自动送料装车系统PLC控制系统正文

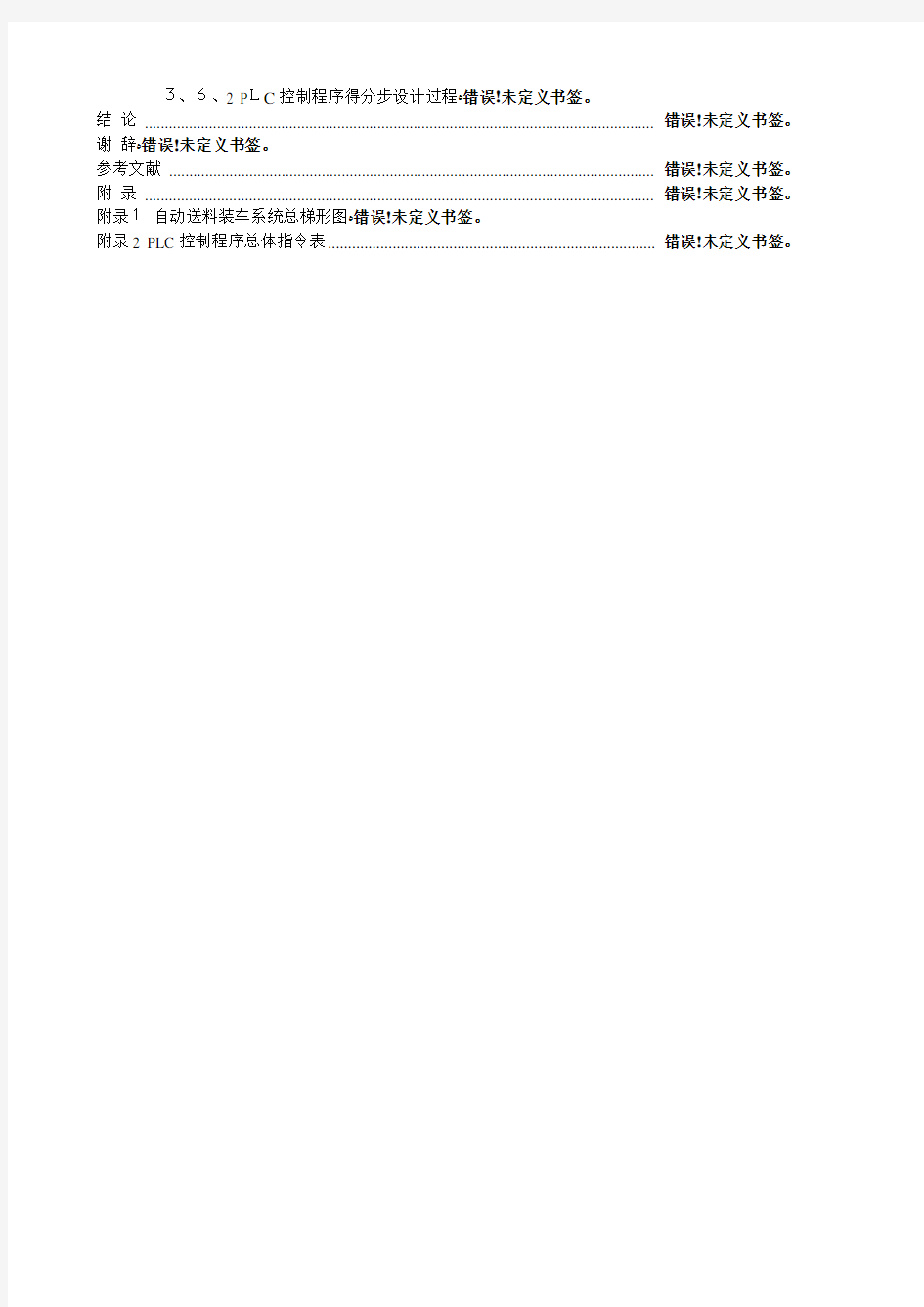
自动送料装车系统PLC控制系统设计
宜春学院物理科学与工程技术学院自动化专业王强
指导老师: 唐勇波
摘要 :利用可编程序控制器(PLC)适应性强、可靠性高、维护方便等特点,采用PLC实现送料装车系统,使物料能够自动传送与装车,减少劳动力,提高生产效率。本设计以系统得控制要求为出发点,进行了系统得硬件设计与软件设计(如梯形图与指令表等)。并且采用PLC编程软件GX Developer,对梯形图进行编写,仿真与调试,测试结果表明采用PLC控制器能够达到设计要求。
关键词:PLC;自动送料;硬件设计;软件设计
ABSTRACT: Programmablelogic controllerreferred to PLC, It is charact erized by high adaptability, high reliability,easy maintenance,etc、This design usesthePLC to realizefeed loading system control requirements、And it makes materials automaticallytransmitand loading, reduce the labor force,improve productionefficiency、This design is to control demand as thestarting p oint of the system, introducing the hardware designand software ofthe system, suc hasladderdiagramand instructionlist、Also this design uses PLC programmingsoftware GXDeveloper towriteladder diagram,simulate and debug、Thetest results show thatadoptingPLC canmeet thedesign requ irements
KEY WORDS:PLC; Automatic feed;Hardware Design; Software Design
目录
1、前言?错误!未定义书签。
1、1 系统设计得意义?错误!未定义书签。
1、2 PLC得应用现状及发展趋势?错误!未定义书签。
1、3 设计得主要内容?错误!未定义书签。
2、PLC控制系统得硬件设计..................................................................................... 错误!未定义书签。
2、1 系统得控制要求 (2)
2、2 系统得主电路图............................................................................................ 错误!未定义书签。
2、3 PLC机型得选择?错误!未定义书签。
2、4 PLC容量得估算?错误!未定义书签。
2、5 PLC输入、输出模块得选择?错误!未定义书签。
2、6 按钮、开关类电器得选择.......................................................................... 错误!未定义书签。
2、7 熔断器得选择.............................................................................................. 错误!未定义书签。
2、8继电器得选择.......................................................................................... 错误!未定义书签。
2、9接触器得选择?错误!未定义书签。
3、PLC控制系统得软件设计?错误!未定义书签。
3、1自动送料装车系统流程图?错误!未定义书签。
3、2 统计输入、输出点数与选择PLC得型号................................................. 错误!未定义书签。
3、3 PLC输入、输出端子得分配?错误!未定义书签。
3、4 PLC输入、输出端子接线图...................................................................... 错误!未定义书签。
3、5 三菱PLC编程软件GX Developer?错误!未定义书签。
3、5、1 GX Developer简介及功能?错误!未定义书签。
3、5、2使用GX Developer编写梯形图 ......................................... 错误!未定义书签。
3、6 PLC控制程序得设计?错误!未定义书签。
3、6、1软件设计方法?错误!未定义书签。
3、6、2 PLC控制程序得分步设计过程?错误!未定义书签。
结论 ............................................................................................................................... 错误!未定义书签。谢辞?错误!未定义书签。
参考文献 ......................................................................................................................... 错误!未定义书签。附录 ............................................................................................................................... 错误!未定义书签。附录1自动送料装车系统总梯形图?错误!未定义书签。
附录2 PLC控制程序总体指令表................................................................................. 错误!未定义书签。
1、前言
1、1 系统设计得意义
自动送料装车系统就就是基于PLC控制而设计得系统,该PLC控制系统实现了物料得自动传送与装车功能,代替了过去采用得人力运送物料。自动送料装车系统广泛应用于工厂物料传输得流水线设备中,可以传输煤粒、细砂等材料。该系统就就是由电动机、传送带、给料器、传送带、小车、开关、按钮等设备组成;它通过控制三台电动机控制物料传送皮带得移动使物料传送。而且由于PLC 体积小、维修方便、操作安全、编程简单、能适应工厂恶劣得工作环境,利用PLC控制送料传送系统将会大大降低劳动力,提高生产效率,为工厂带来更多得利润。
1、2 PLC得应用现状及发展趋势
可编程控制器(即PLC)就就是在19世纪60年代末在美国首先出现得,它用来取代传统得继电器控制系统,实现逻辑控制,顺序控制,定时,计数等功能。随着PLC技术得不断完善与成熟,PLC得处理速度有了大大提高,功能也日趋完善,具有通用性高、可靠性高、编程简单、抗干扰性强、适应性强、维修方便等特点。广泛应用于化工、电力、石油、采矿、冶金、机械等领域。
在可编程控制器产生之前,工业生产过程与机械得控制只要就就是通过继电器来实现。继电器一方面具有操作简单、实用、价格便宜,抗干扰性强得优点,另一方面具有可靠性不高、灵活性差,只具有逻辑、定时得特点。因此,在现代化工厂生产过程中,为了降低劳动成本,减轻工人得工作负担,提高生产效率,同时也为了保障工人得生命安全,要求工业生产过程实现自动化,这就需要PLC控制系统。
随着科学技术得不断发展到今天,PLC得CPU处理速度有了很大得提高,功能也在日趋完善,现在得PLC不仅能实现开关量控制,还能实现模拟量控制、位置控制、联网通信等。PLC未来得发展将在以下几个方面:
1、体积小、速度快、高性能、价格低廉;
2、大型化、多功能、网络化;
3、与其她智能控制系统相互渗透与结合。
使用PLC控制,具有以下优点:
1.编程简单,使用方便
PLC得编程语言指令少,采用简明得梯形图、逻辑图与指令表等编程语言,编程简单易学,而且当改变控制方案而不需改变硬件接线,只需修改用户程序,不必须改变硬件接线。
