反应釜安全操作规程

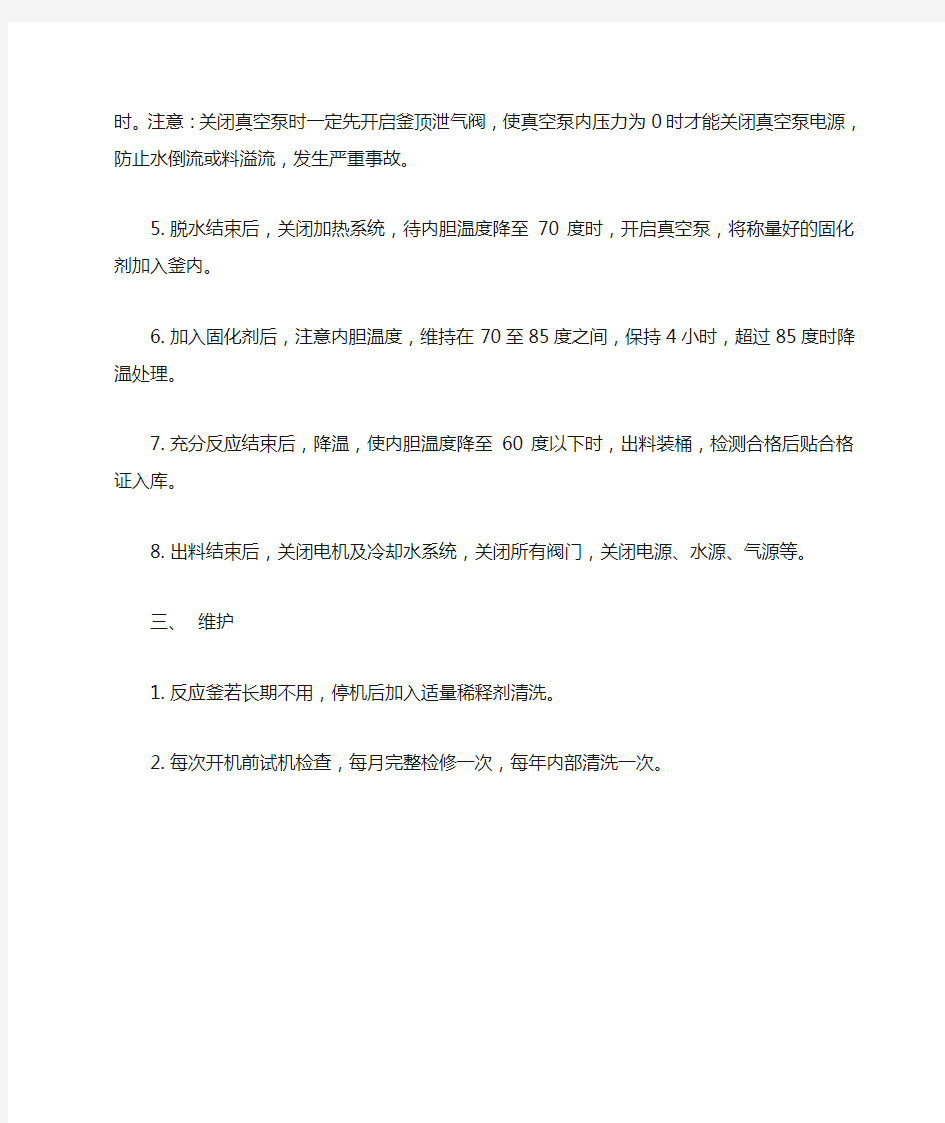
反应釜安全操作规程
一、准备
1.进入车间,必须穿戴工作服、口罩、手套等劳保用品,认真记录操作过程。
2.检查反应釜的供电、供水及抽真空系统是否正常。
3.预加热,检查夹套温度与内胆温度升温速度是否正常。
4.检查供料系统是否正常。
5.检查所有阀门等开启状态是否正常,关闭出料口。
6.操作人员必须经过技能培训和安全培训才能上岗。
二、操作
1.关闭出料口,开启真空泵,将称量好的聚醚多元醇吸入釜内。
2.开启搅拌电机开始搅拌。注意:搅拌电机直至出料结束后才能停机。
3.加热:夹套温度每次加热到135度左右即停止,降到130度以下时再加。关键
是注意内胆温度。80度左右时加入称量好的增塑剂。
4.脱水:加热使内胆温度升至125度左右时,维持这个温度,同时开启真空泵抽真
空2小时。注意:关闭真空泵时一定先开启釜顶泄气阀,使真空泵内压力为0时才能关闭真空泵电源,防止水倒流或料溢流,发生严重事故。
5.脱水结束后,关闭加热系统,待内胆温度降至70度时,开启真空泵,将称量好
的固化剂加入釜内。
6.加入固化剂后,注意内胆温度,维持在70至85度之间,保持4小时,超过85
度时降温处理。
7.充分反应结束后,降温,使内胆温度降至60度以下时,出料装桶,检测合格后
贴合格证入库。
8.出料结束后,关闭电机及冷却水系统,关闭所有阀门,关闭电源、水源、气源等。
三、维护
1.反应釜若长期不用,停机后加入适量稀释剂清洗。
2.每次开机前试机检查,每月完整检修一次,每年内部清洗一次。
模拟理想搅拌反应釜系统
模拟理想搅拌反应釜系统 本文由岩征仪器整理 模拟理想搅拌反应釜系统 连续搅拌釜反应器(CSTRs)也称作理想搅拌反应釜,常用于化学及生物化学行业。这类反应釜可以在稳定状态下运行,具有良好的混合属性,所以我们假定反应釜内的成分是均匀的。使用反应工程接口中的一个新模型,我们能够可视化一个理想反应釜系统内的动力学。 理想搅拌反应釜的应用 反应釜较常用于化工行业,它具有完美混合条件,并支持液位控制。我们假定这类理想搅拌反应釜内能实现完美混合,而且输出成分与反应釜内材料的成分完全相同。在这类系统中,会不断向反应釜中加入反应物,并连续不断地移出反应产物。下图显示了连续搅拌反应釜的不同部件。 连续搅拌釜示意图。
模拟一个级联理想反应釜系统 COMSOL Multiphysics5.0版本提供了理想搅拌反应釜系统模型,其中使用一个新的被称作通用CSTR的反应釜类型,这是反应工程接口中新增的一项功能(点击此处了解本接口的这项新功能及其他更新)。 模型设计用于求解液相的一阶不可逆反应,反应物A产生产物B。反应发生在一个包含两个级联反应釜的理想系统中。下图显示了这些反应釜。第一个反应釜的体积vtank1为1m3,第二个反应釜的体积vtank2初始为 1.5m3。 反应釜系统的详细描述 开始时,两个反应釜中均仅填充了溶剂。含反应物A的溶剂以vf1=1 m3/min的体积流率输入第一个反应釜。第一个反应釜的出口速率设定为vout1 =0.9m3/min。出口流体以vf2=vout1的速度进入第二个反应釜。以vfresh2 =0.5m3/min的速度向第二个反应釜输入新的含反应物A的溶剂。第二个反应釜的出口流速调整为vout2=1m3/min。 模型中包括两个停止条件。如果任何一个反应釜的体积为初始体积的1%或更低,计算就将停止。 下方的第一张图突出显示了每个反应釜中反应物A及产物B的浓度。
实验1连续搅拌釜式反应器停留时间分布的测定
实验一 连续搅拌釜式反应器停留时间分布的测定 一、 实验目的 (1) 加深对停留时间分布概念的理解; (2) 掌握测定液相停留时间分布的方法; (3) 了解停留时间分布曲线的应用。 (4)了解停留时间分布于多釜串联模型的关系,了解模型参数N 的物理意义及计算方法。 (5) 了解物料流速及搅拌转速对停留时间分布的影响。 二、 实验原理 (1)停留时间分布 当物料连续流经反应器时,停留时间及停留时间分布是重要概念。停留时间分布和流动模型密切相关。流动模型分平推流,全混流与非理想流动三种类型。 对于平推流,流体各质点在反应器内的停留时间均相等,对于全混流,流体各质点在反应器内的停留时间是不一的,在0~∞范围内变化。对于非理想流动,流体各质点在反应器内的停留时间分布情况介乎于以上两种理想状态之间,总之,无论流动类型如何,都存在停留时间分布与停留时间分布的定量描述问题。 (2)停留时间分布密度函数E (t ) 停留时间分布密度函数E (t )的定义: 当物料以稳定流速流入设备(但不发生化学变化)时,在时间t =0时,于瞬时间dt 进入设备的N 个流体微元中,具有停留时间为t 到(t +dt )之间的流体微元量dN 占当初流入量N 的分率为E (t )dt ,即 ()=dN E t dt N (1) E (t )定义为停留时间分布密度函数。 由于讨论的前提是稳定流动系统,因此,在不同瞬间同时进入系统的各批N 个流体微元均具有相同的停留时间分布密度,显然,流过系统的全部流体,物料停留时间分布密度为同一个E (t )所确定。根据E (t )定义,它必然具有归一化性质:
()1∞ =? E t dt (2) 不同流动类型的E (t )曲线形状如图1所示。根据E (t )曲线形状,可以定性分析物料在反应器(设备)内停留时间分布。 平推流 全混流 非理想流动 图1 各种流动的E (t )~t 关系曲线图 (3)停留时间分布密度函数E (t )的测定 停留时间分布密度函数E (t )的测定,常用的方法是脉冲法。此法采用的示踪剂,既不与被测流体发生化学反应,又不影响流体流动特性,也就是说,示踪物在反应器(设备)内的停留时间分布与被测流体的停留时间分布相同。所以,当注入一定量Q 的示踪物时,经过t →(t +dt )时间间隔流出的示踪物量占示踪物注入总量Q 的分率就是与示踪物注入同时进入系统的物料中,停留时间为t →(t +dt )的那部分流体物料占总流体的物料的分率, 即: 亦即: ()()??=V C t dt E t dt Q 或 () ()?= V C t E t Q (3) V ——流体体积流量,(ml/s) Q ——加入的示踪物总量,(mg) C (t )——示踪物的出口浓度,(mg/ml)
连续搅拌釜反应器中乙酸乙酯的水解反应
实验报告 课程名称:化工专业实验指导老师:黄灵仙成绩:________________ 实验名称:连续搅拌釜反应器中乙酸乙酯的水解反应实验类型:反应工程实验 一、实验目的和要求 二、实验内容和原理 三、主要仪器设备 四、操作方法和实验步骤 五、实验数据记录和处理 六、实验结果与分析 七、讨论、心得 一、实验目的 1.了解和掌握搅拌釜反应器非理想流动产生的原因; 2.掌握搅拌釜反应器达到全混流状态的判断和操作; 3.了解和掌握某一反应在全混釜中连续操作条件下反应结果的测量方法,以及与间歇反应器内反应结果的差别。 二、实验原理 在稳定条件下,根据全混釜反应器的物料衡算基础,有 A m A A A m A A A A x C C C C C C V F r ττ0000)1()()=-=-= (-(1) 对于乙酸乙脂水解反应: OH H C COO CH H COOC CH OH 52-3K 523-+?→?+ A B C D 当C A0=C B0,且在等分子流量进料时,其反应速度(-r A )可表示如下形式: 2 20A 20 2 A 02)1))/exp()A A A A A x kC C C C RT E k kC r -=-==(((-(2) 则根据文献(物化实验)的乙酸乙酯动力学方程,由(1),(2)可计算出x A 2 20A m )1A A A x kC x C -=(τ(3) 同时由于C A0∝(L 0-L ∞),C A ∝(L t -L ∞),由实验值得: )( 100∞ ---=L L L L x t A (4) 式中: L 0,L ∞—— 分别为反应初始和反应完毕时的电导率 L t —— 空时为m τ时的电导率 根据反应溶液的电导率的大小,由(4)式可以直接得到相应的反应转化率,由(3)式计算得到相同条件下的转化率,两者进行比较可知目前反应器的反应结果偏离全混流反应的理论计算值。 专业: 姓名: 学号: 日期: 地点:
连续式反应釜结构和原理
连续式反应釜结构和原理 本文由岩征仪器整理 连续搅拌反应釜的基本结构如图: 反应釜由搅拌容器和搅拌机两大部分组成。搅拌容器包括筒体、换热元件及内构件。搅拌器、搅拌轴及其密封装置、传动装置等统称为搅拌机。筒体为通常为一圆柱形壳体,可以在罐内装入物料,他提供反应所需的空间,使物料在其内部进行化学反应;传热装置的作用是满足反应所需温度条件;搅拌装置包括搅拌器、搅拌轴等,是实现搅拌的工作部件;传动装置包括电动机、减速器、联轴器及机架等附件,它提供搅拌的动力;轴封装置是保证工作时形成密封条件,阻止介质向外泄漏的部件。 连续搅拌反应釜的基本原理: 在内层放入反应溶媒可做搅拌反应,夹层可通上不同的冷热源(冷冻液,热水或热油)做循环加热或冷却反应。 通过反应釜夹层,注入恒温的(高温或低温)热溶媒体或冷却媒体,对反应釜内的物料进行恒温加热或制冷。同时可根据使用要求在常压或负压条件下进行搅拌反应。 物料在反应釜内进行反应,并能控制反应溶液的蒸发与回流,反应完毕,物料可从釜底的出料口放出,操作极为方便。 连续式反应釜的控制难点 连续搅拌反应釜温度控制的难点主要反应在:
(1)复杂性、时滞性和非线性ls;a)化学反应的生产过程伴随着物理化学反应、生化反应、相变过程及物质和能量的转换和传递,因而是一个十分复杂的工业生产过程;b)所用反应釜容量大、釜壁厚,因此是一个热容量大、纯滞后时间长的被控对象;c)随着反应的进行,各传热媒体的传热系数成非线性变化,并且对各种外界环境的变化比较敏感;加上反应过程增益变化也会很大,甚至增益变化方向都是不一样的;而且,随着反应的进行,釜内固体颗粒增多,釜的传热系数也会随着发生不规则变化。 (2)难控性a)反应过程中,由于化学反应放热过程的复杂性和非线性,各传热媒体的传热系数成非线性变化,并对各种外部干扰的影响较敏感,使得控制有一定的难度;b)反应过程中如果热量移去不及时、不均匀,会使反应温度一直往上升,极易因局部过热而造成“飞温”现象,产生“爆聚”;反之,如果热量移去过多,会造成反应温度一直往下跌,造成反应熄灭。而聚合反应好坏的主要因素就是反应釜温度控制的好坏,温度的变化将直接影响产品的质量和产量,所以此过程的温度控制是重点也是难点;c)反应工艺以及反应设备的约束及外界环境对反应影响的不确定性因素也使得控制的难度增加。 (3)建模难反应过程化学反应机理较为复杂,尤其是聚合反应过程涉及物料、能量的平衡,反应动力学等,加上外界条件如原料纯度、催化剂类型、原料添加数量的变化、热水温度、循环冷却液流量的变化等对系统的影响较大,推导机理模型较为困难;又由于化
连续搅拌反应釜系统的设计与仿真
