烧结气氛论文:烧结工艺对铜基粉末冶金摩擦材料性能的影响

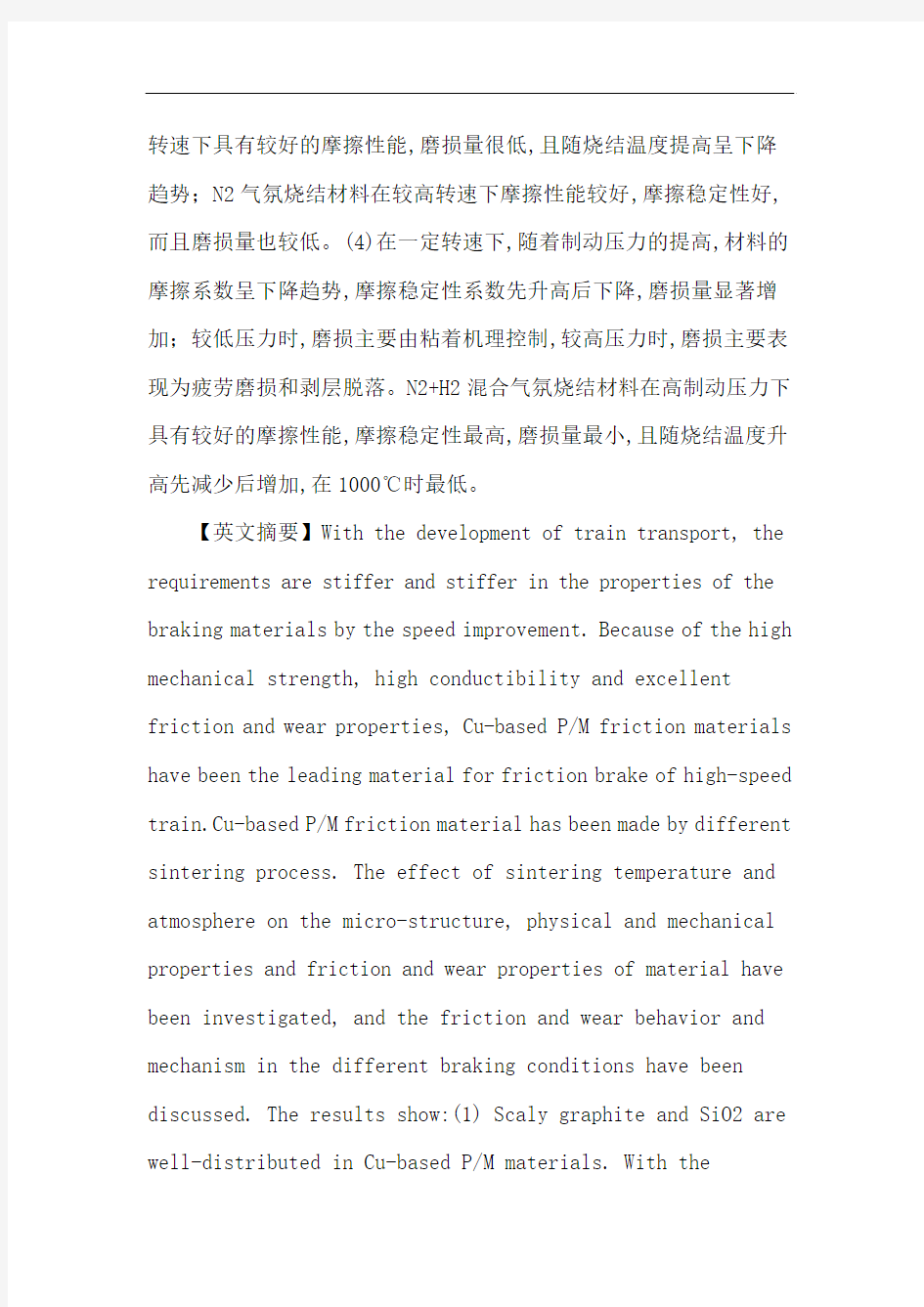
烧结气氛论文:烧结工艺对铜基粉末冶金摩擦材料性能的影响
【中文摘要】随着我国铁路运输业的飞速发展,列车运行速度一提再提,这就对制动摩擦材料提出了更为苛刻的要求。铜基粉末冶金摩擦材料因其具有高的机械强度、高导热性和优良的摩擦磨损性能而成为高速列车制动闸片的首选材料,如何通过制备工艺和原料体系的改进提高材料的耐温性能和摩擦稳定性一直是人们研究的重点。本文通过采用不同的烧结工艺制备了铜基粉末冶金摩擦材料,研究不同烧结温度和烧结气氛对材料显微组织、物理机械性能和摩擦磨损性能的影响,并探讨了材料在不同制动条件下的摩擦磨损行为及机理,结果
表明:(1)铜基粉末冶金摩擦材料中各组元分布均匀,组元间接触紧密,鳞片状石墨垂直于压制方向呈层状分布,SiO2以黑色大颗粒状镶嵌于铜基体内。随的烧结温度提高,材料中各组元间的孔隙减少,当达到一定程度后,孔隙不再减少;烧结气氛对材料的形貌无明显影响。(2)
烧结工艺对材料的物理-机械性能影响较大。随烧结温度的提高,采用N2和N2+H2混合气制备材料的密度先升后降,抗压强度较大,且随之呈上升趋势;H2气氛制备材料的密度呈下降趋势,抗压强度与其他两种气氛下制备的相比显著降低,且呈下降趋势。(3)相同制动压力下,材料的摩擦系数随的转速的提高先升高后降低,磨损量随着转速的提高逐渐增加;在较低转速时,磨损以粘着磨损为主,随着转速提高,磨损逐渐表现为氧化磨损和疲劳磨损。N2+H2混合气氛烧结材料在较低
转速下具有较好的摩擦性能,磨损量很低,且随烧结温度提高呈下降
趋势;N2气氛烧结材料在较高转速下摩擦性能较好,摩擦稳定性好,而且磨损量也较低。(4)在一定转速下,随着制动压力的提高,材料的摩擦系数呈下降趋势,摩擦稳定性系数先升高后下降,磨损量显著增加;较低压力时,磨损主要由粘着机理控制,较高压力时,磨损主要表现为疲劳磨损和剥层脱落。N2+H2混合气氛烧结材料在高制动压力下具有较好的摩擦性能,摩擦稳定性最高,磨损量最小,且随烧结温度升高先减少后增加,在1000℃时最低。
【英文摘要】With the development of train transport, the requirements are stiffer and stiffer in the properties of the braking materials by the speed improvement. Because of the high mechanical strength, high conductibility and excellent friction and wear properties, Cu-based P/M friction materials have been the leading material for friction brake of high-speed train.Cu-based P/M friction material has been made by different sintering process. The effect of sintering temperature and atmosphere on the micro-structure, physical and mechanical properties and friction and wear properties of material have been investigated, and the friction and wear behavior and mechanism in the different braking conditions have been discussed. The results show:(1) Scaly graphite and SiO2 are well-distributed in Cu-based P/M materials. With the
increasing of sintering temperature, the pore volume between different components decreases gradually till reached a certain degree. Sintering atmospheres have no effect on the micro-structure of materials.(2) Sintering process have important effects on the physical and mechanical properties of materials. With the increasing of sintering temperature, the densities of materials sintered in N2 andN2+H2 atmosphere increases firstly and decreases then, but the densities in H2 trends to decrease; the compressive strength of materials sintered in N2 and N2+H2 are higher than that in H2.(3) On the same braking pressure, with speed increased, the frictional coefficient increases firstly and decreases then, but the wear volume increases gradually. The slipping speed changes, the wear mechanism changes also. At low speeds, adhesion wear is the main mechanism, but oxidation and fatigue wear takes on priority at high speeds. The materials sintered in the N2+H2 atmosphere have the best frictional property at low speeds, besides, the wear volumes are the lowest and decreases with the increasing sintering temperature. The materials sintered in the N2 atmosphere have the best frictional property at high speeds, and with high frictional stability and lower wear volume at the same time.(4) At the certain speed, with braking
pressure increased, the frictional coefficient trends to decrease, frictional stability increases firstly and decreases then, but the wear volume increases greatly. On low pressures, the main wear mechanism is adhesion wear, but fatigue and flake wear are the main mechanism on high pressures. The materials sintered in the N2+H2 atmosphere have the best frictional property on high pressure, the highest frictional stability and the lowest wear volumes, besides, with sintering temperature increased, the wear volume decreases firstly and increases then, and has the lowest value in the sintering temperature of 1000℃.
