比较国内外机床与刀具的发展趋势
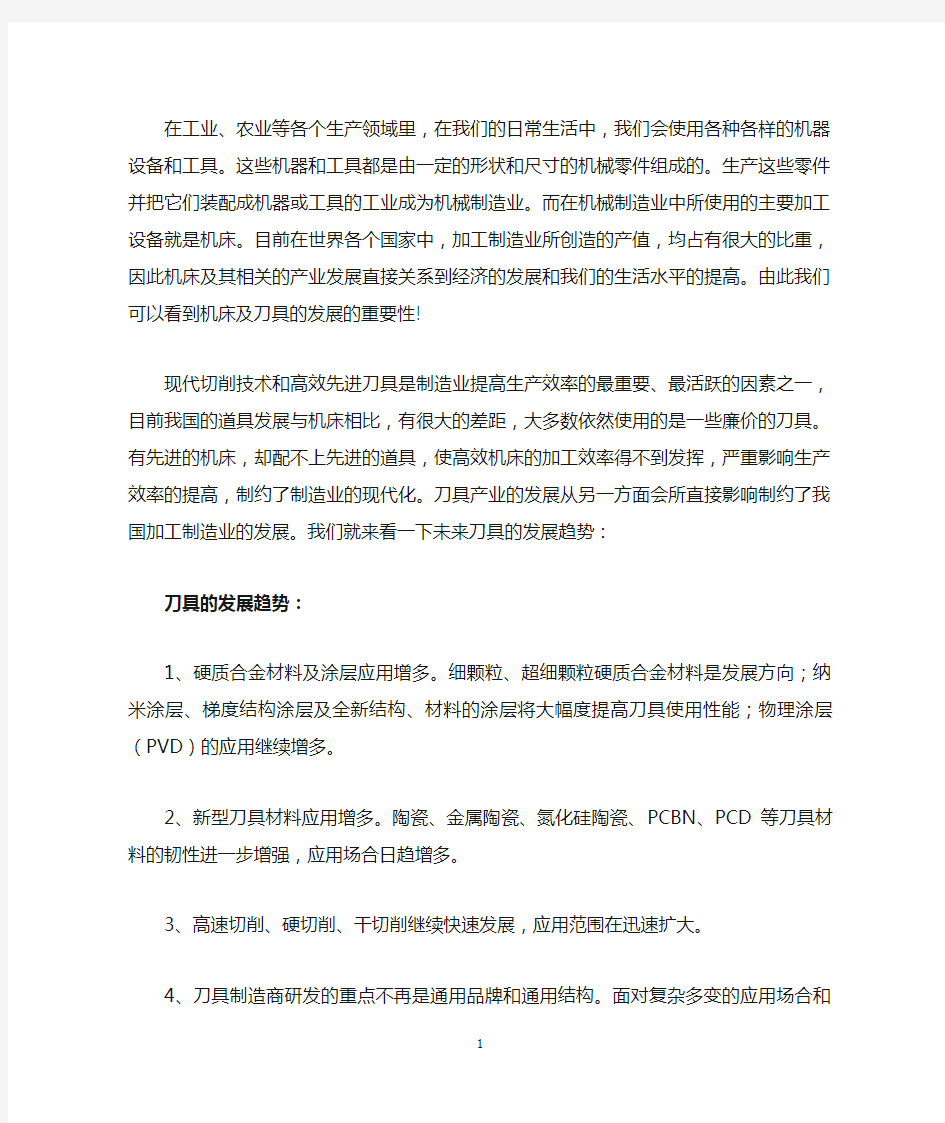

在工业、农业等各个生产领域里,在我们的日常生活中,我们会使用各种各样的机器设备和工具。这些机器和工具都是由一定的形状和尺寸的机械零件组成的。生产这些零件并把它们装配成机器或工具的工业成为机械制造业。而在机械制造业中所使用的主要加工设备就是机床。目前在世界各个国家中,加工制造业所创造的产值,均占有很大的比重,因此机床及其相关的产业发展直接关系到经济的发展和我们的生活水平的提高。由此我们可以看到机床及刀具的发展的重要性!
现代切削技术和高效先进刀具是制造业提高生产效率的最重要、最活跃的因素之一,目前我国的道具发展与机床相比,有很大的差距,大多数依然使用的是一些廉价的刀具。有先进的机床,却配不上先进的道具,使高效机床的加工效率得不到发挥,严重影响生产效率的提高,制约了制造业的现代化。刀具产业的发展从另一方面会所直接影响制约了我国加工制造业的发展。我们就来看一下未来刀具的发展趋势:
刀具的发展趋势:
1、硬质合金材料及涂层应用增多。细颗粒、超细颗粒硬质合金材料是发展方向;纳米涂层、梯度结构涂层及全新结构、材料的涂层将大幅度提高刀具使用性能;物理涂层(PVD)的应用继续增多。
2、新型刀具材料应用增多。陶瓷、金属陶瓷、氮化硅陶瓷、PCBN、PCD等刀具材料的韧性进一步增强,应用场合日趋增多。
3、高速切削、硬切削、干切削继续快速发展,应用范围在迅速扩大。
4、刀具制造商研发的重点不再是通用品牌和通用结构。面对复杂多变的应用场合和加工条件,研发针对性更强的刀片槽形结构、牌号及相应配套刀具取代通用的槽形、牌号的刀片及刀具。
5、刀具制造商角色转变。从单纯的刀具生产、供应,扩展至新切削工艺的开发及相应成套技术和解决方案的开发,为用户提供全面的技术支持和服务
6、信息化程度提高,刀具制造企业合作增强,市场竞争加剧。
世界著名刀具品牌:
山特维克集团旗下品牌——山特维克.可乐满、德国瓦尔特(含德国蒂泰克斯、德国普瑞特)美国万耐特、法国塞菲提、德国多马以及瑞典本土的山高(荷兰嘉伯乐、法国EPB
IMC金属切削集团现旗下品牌——以色列的伊斯卡、英格索尔、特固克
日本东芝——泰珂洛、德国的创新、法国的无敌泰克
美国肯纳金属——旗下知名品牌:美国肯纳金属、德国威迪亚、以色列的赫尼塔、曼彻斯特等
德国——刀柄工具系统有雄克、海默、凯狮、格威法、戴博、瑞品等,丝锥螺纹工具有卡迈斯、脑尼斯、埃莫克.法兰肯、钴领、毅力等
有了好的刀具,在看看机床,作为机加工的主要工具,机床的好坏,先进与否,直接决定了加工产品的质量与生产效率。现代机床业慢慢的从简单到复杂,有半自动向着自动化迈进。随着生产的需要对机床的要求也越来越高,现在就来看看,我国与世界机床的发展趋势
中国机床产业发展趋势可分为以下几个方面:
1.产业发展趋势
(1)产业发展空间巨大,产业整体技术水平提升趋势明显
中国机床行业目前产品门类比较齐全、具备一定的技术基础和制造能力,在强劲市场需求拉动下,产业的上升空间很大。
(2)中低需求将长期存在,产业结构与产能将逐步优化
我国机床产品目前数控化率还比较低,地区和产业发展也不平衡,多种经济形式将长期存在,这些因素都决定未来中国机床市场的中低需求将长期在。
(3)行业内将会涌现出一批大而强、小而精或小而专的企业
以研制重型机床、加工中心、数控车床、精密磨床、齿轮加工机床、电加工机床和锻压机床为代表的大型企业集团或专业化企业将逐渐形成并得到快速发展。产业的国际化水平将进一步提升,预计未来十年内进入世界机床百强的企业将增至十家以上。
(4)产业地域分布更趋合理,产业聚集度将进一步提高
随着国家区域经济规划的逐步落实,特别是市场配置资源手段在地区经济发展中作用的显现,机床行业的产业布局将呈现地域分布的特点。未来将形成以东北、西北、华东、西南、江浙等地区为代表的机床产业集聚区,在集聚区内围绕特色产品或机床产业集团将形成支撑产业群。。
2.技术发展趋势
(1)技术研究模式转变,市场需求拉动成为主导
中国机床行业技术研究模式从被动式到自主创新转变,研究主体从单一向多元转变,市场需求成为研究的主要动力。如超重型龙门车铣复合机床、加工直径28米立式车床等产品都是在国内不断提高的市场需求下研制成功的。因此,在市场需求拉动下,中国机床行业的研究模式将发生重大转变。
(2)技术投入多元化,技术创新平台和产业创新联盟将发挥主导作用
在国家投资继续发挥导向性作用的同时,企业自筹资金、社会化融资、外资将成为技术投入的重要组成部分。以企业为龙头、高校和科研院所参与形成的技术创新平台和同行业企业组成的产业创新联盟将发挥主导作用。
(3)技术研究的国际化程度提高,人才全球化配置趋势明显
由于研究模式的转变和研究投入的多元化,中国机床行业的技术研究国际化参与度将显著提升。这将主要体现在两个方面:一是更多的企业开始与国际领先的研究机构或公司合作研究;二是更多的企业有能力为国际机床用户提供技术服务。
(4)技术研究实力增强,技术发展步伐与发达国家同步
高精度、高速度、复合化、柔性化、智能化、绿色制造将成为中国机床行
业发展的主要方向,产品制造精度、制造能力和技术服务水平将得到极大提升。
(5)技术应用发展趋势预测
●直驱技术将在中高档数控机床上大量采用,机床结构更加适应高速、高精加工需要。
●智能辅助编程和操作软件将成为数控机床的标准配置,机床具备智能化监控功能,配合网络接口可实现远程控制和效能管理
●加工规格、精度和性能指标向极限化发展。
●机床加工效率提高,单位能耗降低,环保加工方法将替代传统
●自动化装置在机床上集成应用,机床的自动化水平更高。
●高效、精密特种加工技术得到充分发展,在一定范围内可替代传统加工方法,更多用户开始应用相关技术组建新的零件生产线。
3、合作共赢是中外机床企业所面临的必然选择
大家都知道,面对金融危机对全球经济的影响,无论是发达国家,还是发展中国家,都达成了这样的共识——合作共赢是共渡难关的必然选择。
机床产业也不应例外,面对后金融危机对全球机床产业的持续影响,面对未来几年中国机床市场的机遇,合作共赢也必将成为中外机床企业所面临的必然选择。
在这里所讲的合作,既包括中外企业之间的合作,也包括国内企业之间的合作;既包括主机企业与配套企业之间的合作,也包括企业与高校、科研院所之间的合作。
合作领域应包括研发与设计、制造、销售和服务、培训等各个层面。在未来5至10年里,中外企业针对汽车、航空航天、船舶、轨道交通、能源等国家重点行业核心制造领域的需求,在高档数控机床、数控系统、关键功能部件等领域开展合作,前景应该看好。全行业应从不同的角度思考寻求合作的广度和深度,不应局限于技术、产品、制造层面的合作,应积极探索商业模式间的合作。
中国机床产业经过几十年的发展历程,目前已经解决了从无到有和从小到大的问题。基于中国市场的巨大需求和装备制造业的产业升级,在各级政府的关怀和支持下,我相信,经过全行业企业的共同努力,通过走合作共赢之路,就一定能够实现“既强又大”的目标。
中国著名机床产业:
沈阳机床有限公司
济南一机床有限公司
济南二机床集团
大连机床集团有限责任公司
北京第一机床厂
汉川机床集团有限公司
