先进铸造工艺在汽车制造中的应用

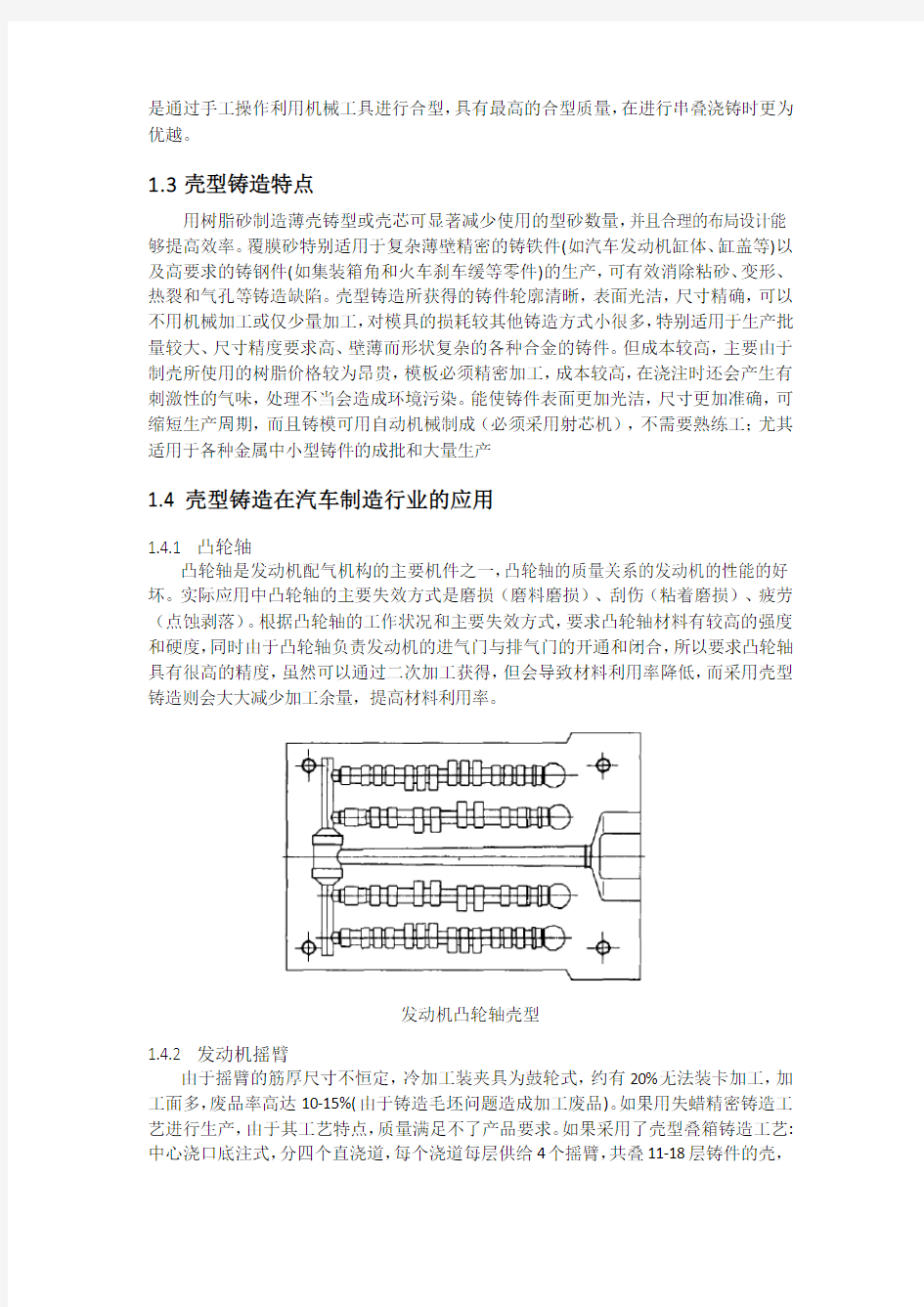
先进铸造工艺在汽车制造中的应用
绪论:随着铸造工艺的不断创新,汽车制造业也随之不断进行着技术改革。本文着重介绍几种先进的铸造工艺的原理、方法及其在汽车制造业中的应用。
关键词:汽车制造壳型铸造半固态铸造挤压铸造消失模铸造
1 壳型铸造在汽车行业的应用
1.1 壳型铸造
壳型铸造就是利用遇热硬化的型砂覆盖在被加热的金属模板表面,使其硬化后形成一层薄壳,用薄壳铸型生产铸件的铸造方法。型砂一般为硅砂或锆砂与树脂的混合料或树脂覆模砂,浇注铸件金属模板的加热温度一般为300℃左右,所形成的薄壳厚度一般为6~12毫米,但其具有足够的强度和刚度,耐高温。因此将上下两片型壳用夹具卡紧或用树脂粘牢后,不用砂箱即可构成铸型。同样也可用上述方法将型芯制成薄壳芯,制造薄壳铸型常用翻斗法,制造薄壳芯常用吹制法。
1.2 壳型铸造流程
1.2.1 造型材料的准备
1、树脂与硬化剂的准备:树脂与等量的12%的乌洛托品硬化剂混合并碾碎,之后
通过100号筛,过筛后再次放入混砂机内混合,以确保硬化剂与树脂混合均匀,最后通过瓷球球磨机研磨30分钟,储存在干燥器中备用。
2、型砂准备及活性处理:根据所要制作的铸件造型选用合适的砂型,将选好的砂
粒转入耐热铁箱内,经过900℃的热处理2小时,自然冷后取出,储存在干燥器
中备用。
1.2.2 结壳
1、将模板或者芯盒放在400℃的炉温内加热。
2、加热后取出模板或芯盒,喷以分型剂,喷好分型剂后模板温度不应低于220℃。
3、将模板或芯盒卡紧在翻斗或者吹芯机上结壳,使型砂均匀覆盖在模板或者芯盒
上,结壳厚度为6~12毫米。
4、取下模板及芯盒,在400℃炉温下硬化,硬化后利用顶壳机顶出壳体。
1.2.3 合型和浇铸
合型通常有粘合法和夹合法两种。粘合法多用一级反应树脂做粘合剂,通常在壳型温度较高时进行粘合,或者另行加热粘合,粘合法可以保证最快的粘合速度。夹合法则
是通过手工操作利用机械工具进行合型,具有最高的合型质量,在进行串叠浇铸时更为优越。
1.3壳型铸造特点
用树脂砂制造薄壳铸型或壳芯可显著减少使用的型砂数量,并且合理的布局设计能够提高效率。覆膜砂特别适用于复杂薄壁精密的铸铁件(如汽车发动机缸体、缸盖等)以及高要求的铸钢件(如集装箱角和火车刹车缓等零件)的生产,可有效消除粘砂、变形、热裂和气孔等铸造缺陷。壳型铸造所获得的铸件轮廓清晰,表面光洁,尺寸精确,可以不用机械加工或仅少量加工,对模具的损耗较其他铸造方式小很多,特别适用于生产批量较大、尺寸精度要求高、壁薄而形状复杂的各种合金的铸件。但成本较高,主要由于制壳所使用的树脂价格较为昂贵,模板必须精密加工,成本较高,在浇注时还会产生有刺激性的气味,处理不当会造成环境污染。能使铸件表面更加光洁,尺寸更加准确,可缩短生产周期,而且铸模可用自动机械制成(必须采用射芯机),不需要熟练工;尤其适用于各种金属中小型铸件的成批和大量生产
1.4 壳型铸造在汽车制造行业的应用
1.4.1 凸轮轴
凸轮轴是发动机配气机构的主要机件之一,凸轮轴的质量关系的发动机的性能的好坏。实际应用中凸轮轴的主要失效方式是磨损(磨料磨损)、刮伤(粘着磨损)、疲劳(点蚀剥落)。根据凸轮轴的工作状况和主要失效方式,要求凸轮轴材料有较高的强度和硬度,同时由于凸轮轴负责发动机的进气门与排气门的开通和闭合,所以要求凸轮轴具有很高的精度,虽然可以通过二次加工获得,但会导致材料利用率降低,而采用壳型铸造则会大大减少加工余量,提高材料利用率。
发动机凸轮轴壳型
1.4.2 发动机摇臂
由于摇臂的筋厚尺寸不恒定,冷加工装夹具为鼓轮式,约有20%无法装卡加工,加工面多,废品率高达10-15%(由于铸造毛坯问题造成加工废品)。如果用失蜡精密铸造工艺进行生产,由于其工艺特点,质量满足不了产品要求。如果采用了壳型叠箱铸造工艺:中心浇口底注式,分四个直浇道,每个浇道每层供给4个摇臂,共叠11-18层铸件的壳,
总计176-288件摇臂,生产率特别高。同时可以使废品率降到了2-4%左右,并且大大提高了生产率,满足一了生产与质量要求,同时也大大地改善了劳动环境。
发动机摇臂壳型铸件
此外,壳型铸造工艺还广泛应用于排气管、差速器外壳及其他外形尺寸要求很高的工程机械铸件,例如用于机械密封的特种铸铁耐磨环,以及其它要求较高、批量较大的高精度铸件等。
1.5 熔模壳型铸造
熔模铸造是一种灵活铸造工艺,由于用该工艺成型的铸件与零件间具有较高的尺寸相似性,所以又称熔模精密铸造。该工艺是使用熔点低的材料制成尺寸精确且表面光度好的零件模型,然后使用耐高温粘结剂与耐火粉料以及辅助添加剂配置成糊状涂料涂覆在熔模表面并撒上合适的骨料,等待涂料干燥硬化,重复上述操作制得具有一定厚度的型壳,然后加热型壳脱掉熔模。最后再将脱模好的型壳高温焙烧,形成具有较高强度的陶瓷型壳。制壳完毕后再向型腔内浇注入金属液,待金属液冷却凝固后去掉陶瓷型壳就能获得与熔模不论是尺寸还是表面光洁度都一致的镁合金铸件。
熔模壳型铸造工艺图
1.6 消失模壳型铸造
镁合金消失模铸造是目前比较先进的镁合金精密铸造工艺之一,该工艺过程是:首先将合适密度的EPS泡沫发泡成与镁合金铸造零件相同的形状(一般将这种泡沫模型叫做白模),并将它们与泡沫制成的浇注系统相粘连成零件模型树。然后利用粘结剂和耐
火粉料配置成消失模涂料,再将配置好的涂料浸涂或刷涂到白模表面,形成均匀的涂料层。接下来将耐火涂料低温(低于EPS泡沫的膨胀变形温度)烘干后,埋在干砂子中震动紧实。最后将熔融金属液直接导入铸型浇口进行浇注,在金属液进入过程中,白模汽化并且金属液迅速取代白模位置,最后等待金属液冷却凝固的到精密度尺寸精密较高的铸件
消失模壳型铸造工艺图
1.7 发展前景
由于熔模壳型铸造技术和消失模壳型铸造技术的出现,使得壳型铸造不仅能够生产较为规则的具有分型面的零件,还能够生产较为复杂的不具有分型面的不规则零件。可以预见,壳型铸造由于其较高的加工精度及表面粗糙度,将会在汽车等精密铸造行业发挥更大的作用。
2 半固态铸造在汽车制造行业的应用
2.1 半固态铸造
半固态铸造成形的原理是在液态金属的凝固过程中进行强烈搅拌,使普通铸造易于形成的树枝晶网络骨架被打碎而保留分散的颗粒状组织形态。这是因为在普通铸造过程中,初晶以枝晶方式长大,当固相率达到20%左右时,枝晶就形成连续网络骨架,失去宏观流动性,所以需要在金属凝固过程中施以强烈搅拌。
2.2 半固态铸造优点
与传统全液态成形技术相比,它具有以下优点:①在工艺方面:成形温度低(Al合金至少可降低120 ℃);延长模具寿命(由于热冲击小);节省能源(由于工艺周期缩短);改善生产条件和环境。②在产品方面:铸件质量提高(减少气孔和凝固收缩);减少加工余量;扩大压铸合金的范围并可以发展金属基复合材料。要实现半固态铸造,首先要制备在半固态具有触变性的非枝晶组织合金。
2.3 非枝晶组织合金的制备方法
非枝晶组织合金的制备方法很多,主要有以下几种:
1.机械搅拌法
机械搅拌法的设备比较简单,并且可以通过控制搅拌温度,搅拌速度和冷却速度等工艺参数来研究金属的搅动凝固规律和半固态金属的流变性能,目前实验室研究大多采用此法。
2.电磁搅拌法
电磁搅拌法是利用电磁感应在凝固的金属液中产生感应电流,感应电流在外加磁场的作用下促使金属固液浆料激烈的搅动,使传统的枝晶组织转变为非枝晶的搅拌组织。将电磁搅拌法与连铸技术相结合可以生产连续的搅拌铸锭,这是目前半固态铸造工业应用的主要生产工艺方法。
3.应变激活法
应变激活法是将常规铸锭经热态挤压预变形制成半成品棒料,通过变形破碎组态组织,然后对热变形的棒料再施加少量的冷变形,在组织中预先储存部分变形能量,最后按需要将变形后的金属棒料分切成一定大小,加热到固液两相区等温一定时间,快速冷却后即可获得非枝晶组织铸锭。在加热过程中先是发生再结晶,然后部分熔化,最终球形固相颗粒分散在液相中,获得半固态组织。
2.4 主要制造工艺
美国是研究半固态铸造技术最早的国家,其研究和应用水平在世界处于领先地位。除美国外,欧洲和日本是半固态铸造技术研究和应用的主要地区。在汽车制造工业中,为满足汽车轻量化的要求,铝合金和镁合金是汽车制造业半固态铸造的主要材料。其主要制造工艺如下:
(1)流变铸造
将金属液从液相到固相冷却过程中进行强烈搅动,在一定的固相分数下压铸或挤压成形。由于直接获得的半固态金属浆液的保存和运送很不方便,因而这种成形方法投入实际应用的较少。用此方法所制成的铝合金铸件的力学性能较挤压铸件高,而与半固态触变成形件的性能相当。
(2)触变铸造
将由搅动铸造所制备的锭坯重新加热到半固态进行压铸或挤压成形。由于半固态坯料的加热、输送很方便,易于实现自动化操作,因此半固态合金触变成形是当今半固态铸造的主要工艺方法。
2.5 半固态铸造在汽车制造行业的应用
在镁合金半固态制品生产主要采用射铸
成型;铝合金半固态主要采用触变成型。目
前利用半固态触变成形生产的汽车零件有主
刹车缸体、轮毂、射油道、衬套、支撑件
等,利用射铸成形生产的镁合金汽车零件有
圆片离合器、油泵箱、齿轮箱等。在使用半
固态成型技术生产汽车零件上,欧美发达国
家仍走在前列。比如美国的Alumax公司是世
界首家专业用半固态成形技术生产汽车及其
图:射油器
它零件的厂家,该公司在1994年就建立了可
年产2400万个汽车零件的半固态成形工厂。
意大利的MM公司(Magneti Marelli)为汽车
公司生产的汽车喷油系统中的射油道,质量
要求高,并且要求耐腐蚀,其形状加工难度也大。采用半固态金属压铸成形后,不但质量可以保证,生产费用还比原来降低50%。
2.6 应用前景
虽然我国已是世界制造业大国,仅次于美、日、德,位于世界第四,但由于生产率低,技术含量差,自主创新开发能力不高,还不是制造业强国。汽车,作为制造业的主要产品,必然是新兴制造技术的主要应用领域。半固态金属加工技术与传统的技术相比,前者在提高产品质量、性能、降低能耗和成本;缩短生产流程;有利于环境保护和提高产品市场竞争力等方面具有独特的优势,以此作为我国从铸造大国成为铸造强国的新的重大突破口,既是当今世界范围内出现的环保压力、市场剧烈竞争、贸易自由化、信息技术迅猛发展的挑战,也是促进制造业旺盛发展、开拓广阔市场、不断扩大应用范围的极好机遇。
更重要的是,我国拥有丰富的镁资源,菱镁矿储量居世界首位,原镁产能和产量均居世界首位。但是镁合金在我国汽车制造领域应用还不多,目前只有上海大众桑塔纳轿车的手动变速箱壳体采用了镁合金。而且镁合金产品的80%是通过铸造方法获得的,无疑以此作为突破口,采用半固态镁合金射铸成型技术,必将使我国镁的资源优势转变为技术经济优势,必将增强铸造行业在全球市场中的竞争力。
3 半固态铸造在汽车制造行业的应用
3.1 挤压铸造
挤压铸造也称为液态模锻,是一种集铸造和锻造特点于一体的新工艺,该工艺是将一定量的金属液体直接浇入敞开的金属型内,通过冲头以一定的压力作用于液态或半凝固的金属上,使之充填、成型和结晶凝固,并在结晶过程中产生一定量的塑性变形,从而获得零件毛坯的一种金属成形方法。
挤压铸造金属液是通过浇包直接注入型腔内,充型平稳,上模缓慢下降平稳施压,气体大部分可以从模具间隙中排出,在制件中不易形成气孔。挤压铸造没有浇注系统,压力传递通过上模端面直接施加在金属液面上,金属液始终在压力作用下结晶凝固,流动成形,因而组织致密均一,晶粒细化。在这些方面,挤压铸造优于压力铸造。
3.2 挤压铸造工艺的应用范围
从其工艺特点和国内外实际应用情况来看,挤压铸造工艺的应用范围如下。
(1)在材料种类方面适用性较广,从理论上讲可用于生产各种类型的合金,如铝合金、镁合金、锌合金、灰口铸铁、球墨铸铁、碳钢、不锈钢等。但比较而言,黑色金属挤压铸造的工艺难点较多,且由于受到模具材料的限制,在黑色金属方面的实际应用远没有在有色金属方面的应用广泛。
(2)挤压铸造适宜于一些形状复杂、且性能上又有一定要求的产品。因为形状复杂的工件采用一般模锻方法成形困难,即使能够成形成本也太高。如果采用常规铸造方法,则在产品的性能上又难以达到要求。对于某些特殊产品采用挤压铸造工艺,既能顺利成形,又能保证产品的性能要求。
(3)一般来讲,挤压铸造工件的壁厚不能太薄,否则在结晶和成形方面都会带来一些问题,甚至产生废品。
多年来,国内外厂商,均把此项工艺用做汽车高档有色金属铸件的方法之一,并迅速的
在发展。
国内外挤压铸造汽车主要零部件表
挤压铸造的汽车零件
3.3 挤压铸造适用材料
挤压铸造工艺的一个重要优势,是可适应多种材料的生产,包括铝、镁、铜、锌甚至是钢铁材料。不论是铸造性好的铸造合金,还是铸造性差的变形合金,甚至是需铸造复合的金属基复合材料,都可以按不同的特点,在采取相应措施后进行生产的。而且铸件是可以进行固溶处理实现强化的。
基于工艺的上述优势,因而在汽车铸件的生产上,也实现了材料的多样化,除常用的铸造铝合金外,主要的还有如下几个方面:
3.3.1高硅铝合金
高硅铝合金因有优良的耐磨性和低的热膨胀系数,因而是活塞和空调压缩机缸体、缸盖、活塞、斜盘、涡旋盘等的首选材料,但是此种材料的初晶硅细化问题和高的缩松、裂纹倾向问题,使材料的铸造生产存在较大难度。目前,国内外用挤压铸造工艺较好的解决了此问题。尤其是在厚壁,复杂铸件上解决得较好。这些在国内外都已形成很大的生产批量。
3.3.2 变形铝合金
用直接挤压铸造法可以生产变形铝合金铸件,甚至是铸造性很差的7075、7A04合金都可以生产出优质铸件,而且铸件可以进行固熔热处理强化,此种材料在强度,尤其是塑性和可焊性方面都明显优于A356铸造铝合金。
但是用间接挤压铸造法难以生产变形铝合金铸件,主要是易产生裂纹。因而在一些复杂的铸件上限制了变形合金的使用。近年发展起来的双重挤压铸造和半固态挤压铸造,可以解决此问题,并且已有成功生产的实例,相信今后有一定的发展前景。
3.3.3 镁合金
在汽车上扩大镁合金构件的使用是当前国内外一大发展潮流,前景广阔。为此在镁合金挤压铸造方面都进行了大量工作,并已在镁轮毂,镁壳体件上实现了批生产。
前段时间由于原镁价格的大幅提升,为镁的大量使用造成了不小的阻力,加上镁的熔炼,加工废料回收及抗腐蚀等的技术问题,也给镁件的,也给镁件的生产造成一定难度,但毕竟在汽车节能、环保的总趋势下,镁件的使用仍是方兴未艾的。
3.3.4 金属基复合材料
高性能汽车发动机,尤其是高增压柴油机活塞,当前一个重要发展方向是使用陶瓷纤维增强铝基复合材料,而这正是挤压铸造的工艺优势,日本“IZUMI”和“Art”公司早年就已大批量生产了这种高技术活塞,月产达10万只以上,并已在丰田公司23种车型得到了使用。其它如美国的康明斯、克列威特(Clevite)和德纳(DANA)公司,俄罗斯及欧盟国家的一些公司也都生产使用了这种挤压铸造活塞,我国从上世纪80年代中即开始此种活塞研制,并已在“解放”、“东风”汽油机及特种大马力柴油机上大批量使用。
3.5 挤压铸造在汽车制造业中的应用实例:
3.5.1 发动机活塞
挤压铸造活塞克服了金属型铸造活塞内部缺陷,又克服了锻造活塞机加工量大,成本高,需要重型设备的缺点。,世界各国都把挤压铸造作为汽车活塞生产的方向之一,已制造出直径为90~400ram大小不一的各类挤压铸造活塞。
3.5.2 铝合金轮毂
采用挤压铸造法生产铝合金轮毂,产品既有接近锻件的优良力学性能,又有精铸件一次精密成形的高效率、高精度,且投资大大低于低压铸造法。挤压铸造特别适合于生产汽车工业中的安全性零件,日本在1979年就在轿车上采用了挤压铸造铝合金轮毂,现已有相当部分的汽车铝轮毂采用挤压铸造工艺生产。
3.6 应用前景
挤压铸造是一种新型的金属成形工艺,从兴起到发展已有半个多世纪的历史,随着理论和应用研究的不断完善和发展,其工艺优点越来越受到世人的注目,其在汽车零件生产中的成功应用,显示了该技术具有良好的发展前景。
4消失模铸造
4.1 概念和来历
消失模铸造(又称实型铸造)是将与铸件尺寸形状相似的石蜡或泡沫模型粘结组
合成模型簇,刷涂耐火涂料并烘干后,埋在干石英砂中振动造型,在负压下浇注,使
模型气化,液体金属占据模型位置,凝固冷却后形成铸件的新型铸造方法。
1958年,美国的H.F.shroyer发明了用可发性泡沫塑料模样制造金属铸件的专利
