轴类零件的数控编程与加工工艺.doc
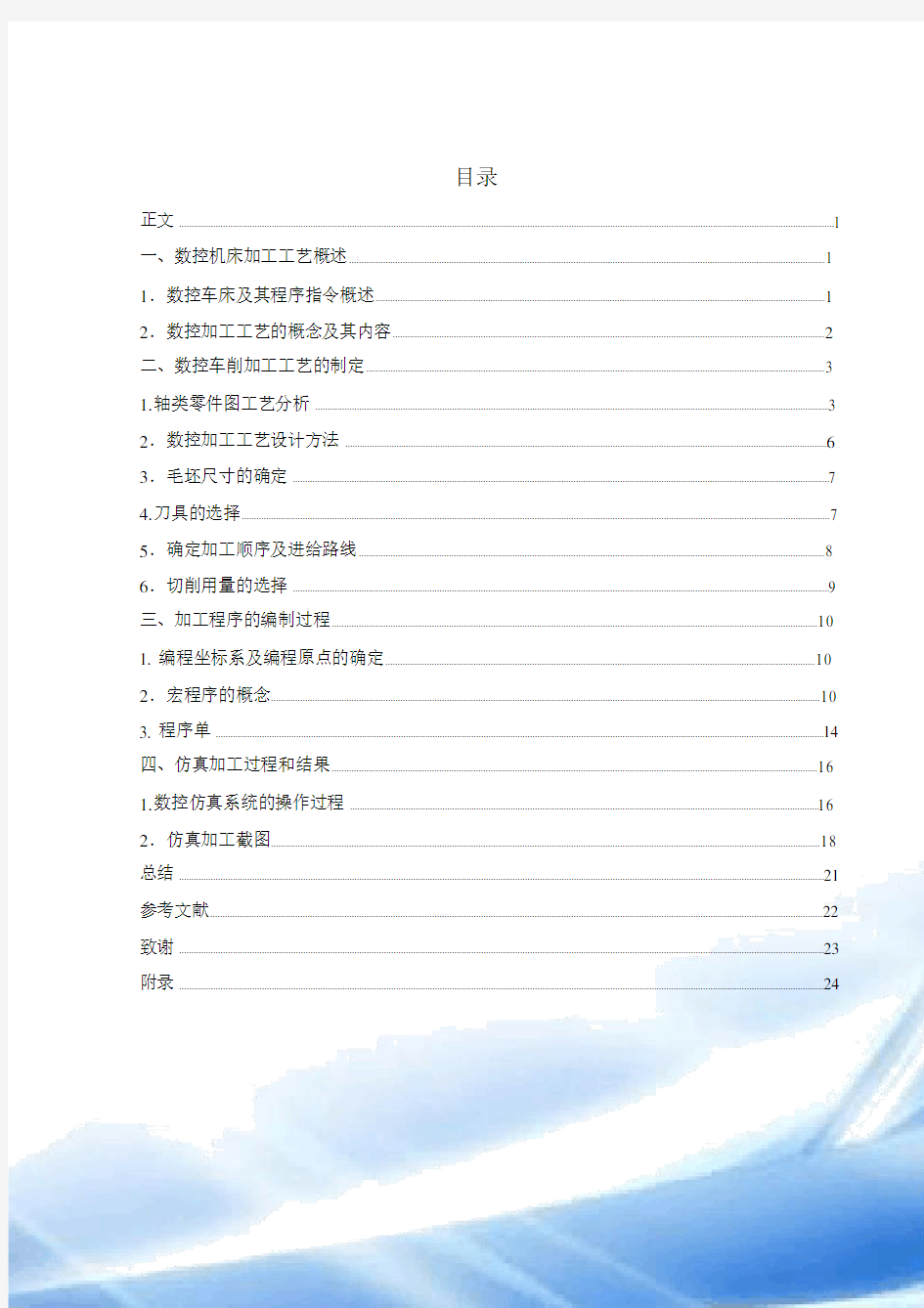

目录
正文 (1)
一、数控机床加工工艺概述 (1)
1.数控车床及其程序指令概述 (1)
2.数控加工工艺的概念及其内容 (2)
二、数控车削加工工艺的制定 (3)
1.轴类零件图工艺分析 (3)
2.数控加工工艺设计方法 (6)
3.毛坯尺寸的确定 (7)
4.刀具的选择 (7)
5.确定加工顺序及进给路线 (8)
6.切削用量的选择 (9)
三、加工程序的编制过程 (10)
1. 编程坐标系及编程原点的确定 (10)
2.宏程序的概念 (10)
3. 程序单 (14)
四、仿真加工过程和结果 (16)
1.数控仿真系统的操作过程 (16)
2.仿真加工截图 (18)
总结 (21)
参考文献 (22)
致谢 (23)
附录 (24)
正文
一、数控机床加工工艺概述
1.数控车床及其程序指令概述
1.1 数控车床的发展
数控技术,简称“数控”。英文: Numerical Control(NC)。是指用数字、文字
和符号组成的数字指令来实现一台或多台机械设备动作控制的技术。它所控制的通常
是位置、角度、速度等机械量和和机械能量流向有关的开关量。数控的产生依赖
于数据载体和二进制形式数据运算的出现。1908 年,穿孔的金属薄片互换式数据载
体问世; 19 世纪末,以纸为数据载体并具有辅助功能的控制系统被发明;1938 年,
香农在美国麻省理工学院进行了数据快速运算和传输,奠定了现代计算机,包括计
算机数字控制系统的基础。数控技术是和机床控制密切结合发展起来的。1952 年,
第一台数控机床问世,成为世界机械工业史上一件划时代的事件,推动了自动化的
发展。
现在,数控技术也叫计算机数控技术,目前它是采用计算机实现数字程序控制
的技术。这种技术用计算机按事先存贮的控制程序来执行对设备的控制功能。由于
采用计算机替代原先用硬件逻辑电路组成的数控装置,使输入数据的存贮、处理、
运算、逻辑判断等各种控制机能的实现,均可通过计算机软件来完成。
车削加工就是在车床上,利用工件的旋转运动和刀具的直线运动或曲线运动来
改变毛坯的形状和尺寸,把它加工成符合图纸的要求
机床是人类进行生产劳动的重要工具,也是社会生产力发展水平的重要标志。数控
机床是一种通过数字信息,控制机床按给定的运动轨迹,进行自动加工的机电一体化的加工装备,经过半个世纪的发展,数控机床已是现代制造业的重要标
志之一,在我国制造业中,数控机床的使用也越来越广泛,是一个企业综合实力的
体现。
数控车床是数字程序控制车床的简称,它集通用性好的万能型车床、加工精度
高的精密型车床和加工效率高的专用型车床的特点于一身,是国内使用量最大,覆
盖面最广的一种数控机床。
1.2 数控编程常用程序指令
G代码 ( 准备功能 )
数控车床FANUC
工件坐标系设定G50
最快速移动 G00 G00
