钢管弯曲变形处理
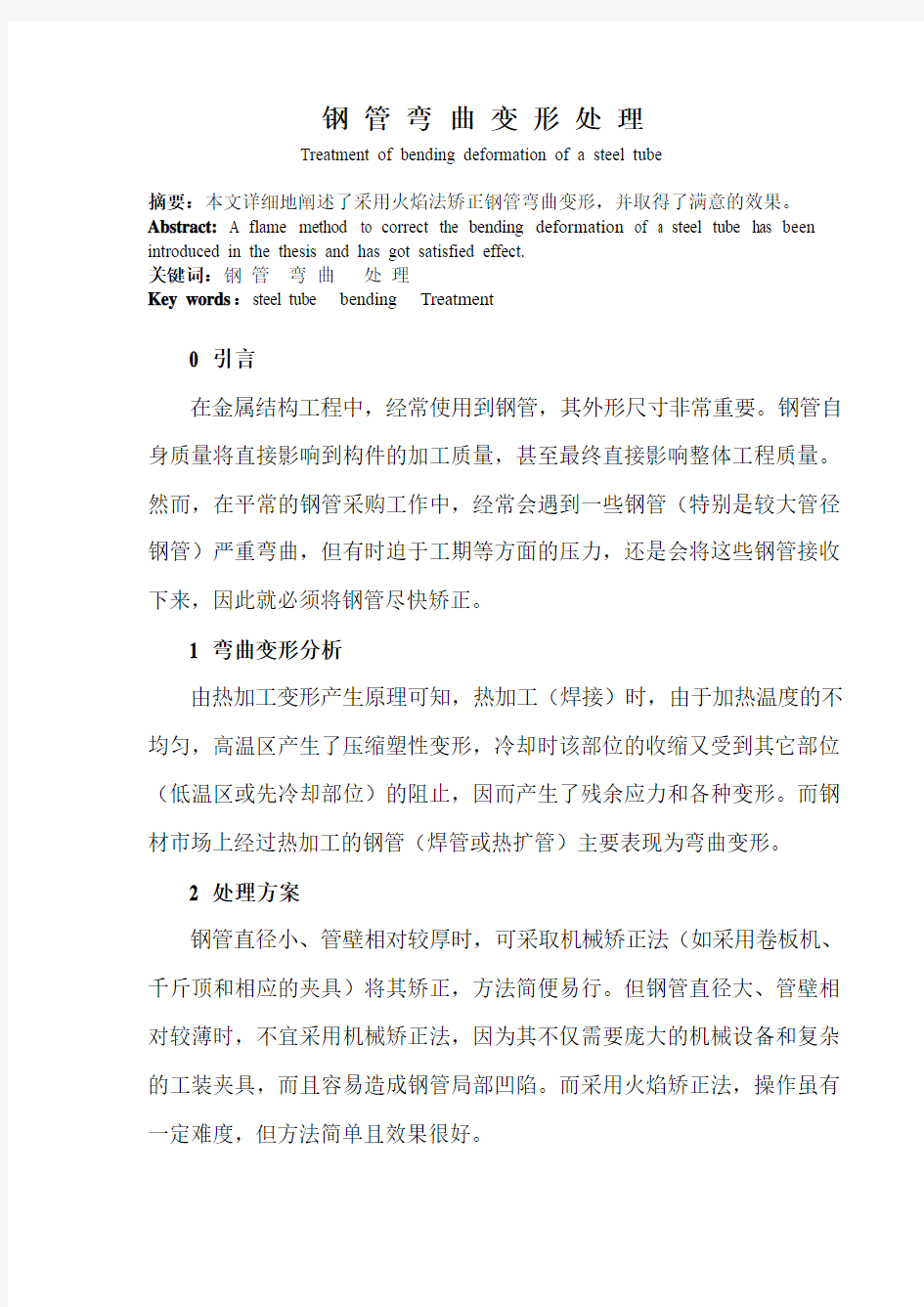
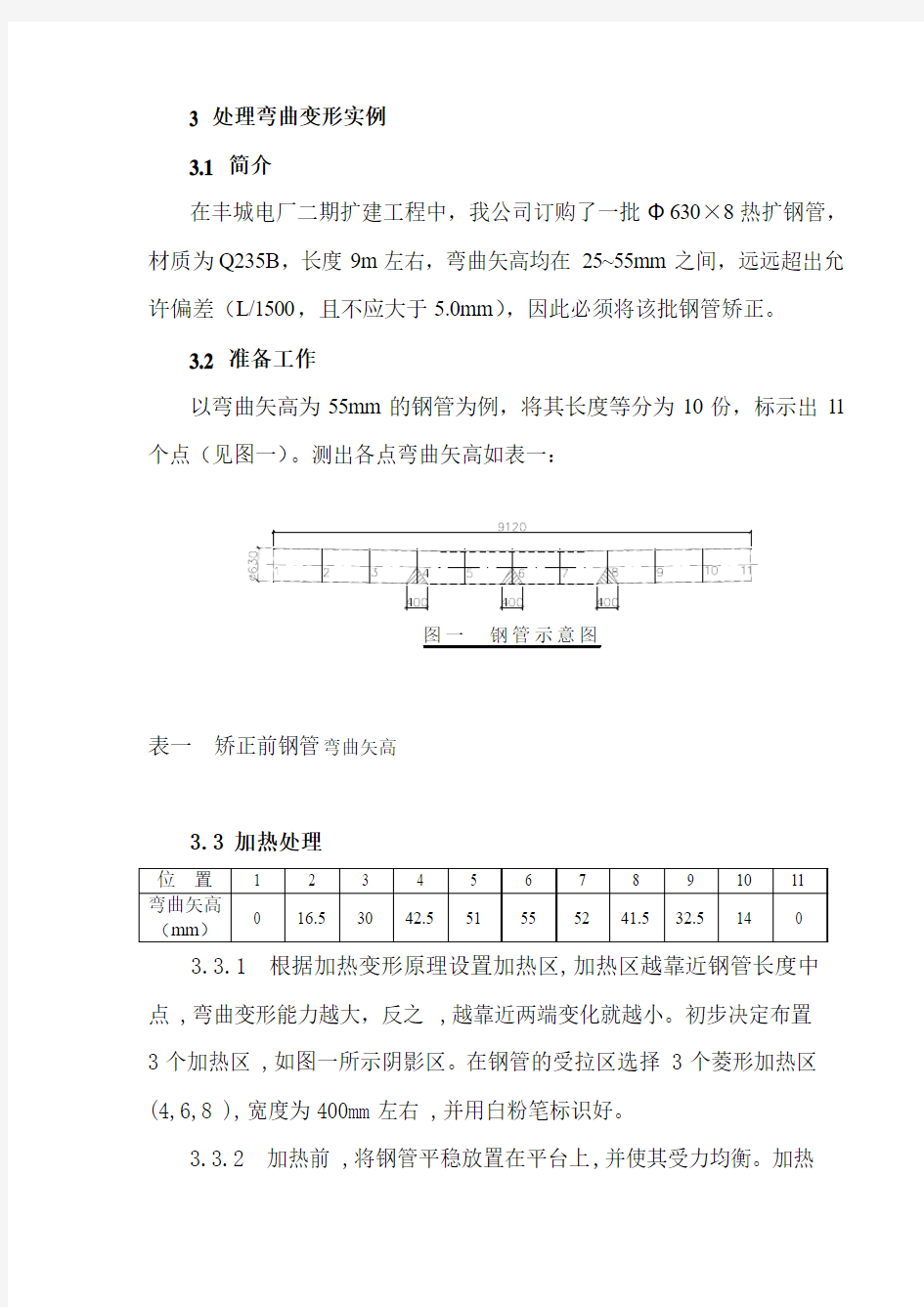
钢管弯曲变形处理
Treatment of bending deformation of a steel tube
摘要:本文详细地阐述了采用火焰法矫正钢管弯曲变形,并取得了满意的效果。Abstract: A flame method to correct the bending deformation of a steel tube has been introduced in the thesis and has got satisfied effect.
