掘进机截割部设计
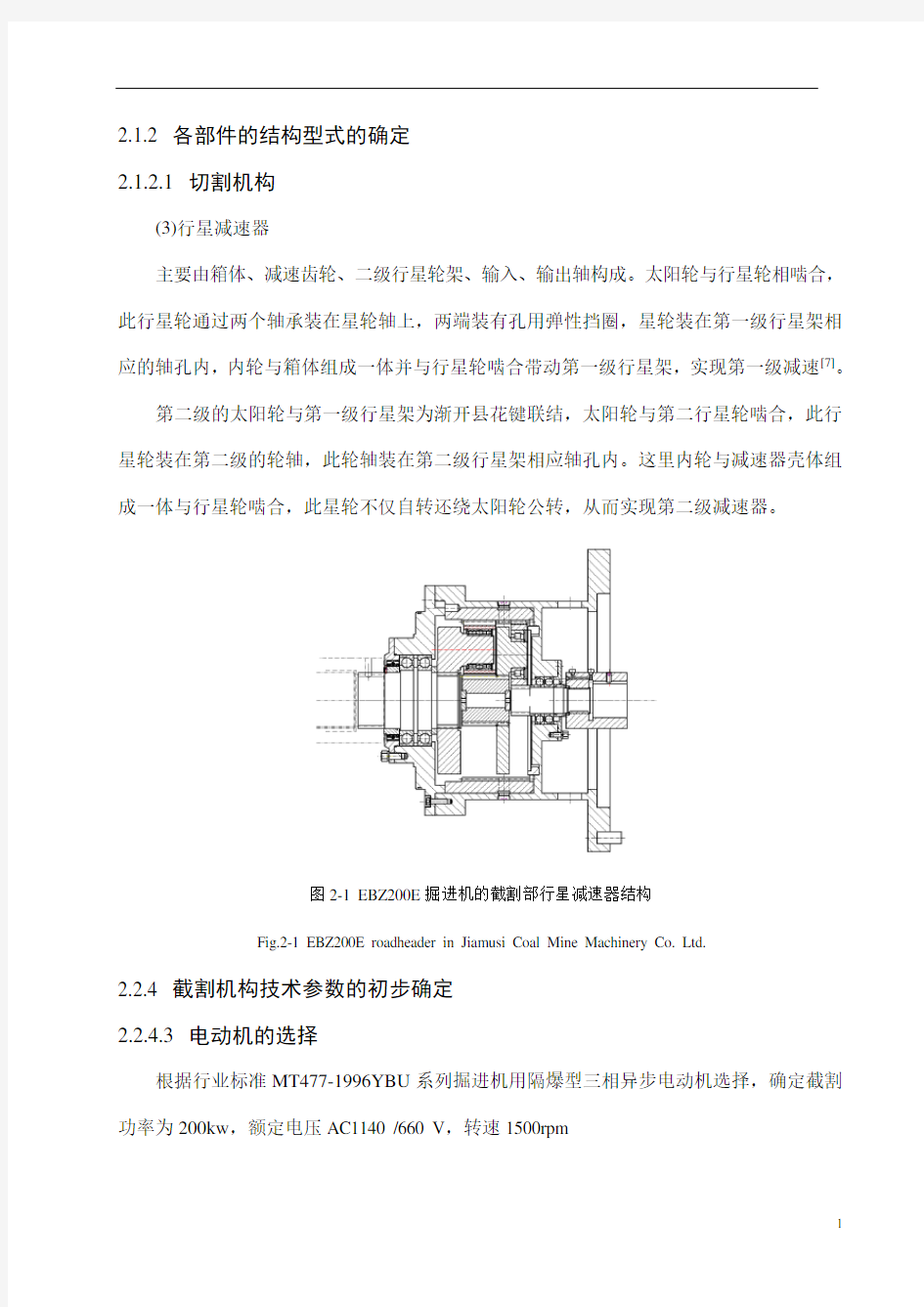

2.1.2 各部件的结构型式的确定
2.1.2.1 切割机构
(3)行星减速器
主要由箱体、减速齿轮、二级行星轮架、输入、输出轴构成。太阳轮与行星轮相啮合,此行星轮通过两个轴承装在星轮轴上,两端装有孔用弹性挡圈,星轮装在第一级行星架相应的轴孔内,内轮与箱体组成一体并与行星轮啮合带动第一级行星架,实现第一级减速[7]。
第二级的太阳轮与第一级行星架为渐开县花键联结,太阳轮与第二行星轮啮合,此行星轮装在第二级的轮轴,此轮轴装在第二级行星架相应轴孔内。这里内轮与减速器壳体组成一体与行星轮啮合,此星轮不仅自转还绕太阳轮公转,从而实现第二级减速器。
图2-1 EBZ200E掘进机的截割部行星减速器结构
Fig.2-1 EBZ200E roadheader in Jiamusi Coal Mine Machinery Co. Ltd.
2.2.4 截割机构技术参数的初步确定
2.2.4.3 电动机的选择
根据行业标准MT477-1996YBU系列掘进机用隔爆型三相异步电动机选择,确定截割功率为200kw,额定电压AC1140 /660 V,转速1500rpm
表2-2电动机的基本参数[13]
功率/kW 效率η/%
功率因数
/cos?堵转转矩堵转电流最小转矩最大转矩冷却水流
量/31
m h-
?
额定转矩额定电流额定转矩额定转矩
200 92 0.85 2.0 6.5 1.2 2.6 1.3
3悬臂式掘进机截割机构方案设计
3.1截割部的组成
掘进机截割部主要由截割电动机、截割机构减速器、截割头、悬臂筒组成。见图3-1.截割部是掘进机直接截割煤岩的装置,其结构型式、截割能力、运转情况直接影响掘进机的生产能力、掘进效率和机体的稳定性,是衡量掘进机性能的主要因素和指标。因此,工作部的设计是掘进机设计的关键。
1 截割头
2 伸缩部
3 截割减速机
4 截割电机
图3-1 纵轴式截割部
?3.2 截割部电机及传动系统的选择
切割电机的选择应根据工作条件选取,由设计要求可知,所设计的掘进机可截割硬度为小于85Mpa的中硬岩,查表2-1可知应该选取功率为200KW的截割电动机。电机动力经传动系统传向截割头进行截割,且机体为焊接结构,前端与行星减速器相联,后端联接回转台。电机输出力矩,通过花键套传递给减速器,再由花键套传到主轴,主轴通过内花套键与截割头相联,把力(矩)传递到割头上,截割头以此方式进行工作。
3.5 传动方案设计
悬臂式掘进机的传动方式为电机输出轴通过联轴器将转矩传递给减速器的输入轴,减速器输出轴通过联轴器将转矩传递给主轴,主轴带动截割头转动。
3.5.2 传动类型的设计
由于行星齿轮传动具有多分流传动、低压力啮合、作用力平衡和运行多变性等一系列特点,所以在同等工作条件下与定轴齿轮传动相比,行星齿轮传动具有外形尺寸小,重量轻、传动效率高、工作可靠和同轴传动等许多突出优点,因此国内外纵轴式掘进机的截割结构传动系统均采用行星齿轮传动,以期在提高承载能力、效率和可靠性的同时,尽可能地减轻重量、缩小外廓尺寸、降低制造成本。要求传动装置体积小、结构紧凑,并满足一定的强度要求和减速比要求。因此,这种工作机构的传动装置多采用行星齿轮传动,以满足以上要求。
如果采用一级减速,则传动比太大,导致齿轮结构很难满足现实要求,因此,决定采用2级齿轮减速。齿轮系的选取有定轴轮系和周转轮系两种。由于悬臂采用内伸缩式,电动机、联轴器、的减速器相对于轴向是固定的,从传动装置体积小、结构紧凑等考虑,采用双级行星齿轮传动。工作机构传动系统布置图3-1。
图3-6传动系统
Fig 3-6 The transmission system
截割电动机通过联轴节、中心轮、行星轮、内齿轮、中心轮、行星轮和联轴节驱动切割头进行切割。
中心轮固定在悬臂主轴上,行星轮与之啮合,同时又与一个内齿轮啮合,内齿轮固定在箱体上。
使减速器的强度能满足电动机的最大转矩和动载荷,即使电动机过载以至停止,减速器也不至于出现机械故障。若减速器的强度不能满足电动机的最大转矩,必须设过载保护装置,如安全销、压紧弹簧、液压或摩擦联轴器等。
4截割部减速机构设计
4.1 电机选择
4.1.1 截割速度
根据设计要求,截割头转速n=46r/min
4.1.2 截割功率
根据所截割煤岩的特性、工作机构的类型,参照类似工作条件、工作范围的国内外各种掘进机,来选定截割电机功率。
表4-1 我国主流掘进机的主要技术性能表
Tablet.4-1 Table of mainly performance of roadheader in China 技术参数AM50 S-100 EBJ-120TP EBZ200TY S150J ELMB-75C EBJ-200SH 断面/㎡6~18 8~23 8~18 9~21 9~23 6~17 8~24 可截割硬度
/MPa
60 70 60 80 80 70 80~100 机重/t 26.8 27 36 51.5 44.6 23.4 53
总功率/kW 174 145 190 250 205 130 314
截割功率/kW 100 100 120 200 150/80 75 200
适应坡度/(°)16 16 16 16 16 16 16
系统压力/MPa 16 16 16 23 16 16 16
外形尺寸/m×m×m 7.5×2.1
×1.65
12.2×2.8
×1.8
8.6×2.1
×1.55
9.8×
2.55×
1.7
9.0×2.8
×1.8
8.22×
2.5×
1.56
10.8×2.7
×1.5
生产厂家淮南佳木斯太原分院太原分院佳木斯南京晨光上海分院
根据设计要求,截割硬度小于85Mpa,选择截割功率为200kW。
4.1.3选择电机
根据截割功率选择电动机型号为:YBUD-200隔爆电动机
其主要性能数据如下:
表4-1
Tablet.4-1
4.2 截割减速器结构设计
根据性能要求:传动比大,输入轴与输出轴具有同轴性,选用行星齿轮传动。
因传动比较大,采用两级行星传动,传动系统简图如图4-2:
图4-1传动系统简图
Fig 4-1 The diagram of transmission system
行星减速器主要由箱体、减速齿轮、二级行星轮架、输入、输出轴构成。太阳轮与行星轮相啮合,此行星轮通过两个轴承装在星轮轴上,两端装有孔用弹性挡圈,星轮装在第一级行星架相应的轴孔内,内轮与箱体组成一体并与行星轮啮合带动第一级行星架,实现第一级减速[7]。
第二级的太阳轮与第一级行星架为渐开县花键联结,太阳轮与第二行星轮啮合,此行星轮装在第二级的轮轴,此轮轴装在第二级行星架相应轴孔内。这里内轮与减速器壳体组成一体与行星轮啮合,此星轮不仅自转还绕太阳轮公转,从而实现第二级减速器。
为了尽量减小减速器体积和重量,将行星减速器的外壳与两级行星传动的内齿圈设计型号额定
功率
同步
转速
满载
转速
YBUD-200200KW 1500
r/min
1460
r/min
成一体。这种结构使得低速级和高速级的内齿圈齿数相等,整个轮系中齿轮的模数也相等。
4.2.1 传动比的分配
确定总传动比并根据传动比分配理论分配各级传动比,并选择齿轮齿数 i 总=0/w n n =1460/46=31.739 高速级的传动比:
1i 6.546=
低速级的传动比:
21
4.849i
i i =
= 4.2.2 各轴功率、转速和转矩的计算
按指导书表4.2-9确定各零件效率取: 联轴器效率 联η=0.99
齿轮啮合效率齿η=0.97(齿轮精度为7级) 滚动轴承效率承η=0.98 滚筒效率 卷筒η=0.96 开式齿轮啮合效率开齿η=0.95 0轴(电动机轴): P 0=P r =200kw n 0=1460r/min
