基于SolidWorks的搅拌器结构优化设计
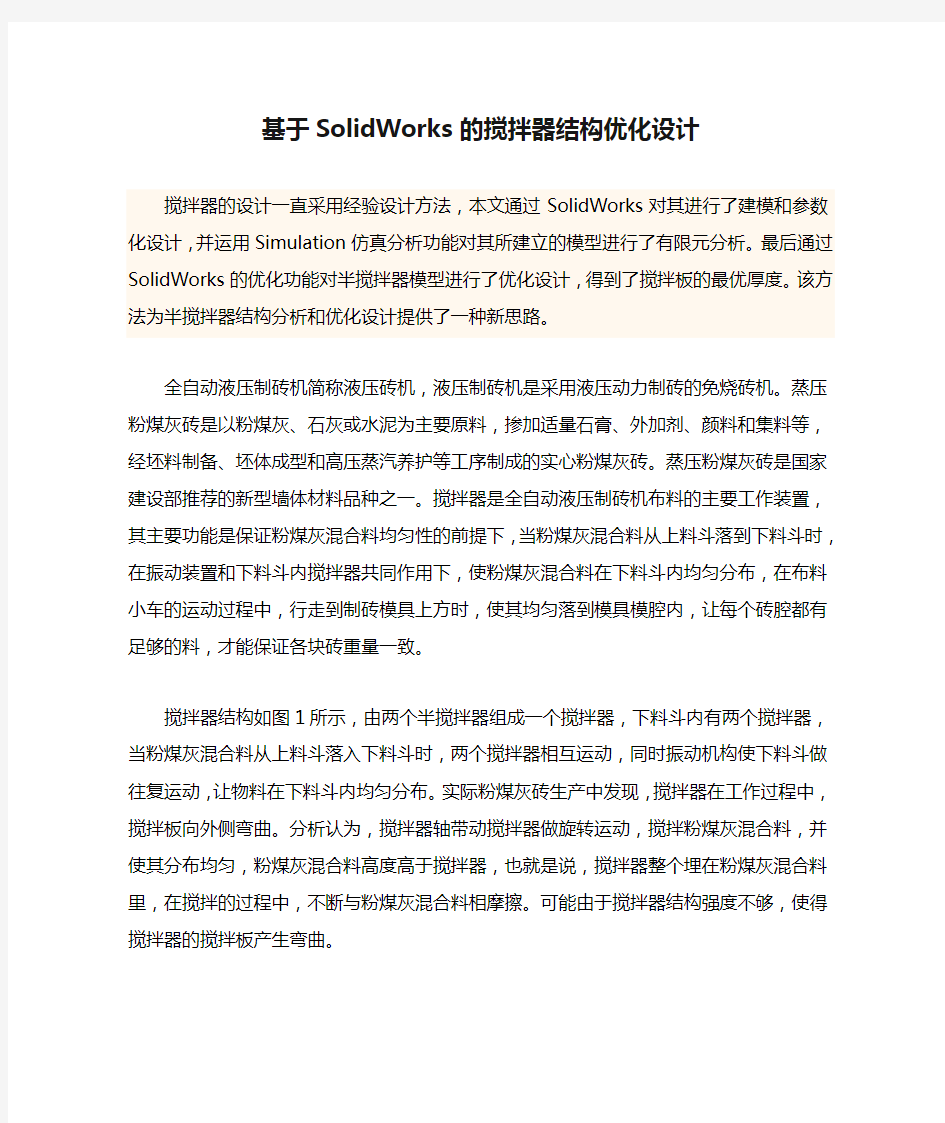

基于SolidWorks的搅拌器结构优化设计
搅拌器的设计一直采用经验设计方法,本文通过SolidWorks对其进行了建模和参数化设计,并运用Simulation仿真分析功能对其所建立的模型进行了有限元分析。最后通过SolidWorks的优化功能对半搅拌器模型进行了优化设计,得到了搅拌板的最优厚度。该方法为半搅拌器结构分析和优化设计提供了一种新思路。
全自动液压制砖机简称液压砖机,液压制砖机是采用液压动力制砖的免烧砖机。蒸压粉煤灰砖是以粉煤灰、石灰或水泥为主要原料,掺加适量石膏、外加剂、颜料和集料等,经坯料制备、坯体成型和高压蒸汽养护等工序制成的实心粉煤灰砖。蒸压粉煤灰砖是国家建设部推荐的新型墙体材料品种之一。搅拌器是全自动液压制砖机布料的主要工作装置,其主要功能是保证粉煤灰混合料均匀性的前提下,当粉煤灰混合料从上料斗落到下料斗时,在振动装置和下料斗内搅拌器共同作用下,使粉煤灰混合料在下料斗内均匀分布,在布料小车的运动过程中,行走到制砖模具上方时,使其均匀落到模具模腔内,让每个砖腔都有足够的料,才能保证各块砖重量一致。
搅拌器结构如图1所示,由两个半搅拌器组成一个搅拌器,下料斗内有两个搅拌器,当粉煤灰混合料从上料斗落入下料斗时,两个搅拌器相互运动,同时振动机构使下料斗做往复运动,让物料在下料斗内均匀分布。实际粉煤灰砖生产中发现,搅拌器在工作过程中,搅拌板向外侧弯曲。分析认为,搅拌器轴带动搅拌器做旋转运动,搅拌粉煤灰混合料,并使其分布均匀,粉煤灰混合料高度高于搅拌器,也就是说,搅拌器整个埋在粉煤灰混合料里,在搅拌的过程中,不断与粉煤灰混合料相摩擦。可能由于搅拌器结构强度不够,使得搅拌器的搅拌板产生弯曲。
图1 搅拌器结构图
本文以全自动液压制砖机搅拌器为例,基于SolidWorks产品设计平台,对搅拌器进行仿真设计和优化设计,通过分析结果和优化方案,缩短设计周期,增加产品的可靠性,降低材料消耗和成本;并模拟各种试验方案,提前发现潜在的问题,减少试验时间和生产经费。
搅拌器结构一直采用传统的设计方法——类比设计和经验设计,产品质量主要依靠设计人员的经验,需要进行方案设计、样机试制,样机试验,方案修改,然后多次循环才能完成。这种设计方法可靠性较差,设计成本高。现代基于三维软件的CAD/CAE设计模式在设计阶段就可以对各种方案进行分析比较和优化,减少或消除样机的制作。通过有限元分析便可了解设备在高压作用下零件的应力分布、变形情况;零件之间的接触力;判定产品的安全性;找出产品经济性与安全性的最佳平衡点。
SolidWorks是应用广泛的三维CAD建模和分析软件,可在完成零件、部件和总成的造型设计后,自动生成有限元网格并进行计算,如果结果不符合设计要求,则重新进行造型和计算,直到满意为止,从而极大地提高设计水平和效率。本文以搅拌器设计中搅拌板厚度设计为例,通过使用SolidWorks的CAD/CAE功能,达到优化设计搅拌器的目的。
一、模型建立及有限元分析
1.搅拌器基本工作参数和模型建立
搅拌器结构见图1,具体参数见表1。
表1 搅拌器结构尺寸
搅拌器材料为Q235A,弹性模量210GPa,泊松比为0.28,抗拉强度为370MPa,屈服强度为235MPa,质量密度为7860kg/m3。利用SolidWorks基于特征的参数化造型功能,可建立该托盘的精确模型,由于模型对称,因此采用半搅拌器分析。
2.有限元仿真分析
使用SolidWorks的Simulation插件,建立算例,对半搅拌器施加载荷和约束,对版搅拌器进行有限元网格划分,如图2。
图2 半搅拌器有限元网格模型
利用Simulation工具对半搅拌器模型进行应力和变形分析,其应力分布和位移分布见图2和图3,从图2的应力分析图上可以看出,半搅拌器的连接板键槽处为应力破坏点,最大应力为226.6Mpa,没超过Q235A 的屈服极限235Mpa。从图3的位移分析来看,半搅拌器的最大为位移为5.51mm,位移变形很大,变形与实际基本相符,因此半搅拌器模型还需要优化。
