半导体封装企业名单

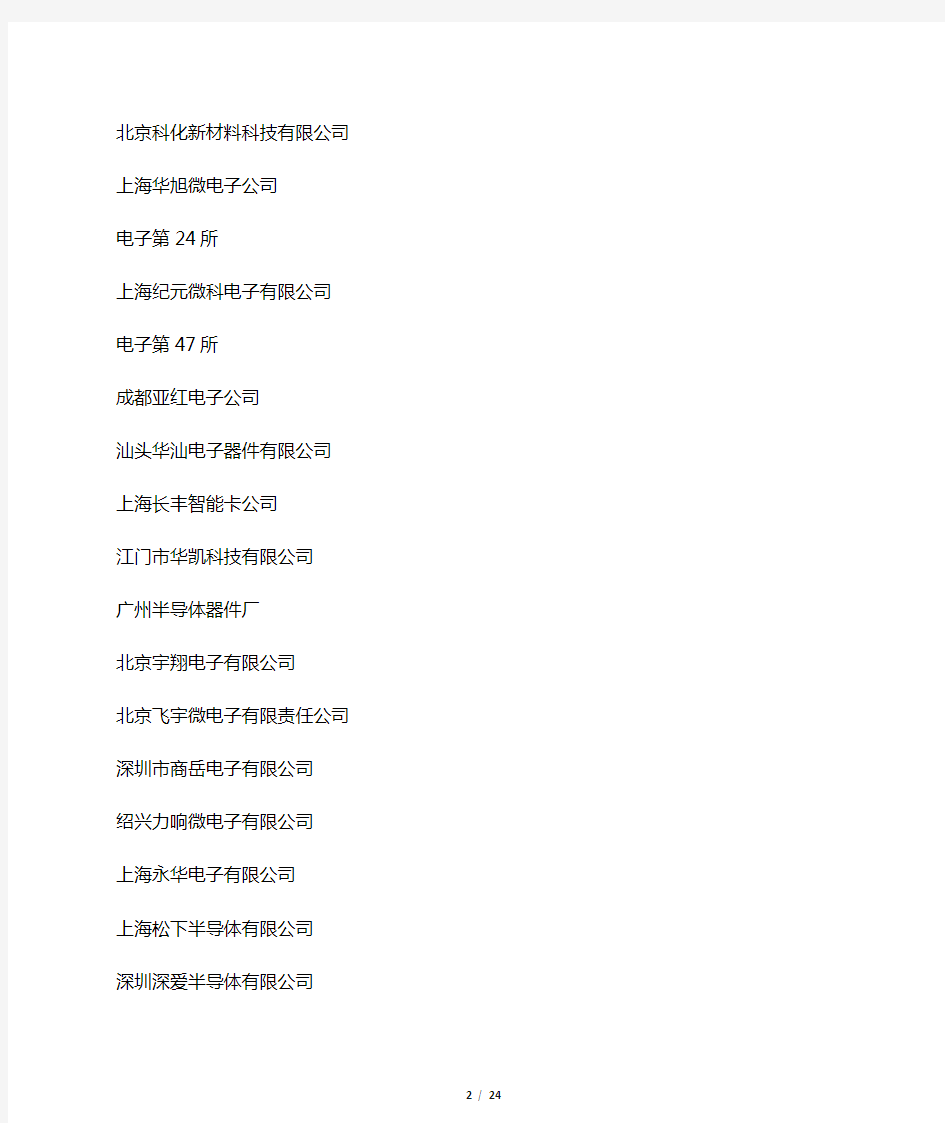
半导体封装企业名单半导体封装企业名单
中电科技集团公司第58研究所
南通富士通微电子有限公司
江苏长电科技股份有限公司
江苏中电华威电子股份有限公司
天水华天科技股份有限公司(749厂)
铜陵三佳山田科技有限公司
无锡华润安盛封装公司(华润微电子封装总厂)中国电子科技集团第13研究所
乐山无线电股份公司
上海柏斯高模具有限公司
浙江华越芯装电子股份有限公司
航天771所
新科-金朋(上海)有限公司
江苏宜兴电子器件总厂
浙江东盛集成电路元件有限公司
北京科化新材料科技有限公司
上海华旭微电子公司
电子第24所
上海纪元微科电子有限公司
电子第47所
成都亚红电子公司
汕头华汕电子器件有限公司上海长丰智能卡公司
江门市华凯科技有限公司
广州半导体器件厂
北京宇翔电子有限公司
北京飞宇微电子有限责任公司深圳市商岳电子有限公司
绍兴力响微电子有限公司
上海永华电子有限公司
上海松下半导体有限公司
深圳深爱半导体有限公司
广东粤晶高科股份有限公司江苏泰兴市晶体管厂
无锡KEC半导体有限公司
捷敏电子(上海)有限公司星球电子有限公司
强茂电子(无锡)有限公司
万立电子(无锡)有限公司
江苏扬州晶来半导体集团
晶辉电子有限公司
济南晶恒有限责任公司(济南半导体总厂)无锡市无线电元件四厂
北京半导体器件五厂
吴江巨丰电子有限公司
苏州半导体总厂有限公司
快捷半导体(苏州)有限公司
无锡红光微电子有限公司
福建闽航电子公司
电子第55所
山东诸城电子封装厂
武汉钧陵微电子封装
外壳有限责任公司
山东海阳无线电元件厂
北京京东方半导体有限公司
电子第44所
电子第40所
宁波康强电子有限公司
浙江华科电子有限公司
无锡市东川电子配件厂
厦门永红电子公司
浙江华锦微电子有限公司
昆明贵研铂业股份有限公司
洛阳铜加工集团有限责任公司
无锡市化工研究设计院
河南新乡华丹电子有限责任公司
安徽精通科技有限公司
无锡华晶利达电子有限公司
电子第43所
中国电子科技集团2所
长沙韶光微电子总公司
上海新阳电子化学有限公司
无锡华友微电子有限公司
均强机械(苏州)有限公司
东和半导体设备(上海)有限公司
复旦大学高分子科学系
清华大学材料科学与工程研究院
哈尔滨工业大学微电子中心
清华大学微电子所电子技术标准化所(4所)信息产业部
电子5所
中科院电子研究所
先进晶园集成电路(上海)有限公司
东辉电子工业(深圳)有限公司半导体工艺设备技术系列讲座清洗技术
半导体工艺设备技术系列讲座清洗技术
控制LSI良率和可靠性关键在于芯片的地损伤化和适应新材料需求。
由于新应用的问世,在以往的批处理的方式的清洗工艺基础上正在加速引入单个圆片清洗方式。
LSI制造工艺里的微粒,金属和有机物构成的器件污染危害非常严重,可使LSI电路产品的良率和可靠性下降,因此,在每一工艺流程环节里多要清除掉付着在硅圆片上的污染物。防止把污染代到下一到工序。由于清除硅圆片污染物的工艺。正是本文将要介绍的半导体清洗工艺。半导体清洗工艺是LSI制造工艺全部过程成中不可缺少的工艺流程,该道工序利用次数约占全部工序利用次数的20%- 25%,使用频度相当高,下图
图1*清洗是大规模集成电路制造过程里不可缺少的工艺环节
清洗工艺是与大规模集成电路制造工艺精密相关的必要工艺,清洗工序利用率在全部制造工序里很高,清晰工序的利用次数约占全部工序利用次数的20%-50%
随着LSI工艺技术向精细化方向迈进,硅圆片清洗工艺的重要性比以往更为突出。虽然在设计线LSI电路是允许少许的污染物存在,但是还是会直接影响电路的良率和可靠性,于是如何清洗这些轻微的污染物也是越来越高的技术要求,详细情况如图2所示
开始批量生产日期
(年)2013
工艺技术时代
DRAM半间距(纳
米)32硅圆片直径(毫米
允许的微粒最大直径(纳
米)
403532.528.
522.52017.516
允许的微粒数量.
每平方厘米基板表面允许的金属原子数量(10的10次方)个0.50.
50.50.
50.50.
50.50.5
0.5
背面的微粒直径(微
米)
0.20.
160.160.
160.160.
140.14
0.140.14
硅氧化膜和硅氧化膜削减(纳
米)
0.80.
70.50.
40.40.
40.40.4
0.4
图2在半导体精细化的过程里对清洗技术要求很高。
随着半导体工艺技术向精细化方向迈进,轻微的污染多影响大规模集成电路的良率和可靠性。图2的内容根据国际半导体技术指南的(ITRS)数据
本文将先说明硅圆片清洗的基本原理,然后介绍LSI精细化带来的新技术课题,最后介绍的技术开发现状。
以不同的药水清洗4种不同的污染物
附着在硅圆片上成为LSI电路污染源的物质,大体上有以下4中:
微粒,自然氧化物,金属和有机物。用于清楚这些污染物的标准方法是“RCA清洗”方法,他是利用高纯度的纯净(去离子)水和药水。把附着在硅圆片上的污染物分离开来或溶解之后实现清楚的方法。半导体清洗的基本概念从1970年开始有美国无限电公司(RCA)的W.Kern先生倡导.
RCA清洗工艺技术的特点在于按照应该被清除的污染物种类选用相应的清洗药水,按照顺序进行不同的药水的清洗工艺,就可以清除掉所有附着在硅圆片上的各种污染物。根据对应的污染物种类,在清洗工艺里(图3)大体上使用以下4种药水1氨水和过氧化氢以及纯水的混合液简称AOM (ammonia peroxide mixture), 2氟酸和纯水的混合液,也叫做稀释的氢氟酸DHF(dilutedHF) 3硫酸和过氧化氢的混合液简称4盐酸和过氧化氢以及纯水的混合液简称SPM (sulfuricperoxide mixture); 4 HPM (hydrochloric peroxide mixture ).