2、抗干扰性强,适应性强
PLC能够适应工业化生产现场,采取了隔离、屏蔽、联锁、滤波等安全措施,使之能抵抗外部干扰,
适应恶劣得生产环境。
3、可靠性高,维护方便
PLC使用软件代替继电器,仅需要少量得输入与输出硬件,可以因触点得接触不良产生故障大为减少,出现故障时只需将PLC得输入、输出模块拔掉,大大缩短了故障修复时间。
1、3设计得主要内容
实现小车得送料装车系统控制要求得方法有多种,比如采用继电器、单片机、可编程控制器等。
在上文已经讲述了采用继电器得特点,一方面具有操作简单、实用、价格便宜,抗干扰性强得优点,另一方面但由于可靠性不高、灵活性差,只具有逻辑、定时得特点,难以达到适应复杂与程序可变控制要求,无法适应激烈得市场竞争,因此在本设计中不采用继电器。
另外如果采用单片机控制小车自动送料与装车,需要加入A/D、D/A转换器,线路接线复杂,且编程显得复杂与困难;而且单片机控制电路容易受外界环境得干扰,适应性不高且不稳定。而由于本人得能力有限,因此也不采用单片机。此外PLC内部具有定时与计数功能,因此我采用PLC来实现小车得自动送料装车得控制。
本设计以系统得控制要求为出发点,介绍了系统得硬件设计与软件设计(如梯形图与指令表等)。并且采用PLC编程软件GX Developer,对梯形图进行编写,仿真与调试,最后得出结论。
要达到设计得控制要求,其过程分为两个部分:一就就是系统得硬件设计,二就就是系统得软件设计。系统得硬件设计内容包括PLC机型得选择、容量得选择、I/O模块得选择、输入与输出设备得选择等;系统得软件设计得内容有分配输入与输出得点数、画出系统流程图、设计梯形图与指令表程序。另外我采用三菱PLC编程软件GX Developer 对梯形图进行编写,经检查无误后再仿真与调试,最终得出结论。
预期得结果就就是:采用PLC编程软件进行系统得调试与仿真,通过控制输入触点得通与断,得出对应得输出。即实现了控制输入开关得通断控制三台电动机得启动与停止,来控制物料传送皮带得移动使物料传送。
2、 PLC控制系统得硬件设计
2、1系统得控制要求
初始状态,红灯L1灭,绿灯L2亮,小车可以开进装料,料斗K2关闭,电动机M1、M2、M3都关闭。当料不满时K1导通,K2关闭不出料。当小车开到称重开关S2处,S2接通,红灯L1亮,绿灯L2灭;按下启动按钮S3,电动机M3运行,电动机M2在M3启动后延迟2秒运行,电动机M1在M2转动后延迟2秒运行;K2在M1运行2秒后导通出料。当料满后,断开称重开关S2,料斗K2关闭;启动按钮S3关闭,电动机M1延时2秒关闭,电动机M2在M1关闭后延时2秒停止,电动机M3在M2关闭后延迟2秒停止,此时红灯L1灭,绿灯L2亮,小车可以开走。当系统发生故障时,黄灯L3亮,正常情况灭如图2-1所示:
图2-1自动送料装车系统
2、2 系统得主电路图
系统主电路原理图如图2-2所示:
图2-2自动送料装车系统主电路原理图
图中,电动机得正反转控制送料开关K1与料斗K2得打开与关闭;交流接触器KM1、KM2、KM3得作用就就是控制电动机M1、M2、M3得运行来控制物料传送皮带送料;FR1、FR2、FR3就就是热继电器,对三台电动机起短路保护与过载保护作用。
2、3 PLC机型得选择
PLC机型选择得原则就就是:在满足控制要求得条件下,应保证工作正常运行,维护方便,以获得最佳得性价比。在选用PLC应考虑以下几个问题:
(1)PLC得性能与控制要求相适应。对于开关量控制得系统,当它对于控制要求不高时,可以选择小型PLC(如MITSUB-ISHI公司FX2NX系列得FX2N—16MR、FX2N—32MR等)。
(2)PLC得机型系列应统一
(3)PLC得CPU处理速度应满足控制要求,具体方法有:选择CPU处理速度快得PLC;优化应用软件;采用高速响应模块;考虑就就是否在线编程。
2、4 PLC容量得估算
PLC容量得估算,包括两个方面:一就就是输入/输出点数估算,二就就是用户存储器得估算。
(1)输入/输出点得估算
通常输入点与输入信号,输出点与输出信号就就是一一对应得,特殊情况下会出现两个信号公用一个输入点。
(2)用户存储器得估算
在本设计中,输入信号有3个,输出信号有7个,则需要3个输入点与7个输出点,因此,可选择FX2N-16MR型PLC,它有8个输入点与8个输出点。
2、5 PLC输入、输出模块得选择
1、开关量输入模块得选择
开关量输入模块得作用就就是检测、转换来自现场设备(如按钮、行程开关、转换开关等)得高电平信号转为PLC内部电平信号。
输入接口电路按PLC输入模块与外部用户设备得接线,可分为汇点输入接线与独立接线。
本设计中选择三相交流输入电源AC380V,三个电动机采用汇点式输入接线方式共用一个电源。
2、开关量输出模块得选择
开关量输出模块得作用就就是将PLC内部低电平转换为外部所需电平得输出信号。
开关量输出模块有三种输出方式:继电器输出、晶体管输出、晶闸管输出。
2、6按钮、开关类电器得选择
在本设计系统中,采用组合开关,用于电源得引入。根据电动机得容量、电流得种类、电压得等级选择。
2、7熔断器得选择
熔断器得选择方法就就是:首先确定熔体得额定电流;再根据熔体得规格,选择熔断器得规格;最后根据被保护电流得性质,选择熔断器得类型。
1.熔体额定电流得选择
熔体额定电流得选择需要满足一定得条件:
(1)I FUN≥I(2-1)
其中I FUN————熔体得额定电流;
I——负载得额定电流。
(2)在本设计中,有三台电动机共用熔断器,则:
I FUN ≥I m/2、5(2-2)
式中:Im -------电路最大电流;
当三台电动机不同时启动时,系统得最大电流为:
Im = 7Iemax+ (2-3)
其中———其余电动机得额定电流之与;
I emax———最大容量得一台电动机得额定电流。
2、熔断器规格得选择
熔断器得额定电压要大于系统电路得工作电压,额定电流也要大于或等于熔体得额定电流。
3、熔断器类型得选择
熔断器必须要根据负载保护特性、短路电流大小与安装条件选择。
2、8继电器得选择
在本设计中选用具有带电保护功能得继电器,防止在运行中因电源断电而导致数据得丢失。
1、时间继电器
由于本设计中要延时2秒,并且从经济角度考虑,可选择空气阻尼式时间继电器,它得延时范围有0、4S--80S与0、4--180s两种,触点得额定电压为380V,额定电流为5A。
2、热继电器
热继电器得选择可按下列公式选择:
IFRN=(0、95~ 1、05)I ed (2-4)
其中:I FRN———热元件整定电流。
2、9 接触器得选择
本设计采用交流接触器。
接触器应参照其主要技术参数选择。它得主要技术参数有:级数、额定工作电压、额定工作电流、额定功率、线圈额定电压、允许操作频率、机械寿命等。
系统设计中主要考虑交流接触器主触头得额定电流与额定电压。
U KMN≥UCN (2-5)
IKMN ≥I N = P MNx 103/KU MN(2-6)
式中U KMN———接触器得额定电压;
U CN———接触器得额定线电压;
IKMN ———接触器得额定电流;
P MN ———电动机得功率;
UM N ———电动机得额定线功率;
K———经验系数,K取值1 ~ 1、4。
3、PLC控制系统得软件设计
3、1 自动送料装车系统流程图
自动送料装车系统流程图如图3-1所示:
图3-1 自动送料装车系统流程图
3、2统计输入、输出点数与选择PLC得型号
1、输入、输出点得统计
输入信号有三个开关按钮S1、S2、S3,需要有3个输入点。
输出信号有8个,3个输出线圈,3个指示灯输出与K1、K2,,总共要8个输出点。
2、PLC型号得选择
由于输入点有3个,输出点有8个,可选择FX2N-18MR型PLC,它有8个输入点,8个输出点,能够满足设计要求。字母R表示PLC为继电器输出。
3、3 PLC输入、输出端子得分配
PLC输入、输出端子得分配如表3-1所示:
三个热继电器得常闭触头不作为输入点,而就就是放到输出电路中,分别与三个输出线圈连接,同样能起到过载与短路保护作用。
检测开关S1X000进料开关K1Y000
料斗K2Y001
称重开关S2X001允许汽车开走L2Y002
允许汽车开进L1Y003
启动开关S3X002电动机M1Y004
电动机M2Y005
电动机M3Y006
故障报警信号灯L3Y007
3、4 PLC输入、输出端子接线图
PLC输入、输出端子接线图如图3-2所示:
图3-2PLC输入、输出端子接线图
3、5三菱PLC编程软件GXDeveloper
3.5.1GX Developer简介及功能
GX Developer就就是MELSOFT可编程控制器MELSOFT编程软件。它有两种型号: 一就就是SW8D5C-GPPW-E(英文版),二就就是SW7D5C-GPPW-C(中文版)。在本设计中使用SW7D5C-GPPW(中文版)可编程控制器编程软件。
