立式加工中心主轴部件设计说明

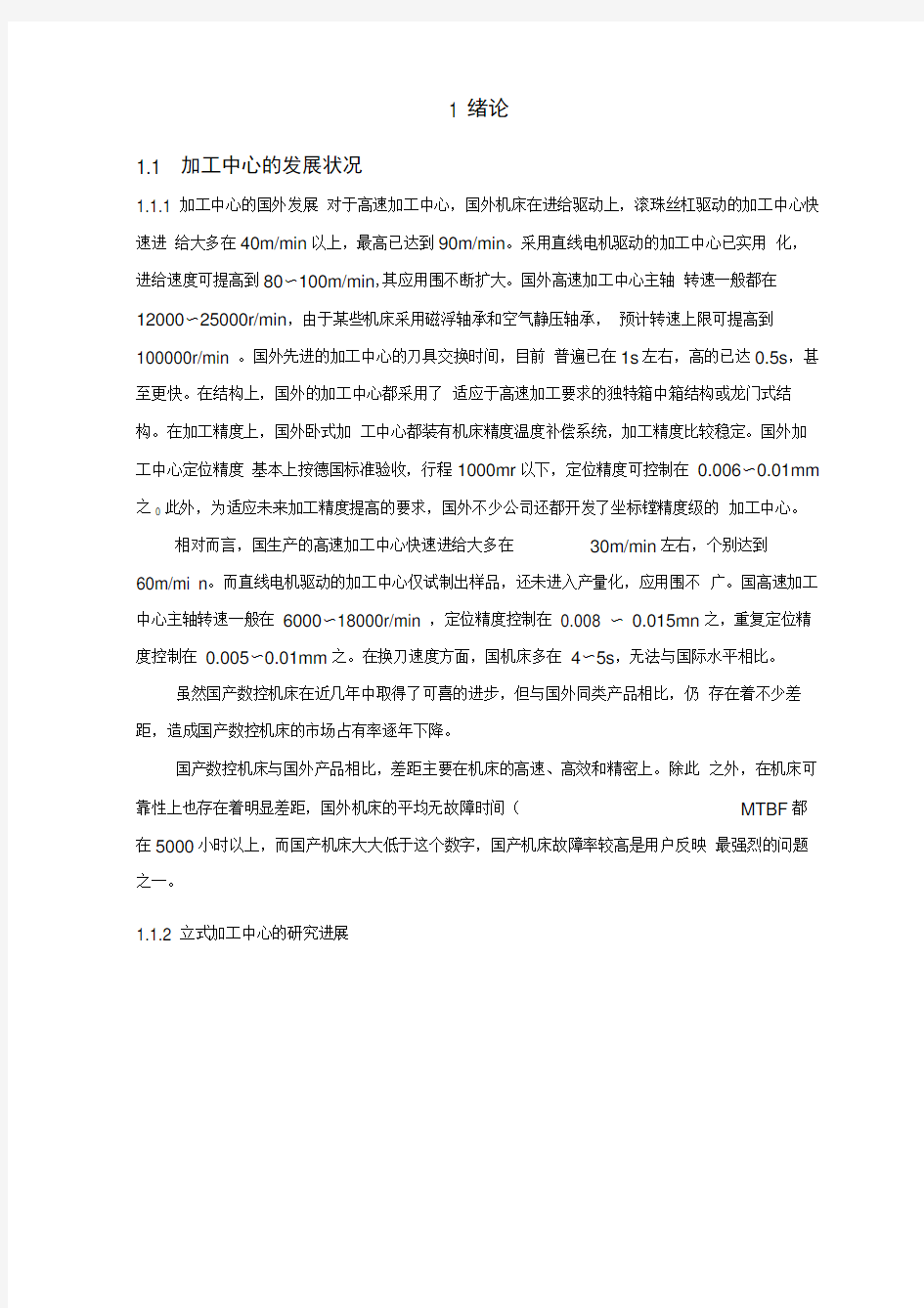
引言
装备工业的技术水平和现代化程度决定着整个国民经济的水平和现代化程度, 数控技术及装备是发展高新技术产业和尖端工业(如:信息技术及其产业,生物技术及其产业,航空、航天等国防工业产业)的使能技术和最基本的装备。制造技术和装备是人类生产活动的最基本的生产资料,而数控技术则是当今先进制造技术和装备最核心的技术。当今世界各国制造业广泛采用数控技术,以提高制造能力和水平,提高对动态多变市场的适应能力和竞争能力。此外世界上各工业发达国家还将数控技术及数控装备列为国家的战略物资,不仅采取重大措施来发展自己的数控技术及其产业,而且在“高精尖”数控关键技术和装备方面对我国实行封锁和限制政
卒
策。
数控机床技术的发展自1953年美国研制出第一台三坐标方式升降台数控铣床算起,至今已有很多年历史了。20世纪90年开始,计算机技术及相关的微电子基础工业的高速发展,给数控机床的发展提供了一个良好的平台,使数控机床产业得到了高速的发展。我国数控技术研究从1958年起步,国产的第一台数控机床是第一机床厂生产的三坐标数控铣床。虽然从时间上看只比国外晚了几年,但由于种种原因,数控机床技术在我国的发展却一直落后于国际水平,到1980年我国的数控机床产量还不到700台。到90年代,我国的数控机床技术发展才得到了一个较大的提速。目前,与国外先进水平相比仍存在着较大的差距。
总之,大力发展以数控技术为核心的先进制造技术已成为世界各发达国家加速经济发展、提高综合国力和国家地位的重要途径。
1 绪论
1.1 加工中心的发展状况
1.1.1 加工中心的国外发展对于高速加工中心,国外机床在进给驱动上,滚珠丝杠驱动的加工中心快速进给大多在40m/min以上,最高已达到90m/min。采用直线电机驱动的加工中心已实用化,进给速度可提高到80?100m/min,其应用围不断扩大。国外高速加工中心主轴转速一般都在12000?25000r/min,由于某些机床采用磁浮轴承和空气静压轴承,预计转速上限可提高到100000r/min 。国外先进的加工中心的刀具交换时间,目前普遍已在1s左右,高的已达0.5s,甚至更快。在结构上,国外的加工中心都采用了适应于高速加工要求的独特箱中箱结构或龙门式结构。在加工精度上,国外卧式加工中心都装有机床精度温度补偿系统,加工精度比较稳定。国外加工中心定位精度基本上按德国标准验收,行程1000mr以下,定位精度可控制在0.006?0.01mm 之0 此外,为适应未来加工精度提高的要求,国外不少公司还都开发了坐标镗精度级的加工中心。
