航空发动机叶片榫头优化设计研究_陈开军
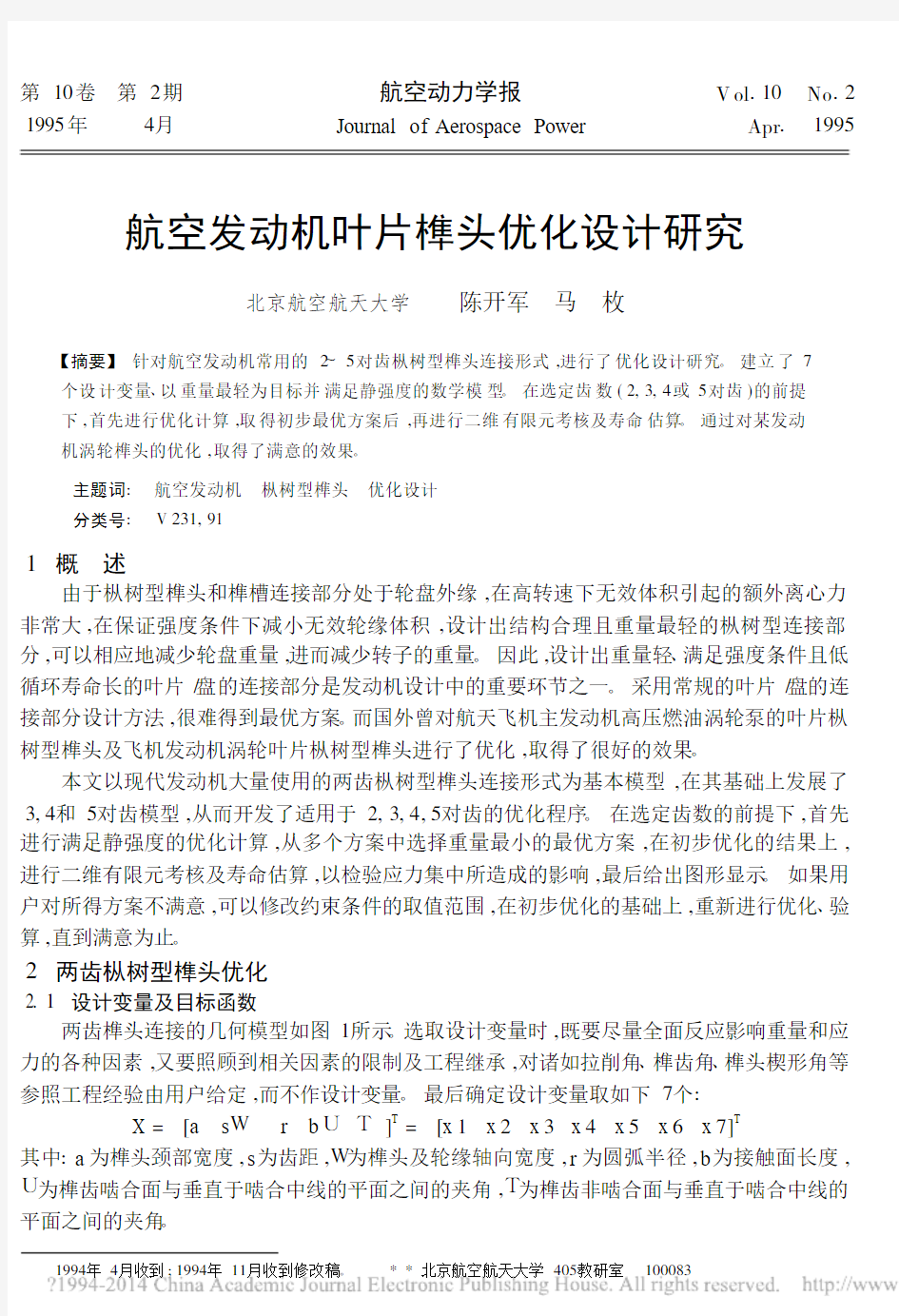

第10卷 第2期航空动力学报 V ol.10No.2 1995年4月Journal of Aerospace Power Apr. 1995
航空发动机叶片榫头优化设计研究
北京航空航天大学 陈开军 马 枚
【摘要】 针对航空发动机常用的2~5对齿枞树型榫头连接形式,进行了优化设计研究。建立了7
个设计变量、以重量最轻为目标并满足静强度的数学模型。在选定齿数(2,3,4或5对齿)的前提
下,首先进行优化计算,取得初步最优方案后,再进行二维有限元考核及寿命估算。通过对某发动
机涡轮榫头的优化,取得了满意的效果。
主题词: 航空发动机 枞树型榫头 优化设计
分类号: V231,91
1 概 述
由于枞树型榫头和榫槽连接部分处于轮盘外缘,在高转速下无效体积引起的额外离心力非常大,在保证强度条件下减小无效轮缘体积,设计出结构合理且重量最轻的枞树型连接部分,可以相应地减少轮盘重量,进而减少转子的重量。因此,设计出重量轻、满足强度条件且低循环寿命长的叶片/盘的连接部分是发动机设计中的重要环节之一。采用常规的叶片/盘的连接部分设计方法,很难得到最优方案。而国外曾对航天飞机主发动机高压燃油涡轮泵的叶片枞树型榫头及飞机发动机涡轮叶片枞树型榫头进行了优化,取得了很好的效果。
本文以现代发动机大量使用的两齿枞树型榫头连接形式为基本模型,在其基础上发展了3,4和5对齿模型,从而开发了适用于2,3,4,5对齿的优化程序。在选定齿数的前提下,首先进行满足静强度的优化计算,从多个方案中选择重量最小的最优方案,在初步优化的结果上,进行二维有限元考核及寿命估算,以检验应力集中所造成的影响,最后给出图形显示。如果用户对所得方案不满意,可以修改约束条件的取值范围,在初步优化的基础上,重新进行优化、验算,直到满意为止。
2 两齿枞树型榫头优化
2.1 设计变量及目标函数
两齿榫头连接的几何模型如图1所示。选取设计变量时,既要尽量全面反应影响重量和应力的各种因素,又要照顾到相关因素的限制及工程继承,对诸如拉削角、榫齿角、榫头楔形角等参照工程经验由用户给定,而不作设计变量。最后确定设计变量取如下7个:
X=[a s W r b U T]T=[x1 x2 x3 x4 x5 x6 x7]T
其中:a为榫头颈部宽度,s为齿距,W为榫头及轮缘轴向宽度,r为圆弧半径,b为接触面长度, U为榫齿啮合面与垂直于啮合中线的平面之间的夹角,T为榫齿非啮合面与垂直于啮合中线的平面之间的夹角。
1994年4月收到;1994年11月收到修改稿。 **北京航空航天大学405教研室 100083
图1 两齿枞树型榫头几何模型
进行优化设计时,首先
由用户给定叶片数Z 、缘板
下表面半径RR 、伸根高度
H H 、轮缘外径RR 1、齿数
m 、拉削角P AN 、榫头材料
密度d 1、轮盘材料密度d 2、
叶身及缘板离心力、榫齿角
度U 1、楔形角2h 、转速N 、榫
头和轮缘的材料许用应力等
条件。
枞树型榫头连接部分重
量由榫头的重量G
榫和轮缘部分的重量G 缘两部分组
成,再求出总重量G 总=G 榫
+G 缘。对于两齿榫头,先分别求出如图1所示榫头7部
分的各部分重量G 31~G 37,再求出图1所示轮缘9部分的各部分重量GE 1~GE 9,再把各部分重量加在一起即可。重量最小目标函数为:
min F (X )=min F (x 1,x 2,x 3,x 4,x 5,x 6,x 7)
=min(G 榫+G 缘)
2.2 约束条件
几何约束主要包括:榫头最小叶颈宽度小于齿距是一种不好的设计〔1〕,所以取:a -s ≥0。
如果T +U 角大于90°,则从形状上考虑就不合理了,所以T +U ≤90,根据经验得出:U ≤T 。
根据文献〔1〕建议:除非盘的材料性能比叶片材料性能好得多,通常盘颈最小宽度不应小于叶片榫头颈部最小宽度,所以
1.0≤盘颈最小宽度/叶片榫头颈部最小宽度≤
2.0
为了防止寻优过程中形状交叉,要求
a -2(m -1)(s /cos(U ))sin(h )≥0
根据第三强度理论,按等强度设计,确定图1中线段BC 的长度为:
(y b -y c )2+(x b -x c )2
≥(3- 1.5b )bPn /([e b ]W cos(P AN ))
其中:Pn 齿面正压力
模型的性能约束主要包括:
榫头I -I 截面(图1)的平均拉伸应力≤许用拉伸应力,即g 1(X )=e I /[e
s ]-1≤0。齿面上的挤压应力≤许用挤压应力,即g 2(X )=e b /[e b ]-1≤0。齿的最大弯曲应力≤许用弯曲应力,即g 3(X )=e c /[e c ]-1≤0。
齿的剪切应力≤许用剪切应力,即g 4(X )=f /[f ]-1≤0。
槽n '-n '截面(图1)的平均拉伸应力≤槽许用拉伸应力,即g 5(X )=e n '/[e n ']-1≤0。
2.3 优化方法及有限元考核根据上述数学模型,选用混合函数法调用Ho oke -Jeev es 法计算。191
第 2 期航空发动机叶片榫头优化设计研究
192航空动力学报第 10 卷
为了检验所得优化结果是否因应力集中的影响而超过许用应力要求,将所得结果进行二维有限元验算。得出计算结果后,调用后置模块显示应力分布图。
2.4 叶片/盘低循环疲劳寿命估算
根据参考文献〔1〕,对材料的持久应力-寿命曲线采用拉格朗日插值方法可求得叶片榫头和轮盘的LCF估计寿命。
2.5 算例及结果分析
采用本程序对某发动机的两齿叶片/盘连接部分进行了优化计算,转速取最大稳态转数N=17000r/min。材料性能数据分别取700℃和600℃时的值。榫头和榫槽部位的材料分别为DZ22和GH4169。叶片数取58,叶片缘板下表面半径取250mm,齿数取2,轮盘半径取240 m m,齿侧面和水平方向的夹角取60°,拉削角取18.5°,楔形角取12°。
表1列出了叶片/盘连接部分优化前后的重量、最大Vio s Mises应力、LCF寿命。从表1中可看出,经优化后的叶片/盘连接部分重量降低了16.46%;榫头危险截面的最大当量应力降低了14.16%,榫头优化后的LCF寿命为原寿命的 3.55倍;轮缘危险截面的最大当量应力降低了17.02%,轮缘优化后的LCF寿命为原寿命的 5.3倍。
表1 优化前后结果比较
LC F寿命(h)最大应力(M Pa)
项 目总重(k g)
榫 头轮 缘榫 头轮 缘
优化前 5.561234151260745.96796.48
优化后 4.6454121366682640.34660.94
在保证静强度条件下,重量降低了16.46%。经有限元考核后证明,应力集中也满足强度条件。
3 3,4,5对齿模型