GX Developer具有以下功能:
1)支持所有三菱PLC系列编程;
2)支持梯形图、指令表、ST、SFC、FB、Label编程;
3)网络参数得设定,进行程序得线上更改、监控与调试。
另外可以使用三菱PLC仿真软件GXSi mul ato r6-C对编程好得程序在电脑中进行虚拟运行。在安装GX Simulator6-C之前,必须先安装GX Developer,并且版本要互相兼容。当安装完它们之后,在桌面或者开始菜单中并没有仿真软件得图标。因为仿真软件被集成到编程软件GX Deve loper中了,这个仿真软件相当于编程软件得一个插件。
3.5.2使用GXDeveloper编写梯形图
具体方法如下:
1、当安装完GXDeveloper与选GX Simulator6-C之后,点选“开始”菜单栏,顺序点选“所有程序”→“MELSOFT应用程序”→“GX Developer”,双击图标打开GX Developer软件。
2、在菜单栏中单击“工程”→“创建新工程”,出现如图所示画面:
在“PLC系列”中选择“FXCPU”,在“PLC类型”中选择“FX2N(C)”,程序类型选择“梯形图”,设定工程名后,再按确定。
3、按确定之后,之后出现下图所示画面:
4、下面列举一个简单得程序,如下图所示:
写完PLC程序后,形成如下图画面:
5、在写完梯形图后,再进行程序转换,将编辑得程序梯形图变换为PLC可识别得内部语言指令。可按F4键或选择菜单“变换”再点“变换”。如下图所示:
6、选择主菜单栏中“工具”→“程序检查”,进行程序检查。出现下图画面:
程序检查(MAIN)”提示框内,检查内容默认为全部选择,检查对象默认为选择“当前得程序作为对象”,点选“执行”,如有出错,则于文本框内会显示出错得软元件名称、出错步数、出错原因说明。
7、用GX Simulator 6C对PLC程序仿真
1)点击菜单栏“工具”→“梯形图逻辑测试起动”,显示“LADDER LOGIC TEST TOOL”提示框,如下图所示:
2)仿真软件会自动运行,同时显示“PLC写入”提示框,软件启动完成,“LADDERLOGICTEST TOOL”提示框内变化“RUN”变色为黄色,“运行状态”栏选为“RUN”。如下图所示。
3)软件启动完成后,软件运行模式为“监视模式”,“监视状态”提示栏显示PLC处于“RUN”状态及程序单循环执行周期时间。
8、PLC程序软元件测试
1)单击主菜单栏中“在线”→“调试”→“软元件测试”,出现“软元件测试”提示框画面,如下图所示:
“位软元件”——指输入X\Y\M\C\S等位软元件,点击“强制ON”接通软元件触点或线圈,点击“强制O FF”断开软元件触点或线圈。
“字软元件”——指输入T/D等字软元件,在“设置值”框内输入设置值,点击“设置”则开始T/D继电器仿真运算。
“执行结果”——显示软元件仿真运行得结果。
2)不同类型得软元件触点得测试中仿真、复位、触点块颜色变化列表如表3-2所示:
表3-2仿真、复位、触点块颜色变化
触点类型仿真动作启动按键模拟状态仿真复位按键触点块颜色
白色→蓝色常开强制ON接通强制ON/OFF取
反
蓝色→白色常闭强制ON断开强制ON/OFF取
反
上升沿脉冲强制ON短促接通强制ON/O FF取反白→蓝→白
下降沿脉冲强制O FF短促接通强制ON/O FF取反白→蓝→白
3)点击“软元件测试”提示框内“关闭”,则退出PLC程序软元件测试模式。
4)点击主菜单栏“工具”→“梯形图逻辑测试旧结束”,则退出仿真测试。
5)退出仿真测试后,软件状态为“读出状态”,如果要继续编辑或修改,可点击“工具条”第3个按键,转为“写入模式。
3、6 PLC控制程序得设计
3.6.1软件设计方法
在软件设计中,常用得方法有经验法、解析法、图解法与计算机辅助设计。
(1)经验法,顾名思义就就就是运用自己或别人得经验设计。
(2)解析法,就就是指利用组合逻辑与时序逻辑得理论,并采用它们对应得解析方法进行逻辑求解,从而得到程序。
(3)图解法,常用得方法有:梯形图法、波形图法、状态转移图法。
(4)计算机辅助设计,就就是指利用应用软件在计算机上设计梯形图,然后传到PLC中。
在本设计中,我采用得软件设计方法就就是梯形图法与指令表,并且使用三菱PLC编程软件G XDeveloper编写梯形图。
3.6.2PLC控制程序得分步设计过程
1、小车到达S2处停止,此时红灯L1亮,绿灯L2灭。其梯形图如图3-3所示:
图3-3梯形图①
当小车到达S2处停止,小车被允许装料。当按下启动按钮S3(X002得电),Y003得电,红灯L1亮;Y003常闭触头断开,Y002断电,绿灯L2灭。
2、当S3接通后,电动机M3运行,延时2秒后M2运行。此时对应得梯形图如图3-4所示:
图3-4梯形图②
按下启动按钮S3(Y002得电),Y006得电(电动机M3运行),延时继电器T0得电,延时2S 后,Y005得电(电动机M2运行)。
3、电动机M2运行后延时2秒电动机M1运行,电动机M1运行后延时2秒料斗K2打开出料。此时对应得梯形图如图3-5所示:
图3-5梯形图③
当Y005(电动机M2)得电,延时继电器T1得电,延时2秒后,Y004(电动机M1)得电,延时继电器T2得电,延时2秒后,Y001得电,料斗K2打开出料。
4.小车被装满料后,称重开关S2断开,料斗K2关闭,电动机M1延时2秒关断。此时对应得梯形图如图3-6所示:
图3-6梯形图④
当称重开关S2断开(梯形图中点动X001),Y001断电,即料斗K2关闭,则Y001为常闭触点,则辅助继电器M3得电,延时继电器T3也得电,延时2S后Y004断电(电动机M1停止)。
5.电动机M2延时M1,2秒后停止;电动机M3延时M2,2S后停止,并且绿灯L2灯亮,红灯L1灯灭,此时表示汽车可以开走。此时对应得梯形图如图3-7所示:
图3-7梯形图⑤
电动机M1停止后(Y004断电),辅助继电器M4得电,延时继电器T4开始计时,2S后,Y005断电(电动机M2停止运行);辅助继电器M5得电,Y006断电,传送电动机M3停止运行。
X002断电(S3启动按钮断开),Y004断电即电动机M1停止,致使Y003断电(红灯L1灭);X002常闭触点、Y002常闭触点接通,Y002得电(绿灯L2亮)。
6、若在运行过程中出现故障,PLC系统将发出故障报警信号,故障报警信号灯L3亮。此时对应得梯形图如图3-8所示:
图3-8梯形图⑥
上图中X002为通电状态,并联连接得常开触点若有一个接通,则Y007得电。电动机M3、M2、M1,料斗K2,进料开关K1中任意一个出现故障Y007得电,就会导致故障灯L3亮。则应该对它们检查确保无误。
结论
在此次设计中,增强了自己研究设计方案得实践能力,使用编程软件设计程序方法得运用能力,锻炼我独立思考,动手实践得能力,同时进一步加深对知识得理解与理论知识与实践得结合。同时我也得出以下几个结论:
1、本设计基本实现了使用PLC控制自动自动送料装车系统设计得控制要求,最后经PLC编程软件得仿真与调试,通过对输入软元件触点强制ON/OFF,输出触点产生相应得颜色变化(白色表示O FF,蓝色表示ON),因此能够达到通过控制输入触点得通与断,得到相应得输出。
2、另外我得设计得一个亮点就就是在系统中增加了一个故障指示灯(即黄灯L3)。当系统某个部分发生故障时,系统则无法正常运行,若不增加一个故障检测部分则无法查出到底就就是那部分出现故障。因此在增加一个检测部分后,当系统出现故障,故障指示灯会亮,然后再查瞧故障检测部分得梯形图,在PLC处于调试状态模式下,输出触点颜色变蓝,某些输入触点会变成白色,则出现故障;在系统正常运行得情况下,输出触点为白色,输入触点全为蓝色,故障指示灯不亮。
3、本设计也存在一些不足之处,比如称重开关S2只起到了检测小车到来得情况,无法起到物料重量得称量得作用。
4、该系统可以改进得方向就就是在称重开关S2处增设两个七段数码管,用来显示每日装车得数量,可以采用脉冲计数得方法。
谢辞
本设计就就是在唐勇波老师得指导下完成得,唐勇波老师不仅就就是我得毕业设计导师,也就就是我班授课老师,她与我们之间亦师亦友,在大学四年中建立了非常深厚得友谊,我要衷心地感谢唐勇波老师。
我也要感谢物理科学与工程技术学院得所有老师们,就就是她们付出辛勤得汗水教会了我们专业得知识,也让我们明白做人得道理。我得导师在大学中不仅教授了许多知识,也在这次毕业设计中给我提供专业知识得指导,设计方面得修改意见,让我在设计中不断提高。我得PLC老师也教会了我们这门课程得知识。在此我要向所有得老师致于真诚得感谢与由衷得敬意。
我也要感谢在大学四年度过风风雨雨得同学们,感谢她们在大学四年对我默默得支持,感谢她们在学习与生活中得帮助,感谢她们在这次毕业设计中给予我得帮助,友谊万岁!