图3 半搅拌器应力云图(N/mm2)
图4 半搅拌器位移云图(N/mm2)
二、半搅拌器结构优化设计
进入优化设计界面,半搅拌器的目标函数为半搅拌器的质量最小化;设计变量为搅拌板厚度,它对半搅拌器的质量和应力有重大影响;约束条件为安全系数,同时不改变其它条件,以防止半搅拌器整体结构出现较大变化。设置搅拌板厚度取值范围为10≤x≤30。经过5次迭代后,最终成功找到托盘模型优化最优解,具体优化过程见图5,优化前后相关数据对比见表2,为便于后期实际生产制造,对优化结果进行了取整。
图5 优化设计界面
表2 优化前后半搅拌器数据对比
由表2可知,与优化前相比,搅拌板厚度增大,它的厚度增大,可以增强搅拌板抗弯性能。利用优化后的设计参数,重新生成半搅拌器模型,经有限元分析,托盘的最大位移为3mm,位移变形减小,说明托盘的强度和刚度有一定提高,可减少其在使用过程中的破损率。
三、结论
本文采用SolidWorks对半搅拌器模型进行了有限元仿真分析,并在分析的基础上,对托盘进行优化设计,半搅拌器优化后的性能更趋于合理,大大降低了设计及试验成本,为产品方案修订提供了方向性和数据性指导。
SolidWorks大装配体技巧
S o l i d W o r k s大装配体技 巧 Prepared on 24 November 2020
SolidWorks大装配之技巧篇 大型装配体设计对于任何三维设计软件来说都是一个艰巨的挑战,操作与计算的延迟通常让人无法忍受。本文以图文和案例的形式为大家讲解利用SolidWorks处理大装配体的各种技巧,指导工程师进行大装配体设计。 大装配体是指达到计算机硬件系统极限或者严重影响设计效率的装配体,大装配体通常造成以下操作性能下降:打开/保存、重建、创建工程图、旋转/缩放和配合。影响大装配体性能的主要因素有:系统设置、装配设计方法、装配技巧、数据管理、操作系统和计算机硬件,本文主要讲解的是装配技巧。 一、配合技巧 (1)配合的运算速度由快到慢的顺序为:关系配合(重合和平行);逻辑配合(宽度、凸轮和齿轮);距离/角度配合;限制配合。 (2)最佳配合是把多数零件配合到一个或两个固定的零件,如图1所示。避免使用链式配合,这样容易产生错误,如图2所示。 (3)对于带有大量配合的零件,使用基准轴和基准面为配合对像,可使配合方案清晰,不容易产生错误。如图3所示的某减速器,零件之间有大量的同轴心配合,配合方案不清晰,一旦某个主要零件发生修改,就会造成配合面丢失,导致大量配合错误产生。而图4的配合方案就很清晰,一旦出错,很容易修改。 (4)尽量避免循环配合,这样会造成潜在的错误,并且很难排除,如图5所示。 (5)尽量避免冗余配合:尽管SolidWorks允许冗余配合(除距离和角度配合外),冗余配合使配合解算速度更慢,配合方案更难理解,一旦出错,更难排查。 (6)尽量减少限制配合的使用,限制配合解算速度更慢,更容易导致错误。 (7)如果有可能,尽量完全定义零部件的位置。带有大量自由度的装配体解算速度更慢,拖动时容易产生不可预料的结果。对于已经确定位置或定型的零部件,使用固定代替配合能加快解算速度。 (8)避免循环参考。大部分循环参考发生在与关联特征配合的时候,有时也会发生在与阵列零部件配合的时候。如果装配体需要至少两次重建才能达到正确的结果,那么装配体中很可能存在循环参考。如图6所示,装配体中零件B 的边线和零件A的边线有一个重合的关联参考,配合时在零件A和B之间添加10mm的距离配合,那么每次重建都会出错,并且零件B每次重建都会伸长10mm,这就是循环参考的典型错误。 二、轻化装配体 使用轻化模式,可以显着提到大装配体的性能。当零部件是轻化状态,零部件只有部分模型信息被载入内存,其他信息只有在需要时才会被载入。表1所示的装配体操作不需要还原零部件。 装配体中零部件各种状态定义如下。 ◎还原状态:零部件的模型信息完全装入内存。 ◎轻化状态:零部件的模型信息部分装入内存,只在需要时才装入内存并参与运算。 ◎压缩状态:零部件的模型信息暂时从内存中清除,零件功能不再可用也不参与运算。