吉林化工学院毕业设计说明书 连续搅拌反应釜系统的控制器设计与仿真Controller Design and Simulation for CSTR 学生学号:11510210 学生姓名:严新宇 专业班级:自动1102 指导教师:王野 职称:工程师 起止日期:2015.03.09~2015.06.26 吉林化工学院 Jilin Institute of Chemical Technology
吉林化工学院信控学院毕业设计说明书 摘要 连续搅拌反应釜(CSTR)是发酵、化工、石油生产、生物制药等工业生产过程中应用最广泛的一种化学反应器,其控制质量直接影响到生产的效益和质量指标。对连续搅拌反应釜通过控制内部的工艺参数,如温度、压力、浓度等稳定,保证反应的正常运行。本文针对连续搅拌反应釜的数学模型,应用泰勒展开得到了线性状态空间表达式,在此基础上设计了LQR控制器,仿真结果表明,控制效果令人满意。 本设计将CSTR的非线性动态模型进行了输入输出线性化,得到CSTR线性状态空间模型。设计出连续搅拌反应釜的极点配置控制器并对系统进行仿真。设计出连续搅拌反应釜的LQR控制器并对其系统进行仿真。并对两种控制方法的控制效果进行了比较。 关键词:连续反应搅拌釜;LQR控制器;MATLAB仿真 I
连续搅拌反应釜系统的控制器设计与仿真 Abstract Continuous stirred tank reactor (CSTR) is the most widely used in fermentation, chemical engineering, petroleum production, bio pharmaceutical and other industrial production process as a chemical reactor, control the quality directly affect the production efficiency and quality index. For continuous stirred tank reactor by controlling the process parameters, such as temperature, pressure, concentration and so on, ensure the normal operation of the reaction. In this paper, based on a continuous stirred reactor mathematical model, the application of Taylor expansion is obtained for the linear state space representation, on this basis, design the LQR controller. Simulation results show that the control effect is satisfactory. In this paper, the nonlinear dynamic model of CSTR is linearized, and the CSTR linear state space model is obtained. The pole assignment controller for continuous stirred tank reactor was designed and the simulation of the system was carried out. The LQR controller of the continuous stirred tank reactor is designed and the system is simulated. The control effect of the two control methods is compared. Key Words: Continuous Stirred Tank; LQR Controller; MATLAB Simulation II
立式搅拌反应釜设计
立式搅拌反应釜工艺设计 1. 推荐的设计程序 1.1 工艺设计 1、做出流程简图; 2、计算反应器体积; 3、确定反应器直径和高度; 4、选择搅拌器型式和规格; 5、按生产任务计算换热量; 6、选定载热体并计算K 值; 7、计算传热面积; 8、计算传热装置的工艺尺寸; 9、计算搅拌轴功率; 1.2 绘制反应釜工艺尺寸图 1.3 编写设计说明书 2. 釜式反应器的工艺设计 2.1 反应釜体积的计算 2.1.1 间歇釜式反应器 V a =V R /φ (2-1) V D =F v (t+t 0) (2-2) 式中 V a —反应器的体积,m 3; V R —反应器的有效体积,m 3。 V D —每天需要处理物料的体积,m 3。 F v —平均每小时需处理的物料体积,m 3/h ; t 0 —非反应时间,h ; t —反应时间,h ; ? =A x R A A A V r dx n t 0 (2-3) 等温等容情况下 ? =A x A A A r dx C t 0 0 (2-4)