在本文结束之前,我再次向我得指导老师与物理科学与工程技术学院所有得老师与同学致于最崇高得敬意与深深得感谢!
参考文献
[1]熊幸明,陈艳,等、电气控制与PLC[M]、北京:机械工业出版社,2011、
[2]廖常初等、PLC基础及应用[M]、北京:机械工业出版社,2003、
[3] 曹辉等、可编程序控制器系统原理及应用[M] 、北京:电子工业出版社,2005、
[4] 陈建明、电气控制与PLC应用[M]、北京:电子工业出版社,2006、
[5]陈立定等、电气控制与可编程序控制器[M]、广州:华南理工大学出版社,2001、[6] 王永华、现代电气及可编程控制技术[M]、北京:北京航空航天大学出版社,2002、[7] 陈少华、机械设备电气控制[M]、广州:华南理工工业大学出版社,2001、
[8]方荣惠,上官璇峰、电机原理及拖动基础[M]、北京:中国矿业大学出版社,2001、[9] 王兆安,黄俊、电力电子技术[M]、西安:西安交通大学出版社,2005、
[10]何伯时、电力拖动自动控制系统[M]、北京:机械工业出版社,2000、
[11]刘建明、电气控制与PLC应用[M]、北京:电子工业出版社,2003、
附录
附录1自动送料装车系统总梯形图
LD X002 LDY004 OUTT3 LDI X002 ORY003 ANIX001 K20ANI Y002 ANI X001 OUT T2 LDY004 OUT Y002 OUTY003 K20OR M4 LD Y008 LDI Y003 LDT2 OUT M4 ORY005 OUT Y002 OR Y001 LD M4 OR Y004 LD X002 AND Y006OR Y005 OR Y000 OR Y008AND Y005 ANI T4ANDX002ANI X001 AND Y00OUTY005 OUTY007
注:指令表阅读顺序为,从上至下,从左至右。
自动装箱生产线系统的设计
自动装箱生产线系统的设计 摘要 在现代化的工业生产中常常需要对产品进行计数和包装,如果这些繁杂的工作由人工完成的话不但效率低,而且劳动强度大,不适合现代化的生产需要。本文主要对基于生产线自动装箱的PLC控制系统进行了详细的研究。该系统有两个传送带,即包装箱传送带和产品传送带。包装箱传送带用来传送产品包装箱,其功能是把已经装满的包装箱运走,并用一只空箱来代替。为使空箱恰好对准产品传送带的末端,使产品刚好落入包装箱中,在包装箱传送带的中间装一光电传感器,用以检测包装箱是否到位。产品传送带将产品从生产车间传送到包装箱,当某一产品被送到传送带的末端,会自动落入包装箱内,并由另一传感器转换成计数脉冲。本控制系统具有精度高、成本低、抗干扰能力强、故障率低、操作维护简单等特点,具有良好的应用价值。 关键词:自动生产系统设计
目录 前言 第1章系统概述 1.1生产线自动化的发展概况 (1) 1.2 国内生产线自动化发展概况 (2) 1.3国外生产线自动化发展概况 (4) 第2章基本知识介绍 1.1 安全保护电路 (5) 2.1 熔断器的选择 (5) 2.2 电源开关的选择 (7) 2.3交流接触器 (9) 2.4热继电器 (10) 2.5时间继电器 (11) 2.6电动机 (12) 2.7行程开关 (14) 2.8 PLC的结构 (16) 2.9 PLC的工作原理 (18) 第2章系统分析 2.1本文主要研究内容 (20)
2.2主要解决的问题 (21) 第3章控制系统的设计 3.1继电接触器主电路 (22) 3.2继电接触器控制电路 (23) 3.3自动装箱生产线的工作原理: (24) 3.4 I/O 分配端 (25) 3.5 接线图 (26) 3.6梯形图 (27) 3.7 指令图 (29) 3.8 流程图 (30) 第4章 结论 (31) 致谢 (33) 参考文献 (34) 前言 在现代化的工业生产中常常需要对产品进行计数,包装,如果这些繁杂的工作
自动送料装车系统 LC控制设计
一、控制要求 1.1 控制对象介绍 自动送料装车系统是用于物料输送的流水线设备,主要是用于煤粉、细砂等材料的运输。 自动送料装车系统一般是由给料器、传送带、小车等单体设备组合来完成特定的过程。这类系统的控制需要动作稳定,具备连续可靠工作的能力。通过三台电机和三个传送带、料斗、小车等的配合,才能稳定、有效率地进行自动送料装车过程。如下图所示: 1.2 控制原理 自动送料装车系统是通过电机和限位开关来控制的。称重开关S2控制汽车开来或开走。三台电机控制三个传送带。进料开关K1控制控制进料与否。检测开关S1控制料斗中物料的空满。 另外,在S2处增设两个七段数码管,用来统计每日的装车数。装车数的统计采用脉冲计数的方法进行。脉冲计数方法是当装料车装满时S2断开后,开始定时放送脉冲;当S2闭合时停止发送脉冲。一个脉冲的宽度即为一辆汽车。用两个数码管计数,所计的数即为装车数。 当S2接通时,红灯L1亮,绿灯L2灭,传送电动机M3运行,传送电动机M2延迟M3电动机2S运行,送料电动机M1延迟M2电动机2S运行,料斗K2延迟M2电动机2S打开出料。当料满后(S2断开后),料斗K2关闭,电动机M1延时2S后关断,M2在M1停后2S后停止,M3在M2停止后2S后停止,L2灯亮,L1灯灭,此时汽车可以开走。 1.3 自动送料装车系统的启停过程示意图 该图中从上到下是启动顺序,从下到上是停止顺序。 1.4 控制要求 初始状态:红灯L1灭,绿灯L2亮,表示允许汽车开进装料,料斗K2,电动机M1,M2,M3皆为OFF。当汽车到来时(S2接通表示),L1亮,L2灭,M3运行,电动机M2在M3通2S后运行,M1在M2通2S后运行,K2在M1通2S后打开出料。当物料满后(用S2断开表示),料斗K2关闭,电动机M1延时2S后关断,
plc加热炉自动送料控制系统设计说明书
课程设计任务书 1.设计题目:加热炉自动送料控制系统设计 2. 设计内容: 1)完成《课程设计指导书》所要求的控制循环。 2)按停止按钮,立即停止。 3)要求可以实现回原点、单周期、连续控制。 3.设计要求 1)画出端子分配图和顺序功能图 2)设计并调试PLC控制梯形图 3)设计说明书 4.进度安排 1)理解题目要求,查阅资料,确定设计方案 2天2)PLC顺序功能图与梯形图设计 5天3)说明书撰写 2天4)答辩 1天 指导教师:
主管院长:年月日 目录 前言 (2) 摘要 (3) 第一部分 PLC概述 (4) PLC设计任务书及基本要求 (5) PLC选型 (7) 第二部分 I/O端口分配表 (8) 加热炉自动控制送料系统设计思想 (9) 程序流程图 (10) 梯形图 (11) 语句指令表 (18) 总结 (21) 附注:参考文献
前言 加热炉自动控制(automatic control of reheating furnace)对加热炉的出口温度、燃烧过程、联锁保护等进行的自动控制。早期加热炉的自动控制仅限控制出口温度,方法是调节燃料进口的流量。现代化大型加热炉自动控制的目标是进一步提高加热炉燃烧效率,减少热量损失。为了保证安全生产,在生产线中增加了安全联锁保护系统。 自动化学科有着光荣的历史和重要的地位,20世纪50年代我国政府就十分重视自动化学科的发展和自动化专业人才的培养。现在,世界上有很多非常活跃的领域都离不开自动化技术,比如机器人、月球车等。另外,自动化学科对一些交叉学科的发展同样起到了积极的促进作用,例如网络控制、量子控制、流媒体控制、生物信息学、系统生物学等学科就是在系统论、控制论、信息论的影响下得到不断的发展。在整个世界已经进入信息时代的背景下,中国要完成工业化的任务还很重,或者说我们正处在后工业化的阶段。 工业加热炉的炉温应当按照生产工艺要求维持在一定的数值。但是炉的热负荷经常在变化(例如常常要打开炉门取出已加热的工件和送入冷的工件),在这种条件下要靠自动控制技术准确控制炉温,保持炉温的误差很小。而靠人力调整则难以做到,从而会造成能源的浪费甚至影响产品质量。 人们每年都把许多重量达到吨级的人造地球卫星准确送入位于数百千米乃至数万千米高空的预先计算好的轨道,并一直保持其姿态正确,也就是使它的太阳能电池帆板保持指向太阳,使它的无线电天线保持指向地球。这只有依靠先进的自动控制技术才能做到。 然而在国际形势日益复杂、科学技术日益进步的今天,人造地球卫星和宇宙飞船已经不能完全满足需要,近年来出现的“空天飞行器”要求既能在大气层外飞行,又能在返回大气层以后转为像飞机那样自主地高速航行,而不像人造卫星或宇宙飞船那样在返回大气层以后只能被动地降落地面。研制这种“空天飞行器”必须解决的技术难题之一就是智能自主控制技术。
自动送料装车系统plc控制设计
自动送料装车系统p l c 控制设计 文件排版存档编号:[UYTR-OUPT28-KBNTL98-UYNN208]