【关键词】烧结气氛烧结温度粉末冶金铜基摩擦材料摩擦磨损
【英文关键词】sintering atmosphere sintering temperature powder metallurgy Cu-based friction material friction and wear
【目录】烧结工艺对铜基粉末冶金摩擦材料性能的影响摘要
6-7ABSTRACT7-8目录9-12第一章绪论
12-25 1.1 高速列车发展概述12-13 1.2 摩擦材料概
述13-16 1.2.1 摩擦材料的种类13-15 1.2.1.1 有机
摩擦材料13-14 1.2.1.2 铸铁14 1.2.1.3 粉末冶金摩擦材料14-15 1.2.1.4 碳/碳复合材料15 1.2.2 摩擦
材料技术要求15-16 1.3 粉末冶金摩擦材料
16-23 1.3.1 粉末冶金摩擦材料组成16-19 1.3.1.1 基体组元17 1.3.1.2 摩擦组元17-18 1.3.1.3 润滑组元18-19 1.3.2 粉末冶金摩擦材料种类19-22 1.3.2.1 铜基粉末冶金摩擦材料19-20 1.3.2.2 铁基粉末冶金摩擦材料20-21 1.3.2.3 铁-铜基粉末冶金摩擦材料
21 1.3.2.4 其它金属基粉末冶金摩擦材料
21-22 1.3.3 粉末冶金摩擦材料在铁道车辆上的应用
22-23 1.4 选题意义和主要工作23-25第2章试验设计和研究方法25-30 2.1 材料组成和制备工艺
25 2.1.1 材料组成25 2.1.2 制备工艺25 2.2 试验方案25-26 2.3 性能检测手段26-30 2.3.1 密度和孔隙率27-28 2.3.2 硬度28 2.3.3 抗压强度
28 2.3.4 组织结构和表面形貌分析28-29 2.3.5 摩擦表面成分及相结构分析29 2.3.6 摩擦磨损性能测试
29-30第3章材料的物理机械性能及组织结构研究
30-38 3.1 烧结温度和气氛对材料密度和孔隙率的影响
30-32 3.2 烧结温度和气氛对材料抗压强度的影响
32-33 3.3 烧结温度和气氛对材料硬度的影响
33-34 3.4 烧结温度和气氛对材料组织结构的影响
34-36 3.5 本章小结36-38第4章材料的摩擦磨损性能研究38-61 4.1 不同温度烧结材料的摩擦磨损性能研究
38-53 4.1.1 转速对材料摩擦磨损性能的影响
38-47 4.1.1.1 转速对材料摩擦系数的影响
39-40 4.1.1.2 不同转速下摩擦系数的稳定性研究
40-41 4.1.1.3 转速对材料磨损量的影响
41-43 4.1.1.4 摩擦磨损机理分析43-47 4.1.2 制动压力对材料摩擦磨损性能的影响47-53 4.1.2.1 压力对材料摩擦系数的影响48-49 4.1.2.2 不同制动压力下摩擦系数的稳定性研究49-50 4.1.2.3 压力对材料磨损量的影响
50-52 4.1.2.4 摩擦磨损机理分析52-53 4.2 不同气氛烧结材料的摩擦磨损性能研究53-60 4.2.1 转速对材料摩擦磨损性能的影响53-57 4.2.1.1 转速对材料摩擦系数的影响53-55 4.2.1.2 不同转速下摩擦系数的稳定性研究
55 4.2.1.3 转速对材料磨损量的影响55-57 4.2.2 制动压力对材料摩擦磨损性能的影响57-60 4.2.2.1 压力对材料摩擦系数的影响57-58 4.2.2.2 不同制动压力下摩擦系数的稳定性研究58-59 4.2.2.3 压力对材料磨损量的影响
59-60 4.3 本章小结60-61结论61-62致谢
62-63参考文献63-68攻读硕士学位期间发表的学术论文68
烧结金属摩擦材料现状与发展动态
烧结金属摩擦材料现状与发展动态 newmaker 1 前言 烧结金属摩擦材料是以金属及其合金为基体,添加摩擦组元和润滑组元,用粉末冶金技术制成的复合材料,是摩擦式离合器与制动器的关键组件。它具有足够的强度,合适而稳定的摩擦系数,工作平稳可靠,耐磨及污染少等优点,是现代摩擦材料家族中应用面最大、量最大的材料。 用粉末冶金技术制造烧结金属摩擦材料已有70年的历史,1929年美国开始了这项工作的研究,30年代末期首先将该材料用在了D-7、D-8铲运机中的离合器片上。发展到现在,所有载荷量高的飞机,包括米格、伊尔、波音707、747和三叉戟等,其制动器摩擦衬材料都采用了烧结金属摩擦材料。在我国,特别是在1965年以后,烧结金属摩擦材料的科研、生产得到迅速发展。迄今,我国已有十多个具有一定生产规模的生产企业,年产铜基和铁基摩擦制品约850万件,广泛应用于飞机、船舶、工程机械、农业机械、重型车辆等领域,基本满足了国内主机配套和引进设备摩擦片的备件供给和使用要求。 2 制造方法与工艺研究 2.1 制造方法 目前,国内外烧结金属摩擦材料的生产仍主要沿用1937年美国S·K·Wellman及其同事们创造的钟罩炉加压烧结法(压烧法),该方法的基本工序是:钢背板加工→往油、电镀铜层(或铜、锡层);配方料混合→压制成薄片→与钢背板烧结成一体→加工沟槽及平面。由于传统的压烧法存在着能耗大、生产效率相对低、原材料粉末利用率低、本钱高等缺点。因此,一些国家对传统工艺作了一些改进,同时十分注重新工艺的研究,在改善或保证产品性能条件下探索和寻求进步经济效益的途径。 新的制造工艺相继问世,其中最令人瞩目的是喷撒工艺(Sprinkling powder procedure),它以生产的高效率和明显的经济效益独具上风。喷撒工艺法以产业规模生产烧结金属摩擦材料始于70年代,美国的威尔曼、西德的奥林豪斯和尤里特、奥地利的米巴等企业拥有这项技术。80年代中期,杭州粉末冶金研究所从奥地利米巴公司引进了该技术。 喷撒工艺的基本流程是:钢背板在溶剂(如四氯化碳中脱脂处理(或钢背板电镀)→在钢背板上喷撒上混合材料→预烧→压沟槽→终烧→精整。 与传统的压烧法相比,喷撒工艺主要有下列一些优点: (1)实现了无加压连续烧结,耗能低。
粉末冶金烧结技术的研究进展