秦川机床集团有限公司
齐重数控装备股份有限公司
齐齐哈尔二机床(集团)有限责任公司
天水星火机床有限责任公司
青海华鼎重型机床有限责任公司
江苏新瑞机械有限公司
四川长征机床集团有限公司
云南CY集团有限公司
桂林机床股份有限公司
武汉重型机床集团有限公司
上海电气机床集团
世界机床工具技术发展成果与趋势
1.机床复合技术进一步扩展
随着技术进步,五轴联动加工技术日趋成熟。芝加哥、汉诺威、东京、北京四大国际机床展览会上,每届都展出四五十台,甚至上百台五轴联动机床。五轴联动不限于X、Y、Z、A、B(或C)轴联动,而是包括U、V、W轴不同组合的多轴控制五轴联动,同时,立卧转换铣头已经广泛应用于五轴立式加工中心。
各类复合机床纷纷亮相。复合机床包括铣车复合、车铣复合、车一镬一钻一齿轮加工等复合、车磨复合、成形复合加工、特种复合加工等,并出现多主轴、多刀塔的复合机床,加工效率大大提高。“一台机床就是一个加工厂”、“一次装卡,完全加工”等理念正在被人接受。
2.智能化技术有新突破
智能化提升了机床的功能和品质,在数控系统上得到了较多体现。在智能化方面具有更强的功能:断电保护功能、加工零件检测和自动补偿学习功能、高精度加工零件智能化参数选用功能。
防震动功能(AVC);热补偿功能(ITC);防碰撞功能(155);语音提示功能(MvA);智能主轴(IPs);智能平衡分析器(IMS);设备维护智能支持系统(IBA)。
三维仿真、智能化刀具管理软件,高精度在线测量系统、刀具磨损补偿、温度补偿等等。
3.机器人使柔性化组合效率更高
机器人与主机的柔性化组合得到广泛应用,机器人与加工中心、车铣复合机床、磨床、齿轮加工机床、工具磨床、电加工机床、锯床、冲压机床、激光加工机床、水切割机床等组成多种形式的柔性单元和柔性生产线。
4.精密加工技术有了新进展
发达国家通过机床结构设计优化、机床零部件的超精加工和精密装配、采用高精度的全闭环控制及温度、振动等动态误差补偿技术,提高机床加工的几何精度,降低形位误差、表面粗糙度等,从而进人亚微米、纳米级超精加工时代。
5.功能部件性能不断提高
功能部件不断向高速度、高精度、大功率和智能化方向发展,并取得成熟的应用。如电主轴、全数字交流伺服电机及驱动装置、力矩电机、直线电机、滚珠丝杠、直线导轨等功能部件的性能指标不断提高。
6.新技术提高了机床的性能
日本大限公司推出机床防碰撞系统和热补偿系统,目前已经有多家公司在机床上应用;日本森精机公司的高刚度、箱中箱的机床主体结构,以及重心驱动技术已开始流行。森精机公司推出的高档数控机床四项新技术,全面提高了机床的性能,四项新技术是:重心驱动(DCG)、电机直接驱动(DDM)、内装电机刀塔(BMT)、八角形滑块(ORC)。日本马扎克公司推出拥有7项智能技术的
i一系列机床,德国DMG集团推出以复合和智能技术创新的第五代机床等表明,新技术的应用使数控机床的技术进步已经到了一个崭新的阶段。
7.数控刀具和测量仪器有了新的发展高速、高效、复合、高精度、高可靠性及环保是数控刀具的发展方向。
发达国家数控刀具制造技术在刀具材料、刀具镀层技术、刀具结构设计、刀具连接件和工具系统、以及切削数据库等方面,都取得了突出成就,使得数控刀具提高到一个崭新的水平。
数字化、高精度、智能化、非接触测量仪器和在线测量技术取得新的进展,新的测量仪器和测量系统不断出现,以三坐标测量机为代表的精密测量仪器应用扩大;带CCD数字摄像头、激光测头及触发测头的多传感测头光学坐标测量仪得到快速发展;激光干涉测量系统和球杆仪在数控机床几何精度和运动精度的监测和监控中,得到了广泛应用。
通过计算机技术、通讯技术将数控机床、数控刀具、数控测量系统和加工工件以及相应的信息集成融合在一起,构成数字化闭环切削加工系统,成为计算机集成制造系统的基本单元。
8.绿色制造技术开始起步
现代数控机床既要高性能、高效率,又要节约资源、低能耗、低污染,加工过程对人友好和宜人化。要从机床的设计开始,材料选用、制造、使用过程直至机床报废回收,形成“绿色”的全过程。欧盟已经启动“绿色机床”研究项目,提出机床绿色和能耗标准设想,说明绿色制造技术开始起步。
宜人化改进,如流线型外罩,宽敞的航空玻璃视窗;可调角度的控制面板和19''显示屏;可调节座椅;通过传输技术授权的开关钥匙;显示机床工作状态的可视光带等,外观造型简洁、明快,富于现代感。
世界机床著名品牌
德国——通快
日本——山崎马扎克
德国——吉德曼
日本——大隈,天田,森精机,捷泰克特
美国——MAG
德国——伊玛铬
瑞士——阿奇夏米尔
美国——哈斯
德国——斯莱福临
中国机床产业与世界机床产业的差距:
目前中国机床产业仅仅在规模方面具有相对比较优势,与机床制造强国相比较,在结构、水平、研发和服务能力等方面都还存在明显的差距:
①低端产品产能过剩,价格战,高端产品主要依赖进口。2009年国产机床的市场占有率虽然已上升至70.1 %,但是进口机床仍高达59亿美元,其中金切机床45.6亿美元,金属成形机床13.4亿美元。进口产品几乎都是高档数控机床(包括成套生产线)。可见,针对高端产品的需求,国产机床长期以来一直存在所供非所需,所需不能供的结构性矛盾,目前虽有改善,但仍然没有从根本上改变。
②高性能数控系统和功能部件的发展滞后于主机,并已成为制约数控机床产业发展的瓶颈。
③自主创新能力不强。基础、关键、共性技术尚未完全掌握,以企业为主体,产学研用相结合,开放式、社会化的研发体系建设尚处于探索阶段。
④中国机床产业还没有实现由生产制造向服务制造模式的转型。尤其是工程集成能力弱,为汽车等重点行业核心制造领域提供成套生产线还处于起步阶段。
⑤产业集中度不高。企业多而散,全行业企业多达5944家;主机企业大而不强,小而不精;配套能力弱,产业分工不清晰;与数控机床产业快速发展相适应的产业链体系还不够完善。
⑥高端人才匮乏,尤其是缺少高端数控机床、数控系统和功能部件研发的领军人才;缺少高级技工;缺少具有国际化视野的复合型管理人才。目前,高端人才不足已成为制约数控机床产业快速、可持续发展的深层次原因。
数控机床与普通机床的结构图比较-国内外发展趋势与就业分析