对于3对齿榫头,由于上两齿重量和离心力和两齿榫头的求法相同,又第3齿的外形和上两齿一样,不同的只是各颈部尺寸,所以第3齿重量和离心力可采用减去多余部分的重量和离心力求出。同理,对于4、5对齿榫头、轮缘和离心力也可求出。
参 考 文 献
1 斯贝M K202发动机应力标准,EGD-3.北京:国际航空编辑部,1979
(责任编辑 王震华)
204J ournal of Aeros pace Pow er V ol.10
RELIABILITY ANALYSIS OF
LOW-CYCLE FATIGUE LIFE FOR A DISC
Lu Wenlin and Zhang Dingzhen
(7th Dept.Northwestern Polytechnical University,X ian 710072)
ABSTRACT When a failure m odel with lo w-cycle fa tigue is identified,the fail-ure functio n for reliability a nalysis reduced as follo ws:As cumulativ e damage of varying-am-plitude cycles is calculated w ith Miner's law,the to tal damag e is considered to be a random va lue v arying from0.3to3,a nd follo w s log arithmic no rmal distribution.Furthermo re,dam-ag e of lo w-cycle lo ads o f each am plitude is evaluated acco rding to the fo rm ula of flo w-cycle fatig ue life prediction propo sed by https://www.360docs.net/doc/348861372.html,ndg raf.Then,the failure functio n for reliability analysis is deriv ed from the above fo rm ulas by transforming strain ex pressio n into stress ex-pressio n.If a stress at cer tain point of a disk is influenced by a disturba nce of so me random va riables,the stochastic finite element metho d is employed to find the v ariance of the stress distribution.When stresses in a disk are in elasto-plastic conditio n,no nlinea r SFEM is re-quired to obtain the v ariance of the stresses.Finally,a numerical exam ple fo r a disk with e-qual thickness is presented and is verified by the M onte-Carlo simulation.
Key words Fatig ue life Stochastic finite elem ent Reliability
OPTIMIZATION OF TURBINE BLADE FIR-TREE ROOTS
Cheng Kaijun and Ma Mei
(4th Dept.Beijing University of Aeronautics and Astronautics,Beij ing 100083) ABSTRACT An o ptimization system for“fir-tree”roo t is dev elo ped for desig n lay out o f the“fir-tree”joint a rea in gas turbine so as to decrease the w eig ht o f aero engine and sho rten the desig n cycle.This sy stem is suitable to desig n the2~5pairs o f teeth used in m odern aero engines.After the o ptimization the smallest w eig ht subject to the static streng th constraints has been attained,the FEM is used to check the distributio n o f stresses,particu-larly the co ncentratio n stress,and the results are sho w n on the screen for making decision.
Key words Aireraft engine Fir-tree Blade root Optimizatio n
C OMMENT O N THE PROBLEM OF TURBULEN CE
Zhao Songnian
(Institute of Atmospheric Physics,The Chinese Academy of Sciences,Beij ing 100029) ABSTRACT This paper points out that Navier-Stokes equa tion is an essential e-quatio n fo r studying turbulent flo w s,it gov erns the mo tio n o f fluid flo w s.Rey no lds equation represents coex istence of ra ndo m and determinativ e pheno mena in the turbulent flo w s.But, Burgers-KdV equatio n has no relation to mechanism of turbulence,so w e can't reg ard it as a "new equatio n"for resea rching turbulent flo ws.