关键词:钢管弯曲处理
Key words:steel tube bending Treatment
0 引言
在金属结构工程中,经常使用到钢管,其外形尺寸非常重要。钢管自身质量将直接影响到构件的加工质量,甚至最终直接影响整体工程质量。然而,在平常的钢管采购工作中,经常会遇到一些钢管(特别是较大管径钢管)严重弯曲,但有时迫于工期等方面的压力,还是会将这些钢管接收下来,因此就必须将钢管尽快矫正。
1 弯曲变形分析
由热加工变形产生原理可知,热加工(焊接)时,由于加热温度的不均匀,高温区产生了压缩塑性变形,冷却时该部位的收缩又受到其它部位(低温区或先冷却部位)的阻止,因而产生了残余应力和各种变形。而钢材市场上经过热加工的钢管(焊管或热扩管)主要表现为弯曲变形。
2 处理方案
钢管直径小、管壁相对较厚时,可采取机械矫正法(如采用卷板机、千斤顶和相应的夹具)将其矫正,方法简便易行。但钢管直径大、管壁相对较薄时,不宜采用机械矫正法,因为其不仅需要庞大的机械设备和复杂的工装夹具,而且容易造成钢管局部凹陷。而采用火焰矫正法,操作虽有一定难度,但方法简单且效果很好。
3 处理弯曲变形实例
3.1 简介
在丰城电厂二期扩建工程中,我公司订购了一批Ф630×8热扩钢管,材质为Q235B,长度9m左右,弯曲矢高均在25~55mm之间,远远超出允许偏差(L/1500,且不应大于5.0mm),因此必须将该批钢管矫正。
3.2 准备工作
以弯曲矢高为55mm的钢管为例,将其长度等分为10份,标示出11个点(见图一)。测出各点弯曲矢高如表一:
图一 钢管示意图
表一矫正前钢管弯曲矢高
3.3 加热处理
3.3.1 根据加热变形原理设置加热区,加热区越靠近钢管长度中
点 ,弯曲变形能力越大,反之 ,越靠近两端变化就越小。初步决定布置
3个加热区 ,如图一所示阴影区。在钢管的受拉区选择 3个菱形加热区(4,6,8 ),宽度为400mm左右 ,并用白粉笔标识好。
3.3.2 加热前 ,将钢管平稳放置在平台上,并使其受力均衡。加热
时 ,2个人同时负责“6”加热区,在钢管的径向对称进行。然后每个人负责“4”或“8”加热区 ,由中心向两侧扩展 ,2人的焊枪移动速度、温度控制应保持一致。在加热过程中 ,严格控制加热温度在 70 0~ 80 0℃之间为宜。因为在这个温度区 ,金相组织基本不发生变化且具有塑性变形能力。在实践中 ,根据火焰的颜色判断温度 ,一般颜色为暗红色至暗樱桃红即可。
3.3.3 待3个加热部位冷却后,测量钢管弯曲变化情况。如变形数据与规范要求相差较小 ,可在两端再设置加热区 ,如相差较大 ,再加热 5和7。待其冷却以后 ,测量数据 ,直到满足要求为止。
3.4 效果检查
经过多次加热处理 ,钢管弯曲矢高已完全满足规范要求。 (见表一、表二 )。成功地解决了钢管弯曲变形问题 ,为下一步的钢构件加工质量奠定了坚实的基础。
表二矫正后钢管弯曲矢高
3.5 结论
矫正工作虽已取得圆满成功 ,但在以后类似的工作中 ,应注意以下几个问题 :(1)加热时 ,不要急于求成。每次加热完毕 ,待其冷却后 ,要测量其数据 ,并记录下来 ,分析钢管的变化情况 ,防止加热过头。(2 )避免在同一部位多次加热 ,以防止破坏材料的机械性能。(3)加热区不
能太宽 ,因为加热过宽时 ,会出现先加热的先冷却的结果 ,使热塑性压缩变形减少 ,矫正效果变差。
钢管弯曲成形专用设备 论文
摘要 全套图纸请加:229826208 本次设计题目是钢管弯曲成形专用设备设计,在设计过程中,要求我们运用机电液的知识完成,其设计的内容主要包括,液压缸的设计,液压控制系统设计,液压站的设计,液压滑台,电气系统设计等内容。 对专用机构中液压缸的设计主要是下滑台液压缸的设计,前后滑台液压缸,弯曲液压缸的设计。其中具体写了设计步骤以及对液压缸性能参数的计算,其中包括液压缸的输出力,液压缸的输出速度计算,计算液压缸的主要结构尺寸,选用标准参数以及计算其输出功率等。活塞杆直径的计算,液压缸行程的确定以及对液压缸结构强度计算与稳定性校核。 液压控制系统设计设计内容主要为明确设计要求,制定基本方案,绘制液压系统图,并且确定液压系统的主要参数,液压系统的主要参数包括载荷的组成和计算,计算液压缸的主要结构尺寸,对其它液压元件的选择具体以及专用件也给予慎重考虑。 液压站的设计主要是满足机床对液压系统的要求,液压站是一种标准化的液压传动装置,它是由油箱,液压泵装置和液压集成系统等三部分组成。 液压滑台机构总体设计包括对机构的其它部分设计和液压缸的安装及空间布局。 根据钢管弯曲成形的本道工序的生产要求,批量,工艺特性,还需进行夹具的设计,由于工件简单,夹紧较方便,故采用手动装置,采用双V形的夹紧方式,采用左右旋螺纹进行夹紧和松开,以便提高生产效率。 电气系统的设计就是运用机电传动的知识,即PLC系统进行控制,PLC控制系统有西门子系统,欧姆龙系统等。 关键词:钢管,液压缸,液压滑台,液压站,弯曲成形,机电液
Abstract This design topic is the steel pipe curving forming special purpose equipment design , in the design process , requests our utilization machine battery solution the knowledge to complete , its design content mainly includes , the hydraulic cylinder design , the hydraulic control system design , the hydraulic pressure stands design , hydraulic pressure sliding table , content and so on electrical system design. To the special-purpose organization in the hydraulic cylinder design mainly is under the sliding table hydraulic cylinder design, around sliding table hydraulic cylinder, curving hydraulic cylinder design,has written the design procedure as well as to the hydraulic cylinder performance parameter computation specifically, including the hydraulic cylinder output strength, the