总第56期第4期 贵阳金筑大学学报 2004年12月 粉末冶金烧结技术的研究进展 林 芸 ① (西安交通大学材料科学与工程学院 西安 710049) 摘 要:烧结作为粉末冶金最重要的一个工艺环节一直以来是人们研究的重点,介绍粉末冶金烧结技术的研究进展,以体现烧结在粉末冶金中的重要地位,推进新材料制备技术的发展。 关键词:粉末冶金 烧结 新技术中图分类号:TF124 文献标识码:B 文章编号:1671-3621(2004)04-0106-0108 现代科学技术的不断发展牵引着工程材料向着复合化、高性能化、功能化、结构功能一体化和智能化方向发展,各行业对材料的性能提出了越来越高的要求。在不断开发新材料的同时,人们也在不断地寻求新型材料的制备方法,小型化、自动化、精密化、省能源、无污染的材料制备方法成为人们追求的目标。现代粉末冶金技术由于其少切屑、无切屑及近净成形的工艺特点,在新材料的制备中发挥了越来越大的作用。它的低耗、节能、节材,易控制产品孔隙度,易实现金属-非金属复合,金属-高分子复合等特点使其成为制取各种高性能结构材料、特种功能材料和极限条件下工作材料的有效途径[1],受到了人们的广泛关注。 从现代复合材料技术的理论来看,粉末冶金复合技术从微观上改变了单一材料的性能,依靠扩散流动使物质发生迁移,同时原材料的晶体组织发生变化,最终“优育”出高性能的复合材料。而烧结作为粉末冶金生产过程中最重要的工序,一直以来是人们研究的重点,各种促进烧结的方法不断涌现,对改进烧结工艺,提高粉末冶金制品的力学性能,降低物质与能源消耗,起了积极的作用。本文简单介绍近几年出现的几种烧结新技术,以期反映粉末冶金在高技术领域所起的重要作用。 1、放电等离子体烧结(Spark Plasma Sintering , SPS ) 放电等离子体烧结(SPS )也称作等离子体活化 烧结(Plasma Activated Sintering ,PAS )或脉冲电流热压烧结(Pulse Current Pressure Sintering ),是自90年代以来国外开始研究的一种快速烧结新工艺[2]。由于它融等离子体活化、热压、电阻加热为一体,具有烧结时间短、温度控制准确、易自动化、烧结样品颗粒均匀、致密度高等优点,仅在几分钟之内就使烧结产品的相对理论密度接近100%,而且能抑制样品颗粒的长大,提高材料的各种性能,因而在材料处理过程中充分显示了优越性。 将瞬间、断续、高能脉冲电流通入装有粉末的模具上,在粉末颗粒间即可产生等离子放电,由于等离子体是一种高活性离子化的电导气体,因此,等离子体能迅速消除粉末颗粒表面吸附的杂质和气体,并加快物质高速度的扩散和迁移,导致粉末的净化、活化、均化等效应。第三代SPS 设备采用的是开关直流脉冲电源,在50Hz 供电电源下,发生一个脉冲的时间为312ms ,由于强脉冲电流加在粉末颗粒间,即可产生诸多有利于快速烧结的效应。首先,由于脉冲放电产生的放电冲击波以及电子、离子在电场中反方向的高速流动,可使粉末吸附的气体逸散,粉末表面的起始氧化膜在一定程度上可被击穿,使粉末得以净化、活化;其次,由于脉冲是瞬间、断续、高频率发生, ? 601?①收稿日期:2004-6-10作者简介:林芸(1965-),女,高级工程师,西安交通大学材料与工程学院在读工程硕士,主要研究方向:金属基复合材料制备工艺。
粉末冶金的烧结技术
粉末冶金的烧结技术 作者:本站整理文章来源:本站搜集点击数:466 更新时间:2008-3-17 16:03:20 1.烧结的方法 不同的产品、不同的性能烧结方法不一样。 ⑴按原料组成不同分类。可以将烧结分为单元系烧结、多元系固相烧结及多元系液相烧结。 单元系烧结是纯金属(如难熔金属和纯铁软磁材料)或化合物(Al2O3、B4C、BeO、M oSi2等)熔点以下的温度进行固相烧结。多元系固相烧结是由两种或两种以上的组元构成的烧结体系,在其中低熔成分的熔点温度以下进行的固相烧结。粉末烧结合金多属于这一类。如Cu-Ni、Fe-Ni、Cu-Au、W-Mo、Ag-Au、Fe-Cu、W-Ni、Fe-C、Cu-C、Cu-W、Ag -W等。多元系液相烧结以超过系统中低熔成分熔点的温度进行的烧结。如W-Cu-Ni、W-Cu、WC-Co、TiC-Ni、Fe-Cu(Cu>10%、Fe-Ni-Al、Cu-Pb、Cu-Sn、Fe-Cu(Cu<10%)等 ⑵按进料方式不同分类。分为为连续烧结和间歇烧结。 连续烧结 烧结炉具有脱蜡、预烧、烧结、制冷各功能区段,烧结时烧结材料连续地或平稳、分段地完成各阶段的烧结。连续烧结生产效率高,适用于大批量生产。常用的进料方式有推杆式、辊道式和网带传送式等。
间歇烧结 零件置于炉内静止不动,通过控温设备,对烧结炉进行需要的预热、加热及冷却循环操作,完成烧结材料的烧结过程。间歇烧结可依据炉内烧结材料的性能确定合适的烧结制度,但生产效率低,适用于单件、小批量生产,常用的烧结炉有钟罩式炉、箱式炉等。 除上述分类方法外。按烧结温度下是否有液相分为固相烧结和液相烧结;按烧结温度分为中温烧结和高温烧结(1100~1700℃),按烧结气氛的不同分为空气烧结,氢气保护烧结(如钼丝炉、不锈钢管和氢气炉等)和真空烧结。另外还有超高压烧结、活化热压烧结等新的烧结技术。 2.影响粉末制品烧结质量的因素 影响烧结体性能的因素很多,主要是粉末体的性状、成形条件和烧结的条件。烧结条件的因素包括加热速度、烧结温度和时间、冷却速度、烧结气氛及烧结加压状况等。 ⑴烧结温度和时间 烧结温度的高低和时间的长短影响到烧结体的孔隙率、致密度、强度和硬度等。烧结温度过高和时间过长,将降低产品性能,甚至出现制品过烧缺陷;烧结温度过低或时间过短,制品会因欠烧而引起性能下降。 ⑵烧结气氛
Fe在铜基粉末冶金摩擦材料中的作用
收稿日期:2006-02-20 基金项目:湖南省科技重大项目产业化研究资助(01-96-10)作者简介:陈 洁(1978-),女(汉),湖南长沙人,在读博士,主要从事复合材料的研究。 Fe 在铜基粉末冶金摩擦材料中的作用 陈 洁,熊 翔,姚萍屏,李世鹏 (中南大学粉末冶金研究院国家重点实验室,湖南 长沙 410083) 摘 要:研究了Fe 在铜基粉末冶金航空摩擦材料中的摩擦磨损作用及机理。研究表明:Fe 在 铜基摩擦材料中起到了摩擦组分的作用,对材料的机械性能和摩擦磨损性能起到了重要的作用。Fe 能提高铜基摩擦材料的强度、硬度;当Fe 含量超过4%后,随Fe 含量的增加,材料的摩擦系数及稳定性增加;高速摩擦条件下,Fe 能促进摩擦面氧化膜的形成,减小材料的摩擦系数和磨损量。 关键词:粉末冶金摩擦材料;摩擦磨损;摩擦组分;摩擦机理中图分类号:TF12512 文献标识码:A 文章编号:1006-6543(2006)04-0016-05 THE WOR KIN G OF Fe IN COPPER -BASED P/M FRICTION MA TERIAL CHEN Jie ,XIONG Xiang ,YAO Ping -ping ,L I Shi -peng (Stare K ey Laboratoty of Powder Metallurgy ,Central S outh University ,Changsha 410083,China ) Abstract :The working mechanism of Fe in a new type of copper -based P/M friction material was studied 1The results show that Fe works as frictional component in copper -based friction ma 2terials ,influening the mechanical and frictional property of