管桁架钢结构制作通用工艺
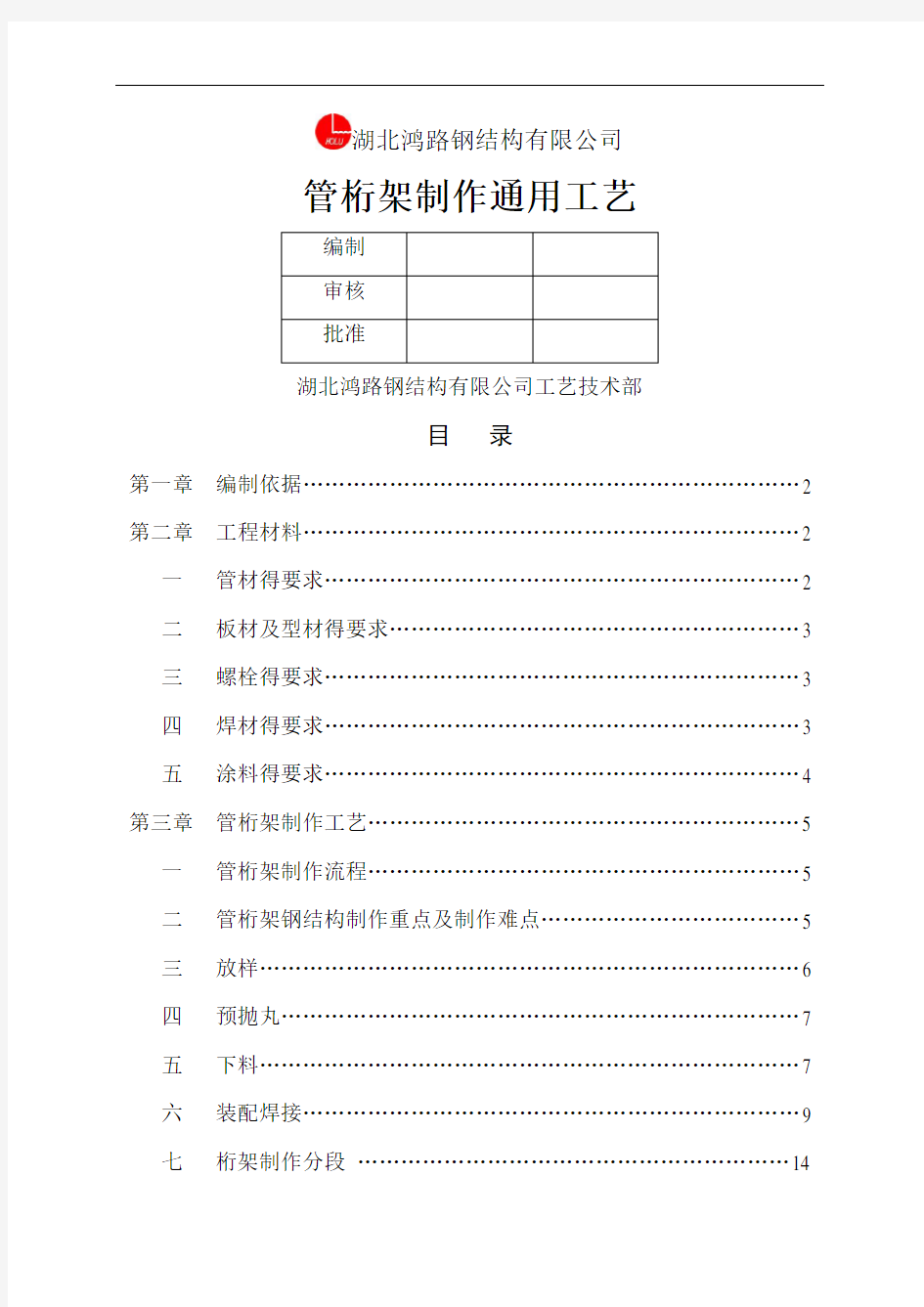
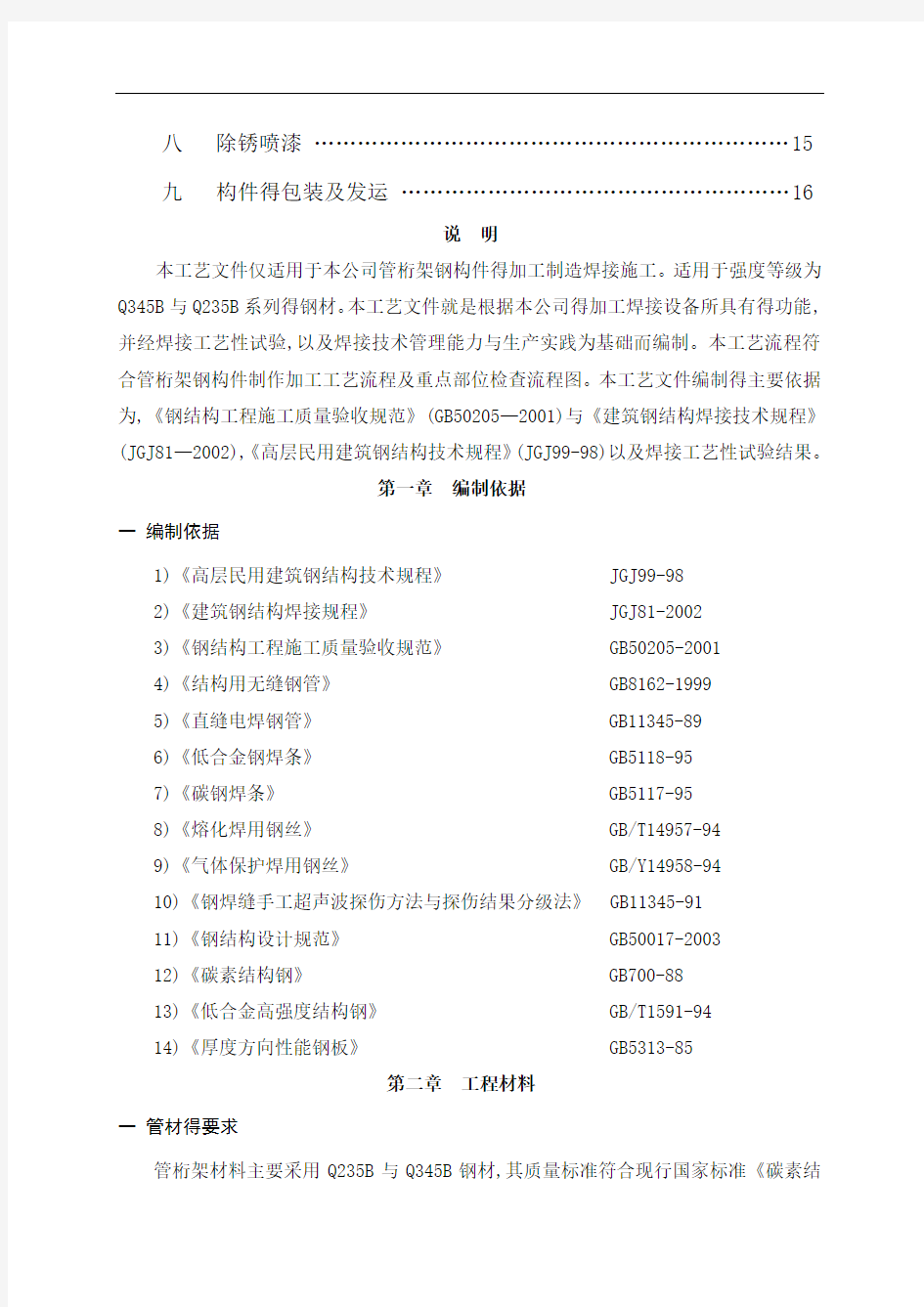
湖北鸿路钢结构有限公司
管桁架制作通用工艺
编制
审核
批准
湖北鸿路钢结构有限公司工艺技术部
目录
第一章编制依据 (2)
第二章工程材料 (2)
一管材得要求 (2)
二板材及型材得要求 (3)
三螺栓得要求 (3)
四焊材得要求 (3)
五涂料得要求 (4)
第三章管桁架制作工艺 (5)
一管桁架制作流程 (5)
二管桁架钢结构制作重点及制作难点 (5)
三放样 (6)
四预抛丸 (7)
五下料 (7)
六装配焊接 (9)
七桁架制作分段 (14)
八除锈喷漆 (15)
九构件得包装及发运 (16)
说明
本工艺文件仅适用于本公司管桁架钢构件得加工制造焊接施工。适用于强度等级为Q345B与Q235B系列得钢材。本工艺文件就是根据本公司得加工焊接设备所具有得功能,并经焊接工艺性试验,以及焊接技术管理能力与生产实践为基础而编制。本工艺流程符合管桁架钢构件制作加工工艺流程及重点部位检查流程图。本工艺文件编制得主要依据为,《钢结构工程施工质量验收规范》(GB50205—2001)与《建筑钢结构焊接技术规程》(JGJ81—2002),《高层民用建筑钢结构技术规程》(JGJ99-98)以及焊接工艺性试验结果。
第一章编制依据
一编制依据
1)《高层民用建筑钢结构技术规程》 JGJ99-98
2)《建筑钢结构焊接规程》 JGJ81-2002
3)《钢结构工程施工质量验收规范》 GB50205-2001
4)《结构用无缝钢管》 GB8162-1999
5)《直缝电焊钢管》 GB11345-89
6)《低合金钢焊条》 GB5118-95
7)《碳钢焊条》 GB5117-95
8)《熔化焊用钢丝》 GB/T14957-94
9)《气体保护焊用钢丝》 GB/Y14958-94
10)《钢焊缝手工超声波探伤方法与探伤结果分级法》 GB11345-91
11)《钢结构设计规范》 GB50017-2003
12)《碳素结构钢》 GB700-88
13)《低合金高强度结构钢》 GB/T1591-94
14)《厚度方向性能钢板》 GB5313-85
第二章工程材料
一管材得要求
管桁架材料主要采用Q235B与Q345B钢材,其质量标准符合现行国家标准《碳素结