用药水清洗之所以能提高LSI。电路的良率,关键在于正确地运用干燥方法处理清洗后的硅圆片。若没有从清洗后的硅圆片上完全把残余的药水除掉,则它容易成为新的污染,因此,结合清洗方式和清洗对对象,选取最佳的干燥方式是十分重要的。
药水名称分子结构清洗温度(°c)清除的对象
APMNH4OH/H2O2/H2O20︿﹀80微粒/有机物
DHF/H2O20︿﹀25氧化膜
SPMH2SO2/H2O280︿﹀150金属/有机物
HPMHCI/H2O2/H2O20︿﹀80金属
图3根据要清除的对象分别使用相应的清洗药水。
在RCA清洗工艺清里,按照不同的药水的清洗工艺顺序进行清洗,就可以把所有附着在硅圆片上的各种污染物清除掉
利用药水和超声波清除微粒
当清除附着在硅圆片的微粒时,使用APM药水,参阅图4所示。按照以下工艺流程进行操作:
首先,由作为强氧化剂的过氧化氢把硅圆片的表面氧化,形成薄的二氧化硅膜;随后,由NH4OH对进行二氧化硅膜蚀刻;通过这种措施把微粒从硅圆片表面上剥离开来。同时由强氧化剂过氧化氢把硅膜氧化,形成二氧化硅。因为这层薄膜上不能在附着微粒,所以它是硅圆片表面的保护膜,具备可防止污染物附着的作用,在包含有NH4OH的碱性溶液里,被清除的微粒和二氧化硅膜都带有同样的电位,相互排斥,不可能在相互吸附。
在用APM构成的清除微粒的工艺流程里,利用由超生波构成的物理清洗作用强化了由药水构成的化学清洗作用,这是因为,药水一受到超声波的振动便产生气泡,气泡破裂之时产生的冲击力可把微粒从硅圆片上剥离开来,从而强化了清洗作用。
图4利用硅圆片表面氧化和蚀刻工艺方法清除微粒
当清除附着在硅圆片表面的微粒时,使用作为氨水和过氧化氢以及纯水APM混合液的药水进行清洗
用氢氟酸清除自然氧化物
对于硅圆片表面的自然氧化物,可用稀释氢氟酸的药水清洗掉,作为强酸的氢氟酸,利用它能溶解二氧化硅的作用,可清除自然氧化膜,详细情况如图5所示
在利用稀释的氢氟酸清洗硅圆片的工艺流程里,将会产生一种在使用其他的3种药水实现清洗都不会发生的独特问题,当对清洗后的硅圆片进行干燥时,在硅圆片表面上堆积一种叫做水痕的(water mark)二氧化硅水合物(SIO2-
nH2O)请参阅图6所示,这种水痕会防碍后续工艺,结果导致产品的良率降低,因此,在使用稀释的氢氟酸清洗硅圆片的工艺流程里,要特别主意当进行干燥时必须采取措施(下文里有介绍)千万不可出现水痕迹现象。
在使用稀释的氢氟酸清洗过程之中之所以产生水痕,是因为干燥清洗后的硅圆片很容易使纯水滴残留在硅圆片上,而水滴里溶解的氧气侵蚀硅表面,致使在疏水性的硅圆片表面干燥后呈现出水痕斑斑的难堪景象,相比之下其他3种药水里多含有过氧化氢,使硅圆片表面被氧,由于被具有亲水性的二氧化硅覆盖。于是纯水不容易残留。也就没有图6所示的生成水痕的机制。所以根本不会产生水痕迹现象。
以强酸清除金属和有机物
对于硅圆片上附着的金属可以利用SPM和HPM药书清除。参阅图7所示。利用SPM药水中的硫酸和HPM药水种的盐酸各自所具有的强氧化能力,可把金属溶解在药水里进行清除。
在利用SPM和HPM进行清洗的工艺过程中,控制药水进行清洗的工艺流程中,控制药水的氢离子浓度(Ph)和还原电位是最重要的,因为根据Ph值和氧化还原电位值才能决定金属正处于那种状态氧化还原电位已变成表征药水具有把金属氧化或还原能力的指标,冽
如药水的(Ph)值,在SPM药水里是由硫酸(在HPM药水由盐酸)的浓度控制的而氧化还原电位是由上述药水的酸浓度和过氧化氢的浓度两种浓度控制的,
当要清除附着在硅圆片上的有机物时,必须要使用一种含有硫酸和过氧化氢而且还要具备分解有机物能力的SPM药水,详细情况请参阅图8所示。成为大规模集成电路污染原因的最具代表性有机物,正是在光刻曝光工艺里使用的感光胶。当经过这一工艺流程之后。虽然利用O2等离子实现消除的清除感光胶
工艺处理。但是往往都有残存的感光胶。在这种情况下,为了清除残存的赶感光胶有机物,就需要通过更强的氧化能力的高温硫酸处理,使碳原子氧化,变成二氧化碳之后被清除掉。
ˉ图5利用氢氟酸清楚自然氧化膜。
在硅圆片表面上生成的自然氧化膜,可利用稀释的氢氟酸(DHF)进行清除,因为,作为强酸的氢氟酸(HF)可把二氧化硅膜溶解掉
图10关键在于适应铜/低介电常数值膜等新材料需求进行新技术开发
由于布线工艺里引入铜/低介电常数值膜等新材料,对应新材料的清洗工艺开发就变的越来越重要。
图11在物理损伤里的实例是微细图形遭到破坏。
对于线条精细且纵横比大的图形由于仅仅受到超声波振动的轻微力作用,便容易被破坏,图12采用二流体清洗技术缓解物理损伤。
由喷嘴喷射出的氮气流和药水雾滴流冲向硅圆片表面并沿着圆片的径向扫描,同时硅圆片不停地旋转,于是硅圆片获得均匀而又全面地清洗,这样地清洗方式,不损伤硅圆片表面地图形,图13隔绝氧气之后可防止产生水痕现象。
在利用氮气地干燥工艺过程中,由于硅圆片周围处于受氮气包围地低氧状态,即使是硅圆片表面具有疏水性也不容易产生水痕现象。
图14利用臭氧水处理以后地硅圆片表面适合以原子层沉积法ALD生成绝缘膜。
因为用稀薄地臭氧水处理以后,在硅圆片表面覆盖有OH原子团,使得利用ALD方法生成High-k值绝缘膜成为可能
新课题日益增多
随着大规模集成电路工艺技术的精细化,近年来,清洗工艺领域已经开始出现许多新技术,请参图9和图10,这些新技术课题大体上可以分为以下4类
1降低物理损伤2减少由蚀刻工艺导致对二氧化硅膜层的侵蚀程度,3采用对纵横不大的结构4运用新材料
1关于减少物理损伤问题,主要时清除附着在硅圆片上的微粒时应该超声波清洗所面临的课题。
因为在设计线宽小的大规模集成电路的细线条图形十分脆弱,超声波的轻微振动力足以使之遭受破坏,参阅图11所示,尤其使加工尺寸小的晶体管栅机部位更成问题,要解决这一问题,必须研究超声波清洗工艺的低损伤或者寻求取代超声波清洗的新工艺。
2关于减少对二氧化硫硅膜的侵蚀问题,它是利用APM药水清除微粒使所要研究的新课题,所谓二氧化硅膜遭受到侵蚀的问题。实际上是硅圆片表面氧化和过渡蚀刻所导致的二氧化硅膜遭到削薄的现象,这种现象对于具有厚氧化层的部位并不成问题,但是,在晶体管的源、漏区域或栅极测壁的间隔层等部位却是严重的问题,特别使在晶体管源、漏区域内里形成超浅结
USJ(ultrashallow,junction)的二氧化硅膜的遭到削薄,纳正是晶体管性能降低的原因。这可能把离子注入工艺流程里的杂质原子的一部分液被削减的技术对策,必须优化NH4OH和H2O2的混合比或者是药水的温度,
分别采用High—k值和Low—k值材料
3关于采用纵横比大的结构,这个问题不分清洗药液水种类,他是所有清洗工艺共同面临新研究课题,特别是,在纵横比大的接触孔(contact hole )清洗工艺过程里,药水很难波及到孔内各个角落,非常容易残留污染,而且,当清洗完成之后进行干燥工艺处理时,很难把药水从接触孔里完全排除,在硅圆片上混杂有疏水性和亲水性表面区域里将会发生水痕的现象,为了解决这些研究课题,必须改进清洗和干燥工艺技术,当进行干燥工艺处理时,采取利用异丙醇方式等。
4关于采用新材料,这也时全体清洗工艺所面临的新研究课题,冽如,晶体管制造工艺里的清洗工艺才用的栅极绝缘膜时高介电常数(high-k)值材料,而遇到的栅极的电极又是金属材料,对于布线工艺里的清洗处理,它应当适应铜材料和低介质电常数(low-k)值材料的需求,以往的清洗药水对于新材料可能适用也
可能具有腐蚀性,所以必须研究新的清洗用的药水。目前,面向晶体管制造工艺的清洗药水已有实用化的方案,即利用把金属变成络合物之后溶解在药水里的整合剂或界面激活剂,而面向布线工艺的清洗药水,也开发出了清洗药水,力图取代无机清洗药水,对应课题的新技术开发
接下来,将介绍对应课题的新技术开发;1二流体清洗方法。2利用氮气保护的干燥技术,3用稀薄臭氧水的表面处理技术。1
1二流体清洗方法是在清除微粒过程中抑制物理损伤的技术方法。详细情况如图12所示,顾名思义,它是利用氮气流和在氮气流中把药水物化形成的流体,进行的清洗技术方法,这种二流清洗技术全面。它既有以往清洗方式里的(APM)化学清洗作用而且又具备采用超声波技术的物理清洗作用。关于二流体清洗方法使用要领如下;首先,使用Ph值高的药水可以控制使微粒足以付着在硅圆片上的静电引力,可很好的实现化学清洗作用。其次,在氮气流中加速药水雾化,时投向硅圆片的药水雾滴破裂时产生涡流把附着的微粒清除掉,正确地进行物理清洗,最后,在化学和物理地清洗基础之上。利用氮气流和高速旋转硅圆片产生地离心力可把残存地药水膜清除干净。
2利用氮气保护的干燥技术是防止成生水痕的新技术,特别是在纵横不大地结构里容易发生水痕可以用这种方法克服,所谓利用氮气保护地干燥方法,它是把清洗后的硅圆片进行干燥处理时,在清洗用水里采用防止氧气溶解地措施,从而控制产生水痕,当对硅圆片进行干燥处理时,时它同氧气隔绝并同时采取氮气保护措施,详细情况请参阅图13所示。由于硅圆片周围处于氮气地包围下地低氧状态。即使是硅圆片表面具有疏水性也因为缺少氧气而很难发生水痕现象。3用稀薄臭氧水地表面处理技术,它对利用原子层沉积ALD (atomic layer deposition )方法在硅圆片上生成高介电常数(high-k)值绝缘膜时时必须具备地技术,由于使用稀薄地臭氧水清洗后的硅圆片表面被OH原子团覆盖,使得用ALD方法可堆积每个原子层厚度地高介电常数(high-k)值绝缘膜,具体情况如图14所示,因为,仅仅是通过稀释地氢氟酸DHF清除过氧化膜的硅圆片上是不能用ALD方法生成绝缘膜的。