数控车床 FANUC
直线插补 G01 G01
圆弧插补 G02/G03 G02/G03
外圆车销固定循环G71
端面车销固定循环G90
数控车床 FANUC
横轴Z
众轴X
主轴正转 M03
主轴反转 M04
主轴停止 M05
冷却液开 M07 M08
冷却液关 M09
M98调用子程序
M99子程序结束
数控车床 FANUC
切刀切槽G75
进给量R
切削速度 F
2.数控加工工艺的概念及其内容
数控加工工艺是采用数控机床加工零件时所运用各种方法和技术手段的总和,使用于整个数控加工工艺过程。数控加工工艺是伴随着数控机床的产生、发展而逐步完善起来的一种使用技术,它是人们大量数控加工实践的经验总结。
其内容为:分析形位公差,确定设计基准,并考虑如何设定定位基准、分析
产品尺寸公差,考虑利用何种设备才能达到公差要求、根据产品形状,材料等条件,考虑产品刀具的选择使用、考虑产品的特殊要求,例如是否需要挤压,热处理或者表面处理等、根据那个书上说的什么先粗后精,先内后外??等原则安排工艺。总之一句话以最少的成本,最高的效率,加工出符合图纸要求的合格产品就是工艺。
在数控加工中,从零件的设计图纸到零件成品合格交付,不仅要考虑到数控程序的编制,还要考虑到诸如零件加工工艺路线的安排、加工机床的选择、切削刀具的选择、零件加工中的定位装夹等一系列因素的影响,在开始编程前,必须要对零件设计图纸和技术要求进行详细的数控加工工艺分析,以最终确定哪些是零件的技术关键,哪些是数控加工的难点,以及数控程序编制的难易程度。
二、数控车削加工工艺的制定
1.轴类零件图工艺分析
在图样分析中,应正确的分析零件图,在确定加工的部位和加工顺序后,再根据零件图的技术要求,分析零件的形状、基准面、粗糙度等级等。来确定走刀路线和
刀具选择。如图 1 轴类件
图 1 零件图
该零件是材料为铝合金且一端带有抛物线的轴类零件。本零件上由圆柱面、内
圆锥面、顺圆弧面、逆圆弧面、抛物线等部分组成。零件车削加工成形轮廓的结构
形状较复杂、需两头加工,零件的加工精度和表面质量要求都很高。
该零件重要的径向加工部位有Φ39mm圆柱段(表面粗糙度Rɑ=1.6 μm)、Φ25.287mm圆柱段(表面粗糙度Rɑ=1.6 μm)、Φ 50mm圆柱面和Φ 32mm圆柱面连接区、
R12mm和 R5mm圆弧过渡区(表面粗糙度Rɑ=1.6 μm)、抛物线 X=Z2/ (-32) 段(表面粗糙度 Rɑ=1.6 μm)。零件符合数控加工尺寸标注要求,轮廓描述清楚完整。
1.1加工前的零件预加工
零件毛胚在热处理前先行粗车加工,为数控车削加工工序提供可靠的工艺基准:
用车床三爪卡盘装夹零件,零件的内孔、外圆以及所在端面均留2mm-3mm余量;经
调质处理后进行的半精车加工工序中,零件的各外圆及零件端面的曲线轨迹均留
0.5mm余量;
数控编程任务书见表 1
表 1 数控编程任务书
产品零件图号任务书编号