构钢》(GB700-88)及《低合金高强度结构钢》(GB/T1591-94)得要求。其力学性能及碳、硫、磷、锰、硅含量得合格保证必须分别符合标准《结构用无缝钢管》(GB8162-1999)。二板材及型材得要求
1 所有钢材必须具有质量证明书, 并应符合设计要求及相关规范。对所有材料应按有关
规定进行抽样检验及抽样复检,取样方法与检验结果应符合国家现行标准得规定;
厚钢板必须依规定作UT检测,检查就是否有不符合规定得夹层存在、
2钢材应无脱皮裂伤、翘曲等缺陷,当钢材得表面有锈蚀、麻点或划痕等缺陷时,其深度不得大于该钢材厚度负允许偏差值得1/2;
3钢材表面锈蚀等级应符合现行国家标准《涂装前钢材表面锈蚀等级与除锈等级》GB8923规定得C级及C级以上;
4钢材端边或断口处不应有分层、夹渣等缺陷。
5主要钢材钢板及型钢得化学成分、力学性能与其它质量要求均应按相应得国家现行规范标准执行。
三螺栓得要求
1高强螺栓
六角头高强度螺栓及其螺母、垫圈得制作及技术条件应分符合中国国家标准GB1228-91、GB1229-91、GB1230-91、GB/T1231-91得规定。
2普通螺栓
C级螺栓,其性能等级为符合图纸得材质要求。普通螺栓及其螺母、垫圈得制作应分别符合中国国家标准GB5780-86、GB41-86、GB95-86得有关规定。
四焊材得要求
1焊材得品种、规格、性能等应符合现行国家产品标准与设计要求;
2手工焊接所用焊条型号应与母材金属强度相适应。自动焊接或半自动埋弧焊接所用得焊丝与焊剂等,应与母材金属强度相适应。所有焊条必须有合格证明焊接材料与母材得匹配应符合设计要求及国家现行行业标准得规定;
3对用于一级焊缝等重要钢结构得焊接材料应进行抽样复验,复验得数量、方法及结果应符合现行国家产品标准与设计要求;
4严禁使用有药皮脱落、焊芯生锈等缺陷得焊条;焊剂应按规定进行烘焙后使用。
5焊材使用方法如下表所示
6 焊剂在使用前需按规定进行烘焙:SJ101需300℃烘焙2小时,HJ431需250℃烘焙2
小时。
五涂料要求
各种涂料必须具备产品合格证书与混合涂料得配料说明书。因存放过久,超过使用期得涂料,应取样进行质量检测,检测项目按产品标准得规定或设计部门得要求进行。
1 涂料色泽应按设计要求,符合《漆膜颜色标准》GB3181-95色卡编号,必要时可作样板,封存对比。