一、控制要求 1.1 控制对象介绍 自动送料装车系统是用于物料输送的流水线设备,主要是用于煤粉、细砂等材料的运输。 自动送料装车系统一般是由给料器、传送带、小车等单体设备组合来完成特定的过程。这类系统的控制需要动作稳定,具备连续可靠工作的能力。通过三台电机和三个传送带、料斗、小车等的配合,才能稳定、有效率地进行自动送料装车过程。如下图所示: 1.2 控制原理 自动送料装车系统是通过电机和限位开关来控制的。称重开关S2控制汽车开来或开走。三台电机控制三个传送带。进料开关K1控制控制进料与否。检测开关S1控制料斗中物料的空满。 另外,在S2处增设两个七段数码管,用来统计每日的装车数。装车数的统计采用脉冲计数的方法进行。脉冲计数方法是当装料车装满时S2断开后,开始定时放送脉冲;当S2闭合时停止发送脉冲。一个脉冲的宽度即为一辆汽车。用两个数码管计数,所计的数即为装车数。 当S2接通时,红灯L1亮,绿灯L2灭,传送电动机M3运行,传送电动机M2延迟M3电动机2S运行,送料电动机M1延迟M2电动机2S运行,料斗K2延迟M2电动机2S打开出料。当料满后(S2断开后),料斗K2关闭,电动机M1延时2S
后关断,M2在M1停后2S后停止,M3在M2停止后2S后停止,L2灯亮,L1灯灭,此时汽车可以开走。 1.3 自动送料装车系统的启停过程示意图 该图中从上到下是启动顺序,从下到上是停止顺序。 1.4 控制要求 初始状态:红灯L1灭,绿灯L2亮,表示允许汽车开进装料,料斗K2,电动机M1,M2,M3皆为OFF。当汽车到来时(S2接通表示),L1亮,L2灭,M3运行,电动机M2在M3通2S后运行,M1在M2通2S后运行,K2在M1通2S后打开出料。当物料满后(用S2断开表示),料斗K2关闭,电动机M1延时2S后关断,M2在M1停2S后停止,M3在M2停2S后停止,L2亮,L1灭,表示汽车可以开走。 设计要求:当料不满(S1为OFF,灯灭),料斗开关K2关闭(OFF),灯灭,不出料,进料开关K1打开(K1为ON)进料,否则不进料。当汽车到来时M3运行,电机M2在M3运行2S后运行,M1在M2运行2S后运行,K2在M1运行2S后打开出料,当料满后(用S2断开表示),电动机M1延迟2S后关断,M2在M1停2S 后停止,M3在M2停2S后停止,而且具有每日装车数的统计功能。 三.系统分配 I/O地址表 PLC外部接线图
自动送料控制系统PLC控制程序设计
毕业设计(论文)任务书
毕业设计(论文)申报表
西南科技大学高等教育自学考试 毕业设计(论文)进度检查及成绩评定表
摘要 可编程序控制器简称PLC,由于PLC的可靠性高、环境适应性强、灵活通用、使用方便、维护简单,所以PLC的应用领域在迅速扩大。对早期的PLC,凡是有继电器的地方,都可采用。而对当今的PLC几乎可以说凡是需要控制系统存在的地方就需要PLC。尤其是近几年来,PLC的成本下降,功能又不段增强,所以,目前PLC在国内外已被广泛应用于各个行业。 本设计是为了实现送料手动和自动化的转化,改变以往单纯手动送料,减少了劳动力,提高了生产效率,实现了自动化生产。而且自动送料的设计是由于工作环境恶劣,人很难进入工作环境的情况下孕育而成的。本文从第一章前言开始,第二章简单的介绍了西门子S7-200PLC,第三章介绍了自动控制系统的控制要求,第四章介绍了为什么要选择用PLC来做自动控制系统,第五章介绍了自动系统的具体设计,包括PLC 的I/O地址分配、流程图、梯形图、程序图、端子接线图,第六章通过程序调试最后得出结论。 关键词:西门子S7-200PLC、自动控制送料、自动化、程序设计
目录 1 前言 (4) 2 西门子S7-200 PLC简介 (5) 2.1 S7-200PLC的系统组成 (5) 2.2 S7-200PLC的性能特点 (6) 2.3 S7-200PLC的编程语言 (7) 3 控制系统介绍和控制要求 (8) 3.1 自动控制送料系统的内容 (8) 3.2 自动控制送料系统在生产中的地位 (9) 4 自动送料系统方案的选择 (9) 4.1 可编程控制器PLC的优点 (9) 4.2 小车送料系统方案的选择 (10) 5 自动送料系统程序设计 (11) 5.1 送料小车PLC 的I/O地址分配 (11) 5.2 PLC流程图 (12) 5.3 PLC梯形图设计 (13) 5.4 PLC程序图 (15) 5.5 PLC端子接线图 (17) 6 系统程序调试及结论 (18) 6.1调试自动控制送料系统程序 (18) 6.2此次设计的心得体会 (19)
自动装箱气动控制系统设计(正式版)
文件编号:TP-AR-L2924 In Terms Of Organization Management, It Is Necessary To Form A Certain Guiding And Planning Executable Plan, So As To Help Decision-Makers To Carry Out Better Production And Management From Multiple Perspectives. (示范文本) 编订:_______________ 审核:_______________ 单位:_______________ 自动装箱气动控制系统 设计(正式版)
自动装箱气动控制系统设计(正式版) 使用注意:该安全管理资料可用在组织/机构/单位管理上,形成一定的具有指导性,规划性的可执行计划,从而实现多角度地帮助决策人员进行更好的生产与管理。材料内容可根据实际情况作相应修改,请在使用时认真阅读。 目前,实现自动化生产是各个工业部门提高效率、增加产能的重要手段之一。在自动化生产流水线上,包装环节是不可或缺的一个部分。实现自动装箱的方法有多种,而其中气动控制系统的应用十分广泛。气动控制系统具有装置结构简单、轻便,安装维护方便,压力等级低,使用安全,环保无污染,响应速度快,防火、防爆、防潮,且气源制造简单,成本低等优点,适合工业中复杂的工作环境。此外,针对自动装箱系统需要产品在箱内整齐划一的特点,气动控制系统通过多个行程开关及气缸的组合设计,使得在自动装箱过程中,不但能够提高装箱效率,而且还
能够高品质地完成产品的整齐装箱。 自动装箱气动控制系统的组成 装箱系统的全部动作由托箱气缸、托产品气缸、装箱气缸和推箱气缸完成。四个气缸都是普通双作用气缸,驱动气缸动作的是四个二位五通的双电控换向阀,气缸动作的位置和距离由多个行程开关来决定。 2.1.产品托放过程 在自动装箱系统工作时,首先运送纸箱的传送带启动,当第一个纸箱到位后,触动行程开关1,纸箱传送带停止运行,同时产品传送带开始运行。当产品排列在托物板上,每排满规定的个数,就碰到行程开关2,此时产品传送带停止运行,电磁铁3YA通电,托产品气缸B将托物板托起,使产品通过搁物板后搁在搁物板上(搁物板采用的是只能上翻,不能下翻的设计)。这时行程开关2松开,产品传送带继续运送
自动送料装车控制系统设计
自动送料装车控制系统设计 1.设计任务 (1)硬件设计自动送料装车系统控制电路 设计煤矿或沙场自动送料装车系统。完成工作流程图;主电路图;控制器接线图;元件选型;电机选择,有必要的设计计算。(给简易控制系统示意图。) (2)软件设计自动送料装车系统控制程序 控制要求:能够控制启动/停止;装车完毕闪烁提示,汽车开走,进行下一轮的装载工作等。 (3)机械设计自动送料输送带机械结构。 2.要求 (1)绘制硬件接线框图;控制流程框图及其它原理图。 (2)撰写设计说明书,并附程序清单及其功能注释。 (3)调试控制程序。 二、进度安排及完成时间 1.设计时间三周(从2012年12月3日至2012年12月21 日) 2.进度安排 第1周:布置设计任务;补充相关知识;查阅资料;撰写绪论,确定系统组成方案。 第2周:输送带传动装置结构设计;绘制装配图、零件图。 控制系统硬件设计,选择电气元件,设计系统框图、外部电路接线图。 第3周:编写主程序、功能子程序并调试。并记录存在的问题和解决问题的方法;整理设计资料;按格式模版撰写设计说明书;上交设计作业(打印稿及电子文档);并参加答辩。注:程序设计2人;硬件电路设计2人;机械结构设计2~3人。
目录 第1章绪论 (1) 1.1自动送料装车控制的发展 (1) 1.2自动送料装车控制系统设计的目的和意义 (1) 第2章确定课题设计方案 (3) 2.1 初定动力部分 (3) 2.2 初定传动部分 (3) 2.3 初定执行机构 (3) 2.4 控制器选型 (4) 2.5 系统总体工作流程 (5) 第3章机械结构设计 (6) 3.1系统设计的原始参数 (6) 3.2初选输送带 (6) 3.2带速和滚筒转速计算 (7) 3.3牵引力和电动机功率计算 (7) 3.4电机的选型和传动比的确定 (7) 3.4.1电机的选型 (7) 3.4.2传动比的确定 (7) 3.5传动装置的布置方式 (8) 3.6 传动滚筒的作用及类型 (8) 第4章硬件部分设计 (10) 4.1 主电路的设计 (10) 4.2 PLC机型的选择 (11) 4.4开关的选择 (11) 4.5熔断器的选择 (12) 4.6 接触器的选择(KM) (14) 4.7 传感器的选择 (14) 4.7.1称重传感器的选择 (14) 4.7.2霍尔传感器的选择 (14) 4.8 继电器的选择 (15) 4.9 行程开关的选择 (15)