Key words Turbulence Navier-Sto kes equa tions Reynolds
航空发动机涡扇叶片及其成形工艺
航空发动机涡扇叶片及其成形工艺 涡扇发动机具有耗油率低、起飞动力大、噪音低和迎风面积大等特点。60年代中期,它只应用于客机和轰炸机,当时人们普遍认为,它很难在高速歼击机上应用。自70年代以来,带加力的高推比涡扇发动机的相继问世,使战斗机的性能提高到了一个新的水平,从而彻底改变了人们对涡扇发动机的偏见。90年代中期,又为第四代战斗机成功研制了推重比10带加力的涡扇发动机。与此同时,为满足发展巨型、远程运输机、宽机身客机的需要,国外先进的发动机厂家又研制成功了大推力、低耗油率、大流量比的涡扇发动机。时至今日,涡扇发动机已是应用数量最多、范围最广和最有发展前景的航空发动机。 风扇叶片是涡扇发动机最具代表性的重要零件,涡扇发动机的性能与它的发展密切相关。初期的风扇叶片材料为钛合金,具有实心、窄弦、带阻尼凸台结构。现今,风扇叶片在材料、结构方面已改进许多。为了增强刚性,防止振动或颤振,提高风扇叶片的气动效率,用宽弦结构代表了窄弦、带阻尼凸台结构;为了减轻重量,用夹芯或空心结构取代了实心结构;为了增大流量比,提高大推力涡扇发动机推进效率,风扇转子直径已增大到了3242mm,风扇叶尖速度已高达457m/s。而这些材料新、叶身长、叶弦宽、结构复杂的风扇叶片的成形工艺是非常复杂的。因此,风扇叶片的成形工艺始终是涡扇发动机的关键制造技术之一。 1早期风扇叶片 早期风扇叶片为大尺寸实心结构,为防止共振及颤振,它的叶身中部常带有一个阻尼凸台(又称减振凸台)。所有叶片的凸台连成一环状,既增强了刚性又改变了叶片固有频率,减小了叶根弯曲和扭转应力。阻尼凸台接合面喷涂有耐磨合金,当叶片振动时,接合面相互摩擦可起阻尼作用。阻尼凸台一般位于距叶根约整个叶片长度的50%~70%处。阻尼凸台的存在带来一系列问题,如:由于它的存在及它与叶身连接处的局部加厚,使流道面积减少约2%,使空气流量降低,造成气流压力损失,使压气机效率下降,发动机耗油率增加;增加了叶身重量,使叶片离心力负荷加大;使叶片制造工艺更加复杂。在有些风扇叶片上,为了增强抗外物撞击损伤能力,叶身上除了阻尼凸台以外,还有较厚的加强筋。 CFM56-3和CFM56-5发动机风扇转子直径约1700mm,风扇叶片长约600mm,由整体钛合金锻件经机械加工而成。风扇叶片毛坯先镦锻出叶根和阻尼凸台,经预锻成形,再精锻、切边。叶身成形可用数控铣、数控仿形磨、电解加工和抛光等工艺。随着叶片批量生产的增加,应尽量采用精锻法生产出钛合金风扇叶片的锻坯,以提高材料的利用率,减少机械加工工作量和提高风扇叶片的使用寿命。但生产这样大的风扇叶片精锻毛坯,需要使用昂贵的高精度的万吨级机械压力机或螺旋压力机,所需模具的尺寸大、精度也高。因此,精锻工序的成本很高。4钛合金宽弦无凸台空心风扇叶片5高韧性环氧复合材料风扇叶片
航空发动机涡轮叶片发射率测量
收稿日期:2010-04-02;修回日期:2010-12-06基金项目:航空基金(2008ZD24014)作者简介:熊 兵(1975-),男,四川渠县人,工程师,硕士,主要从事航空发动机特种测试技术工作 。 第24卷第2期燃气涡轮试验与研究Vol.24,No.22011年5月Gas Turbine Experiment and Research May,2011 摘要:对于复杂环境下的涡轮叶片表面温度场测量,红外测温技术是目前该领域最佳方法之一,而发射率的准确测 量是红外测温的关键。本文针对涡轮叶片发射率的测量,阐述了热电偶对比法的原理和技术细节,并根据某型发动机涡轮转子叶片温度场试验测试的需求,在600~800℃温度范围内进行了发射率测量。试验数据分析表明,其发射率为 0.914,可作为ROTAMAP II 辐射高温计的预先设定值。而误差分析表明,该方法具有较高的精度。 关键词:辐射测温;发射率;涡轮叶片中图分类号:V241.06 文献标识码:A 文章编号:1672-2620(2011)02-0045-04 Emissivity Measurement of Aero-engine Turbine Blade XIONG Bing ,SHI Xiao -jiang ,CHEN Hong -min ,XU Feng -hua (China Gas Turbine Establishment ,Jiangyou 621703,China) Abstract :The infrared temperature measurement technique is one of the best methods of measuring sur -face temperature field of turbine blades in complicated conditions.Exactly measuring emissivity is a key factor in infrared temperature measurement.Aiming to the measurement of turbine blade emissivity,the principle and techniques details of thermocouple antithesis are described.According to requirements of an aero-engine turbine blade measurement,the emissivities in temperature range from 600℃to 800℃are measured,and test data are analyzed.The emissivity 0.914can be used as the initialization value for the ROTAMAP II infrared thermometer.The error analysis indicates that this method is of upper preci -sion. Key words :infrared temperature measurement ;emissivity ;turbine blade 1引言 物体的发射率表征了该物体表面辐射能力的强弱,任何物体的发射率都等于它在相同温度和相同条件下的吸收率。红外辐射测温技术作为涡轮叶片温度场测量的有效手段,已取得很好的应用效果[1]。红外高温计测量涡轮转子叶片温度场采用的是全发射率,而叶片发射率作为红外测温系统的一个输入参数,需要先确定,才能在试验中准确测出叶片的真实温度。发射率的测量误差直接影响红外高温计测温的精度,因此必须准确测量。 2全辐射测温与发射率的关系 全辐射测温理论上是测量所有波长的辐射能量,当真实温度为T 的待测物体与温度为T b 的绝对黑体在整个光谱范围内总的辐射能量相等时,温度 T b 就定义为待测物体的辐射温度。由普朗克定律可知,绝对黑体在温度T b 下的全辐射功率M b 为: M b = 乙 c 1λ-5(e c 2/λT b -1)-1d λ=σT b 4 (1) 式中:λ为波长;T b 为黑体辐射温度;c 1、c 2分别为普朗克第一和第二辐射常数,c 1=3.741833×10-16W ·m 2, c 2=1.438832×10-2m ·K ;σ为斯蒂芬-玻尔茨曼常 45
航空发动机期末复习习题
一、填空题(请把正确答案写在试卷有下划线的空格处) 容易题目 1.推力是发动机所有部件上气体轴向力的代数和。 2.航空涡轮发动机的五大部件为进气装置;压气机;燃烧室;涡轮和排气装置; 其中“三大核心”部件为:压气机;燃烧室和涡轮。 3.压气机的作用提高空气压力,分成轴流式、离心式和组合式三种 4.离心式压气机的组成:离心式叶轮,叶片式扩压器,压气机机匣 5.压气机增压比的定义是压气机出口压力与进口压力的比值,反映了气流在压气 机内压力提高的程度。 6.压气机由转子和静子等组成,静子包括机匣和整流器 7.压气机转子可分为鼓式、盘式和鼓盘式。 8.转子(工作)叶片的部分组成:叶身、榫头、中间叶根 8.压气机的盘式转子可分为盘式和加强盘式。 9.压气机叶片的榫头联结形式有销钉式榫头;燕尾式榫头;和枞树形榫头。 10.压气机转子叶片通过燕尾形榫头与轮盘上燕尾形榫槽连接在轮盘。 11压气机静子的固定形式燕尾形榫头;柱形榫头和焊接在中间环或者机匣上。 12压气机进口整流罩的功用是减小流动损失。 13.压气机进口整流罩做成双层的目的是通加温热空气