10 数控数控编程
零件名称轴
任务书
共 1 页第 1 页使用数控设备数控车床
主要工艺说明及技术要求
1.数控车削加工零件的尺寸精度和表面质量均需达到图纸要求。
2.此零件在工艺方面还有以下要求:
(1)毛坯尺寸 :Φ 52×132mm;
(2)未注倒角: C2;
(3)未注公差的尺寸,允许误差±0.03 ;
(4)未注形位公差按8 级。
编程时间2012 年 12 月 1 日经手人编审编审批梁绍帅李莉芳梁绍帅李莉芳制核程核准
1.2 轴类零件数控加工工艺内容的选择
( 1)通用机床无法加工的内容应作为优先选择内容;
(2)通用机床难加工,质量也难以保证的内容应作为重点选择内容;
(3)通用机床加工效率低、工人手工操作劳动强度大的内容,可在数控机床尚存在富裕加工能力时选择。
1.3 数控加工工序的划分
(1)以一次安装、加工作为一道工序。
(2)以同一把刀具加工的内容划分工序。
(3)以加工部位划分工序。
(4)以粗、精加工划分工序。
1.4 顺序安排原则
(1)上道工序的加工不能影响下道工序的定位和夹紧,中间穿插有通用机床加工工序的也应综合考虑;
(2)先进行内腔加工,后进行外形加工;
(3)以相同定位、夹紧方式加工或用同一把刀具加工的工序,最好连续加工,以减少重复定位次数、换刀次数和挪动压板次数。
1.5 确定装夹方案
(1 )定位安装的基本原则
1)尽量减少装夹次数,尽可能在一次定位装夹后加工出全部待加工面。
2)力求设计基准、工艺基准和编程计算基准统一。
3)避免采用占机人工调整加工方案,以便能充分发挥出数控机床的效能。
(2 )选择夹具
保证夹具的坐标方向和机床的坐标方向相对固定不变;要协调零件和机床坐标系的尺寸关系。
零件采用机床携带标准的三爪卡盘,找正并夹紧,需进行两次装夹。第一次装
夹夹住的部分为毛坯的外表面,加工右端外轮廓,第二次装夹夹住已经加工过的右
端外圆柱面,然后再夹住右端Φ31mm处加工左端。夹紧时一定要注意夹紧力的大小要适当,在夹紧时要防止工件变形。
确定坯件轴线和左端面为定位基准。左端和右端均采用三爪自定心卡盘定心夹
紧并找正。
2.数控加工工艺设计方法
数控加工工序设计的主要任务是进一步把本工序的加工内容、切削用量、工艺
装备、定位夹紧方式及刀具运动轨迹确定下来,为编制加工程序作好准备。
2.1 确定走刀路线和安排加工顺序
走刀路线就是刀具在整个加工工序中的运动轨迹,它不但包括了工步的内容,
也反映出工步顺序。走刀路线是编写程序的依据之一。确定走刀路线时应注意以下
几点:
(1)寻求最短加工路线
(2)最终轮廓一次走刀完成
(3)选择切入切出方向
(4)选择使工件在加工后变形小的路线
2.2 确定定位和夹紧方案
在确定定位和夹紧方案时应注意以下几个问题:
(1)尽可能做到设计基准、工艺基准和编程计算基准的统一;
(2)尽量将工序集中,减少装夹次数,尽可能在一次装夹后能加工出全部待
加工表面;