相对而言,国生产的高速加工中心快速进给大多在30m/min左右,个别达到
60m/mi n。而直线电机驱动的加工中心仅试制出样品,还未进入产量化,应用围不广。国高速加工中心主轴转速一般在6000?18000r/min ,定位精度控制在0.008 ?0.015mn之,重复定位精度控制在0.005?0.01mm之。在换刀速度方面,国机床多在4?5s,无法与国际水平相比。
虽然国产数控机床在近几年中取得了可喜的进步,但与国外同类产品相比,仍存在着不少差距,造成国产数控机床的市场占有率逐年下降。
国产数控机床与国外产品相比,差距主要在机床的高速、高效和精密上。除此之外,在机床可靠性上也存在着明显差距,国外机床的平均无故障时间(MTBF都在5000小时以上,而国产机床大大低于这个数字,国产机床故障率较高是用户反映最强烈的问题之一。
1.1.2 立式加工中心的研究进展
图1-1立式加工中心结构图
1-切削箱2-X轴伺服电机3-Z轴伺服电机4-主轴电机
5-主轴箱6-刀库7-数控柜8-操纵面板
9-驱动电柜10-工作台11-滑座12-立柱
13-床身14-冷却水箱15-间歇润滑油箱16-机械手
典型加工中心的机械结构主要有基础支承件、加工中心主轴系统、进给传动系统、工作台交换系统、回转工作台、刀库及自动换刀装置以及其他机械功能部件组成。图1-1所示为立式加工中心结构图。
1.2课题的目的及容
力卩工中心是典型的集高新技术于一体的机械加工设备,它的发展代表了一个国家设计、制造的水平,因此在国外企业界都受到高度重视。
毕业设计的基本数据:
1、工作台尺寸:600mm< 400mm最大承载:600kg
2、主轴功率: 3.5 - 5KW;主轴转速:20 - 3000rpm
3、进给速度:X、丫向1 - 10000mm/min ;Z向1 - 5000mm/min
4、行程:X、丫向、Z向:600mn< 400mn< 400mm
5、定位精度:土0.025mm 重复精度:土0.01mm
&圆盘式刀库:10个刀位,换刀时间为6秒
1.3 课题拟解决的关键问题
各类机床对其主轴组件和进给组件的要求,主要是精度问题,就是要保证机床在一定的载荷与转速下,组件能带动工件或刀具精确地、稳定地绕其轴心旋转,并长期地保持这一性能。主轴组件和进给组件的设计和制造,都是围绕着解决这个基本问题出发的。为了达到相应的精度要求,通常,主轴组件和进给组件应符合以下几点设计要求:
1、旋转精度高,保证加工零件的几何精度和表面粗糙度。
2、在允许的条件下,尽量提高刚度值。使主轴组件和进给组件在外力的作用下,仍能保持一定工作精度的能力。
3、提高抗振性,保证切削过程中的平稳运转。