14.轴流式压气机转子的组成盘;鼓(轴)和叶片。 15.压气机进口可变弯度导流叶片(或可调整流叶片)的作用是防止压气机喘振。 16.压气机是安装放气带或者放气活门的作用是防止压气机喘振 17.采用双转子压气机的作用是防止压气机喘振。 18压气机机匣的基本结构形式:整体式、分半式、分段式。 19压气机机匣的功用:提高压气机效率;承受和传递的负载;包容能力 20整流叶片与机匣联接的三种基本方法:榫头联接;焊接;环 21.多级轴流式压气机由前向后,转子叶片的长度的变化规律是逐渐缩短。 22.轴流式压气机叶栅通道形状是扩散形。 23.轴流式压气机级是由工作叶轮和整流环组成的。 24.在轴流式压气机的工作叶轮内,气流相对速度减小,压力、密度增加。 25.在轴流式压气机的整流环内,气流绝对速度减小,压力增加。 26.叶冠的作用:①可减少径向漏气而提高涡轮效率;②可抑制振动。 27.叶身凸台的作用:阻尼减振,避免发生共振或颤震,降低叶片根部的弯曲扭 转应力(防止叶片振动)。 28.涡轮工作条件:燃气温度高,转速高,负荷高,功率大 29.涡轮的基本类型:轴流式涡轮,径向式涡轮
(完整版)航空发动机试验测试技术
航空发动机试验测试技术 航空发动机是当代最精密的机械产品之一,由于航空发动机涉及气动、热工、结构与 强度、控制、测试、计算机、制造技术和材料等多种学科,一台发动机内有十几个部件和 系统以及数以万计的零件,其应力、温度、转速、压力、振动、间隙等工作条件远比飞机 其它分系统复杂和苛刻,而且对性能、重量、适用性、可靠性、耐久性和环境特性又有很 高的要求,因此发动机的研制过程是一个设计、制造、试验、修改设计的多次迭代性过程。在有良好技术储备的基础上,研制一种新的发动机尚要做一万小时的整机试验和十万小时 的部件及系统试验,需要庞大而精密的试验设备。试验测试技术是发展先进航空发动机的 关键技术之一,试验测试结果既是验证和修改发动机设计的重要依据,也是评价发动机部 件和整机性能的重要判定条件。因此“航空发动机是试出来的”已成为行业共识。 从航空发动机各组成部分的试验来分类,可分为部件试验和全台发动机的整机试验, 一般也将全台发动机的试验称为试车。部件试验主要有:进气道试验、压气机试验、平面 叶栅试验、燃烧室试验、涡轮试验、加力燃烧室试验、尾喷管试验、附件试验以及零、组 件的强度、振动试验等。整机试验有:整机地面试验、高空模拟试验、环境试验和飞行试 验等。下面详细介绍几种试验。 1进气道试验 研究飞行器进气道性能的风洞试验。一般先进行小缩比尺寸模型的风洞试验,主 要是验证和修改初步设计的进气道静特性。然后还需在较大的风洞上进行l/6或l/5的 缩尺模型试验,以便验证进气道全部设计要求。进气道与发动机是共同工作的,在不同状 态下都要求进气道与发动机的流量匹配和流场匹配,相容性要好。实现相容目前主要依靠 进气道与发动机联合试验。 2,压气机试验 对压气机性能进行的试验。压气机性能试验主要是在不同的转速下,测取压气机特性 参数(空气流量、增压比、效率和喘振点等),以便验证设计、计算是否正确、合理,找出 不足之处,便于修改、完善设计。压气机试验可分为: (1)压气机模型试验:用满足几何相似的缩小或放大的压气机模型件,在压气机试验台上按任务要求进行的试验。 (2)全尺寸压气机试验:用全尺寸的压气机试验件在压气机试验台上测取压气机特性,确定稳定工作边界,研究流动损失及检查压气机调节系统可靠性等所进行的试验。 (3)在发动机上进行的全尺寸压气机试验:在发动机上试验压气机,主要包括部件间的匹配和进行一些特种试验,如侧风试验、叶片应力测量试验和压气机防喘系统试验等。 3,燃烧室试验 在专门的燃烧室试验设备上,模拟发动机燃烧室的进口气流条件(压力、温度、流量) 所进行的各种试验。主要试验内容有:燃烧效率、流体阻力、稳定工作范围、加速性、出 口温度分布、火焰筒壁温与寿命、喷嘴积炭、排气污染、点火范围等。 由于燃烧室中发生的物理化学过程十分复杂,目前还没有一套精确的设计计算方法。因此,燃烧室的研制和发展主要靠大量试验来完成。根据试验目的,在不同试验器上,采 用不同的模拟准则,进行多次反复试验并进行修改调整,以满足设计要求,因此燃烧室试 验对新机研制或改进改型是必不可少的关键性试验。
1.现代航空发动机发展综述.
第一章现代航空发动机发展综述 (2 第一节航空发动机发展的回顾 (2 一、涡轮喷气发动机的出现,使飞机性能大幅度提高 (2 二、涡轮风扇发动机的出现,再次改变了航空业的面貌 (3 三、宽体、大型、远程飞机要求发展高涵道比涡轮风扇发动机 (4 四、九十年代新型旅客机要求发展性能更好的发动机 (5 五、新一代战斗机要求发展推重比为10一级的发动机 (5 六、小结 (6 第二节军用航空发动机发展 (6 一、军用航空发动机发展 (6 二、第三代战斗机及所用发动机 (7 三、第四代战斗机及所用发动机 (7 四、第五代发动机的发展 (8 第三节大涵道比风扇发动机发展 (10 一、前言 (10 二、飞机的发展 (10 三、大涵道比涡扇发动机发展 (12 第四节现代涡轮轴发动机发展 (13 一、早期涡轮轴发动机的发展 (13
二、第三代涡轮轴发动机 (13 三、第四代涡轮轴发动机发展 (14 第一章现代航空发动机发展综述 第一节航空发动机发展的回顾 二次大战中,各种飞机用的发动机均是活塞式发动机。这种发动机工作时只输出功率,不能直接产生推进飞机前进的推力或拉力,因此需采用空气螺旋桨(简称螺旋桨作为推进器,螺旋桨由发动机带转后,在桨叶上产生推进飞机前进的拉力。这种由活塞式发动机与螺旋桨组成的飞机动力装置,在二战中得到了极大的发展,发动机最大的功率达到3500kW左右,发动机的耗油率低的约为0.28kg/(kW.h,发动机的功率重量比(功率/重量达到2马力/公斤,成为战斗机、轰炸机、运输机等的动力,在战争中发挥了重大作用。但是,它却限制了飞机飞行速度的提高, 其主要原因有二:首先,推进飞机前进的推进功率与飞机的飞行速度的三次方成正比,当飞行速度提高后,飞机所需的大功率发动机根本无法实现,例如,一架装有2000马力、重4吨的飞机, 要将它的飞行速度由400km/h提高到800km/h时, 姑不考虑螺旋桨在高速飞行时效率大幅度降低的因素,就需将发动机功率提高8倍即需16000马力, 这么大功率的航空活塞式发动机显然是不可能实现的。即使能实现,其重量将高达8吨,比飞机还重。另外,当飞机飞行速度增大后,空气作用在桨叶叶尖处的相对速度大大提高,超出声速很多,损失大增,使桨叶的效率大幅度降低,为了能得到足够的拉力,要求再增大发动机的功率,使发动机的功率还要再增加很多。由此可以看出,采用活塞式发动机作动力的飞机,飞行速度是受到限制的,不可能接近声速,更不可能达到声速、超过声速,当时最先进的战斗机飞行速度也只有600-700km/h。 一、涡轮喷气发动机的出现,使飞机性能大幅度提高 早在二战中、后期,一些国家已开始研制涡轮喷气发动机,但真正用于飞机上却是在距今半个世纪前、即四十年代末期。涡轮喷气发动机一出现,由于它具有活塞式发动机无法比拟的优点,很快改变了航空界的面貌,飞机性能得到质的飞跃。
航空发动机涡轮叶片
摘要 摘要 本论文着重论述了涡轮叶片的故障分析。首先引见了涡轮叶片的一些根本常识;对涡轮叶片的结构特点和工作特点进行了详尽的论述,为进一步分析涡轮叶片故障做铺垫。接着对涡轮叶片的系统故障与故障形式作了阐明,涡轮叶片的故障形式主要分为裂纹故障和折断两大类,通过图表的形式来阐述观点和得出结论;然后罗列出了一些实例(某型发动机和涡轮工作叶片裂纹故障、涡轮工作叶片折断故障)对叶片的故障作了详细剖析。最后通过分析和研究,举出了一些对故障的预防措施和排除故障的方法。 关键词:涡轮叶片论述,涡轮叶片故障及其故障类型,故障现象,故障原因,排除方法
