循环流化床锅炉旋风分离器改造及应用效果
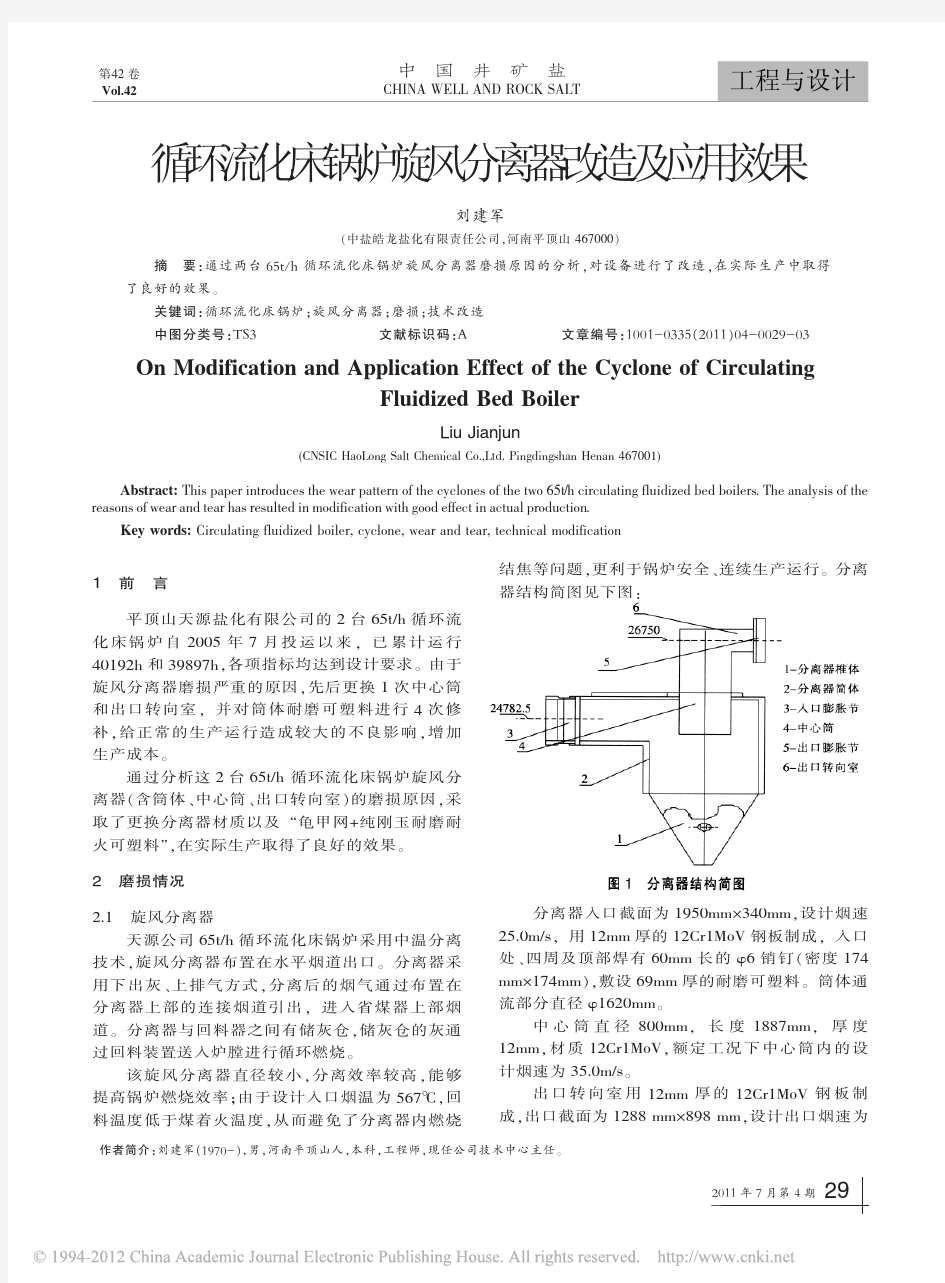

旋风分离器计算
作成 作成::时间时间::2009.5.14 一、問題提出 PHLIPS FC9262/01 這款吸塵器不是旋風除塵式的,現在要用這款吸塵器測參數選擇旋風分離裝置。二、計算過程 1.選擇工作狀況選擇工作狀況:: 根據空氣曲線選擇吸入效率最高點的真空度和流量作為旋風分離器的工作狀態。 吸塵器旋風分離器選擇 Bryan_Wang
已知最大真空度h和最大流量Q,則H-Q曲線的兩個軸截距已知,可確H-Q直線的方程。 再在這個直線上求得吸入功率H*Q最高點(求導數得)。求解過程不再詳述。求得最大吸入功率時真空度H=16.5kPa;流量Q=18.5L/s;吸入功率P2=305.25w 現將真空度及流量按照吸入功率計算值與實際值的比例放大,得真空度H=18.3kPa;流量Q=20.5L/s;2.選擇旋風分離器 為使旋風分離裝置體積最小,選擇允許的最小旋風分離器尺寸。一般旋風分離器筒體直徑不小于50mm,故選擇筒體直徑為50mm。按照標準旋風分離器的尺寸比例,確定旋風除塵器的結構尺寸。 D0=50mm b=12.5mm a=25mm de=25mm h0=20mm h=75mm H-h=100mm D2=12.5mm 計算α約為11度 發現計算得到的吸入功率最大值與產品標稱值375W相差一些,可能是由于測量誤差存在以及壓力損失的原因。
一般要求旋風分離器進氣速度不超過25m/s,這里取旋風分離器進氣速度為22m/s. 計算入口面積為S=3.125e-4平方米。 則單個旋風除塵器流量為Q=6.9e-3平方米/秒則所需旋風除塵器個數為3個計算分級效率 根據GB/T 20291-2006吸塵器標準,這里使用標準礦物灰塵,為大理石沙。进气粒径分布 103058 10019037575015002010 10102016113 顆粒密度ρp=2700kg/m3 進口含塵濃度取為10g/Nm3,大致選取空氣粘度μ=1.8e-6Pa*s 按照以下公式計算顆粒分級效率: 平均粒徑(μm)比重(%)
旋风分离器设计方案
旋风分离器设计方案 用户:特瑞斯信力(常州)燃气设备有限公司 型号: XC24A-31 任务书编号: SR11014 工作令: SWA11298 图号: SW03-020-00 编制:日期:
本设计中旋风分离器属于中压容器,应以安全为前提,综合考虑质量保证的各个环节,尽可能做到经济合理,可靠的密封性,足够的安全寿命。设计标准如下: a. TSG R0004-2009《固定式压力容器安全技术监察规程》 b. GB150-1998《钢制压力容器》 c. HG20584-1998《钢制化工容器制造技术要求》 d. JB4712.2-2007《容器支座》 2、旋风分离器结构与原理 旋风分离器结构简单、造价低廉,无运动部件,操作范围广,不受温度、压力限制,分离效率高。一般主要应用于需要高效除去固、液颗粒的场合,不论颗粒尺寸大小都可以应用,适用于各种燃气及其他非腐蚀性气体。 说明: 旋风分离器的总体结构主要由:进 料布气室、旋风分离组件、排气室、 集污室和进出口接管及人孔等部分组 成。旋风分离器的核心部件是旋风分 离组件,它由多根旋风分离管呈叠加 布置组装而成。 旋风管是一个利用离心原理的2 英寸管状物。待过滤的燃气从进气口 进入,在管内形成旋流,由于固、液 颗粒和燃气的密度差异,在离心力的 作用下分离、清洁燃气从上导管溜走, 固体颗粒从下导管落入分离器底部, 从排污口排走。由于旋风除尘过滤器 的工作原理,决定了它的结构型式是 立式的。常用在有大量杂物或有大量 液滴出现的场合。
其设计的主要步骤如下: ①根据介质特性,选择合适的壳体材料、接管、法兰等部件材料; ②设计参数的确定; ③根据用户提供的设计条件及参数,根据GB150公式,预设壳体壁厚; ④从连接的密封性、强度等出发,按标准选用法兰、垫片及紧固件; ⑤使用化工设备中心站开发的正版软件,SW6校核设备强度,确定壳体厚度及接管壁厚; ⑥焊接接头型式的选择; ⑦根据以上的容器设计计算,画出设计总设备图及零件图。 4、材料的选择 ①筒体与封头的材料选择: 天然气最主要的成分是甲烷,经过处理的天然气具有无腐蚀性,因此可选用一般的钢材。由操作条件可知,该容器属于中压、常温范畴。在常温下材料的组织性和力学性能没有明显的变化。综合了材料的机械性能、焊接性能、腐蚀情况、强度条件、钢板的耗材量与质量以及价格的要求,筒体和封头的材料选择钢号为Q345R的钢板,使用状态为热轧(设计温度为-20~475℃,钢板标准GB 713-2008 锅炉和压力容器用钢板)。 ②接管的材料选择: 根据GB150《钢制压力容器》引用标准以及接管要求焊接性能较好且塑性好的要求,故选择16Mn号GB6479《高压化肥设备用无缝钢管》作各型号接管。因设备设计压力较高,涉及到开孔补强问题,在后面的强度计算过程中,选择16MnII锻件作为接管材料。 ③法兰的材料选择: 法兰选用ASME B16.5-2009钢制管法兰,材质:16MnII,符合NB/T47008-2009压力容器用碳素钢和低合金钢锻件标准。 ④其他附件用材原则: 与受压件相焊的的垫板,选用与壳体一致的材料:Q345R GB713-2008; 其余非受压件,选用Q235-B GB3274 《碳素结构钢和低合金钢热轧厚钢板和