技术并取得了专利。最初所用的模样是采用聚苯乙烯板材加工制成的,采用粘土砂造型,用来生产艺术品铸件。采用这种方法,造型后泡沫塑料模样不必起出,而是在浇入液态金属后,聚苯乙烯在高温下分子裂解,而让出空间充满金属液,凝固后形成铸件。1961年德国的Grunzweig和Harrtmann公司购买了这一专利技术加以开发,并在1962年在工业上得到应用。
采用无粘结剂干砂生产铸件的技术由德国的H.Nellen和美国T.R.Smith于1964
年申请了专利。由于无粘结剂的干砂在浇注过程中经常发生坍塌的现象,所以1967年
德国的A.Wittemoser采用了可以被磁化的铁丸来代替硅砂作为造型材料,用磁力场作为"粘结剂",这就是所谓"磁型铸造"。
1971年,日本的Nagano发明了V法(真空铸造法),受此启发,今天的消失模铸造
在很多地方也采用抽真空的办法来固定型砂。
在1980年以前使用无粘结剂的干砂工艺必须得到美国"实型铸造工艺公司"(Full Mold Process,Inc)"的批准。在此以后,该专利就无效了。因此,近20年来消失模铸造技术在全世界范围内得到了迅速的发展。
4.2 特点
4.2.1 消失模铸造主要具有以下优点:
1.铸件精度高。消失模铸造无需起模,无分型面,无砂芯,因此铸件不存在飞边
毛刺和拔模斜度,减小了型芯组合造成的尺寸误差,与传统铸造相比可减少40%至50%的机械加工量。
2.设计灵活。在设计铸件时更加灵活,不需要考虑分型、拔模等限制条件,可以
通过泡沫塑料模片的组合铸造出高度复杂的零件。
3.清洁生产。型砂中不使用化学粘合剂,主要利用真空法来固定型砂,铸造过程
中温度较低,不会导致泡沫塑料分解,对环境影响较小。
4.成本较低。工艺操作简单,降低了操作工人的培训成本;使用的金属模具寿命
可达10万次以上,降低了模具的维护成本;工厂设计成本降低,节约了固定资产投资。
4.2.2 消失模铸造也存在一些缺点:
1.模具成本较高,小批量的铸件会大幅度提高单个铸件的平均成本
2.铸件材质受到限制,适用性由好至差的顺序大致为灰铸铁——非铁合金——普
通碳素钢——球墨铸铁——低碳钢和合金钢。
3.铸件结构越大越复杂,越能体现出消失模铸造的优势,但是对于内部有狭窄通
道和夹层的铸件要先进行试验才能投入生产。
4.3 消失模铸造在汽车制造行业的应用
自20世纪80年代起,消失模铸造技术就引起了发达国家汽车厂家的兴趣,最早的消失模铸造技术就是从汽车行业开始的。消失模铸造技术特别适合于汽缸体、汽缸盖、进排气歧管等形状复杂、需要砂芯成型的汽车铸件。这是因为大量生产过程中,这类零件铸造的制芯和清理都很麻烦,而消失模铸造恰恰不需要砂芯,简化了清理工序。目前最为成熟的消失模铸造产品包括铝合金铸件(如进气歧管、缸体、缸盖等)、铸铁件(如曲轴、缸盖、变速器壳体等)。比较先进的铸造件包括对于汽车轻量化有重要意义的镁合金铸件,消失模铸造能够节约铸造材料,降低材料成本,进而推动镁合金零件的普及。
美国是最早应用消失模铸造法进行批量生产汽车铸件的国家。福特汽车公司1980年在加拿大的Essex铸铝厂建造了第一条干砂消失模铸造生产线,1984年已实现自动化生产,生产进、排气管及部分气缸盖。2001年通用汽车公司所属的SMCO消失模生产线正式投产,是目前世界上技术最先进,规模最大的消失模生产工厂,其生产的Vortec4200六缸缸体和缸盖是目前最复杂、最有代表性的消失模铸造产品。
我国是世界上较早研究使用消失模铸造的国家之一,略晚于欧洲,几乎与日本同步。但是由于历史原因,长期以来发展缓慢,直到近20年才开始较快发展。早期使用消失模技术进行生产和试生产的厂家全国之有2到3家,年产量不到100吨,而1999年的消失模铸件年产量已超过4万吨。但是,目前我国的消失模铸造技术仍然处于起步阶段,投产的生产线主要依靠外国进口,国产设备相对简陋,自动化程度和产品技术含量较低。由于以上原因,国内采用高度自动化消失模生产线大批量生产汽车铸件的厂家还很少,与国际先进水平还存在着很大的差距。
5结语
随着汽车轻量化越来越被人们关注,各种先进的铸造工艺不断完善,不断创新。在汽车制造中的应用也越来越广泛,在质量越来越好的同时成本也越来越低,越来越受到重视,也不断展示出良好的发展前景。
参考文献
1.陈果,镁合金消失模—壳型复合铸造工艺研究
2.孙嘉良,壳型铸造工艺在汽车铸造中的应用
3.苏以人,低合金铸铁凸轮轴的壳型和金属型铸造
4.张志峰;田战峰;杨必成汽车用铝合金半固态零件触变压铸工艺研究
5.赵大志;路贵民;崔建忠半固态铸造技术的发展状况及前景
6.侯文杰;谭建波;刘江成半固态流变压铸的研究现状与发展趋势
7.苏华钦、胡彬;国内外半固态铸造的工业应用现状及面临的机遇与对策
8.赖华清、余翔、范宏训;半固态铸造工艺及其在汽车生产中的应用
【毕节职业技术学院】-汽车制造与装配技术
毕节职业技术学院汽车制造与 装配技术专业建设方案项目组长:杨慧 项目副组长:孙波周天生张治国彭永贤吕善进项目成员:熊荣谦曹东冬余鹏何志勇张倩 李仲勋刘鹏杜静李世勇王义 陈伟贺丽叶刘世鹏文江李玲珑 蔡泽荣王锦 项目概述:本项目面向毕节试验区汽车装配制造业产业集群,以汽车制造与装配专业建设为重点,带动其专业群(汽车制造与维修、汽车运用与维修等专业)的发展。建设内容包括人才培养模式与课程体系改革、实验实训条件建设、师资队伍建设、校企合作制度与管理运行机制建设等。 本项目建设预算投资250.5万元,其中申请中央财政支持217.5万元,地方财政配套支持20万元,学校自筹投入13万元。 一、汽车制造与装配技术专业建设背景 装备制造业是为国民经济各行业提供技术装备的战略性产业,是高新技术的载体及转化为生产力的桥梁和通道。因此,国家“十二五”规划提出装备制造业要努力实现由“中国制造”向“中国创造”转变。 贵州“十二五”的规划中强调:要大力实施工业强省战略,加快推进产业结构调整升级,在西部地区实现赶超进位,实现经济社会发展历史性跨越的条件更加充分,全面建成小康社会的基础更加牢固。
据测算,我国技能劳动者需求总量将增长 20%-25%,其中高级以上技能劳动者所占比例预计增长 15-20%。据此推算,我国现有高技能人才数量对比企业需求,仍有几百万人的缺口,而且这种需求以每年10.1%的速度增长,构成了制造类人才需求的巨大空间。 毕节地区力帆骏马振兴车辆有限公司是云南力帆骏马车辆有限公司在省外设立的第一家创造生产企业,公司由毕节地区振兴机械厂和云南力帆骏马车辆有限公司合资组建成立。为了扩大生产规模,做大做强毕节地区机械制造加工业,公司决定进行异地技改建厂,于2007年9月正式开工,于2009年5月建成试生产,投产后年设计生产规模为5万辆“振兴”牌系列变型农用车,达到每年20亿元以上的工业产值,新增就业岗位3500个以上。力帆骏马二期技改项目改造,将形成一个年产10万辆轻卡、2万辆重卡的现代化、规模化的各型载荷汽车及配件的生产制造基地,将新增劳动就业2万余人、实现工业生产总产值100亿元以上、新增税收3亿余元。 力帆二期技改项目开工后,园区又以力帆为媒,以商招商,引进浙江万里扬变速器股份有限公司、杭州世宝方向机有限公司等22户规模较大的零部件生产企业进驻园区,并于2011年12月18日与力帆汽车研发中心一同开工。这对于推动毕节高新技术产业基地建设、加快毕节汽车制造与装配业将起到了积极的推动作用。 汽车相关行业突出矛盾是人员素质远远满足不了行业发展需要,由于经过系统学习的汽车专业人员供不应求,导致大量未经任何培训的人员进入汽车行业。据抽样调查,主要存在具有专业技术职称证书比例较低、专业技术管理及经营管理人员结构不
铸造生产的工艺流程
铸造生产的工艺流程 铸造生产是一个复杂的多工序组合的工艺过程,它包括以下主要工序: 1)生产工艺准备,根据要生产的零件图、生产批量和交货期限,制定生产工艺方案和工艺文件,绘制铸造工艺图; 2)生产准备,包括准备熔化用材料、造型制芯用材料和模样、芯盒、砂箱等工艺装备; 3)造型与制芯; 4)熔化与浇注; 5)落砂清理与铸件检验等主要工序。 成形原理 铸造生产是将金属加热熔化,使其具有流动性,然后浇入到具有一定形状的铸型型腔中,在重力或外力(压力、离心力、电磁力等)的作用下充满型腔,冷却并凝固成铸件(或零件)的一种金属成形方法。