加速普及单个圆片清洗方式
最后,作为有关清洗工艺的最新技术动向,介绍单个圆片清洗技术,
在现在的清洗工艺技术里,采取的是把多个硅圆片汇聚起来进行清洗的批处理方式,这种清洗方式同逐个对单个硅圆片进行清洗的方式相比,优点是清洗处理吞吐量大而且拥有成本低(lowcostof ownership ),这正是它成为主流清洗工艺的主要原因。然而,单个硅圆片清洗方式比多个硅圆片一起进行批处理方式优越之处在于很少有交叉污染,只是(cross contamination )它的应用依局限于厚的二氧化硅膜剥离和硅圆片背面清洗以及硅圆片研磨后的清洗工艺等领域。
不过最近,单个圆片清洗工艺的应用领域开始扩大,曾经批量生产逻辑LSI 电路产品的企业也开始积极地引入单个圆片清洗工艺技术,以铜/低介电常数值材料布线工艺里地需要为转机,是单个硅圆片清洗技术迅速发展。在小规模生产和短生产周期TAT (turn aound time )化地需求下,晶体管制造工艺里也开始引入单个硅圆片清洗技术,今后,推广普及单个硅圆片清洗技术依需要研究很多地课题,诸如通过缩短每个硅圆片地处理时间,选择清洗药水,以及化学和物理清洗并用等措施,力图提高单个硅圆片清洗技术处理吞吐量
晶圆测试
晶圆测试
在晶圆制造完成之后,是一步非常重要的测试。这步测试是晶圆生产过程的成绩单。在测试过程中,每一个芯片的电性能力和电路机能都被检测到。晶圆测试也就是芯片测试(die sort)或晶圆电测(wafer sort)。
在测试时,晶圆被固定在真空吸力的卡盘上,并与很薄的探针电测器对准,同时探针与芯片的每一个焊接垫相接触(图
4.18)。电测器在电源的驱动下测试电路并记录下结果。测试的数量、顺序和类型由计算机程序控制。测试机是自动化的,所以在探针电测器与第一片晶圆对准后(人工对准或使用自动视觉系统)的测试工作无须操作员的辅助。
测试是为了以下三个目标。第一,在晶圆送到封装工厂之前,鉴别出合格的芯片。第二,器件/电路的电性参数进行特性评估。工程师们需要监测参数的分布状态来保持工艺的质量水平。第三,芯片的合格品与不良品的核算会给晶圆生产人员提供全面业绩的反馈。合格芯片与不良品在晶圆上的位置在计算机上以晶圆图的形式记录下来。从前的旧式技术在不良品芯片上涂下一墨点。
晶圆测试是主要的芯片良品率统计方法之一。随着芯片的面积增大和密度提高使得晶圆测试的费用越来越大。2这样一来,芯片需要更长的测试时间以及更加精密复杂的电源、机械装置和计算机系统来执行测试工作和监控测试结果。视觉检查系统也是随着芯片尺寸扩大而更加精密和昂贵。芯片的设计人员被要求将测试模式引入存储阵列。测试的设计人员在探索如何将测试流程更加简化而有效,例如在芯片参数评估合格后使用简化的测试程序,另外也可以隔行测试晶圆上的芯片,或者同时进行多个芯片的测试。晶圆的测试良品率在第六章具体讲述。IC制造中的危害和预防
IC制造中的危害和预防
顾爱军范钦文(中国电子集团公司第58研究所,江苏无锡214035)
摘要:
本文论述了关于IC制造中使用的工艺气体和厂房设施,、生产设备的危害及防护。
中图分类号:
TN405文献标识码:A1前言
IC制造业是“印钞票的机器”,但也是高风险的行业。因为在IC制造过程中要使用大量的高毒性、腐蚀性、易燃易爆等特种工艺气体,还有可燃性塑料(火灾的重大隐患)。只有做好相应的安全管理工作,才能使这个行业产生巨大的利润。
2 IC制造中的危害和预防
2.1特种工艺气体的危害及防护
IC制造中所用的特种气体大多以液化压缩填充于钢瓶内,压缩气体是一种能量储存方式,具有潜在的释放危险,所以气瓶都必须牢固放置,严禁跌倒。气瓶一般放置于气瓶柜内,气瓶柜要防止气体泄漏时不至于因压力过大而失去阻隔功能,要有足够的排风量,淋水消防设备,在钢瓶上要装置限流孔。气瓶柜是放置在气瓶房内,其位置可在建筑物内、靠近建筑物、或远离建筑物15
米。如果气瓶房在建筑物内或靠近建筑物,必须与室外变电站分开,根据距离远近决定保护程度,内墙应有两小时的防火墙,所有门至少是1小时30分钟防火等级及自动关闭的门。
气体按其危险性分类可分为:
不可燃气体、可燃气体、有毒气体、腐蚀性气体、氧化性气体、低温气体,下面就分别介绍其危险性和防护。
2.1.1不可燃气体
不可燃气体有N
2、Ar、He等,它们具有窒息性,即取代肺中的氧气后能让人窒息而死。当氧气被其他气体所取代后,在不同的氧气含量的情况下,对人体造成的危害如下:
●19.5%人类正常生活所需要的最低氧气浓度极限。
●15-
19.5%工作能力下降,冠状动脉,肺部和循环系统出现先期症状。
●12-14%呼吸,脉搏加快,渐渐失去知觉。
●10-12%呼吸,脉搏进一步加快,丧失判断能力,嘴唇发紫。
●8-10%无意识,呕吐。●6-8%8分钟死亡率100%,6分钟死亡率50%,4-5分钟尚可恢复。
●4%40秒钟内昏迷,抽搐,停止呼吸,直至死亡。
缺氧的急救措施:
绝对不要不带呼吸器就冲进缺氧区域。
有人认为:
我可以尽量摒住呼吸,冲进缺氧区域把伤员救出来。
事实上:
不可以!!!!1 50%这样做的人会因此而丧命。
对不可燃气体要进行的危险防护有:
(a)保证空气的流动,配备排风。
(b)按正确的操作流程对钢瓶操作。
(c)监测氧气浓度。
(d)配备个人防护系统。
(e)不可以一人单独工作。
2.1.2可燃气体
可燃气体有C2H
2、H
2、CH
4、SIH
4、PH
3、NH3等,它们具有窒息性,可燃性,其中有些气体如H
2、CH
4、SIH
4、PH3还具有爆炸的可能性。硅烷和空气混合,在室温下就会引燃。FMRC 测试结果显示,自燃发生在开始泄漏时或流量被关闭时。通常是
6.35mm直径的管路,压力在100至300psi左右当管内压力减至50psi时开始燃烧。对可燃气体要进行的危险防护有:
(a)保证空气的流动,配备排风。
(b)正确的钢瓶操作流程。
(c)使用防爆设备。
(d)避免任何火花产生的可能。
2.1.3有毒气体
有毒气体有AsH
3、PH
3、COCL2等,它们的毒性对身体有害,有的可能造成人员中毒死亡。中毒途径有吸人、吸收(通过皮肤)、吞食、注射(通过伤口)。对有毒气体的危险防护有:
(a)提供排风系统。
(b)正确操作气瓶。
(c)毒气监测系统。
(d)配备适当的个人装备。
(e)相关知识的培训。
2.1.4腐蚀性气体
腐蚀性气体可分为低腐蚀性气体如H
F、BCL
3、SICL4和高腐蚀性气体如HCL、
BF3、二氯甲烷(DCS)、三氯甲烷(TCS)及三氯化氯(CLF3)等,它们具有摧毁人的生理组织以及腐蚀设备的危害。
由于DCS及TCS的蒸气压很低,不能长距离传送,加热管路或钢瓶可增加传送距离。加热设备应有高温隔断装置,过流量隔断阀或按钮及远处隔断装置可提供紧急隔断功能,DCS钢瓶若是碳钢制则使用期限不超过一年。三氟化氯气瓶应与其他气瓶分开,气瓶柜内要有紧急关断装置,注意千万不可装淋水头,因为泄漏气体会与水反应形成爆炸性物质。如果温度超过
450、则用镍材质管路,管路应使用双重套管,外层管应用氮气测漏装置,二氧化氯侦测器用来侦测三氟化氯气体的泄漏。对腐蚀性气体要进行的危险防护有:
(a)提供排风系统。
(b)正确操作气瓶。
(c)采用相容的原材料。
(d)降低含水量。
(e)配备适当的个人防护设备。
2.1.5氧化性气体
氧化性气体有O
2、N20等。它们具有助燃性、高反应性。当含氧量等于或高于
23.5%时,燃烧特性发生改变:
可燃范围增大、自然温度下降。即通常不会燃烧的物质在高氧环境会燃烧;通常会燃烧的物质在高氧环境会极易燃烧,且燃烧速度极快。曾有实验证明,含氧量过高的衣物是极为危险的,只要有引燃点就会爆炸。所以从高氧环境下出来的人员、物品必须与引燃点隔离;并用新鲜空气吹至少30分钟;有关人员应及时更换衣服。
因此对氧化性气体的危险防护有
(a)提供排风系统。
(b)正确操作气瓶。
(c)使用相容的原料。
(d)避免引燃点。
(e)确认系统经过适当的清洗。
2.1.6低温气体
低温液体是指在常压下沸点低于-240,例如:
液氧、液氩、液氮、液氢、液氦。它们的低温可能会引起冻伤,以及引起周围物品的损伤危险,包括过冷、过大的体积膨胀、雾。对低温液体的危险防护有:
(a)提供排风系统。
(b)正确操作气瓶。
(c)正确的系统设计。
(d)适当的个人防护设备。
2.2厂房设施、生产设备的危害
2.2.1排风管
排风管可能将热和火焰吸人,会把排风管内一些可燃性液体(如光刻胶、真空泵油)或硅烷粉末点燃,排风管材料本身就是可燃物,当温度超过其燃点时,会造成管路断裂而使烟四处蔓延。
2.2.2湿法腐蚀槽
湿腐槽是由聚丙烯(PP)、不易燃聚丙烯(FRPP)、聚氯乙烯等是耐腐塑料制作而成,湿法腐蚀设备内含有大量的电路装置,是潜在的引火源。如果在净化间的空调和排风系统无法正常工作时,大量的热和烟流动造成的危害将比火灾产生的影响还大。
2.2.3离子注入机
注人机设备是高电压大电流设备,还有剧毒物质,极易造成对人伤害、设备危害及火灾。在人员方面,因设备接地不好或对电器设备不做上锁/开锁(Lock out/tag out)表示及过电流保护,造成人与高电压接触而产生触电,轻则受伤,重则造成生命危险。剧毒性气体使用不当,也是会造成人员伤亡。高压放电会对精密的电气装置造成破坏。油式的高压变压器因其高电流破坏绝缘造成绝缘油(矿物油)燃烧,甚至造成绝缘油泄漏而燃烧的问题,为减少危险可把变压器更换成千式的变压器。
