合理选取送风参数,动态调节料制,匹配好送风参数,控制首炉铁出铁时间,控制充足的炉缸温度等一系列操作技术,为开炉达产创造了条件;采取快速降硅、富氧喷煤等强化冶炼手段,实现了开炉后指标的快速提升。 马钢4号3200m3高炉于2015年3月开工建设,2016年7月建成,设计炉容为3200m3,设32个风口、4个铁口,设计上采用适当矮胖的操作炉型、砖壁合一薄内衬结构。高炉炉底炉缸采用了陶瓷杯﹢碳砖炉底和炉缸结构,关键部位采用进口超微孔碳砖。冷却设备采用全冷却壁冷却结构、联合软水密闭循环冷却系统,热风系统采用3座卡鲁金顶燃式热风炉,煤气系统采用重力﹢旋风﹢全干法布袋除尘结合TRT 余压发电系统,双矩形平坦式出铁场和底滤法渣处理系统等。 本文对马钢4号高炉安全顺利开炉达产的实践进行了总结。马钢通过合理选取送风参数,动态调节料制,匹配好送风参数,控制首炉铁出铁时间,控制充足的炉缸温度等一系列操作技术,为开炉达产创造了条件;采取快速降硅、富氧喷煤等强化冶炼手段,实现了开炉后指标的快速提升。 开炉前准备工作 4号高炉是马钢首座3000m3级高炉,面对新工艺、新流程和新设备,开炉前,马钢组织编制了各岗位教材和岗位操作规程,并模拟事故状态制订了多个应急预案,对各岗位人员开展大量的理论培训和模拟实
操演练。同时,马钢对设备进行充分的单试、联试。热风炉、高炉烘炉方案和开炉方案结合本高炉特点,吸取其他高炉经验,注重操作性。 热风炉烘炉。4号高炉配套3座卡鲁金顶燃式热风炉,燃料采用低热值的高炉煤气;热风炉采用助燃空气、煤气双预热系统,设计风温≥1250℃。为此,马钢在制订烘炉方案时,不仅考虑了硅砖低温相变引起的体积膨胀对热风炉砌体稳定性的影响,而且为避免3座热风炉在烘炉后期同时需要大量焦炉煤气的问题,热风炉采用每间隔2.5天点火1座热风炉的方式,依次点燃1号、2号、3号热风炉。热风炉采用焦炉煤气烘炉,开始烘炉时间为2016年5月10日,6月18日烘炉结束,单座热风炉烘炉时间为34.5天。 高炉烘炉。高炉烘炉的目的是在低温区烘干热风总管、送风围管水分,逐步加热本体炉墙,去除本体水分,防止耐材急剧膨胀、变形;高温区烘干炉缸耐材水分,固化不定形耐材。4号高炉烘炉于2016年6月28日进行,用时288h(含气密性耐压试验),包括初始升温、低温保温、再升温、高温保温、降温凉炉等5个阶段,降温凉炉期间进行高炉气密性耐压试验。 热风炉、高炉检漏耐压试验。热风炉、高炉检漏耐压试验的目的,是检验施工质量及设计能力是否满足高炉正常生产时高压的要求。马钢于2016年6月18日对高炉送风系统进行了检漏耐压试验,方案充分考虑到热风炉混风室硅砖结构特点及冷风管系耐温要求。由于风机原因,
直流电弧炉技术
直流电弧炉技术 德国MAN-GHH集团早在1984年,就开始Unarc型直流电弧炉的研究开发工作。但在其国内,由MAN-GHH集团提供的大型Unarc型直流电弧炉到目前为止仅有两台,它们分别是德国乔奇斯玛丽赫特钢厂的125t 电弧炉(1994年投产)和德国普瑞奥萨克钢公司佩尼钢厂的100t电弧炉(1995年投产),而且都是代替原有转炉的。 (1)MAN-GHH集团直流电弧炉的特点: MAN-GHH集团直流电弧炉的炉底电极特点是:根据炉子的不同容量,把100~250根触针埋入炉子中央部分的耐火材料里。在触针的下端进行强制空冷,以防耐火材料中的触针熔损。尽管耐火材料中与钢水接触部分的触针上部会熔化。由于触针反复熔化和凝固,不会有消耗。但是,耐火材料一旦减少,触针就会损耗。所以,在触针上装有热电偶,到设定温度就更换炉底电极。 (2)德国乔奇斯玛丽赫特钢厂125t直流电弧炉的设备与生产工艺 ①125t直流电弧炉的设备 该直流电弧炉的炉壳直径7300mm,变压器功率130MVA,底电极强 制空冷,顶电极直径700 mm;以天然气为燃料的5只烧嘴分别布置在 炉门口、EBT出钢口上部和炉壁三个区域,天然气消耗量为400m3/h,氧耗为800m3/h。底电极为触针型(原为190根,1996年10月已改为244 根)。触针直径45mm,触针长度1590mm,触针露出小炉底25~35mm。炉下底电极顶出装置为6只液压缸,顶距3m,电炉配备EBT出钢系统。炉盖为全水冷结构,中心部位的小炉盖内径800mm,外径1300mm。炉 盖向出钢口旋转,最大旋转角为85°。炉子通过液压向出钢侧和炉门侧倾动。出钢侧最大倾角为25°,向炉门侧最大倾角为15°。炉壳上部贴 有17块水冷块。700电极有喷淋装置。电炉水冷系统采用闭循环,循 环水量为1900m3/h,进口水温27℃,出口水温35~40℃。 ②125t直流电弧炉的冶炼工艺及其冶金效果 a.125t直流电弧炉的冶炼工艺 125t直流电弧炉的冶炼工艺主要围绕熔料、去磷和升温三大任务展开。 其冶炼工艺流程为:补炉→进料(第一料篮)→通电→氧气和天然气助燃→停电进料(第二料篮)→通电→氧气和天然气助燃→成分分析→测温→流渣→测温和成分分析→定氧→停电出钢(打开EBT出钢口)→塞EBT出钢口→补炉。 具体工艺操作要点为: 补炉:在中后期3~4炉补一次,补炉砂用量6kg/t;采用旋转补炉机喷补。另外,炉门口是补炉重点,基本上每炉都要补一次。 进第1次料:料重为总料重的60%~70%。料高用料篮压。同时,通过计算机画面作通电前的设备检查。
大型炼钢电弧炉对电网及自身的影响和抑制方案
大型炼钢电弧炉对电网及自身地影响和抑制方案.txt26选择自信,就是选择豁达坦然,就是选择在名利面前岿然不动,就是选择在势力面前昂首挺胸,撑开自信地帆破流向前,展示搏击地风采.大型炼钢电弧炉对电网及自身地影响和抑制方案 翁利民,陈允平,舒立平 (武汉大学电气项目学院,湖北省武汉市430072) 摘要:详细分析了现代大型炼钢电弧炉对电网不利影响地4个方面:即电压波动、电压畸变、负序电压与电流、功率因数低,并结合实际从量地概念上认识其对自身在增加损耗、继电保护误动、增加网损、降低生产效益等方面地影响;介绍了抑制电弧炉地常规有效措施,得出了合理地结论. 关键词:电压闪变;电压波动;SVC;滤波器 1 引言 现代大型超高功率炼钢电弧炉,因为其容量大,是用电大户,对电网地影响具有举足轻重地作用.它具有功率因数低,无功波动负荷大且急剧变动,产生有害地高次谐波电流,三相负荷严重不平衡产生负序电流等对电网不利地因素,使得电网电能质量恶化,危及发配电和大量用户,也影响电炉自身地产量、质量,使电耗、电极消耗增大,从而成为电网地主要公害之一.现在有关大型电炉对电网公害抑制地研究也正在深入开展,有必要对其不利影响和抑制对策作一概述性地分析. 2 现代大型电炉对电网地影响 2.1 引起电网电压急剧波动 大型电炉在打孔期和熔化期电弧长度急剧变化,引起无功负荷急剧波动,其工作短路功率为电炉变压器额定功率地两倍左右,其最大波动无功为电炉变压器额定功率地1.5倍左右(具体倍数取决于短网阻抗、电炉变压器阻抗、供电系统阻抗之和地大小,总阻抗大则工作短路倍数小,反之则大).无功地急剧波动,引起电网电压地急剧波动,其波动频率一般为1~15Hz,使灯光和电视机屏幕产生闪烁,使人视觉疲劳而感到烦躁,此外还影响到晶闸管设备和精密仪表等地稳定运行,甚至产生质量事故.国标GB12326-2000《电能质量电压允许波动和闪变》规定了电力系统公共供电点各级电压等级地电压波动和闪变允许值. 