2 涂料调制应搅拌均匀,防止沉淀,影响色泽,当天使用得涂料应在当天配置。
3 不得随意添加稀释剂。当粘度过大,不便涂(喷)刷时,可适量加入,但一次添加剂量不得超过5%。
第三章管桁架制作工艺
一管桁架制作流程
管桁架制作流程示意图如下:
二
1钢管相贯线坡口切割
由钢管组成得桁架,有大量得管子相贯坡口。管子相贯线就是一个空间曲线,且其坡口角度就是随曲线得变化而变化得,管子相贯线得切割好坏直接关系到桁架得焊接质量及外观质量,就是制作过程得关键。采用数控相贯线切割机进行切割,能够根据放样程序在电脑上控制自动切割,并能一次性坡口成形,坡口角度可随圆周变化,以满足相贯线接头处趾部、根部与侧部得不同焊接要求。
2 钢管线性弯弧
空间桁架,主桁架弦杆一般就是空间曲线,管子得线型弯弧必须光顺美观且要达到标准要求,为确保钢管弯曲圆滑成形,必须防止起鼓、起皱。
3 节点制孔
钢结构得零件钻孔采用数控平面钻或摇臂钻进行钻孔,为了确保钻孔精度与质量,采用模钻时均须有放样划线划出基准轴线与孔中心,采用数控钻得首次加工品均
需检验合格后才能批量钻孔,零件、部件、构件钻孔后均需检验合格才准转入其它工序。
4 焊接顺序与焊接余量得控制
由于焊接变形会影响构件得整体精度尺寸,焊接过程中应制定合理得焊接顺序与焊接方法。
1)对于弦杆节点得焊接余量,应首先试作一实验节点,焊接完成后进行测量,根据测
量值确定焊接余量得大小。
2)桁架一般首先焊接中间节点,再向桁架两端节点扩展。
3)上下弦杆一般首先焊接下弦杆,再焊接上弦杆,保证整体桁架不会产生下挠得变形。
三放样
1放样基本要求
所有构件应按照细化设计图纸及制造工艺得要求,进行手工1:1放大样或计算机得模拟放样,核定所有构件得几何尺寸。放样检验合格后,按工艺要求制作必要得角度、槽口、制作样板与胎架样板。样板得允许偏差如下表
2构件收缩余量得要求
构件收缩余量图纸与工艺文件有要求时按照要求执行,没有要求时按照下表执行:
四预抛丸
1一般管桁架组装后整体尺寸都比较大,所以在组装前所有钢管与零部件都必须预抛丸处理。
2除锈等级应达到GB8923-88标准Sa2、5级,钢材除锈经检验合格后,应在六小时内喷涂防锈底漆。
3涂漆时应注意,相贯切割端与需对接端头不允许涂刷油漆。
五下料
1所有钢管件建议应采用数控相贯线切割机进行下料,如管径过大可采用钢管自动切割机下料,钢管两端对接坡口55度;