循环流化床燃烧技术旋风分离器
循环流化床燃烧技术 一、概念 循环流化床(CFB)燃烧技术是一项近二十年发展起来的清洁煤燃烧技术。它具有燃料适应性广、燃烧效率高、氮氧化物排放低、低成本石灰石炉内脱硫、负荷调节比大和负荷调节快等突出优点。 自循环流化床燃烧技术出现以来,循环床锅炉在世界范围内得到广泛的应用,大容量的循环床锅炉已被发电行业所接受。 循环流化床低成本实现了严格的污染排放指标,同时燃用劣质燃料,在负荷适应性和灰渣综合利用等方面具有综合优势,为煤粉炉的节能环保改造提供了一条有效的途径。 二、循环流化床燃烧技术发展历史回顾 主循环回路是循环流化床锅炉的关键,其主要作用是将大量的高温固体物料从气流中分离出来,送回燃烧室,以维持燃烧室稳定的流态化状态,保证燃料和脱硫剂多次循环、反复燃烧和反应,以提高燃烧效率和脱硫效率。 分离器是主循环回路的关键部件,其作用是完成含尘气流的气固分离,并把收集下来的物料回送至炉膛,实现灰平衡及热平衡,保证炉内燃烧的稳定与高效。从某种意义上讲,CFB锅炉的性能取决于分离器的性能,所以循环床技术的分离器研制经历了三代发展,而分离器设计上的差异标志了CFB燃烧技术的发展历程。 ●(一)绝热旋风筒分离器 德国Lurgi公司较早地开发出了采用保温、耐火及防磨材料砌装成筒身的高温绝热式旋风分离器的CFB锅炉[1]。分离器入口烟温在850℃左右。应用绝热旋风筒作为分离器的循环流化床锅炉称为第一代循环流化床锅炉,目前已经商业化。Lurgi公司、Ahlstrom公司、以及由其技术转移的Stein、ABB-CE、AEE、EVT等设计制造的循环流化床锅炉均采用了此种形式。 这种分离器具有相当好的分离性能,使用这种分离器的循环流化床锅炉具有较高的性能。但这种分离器也存在一些问题,主要是旋风筒体积庞大,因而钢耗较高,锅炉造价高,占地较大,旋风筒内衬厚、耐火材料及砌筑要求高、用量大、费用高启动时间长、运行中易出现故障;密封和膨胀系统复杂;尤其是
旋风分离器的设计(苍松参考)
旋风分离器的设计 姓名:顾一苇 班级:食工0801 学号:2008309203499 指导老师:刘茹 设计成绩:
华中农业大学食品科学与技术学院 食品科学与工程专业 2011年1月14日 目录 第一章、设计任务要求与设计条件 (3) 第二章、旋风分离器的结构和操作 (4) 第三章、旋风分离器的性能参数 (6) 第四章、影响旋风分离器性能的因素 (8) 第五章、最优类型的计算 (11) 第六章、旋风分离器尺寸说明 (19) 附录 1、参考文献 (20)
任务要求 1.除尘器外筒体直径、进口风速及阻力的计算 2.旋风分离器的选型 3.旋风分离器设计说明书的编写 4.旋风分离器三视图的绘制 5.时间安排:2周 6.提交材料含纸质版和电子版 设计条件 风量:900m3/h ; 允许压强降:1460Pa 旋风分离器类型:标准型 (XLT型、XLP型、扩散式) 含尘气体的参数: ?气体密度:1.1 kg/m3 ?粘度:1.6×10-5Pa·s ?颗粒密度:1200 kg/m3 ?颗粒直径:6μm
旋风分离器的结构和操作 原理: ?含尘气体从圆筒上部长方形切线进口进入,沿圆筒内壁作旋转流动。 ?颗粒的离心力较大,被甩向外层,气流在内层。气固得以分离。 ?在圆锥部分,旋转半径缩小而切向速度增大,气流与颗粒作下螺旋运动。 ?在圆锥的底部附近,气流转为上升旋转运动,最后由上部出口管排出; ?固相沿内壁落入灰斗。 旋风分离器不适用于处理粘度较大,湿含量较高及腐蚀性较大的粉尘,气量的波动对除尘效果及设备阻力影响较大。 旋风分离器结构简单,造价低廉,无运动部件,操作范围广,不受温度、压力限制,分离效率高。一般用于除去直径5um以上的尘粒,也可分离雾沫。对于直径在5um以下的烟尘,一般旋风分离器效率已不高,需用袋滤器或湿法捕集。其最大缺点是阻力大、易磨损。
循环流化床锅炉旋风分离器改造
