首钢京唐公司1号高炉施工工艺探讨

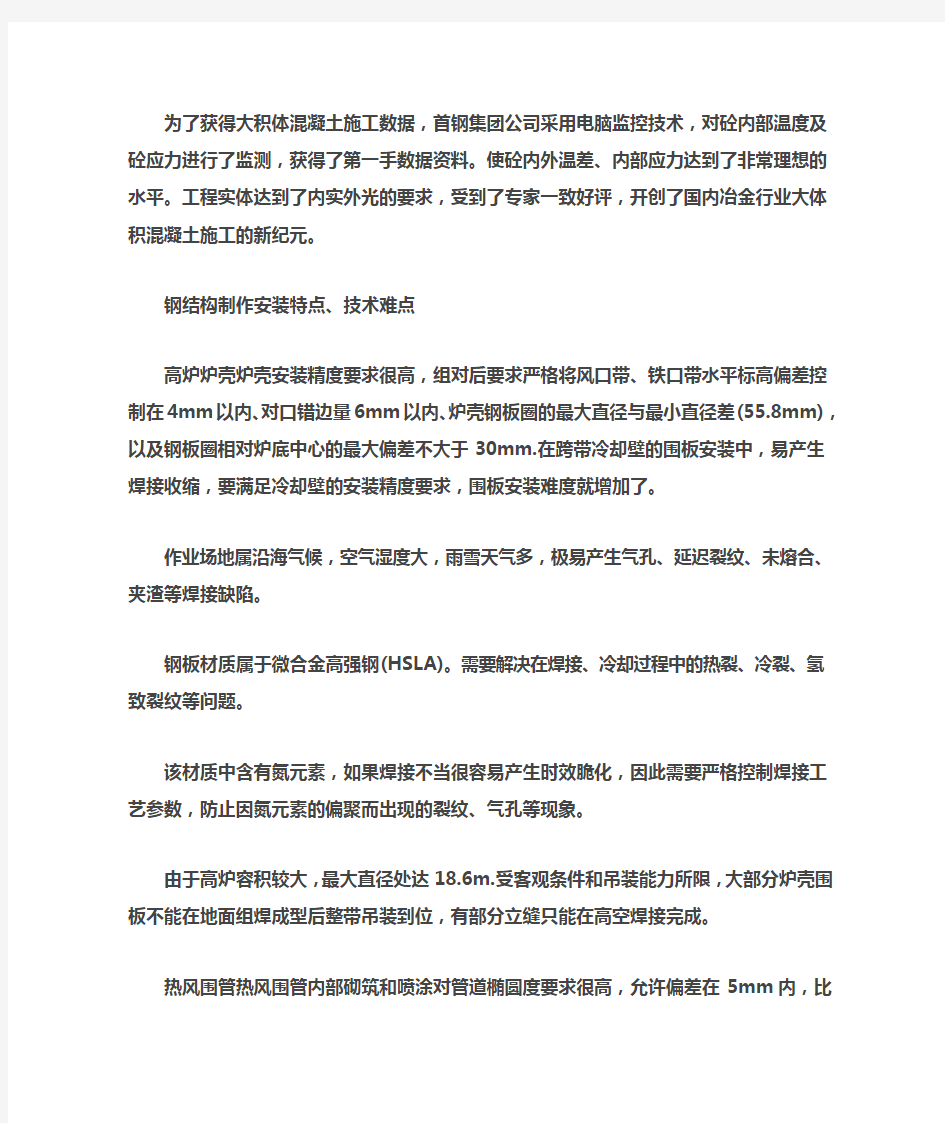
在首钢京唐钢铁厂一期一步5500m3高炉施工中,北京首钢建设集团有限公司(首建集团公司)全面总结了日本、欧洲5000m3以上高炉及国内大型高炉的设计和生产经验,坚持“高效、低耗、优质、长寿、清洁”的设计理念,采用先进实用、成熟可靠、节能环保、优质长寿的工艺技术和设备材料,实现了高炉的大型化、高效化、现代化、长寿化、清洁化。此高炉为国内首座5000m3以上特大型高炉,采用了当今国际炼铁技术领域的十大类、68项先进技术,具有21世纪国际先进水平和强大的竞争力。一期一步高炉总高126.4m,有效容积5500m3,年工作日355天,年生产449万吨铁水,设计寿命25年(一代炉龄)。共完成土方6.4万m3,浇筑混凝土5.315万m3,钢结构制作安装2.9万吨,设备安装9224吨,电缆敷设123.5公里,各种管道4.5公里,并成功实现了1号5500m3高炉基础混凝土连续浇筑84.5小时,共10454m3.