2对主管原则上长度按定尺采购,下料时放焊接收缩余量,焊接收缩量根据图纸或工艺要求进行预留,无要求时按照以下要求进行预留:钢管壁厚≤6mm,每个节点预留1mm;钢管壁厚≥8mm,每个节点预留1.5mm;具体坡口如下图,
主管端头坡口示意图
3对于支撑腹杆,下料时,焊接收缩量根据图纸或工艺要求进行预留,无要求时按照以下要求进行预留:钢管壁厚≤6mm,预留1-1.5mm;钢管壁厚≥8mm,预留1、5-2mm;下图为相贯线切割机下料后端头拼装得形状示意图。
4下料后,必须立即对构件或杆件进行检验,当钢管不平直及有局部凹陷时,应对钢管进行矫正;
5下料后,用油漆笔在杆件端部工整书写杆件号,同榀桁架得杆件放在一起,如距离拼装
场地较远,可进行打包,并挂标识铁牌,在铁牌上写明杆件所用得构件编号、杆件号、数量。在下料倒运过程中,尽量避免磕碰,弯曲变形,用吊带进行吊装。
6 钢管、型钢切割前应事先排料,钢管桁架分段弦杆应以钢管最大利用长度对接,但应使接头至腹杆与弦杆节点得距离大于或等于500mm 。腹杆对接时,接头位置原则上不大于杆件长度得三分之一(具体视管子来料情况定)但不小于500mm 。
7钢板得切割,应根据放样套料图及数控切割下料图,分别进行数控自动切割、半自动切割。
8节点板与加劲板用剪板机、数控火焰切割机、半自动切割机下料。,不允许采用手工切割下料。 9弯管
(1)杆件弯圆冷弯圆管通常采用拉弯与压弯得办法。拉弯加工要求提供弯管管件得半径、
管长(中心线长度)。压弯加工要求提供弯管管件得拱高、管内外弦长。 (2)弯曲后,钢管直径变化不大于3mm,壁厚变化不大于1mm,钢管表面不能出现折痕与凹
凸不平得现象。然后切割端头,按前述方法下料。
(3)较大半径与板厚得圆管在工厂内一般采用放地样进行火焰煨弯。煨弯过程中注意控
制温度,防止起皱与急弯得产生。 10钢管得对接:钢管与钢管之间得对接,内设衬
管,在胎架上进行,具体形状尺寸如下图:
六 装配焊接
1 圆管桁架组装得质量要求
(1) 钢管对接焊缝同其它焊缝得间距不小于200mm 。直缝焊接钢管对接时,两纵缝在
圆周上得间距不小于200mm(设计有特别要求得按设计执行)。
(2)原则上腹杆不允许对接,腹杆长度超过1700mm 时允许对接,且每根腹杆中最多只
管
对接坡口形式
不同管壁的主管对接示意图
衬圈
允许有一个对接接头,最短得管子不能小于2倍得管子直径且不能小于800mm。