materials 1Fe can increase the strength and hardness of friction material ;when Fe is more than 4%,with the increase of Fe ,the friction coefficient and stability of the material are enhanced 1At the same time ,at high speed friction ,Fe takes part in formation of oxide film on friction surface ,so the wear loss of friction material is de 2creased 1 K ey w ords :P/M friction material ;friction and wear ;friction component ;friction mechanism 铜基粉末冶金摩擦材料由于其良好的导热性、耐磨性而被广泛应用于各种离合器和刹车装置中[1]。粉末冶金摩擦材料是以金属及其合金为基体,添加硬质颗粒摩擦组元和固体润滑组元,用粉末冶金的方法制造而成的金属基颗粒复合材料[2]。因此,可以通过调节和控制复合材料中各组元的含量及存在形式来改善材料的物理机械性能,进而提高材料的摩擦磨损性能,最终得到综合性能优异的粉末冶金摩擦材料。 粉末冶金摩擦材料中大都加有Fe 作为摩擦组元,以提高材料的摩擦系数[3,4],其含量一般在5%~25%的范围内。有资料显示[5],Fe 含量在5%以下时,摩擦系数才有所提高,随后Fe 含量增加,材料的摩擦系数变化不大,且Fe 含量增加,材料磨损量增加,对偶磨损量则减少[6]。本文即针对Fe 在新型铜基粉末冶金摩擦材料中的作用机理进行了系统的分析,明确了Fe 对铜基粉末冶金摩擦材料摩擦磨损性能的影响。 第16卷 第4期 2006年8月 粉末冶金工业POWDER METALL URG Y IN DUSTR Y Vol.16No.4Aug.2006
开题报告 瓷砖低温烧结技术的研究与应用 硕士.pdf
开题报告(在职) 学位论文题目: 工程领域名称:仪器仪表工程学号: 姓名: 校内导师姓名: 企业方导师姓名: 硕士生所在单位名称: 填表日期:
填表说明 1、研究生须认真填写本表相关内容。 2、开题报告内容见《中国计量学院在职攻读工程硕士专业学位研究生管理规定》 3、所列栏目填写不下的,可以另加附页。 4、本表采取双面印制,且保持原格式不变,纸张限用A4(页边距为上、下: 2.5cm, 左为2.6cm,右为2.1cm;字体为宋体小四,行间距为18磅),整齐装订。 5、开题报告完成,此表经相关人员签字后,须交学院研究生教务秘书保存。
开题报告登记表内容应包括以下部分,不少于3000字: (1)说明选题来源、选题依据、国内外研究动态; (2)说明选题在理论研究或实际应用方面的意义和价值; (3)阐述学位论文中自身研究工作部分,论证完成研究工作拟采取的主要理论、技术路线和实施方案; (4)说明研究工作要实现的最终目标和研究成果形式。 1、选题简介、目的和意义 1.1 选题简介 本课题以瓷砖低温烧结技术的研究及应用为研究方向,系统研究了添加溶剂 的成分及比例对瓷砖烧制的结构的影响。 1.2选题的目的与意义 瓷砖生产普遍采用高温烧制(一般温度在1200℃),其中烧制能耗占总生产成本的30%以上,如果烧制温度降低100℃,能够降低总能耗20-30%,并能够大大减少CO2废气的排放量,不仅对保护大气环境有着重要的意义,而且还能创造更高的经济效益和社会效益。所以瓷砖低温烧结技术对我国瓷砖行业的发展具有重要意义。 2.引言 2.1瓷砖的应用及分类 瓷砖是以耐高温的半金属氧化物和金属氧化物,经过研磨、混合、压制、施釉、烧结等 工艺后,从而形成的一种能够耐酸碱的石质或者瓷质建筑或装饰材料,瓷砖的原材料多由粘土、石英沙等等混合而成。 瓷砖根据吸水率不同,可以分为:瓷质砖、炻瓷质、细炻质、陶质砖;根据用途可以分为:外墙砖、内墙砖、地砖、广场砖、工业砖等;根据成型工艺不同,可以分为:干压成型砖、挤压成型砖、可塑成型砖;根据施釉工艺,可以分为:有釉砖、无釉砖;依品种可以分为:抛光砖、仿古砖、瓷片、全抛釉、抛晶砖、微晶石、劈开砖、广场砖(文化砖);依生产工艺分:印花砖、抛光砖、斑点砖、水晶砖、无釉砖;随着现代瓷砖工艺技术不断壮大发展,还衍生出多种创意瓷砖来迎合人们不断更新的家居装修理念。如:喷墨印花砖、木纹砖等。1.2瓷砖的发展历史 根据历史学家考证,人类制砖已经有4000多年的历史,古老的埃及金字塔、古巴比伦遗址以及古希腊城市遗址中都曾发现美丽的瓷砖墙面。到了中世纪,英国人们铺在教堂和修道 院的地板上不同色彩的几何形瓷砖,伊比利亚半岛的马赛克;文艺复兴时期的意大利马约利 卡陶器地板砖,安特卫普的陶瓷,以及德国的瓷砖都曾在瓷砖历史上占据了一席之地。 可以说欧洲是现代瓷砖的诞生地,其中尤以意大利和西班牙最为出名。到上世纪70年代,随着“意大利家用产品新风貌”展览会在美国现代艺术博物馆等地成功展出,意大利从此确 立了家居设计的世界领导者地位。来自意大利的设计师在瓷砖的设计中融入个人的需求,同 时对细节近似疯狂的精雕细琢,给了居家主人细致入微的感受。现代瓷砖设计的另一个代表 的是西班牙,西班牙瓷砖以绚丽的色彩、丰富的纹理,多种多样的花色品种而备受客户青睐。 我国的瓷砖烧制历史也十分悠久,最早商朝便有陶瓷制品;进入周朝后便有了砖瓦建筑;春秋战国时期的陶瓷砖,其表面已有了非常精美的纹饰;到了秦汉时期,古建筑已大规模使 用陶瓷材料,留下了“秦砖汉瓦”的佳话。到了东汉时期,浙江的越窑的青瓷技术逐渐成熟 起来。直至魏晋南北朝,青瓷已经独霸中国的瓷器市场。唐朝的彩陶艺术得到了巨大的发展,最大的成就是世人所熟知的“唐三彩”。经过近千年的发展,中国陶瓷到明朝时期迎来了新的辉煌。瓷器不再单调乏味,而是油光异彩,有蓝釉、祭红釉、郎窑红釉、豆红釉、黄釉、孔 雀绿釉、黑釉等。尤以明代宣德瓷器最为出名。清代虽然是中国封建社会的衰落时期,但陶
摩擦材料