数控机床与普通机床的结构图比较,国内外发展趋势与就业分析 数控机床与普通机床结构图比较 在传统的普通机床中,主运动一般采用多轴乘积式分级变速机构,系统构造复杂,传动链长,从而导致传动精度低且动态性能差。现代数控机床多采用直流或交流调速电机驱动主轴的转动,由电机加无级调速或者很少几级分级变速实现传动,分级变速采用3、4对变速齿轮或塔轮,这种传动方式的传动链断,不仅传动精度高而且实现自动控制比较容易。数控机床的进给运动都采用伺服系统,因而步进电机,滚珠丝杆、滚动导轨或滚动支承等功能元件的应用愈来愈普遍,使得进给箱与滑板箱的构造也得以简化。 国内外发展趋势 目前,数控机床的发展日新月异,高速化、高精度化、复合化、智能化、并联驱动化、、极端化、绿色化已成为数控机床发展的趋势和方向。 1..高速化 随着汽车、国防、航空、航天等工业的高速发展以及铝合金等新材料的应用,对数控机 床加工的高速化要求越来越高。其中主要是主轴转速、进给率、运算速度、换刀速度提高 2.高精度化 数控机床精度的要求现在已经不局限于静态的几何精度,机床的运动精度、热变形以及对振动的监测和补偿越来越获得重视。 3.功能复合化 复合机床的含义是指在一台机床上实现或尽可能完成从毛坯至成品的多种要素加工。根据其结构特点可分为工艺复合型和工序复合型两类。工艺复合型机床如镗铣钻复合——加工中心、车铣复合——车削中心、铣镗钻车复合——复合加工中心等;工序复合型机床如多面多轴联动加工的复合机床和双主轴车削中心等。采用复合机床进行加工,减少了工件装卸、更换和调整刀具的辅助时间以及中间过程中产生的误差,提高了球体磨床零件加工精度,缩短了产品制造周期,提高了生产效率和制造商的市场反应能力,相对于传统的工序分散的生产方法具有明显的优势。 4 控制智能化 随着人工智能技术的发展,为了满足制造业生产柔性化、制造自动化的发展需求,数控机床的智能化程度在不断提高。主要包括加工过程自适应控制技术、加工参数的智能优化与选择、智能故障自诊断与自修复技术、智能故障回放和故障仿真技术、智能化交流伺服驱动装置、智能4M数控系统等。 5. 驱动并联化 并联运动机床克服了传统机床串联机构移动部件质量大、系统刚度低、刀具只能沿固定导轨进给、作业自由度偏低、设备加工灵活性和机动性不够等固有缺陷,在机床主轴(一般为动平台)与机座(一般为静平台)之间采用多杆并联联接机构驱动,可实现多坐标联动数控加工、装配和测量多种功能,更能满足复杂特种零件的加工,具有现代机器人的模块化程度高、重量轻和速度快等优点。
数控刀具的主要材料种类及用途
数控刀具的主要材料种类及用途 机床与刀具的发展是相辅相成、相互促进的。刀具是由机床、刀具和工件组成的切削加工工艺系统中最活跃的因素,刀具切削性能的好坏取决于刀具的材料和刀具结构。切削加工生产率和刀具寿命的高低加工成本的多少、加工精度和加工表面质量的优劣等,在很大程度上取决于刀具材料、刀具结构及切削参数的合理选择。近几十年来,作为切削加工最基本丰素的刀具材料得到了迅速发展,刀具的结构形式也得到了极大丰富。 数控刀具主要材料种类 (1)超硬刀具。所谓超硬材料是指人造金刚石和立方氮化硼(简称CBN),以及用这些粉末与结合剂烧结而成的聚晶金刚石(简称PCD)和聚晶立方氮化棚(简称PCBN)等。超硬材料具有优良的耐磨性,主要运用于高速切削及难切削材料的加工。 (2)陶瓷刀具。陶瓷刀具具有很高的硬度、耐磨性能及良好的高温力学性能,与金属的亲合力小,不易与金属产生粘结,并且化学稳定性好。陶瓷刀具主要应用于钢、铸铁及其合金和难加工材料的切削加工,可以用于超高速切削、高速切削和硬材料切削。 (3)涂层刀具。刀具涂层技术自问世以来,对刀具性能的改善和加工技术进步起着非常重要的作用,涂层技术将传统刀具涂覆一层薄膜后,刀具性能发生了巨大的变化。主要的涂层材料有:Tic、TiN、Ti(C,N)、TiALN、ALTiN等。涂层技术己应用于立铣刀、铰刀、钻头、复合孔加工刀具、齿轮滚刀、插齿刀、剃齿刀、成形拉刀及各种机夹可转位刀片,满足高速切削加工高强度、高硬度铸铁(钢)、锻钢、不锈钢、钛合金、镍合金、镁合金、铝合金、粉末冶金、非金属等材质工件的生产技术不同要求。 (4)硬质合金。硬质合刀具是数控加工刀具的主导产品,有的国家有90%以上的车刀和55%以上的铣刀都采用了硬质合金制造,而且这种趋势还在增加。硬质合金可分为普通硬质合金、细晶粒硬质合金和超晶粒硬质合金。按化学成分区
国内外数控机床对比
国内外当下主产机床对比 1 中高档、中低档数控系统的综合比较 以下精选各数控公司的中高档数控系统、中低档数控系统中最佳性能产品加以比较: (1)广州数控GSK21M数控系统 系统具有4轴3联动控制功能,可扩展至7轴4联动控制;支持直线、圆弧、样条曲线插补;最快进给速度可达60m/min;系统具有256点输入输出点;,支持梯形图编程;具有99组刀具长度补偿和刀具半径补偿;直线坐标轴具有反向间隙及螺距误差补偿;系统支持刚性攻丝;系统采用4级密码控制系统操作权限;采用电子盘,用户程序容量可达32MB;系统可通过RS232接口实现与PC机通信,用于传输程序、参数和梯形图。支持U盘存储。 (2)凯恩帝K1000M/T II系列数控系统 系统具有4轴4联动控制功能;数字量输入输出点数可达40/24个,支持梯形图编程;数控系统NC代码处理速度可达10000/18s,最快进给速度可达24m/min;系统具有直线插补、圆弧插补、螺旋线插补等基本插补控制功能;具有刀具半径补偿、刀具长度补偿;具有反向间隙和螺距误差补偿;系统支持刚性攻丝;系统采用4级密码控制系统操作权限;采用电子盘,用户程序容量可达640KB;系统可通过RS232接口实现与PC机通信传输程序、参数和偏置。支持U盘存储。(3)华中数控世纪星HNC-21M/T系列数控系统 系统基于嵌入式PC,具有5轴4联动控制功能,具有脉冲输出接口、模拟量输出接口;数字量输入输出点数可达40/32个;系统最小分辨率1μm,最大移动速度:16m/min;系统具有直线、圆弧、螺旋线、正弦线插补,自动加减速控制;支持小线段连续加工功能,适用于复杂模具加工;系统支持反向间隙补偿,多达5000点的双向螺距误差补偿功能; 8MB Flash程序断电存储,8MBRAM加工缓冲区,可选配硬盘支持2GB数控程序存储;可采用RS232接口传输数控代码,可选配以太网接口;系统具有刀具半径补偿、刀尖半径补偿和刀具长度补偿等。(4)大连大森dasen-3i、dasen-9i 自1995年成立以来,陆续推出了大森Ⅰ型、Ⅱ型、Ⅲ型及大森Ⅵ型数控系统,属于中、低档数控产品。目前供应的大森3i型数控系统是大森Ⅲ型数控系统的升级产品:系统具有3轴3联动控制功能;具有PLC在线显示、编辑、监控功能;加工程序容量可升级为240KB;最快速移动速度可达240m/min;计算机联机传输速度可达19200bps;采用130,000p/r绝对值编码器。 大森9i型数控系统,具有3轴2轴联动控制功能;最小分辨率1μm,最大移动速度30m/min;RS232通信接口;具有反向间隙补偿和螺距误差补偿功能;具有刀具半径、刀尖半径、刀具长度补偿功能;程序容量40MB以上,最多支持100个数控程序;采用内置PLC,数字量输入输出点可达44/44个。 (5)日本FANUC公司Fanuc-0i MB/TB系列数控系统 系统具有4轴4联动控制功能;具有4路D/A模拟量伺服闭环控制接口;数字量输入输出点数可达96/64;分辨率1μm时进给速度可达240m/min,分辨率为0.1μm时进给速度可达100m/min;系统具有直线、圆弧、螺旋线插补功能,支持刚性攻丝;数控系统具有刀具半径补偿、刀具长度补偿,且几何误差、磨损误差可以分别补偿;数控系统支持反向间隙补偿、螺距误差补偿;PMC指令处理速度可达3.3ms/1000步,采用梯形图编程,最大存储容量可达4000步;系统支持密码
数控刀具种类_数控车床刀片型号