循环流化床锅炉旋风分离器改造 俞信福 (宁波热电股份有限公司,浙江宁波 315800) [摘要]通过对我公司6#炉主蒸汽流量长期达不到额定出力的分析,首先从运行的角度入手,查阅相关资料分析入口烟速、飞灰浓度和粒 径、烟气温度等因素对分离器的影响不致于使其阻力严重偏低;然后从结构上对照设计图纸,实地观察为分离器短路造成其压差偏少,因此有针对性地对旋风分离器进行了改造,取得了较好的效果,为以后类似问题的解决提供了一定的思路。[关键词]循环流化床锅炉;旋风分离器;中心筒;短路 分离器是循环流化床锅炉的主要部件之一,它的分离性能对整个锅炉设计与稳定运行起着至关重要的作用。旋风分离器是目前循环流化床锅炉中应用最为广泛的一种分离装置,其结构简单,且分离效率较高,问题主要是体积较大。 1设备介绍 我公司6#炉为次高压循环流化床锅炉,由杭州锅炉集团有限公司制造生产的,型号为:NG-130/5.3-M7,在炉膛与尾部烟道之间布置有两台蜗壳式旋风分离器。旋风分离器的上半部分为蜗壳式入口,下半部分为锥形。烟气出口为圆筒形,由防磨耐热铸件拼接而成。颗粒和烟气先旋转下流至圆柱体的底部,粗颗粒将被分离,洁净烟气向上流动,离开旋风分离器。粗颗粒进入回料器。 旋风分离器为膜式包墙过热器结构,其顶部与底部均与环形集箱相连,墙壁管子在顶部向内弯曲,使得在旋风分离器管子和烟气出口圆筒之间形成密封结构。旋风分离器中心筒由5排筒板构成,每排筒板由24块ZG8Cr26Ni4Mn3Nre 组成,筒体进口内径Φ1470mm ,出口内径1662mm ,中心筒伸出长度1545mm ,并要求满焊,中心筒上部与耐磨浇注料相接并采用密封套结构,密封套用不锈钢丝网将硅酸铝棉板裹住,并用不锈钢丝将其缝牢,不锈钢丝和不锈钢丝网材料均为1Cr18Ni9Ti ,在密封套与耐磨浇注料之间用硅酸铝棉板塞实,以防气流短路。 2问题的提出及分析 我公司6#炉2005年1月投入运行以来,流量只能达到110t/h ,再带高就出现主蒸汽超温,减温水每只6t/h 全开主蒸汽温度还在455℃以上。从运行的角度对影响旋风分离器分离效率的因素进行分析,由于主蒸汽超温,首先想到温度对旋风分离器分离效率的影响,通过查阅资料,烟气温度影响着烟气的粘度,随着温度的升高,烟气的粘度随之增加,因而作用在运动颗粒的粘性阻力也会增加,从而使其分离效率下降。但是烟气的密度随着温度的增加而减少,从而使粘性阻力减少,因此烟气的温度对旋风分离器分离效率的作用并不明显。 旋风分离器进口烟速对其分离效率的影响,分离器的效率随着进口烟速的增大而增大,虽然当进口烟速过高时,由于紊流增加和尘粒反弹等因素使分离器的效率有所下降,按运行锅炉炉膛出口的压力和高温过热器进口压力比较,进口烟速不可能过高。最后是灰粒,灰粒的许多物理化学性能都对旋风分离器性能有影响,其中飞灰的浓度和粒径影响较大,分离效率随着飞灰的浓度的增加而增大,同时也随着飞灰的粒径增加而增大,而运行中5#炉和6#炉在用同一种煤时颗粒也一样,既使燃用不同的煤种锅炉负荷还是不会上来。从结构上分析旋风分离器为锅炉厂整体制造提供,与其进口烟道接口的支吊架位置材料都由锅炉厂提供,现场只是整体拼装,不可能出现大的偏差。从运行的参数比较分析,主要为分离器阻力偏低,主蒸汽超温,锅炉流量带不上。运行时分析是否为旋风分离器保温有问题,但保温问题也不应该影响分离器的效率,也考虑筒板少装,但4#炉的中心筒只有4排比三期少一排,也未出现炉膛灰浓度提不上,锅炉流量带不上情况。因此问题还是出在旋风分离器本身,5月下旬6#炉停炉时,经检查旋风分离器保温完好,从旋风分离器出口烟道处检查发现中心筒上部筒板开裂严重,大的裂缝有20mm ,长度大的为300mm 以上(一块筒板的有效高度为525mm ),中心筒上部耐磨浇注料与密封套之间的硅酸铝棉板已大部分 被短路的烟气拉走,因此在中心筒上部第二块筒板处均匀地割了4块,高度为300mm ,塞入用不锈钢丝网将硅酸铝棉板裹住缝牢的密封套,并在密封套与耐磨浇注料之间通过4个孔用硅酸铝棉板塞实,再用原筒板把4个孔补回,用专用焊条( 奥407铬26镍21不锈钢焊条)焊接,较大的缝采取耐热钢筋衬,并且满焊。投入运行的初期,主蒸汽流量曾到过120t/h ,以后一直在100t/h 以内。经过分析可能为焊缝为表面成形,且从4个孔塞棉的难度较大,中心筒出现裂缝后把部分硅酸铝棉板拉走,重新形成短路。8月份6#炉停炉后,与有关技术老师傅探讨后,对旋风分离器中心筒与分离器的密封进行了改造,见图1。 图1分离器中心改造图 保温层与分离器中心筒之间用硅酸铝棉板塞实后,用4mm 的SUS309密封,密封板外径Φ1770mm 内径Φ1610mm 的圆环分成若干段安装,每隔100mm 加一块4mm 的SUS309尺寸为40mm ×80mm 的筋板,并要求满焊,对旋风分离器中心筒出现的裂缝再次进行满焊,焊条仍为奥407铬26镍21不锈钢焊条。 3分离器改造前后运行参数比较 旋风分离器改造前主蒸汽流量长期不超过100t/h ,炉膛顶部P16/P19差压不超过1kPa (一般在0.75kPa 左右),(下转第144页)
旋风分离器设计计算的研究.