摩擦材料 一、概论 摩擦材料是一种应用在动力机械上,依靠摩擦作用来执行制动和传动功能的部件材料。它主要包括制动器衬片(刹车片)和离合器面片(离合器片)。刹车片用于制动,离合器片用于传动。 任何机械设备与运动的各种车辆都必须要有制动或传动装置。摩擦材料是这种制动或传动装置上的关键性部件。它最主要的功能是通过摩擦来吸收或传递动力。如离合器片传递动力,制动片吸收动能。它们使机械设备与各种机动车辆能够安全可靠地工作。所以说摩擦材料是一种应用广泛又甚关键地材料。 摩擦材料是一种高分子三元复合材料,是物理与化学复合体。它是由高分子粘结剂(树脂与橡胶)、增强纤维和摩擦性能调节剂三大类组成及其它配合剂构成,经一系列生产加工而制成的制品。摩擦材料的特点是具有良好的摩擦系数和耐磨损性能,同时具有一定的耐热性和机械强度,能满足车辆或机械的传动与制动的性能要求。它们被广泛应用在汽车、火车、飞机、石油钻机等各类工程机械设备上。民用品如自行车、洗衣机等作为动力的传递或制动减速用不可缺少的材料。 二、摩擦材料发展简史 自世界上出现动力机械和机动车辆后,在其传动和制动机构中就使用摩擦片。初期的摩擦片系用棉花、棉布、皮革等作为基材,如:将棉花纤维或其织品浸渍橡胶浆液后,进行加工成型制成刹车片或刹车带。其缺点:耐热性较差,当摩擦面温度超过120℃后,棉花和棉布会逐渐焦化甚至燃烧。随着车辆速度和载重的增加,其制动温度也相应提高,这类摩擦材料已经不能满足使用要求。人们开始寻求耐热性好的、新的摩擦材料类型,石棉摩擦材料由此诞生。 石棉是一种天然的矿物纤维,它具有较高的耐热性和机械强度,还具有较长的纤维长度、很好的散热性,柔软性和浸渍性也很好,可以进行纺织加工制成石棉布或石棉带并浸渍粘结剂。石棉短纤维和其布、带织品都可以作为摩擦材料的基材。更由于其具有较低的价格(性价比),所以很快就取代了棉花与棉布而成为摩擦材料中的主要基材料。1905年石棉刹车带开始被应用,其制品的摩擦性能和使用寿命、耐热性和机械强度均有较大的提高。1918年开始,人们用石棉短纤维与沥青混合制成模压刹车片。20世纪20年代初酚醛树脂开始工业化应用,由于其耐热性明显高于橡胶,所以很快就取代了橡胶,而成为摩擦材料中主要的粘结剂材料。由于酚醛树脂与其他的各种耐热型的合成树脂相比价格较低,故从那时起,石棉-酚醛型摩擦材料被世界各国广泛使用至今。 20世纪60年代,人们逐渐认识到石棉对人体健康有一定的危险性。在开采或生产过程中,微细的石棉纤维易飞扬在空气中被人吸入肺部,长期间处于这种环境下的人们比较容易患上石棉肺一类的疾病。因此人们开始寻求能取代石棉的其它纤维材料来制造摩擦材料,即无石棉摩擦材料或非石棉摩擦材料。20世纪70年代,以钢纤维为主要代替材料的半金属材料在国外被首先采用。80年代-90年代初,半金属摩擦材料已占据了整个汽车用盘式片领域。20世纪90年代后期以来,NAO(少金属)摩擦材料在欧洲的出现是一个发展的趋势。无石棉,采用两种或两种以上纤维(以无机纤维为主,并有少量有机纤维)只含少量钢纤维、铁粉。NAO(少金属)型摩擦材料有助于克服半金属型摩擦材料固有的高比重、易生锈、易产生制动噪音、伤对偶(盘、鼓)及导热系数过大等缺陷。目前,NAO (少金属)型摩擦材料已得到广泛应用,取代半金属型摩擦材料。2004年开始,随汽车工业飞速发展,人们对制动性能要求越来越高,开始研发陶瓷型摩擦材料。陶瓷型摩擦材料主要以无机纤维和几种有机纤维混杂组成,无石棉,无金属。其特点为: 1. 无石棉符合环保要求; 2. 无金属和多孔性材料的使用可降低制品密度,有利于减少损伤制动盘(鼓)和产生制动噪音的粘度。 3. 摩擦材料不生锈,不腐蚀; 4. 磨耗低,粉尘少(轮毂)。 三、摩擦材料分类 在大多数情况下,摩擦材料都是同各种金属对偶起摩擦的。一般公认,在干摩擦条件下,同对偶摩擦系数大于0.2的材料,称为摩擦材料。 材料按其摩擦特性分为低摩擦系数材料和高摩擦系数材料。低摩擦系数材料又称减摩材料或润滑材料,其作用是减少机械运动中的动力损耗,降低机械部件磨损,延长使用寿命。高摩擦系数材料又称摩阻材料(称为摩擦材料)。
粉末冶金常识
粉末冶金常识 1、粉末冶金常识之什么是粉末冶金? 粉末冶金是一门制造金属粉末,并以金属粉末(有时也添加少量非金属粉末)为原料,经过混合、成形 和烧结,制造材料或制品的技术。它包括两部分内容,即:(1)制造金属粉末(也包括合金粉末,以下统称“金属粉末“)。 (2)用金属粉末(有时也添加少量非金属粉末)作原料,经过混合、成形和烧结,制造材料(称为“粉末冶金材料“)或制品(称为“粉末冶金制品“)。 2、粉末冶金常识之粉末冶金最突岀的优点是什么? 粉末冶金最突岀的优点有两个: (1)能够制造目前使用其他工艺无法制造或难于制造的材料和制品,如多孔、发汗、减震、隔音等材料和 制品,钨、钼、钛等难熔金属材料和制品,金属-塑料、双金属等复合材料及制品。 (2)能够直接制造岀合乎或者接近成品尺寸要求的制品,从而减少或取消机械加工,其材料利用率可以高 达95%X上,它还能在一些制品中以铁代铜,做到了“省材、节能“。 粉末冶金件 3、粉末冶金常识之什么是"铁基"?什么是铁基粉末冶金? 铁基是指材料的组成是以铁为基体。铁基粉末冶金是指用烧结(也包括粉末锻造)方法,制造以铁为主要成分的粉末冶金材料和制品(铁基机械零件、减磨材料、摩擦材料,以及其他铁基粉末冶金材料)的工艺总称。 4、粉末冶金常识之用于粉末冶金的粉末制造方法主要有哪几类? 粉末制造方法主要有物理化学法和机械粉碎法两大类。前者包括还原法、电解法和羰基法等;后者包括研磨法和雾化法。 5、粉末冶金常识之用还原法制造金属粉末是怎么回事? 该法是用还原剂把金属氧化物中的氧夺取出来,从而得到金属粉末的一种方法。 6、粉末冶金常识之什么叫还原剂? 还原剂是指能够夺取氧化物中氧的物质。制取金属粉末所用的还原剂,是指能够除掉金属氧化物中氧的物质。就金属氧化物而言,凡是与其中氧的亲合力大于这种金属与氧的亲合力的物质,都称其为这种金属氧化物的还原剂。 7、粉末冶金常识之粉末还原退火的目的是什么? 粉末还原退火的目的主要有以下三个方面:(1)去除金属粉末颗粒表面的氧化膜;(2)除掉颗粒表面吸附的气体和水分等异物;(3 )消除颗粒的加工硬化。 粉末冶金工艺流程图 8、粉末冶金常识之用于粉末冶金的粉末性能测定一般有哪几项? 用于粉末冶金的粉末性能测定一般有三项:化学成分、物理性能和工艺性能。9、用于粉末冶金的粉末物 理性能主要包括那几项? 用于粉末冶金的粉末物理性能主要包括以下三项:( 1)粉末的颗粒形状;( 2)粉末的粒度和粒度组成;(3)粉末的比表面。
基于T-S模糊模型的炼铁烧结过程建模毕业论文
基于T-S模糊模型的炼铁烧结过程建模毕业论文 目录 第一章课题描述 (1) 1.1炼铁烧结介绍 (1) 1.2 T-S模糊模型介绍: (2) 1.3 T-S模糊模型的特点: (4) 1.4 本论文的大致工作: (5) 第二章基础知识 (6) 2.1模糊集合的基本概念 (6) 2.2模糊集合的基本运算: (8) 2.3模糊C均值聚类(FCM)算法 (9) 2.4最小二乘法 (10) 2.5 逐步回归方法: (11) 第三章炼铁烧结的工艺流程 (15) 3.1原料的准备: (16) 3.2配料与混合: (16) 3.3烧结生产: (17) 3.4烧结过程中用到的化学反应: (19) 第四章运用T-S模糊模型对炼铁烧结过程进行建模 (21)