2.2 使电网电压波形产生畸变 电炉在熔化和打孔期,电弧电流是不规则地,且急剧变化,其电流波形不是正弦波,可分解为2次和2次以上地各次谐波电流,主要为2~7次,其中2次和3次最大,其平均值可达基波分量地5%~10%,最大可达15%~30%;4~7次平均值为2%~6%,最大值可达6%~15%.而电网中地铁磁元件也产生高次谐波,以3次和5次谐波电流较大,其中3次分量最大,而电炉刚好也是3次谐波电流很大,这对电网是极为不利地.谐波电流流入电网,使其电压波形发生畸变,引起电气设备发热、振动,增加损耗,干扰通信,使电力电缆局部放电绝缘损坏,电容器过载损坏等,国家标准GB/T14549-1993《电能质量公用电网谐波》规定了电压波形畸变率限值. 2.3 使电网电压产生负序分量 电炉在熔化期,特别是打孔期,各相电弧电压是独立变化地,三相电弧各自发生急剧无规则变化,故其三相电流是不对称地.在正常生产情况下,产生地负序电流约为电炉变压器额定电流地25%左右;在不正常情况下,如一相断弧时,可达56%左右,如两相短路地同时,第三相又断弧,此时可达86%左右.负序电流流入电网,使电网电压产生负序分量,影响发电机和用电设备使用效果,严重时可能造成损坏,还会使继电保护误动作,其严重程度一般用不平衡度(即负序电压与正序电压分量之比地百分数)表示,国标GB/T15543-1995《电能质量三相电压允许不平衡度》对于对称三相电网规定:负序电压不大于2%,短时不超过4%.一般来讲,在电网公共连接点上地短路容量为电炉变压器额定容量地30~40倍以上时,电网是允许地,否则应采取使三相达到平衡对称地补偿措施.
温度自动控制系统的设计毕业设计
论文题目:温度自动控制系统的设计
毕业设计(论文)原创性声明和使用授权说明 原创性声明 本人郑重承诺:所呈交的毕业设计(论文),是我个人在指导教师的指导下进行的研究工作及取得的成果。尽我所知,除文中特别加以标注和致谢的地方外,不包含其他人或组织已经发表或公布过的研究成果,也不包含我为获得及其它教育机构的学位或学历而使用过的材料。对本研究提供过帮助和做出过贡献的个人或集体,均已在文中作了明确的说明并表示了谢意。 作者签名:日期: 指导教师签名:日期: 使用授权说明 本人完全了解大学关于收集、保存、使用毕业设计(论文)的规定,即:按照学校要求提交毕业设计(论文)的印刷本和电子版本;学校有权保存毕业设计(论文)的印刷本和电子版,并提供目录检索与阅览服务;学校可以采用影印、缩印、数字化或其它复制手段保存论文;在不以赢利为目的前提下,学校可以公布论文的部分或全部内容。 作者签名:日期:
学位论文原创性声明 本人郑重声明:所呈交的论文是本人在导师的指导下独立进行研究所取得的研究成果。除了文中特别加以标注引用的内容外,本论文不包含任何其他个人或集体已经发表或撰写的成果作品。对本文的研究做出重要贡献的个人和集体,均已在文中以明确方式标明。本人完全意识到本声明的法律后果由本人承担。 作者签名:日期:年月日 学位论文版权使用授权书 本学位论文作者完全了解学校有关保留、使用学位论文的规定,同意学校保留并向国家有关部门或机构送交论文的复印件和电子版,允许论文被查阅和借阅。本人授权大学可以将本学位论文的全部或部分内容编入有关数据库进行检索,可以采用影印、缩印或扫描等复制手段保存和汇编本学位论文。 涉密论文按学校规定处理。 作者签名:日期:年月日 导师签名:日期:年月日
电弧炉熔炼工安全操作规程通用版