T 0=9.55P 0/n 0=9.55×200×103
/1460=1308.22N.m Ⅰ轴:
P 1= P 0×联η=P 0×联η=200×0.99=198kw n 1=1460r/min
T 1=9.55×P 1/n 1=9.55×198×103/1460=1295.14N.m
Ⅱ轴:
P 2=P 1×12η=P 0×齿η×承η=200×0.97×0.98=190.12kw n 2= n 1/i 1=1460/6.546=223.04r/min
T 2=9.55×P 2/ n 2=9.55×190.12×103/223.04=8127.33N.m Ⅲ轴:
P 3=P 2×23η= P 2×齿η×承η=190.12×0.97×0.98=180.73kw n 3= n 2/2i =223.04/4.849=45.997r/min
T 3=9.55×P 3/ n 3=9.55×180.73×103/45.997=37523.57N.m
4.2.3 齿轮部分设计
4.2.3.1 高速级齿轮传动的设计
(1)选择齿轮材料:
太阳轮选用45#钢 调质处理HRC1=56—62 行星轮选用45#钢 调质处理HRC2=56—62 (2)按齿面接触疲劳强度设计计算:
齿宽系数 d ψ,查教材表8-23按齿轮相对轴承为非对称布置,取d ψ=0.5 齿轮齿数的选择: 传动比条件:
3113/1z z i =-
同心条件(各齿轮模数相同):
3122z z z =+
均布条件(N 为整数):
13()/z z k N +=
邻接条件:
*122()/sin(180/)2a z z k z h +>+o
根据以上四个条件选择1z =21 2z =57 3z =135 k=3
实际传动比 u=Z 3/Z 1+1=7.429
传动比误差u u /?=(7.429-7.399)/7.429=0.0041 误差在±5%内,合适 1)确定齿轮传动精度等级,
比照公式:(0.0130.022)t v n =--(4-1) 估取圆周速度V t =6.08m/s,参考教材表8-14,8-15选取II 公差组7级 2)太阳轮分度圆直径d 1, 由下式得:
1d ≥
(4-2) a 齿宽系数d ? : 查表按齿轮相对轴承为非对称布置,取d ?=0.8 b 太阳轮转矩T 1 : T 1 =108494N.mm
c 载荷系数K : K=K A K v K βK α (4-3) 使用系数K A : 查表得K A =1.3 动载荷系数K v : 查表得K v =1.2 齿向载荷分布系数K β: 查表取K β=1 齿间载荷分配系数K α :由下式及其β=0得
1211[1.88 3.2(
)]cos Z Z γαεεβ==-+=[1.88-3.2(112080
+)]=1.68 查表并插值得 K α=1.16
则载荷系数K 的初值K t K t =1.3×1.2×1×1.16=1.81
d 弹性系数E Z : 查表取得E Z
e 节点影响系数(120,0x x β===): 根据条件查图可得H Z =2.5
f 重合度系数Z ε : 查表(0βε=) ,取Z ε=0.87
g 许用接触应力[]H δ: lim1[]/H H N w H Z Z S δσ=?? (4-4)
接触疲劳极限应力lim1H σ,lim 2H σ,查表可得lim1H σ=570N/mm 2, lim 2H σ=460N/mm 2
应力循环次数N : 1016060146030085 1.0510h N njL ==????=?
21/N N u ==101.0510/7.429?=1.42×109
则查表得出接触强度的寿命系数12,N N Z Z (不允许有点蚀),121N N Z Z == 硬化系数w Z : 根据设计条件查图可取w Z =1
接触强度安全系数S H ,按照一般可靠度查S Hmin =1.0—1.1,取S H =1.1,
1[]H δ=570×1×1/1.1=518N/mm 2 2[]H δ=460×1×1/1.1=418N/mm 2
所以太阳轮分度圆直径d 1的设计初值d 1t 为
173.49t d mm ≥=
齿轮模数m : m= 11/t d Z =73.49/21=3.50 取m=4 太阳轮分度圆直径的参数圆整值: 11't d Z m ==21×4=84mm
圆周速度v : 11'/60000841460/60000 6.42/t v d n m s ππ==??= 与估取值 6.08/t v m s =相近,对K V 取值影响不大,不必修正K V 所以可以取定: K V =K Vt =1.2,K=K t =1.81 太阳轮分度圆直径d 1: d 1=1't d =84mm 行星轮分度圆直径d 2: d 2=mZ 2=4×57=228mm 中心距a : a=
12()4(2157)
16022
m Z Z ++==mm 齿宽b : 1min 0.573.4936.74d t b d ?=?=?=mm ,取37 行星轮齿宽b 2 : b 2=b=37mm
太阳轮齿宽b 1: b 1=b 2+(5--10) 取b 1=45 内齿圈分度圆直径:d 3=mZ 3=4×135=540mm
4.2.3.2 低速级齿轮传动的设计
(1)选择齿轮材料:
太阳轮选用45#钢 调质处理HRC1=56—62 行星轮选用45#钢 调质处理HRC2=56—62 (2)按齿面接触疲劳强度设计计算:
齿宽系数 d ψ,查教材表8-23按齿轮相对轴承为非对称布置,取d ψ=0.5 齿轮齿数的选择: 传动比条件:
3113/1z z i =-
同心条件(各齿轮模数相同):
3122z z z =+
均布条件(N 为整数):
13()/z z k N +=
邻接条件:
*122()/sin(180/)2a z z k z h +>+o
根据以上四个条件选择1z =29 2z =53 3z =135 k=3 实际传动比 u=Z 3/Z 1+1=5.5
传动比误差u u /?=(5.5-5.481)/5.5=0.0035 误差在±5%内,合适
1)确定齿轮传动精度等级比照公式:
(0.0130.022)t v n =--(4-5) 估取圆周速度V t =1.29m/s,参考教材表8-14,8-15选取II 公差组7级 2)太阳轮分度圆直径d 1, 由下式得:
2d ≥
(4-6) a 齿宽系数d ? : 查表按齿轮相对轴承为非对称布置,取d ?=0.5 b 太阳轮转矩T 2 : T 2 =7287860N.m m
c 载荷系数K : K=K A K v K βK α (4-7) 使用系数K A : 查表得K A =1.3 动载荷系数K v : 查表得K v =1.2 齿向载荷分布系数K β: 查表取K β=1
齿间载荷分配系数K α : 由下式及其β=0得
1211[1.88 3.2(
)]cos Z Z γαεεβ==-+=[1.88-3.2(112080
+)]=1.68 查表并插值得 K α=1.16
则载荷系数K 的初值K t K t =1.3×1.2×1×1.16=1.81 d 弹性系数E Z : 查表取得E Z
e 节点影响系数(120,0x x β===): 根据条件查图可得H Z =2.5
f 重合度系数Z ε : 查表(0βε=) ,取Z ε=0.87
g 许用接触应力[]H δ: lim1[]/H H N w H Z Z S δσ=?? (4-8) 接触疲劳极限应力lim1H σ,lim 2H σ,查表可得lim1H σ=570N/mm 2, lim 2H σ=460N/mm 2 应力循环次数N : 816060197.3230085 1.4210h N njL ==????=?