4.1 从各类公式中总结整个构建模型的过程 (21) 4.2 利用T-S模糊模型对炼铁烧结数据进行仿真 (22) 4.2.1 确定T-S模糊模型的后件结构 (24) 4.2.2确定T-S模糊模型的前件参数与结构 (24) 4.2.3 确定模糊模型的后件参数 (24) 4.3 利用MATLAB对模型进行仿真 (24) 第五章结论 (27) 致谢 (29) 第一章课题描述 1.1炼铁烧结介绍 炼铁烧结的过程其实就是使用粉末状和细砂状的含铁材料经过化学反应和人工冶制,生产出具有十分不错的冶铁性能的精铁矿,是高炉炼铁前不可缺少的步骤之一。在炼铁烧结中,减少高炉的燃料热损耗是所有炼铁厂的首要任务,但是想要全面提高人造烧结矿的质量还要加强常温的强度,所以要达到这个目的,就要提高烧炉原材料的还原性,还要加强焦炭以及煤粉的利用率,并降低燃耗。炼铁厂一般先要将加工的铁矿粉和自然界的精矿石进行打磨和筛选,按照规定来使用颗粒半径小于8mm的铁矿粉,同时颗粒半径小于8mm的返矿粉可冶铁厂生产出来的废料,例如硫酸渣,高炉炉尘,轧钢皮等按照规定比例延迟后,再调整高炉的热量多少和酸碱度的大小和熔剂,例如:石灰石、生石灰、消石灰,将所有的准备工作做好之后再将高炉点火。因为燃料进行化学时放出的大量热量,燃
烧结气氛论文:烧结工艺对铜基粉末冶金摩擦材料性能的影响
烧结气氛论文:烧结工艺对铜基粉末冶金摩擦材料性能的影响 【中文摘要】随着我国铁路运输业的飞速发展,列车运行速度一提再提,这就对制动摩擦材料提出了更为苛刻的要求。铜基粉末冶金摩擦材料因其具有高的机械强度、高导热性和优良的摩擦磨损性能而成为高速列车制动闸片的首选材料,如何通过制备工艺和原料体系的改进提高材料的耐温性能和摩擦稳定性一直是人们研究的重点。本文通过采用不同的烧结工艺制备了铜基粉末冶金摩擦材料,研究不同烧结温度和烧结气氛对材料显微组织、物理机械性能和摩擦磨损性能的影响,并探讨了材料在不同制动条件下的摩擦磨损行为及机理,结果 表明:(1)铜基粉末冶金摩擦材料中各组元分布均匀,组元间接触紧密,鳞片状石墨垂直于压制方向呈层状分布,SiO2以黑色大颗粒状镶嵌于铜基体内。随的烧结温度提高,材料中各组元间的孔隙减少,当达到一定程度后,孔隙不再减少;烧结气氛对材料的形貌无明显影响。(2) 烧结工艺对材料的物理-机械性能影响较大。随烧结温度的提高,采用N2和N2+H2混合气制备材料的密度先升后降,抗压强度较大,且随之呈上升趋势;H2气氛制备材料的密度呈下降趋势,抗压强度与其他两种气氛下制备的相比显著降低,且呈下降趋势。(3)相同制动压力下,材料的摩擦系数随的转速的提高先升高后降低,磨损量随着转速的提高逐渐增加;在较低转速时,磨损以粘着磨损为主,随着转速提高,磨损逐渐表现为氧化磨损和疲劳磨损。N2+H2混合气氛烧结材料在较低
转速下具有较好的摩擦性能,磨损量很低,且随烧结温度提高呈下降 趋势;N2气氛烧结材料在较高转速下摩擦性能较好,摩擦稳定性好,而且磨损量也较低。(4)在一定转速下,随着制动压力的提高,材料的摩擦系数呈下降趋势,摩擦稳定性系数先升高后下降,磨损量显著增加;较低压力时,磨损主要由粘着机理控制,较高压力时,磨损主要表现为疲劳磨损和剥层脱落。N2+H2混合气氛烧结材料在高制动压力下具有较好的摩擦性能,摩擦稳定性最高,磨损量最小,且随烧结温度升高先减少后增加,在1000℃时最低。 【英文摘要】With the development of train transport, the requirements are stiffer and stiffer in the properties of the braking materials by the speed improvement. Because of the high mechanical strength, high conductibility and excellent friction and wear properties, Cu-based P/M friction materials have been the leading material for friction brake of high-speed train.Cu-based P/M friction material has been made by different sintering process. The effect of sintering temperature and atmosphere on the micro-structure, physical and mechanical properties and friction and wear properties of material have been investigated, and the friction and wear behavior and mechanism in the different braking conditions have been discussed. The results show:(1) Scaly graphite and SiO2 are well-distributed in Cu-based P/M materials. With the
粉末冶金烧结工艺
粉末冶金中的烧结 烧结是粉末冶金过程中最重要的工序。在烧结过程中,由于温度的变化粉末坯块颗粒之间发生粘结等物理化学变化,从而增加了烧结制品的电阻率、强度、硬度和密度,减小了孔隙度并使晶粒结构致密化。 一.定义 将粉末或粉末压坯经过加热而得到强化和致密化制品的方法和技术。 二.烧结分类 根据致密化机理或烧结工艺条件的不同,烧结可分为液相烧结、固相烧结、活化烧结、反应烧结、瞬时液相烧结、超固相烧结、松装烧结、电阻烧结、电火花烧结、微波烧结和熔浸等。 1.固相烧结:按其组元的多少可分为单元系固相烧结和多元系固相烧结两类。 单元系固相烧结纯金属、固定成分的化合物或均匀固溶体的松装粉末或压坯在熔点以下温度(一般为绝对熔点温度的2/3一4/5)进行的粉末烧结。 单元系固相烧结过程大致分3个阶段: (1)低温阶段(T烧毛0.25T熔)。主要发生金属的回复、吸附气体和水分的挥发、压坯内成形剂的分解和排除。由于回复时消除了压制时的弹性应力,粉末颗粒间接触面积反而相对减少,加上挥发物的排除,烧结体收缩不明显,甚至略有膨胀。此阶段内烧结体密度基本保持不变。 (2)中温阶段(T烧(0.4~。.55T动。开始发生再结晶、粉末颗粒表面氧化物被完全还原,颗粒接触界面形成烧结颈,烧结体强度明显提高,而密度增加较慢。 (3)高温阶段(T烧二0.5一。.85T熔)。这是单元系固相烧结的主要阶段。扩散和流动充分进行并接近完成,烧结体内的大量闭孔逐渐缩小,孔隙数量减少,烧结体密度明显增加。保温一定时间后,所有性能均达到稳定不变。 (2)多元固相烧结:组成多元系固相烧结两种组元以上的粉末体系在其中低熔组元的熔点以下温度进行的粉末烧结。 多元系固相烧结除发生单元系固相烧结所发生的现象外,还由于组元之间的相互影响和作用,发生一些其他现象。对于组元不相互固溶的多元系,其烧结行为主要由混合粉末中含量较多的粉末所决定。