操作规程编号:YTO-FS-PD307 电弧炉熔炼工安全操作规程通用版 In Order T o Standardize The Management Of Daily Behavior, The Activities And T asks Are Controlled By The Determined Terms, So As T o Achieve The Effect Of Safe Production And Reduce Hidden Dangers. 标准/ 权威/ 规范/ 实用 Authoritative And Practical Standards
电弧炉熔炼工安全操作规程通用版 使用提示:本操作规程文件可用于工作中为规范日常行为与作业运行过程的管理,通过对确定的条款对活动和任务实施控制,使活动和任务在受控状态,从而达到安全生产和减少隐患的效果。文件下载后可定制修改,请根据实际需要进行调整和使用。 1.检查炉体、炉盖、冷却系统、炉体倾侧机构是否正常,电炉接地是否良好。 2.检查所用工具,确保其齐备、干燥和放置位置正确。 3.炉料应经过检查,其品种、规格、块度要符合规定。炉料中严禁混入密封盒子、箱子和管子之类物件及易爆品。 4.送电前,将电极升起并进行严格检查,防止短路。禁止带负荷送电。通电时先用10分钟低压,当电极埋入炉料时,才能将功率加到最大。 5.清除炉渣时,先要除去电极电压,用力不得过猛,以免钢水溅出。 6.熔炼过程中,需往炉内加粒粉状材料时,要站在炉门侧面加料,防止喷火伤人。不得添加湿料。 7.用氧气来烧穿电炉的金属出口时,应遵守如下规定: (1)氧气瓶应离明火10米远。如实际情况不允许时,应
本科毕业设计(论文)文献综述的写作指导及综述模板(格式)
本科毕业设计(论文)文献综述的写作指导 为了促使学生熟悉更多的专业文献资料,进一步强化学生搜集文献资料的能力,提高对文献资料的归纳、分析、综合运用能力及独立开展科研活动的能力,现对本科学生的毕业设计(论文)中文献综述的写作提出一些指导,供教员和学生参考。 一、文献综述的概念 文献综述是针对某一研究领域或专题搜集大量文献资料的基础上,就国内外在该领域或专题的主要研究成果、最新进展、研究动态、前沿问题等进行综合分析而写成的,能比较全面地反映相关领域或专题历史背景、前人工作、争论焦点、研究现状和发展前景等内容的综述性文章,是高度浓缩的文献产品。“综”是要求对文献资料进行综合分析、归纳整理,使材料更精练明确、更有逻辑层次;“述”就是要求对综合整理后的文献进行比较专门的、全面的、深入的、系统的评述。 文献综述根据其涉及的内容范围不同,综述可分为综合性综述和专题性综述两种类型。所谓综合性综述是以一个学科或专业为对象的,而专题性综述则是以一个论题为对象的。本科毕业设计(论文)文献综述主要为专题性综述。 二、撰写文献综述的基本要求 文献综述主要用以介绍与主题有关的详细资料、动态、进展、展望以及对以上方面的评述。除综述题目外,其内容一般包含前言、主题、总结、参考文献四个部分,撰写文献综述时可按这四部分拟写提纲,再根据提纲进行撰写工作。 前言部分,主要说明写作的目的,介绍有关的概念、定义以及综述的范围,扼要说明有关主题的现状或争论焦点,使读者对全文要叙述的问题有一个初步的轮廓。 主题部分,是综述的主体,其写法多样,没有固定的格式。可按年代顺序综述,也可按不同的问题进行综述,还可按不同的观点进行比较综述,不管用那一种格式综述,都要将所搜集到的文献资料进行归纳、整理和分析比较,阐明有关主题的历史背景、现状、发展方向以及对这些问题的评述。主题部分应特别注意代表性强、具有科学性和创造性文献的引用和评述。 总结部分,将全文主题进行扼要总结,提出自己的见解并对进一步的发展方向做出预测。