hydraulic cylinder output speed computation, calculates the hydraulic cylinder the main structure size, selects the standard parameter as well as calculate sits output and so on. Connecting rod diameter computation, hydraulic cylinder stroke determination as well as to hydraulic cylinder structural strength computation and stable examination. The hydraulic control system design content mainly for is clear about the design request, formulation basic plan, plan hydraulic scheme, and the determination hydraulic system main parameter, the hydraulic system main parameter including the load composition and the computation, calculates the hydraulic cylinder the main structure size, is concrete as well as special-purpose to other hydraulic pressure parts choices also gives careful consideration. The hydraulic pressure stands the design mainly is satisfies the engine bed to the hydraulic system request, the hydraulic pressure station is one kind of standardized hydraulic gear, it is by the fuel tank, the hydraulic pump installment and the hydraulic pressure integrative system and so on three parts is composed. Hydraulic pressure sliding table organization system design including to organization other parts of designs and hydraulic cylinder installment and spatial layout. According to steel pipe curving forming this working procedure production request, batch, craft characteristic, but also must carry on the jig the design, because the work piece is simple, clamps conveniently, therefore uses the hand gear, uses a pair of V shape to clamp the way about, uses turns on lathe the thread to carry on clamps with the pine opens, in order to enhancement
薄壁钢管弯曲模具设计
薄壁钢管弯曲模具设计(图) 弯管在制冷、机械、化工等行业中的应用十分广泛,薄壁钢管弯管的批量生产,一般是在弯管机上冷弯成形,由于薄壁钢管管壁支撑失稳临界力较低,弯曲部位常出现瘪皱等变形缺陷。这些缺陷不但削弱钢管的强度,降低其承载能力,而且容易造成管内流动介质速度不均、产生涡流和弯曲部位积聚污垢等,影响弯管的正常使用,因此消除弯管缺陷成了弯管过程中最大难点,必须高度重视。 一、薄壁钢管弯曲受力与变形分析 薄壁钢管弯曲时,管子在外力作用下弯曲变形,其弯曲部分的外缘在拉应力作用下管壁变薄,而管子内缘在压应力作用下管壁增厚。由于在管子弯曲过程中,外缘拉应力和内缘压应力的合力都向中部作用,导致管子弯曲部位在水平面上的直径变大,垂直面上的直径减小,出现椭圆形。同时,如果弯曲模具弧槽参数选择不当,不能起到强化弯曲部位管壁的作用,则管子内缘在压应力作用下,因管壁失稳临界力较低而产生波浪形皱褶。由以上分析可知:薄壁钢管弯曲时极易产生瘪皱缺陷。因此设计薄壁钢管弯曲模具时,必须合理确定其结构参数,以便钢管弯曲时,在模具作用下使管子产生一预加反应力,以抵消薄壁钢管弯曲时产生的椭圆变形,对弯曲部位的瘪皱缺陷进行合理控制。 二、薄壁钢管弯曲模具设计 简易薄壁钢管弯管机的结构如图1所示,弯管模具如图2所示,由弯管模块、滚动压轮和导轮组成。滚动压轮和导轮安装于滚轮座中,并可在转盘的滑槽中上下移动。弯管时,扳动手柄带动转盘绕轴转动,由导轮向管子施加压力,使其发生弯曲变形。同时滚动压轮在钢管弯曲部位施加一定压力,通过轮上弧槽使之产生一反向预压力,以抵消钢管弯曲时产生的椭圆变形,使管子内缘与弯管模块弧槽紧密贴合,以强化弯曲部位管壁,消除内壁皱褶。 1.弯曲模块 钢管弯曲后的半径和形状取决于弯管模块,因此,必须合理确定其结构参数,弯管模块如图3所示:
弯管一般知识及计算下料方法
第一章煨管设备及弯管计算弯管按其制作方法不同,可分为煨制弯管、冲压弯管和焊接弯管。煨制弯管又分为冷煨和热煨两种。本章着重介绍常用煨管设备的结构特点、性能及操作等方面的知识,以及煨制弯管的下料计算。 第一节弯管的一般知识 弯管是改变管道方向的管件。在管子交叉、转弯、绕梁等处,都可以看到弯管。 煨制弯管具有较好的伸缩性、耐压高、阻力小等优点。因此,在施工中常被采用。 弯管的主要形式有:各种角度的弯头、U形管、来回弯(或称乙字弯)和弧形弯管等,如图1—1所示。 弯头是带有一个任意弯曲角的管件,它被用在管子的转弯处。弯头的弯曲半径用R表示。R较大时,管子的弯曲部分就较大,弯管就比较平滑;R较小时,管子的弯曲部分就较小,弯得就较急。 来回弯是带有两个弯曲角(一般为135°)的管件。来回弯管子弯曲端中心线间的距离叫做来回弯的高度,用字母h表示。室内采暖立支管与干管及散热器连接,管道与不在同一平面上的接点连接时,一般需采用来回弯。 U形管是成正半圆形的管件。管子的两端中心线问的距离d等于两倍弯曲半径R。U形管可代替两个90°弯头,经常用来连接上下配置的两个圆翼形散热器。 图1-1弯管的主要形式 弧形弯管是带有三个弯曲角的管件。中间角一般成90°,侧角成135°。弧形弯管用于绕过其它管子,在有冷热水供应的卫生设备配管时,经常采用弧形弯管。 弯管尺寸由管径、弯曲角度和弯曲半径三者确定。弯曲角度根据图纸和施工现场实际情况确定,然后制出样板,照样板煨制并按样板检查煨制管件弯曲角度是否符合要求。样板可用圆钢煨制,圆钢的直径根据所煨管径的大小选用,10-14mm即可。弯管的弯曲半径应按管径大小、设计要求及有关规定而定。既不能过大,也末虚选得太小。因为弯曲半径过大,不但用材料多,而且管子弯曲部分所占的地方也大,这样会给管道装配带来困难;弯曲半径选