基础混凝土施工的主要特点和技术难点
高炉基础2007年3月12日正式开始施工, 4月2日上午9:00开始浇筑砼,经过连续84.5个小时的不间断浇注,顺利完成了浇注混凝土10454m3的施工任务。整个高炉基础施工历时24天。
5500m3高炉基础浇注是国内最厚的大体积混凝土浇注工程,工程量最大,质量要求高,养护困难,必须一次不间断连续浇注完成。首建集团公司高度重视,组织工程技术人员制定了详细周密的技术方案和施工组织实施方案,并聘请国内知名的混凝土裂缝专家进行评审和技术把关。施工中采用了国内最先进的测温技术和应力应变技术,随时掌握内外温差,确保控制在25℃以内。搅拌站至高炉工地往返6公里的运距,采用了26台9m3的水泥罐车,每台按规定时间跑12个往返,共1248车次。整个施工过程没有发生任何安全质量问题,创造了中国冶金工程建设史上的新纪录。
为了获得大积体混凝土施工数据,首钢集团公司采用电脑监控技术,对砼内部温度及砼应力进行了监测,获得了第一手数据资料。使砼内外温差、内部应力达到了非常理想的水平。工程实体达到了内实外光的要求,受到了专家一致好评,开创了国内冶金行业大体积混凝土施工的新纪元。
钢结构制作安装特点、技术难点
高炉炉壳炉壳安装精度要求很高,组对后要求严格将风口带、铁口带水平标高偏差控制在4mm以内、对口错边量6mm以内、炉壳钢板圈的最大直径与最小直径差(55.8mm),以及钢板圈相对炉底中心的最大偏差不大于30mm.在跨带冷却壁的围板安装中,易产生焊接收缩,要满足冷却壁的安装精度要求,围板安装难度就增加了。
作业场地属沿海气候,空气湿度大,雨雪天气多,极易产生气孔、延迟裂纹、未熔合、夹渣等焊接缺陷。
钢板材质属于微合金高强钢(HSLA)。需要解决在焊接、冷却过程中的热裂、冷裂、氢致裂纹等问题。
该材质中含有氮元素,如果焊接不当很容易产生时效脆化,因此需要严格控制焊接工艺参数,防止因氮元素的偏聚而出现的裂纹、气孔等现象。
由于高炉容积较大,最大直径处达18.6m.受客观条件和吊装能力所限,大部分炉壳围板不能在地面组焊成型后整带吊装到位,有部分立缝只能在高空焊接完成。
热风围管热风围管内部砌筑和喷涂对管道椭圆度要求很高,允许偏差在5mm内,比普通大直径卷焊钢管制作椭圆度要求提高了5mm. 42个短节对应高炉42个风口直吹管,要确保42套风口设备的安装精度,对短节弦长以及相互间尺寸的加工和安装精度提出了很高要求。
热风围管安装精度,环管上表面高低差要求控制在10mm内。围管内表面至高炉外壳的距离允许偏差要求控制在20mm以内。
上升管、五通球上升管在70m高空对接安装,垂直度控制在20mm以内。
五通球需开5个孔与四根上升管和一根下降管相联,然后在110m高空进行组对安装,开孔位置允许偏差3mm,开孔直径与支管直径之差2~5mm.五通球在113m高空安装组对,安装标高偏差要求控制在±30mm以内,纵横中心偏差不超过30mm.构件的安装顺序给吊车的设置和吊装带来很大难度。五通球重量达62吨,安装中心标高▽113m,DBQ4000吊车只能在五通球吊装到位后擎住,再利用630吨吊车进行第四根上升管弯管的安装。
下降管下降管上联五通球,下接旋风除尘器,是自立门架式结构的超长(66m)钢管斜横梁,中间无支撑,两端为固定口连接。设计要求整体门架结构形成前,五通球及旋风除尘器伸出部分不能承受较大的悬臂弯矩。
下降管安装位置高(上口标高113.2m,下口标高63.103m),重量大(176t),其下是矩形出铁厂房;吊装重量大,考虑施工成本及场地狭窄的现场条件,无法使用两台超大型吊车抬吊就位。同时沿海施工吊装构件高空横向风力大(常年3级风以上)。
由于五通球上伸出弯管及旋风除尘器上斜插管为空间结构,管壁厚20mm,空中组装误差及焊接变形较大,下降管与其为固定口相连,空中组对困难。
炉体框架炉体框架柱截面尺寸大,内部结构极为复杂,施工图深化设计和加工制作难度很大。
框架结构内部采用了横向横隔板、纵向T型加劲肋的结构形式。框架柱在12m内就有9组横隔板和10根T型钢,箱型柱内部结构复杂,焊接量大,易变形。
框架柱单节柱最重达101吨。
各层平台采用八卦式结构布置,设计要求平台梁两端安装精度控制在1mm以内,以保证高强螺栓的安装。
防腐蚀要求高该地区属于沿海地区,空气湿度大,氯离子含量高,对钢结构腐蚀性强,因此除锈防腐是非常重要的环节。因此采用喷砂除锈达到Sa2.5级后,刷富锌底漆,它是性能优异、具备阴极保护的电化学涂料。