电弧炉炼钢讲义
1电弧炉炼钢概述 1.1电弧炉炼钢的发展概况:大致可分为三个阶段 (1)研究阶段(从1800年至1900年) 1800年,英国人戴维(Humphrey Davy)发明了碳电极;1849年,法国人德布莱兹(Deprez)研究用电极熔化金属;1866年,德国人冯·西门子(Werner Von Siemens)发明了电能发生器;1879年,德国人威廉姆斯·西门子(C Williams Siemens)采用水冷金属电极进行了实验室规模的炼钢试验,但电耗太高,无法投入大生产;1885年,瑞典ASEA(即瑞典通用电气)公司设计了一台直流电弧炉;1888年,法国人海劳尔特(Paul Heroult)用间接电阻加热炉进行熔炼金属实验;1889~1891年,同步发电机和变压器推广应用;1899年,海劳尔特研制成功交流电弧炉;1900年,海劳尔特开始用交流电弧炉冶炼铁合金; (2)初级阶段(从1900年至1960年) 1905年,德国人林登堡(R.Lindenberg)建成第一台炼钢用二相交流电弧炉(海劳尔特式),该炉特点是采用方形电极,电极手动升降,炉盖固定不可移动,加料从炉门口人工加入;1906年,林登堡成功地炼出了第一炉钢水,浇注成钢锭,从此开创了电弧炉炼钢的新纪元;1909~1910年,德国和美国分别制成了6t和5t的三相交流电弧炉投产;1920年,采用了电极自动升降调节器,提高了电极升降速度;1926年,德国德马克公司将炉盖改为移出式,首次实现了顶装料;1930年,出现了炉体开出式电弧炉;1936年,德国人制造了18t炉盖旋转式电弧炉;1939年,瑞典人特勒福斯提出了电弧炉电磁搅拌的思想;1960年,为使三相电抗平衡,美国出现了短网等边三角形布置;此阶段由于电力、电极、用氧水平、炉容量等的限制,故炼钢成本大大高于平炉,因而只适合于冶炼合金钢、特殊钢。随着第二次世界大战的爆发,电炉钢的产量迅速增长。 (3)大发展阶段(从1960年至今) 由于钢铁工业内部结构在50年代中期发生了重大变化,及LD转炉取代了OH平炉的炼钢龙头地位,但是LD炉不能象平炉那样100%地采用废钢为原料,故伴随着平炉的逐步退出炼钢舞台,废钢过剩的问题就日益突出,因此就要求EAF电炉在冶炼合金钢的同时,还要担负起一部分冶炼普通钢种的任务。这样就对EAF提出了如何大幅度提高生产率和降低生产成本的发展方向。1964年,美国碳化物公司的施瓦伯(W.E.Schwabe)和西北钢线材公司的罗宾逊(C.G.Robinson)共同提出了电弧炉超高功率的概念,并在两台135t的电弧炉上采用不同功率水平进行试验;不久就在世界各国推广UHP操作,使冶炼时间大大缩短,从3~4小时减少到2小时(功率水平500kVA/t)。从七十年代开始,为了最大限度地利用变压器的工作效率,围绕着如何进一步提高功率利用率和时间利用率,各国相继发展了一系列的相关技术,例如:炉壁、炉盖水冷化、长弧泡沫渣操作、氧燃烧嘴、偏心炉底出钢、废钢预热、炉底吹气、双炉壳电弧炉等等。因此,变压器的功率水平达到800~1100kVA/t,冶炼时间进一步降低至1小时以下,电耗降至400kWh/t以下。并逐步在特殊钢厂推广运行“废钢预热—电弧炉—炉外精炼—连铸—热送轧制或连轧”的工艺模式,把电弧炉演变成了单纯的废钢快速熔化设备。为了根本上克服交流超高功率电弧炉的电弧不稳定、三相功率不平衡带来的炉壁热点问题,对前级电网造成的剧烈冲击(闪烁问题),70年代开始了直流电弧炉的研究,并于80年代中期投入工业生产,从此电弧炉又在交流和直流两方面同时发展。 