SolidWorks-装配体实例详解
第9章装配体设计·97· 第9章装配体设计 装配体设计是三维设计中的一个环节,不仅可以利用三维零件模型实现产品的装配,还可以使用装配体的工具实现干涉检查、动态模拟、装配流程、运动仿真等一系列产品整体的辅助设计。 将两个或多个零件模型(或部件)按照一定约束关系进行安装,形成产品的装配。由于这种所谓的“装配”,不是真正的在装配车间的真实环境下完成,因此也称为虚拟装配。 9.1:插入零部件及配合 9.1.1 案例介绍及知识要点 组装如图9-1所示的链轮组件。 图9-1 链轮组件 知识点 ?插入零部件 ?从设计库中插入标准件 ?移动零部件和旋转零部件 ?镜向零部件 ?特征驱动零部件 ?添加配合关系
SolidWorks实用教程 ·98· 9.1.2操作步骤 <1>新建零件 单击菜单栏中的【新建】按钮,系统自动激活【新建Solidworks文件】对话框,选择【装配体】模板,如图9-2所示,单击【确定】按钮。 图9-2 文件模板 <2>插入基体零件 单击【浏览】按钮,在【查找范围】文本框中选择光盘中的“第九章/插入零部件及配合/链轮组件/支撑架”,单击【打开】按钮,如图9-3所示,再单击【确定】按钮。 图9-3 插入基体零件 <3>保存文件 Ctrl+S保存文件,如图9-4所示,命名为“链轮组件”,单击【保存】,系统将自动添加文件后缀“.sldasm”,单击【保存】按钮。
第9章装配体设计·99 · 图9-4 保存文件 <4>插入“轴组件”子装配体 按S键,出现S 工具栏,单击【插入零部件】按钮,弹出【插入零部件】属性管 理器对话框。单击【浏览】按钮,选择子装配体“轴组件”,单击【打开】按钮,在视图区域任意位置单击,如图9-5所示。 图9-5 插入“轴组件” <5>旋转插入“轴组件” 为了便于进行配合约束,旋转“轴组件” ,单击【移动零部件】 下拉按钮,选择【旋转零部件】命令,弹出【旋转零部件】属性管理器对话框,此时鼠标变为图标,旋转至合适位置,单击【确定】按钮,如图9-6所示。
SolidWorks与Pro-E的区别(机械设计)
SolidWorks与Pro-E的区别(机械设计) SolidWorks与Pro-E的区别 关键字: SolidWorks烟台威海 SolidWorks一贯倡导三维CAD软件的易用性、高效性。SolidWorks软件的特点和优点包括: 1全Windows界面,操作非常简单方便 SolidWorks是在Windows环境下开发的,简易方便的工作界面; 利用Windows的资源管理器或SolidWorksExplorer可以直观管理SolidWorks文件;SolidWorks软件非常容易学习; SolidWorks采用内核本地化,全中文应用界面; SolidWorks全面采用Windows的技术,支持特征的"剪切、复制、粘贴"操作; 支持拖动复制、移动技术; 2清晰、直观、整齐的"全动感"用户界面 "全动感"的用户界面使设计过程变的非常轻松:动态控标用不同的颜色及说明提醒设计者目前的操作,可以使设计者清楚现在做什么;标注可以使设计者在图形区域就给定特征的有关参数;鼠标确认以及丰富的右键菜单使得设计零件非常容易;建立特征时,无论鼠标在什么位置,都可以快速确定特征建立; 图形区域动态的预览,使得在设计过程中就可以审视设计的合理性; 利用FeatureManager设计树设计人员可以更好地通过管理和修改特征来控制零件、装配和工程图; PropertyManager属性管理器,提供了非常方便的查看和修改属性操作;PropertyManager属性管理器,减少了图形区域的对话框,使设计界面简捷、明快; ConfigerationManager属性管理器很容易地建立和修改零件或装配的不同形态,大大提高了设计效率; 