底漆:环氧富锌漆一遍,干膜厚度60μm(室外);中间漆:环氧云铁漆一遍,干膜厚度80μm(室外);面漆:脂肪族聚氨酯面漆两遍,干膜厚度60μm(室外)。
在炉本体钢结构制作安装中采取的有效措施
高炉炉壳安装和焊接控制工艺炉壳安装和焊接工艺流程:设备调试→炉壳吊装组对→装配交检→焊前预热→炉壳立缝焊接→炉壳环缝焊接→焊接检验→焊后热处理。
高炉第1带~12带炉壳按出厂单元进行吊装、组对焊接;第13带~16带先在安装现场组焊成单带,然后整带安装就位;第17带~22带在工厂每相邻两带组焊成一个单元,然后发运到安装现场直接吊装就位。第23带、第24带+25带分别在工厂组焊成带,然后发运到安装现场直接吊装就位。
吊装组对后调整、测量,再调整、复测,合格后加固,进行焊接,采用二氧化碳气体保护焊的方法。
严格执行焊前预热、焊后缓冷、焊后热处理工艺,采用电加热方法,利用计算机控制技术+WDJK-360型控制柜对履带式电加热器进行适时控制,设定控制参数实现全程自动控制,保证了焊接和热处理的质量;同时这也是解决由于现场高湿度可能引起焊接缺陷问题的措施之一。
预热温度:120~150℃;后热温度:250~300℃;热处理温度:650℃。
严格控制焊接程序,先焊炉内侧焊缝,然后在外侧碳弧气刨清根、打磨合格后,再对外侧焊缝实施焊接,同时采取对称焊、多层多道焊、分段退焊等方法,最大限度降低因为厚板焊接存在的拘束度过大而产生裂纹的可能性。
针对BB503材料的特点:在焊接过程中为防止氮元素在焊缝处偏聚,严格控制熔合比,严格控制焊接线能量和层间温度。
针对沿海焊接施工的特点,严格执行了以下控制措施:在炉壳对接、组焊过程中,视天气情况,适当采取防风、防雨、防雪等措施,确保焊接质量要求。
严格清理焊接坡口表面及两侧距坡口边缘30㎜内的水渍、铁锈、油污、渣和其它杂质。
严格控制焊材的含水量:CO2气体保护焊用的CO2气体应保持干燥,气体纯度不小于99.8%(体积法),含水量不大于0.005%(重量法)。
严格执行焊前预热、焊后后热、缓冷的工艺措施。
为保证炉壳的尺寸和炉顶标高,采取了带与带之间预留间隙的方法进行调整,通过计算使间隙在2~4mm内,在焊后收缩的情况下,完全满足了冷却壁的安装和炉顶设备安装的要求。
热风围管制作、安装工艺采用数控切割,切割后的尺寸极限偏差控制在±1mm内。
围管短节组对过程中,依次检查组对后内侧和外侧弦长,以保证围管整体圆度。
制作完成后整体预拼装,对有超差部分进行地面调整。
在9.9m平台上组对,提前在平台上划出十字中心线、围管内外边缘线,围管整体组装完后进行焊接加固,防止变形。
在34m平台上设立4个吊点,利用滑轮组进行同步整体吊装,吊装过程中全程监测高度。
吊装到位后测量环管内表面至高炉外壳的距离,在确保合格后利用垂直吊杆固定。
上升管制作安装工艺采用数控切割下料,把切割偏差控制在了±1mm以内。
上升管地面组对,整体吊装,减少高空作业难度和满足上升管垂直度的要求。
五通球制作安装工艺措施球片用专用胎具压制,为保证各块边缘成形精度,在每块四周加放3倍板厚的压头量。
五通球支架和支撑按30°周圈布置,在基准圆外侧的球壳板处均匀点焊定位块,然后以定位块和胎具为基准,按顺序装配赤道带壳板。待纵缝定位焊接完成后装上、下极带。
五通球与上升管四个接口设立活动短节,以便在高空组对时调整,提高了组装精度,加快了施工进度。
根据五通球焊接容易变形等特点,首建集团公司经过精确定位,对五通口相贯线进行精确切割,并加设16道放射型防变形拉筋,保证了其椭圆度达到图纸及规范要求。
下降管计算机模拟吊装技术。根据现有施工场地及吊车起重能力,确定吊装构件大小(分2段吊装),施工前用计算机模拟整个吊装过程,精确制定下降管部件现场组对位置、吊车及起吊重物运行路线、就位过程,确保构件平稳无障碍吊装。
精确计算构件重心,确定主吊点及调整绳悬挂点,确保构件按安装位置角度起吊。
下降管上装有梯子、栏杆及均压放散管等附件,必须精确计算组装后构件的重心,选择正确的主吊点及调整绳悬挂点,在离开地面前调整好角度,才能精确安装就位,实现与固定口的组对。
采用可调式支架,空中调整及支撑上管段。
按照安装位置,用计算机模拟设计上管段“人”字形支撑架,支脚与炉顶平台梁铰接,在炉顶平台设链式起重机,用钢丝绳拉支架顶住横梁,在五通球上焊接吊耳挂固定定滑轮,通过链式起重机、钢丝绳调整支撑架位置,进而支撑或调整管段安装角度。
仪器精确测量五通球伸出管及旋风除尘器斜插管空间位置,确定下管段长度及角度。