2.2.4光刻机
光刻机使用了激光技术,一般用于对焦、对位、硅片传送等精密控制系统。根据美国USHA21CFR1040:10&
1041.11FDA激光产品及NFPAEl
36.1美国激光安全标准,这些激光可分为Classl,Class2,Class3a,Class3b及Class4,其中CLss4危害眼睛等级最高,因此就必须考虑对人员安全进行保护。另外像深紫外光等强光,也需要有防护装置,在深亚微米微曝技术变革中使用了较高电压CYMER激光,其激光等级是Class4及Class3b,还使用高毒性的氟气体,为此我们必须高度重视。
2.2.5涂胶显影轨道
光刻胶、显影液等化学试剂和纯水的泄漏会对人员和设备造成危害。从TEL 公司的统计数字来看,人为失误占总灾害间接原因最高,约2/3。在更换HMDS的过滤器时接地良好,避免飞溅的液体引起火灾。
2.2.6炉管
氧化炉管其风险来自气体泄漏、火灾爆炸、高电压设施及地震。因其设备使用自燃性硅烷,不当操作阀门则会引起大量硅烷从排风管流出。另外因不当化学物质混合,引起化学物质在炉管内爆炸。另因炉管的高度,因此在强烈地震时,若无良好的固定防止倾倒设计,在地震时,具有较高风险。
国内封测厂一览表
国内封测厂一览表 类型地点封测厂名备注 外商上海市英特尔(Intel)英特尔独资 外商上海市安可(AmKor)安可独资 外商上海市金朋(ChipPAC)星科金朋(STATSChippac) (原为现代电子) 外商上海市新加坡联合科技(UTAC)联合科技独资 外商江苏省苏州市飞利浦(Philips)飞利浦独资 外商江苏省苏州市三星电子(Samsung)三星电子独资 外商江苏省苏州市超微(AMD) Spansion 专做FLASH内存 (原为超微独资) 外商江苏省苏州市国家半导体(National Semiconductor)国家半导体独资 外商江苏省无锡市无锡开益禧半导体(KEC)韩国公司独资 外商江苏省无锡市东芝半导体(Toshiba) 1994年东芝与华晶电子合资,2002年4月收购成为旗下半导体公司,原名为华芝半导体公司 外商天津市摩托罗拉(Motorola) Freescale (原为摩托罗拉独资) 外商天津市通用半导体(General Semiconductor) General独资 外商广东省深圳市三洋半导体(蛇口)曰本三洋独资 外商广东省东莞市 ASAT ASAT LIMITED(英国)独资 外商广东省东莞市清溪三清半导体三洋半导体(香港) 外商江苏省苏州市快捷半导体(Fairchild) 合资上海市上海新康电子上海新泰新技术公司与美国siliconix公司合资 合资上海市松下半导体(Matsushita)曰本松下、松下中国及上海仪电控股各出资59%、25%、16%成立 合资上海市上海纪元微科微电子(原阿法泰克电子)泰国阿法泰克公司占51%,上海仪电控股占45%,美国微芯片公司占4%。
半导体封装测试企业名单
1 2 3 4 5 6 7 8 9 10 11 12 13 14 15 16 17 18 申报企业名称 武汉新芯集成电路制造有限公司 上海集成电路研发中心有限公司 无锡华润微电子有限公司 中国电子科技集团公司第五十五研究所 华越微电子有限公司 中国电子科技集团公司第五十八研究所 珠海南科集成电子有限公司 江苏东光微电子股份有限公司 无锡中微晶园电子有限公司 无锡华普微电子有限公司 日银IMP微电子有限公司 中电华清微电子工程中心有限公司 中纬积体电路(宁波)有限公司 深圳方正微电子有限公司 北京华润上华半导体有限公司 福建福顺微电子有限公司 北京半导体器件五厂 贵州振华风光半导体有限公司 企业类别 芯片制造 芯片制造 芯片制造 芯片制造 芯片制造 芯片制造 芯片制造 芯片制造 芯片制造 芯片制造 芯片制造 芯片制造 芯片制造 芯片制造 芯片制造 芯片制造 芯片制造 芯片制造
21 22 23 24 25 26 27 28 29 30 31 32 33 34 35 36 37 38 39 40 41 42 常州市华诚常半微电子有限公司 锦州七七七微电子有限责任公司 北京燕东微电子有限公司 河南新乡华丹电子有限责任公司 西安微电子技术研究所 长沙韶光微电子总公司 威讯联合半导体(北京)有限公司 英特尔产品(上海)有限公司 上海松下半导体有限公司 南通富士通微电子股份有限公司 瑞萨半导体(北京)有限公司 江苏长电科技股份有限公司 勤益电子(上海)有限公司 瑞萨半导体(苏州)有限公司 日月光半导体(上海)有限公司 星科金朋(上海)有限公司 威宇科技测试封装有限公司 安靠封装测试(上海)有限公司 上海凯虹电子有限公司 天水华天科技股份有限公司 飞索半导体(中国)有限公司 无锡华润安盛科技有限公司 芯片制造 芯片制造 芯片制造 芯片制造 芯片制造 芯片制造 封装 封装 封装 封装 封装 封装 封装 封装 封装 封装 封装 封装 封装 封装 封装 封装
半导体封装技术向高端演进 (从DIP、SOP、QFP、PGA、BGA到CSP再到SIP)
半导体器件有许多封装形式,按封装的外形、尺寸、结构分类可分为引脚插入型、表面贴装型和高级封装三类。从DIP、SOP、QFP、PGA、BGA到CSP再到SIP,技术指标一代比一代先进。总体说来,半导体封装经历了三次重大革新:第一次是在上世纪80年代从引脚插入式封装到表面贴片封装,它极大地提高了印刷电路板上的组装密度;第二次是在上世纪90年代球型矩阵封装的出现,满足了市场对高引脚的需求,改善了半导体器件的性能;芯片级封装、系统封装等是现在第三次革新的产物,其目的就是将封装面积减到最小。 高级封装实现封装面积最小化 芯片级封装CSP。几年之前封装本体面积与芯片面积之比通常都是几倍到几十倍,但近几年来有些公司在BGA、TSOP的基础上加以改进而使得封装本体面积与芯片面积之比逐步减小到接近1的水平,所以就在原来的封装名称下冠以芯片级封装以用来区别以前的封装。就目前来看,人们对芯片级封装还没有一个统一的定义,有的公司将封装本体面积与芯片面积之比小于2的定为CSP,而有的公司将封装本体面积与芯片面积之比小于1.4或1.2的定为CSP。目前开发应用最为广泛的是FBGA和QFN等,主要用于内存和逻辑器件。就目前来看,CSP的引脚数还不可能太多,从几十到一百多。这种高密度、小巧、扁薄的封装非常适用于设计小巧的掌上型消费类电子装置。 CSP封装具有以下特点:解决了IC裸芯片不能进行交流参数测试和老化筛选的问题;封装面积缩小到BGA的1/4至1/10;延迟时间缩到极短;CSP封装的内存颗粒不仅可以通过PCB板散热,还可以从背
面散热,且散热效率良好。就封装形式而言,它属于已有封装形式的派生品,因此可直接按照现有封装形式分为四类:框架封装形式、硬质基板封装形式、软质基板封装形式和芯片级封装。 多芯片模块MCM。20世纪80年代初发源于美国,为解决单一芯片封装集成度低和功能不够完善的问题,把多个高集成度、高性能、高可靠性的芯片,在高密度多层互联基板上组成多种多样的电子模块系统,从而出现多芯片模块系统。它是把多块裸露的IC芯片安装在一块多层高密度互连衬底上,并组装在同一个封装中。它和CSP封装一样属于已有封装形式的派生品。 多芯片模块具有以下特点:封装密度更高,电性能更好,与等效的单芯片封装相比体积更小。如果采用传统的单个芯片封装的形式分别焊接在印刷电路板上,则芯片之间布线引起的信号传输延迟就显得非常严重,尤其是在高频电路中,而此封装最大的优点就是缩短芯片之间的布线长度,从而达到缩短延迟时间、易于实现模块高速化的目的。 WLCSP。此封装不同于传统的先切割晶圆,再组装测试的做法,而是先在整片晶圆上进行封装和测试,然后再切割。它有着更明显的优势:首先是工艺大大优化,晶圆直接进入封装工序,而传统工艺在封装之前还要对晶圆进行切割、分类;所有集成电路一次封装,刻印工作直接在晶圆上进行,设备测试一次完成,有别于传统组装工艺;生产周期和成本大幅下降,芯片所需引脚数减少,提高了集成度;引脚产生的电磁干扰几乎被消除,采用此封装的内存可以支持到800MHz的频
半导体封装公司一览