文章编号:1OO8-7524C 2OO3D O8-OO21-O3 IMS P 旋风分离器设计计算的研究 蔡安江 C 西安建筑科技大学机电工程学院, 陕西西安 摘要:在理论研究和设计实践的基础上, 提出了旋风分离器的设计计算方法O 关键词:旋风分离器9压力损失9分级粒径9计算中图分类号:TD 922+-5 文献标识码:A 71OO55D O 引言 旋风分离器在工业上的应用已有百余年历 离器性能的关键指标压力损失AP 作为设计其筒体直径D O 的基础, 用表征旋风分离器使用性能的关键指标分级粒径dc 作为其筒体直径D O 的修正依据, 来高效~准确~低成本地完成旋风分离器的设计工作O 1 压力损失AP 的计算方法 压力损失AP 是设计旋风分离器时需考虑的关键因素, 对低压操作的旋风分离器尤其重要O 旋风分离器压力损失的计算式多是用实验数据关联成的经验公式, 实用范围较窄O 由于产生压力损失的因素很多, 要详尽计算旋风分离器各部分的压力损失, 我们认为没有必要O 通常, 压力损失的表达式用进口速度头N H 表示较为方便O 进口速度头N H 的数值对任何旋风分离器将是常数O 目前, 使用的旋风分离器为减少压
力损失和入口气流对筒体内气流的撞击~干扰以及其内旋转气流的涡流, 进口形式大多从切向进口直入式改为18O ~36O 的蜗壳式, 但现有文献上的压力损失计算式均只适用于切向进口, 不具有通用性, 因此, 在参考大量实验数据的基础上, 我们提出了压力损失计算的修正公式, 即考虑入口阻力系数, 使其能适用于各种入口型式下的压力损失计算O 修正的压力损失计算式是: 史O 由于它具有价格低廉~结构简单~无相对运动部件~操作方便~性能稳定~压力损耗小~分离效率高~维护方便~占地面积小, 且可满足不同生产特殊要求的特点, 至今仍被广泛应用于化工~矿山~机械~食品~纺织~建材等各种工业部门, 成为最常用的一种分离~除尘装置O 旋风分离器的分离是一种极为复杂的三维~二相湍流运动, 涉及许多现代流体力学中尚未解决的难题, 理论研究还很不完善O 各种旋风分离器的设计工作不得不依赖于经验设计和大量的工业试验, 因此, 进行提高旋风分离器设计计算精度~提高设计效率, 降低设计成本的研究工作就显得十分重要O 科学合理地设计旋风分离器的关键是在设计过程中充分考虑其所分离颗粒的特性~流场参数和运行参数等因素O 一般旋风分离器常规设计的关键是确定旋风分离器的筒体直径D O , 只要准确设计计算出筒体直径D O , 就可以依据设计手册完成其它结构参数的标准化设计O 鉴于此, 我们在理论研究和设计实践的基础上, 提出了分级用旋风分离器筒体直径D O 的计算方法O 即用表征旋风分 收稿日期:2OO3-O3-O3 -21- AP = CjPV j 7N H 2
循环流化床锅炉旋风分离器返料器设计运行
循环流化床锅炉旋风分离器返料器设计运行 作者:华升加油枪加油机日期:2010-9-10 22:58:2 字体大小: 小中大 永嘉县华升阀门厂:滑过渡造成旋风分离器内壁不光滑,施工后应采取措施保证内壁光滑,在直段和锥段结合处也要保证光滑过渡。1.2.2保证返料器和旋风分离器之间密封良好如果密封不严,则会破坏炉膛、旋风分离器及返料器之间的压力平衡,造成返料间断或不返料,导致旋风分离器因堵灰而结焦。施工过程中,在保证整个锅炉密封的同时,要更加注意旋风分离器和返料器之间的密封。不要在旋风分离器上随意开一些检修孔和观察孔,开孔过多会影响旋风分离器的性能,也会导致旋风分离器因密封不严而漏风。1.2.3保证返料器各处尺寸在施工过程中,要保证返料器各处的尺寸,特别要注意返料器尺寸中的A、B两个尺寸(见图1),以防偏大或偏小。由于各地的煤质不同,其颗粒度的大小也不同,特别是低位发热量较低且小颗粒所占比例较大的无烟煤,运行时循环灰量比较大。锅炉运行一定时间后,尺寸A因磨损而不断减小,要经常检查耐火砖的损坏情况,避免尺寸A的数值为零或负值。这样将会导致呈正压的炉膛密相区热烟气反窜进入旋风分离器内,破坏旋风分离器的工作条件,使返料被迫中止。在安装时,尺寸B过小会使返料阻力增大,过大则会影响返料器位置的物料充满度,均不利于返料,应严格按图纸施工。图1U型返料器1.2.4采用冷却套管结构,控制返料器的温度当今国内已经研制出包敷整个旋风分离器的鳍片式及单管式旋风分离器,分为水冷与汽冷两种型式。由于水冷式旋风分离器在边壁处对热灰的温降较大,不利于煤的燃尽,使飞灰含碳量较高,目前多采用绝热分离器与汽冷分离器。在绝热分离器的料腿位置加设水冷套,以防止此位置因温度过高而结焦。加设水冷套装置的绝热分离器,运行十分稳定,飞灰含碳量较低。汽冷分离器的使用不但缩短了锅炉启动时间,还保持分离器内壁处于较高温度,且能有效地防止结焦的发生,倍受用户的青睐。1.2.5采取合适的风管结构风量和风压是返料器正常运行的基础,风量和风压只有同时达到要求,才能使返料器正常工作,任何一项达不到,返料器都不能正常工作。随着循环流化床锅炉的发展,返料器位置当前的送风方式大致分为集中送风和分配送风两种。集中送风大多应用于75t/h以下锅炉中,返料量少,返料器位置的流化风与返料风共用一个风箱(见图2),两者的风量分配通过彼此的风帽开孔率来达到,风箱接于一次风入口(或出口)处,风箱前的阀门保持一定开度就能达到运行需要。分配送风大多应用于130t/h以上锅炉中,返料量大,返料器位置的流化风与返料风各有一个风箱,通过支管接于返料专用风机母管上,在支管上设置调节阀。母管上设置流量计(见图3),从而较好地分配风量和控制总风量,达到控制返料量和返料温度的目的。如果返料风量达到最大但仍达不到运行要求,说明返料风压衰降过多,多为返料风管的沿程阻力过大所致,可通过增粗返料风管的途径来达到提高返料风压的目的。图2U型返料器1一返料器;2一风室;3一调节阀;4一风管;5~放渣管图3U型返料器1一返料器;2一返料风室;3一流化风室;4一调节阀;5一流