用进口高精度TDA5005全站仪精确测量五通球伸出管口、旋风除尘器斜插管口相对高炉中心线的角度、位置座标点,计算确定下段管的长度,测量精度达到了0.3mm.三角形法测量下管段吊起角度,配重调整,使吊起角度与安装就位角度完全相同。按安装就位角度精确计算下管段重心,用吊车试吊离地面,下管段上口挂重锤,由下管口下部拉钢线,用钢角尺测量使钢线与重锤线垂直后,测量两钢线长度与计算值对比,然后在两管端调整配重,直至两者相等后起吊。
选择晴朗风力小的天气,上午10点钟以后吊装,避免沿海早晚风大的影响。
通过实施以上6项措施,下降管上段2小时吊装就位组对完,下段4小时吊装就位组对完,管口长度偏差23mm,径向偏差5mm,高于规范径向偏差10mm的要求,而且快捷安全完成吊装任务。
炉体框架柱、梁针对框架柱、梁结构复杂,节点深化困难的问题。首建集团公司成立了专门的详图深化设计小组,利用AutoCAD进行空间建模,在此基础上拆分零部件图,提高了详图质量,确保了配合尺寸精度,满足了工程需要。
炉体箱型柱、梁造型复杂,内部加劲肋数量多,焊接过程中易变形。首建集团公司根据不同的构件和不同的节点形式采用如下控制方法,对控制焊接变形和残余应力达到了事半功倍的效果:划分制作单元,安排合理装配、焊接顺序:翼缘板、腹板、隔板、T型肋等均经过变形校正后方可进行装配。装配时按结构特点,采取一次装配、焊接、二次装配、二次焊接的方法,确保装配、焊接质量。
采用手工电弧焊、二氧化碳气体保护焊、埋弧焊接等多种焊接方式以适应不同的结构型式和空间位置。
厚板焊接采用焊前预热、多层多道焊、分段退焊、焊后缓冷等方法,焊接过程中控制层间温度在100~200℃,以控制焊接变形和应力。
对焊缝集中的部位:采用小规范、对称焊等方法,以减小焊接应力和变形。
在满足设计要求的情况下,隔板和加劲肋采用间断焊接的方法。
对于要求开坡口的部位,尽量采用双面对称坡口,并在多层焊接过程中采用对称焊。
针对炉体框架柱、梁安装精度高的要求及构件重量大的问题,首建集团公司采取了以下措施进行控制。
利用CAD在电脑上对柱基数据进行测量,复核基础的标高以及和炉基中心的距离。保证安装时立柱间对角线距离控制在了7mm内,比相关规范15mm的要求有了明显提高。
安装时用经纬仪测中心线的垂直度,用水准仪测量检查标高,下部用千斤和倒链微调,合格后将垫板垫实、螺栓把紧。
经过计算,首建集团公司选用4000t.m吊车对炉体框架柱进行吊装,选用300t履带吊对炉体框架梁进行吊装。
通过以上的措施,既解决了由于结构复杂,给详图深化设计带来的困难,又消除了构件制作中的焊接变形,所安装的炉体框架柱垂直度偏差最大为10mm、均在规范要求的20mm 以内,炉体框架梁水平度均在2mm内。
新技术应用
高炉炉壳BB503特厚钢板焊接技术;厚板热处理采用计算机自动控制。
使用进口的高精度TDA5005全站仪,对高炉标高及中心线进行三维坐标测量(TDA5005全站仪其角度测量精度标准偏差±0.5〞;自动水平补偿设置精度±0.3〞;总精度±0.3mm;测距精度±0.2mm)。
大截面厚板箱型梁焊接、热处理工艺及应用技术。
采用数控相贯线切割机进行钢管切割下料,并采用数控编程对每根构件尺寸及每个相贯口形状进行切割下料。该方法操作简单,工艺先进,切割精度和效率高。尤其是对各种复杂的钢管贯口,更能体现其自动切割、高效切割和高质量切割的优点。
计算机信息化管理:模拟吊装、详图设计、资料管理。
具有沿海地区特色的钢结构防腐技术。
高炉碳砖砌筑的技术难点及采取的措施高炉碳砖历时103天,比预定时间提前近25天。高炉筑炉工程于3月15日开工,共用耐火砖6.9万块,每天平均砌筑量达到40吨。面对炉缸直径达到15.5m的首钢京唐公司1号高炉,首建集团公司克服了各种困难,提前并圆满地完成了筑炉工程。这项工程可以说是首钢精度最高、质量最好的高炉砌筑工程。
在高炉炉内砌筑中,此次高炉本体筑炉施工材料均选用国外产品,特别是首钢首次选用日本NDK要求精度较高且比以前施工过的高炉碳砖单位体积(3m×0.7m×0.6m)和单重(最重2吨/块)都大的多的四层满铺碳砖,其砌筑质量要求的平整度和泥缝要在0.5mm以内(国际特类砌体其泥浆浆缝不大于0.5mm)。针对此次高炉的特点,首建集团公司首先在施工找平层上下工夫,改变标尺原做法,提高标尺加工精度。在标尺安装中确保标尺安装后的标高差在-1mm内,并在找平层施工完为让开冬季的时间段内对炉底找平层进行四层防护。在砌筑第一层满铺碳砖前再次对272m2的基层测量后找平,对于平整度超过1mm的部位再次人工进行加工(国标GB50211-2004中6.2.5条规定其标高误差不应超过-2mm),做到精益求精。