目前国内大中型半导体企业一览! 我国具有规模的封测厂列表 半导体,芯片,集成电路,设计,版图,芯片,制造,工艺,制程,封装, 测,wafer,chip,ic,design,eda,process,layout,package,FA,QA,diffusion,etch,photo,i mplant,metal,cmp,lithography,fab,fables 类型地点封测厂名 外商上海市英特尔(Intel)英特尔独资 外商上海市安可(AmKor)安可独资 外商上海市金朋(ChipPAC)星科金朋(STATSChippac) (原为现代电子) 外商上海市新加坡联合科技(UTAC)联合科技独资 外商江苏省苏州市飞利浦(Philips)飞利浦独资 外商江苏省苏州市三星电子(Samsung)三星电子独资 外商江苏省苏州市超微(AMD) Spansion 专做FLASH内存 (原为超微独资) 外商江苏省苏州市国家半导体(National Semiconductor)国家半导体独资 外商江苏省苏州市快捷半导体(Fairchild) 外商江苏省无锡市无锡开益禧半导体(KEC)韩国公司独资 外商江苏省无锡市东芝半导体(Toshiba) 1994年东芝与华晶电子合资,2002年4月收购成为旗下半导体公司,原名为华芝半导体公司 外商天津市摩托罗拉(Motorola) Freescale (原为摩托罗拉独资) 外商天津市通用半导体(General Semiconductor) General独资 外商广东省深圳市三洋半导体(蛇口)曰本三洋独资 外商广东省深圳市 ASAT ASAT LIMITED(英国)独资 外商广东省东莞市清溪三清半导体三洋半导体(香港) 合资上海市上海新康电子上海新泰新技术公司与美国siliconix公司合资 合资上海市松下半导体(Matsushita)曰本松下、松下中国及上海仪电控股各出资59%、25%、16%成立 合资上海市上海纪元微科微电子(原阿法泰克电子)泰国阿法泰克公司占51%,上海仪电控股占45%,美国微芯片公司占4%。 合资江苏省苏州市曰立半导体(Hitachi)曰立集团与新加坡经济发展厅合资 合资江苏省苏州市英飞凌(Infineon)英飞凌与中新苏州产业园区创业投资有限公司合资 合资江苏省无锡市矽格电子矽格电子与华晶上华合资 合资江苏省南通市南通富士通微电子南通华达微电子与富士通合资 合资北京市三菱四通电子曰本三菱与四通集团合资 合资广东省深圳市深圳赛意法电子深圳赛格高技术投资股份有限公司与意法半导体合资
半导体集成电路封装技术试题汇总(李可为版)
半导体集成电路封装技术试题汇总 第一章集成电路芯片封装技术 1. (P1)封装概念:狭义:集成电路芯片封装是利用(膜技术)及(微细加工技术),将芯片及其他要素在框架或基板上布置、粘贴固定及连接,引出接线端子并通过可塑性绝缘介质灌封固定,构成整体结构的工艺。 广义:将封装体与基板连接固定,装配成完整的系统或电子设备,并确保整个系统综合性能的工程。 2.集成电路封装的目的:在于保护芯片不受或者少受外界环境的影响,并为之提供一个良好的工作条件,以使集成电路具有稳定、正常的功能。 3.芯片封装所实现的功能:①传递电能,②传递电路信号,③提供散热途径,④结构保护与支持。 4.在选择具体的封装形式时主要考虑四种主要设计参数:性能,尺寸,重量,可靠性和成本目标。 5.封装工程的技术的技术层次? 第一层次,又称为芯片层次的封装,是指把集成电路芯片与封装基板或引脚架之间的粘贴固定电路连线与封装保护的工艺,使之成为易于取放输送,并可与下一层次的组装进行连接的模块元件。第二层次,将数个第一层次完成的封装与其他电子元器件组成一个电子卡的工艺。第三层次,将数个第二层次完成的封装组成的电路卡组合成在一个主电路版上使之成为一个部件或子系统的工艺。第四层次,将数个子系统组装成为一个完整电子厂品的工艺过程。 6.封装的分类?
按照封装中组合集成电路芯片的数目,芯片封装可分为:单芯片封装与多芯片封装两大类,按照密封的材料区分,可分为高分子材料和陶瓷为主的种类,按照器件与电路板互连方式,封装可区分为引脚插入型和表面贴装型两大类。依据引脚分布形态区分,封装元器件有单边引脚,双边引脚,四边引脚,底部引脚四种。常见的单边引脚有单列式封装与交叉引脚式封装,双边引脚元器件有双列式封装小型化封装,四边引脚有四边扁平封装,底部引脚有金属罐式与点阵列式封装。 7.芯片封装所使用的材料有金属陶瓷玻璃高分子 8.集成电路的发展主要表现在以下几个方面? 1芯片尺寸变得越来越大2工作频率越来越高3发热量日趋增大4引脚越来越多 对封装的要求:1小型化2适应高发热3集成度提高,同时适应大芯片要求4高密度化5适应多引脚6适应高温环境7适应高可靠性 9.有关名词: SIP :单列式封装 SQP:小型化封装 MCP:金属鑵式封装 DIP:双列式封装 CSP:芯片尺寸封装 QFP:四边扁平封装 PGA:点阵式封装 BGA:球栅阵列式封装 LCCC:无引线陶瓷芯片载体 第二章封装工艺流程 1.封装工艺流程一般可以分为两个部分,用塑料封装之前的工艺步骤成为前段操作,在成型之后的工艺步骤成为后段操作
半导体封装企业名单
半导体封装企业名单半导体封装企业名单 中电科技集团公司第58研究所 南通富士通微电子有限公司 江苏长电科技股份有限公司 江苏中电华威电子股份有限公司 天水华天科技股份有限公司(749厂) 铜陵三佳山田科技有限公司 无锡华润安盛封装公司(华润微电子封装总厂)中国电子科技集团第13研究所 乐山无线电股份公司 上海柏斯高模具有限公司 浙江华越芯装电子股份有限公司 航天771所 新科-金朋(上海)有限公司 江苏宜兴电子器件总厂 浙江东盛集成电路元件有限公司 北京科化新材料科技有限公司 上海华旭微电子公司 电子第24所 上海纪元微科电子有限公司
电子第47所 成都亚红电子公司 汕头华汕电子器件有限公司上海长丰智能卡公司 江门市华凯科技有限公司 广州半导体器件厂 北京宇翔电子有限公司 北京飞宇微电子有限责任公司深圳市商岳电子有限公司 绍兴力响微电子有限公司 上海永华电子有限公司 上海松下半导体有限公司 深圳深爱半导体有限公司 广东粤晶高科股份有限公司江苏泰兴市晶体管厂 无锡KEC半导体有限公司 捷敏电子(上海)有限公司星球电子有限公司 强茂电子(无锡)有限公司 万立电子(无锡)有限公司 江苏扬州晶来半导体集团
晶辉电子有限公司 济南晶恒有限责任公司(济南半导体总厂)无锡市无线电元件四厂 北京半导体器件五厂 吴江巨丰电子有限公司 苏州半导体总厂有限公司 快捷半导体(苏州)有限公司 无锡红光微电子有限公司 福建闽航电子公司 电子第55所 山东诸城电子封装厂 武汉钧陵微电子封装 外壳有限责任公司 山东海阳无线电元件厂 北京京东方半导体有限公司 电子第44所 电子第40所 宁波康强电子有限公司 浙江华科电子有限公司 无锡市东川电子配件厂 厦门永红电子公司
晶圆封装测试工序和半导体制造工艺流程
A.晶圆封装测试工序 一、IC检测 1. 缺陷检查Defect Inspection 2. DR-SEM(Defect Review Scanning Electron Microscopy) 用来检测出晶圆上是否有瑕疵,主要是微尘粒子、刮痕、残留物等问题。此外,对已印有电路图案的图案晶圆成品而言,则需要进行深次微米范围之瑕疵检测。一般来说,图案晶圆检测系统系以白光或雷射光来照射晶圆表面。再由一或多组侦测器接收自晶圆表面绕射出来的光线,并将该影像交由高功能软件进行底层图案消除,以辨识并发现瑕疵。 3. CD-SEM(Critical Dimensioin Measurement) 对蚀刻后的图案作精确的尺寸检测。 二、IC封装 1. 构装(Packaging) IC构装依使用材料可分为陶瓷(ceramic)及塑胶(plastic)两种,而目前商业应用上则以塑胶构装为主。以塑胶构装中打线接合为例,其步骤依序为晶片切割(die saw)、黏晶(die mount / die bond)、焊线(wire bond)、封胶(mold)、剪切/成形(trim / form)、印字(mark)、电镀(plating)及检验(inspection)等。 (1) 晶片切割(die saw) 晶片切割之目的为将前制程加工完成之晶圆上一颗颗之晶粒(die)切割分离。举例来说:以
0.2微米制程技术生产,每片八寸晶圆上可制作近六百颗以上的64M微量。 欲进行晶片切割,首先必须进行晶圆黏片,而后再送至晶片切割机上进行切割。切割完后之晶粒井然有序排列于胶带上,而框架的支撐避免了胶带的皱褶与晶粒之相互碰撞。 (2) 黏晶(die mount / die bond) 黏晶之目的乃将一颗颗之晶粒置于导线架上并以银胶(epoxy)粘着固定。黏晶完成后之导线架则经由传输设备送至弹匣(magazine)内,以送至下一制程进行焊线。 (3) 焊线(wire bond) IC构装制程(Packaging)则是利用塑胶或陶瓷包装晶粒与配线以成集成电路(Integrated Circuit;简称IC),此制程的目的是为了制造出所生产的电路的保护层,避免电路受到机械性刮伤或是高温破坏。最后整个集成电路的周围会向外拉出脚架(Pin),称之为打线,作为与外界电路板连接之用。 (4) 封胶(mold) 封胶之主要目的为防止湿气由外部侵入、以机械方式支持导线、內部产生热量之去除及提供能够手持之形体。其过程为将导线架置于框架上并预热,再将框架置于压模机上的构装模上,再以树脂充填并待硬化。 (5) 剪切/成形(trim / form) 剪切之目的为将导线架上构装完成之晶粒独立分开,并把不需要的连接用材料及部份凸出之树脂切除(dejunk)。成形之目的则是将外引脚压成各种预先设计好之形状,以便于装置于
半导体封装技术