ABSTRACT ABSTRACT This paper emphatically discusses the failure analysis of turbine blade.First introduced some basic knowledge of turbine blades;The structure characteristics and working characteristics of turbine blade were described in she wants,for the further analysis of turbine blade failure Then the failure and failure mode of turbine blades;Turbine blade failure form mainly divided into two major categories of crack fault and broken,Through the graph form to illustrate ideas and draw conclusions ;Then lists some examples(WJ5 swine and turbine engine blade crack fault,turbine blade folding section)has made the detailed analysis of the blade.Through the analysis and research,finally give the preventive measures for faults and troubleshooting methods. Key words: The turbine blades is discussed,turbine blade fault and failure type,The fault phenomenon,fault caus,Elimination method
大修航空发动机涡轮叶片的检修技术
编订:__________________ 单位:__________________ 时间:__________________ 大修航空发动机涡轮叶片 的检修技术 Deploy The Objectives, Requirements And Methods To Make The Personnel In The Organization Operate According To The Established Standards And Reach The Expected Level. Word格式 / 完整 / 可编辑
文件编号:KG-AO-4381-88 大修航空发动机涡轮叶片的检修技 术 使用备注:本文档可用在日常工作场景,通过对目的、要求、方式、方法、进度等进行具体、周密的部署,从而使得组织内人员按照既定标准、规范的要求进行操作,使日常工作或活动达到预期的水平。下载后就可自由编辑。 介绍了涡轮叶片的清洗、无损检测、叶型完整性检测等预处理,以及包括表面损伤修理、叶顶修复、热静压、喷丸强化及涂层修复等在内的先进修理技术。 涡轮叶片的工作条件非常恶劣,因此,在性能先进的航空发动机上,涡轮叶片都采用了性能优异但价格十分昂贵的镍基和钴基高温合金材料以及复杂的制造工艺,例如,定向凝固叶片和单晶叶片。在维修车间采用先进的修理技术对存在缺陷和损伤的叶片进行修复,延长其使用寿命,减少更换叶片,可获得可观的经济收益。为了有效提高航空发动机的工作可靠性和经济性,涡轮叶片先进的修理技术日益受到发动机用户和修理单位的重视,并获得了广泛的应用。 1.修理前的处理与检测
航 空 发 动 机 叶 片 涂 层
航空发动机叶片涂层技术 一.涡轮叶片是先进航空发动机核心关键之一 航空发动机被称为现代工业“皇冠上的明珠”,航空发动机是飞机的“心脏”,价值一般占到整架飞机的20%-25%。目前,能独立研制、生产航空发动机的国家只有美、英、法、俄、中5个。但是,无论“昆仑”、“秦岭”发动机、还是“太行”系列,我国航空发动机的水平距离这一领域的“珠穆朗玛”依然存在不小的差距。美、俄、英、法四个顶级“玩家”能够自主研发先进航空发动机。西方四国由于对未来战场与市场的担忧,在航空发动机核心技术上一直对中国实施禁运和封锁。技术难关有很多。本人认为涡轮叶片是先进航空发动机的核心技术之一。 随着航空航天工业的发展,对发动机的性能要求越来越高,要使发动机具有高的推重比和大的推动力,所采用的主要措施是提高涡轮进口温度。国外在20世纪90年代,要求涡轮前燃气进口温度达1850-1950K。美国在IHPTET计划中要求:在海平面标准大气条件下,航空燃气涡轮机的的涡轮进口温度高达2366K。涡轮进口温度的提高要求发动机零件必须具有更高的抗热冲击、耐高温腐蚀、抗热交变和复杂应力的能力。对于舰载机,由于在海洋高盐雾环境下长期服役,要求发动机的叶片的耐腐蚀性更高;常在沙漠上飞行的飞机,发动机的叶片要具有更好的耐磨蚀。 众所周知:镍基和钴基高温合金具有优异的高温力学和腐蚀性
能,广泛用于制造航空发动机和各类燃气轮机的涡轮叶片(blade and vane)。就材质来看:各国的高温合金型号虽各不相同,但就相近成分的高温合金来说,其性能相近(生产工艺方法不同有也造成性能有大的差异)。好的高温合金的使用温度也只有1073K左右,为达到前面所说的要求温度,采用的方法有二:一是制成空心的叶片。空心叶片自20世纪60年代中期出现以来,经历了对流冷却、冲击冷却、气膜冷却以及综合冷却的发展历程,使进气口温度高出叶片材料约300—500℃,内腔的走向复杂化和细致化。这一步的改进仍难满足需要,且英国发展计划将取消冷却。二是涂层,常进行多材质多层次涂层。 PVT公司研究表明:军用直升机上的发动机叶片采用涂层,在沙漠上飞行,寿命可提高3倍左右,不仅大大降低了制造发动机叶片的成本,同时也使飞机的维护时间延长了两倍。 二.涡轮叶片的涂层 高温合金的生产方法或晶形结构对产品的性能是有很大影响的,如图1所示,GE公司20年前开始采用单晶高温合金制作战机用发 Fig.1 Comparative preperties of polycrystal,columnar and single-crystal superallys
航空发动机叶片材料及制造技术现状
航空发动机叶片材料及制造技术现状 在航空发动机中,涡轮叶片由于处于温度最高、应力最复杂、环境最恶劣的部位而被列为第一关键件,并被誉为“王冠上的明珠”。涡轮叶片的性能水平,特别是承温能力,成为一种型号发动机先进程度的重要标志,在一定意义上,也是一个国家航空工业水平的显著标志【007】。 航空发动机不断追求高推重比,使得变形高温合金和铸造高温合金难以满足其越来越高的温度及性能要求,因而国外自7O年代以来纷纷开始研制新型高温合金,先后研制了定向凝固高温合金、单晶高温合金等具有优异高温性能的新材料;单晶高温合金已经发展到了第3代。8O年代,又开始研制了陶瓷叶片材料,在叶片上开始采用防腐、隔热涂层等技术。 1 航空发动机原理简介 航空发动机主要分民用和军用两种。图1是普惠公司民用涡轮发动机主要构件;图2是军用发动机的工作原理示意图;图3是飞机涡轮发动机内的温度、气流速度和压力分布;图4是罗尔斯-罗伊斯喷气发动机内温度和材料分布;图5为航空发动机用不同材料用量的发展变化情况。 图1 普惠公司民用涡轮发动机主要构件 图2 EJ200军用飞机涡轮发动机的工作原理
图3 商用涡轮发动机内的温度、气流速度和压力分布 图4 罗尔斯-罗伊斯喷气发动机内温度和材料分布 图5 航空发动机用不同材料用量的变化情况
1变形高温合金叶片 1.1 叶片材料 变形高温合金发展有50多年的历史,国内飞机发动机叶片常用变形高温合金如表1所示。高温合金中随着铝、钛和钨、钼含量增加,材料性能持续提高,但热加工性能下降;加入昂贵的合金元素钴之后,可以改善材料的综合性能和提高高温组织的稳定性。 1.2 制造技术 生产工艺。变形高温合金叶片的生产是将热轧棒经过模锻或辊压成形的。模锻叶片主要工艺如下: (1)镦锻榫头部位; (2)换模具,模锻叶身。通常分粗锻、精锻两道工序;模锻时,一般要在模腔内壁喷涂硫化钼,减少模具与材料接触面之阻力,以利于金属变 形流动; (3)精锻件,机加工成成品; (4)成品零件消应力退火处理; (5)表面抛光处理。分电解抛光、机械抛光两种。 常见问题。模锻叶片生产中常见问题如下: (1)钢锭头部切头余量不足,中心亮条缺陷贯穿整个叶片; (2) GH4049合金模锻易出现锻造裂纹; (3)叶片电解抛光中,发生电解损伤,形成晶界腐蚀; (4) GH4220合金生产的叶片,在试车中容易发生“掉晶”现象;这是在热应力反复作用下,导致晶粒松动,直至剥落。 发展趋势。叶片是航空发动机关键零件.它的制造量占整机制造量的三分之一左右。航空发动机叶片属于薄壁易变形零件。如何控制其变形并高效、高质量地加工是目前叶片制造行业研究的重要课题之一。
(整理)(7)航空发动机叶片.