自动装箱气动控制系统设计
编订:__________________ 审核:__________________ 单位:__________________ 自动装箱气动控制系统设 计 Deploy The Objectives, Requirements And Methods To Make The Personnel In The Organization Operate According To The Established Standards And Reach The Expected Level. Word格式 / 完整 / 可编辑
文件编号:KG-AO-9452-51 自动装箱气动控制系统设计 使用备注:本文档可用在日常工作场景,通过对目的、要求、方式、方法、进度等进行具体的部署,从而使得组织内人员按照既定标准、规范的要求进行操作,使日常工作或活动达到预期的水平。下载后就可自由编辑。 目前,实现自动化生产是各个工业部门提高效率、增加产能的重要手段之一。在自动化生产流水线上,包装环节是不可或缺的一个部分。实现自动装箱的方法有多种,而其中气动控制系统的应用十分广泛。气动控制系统具有装置结构简单、轻便,安装维护方便,压力等级低,使用安全,环保无污染,响应速度快,防火、防爆、防潮,且气源制造简单,成本低等优点,适合工业中复杂的工作环境。此外,针对自动装箱系统需要产品在箱内整齐划一的特点,气动控制系统通过多个行程开关及气缸的组合设计,使得在自动装箱过程中,不但能够提高装箱效率,而且还能够高品质地完成产品的整齐装箱。 自动装箱气动控制系统的组成 装箱系统的全部动作由托箱气缸、托产品气缸、
自动,送料装车系统.
自动送料装车系统控制设计 摘要送料装车控制系统在冶金、采矿运输、和生产制造等许多领域中都得到了普遍的应用,它通过自动输送设备实现物料的传输、接收、装运、处理、装配和存储的自动化,把工厂的各个生产部门、各个储存点联系起来。送料装车控制系统的工作环境通常比较恶劣,设备所处环境一般粉尘较大、操作分散,所以对送料装车控制系统工作的安全性、可靠性、维护简便性要求比较高。用可编程控制器(PLC)控制的自动送料装车动作稳定,具备连续可靠的工作的能力。本文以日本三菱FX2N系列PLC为主控制器控制运料小车的自动往返顺序的控制,实现了送料车的装料、送料、卸料的功能。次系统主要是由基本设备、运料存储装置和控制系统三大部分组成,重点研究自动化生产线的控制。 关键词自动送料装车,PLC,控制系统 ABSTRACT Key Words:
1绪论 1.1自动送料装车控制的发展 送料装车设备广泛地应用于建材、冶金、煤炭、电力、化工、轻工等工业生产部门。老式送料装车设备因为没有计量而存在多装、少装的问题。特别是在运输的过程中,不允许车辆超载,多装了,得卸掉,少装了,得进行二次装车,使得装车工作进行非常缓慢。 随着当今社会科学技术的发展,各类物料输送的生产线对自动化程度的要求越来越高,原有的生产送装料设备已经远远的不能满足当前高度自动化的需要。由于控制系统的不断发展和革新,使得生产线的运输控制也将得到不断的改善和生产效率的不断提高,送料装车的控制经历了以下几个阶段: 1.手动控制:在20世纪60年代末70年代初期,便有一些工业生产采用PLC来实现送料装车的控制,但是限于当时的技术还不够成熟,只能采用手动的控制方式来控制机器设备,而且早期送料装车控制系统多为继电器和接触器所组成的复杂控制系统,这种系统存在设计周期长、体积大、成本高等缺陷,几乎无数据处理和通信功能,必须要有专人负责操作。 2.自动控制:在20世纪80年代,由于计算机的价格普遍下降,这时的大型工控企业将PLC充分的与计算机相结合,通过机器人技术,自动化设备终于实现了PLC在送料装车控制系统中自动控制方面的应用。 3.全自动控制:现阶段,由于PLC技术向高性能、高速度、大
自动装箱气动控制系统设计通用版
安全管理编号:YTO-FS-PD704 自动装箱气动控制系统设计通用版 In The Production, The Safety And Health Of Workers, The Production And Labor Process And The Various Measures T aken And All Activities Engaged In The Management, So That The Normal Production Activities. 标准/ 权威/ 规范/ 实用 Authoritative And Practical Standards
自动装箱气动控制系统设计通用版 使用提示:本安全管理文件可用于在生产中,对保障劳动者的安全健康和生产、劳动过程的正常进行而采取的各种措施和从事的一切活动实施管理,包含对生产、财物、环境的保护,最终使生产活动正常进行。文件下载后可定制修改,请根据实际需要进行调整和使用。 目前,实现自动化生产是各个工业部门提高效率、增加产能的重要手段之一。在自动化生产流水线上,包装环节是不可或缺的一个部分。实现自动装箱的方法有多种,而其中气动控制系统的应用十分广泛。气动控制系统具有装置结构简单、轻便,安装维护方便,压力等级低,使用安全,环保无污染,响应速度快,防火、防爆、防潮,且气源制造简单,成本低等优点,适合工业中复杂的工作环境。此外,针对自动装箱系统需要产品在箱内整齐划一的特点,气动控制系统通过多个行程开关及气缸的组合设计,使得在自动装箱过程中,不但能够提高装箱效率,而且还能够高品质地完成产品的整齐装箱。 自动装箱气动控制系统的组成 装箱系统的全部动作由托箱气缸、托产品气缸、装箱气缸和推箱气缸完成。四个气缸都是普通双作用气缸,驱动气缸动作的是四个二位五通的双电控换向阀,气缸动作的位置和距离由多个行程开关来决定。 2.1.产品托放过程
计算机控制送料装置的控制系统
1.设计说明 1.1设计的原始资料及依据 设计一个送料装置的控制电路,要求用计算机对其控制和监视。 1.2设计主要内容及要求 (1)当料斗内有料发出信号,电动机拖动料斗前进,到达下料台,电动机自动停止,进行卸料; (2)当卸料完毕发出信号,电动机反转拖动料斗退回,到达上料台电动机又自动停止、装料,周而复始工作; (3)无料状态下,电动机能实现点动,进行正、反试车工作。 (4)有短路、过载保护; (5)用计算机组态对系统进行监控。
2.概述 2.1 基于PLC控制的自动送料装车系统简介 自动送料装车系统是用于物料输送的流水线设备,主要是用于煤粉、细砂等材料的运输。自动送料装车系统一般是由给料器、传送带、小车等单体设备组合来完成特定的过程。这类系统的控制需要动作稳定,具备连续可靠工作的能力。通过三台电机和三个传送带、料斗、小车等的配合,才能稳定、有效率地进行自动送料装车过程。本次自动送料装车系统采用了PLC控制。从送料小车运行的工艺流程来看,其控制系统属于自动运行的控制系统,因此,此送料小车的电气控制系统设计采用自动扫描循环工作方式。而在程序设计上采用整体式设计方法,这样就可以使读者一目了然地看懂整个程序,从而在一定程度上省去了使用人员阅读并分析程序的大量宝贵时间,同时也使得程序的设计、修改和故障查找工作大为简化。 自动送料装车系统控制系统的软件部分(信号显示和故障显示)均采用经验设计法,而自动程序则采用顺序控制法设计。 为了使整个控制过程更加完善,本设计采用北京亚控公司的组态王 6.5仿真软件对整个系统进行组态模拟仿真,以进一步充分检验并修改系统硬件与软件。下面我们先介绍一下PLC及组态各自的特点。 2.2 PLC的特点 1. 可靠性高,抗干扰能力强 高可靠性是电气控制设备的关键性能。PLC由于采用现代大规模集成电路技术,采用严格的生产工艺制造,内部电路采取了先进的抗干扰技术,具有很高的可靠性。例如三菱公司生产的F系列PLC平均无故障时间高达30万小时。一些使用冗余CPU的PLC的平均无故障工作时间则更长。从PLC的机外电路来说,使用PLC构成控制系统,和同等规模的继电接触器系统相比,电气接线及开关接点已减少到数百甚至数千分之一,故障也就大大降低。此外,PLC带有硬件故障自我检测功能,出现故障时可及时发出警报信息。在应用软件中,应用者还可以编入外围器件的故障自诊断程序,使系统中除PLC 以外的电路及设备也获得故障自诊断保护。这样,整个系统具有极高的可靠性也就不奇怪了。 2. 配套齐全,功能完善,适用性强
自动装箱系统设计