(3)避免采用占机人工调整时间长的装夹方案;
(4)夹紧力的作用点应落在工件刚性较好的部位。
2.3 确定刀具和工件的相对位置
对刀点是指通过对刀确定刀具和工件相对位置的基准点。,对刀点往往就选择在零件的加工原点。对刀点的选择原则如下:
(1)所选的对刀点应使程序编制简单;
(2)对刀点应选择在容易找正、便于确定零件加工原点的位置;
(3)对刀点应选在加工时检验方便、可靠的位置;
(4)对刀点的选择应有利于提高加工精度。
换刀点是为加工中心、数控车床等采用多刀进行加工的机床而设置的,因为这些机床在加工过程中要自动换刀。对于手动换刀的数控铣床,也应确定相应的换刀位置。为防止换刀时碰伤零件、刀具或夹具,换刀点常常设置在被加工零件的轮廓之外,并留有一定的安全量。
2.4 确定切削用量
编程人员在确定切削用量时,要根据被加工工件材料、硬度、切削状态、背吃刀量、进给量,刀具耐用度,最后选择合适的切削速度。
3.毛坯尺寸的确定
毛坯制造尺寸和零件尺寸的差值称为毛坯加工余量。由于现有毛坯制造工艺技术的限制,加之产品零件的精度和表面的要求有越来越高,所以毛坯上某些表面仍需留有一定的加工余量,以便通过机械加工使毛坯得到最大的利用率来达到零件的质量要求。
根据要求和零件尺寸分析本零件应该选择选择Φ52x130mm的铝合金材料。
4.刀具的选择
刀具的选择是数控加工工艺设计中的重要内容之一。刀具选择合理和否不仅影
响机床的加工效率,而且还直接影响到加工质量。因此,掌握刀具的种类及用途在
数控车削加工中至关重要。
经过分析该轴类零件比较简单,只需加工外轮廓,因此选择两把外圆刀即可所
以完成所有加工粗车和精车选用两把35°硬质合金刀,为防止副后刀面和工件轮廓干涉,副偏角不宜太小,选Kr′=35。
刀具明细表如下表2:
表 2 刀具明细表
零件名数控加
程序编使用设
零件图号材料工刀具车间
称号备
明细表
PT 轴类图铝合金O0001 机 3 数控车
床
刀具号刀位号刀具名
规格
刀补地换刀方加工部称址式位
T01 1 外圆车35°左
01 自动
外圆轮刀偏刀片廓
T02 2 外圆车35 °右
02 自动
外圆轮刀偏刀片廓
5.确定加工顺序及进给路线
加工顺序按由粗到精、由近及远(从左到右)的原则确定。即先从右到左进行粗车(留 0.2mm的精加工余量),然后从右到左进行精加工,之后,再掉头装夹,同
左端相似,先从右到左进行粗车(留 0.2mm的精加工余量),再从右到左进行精加工。
加工工序表如下表 3
:
表 3 数控加工工序卡
机械产品名称或代号零件名称零件图号
厂数控加工工序卡
轴的加工轴
工艺程序编夹具名
序
夹具编号使用设备加工车间号称
号
O0001 三爪卡
数控车床机 3 盘
工步
工步内容刀具号刀具规格
主轴转进给速背吃刀号速度 mm/r 量 mm
1 车右端端面T0101 93°外圆车刀r/min
0.2 2 500
2 粗车右端外轮廓T0101 93°外圆车刀500 0.2 2