综上所述,在电弧炉炼钢诞生起至今的约100多年的时间里,从开始时的小型电弧炉专门冶炼合金钢种,到后来变化为大型电弧炉兼炼合金钢和普碳钢,直至近来的超高功率大型(交、直流)电弧炉仅仅作为废钢熔化设备。 1.2 电弧炉炼钢的特点 优点:靠电弧加热,热效率高,能调节炉内气氛,与平炉、转炉相比,基建投资少,占地面积小 缺点:电弧是点热源,电力、电极、耐材消耗高,生产率较低,成本比转炉高 1.3 传统碱性电弧炉炼钢方法及工艺流程介绍 1.3.1 常用冶炼方法:一般可分为氧化法、不氧化法和返回吹氧法三种。 氧化法:在炉料熔清后,通过向钢液中加矿或吹氧进行脱P、脱C操作,并造成熔池沸腾,去除钢中[H]、[N]气体及非金属夹杂物,再经过还原期脱O、脱S、调整钢液化学成分及温度后出钢。此法的特点在于可使钢中[P]、[S]、[H]、[N]、[O]等都可降低至规格范围内,达到纯洁钢液的目的,因此大多数钢种均采用此法冶炼。而此法不足之处在于钢中若含有大量合金元素时,则会造成其氧化损失,并对操作带来不良影响,故一般配料时多用碳素废钢,这又造成后期合金化的困难。 不氧化法:冶炼过程中没有氧化期,能充分回收原料中的合金元素。炉料熔清后,经还原调整成分及温度后即可出钢。优点是可在炉料中配入大量合金钢切头、切尾、废钢锭、注余、汤道、切屑等,减少铁合金的消耗量,降低钢的成本。缺点是冶炼过程中不能去P、去气去夹杂,因此要求配入清洁无锈、无油污的低P且C含量合适的钢铁料,并在冶炼中防止钢液吸气过多。 返回吹氧法:在炉料中配入大量的合金钢返回料,根据C和O的亲和力在一定温度下大于某些合金元素与O的亲和力的理论,当钢液温度升高至一定温度后,向钢液中吹氧,达到在脱C以便去气去夹杂的同时,又能够避免钢中合金元素氧化损失的目的。这样做,既降低了成本,又提高了质量。 1.3.2 碱性电弧炉氧化法冶炼工艺流程介绍 上炉出钢→补炉(fettling)→装料(charging)→熔化期(melting)→氧化期(oxidizing)→还原期(reducing)→出钢(tapping) 补炉:上炉出钢毕,迅速将炉体损坏部位进行修补,以保证下一炉钢的冶炼。新炉子在炉役期的前几炉可不补炉。装料:将配好的炉料(burden)按一定规律装入料罐(bucket)中,然后将料罐吊至炉前,打开炉盖,将炉料一次卸入炉内。一炉钢可视情况一次装料或多次装料。熔化期:从通电至炉料完全熔清称为熔化期。其主要任务是迅速熔化全部炉料,并及早形成一定的炉渣,起到稳定电弧、防止金属挥发与吸气,提早脱P等作用。氧化期:待炉料全部熔清后,取样分析,进入氧化期。其主要任务是最大限度地脱P (dephosphorization)、去除钢中气体([H]、[N])和非金属夹杂物(non-metallic inclusions),并升温至稍高于出钢温度。还原期:氧化期任务完成后,停电扒除氧化渣,重新造新渣,进入还原期。其主要任务是脱O(deoxidization)、脱S(desulphurization),调整钢液的成分和温度。出钢:当钢液成分和温度均符合出钢要求,则打开出钢口,摇炉出钢。出钢时要做到钢渣混冲,利用钢渣在钢包(ladle)中激烈运动,最大限度地脱S,并防止二次氧化、二次吸气。 2、电弧炉的电气设备 2.1 电弧的概念与交流电弧的特性 2.1.1 电弧:电弧是电流通过两极间气体时使之电离的一种放电现象。 阴极放电:热电子发射,强电场发射。电子自阴极发射后,以极高速度向阳极冲击,在运动中与极间气体碰撞,使其电离成正、负离子,形成电弧。电弧中的电子数目或者电弧电流大小与两极间电功率、阴极材质、气体种类等都有关系。 2.1.2 交流电弧的特性