发动机叶片 一、 发动机与飞机 1. 发动机种类 1) 涡轮喷气发动机(WP )WP5、WP6、WP7、……WP13 2) 涡轮螺桨发动机(WJ )WJ5、WJ6、WJ7 3) 涡轮风扇发动机(WS )WS9、WS10、WS11 4) 涡轮轴发动机(WZ )WZ5、WZ6、WZ8、WZ9 5) 活塞发动机(HS )HS5、HS6、HS9 2. 发动机的结构与组成 燃气涡轮发动机主要由压气机、燃烧室和涡轮三大部件以及燃油系统、滑油系统、空气系统、电器系统、进排气边系统及轴承传力系统等组成。(发动机的整体构造如下图1)三大部件中除燃烧外的压气机与涡轮都是由转子和静子构成,静子由内、外机匣和导向(整流)叶片构成;转子由叶片盘、轴及轴承构成,其中叶片数量最多(见表1~5) 3. 发动机工作原理及热处理过程
工作原理:发动机将大量的燃料燃烧产生的热能,势能给涡轮导向器斜切口膨胀产生大量的动能,其一部分转换成机械功驱动压气机和附件,剩余能由尾喷管膨胀加速产生推力。 热力过程:用p-υ或T-S 图来表示发动机的热力过程: 4. 飞机与发动机 发动机是飞机的动力,也是飞机的心脏,不同用途的飞机配备不同种类的发动机。如: 1) 军民用运输机、轰炸机、客机、装用WJ 、WS 、WP 类发 动机。 2) 强击机、歼击机、教练机、侦察机、装用WP 、WS 、HS 类发动机。 3) 军民用直升机装用WZ 类发动机。 二、 叶片 在燃气涡轮发动机中叶片无论是压气机叶片还是涡轮叶片,它们的数量最多,而发动机就是依靠这众多的 叶片完成对气体的
压缩和膨胀以及以最高的效率产生强大的动力来推动飞机前进的工作。叶片是一种特殊的零件,它的数量多,形状复杂,要求高,加工难度大,而且是故障多发的零件,一直以来各发动机厂的生产的关键,因此对其投入的人力、物力、财力都是比较大的,而且国内外发动机厂家正以最大的努力来提高叶片的性能,生产能力及质量满足需要。 1.叶片为什么一定要扭 在流道中,由于在不同的半径上,圆周速度是不同的,因此在不同的半径基元级中,气流的攻角相差极大,在叶尖、由于圆周速度最大,造成很大的正攻角,结果使叶型叶背产生严重的气流分离;在叶根,由于圆周速度最小,造成很大的负攻角,结果使叶型的叶盆产生严重的气流分离。因此,对于直叶片来说。除了最近中径处的一部分还能工作之外,其余部分都会产生严重的气流分离,也就是说,用直叶片工作的压气机或涡轮,其效率极其低劣的,甚至会达到根本无法运转的地步。 发动机叶片数量统计如下(以WJ6、WS11为例)表: 1.WJ6 压气机叶片数量见表1 表1 涡轮叶片数量见表2 表2
航空发动机叶片裂纹检测技术及应用分析
航空发动机叶片裂纹检测技术及应用分析 航空发动机作为飞机动力的核心,是体现飞机性能的标准之一。大多采用复杂型面叶片,在运行过程中因为会受到应力、离心力已于弯矩应力的影响,所以容易生成疲劳裂纹、层间分离等损伤。这种损伤会降低航空发动机的性能,给装备带来安全隐患,甚至会引发灾难。因此发展、使用高效的检测技术是解决这类问题的关键。 大部分应用于航空发动机叶片检测的方法主要有孔探法以及常规的检测方法如磁粉、射线、涡流电磁法,其中孔探法是发动机外场检测应用最多的一种技术,这种技术检测时间长,对人力的要求很高,并且操作过程较为复杂且必须十分谨慎。常规的检测方法对复杂曲面结构缺陷的检测存在这一定的局限性。近年来已出现一些高效的无损检测方法如声波/超声波检测、电磁超声非线性检测、相控阵检测等已经逐步应用于发动机叶片的探伤。红外热成像技术亦是较为先进的无损检测技术之一,它主要是通过对被测结构件表面的温度变化进行捕捉,利用红外热成像仪采集表面因温度变化而产生的红外信号检测的。 红外热成像技术是用超声波对工件表面积局部进行激励进而进行加热,通过热成像仪捕捉裂纹区域的局部红外图像。由于在固体器件中超声波传播速度快,所以从发出激励信号到采集到反馈信号是极短时间的过程,又因为深度、裂纹大小不同,红外信号传播到试件表面并得到反馈是随着时间、裂纹规模变化的,最后经过图像处理可以对试件的裂纹进行识别与定位。 1 检测原理及方法概述 1.1 检测原理概述 超声红外热成像检测技术的原理是先将低频高能的超声波注入被测零件,被测零件会产生小幅的机械振动,如果存在裂纹,那么由于裂纹两侧因震动频率不同(即出现相位差)而出现部分热效应(即
航空发动机文献综述
X学院 学院:机电工程学院班级:2008级机制x班姓名:x x 学号:20081060xxxx 指导老师:xxx
文献综述 课题名称:航空发动机制造工艺 前言: 航空发动机是飞行器的核心部件,它是飞行器翱翔蓝天的动力源,其重要性可以用飞行器的“心脏”来形容,它的性能好坏直接关系到飞行器飞行品质的高低,它的发展无不促进着人类航空事业的进步。 1883年汽油内燃机问世之后,为莱特兄弟的“飞行者”号首次飞入蓝天奠定了坚实的基础;喷气式发动研制问世,让人类首次超越了声音的速度,真正做到了再蓝天中自由翱翔,地球因航空旅行时间缩短而促进了经济全球化进程,继而带动了人类社会的发展进步。 人类世界正是因为有了活塞式发动机才实现了蓝天梦,有了空气喷气式发动机才做到了在蓝天之中飞得更高更远。航空发动机改变了人类生活促进了世界进步,追根溯源还是发动机制造工艺的不断发展所致。制造工艺是发动机进步的基石,也是人类前进的助力,它必将在不断进步的同时,更好的改变人类生活,人类生活也必将因装备更好发动机的飞机而愈加美好。 航空发动机制造工艺国际国内现状: 航空发动机的设计和制造是一项复杂的系统性工程,它必须由多团队、多领域、多部门共同参与。该工程涉及到大量的知识与信息,需要在严格的流程管理控制下实现信息之间的交互和协作,以支持并行的、协同的发动机设计和制造。航空发动机产品零组件构型复杂,零部件数量庞大,加工制造精度高,所用工艺方法自然很是繁复,是世界上最主要的一种技术密集型产品。 长期以来,国内的航空发动机的工艺设计与管理水平比较落后,近年来随着计算机在企业的逐渐深入,大部分航空发动机制造企业已摆脱了手工方式的工艺编制,实现了“工艺设计计算机化”。但这种“工艺计算机化”的应用层次依旧较浅,计算机在工艺部门的应用仅仅停留在文字处理,工艺简图绘制等简单应用阶段,工艺编制效率虽有所提高,但并没有脱离传统工艺编制的模式,其缺陷依然存在。 国内的航空发动机制造工艺主要存在以下问题。第一,工艺设计重复工作多,工艺编制效率低。因发动机的工艺设计涉及的内容多,工作量巨大,传统的工艺设计是由工艺师逐件设计的,忽略了同类零件之间的内在联系,同类零件之间在工艺上应用的继承性和一致性,没有得到足够的重视。 第二,工艺设计环境不统一,工艺质量难以保证。不少企业片面追求所谓的“工艺计算机化”,利用基于文字、表格处理软件、二维制图软件等通用软件开发工艺卡片填写系统。这些系统虽有简单、直观的特点和“所见即所得”的界面风格,并取得了一定的应用效果,但由于工艺设计环境五花八门、层次不一,忽视了企业信息化中产品工艺数据间关联关系的重要性,造成工艺数据的准确性、一致性难以保证,工艺设计质量难以保证,工艺信息集成困难等问题。 第三,工艺知识与经验没有得到有效管理与利用,工艺设计智能化程度低。航空发动机的工艺设计与制造是一项技术性、经验性非常强的工作,所涉及的范围十分广泛,用到的信息量相当庞大,并与具体的生产环境及个人经验水平密切相关。现有的工艺设计系统未能提供较好的手段和方式来保留老一辈工艺人员的知识与经验,造成企业知识资源白白浪费、流失。 另外,国内制造工艺还存在各系统问集成性差、工艺信息交流、共享不畅通等问题依旧存在,国内航空发动机制造工艺落后的局面需要改变。 国际航空发动机制造工艺,其现状优于国内的。国际先进航空企业已经大规模使用CAD、