管子弯曲
管子弯曲 管子弯曲原理 弯曲时管子截面的变化 金属材料当其所受外力超过材料的屈服极限时,将产生永久的塑性变形,这就是管子弯曲的基本原理。 管子在弯曲时,其管壁外侧因受拉伸而变薄,内侧因受压缩而变厚,但其中性层M -M处不受压力,因此其长度和厚度都不改变。由于拉伸和压缩作用的结果,在弯曲过程中,管子截面有所改变,有由圆形变成椭圆的趋势。此时椭圆的短轴位于管子的弯曲平面B - B 上,而长轴在A -A上(如图)。这种变形随着弯曲半径、弯曲角度与管子材料、管径大小的不同而有所不同。 弯曲角的影响 (1)弯曲角度对变形的影响 管子外层金属组织的伸长和内层组织的缩短,在弯曲角大的时候很大,而在弯曲角小的时候就很小,如右图所示。 (2)管子的直径大小对变形的影响 管径对变形大小的影响 在管径小的最外层组织距离中性层近,而在管径大的最外层组织距离中性层远,如左图所示。因此弯曲相同角度,管径愈大变形程度愈大。 弯曲断面变形焊缝应放在管径的四分之一处
弯曲断面处没有改变位置的零点 在管子弯曲时,断面的变形是由弯曲的一瞬间产生的。管子弯曲处断面的变形会通讨横断面上的许多零点,也就是在弯曲过程中没有改变位置的a,b,c,d各点,如4.5所示。显然,这些点的应力最小,通过管子各横断面上相应点的连线就是管子的安全线,因此,在弯制有缝钢管时,应把焊缝放在安全线上,它约在平面图上管径的1/4处,如右图所示。 管子弯曲的技术要求 弯管时允许的圆度百分率 确定管子弯曲质量的主要技术特征是椭圆度、截面收缩率、外侧减薄率、内侧增厚折皱以及弯曲形状和表面质量等。管子弯曲质量同采用的弯制工艺、管子材料和尺寸参数以及弯曲半径等有关。 (1)管子弯曲半径一般采用2~3倍管子外径,只有在个别情况下才允许小于2倍,但不得小于1.5倍。 (2)外径大于120mm的碳素钢蒸汽管和任何直径的合金钢管,冷弯后应进行不低于600℃的高温退火,保温不少于40min,退火后先在炉中冷却,温度降至500℃以下时,可在空气中冷却。 (3)弯曲后的弯曲角。和旋转角ψ的公差均为±0.5o,管段长度L的公差为±7mm。 (4)管子弯曲以后的变形有如下要求。 ①管子弯曲时,受弯曲力的作用,使其截面变为椭圆。这样就增大了流体的压头损失,因此其圆度符合表4.1的规定。 弯管方法 管子的弯管方法主要分为冷弯和热弯两种,冷弯是在常温下用弯管机直接弯管,热弯则是将管子的弯曲部分加热到一定温度后,再用机械(弯管机)或手工进行弯管。两种方法各有其优缺点。 冷弯不会破坏金属原来的性质,不会产生热变形。但是冷弯需要消耗更多的弯管功率,且回弹和残余应力都有较明显的增大,而且冷弯不能弯制曲率半径很小的急转弯头。 热弯则具有冷弯不能比拟的适应性。例如,在一根管子上两相邻弯头之间直线距离
(整理)高强度钢管新弯曲方法“PRB”的发展
高强度钢管新弯曲方法“PRB”的发展 O.Sonobe1,Hashimoto1,K.Suzuki1,A. Sato1 Y.Ueno2 M.Okada3 1 钢材研究实验室。日本JFE钢铁公司 2 Chassis产品化,丰田汽车公司,日本 3 TAIYO公司,日本 摘要:JFE钢铁工程控股公司,丰田发动机公司和太阳公司为薄壁高强度钢管研究出了一种新方法(PRB:通过压紧模推挤和压弯模回转使直径微缩的方法)。我们采用高强度电阻焊钢管的弯曲试验和有限元模拟来研究PRB的弯曲性能。在PRB方法中,通过沿周向施加压应力来使钢管弯曲,这就能够使小直径或者多重直径的高强度钢管和(或)薄壁钢管弯曲,而不使用传统旋转拉弯方法中必需的心轴或脱模钳。传统旋转式拉弯方法中心轴和脱模钳需要很长的调整时间并且最终会磨损,这种新方法取消了心轴和脱模钳,能够高效的弯曲薄壁高强度钢管,并且它能弯曲不规则形状的钢管,如两端带有突沿的钢管。PRB的应用能生产出采用590MPa级电阻焊钢管的纵臂和采用780MPa级电阻焊钢管的下臂。 关键词:新弯曲法、心轴、脱模钳、效率、传统弯曲、PRB。 1.引言 最近,在汽车结构零件制造领域减轻质量和增加强度越来越重要,能同时满足两个要求的一种方法是把电阻焊钢管用于封闭截面的汽车零件 [1][2]。当采用高强度钢管制造汽车零件,如副车架,下臂等时,钢管液压成形或其他成形之前通常需要弯曲操作,因此改善材料的可成型性和弯曲过程的生产效率是十分重要的[3]。 JFE钢铁工程控股公司,丰田发动机公司和太阳公司为薄壁高强度钢管研究出了一种新方法。 在PRB方法中,通过沿周向施加压应力来使钢管弯曲,这就能够使小直径或者多重直径的高强度钢管和(或)薄壁钢管弯曲,而不使用传统旋转拉弯方法必需的心轴或脱模钳。因为PRB
弯管标准化
弯管标准化 一:模具设计选型简介 1.一管一模 2.对于一根管子来说,无论有几个弯,不管弯曲角度如何(不应大于180°),其弯曲半径最好 统一。既然一管一模,那么,对于不同直径规格的管子,应该选取多大的弯曲半径才适宜呢?最小弯曲半径取决于材料特性、弯曲角度、弯曲后的管壁外侧的变薄允许量和内侧起皱的大小、以及弯曲处的椭圆度的大小。一般说来,最小弯曲半径不应小于管子外径的2—2.5倍,最短直线段不应小于管子外径的1.5—2倍,特殊情况除外。 3.一管二模(复合模或多层模) 对于不能实现一管一模的情况,譬如客户的装配界面空间狭小,管路走向布局有限,导致一管多半径或直线段较短的情况出现,这时,在设计弯管模时,考虑双层模或多层模(目前我司的弯管设备最多支持3层模的设计),甚至是多层复合模。 双层或多层模:一管出现双半径或者三半径的情况,如下实例: 双层或多层复合模:直线段短,不利于夹持的情况,如下实例:
4.多管一模 5.我司所用的多管一模,就是同一直径规格的管子应尽量采用同一种弯曲半径。也就是使用同 一套模具弯制不同形状的管件。这样,才能有利于最大限度地压缩专用工艺设备,减少弯模的制造量,从而降低生产成本。 6.在一般情况下,同一直径规格的管子只采用一种弯曲半径不一定能够满足实际位置的装配需 要。因此,相同直径规格的管子可以选取2—4种弯曲半径,以适应实际的需要。如果弯曲半径取2D(这里D为管子外径),那么2D、2.5D、3D、4D即可。当然,这种弯曲半径的比例不是固定不变的,应按发动机空间布局的实际情况选定,但是半径不宜选取过大。而弯曲半径的规格也不宜过多,否则会失去多管一模所带来的利益。 7.一根管子上采用同一个弯曲半径(即一管一模)和同规格管子的弯曲半径标准化(多管一模), 这是当前国外弯管设计造型的特点和总的趋势,是机械化和自动化代替手工劳动的必然结果,也是设计适应先进的加工工艺和先进的加工工艺促进设计的两者的结合。 二:弯管椭圆度计算 弯管机在进行工作运行时,在内压应力作用下,(内压应力状态参考配管力学)将使圆形的横截面趋于椭圆,产生短轴及长轴。在长轴处产生附加应力,此应力属于局部应力。椭圆度愈大,此附加应力也愈大,甚至形成高应力区,出现局部塑性变形,达到一定值后,将导致弯管承载能力减低而破坏。 所以,目前在技术规范中对弯管的椭圆度都有严格的规定。规定如下: 本规范适用于弯管工段,用于指导弯管工艺检验弯管质量
管材弯曲半径及配对管夹型号
Q/SDY0306-2012 2012-10-25 发布 2012-11-01实施 1 管材弯曲及管夹选用 1 范围 1.1 本标准规定了公司管材弯曲半径、管夹型号及管材弯曲制作要求。 1.2 本标准适用于公司技术人员对弯管半径及管夹型号的选取及弯管人员对弯管的制作规定。 2 尺寸参数与管夹选型 尺寸参数见图1、表1 图 1 表 1 公称直径 管线外径D 0 mm 弯曲半径R mm 管夹型号 小半径 大半径 DN4 6.35(英制) 20 — SP106,4PP-DP-AS 6 20 — SP106PP-DP-AS DN6 10 30 — SP110PP-DP-AS DN8 9.53(英制) 30 — SP109,5PP-DP-AS 10 30 — SP110PP-DP-AS DN10 17.1(英制) 45 — SP217,2PP-DP-AS 14 45 — SP214PP-DP-AS DN15 21.3(英制) 55 — SP321,3PP-DP-AS 18 45 — SP218PP-DP-AS DN20 26.7(英制) 70 — SP426,9PP-DP-AS 25 65 — SP325PP-DP-AS — 28 70 — SP328PP-DP-AS DN25 33.4(英制) 85 — SP533,7PP-DP-AS 32 80 — SP532PP-DP-AS DN32 38 100 — SP538PP-DP-AS DN38 42 110 — SP542PP-DP-AS 张家港中集圣达因低温装备有限公司企业标准
Q/SDY0306-2012 2 表 1 公称直径 管线外径D 0 mm 弯曲半径R mm 管夹型号 小半径 大半径 DN40 48.3(英制) 120 — SP648,3PP-DP-AS 45 115 — SP644,5PP-DP-AS DN50 60.3(英制) 150 — SP760,3PP-DP-AS 57 125 145 SP757,2PP-DP-AS DN65 73.0(英制) 150 — SP773PP-DP-AS 76 150 190 SP776,1PP-DP-AS DN80 88.9(英制) 250 — SP888,9 PP-DP-AS 89 250 — SP889 PP-DP-AS DN100 114.3(英制) 300 — SP6114,3 PP-DP-AS 108 300 — SP6108 PP-DP-AS DN150 168.3(英制) 350 — SP7168,3 PP-DP-AS 159 350 — SP7159 PP-DP-AS DN200 217.3(英制) 500 — SP9219 PP-DP-AS 219 500 — SP9273,1 PP-DP-AS 3 制作要求 管件的弯曲一般应在弯管机上进行冷弯,制弯模具及辅助工具工作面应光滑、无铁屑油污。具体弯制方法和要求按Q/SDYGC604-2006 《管型材弯制工艺守则》的规定。 附加说明: 本标准由技术中心提出并起草,2009年5月首次发布,2012年10月第一次修改。 编制:姜艾荣、钱红华、高洁、吴小芳 审核:邱国洪 批准:王淑华 (续)
大口径钢管的弯曲成型工艺的研究及应用
大口径钢管的弯曲成型工艺的研究及应用 摘要:结合沈阳奥林匹克体育中心体育场罩棚钢结构工程大口径钢管的弯曲加工技术,对大口径钢管几种不同的弯曲加工技术进行了总结,并对其各自的优缺点进行了对比分析。 关键词:大口径钢管中频弯管钢管冷弯成型质量控制 一.工程概况 沈阳奥林匹克体育中心体育场为一座可容纳六万人的大型体育场,是2008年北京奥运会的主要分赛场之一。其南北看台顶部设置了一对平行投影为梭形的空间钢网壳罩棚结构,在东西两端采用平行弦桁架将南北网壳进行局部连接,该罩棚几何外形可以认为取自一直径约为433米的球体,空间形体近似为一块两端点着地且倾斜放置的西瓜皮,两着地点间水平距离360m,正中最宽处水平投影尺寸111m,最高点距地约82m,钢结构总重量约1.2万吨,总建筑面积1.4万多平方米。 该罩棚主体结构形式为大跨度拱桁架结合单层(管)网壳的结构体系,根据结构构件的功能,其主体结构相应可分为主拱、环拱及南北联系桁架三部分,其中主拱为倒三角形拱桁架,跨度达360mm,为国内类似结构工程中最大跨度;环拱是由28榀弧形钢管及三道纵向系杆组成的单层网壳结构;南北联系桁架为平面管桁架。东西两面分别由主拱和环拱组成的罩棚结构通过南北两面联系桁架联系在一起,形成完整的结构体系。
二. 大口径钢管的弯曲成型 1. 大口径钢管的弯曲成型加工工艺的选定 本工程的结构造型近似为球面的一部分,大部分杆件为弧形,同时这些杆件又均为大口径钢管,因此,大口径钢管弯曲成型的质量和效率是保证本工程整体质量及工期的重要前提。 2).中频弯管适用范围 中频弯管受设备的转臂范围及进料宽度的限制,根据本中频弯管机的相关参数,限定其适用的弯曲范围为曲率半径在R4.6m~R20m之间的大口径钢管。 3).中频弯管工艺特点 (1).中频弯管是利用中频弯管机的加热圈套在钢管上对其加热,加热带是很窄的一圈,约为40mm左右,加热温度控制在800~850℃。 (2).钢管进行弯曲时,利用钢管自身两端冷却的部分作为支撑,使弯曲在加热带较窄小的宽度里进行,从而达到钢管弯曲成型后圆度不变或变形很小的效果。(3).弯曲成型的最小半径是被弯曲钢管外径的5倍。 (4).钢管最佳成型内R应在中频弯管机的转臂范围内,并需一次成型,成型后表面比较光滑,但当一根钢管有两种或两种以上的弯曲R时,要保证整体形状,达到图纸要求是比较困难的;对于内R在中频弯管机的转臂范围外的钢管,只能以直代曲,间隔弯曲,会导致在加热弯管处与冷却平直处有较明显的凹凸伤痕,一般在6mm左右。 (5).当弯曲后的钢管总拱高超过弯管机的进料宽度时,若发现超差就很难重弯;如果必须重弯,也只能是间断补偿。 (6).另外由于钢管需进行反复加热,其材性在高温之下将受到影响,尤其是对高强度材质的钢管影响会更大。 (7).钢管热弯后有三种冷却方法,即水冷、风冷及自然冷却,现时一般采用风冷或自然冷却。 4).中频弯管前的准备 (1).验证待弯钢管的钢印标记等内容应符合图样要求,钢管两段预留弯管加工所需的余量(具体可根据试验确定)。 (2).对待弯曲钢管的表面污物清理干净后进行宏观检查,有重皮、表面裂纹、划痕、凹坑及表面腐蚀严重的钢管部位应进行修磨。