图1 铸造成形过程 铸件一般作为毛坯经切削加工成为零件。但也有许多铸件无需切削加工就能满足零件的设计精度和表面粗糙度要求,直接作为零件使用。 型砂的性能及组成 1、型砂的性能 型砂(含芯砂)的主要性能要求有强度、透气性、耐火度、退让性、流动性、紧实率和溃散性等。 2、型砂的组成 型砂由原砂、粘接剂和附加物组成。铸造用原砂要求含泥量少、颗粒均匀、形状为圆形和多角形的海砂、河砂或山砂等。铸造用粘接剂有粘土(普通粘土和膨润土)、水玻璃砂、树脂、合脂油和植物油等,分别称为粘土砂,水玻璃砂、树脂砂、合脂油砂和植物油砂等。为了进一步提高型(芯)砂的某些性能,往往要在型(芯)砂中加入一些附加物,如煤粉、锯末、纸浆等。型砂结构,如图2所示。 图2 型砂结构示意图 工艺特点 铸造是生产零件毛坯的主要方法之一,尤其对于有些脆性金属或合金材料(如各种铸铁件、有色合金铸件等)的零件毛坯,铸造几乎是唯一的加工方法。与其它加工方法相比,铸造工艺具有以下特点: 1)铸件可以不受金属材料、尺寸大小和重量的限制。铸件材料可以是各种铸铁、铸钢、铝合金、铜合金、镁合金、钛合金、锌合金和各种特殊合金材料;铸件可以小至几克,大到数百吨;铸件壁厚可以从0.5毫米到1米左右;铸件长度可以从几毫米到十几米。 2)铸造可以生产各种形状复杂的毛坯,特别适用于生产具有复杂内腔的零件毛坯,如各种箱体、缸体、叶片、叶轮等。 3)铸件的形状和大小可以与零件很接近,既节约金属材料,又省切削加工工时。4)铸件一般使用的原材料来源广、铸件成本低。 5)铸造工艺灵活,生产率高,既可以手工生产,也可以机械化生产。 铸件的手工造型
汽车制造与装配技术专业建设与发展规划2020
文档来源为:从网络收集整理.word版本可编辑.欢迎下载支持. 汽车制造与装配技术专业建设发展规划 (2016-2020年) 贵州装备制造职业技术学院 汽车工程系 2016年5月 1文档来源为:从网络收集整理.word版本可编辑.
文档来源为:从网络收集整理.word版本可编辑.欢迎下载支持. 一、汽车制造与装配技术专业建设背景和建设基础 (一)国际国内经济现状 目前来看,世界经济持续低迷,国际油价一路走低,国际金融动荡不已。我国经济也进入了新常态,过去以固定资产投资、房地产拉动为特征的扩张式高速增长也一去不复返了,劳动力和地价成本不断上升,某些要素成本甚至接近或超过了美国,与此同时,美国政府推进了“再工业业化”,在这种情况下,局部高端制造业势必回流到美国,而大量的劳动密集型产业也有向越南、印尼等要素成本更低的国家转移的趋势。目前国际国内经济形式复杂多变,中央政府审时度势提出了“万众创业、大众创新”的思路,以互联网 +、机器人、3D打印、新能源汽车等为代表战略新兴产业正在神州大地逐步兴起,上述产业发展成熟后,将极大地改变我们现有的产业格局、生产方式乃至生活方式。 (二)国内汽车产业现状及发展趋势 汽车产业具有高度技术密集型特点,聚集着许多科技领域里的新材料、新设备、新工艺和新技术。特别是电控技术和新能源技术、车联网技术嫁接到汽车产业上后,使得它处于价值链的高端,同时汽车是由成千上万颗零件组成,这就决定了它对国民经济强大的带动作用。作为重要的支柱产业,我国汽车产业,特别是乘用车产业,经过十多年高速发展,目前已经进入平稳发展阶段,随着经济增长持续放缓、国内一线城市汽车限牌逐步增多,汽车企业将从过去比拼产量、 2文档来源为:从网络收集整理.word版本可编辑.
汽车制造与装配技术方向人才培养方案
2013级机械设计与制造专业 (汽车制造与装配技术方向)人才培养方案 (专业代码:580101) 1.【人才培养目标】 本专业方向培养德、智、体、美全面发展,爱岗敬业,具有较强的学习能力和创新意识,面向“汽车制造业”,掌握汽车发动机工作原理和结构、汽车底盘结构、汽车制造与装配工艺等知识,具备汽车典型零部件加工、汽车装配与调试、数控设备操作等实践工作能力的高素质技能型人才。 2.【人才培养规格】 1.思想品德和职业道德要求 热爱社会主义祖国,拥护党的基本路线,懂得马克思列宁主义、毛泽东思想、邓小平理论和“三个代表”重要思想的基本原理,认真学习践行科学发展观,具有爱国主义、集体主义、社会主义思想和良好道德品质,具有敬业精神、创新精神、开拓精神、团队合作精神以及良好的综合素质。 2.职业岗位知识要求 掌握交通运输(汽车制造与装配)领域所必需的较为系统的基础科学理论,扎实的学科基础理论和必要的专业知识;具有较强的计算机应用能力,汽车应用英语阅读能力,机械知识能力,能正确使用各种测量器械,能够编制和实施典型汽车零件加工工艺与装配流程、分析解决一般机械加工工艺技术问题的基本能力;具备在汽车制造企业担任生产车间(工段)或技术部门技术管理工作的能力。 3.职业岗位能力要求 (1)掌握较扎实的自然科学基础知识,具有一定的人文、社会科学和管理科学基础知识,并具有一定的外语基础知识; (2)掌握计算机操作及应用方面的知识; (3)机械制图及计算机辅助绘图知识; (4)掌握现代汽车构造及先进技术的基本知识; (5)掌握汽车制造、装配工艺的基本知识与运用。
(6)掌握汽车制造业的质量、设备、技术、安全方面的基本知识与运用。 (7)编制和实施典型汽车零件加工工艺与装配流程、分析解决一般机械加工工艺技术问题的基本能力; (8)具备在汽车制造企业担任生产车间(工段)或技术部门技术管理工作的能力。 4.考取证书 (1)通过高职高专英语应用能力考试和国家计算机等级一级考试。 (2)考取汽车修理中级工证书、制图员证书、三维立体制图员证书、汽车营销师证书、机动车驾驶证书等。 3.【招生对象与学制】 招生对象:高中毕业生或中职毕业生 学制:三年 4.【毕业要求】 (1)学分要求:学生在毕业前应获得158学分方能毕业,其中:公共基础课程36学分,专业课、岗位技能课、专业拓展课122学分。 (2)职业资格证书要求:毕业时须取得数控车工、加工中心操作工或汽车装调工等职业资格证书。 5.【人才培养模式】 在教学组织上,按照学习规律,把培养过程分为三个阶段,第一个阶段(1.5年)为基本素质和基本职业能力培养阶段;第二阶段(1.0年)为职业岗位技能培养阶段,使学生获得必备的职业岗位技能,取得数控车工或维修电工等中级工职业资格证书,并结合具体的生产项目组织学生针对性进行生产性实习;第三阶段(0.5年)为顶岗实习阶段,使学生进入岗位工作角色,培养岗位工作能力,实现校企对接。 6.【面向岗位(群)、工作任务与职业能力分析】 6.1面向岗位(群) 本专业方向毕业生面向汽车制造、机械制造行业,可到汽车制造与装配企业或汽车零配件制造企业就业,从事汽车零部件制造工艺编制、汽车零部件加工和汽车装配与调试、汽车零部件检验与整车装配过程中的过程检验、整车下线检查和调试、汽车性能检测与评价、汽车保险理赔和配件销售检验等基层技术工作。
低压铸造原理及特点
第一节概述 在二十世纪初期,国外开始研究并应用低压铸造工艺,同时期,英国https://www.360docs.net/doc/491578403.html,ke登记了第一个低压铸造专利,主要用于巴氏合金的铸造。法国人制定了用于铝合金和铜合金的计划,并首先在铝合金铸造生产中得到推广使用。 第二次世界大战爆发后,随着航空工业的发展,英国广泛地采用低压铸造生产技术要求较高的航空发动机的气缸等轻铝合金铸件,并采用金属性低压铸造,大量生产高硅铝合金铸件。北美的汽车工业和电机工业又广泛采用金属型低压铸造生产汽缸、电机转子等重要铸件。这样,低压铸造工艺迅速扩散到通用机械、纺织机械、仪表和商业产品的领域。 我国从五十年代开始研究低压铸造,但发展一直比较缓慢。随着汽车工业的发展,和大量新技术的采用,在上世纪末和本世纪初,低压铸造在我国得到快速发展,国产低压铸造机的功能和性能,及使用的稳定性和可靠性已经接近或达到国际先进水平,被大量用于汽车轮毂、汽车缸盖等铸件的生产。 第二节低压铸造原理及特点 低压铸造是使液体金属在压力作用下充填型腔,以形成铸件的一种方法。由于所用的压力较低,所以叫做低压铸造。其工艺过程如下:在装有合金液的密封容器(如坩埚)中,通入干燥的压缩空气,作用在保持一定浇注温度的金属液面上,造成密封容器内与铸型型腔的压力差,使金属液在气体压力的作用下,沿升液管上升,通过浇口平稳地进入型腔,并适当增大压力并保持坩埚内液面上的气体压力,使型腔内的金属液在较高压力作用下结晶凝固。然后解除液面上的气体压力,使开液管中未凝固的金属液依靠自重流回坩埚中,再开型并取出铸件,至此,一个完整的低压浇铸工艺完成。低压铸造工艺过程演示如下: 低压铸造过程动画演示