数控刀具种类_数控刀片型号 数控刀具是指与数控机床(包括加工中心、数控车床、数控镗铣床、数控钻床、自动线以及柔性制造系统)相配套使用的各种刀具的总称,是数控机床不可缺少的关键配套产品。在国外数控刀具发展很快,品种很多,已形成系列。在我国,由于对数控刀具的研究开发起步较晚,数控刀具成了工具行业中最薄弱的一个环节。数控刀具的落后已经成为影响我国国产和进口数控机床充分发挥作用的主要障碍。 数控刀具必须适应数控机床高速、高效和自动化程度高的特点,一般应包括刀具及连接刀柄:刀柄要连接刀具并装在机床的动力头上,因此已逐渐标准化和系列化。近年来,快速发展的数控加工技术促进了数控刀具的发展。每当一种新型数控刀具产品的面市,会使数控加工技术跃上一个新台阶,产生巨大的经济和社会效益。 数控刀具的分类方法很多。一般可按下列方法进行分类。 1.按刀具切削部分的材料分 按刀具切削部分的材料可分为高速钢刀具、硬质合金刀具、陶瓷刀具、立方氮化硼刀具、金 刚石刀具和涂层刀具等。 2.按刀具的结构形式分 按刀具的结构形式可分为整体式、镶嵌式和特殊形式等。 (1)整体式。整体式包括钻头和立铣刀等。
(2)镶嵌式。镶嵌式包括刀片采用焊接和机夹式等。 (3)特殊形式。特殊形式包括复合式和减振式等。 3。按切削加工工艺分 按切削加工工艺可分为车削刀具、铣削刀具、钻削刀具和镗削刀具等。 (1)车削刀具。车削刀具包括外圆车刀、内孔车刀、切槽(断)刀、端面车刀、螺纹车刀等: (2)铣削刀具。铣削刀具包括面铣刀、立铣刀和螺纹铣刀等。 (3)钻削刀具。钻削刀具包括钻头、铰刀和丝锥等。 (4)镗削刀具。镗削刀具包括粗镗刀和精镗刀等。 数控加工刀具可分为常规刀具和模块化刀具两大类。 模块化刀具是发展方向。发展模块化刀具的主要优点:减少换刀停机时间,提高生产加工时间;加快换刀及安装时间,提高小批量生产的经济性;提高刀具的标准化和合理化的程度;提高刀具的管理及柔性加工的水平;扩大刀具的利用率,充分发挥刀具的性能;有效地消除刀具测量工作的中断现象,可采用线外预调。事实上,由于模块刀具的发展,数控刀具已形成了三大系统,即车削刀具系统、钻削刀具系统和镗铣刀具系统。 (1)从结构上可分为 ② 体式 ②镶嵌式可分为焊接式和机夹式。机夹式根据刀体结构不同,分为 可转位和不转位; ③减振式当刀具的工作臂长与直径之比较大时,为了减少刀具的振
国内数控机床发展现状研究
国内数控机床发展现状研究 1国内数控机床发展概述 国内的数控机床近几年发展十分迅速,各种各样的数 控加工机床如雨后春笋般被不断被研发。低端机床的研 制量很大,但是对于高端机床设备的研发却始终依靠引 进与复制模式。总体上对国外技术依赖性太强,缺乏独立 的高端机床知识产权。 国内机床行业一直肩负着研制高端数控机床,支撑国 内重点项目与军品项目的建设。国产XNZD2415五轴机 床,综合传统机床与并联机床各自的特点,技术革新方面 也开了一个先河。拥有自己的安全可靠的控制系统,能够 很好地实现人机互动,较高精度的实现五轴联动。并且机 床的作业范围很广,实用性很强。 国内铣床也实现了五轴联动技术,采用刀具内冷却与 应力控制等高新技术。可用于潜艇涡轮,复杂型腔模具与 航天、军工等高难度、高质量要求的加工。 国内柔性制造系统也有了长足发展,采用模拟加工与 实际加工想结合方式,不仅能够提高加工质量与效率,还 大大降低了加工的成本与周期。 近几年我国的机床行业产值早已突破千亿,特别是技 术加工机床,占总产值的三分之一左右。中国继日、德、 意 ' ' 成为第四大机床销售国。 然而世界各国,特别是发达国家,机床行业的发展早 已经脱离初级阶段,进入层次更高的超高精度、超高效率、 超高质量领域发展,各种高新数控加工机床其科技水平超 过当前国内机床行业的发展。国内的机床行业发展虽然 很迅速,但是还是处于发达国家早已过渡完成的初级阶 段。 近十年来我国机床行业发展迅速,归结于中国快速发 展的相关制造业的急迫需求。虽然近几年的机床发展迅 速,销量也十分巨大,但是低端的数控机床占了很大一部 分,这也造成了中国基础制造业水平低下的原因。对于大 部分中高端数控机床和特种加工机床,仍需要大量的进 口,这方面中国缺少自己的知识产权,一直处于被动的 地位。我国机床的需求量在未来几年内还很大,在世界机 床总需求量中占据很大比重。如果中国的机床行业的技 术,特别是数控加工机床的高端技术一直缺乏,中国的机 床行业与制造行业将处于一个被动发展的模式。 很长一段时间,中国数控机床一直是一个低端的迅速 扩张,中端进展缓慢,关键高端设备依赖国外支持,特别是 在国家重点项目需要主要依靠进口,技术由他人控制。国 内企业在数控机床技术,与国外相比,产品设计、质量、 精度、性能较国外数控技术落后5_10年,在高精度和先 进技术的差距可以达到10—15年。与此同时,中国的技 术和技
机床与刀具简答题2
四、简答题: ▲为什么说对刀具耐用度的影响,υ为最大、f其次、p 最小? υ↑--P↑---切削热↑----温度T急剧↑ f↑--F↑---刀头散热面积不变-----温度T↑ a p--F↑(成倍)--刀头散热面积↑(成倍)--温度T基本不变 ▲试述粗加工与精加工时如何选择切削用量?选择原则是什么? 切削深度的选择:粗加工时尽可能一次去除加工余量 精加工时应一次切除精加工工序余量 进给量的选择:粗加工时的进给量应根据机床系统的强度和刀具强度选择 精加工时,一般切削深度不大,切削力较小 切削速度的选择:粗加工时切削速度受机床功率限制; 而精加工时,主要受刀具耐用度的限制 选择原则:首先选取尽可能大的被吃刀量;其次根据机床动力和刚性限制条件或加工表面粗糙度的要求,选取尽可能大的进给量;最后利用切削用量手册选取或者用公式计算确定切削速度。 ▲为什么加工塑性材料时,应尽可能采用大的前角?若前角选得过大又会带来什么问题,如何解决这个矛盾? γo↑→变形程度↓→切削力F↓→切削温度θ↓→刀具耐用度T↑,质量↑(2分)同时:γo↑→刀刃和刀头强度↓,散热面积容热体积↓断屑困难。(2分) 应根据不同切削条件,选择合理前角 ▲简述刀具材料应具备的基本性能。 高硬度;高耐磨性;高温硬度(红硬性);足够的强度与韧性;工艺性
▲我国金属切削机床按加工性质和所用刀具分为12类。请写出各类机床的名称及代号。 ▲试述粗加工与精加工时如何选择切削用量?选择原则是什么? 切削深度的选择:粗加工时尽可能一次去除加工余量; 精加工时应一次切除精加工工序余量 进给量的选择:粗加工时的进给量应根据机床系统的强度和刀具强度选择 精加工时,一般切削深度不大,切削力较小 切削速度的选择:粗加工时切削速度受机床功率限制; 而精加工时,主要受刀具耐用度的限制 选择原则:首先选取尽可能大的被吃刀量;其次根据机床动力和刚性限制条件或加工表面粗糙度的要求,选取尽可能大的进给量;最后利用切削用量手册选取或者用公式计算确定切削速度。 ▲ B665, CB3463-1, M2110B各表示哪类机床,解释其中字母“B”的不同意义? B665:B表示机床类型,指刨床。CB3463-1:B表示半自动。 M2110B:B是指机床的第二次改进。 ▲简述刀具耐用度和刀具寿命的区别及其联系。 区别:刀具耐用度:是指刃磨后的刀具自开始切削直到磨损量达到磨钝标准为止的切削时间,指正常使用时间范围。 刀具寿命:是指一把新刀具到“报废”为止所经历的切削时间,指到报废的时间范围。 联系:刀具寿命等于刀具耐用度和(n+1)的乘积。 ▲解释为什么端铣较周铣平面时,表面质量相对较好?