如铜一石墨混合粉末的烧结主要是铜粉之间的烧结,石墨粉阻碍铜粉间的接触而影响收缩,对烧结体的强度、韧性等都有一定影响。对于能形成固溶体或化合物的多元系固相烧结,除发生同组元之间的烧结外,还发生异组元之间的互溶或化学反应。烧结体因组元体系不同有的发生收缩,有的出现膨胀。异扩散对合金的形成和合金均匀化具有决定作用,一切有利于异扩散进行的因素,都能促进多元系固相烧结过程。如采用较细的粉末,提高粉末混合均匀性、采用部分预合金化粉末、提高烧结温度、消除粉末颗粒表面的吸附气体和氧化膜等。 2.活化烧结:是指采用物理或化学的手段使烧结温度降低、烧结时间缩短、烧结体活化烧结性能提高的一种粉末冶金方法.活化烧结工艺分为物理活化烧结工艺和化学活化烧结工艺两大类。 物理活化烧结:物理活化烧结工艺有依靠周期性改变烧结温度、施加机械振动、超声波和外应力等促进烧结过程。 化学活化烧结工艺:(1)预氧化烧结。(2)改变烧结气氛的成分和含量。(3)粉末内添加微量元素。(4)使用超细粉末、高能球磨粉末进行活化烧结。活化烧结主要用于钨、钼、铼、铁、钽、钒、铝、钛和硬质化合物材料等的烧结。 活化烧结过程烧结过程是一个物理化学反应过程,其烧结反应速度常数K可用下式表示
烧结生成工艺及生产的工艺流程实验研究毕业论文
烧结生成工艺及生产的工艺流程实验研究毕业 论文 目录 1综述 (1) 1.1烧结生产概况 (1) 1.1.1国烧结生产现状 (1) 1.1.2国外烧结生产现状 (2) 1.1.3烧结生产的目的 (3) 1.1.4烧结矿指标对高炉冶炼过程的影响 (4) 1.1.5生产新工艺和新技术 (6) 1.2烧结成矿机理 (10) 1.2.1烧结过程中的固相反应 (10) 1.2.2烧结过程中的液相生成 (10) 1.2.3烧结过程中的冷凝固结 (11) 1.3烧结矿矿相结构及物理性质对烧结矿质量的因素 (11) 1.4烧结矿指标和冶金性能的影响因素 (13) 1.5烧结生成工艺及生产的工艺流程 (16) 1.5.1烧结生成工艺 (16) 1.5.2烧结生产的工艺流程 (17) 1.5.2.1烧结原料的准备 (17) 1.5.2.2配料与混合 (17) 1.5.2.3烧结生产 (18) 1.6课题的意义 (21) 2、原、燃料条件及评价 (22) 2.1烧结用原料条件 (22) 2.2 烧结用燃料性质评价 (22) 2.2.1 燃料的粒度 (22) 2.2.2燃料的基本性质 (23) 2.2.2.1燃料的工业分析、元素分析 (23) 2.2.2.2. 燃料的灰成分和灰熔点 (24) 2.2.3 燃料的反应性 (26) 2.2.4 燃料的热分析 (26) 2.2.4.1粉末状燃料的分析 (26) 2.2.4.2 颗粒状燃料的热分析 (27) 2.3原、燃料配比 (28) 3、实验研究容和方法 (29) 3.1实验方法过程及性能检测 (29) 3.1.1烧结矿 (29)
3.1.2.落下实验 (30) 3.1.3.转鼓实验 (31) 3.1.4.还原实验 (31) 3.1.5.滴落实验 (32) 3.2烧结矿生产和质量指标 (33) 4、实验结果及分析 (35) 4.1 烧结矿产量,强度,化学和矿物组成实验结果及其分析 (35) 4.1.1烧结料混合指标 (35) 4.1.2.烧结矿的产量指标 (36) 4.1.3半焦、无烟煤粒度对烧结矿强度的影响 (37) 4.1.4烧结矿的化学成分和转鼓强度 (39) 4.2 烧结矿冶金性能 (41) 4.2.1烧结矿的还原性能与还原粉化性能 (41) 4.2.2烧结矿的软化熔滴性能 (42) 5、结论 (44) 6、参考文献 (45)
粉末冶金摩擦材料原料作用分析
高铁粉末冶金刹车片用原材料作用分析粉末冶金摩擦材料的问世距今已有近百年的历史,尤其在近几年发展尤为迅猛。粉末冶金工艺可以将金属和非金属组分的不同性能很好地配合于一种材料中,已有逐渐代替有机物粘结高分子材料的趋势。 粉末冶金摩擦材料一般由三部分组成:构成基体金属骨架的组元、润滑组元和摩擦组元。是一种含有金属和非金属多种组分的假合金。 1构成基体金属骨架的组元 简称基体组元。常用铜、铁、二硫化钼、镍、钛、铬、钼、钨、磷、锡、铝、锌等。 基体组元由基本组元和辅助组元两部分组成,基本组元在成分中占的比重最大。在铁基中,基本组元是铁。在铜基中,基本组元是铜。辅助组元与基本组元形成合金,从而改善基本组元的性能,或者是赋予基本组元以某种所需要的性能。辅助组元在铁基材料中有二硫化钼、镍、铬、钼、铜及磷等。在铜基中主要是锡、铝、锌及磷等。 粉末冶金摩擦材料的性能、工艺特点在很大程度上取决于基体组元的化学成分、结构和物理机械性能。基体组元保证了材料的承载能力、热稳定性、耐磨性,以及在高温工作时保持住摩擦剂和润滑剂颗粒的能力。一般在粉末冶金摩擦材料中,基体组元占铁基材料的50%~70%,占铜基材料的60%~90%。 1.1铁 近年来铁基粉末冶金摩擦材料的发展很快,主要是由于它节省有色金属,在高温高负荷下显示出更加优良的摩擦性能,机械强度高,能够承受比较大的压力,因而它应用在很多领域。但是,由于铁与对偶具有很强的亲和性,有利于粘结过程的发展,因此需加入大量的其他元素使铁合金化以降低铁的塑性,提高其强度、屈服极限和硬度,以克服次缺点,但同时也提高了成本和加工工艺复杂度。 铁基材料的基体组元中,加入镍、铬、钼,主要目的在于提高材料机械-物理性能和耐热耐腐性能。加入磷,能提高材料的强度,提高耐磨性。加入二硫
摩擦材料
摩擦材料 定义:是一种由粘结剂、增强纤维、摩擦性能调节剂和其它配合剂组成的复合材料 粘结剂: ★酚醛树脂 ★橡胶 ★橡胶和酚醛树脂共混 增强材料:无机或有机纤维 填料:摩擦性能调节剂和配合剂组成 粘结剂: 摩擦材料所用的有机粘结剂为酚醛类树脂和合成橡胶,而以酚醛类树脂为主。它们的特点和作用是当处于一定加热温度下时先呈软化而后进入粘流态,产生流动并均匀分布在材料中形成材料的基体,最后通过树脂固化作用的橡胶硫化作用,把纤维和填料粘结在一起,形成质地致密的有相当强度及能满足摩擦材料使用性能要求的摩擦片制品。 增强纤维: 纤维增强材料构成摩擦材料的基材,它赋予摩擦制品足够的机械强度,使其能承受摩擦片在生产过程中的磨削和铆接加工的负荷力以及使用过程中由于制动和传动而产生的冲击力、剪切力、压力。 填料: 增摩填料: 莫氏硬度通常为3~9。硬度高的增摩效果显著明显。5.5硬度以上的填料属硬质填料,但要控制其用量、粒度。(如氧化铝、锆英石等) 减磨填料: 一般为低硬度物质,低于莫氏硬度2的矿物。如:石墨、二硫化钼、滑石粉、云母等。它既能降低摩擦系数又能减少对偶材料的磨损,从而提高摩擦材料的使用寿命。 分类: 石棉摩擦材料分为以下几类: a 石棉纤维摩擦材料,又称为石棉绒质摩擦材料。生产:各种刹车片、离合器片、火车合成闸瓦、石棉绒质橡胶带等。 b 石棉线质摩擦材料。生产:缠绕型离合器片、短切石棉线段摩擦材料等。 c 石棉布质摩擦材料。生产:制造层压类钻机闸瓦、刹车带、离合器面片等。 d 石棉编织摩擦材料。生产:制造油浸或树脂浸刹车带。石油钻机闸瓦等。 分类: B 无石棉摩擦材料分为以下几类: a 半金属摩擦材料,应用于轿车和重型汽车的盘式刹车片。其材质配方组成中通常含有30%~50%左右的铁质金属物(如钢纤维、还原铁粉、泡沫铁粉)。半金属摩擦材料因此而得名。是最早取代石棉而发展起来的一种无石棉材料。其特点:耐热性好,单位面积吸收功率高,导热系数大,能适用于汽车在高速、重负荷运行时的制动工况要求。但其存在制动噪音大、边角脆裂等缺点。 b NAO摩擦材料。从广义上是指非石棉-非钢纤维型摩擦材料,但现盘式片也含有少量的钢纤维。NAO摩擦材料中的基材料在大多数情况下为两种或两种以上纤维(以无机纤维,并有少量有机纤维)混合物。因此NAO摩擦材料是非石棉混合纤维摩擦材料。通常刹车片