4、控制温升,避免热变形,防止温度过高会改变轴承等元件的间隙、破坏润滑条件,加速磨损,影响加工精度。
5、保证耐磨性,以保持其原始精度的能力。
2 加工中心机械系统方案拟定
2.1 加工中心主轴组件的组成主轴组件是由主轴、主轴支承、装在主轴上的传动件和密封件等组成的。主轴的启动、停止和变速等均由数控系统控制,并通过装在主轴上的刀具参与切削运动,是切削加工的功率输出部件。主轴是加工中心的关键部件,其结构的好坏对加工中心的性能有很大的影响,它决定着加工中心的切削性能、动态刚度、加工精度等。主轴部刀具自动夹紧机构是自动刀具交换装置的组成部分。
2.2 机械系统方案的确定
2.2.1 主轴传动机构对于现在的机床主轴传动机构来说,主要分为齿轮传动和同步带传动。齿轮传
动是机械传动中最重要的传动之一,应用普遍,类型较多,适应性广。
其传递的功率可达近十万千瓦,圆周速度可达200m/s,效率可达0.99。齿轮传动大多数为传动比固定的传动,少数为有级变速传动。但是齿轮传动的制造及安装精度要求高,价格较贵,且不宜用于传动距离过大的场合。
同步带是啮合传动中唯一一种不需要润滑的传动方式。在啮合传动中,它的结构最简单,制造最容易,最经济,弹性缓冲的能力最强,重量轻,两轴可以任意布置,噪声低。它的带由专业厂商生产,带轮自行设计制造,它在远距离、多轴传动时比较经济。同步带传动时的线速度可达50m/s (有时允许达100m/s),传动功率可达300kw,传动比可达10 (有时允许达20),传动效率可达0.98。
同步带传动的优点是:
无滑动,能保证固定的传动比;预紧力较小,轴和轴承上所受的载荷小;带的厚度小,单位长度的质量小,故允许的线速度较高;带的柔性好,故所用带轮的直径可以较小。其主要缺点是安装时中心距的要求严格。
由于齿轮传动需要具备较多的润滑条件,而且为了使主轴能够达到一定的旋转精度,必须选择较好的工作环境,以防止外界杂物侵入。而同步带传动则避免了这些状况,并且传动效率和传动比等都能符合课题的要求,故在本课题的主轴传动方
式中选择同步带传动。
2.3 加工中心主轴组件总体设计方案的确定
综合2.1 ,2.2 节中的方案,本课题的总体设计方案现确定如下:
由于同步带无滑动,能保证固定的传动比,且传动效率高,允许的线速度较高,无需安置
在很良好的工作环境中,所以在主轴传动方式中选择同步带传动。但是需要注意的是同步带的安装
具有严格的要求。
在主轴的进给运动中,采用滚珠丝杠。其耐磨性好、磨损小,低速运行时无爬
行、无振动,能够很好地确保Z轴的进给精度。