加工中心的刀具及参数选择
加工中心的刀具及参数选择 刀具的选择和切削用量的确定是数控加工工艺中的重要内容,它不仅影响数控机床的加工效率,而且直接影响加工质量。CAD/CAM技术的发展,使得在数控加工中直接利用CAD的设计数据成为可能,特别是微机与数控机床的联接,使得设计、工艺规划及编程的整个过程全部在计算机上完成,一般不需要输出专门的工艺文件。现在,许多CAD/CAM软件包都提供自动编程功能,这些软件一般是在编程界面中提示工艺规划的有关问题,比如,刀具选择、加工路径规划、切削用量设定等,编程人员只要设置了有关的参数,就可以自动生成NC程序并传输至数控机床完成加工。因此,数控加工中的刀具选择和切削用量确定是在人机交互状态下完成的,这与普通机床加工形成鲜明的对比,同时也要求编程人员必须掌握刀具选择和切削用量确定的基本原则,在编程时充分考虑数控加工的特点。本文对数控编程中必须面对的刀具选择和切削用量确定问题进行了探讨,给出了若干原则和建议,并对应该注意的问题进行了讨论。 一、数控加工常用刀具的种类及特点 数控加工刀具必须适应数控机床高速、高效和自动化程度高的特点,一般应包括通用刀具、通用连接刀柄及少量专用刀柄。刀柄要联接刀具并装在机床动力头上,因此已逐渐标准化和系列化。数控刀具的分类有多种方法。根据刀具结构可分为: ①整体式; ②镶嵌式,采用焊接或机夹式连接,机夹式又可分为不转位和可转位两种;
③特殊型式,如复合式刀具,减震式刀具等。 根据制造刀具所用的材料可分为: ①高速钢刀具; ②硬质合金刀具; ③金刚石刀具; ④其他材料刀具,如立方氮化硼刀具,陶瓷刀具等。 从切削工艺上可分为: ①车削刀具,分外圆、内孔、螺纹、切割刀具等多种; ②钻削刀具,包括钻头、铰刀、丝锥等; ③镗削刀具; ④铣削刀具等。 为了适应数控机床对刀具耐用、稳定、易调、可换等的要求,近几年机夹式可转位刀具得到广泛的应用,在数量上达到整个数控刀具的30%~40%,金属切除量占总数的80%~90%。数控刀具与普通机床上所用的刀具相比,有许多不同的要求,主要有以下特点: ⑴刚性好(尤其是粗加工刀具),精度高,抗振及热变形小; ⑵互换性好,便于快速换刀; ⑶寿命高,切削性能稳定、可靠; ⑷刀具的尺寸便于调整,以减少换刀调整时间; ⑸刀具应能可靠地断屑或卷屑,以利于切屑的排除; ⑹系列化,标准化,以利于编程和刀具管理。 二、数控加工刀具的选择 刀具的选择是在数控编程的人机交互状态下进行的。应根据机床的加工能力、工件材料的性能、加工工序、切削用量以及其它相关因
数控车床常用刀具及选择
数控车床常用刀具及选择 1.数控刀具的结构数控车床刀具种类繁多,功能互不相同。根据不同的加工条件正确选择刀具是编制程序的重要环节,因此必须对车刀的种类及特点有一个基本的了解。在数控车床上使用的刀具有外圆车刀、钻头、镗刀、切断刀、螺纹加工刀具等,其中以外圆车刀、镗刀、钻头最为常用。 数控车床使用的车刀、镗刀、切断刀、螺纹加工刀具均有整体式和机夹式之分,除经济型数控车床 外,目前已广泛使用可转位机夹式车刀。 (1) 数控车床可转位刀具特点 数控车床所采用的可转位车刀,其几何参数是通过刀片结构形状和刀体上刀片槽座的方位安装组合形成的,与通用车床相比一般无本质的区别,其基本结构、功能特点是相同的。但数控车床的加工工序是自动完成的,因此对可转位车刀的要求又有别于通用车床所使用的刀具,具体要求和特点如下表所示。 表2-2 可转位车刀特点 (2) 可转位车刀的种类可转位车刀按其用途可分为外圆车刀、仿形车刀、端面车刀、内圆车刀、 切槽车刀、切断车刀和螺纹车刀等,见表2-3。 表2-3 可转位车刀的种类
端面车刀900、450、750 普通车床和数控车床 内圆车刀450、600、750、900、910、930、 950、107.50 普通车床和数控车床 切断车刀普通车床和数控车床 螺纹车刀普通车床和数控车床 切槽车刀普通车床和数控车床 (3) 可转位车刀的结构形式 ①杠杆式: 结构见图2-16,由杠杆、螺钉、刀垫、刀垫销、刀片所组成。这种方式依靠螺钉旋紧压靠杠杆,由杠杆的力压紧刀片达到夹固的目的。其特点适合各种正、负前角的刀片,有效的前角范围为-60°~ +180°;切屑可无阻碍地流过,切削热不影响螺孔和杠杆;两面槽壁给刀片有力的支撑,并确保转位精度。 ②楔块式: 其结构见图2-17,由紧定螺钉、刀垫、销、楔块、刀片所组成。这种方式依靠销与楔块的挤压力将刀片紧固。其特点适合各种负前角刀片,有效前角的变化范围为-60~+180。两面无槽壁,便于仿形切削 或倒转操作时留有间隙。 ③楔块夹紧式: 其结构见图2-18,由紧定螺钉、刀垫、销、压紧楔块、刀片所组成。这种方式依靠销与楔块的压下力将刀片夹紧。其特点同楔块式,但切屑流畅不如楔块式。 此外还有螺栓上压式、压孔式、上压式等形式。 2、刀片材料 刀具材料切削性能的优劣直接影响切削加工的生产率和加工表面的质量。刀具新材料的出现,往往
国内外数控机床发展现状教学内容
国内外数控机床发展 现状
国内外数控机床发展现状分析 摘要:简述了国内数控机床近年来的发展。近年国内数控机床发展迅速,产量不断增加,但高端产品数量太少,无法与国外数控机床竞争。而国外数控机床,尤其是西门子和发那科则占据了绝大部分世界市场。我国数控机床产业还存在诸多问题有待解决。 关键词:数控机床、发展、现状 当今世界,工业发达国家对机床工业高度重视,竟相发展机电一体化、高精、高效、高自动化先进机床,以加速工业和国民经济的发展。如今国内数控机床发展迅速,年产量逐年攀升,但所产机床精度等方面达不到要求。长期以来,欧、美、亚在国际市场上相互展开激烈竞争,已形成一条无形战线,特别是随微电子、计算机技术的进步,数控机床在20世纪80年代以后加速发展,各方用户提出更多需求,早已成为四大国际机床展上各国机床制造商竞相展示先进技术、争夺用户、扩大市场的焦点。 虽然大力发展装备制造业已成为全社会的共识,但国内绝大多数重要机械制造装备的数字化控制系统却不是中国造。尤其是关系国家战略地位和体现国家综合国力水平的高档数控机床,它的“大脑”和“心脏”却要大部分从国外引进。专家呼吁,以数控机床为代表的“中国制造”不能没有创造,开发自主知识产权的数控系统迫在眉睫。 一、国内数控机床发展现状 1.1 国内数控机床近几年发展 我国的数控机床无论从产品种类、技术水平、质量和产量上都取得了很大的发展,在一些关键技术方面也取得了重大突破。据统计,目前我国可供市场的数控机床有1500种,几乎覆盖了整个金属切削机床的品种类别和主要的锻压机械。这标志着国内数控机床已进入快速发展的时期。 近年来我国机床行业不断承担为国家重点工程和国防军工建设提供高水平数控设备的任务。如国产XNZD2415型数控龙门混联机床充分吸取并联机床的配置灵活与多样性和传统机床加工范围大的优点,通过两自由度平行四边形并联机构形成基础龙门,在并联平台上附加两自由度串联结构的A、C轴摆角铣头,配以工作台的纵向移动,可完成五自由度的运动。该构型为国际首创。基于RT一Linux开发的数控系统具有的实时性和可靠性,能在同一网络中与多台PLC相连接,可控制机床的五轴联动,实现人机对话。该机床的作业空间4.5mx1.6mx1.2m,A轴转角±1050,C轴连续转角0一4000,主轴转速(无级)最高 10000r/min,重复定位精度±0.01mm,可实现三维立体曲面如水轮机叶片,导叶的五轴联动高速切削加工。 超精密球的加面车床为陀螺仪工提供了基础设备,这类车床也可用于透镜模具、照相机塑料镜片、条型码阅读设备、激光加工机光路系统用聚焦反射镜等产品的加工。 高速五轴龙门铣床采用铣头内油雾润滑冷却、横梁预应力反变形控制等技术。这类铣