低压铸造独特的优点表现在以下几个方面: 1.低压铸造的浇注工艺参数可在工艺范围内任意设置调整,可保证液体金属充型平稳,减少或避免金属液在充型时的翻腾、冲击、飞溅现象,从而减少了氧化渣的形成,避免或减少铸件的缺陷,提高了铸件质量; 2.金属液在压力作用下充型,可以提高金属液的流动性,铸件成形性好,有利于形成轮廓清晰、表面光洁的铸件,对于大型薄壁铸件的成形更为有利; 3.铸件在压力作用下结晶凝固,并能得到充分地补缩,故铸件组织致密,机械性能高; 4.提高了金属液的工艺收得率,一般情况下不需要冒口,使金属液的收得率大大提高,收得率一般可达90%。 5.劳动条件好;生产效率高,易实现机械化和自动化,也是低压铸造的突出优点。 6.低压铸造对合金牌号的适用范围较宽,基本上可用于各种铸造合金。不仅用于铸造有色合金,而且可用于铸铁、铸钢。特别是对于易氧化的有色合金,更显示它的优越性能,即能有效地防止金属液在浇注过程中产生氧化夹渣。 7.低压铸造对铸型材料没有特殊要求,凡可作为铸型的各种材料,都可以用作低压铸造的铸型材料。与重力铸造和特种铸造应用的铸型基本相同,如砂型(粘土砂、水玻璃砂、树脂砂等)、壳型、金属型、石墨型、熔模精铸壳型、陶瓷型等都可应用。总之,低压铸造对铸型材料要求没有严格限制。 第三节低压铸造工艺设计
汽车制造与装配技术业建设与发展规划2016-2020
汽车制造与装配技术专业建设发展规划 (2016-2020年) 贵州装备制造职业技术学院 汽车工程系 2016年5月
一、汽车制造与装配技术专业建设背景和建设基础 (一)国际国内经济现状 目前来看,世界经济持续低迷,国际油价一路走低,国际金融动荡不已。我国经济也进入了新常态,过去以固定资产投资、房地产拉动为特征的扩张式高速增长也一去不复返了,劳动力和地价成本不断上升,某些要素成本甚至接近或超过了美国,与此同时,美国政府推进了“再工业业化”,在这种情况下,局部高端制造业势必回流到美国,而大量的劳动密集型产业也有向越南、印尼等要素成本更低的国家转移的趋势。目前国际国内经济形式复杂多变,中央政府审时度势提出了“万众创业、大众创新”的思路,以互联网 +、机器人、3D打印、新能源汽车等为代表战略新兴产业正在神州大地逐步兴起,上述产业发展成熟后,将极大地改变我们现有的产业格局、生产方式乃至生活方式。 (二)国内汽车产业现状及发展趋势 汽车产业具有高度技术密集型特点,聚集着许多科技领域里的新材料、新设备、新工艺和新技术。特别是电控技术和新能源技术、车联网技术嫁接到汽车产业上后,使得它处于价值链的高端,同时汽车是由成千上万颗零件组成,这就决定了它对国民经济强大的带动作用。作为重要的支柱产业,我国汽车产业,特别是乘用车产业,经过十多年高速发展,目前已经进入平稳发展阶段,随着经济增长持续放缓、国内一线城市汽车限牌逐步增多,汽车企业将从过去比拼产量、
盲目扩张,转向以提高产品质量、优化服务能力,特别是转向以电动汽车为代表的新能源汽车方向发展。 图表1:2009-2014年中国商用车、乘用车销量占比变化趋势图(单位:%) 图表2:2009-2014年中国汽车产销量走势图(单位:万辆,%)
熔模铸造工艺流程-图文.
熔模铸造工艺流程 模具制造 制溶模及浇注系 统 模料处理 模组焊接 模组清洗 上涂料及撒砂 涂料制备 重
复 型壳干燥(硬化 多 次 脱蜡 型壳焙烧 浇注 熔炼 切 割 浇 口 抛 光 或 机
工 钝化 修整焊补 热处理 最后清砂 喷丸或喷砂 磨内
口 震 动 脱 壳 模料 制熔模用模料为日本牌号:K512模料 模料主要性能: 灰分≤0.025% 铁含量灰分的10% ≤0.0025% 熔点 83℃-88℃(环球法)60℃±1℃ 针入度 100GM(25℃)3.5-5.0DMM 450GM(25℃)14.0-18.0DMM 收缩率 0.9%-1.1% 比重 0.94-0.99g/cm3 颜色新蜡——兰色、深黄色 旧蜡——绿色、棕色
蜡(模)料处理 工艺参数: 除水桶搅拌时温度 110-120℃ 搅拌时间 8-12小时 静置时温度 100-110℃ 静置时间 6-8小时 静置桶静置温度 70-85℃ 静置时间 8-12小时 保温箱温度 48-52℃ 时间 8-24小时 二、操作程序 1、从脱蜡釜泄出的旧蜡用泵或手工送到除水桶中,先在105-110℃下置6-8小时沉淀,将水分泄掉。 2、蜡料在110-120℃下搅拌8-12小时,去除水份。 3、将脱完水的蜡料送到70-85℃的静置桶中保温静置桶中保温静置8-12小时。 4、也可将少量新蜡加入静置桶中,静置后清洁的蜡料用手工灌到保温箱蜡缸中,保温温度48-52℃,保温时间8-24小时后用于制蜡模。
5、或把静置桶中的回收蜡料输入到气动蜡模压注机的蜡桶中,保温后压制浇道。 三、操用要点 1、严格按回收工艺进行蜡料处理。 2、除水桶、静置桶均应及时排水、排污。 3、往蜡缸灌蜡时,蜡应慢没缸壁流入,防止蜡液中进入空气的灰尘。 4、蜡缸灌满后应及时盖住,避免灰尘等杂物落入。 5、经常检查每一个桶温,防止温度过高现象发生。 6、作业场地要保持清洁。 7、防止蜡液飞溅。 8、严禁焰火,慎防火灾。 压制蜡(熔)模 一、工艺参数 室温20-24℃压射蜡温50-55℃ 压射压力0.2-0.5Mpa 保压时间10-20S 冷却水温度15±3℃ 二、操作程序
阀门铸造工艺
阀门铸造工艺介绍 1
一、何为铸造:阀门铸造工艺*第一节铸造的概述及特点 将液体金属浇到具有与零件形状相适应的铸型空腔中,待其凝固后,以获 得一定形状尺寸和表面质量的零件的产品,称之为铸造。 二、铸造概述: 铸造具有悠久的历史,约在公元前三千年,人类已铸出多种精美的青铜器。但几千年来是靠手工用粘土、砂等天然材料制造的。铸件的产量很小,随着工 业革命的发展,机械化的增加,铸件需求量的提高,在20 世纪30 年代开始使用气动机器和人工合成造型的粘土砂工艺生产。随着时代的发展,各类造型方 法应运而生。例如:1933 年出现水泥砂型,1967 年出现水泥流态砂型;1944 年出现冷却覆膜树脂砂壳型;1955 年出现热法覆膜树脂砂壳型,1958 年出现呋喃树脂自硬砂型;1947 年出现CO2硬化水玻璃砂型,1968 年出现了有机硬化剂的水玻璃(有机脂水玻璃)工艺等。近年来,用物理手段制造铸型的新方法,如: 磁丸造型,真空密封造型法,失膜造型等。 铸造由于可选用多样成分、性能的铸造合金,加工基本建设投资小,工艺 灵活性大,生产周期短等优点,被广泛用于机械制造、矿山冶金、交通运输、 石化通用设备、农业机械、能源动力、轻工纺织、土建工程、电力电子、航天 航空、国际军工等国民经济各部门,是现代大机械工业的基础。 2
铸造在中国已有漫长的历史,但铸造技术长期处于停滞状态,改革开放以来,我国的铸造技术有了很大的发展,突出的表现在三个方面:造型、造芯的机械化、自动化程度明显提高;自硬性化学型砂取代干型粘土砂和油砂;铸造 工艺技术由凭经验走向科学化,如:计算机模拟设计。这一系列的改革对提高 生产效率,降低劳动强度,改善生产环境,提高铸件内在质量和外观质量,节 约原材料和能源起了重大的作用。 三、铸造特点: 1、铸造的适应性很广,灵活性很大,产品要求及所处各种工况,可制造多 种金属材料的产品,如:铁、碳素钢、低合金钢、铜、铜合金、铝、铝合 金、钛合金等等。与其他成型方式相比,铸造不受零件的重量、尺寸和形 状限制。重量可从几克到几百吨,壁厚由0.3mm 到1m,形状只要在铸造 工艺性范围内,是十分复杂的,还是机械加工困难的,甚至难以制得的零 件,都可通过铸造的方式获得。 2、铸造所用的原材料大多来源广,价格低廉,如废钢、砂等。但由于近期国 内铸造和钢铁业大量兴起,这些原材料价格出现上涨。 3、铸件可通过先进的铸造工艺方法,提高铸件的尺寸精度和表面质量,使零 件做到少切割和无切割。对产品制造达到省工省料的效果,节约总体的制 作成本。 3