3灵活的草图绘制和检查功能 草图绘制状态和特征定义状态有明显的区分标志,设计者可以很容易清楚自己的操作状态; 草图绘制更加容易,可以快速适应并掌握SolidWorks灵活的绘图方式:单击-单击式或单击-拖动式;单击-单击式的绘制方式非常接近AutoCAD软件; 绘制草图过程中的动态反馈和推理可以自动添加几何约束,使得绘图时非常清楚和简单; 草图中采用不同的颜色显示草图的不同状态; 拖动草图的图元,可以快速改变草图形状甚至是几何关系或尺寸值; 可以绘制用于管道设计或扫描特征的3D草图; 可以检查草图的合理性; 4强大的特征建立能力和零件与装配的控制功能 强大的基于特征的实体建模功能。通过拉伸、旋转、薄壁特征、高级抽壳、特征阵列以及打孔等操作来实现零件的设计; 可以对特征和草图进行动态修改; 功能齐备和全相关的钣金设计能力。利用钣金特征可以直接设计钣金零件,对钣金的正交切除、角处理以及边线切口等处理非常容易;SolidWorks提供了大量的钣金成形工具,采用简单的拖动技术就可以建立钣金零件中的常用形状; 利用FeaturePalette窗口,只需简单地拖动到零件中就可以快速建立特征;
Solidworks机械设计说明书
井冈山大学 Soildworks机械设计 机电工程学院 班级:11机制本二班 学号:110612029 姓名:罗斌 指导老师:康志成
目录 一、设计内容 (2) 二、齿轮传动总体设计 (4) 三、各齿轮的设计 (4) 1、结构尺寸设计 (4) 2、材料的选择,结构形式设计 (4) 3、3D软件设计零件 (6) 四、轴的设计 (7) 五、机架的设计 (8) 六、零件的装配 (9) 七、设计小结 (10) 八、参考资料 (10)
一、设计内容 1. 已知条件: 电机功率4kw ,小带轮转速n 1=960r/min, 传动比i=3.5,传动比允许误差≤±5%;轻度冲击;两班工作制。 2. 设计内容和要求。 1) V 带传动的设计计算。 2) 轴径设计。 取45号钢时,按下式估算: dmin=11003.1/3?≥n p ,并圆整; 3) V 带轮的结构设计。 选择带轮的材料、结构形式、计算基本结构尺寸; 4) 用3D 软件设计零件及装配图,并标注主要的特征尺寸; 5) 生成大带轮零件图(工程图),并标注尺寸、粗糙度等。 二、 V 带传动总体设计 1)确定计算功率。 由表13-8得工作情况系数K α=1.2,故 Pc=K α=1.2×4=4.8kw 2)选择V 带的带型。 根据带轮的功率Pc=4.8、小带轮的转速n 1=960r/min ,由图13-15查得此坐标位于A 型与B 型交界处,本次试验选用B 型。 3)求大、小带轮轮基准直径d ?、d ? 由表13-9,d ?应不小于125,现取d ?=140mm ,由式(13-9)得 d ?=(n ?/n ?) ×d ? (1-ε)=3.5×140×(1-0.02)=480.2
Solidworks装配体
实验四 SolidWorks 装配体 一、 实验目的 1. 掌握零件装配操作及运动模拟方法 二、 实验内容 完成零件装配与运动模拟 三、 实验步骤 1. 物质动力 物质动力是以现实的方式查看装配体零部件运动的方法之一。启动物质动力功能后,拖动一个零部件时,此零部件就会向其接触的零部件施加作用力,并使接触的零部件在所允许的自由度范围内。物质动力可以在整个装配体范围内应用,拖动的零部件依次可以顺次推动 (1) SolidWorks 文件】对话框,选择【装配体】模板,单击【确定】按钮,进入装配体窗口,出现【插入零部件】属性管理器,选中 【生成新装配体时开始指令】和【图形预览】复选框,单击【浏览】 按钮,出现【打开】对话框,在文件夹“物质动力下”选择要插入的零件“底板”,单击【打开】 1所示。 (2) 选择“底板”、“滑块”的右视图,单击【重合】按钮,单击【确定】按钮 ,完成重合配合,如图2所示。 (3) 选择“底板”上表面和“滑块 1”下表面,单击【重合】按钮,单击【确定】按钮 ,完成重合配合,如图3所示。 图1 物质动力实例 图2 “底板”、“滑块”右视图重合配合 图3 “底板”上表面、“滑块1”下表面重合配合