对于零级反应 A A x k C t 0 = (2-5) 对一级反应 A x k t -= 11ln 1 (2-6) 对二级反应 2A →P ;A+B →P (C A0=C B0) () A A A x kC x t -= 100 (2-7) 对二级反应 A+B →P ()A B A B x x C C k t ---= 11ln 100 (2-8) φ—装料系数,一般为0.4~0.85,具体数值可按下列情况确定: 不带搅拌或搅拌缓慢的反应釜 0.8~0.85; 带搅拌的反应釜 0.7~0.8; 易起泡沫和在沸腾下操作的设备 0.4~0.6。 2.2反应器直径和高度的计算 在已知搅拌器的操作容积后,首先要选择罐体适宜的长径比(H/D),以确定罐体直径和高度。长径比的确定通常采用经验值,即2-1 表2-1 罐体长径比经验表 在确定了长径比和装料系数之后,先忽略罐底容积,此时 ??? ? ??≈ ≈ i i i D H D H D V 32 44 π π (2-9) 选择合适的高径比,将上式计算结果圆整成标准直径。椭圆封头选择标准件,其内径与筒体内径相同。可参照《化工设备机械基础课程设计指导书》的附录查找。通过式(2-10)得出罐体高度。 π 4 2?-= i D V V H 封 (2-10) 其中 V 封——封头容积,m 3
连续搅拌釜式反应器(CSTR)控制系统设计 连续
连续连续搅拌釜式反应器搅拌釜式反应器搅拌釜式反应器((CSTR )控制系统设计 1. 前言 连续搅拌釜式反应器(continuous stirred tank reactor ,简称为CSTR )是聚合化学反应中广泛使用的一种反应器,该对象是过程工业中典型的、高度非线性的化学反应系统。 在早期反应釜的自动控制中,将单元组合仪表组成位置式控制装置,但是化学反应过程一般都有很强的非线性和时滞性,采用这种简单控制很难达到理想的控制精度。随着计算机技术和PLC 控制器的发展,越来越多的化学反应采用计算机控制系统,控制方法主要为数字PID 控制。但PID 控制是一种基于对象有精确数学模型的线性过程,而CSTR 模型最主要的一个特征就是非线性,因此PID 控制在这一过程中的应用受到限制。随着现代控制理论和智能控制的发展,更加先进有效的控制方法应用于CSTR 的控制,如广义预测控制,神经模糊逆模PID 复合控制,自抗扰控制,非线性最优控制,基于逆系统方法控制,基于补偿算子的模糊神经网络控制,CSTR 的非线性H ∞控制等。但任何一种复杂的化工反应过程都不能用一种简单的控制方式达到理想的控制效果。目前先进的反应釜智能控制技术就是将智能控制理论和传统的控制方法相结合,如钟国情、何应坚等于1998年对基于专家系统的CSTR 控制系统进行了研究[1],宫会丽、杨树勋等于2003年发表了关于PID 参数自适应控制的新方法[2],冯斌、须文波等于1999年阐述了利用遗传算法的寻优PID 参数的模型参考自适应控制方法等[3]。但由于这些控制方法的算法比较复杂,在算法的工程实现、现场调试及通用型方面存在着局限性,因此研究一种相对简单实用的CSTR 控制方法,更易为工程技术人员所接受。 本文在对CSTR 过程及其数学模型进行详细分析的基础上,针对过程的滞后性,采用Smith 预估算法与PID 控制相结合的方法实现CSTR 过程的控制,该方法具有实用性强及控制方法简单等特点,基于西门子PCS7系统完成了CSTR 过程控制系统设计。 2.工艺过程及数学模型工艺过程及数学模型分析分析 2.1 CSTR 工艺过程分析 CSTR 在化工生产的核心设备中占有相当重要的地位,在染料、医药试剂、食品及合成材料工业中,CSTR 得到了广泛的应用。 在CSTR 中,反应原料以稳定的流速进入反应器,反应器的反应物料以同样稳定流速流出反应器。由于强烈搅拌的作用,刚进入反应器的新鲜物料与已存留在反应器的物料在瞬间达到完全混合,使釜内物料的浓度和温度处处相等。同样,在反应器出口处即将流出反应器的物料浓度也应该与釜内物料浓度一致,因此流出反应器的物料浓度与反应器内的的物料浓度相等。连续搅拌釜式反应器中的反应速率即由釜内物料的温度和浓度决定。 2.2 CSTR 的数学模型分析 CSTR 是一个存在严重非线性的动态系统,针对该系统的建模、状态估计和控制都存在着相当的难度。一般常规的线性控制方法已不能满足要求,为了提高其性能,必须采用先进的控制技术。 本文针对某化工过程CSTR 系统,在符合实际情况的条件下假设:系统物料混合是完全的;流出物料的体积等于流入物料的体积;同时不失一般性,假定反应釜中所发生的是一级不可逆放热反应。系统的结构如图1所示。
连续搅拌釜式反应器课程设计报告书
摘要 在工业过程中,温度是最常见的控制参数之一,反应器温度控制是典型的温度控制系统。对温度的控制效果将影响生产的效率和产品的质量,如果控制不当,将损害工艺设备,甚至对人身安全造成威胁。因此反应器温度的控制至关重要。 连续搅拌釜式反应器是化学生产的关键设备,是一个具有大时滞、非线性和时变特性、扰动变化激烈且幅值大的复杂控制对象。结合控制要求,通过分析工艺流程,本论文设计了串级PID分程控制方案。方案选定后,进行了硬件和软件的选择。硬件上选用西门子公司的S7-200 PLC,并用相应的STEP7软件编程。利用Matlab 7.0对系统进行了仿真。 关键词:温度反应器串级PID 西门子S7-200PLC