钢管成型理论及工艺
第三章 钢管成形理论及工艺 1.管材穿孔为什么一般采用斜轧?试述斜轧穿孔过程中穿孔机调整参数对“孔腔”形成的 影响。 穿孔的变形过程主要取决于工具的形状及位置,因此调整穿孔机工具的相对位置对实现 顺利穿孔,提高穿孔质量是至关重要的。二辊斜轧穿孔机调整的主要参数有: 1)轧制中心线:即穿孔机顶杆的中心线。它也是管坯到毛管的中心线的运动轨迹。 2) 轧机中心线:即穿孔机本身的中心线。一般说来为了使穿孔过程比较稳定,安装 设备时使轧制线比轧机中心线低3~6mm。 3) 前-后台中心线:常以管坯受料槽与轧制线的相对高度衡量,原则上以受料槽中 的管坯中心线略低于轧制线为宜。 调整三条线的目的就是使三条线处于一个合适的位置或三线对中,使轧辊、导板(导盘)、 顶头在轧制中处于正确的空间关系,以获得合理的变形区。 4) 辊间距 B:指两轧辊辗轧带之间的间距。间距的大小必须保证管坯有足够的顶前 压下量;同时应保证轧辊相对于轧制线对称。 5)导板距 L:指两导板过渡带之间的距离。调整导板距主要依据椭圆度的大小ξ=L / B,一般ξ≈1.01~1.15。同时还要调整导板在轧制线方向上的位置,原则上要保证管坯接 触轧辊经约两个螺距后再接触导板;同时要保证毛管最后离开轧辊。 6) 顶前压下率:它指坯料在碰到顶头之前其径向的压下程度。顶前压下量过大则坯料 穿孔前容易出现孔腔,影响穿孔质量;过小则坯料中心不能形成有利于穿孔的“疏松”状态, 造成顶头阻力过大而“轧卡”。 7) 顶头位置 C:因为实测顶头位置较困难,常用顶杆位置Y表示。C指顶头鼻部伸 出辗轧带的距离,其大小直接影响穿孔能否进行及穿后毛管的质量。C过大则不利于咬入, 顶头阻力大,易轧卡;C过小则坯料中心容易出现“孔腔”,影响毛管的质量。 8) 轧辊倾角α和轧辊转速:轧辊倾角是斜轧穿孔中最积极的工艺参数。适当增加α弊 少利多,α增加可提高穿孔效率和改善毛管质量,不利是穿孔负荷增加。轧辊转速会影响穿 孔速度。 穿孔机调整的目的就是保证能在穿孔时轧机顺利地咬入管坯和抛出毛管,并获得一定尺 寸精度和内外表面质量,为此需要对三条线、四个主要参数(顶前压下率除外)进行调整, 原则上应使管坯能按时顺利通过变形区内各点各段,完成变形的全过程。 2.穿孔过程中钢管是如何运动的,为什么? 斜轧穿孔过程中存在着两种变形:基本变形和附加变形。 基本变形也称有用变形,是几何尺寸的变形关系,与轧件本身的性质无关,仅仅取决于 变形区的几何形状。穿孔过程中基本变形就是延伸变形、切向变形和径向变形(壁厚压缩)。 根据体积不变定律可知,壁厚压缩的金属流向纵向(延伸)和切向,由于切向变形受到孔型 的限制,因此,纵向(延伸)变形是主要的。 附加变形指的是轧件内部的变形,也称无用变形,是由于轧件变形不均匀引起的,它对 基本变形没有益处,只能增大轧件的变形应力,引起毛管中产生缺陷的几率增大。 3.钢管纵轧变形过程中包括哪几部分变形,容易出现的缺陷及解决办法是什么? 在轧辊、导板、顶头构成的变形区中有八个特征点,分别是: ①管坯与轧辊接触点; ⑤管坯进入顶头辗轧带; ②管坯与导板接触点; ⑥毛管离开导板或顶头;
冷弯管弯制工法
冷弯管弯制工法
一、工法特点 1、能够很好的控制冷弯管管口、弯曲段的椭圆度,平面度,直焊缝高度。 2、能够对母材管口,外防腐层和内减阻涂层起到很好的保护。 二、适用范围 本工法适用于管径φ400mm-φ1066mm范围内,管壁厚7.1-26.2毫米之间,曲率半径≥40D,X50-X70材质的钢管。 三、工艺原理 1、屈服原理:通过在钢管预定的地方(钢管的内、外部)施加一定的作用力,使之发生塑性变形,达到一定的弯曲角度的施工原理。 2、曲率半径:冷弯管就是通过若干次微分塑性变形,达到圆弧状所形成的。进给量为300毫米,曲率半径大于或等于40D。 四、工艺流程 弯管工艺流程图 中心标示 钢管就位找正焊缝位置进管胎芯进入管内 吊车吊起管端调整胎芯位确定起弯点启动绞车 弯制准备阶段 涨紧胎芯 起升刚性 基座至水平 伸出楔块油 缸托住钢管 起升主油缸 至一定高度 缩回 主油缸 缩回楔 块油缸 启动绞车 进给300mm 缩回 胎芯 胎芯退 回600mm 达到弯制角度 偶数次 奇数次 弯制阶段 奇数次
五、工法要点 (一) 施工准备 1、施工场地选择 施工场地宽阔平整,有足够的工作面积,且要求布局合理。在工作区内不允许有高压线等不适合吊装作业的障碍物,作业地面要求平整、坚硬,适合运输设备的进入和装卸。 2、管堆的制作 根据冷弯管的堆放规则,弯管应堆放在管堆上,管堆用不损害钢管材质和防腐层的材料堆砌而成。不允许放置在石头、砖瓦等硬性物体上。管堆的高度应保证弯管离开地面200mm 以上,且弯管只能进行单层堆放。 3、设备的就位 为严格执行施工规范,弯管机必须水平放置,且具有可调性。在设备下方垫一层碎石,既可以强化地基,还可以调整设备的平整度,然后组装、调试好设备,在弯管施工 启动绞 车出管 胎芯相对 于钢管后退 吊车大钩跟 随钢管前进 胎芯退 出弯管 吊至 堆管场 放下 大钩 检漏 测量 标示 作技 术资料 上报 存档 弯制结束阶段
弯管技术规范
弯管技术规范 1) 根据管道材质和管径的不同,弯管制作有冷弯和热弯之分。 2) 弯管宜采用壁厚为正公差的管道制作。 3) 有缝钢管制作弯管时,焊缝应避开受拉(压)区。 4) 弯制钢管,弯曲半径应符合下列规定: 热弯:应不小于管道外径的3.5倍; 冷弯:应不小于管道外径的4倍; 焊接弯头:应不小于管道外径的1.5倍; 冲压弯头:应不小于管道外径。 5) 钢管应在其材料特性允许范围内冷弯或热弯。 6) 加热制作弯管时,铜管加热温度范围为500~600℃;铜合金管加热温度范围为600~700℃。 7) 弯管质量应符合下列规定: a 不得有裂纹(目测或依据设计文件规定); b 不得存在过烧、分层等缺陷; c 不宜有皱纹; d 测量弯管任一截面上的最大外径与最小外径差,应符合表4.2.3.2-3规定; e 各类金属管道的弯管,管端中心偏差值△不得超过3mm/m,当直管长度L大于3m时,其偏差不得超过10mm。 8) П形弯管的平面度允许偏差△应符合表4.2.3.2-4规定。 9) 钢塑复合管管径不大于50mm时可用弯管机冷弯,但其弯曲半径不得小于8倍管 表4.2.3.2-3 弯管最大外径与最小外径之差 管子类别最大外径与最小外径之差 钢管为制作弯管前管道外径的8% 铜管为制作弯管前管道外径的9% 铜合金管为制作弯管前管道外径的8% 表4.2.3.2-4 П形弯管的平面度允许偏差△(mm)长度L <500 500—1000 >1000—1500 >1500 平面度△≤3 ≤4≤6 ≤10