(4) ,如图4所示。 (5) 单击【移动零部件】按钮,出现【移动零部件】属性管理器,选择【自由拖动】 选项,指针变成形状,展开【高级配合】标签,选中【标准拖动】单选按钮,按住鼠标拖动,观察移动情况,如图5所示。 图4 完成其余零件装配 图5 【自由拖动】 (6) 选中【碰撞检查】单选按钮,选中【碰撞时停止】、【高亮显示面】和【声音】复 选框,选择“手柄”,由于销钉的影响,滑块<1>被拖动到如图6所示位置,停止并发出“叮铛”声。 图6 碰撞时停止 (7) 选中【物质动力】单选按钮,选择“滑块<1>”,在零件上出现一个符号,这个 符号代表质量中心。拖动“滑块<1>”,当“滑块<1>”移动到槽尾部时,“滑块 <1>”将拖动“滑块<2>”同时移动,直到“滑块<2>”零件到达“底板”槽的尾部,发生碰撞时停止,如图7所示。 图7 物质动力 2. 万向节装配 (1) 将万向节各零件装配起来形成装配体,如图所示;
Solidworks机械设计
Solidworks机械设计 ——轴承 班级:机械1204 姓名:孙洪蕾 学号:A08121051
轴承 一.创建内外圈实体。 1.新建文件。 启动solidworks,新建一个零件文件。 2.绘制旋转草图。 选择前视基准面作为草图绘制平面。新建一张草图,利用草图工具绘制基体旋转的草图轮廓,并标注尺寸。 3旋转实体。 单击“特征”工具栏中的“旋转凸台/基体”按钮,在属性管理器中设置旋转类型为单向,角度为360度,默认草图中的中心线为旋转轴,生成旋转特征。
4.创建轴承内外圈圆角。 选择轴承外圈的外边线,单击“特征”工具栏中的“圆角”,在属性管理器中指定圆角的类型为“等半径”,在文本框中设置圆角半径为3.5mm,生成圆角特征。同理,生成内圈圆角。
5.为轴承内外圈指定材质。 (1)设置材质。在“设计树”右击材质选项,选择编辑材料。(2)指定材质。在展开的材料列表中选择“钢”--“合金钢”,单击“应用”,为轴承内外圈指定材料为合金钢。 (3)保存文件。至此,轴承内外圈就创建完成了。 二.创建轴承的保持架。 1.新建文件。 启动solidworks,新建一个零件文件。 2.新建草图。 选择前视基准面作为草图绘制平面,新建一张草图。 3.绘制凸台拉伸草图。 利用草图工具以坐标原点为圆心绘制一个直径为160mm的圆,作为拉伸特征的草图轮廓。
4.凸台拉伸实体。 单击“拉伸凸台/基体”,在属性管理器中设置拉伸终止条件为“两侧对称”,拉伸深度为3mm,生成一个以前是基准面为对称面,前后各拉伸1.5mm的圆柱。 5.新建草图。 选择上视基准面作为草图绘制平面,新建一张草图。 6.绘制旋转草图。 (1)绘制一条竖直中心线,并标注中心线到原点的距离为58.75mm。(2)绘制一个以坐标点(58.75,0)为圆心,直径为30mm的圆。(3)单击“剪裁实体”,减掉中心线左侧的半圆。 (4)单击“直线”,绘制一条将半圆封闭的竖直直线。
SolidWorks-装配体实例详解 -爆炸篇
第9章装配体设计·109· 9.2:装配体检查 9.2.1案例介绍及知识要点 对如图9-93所示的链轮组件进行干涉检查并修复。 图9-93干涉检查 知识点 ?干涉检查 ?装配体中编辑零部件 9.2.2 操作步骤 <1>打开装配体 打开光盘中的“第9章/装配体检查/干涉检查/链轮组件”
SolidWorks实用教程 ·110· <2>干涉检查 切换到【评估】工具栏,单击【干涉检查】按钮,弹出【干涉检查】属性管理器对话框,单击【计算】按钮,如图9-94所示。 图9-94 干涉检查 <3>查看干涉位置 单击【结果】选项组下的目录,可以显示干涉的零件,如图9-95所示,干涉1和干涉2都为轴承和轴干涉,干涉3和干涉11都为键和顶丝干涉,干涉4和干涉12都为轴和链轮,干涉5和13干涉都为链轮和键,干涉6和干涉14都为链轮和顶丝,干涉7、干涉8、干涉9和干涉10都为连接板和螺栓干涉。 图9-95 检查干涉位置 <4>忽略干涉 在【结果】选项组下的文本框中选中“螺栓和连接板的4个干涉、顶丝和链轮的2个干涉”,单击【忽略】按钮,单击【确定】按钮。如图9-96所示