(7)航空发动机叶片-15页文档资料
发动机叶片 一、发动机与飞机 1.发动机种类 1)涡轮喷气发动机(WP)WP5、WP6、WP7、……WP13 2)涡轮螺桨发动机(WJ)WJ5、WJ6、WJ7 3)涡轮风扇发动机(WS)WS9、WS10、WS11 4)涡轮轴发动机(WZ)WZ5、WZ6、WZ8、WZ9 5)活塞发动机(HS)HS5、HS6、HS9 2.发动机的结构与组成 燃气涡轮发动机主要由压气机、燃烧室和涡轮三大部件以及燃油系统、滑油系统、空气系统、电器系统、进排气边系统及轴承传力系统等组成。(发动机的整体构造如下图1)三大部件中除燃烧外的压气机与涡轮都是由转子和静子构成,静子由内、外机匣和导向(整流)叶片构成;转子由叶片盘、轴及轴承构成,其中叶片数量最多(见表1~5) 3. 工作原理:发动机将大量的燃料燃烧产生的热能,势能给涡
轮导向器斜切口膨胀产生大量的动能,其一部分转换成机械功驱动压气机和附件,剩余能由尾喷管膨胀加速产生推力。 热力过程:用p-υ或T-S 图来表示发动机的热力过程: 4. 发动机是飞机的动力,也是飞机的心脏,不同用途的飞机配备不同种类的发动机。如: 1) 军民用运输机、轰炸机、客机、装用WJ 、WS 、WP 类发 动机。 2) 强击机、歼击机、教练机、侦察机、装用WP 、WS 、HS 类发动机。 3) 军民用直升机装用WZ 类发动机。 二、 叶片 在燃气涡轮发动机中叶片无论是压气机叶片还是涡轮叶片,它们的数量最多,而发动机就是依靠这众多的叶片完成对气体的压缩和膨胀以及以最高的效率产生强大的动力来推动飞机前进的工作。叶片是一种特殊的零件,它的数量多,形状复杂,要求高,
航空发动机转子叶片装配工艺设计.docx
航空发动机转子叶片装配工艺设计1概述 大涵道比涡扇发动机普遍追求大推力、大功率等性能指标。为了驱动大风扇、提高效率,涡轮结构一般采用多级低压涡轮。[1]低压涡轮转子叶片作为其中重要零件之一,不仅加工难度大,制造成本昂贵,工作时又需要在高温高压状态下运转,承载受力大,工况复杂。[2]面对如此恶劣的条件,转子叶片表面微小的损伤都极有可能被催化放大,进而产生裂纹、掉块等故障,严重威胁发动机可靠性和稳定性。因此无论从控制投入成本、生产周期亦或保障发动机性能角度考虑,转子叶片的表面质量都需要全方位严加要求。由于结构设计特殊性,低涡转子叶片榫头安装到盘组件榫槽时,需要克服一定阻力。为避免施加装配外力造成转子叶片表面损伤,国外安装转子叶片采用专用装配工艺,而国内在该工艺研究方面一直处于瓶颈状态。[3-4]目前国内采用手动敲击叶片的装配方式,易造成叶片损伤、叶冠错齿等情况,存在安全隐患,影响装配质量。本文基于对多级低压涡轮盘片组件的结构分析,提供了一种转子叶片的新型装配工艺,操作方式简单,在一定程度上降低了装配应力,确保发动机装配质量和性能。 2结构分析 锯齿形叶冠为发动机低压涡轮转子叶片常用叶冠形状。由于相邻叶片间叶冠锯齿存在咬合,因此该型叶冠叶片在盘组件上的装分操作,需要整圈叶片沿盘组件同时轴向移动方能实现。图1低涡转子叶片装配结构示意图受机件加工误差、叶片间相互约束等因素影响,整圈叶
片需克服一定阻力才能沿盘组件移动。而鉴于转子叶片和涡轮盘的装配结构特点和可操作性,转子叶片的外力可作用位置仅限于内缘板附近位置。国内现多采用橡胶锤或其他类似工具敲砸缘板的方法施加冲击外载:操作者首先将所有叶片榫头搭接到涡轮盘榫槽上,同时确保叶片叶冠处于正常咬合状态;准备好后手持橡胶锤,敲砸若干相邻叶片的缘板,使其轴向移动一小段距离,接着再对邻近若干叶片敲击,如此逐组进行,整圈叶片得以轴向移动一定距离,重复操作,最终实现叶片装分。这种方法看似简单,但实际存在很大安全风险:人工施加冲击外载,难以控制施力大小,力过小无法实现叶片安装,力过大容易损伤叶片,且叶片内缘板结构较窄,强度不高,现场已多次出现缘板砸伤事故。 3工艺设计 3.1总体方案 转子叶片在涡轮盘组件上的装配工艺设计,主要即加载装置和支承装置两大工艺装置的设计。加载装置,主要为叶片装分提供稳定均匀载荷,受装配结构限制,仅可设置在叶片内缘板附近位置加载;支承装置,在装分过程中支承定位叶片和涡轮盘组件,具备无级调控两者相对轴向距离的功能,可适应过程中叶片和涡轮盘组件的任意轴向状态。此外,考虑到低涡的多级结构,因此该工艺设计需要具有通用适应性,加载装置和支承装置应能实现各级转子叶片的装分。 3.2工艺原理 转子叶片装分原理见图2。利用支承装置对叶片和盘组件分别进
先进航空发动机关键制造技术发展现状与趋势
先进航空发动机关键制造技术发展现状与趋势 一、轻量化、整体化新型冷却结构件制造技术1 整体叶盘制造技术整体叶盘是新一代航空发动机实现结构创新与 技术跨越的关键部件,通过将传统结构的叶片和轮盘设计成整体结构,省去传统连接方式采用的榫头、榫槽和锁紧装置,结构重量减轻、零件数减少,避免了榫头的气流损失,使发动机整体结构大为简化,推重比和可靠性明显提高。在第四代战斗机的动力装置推重比10 发动机F119 和EJ200上,风扇、压气机和涡轮采用整体叶盘结构,使发动机重量减轻20%~30%,效率提高5%~10%,零件数量减少50% 以上。目前,整体叶盘的制造方法主要有:电子束焊接法;扩散连接法;线性摩擦焊接法;五坐标数控铣削加工或电解加工法;锻接法;热等静压法等。在未来推重比15~20 的高性能发动机上,如欧洲未来推重比15~20 的发动机和美国的IHPTET 计划中的推重比20的发动机,将采用效果更好的SiC 陶瓷基复合材料或抗氧化的C/C 复合材料制造整体涡轮叶盘。2 整体叶环(无盘转子)制造技术如果将整体叶盘中的轮盘部分去掉,就成为整体叶环,零件的重量将进一步降低。在推重比15~20 高性能发动机上的压气机拟采用整体叶环,由于采用密度较小的复合材料制造,叶片减轻,可以直接固定在承力环上,从而取消了轮盘,使结构质量减轻70%。目前正
在研制的整体叶环是用连续单根碳化硅长纤维增强的钛基复合材料制造的。推重比15~20 高性能发动机,如美国XTX16/1A 变循环发动机的核心机第3、4 级压气机为整体叶环转子结构。该整体叶环转子及其间的隔环采用TiMC 金属基复合材料制造。英、法、德研制了TiMMC 叶环,用于改进EJ200的3级风扇、高压压气机和涡轮。3 大小叶片转子制造技术大小叶片转子技术是整体叶盘的特例,即在整体叶盘全弦长叶片通道后部中间增加一组分流小叶片,此分流小叶片具有大大提高轴流压气机叶片级增压比和减少气流引起的振动等特点,是使轴流压气机级增压比达到3 或3 以上的有发展潜力的技术。4 发动机机匣制造技术在新一代航空发动机上有很多机匣,如进气道机匣、外涵机匣、风扇机匣、压气机机匣、燃烧室机匣、涡轮机匣等,由于各机匣在发动机上的部位不同,其工作温度差别很大,各机匣的选材也不同,分别为树脂基复合材料、铁合金、高温合金。树脂基复合材料已广泛用于高性能发动机的低温部件,如F119 发动机的进气道机匣、外涵道筒体、中介机匣。至今成功应用的树脂基复合材料有PMR-15(热固性聚酰亚胺)及其发展型、Avimid(热固性聚酰亚胺)AFR700 等,最高耐热温度为290℃~371℃,2020 年前的目标是研制出在425℃温度下仍具有热稳定性的新型树脂基复合材料。树脂基复合材料构件的制造技术是集自动铺带技术(ATL)、自动纤维铺放