在272m2的基层上砌筑第一层满铺碳砖是整个高炉砌筑的关键,砌筑施工中首先对大砖进行预码,这样的2吨大砖有时一块要预码十余次直到与其它相邻大砖没有一丝错台后再砌筑,确保了砌完第一层347块大砖后用水平仪测量510个点达到±1mm的平整度(国标GB50211-2004中6.2.2条规定其标高误差不应超过5mm)。远远超过了国标,在砌筑第二、三、四层时主动加压用更高标准组织施工,砌筑完第四层后用水平仪测量510余点,其平整度达到了±0.5mm,且砖间缝无一超过0.3mm(施工要求为0.5mm)。由于在质量上的高标准严要求确保了每道工序施工工艺的高标准完成。
首钢京唐介绍
首钢京唐公司介绍 首钢京唐钢铁联合有限责任公司钢铁厂项目是纳入国家“十一五”规划纲要的重点工程。项目建设始终得到党中央、国务院的亲切关怀,得到了北京市、河北省和唐山市的大力支持,得到了社会各界的关心和帮助。胡锦涛、吴邦国、温家宝、贾庆林、李长春、李克强、贺国强等党和国家领导人,相继到首钢京唐公司钢铁厂建设工地考察调研,对项目建设作出重要指示。 一、项目沿革 2005年2月18日,国家发改委下发“发改工业〔2005〕273号《关于首钢实施搬迁、结构调整和环境治理方案的批复》”,批准首钢“按照循环经济的理念,结合首钢搬迁和唐山地区钢铁工业调整,在曹妃甸建设一个具有国际先进水平的钢铁联合企业”。 2005年10月9日,“首钢京唐钢铁联合有限责任公司”在唐山市注册成立。2005年l0月22日,首钢京唐钢铁联合有限责任公司成立大会在曹妃甸隆重举行。时任中共中央政治局委员、国务院副总理曾培炎莅会讲话并为公司揭牌 2006年3月14日,十届全国人大四次会议表决通过的《中华人民共和国国民经济和社会发展第十一个五年规划纲要》提出:结合首钢等城市钢铁企业搬迁和淘汰落后生产能力,建设曹妃甸等钢铁基地。 2007年2月7日,国务院常务会议讨论批准了国家发改委上报的《关于审批首钢京唐钢铁项目可行性研究报告的请示》,同意结合首钢搬迁,河北省淘汰落后产能,首钢京唐钢铁联合有限责任公司在河北曹妃甸建设年设计能力970万吨的钢铁项目。 2007年3月12日,首钢京唐钢铁联合有限责任公司钢铁厂项目开工仪式在首钢篮球中心隆重举行。时任中共中央政治局委员、国务院副总理曾培炎作重要讲话,并宣布开工。中共中央政治局委员、北京市委书记刘淇出席开工仪式。 二、建设目标、建设规模、建设内容 建设目标:坚持高起点、高标准、高要求,实现产品一流、管理一流、环境一流、效益一流,成为科学发展、自主创新、循环经济的示范企业。 建设规模:项目设计年产铁898万吨、钢970万吨、钢材913万吨。计划分两个阶段建成投产,第一步工程形成年产钢485万吨生产能力,整个一期工程于2010年建成投产。 建设内容:包括主体工程和辅助工程两大部分。主体工程部分主要包括:建设4座70孔7.63米焦炉及配套的干熄焦设施,2台550 平方米烧结机,1台504 平方米球团带式焙烧机,2座5500 立方米高炉,2座300吨脱磷转炉、3座300吨脱碳转炉、1座LF精炼炉、2套RH真空精炼装置、2台2150毫米双流板坯连铸机、1台1650毫米双流板坯连铸机,2250 毫米、1580毫米热连轧机组各1套,2230毫米、1700毫米、1550毫米酸洗——冷轧联合机组各1套以及配套的连续退火机组、热镀锌线等。辅助工程部分主要包括:一个大型综合料场,2台7.5万立方米/小时制氧机,2座300兆瓦燃煤——燃气混烧供热发电机组、2座150兆瓦CCPP燃气——蒸汽联合循环发电机组,5万立方米/日淡水的海水淡化设施和相应的公辅配套设施。 三、项目主要特点
首钢京唐公司钢铁厂项目简介