汽车制造与装配技术复习题
一、填空 1、汽车装配技术主要包括:冲压、焊接、涂装和总装等4大部分。 2、汽车装配线一般是由输送设备和专业设备构成的有机整体。 3、生产过程是由加工过程、检验过程、运输过程、自然失效过程及等待间歇过程等组成。 4、装配生产组织形式包括固定式装配和流水式装配两大类。 5、强制流水装配方式又分为间隙式移动和连续式移动2 种 6、冲压方法多种多样,但概括起来可分为分离工序和变形工序两大类。 7、冷冲压所用设备压力机类型很多,按传动方式的不同,主要有机械压力机和液压压力机两大类, 8、焊接接头包括焊缝、熔合区和热影响区3 部分。 9、焊接接头型式主要有对接接头、T 形接头、角接接头、搭接接头等4 种。 10、手工电弧焊常用的引弧方法有直击法和划擦法。 11、手工电弧焊的基本操作包括引弧、运条、收弧和焊件清理等4 个基本过程 12、电阻焊方法主要有4 种,即点焊、缝焊、凸焊、对焊。 13、矫正通常有火焰矫正和机械矫正等形式。 14、常用涂装方法的四种方法浸涂、喷涂、刷涂、电泳涂装。 15、喷枪按涂料的供给方法分为吸力式、重力式和压力式3 种 16、烘干设备按加热和传热方式分为对流式、辐射式和感应式3 种。 17、影响颜色的三大要素也称为视觉的三大要素,即光线、物体和观察者。 18、色彩的三属性包括色调、明度、彩度,也称为颜色的三个空间或颜色三属性。 19、涂料由3 大部分组成,分别为:主要成膜物质、次要成膜物质和辅助成膜物质。 20、涂料的干燥方式主要有自然干燥、加速干燥和高温烘烤干燥3 种。 21、电泳涂装法有阳极电泳法和阴极电泳法2 种 22、汽车制造的四大工艺包括冲压、焊装、涂装、总装。 二、名词解释 1、生产过程——产品从原材料到制成成品所经过的一切劳动阶段,称生产过程 2、工艺过程——就是指生产对象在质和量的状态以及外观发生变化的那部分过程。 3、冲压——冲压是在常温下利用冲模在压力机上对材料施加压力,使其产生分离或变形,从而获得一定的形状、尺寸和性能的零件加工方法。 4、焊接——就是通过加热或加压,或两者并用,用或不用填充材料,使焊件达到原子间结合的一种加工方法。 5、涂装——指将涂料涂覆于物面(基底表面)上,经干燥成膜的工艺。 6、汽车总装配工艺——汽车总装配就是使生产对象在数量、外观发生变化的工艺过程 7、涂料——是指涂布在物体的表面上,能够形成具有保护、装饰或其他特殊性能的固态保护膜的类液体或固体材料的总称。 三、判断 1、汽车总装配具有小批量的特点。 2、车身生产具有制造投资大、周期长这样的特点 3、选择装配线设备时要考虑的问题包括:产品生产纲领、产品质量要求、设备的先进性、设备的可靠性、设备的价格。
汽车制造与装配技术专业人才培养方案
贵州装备制造职业技术学院 汽车制造与装配技术专业人才培养方案 汽车工程系 二〇一六年三月
汽车制造与装配技术专业人才培养方案 (三年制) 一、专业名称(专业代码) 汽车制造与装配技术(560702) 二、教育类型及学历层次 高等职业教育大专 三、招生对象与学制 高中毕业生及同等学历者三年制 四、培养目标 本专业主要培养德、智、体、美全面发展,重点面向现代汽车制造业和贵州地区汽车后市场的现代汽车制造、装配、调试、新车检验、机电维修、汽车检测和维修服务顾问等工作岗位,具有良好的职业道德和团队精神,掌握扎实的现代汽车理论知识,同时能运用现代汽车制造和检测设备对汽车进行制造、装配、检测、故障诊断和维修;具有较强实际动手能力、拓展能力和创新精神;具有工匠精神的高素质技术技能型人才。 五、职业范围
六、人才规格 本专业毕业生应具有以下职业素养、专业知识和技能: (一)职业素养 1.具有良好的职业道德与职业素养,遵纪守法、爱岗敬业、诚实守信; 2.具有良好的身体素质,健康的职业竞争心态和自主创业精神; 3.具有良好的人际交往能力和团队协作能力,具有分析问题处理问题的能力; 4.具有用户至上,质量第一的责任意识; 5.具有安全生产,节能环保的责任意识; 6.具有法律维权意识; 7.具有一定的自学能力和继续学习能力。 (二)知识与技能要求 1. 知识要求 (1)掌握本专业必备的文化体育基础知识,具体课程包括:思想政治、实用英语、应用数学、体育与健康、计算机应用基础与信息处理等; (2)熟练掌握本专业所必需的汽车基本专业知识,具体课程包括:汽车概论、机械制图及CAD、汽车工程材料、公差配合与技术测量、汽车电工电子基础、机械设计基础、机械制造基础等; (3)熟练掌握汽车综合专业知识,具体课程包括:汽车构造、汽车制造工艺、汽车电子控制技术、汽车检测技术、汽车维修企业管
《铸造工艺学》课后习题答案-董选普
《铸造工艺学》课后习题答案 湖南大学 1、什么是铸造工艺设计? 铸造工艺设计就是根据铸造零件的结构特点、技术要求、生产批量、生产条件等,确定铸造方案和工艺参数,绘制铸造工艺图,编制工艺卡等技术文件的过程。 2、为什么在进行铸造工艺设计之前要弄清楚设计的依据,设计依据包括哪些内容? 在进行铸造工艺设计前设计者应该掌握生产任务和要求,熟悉工厂和车间的生产条件这些是铸造工艺设计的基本依据,还需要求设计者有一定的生产经验,设计经验并应对铸造先进技术有所了解具有经济观点发展观点,才能很好的完成设计任务 设计依据的内容 一、生产任务1)铸件零件图样提供的图样必须清晰无误有完整的尺寸,各种标记2)零件的技术要求金属材质牌号金相组织力学性能要求铸件尺寸及重量公差及其它特殊性能要求3)产品数量及生产期限产品数量是指批量大小。生产期限是指交货日期的长短。二、生产条件1)设备能力包括起重运输机的吨位,最大起重高度、熔炉的形式、吨位生产率、造型和制芯机种类、机械化程度、烘干炉和热处理炉的能力、地坑尺寸、厂房高度大门尺寸等。2)车间原料的应用情况和供应情况3)工人技术水平和生产经验4)模具等工艺装备制造车间的加工能力和生产经验 三、考虑经济性对各种原料、炉料等的价格、每吨金属液的成本、各级工种工时费用、设备每小时费用等、都应有所了解,以便考核该工艺的经济性。 3.铸造工艺设计的内容是什么? 铸造工艺图,铸件(毛坯)图,铸型装配图(合箱图),工艺卡及操作工艺规程。 4.选择造型方法时应考虑哪些原则? 1、优先采用湿型。当湿型不能满足要求时再考虑使用表干砂型、干砂型或其它砂型。 选用湿型应注意的几种情况1)铸件过高的技术静压力超过湿型的抗压强度时应考 虑使用干砂型,自硬砂型等。2)浇注位置上铸件有较大水平壁时,用湿型易引起 夹砂缺陷,应考虑使用其它砂型3)造型过程长或需长时间等待浇注的砂型不宜 选用湿型4)型内放置冷铁较多时,应避免使用湿型 2、造型造芯方法应和生产批量相适应 3、造型方法应适用工厂条件 4、要兼顾铸件的精度要求和生产成本 5-浇注位置的选择或确定为何受到铸造工艺人员的重视?应遵循哪些原则? 确定浇注位置是铸造工艺设计中重要的一环,关系到铸件的内在质量、铸件的尺寸精度铸造工艺过程中的难易,因此往往须制定出几种方案加以分析,对此择优选用。 应遵循的原则为:1、铸件的重要部分应尽量置于下部2、重要加工面应朝下或呈直立状态3、使铸件的大平面朝下,避免夹砂伤疤类缺陷4、应保证铸件能充满5、应有利于铸件的补缩6、避免用吊砂,吊芯或悬臂式砂芯,便于下芯,合箱及检验7、应使合箱位置,浇注位置和铸件冷却位置相一致 5为什么要设计分型面?怎样选择分型面? 分型面的优劣,在很大程度上影响铸件的尺寸精度、成本和生产率。选择分型面的原则:1、应使铸件的全部或大部置于同一半型内2、应尽量减少分型面数目,分型面少,铸件精度容易保证3、分型面应尽量选用平面4、便于下芯,合箱,检查型腔尺寸。5、不使砂箱过高6、受力件的分型面的选择不应削弱铸件结构强度7、注意减轻铸件的清理和机
汽车制造与装配技术人才培养方案