Abstract In the industrial process, temperature is one of the most common control parameters, reactor temperature control system is a typical temperature control system. The temperature control effect will influence the production efficiency and product quality, if it is not controlled properly, process equipment will be damaged, even personal safety will be threatened. Thus the reactor temperature control is essential. Continuous stirred tank reactor is the key equipment in chemical production, it is a complicated control object with a large time delay, nonlinearity,time-varying characteristics and drastic changes and large amplitude disturbance. Combined with the control requirements, in this paper I design the cascade PID control scheme after a careful analysis of the production process.The hardware and software selection are done following the selection of control scheme. As to hardware, the S7-200 PLC of Siemens is chosen, and the corresponding software STEP7 is chosen for programming.Matlab7.0 work for the simulation. Keywords:temperature cascade PID Siemens S7-200 PLC
【CN109870908A】一种用于连续搅拌釜式反应器系统的采样控制方法【专利】
(19)中华人民共和国国家知识产权局 (12)发明专利申请 (10)申请公布号 (43)申请公布日 (21)申请号 201910146505.1 (22)申请日 2019.02.27 (71)申请人 南京理工大学 地址 210094 江苏省南京市玄武区孝陵卫 200号 (72)发明人 李实 邹文成 张晶 向峥嵘 (74)专利代理机构 南京理工大学专利中心 32203 代理人 马鲁晋 (51)Int.Cl. G05B 13/04(2006.01) (54)发明名称 一种用于连续搅拌釜式反应器系统的采样 控制方法 (57)摘要 本发明公开了一种用于连续搅拌釜式反应 器系统的采样控制方法,该方法包括以下步骤: 首先建立连续搅拌釜式反应器系统的状态空间 模型;然后对于一个采样周期内系统不发生切换 时与一个采样周期内系统发生切换时的情况,分 别构造相应的李雅普诺夫函数,并设置相应的控 制率;最后设置采样周期与平均驻留时间以使构 造的李雅普诺夫函数有界,证明闭环系统的稳定 性,从而完成连续搅拌釜式反应器系统的采样控 制方法。本发明的采样控制方法使连续搅拌釜式 反应器系统在不同运行条件下具有更好的性能 与鲁棒性,且方法简单,使控制成本显著降低,且 更加便于用微处理器实现,具有较高的工程实用 价值。权利要求书4页 说明书5页 附图1页CN 109870908 A 2019.06.11 C N 109870908 A
1.一种用于连续搅拌釜式反应器系统的采样控制方法,其特征在于,包括以下步骤:步骤1、根据连续搅拌釜式反应器系统结构图,建立连续搅拌釜式反应器系统的模型,然后建立连续搅拌釜式反应器系统的状态空间模型; 步骤2、根据步骤1建立的连续搅拌釜式反应器系统的状态空间模型,构造当一个采样周期内系统不发生切换时的李雅普诺夫函数,并设置相应的控制率; 步骤3、根据步骤1建立的连续搅拌釜式反应器系统的状态空间模型,构造当一个采样周期内系统发生切换时的李雅普诺夫函数,并设置相应的控制率; 步骤4、在步骤2和步骤3的基础上,设置采样周期与平均驻留时间以使构造的李雅普诺夫函数有界,即完成连续搅拌釜式反应器系统的采样控制。 2.根据权利要求1所述的用于连续搅拌釜式反应器系统的采样控制方法,其特征在于,步骤1所述根据连续搅拌釜式反应器系统结构图,建立连续搅拌釜式反应器系统的模型,然后建立连续搅拌釜式反应器系统的状态空间模型,具体为: 步骤1-1、根据连续搅拌釜式反应器系统结构图,建立连续搅拌釜式反应器系统的模型 为: 式中,C A 为反应物A浓度,为反应物入口浓度,为反应物入口温度,T 1为反应器温度,V为反应器的体积,V ρ为流体的体积,C P 为流体的热容量,R为气体常数,E为活化能,q σ为进料流速,UA为传热常数,T c 为冷却液温度,a 0为反应速率常数,ΔH为反应焓,f为饲料流指数,ρ为流体密度,为“*”的导数; 步骤1-2、由步骤1- 1的模型建立连续搅拌釜式反应器系统的状态空间模型为: 式中,x 1,x 2均代表系统状态,h 1,σ(t),h 2,σ(t)代表控制增益,f 1,σ(t),f 2,σ(t)代表未知连续非线性函数,σ(t)为切换信号,u代表控制器输入, 表示为如下形式: 式中,t k 为采样点,k为正整数。 3.根据权利要求2所述的用于连续搅拌釜式反应器系统的采样控制方法,其特征在于,步骤2所述根据步骤1建立的连续搅拌釜式反应器系统的状态空间模型,构造一个当采样周期内系统不发生切换时的李雅普诺夫函数,并设置相应的控制率,具体为: 当一个采样周期内系统不发生切换时,即当切换信号满足如下形式时: σ(t k )=σ(t k+1)=l (4) 式中,l为切换的第l个子系统; 权 利 要 求 书1/4页2CN 109870908 A