首钢京唐钢铁联合有限责任公司简介 首钢京唐钢铁联合有限责任公司钢铁厂项目是国家“十一五”规划纲要确定的重点钢铁建设项目,由首钢和唐钢共同出资建设,于2005年10月在唐山市注册成立。 钢铁厂地理位置和区位优势 钢铁厂位于唐山市南部渤海湾曹妃甸岛,西距北京市220km,北距唐山市80km。曹妃甸地处环渤海经济圈内,辐射北京、天津、河北等7个省市区,为企业发展提供了广阔的空间。 曹妃甸钢铁厂临海优势明显,有“面向大海有深槽,背靠陆地有浅滩”的天然良港和建厂条件。港口可满足25万t 级以上大型船舶进出,有利于大幅度降低原料和产品运输成本。钢铁厂建设用地来源于滩涂围海造地,不占用耕地资源。 建设规模、主体设施和主要特点 钢铁厂一期工程建设包括焦化、烧结、球团、炼铁、炼钢、连铸、热轧、冷轧等主要生产工艺流程以及制氧、发电、海水淡化等配套公辅系统,年产生铁898万t,钢坯970万t,钢材912万t。 主体工艺设施配置:500m2烧结机2台,60孔7.63m焦炉4座,504m2带式焙烧机球团生产线1条(预留)、5500m3高炉2座、300t脱磷转炉2座、300t脱碳转炉3座(其中预留1座)、2150mm双流板坯连铸机2台、1650mm双流板坯连铸机1台、2250mm和1580mm热连轧机各1套,2230mm、1700mm和1550mm冷连轧机组各1套。预留熔融还原炼铁炉、薄板坯连铸连轧短流程生产系统,预留化工产品深加工设施。 主要公共辅助生产设施:2台300MW燃煤-燃气混烧自备电厂发电机组、1台150MW燃气-蒸汽联合循环发电机组、2台余压发电机组、2台30MWCDQ余热发电机组、2台75000 m3/h制氧机组。 新钢厂建设规模宏大,工艺装备精良,技术先进可靠,创新亮点很多。主要有五个特点: 第一、装备大型。钢铁厂集中采用了目前我国最大、世界上为数不多的大型焦炉、烧结机、球团焙烧机、高炉、转炉、板坯连铸机、热连轧机和冷连轧机。构成了高效率、低成本的生产运行系统,具有现代化钢铁厂的标志,体现了钢铁厂综合
首钢京唐公司干熄焦烘炉及开工方案
首钢京唐钢铁联合有限责任公司焦化作业部干熄焦烘炉及开工方案 首钢京唐钢铁联合有限责任公司焦化作业部 2007年10月
目录第一部分前言 第二部分开工投产指挥系统 第三部分烘炉、开工项目及进度计划第四部分干熄焦的烘炉 第五部分开工热态调试 第六部分安全注意事项
第三部分烘炉、开工项目及进度计划 一、在烘炉开工的准备阶段前一周完成,并具备投产条件。 1、除盐水站能连续制纯水,确保干熄焦投产用水。 2、电机车单体、联动试车完毕,具备投产条件 3、装入装置单体、联动试车完毕,具备投产条件 4、排出装置单体、联动试车完毕,具备投产条件 5、干熄槽砌筑完毕,内部杂物清理干净,烘炉系统管道及设备安装、调试完毕, 各测温、测压、测量、料位计等计器仪表安装完毕,具备投产条件。烘炉用测温和记录仪安装完毕。 6、锅炉系统水压、酸洗、密封试验完毕,安全阀及安全系统经上级部门校验合 格,具备投产条件 7、气体循环系统及除尘系统单体、联动试车完毕,具备投产条件 8、各动力管道(风、水、电、气、蒸汽)安装、接点试压完毕,各电力电气设 备安装调试完毕,单体、联动试车完毕,并得到有关管理部门的使用批准,具备投产条件。 9、烘炉、开工、正常生产各种原始记录(岗位记录、设备点检记录)及生产报 表编制、审批完毕,具备投产条件。 10、烘炉、开工、正常生产所必备的工具、用具、原料等准备完毕,具备烘 炉、开工、投产条件。 11、各生产岗位及维护人员配备完毕,具备投产条件 12、各岗位“生产操作手册”初稿编制审查完毕,具备投产条件 13、开工投产指挥系统组织安排完毕,具备开工条件 14、EI系统调整完毕 15、基建各项尾工、现场清理完毕 二、烘炉开工的准备阶段 周期:天累计天数:天 1、1DC、2DC人孔门进风调节板安装 2、排出装置排灰管2处隔板放置 3、气体放散阀进风调节板放置 4、1DC、2DC排灰球阀下部隔板放置 5、循环系统烘炉放水孔法兰取掉 6、炉顶装入装置集尘挡板关闭 7、有关连锁解除,仪表指示校正 8、CDQ系统调整 9、锅炉上水,水位调整 10、设备运转试验 11、斜道配风调整板的校正 12、物料准备 13、表面碎耐火砖铺设 14、装冷焦 15、排焦试验 16、冷焦造型,焦炭表面温度的测量
首钢京唐钢铁厂综合污水处理核心工艺设计简介