第9章装配体设计·111 · 图9-96 忽略干涉 <5>打开干涉零件 在FeatureManager设计树中展开“轴组件”特征树,单击“轴”,在关联菜单中单击【打开零件】按钮。如图9-97所示 图9-97 查看干涉零件 <6>修改干涉问题 双击轴,显示轴的直径为“36”,的确与直径为“35”的孔干涉,所以修改轴的直径为“35”,如图9-98所示,单击【重新建模】按钮并回车,单击【确定】按钮,单击【保存】按钮,保存修改的零件,单击【关闭】按钮,在对话框单击【是】按钮。
机械设计SolidWorks毕业设计.
对齿轮、轴及小齿轮轴的三维建模 Ⅰ、齿轮三维模型的形成 SolidWorks 的插件GearTrax 用以生成各种齿轮模型。根据机械设计数据,选择直齿,输入齿轮的模数m = 2,大小齿轮齿数88和22,点击齿面厚,键入大小齿轮的齿轮宽度b 50mm ,。分别点1 = b 44mm 2 =击激活大小齿轮后,点击完成,插件自动将成型的齿轮导入SolidWorks 中,从而完成齿轮建模。 GearTrax2008 操作 大齿轮的大体建模大齿轮的大体建模 得到了大齿轮的大体建模,然后修改大齿轮: ①通过【拉伸切除】命令构造轮毂直径为50mm,键槽高、宽分别为5mm、10mm。 ②修改大齿轮,按工程图画减重槽和减重孔,利用【拉伸切除】命令,先画减重槽,深度为10mm,利用基准面通过【镜像】命令,画出另一侧。
③通过【拉伸切除】命令打一个减重孔,孔径为36mm,【插入】-【参考几何体】-【基准轴】命令,选择圆心为基准轴,通过【圆周阵列】命令,选择基准轴和阵列的数目,完成多个减重孔成型 ④通过【倒角】命令倒角,最后成型。 齿轮的工程图 加工轮毂和键糟加工减重槽
加工减重孔插入基准轴 减重孔圆周整列大齿轮的三维建模 小齿轮轴的三维建模 在导入小齿轮的基础上,按照二维工程图进行建模。 ①依次用【拉伸】命令构造小齿轮轴,完成小齿轮轴的大体建模 ②然后利用【插入】-【参考几何体】-【基准面】命令,在小齿轮轴的外伸端建立基准平面1,如图,再在该基准平面上利用【拉伸切除】命令,按照高速轴和V 带轮联接键的尺寸:高速轴和V 带轮联接键为:键8X28 GB1096-79b ×h = 8×7,L = 28,绘制草图,选择切除厚度,完成键槽的成型。 ③利用【倒角】和【倒圆角】命令修改小齿轮轴,完成建模。 小齿轮轴工程图
SolidWorks装配体选择工具
SolidWorks装配体选择工具 今天我们来看下SolidWorks提供了哪些工具以帮助我们在装配体中快速的选择到多个零件。点开常用工具栏中选择旁边的下拉按钮,可以看到如下图的一些选择命令。下面,我们就下面的命令做下简单的说明。 1.框选取 通过以指针拖动选框来选择零件。 从左到右选择时,框中的所有零件都被选择中;从右到左选择时,与框边界交叉的零件也被选择中。 从左往右拖动示例 从右往左拖动示例 按住Shift继续框选时,只会添加被选择中的零件; 安装Ctrl继续框选时,切换被选择中的零件的选择状态;
对于未在继续选择时选中的零件不受影响,继续维持原状态。 2.套索选取 选择套索绘制区域中包含的零件。 顺时针与逆时针绘制套索无差别。 套索选取示例 3.选择所有 选择装配体的所有零件,也可以通过快捷键Ctrl+A选取。 全选示例 4.卷选 自定义一个临时的3D立方体状的空间,以选择零件。 选择命令后,在与计算机屏幕平行的平面上拖出一个矩形(选择对象与框选的原则相同)。在默认情况下,该平面通过装配体的原点,也可以通过预选项目控制平面的位置。