机床与刀具2014复习 2
一、填空题: 1、刀具角度标注通常采用主剖面参考系,它由基面、切削平面及主剖面三个基准平面构成,刀具的主偏角、副偏角和刀尖角在基面内测量。 2、我们将金属切削运动分为主运动和进给运动,其中主运动只能有一个。而进给运动则可能有多个。外圆磨削时,共有砂轮转动、工件转动和工件移动三个运动,它们分别属主运动、径向进给运动和轴向进给运动。 3、金属切削过程中,切削用量三要素表示三个物理量,它们的名称、代号分别为切削速度v、进给量f、和背吃刀量ap,其中切削速度v对切削温度及刀具耐用度影响最大。 4 、由法平(剖)面Pn、基面Pr及切削平面Ps三个基准平面构成的刀具标注角度参考系称正交平面 参考系,对应此参考系的六个独立刀具标注角度为前角、 后角、副后角、主偏角、副偏角和刃倾角。 5、金属切削过程中,切削速度、进给量和背吃刀量称为切削用量三要素。若背吃刀量增加,切削变形不变,而切削力成倍增大。 6、切屑通常分为带状切削、节状切削、粒状切削、和崩碎切削等四种形态。一般,在切削脆性材料铸铁时,不会产生的切屑形态为 带状切削。 7、刀具的主切削刃与基面之间的夹角称为刃倾角,改变刃倾角可以改变切屑流出方向。当刀尖位于切削刃的最高点时,其角度为正,切屑流向已加工表面 表面;反之,切屑流向待加共表面表面。 9、通常切削用量的选择应考虑有效控制切削温度以提高刀具的耐用度,在机床条件允许下,选用大的进给 量,背吃刀量,比选用大的切削速度有利。 10、砂轮的五个特性参数包括磨料、粒度、硬度、结合剂和气孔。其中,硬度是指磨粒在磨削力作用下,从砂轮表面脱落的难易程度。工件材料越硬,则选用的砂轮越软。 11、、砂轮的组织由磨粒、结合剂、气孔三部分组成,粗磨时,应选择软砂轮,精磨时应选择紧密组织砂轮。 12、铣削加工时,工件的进给方向与铣刀转动方向一致的称为顺铣,方向相反的则称为逆 铣。采用顺铣方法加工,加工表面质量较好,铣刀寿命也可提高。对于进给丝杆和螺母有间隙的铣床,采用顺铣方法会造成工作台窜动。 13、齿轮加工按轮齿成形原理分两大类:分别是成形法和展成法,铣齿加工属成形法,滚齿加工属展成法。其中,展成加工的加工精度和生产率较高,一把刀可加工相同模数、压力角的任何齿数的齿轮。
与国内外数控系统的比较
2011年7月,中国机床工具工业协会执行副理事长王黎明日前指出:中国95%的高档机床数控系统仍依赖进口,国内高档系统的自给率不到5%,其中日本成为主要的进口国,约占1/3。在国际市场上,中、高档数控系统主要由以日本发那科公司、德国西门子公司为代表的少数企业所垄断,其中发那科占一半左右。在国内市场上,主要规模生产企业有20多家,以华中数控、广州数控、大连大森、北京凯恩帝、南京华兴等5家企业为代表。质量稳定性(可靠性)国内外存较大的差距 目前世界上的数控系统种类繁多,形式各异,组成结构上都有各自的特点。这些结构特点来源于系统初始设计的基本要求和工程设计的思路。例如对点位控制系统和连续轨迹控制系统就有截然不同的要求。对于T系统和M系统,同样也有很大的区别,前者适用于回转体零件加工,后者适合于异形非回转体的零件加工。对于不同的生产厂家来说,基于历史发展因素以及各自因地而异的复杂因素的影响,在设计思想上也可能各有千秋。例如,美国Dynapath系统采用小板结构,便于板子更换和灵活结合,而日本FANUC系统则趋向大板结构,使之有利于系统工作的可靠性,促使系统的平均无故障率不断提高。然而无论哪种系统,它们的基本原理和构成是十分相似的。 一般整个数控系统由三大部分组成,即控制系统,伺服系统和位置测量系统。控制系统按加工工件程序进行插补运算,发出控制指令到伺服驱动系统;伺服驱动系统将控制指令放大,由伺服电机驱动机械按要求运动;测量系统检测机械的运动位置或速度,并反馈到控制系统,来修正控制指令。这三部分有机结合,组成完整的闭环控制的数控系统。 数控系统到目前为止共发展了六代,第一代是电子管数控系统,第二代是晶体管数控系统,第三代是集成电路数控系统,第四代是小型计算机数控系统,第五代是微型计算机数控系统,第六代是PC数控系统。 PC数控系统目前是最先进的结构体系,PC数控系统的发展,形成了PC嵌入NC的“NC+PC”结构和NC嵌入PC的“PC+NC”结构两大主要流派。后者又正在演变成PC+I/O的“软件化”结构。 在NC+PC系统方面,起主导作用的是一些老的数控系统生产大厂。因为他们在数控系统方面有着深厚的基础,为使所掌握的技术优势与新的PC化潮流相融合,因此走出了一条以传统数控平台为基础(完成实时控制任务),以流行PC为前端(完成非实时任务)的PC数控系统发展道路,并在商品化方面取得了显著成绩。NC+PC系统的典型代表有日本FANUC 公司的18i、16i系统、德国西门子公司的840D系统、法国NUM公司的1060系统、美国AB公司的9/360系统等。 在PC+NC系统方面,主导公司是一些后起之秀。由于他们没有历史包袱,因此彻底摆脱了传统NC的约束,直接站在PC平台基础上,通过增扩NC控制板卡(如基于DSP的运动控制卡等)来发展PC数控系统。典型代表有美国DELTA TAU公司用PMAC多轴运动控制卡构造的PMAC-NC系统、日本MAZAK公司用三菱公司的MELDASMAGIC 64构造的MAZA TROL 640系统、中国华中数控系列产品、航天数控系列产品、广州数控部分产品、南京四开公司产品等。 从目前的情况看,新推出的PC数控系统已越来越多地采用PC+NC结构,NC+PC结构的发展已呈下降趋势。 随着PC技术水平和数控软件设计水平的提高,PC+NC结构正逐渐发展成PC+I/O的软件化结构和PC+实时网络的分布式结构。典型代表有美国MDSI公司的OPEN CNC、德国POWER AUTOMA TION公司的PA8000 NT、大连光洋公司、陕西华拓科技公司等系列产品。 常用的数控系统有发那科、西门子、三菱、广数、华中等数控系统。 发那科(FANUC)系统 FANUC系统在设计中大量采用模块化结构。这种结构易于拆装、各个控制板高度集成,使可靠性有很大提高,而且便于维修、更换。FANUC系统设计了比较健全的自我保护电路。FANUC系统性能稳定,操作界面友好,系统各系列总体结构非常的类似,具有基本统一的操作界面。FANUC系统可以在较为宽泛的环境中使用,对于电压、温度等外界条件的要求不是特别高,因此适应性很强。 西门子(SINUMERIK)数控系统 SINUMERIK 不仅意味着一系列数控产品,其力度在于生产一种适于各种控制领域不同控制需求的数控系统,其构成只需很少的部件。它具有高度的模块化、开放性以及规范化的结构,适于操作、编程和监控。 三菱(MITSUBISHI)数控系统