由于加工中心具备自动换刀功能,所以在主轴组件中还应有主轴准停装置、刀具自动夹紧机构以及切屑清除机构。在本课题中,主轴准停机构采用磁力传感器检测定向,其不仅能够使主轴停止在调整好的位置上,而且能够检测到主轴的转速,并在加工中心的操控面板上显示出来,方便机床操作者调整转速。
在换刀过程中,刀具自动夹紧机构也是不可获缺的一部分。它控制着刀杆的松紧,使刀具在加工时能紧紧地固定在主轴上,在换刀时能轻松地卸载。本课题采用了液压缸运行的方式,通过活塞、拉杆、拉钉等一系列元件的运动来达到刀杆的松紧目的。同时,为了减少液压推力对主轴支承的磨损,在主轴的部设置了一段碟形弹簧,使活塞对拉杆的作用起到一个缓冲的作用。同时,在换刀过程中,活塞及拉杆的部将被加工成中空状。其间将通入一定的压缩空气来清除切屑。使刀杆和主轴始终具有很好的配合精度。
在伺服系统中,本课题在进给系统中选用直流伺服电动机,而在主运动系统中则选用交流伺服电动机。由于直流伺服电动机具有电刷和换向器,需要常常维修,故不适合于主运动系统中。
3主轴主运动部件的设计
3.1主轴电动机的选用
3.1.1主电机功率估算
由毕业设计任务书知主轴功率5kw
主电机功率P E£m 竺kw 5.36kw
m 0.99 50.98
式中:n m——机床主传动系统传动效率。滚珠轴承传动效率0.99,同步带传动
效率0.98
3.1.2 主电机选型
利用交流伺服系统可进行精密定位控制,可作为CN(机床、工业机器人等的执
行元件。
FANU交流主轴电机S系列从0.65kW?37kV共分13种。它的特点是转速高、输出功率大、性能可靠、精度好、振动小、噪音低,既适合于高速切削又适合于低速重切削⑸。该系列可应用在各种类型的数控机床上。根据主电机功率PE=5.36kW故本
课题选用FANU交流主轴电机6S型号。其主要技术参数如下:
额定输出功率:5.5km/h ;
最高速度:3000r/min ;
额定输出转矩:35.0N ? M
转子惯量:0.022N m s。
3.2主轴
3.2.1主轴的结构设计
主轴的主要参数是指:主轴前轴颈直径D;主轴孔径d;主轴悬伸量a和主轴支
承跨距L,见图3-1
图3-1主轴主要参数示意图
(1 )主轴轴径的确定
主轴轴径通常指主轴前轴颈的直径,其对于主轴部件刚度影响较大。加大直径
D,可减少主轴本身弯曲变形引起的主轴轴端位移和轴承弹性变形引起的轴端位移,从而提高主轴部件刚度。但加大直径受到轴承d n值的限制,同时造成相配零件
尺寸加大、制造困难、结构庞大和重量增加等,因此在满足刚度要求下应取较小值。
设计时主要用类比分析的方法来确定主轴前轴颈直径D。加工中心主轴前轴颈
直径D按主电动机功率来确定,由《现代数控机床结构设计》查得D=85mm 由于装配需要,主轴