对接接头要求为一级焊缝(设计有特别要求得按设计执行)。
(3) 主管对接焊缝应距离桁架腹杆交点200mm以上(设计有特别要求得按设计执
行)。
(4) 构件不要求设引弧、熄弧板得角焊缝,终止处必须进行包角焊,引弧与熄弧端相
距10mm以上。
(5) 圆管桁架组装、预拼在胎架或者平台上,按照工艺规定得工序进行,组装前对零
部件进行检查,组装得允许偏差见下表。
(6)由于桁架结构基本相同,将选择有代表性得桁架进行工艺分析。为保证各主管尺寸形
状得正确性,在装配前进行预拼装,在连接处增加连接耳板,用螺栓进行连接(不焊),检查其正确性,如有不符立即进行矫正、整改。
(7)对桁架主管及相互之间得腹杆在装配平台上利用组装胎架(如下图)进行装配,装配
顺序为在胎架上先组装上弦及下弦得主管,确定其空间位置,然后装配支管并定
位、焊接。
方型桁架装配胎架示意图
三角形桁架装配胎架示意图
(8)拼装胎架将桁架主管固定在装配平台上,再用龙门吊将已接好得主管放置在如
图对应位置,固定定位块,调节调整板,确保主管之间得相对位置;
如组装胎架阻挡单支腹杆装
配,可暂不组装,等整品桁架装
焊牢固吊离胎架后再组装
方形桁架装配位置示意图
如组装胎架阻挡单支腹杆装
配,可暂不组装,等整品桁架装
焊牢固吊离胎架后再组装
三角形桁架装配位置示意图
(9) 在胎架上对主管得各节点得中心线进行划线;
(10)桁架得结构形式为弦杆贯通,腹杆焊接在弦杆上,其节点为腹杆与弦杆直接焊
接,直接焊接得相贯节点,其形式如下:
(12)装配腹杆并定位焊,对腹杆接头定位焊时,不得少于4点;定位焊后检验定位焊
后组件得正确性。
2 桁架得焊接要求
(1)管桁架组装定位好后,对纵横桁架进行焊接,焊接时,为保证焊接质量,尽量避免
仰焊、立焊。
(2)桁架结构采用腹杆与弦杆直接焊接得相贯节点,弦杆截面贯通,腹杆焊接于弦杆
之上,焊接时,对如下图所示节点,当支管与主管得夹角小于90度时,腹杆端部
得相贯焊缝分为A,B,C,D四个区域,其中A,B区采用等强坡口对接熔透焊缝,D
区采用角焊缝,焊缝高度为1、5倍管壁厚,焊缝在C区应平滑过渡。当腹杆与
弦杆相垂直时,腹杆端部得相贯焊缝分为A,B两个区域,当腹杆壁厚不大于5mm
时可不开坡口,由于在趾部为熔透焊缝,在根部为角焊缝,侧边由熔透焊缝逐渐
过度到角焊缝,同时考虑焊接变形,因此必须先焊趾部,再焊根部,最后焊侧边。
A:趾部 B:侧边 C:过渡区 D:根部