数控机床刀具的选择
数控机床刀具的选择 数控机床刀具的选择 由于数控机床的主轴转速及范围远远高于普通机床,而且主轴输出功率较大,因此与传统加工方法相比,对数控加工刀具的提出了 更高的要求,包括精度高、强度大、刚性好、耐用度高,而且要求 尺寸稳定,安装调整方便。这就要求刀具的结构合理、几何参数标 准化、系列化。数控刀具是提高加工效率的先决条件之一,它的选 用取决于被加工零件的几何形状、材料状态、夹具和机床选用刀具 的刚性。 数控机床选择刀具应考虑以下方面: (1)根据零件材料的切削性能选择刀具。如车或铣高强度钢、钛 合金、不锈钢零件,建议选择耐磨性较好的可转位硬质合金刀具。 (2)根据零件的加工阶段选择刀具。即粗加工阶段以去除余量为主,应选择刚性较好、精度较低的刀具,半精加工、精加工阶段以 保证零件的加工精度和产品质量为主,应选择耐用度高、精度较高 的刀具,粗加工阶段所用刀具的精度最低、而精加工阶段所用刀具 的'精度最高。如果粗、精加工选择相同的刀具,建议粗加工时选用 精加工淘汰下来的刀具,因为精加工淘汰的刀具磨损情况大多为刃 部轻微磨损,涂层磨损修光,继续使用会影响精加工的加工质量, 但对粗加工的影响较小。 (3)根据加工区域的特点选择刀具和几何参数。在零件结构允许 的情况下应选用大直径、长径比值小的刀具;切削薄壁、超薄壁零件 的过中心铣刀端刃应有足够的向心角,以减少刀具和切削部位的切 削力。加工铝、铜等较软材料零件时应选择前角稍大一些的立铣刀,齿数也不要超过4齿。 选取刀具时,要使刀具的尺寸与被加工工件的表面尺寸相适应。生产中,平面零件周边轮廓的加工,常采用立铣刀;铣削平面时,应
选硬质合金刀片铣刀;加工凸台、凹槽时,选高速钢立铣刀;加工毛坯表面或粗加工孔时,可选取镶硬质合金刀片的玉米铣刀;对一些立体型面和变斜角轮廓外形的加工,常采用球头铣刀、环形铣刀、锥形铣刀和盘形铣刀。 在进行自由曲面加工时,由于球头刀具的端部切削速度为零,因此,为保证加工精度,切削行距一般很小,故球头铣刀适用于曲面的精加工。而端铣刀无论是在表面加工质量上还是在加工效率上都远远优于球头铣刀,因此,在确保零件加工不过切的前提下,粗加工和半精加工曲面时,尽量选择端铣刀。另外,刀具的耐用度和精度与刀具价格关系极大,必须引起注意的是,在大多数情况下,选择好的刀具虽然增加了刀具成本,但由此带来的加工质量和加工效率的提高,则可以使整个加工成本大大降低。 在加工中心上,所有刀具全都预先装在刀库里,通过数控程序的选刀和换刀指令进行相应的换刀动作。必须选用适合机床刀具系统规格的相应标准刀柄,以便数控加工用刀具能够迅速、准确地安装到机床主轴上或返回刀库。编程人员应能够了解机床所用刀柄的结构尺寸、调整方法以及调整范围等方面的内容,以保证在编程时确定刀具的径向和轴向尺寸,合理安排刀具的排列顺序。
数控刀具选用习题与答案
单元二数控刀具与选用习题 一判断题 1.一般车削工件,欲得良好的精加工面,可选用正前角刀具。() 2.刀具前角越大,切屑越不易流出,切削力越大,但刀具的强度越高。() 3.粗车削应选用刀尖半径较小的车刀片。() 4.主偏角增大,刀具刀尖部分强度与散热条件变差。() 5.判断刀具磨损,可借助观察加工表面之粗糙度及切削的形状、颜色而定。() 6.精车削应选用刀尖半径较大的车刀片。( ) 7.高速钢车刀的韧性虽然比硬质合金高,但不能用于高速切削。( ) 8.硬质合金是一种耐磨性好,耐热性高,抗弯强度和冲击韧性多较高的一种刀具材料。() 9.在工具磨床上刃磨刀尖能保证切削部分具有正确的几何角度和尺寸精度及较小的表面粗糙度。( ) 10.YT类硬质合金中含钴量愈多,刀片硬度愈高,耐热性越好,但脆性越大。( ) 11.在切削过程中,刀具切削部分在高温时仍需保持其硬度,并能继续进行切削。这种具有高温硬度的性质称为红硬性。 ( ) 12.刀具的材料中,它们的耐热性由低到高次排列是碳素工具钢、合金工具钢,高速钢和硬质合金。() 13.数控机床对刀具材料的基本要求是高的硬度、高的耐磨性、高的红硬性和足够的强度和韧性。() 14.刀具规格化的优点之一为选用方便。() 二填空题 1.常用的刀具材料有高速钢、、陶瓷材料和超硬材料四类。 2.加工的圆弧半径较小时,刀具半径应选。 3.铣刀按切削部分材料分类,可分为铣刀和刀。 4.当金属切削刀具的刃倾角为负值时,刃尖位于主刀刃的最高点,切屑排出时流向工件表面。 5.工件材料的强度和硬度较低时,前角可以选得些;强度和硬度较高时,前角选得些。刀具切削部分的材料应具备如下性能;高的硬度、、、。 6.常用的刀具材料有碳素工具钢、合金工具钢、、四种。 7.影响刀具寿命的主要因素有;工件材料. 、、。 8.刀具磨钝标准有和两种料。
比较国内外机床与刀具的发展趋势
在工业、农业等各个生产领域里,在我们的日常生活中,我们会使用各种各样的机器设备和工具。这些机器和工具都是由一定的形状和尺寸的机械零件组成的。生产这些零件并把它们装配成机器或工具的工业成为机械制造业。而在机械制造业中所使用的主要加工设备就是机床。目前在世界各个国家中,加工制造业所创造的产值,均占有很大的比重,因此机床及其相关的产业发展直接关系到经济的发展和我们的生活水平的提高。由此我们可以看到机床及刀具的发展的重要性! 现代切削技术和高效先进刀具是制造业提高生产效率的最重要、最活跃的因素之一,目前我国的道具发展与机床相比,有很大的差距,大多数依然使用的是一些廉价的刀具。有先进的机床,却配不上先进的道具,使高效机床的加工效率得不到发挥,严重影响生产效率的提高,制约了制造业的现代化。刀具产业的发展从另一方面会所直接影响制约了我国加工制造业的发展。我们就来看一下未来刀具的发展趋势: 刀具的发展趋势: 1、硬质合金材料及涂层应用增多。细颗粒、超细颗粒硬质合金材料是发展方向;纳米涂层、梯度结构涂层及全新结构、材料的涂层将大幅度提高刀具使用性能;物理涂层(PVD)的应用继续增多。 2、新型刀具材料应用增多。陶瓷、金属陶瓷、氮化硅陶瓷、PCBN、PCD等刀具材料的韧性进一步增强,应用场合日趋增多。 3、高速切削、硬切削、干切削继续快速发展,应用范围在迅速扩大。 4、刀具制造商研发的重点不再是通用品牌和通用结构。面对复杂多变的应用场合和加工条件,研发针对性更强的刀片槽形结构、牌号及相应配套刀具取代通用的槽形、牌号的刀片及刀具。 5、刀具制造商角色转变。从单纯的刀具生产、供应,扩展至新切削工艺的开发及相应成套技术和解决方案的开发,为用户提供全面的技术支持和服务 6、信息化程度提高,刀具制造企业合作增强,市场竞争加剧。 世界著名刀具品牌: 山特维克集团旗下品牌——山特维克.可乐满、德国瓦尔特(含德国蒂泰克斯、德国普瑞特)美国万耐特、法国塞菲提、德国多马以及瑞典本土的山高(荷兰嘉伯乐、法国EPB IMC金属切削集团现旗下品牌——以色列的伊斯卡、英格索尔、特固克 日本东芝——泰珂洛、德国的创新、法国的无敌泰克 美国肯纳金属——旗下知名品牌:美国肯纳金属、德国威迪亚、以色列的赫尼塔、曼彻斯特等 德国——刀柄工具系统有雄克、海默、凯狮、格威法、戴博、瑞品等,丝锥螺纹工具有卡迈斯、脑尼斯、埃莫克.法兰肯、钴领、毅力等