随着半导体技术的发展,摩尔定律接近失效的边缘。产业链上IC 设计、 晶圆制造、封装测试各个环节的难度不断加大,技术门槛也越来越高,资 本投入越来越大。由单个企业覆盖整个产业链工艺的难度显著加大。半导 体产业链向专业化、精细化分工发展是一个必然的大趋势。 全球半导体产业整体成长放缓,产业结构发生调整,产能在区域上重新分 配。半导体产业发达地区和不发达地区将会根据自身的优势在半导体产 业链中有不同侧重地发展。封装产能转移将持续,外包封装测试行业的增 速有望超越全行业。 芯片设计行业的技术壁垒和晶圆制造行业的资金壁垒决定了,在现阶段, 封装测试行业将是中国半导体产业发展的重点。 在传统封装工艺中,黄金成本占比最高。目前采用铜丝替代金丝是一个大 的趋势。用铜丝引线键合的芯片产品出货占比的上升有助于提高封装企 业的盈利能力。 半导体封装的发展朝着小型化和多I/O 化的大趋势方向发展。具体的技术 发展包括多I/O 引脚封装的BGA 和小尺寸封装的CSP 等。WLSCP 和 TSV 等新技术有望推动给芯片封装测试带来革命性的进步。 中国本土的封装测试企业各有特点:通富微电最直接享受全球产能转移; 长电科技在技术上稳步发展、巩固其行业龙头地位;华天科技依托地域优 势享受最高毛利率的同时通过投资实现技术的飞跃。 中国本土给封装企业做配套的上游企业,如康强电子和新华锦,都有望在 封装行业升级换代的过程中提升自己的行业地位。 风险提示:全球领先的封装测试企业在中国大陆直接投资,这将加大行 业内的竞争。同时用工成本的上升将直接影响半导体封装企业的盈利能 力。 半导体封装产能持续转移 半导体封装环节至关重要 半导体芯片的大体制备流程包括芯片设计->圆晶制造->封装测试。所谓半导体 ?封装(Packaging)?,是半导体芯片生产过程的最后一道工序,是将集成电路用绝缘的材料打包的技术。封装工艺主要有以下功能:功率分配(电源分配)、信号分配、散热通道、隔离保护和机械支持等。封装工艺对于芯片来说是必须的,也是至关重要的一个环节。因为芯片必须与外界隔离,以防止空气中的杂质对芯片电路的腐蚀而造成电气性能的下降。另外,封装后的芯片也更便于安装和运输。可以说封装是半导体集成电路与电路板的链接桥梁,封装技术的好坏还直接影响到芯片自身的性能和PCB 的设计与制造, 产业分工精细化 随着半导体产业的发展,?摩尔?定律持续地发酵,IC 芯片集成度以几何级数 上升,线宽大幅下降。以INTEL CPU 芯片为例,线宽已经由1978 年推出的8086 的3 μm 发展到2010 年推出Core i 7 的45nm , 对应的晶体管集成度由2.9 万只发展到7.8 亿只。产业链上IC 设计、晶圆制造、封装测试各个环节的难度不断加大,技术门槛也越来越高。同时随着技术水平的飞升和规模的扩大,产业链中的多个环节对资本投入的要求也大幅提高。由单个企业做完覆盖整个产业链工艺的难度越来越大。在这样的大环境下,产业链向专业化、精细化分工发展是一个必然的大趋势。 目前全球的半导体产业链大致可以归纳为几大类参与者:IDM 集成设备制造商;
半导体封装方式
半导体封装简介: 半导体生产流程由晶圆制造、晶圆测试、芯片封装和封装后测试组成。塑封之后,还要进行一系列操作,如后固化(Post Mold Cure)、切筋和成型 (Trim&Form)、电镀(Plating)以及打印等工艺。典型的封装工艺流程为: 划片装片键合塑封去飞边电镀打印切筋和成型外观检查成品测试包装出货。 一、DIP双列直插式封装 1. 适合在PCB(印刷电路板)上穿孔焊接,操作方便。 2. 芯片面积与封装面积之间的比值较大,故体积也较大。 二、QFP塑料方型扁平式封装和PFP塑料扁平组件式封装 QFP封装的芯片引脚之间距离很小,管脚很细,一般大规模或超大型集 成电路都采用这种封装形式,其引脚数一般在100个以上。用这种形式 封装的芯片必须采用SMD(表面安装设备技术)将芯片与主板焊接起来。 采用SMD安装的芯片不必在主板上打孔,一般在主板表面上有设计好 的相应管脚的焊点。将芯片各脚对准相应的焊点,即可实现与主板的焊 接。用这种方法焊上去的芯片,如果不用专用工具是很难拆卸下来的。 PFP(Plastic Flat Package)方式封装的芯片与QFP方式基本相同。唯一的 区别是QFP一般为正方形,而PFP既可以是正方形,也可以是长方形。 QFP/PFP封装具有以下特点: 1.适用于SMD表面安装技术在PCB电路板上安装布线。 2.适合高频使用。 3.操作方便,可靠性高。 4.芯片面积与封装面积之间的比值较小。 三、PGA插针网格阵列封装 一种名为ZIF的CPU插座,专门用来满足PGA封装的CPU在安装和 拆卸上的要求。ZIF(Zero Insertion Force Socket)是指零插拔力的插座。 1. 插拔操作更方便,可靠性高。 2. 可适应更高的频率。
半导体封装技术大全
半导体封装技术大全 1、BGA(ball grid array) 球形触点陈列,表面贴装型封装之一。在印刷基板的背面按陈列方式制作出球形凸点用以代替引脚,在印刷基板的正面装配LSI 芯片,然后用模压树脂或灌封方法进行密封。也称为凸点陈列载体(PAC)。引脚可超过200,是多引脚LSI 用的一种封装。封装本体也可做得比QFP(四侧引脚扁平封装)小。例如,引脚中心距为1.5mm 的360 引脚BGA仅为31mm 见方;而引脚中心距为0.5mm 的30 4 引脚QFP 为40mm 见方。而且BGA不用担心QFP 那样的引脚变形问题。该封装是美国Motorola 公司开发的,首先在便携式电话等设备中被采用,今后在美国有 可能在个人计算机中普及。最初,BGA的引脚(凸点)中心距为1.5mm,引脚数为225。现在也有一些LSI 厂家正在开发500 引脚的BGA。BGA的问题是回流焊后的外观检查。现在尚不清楚是否有效的外观检查方法。有的认为,由于焊接的中心距较大,连接可以看作是稳定的,只能通过功能检查来处理。美国Motorola 公司把用模压树脂密封的封装称为OMPAC,而把灌封方法密封的封装称为 GPAC(见OMPAC 和GPAC)。 2、BQFP(quad flat package with bumper) 带缓冲垫的四侧引脚扁平封装。QFP 封装之一,在封装本体的四个角设置突起(缓冲垫) 以防止在运送过程中引脚发生弯曲变形。美国半导体厂家主要在微处理器和ASIC 等电路中采用此封装。引脚中心距0.635mm,引脚数从84 到196 左右(见QFP)。 3、碰焊PGA(butt joint pin grid array) 表面贴装型PGA 的别称(见表面贴装型PGA)。 4、C-(ceramic) 表示陶瓷封装的记号。例如,CDIP 表示的是陶瓷DIP。是在实际中经常使用的记号。 5、Cerdip 用玻璃密封的陶瓷双列直插式封装,用于ECL RAM,DSP(数字信号处理器)等电路。带有玻璃窗口的Cerdip 用于紫外线擦除型EP ROM 以及内部带有EPROM 的微机电路等。引脚中心距2.54mm,引脚数从8 到42。在日本,此封装表示为DIP-G(G 即玻璃密封的意思)。 6、Cerquad 表面贴装型封装之一,即用下密封的陶瓷QFP,用于封装DSP 等的逻辑LSI 电路。带有窗口的Cerquad 用于封装EPROM 电路。散热性比塑料QFP 好,在自然空冷条件下可容许1. 5~ 2W 的功率。但封装成本比塑料QFP 高3~5 倍。引脚中心距有1.27mm、0.8m m、0.65mm、 0.5mm、 0.4mm 等多种规格。引脚数从32 到368。 7、CLCC(ceramic leaded chip carrier) 带引脚的陶瓷芯片载体,表面贴装型封装之一,引脚从封装的四个侧面引出,呈丁字形。带有窗口的用于封装紫外线擦除型EPRO M 以及带有EPROM 的微机电路等。此封装也称为 QFJ、QFJ-G(见QFJ)。 8、COB(chip on board) 板上芯片封装,是裸芯片贴装技术之一,半导体芯片交接贴装在印刷线路板上,芯片与基板的电气连接用引线缝合方法实现,芯片与基板的电气连接用引线缝合方法实现,并用树脂覆盖以确保可靠性。虽然COB 是最简单的裸芯片贴装技术,但它的封装密度远不如TAB 和倒片焊技术。 9、DFP(dual flat package) 双侧引脚扁平封装。是SOP 的别称(见SOP)。以前曾有此称法,现在已基本上不用。 10、DIC(dual in-line ceramic package) 陶瓷DIP(含玻璃密封)的别称(见DIP). 11、DIL(dual in-line) DIP 的别称(见DIP)。欧洲半导体厂家多用此名称。 12、DIP(dual in-line package) 双列直插式封装。插装型封装之一,引脚从封装两侧引出,封装材料有塑料和陶瓷两种。 DIP 是最普及的插装型封装,应用范围包括标准逻辑IC,存贮器LSI,微机电路等。引脚中心距2.54mm,引脚数从6 到64。封装宽度通常为15.2mm。有的把宽度为7.52m m 和10.16mm 的封装分别称为skinny DIP 和slim DIP(窄体型DIP)。但多数情况下并不加区分,只简单地统称为DIP。另外,用低熔点玻璃密封的陶瓷DIP 也称为cerdip(见cerdip)。 13、DSO(dual small out-lint) 双侧引脚小外形封装。SOP 的别称(见SOP)。部分半导体厂家采用此名称。 14、DICP(dual tape carrier package) 双侧引脚带载封装。TCP(带载封装)之一。引脚制作在绝缘带上并从封装两侧引出。由于利用的是TAB(自动带载焊接)技术,封装外形非常薄。常用于液晶显示驱动LSI,但多数为定制品。另外,0.5mm 厚的存储器LSI 簿形封装正处于开发阶段。在日本,按照E
半导体封装过程wire bond 中 wire loop 的研究及其优化