21/N N u ==81.4210/5.5?=2.58×107
则查表得出接触强度的寿命系数12,N N Z Z (不允许有点蚀),121N N Z Z == 硬化系数w Z : 根据设计条件查图可取w Z =1
接触强度安全系数S H ,按照一般可靠度查S Hmin =1.0—1.1,取S H =1.1,
1[]H δ=570×1×1/1.1=518N/mm 2 2[]H δ=460×1×1/1.1=418N/mm 2
所以太阳轮分度圆直径d 1的设计初值d 1t 为
2113.8t d mm ≥=
齿轮模数m : m= 22/t d Z =113.8/29=3.92 取m=4 太阳轮分度圆直径的参数圆整值: 11't d Z m ==29×4=116mm
圆周速度v : 12'/60000120197.32/60000 1.24/t v d n m s ππ==??= 与估取值 1.29/t v m s =相近,对K V 取值影响不大,不必修正K V 所以可以取定: K V =K Vt =1.2,K=K t =1.81 太阳轮分度圆直径d 1: d 1=1't d =116mm 行星轮分度圆直径d 2: d 2=mZ 2=4×53=212mm 中心距a : a=
12()4(2953)
16422
m Z Z ++==mm 齿宽b : 1min 0.5113.856.9d t b d ?=?=?=mm ,取57 行星轮齿宽b 2 : b 2=b=57mm
太阳轮齿宽b 1: b 1=b 2+(5--10) 取b 1=65mm 内齿圈分度圆直径: d 3=mZ 3=4×135=540mm
4.2.4 轴设计及校核
输入轴、中间空心轴和输出轴只承受转矩作用而无弯矩作用,所以在设计计算时只需按照许用转应力计算公式计算出最小轴径,然后按照轴上零部件进行设计,不需要再对轴进行校核计算 输入轴:
材料40Cr (100.798A =:) 功率158.4P =KW 转速1460n =r/min
10047.7d ≥==输入 (4-9) 输出轴:
材料40Cr (100.798A =:) 功率143.14P =KW 转速36n =r/min
100158.4d ≥==输出 (4-10) 中间空心轴
材料40Cr (100.798A =:) 功率150.58P =KW 转速197.32n =r/min
0.53d
d
ν=
= (4-11) ()()
3
3
4
4
1
1
1.03110.53ν==-- (4-12) ()3
3341110100 1.03108.793.59
1P d A n ν≥=??=-g 中间 (4-13) 行星轮轴
行星轮轴不仅承受啮合作用力对其施加的载荷,而且还要承受行星齿轮的离心力对其施加的载荷。
图4-2齿轮运动简图 Fig.4-2 The diagram of gear's load
行星轮c 作用于中心轮a 的切向力: 高速级: 111120001036.11
20007771'388.89
a ca p a T F n d =
=?=? N (4-14)
低速级: 222220007287.86
200024987'3194.44
a ca p a T F n d =
=?=?
中心轮a 作用于行星轮c 的切向力:
高速级: 11-7771ac ca F F =-= (4-15) 低速级: 2224987ac ca F F =-=-
内齿轮b 作用于行星轮c 的切向力:
高速级: 11-7771bc ac F F == (4-16) 低速级: 2224987bc ac F F ==-
转臂x 作用于行星轮c 的切向力:
高速级: 11215542xc ac F F =-= (4-17) 低速级: 22249974xc ac F F =-=
转臂x 所受的作用力:
高速级: 1115542cx xc F F =-=- (4-18) 低速级: 2249974cx xc F F =-=-
内齿轮b 所受的切向力:
高速级: 117771cb bc F F =-= (4-19) 低速级: 2224987cb bc F F =-=
啮合作用力载荷为中心轮a 和内齿轮b 作用于行星轮c 的切向力之和:
高速级: ac1bc1ac1215542F F F F =+==-啮合1
(4-20) 低速级: ac2bc2ac2249974F
F F F =+==-啮合2
离心力:
高速级:1122
106.7310198L c x
x F d bn r λ-=?= (4-21) 低速级:1122
106.731073L c x
x F d bn r λ-=?= 两种作用力在同一平面内,方向垂直,其合力为:
高速级:
115543c F == (4-22)
低速级:
49975F ==c2
行星轮轴最可能的失效形式是剪断,应校核其剪切应力 材料40Cr []4052τ=: 高速级: []122
14415543
5.53.1460c F d ττπ?=
== (4-23)
低速级: []222
24449975
6.373.14100
c F
d ττπ?=
==
4.2.5 轴承设计及校核
在结构要求很紧凑时.可选用无内圈和外圈的滚针轴承,此时滚道就是行星轮孔壁和行星轴表面。
由于掘进机截割机构行星减速器的外廓尺寸受到极大的限制,行星齿轮直径太小 ,其轴承的选用便是要解决的难题之一。
根据上述限制条件,一般要选择内外径之差如此小的轴承,通常会首先选用滚针轴承或滑动轴承可是采用滚针轴承虽能满足尺寸方面的要求,但在承受强烈冲击及重负荷的工况下,其使用寿命不能满足可靠性方面的要求。而滑动轴承因偏载、润滑等问题,同样保证不了可靠性要求。为了解决这一难题,在该机的设计中采用了另一种形式,即用行星齿轮内孔充当轴承滚子的外圈滚道,行星轴圆柱面充当本轴承滚子的内圈滚道,在内外滚道间充填短圆柱滚子,与行星齿轮、行星轴等共同组成行星齿轮轴承。 在该轴承的设计中,重点考虑了以下几个方面:
1)结构。短圆柱滚子安装在齿轮内孔和轴之间阀。在圆周上排列着的短圆柱滚子问设有保持架,在轴向方向因有多排短圆柱滚子,排与排之间设有铝青铜制成的隔环,防止排与排间的运动干涉。
2)润滑。由于良好的润滑可以减小摩擦 ,降低发热,使行星齿轮轴承正常运转.延长其使用寿命。当多排圆柱滚子披密集地安装在行星齿轮孔及轴之间,处于中间排的短圆柱滚子润滑比较困难。在行星齿轮齿根处钻几个直通至排与排之间的小孔,小孔的个数视短圆柱滚子排数而定.小孔座均匀分布在齿轮圆周上。
3)精度。由于行星齿轮内孔充当轴承外滚道,行星轴表面充当轴承内滚道,因此对行星齿轮内孔及轴的形状精度、尺寸精度和表面粗糙度等要求较高,均按滚动轴承的精度标准予 以考虑。另外 ,尺寸公差的给出除参照标准推荐值外,还同时考虑短圆柱滚子、厢环、挡环等相关 件的尺寸精度 ,并通过计算确定,最终还要满足滚动轴承标准中关于滚子轴承轴向游隙和径向游隙的要求。
4)材料及热处理。该轴承中与短圆柱滚子相接触的行星齿轮和轴表面,除具有高的加工质量外,还要有很高的热处理硬度.同时为兼顾齿轮和轴对高强度的要求.因此在选
择材料时,通常采用高强度渗碳淬火钢.如 18Cr2N4W 、20Cr2N4A 等.这类钢材除具有很高的强度,而且通过渗碳淬火,可使渗碳表面达到 HRC58—63。
4.2.6 花键设计及校核
花键设计及校核
花键联结为多齿工作,承载能力高,对中性好,导向性好,齿根较浅,应力集中小,对轴榖的削弱小。
矩形花键加工方便,可用磨削方法获得较高的精度。按齿数和齿高不同规定有轻、中两个系列。应用广泛。一般用于轻载和中载。
渐开线花键受载时齿上有径向分力,能起自动定心的作用,使各齿载荷作用均匀,强度高,寿命长,加工工艺与齿轮加工相同,易获得较高的精度和互换性。用于载荷较大,定心精度要求高,以及尺寸较大的联结。齿根有平齿根和圆齿根,渐开线有标准压力角30°、37.5°和45°。30°压力角花键应用广泛,既适用于传递运动,又适用于传递动力,不仅适用于固定联结,而且适用于滑动和浮动联结,45°花键适用于固定联结,通常用于传动精度要求不太高的结构上,37.5°花键介于上述两者之间,常用于联轴器。
联轴器花键:
压力角37.5D α=o ,20Z = 2.5m = 大径尺寸(0.9)66.15ee D m Z =+=
强度校核:一般的花键联结只进行挤压强度和耐磨性计算。对于静联结,其主要失效形式是齿面压溃,偶尔也会发生齿根被折断,对于动联结,主要的失效形式是工作面的过度磨损。本次设计的花键都是静联结,其强度条件为:
2p pp m
T
Zhld σσψ=≤ (4-24)
()()
21046.58
0.0210.8200.9 3.54020 2.5p pp σσ?=
=≤?????? 满足强度
输出轴花键:
选用压力角30D α=o 20Z = 2.5m = 大径尺寸(1)52.5ee D m Z =+= 强度校核 ()
237970.81
0.0460.829 3.56629 3.5p pp σσ?=
=≤????? 满足强度
低速太阳轮花键
根据结构,高速级转臂与低速级太阳轮联结的外花键与低速级太阳轮设计成一体,所以该花键联结的尺寸参照太阳轮的尺寸,只进行强度校核。
()
27287.86
0.180.829448294p pp σσ?=
=≤????? 满足强度
4.3联轴器的选择
4.3.1输入端联轴器的选择
计算转矩:n w
C T n
p K T K T ≤?=?=9550 Nm (4-25) 查表知K=2.5.