连续搅拌釜式反应器设计
学院:化工学院 专业:化学工程与工艺
目录 一、设计任务.............................................................................................................................. - 1 - 二、确定反应器及各种条件...................................................................................................... - 1 - 三、反应釜相关数据的计算...................................................................................................... - 1 - 1.体积................................................................................................................................... - 1 - 2.内筒的高度和内径........................................................................................................... - 2 - 3.内筒的壁厚....................................................................................................................... - 2 - 四、夹套的计算.......................................................................................................................... - 3 - 1.夹套的内径和高度........................................................................................................... - 3 - 2.夹套壁厚........................................................................................................................... - 3 - 五、换热计算.............................................................................................................................. - 3 - 1.所需的换热面积............................................................................................................... - 3 - 2.实际换热面积................................................................................................................... - 4 - 3.冷却水流量....................................................................................................................... - 4 - 六、搅拌器的选择...................................................................................................................... - 4 - 七、设计结果一览表................................................................................................................ - 5 - 八、参考文献................................................................................................. 错误!未定义书签。
实验三 连续搅拌釜式反应器液相反应的动力学参数测定
实验三 连续搅拌釜式反应器液相反应的动力学参数测定 一、实验目的 连续流动搅拌釜式反应器与管式反应器相比较,就生产强度或溶剂效率而论,搅拌釜 式反应器不如管式反应器,但搅拌釜式反应器具有其独特性能,在某些场合下,比如对于 反应速度较慢的液相反应,选用连续流动的搅拌釜式反应器就更为有利,因此,在工业上, 这类反应器有着特殊的效用。 对于液相反应动力学研究来说,间歇操作的搅拌釜式反应器和连续流动的管式反应器 都不能直接测得反应速度,而连续操作的搅拌釜式反应器却能直接测得反应速度。但连续 流动搅拌釜式反应器的性能显著地受液体的流动特性的影响。当连续流动搅拌釜式反应器 的流动状况达到全混流时,即为理想流动反应器——全混流反应器,否则为非理想流动反 应器。在全混流反应器中,物料的组成和反应温度不随时间和空间而变化,即浓度和温度 达到无梯度,流出液的组成等于釜内液的组成。对于偏离全混流的非理想流动搅拌釜式反 应器,则上述状况不复存在。因此,用理想的连续搅拌釜式反应器(全混流反应器)可以 直接测得本征的反应速度,否则,测得的为表观反应速度。 用连续流动搅拌釜式反应器进行液相反应动力学,通常有三种实验方法:连续输入法、 脉冲输入法和阶跃输入法。本实验采用连续输入的方法,在定常流动下,实验测定乙酸乙 酯皂化反应的反应速度和反应常数。同时,根据实验测得不同温度下的反应速度常数,求 取乙酸乙酯皂化反应的活化能,进而建立反应速度常数与温度关系式(Arrhenius formula ) 的具体表达式。通过实验练习初步掌握一种液相反应动力学的实验研究方法。并进而加深 对连续流动反应器的流动特性和模型的了解;加深对液相反应动力学和反应器原理的理解。 二、实验原理 1.反应速度 连续流动搅拌釜式反应器的摩尔衡算基本方程: dt dn dV r F F A v A A AO =---?)(0 (1) 对于定常流动下的全混流反应器,上式可简化为 0)(=---V r F F A A AO (2) 或可表达为 V F F r A AO A -=-)( (3) 式中;AO F ——流入反应器的着眼反应物A 的摩尔流率, 1-?s mol ; A F ——流出反应器的着眼反应物A 的摩尔流率, 1-?s mol ; )(A r -——以着眼反应物A 的消耗速度来表达的反应速度,13--??s m mol ;由全 混流模型假设得知反应速度在反应器内一定为定值。 V ——反应器的有效容积,3-m ;
搅拌反应釜设计
<<化工容器>>课程设计 —搅拌反应釜设计 姓名: 余景超 学号: 2010115189 专业: 过程装备与控制工程 学院: 化工学院 指导老师: 淡勇老师 2013年 6 月18 日
目录一设计内容概述 1. 1 设计要求 1. 2 设计参数 1. 3 设计步骤 二罐体和夹套的结构设计 2. 1 几何尺寸 2. 2 厚度计算 2. 3 最小壁厚 2. 4 应力校核 三传动部分的部件选取 3.1 搅拌器的设计 3.2 电机选取 3.3 减速器选取 3.4 传动轴设计 3.5 支撑与密封设计 四标准零部件的选取 4.1 手孔 4.2 视镜
4.3 法兰 4.4 接管五参考文献
一设计内容概述 (一)设计内容:设计一台夹套传热式配料罐 设计参数及要求 容器内夹套内 工作压力,MPa 0.18 0.25 设计压力,MPa 0.2 0.3 工作温度,℃100 130 设计温度,℃120 150 介质染料及有 机溶剂 冷却水或蒸汽 全容积, 3 m 1.0 操作容积, 3 m0.80 传热面积, 2 m 3 腐蚀情况微弱推荐材料Q235--A 接管表 符号公称尺 寸DN 连接面形 式 用途 A 25 蒸汽入口 B 25 加料口 C 80 视镜 D 65 温度计管口 E 25 压缩空气入口 F 40 放料口 G 25 冷凝水出口 H 100 手孔
(二)设计要求: 压力容器的基本要求是安全性和经济性的统一。安全是前提,经济是目标,在充分保证安全的前提下,尽可能做到经济。经济性包括材料的节约,经济的制造过程,经济的安装维修。 搅拌容器常被称为搅拌釜,当作反应器用时,称为搅拌釜式反应器,简称反应釜。反应釜广泛应用于合成塑料、合成纤维、合成橡胶、农药、化肥等行业。反应釜由搅拌器、搅拌装置、传动装置、轴封装置及支座、人孔、工艺接管等附件组成。 压力容器的设计,包括设计图样,技术条件,强度计算书,必要时还要包括设计或安装、使用说明书。若按分析设计标准设计,还应提供应力分析报告。强度计算书的内容至少应包括:设计条件,所用规范和标准、材料、腐蚀裕度、计算厚度、名义厚度、计算应力等。设计图样包括总图和零部件图。 设计条件,应根据设计任务提供的原始数据和工艺要求进行设计,即首先满足工艺设计条件。设计条件常用设计条件图表示,主要包括简图,设计要求,接管表等内容。简图示意性地画出了容器的主体,主要内件的形状,部分结构尺寸,接管位置,支座形式及其它需要表达的内容。 (二)设计参数和技术性能指标 (三)设计步骤: 1.进行罐体和夹套设计计算; 2.搅拌器设计; 3.传动系统设计; 4.选择轴封; 5.选择支座形式并计算; 6.手孔校核计算; 7.选择接管,管法兰,设备法兰。
连续搅拌釜式反应器(CTRS)控制系统设计
河南工业大学 开放实验室实验项目设计报告连续搅拌釜式反应器(CTRS)控制系统设计 学校:河南工业大学 学院:机电工程学院 专业:机械设计制造及其自动化 姓名:冷会昌 学号:20074050602
目录 1 前言 (2) 2 工艺过程简介 (2) 2、1 过程变量说明 (3) 2、2 操作变量说明 (3) 3 反应过程特性 (3) 4 实验内容 (5) 5 反应过程开车及正常运行 (6) 6 开车步骤顺序控制 (7) 7 思考题 (8) 8 心得体会 (9)