3 精车右端外轮廓T0101 93°外圆车刀1000 0.1
4 车右端抛物线T0101 93°外圆车刀500 0.1 0.5
5 车右端 R5 圆弧T0202 93°外圆车刀500 0.2 2
6 粗车左端外轮廓T0101 93°外圆车刀500 0.2 2
7 精车左端外轮廓T0101 93°外圆车刀1000 0.1
编制梁绍帅审核批准第 1 页共 1 页6.切削用量的选择
一般应遵循下述原则:
1)粗车时,切削深度和进给量均较大,故选择较低的切削速度;精车时,则选择较高的切削速度。
2)工件材料的加工性较差时,应选较低的切削速度。故加工灰铸铁的切削速度应较加工中碳钢低,而加工铝合金和铜合金的切削速度则较加工钢高得多。
3)刀具材料的切削性能越好时,切削速度也可选得越高。因此,硬质合金刀具的切削速度可选得比高速钢高度好几倍,而涂层硬质合金、陶瓷、金刚石个立方氧化硼刀具的切削速度又可选得比硬质合金刀具高许多。
此外,在确定精加工、半精加工的切削速度时,应注意避开积屑瘤和鳞刺产生的区域;在易发生振动的情况下,切削速度应避开自激震动的临界速度,在加工带硬皮的铸锻件时,加工大件、细长件和薄壁件时,以及断续切削时,应选用较低的切削速度。
根据对此轴类零件图的分析得出
背吃刀量:粗车时ap=0.2mm;精车时 ap=0.1mm
车外轮廓时主轴转速Vc=500r/min ,精车时的切削速度Vc=1000r/min 。
进给速度:粗车外圆时,f=0.2mm/r ,精车外圆时, f=0.1 mm/r 。
三、加工程序的编制过程
1.编程坐标系及编程原点的确定
工件坐标系是编程人员在编程时使用的,编程人员选择工件上的某一已知点为原点(也称程序原点),建立一个新的坐标系,称为工件坐标系。工件坐标系一旦建立便一直有效,直到被新的工件坐标系所取代。
工件坐标系的原点选择要尽量满足编程简单,尺寸换算少,引起的加工误差小等条件。一般情况下,程序原点应选在尺寸标注的基准或定位基准上。对车床编程而言,工件坐标系原点一般选在,工件轴线和工件的前端面、后端面、卡爪前端面的交点
上。对刀点是零件程序加工的起始点,对刀的目的是确定程序原点在机床坐标系中的位置,对刀点可和程序原点重合,也可在任何便于对刀之处,但该点和程序原点之间必须有确定的坐标联系。可以通过 CNC 将相对于程序原点的任意点的坐标转换为相对于机床零点的坐标。
程序在编写过程中需要进行坐标点的计算,需要认真仔细。样图中没有的坐标
需要通过 Auto CAD 捕捉出来。总之在编程的过程中需要静下心来认真对待,因为
这是加工零件相对比较重要的方面。
2.宏程序的概念
在编程工作中,我们经常把能够完成某一功能的一系列指令像子程序那样存入
存储器,用一个总指令来代表他们,使用时只需要给出这个总指令就能执行其功能
所存入的依稀凌志玲称作用户宏程序本体,简称宏程序。这个总指令称作用户宏程