=?=?=n
p K T K T w
C 9550
2.5*9550*0.99*200/1460=2590.3Nm 根据工作情况要求,决定高速轴Ⅰ与电动机轴之间选用弹性柱销联轴器。按]1[表4-2-22查联轴器型号为:HL5联轴器55?142 GB5014-85
?4.3.2 输出端联轴器的选择
计算转矩:n w
C T n
p K T K T ≤?=?=9550 Nm 查表知K=2.5.
=?=?=n p K T K T w
C 9550
2.5*9550*14
3.14/36=94929.65Nm 根据工作情况要求,低速轴Ⅴ与工作机主轴之间需要选用三个涨套联轴器。涨套联轴器是靠正压力产生涨紧力,而通过涨紧力产生的摩擦力传递扭矩。涨套联轴器除具有传递扭矩大、对中性好、结构简单、拆装方便等优点之外,还可起缓冲和过载保护作用。
所以选用18Z 型胀紧联结套。标记为: 18Z 型胀紧联结套120×112 ;其基本尺寸为
表4-2 Tablet.4-2
d D i L Mt Ft dt n Ma Pt G
基本尺寸额定负
载螺母胀套与轴结合
面上压力
重量
mm (KN.m) KN dt n N.m
N/m2
m kg 120 165 100 112 40.3 673 M12 15 145 165 8.3
掘进机截割部设计汇总
2.1.2 各部件的结构型式的确定 2.1.2.1 切割机构 (3)行星减速器 主要由箱体、减速齿轮、二级行星轮架、输入、输出轴构成。太阳轮与行星轮相啮合,此行星轮通过两个轴承装在星轮轴上,两端装有孔用弹性挡圈,星轮装在第一级行星架相应的轴孔内,内轮与箱体组成一体并与行星轮啮合带动第一级行星架,实现第一级减速[7]。 第二级的太阳轮与第一级行星架为渐开县花键联结,太阳轮与第二行星轮啮合,此行星轮装在第二级的轮轴,此轮轴装在第二级行星架相应轴孔内。这里内轮与减速器壳体组成一体与行星轮啮合,此星轮不仅自转还绕太阳轮公转,从而实现第二级减速器。 图2-1 EBZ200E掘进机的截割部行星减速器结构 Fig.2-1 EBZ200E roadheader in Jiamusi Coal Mine Machinery Co. Ltd. 2.2.4 截割机构技术参数的初步确定 2.2.4.3 电动机的选择 根据行业标准MT477-1996YBU系列掘进机用隔爆型三相异步电动机选择,确定截割功率为200kw,额定电压AC1140 /660 V,转速1500rpm
表2-2电动机的基本参数[13] 功率/kW 效率η/% 功率因数 /cos?堵转转矩堵转电流最小转矩最大转矩冷却水流 量/31 m h- ? 额定转矩额定电流额定转矩额定转矩 200 92 0.85 2.0 6.5 1.2 2.6 1.3
3悬臂式掘进机截割机构方案设计 3.1截割部的组成 掘进机截割部主要由截割电动机、截割机构减速器、截割头、悬臂筒组成。见图3-1.截割部是掘进机直接截割煤岩的装置,其结构型式、截割能力、运转情况直接影响掘进机的生产能力、掘进效率和机体的稳定性,是衡量掘进机性能的主要因素和指标。因此,工作部的设计是掘进机设计的关键。 1 截割头 2 伸缩部 3 截割减速机 4 截割电机 图3-1 纵轴式截割部 ?3.2 截割部电机及传动系统的选择 切割电机的选择应根据工作条件选取,由设计要求可知,所设计的掘进机可截割硬度为小于85Mpa的中硬岩,查表2-1可知应该选取功率为200KW的截割电动机。电机动力经传动系统传向截割头进行截割,且机体为焊接结构,前端与行星减速器相联,后端联接回转台。电机输出力矩,通过花键套传递给减速器,再由花键套传到主轴,主轴通过内花套键与截割头相联,把力(矩)传递到割头上,截割头以此方式进行工作。 3.5 传动方案设计 悬臂式掘进机的传动方式为电机输出轴通过联轴器将转矩传递给减速器的输入轴,减速器输出轴通过联轴器将转矩传递给主轴,主轴带动截割头转动。
机械毕业设计998掘进机的截割机构的设计
摘要 随着煤炭行业机械化程度的加快,煤炭行业以前只是重视采煤的机械化,大多数的煤炭行业很少有在掘进方面有较大的投入和研究,这样就造成了采掘速度远远大于开拓速度,此时怎样来提高出煤量,开拓的机械化就显得极其重要了。作为我国主要能源的煤炭资源在开采上日趋机械化的同时,迫切需要拥有先进的掘进机械,掘进机的研制成功标志着我国的煤炭行业已达到世界的先进水平。 掘进机截割机构是掘进机的主要组成部分,按照掘进机截割部的总体、动力部分、传动部分以及执行部分的设计思路进行掘进机截割部的设计。在设计时,动力部分做选型计算,传动部分的行星减速机构做具体的设计计算和校核,执行部分只对执行元件进行设计计算和校核。设计对于提高和改进掘进机工作性能,发展我国大口径全断面掘进机产业以及进一步提高我国的盾构研发能力、改善研发条件具有重大战略意义。 关键词:掘进机; 截割臂; 行星减速器
Abstract With the accelerating of coal industry, the degree of mechanization mining coal industry is the importance before, the most mechanized excavating in coal industry has rarely have large investment and research, thus causing the mining speed than develop, how to improve the speed of coal, development of a mechanized appears very important. As our main source of energy in the exploitation of coal resources in the increasingly urgent need, mechanized excavating the advanced mechanical, swinging the successful development of the coal industry, China has reached the advanced world level. Determing cutting mechanism is the main component, the product in accordance with the overall determing cutting parts, power transmission part and the part, the part of the design thought for the design of determing cutting. In the design, selection of part, transmission parts of planetary gearhead institutions do specific design calculation and test execution part only, design calculation of actuators and checking. Design for improvement in China, the development work performance swinging big caliber, whole section roadheader industry and further enhance our shield developing capability, improve development condition with the strategic significance. Key words:roadheader ; cutting arm ; planetary-gear drive
掘进机截割头设计
掘进机截割头设计 煤矿掘进是煤炭生产和建设的基础工程。近年来,我国煤矿掘进机械化得到了迅速的发展,装备水平也有很大的提高,在自主创新能力上也有长足的进步。 煤炭工业是我国国民经济的主要支柱产业。在未来50年内,煤炭仍是主要的能源和战略物质,具有不可替代性,是国民经济和社会发展的保证。随着国民经济的快速发展,以及国加入WTO后,煤炭工业现代化的步伐也在加快。目前,国内掘进机发展水平相对落后,巷道掘进成为煤矿发展的一个瓶颈,制约着煤炭工业的发展。各国早期研制的悬臂式掘进机都是以煤炭为作业对象,机重在13-17吨之间、切割功率在30KW左右的轻型机,代表机型是前苏联的ЛК-3型掘进机。中期产品主要是用于切割煤系地层中的各种煤岩的中型掘进机,机重在25吨左右、切割功率50-100KW,可切岩石硬度系数f6,如英国的MKA-2400型、奥地利的AM-50型、日本的S100型等。近期产品主要是以煤系地层中的中硬度岩石为作业对象的重型机,一般机重40-80吨、切割功率150-200KW、可切岩石硬度系数f8,如英国的LH-1300型、奥地利的AM-75型、日本的S200M型掘进机等。 我国的掘进机技术开发工作始于1965年,最初是仿前苏联的ЛК-3型掘进机,1979年后,先后从日本、奥地利、英国、美国、西德、原苏联、匈牙利引进了多种型号的掘进机,通过引进日本MRH-5100-41型、奥地利AM-50等型掘进机的制造技术和先进加工设备,并进行技术转化,到1989年底,我国已自行研制成功了AM50、ELM-55、EMIA-30、EL-90、5100等6种8个型号的掘进机,使我国中小型掘进机不再依赖进口。此后,我国又开始了重型掘进