首钢京唐钢铁厂综合污水处理 核心工艺设计简介 摘要:进入二十一世纪,能源及环保已成为当今世界可持续发展的两大主题。鉴于我国水资源日趋紧张及水污染的严重形势,污水处理及回用迫在眉睫。钢铁工业作为国民经济各行业中的用水大户,其污水的处理及回用意义尤为重要。新建的首钢京唐钢铁联合有限责任公司采用国际先进工艺装备,建设规模为年产钢坯970万t。钢材品种全部为板材产品。生产流程为原料、焦化、烧结、球团、炼铁、炼钢、连铸、热轧、冷轧的长流程生产工艺。公辅生产工艺遵循循环经济的理念,延长生产过程中水的使用周期,实施生产污水资源化。结合首钢污水治理工程的实践经验以及对新建首钢京唐钢铁厂污水水质的设计,对京唐钢铁厂生产污水采用新型、改进的沉淀、过滤的物理一化学处理工艺,对水中的油、悬浮物、硬度、碱度等有害物质进行有效去除,节约全厂工业新水耗量,提高全厂经济和环境效益。污水处理站进水经处理后最终全部回用。 1 概述 钢铁工业作为国家的重点行业,近年来得到了飞速发展,钢铁产量已占世界总产量的三分之一。日益增长的产量,一方面较高的用水量加剧了水资源的消耗,另一方面所排放的污水对环境又造成可严重污染。 “节能、减排”是我国当前的工作重点,国家发改委会同有关部门制定的《节能减排综合性工作方案》中明确规定,“2010年,单位工业增加值用水量降低30%,……‘十一五’期间实现重点行业节水31亿m3”。为适应新时期对社会经济可持续发展的要求,新建的首钢京唐钢铁联合有限责任公司,事项清洁生产和末端处理技术措施。清洁生产是指通过调整产品结构、控制废物产生源和加强生产管理,减少污染物的排放量和降低能源消耗量;末端处理是指通过对污染物技术处理,实现污染物的达标并回用。为此,京唐钢铁厂新建2座综合污水处理站,每座站生产污水平均处理能力:24000m3;日最大处理能力:30000m3。处理后的生产污水全部回用各工序。 2 钢铁厂生产污水的分类及特点
首钢京唐公司打造精益管理升级版
首钢京唐公司打造精益管理升级版首钢京唐公司打造精益管理升级版 2019年04月25日 首钢京唐公司运输部成品码头5号成品库内,两辆天车正在精准地吊装着冷轧板卷,而天车的操作室内却空无一人;在炼钢部,连铸2号机板坯质量检测系统的上线运行,实现了板坯表面质量在线实时检测,提前自动判定板坯的缺陷,缺陷检出率稳定在95%以上……这些,是首钢京唐公司运用信息化、自动化手段,采用先进智能装备,创新工艺流程,实现精细管理最优化的真实写照。 多年来,首钢京唐公司持续挖掘内部潜力,导入精益思想,倡导精益文化,推行精益方法,建立精益组织,形成精益流程,提升精益制造,推进质量、生产、成本、技术、经营、安全管理精益化,一步一个脚印,不断打造精益管理的升级版。 导入理念导入理念,,推进精益管理升级 推进精益管理升级 推行精益管理、倡导以最少的投入实现最大产出。正是精益的这一核心理念,引领着首钢京唐公司在挖掘潜力和持续创新的道路上不断前行。 首钢京唐公司把“精细、规范、协调、执行”的管理理念,严细到每一个环节、每一个细节。回顾首钢京唐公司多年来的管理历程,“精益”二字贯穿始终。2009年,随着首钢京唐公司一期工程的投产,“精益生产体系”的目标随之建立起来;2011年,树立“精细化管理、精细化操作”工作理念,推行全方位的精细化;2012年,按照“持续改进,追求精益”理念,首钢京唐公司成功导入精益六西格玛管理;2014年,首钢京唐公司聚焦现场,结合岗位作业实际和专业管理,强化基础管理,推进6S/QTI。 2018年年初,首钢京唐公司明确了“加快完善精益管理体系,优化组织架构,整合现有精益改善推进组织,实现统一管理、分级推进、形成合力”的思路。为强化持续改善的精益管理,首钢京唐公司以“安全、质量、成本、效率、环境”为出发点和落脚点,构建了以QTI 为代表的员工自主管理、自我改善的创新机制,通过新机制的建立,降低公司生产运营成本,提升公司内在竞争力,促进公司可持续发展。 在持续推进6S/QTI 管理过程中,首钢京唐公司按照有利于提升安全管理水平,有利于提高效率、效益,有利于提高产品质量的基本原则,聚焦设备和生产现场,结合岗位作业和专业管理,在巩固和提高6S 现场管理的基础上,从生产现场深化打造、TPM 初期清扫及两源治理、专项工作推进入手,不断提升管理水平,形成了具有京唐特色的设备及现场精益管理体系。6S 标准化管理体系共建立一级标准294份、二级标准1665份、三级标准864份,将2823份现场管理标准编号建库,实施动态管理。并将改善后成果纳入管理标准,循环完善、持续提升。 首钢京唐公司将日常安全管理与安全标准化相结合,不断强化安全管理体系,有力促进了安全标准化建设的创建。公司炼铁作业部(炼铁、烧结球团),炼钢作业部(炼钢),热轧作业部(轧钢),冷轧作业部(轧钢),能源与环境部(煤气)被评为冶金安全生产标
首钢京唐公司钢铁厂项目简介
首钢京唐公司钢铁厂项 目简介 文件排版存档编号:[UYTR-OUPT28-KBNTL98-UYNN208]