顶点:平面将通过该顶点。 边线或非平面:平面将在最接近原点的位置与该边线或面相交。 平面或参考基准面:在该平面上将绘制矩形,显示图变为与该平面垂直 拖出矩形 释放鼠标按键,会自动生成立方体; 拖动立方体上出现的控标调整范围,调整时可以实时预览当前选择到的对象;单击空白区域确定。 卷选示例
选择装配体中所有压缩的零件。 6.选取隐藏 选择装配体中所有隐藏的零件。 7.选取配合到 选择与当前选中的零件(一个或多个)有配合关系的零件; 之前选中的零部件不会被包括在其中; 隐藏或压缩的零件也会被选中。 选取配合到示例 8.选取内部零部件 选择被其它零部件包含的所有零件; 装配体中的零部件显示状态发生变化时,选择到的对象也会发生变化。 选取内部零部件示例 9.按大小选择 在弹出的窗口中调整或输入尺寸百分比,小于输入的装配体尺寸百分比的零件将被选中,隐藏、压缩的零件不会被选中。
SolidWorks大装配体技巧
SolidWorks大装配之技巧篇 大型装配体设计对于任何三维设计软件来说都是一个艰巨的挑战,操作与计算的延迟通常让人无法忍受。本文以图文和案例的形式为大家讲解利用SolidWorks处理大装配体的各种技巧,指导工程师进行大装配体设计。 大装配体是指达到计算机硬件系统极限或者严重影响设计效率的装配体,大装配体通常造成以下操作性能下降:打开/保存、重建、创建工程图、旋转/缩放和配合。影响大装配体性能的主要因素有:系统设置、装配设计方法、装配技巧、数据管理、操作系统和计算机硬件,本文主要讲解的是装配技巧。 一、配合技巧 (1)配合的运算速度由快到慢的顺序为:关系配合(重合和平行);逻辑配合(宽度、凸轮和齿轮);距离/角度配合;限制配合。 (2)最佳配合是把多数零件配合到一个或两个固定的零件,如图1所示。避免使用链式配合,这样容易产生错误,如图2所示。 (3)对于带有大量配合的零件,使用基准轴和基准面为配合对像,可使配合方案清晰,不容易产生错误。如图3所示的某减速器,零件之间有大量的同轴心配合,配合方案不清晰,一旦某个主要零件发生修改,就会造成配合面丢失,导致大量配合错误产生。而图4的配合方案就很清晰,一旦出错,很容易修改。 (4)尽量避免循环配合,这样会造成潜在的错误,并且很难排除,如图5所示。
(5)尽量避免冗余配合:尽管SolidWorks允许冗余配合(除距离和角度配合外),冗余配合使配合解算速度更慢,配合方案更难理解,一旦出错,更难排查。 (6)尽量减少限制配合的使用,限制配合解算速度更慢,更容易导致错误。 (7)如果有可能,尽量完全定义零部件的位置。带有大量自由度的装配体解算速度更慢,拖动时容易产生不可预料的结果。对于已经确定位置或定型的零部件,使用固定代替配合能加快解算速度。 (8)避免循环参考。大部分循环参考发生在与关联特征配合的时候,有时也会发生在与阵列零部件配合的时候。如果装配体需要至少两次重建才能达到正确的结果,那么装配体中很可能存在循环参考。如图6所示,装配体中零件B的边线和零件A的边线有一个重合的关联参考,配合时在零件A和B之间添加10mm的距离配合,那么每次重建都会出错,并且零件B每次重建都会伸长10mm,这就是循环参考的典型错误。 二、轻化装配体 使用轻化模式,可以显著提到大装配体的性能。当零部件是轻化状态,零部件只有部分模型信息被载入内存,其他信息只有在需要时才会被载入。表1所示的装配体操作不需要还原零部件。 装配体中零部件各种状态定义如下。 ◎还原状态:零部件的模型信息完全装入内存。
Solidworks 选项模板零件装配体工程图