掘进自动化工作面研究及应用新的
掘进自动化工作面研究及应用 赵学雷屈小兵李卫涛 (潞安环能股份公司王庄煤矿,山西长治046031) 摘要:王庄煤矿于2008年8月份建成全国第一个掘进自动化工作面。该工作面系统由自动化掘进机、掘进机前配套设备、离心式除尘系统等组成,实现了掘锚联合作业、掘进机自动化控制等功能,极大的降低了工人的劳动强度,改善了作业环境,提高了生产效率。 关键词:掘进自动化工作面掘进机自动化技术掘进机前配套技术矿用离心式除尘系统工艺设备自动化技术 1 6207掘进自动化工作面概况 1.1 地质条件 6207工作面地面位置位于山西省长治市屯留县岭上村南,井下位置位于+630水平62采区,地面标高为924-927m,工作面标高626-675m,工作面埋深300m左右。开采3#煤层,在本工作面范围内,煤层厚度稳定,煤层下部有一层夹矸较厚,为0.3m,工作面外部煤层较薄,里部较厚。 该工作面整体为一个向西南方向倾斜的单斜构造,煤层倾角1~5度,工作面里段煤层倾角3~6度,外段煤层倾角1~3度,工作面内无其它地质构造。煤层平均厚度为6.5m,含矸0~5层,一般含夹矸4~5层。6207工作面回采巷道沿煤层底板掘进,巷道断面尺寸:宽×高=5×3.5m2,顶部尚有3m左右的煤层,并含有夹矸。直接顶为厚2.95m的泥岩,节理发育,含植物化石。老顶为厚层灰白色的细粒砂岩,致密坚硬,抗压强度高,不易冒落。巷道两帮为强度较低的3#煤层。底板为厚3.1m强度较小的泥岩。由于巷道围岩整体强度较低,直接顶又为易破碎、冒落的泥岩,与顶煤形成复合顶板,不稳定煤、岩复合顶板厚度达6m左右,加之巷道断面尺寸又大,巷道维护较困难。 1.2 支护设计 1.2.1顶板支护 锚杆长度为2.4m,锚杆间排距为1150×1000mm,每排采用φ22的高强左旋无纵筋螺纹钢锚杆5根,树脂药卷加长锚固。巷道顶板采用锚索加强支护,每3
悬臂掘进机自动截割控制关键技术_刘建功
n 煤炭科技#机电与信息化n 悬臂掘进机自动截割控制关键技术 刘建功1 吴 淼2 魏景生2,3 田 劼2 杨 阳2 陈国强2 李 睿2 (11河北冀中能源集团,河北省邢台市中兴西大街191号,054021;21中国矿业大学(北京)机电与信息工程学院,北京市海淀区学院路,100083;31石家庄煤矿机械有限责任公司,河北省石家庄市跃进路111号,050031 摘 要 阐述了悬臂掘进机巷道自动截割控制的4个关键技术,即掘进巷道断面自动成形控制、截割头恒功率自动牵引调速控制、掘进机位姿检测控制以及掘进机定向掘进控制。 其中前2个关键技术已在EBZ160、EBZ200和EBH 300机型上得到实施,试验效果很好。认为,该关键技术的研究为实现掘进工作面智能化、自动化、信息化和无人化奠定了基础。 关键词 悬臂掘进机 位姿检测 定向掘进 断面自动成形 恒功率调速中图分类号 T D42115 文献标识码 A S tudy on the key technologies of automatic cutting control of boom -type roadheaders Liu Jiang ong 1,Wu Miao 2,Tian Jie 2,Yang Yang 2,Chen Guoqiang 2,Li Rui 2 (11H eb ei Jizhong Energy Group,Xingtai,H eb ei plovince,054021,Ch ina; 21School of M echanical Electronic and Inform ation Engineering,Chin a University of M ining an d T echnology(Beijing),Beijing 100083,C hina) Abstract Fo ur key techno log ies on automat ic cutting contro l of boom-ty pe r oadheaders w ere presented in this pa per,i 1e 1mine lanew ay sect ion automatic fo rming co nt ro l,cutting head const ant pow er speed regulation contr ol,po sitio n detection co nt ro l and directional ex cavatio n contr ol o f boo m-type roadheaders 1W here the anterio r tw o key technolog ies had been put in practice in EBZ160and EBZ200boom -type roadheaders,and effects o f ex periment wer e ver y well 1Wr iters think that the research on abov e fo ur key technolog ies laid a fo undatio n for realizing the in -telligentizatio n,automatizatio n,infor matio nization and unmanned operating at driv ing face 1 Key words boo m -type ro adheader;position detect ion;dir ect ional ex cavatio n;automatic form ing contr ol;constant pow er speed r eg ulation *国家高技术研究发展计划(863计划)重点项目(2008A A062201) 掘进机主要用于巷道的挖掘,是现代化矿井生 产不可缺少的设备,掘进机的发展方向是操作控制方式的智能化、自动化、信息化和无人化,未来的矿山机械将全面装备融合电子化、自动化、机器人化为一体的机电一体化技术,逐渐发展为掘进机器人。目前国内外已开始该方面的研究,但仍处于理论研究、试验调试阶段,都没有达到市场化水平。为此,国家设立863重点项目/煤矿井下采掘装备遥控关键技术0。其中课题一/掘进机远程控制技术及监测系统0研究目标为:以掘进机远程监测和控制的关键技术为核心,重点研究煤巷悬臂式掘进 装备可视化远程监控技术,开发出配装国产自主研发的悬臂式掘进机及远程监控系统,以满足我国煤矿井下采掘装备远距离遥控和安全作业的需要,研制的掘进机可视化遥控装备能满足煤矿井下掘进作业和煤矿安全规程的要求。总之,实现巷道掘进的自动化,需解决4个方面的关键理论和技术问题。1 掘进巷道断面自动成形控制 悬臂式掘进机截割头在空间的行走轨迹决定截割断面形状。由截割臂相对于掘进机机体的垂直摆动、水平摆动以及截割头的伸缩实现。垂直摆动与水平摆动是2个分别独立的液压控制系统,既可以单独实现截割头垂直或水平运动,也可以实现复合 54 中国煤炭第34卷第12期2008年12月
EBZ160型掘进机截割头安装安全技术措施
EBZ160型掘进机截割头安装安全技术措施 一、安装场地:本次安装场地设在二采区轨道下山距二采区轨道下山下部车场联络巷口向上10米处。 二、运输路线:地面→副斜井→8#煤运输大巷→8#煤轨道大巷→15#煤轨道暗斜井上部车场→轨道暗斜井→15#煤轨道暗斜井下部车场→二采区轨道下山(组装点)。 三、运输前的准备工作: 1、运输人员必须熟悉运输线路的基本情况。 2、对所用的材料车进行检查,保证完好不带病作业。 3、对捆绑车辆及物件所用的钢丝绳认真检查,严禁使用断丝断股严重锈蚀的钢丝绳。 四、设备卸车 1、设备卸车时,必须将车支设牢靠,且人员站在安全的地点,并且要掌握物件重心平衡,以防物件滑出伤人。 2、所有重车必须根据所装物件的不同,选择不同的卸车方式。 3、设备卸车如果需用起吊时,必须严格遵守本措施起吊安全技术措施的有关规定。 4、设备卸车时如需人工抬运时必须保证同肩同口令,步调统一,轻抬轻放,并清理好退路,保证道路畅通。 五、安装安全技术措施 1、安装前由专人准备好安装所需的吊索吊具及配套工具,将现场场地进行平整,将掘进机接电退至单轨吊轨道下方,使用手拉葫芦将截割头吊起进行安装。 2、安装时使用单轨吊轨道作为起吊点,严禁使用原支护巷道的锚杆起吊设备。设备吊装所用的手拉葫芦、滑轮、链环必须安全可靠。起吊时要有专人指挥,统一信号。 3、现场必须要有专职安全员现场监督,现场工作人员要做好互保,联保工作,要熟悉作业环境和所从事的内容。 六、起吊安全技术措施 1、起吊前,必须认真检查起吊用具(特殊焊制的吊环等)及起吊工具。每次起吊前,保证吊具不滑动,吊钩与重物连接牢固可靠。使用手拉葫芦起吊设备(重物)前,必须对手拉葫芦进行全面检查,检查各部件是否齐全、灵活可靠,发现问题及时处理。严禁手拉葫