序调用指令。在编辑时,编程员只要记住宏程序指令而不必记住宏程序。
宏程序本体既可以有机床生产厂提供,也可以由机床用户自己编制。使用时,
先将用户宏主体像子程序一样存入到内存里,然后用子程序调用指令调用。
(1)变量的表示和使用
1)变量表示
#I(I=1,2,3, ?) 或#[< 式子 >]
例: #5, #109, #501,#[#1+#2 -12]
2)变量的使用①变量号
可用变量代替
例: #[#30] ,设 #30=3则为#3
②变量不能使用地址O,N,I
例:下述方法下允许O#1;I#2 6.00 ×100.0;N#3Z200.0 ;
③变量号所对应的变量,对每个地址来说,都有具体数值范围
例: #30=1100时,则 M#30是不允许的
④ #0为空变量,没有定义变量值的变量也是空变量
( 2) 控制指令
控制指令起到控制程序流向的作用。
控制指令分为无条件转移指令、条件转移指令和循环指令三种。
1)无条件转移指令
GOTO n
该指令为无条件转移指令。当执行该程序段时,将无条件转移到n 程序段执行。
例: GOTO N1000
当执行该程序段时,将无条件转移到N1000程序段执行。
2)条件转移指令
○1 IF[ 条件表达式 ] GOTO n
如果指定的条件表达式成立,则转移到顺序号为N 的程序段;否则,执行下一个程序段。
例: IF[#1 GT 10] GOTO N20; 其变量 #1 的值大于 10 条件成立,则执行N20程序段;否则按顺序执行。
○2 IF[ 条件表达式 ] THEN<表达式 >;
如果条件表达是成立,执行预先定义的宏程序语句,且只执行一个宏程序语句。
例: IF[#1EQ#2] THEN #3=0, 如果 #1 和#2 的值相等, 0 赋值给 #3。
说明 :
a、条件表达式必须包括运算符。运算符插在两个变量之间或常数和变量之间,
并且用 [ ]括起来。表达式可以替代变量。
b、运算符有两个英文字母构成,用来判断大、小或相等。字母表示见运算符号对照表 3.1 。
表 4 运算符号对照表
运算符含义运算符含义
LE小于或等于(≦)GE大于或等于(≧)
NE不等于(≠)LT小于(﹤)
GT大于(﹥)EQ等于(﹦)
2.1 宏程序格式
粗加工
O001
T0101M04S500
G00X__Z__
#1=_x_设 #1为 X,值设为第一刀,刀具到达曲线坐标系中的 X 值#2=_z_设 #2为Z,值设为第一刀,刀具到达曲线坐标系中的 Z 值WHILE[#2LE0]DO1当 Z 小于等于零时 do1如果满足则进行 do1至 end1间程序,
如果不满足则跳到end1之后
GOOX[2*#1]
Z[#2-?]刀具第一刀所达到工件坐标系中的z 值
G00U1
G00Z2
#2=#2+2
#1=__表达式
End1
精加工
G00X0
Z0
#1=0
#2=0
WHILE[#2GE-?]DO1
GO1X[2*#1]
Z[#2-?]