南京师范大学 电气与自动化科学学院 毕业设计(论文) 半导体封装过程wire bond中wire loop的研究及其优化 专业机电一体化 班级学号22010439 学生姓名刘晶炎 单位指导教师储焱 学校指导教师张朝晖 评阅教师 2005年5月30日
摘要 在半导体封装过程中,IC芯片与外部电路的连接一段使用金线(金线的直径非常小0.8--2.0 mils)来完成,金线wire bond过程中可以通过控制不同的参数来形成不同的loop形状,除了金线自身的物理强度特性外,不同的loop形状对外力的抵抗能力有差异,而对于wire bond来说,我们希望有一种或几种loop形状的抵抗外力性能出色,这样,不仅在半导体封装的前道,在半导体封装的后道也能提高mold过后的良品率,即有效地抑制wire sweeping, wire open.以及由wire sweeping引起的bond short.因此,我们提出对wire loop的形状进行研究,以期得到一个能够提高wire抗外力能力的途径。 对于wire loop形状的研究,可以解决: (1)金线neck broken的改善。 (2)BPT数值的升高。 (3)抗mold过程中EMC的冲击力加强。 (4)搬运过程中抗冲击力的加强。 关键词:半导体封装,金线,引线焊接,线型。
Abstract During the process of the semiconductor assembly, we use the Au wire to connect the peripheral circuit from the IC. (The diameter of the Au wire is very small .Usually, it’s about 0.8mil~2mil.) And during the Au wire bonding, we can get different loop types from control the different parameters. Besides the physics characteristic of the Au wire, the loop types can also affect the repellence under the outside force. For the process of the wire bond, we hope there are some good loop types so that improve the repellence under the outside force. According to this, it can improve the good device ratio after molding. It not only reduces the wire sweeping and the wire open of Au wires but also avoid the bond short cause by the wire sweeping. Therefore, we do the disquisition about the loop type for getting the way to improve the repellence under outside forces. This disquisition can solve the problem about: (1)Improve the neck broken of Au wire. (2)Heighten the BST data. (3)Enhance the resist force to EMC during the molding process. (4)Decrease the possibility of device broken when it be moved. Keyword: the semiconductor assembly, Au wire, wire bond, wire loop.
半导体封装企业名单
半导体封装企业名单 半导体封装企业名单 中电科技集团公司第58研究所 南通富士通微电子有限公司 江苏长电科技股份有限公司 江苏中电华威电子股份有限公司 天水华天科技股份有限公司(749厂) 铜陵三佳山田科技有限公司 无锡华润安盛封装公司(华润微电子封装总厂)中国电子科技集团第13研究所 乐山无线电股份公司 上海柏斯高模具有限公司 浙江华越芯装电子股份有限公司 航天771所 新科-金朋(上海)有限公司 江苏宜兴电子器件总厂 浙江东盛集成电路元件有限公司 北京科化新材料科技有限公司 上海华旭微电子公司 电子第24所 上海纪元微科电子有限公司 电子第47所 成都亚红电子公司 汕头华汕电子器件有限公司 上海长丰智能卡公司 江门市华凯科技有限公司 广州半导体器件厂 北京宇翔电子有限公司 北京飞宇微电子有限责任公司 深圳市商岳电子有限公司 绍兴力响微电子有限公司 上海永华电子有限公司 上海松下半导体有限公司 深圳深爱半导体有限公司 广东粤晶高科股份有限公司 江苏泰兴市晶体管厂 无锡KEC半导体有限公司 捷敏电子(上海)有限公司 星球电子有限公司 强茂电子(无锡)有限公司 万立电子(无锡)有限公司 江苏扬州晶来半导体集团 晶辉电子有限公司
济南晶恒有限责任公司(济南半导体总厂)无锡市无线电元件四厂 北京半导体器件五厂 吴江巨丰电子有限公司 苏州半导体总厂有限公司 快捷半导体(苏州)有限公司 无锡红光微电子有限公司 福建闽航电子公司 电子第55所 山东诸城电子封装厂 武汉钧陵微电子封装 外壳有限责任公司 山东海阳无线电元件厂 北京京东方半导体有限公司 电子第44所 电子第40所 宁波康强电子有限公司 浙江华科电子有限公司 无锡市东川电子配件厂 厦门永红电子公司 浙江华锦微电子有限公司 昆明贵研铂业股份有限公司 洛阳铜加工集团有限责任公司 无锡市化工研究设计院 河南新乡华丹电子有限责任公司 安徽精通科技有限公司 无锡华晶利达电子有限公司 电子第43所 中国电子科技集团2所 长沙韶光微电子总公司 上海新阳电子化学有限公司 无锡华友微电子有限公司 均强机械(苏州)有限公司 东和半导体设备(上海)有限公司 复旦大学高分子科学系 清华大学材料科学与工程研究院 哈尔滨工业大学微电子中心 清华大学微电子所电子技术标准化所(4所)信息产业部 电子5所 中科院电子研究所 先进晶园集成电路(上海)有限公司 东辉电子工业(深圳)有限公司
中国半导体封装测试工厂
中国半导体封装测试工厂 上海华旭微电子有限公司 上海芯哲微电子科技有限公司 沈阳中光电子有限公司 超威半导体公司 葵和精密(上海) 新义半导体 快捷半导体 安靠封测(上海) 东莞乐依文半导体有限公司 日月光(威海) 日月光(上海)威宇半导体 日月芯 嘉盛半导体 罗姆电子(天津)有限公司 长风 尼西 成都亚光电子股份有限公司 宏茂微电子 上海斯伦贝谢智能卡技术有限公司飞思卡尔半导体 晶诚(郑州)科技有限公司 银河微电子 捷敏电子 捷敏电子(合肥) 通用半导体 通用半导体(西安爱尔) 超丰 勤益电子(上海) 广州半导体器件 桂林斯壮半导体 无锡华润华晶微电子 合肥合晶 华越芯装电子 苏州奇梦达公司 英飞凌科技(无锡)有限公司 江苏长电科技股份有限公司 吉林市华星电子有限公司 凯虹电子开益禧半导体 京隆科技 震坤 乐山菲尼克斯(ON Semi) 菱生 骊山微电子 绍兴力响微电子 绍兴力响微电子有限公司 美光半导体 巨丰电子 上海纪元微科 美国芯源系统 南方电子 南通富士通微电子股份有限公司美国国家半导体有限公司 华微 凤凰半导体 飞利浦 清溪三清半导体 瑞萨半导体 威讯联合 三星电子(半导体) 晟碟半导体 三洋半导体 三洋 上海旭福电子 永华电子 汕头华汕电子 深爱半导体 矽格电子 中芯国际 中芯国际 中芯国际 中芯国际 飞索半导体 深圳赛意法电子 天水华天微电子 东芝半导体 芯宇 优特半导体(上海) 新康电子/威旭 晶方半导体科技(苏州)有限公司无锡华润安盛科技有限公司 无锡红光微电子
厦门华联电子有限公司 扬州晶来半导体有限公司 矽德半导体 扬州市邗江九星电子有限公司 广东粤晶高科 中星华电子 瑞特克斯(成都)电子 潮州市创佳微电子有限公司 恒诺微电子(嘉兴)有限公司 恒诺微电子上海 英特尔产品成都 英特尔产品上海 上海松下半导体 苏州松下半导体 矽品 日立半导体(苏州)有限公司 江门市华凯科技有限公司 江阴长电先进封装有限公司 阳信长威电子有限公司长威电子 星科金朋 浙江金凯微电子 长沙韶光微电子 深圳世纪晶源科技有限公司 国内的十大封装测试企业(这是05年的排名了): 1.飞思卡尔(Freescale)(天津) 2.RF(MicroDevices)(北京) 3.深圳赛意法(Sig-STMicro) 4.Intel(上海) 5.上海松下(Matsushita)半导体 6.南通富士通(Fujitsu)微电子 7.苏州英飞凌(Infineon) 8.北京瑞萨(Renesas)半导体 9.江苏长电科技 10.乐山菲尼克斯(Phenix)半导体
IC半导体封装测试流程
IC半导体封装测试流程 更多免费资料下载请进:https://www.360docs.net/doc/489139080.html,好好学习社区