径,弯曲角度不得大于10°。 10) 管道转弯处宜采用管件连接。DN≤32的管材,当采用直管材折曲转弯时,其弯曲半径不应小于12 DN,且在弯曲时应套有相应口径的弹簧管。管道弯曲部位不得有凹陷和起皱现象。 11) 铝塑复合管直接弯曲时,公称外径De不大于25mm的管道可采用在管内放置专用弹簧弯曲;公称外径De为32mm的管道宜采用专用弯管器弯管。 12) 铜管弯管:铜及铜合金管煨弯时尽量不用热煨,因热煨后管内填充物(如河砂、松香等)不宜清除。一般管径在l00mm以下者采用弯管机冷弯;管径在100mm以上者采用压制弯头或焊接弯头。铜弯管的直边长度不应小于管径,且不少于30mm。 a 热煨弯(一般用于黄铜管) a) 先将管内充人无杂质的干细沙,并用木锤敲实,然后用木塞堵住两端口,再在管壁上画出加热长度的记号,应使弯管的直边长度不小于其管径,且不小于30mm。 b) 用木碳对管身的加热段进行加热,如采用焦炭加热,应在关闭炭炉吹风机的条件下进行,并不断转动管道,使加热均匀。 c) 当加热至400~500℃时,迅速取出管道放在胎具上弯制,在弯制过程中不得在管身上浇水冷却。 d) 热煨弯后,管内不易清除的河沙可用浓度15%~20%的氢氟酸在管内存留3h使其溶蚀,再用10%~15%的碱中和,以干净的热水冲洗,再在120~150℃温度下经3~4h烘干。
管材最小弯曲半径
d k 无缝钢管不锈钢管 不锈无缝钢管焊接钢管d K 壁厚R d K 壁厚R d K 壁厚R d K 壁厚 R l 最小热冷68101214141618182022 253232383844.54557 57 76 89102108133159159194219245273325371111.51.51.531.51.531.53333.533.533.53.5444 444.566668810 1515202530183040284050506060807010090110150180220270340450420500500600700800900 1418(22)2532384557(76)89102(108)133139 22222.52.52.52.53.54444 18285050607090110225250360400450 681012141618202225323841577689102108133159194219111.51.51.51.51.51.51.533334446661012 151520253030404060608080100180220270340420600800900 13.51721.2526.7533.542.25486075.588.5114125150 41″83″21″43″1″141″121″2″221″3″4″5″6″ 2.752.75 3.253.253.53.53.7544 40506580100130150180225265340400500 80100130160200250290360450530680 404550557085100120150170230 中国第一重型机械集团公司标准 管材最小弯曲半径 CFHI SD 圆圆猿原2008代替YZB 223-89 中国第一重型机械集团公司2008-12-01批准 2008-12-31实施mm 1 1 返回总目录 返回分目录 后退后退 返回分目录返回总目录
管折弯含弯管的一般知识(优质参考)
第一节弯管的一般知识 弯管是改变管道方向的管件。在管子交叉、转弯、绕梁等处,都可以看到弯管。 煨制弯管具有较好的伸缩性、耐压高、阻力小等优点。因此,在施工中常被采用。 弯管的主要形式有:各种角度的弯头、U形管、来回弯(或称乙字弯)和弧形弯管等,如图1—1所示。 弯头是带有一个任意弯曲角的管件,它被用在管子的转弯处。弯头的弯曲半径用R表示。R较大时,管子的弯曲部分就较大,弯管就比较平滑;R较小时,管子的弯曲部分就较小,弯得就较急。 来回弯是带有两个弯曲角(一般为135°)的管件。来回弯管子弯曲端中心线间的距离叫做来回弯的高度,用字母h表示。室内采暖立支管与干管及散热器连接,管道与不在同一平面上的接点连接时,一般需采用来回弯。 U形管是成正半圆形的管件。管子的两端中心线问的距离d等于两倍弯曲半径R。U形管可代替两个90°弯头,经常用来连接上下配置的两个圆翼形散热器。 图1-1弯管的主要形式 弧形弯管是带有三个弯曲角的管件。中间角一般成90°,侧角成135°。弧形弯管用于绕过其它管子,在有冷热水供应的卫生设备配管时,经常采用弧形弯管。 弯管尺寸由管径、弯曲角度和弯曲半径三者确定。弯曲角度根据图纸和施工现场实际情况确定,然后制出样板,照样板煨制并按样板检查煨制管件弯曲角度是否符合要求。样板可用圆钢煨制,圆钢的直径根据所煨管径的大小选用,10-14mm即可。弯管的弯曲半径应按管
径大小、设计要求及有关规定而定。既不能过大,也末虚选得太小。因为弯曲半径过大,不但用材料多,而且管子弯曲部分所占的地方也大,这样会给管道装配带来困难;弯曲半径选得太小时,弯头背部管壁由于过分伸长而减薄,使其强度降低,而在弯头里侧管壁被压缩,形成皱纹状态。因此,一般规定:热煨弯管的弯曲半径应不小于管子外径的3.5倍;冷煨弯管的弯曲半径应不小于管子外径的4倍;焊接弯头的弯曲半径应不小于管子外径的1.5倍;冲压弯头弯曲半径应不小于管子外径。 弯管时,弯头里侧的金属被压缩,管壁变厚;弯头背面的金属被拉伸、管壁变薄。弯曲半径越小,弯头背面管壁减薄就越严重,对背部强度的影响就越大。为了使管子弯曲后不致对原有的工作性能有过大改变,一般规定管子弯曲后,管壁减薄率不得超过15%。管壁减薄率可按下式进行计算: 式中A——管子弯曲后外侧母线处管壁的减薄率(%); D W——管子外径(mm); R——弯管的弯曲半径(mm)。 弯管时,由于管子弯曲段内外侧管壁厚度的变化,还使得弯曲段截面由原来的圆形变成了椭圆形。弯管断面形状的改变,会使管子的过流断面面积减小,从而增加流体阻力,同时还会降低管子承受内压力的能力,因此,一般对弯管的椭圆率做以下规定:管径小于或等于150mm时,椭圆率不得大于10%;管径小于或等于200mm时,椭圆率不得大于8%。 管道的椭圆率可按下式进行计算: 式中T——椭圆率(%); d1——最大椭圆变形处的长径(mm); d2——最大椭圆变形处的短径(mm)。 应用水、煤气钢管和直缝焊接钢管制作冷煨弯管或热煨弯管时,管子的焊缝应位于距侧面中心线45°的地方,如图1-2所示。以免弯曲时,管子焊缝开裂。