汽车制造与装配技术专业人才培养方案世界十大汽车制造商全部落户中国,中国已名副其实地成为世界汽车生产大国和最大的汽车市场。我国有独立制造装配汽车的生产企业共455家,另外从事汽车总成及零部件生产的厂商有数千家。随着我国国民经济的持续快速发展,汽车制造业和交通运输业发展突飞猛进,汽车已成为国民经济和日常生活中不可缺少的重要的交通工具,汽车工业也成为了我国国民经济的支柱产业,必然需要大量能从事在生产第一线的“有道德、会操作、精维护、懂管理”,具有专门理论知识、较强实践技能的汽车制造及装配专业人才,为汽车制造及装配专业群的发展也带来了前所未有的机遇。 本专业立足新疆,面向西北地区,培养品德高尚、技能精湛、身心健康的高技能型人才;建立为汽车制造产业服务的人才培养基地。努力在实现专业教学环节实现“五个对接”即:专业与产业对接、职业与岗位对接、专业课程内容与职业标准对接、教学过程与生产过程的对接、学历岗位证书与职业资格证书的对接。 培养人才定位为服务汽车前市场,主要岗位有车身焊接工、汽车装配工、汽车改装工、汽车调试工、车间调度员等。 人才培养模式的设置是以人才培养目标与行业发展要求为导向,力求与企业密切合作,本专业依靠正和车辆有限公司、中集(车辆)新疆有限公司、东风汽车新疆有限公司等汽车制、改装企业,实行“工学结合、德能并重”的1243人才培养模式,努力保证人才培养质量。 汽车制造与装配技术专业组织本专业教师和企业一线技术人员共同组成专业建设指导委员会,该委员会根据人才市场需求,结合我院实际及示范院校建设要求,制订了本人才培养方案。 一、专业名称 专业名称:汽车制造与装配技术 专业代码:580401 二、教育类型及学历层次 教育类型:高等职业教育 学历层次:大专 三、招生对象、学制与毕业要求 招生对象:高中毕业生或同等学历者
铸造工艺设计步骤
铸造工艺设计: 就是根据铸造零件的结构特点,技术要求,生产批量和生产条件等,确定铸造方案和工艺参数,绘制铸造工艺图,编制工艺卡等技术文件的过程.设计依据: 在进行铸造工艺设计前,设计者应掌握生产任务和要求,熟悉工厂和车间的生产条件,这些是铸造工艺设计的基本依据.设计内容: 铸造工艺设计内容的繁简程度,主要决定于批量的大小,生产要求和生产条件.一般包括下列内容: 铸造工艺图,铸件(毛坯)图,铸型装配图(合箱图),工艺卡及操作工艺规程.设计程序: 1零件的技术条件和结构工艺性分析;2选择铸造及造型方法;3确定浇注位置和分型面;4选用工艺参数;5设计浇冒口,冷铁和铸肋;6砂芯设计;7在完成铸造工艺图的基础上,画出铸件图;8通常在完成砂箱设计后画出;9综合整个设计内容.铸造工艺方案的内容: 造型,造芯方法和铸型种类的选择,浇注位置及分型面的确定等.铸件的浇注位置是指浇注时铸件在型内所处的状态和位置.分型面是指两半铸型相互接触的表面.确定砂芯形状及分盒面选择的基本原则,总的原则是: 使造芯到下芯的整个过程方便,铸件内腔尺寸精确,不至造成气孔等缺陷,使芯盒结构简单.1保证铸件内腔尺寸精度;2保证操作方便;3保证铸件壁厚均匀;4应尽量减少砂芯数目;5填砂面应宽敞,烘干支撑面是平面;6砂芯形状适应造型,制型方法.铸造工艺参数通常是指铸型工艺设计时需要确定的某些数据.1铸件尺寸公差: 是指铸件各部分尺寸允许的极限偏差,它取决于铸造工艺方法等多种因素.2主见重量公差定义为以占铸件公称质量的百分率为单位的铸件质量变动的允许值.3机械加工余量: 铸件为保证其加工面尺寸和零件精度,应有加工余量,即在铸件工艺设计时预先增加的,而后在机械加工时又被切去的金属层厚度,称为机械加工余量,简称加工余量.代号用MA,由精到粗分为ABCDEFGH和J9个等级。
(完整版)汽车制造与装配技术专业简介
汽车制造与装配技术专业简介 一、社会需求 汽车产业是国民经济重要的支柱产业,产业链长、关联度高、就业面广、消费拉动大,在国民经济和社会发展中发挥着重要作用。国家颁布的《汽车产业调整振兴规划细则》明确提出,未来十年,将是中国汽车产业从汽车大国迈向汽车强国的关键时期。重庆是我国第二大汽车制造基地,全国四大汽车制造商在重庆均有布局,随着韩国现代汽车签约落户,重庆已经建成千亿级汽车城,需要大量的汽车制造与装配技术高素质技能型人才。 二、培养目标 本专业培养具有汽车装配、调试、试验、质量控制、车身匹配、生产管理等能力的高素质技能型专门人才。 三、主干课程 汽车构造,汽车装配技术、汽车车身焊接技术、汽车涂装技术、汽车检测技术与调试(社会需求变化,课程作相应调整)。 四、培养模式 1.理实一体 让学生在“学中做、做中学”,变抽象为具体,增强教学效果,培养了学生的实际动手能力。 2. 任务驱动 所有专业课程学习均采用任务驱动教学,为学生提供体验实践的情境和感悟问题的情境,围绕任务展开学习,以任务的完成结果检验和总结学习过程,让学生主动探究、实践、思考、运用。 3.课证融合
教学中融入行业职业标准,嵌入职业工程师(技师)课程,帮助学生考取汽车装调师、汽车机电师、汽车涂装师等职业资格证书、提高就业竞争力和薪酬待遇。 五、教学条件 1.师资队伍 我校有40余个专业。本专业教学团队现有专兼职教师38名,其中具有硕士及以上学位教师占42%,副高级及以上职称教师占32%,中级职称教师占40%,双师素质教师占75%。 2.电化教室 所有教室均为中央空调多媒体教室。 3.实习实训 本专业除拥有汽车构造实训室、汽车电器实训室、汽车整车实训室等20多个校内实训室和汽车装配等多个虚拟仿真实训室外,还拥有长安铃木、上海依维柯、东风小康等10余个校外实训基地,供学生专业实习实训。 4.图书资源 学校图书馆藏书近45万册,电子图书35万余册。期刊700余种。本专业藏书近万册,电子图书近2万册,各种学术期刊、杂志20余种,并享有“超星”、“万方”和“维普”等网络数据资源。内容丰富,可充分满足教师和学生的专业阅读和知识扩展需要。
铸造工艺_特点及其应用
铸造(casting) 铸造是将金属熔炼成符合一定要求的液体并浇进铸型里,经冷却凝固、清整处理后得到有预定形状、尺寸和性能的铸件的工艺过程。铸造毛坯因近乎成形,而达到免机械加工或少量加工的目的降低了成本并在一定程度上减少了时间.铸造是现代制造工业的基础工艺之一。把金属材料做成所需制品的工艺方法很多,如铸造、锻造、挤压、轧制、拉延、冲压、切削、粉末冶金等等。其中,铸造是最基本、最常用的工艺。 铸造种类很多,按造型方法习惯上分为: ①普通砂型铸造,包括湿砂型、干砂型和化学硬化砂型3类。 ②特种铸造,按造型材料又可分为以天然矿产砂石为主要造型材料的特种铸造(如熔模铸造、泥型铸造、铸造车间壳型铸造、负压铸造、实型铸造、陶瓷型铸造等)和以金属为主要铸型材料的特种铸造(如金属型铸造、压力铸造、连续铸造、低压铸造、离心铸造等)两类。 铸造可按铸件的材料分为: 黑色金属铸造(包括铸铁、铸钢)和有色金属铸造(包括铝合金、铜合金、锌合金、镁合金等) 铸造有可按铸型的材料分为: 砂型铸造和金属型铸造。 按照金属液的浇注工艺可分为: 1、重力铸造:指金属液在地球重力作用下注入铸型的工艺,也称浇铸。广义的重力铸造包括砂型浇铸、金属型浇铸、熔模铸造、消失模铸造,泥模铸造等;窄义的重力铸造专指金属型浇铸。 2、压力铸造是指金属液在其他外力(不含重力)作用下注入铸型的工艺,按照压力的大小,又分为高压铸造(压铸)和低压铸造。 补充知识: 1、精密铸造是相对于传统的铸造工艺而言的一种铸造方法。它能获得相对准确地形状和较高的铸造精度。较普遍的做法是:首先做出所需毛坯(可 留余量非常小或者不留余量)的电极,然后用电极腐蚀模具体,形成空腔。再用浇铸的方法铸蜡,获得原始的蜡模。在蜡模上一层层刷上耐高温的液体砂料。待获得足够的厚度之后晾干,再加温,使内部的蜡模溶化掉,获得与所需毛坯一致的型腔。再在型腔里浇铸铁水,固化之后将外壳剥掉,就能获得精密制造的成品 2、选择铸造方式时应考虑:a.优先采用砂型铸造b.铸造方法应和生产批量相适 c.造型方法应适合工厂条件d.要兼顾铸件的精度要求和成 3、金属材料的力学性能主要指:强度、刚度、硬度、塑性、韧性等。
铸造工艺设计基础