连续搅拌釜式反应器(CTRS)控制系统设计 1、前言 本连续反应过程是工业常见的典型的带搅拌的釜式反应器(CSTR)系统,同时又是高分子聚合反应。本实验是当前全实物实验根本无法进行的复杂、高危险性实验,又是非常重要的基础反应动力学实验和反应系统控制实验内容。此外,全实物实验还面临物料消耗、能量消耗、反应产物的处理、废气废液的处理和环境污染问题,以上各项问题比间歇反应更严重,因为连续反应的处理量大大超过间歇过程。现有的连续反应实验系统实际上都是水位及流量系统,根本没有反应现象。在本连续反应实验系统上除了进行常规控制系统实验外,还可以进行模糊控制、优化控制、深层知识专家系统(例如SDG法)故障诊断等高级控制实验。 2、工艺过程简介 连续反应实验系统以液态丙烯为单体、以液态已烷为溶剂,在催化剂与活化剂的作用下,在反应温度70 1.0℃下进行悬浮聚合反应,得到聚丙烯产品。 在工业生产中为了提高产量,常用两釜或多釜串联流程。由于在每一个反应釜中的动态过程内容相似,为了提高实验效率、节省实验时间,特将多釜反应器简化为单反应器连续操作系统。 丙烯聚合反应是在己烷溶剂中进行的,采用了高效、高定向性催化剂。己烷溶剂是反应生成物聚丙烯的载体,不参与反应,反应生成的聚丙烯不溶于单体丙烯和溶剂,反应器内的物料为淤浆状,故称此反应为溶剂淤浆法聚合。 见图1-1所示,连续反应实验系统包括:带搅拌器的釜式反应器。反应器为标准盆头釜,为了缩短实验时间,必须减小时间常数,亦即缩小反应器容积,缩小后的反应器尺寸为:直径1000 mm,釜底到上端盖法兰高度1376 mm,反应器总容积1.037 m3 ,反应釜液位量程选定为0-1300 mm (0-100%)。反应器耐压约2.5MPa,为了安全,要求反应器在系统开、停车全过程中压力不超过1.5 MPa。反应器压力报警上限组态值为1.2 MPa。 丙烯聚合反应过程主要有三种连续性进料(控制聚丙烯分子量的氢气在实验中不考虑),第一种是常温液态丙烯,F4为丙烯进料流量、V4是丙烯进料双效阀;第二种是常温液态己烷,F5己烷进料流量、V5己烷进料阀;第三种是来自催化剂与活化剂配制单元的常温催化剂与活化剂的混合液,F6为催化剂混合液进料流量、V6催化剂混合液进料阀。催化剂可以用三氯化钛(TiCl3),活化剂可以用一氯二乙基铝(Al(C2H5)2Cl),两种化合物用己烷溶剂稀释成混合液,催化剂浓度4%,活化剂与催化剂克分子浓度之比为2∶1。由于催化剂量小,常用计量泵控制,在本实验中用精小型控制阀代替。 反应器内主产物聚丙烯重量百分比浓度为A,反应温度为T1,液位为L4。反应器出口浆液流量F9,出口双效阀V9,出口泵,出口泵开关S5(开关),反应器夹套第一冷却水入口流量F7,双效阀V7,反应器夹套第二冷却水入口流量F8,双效阀V8,反应器夹套加热热水阀S6(开关),反应器搅拌电机开关S8。 2、1 过程变量说明 连续反应实验系统在盘面所涉及的传感器输出变量、变量正常工况的数据、计量单位如
实验二 连续搅拌釜式反应器液相反应的动力学参数测定
实验二 连续搅拌釜式反应器液相反应的动力学参数测定 一、实验目的 连续流动搅拌釜式反应器与管式反应器相比较,就生产强度或溶剂效率而论,搅拌釜式反应器不如管式反应器,但搅拌釜式反应器具有其独特性能,在某些场合下,比如对于反应速度较慢的液相反应,选用连续流动的搅拌釜式反应器就更为有利,因此,在工业上, 这类反应器有着特殊的效用。 对于液相反应动力学研究来说,间歇操作的搅拌釜式反应器和连续流动的管式反应器都不能直接测得反应速度,而连续操作的搅拌釜式反应器却能直接测得反应速度。但连续流动搅拌釜式反应器的性能显著地受液体的流动特性的影响。当连续流动搅拌釜式反应器的流动状况达到全混流时,即为理想流动反应器——全混流反应器,否则为非理想流动反应器。在全混流反应器中,物料的组成和反应温度不随时间和空间而变化,即浓度和温度达到无梯度,流出液的组成等于釜内液的组成。对于偏离全混流的非理想流动搅拌釜式反应器,则上述状况不复存在。因此,用理想的连续搅拌釜式反应器(全混流反应器)可以 直接测得本征的反应速度,否则,测得的为表观反应速度。 用连续流动搅拌釜式反应器进行液相反应动力学,通常有三种实验方法:连续输入法、脉冲输入法和阶跃输入法。本实验采用连续输入的方法,在定常流动下,实验测定乙酸乙酯皂化反应的反应速度和反应常数。同时,根据实验测得不同温度下的反应速度常数,求取乙酸乙酯皂化反应的活化能,进而建立反应速度常数与温度关系式(Arrhenius formula )的具体表达式。通过实验练习初步掌握一种液相反应动力学的实验研究方法。并进而加深对连续流动反应器的流动特性和模型的了解;加深对液相反应动力学和反应器原理的理解。 二、实验原理 1.反应速度 连续流动搅拌釜式反应器的摩尔衡算基本方程: dt dn dV r F F A v A A AO = -- -? )(0 (1) 对于定常流动下的全混流反应器,上式可简化为 0)(=---V r F F A A AO (2) 或可表达为 V F F r A AO A -= -)( (3) 式中;AO F ——流入反应器的着眼反应物A 的摩尔流率, 1 -?s mol ; A F ——流出反应器的着眼反应物A 的摩尔流率, 1 -?s mol ; )(A r -——以着眼反应物A 的消耗速度来表达的反应速度,1 3 --??s m mol ;由全 混流模型假设得知反应速度在反应器内一定为定值。 V ——反应器的有效容积,3 -m ;