机加工刀具的选择
刀具的选择和切削用量的确定是数控加工工艺中的重要内容,它不仅影响数控机床的加工效率,而且直接影响加工质量。CAD/CAM技术的发展,使得在数控加工中直接利用CAD的设计数据成为可能,特别是微机与数控机床的联接,使得设计、工艺规划及编程的整个过程全部在计算机上完成,一般不需要输出专门的工艺文件。 现在,许多CAD/CAM软件包都提供自动编程功能,这些软件一般是在编程界面中提示工艺规划的有关问题,比如,刀具选择、加工路径规划、切削用量设定等,编程人员只要设置了有关的参数,就可以自动生成NC程序并传输至数控机床完成加工。因此,数控加工中的刀具选择和切削用量确定是在人机交互状态下完成的,这与普通机床加工形成鲜明的对比,同时也要求编程人员必须掌握刀具选择和切削用量确定的基本原则,在编程时充分考虑数控加工的特点。本文对数控编程中必须面对的刀具选择和切削用量确定问题进行了探讨,给出了若干原则和建议,并对应该注意的问题进行了讨论。 一、数控加工常用刀具的种类及特点 数控加工刀具必须适应数控机床高速、高效和自动化程度高的特点,一般应包括通用刀具、通用连接刀柄及少量专
用刀柄。刀柄要联接刀具并装在机床动力头上,因此已逐渐标准化和系列化。数控刀具的分类有多种方法。根据刀具结构可分为:①整体式;②镶嵌式,采用焊接或机夹式连接,机夹式又可分为不转位和可转位两种;③特殊型式,如复合式刀具,减震式刀具等。根据制造刀具所用的材料可分为:①高速钢刀具;②硬质合金刀具;③金刚石刀具;④其他材料刀具,如立方氮化硼刀具,陶瓷刀具等。从切削工艺上可分为:①车削刀具,分外圆、内孔、螺纹、切割刀具等多种; ②钻削刀具,包括钻头、铰刀、丝锥等;③镗削刀具;④铣削刀具等。为了适应数控机床对刀具耐用、稳定、易调、可换等的要求,近几年机夹式可转位刀具得到广泛的应用,在数量上达到整个数控刀具的30%~40%,金属切除量占总数的80%~90%。 数控刀具与普通机床上所用的刀具相比,有许多不同的要求,主要有以下特点: ⑴刚性好(尤其是粗加工刀具),精度高,抗振及热变形小; ⑵互换性好,便于快速换刀; ⑶寿命高,切削性能稳定、可靠; ⑷刀具的尺寸便于调整,以减少换刀调整时间; ⑸刀具应能可靠地断屑或卷屑,以利于切屑的排除; ⑹系列化,标准化,以利于编程和刀具管理。
机床结构与刀具
机床结构与刀具 机床结构 具车削加工是机械加工中应用最为广泛的方法之一,主要用于回转体零件的加工。车床的加工工艺类型主要包括:钻中心孔、车外圆、车端面、钻孔、镗孔、铰孔、切槽、车螺纹、滚花、车锥面、车成形面、攻螺纹,此外借助于标准夹具(如四爪单动卡盘)或专用夹具,在车床上还可完成非回转体零件上的回转表面加工。 根据被加工零件的类型及尺寸不同,车削加工所用的车床有卧式、立式、仿形、仪表等多种类型。按被加工表面不同,所用的车刀也有外圆车刀、端面车刀、镗孔刀、螺纹车刀、切断刀等不同类型。此外,恰当地选择和使用夹具,不仅可以可靠地保证加工质量,提高生产率,还可以有效地拓展车削加工工艺范围。 普通车床 结构 CA6140型普通车床的主要组成部件有:主轴箱、进给箱、溜板箱、刀架、尾架、光杠丝杠和床身。 主轴箱:又称床头箱,它的主要任务是将主电机传来的旋转运动经过一系列的变速机构使主轴得到所需的正反两种转向的不同转速,同时主轴箱分出部分动力将运动传给进给箱。主轴箱中等主轴是车床的关键零件。主轴在轴承上运转的平稳性直接影响工件的加工质量,一旦主轴的旋转精度降低,则机床的使用价值就会降低。
进给箱:又称走刀箱,进给箱中装有进给运动的变速机构,调整其变速机构,可得到所需的进给量或螺距,通过光杠或丝杠将运动传至刀架以进行切削。 丝杠与光杠:用以联接进给箱与溜板箱,并把进给箱的运动和动力传给溜板箱,使溜板箱获得纵向直线运动。丝杠是专门用来车削各种螺纹而设置的,在进工件的其他表面车削时,只用光杠,不用丝杠。同学们要结合溜板箱的内容区分光杠与丝杠的区别。 溜板箱:是车床进给运动的操纵箱,内装有将光杠和丝杠的旋转运动变成刀架直线运动的机构,通过光杠传动实现刀架的纵向进给运动、横向进给运动和快速移动,通过丝杠带动刀架作纵向直线运动,以便车削螺纹。刀架、尾架和床身。 数控车床 一、数控车床类型 按结构分类 数控车床分为立式数控和卧式数控车床两种类型。 1)立式数控车床 用于回转直径较大的盘类零件的车削加工。 2)卧式数控车床 用于轴向尺寸较大或较小的盘类零件加工。相对与立式数控车床来说,卧式数控车床的结构形式较多、加工功能丰富、使用的面积较广。
数控机床刀具选择和合理使用
数控机床刀具选择和合理使用 数控加工刀具必须适应数控机床高速、高效和自动化程度高的特点,一般应包括通用刀具、通用连接刀柄及少量专用刀柄。刀柄要联接刀具并装在机床动力头上,因此已逐渐标准化和系列化。数控刀具的分类有多种方法。 根据刀具结构可分为:①整体式;②镶嵌式,采用焊接或机夹式联接,机夹式又可分为不转位和可转位两种;③特殊型式,如复合式刀具、减震式刀具等。根据制造刀具所用的材料可分为:①高速钢刀具;②硬质合金刀具;③金刚石刀具;④其他材料刀具,如立方氮化硼刀具、陶瓷刀具等。 从切削工艺上可分为:①车削刀具,分外圆、内孔、螺纹、切割刀具等多种;②钻削刀具,包括钻头、铰刀、丝锥等;③镗削刀具;④铣削刀具等。为了适应数控机床对刀具耐用、稳定、易调、可换等的要求,近几年机夹式可转位刀具得到广泛的应用,在数量上达到整个数控刀具的30%~40%,金属切除量占总数的80%~90%。 数控刀具与普通机床上所用的刀具相比,有许多不同的要求,主要有以下特点:①刚性好(尤其是粗加工刀具)、精度高、抗振及热变形小;②互换性好,便于快速换刀;③寿命高,切削性能稳定、可靠;④刀具的尺寸便于调整,以减少换刀调整时间;⑤刀具应能可靠地断屑或卷屑,以利于切屑的排除;⑥系列化、标准化,以利于编程和刀具管理。 刀具的选择是在数控编程的人机交互状态下进行的。应根据机床的加工能力、工件材料的性能、加工工序、切削用量以及其它相关因素正确选用刀具及刀柄。刀具选择总的原则是:安装调整方便、刚性好、耐用度和精度高。在满足加工要求的前提下,尽量选择较短的刀柄,以提高刀具加工的刚性。选取刀具时,要使刀具的尺寸与被加工工件的表面尺寸相适应。生产中,平面零件周边轮廓的加工,常采用立铣刀;铣削平面时,应选硬质合金刀片铣刀;加工凸台、凹槽时,选高速钢立铣刀;加工毛坯表面或粗加工孔时,可选取镶硬质合金刀片的玉米铣刀;对一些立体型面和变斜角轮廓外形的加工,常采用球头铣刀、环形铣刀、锥形铣刀和盘形铣刀。 在进行自由曲面(模具)加工时,由于球头刀具的端部切削速度为零,因此,为保证加工精度,切削行距一般采用顶端密距,故球头常用于曲面的精加工。而平头刀具在表面加工质量和切削效率方面都优于球头刀,因此,只要在保证不过切的前提下,无论是曲面的粗加工还是精加工,都应优先选择平头刀。另外,刀具的耐用度和精度与刀具价格关系极大,必须引起注意的是,在大多数情况下,选择好的刀具虽然增加了刀具成本,但由此带来的加工质量和加工效率的提高,则可以使整个加工成本大大降低。