旋风分离器的设计
旋风分离器的设计公司内部编号:(GOOD-TMMT-MMUT-UUPTY-UUYY-DTTI-
旋风分离器的设计 姓名:顾一苇 班级:食工0801 指导老师:刘茹 设计成绩: 华中农业大学食品科学与技术学院 食品科学与工程专业 2011年1月14日 目录 第一章、设计任务要求与设计条件 (3) 第二章、旋风分离器的结构和操作 (4) 第三章、旋风分离器的性能参数 (6) 第四章、影响旋风分离器性能的因素 (8) 第五章、最优类型的计算 (11) 第六章、旋风分离器尺寸说明 (19) 附录 1、参考文献 (20) 任务要求 1.除尘器外筒体直径、进口风速及阻力的计算 2.旋风分离器的选型 3.旋风分离器设计说明书的编写 4.旋风分离器三视图的绘制
5.时间安排:2周 6.提交材料含纸质版和电子版 设计条件 风量:900m3/h ; 允许压强降:1460Pa 旋风分离器类型:标准型 (XLT型、XLP型、扩散式) 含尘气体的参数: 气体密度: kg/m3 粘度:×10-5Pa·s 颗粒密度:1200 kg/m3 颗粒直径:6μm 旋风分离器的结构和操作 原理: 含尘气体从圆筒上部长方形切线进口进入,沿圆筒内壁作旋转流动。 颗粒的离心力较大,被甩向外层,气流在内层。气固得以分离。 在圆锥部分,旋转半径缩小而切向速度增大,气流与颗粒作下螺旋运动。 在圆锥的底部附近,气流转为上升旋转运动,最后由上部出口管排出; 固相沿内壁落入灰斗。 旋风分离器不适用于处理粘度较大,湿含量较高及腐蚀性较大的粉尘,气量的波动对除尘效果及设备阻力影响较大。 旋风分离器结构简单,造价低廉,无运动部件,操作范围广,不受温度、压力限制,分离效率高。一般用于除去直径5um以上的尘粒,也可分离雾沫。对于
循环流化床锅炉旋风分离器的最新发展与高效运行 刘佳斌资料
循环流化床锅炉旋风分离器的最新发展与高效运行 刘佳斌 (山东大学能源与动力工程学院济南250010) 摘要:循环流化床的分离机构是循环流化床的关键部件之一,其主要作用是将大量高温固体物料从气流中分离出来,送回燃烧室,以维持燃烧室的快速流态化状态,保证燃料和脱硫剂多次循环、反复燃烧和反应。这样,才有可能达到理想的燃烧效率和脱硫效率。 关键词: 旋风分离器、循环流化床锅炉、循环效率、发展。 图1 75t/h循环流化床锅炉简图 1.循环流化床旋风分离器的工作原理 如图2、3为普遍采用的高温旋风分离器结构。此类分离器的体积庞大,占地面积与炉膛基本相当,它是利用旋转的含尘气体所产生的离心力,将颗粒从气流中分离出的一种干式气固分离装置。含灰烟气在炉膛出口处分进入旋风分离器,旋风分离器的圆形筒体和气体的切向入口使气固混合物进入围绕旋风分离器的2个同心涡流,外部涡流向下,内部涡流向上。由于固体密度比烟气密度大,在离心力作用下固体离开外部涡流移向壁面, 再沿旋风分离器的循环流化床的分离机构是循环流化床的关键部件 之一,其主要作用是将大量高温固体物料从气流中分 离出来,送回燃烧室,以维持燃烧室的快速流态化状态, 保证燃料和脱硫剂多次循环、反复燃烧和反应。这样, 才有可能达到理想的燃烧效率和脱硫效率。因此,循环 流化床分离机构的性能优劣,将直接影响整个循环流 化床锅炉的出力、效率及运行寿命。 随着循环流化床锅炉大型化的发展,对分离器提出 了更高的要求,它不但要能处理大容量的烟气,还要求 能在恶劣的环境中可靠、稳定运行。多年的商业运行 经验表明,高温旋风分离器目前仍是最适合(大型)循 环流化床锅炉的分离器之一。 图 3 高温旋风分离
旋风分离器计算结果
旋风除尘器性能的模拟计算 一、下图为旋风除尘器几何形状及尺寸,如图1所示,图中D、L 及入口截面的长宽比在数值模拟中将进行变化与调整,其余参数保持不变。 图1 旋风分离器几何形状及尺寸(正视图)
旋风分离器的空间视图如图2所示。 图2 旋风分离器空间视图 二、旋风分离器数值仿真中的网格划分 仿真计算时,首先对旋风除尘器进行网格划分处理,计算网格采用非结构化正交网格,如图3所示。 图3 数值仿真时旋风分离器的网格划分(空间)
图4为从空间不同角度所观测到的旋风分离器空间网格。 图4 旋风分离器空间网格空间视图 本数值仿真生成的非结构化空间网格数大约为125万,当几何尺寸(如D、L及长宽比)改变时,网格数会略有变化。 三、对旋风分离器的数值模拟仿真 采用混合模型,应用Eulerian(欧拉)模型,欧拉方法,对每种工况条件下进行旋风分离器流场与浓度场的计算,计算残差<10-5,每种工况迭代约50000步,采用惠普工作站计算,CPU耗时约12h。 以下是计算结果的后处理显示结果。由于计算算例较多,此处仅列出了两种工况条件下的计算后处理结果。 图5是L=1.3m,D=1.05m 入口长宽比1:3,入口速度10m/s时,在y=0截面(旋风分离器中心截面)上粒径为88微米烟尘的体积百分数含量分布图。可以明显看出由于旋风除尘器的离心作用,灰尘被甩到外壁附近,而在靠近中心排烟筒下方筒壁四周,烟尘的体积浓度最大。
粒径88微米烟尘的空间浓度分布(空间) 粒径88微米烟尘的浓度分布(旋风分离器中心截面)
粒径200微米烟尘的空间浓度分布(空间) 粒径200微米烟尘的浓度分布(旋风分离器中心截面) 图5 L=1.3m、D=1.05m、长宽比1:3,入口速度10m/s时烟尘空间分布
旋风分离器设计