横轴式掘进机截割头设计
横轴式掘进机截割头设计 摘要:随着社会的不断发展和科技水平的不断提高,人类征服自然的领域也在不断扩大,其中比较具有代表性的就是掘进机,掘进机的出现具有很重要的实用意义。自从掘进机开始进入人们的生活视线,就被广泛地应用到铁路穿山隧道、引水隧道等各施工过程中.掘进机的功能除了能应用在隧道施工外,像以采掘为目的的煤巷开挖、矿巷开掘中也广泛采用了掘进机,这样工作效率高。以上介绍使用的就是部分断面掘进机,而横轴掘进机是其中的一种。 本次毕业设计就是为了研究横轴式掘进截割头的设计,具体设计内容包括:1.收集基本资料,例如:先对掘进机现在在国内外的发展趋势进行了解,接着对掘进机结构进行学习分析,从而发现掘进机本身有什么需要改进之处,还有就是掘进机对截割的矿岩都有什么要求等;2.对资料进行学习和总结。将自己收集的数据进行整理列表,这样看起来一目了然;3.CAD的学习制作等。通过简单的CAD软件学习,将自己想要设计的截割头画出来。并通过计算得到基本数据,进行数据分析和结构分析相结合。对掘进机的具体结构用途也要进行了解和掌握,这样有利于截割头的整体计算。 掘进机结构的优化设计和制造精度对今后的工作性能都会有决定性的影响因为截割头是掘进机的核心部位,所以它的研究自然也就成了重中之重。煤炭是人类生产生活的重要能源,随着工业的不断发展,生产规模的不断扩大,煤炭在国民经济中的地位也显得越来越重要。随着采煤机械化的发展,大大提高了工作面的广度,对开采强度,工作面的推进速度要求也越来越快,这就要求加快掘进速度,提高工作效率以适应人们对工具的需求。切割头是掘进机的工作机构,它的主要功能就是破碎岩石或者分离煤层。经过对煤岩切割过程的研究了解,认识到影响切割效果的因素很多,因而掘进机截割头的设计变的复杂许多。为提高工作效率,加快生产力,满足人们对机械化的高要求,截割头的设计成了重中之重。如果在截割头的每一转中,参加切割的各个截齿都能同时从岩石中切下等体积的煤岩,也就是每个镐齿的受力相等,磨损程度也相同,机械运动也比较平稳,只有满足这些要求,才可以达到自己当初设计的初衷。 关键词:横轴;掘进机;截割头;截割头参数;截齿
掘进机截割部设计
各部件的结构型式的确定 2.1.2.1 切割机构 (3)行星减速器 主要由箱体、减速齿轮、二级行星轮架、输入、输出轴构成。太阳轮与行星轮相啮合,此行星轮通过两个轴承装在星轮轴上,两端装有孔用弹性挡圈,星轮装在第一级行星架相应的轴孔内,内轮与箱体组成一体并与行星轮啮合带动第一级行星架,实现第一级减速[7]。 第二级的太阳轮与第一级行星架为渐开县花键联结,太阳轮与第二行星轮啮合,此行星轮装在第二级的轮轴,此轮轴装在第二级行星架相应轴孔内。这里内轮与减速器壳体组成一体与行星轮啮合,此星轮不仅自转还绕太阳轮公转,从而实现第二级减速器。 图2-1 EBZ200E掘进机的截割部行星减速器结构
EBZ200E roadheader in Jiamusi Coal Mine Machinery Co. Ltd. 截割机构技术参数的初步确定 电动机的选择 根据行业标准MT477-1996YBU系列掘进机用隔爆型三相异步电动机选择,确定截割功率为200kw,额定电压AC1140 /660 V,转速1500rpm 表 2-2电动机的基本参数[13] 功率/kW效率η/% 功率因数 /cos?堵转转矩堵转电流最小转矩最大转矩 冷却水流 量/31 m h- ? 额定转矩额定电流额定转矩额定转矩 20092
3悬臂式掘进机截割机构方案设计 截割部的组成 掘进机截割部主要由截割电动机、截割机构减速器、截割头、悬臂筒组成。见图3-1.截割部是掘进机直接截割煤岩的装置,其结构型式、截割能力、运转情况直接影响掘进机的生产能力、掘进效率和机体的稳定性,是衡量掘进机性能的主要因素和指标。因此,工作部的设计是掘进机设计的关键。 1 截割头 2 伸缩部 3 截割减速机 4 截割电机 图3-1 纵轴式截割部 ? 截割部电机及传动系统的选择 切割电机的选择应根据工作条件选取,由设计要求可知,所设计的掘进机可截割硬度为小于85Mpa的中硬岩,查表2-1可知应该选取功率为200KW的截割电动机。电机动力经传动系统传向截割头进行截割,且机体为焊接结构,前端与行星减速器相联,后端联接回转台。电机输出力矩,通过花键套传递给减速器,再由花键套传到主轴,主轴通过内花套键与截割头相联,把力(矩)传递到割头上,截割头以此方式进行工作。
掘进机主要部件结构及工作原理
掘进机主要部件结构及工作原理 1截割部结构 截割部主要由截割头组件1、悬臂段2、截割减速器3、截割电机7组成,如图1所示。截割减速器3两端的法兰盘分别与电动机7和悬臂段2连接成一体,悬臂段2中的传动轴通过花键及螺钉与截割头组件1相连接。电动机7经截割减速器3、悬臂段2中的传动轴驱动截割头组件1旋转截割煤、岩。截割部靠销轴4与截割头升降油缸相连接,靠销轴8 与截 割头 回转 台相 连 接。 在截 割头升降油缸推动下,可绕销轴8上下摆动;在截割头回转油缸推动下,可随截割头回转台左、右摆动。 图1 截割部结构 1-截割头组件;2-悬臂段;3-截割减速器;4、6、8-销轴;5-盖板;7-截割电机2.装运部结构 装运部的作用是将截割头破碎下来的煤和岩石装运到配套的转运设备上去。它由装载部(铲板部)和运输部(第一运输机)两部分组成。装载部(铲板部)的结构如图2所示,它由主铲板2、侧铲板1、星轮驱动装置4、弧形三齿星轮5等组成,两台低速大转矩马达直接驱动两个弧形三齿星轮5旋转,将截割头破碎下来的煤和岩石装运到运输部(第一运输机)的机尾溜槽8中。铲板通过耳座6与铲板升降油缸连接,通过支点耳座7与本体部连接;铲板升降油缸推动铲板绕支点耳座7可上下摆动。 星轮驱动装置结构如图3所示,弧形三齿星轮1通过定位销2和螺钉4与旋转盘3连
接,液压马达6的输出轴插入旋转盘3的花键孔,带动旋转盘3及弧形三齿星轮1旋转。 第一运输机位于机体中部,是中双链刮板式运输机,其结构如图4。运输机分前溜槽1和后溜槽3,前、后溜槽用高强度螺栓2联接,运输机前端通过插口插入铲板部和本体部连接的销轴上,后端通过高强度螺栓固定在本体上。运输机采用二个液压马达5直接驱动链轮,带动刮板链实现物料运输。紧链装置4采用丝杠螺母机构对刮板链的松紧程度进行调整,弹簧座起缓冲的作用。 图2 铲板部结构 1-侧铲板;2-主铲板;3-运输机尾链轮;4-星轮驱动装置;5-三齿星轮; 6-铲板升降油缸连接耳座;7-铲板支点耳座;8-运输机溜槽 图3 星轮驱动装置结构 1-弧形三齿星轮;2-定位销;3-旋转盘;4-螺钉;5-马达座;6-液压马达 图4 第一运输机结构 1-前溜槽;2-高强度螺栓;3-后溜槽;4-紧链装置;5-液压马达 3本体部(机架) 本体部由回转台、回转轴承、本体架等组成,本体架采用整体箱形焊接结构,主要结构件为加厚钢板,其结构如图5所示。 图5本体部结构 1-连接铲板部的销轴;2-连接截割部升降油缸的销轴;3-连接截割部的销轴;
掘进机截割头设计解析
掘进机截割头设计解析 【摘要】在大型施工活动中,都需要借助掘进机才能够顺利推进工程进度,而截割头又是掘进机的重要组成零配件,它被用来打通和破碎坚固的地质岩层。经过多年的施工经验,本文发现影响岩层切割效率的因素十分多样化,因此必须做好截割头的设计工作,以提高其在实际工作中的使用寿命和工作效率。本文针对如何改进截割头的工作性能提出了几点建议和措施。 【关键词】掘进机;截割头;设计 悬臂式掘进机是当前最先进的一种工程设备,它具备切割、装载、运输、搬运、调度和清除场地的多种复合功能。因此,它的内部结构也十分复杂,主要由切割头、液压器、装载头、动力系统、传动系统、控制系统等重要功能配件构成。作为掘进机的重要工作部件,切割功能主要依靠切割刀、液压臂、动力传动器、升压器、动力电源等共同配合来完成。切割机在正常工作时,主要是利用切割头的前后运动和切割液压臂的纵向或横向摆动带动切割刀来完成切割。 截割部在正常运转时,切割头的运动主要是依靠驱动电源带动液压臂运动来实现,装在切割头上的刀片获得足够的力将坚硬的岩层破碎。如果需要推进切割深度,可以通过机械的动力系统朝前驱动来实现。切割机头被安装在能够自由转动的操作平台上,这样就可以利用操作平台连接的两个回转液压缸提供的动力来完成各种切割动作,通过这种动力设计,能够帮助切割机头实现多种工作角度变换,因此可以为操作人员提供多种切割方案。 掘进机的工作效率主要取决于截割头的设计,截割头要求各截齿负荷均匀,切割平稳,摆动小;截割比能消耗低,截齿消耗少;切割效率高,产生粉尘量小。 1设计简述 截割头的主要参数包括:截割头的长度、直径、锥角、螺旋叶片的头数与升角、截线间距等,这些参数直接影响掘进机的截割性能。 1.1截割头的长度 截割头的长度不仅与截割阻力的大小有关,还影响机器工作的循环时间和生产率。因此,必须合理地选取截割头的长度。 由于工作面煤壁附近的煤岩有压张效应,在压出带范围内,煤岩的抗截强度明显减弱,截割能力和单位能耗降低。因此,截割头的长度应设计在压出带范围内。 如果截割头长度过长,能够有效提高掘进机的工作效率,但是需要提供更多的动力。如果切割机的功率太小难以满足这样的施工要求,就会因为过大的阻力