航空发动机叶片增材制造
航空发动机叶片增材制造调查报告 总体来说,有这样几种可行性方向。 一、工艺方向,包括整体增材制造或者表面增材强化: 1. 整体增材制造:使用3d打印代替传统加工工艺,整体打印。目前可行的3d打印技术包括: FDM:熔融沉积(Fused Deposition Modeling) SLM:选择性激光熔融技术(Selective Laser Melting) SLS:选择性激光烧结成型法(Selective Laser Sintering) DMLS:直接金属激光烧结(Direct Metal Laser Sintering) LMD:激光金属沉积(laser metal deposition) 相比于熔模铸造,增材制造具有的优势多于劣势,因此具有较大研究价值。如何解决增材制造新工艺存在的技术弱点正是需要研究的方向。总结有如下几点: ①强度问题:目前最常用为镍基合金增材,使用何种材料可提升强度? ②精度问题:粘结剂喷射,然后是适当的烧结和表面处理是一种很有前途的合金制造工艺 [1],如何进一步提升表面精度? ③温度问题:3d打印叶片目前只是在常温叶片制造上有一些应用,针对于航空发动机涡轮的耐高温叶片(1400-1700℃)则鲜有研究。需要解决问题包括:除镍基合金外,打印粉末采用何种耐高温材料(金属、非金属、复合材料[2])?最佳的高温合金打印方法是哪一种? ④建立模型:建立增材制造叶片的收缩模型、疲劳模型、力学模型等。 2.表面增材强化:使用激光熔覆或等离子喷涂,在已有叶片表面上增加强化散热层,叶片为多层结构。(滕海灏) 二、产品方向,叶片结构智能化和新材料应用。目前叶片结构如下图所示[3],采用熔模铸造的工艺方案,其优缺点见上表。如前所述,如果采用3d打印工艺加工这种空心叶片结构将会实现多方面的优化。就产品本身而言,可以在如下方面进行研究。
航空发动机涡轮叶片相控阵超声检测研究
航空发动机涡轮叶片相控阵超声检测研究 江文文,柏逢明 (长春理工大学电子信息工程学院,长春 130022) 摘 要:超声波无损检测技术(UNT )是航空工件检测中应用较多的一种检测方法。本文对航空发动机涡轮叶片进行了超 声波无损检测;传统检测是用反射波形和波幅特征分析检测出发动机涡轮叶片缺陷;相控阵超声检测(PAUT )是利用相位延迟达到相控效果,形成清晰的图像,和传统超声波检测相比,更能直观的显示缺陷的位置和形状。关键词:超声波检测;相控阵;发动机叶片;相位延迟中图分类号:U464 文献标识码:A 文章编号:1672-9870(2011)04-0066-04 Phased Array Ultrasonic Nondestructive Testing for Aero-engine Turbine Blade JIANG Wenwen ,BAI Fengming (School of Electronics and Information Engineering ,Changchun University of Science and Technology ,Changchun 130022)Abstract :Ultrasonic Nondestructive Testing (UNT )is widely used in aviation component test .This paper adopts UNT in aero-engine turbine blade .Traditional detection uses reflection waveform and amplitude characteristic to check out flaw in engine turbine blade .Phased Array Ultrasonic nondestructive Testing (PAUT )takes advantage of phased delay to obtain phased effect and product clear image .Comparing with traditional ultrasonic detection ,PAUT shows po-sition and sharp of flaw more directly. Key words :ultrasonic testing ;phased arrays ;engine blade ;phased delay 航空发动机的涡轮叶片裂纹是危害飞行安全的重要因素,即使是微小的裂纹对飞机都可能造成无法挽回的后果。航空发动机涡轮叶片除了承受巨大的交变拉应力和扭转应力,还需要在高压腐蚀性燃气的冲击下高速旋转。此外还存在高温氧化、热腐蚀和磨损的问题。而叶片的生产成本很高,因此为了节省经济成本,必须寻找有效的检测手段,及时检测出飞机存在的危险因素。随着技术的发展,我们还需要对涡轮叶片进行定性和定量的分析,确定缺陷的大小和形状等。 超声波检测因其灵敏度高,穿透力强,分辨力好,检验速度快,成本低,设备简单和对人体无害等一系列优点广泛用于航空航天领域。 1传统超声波检测 传统超声波无损检测系统是由超声波换能器、发射电路、回波接受电路、主控电路和显示装置组成。超声波检测的基本原理[1]如图1 所示。 图1超声波检测原理图 Fig.1Ultrasonic testing schematic diagram 传统检测多用脉冲反射法。当工件完好时,超声波可顺利传播到达底面,示波屏中只有表示发射脉冲T 和底波回波B 两个信号。若工件中存在缺陷,在示波屏中有表示发射脉冲T 和底波回波B ,还有表示缺陷波的回波F 。如图2所示,根据缺陷回波 收稿日期:2011-07-01 作者简介:江文文(1987-),女,硕士研究生,主要从事检测技术与过程控制,E-mail :bingdongdeleishui1@https://www.360docs.net/doc/348861372.html, 。 通讯作者:柏逢明(1956-),男,教授,博士生导师,主要从事非线性系统理论、保密通信检测及无线电技术应用研究,E-mail :baifm@https://www.360docs.net/doc/348861372.html, 。 长春理工大学学报(自然科学版) Journal of Changchun University of Science and Technology (Natural Science Edition ) 第34卷第4期2011年12月 Vol.34No.4Dec.2011