旋风分离器: 旋风分离器,是用于气固体系或者液固体系的分离的一种设备。工作原理为靠气流切向引入造成的旋转运动,使具有较大惯性离心力的固体颗粒或液滴甩向外壁面分开。旋风分离器的主要特点是结构简单、操作弹性大、效率较高、管理维修方便,价格低廉,用于捕集直径5~10μm以上的粉尘,广泛应用于制药工业中。 主要功能: 旋风分离器设备的主要功能是尽可能除去输送气体中携带的固体颗粒杂质和液滴,达到气固液分离,以保证管道及设备的正常运行,在西气东输工程中,旋风分离器是较重要的设备。 机构简介: 旋风分离器,是用于气固体系或者液固体系的分离的一种设备。工作原理为靠气流切向引入造成的旋转运动,使具有较大惯性离心力的固体颗粒或液滴甩向外壁面分开。是工业上应用很广的一种分离设备。 工作原理: 旋风分离器是利用气固混合物在作高速旋转时所产生的离心力,将粉尘从气流中分离出来的干式气固分离设备。由于颗粒所受的离心力远大于重力和惯性力,所以分离效率较高。 常用的(切流)切向导入式旋风分离器的分离原理及结构如图所示。主要结构是一个圆锥形筒,筒上段切线方向装有一个气体入口管,圆筒顶部装有插入筒内一定深度的排气管,锥形筒底有接受细粉的出
粉口。含尘气流一般以12—30m/s速度由进气管进入旋风分离器时,气流将由直线运动变为圆周运动。旋转气流的绝大部分,沿器壁自圆筒体呈螺旋形向下朝锥体流动。此外,颗粒在离心力的作用下,被甩向器壁,尘粒一旦与器壁接触,便失去惯性力,而靠器壁附近的向下轴向速度的动量沿壁面下落,进入排灰管,由出粉口落入收集袋里。旋转下降的外旋气流,在下降过程中不断向分离器的中心部分流入,形成向心的径向气流,这部分气流就构成了旋转向上的内旋流。内、外旋流的旋转方向是相同的。最后净化气经排气管排出器外,一部分未被分离下来的较细尘粒也随之逃逸。自进气管流入的另一小部分气体,则通过旋风分离器顶盖,沿排气管外侧向下流动,当到达排气管下端时,与上升的内旋气流汇合,进入排气管,于是分散在这部分上旋气流中的细颗粒也随之被带走,并在其后用袋滤器或湿式除尘器捕集。 净化天然气通过设备入口进入设备内旋风分离区,当含杂质气体沿轴向进入旋风分离管后,气流受导向叶片的导流作用而产生强烈旋转,气流沿筒体呈螺旋形向下进入旋风筒体,密度大的液滴和尘粒在离心力作用下被甩向器壁,并在重力作用下,沿筒壁下落流出旋风管排尘口至设备底部储液区,从设备底部的出液口流出。旋转的气流在筒体内收缩向中心流动,向上形成二次涡流经导气管流至净化天然气室,再经设备顶部出口流出。 特点: 旋风分离器的主要特点是结构简单、操作弹性大、效率较高、管
循环流化床分离器
循环流化床分离装置 摘要: 气固两相流中的气固分离 气固分离器是循环流化床锅炉的关键部件,循环流化床锅炉采用高温气固分离还是中温气固分离是一个复杂的技术经济问题,气固分离器需要满足下述要求才能被循环流化床锅炉采用:(1)能有效地连续工作;(2)适应颗粒浓度变化;(3)具有较低的运行阻力和较高的分离效率。气固分离器在循环流化床中起着重要作用。它用在循环流化床锅炉中不同位置,则起着不同作用。用于循环流化床锅炉主循环回路的气固分离器主要有旋风分离器、惯性分离器两类。 关键字:旋风分离器、高温方形分离器、惯性分离器、组合分离器、分离器的性能指标、分离器的影响因素 引言:在循环流化床锅炉里,通常将分离器布置在锅炉炉膛出口,以便将高温烟气流中的热固体物料分离下来进入回料斗,再通过回料阀进人炉膛继续循环,以便保证炉膛内一定的灰浓度同时也提高了锅炉的燃烧效率。由于旋风筒是装在炉膛出口,烟温较高,锅炉满负荷运行时,炉膛出口温度一般为800~850摄氏度,因此旋风简要求由耐热材料制作这就是常说的高温温旋风分离器。除在炉膛出口安装旋风筒的布置方式外,也可采用过热器、再热器、省煤器之后布置旋风筒的半塔式布置,此处烟温较低,一般400~450左右摄氏度,这就是常说的中温旋风分离器。采用中温旋风分离,可以减少分离器体积和避免分离器在高温下的恶劣条件。旋风分离器的缺点是体积大,造价高。 惯性分离器多采用耐温耐磨的非金属材料作成,组合成特殊烟气通道,安装在循环流化床锅炉出口,烟气流通过分离器各内壁时,固体颗粒被分离下来进入料斗再通过回料阀,将分离下来的固体颗粒返回炉膛进行循环。与旋风分离器相比,这类分离器体积较小,适合于循环流化床锅炉整体化,但通常分离效率不佳,需要串联一个效率更高的分离器作为性能补偿。循环流化床燃烧技术兴起之前,气固分离技术广泛应用于化工、冶金、建材、医药等工业领域,在电力行业则着重于煤粉炉或层燃炉的烟气除尘。与循环流化床锅炉分离器不同的是,前者的目的是净化烟气,尽可能降低粉尘排放,其所处理的流动介质(烟气)一般含尘浓度不高(大多小于0.1kg/m3),温度较低(小于200。C),粉尘粒度较细微(多在
旋风分离器的工艺计算
旋风分离器的工艺计算 》 : *
目录 一.前言 (3) 应用范围及特点 (3) 分离原理 (3) 分离方法 (4) ) 性能指标 (4) 二.旋风分离器的工艺计算 (4) 旋风分离器直径的计算 (5) 由已知求出的直径做验算 (5) 计算气体流速 (5) < 计算旋风分离器的压力损失 (5) 旋风分离器的工作范围 (6) 进出气管径计算 (6) 三.旋风分离器的性能参数 (6) 分离性能 (6) ~ 临界粒径d pc (7) 分离效率 (8) 旋风分离器的压强降 (8) 四.旋风分离器的形状设计 (9) 五.入口管道设计 (10) $ 六.尘粒排出设计 (10) 七.算例(以天然气作为需要分离气体) (11) 工作原理 (11) 基本计算公式 (12) 算例 (13) ( 八.影响旋风分离器效率的因素 (14) 气体进口速度 (14) 气液密度差 (14) 旋转半径 (14) 参考文献 (15) …