掘进机行走机构减速器设计(开题分析方案)
一、课题名称 132型掘进机行走减速器设计 二、课题研究背景 掘进机分为两种:开敞式掘进机和护盾式掘进机。价格一般在上亿元人民币。英文:roadheader用于开凿平直地下巷道的机器。主要有行走机构、工作机构、装运机构和转载机构组成。随着行走机构向前推进,工作机构中的破碎头不断破碎岩石,并将碎岩运走。有安全、高效和成巷质量高等优点,但造价大,机构复杂,损耗也较大。 近年来随着我国煤炭行业的迅速发展,与之唇齿相依的煤机行业也日益受到重视。在煤炭行业纲领性文件《关于促进煤炭工业健康发展的若干意见》中,在全国煤炭工业科学技术大会上以及国家发改委出台的煤炭行业结构调整政策中,都涉及到发展大型煤炭井下综合采煤设备等内容。 掘进和回采是煤矿生产的重要生产环节,国家的方针是:采掘并重,掘进先行。煤矿巷道的快速掘进是煤矿保证矿井高产稳产的关键技术措施。采掘技术及其装备水平直接关系到煤矿生产的能力和安全。高效机械化掘进与支护技术是保证矿井实现高产高效的必要条件,也是巷道掘进技术的发展方向。随着综采技术的发展,国内已出现了年产几百万吨级、甚至千万吨级超级工作面,使年消耗回采巷道数量大幅度增加,从而使巷道掘进成为了煤矿高效集约化生产的共性及关键性技术。 我国煤巷高效掘进方式中最主要的方式是悬臂式掘进机与单体锚杆钻机配套作业线,也称为煤巷综合机械化掘进,在我国国有重点煤矿得到了广泛应用,主要掘进机械为悬臂式掘进机。 我国煤巷悬臂式掘进机的研制和应用始于20世纪60年代,以30~50kW的小功率掘进机为主,研究开发和生产使用都处于实验阶段。80年代初期,我国淮南煤机厂<现重组为凯盛重工)引进了奥地利奥钢联公司AM50型掘进机、佳木斯煤机厂<现隶属于国际煤机)引进了日本三井三池制作所S-100型掘进机,通过对国外先进技术的引进、消化、吸收,推动了我国综掘机械化的发展。但当时引进的掘进机技术属于70年代的水平,设备功率小、机重轻、破岩能力低及可靠性差,仅适合在条件较好的煤巷中使用,加之国产机制造缺陷,在使用中暴露了很多问题。国内进一步加强对引进机型的消化吸收工作,积极研制开发了适合我国地质条件和生产工艺的综合机械化掘进装备。经过近30年的消化吸收和自主研发,目前,我国已形成年产1000余台的掘进机加工制造能力,研制生产了20多种型号的掘进机,其截割功率从30kW 到200kW ,初步形成系列化产品,尤其是近年来,我国相继开发了以EBJ-120TP型掘进机为代表的替代机型,在整体技术性能方面达到了国际先进水平。基本能够满足国内半煤岩掘进机市场的需求,半煤岩掘进机以中型和重型机为主,能截割岩石硬度为f=6~8,截割功率在120kW以上,机重在 35t以上。煤矿现用主流半煤岩巷悬臂式掘进机以煤科总院太原研究院院生产的EBJ-120TP型、EBZ160TY型及佳木斯煤机厂生产的S150J型三种机型为主,占半煤岩掘进机使用量的80%以上。 然而,国内目前岩巷施工仍以钻爆法为主,重型悬臂式掘进机用于大断面岩巷的掘进在我国处于实验阶段,但国内煤炭生产逐步朝向高产、高效、
掘进机截割部设计
掘进机截割部设计 Company number:【0089WT-8898YT-W8CCB-BUUT-202108】
各部件的结构型式的确定 2.1.2.1 切割机构 (3)行星减速器 主要由箱体、减速齿轮、二级行星轮架、输入、输出轴构成。太阳轮与行星轮相啮合,此行星轮通过两个轴承装在星轮轴上,两端装有孔用弹性挡圈,星轮装在第一级行星架相应的轴孔内,内轮与箱体组成一体并与行星轮啮合带动第一级行星架,实现第一级减速[7]。 第二级的太阳轮与第一级行星架为渐开县花键联结,太阳轮与第二行星轮啮合,此行星轮装在第二级的轮轴,此轮轴装在第二级行星架相应轴孔内。这里内轮与减速器壳体组成一体与行星轮啮合,此星轮不仅自转还绕太阳轮公转,从而实现第二级减速器。 图2-1 EBZ200E掘进机的截割部行星减速器结构 EBZ200E roadheader in Jiamusi Coal Mine Machinery Co. Ltd. 截割机构技术参数的初步确定 电动机的选择 根据行业标准MT477-1996YBU系列掘进机用隔爆型三相异步电动机选择,确定截割功率为200kw,额定电压AC1140 /660 V,转速1500rpm 表 2-2电动机的基本参数[13] 功率/kW 效率η/% 功率因数 /cos? 堵转转矩堵转电流最小转矩最大转矩冷却水流 量/31 m h- ?额定转矩额定电流额定转矩额定转矩 200 92
3悬臂式掘进机截割机构方案设计 截割部的组成 掘进机截割部主要由截割电动机、截割机构减速器、截割头、悬臂筒组成。见图3-1.截割部是掘进机直接截割煤岩的装置,其结构型式、截割能力、运转情况直接影响掘进 机的生产能力、掘进效率和机体的稳定性,是衡量掘进机性能的主要因素和指标。因 此,工作部的设计是掘进机设计的关键。 1 截割头 2 伸缩部 3 截割减速机 4 截割电机 图3-1 纵轴式截割部 截割部电机及传动系统的选择 切割电机的选择应根据工作条件选取,由设计要求可知,所设计的掘进机可截割硬 度为小于85Mpa的中硬岩,查表2-1可知应该选取功率为200KW的截割电动机。电机动力经传动系统传向截割头进行截割,且机体为焊接结构,前端与行星减速器相联,后端 联接回转台。电机输出力矩,通过花键套传递给减速器,再由花键套传到主轴,主轴通 过内花套键与截割头相联,把力(矩)传递到割头上,截割头以此方式进行工作。 传动方案设计 悬臂式掘进机的传动方式为电机输出轴通过联轴器将转矩传递给减速器的输入轴, 减速器输出轴通过联轴器将转矩传递给主轴,主轴带动截割头转动。 传动类型的设计 由于行星齿轮传动具有多分流传动、低压力啮合、作用力平衡和运行多变性等一系 列特点,所以在同等工作条件下与定轴齿轮传动相比,行星齿轮传动具有外形尺寸小, 重量轻、传动效率高、工作可靠和同轴传动等许多突出优点,因此国内外纵轴式掘进机 的截割结构传动系统均采用行星齿轮传动,以期在提高承载能力、效率和可靠性的同 时,尽可能地减轻重量、缩小外廓尺寸、降低制造成本。要求传动装置体积小、结构紧
掘进机截割减速器限位副失效机理研究
目录 摘要 ................................................................................................................................ I Abstract ................................................................................................................................ III 1绪论 (1) 1.1掘进机概述 (1) 1.1.1掘进机概念及分类 (1) 1.1.2悬臂式掘进机的总体结构 (1) 1.1.3悬臂式掘进机的截割机构 (2) 1.2课题研究现状 (3) 1.2.1行星齿轮传动轴向力研究现状 (3) 1.2.2 太阳轮限位副磨损研究现状 (3) 1.3课题研究的背景及意义 (4) 1.4本文主要研究内容 (4) 2 EBZ-260型掘进机截割减速器运动分析 (7) 2.1 EBZ-260型掘进机技术特点和结构组成 (7) 2.1.1 EBZ-260型掘进机技术特点 (7) 2.1.2 EBZ-260型掘进机结构组成 (7) 2.2 EBZ-260型掘进机技术参数 (7) 2.3行星齿轮传动概述 (8) 2.3.1行星齿轮传动定义及其分类 (8) 2.3.2 行星齿轮传动特点 (9) 2.4 EBZ-260型掘进机截割减速器结构形式及主要参数 (10) 2.4.1 EBZ-260型掘进机截割减速器结构形式 (10) 2.4.2 EBZ-260型掘进机截割减速器齿轮参数 (10) 2.5 EBZ-260型掘进机截割减速器传动比和转速的计算 (11) 2.5.1 EBZ-260型掘进机截割减速器传动比的计算 (11) 2.5.2 EBZ-260型掘进机截割减速器转速的计算 (11) 2.6本章小结 (13) 3 掘进机截割减速器太阳轮轴向力的计算 (14) 3.1 SolidWorks 2014软件 (14) 3.1.1简述 (14) 3.1.2 SolidWorks 2014三维实体建模过程 (14) 3.2有限元方法简介 (14) 3.2.1有限元方法概述 (14) 3.2.2有限元方法分析基本思想 (14) 3.3 SolidWorks Simulation简介 (14) 1