IC半导体封装测试流程 第1章前言 1.1 半导体芯片封装的目的 半导体芯片封装主要基于以下四个目的[10, 13]: ●防护 ●支撑 ●连接 ●可靠性 图1-1 TSOP封装的剖面结构图 Figure 1-1 TSOP Package Cross-section 第一,保护:半导体芯片的生产车间都有非常严格的生产条件控制,恒定的温度(230±3℃)、恒定的湿度(50±10%)、严格的空气尘埃颗粒度控制(一般介于1K到10K)及严格的静电保护措施,裸露的装芯片只有在这种严格的环境控制下才不会失效。但是,我们所生活的周围环境完全不可能具备这种条件,低温可能会有-40℃、高温可能会有60℃、湿度可能达到100%,如果是汽车产品,其工作温度可能高达120℃以上,为了要保护芯片,所以我们需要封装。 第二,支撑:支撑有两个作用,一是支撑芯片,将芯片固定好便于电路的连接,二是封装完成以后,形成一定的外形以支撑整个器件、使得整个器件不易损坏。 第三,连接:连接的作用是将芯片的电极和外界的电路连通。
引脚用于和外界电路连通,金线则将引脚和芯片的电路连接起来。载片台用于承载芯片,环氧树脂粘合剂用于将芯片粘贴在载片台上,引脚用于支撑整个器件,而塑封体则起到固定及保护作用。 第四,可靠性:任何封装都需要形成一定的可靠性,这是整个封装工艺中最重要的衡量指标。原始的芯片离开特定的生存环境后就会损毁,需要封装。芯片的工作寿命,主要决于对封装材料和封装工艺的选择。 1.2 半导体芯片封装技术的发展趋势 ● 封装尺寸变得越来越小、越来越薄 ● 引脚数变得越来越多 ● 芯片制造与封装工艺逐渐溶合 ● 焊盘大小、节距变得越来越小 ● 成本越来越低 ● 绿色、环保 以下半导体封装技术的发展趋势图[2,3,4,11,12,13]: 图1-2 半导体封装技术发展趋势 Figure 1-2 Assembly Technology Development Trend 小型化
半导体封装前沿技术
最新封装技术与发展 芯片制作流程 封装大致经过了如下发展进程: 结构方面:DIP 封装(70 年代)->SMT 工艺(80 年代LCCC/PLCC/SOP/QFP)->BGA 封装(90 年代)->面向未来的工艺(CSP/MCM) 材料方面:金属、陶瓷->陶瓷、塑料->塑料; 引脚形状:长引线直插->短引线或无引线贴装->球状凸点; 装配方式:通孔插装->表面组装->直接安装 封装技术各种类型 一.TO 晶体管外形封装 TO (Transistor Out-line)的中文意思是“晶体管外形”。这是早期的封装规格,例如TO-92,TO-92L,TO-220,TO-252 等等都是插入式封装设计。近年来表面贴装市场需求量增大,TO 封装也进展到表面贴装式封装。 TO252 和TO263 就是表面贴装封装。其中TO-252 又称之为D-PAK,TO-263 又称之为D2PAK。D-PAK 封装的MOSFET 有3 个电极,栅极(G)、漏极(D)、源极(S)。其中漏极(D)的引脚被剪断不用,而是使用背面的散热板作漏极(D),直接焊接在PCB 上,一方面用于输出大电流,一方面通过PCB 散热。所以PCB 的D-PAK 焊盘有三处,漏极(D)焊盘较大。
二.DIP 双列直插式封装 DIP(DualIn-line Package)是指采用双列直插形式封装的集成电路芯片,绝大多数中小规模集成电路(IC)均采用这种封装形式,其引脚数一般不超过100 个。封装材料有塑料和陶瓷两种。采用DIP 封装的CPU 芯片有两排引脚,使用时,需要插入到具有DIP 结构的芯片插座上。当然,也可以直接插在有相同焊孔数和几何排列的电路板上进行焊接。DIP 封装结构形式有:多层陶瓷双列直插式DIP,单层陶瓷双列直插式DIP,引线框架式DIP (含玻璃陶瓷封接式,塑料包封结构式,陶瓷低熔玻璃封装式)等。 DIP 封装具有以下特点: 1.适合在PCB (印刷电路板)上穿孔焊接,操作方便。 2. 比TO 型封装易于对PCB 布线。 3.芯片面积与封装面积之间的比值较大,故体积也较大。以采用40 根I/O 引脚塑料双列直插式封装(PDIP)的CPU 为例,其芯片面积/封装面积=(3×3)/(15.24×50)=1:86,离1 相差很远。(PS:衡量一个芯片封装技术先进与否的重要指标是芯片面积与封装面积之比,这个比值越接近1 越好。如果封装尺寸远比芯片大,说明封装效率很低,占去了很多有效安装面积。) 用途:DIP 是最普及的插装型封装,应用范围包括标准逻辑IC,存贮器LSI,微机电路等。Intel 公司早期CPU,如8086、80286 就采用这种封装形式,缓存(Cache )和早期的内存芯片也是这种封装形式。 三.QFP 方型扁平式封装 QFP(Plastic Quad Flat Pockage)技术实现的CPU 芯片引脚之间距离很小,管脚很细,一般大规模或超大规模集成电路采用这种封装形式,其引脚数一般都在100 以上。基材有陶瓷、金属和塑料三种。引脚中心距有1.0mm、0.8mm、0.65mm、0.5mm、0.4mm、0.3mm 等多种规格。 其特点是: 1.用SMT 表面安装技术在PCB 上安装布线。 2.封装外形尺寸小,寄生参数减小,适合高频应用。以0.5mm 焊区中心距、208 根I/O 引脚QFP 封装的CPU 为例,如果外形尺寸为28mm×28mm,芯片尺寸为10mm×10mm,则芯片面积/封装面积=(10×10)/(28×28)=1:7.8,由此可见QFP 封装比DIP 封装的尺寸大大减小。 3.封装CPU 操作方便、可靠性高。 QFP 的缺点是:当引脚中心距小于0.65mm 时,引脚容易弯曲。为了防止引脚变形,现已出现了几种改进的QFP 品种。如封装的四个角带有树指缓冲垫的BQFP(见右图);带树脂保护环覆盖引脚前端的GQFP;在封装本体里设置测试凸点、放在防止引脚变形的专用夹具里就可进行测试的TPQFP 。 用途:QFP 不仅用于微处理器(Intel 公司的80386 处理器就采用塑料四边引出扁平封装),门陈列等数字逻辑LSI 电路,而且也用于VTR 信号处理、音响信号处理等模拟LSI 电路。四.SOP 小尺寸封装 SOP 器件又称为SOIC(Small Outline Integrated Circuit),是DIP 的缩小形式,引线中心距为1.27mm,材料有塑料和陶瓷两种。SOP 也叫SOL 和DFP。SOP 封装标准有SOP-8、SOP-16、SOP-20、SOP-28 等等,SOP 后面的数字表示引脚数,业界往往把“P”省略,叫SO (Small Out-Line )。还派生出SOJ (J 型引脚小外形封装)、TSOP (薄小外形封装)、VSOP (甚小外形封装)、SSOP (缩小型SOP )、TSSOP (薄的缩小型SOP )及SOT (小外形晶
晶圆封装测试工序和半导体制造工艺流程_百度文库(精)
晶圆封装测试工序和半导体制造工艺流程.txt-两个人同时犯了错,站出来承担的那一方叫宽容,另一方欠下的债,早晚都要还。-不爱就不爱,别他妈的说我们合不来。A.晶圆封装测试工序 一、 IC检测 1. 缺陷检查Defect Inspection 2. DR-SEM(Defect Review Scanning Electron Microscopy 用来检测出晶圆上是否有瑕疵,主要是微尘粒子、刮痕、残留物等问题。此外,对已印有电路图案的图案晶圆成品而言,则需要进行深次微米范围之瑕疵检测。一般来说,图案晶圆检测系统系以白光或雷射光来照射晶圆表面。再由一或多组侦测器接收自晶圆表面绕射出来的光线,并将该影像交由高功能软件进行底层图案消除,以辨识并发现瑕疵。 3. CD-SEM(Critical Dimensioin Measurement 对蚀刻后的图案作精确的尺寸检测。 二、 IC封装 1. 构装(Packaging) IC构装依使用材料可分为陶瓷(ceramic)及塑胶(plastic)两种,而目前商业应用上则以塑胶构装为主。以塑胶构装中打线接合为例,其步骤依序为晶片切割(die saw)、黏晶(die mount / die bond)、焊线(wire bond)、封胶(mold)、剪切/成形(trim / form)、印字(mark)、电镀(plating)及检验(inspection)等。 (1 晶片切割(die saw) 晶片切割之目的为将前制程加工完成之晶圆上一颗颗之晶粒(die)切割分离。举例来说:以0.2微米制程技术生产,每片八寸晶圆上可制作近六百颗以上的64M微量。 欲进行晶片切割,首先必须进行晶圆黏片,而后再送至晶片切割机上进行切割。切割完后之晶粒井然有序排列于胶带上,而框架的支撐避免了胶带的皱褶与晶粒之相互碰撞。 (2 黏晶(die mount / die bond) 黏晶之目的乃将一颗颗之晶粒置于导线架上并以银胶(epoxy)粘着固定。黏晶完成后之导线架则经由传输设备送至弹匣(magazine)内,以送至下一制程进行焊线。 (3 焊线(wire bond) IC构装制程(Packaging)则是利用塑胶或陶瓷包装晶粒与配线以成集成电路(Integrated Circuit;简称IC),此制程的目的是为了制造出所生产的电路的保护层,避免电路受到机械性刮伤或是高温破坏。最后整个集成电路的周围会向外拉出脚架(Pin),称之为打线,作为与外界电路板连接之用。 (4 封胶(mold)