' 旋风分离器的工艺计算 摘要:分离器已经使用十分广泛无论在家庭生活中还是工业生产,而且种类繁多每种都有各自的优缺点。现阶段旋风分离器运用比较广泛,它的性能的好坏主要决定于旋风分离器性能的强弱。这篇文章主要是讨论旋风分离器工艺计算。旋风分离器是利用离心力作用净制气体,主要功能是尽可能除去输送介质气体中携带的固体颗粒杂质和液滴,以达到气固液分离,以保证管道及设备的正常运行。在本篇文章中,主要是对旋风分离器进行工艺计算。 [ 关键字:旋风分离器、工艺计算 一.前言 旋风分离器设备的主要功能是尽可能除去输送介质气体中携带的固体颗粒杂质和液滴,达到气固液分离,以保证管道及设备的正常运行。它是利用旋转气流产生的离心力将尘粒从气流中分离出来。旋风分离器结构简单,没有转动部分制造方便、分离效率高,并可用于高温含尘气体的分离,而得到广泛运用。 ' 旋风分离器采用立式圆筒结构,内部沿轴向分为集液区、旋风分离区、净化室区等。内装旋风子构件,按圆周方向均匀排布亦通过上下管板固定;设备采用裙座支撑,封头采用耐高压椭圆型封头。设备管口提供配对的法兰、螺栓、垫片等。 通常,气体入口设计分三种形式: a) 上部进气 b) 中部进气 c) 下部进气 对于湿气来说,我们常采用下部进气方案,因为下部进气可以利用设备下部空间,对直径大于300μm或500μm的液滴进行预分离以减轻旋风部分的负荷。而对于干气常采用中部进气或上部进气。上部进气配气均匀,但设备直径和设备高度都将增大,投资较高;而中部进气可以降低设备高度和降低造价。 应用范围及特点 旋风分离器适用于净化大于1-3微米的非粘性、非纤维的干燥粉尘。它是一种结构简单、
循环流化床锅炉旋风分离器改造及应用效果.
第42卷 中国井矿盐 Vol.42 CHINAWELLANDROCKSALT 工程与设计 循环流化床锅炉旋风分离器改造及应用效果 刘建军 (中盐皓龙盐化有限责任公司,河南平顶山467000) 摘要:通过两台65t/h循环流化床锅炉旋风分离器磨损原因的分析,对设备进行了改造,在实际生产中取得 了良好的效果。 关键词:循环流化床锅炉;旋风分离器;磨损;技术改造中图分类号:TS3 文献标识码:A 文章编号:1001-0335(2011)04-0029-03 OnModificationandApplicationEffectoftheCycloneofCirculating FluidizedBedBoiler LiuJianjun (CNSICHaoLongSaltChemicalCo.,Ltd.PingdingshanHenan467001) Abstract:Thispaperintroducesthewearpatternofthecyclonesofthetwo65t/hcirculatingfluid izedbedboilers.Theanalysisofthereasonsofwearandtearhasresultedinmodificationwithgoo deffectinactualproduction. Keywords:Circulatingfluidizedboiler,cyclone,wearandtear,technicalmodification 结焦等问题,更利于锅炉安全、连续生产运行。分离器结构简图见下图:6267505 1-分离器椎体2-分离器简体 24782.534 2 3-入口膨胀节4-中心筒5-出口膨胀节6-出口转向室 1前言 平顶山天源盐化有限公司的2台65t/h循环流化床锅炉自2005年7月投运以来,已累计运行 40192h和39897h,各项指标均达到设计要求。由于旋风分离器磨损严重的原因,先后更换1次中心筒和出口转向室,并对筒体耐磨可塑料进行4次修 补,给正常的生产运行造成较大的不良影响,增加生产成本。
旋风分离器地设计
旋风分离器的设计 姓名: 顾一苇 班级: 食工0801 学号: 29 指导老师: 刘茹 设计成绩: 华中农业大学食品科学与技术学院 食品科学与工程专业 2011年1月14日 目录 第一章、设计任务要求与设计条件 (3) 第二章、旋风分离器的结构与操作 (4) 第三章、旋风分离器的性能参数 (6) 第四章、影响旋风分离器性能的因素 (8) 第五章、最优类型的计算 (11) 第六章、旋风分离器尺寸说明 (19) 附录 1、参考文献 (20) 任务要求 1.除尘器外筒体直径、进口风速及阻力的计算 2.旋风分离器的选型
3.旋风分离器设计说明书的编写 4.旋风分离器三视图的绘制 5.时间安排:2周 6.提交材料含纸质版与电子版 设计条件 风量:900m3/h ; 允许压强降:1460Pa 旋风分离器类型:标准型 (XLT型、XLP型、扩散式) 含尘气体的参数: ?气体密度:1、1 kg/m3 ?粘度:1、6×10-5Pa·s ?颗粒密度:1200 kg/m3 ?颗粒直径:6μm 旋风分离器的结构与操作 原理: ?含尘气体从圆筒上部长方形切线进口进入,沿圆筒内壁作旋转流动。 ?颗粒的离心力较大,被甩向外层,气流在内层。气固得以分离。 ?在圆锥部分,旋转半径缩小而切向速度增大,气流与颗粒作下螺旋运动。 ?在圆锥的底部附近,气流转为上升旋转运动,最后由上部出口管
排出; ?固相沿内壁落入灰斗。 旋风分离器不适用于处理粘度较大,湿含量较高及腐蚀性较大的粉尘,气量的波动对除尘效果及设备阻力影响较大。 旋风分离器结构简单,造价低廉,无运动部件,操作范围广,不受温度、压力限制,分离效率高。一般用于除去直径5um以上的尘粒,也可分离雾沫。对于直径在5um以下的烟尘,一般旋风分离器效率已不高,需用袋滤器或湿法捕集。其最大缺点就是阻力大、易磨损。
旋风分离器的工艺计算
旋风分离器的工艺计算