掘进机总体设计及行走部设计
中国矿业大学本科生毕业设计 姓名: ** 学号:****** 学院:应用技术学院 专业:机械工程及自动化 设计题目:掘进机总体设计及行走部设计专题:行走减速器与机架连接的改进指导教师: **** 职称:副教授 20**年6 月徐州
中国矿业大学毕业设计任务书 学院应用技术学院专业年级学生姓名 ** 任务下达日期:20**年 3 月8 日 毕业设计日期20** 年 3 月9 日至20** 年 6 月13 日毕业设计题目:掘进机总体设计及行走部设计 毕业设计专题题目:行走减速器与机架的连接改进 毕业设计主要内容和要求: 一、主要设计参数: 机身长:8-8.5m 机身宽:2~2.2m 机身高:1.5~1.65m 卧底深度: 245mm 装机功率:190kW 截割功率:120kW 经济截割煤岩硬度:≤60MPa 可掘巷道断面:18~20m2 最大可掘高度:3.75~4m 最大可掘宽度:5m 龙门高度:350~400mm 刮板速度:0.9~1.0m/s 运输形式:双边链履带宽度:2×500mm 行走速度:4.5m/min(工作)9m/min(调动) 额定电压:1140/660v 二、设计要求 1、查阅有关资料、完成履带式半煤岩掘进机总体方案的设计; 2、完成底盘总体传动及结构设计及减速器的设计; 3、主要部件、组件、零件图设计; 4、编写完成整机设计计算说明书 院长签字:指导教师签字:
指导教师评语(①基础理论及基本技能的掌握;②独立解决实际问题的能力;③研究内容的理论依据和技术方法;④取得的主要成果及创新点;⑤工作态度及工作量;⑥总体评价及建议成绩;⑦存在问题;⑧是否同意答辩等): 成绩:指导教师签字: 年月日
EBZ-160综掘机截割头常见故障及原因分析
EBZ-160综掘机截割头常见故障及 原因分析 [ 2012-05-12 10:25:00 ] [摘要] 通过研究EBZ -160综掘机截割部的结构形式及现场使用状况分析。提出在使用过程中故障产生的原因及预防方法。 [关键词] 截割头;故障原因;预防方法 概述 贵州盘江精煤股份有限公司现有多台在各矿使用,主要为辽宁三一重型装备有限公司生产的型号为EBZ-160悬臂式综掘机。 该掘进机由截割部铲板部、第一运输机、机架、行走部、后支承座、液压系统、冷却水系统、润滑系统等部分组成;掘进机在液压,电控系统的控制下,配合协调一致,轻松灵活地完成掘进作业。 一、截割部结构形式 截割部由截割头,伸缩油缸,截割减速机,截割电机组成。截割头为圆锥台形,截割头最大外经为1120mm,长925mm,在其圆周分布42组截齿,截割头通过花键套和2个M30的高强度螺栓与花键轴相连;伸缩部位于截割头和截割减速机中间,通过伸缩油缸使截割
头具有550mm的伸缩行程;截割减速机是两级行星齿轮传动,它和伸缩部用26个M24的高强度螺栓相连,截割电机为双速水冷电机,使截割头获得2种转速,它与截割减速机通过定位销和25个M24的高强度螺栓相连。 二、截割头常见故障原因分析 1、截割过负荷引起截割头不转。 EBZ-160掘进机为半煤岩掘进机,截割最大岩石硬度为60~80Mpa,理论生产能力为210m3/h,适应坡度为土18°,若该综掘机在工作过程中,遇到岩石硬度系数超过设计强度时,整个截割部出现过负荷,引起截割头不转,出现该种情况时,要对掘进工艺进行改进,一方面减少进刀量,另一方面可采用放炮破岩的方法降低掘进负荷。 2、伸缩部内主轴损坏引起截割头不转。 主轴损坏有以下情况:一是主轴花键磨损严重或花键严重损坏,导致主轴与截割花键不能正常啮合,造成截割头不转;二是主轴自身断裂或前端轴承抱死,造成截割头不转。 3、截割减速机内轴承、齿轮损坏引起截割头不转。 截割减速机是两级行星齿轮传动,主要完成电
纵轴式掘进机截割头的设计
龙源期刊网 https://www.360docs.net/doc/3b9282535.html, 纵轴式掘进机截割头的设计 作者:廉浩冯健 来源:《中国新技术新产品》2014年第03期 摘要:本文介绍了纵轴式掘进机截割头的设计原则,讨论了提高截割头截割效率的合理 方案,提供了设计用的主要数据。 关键词:截割头;设计原则;截割效率 中图分类号:TD42 文献标识码:A 1 概要 本文以纵轴式掘进机的截割头为研究对象。截割头是掘进机的关键部件,它直接参与对工作面的掘进工作。其设计参数较多,这些参数之间互相影响和制约,同时截割头的设计质量的好坏决定了掘进机整机的截割性能,这对截割头的使用寿命,以及整机的稳定性和可靠性都有着直接的影响。 2 工作原理 掘进机的工作过程是:操纵行走机构向工作面推进,使截割头在工作面的左下角钻入,水平摆动油缸使截割头横向截割到巷道的右侧。然后利用升降油缸把截割头上升接近等于截割头直径的距离,并使截割头向巷道左侧截割。如此往复截割运动,截割头就可以完成整个工作面的截割。当然掘进机的截割方式与掘进巷道断面的大小,形状,煤岩的分布情况有关。在截割头截落煤岩后,由装运机构将其装进掘进机中间的输送机构,再最终装进矿车或巷道输送 机。因此,纵向截割头通常的截割过程可以总结为纵向钻进、水平摆动截割和垂直摆动截割三种工作方式。 3 结构研究 3.1 影响设计的因素 如果能保证在旋转截割的过程中,使参加截割的每个截齿都截割相同大小的煤岩,让各截齿的受力相等、运行平稳,并且产生的磨损也基本相同,这样的截割头设计是最理想的。但是有很多因素影响截割头的设计,主要有以下几个方面: (1)煤岩自身的性质,主要有抗截强度、硬度、磨蚀性、坚固性系数等; (2)截割头的结构参数,主要有截割头的几何形状、外形尺寸、截齿排列、截齿数量以及截线间距等;
EBJ160重型掘进机截割机构行星减速器的设计
设计?计算文章编号:1003-0794(1999)10-0001-03 EBJ-160重型掘进机截割机构行星减速器的设计 (030006) 煤科总院太原分院 潘玮 摘要:论述了重型掘进机截割机构行星减速器的工况特点,并介绍了针对其工况特点进行的结构设计。 关键词:重型掘进机;截割机构;行星减速器;设计 中图号:TD421.5;T H132.46 文献标识码:A 近年,在我国煤矿中,薄煤层回采巷道需要开掘围岩,中厚煤层回采巷道随着单工作面产量的迅速提高,也需通过开掘围岩来加大巷道断面,以保证设备运输等方面的要求。因此,在“八五”计划中,EBJ-160重型掘进机的研究成为国家重点攻关项目。 本文仅就EBJ-160重型掘进机截割部中行星减速器的研究设计进行重点论述。 1 工况特点及要求 1.1 低速重载小体积 由于国内外掘进机均向着重型化方向发展,其截割机构传递的功率相应地也越来越大,但是截割机构外形尺寸却没有随功率的增加而成比例地增加。特别是一般掘进机因其工作特点所致,截割臂的外形多设计呈宝塔状,即越靠近截割头—动力输出端,其外形尺寸越小。因此,处于截割臂前端的传动,在设计上因尺寸问题而受到极大的限制。 1.2 冲击负荷大 掘进机是通过截割头完成截割煤岩的,因破碎机理所致,当截割煤岩时,煤岩的反作用力使截割头承受着强大的截割阻力和冲击负荷,由于截割机构的传动为刚性传动,势必使截割阻力和冲击负荷毫无保留地传递至齿轮、轴、轴承等传动件上。 1.3 载荷变化大 截割时,由于受被截割物料软硬不匀,牵引速度和截割深度的影响,载荷始终处于大幅度波动之中,而其载荷又不易被测定,因此掘进机尚无准确的载荷谱供设计参考。 1.4 高可靠性 我国越来越重视掘进设备的可靠性,相应地制定了一套试验检测标准和规范。如新设计掘进机的减速器必须进行性能试验和耐久性试验,截割减速器的耐久性试验为连续满载运行1000h。 2 传动类型的确定 由于行星齿轮传动具有多分流传动、低压力啮合、作用力平衡和运行多变性等一系列特点,所以在同等工作条件下与定轴齿轮传动相比,行星齿轮传动具有外廓尺寸小、重量轻、传动效率高、工作可靠和同轴传动等许多突出优点,因此国内外大多数掘进机的截割机构传动系统均采用行星齿轮传动,以期在提高承载能力、效率和可靠性的同时,尽可能地减轻重量、缩小外廓尺寸、降低制造成本。同样,EBJ-160重型掘进机截割机构根据其工况特点及外形尺寸等限制条件,在其传动系统中也采用了行星齿轮传动(见图1)。 图1 EBJ-160重型掘进机截割传动系统 ? 1 ? 1999年第10期 煤 矿 机 械