. 三维参数化建模之模板 零件建模的好坏直接影响装配和参数化驱动工作的开展。零件建模思路和顺序得当,不仅可以便于装配,而且参数化驱动时返工较少,还可以大大减轻工作的难度。欲达到理想的建模效果,定义标准程度较高的模板就显得尤为重要。如果工作前期零件模板定制不够合理,势必造成重复性劳动过多,设计效率低。因此,必须制作适合自己所需要的模板,提高设计效率。 模板包括零件、工程图、装配体模板。将SolidWorks【工具】—【选项】—【文件属性】中与工作相关的选项如箭头、自定义属性、材质属性、字体等做统一规定,并作为模板使用。模板设定完成后,零件模板以格式*.prtdot保存,并命名为自命名文件名。工程图模板以格式*.drwdot 保存,并命名为自命名文件名,在定义工程图模板时应按照国标企标进行定义,尤其是标题栏的大小和字体的设置。装配体模板以格式*.asmdot保存,并命名为自命名文件名。设计模板的存放默认路径在SolidWorks的安装目录SolidWorks\lang\Chinese-simplified\data\Tutorial 和SolidWorks\data\Templates中。也可以【工具】—【选项】—【系统选项】—【文件位置】中设定文件模板的位置。并对【默认模板】进行更新。在设计过程中如无特殊要求,就无需重复修改选项参数,使用自定义模板即可。 模板具体设置如下: 一、【系统选项】: 路径: Solidworks—【工具】—【选项】—【系统选项】 需要调的部分有 1、工程图
专业资料word . (图中第一项“自动放置从模型插入的尺寸”是否需要打对勾?如果打在导入工程图的时候会自动把零件所做的尺寸都会添加进去,要不打勾,在导入工程图的时候我们可以指定把哪些尺寸放进来,…… 第二项谁有更好的方法,说是自动缩放,但实际效果并不是很理想。) 2、文件位置 文件位置,即模板存放的位置有两种方法: (1)、使用原来的SW默认的位置这种方法直接把做好的模板放到SW的默认位置SolidWorks\lang\Chinese-simplified\data\Tutorial覆盖原来的文件即可,如果新用户或SW 出现问题需要重装的时候得重新加载。 (2)、可以像图中“文件模板”一样用“添加”的方式把模板存放到我们指定的位置,新用户或者出现SW重装的问题,得重新设定。 专业资料word .
solidworks装配体
第10章装配设计 10.1 上机指导 10.1.1 物质动力 物质动力是以现实的方式查看装配体零部件运动的方法之一。启动物质动力功能后,拖动一个零部件时,此零部件就会向其接触的零部件施加作用力,并使接触的零部件在所允许的自由度范围内。物质动力可以在整个装配体范围内应用,拖动的零部件依次可以顺次推动一个零部件向前移动,继而推动另一个零部件移动。 例10.14物质动力实例(零件尺寸自由定义,只需画出大概图形即可) 界面尺寸 长度为800,孔在中间,孔尺寸及销尺寸随自己定义,主要目的在于学习装配及干涉检查;
(1) 单击【新建】按钮,出现【新建SolidWorks文件】对话框,选择【装配体】模 板,单击【确定】按钮,进入装配体窗口,出现【插入零部件】属性管理器,选中 【生成新装配体时开始指令】和【图形预览】 复选框,单击【浏览】按钮,出现【打 开】对话框,选择要插入的零件“底板”,单击【打开】按钮,单击原点,则插入 “底板”,定位在原点,插入其余零件,单击【保存】按钮,保存为“物质动 力实例”,如图10.61所示。 (2) 选择“底板”、“滑块”的右视图,单击【重合】按钮,单击【确定】按钮, 完成重合配合,如图10.62所示。 (3) 选择“底板”上表面和“滑块1”下表面,单击【重合】按钮,单击【确定】按钮 ,完成重合配合,如图10.63所示。 图10.61 物质动力实例 图10.62 “底板”、“滑块”右视图重合配合图10.63 “底板”上表面、“滑块1”下表面重合配合 (4) ,如图10.64所示。 (5) 单击【移动零部件】按钮,出现【移动零部件】属性管理器,选择【自由拖动】 选项,指针变成形状,展开【高级配合】标签,选中【标准拖动】单选按钮,按 住鼠标拖动,观察移动情况,如图10.65所示。 图10.64 完成其余零件装配图10.65 【自由拖动】 (6) 选中【碰撞检查】单选按钮,选中【碰撞时停止】、【高亮显示面】和【声音】复 选框,选择“手柄”,由于销钉的影响,滑块<1>被拖动到如图10.66所示位置,