铸造工艺设计基础 铸造生产周期较长,工艺复杂繁多。为了保证铸件质量,铸造工作者应根据铸件特点,技术条件和生产批量等制订正确的工艺方案,编制合理的铸造工艺流程,在确保铸件质量的前提下,尽可能地降低生产成本和改善生产劳动条件。本章主要介绍铸造工艺设计的基础知识,使学生掌握设计方法,学会查阅资料,培养分析问题和解决问题的能力。 §1-1 零件结构的铸造工艺性分析 铸造工艺性,是指零件结构既有利于铸造工艺过程的顺利进行,又有利于保证铸件质量。 还可定义为:铸造零件的结构除了应符合机器设备本身的使用性能和机械加工的要求外,还应符合铸造工艺的要求。这种对铸造工艺过程来说的铸件结构的合理性称为铸件的铸造工艺性。 另定义:铸造工艺性是指零件的结构应符合铸造生产的要求,易于保证铸件品质,简化铸造工艺过程和降低成本。 铸造工艺性不好,不仅给铸造生产带来麻烦,不便于操作,还会造成铸件缺陷。因此,为了简化铸造工艺,确保铸件质量,要求铸件必须具有合理的结构。 一、铸件质量对铸件结构的要求 1.铸件应有合理的壁厚 某些铸件缺陷的产生,往往是由于铸件结构设计不合理而造成的。采用合理的铸件结构,可防止许多缺陷。 每一种铸造合金,都有一个合适的壁厚范围,选择得当,既可保证铸件性能(机械性能)要求,又便于铸造生产。在确定铸件壁厚时一般应综合考虑以下三个方面:保证铸件达到所需要的强度和刚度;尽可能节约金属;铸造时没有多大困难。 (1)壁厚应不小于最小壁厚 在一定的铸造条件下,铸造合金能充满铸型的最小壁厚称为该铸造合金的最小壁厚。为了避免铸件的浇不足和冷隔等缺陷,应使铸件的设计壁厚不小于最小壁厚。各种铸造工艺条件下,铸件最小允许壁厚见表7-1~表7-5 合金种类铸件最大轮廓尺寸为下列值时/㎜ ﹤200200-400400-800800-12501250-2000﹥ 2000 碳素铸钢 低合金钢 高锰钢 不锈钢、耐热钢灰铸铁 孕育铸铁 (HT300以上)球墨铸铁8 8-9 8-9 8-11 3-4 5-6 3-4 9 9-10 10 10-12 4-5 6-8 4-8 11 12 12 12-16 5-6 8-10 8-10 14 16 16 16-20 6-8 10-12 10-12 16~18 20 20 20-25 8-10 12-16 12-14 20 25 25 - 10-12 16-20 14-16铸件最大轮廓为下列值时mm
汽车制造与装配技术专业简介
汽车制造与装配技术专业简介 专业代码560701 专业名称汽车制造与装配技术 基本修业年限三年 培养目标 本专业培养德、智、体、美全面发展,具有良好职业道德和人文素养,掌握汽车及零部件生产的基本工艺方法及工艺装备等基本知识,具备安全、规范操作汽车及零部件生产工装设备等能力,从事生产现场工艺实施、技术检测、质量控制、生产管理等工作的高素质技术技能人才。 就业面向 主要面向汽车整车及零部件制造企业,在生产、技术、管理等岗位群,从事汽车零部件、总成加工制造,汽车的装配、调整,汽车质量检验、检测,生产设备维修,生产计划与生产调度等工作。 主要职业能力 1.具备对新知识、新技能的学习能力和创新创业能力; 2.具备较强的安全意识、环保意识和质量意识; 3.具备良好的人际交流、语言表达、团队合作、计划组织能力; 4.具备识读图纸及工艺文件,安全规范地操作专业设备,从事汽车零部件制造与装调的能力; 5.具备基本的计算机操作能力和外语应用能力; 6.具备对汽车零部件及整车生产现场实施质量监控与管理的能力; 7.掌握整车及零部件生产、装配、检测及设备维修、技术管理等机电知识和专业理论。
核心课程与实习实训 1.核心课程 机械制造及自动化、汽车电控技术、汽车发动机装配与调试、汽车底盘装配与调试、汽车电器与电子控制系统装配与调试、汽车装配生产现场管理、汽车装配与调整技术、汽车性能检测等。 2.实习实训 在校内进行钳工、汽车各总成拆装、汽车性能检测等实训。在汽车整车及零部件制造企业进行实习。 职业资格证书举例 汽车生产线操作调整工汽车(拖拉机)装配工 衔接中职专业举例 汽车制造与检修汽车运用与维修 接续本科专业举例 车辆工程机械设计制造及其自动化
汽车制造与装配技术专业教学标准汇总
汽车制造与装配技术专业教学标准 世界十大汽车制造商全部落户中国,中国已名副其实地成为世界汽车生产大国和最大的汽车市场。我国有独立制造装配汽车的生产企业共455家,另外从事汽车总成及零部件生产的厂商有数千家。随着我国国民经济的持续快速发展,汽车制造业和交通运输业发展突飞猛进,汽车已成为国民经济和日常生活中不可缺少的重要的交通工具,汽车工业也成为了我国国民经济的支柱产业,必然需要大量能从事在生产第一线的“有道德、会操作、精维护、懂管理”,具有专门理论知识、较强实践技能的汽车制造及装配专业人才,为汽车制造及装配专业群的发展也带来了前所未有的机遇。 本专业立足河北,面向华北地区,培养品德高尚、技能精湛、身心健康的高技能型人才;建立为汽车制造产业服务的人才培养基地。努力在实现专业教学环节实现“五个对接”即:专业与产业对接、职业与岗位对接、专业课程内容与职业标准对接、教学过程与生产过程的对接、学历岗位证书与职业资格证书的对接。 培养人才定位为服务汽车前市场,主要岗位有车身焊接工、汽车装配工、汽车改装工、汽车调试工、车间调度员等。 人才培养模式的设置是以人才培养目标与行业发展要求为导向,力求与企业密切合作,本专业依靠正和车辆有限公司、中集(车辆)新疆有限公司、东风汽车新疆有限公司等汽车制、改装企业,实行“工学结合、德能并重”的800人才培养模式,努力保证人才培养质量。 汽车制造与装配技术专业组织本专业教师和企业一线技术人员共同组成专业建设指导委员会,该委员会根据人才市场需求,结合我院实际及示范院校建设要求,制订了本人才培养方案。 一、专业名称 专业名称:汽车制造与装配技术 专业代码:580401 二、教育类型及学历层次 教育类型:高等职业教育 学历层次:大专
铸造及其特点
铸造是熔炼金属,制造铸型,并将金属液浇入铸型,凝固后获得一定形状和性能铸件的成形方法。铸造是获得零件毛坯的主要方法之一。与其它加工方法比较,铸造具有适应性广、生产成本低的优点,尤其在制造内腔复杂的构件时,更显其优越性。在机械产品中,铸件占有很大的比例,如机床中为 60%~80%。但是铸造存在着铸件质量不稳定、尺寸精度不高,工人劳动强度大,工作环境差等问题。铸造按其工艺特点分为砂型铸造和特种铸造两大类。砂型铸造是最基本和应用最广泛的铸造方法,它是以型砂制造铸型的。 锻造及其特点 锻造是在加压设备及工模具的作用下使坯料、铸锭产生局部或全部塑性变形,以获得一定几何尺寸、形状和质量的锻件的成形方法。锻造可分为自由锻、模锻、胎模锻。各类塑性良好的金属材料,如钢、铝、铜及其合金等都具有良好的锻造性能。锻件内部组织致密、均匀,力学性能优于相同化学成分的铸件,能承受较大的载荷和冲击,因此力学性能要求较高的重要零件一般都采用锻件毛坯,如主轴、传动轴、齿轮、凸轮、连杆等。锻造还可节省金属材料,节省切削加工工时,提高生产率。但锻件形状的复杂程度不如铸件,尤其是不能加工脆性材料(如铸铁)和难以锻出具有复杂内腔的零件毛坯, 焊接及其特点 焊接是通过加热或加压(或两者并用)、并且用(或不用)填充材料,使工件形成原子间结合的连接方法。焊接实现的连接是不可拆卸的永久性连接。与铆接相比,焊接具有节省金属材料、生产率高、连接质量优良、劳动条件好、易于实现自动化等优点。在机械制造工业中,焊接广泛用于制造各种金属结构件(如厂房屋架、桥梁、船舶、车辆、压力容器、管道等)及某些机械零件的毛坯,还常用于修补铸件、锻件的某些缺陷和局部受损坏的零件,在生产中有较大的经济意义。 热处理及其特点 热处理是采用适当的方式对金属材料或工件进行加热、保温和冷却以获得所预期的组织结构与性能的工艺。热处理能显着提高钢的力学性能,满足零件使用要求和延长寿命;还可改善钢的加工性能,提高加工质量和劳动生产率,因此热处理在机械制造中应用很广。如汽车、拖拉机中有 70%~80%的零件要进行热处理;各种刀具、量具、模具等几乎 100%要进行热处理。 热处理按目的与作用不同,分为以下三类: (1)整体热处理指对工件整体进行穿透加热的热处理。主要包括退火、正火、淬火和回火等。 (2)表面热处理指为改变工件表面的组织和性能,仅对其表面进行热处理的工艺。主要包括火焰淬火、感应淬火等。 (3)化学热处理指将工件置于适当的活性介质中加热、保温、使一种或几种元素渗入它的表层,以改变其化学成分、组织和性能的热处理。主要包括渗碳、渗氮、碳氮共渗等。