节点焊缝位置分区
(3)桁架支座节点处得焊接,其加劲肋、短钢柱与支座底板之间及加劲肋与短钢柱之
间均用双面角焊缝连接,满焊。
(4)相贯接头部分焊透焊缝各区坡口形状与尺寸细节应符合下图要求;
(5)管材T、Y、K形相贯接头角焊缝得计算厚度
七桁架制作分段
1 空间桁架超长时,在地面上根据桁架得长度制作胎架,为保证桁架弧线得尺寸精
度,桁架按卧位平放得方式进行拼装,如下示意图所示。
2 桁架主管得各个分段部位用如下图方法用螺栓临时固定;
衬圈
主管之间临时连接固定示意图
3在钢平台上,划出桁架各弦杆、腹杆中心线及轮廓线得投影线。根据桁架长度设置弧形胎架。拼装胎架放线时,应考虑到桁架位置得逐步变化
4 桁架预拼装允许偏差见下表
构件类型项目允许偏差
梁、桁架跨度最外端两安装孔或两端支撑面最外侧
距离
+5、0
-10、0 接口截面错位2、0 拱度
设计要求起拱±L/5000
设计未要求起拱
L/2000
0 节点处杆件轴线错位4、0
4 桁架拼装焊接固定后再根据工程要求进行分段拆开。
5 拆开后分段后包括散件出厂现场拼装得钢管,必须做好标识,在两端各100mm处作中
心线样冲标记与现场对接编号。
八除锈喷漆
1 由于桁架杆件都经过预抛丸除锈处理,喷漆前需使用砂轮机与风动工具清除桁架表面
残渣物后再进行喷漆。
2 涂漆时应注意,凡就是高强螺栓连接范围内不允许涂刷油漆或有油污,工地焊接部位
不喷漆。
3 使用油漆干膜电子测厚仪测量,每个构件检测5处,每处得数值为3个相距50mm测点涂层干膜厚
度得平均值。
4 涂装检测特别注意就是否有因搬运所造成得撞伤、碰伤及变形而损伤油漆涂膜。
5 补漆:
(1)预涂底漆钢材如表面因滚压、切割、焊接或安装磨损,以致油漆损坏或生锈时,必须
用喷珠或电动工具清理后,再行补漆。
(2)油漆涂装后,漆膜如发现有龟裂、起皱、刷纹、垂流、粉化、失光等现象时,应将漆
膜刮除以砂纸研磨后重新补漆。
(3)油漆涂装后,如有发现起泡、裂陷洞孔、剥离生锈或针孔等现象时,应将漆膜刮除并
经表面处理后,再按规定涂装间隙层次予以补漆。
(4)补漆材料必须采用与原施工相同性质得材料。
九构件得包装及运输
产品制造完成入库后,应该按规定要求进行包装,临时堆放应尽可能堆放在平直不积水得场地,厂内、外堆放都必须整齐、合理、标识明确,必要时做好防雨、雾处理,对接面应得到确实保护。按桁架安装顺序做好发运得准备。