粉末冶金的烧结技术简易版
In Order To Simplify The Management Process And Improve The Management Efficiency, It Is Necessary To Make Effective Use Of Production Resources And Carry Out Production Activities. 编订:XXXXXXXX 20XX年XX月XX日 粉末冶金的烧结技术简易 版
粉末冶金的烧结技术简易版 温馨提示:本安全管理文件应用在平时合理组织的生产过程中,有效利用生产资源,经济合理地进行生产活动,以达到实现简化管理过程,提高管理效率,实现预期的生产目标。文档下载完成后可以直接编辑,请根据自己的需求进行套用。 1.烧结的方法 不同的产品、不同的性能烧结方法不一 样。 ⑴按原料组成不同分类。可以将烧结分为 单元系烧结、多元系固相烧结及多元系液相烧 结。 单元系烧结是纯金属(如难熔金属和纯铁 软磁材料)或化合物(Al2O3、B4C、BeO、MoSi2 等)熔点以下的温度进行固相烧结。多元系固相 烧结是由两种或两种以上的组元构成的烧结体
系,在其中低熔成分的熔点温度以下进行的固相烧结。粉末烧结合金多属于这一类。如Cu-Ni、Fe-Ni、Cu-Au、W-Mo、Ag-Au、Fe-Cu、W-Ni、Fe-C、Cu-C、Cu-W、Ag-W等。多元系液相烧结以超过系统中低熔成分熔点的温度进行的烧结。如W-Cu-Ni、W-Cu、WC-Co、TiC-Ni、Fe-Cu(Cu>10%、Fe-Ni-Al、Cu-Pb、Cu-Sn、Fe- Cu(Cu<10%)等 ⑵按进料方式不同分类。分为为连续烧结和间歇烧结。 连续烧结 烧结炉具有脱蜡、预烧、烧结、制冷各功能区段,烧结时烧结材料连续地或平稳、分段
烧结矿粉的液相流动性能探索毕业论文
烧结矿粉的液相流动性能探索毕业论文 目录 摘要.............................................. 错误!未定义书签。Abstract .............................................. 错误!未定义书签。引言.. (1) 1文献综述 (2) 1.1我国铁矿粉资源利用概况 (2) 1.2铁矿粉烧结工艺概述 (4) 1.3化学成分对烧结矿质量的影响 (6) 1.3.1含Fe品位的影响 (6) 1.3.2脉石成分的影响 (6) 1.4烧结基础特性 (8) 1.4.1同化性能 (9) 1.4.2液相流动性能 (9) 1.4.3粘结相强度 (10) 1.4.4铁酸钙生成性能 (12) 1.5液相流动性的测定与评价 (12) 2烧结矿粉的理化基础特性 (15) 2.1化学成分 (15) 2.1.1TFe和FeO含量 (15) 2.1.2脉石成分含量 (17) 2.2烧损 (25)
2.3小结 (27) 3液相流动性指数测定 (28) 3.1实验设备与方法 (28) 3.2实验结果与分析 (29) 3.3铁矿粉流动性能的影响因素 (31) 3.4优化配矿建议 (33) 4液相流动性能新探索 (34) 4.1实验设备与方法 (34) 4.2实验结果 (36) 4.3分析与讨论 (41) 4.3.1可熔铁矿粉流动性能探究 (41) 4.3.2未熔铁矿粉流动性能探究 (46) 4.3.3探索实验的优点和可靠性 (47) 5铁酸钙液相流动性能探索 (48) 5.1实验方法 (48) 5.2实验结果 (49) 5.3分析与讨论 (51) 5.3.1铁酸钙液相流动性能分析 (51) 5.3.2不同条件下流动性能的对比 (55) 结论 (57) 参考文献 (58) 附录A 外文原文 (61) 附录B 外文译文 (68) 致谢 (83)
关于摩擦材料
无石棉摩擦材料分为以下几类: a 半金属摩擦材料,应用于轿车和重型汽车的盘式刹车片。其材质配方组成中通常含有30%~50%左右的铁质金属物(如钢纤维、还原铁粉、泡沫铁粉)。半金属摩擦材料因此而得名。是最早取代石棉而发展起来的一种无石棉材料。其特点:耐热性好,单位面积吸收功率高,导热系数大,能适用于汽车在高速、重负荷运行时的制动工况要求。但其存在制动噪音大、边角脆裂等缺点。 b NAO摩擦材料。从广义上是指非石棉-非钢纤维型摩擦材料,但现盘式片也含有少量的钢纤维。NAO摩擦材料中的基材料在大多数情况下为两种或两种以上纤维(以无机纤维,并有少量有机纤维)混合物。因此NAO摩擦材料是非石棉混合纤维摩擦材料。通常刹车片为短切纤维型摩擦块,离合器片为连续纤维型摩擦片。 c 粉末冶金摩擦材料。又称烧结摩擦材料,系将铁基、铜基粉状物料经混合、压型,并在在高温下烧结而成。适用于较高温度下的制动与传动工况条件。如:飞机、载重汽车、重型工程机械的制动与传动。优点:使用寿命长;缺点:制品价格高,制动噪音大,重而脆性大,对偶磨损大。 d 碳纤维摩擦材料。系用碳纤维为增强材料制成的一类摩擦材料。碳纤维具有高模量、导热好、耐热等特点。碳纤维摩擦材料是各种类型摩擦材料中性能最好的一种。碳纤维摩擦片的单位面积吸收功率高及比重轻,特别适合生产飞机刹车片,国外有些高档轿车的刹车片也使用。因其价格昂贵,故其应用范围受到限制,产量较少。在碳纤维摩擦材料组分中,除了碳纤维外,还使用石墨,碳的化合物。组分中的有机粘结剂也要经过碳化处理,故碳纤维摩擦材料也称为碳——碳摩擦材料或碳基摩擦材料。 编辑本段5 摩擦材料的技术要求 5.1 适宜而稳定的摩擦系数 摩擦系数是评价任何一种摩擦材料的一个最重要的性能指标,关系着摩擦片执行传动和制动功能的好坏。它不是一个常数,而是受温度、压力、摩擦速度或表面状态及周围介质因素等影响而发生变化的一个数。理想的摩擦系数应具有理想的冷摩擦系数和可以控制的温度衰退。由于摩擦产生热量,增高了工作温度,导致了摩擦材料的摩擦系数发生变化。 温度是影响摩擦系数的重要因素。摩擦材料在摩擦过程中,由于温度的迅速升高,一般温度达200℃以上,摩擦系数开始下降。当温度达到树脂