摘要: 在工业生产中,常常需要对产品进行计数、装箱。如果用人工操作不但麻烦,而且效率低、劳动强度大。随着微机控制的普及,特别是单片机的应用,给该系统的设计带来了极大的方便。 本论文设计了一种以8051单片机为核心的流水线产品计数及装箱控制系统,可以对工业自动化生产流水线上的产品进行精确的计数和装箱。为了读键盘给定值及检测和控制,专门扩展一个8255A可编程接口及程序存储器EPROM2732(4K*8 200ns可用紫外线擦除标准EPROM)。扩展的8255A的B口用于给定值或产品计数显示。 关键词:装箱;自动控制;单片机 正文: 1、自动装箱控制系统设计方案 1.1 控制方案列举分析 自动装箱的关键在于依据装箱过程,设计出一个能够得以实现自动控制的结构方案。显然,自动装置的选择取决于这一过程的需求及特性。依据定义,一个自动装置即能通过自动控制或遥控方法完成任务的一台机器或一个机构。它可以是简单的,例如,从一个位置移向另一位置的一种单轴结构的气动压力联动装置,也可以是复杂的,例如,具有六轴结构的能动外科手术的机器人。而包装过程的各个项目选择以及各类工业自动化机构,可以在一个具体工作场所的空间围,使每一个设计方案完成一项任务。 由系统功能要求、方案选择和设备配置,可以设计出一个自动装箱系统,其
图1.1 产品自动装箱系统原理图 在图1.1中,该系统带有两个传送带,即包装箱传送带和产品传送带。包装箱传送带用来传送产品包装箱,其功能是把已经装满的包装箱运走,并用一只空箱来代替。为使空箱恰好对准产品传送带的末端,以便使产品刚好落入箱中,在空包装箱传送带的中间装一检测控制器1,用以检测包装箱是否到位。产品传送带将产品从车间传送到包装箱。当某一产品被送到传送带的末端,会自动落入包装箱,并由检测器2转换成计数脉冲。 产品计数可以由硬件完成(如MCS-51系列单片机中的定时器/计数器),也可以用软件来完成。本系统采用软件计数方法。 系统工作步骤如下: (1)用键盘设置每个包装箱所装的产品数量以及包装箱数,并分别存放在PARTS和BOXES单元中。 (2)接通电源,使传送带1的驱动电机转动。由控制程序控制传送带1的驱动电机持续运动,当包装箱运行到检测器1的光源和传感器的中间时,通过检测光电传感器的状态,判断传送带1上的包装箱是否到位。 (3)当包装箱到位时,关断电机电源,使传送带1停止运动。 (4)启动传送带2电机,使产品沿传送带向前运动,并转入箱。 (5)当产品一个一个落下时,通过检测器2的检测,将产生一系列脉冲信号。 (6)从检测器2来的输出脉冲,由计算机进行计数,并不断地与存在PRESET 单元中的给定值进行比较。 (7)当产品数与给定值不等时,将继续控制传送带2运动,以便继续装入产品,直到零件数与给定值相等,停止传送带2电机,不再转入产品。 (8)再次启动传送带1的电机,使装满产品的箱子继续向前运动,并把存放箱子数的存单元加1,然后再与给定的箱子数进行比较。如果不够,则带动下一个空箱到达指定位置,继续上述过程。直到产品数与给定值相等,停止包装,等待下面操作命令。 当传送带2上的产品和传送带1上的箱子足够多时,这个过程可以继续不断进行下去,这就是产品自动包装生产线的流程。 必要时操作人员可以随时通过停止(STOP)键停止传送带运动,并通过键盘重新设置给定值,然后再起动。
自动送料装车系统PLC控制设计
P L C课程设计 自 动 送 料 装 车 系 统 学院:机械工程学院 班级:机电1311
目录 第一章 PLC控制系统原理设计和分析 (3) 1.1设计要求 (3) 1.2控制原理 (4) 1.3元素定义 (4) 第二章.PLC控制系统原理结构分析 (5) 2.1结构框图 (5) 2.12自动送料装车控制系统的操作面板 (5) 第三章:PLC 控制系统 (6) 3 PLC的选型 (6) 第四章:PLC控制系统 (7) 4.1初始状态 (7) 4.2装车系统 (8) 4.3停机控制系统 (10) 4.4 程序时序图 (10) 4.5 I/O地址分配表 (11) 4.6 I/O接线图 (11) 4.7 程序设计梯形图 (12) 4.8 程序说明 (15) 第五章系统调试 (16) 遇到的问题及解决 (16) 参考文献 (18)
第一章 PLC控制系统原理设计和分析 1.1设计要求 1.初始状态 红灯L1灭,绿灯L2亮,表示允许汽车开进装料,进料阀指示灯K1、料斗指示灯K2不亮,电机M1,M2,M3皆为停止。 2.启动操作 按下启动按钮,开始下列操作: 系统自动检测料斗是否已满(传感器S1亮表示满),如果料斗未满,则打开K1进料,当料斗满时(传感器S1亮),K1停止,然后红灯L1亮,绿灯L2灭,表示正在装车。同时电机M3启动,M3启动2S后M2启动,M2启动2S后M1启动,M1启动2S之后K2打开(出料)。当车装满时(传感器S2亮),首先K2关闭,M1,M2,M3顺序延时2S分别停止。等到车离开(传感器S2灭)时,继续循环上述的运行。 3.停止操作 按下停止按钮系统恢复初始状态。
自动送料装车系统PLC控制设计
自动送料装车系统P L C 控制设计 Revised as of 23 November 2020
P L C课程设计 自 动 送 料 装 车 系 统 学院:机械工程学院 班级:机电1311
目录 第一章 PLC控制系统原理设计和分析 (3) 设计要求 (3) 控制原理 (4) 元素定义 (4) 第二章.PLC控制系统原理结构分析 (5) 结构框图 (5) 自动送料装车控制系统的操作面板 (5) 第三章:PLC 控制系统 (6) 3 PLC的选型 (6) 第四章:PLC控制系统 (7) 初始状态 (7) 装车系统 (8) 停机控制系统 (10) 程序时序图 (10) I/O地址分配表 (11) I/O接线图 (11) 程序设计梯形图 (12)
程序说明 (15) 第五章系统调试 (16) 遇到的问题及解决 (16) 参考文献 (18) 第一章 PLC控制系统原理设计和分析 设计要求 1.初始状态 红灯L1灭,绿灯L2亮,表示允许汽车开进装料,进料阀指示灯K1、料斗指示灯K2不亮,电机M1,M2,M3皆为停止。 2.启动操作 按下启动按钮,开始下列操作: 系统自动检测料斗是否已满(传感器S1亮表示满),如果料斗未满,则打开K1进料,当料斗满时(传感器S1亮),K1停止,然后红灯L1亮,绿灯L2灭,表示正在装车。同时电机M3启动,M3启动2S后M2启动,M2启动2S后M1启动,M1启动2S 之后K2打开(出料)。当车装满时(传感器S2亮),首先K2关闭,M1,M2,M3顺序延时2S分别停止。等到车离开(传感器S2灭)时,继续循环上述的运行。
生产线自动装箱的PLC控制课程设计
机械系统传动与控制课程设计说明书 设计题目: 班级: 姓名: 学号: 指导教师: 提交日期:
目录 1 课程设计的内容及目的 2 总体方案设计 2.1 控制要求的分析 2.2 控制方式选择 3 控制系统设计 3.1 原理图 3.1.1 主电路 3.1.2 地址分配 3.2 接线图 3.3 元件选型 3.4 PLC程序 4 课程设计总结 5 附录 附表1:元器件选型明细表 附图2:原理图 附图3:接线图
1 课程设计的内容及目的 对生产线上某种产品自动按指定数量(如12个)装箱,产箱装箱前及装箱后都由传送带传送。 生产线自动装箱控制装置示意图如图所示,生产产品由传送带A传送,装入由B传送的空箱中。每12个产品装入一箱,当传送带A传送12个产品装入一箱后,传送带B将该箱产品移走,并传送下一个空箱到指定位置等待传送带A传送来的产品。 图1装箱流程图
2 总体方案设计 2.1 控制要求的分析 用PLC控制整个控制装置要达到以下要求: 1、按下控制装置启动按钮后,传送带B先启动运行,拖动空箱体前移至指定位置,达到指定位置后,由SQ2发出信号,使传送带B制动停止。 2、传送带B停车后,传送带A启动运行,产品逐一落入箱内,由传感器检测产品数量,当累计产品数量达到12个时,传送带A制动停车,传送带B启动运行。 3、上述过程周而复始进行,直到按下停止按钮,传送带A和传送带B同时停止。 4、应有必要的信号指示,如电源有电、传送带A工作和传送带B工作等。 5、传送带A和传送带B应有独立点动控制,以便于调试和维修。 2.2 控制方式选择 1 当按下控制装置的自动控制按钮后,传送带B先启动运行,拖动空箱前移至指定位置,达到指定位置后,由SQ2发出信号,使传送带B制动停止。 2 传送带B停车后,传送带A启动运行,产品逐一落入箱内,由传感器检测产品数量达12个时,传送带A制动停止,传送带B启动运行。 3 上述过程循环地进行,直到按下停止按钮,传送带A和传送带B同时停止,其工作流程图如图2-3所示。 4 当按下手动选择按钮后,系统停止上述的自动控制运行,而可以手动进行控制传送带A和传送带B的运行,以便于调试和维修。
自动送料装车系统
PLC大型设计任务书 自动送料撞车系统 系别:电气工程系 班级:电气1004班 姓名:蔡英杰 指导老师:
前言 送料小车控制系统采用了PLC控制,从自动装车送料小车的工艺流程来看,它的控制系统属于自动和手动控制相结合的系统。传统的运料小车大都是继电器控制,而继电器控制有着接线繁多,故障率高的缺点,且维护维修不易等缺点。作为目前国内控制市场上的主流控制器,PLC在市场、技术、行业影响等方面有重要作用,利用PLC控制来代替继电器控制已是大势所趋。 在国际上PLC迅速发展的形势下,我国多数PLC厂家还没有拥有自主知识产权,能够参与国际竞争的PLC产品,其中之一就是研发实力不够。虽然资金投入、生产和质量管理等因素也占有非常大的比重,但对产品的质量起着决定性作用的是研发投入、研发成果产品化以及生产工艺等。而技术则是贯穿着其中每一个环节,PLC核心技术的开发、产品的后续开发、生产工艺的技术水平是决定产品质量的前提,如何在技术上进一步增强自己的实力,将是国产品牌取得市场竞争优势的关键。 依据得到的样本分析,初步得出正在使用的众多PLC的品牌中,西门子、三菱及omron占据绝对的优势,60%左右的用户使用了这些品牌的PLC产品,而rockwell/ab、ge-fanuc和富士等品牌也占有相当的市场份额。 我国可编程控制器的引进、应用、研制、生产是伴随着改革开放开始的。最初是在引进设备中大量使用了可编程控制器。接下来在各种企业的生产设备及产品中不断扩大了PLC的应用。
目前,我国自己已可以生产中小型可编程控制器。上海东屋电气有限公司生产的CF系列、杭州机床电器厂生产的DKK及D系列、大连组合机床研究所生产的S系列、苏州电子计算机厂生产的YZ系列等多种产品已具备了一定的规模并在工业产品中获得了应用。此外,无锡华光公司、上海乡岛公司等中外合资企业也是我国比较著名的PLC生产厂家。可以预期,随着我国现代化进程的深入,PLC在我国将有更广阔的应用天地。 在工业生产过程中,大量的开关量顺序控制,它按照逻辑条件进行顺序动作,并按照逻辑关系进行连锁保护动作的控制,及大量离散量的数据采集。传统上,这些功能是通过气动或电气控制系统来实现的。1968年美国GM(通用汽车)公司提出取代继电气控制装置的要求,第二年,美国数字设备公司(DEC)研制出了基于集成电路和电子技术的控制装置,首次采用程序化的手段应用于电气控制,这就是第一代可编程序控制器,称Programmable,是世界上公认的第一台PLC。 限于当时的元器件条件及计算机发展水平,早期的PLC主要由分立元件和中小规模集成电路组成,可以完成简单的逻辑控制及定时、计数功能。20世纪70年代初出现了微处理器。人们很快将其引入可编程控制器,使PLC增加了运算、数据传送及处理等功能,完成了真正具有计算机特征的工业控制装置。 本设计的任务设计一个PLC控制的自动送料装车系统,系统控制要求如下:
自动送料机控制系统设计
摘要 粉粒、粒状等固态物料的实时、精确计量一直是固态送料领域的难题。经过几十年的发展,随着传感技术、计算机技术、机电设备的发展,送料设备不断地完善,现在自动送料系统是生产中一个中间关键环节,它的作用是将生产中粉状、粒状物料以一定量一定速度输送到后续设备,以实现整个生产的自动化。 本文设计了基于单片机控制的送料机自动送料机控制系统的结构组成,论述了单片机AT89C51在实现其生产过程控制的硬件与软件的设计方法。系统以AT89C51控制核心,用2864A做外扩存储器来存储系统的初始数据,其主要作用的是:为了给系统设置一个合适的初态,当出现系统程序错乱,能回到的初态;利用扩展并行接口来外接控制按键,以此来接收操作命令。同时为了让工作者能了解到各按键的状态,再给系统接入发光二极管来显示相应按键的状态;采用LED静态显示来显示工作时间量变化情况;为了使LED位信息与单片机输出的信息相对应,在两者之间接了译码器MC14511B;为了能及时确定生产线的满料状态,给系统设计了一个满料中断电路,同时为抗干扰,将满料信号进行光耦隔离;为了让系统能稳定工作,防止程序乱飞,给系统设计了一个看门狗电路;为解决各外设与单片机AT89C51速度不等的情况,在两者之间接了锁存器;最后给系统接了一个内部时钟振荡器。 本设计的最终目标是做到用一台电机控制两条生产线,由方向阀来控制系统是处于送料还是排料状态,具有抗干扰性,实现供料自动化,提高生产效率。同时本控制系统可以根据送料工艺的需要,设置两条生产线的输送、排料、满料、空料等参数值。 关键词:自动送料机控制系统、单片机、AT89C51 、硬件设计、软件设计
生产线自动装箱装置控制系统设计
(此文档为word格式,下载后您可任意编辑修改!) 攀枝花学院本科毕业设计(论文) 生产线自动装箱装置 控制系统设计 学生姓名: 学生学号: 院(系): 年级专业: 指导教师: 助理指导教师:
二〇一三年五月
摘要 在现代化工业生产中时常需要对生产产品进行包装和计数,如果这么多繁杂的工作都完全由人工去完成的话不仅效率低下,而且劳动强度非常大,不能够满足现代化的生产需要。 本文主要对生产线自动装箱的PLC控制系统进行了细密的科学研究。此系统拥有有两个传送带,即生产产品传送带和包装箱传送带。产品传送带将生产产品从生产车间流水线传送到包装箱,当某一刻生产产品被送到传送带的末端时,就会自动地进入包装箱中,并由另一个传感器将其转换成计数脉冲。包装箱传送带则用来传第产品包装箱,其作用就是把已经装满了的包装箱运走,并用另外一只空箱来代替。为了使传送过来的空箱刚好对准产品传送带的末端,使产品准确落入空箱中,因此在包装箱的传送带中间装有一个光电传感器,用来检测空箱是否按照正确的方式传送到位。 此控制系统具有成本低、精度高、故障率低、抗干扰能力强、操作维护简单等特点,具有优良的实际应用价值。 关键词:系统,生产,自动,设计
ABSTRACT Often need to carry out counting and package on the product in the commercial run being modernized, not only the inefficient, moreover intensity of labour working from the words that the manpower accomplishes if these are complicated and overloaded is big , the childbirth being unfit to be modernized needs. Detailed research the main body of a book has been carried out on the PLC navar enchasing owing to production line automation mainly. Be system's turn to have two conveyer belts , be package box conveyer belt and product conveyer belt. The package box conveyer belt is used to deliver the product package box , whose function is that the package box luck already filling to full is leaked , is uses one to replace to come empty space box and. End being to make the empty space box aim at the product conveyer belt fitly, just the drop-in package box is hit by the messenger product, before package box conveyer belt centre install one photoelectricity sensor, in order to check if package box arrive at a place. And the product conveyer belt transmits a product from producing a workshop to package box , pawn some one products deliver to the conveyer belt end , the meeting automation drop-in package box inner, change from another sensor becoming counting pulse. Navar has accuracy height , the low , anti-interference ability of cost is strong , the malfunction leads a characteristic low , operation upkeep waits for simplely, have fine application value. Key words: System, Produce, V oluntarily, Design