目录 一.前言 (3) 1.1应用范围及特点 (3) 1.2分离原理 (3) 1.3分离方法 (4) 1.4性能指标 (4) 二.旋风分离器的工艺计算 (4) 2.1旋风分离器直径的计算 (5) 2.2由已知求出的直径做验算 (5) 2.2.1计算气体流速 (5) 2.2.2计算旋风分离器的压力损失 (5) 2.2.3旋风分离器的工作范围 (6) 2.3进出气管径计算 (6) 三.旋风分离器的性能参数 (6) 3.1分离性能 (6) 3.1.1临界粒径d pc (7) 3.1.2分离效率 (8) 3.2旋风分离器的压强降 (8) 四.旋风分离器的形状设计 (9) 五.入口管道设计 (10) 六.尘粒排出设计 (10) 七.算例(以天然气作为需要分离气体) (11) 7.1工作原理 (11) 7.2基本计算公式 (12) 7.3算例 (13) 八.影响旋风分离器效率的因素 (15) 8.1气体进口速度 (15) 8.2气液密度差 (15) 8.3旋转半径 (15) 参考文献 (15)
旋风分离器的工艺计算 摘要:分离器已经使用十分广泛无论在家庭生活中还是工业生产,而且种类繁多每种都有各自的优缺点。现阶段旋风分离器运用比较广泛,它的性能的好坏主要决定于旋风分离器性能的强弱。这篇文章主要是讨论旋风分离器工艺计算。旋风分离器是利用离心力作用净制气体,主要功能是尽可能除去输送介质气体中携带的固体颗粒杂质和液滴,以达到气固液分离,以保证管道及设备的正常运行。在本篇文章中,主要是对旋风分离器进行工艺计算。 关键字:旋风分离器、工艺计算 一.前言 旋风分离器设备的主要功能是尽可能除去输送介质气体中携带的固体颗粒杂质和液滴,达到气固液分离,以保证管道及设备的正常运行。它是利用旋转气流产生的离心力将尘粒从气流中分离出来。旋风分离器结构简单,没有转动部分制造方便、分离效率高,并可用于高温含尘气体的分离,而得到广泛运用。 旋风分离器采用立式圆筒结构,内部沿轴向分为集液区、旋风分离区、净化室区等。内装旋风子构件,按圆周方向均匀排布亦通过上下管板固定;设备采用裙座支撑,封头采用耐高压椭圆型封头。设备管口提供配对的法兰、螺栓、垫片等。 通常,气体入口设计分三种形式: a) 上部进气 b) 中部进气 c) 下部进气 对于湿气来说,我们常采用下部进气方案,因为下部进气可以利用设备下部空间,对直径大于300μm或500μm的液滴进行预分离以减轻旋风部分的负荷。而对于干气常采用中部进气或上部进气。上部进气配气均匀,但设备直径和设备高度都将增大,投资较高;而中部进气可以降低设备高度和降低造价。 1.1应用范围及特点 旋风分离器适用于净化大于1-3微米的非粘性、非纤维的干燥粉尘。它是一种结构简单、操作方便、耐高温、设备费用和阻力较高(80~160毫米水柱)的净化设备,旋风分离器在净化设备中应用得最为广泛。改进型的旋风分离器在部分装置中可以取代尾气过滤设备。 1.2分离原理 旋风分离器的分离原理有两种: 一、利用组分质量(重量)不同对混合物进行分离(如分离方法1、2、3、6)。 二、利用分散系粒子大小不同对混合物进行分离(如分离方法4、5)。
第十二讲 旋风分离器的设计和非标设计方法
第十二讲旋风分离器的设计和非标设计方法 旋风分离器是对流干燥系统的重要组成部分。我们对此必须要足够地重视,有一些失败的对流干燥系统,不是干燥器设计不合理,而是旋风分离器设计或选用不合理。 在气流干燥和旋转闪蒸干燥系统中,有80~90%的产品是通过旋风分离器回收的,只有10~20%的产品是通过布袋除尘器回收的。如果旋风分离器‘失灵’,大量的产品就‘拥挤’到布袋除尘器中,增加布袋除尘器的阻力,造成风机风压不够,以致干燥系统‘瘫痪’。 在喷雾干燥系统中,对于喷雾干燥塔底部作为主要回收产品的系统来说,也有将近30%的产品要通过旋风分离器回收;对于喷雾干燥塔底部不收集产品的系统(如中药浸膏喷雾干燥系统),就有全部或85%以上的产品要通过旋风分离器收集。 对于振动流化床干燥系统和转筒干燥系统也有5~10%的细微颗粒要通过旋风分离器回收。 一、旋风分离器的结构和工作原理: (一)、旋风分离器的结构: 一般来说,旋风分离器由进风管,直筒,锥形筒,排灰管,锁风阀和排风管组成(见图1)。 (二)、工作原理: 当含尘气流以14~22m/s速度由进风管进入旋风分离器时,气流将由直线运动变为圆周运动。旋转气流的绝大部分沿直圆筒的内壁呈螺旋形向下,
朝锥形筒体运动。通常称此气流为‘外旋气流’。含尘气流在旋转过程中产生离心力,将重度大于气体的尘粒甩向筒内壁。尘粒一旦与筒壁接触,便失去惯性力,而靠入口速度的动量和向下的重力沿壁面下落,进入排灰管。旋转下降的外旋气流在到达锥体时,因圆锥形的收缩而向除尘器中心靠拢。根据‘旋转矩’不变原理,其切向速度不断提高。当气流到达锥体下端某一位置时,即以同样的旋转方向从旋风分离器中部,由下反转而上,继续作螺旋运动,即为‘内旋气流’。最后净化气体经排风内管排出器外,一部分未被捕获的尘粒也由此随排风排出旋风分离器。 自进气管流入的另一小部分气体,则向旋风分离器顶盖流动,然后沿排气管外侧向下流动。当到达排气管下端时,即反转向上随上升的中心气流(内旋气流)一同从排气管排出。分散在这一部分上旋气流中的尘粒也随同被带走。 二、旋风分离器的内部气流分布简介和旋风分离器的特点: 由于旋风分离器的分离,捕集过程是一种极为复杂的三维,二相湍流运动,致使理论与实验研究十分困难。.另外,设备的结构不同,几何尺寸的不一,尤其是气—固两相本身物理性质的差异,操作条件的变化等等因素,都对旋风分离器的主要性能----效率,压力损失有显著的影响.因此,至今仍无法全面掌握它们运动的内在规律,更不能从理论上建立一套完整的成熟的数学模型。我们在这里仅介绍与我们有关旋风分离器的定性和半定量的知识。 (一)、旋风分离器的内部气流分布简介: 1.气流在旋风分离器内是复杂的三维运动,器内任一点上都有切向、径向和轴向速度,其中切向速度对分离性能和压力损失影响最大。在旋风分