钢管弯管工艺参数介绍
硬管弯管工艺参数 一、 目的 为了满足硬管产品弯管工艺的要求,确保产品在装配后两端的密封效果可靠,有必要对硬管产品弯管所涉及到的相关弯管工艺参数进行整理并归类,供设计时选用。 二、 相关弯管工艺参数的定义: 1、最合适弯曲半径R:弯曲时为了保证弯曲圆弧处圆滑,不褶皱而规定的最合适弯曲R轮半径。 2、最短距离L1:从管端口至弯曲起弯点间的距离。(见附图) 3、最短距离L2:连续两道圆弧间直线段距离。(见附图) 三、相关弯管工艺参数的主要内容: 一)为了保证弯曲圆弧质量,对以下不同规格的硬管弯曲时所选用的最合适弯曲半径进行统计,供设计参考并选用。 序号 管材规格(mm) 最合适弯曲半径R 序号管材规格(mm) 最合适弯曲半径R 1 Φ4.76x0.7 ≥15 19 Φ28x1.5 ≥105 2 Φ6.0x0.7 ≥15 20 Φ31.8x1.5 ≥50 3 Φ6.35x0.7 ≥20 21 Φ35x1.2 ≥80 4 Φ8.0x0.7 ≥30 22 Φ38.1x1. 5 ≥50 5 Φ10x0.7 ≥30 23 Φ54x1.5 ≥80 6 Φ12x0. 7 ≥30 24 Φ57x1. 8 ≥86 7 Φ12x1 ≥30 25 Φ60x1.2 ≥72 8 Φ8x1 ≥25 26 Φ63x1.2 ≥76 9 Φ10x1 ≥20 27 Φ70x2.5 ≥85 10 Φ10x2 ≥20 28 Φ80x1.5 ≥100 11 Φ12x1 ≥30 29 Φ90x1.5 ≥110 12 Φ14x1.5 ≥35 30 Φ100x1.5 ≥120 13 Φ15x1.5 ≥40 31 Φ101.6x1.5 ≥122 14 Φ16x1.5 ≥40 32 Φ110x1.8 ≥132 15 Φ18x1.5 ≥45 33 Φ120x2 ≥145 16 Φ20x1.5 ≥50 17 Φ22x1.5 ≥70 18 Φ25x1.5 ≥70
弯管制作工艺
弯管制作 1、弯管宜采用壁厚为正公差的管子制作。弯曲半径与直管壁厚的关 系宜符合表 1 的规定。 表1 弯曲半径与直管壁厚的关系 弯曲半径R 制作弯管用管子的壁厚 R≥6Do 1.06td 6Do>R≥5Do 1.08td 5Do>R≥4Do 1.14td 4Do>R≥3Do 1.25td 2、弯管弯曲半径应符合设计文件和国家现行有关标准的规定。当无 规定时,高压钢管的弯曲半径宜大于管子外径的 5 倍,其他管子的弯曲半径宜大于管子外径的 3.5 倍。 3、有缝管制作弯管时,焊缝应避开手拉(压)区。 4、金属管应在其材料特性允许范围内进行冷弯或热弯。 5、采用高合金钢管或有色金属管制作弯管时,宜采用机械方法;当 。铅管加热制作弯管时,不得允砂。 击 允砂制作弯管时,不得用铁锤敲 6、金属管热弯或冷弯后,应按设计文件的规定进行热处理。当设计 文件无规定时,应符合下列规定: 1 初制作弯管温度自始至终保持温度在900℃以上的情况外,名义厚度大于19mm 的碳素钢管制作弯管后,应按本规范表2
表2 管道热处理基本要求 名义厚母材最小规 恒温时间最短 度定抗拉强度(mim/mm ) 别热处理温度恒温时间母材类 t(mm) (Mpa) (h) (℃) 碳钢(C)、≤19 全部不要求——碳锰钢(C-Mn) >19 全部600~650 2.4 1 铬钼合金钢≤19 ≤490 不要求——(C-Mo 、Mn-Mo 、Cr-Mo) >19 全部600~720 2.4 1 Cr≤0.5% 全部>490 600~720 2.4 1 铬钼合金钢(C-Mo )≤13 ≤490 不要求—— 0.5%
弯管加工工艺
3弯管 3.1弯管宜采用壁厚为正公差的管子制作。高压钢管的弯曲半径宜大于外径的5倍,其他管子的弯曲半径宜大于管子外径的35倍,有缝管制作弯管时,焊缝应避开管拉(压)区。 弯曲半径与管子壁厚的关系 3.2不锈钢管宜冷弯,铝锰合金管不得冷弯其他材质的管子可冷弯或热弯。高、中合金钢管热弯时不得浇水,低台金钢管一般不宜浇水,热弯后应在5℃以上静止空气中缓慢冷却。 3.3热煨弯头常用:地炉加热煨弯,火焰弯管机,中频电热弯管机等,热煨弯管测温常热用电偶,光学高温计等。 3.4采用热弯管时,不论管径大小,一律按规定装干燥的细砂。加热铜管应用术炭作燃料,加热铝管应先用焦炭打底,上面铺木炭以调节温度。存加热过程中应关闭鼓风机.并不断转动管子,防止温度过高使管子熔化。 3.5采用高合金钢管或有色金属管制作弯管,宜采用机械方法,当充砂制作弯管时,不得用铁锤敲击。铅管加热制作弯管时,不得充砂。 3.6除制作弯管温度自始至终保持在900℃以上的情况外,壁厚大于19mm的碳素钢管制作弯管后,应按规定进行热处理按规定,中、低合金钢管进行热弯时, 对公称直径大或等于是100mm或壁厚大于或等于是13mm的,应按设计文件的要求进行完全退火,正火加回火或回火处理。中、低合金钢管进行冷弯时,对公称直径大于或等于100mm,或壁厚大于或等于13mm的,应按规定要求进行热处理。奥氏体不锈钢管制作的弯管,可不进行热处理,当设计文件要求热处理时,应按设计文件规定进行.
3.7输送剧毒流体或设计压力P大于或等于1OMPa的弯管,制作弯管前,后的壁厚之差,不得超过制作弯管前管子壁厚的10%;其它弯管,制作弯管前,后的管子壁厚之羞,不得超过制作弯管前管子壁厚的15%,且均不得小于管子的设计壁厚。 3.8输送剧毒流体或设计压力P大于或等于lOMPa的弯管,管端中心偏差值A不得超过1.5mm/m,当直管长度L人于3m时,其偏差不得超过5mm。其他类别的弯管.管端中心偏差值Δ得超过3mm/m当直管长度L大于3m时,其偏差不得超过lOmm。 高压钢管制作弯管后,应进行表面无损探伤,需要热处理的应在探伤后进行;当自缺陷时,可进行修磨,修磨后的弯管壁不得小于管子公称壁厚的90%,且不得小于设计壁厚。弯管加工合格后,应按规定填写高压管件加工记录。 3.9高压钢管制作弯管后,应进行表面无损探伤,需要热处理的应在探伤后进行;当有缺陷的90%,且不得小于设计壁厚。弯管加工合格后,应按规定填写高压管件加工记录。 3.10高压管子弯曲可采用冷弯和热弯。钢号为20g,、]SMnV、12CrMo、15CrMO、ICrlSNi9ii、CrlSNil3M021i的高压管子,应尽量。采用冷弯,冷弯后般不进行热处理。 3.11当采用热弯时,将引起机械性能变化,所以 311.1 20号钢的管予热弯时其热弯温度以800℃- 900℃为宜,加热温度不应超过1000℃,终弯温度不得低于800℃。 3.11.215MnV管子热弯时,其热弯温度以950℃~i000℃为宜,加热温度不应超过1050℃,终弯温度不得低于800℃。