GOOU1
GOOZ2
#2=#2-0.1
#1=__表达式
END1
3.程序单
O0001程序开始T0101M04S500
G0X120Z30
X52Z2
G73U25W0R13仿形循环粗加工右端外轮廓G73P1Q2U0.2W0F0.2
N1G42G0X0
G1Z0
X6Z0
X10Z-2
X10Z-15
X14Z-15
X14Z-18
G02X20Z-21R3
G1X20Z-26
X31Z-26
X31Z-54
X22.34Z-61.5
G3X25.287Z-67.5R12
G1X25.287Z-74
X32
Z-77
N2X50Z-95
M05
T0101M04S1000
G0X52Z2
G70P1Q2精加工
G0G40x31
z-26
#1=-4.5
#2=12
WHILE[#2GE0]DO1
G1X[2*[#1+15.5]]Z[#2-38]
#2=#2-0.5
#1=-#2*#2/32
END1
G0X100
Z50
T0202
G0G41X50Z-61.5
G1X22.34
Z-61.5
G03X31Z-54R5
G0G40X100
Z50
M00 程序暂停并掉头加工T0101
G0X52Z2
G71U2R2
G71P3Q4U0.2W0F0.2 循环粗加工
N3G42G0X0
G1Z0
X35Z0
X39Z-2
X39Z-29
G2X45Z-32R3
N4G1X50
G70P3Q4 精加工
G0G40X100
Z50
M05
M30程序结束
四、仿真加工过程和结果
1.数控仿真系统的操作过程
1.1 启动及其回参考点的过程
在刚刚进入 FANUC 0i系统,机床处于锁定状态,需要启动系统,具体操作步骤
如下:按下“启动”按钮,检查车床电机和私服系统的指示灯是否变亮。按下“急
停”按钮,将其松开。
若要关闭系统则按下“停止”按钮。
在进行其他操作之前,需要将车床回参考点,具体操作步骤如下:
(1)检查操作面板上的回原点指示灯是否亮,若已亮,说明已经进入回
原点操作。若不亮,需要按下回原点,转入回原点操作模式。
(2)在回原点模式下,依次按下操作面板上的x 轴选择按钮,和正向移
动按钮,此时 x 轴将回原点。
(3)在回原点模式下,依次按下操作面板上的z 轴选择按钮,和正向移
动按钮,此时 z 轴将回原点
1.2 数控车床仿真系统的对刀过程
数控程序一般按工件坐标系编程,对刀的过程就是建立工件坐标系和机床坐标
系之间关系的过程。在对刀操作中,将工件右端面中心点设为工件坐标系原点,将
工件上其他点设为工件坐标系原点的方法和对刀方法相似。
按“ MDI”键—— PROGRAM——键入 T0101——按“ EOB”键——按“ INSERT”键——按“循环启动”键,调出T01 外圆车刀。
通过手动操作将机床移到刀具和工件非常接近的位置,具体操作如下:
①按下操作面板上的手动按钮,机床进入手动操作模式,按下控制面板上的X 按钮,按下方向按钮,使机床再x 轴方向移动,同理使机床在z 轴方向移动。通过试图的旋转和放大等操作来观测机床的运行情况,多次进行上述的手动操作。
②按下操作面板上的主轴转动按钮,使主轴转动。
③再按下 z 轴方向选择按钮,按下方向按钮,使机床再z 轴方向移动,用所选
刀具来试切工件外圆。
④按下方向 +按钮,保持 x 向坐标不变,沿着z 向退刀。
接下来是测量试切直径,按下操作面板上的主轴转动按钮,使主轴停转;点击
菜单上的测量键,弹出测量对话框,点击试切外圆时所切线段,记下对话框下半部
中对应的 x 的值。
设置 x 向坐标:按“编辑”键然后按“ OFFSETSETING”键点击软键“形状”在
番号 01 区域输入“ X()”点击软键“测量”完成 X 轴的对刀。
设置 z 向坐标:点击工具栏“测量”得Z()将“ Z()+2=Z-k”在01区域输入 Z-k 点击软键“测量”完成Z 轴的对刀。
1.3 程序的导入及其加工
程序的导入:
按“编辑”模式,按下PROGRAM,点击软键“操作点击软键向右的黑色箭头点击
工具栏“ DNC传送”选择保存的程序并在操控面板上输入O0001,点击软键“READ”,点击软键“ EXEC”程序被导入 NC系统。
自动加工:
当NC程序经过检查无误后,就可以进行自动加工了。首先检查机床是否回
零,若没有,先将机床回零。其次,检查程序光标是否在程序头,若不是,先将光标
跳转到程序头。然后按下操作面板上的“自动运行”按钮,让机床进入自动运行模
式。最后按下操作面板上的“循环启动”按钮,程序开始执行。程序执行完毕,程序
返回程序头,准备下一次执行。
2.仿真加工截图
粗车右端外轮廓
右偏刀加工圆弧精车右端外轮廓
车削左端外轮廓成果测量图