首钢京唐钢铁联合有限责任公司简介 首钢京唐钢铁联合有限责任公司钢铁厂项目是国家“十一五”规划纲要确定的重点钢铁建设项目,由首钢和唐钢共同出资建设,于2005年10月在唐山市注册成立。 钢铁厂地理位置和区位优势 钢铁厂位于唐山市南部渤海湾曹妃甸岛,西距北京市220km,北距唐山市80km。曹妃甸地处环渤海经济圈内,辐射北京、天津、河北等7个省市区,为企业发展提供了广阔的空间。 曹妃甸钢铁厂临海优势明显,有“面向大海有深槽,背靠陆地有浅滩”的天然良港和建厂条件。港口可满足25万t 级以上大型船舶进出,有利于大幅度降低原料和产品运输成本。钢铁厂建设用地来源于滩涂围海造地,不占用耕地资源。 建设规模、主体设施和主要特点 钢铁厂一期工程建设包括焦化、烧结、球团、炼铁、炼钢、连铸、热轧、冷轧等主要生产工艺流程以及制氧、发电、海水淡化等配套公辅系统,年产生铁898万t,钢坯970万t,钢材912万t。 主体工艺设施配置:500m2烧结机2台,60孔7.63m焦炉4座,504m2带式焙烧机球团生产线1条(预留)、5500m3高炉2座、300t脱磷转炉2座、300t脱碳转炉3座(其中预留1座)、2150mm双流板坯连铸机2台、1650mm双流板坯连铸机1台、2250mm和1580mm 热连轧机各1套,2230mm、1700mm和1550mm冷连轧机组各1套。预留熔融还原炼铁炉、薄板坯连铸连轧短流程生产系统,预留化工产品深加工设施。 主要公共辅助生产设施:2台300MW燃煤-燃气混烧自备电厂发电机组、1台150MW 燃气-蒸汽联合循环发电机组、2台余压发电机组、2台30MWCDQ余热发电机组、2台75000 m3/h制氧机组。 新钢厂建设规模宏大,工艺装备精良,技术先进可靠,创新亮点很多。主要有五个特点: 第一、装备大型。钢铁厂集中采用了目前我国最大、世界上为数不多的大型焦炉、烧结机、球团焙烧机、高炉、转炉、板坯连铸机、热连轧机和冷连轧机。构成了高效率、低成本的生产运行系统,具有现代化钢铁厂的标志,体现了钢铁厂综合竞争力,代表着中国钢铁工业的发展方向。目前,全世界超过5000 m3的高炉共有13座,新建的
京唐钢铁
首钢搬迁配套项目亏损调查:失控的1号高炉 首钢京唐钢铁联合有限责任公司(下称京唐钢铁)工程部部长杜朝辉清楚地记得去年5月8日是星期六,那天下午2点,杜朝辉参加完接待活动后开车回京,当车行驶到唐山西外环时,曹妃甸的同事来电告知他:1号高炉炼钢主控室电缆失火。 火灾直接导致京唐钢铁近650公里电缆被烧,架空管道焊接钢板开焊,整个炼钢厂区全面停产、半停产长达一年零两个月,经营损失延续至今。 这场意外的事故,为京唐钢铁持续不断的经营亏损添加了沉重的一笔。京唐钢铁持续亏损已被业内人士广为所知,据本报记者获得的资料,京唐钢铁自2009年投产至今,净亏损已超过50亿元。其中,2010年和2009年,京唐钢铁分别净亏损31.37亿元、5.3亿元;2011年,京唐钢铁预亏额再度超过30亿元,今年一季度已净亏损9.13亿元。 作为首钢搬迁的最重要配套项目,京唐钢铁被视为暮气渐浓的首钢重新崛起的押宝项目。2005年底,京唐钢铁在一系列政府政策的“关照”中注册成立,是纳入国家“十一五”规划纲要的重点工程,股权结构为首钢和唐钢分别占股51%和49%。国家批复京唐钢铁的总投资为677.31亿元;其中,银行贷款为338.6亿元;项目资本金投入为338.71亿元,由首钢和唐钢按照各自股权比例分别出资。 京唐钢铁拥有全国仅有的两座5500立方米高炉,分别于2009年5月21日和2010年6月26日投产。在此之前,国内最大的高炉容积是4500立方米,首钢寄望“把京唐公司建设成为世界最先进的钢厂之一”,“给中国钢铁工业做一个示范”。 京唐钢铁的“示范”作用,还在于其220项先进技术中,有三分之二是首钢自主创新或集成创新。这一点也成为京唐钢铁投产后高炉故障不断的理由之一。 一家总投资达677亿元、设备达到世界先进水平的钢铁企业,一个几乎决定老首钢发展命运的项目,为何如此惨淡开场? “京唐公司是新技术,有一个磨合、适应的过程,加上设备折旧增多、钢铁业不景气等。” 首钢总经理助理韩庆对本报记者解释京唐钢铁亏损的原因。 首钢董事长朱继民一方面对本报记者承认京唐钢铁亏损事实,另一方面则特别强调,“京唐现在是亏损,并不代表以后还亏损。” 然而,以京唐钢铁今年扩大的亏损额度来看,朱继民的话更多是一个愿望。今年7月,工信部召开全国主要钢铁企业摸底调研会议,据河北省钢铁企业汇报情况,河北省除了京唐钢铁外均有盈利,今年上半年,京唐钢铁亏损近20亿元。