OPNET Go-back-N ARQ仿真
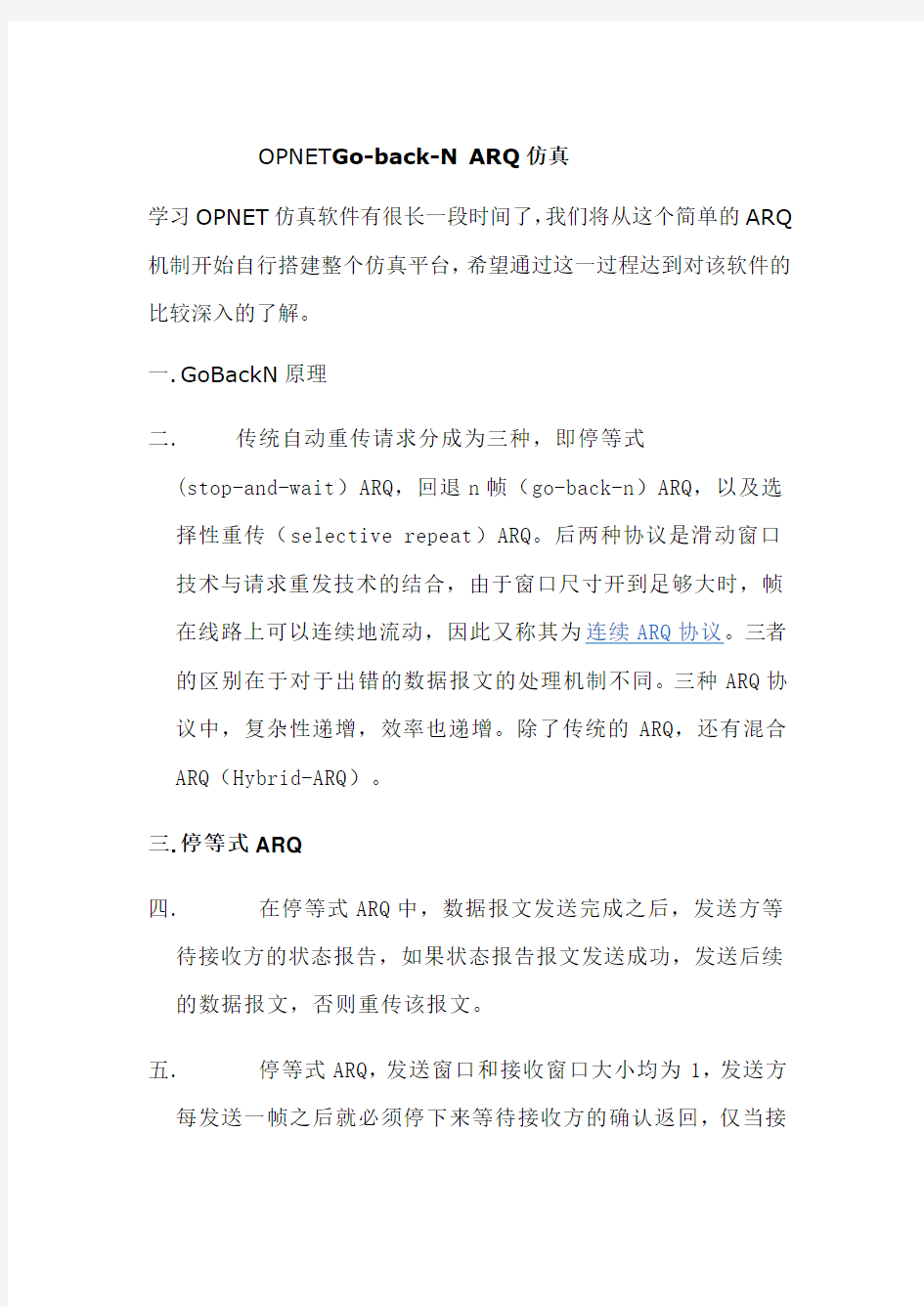

OPNET Go-back-N ARQ仿真
学习OPNET仿真软件有很长一段时间了,我们将从这个简单的ARQ 机制开始自行搭建整个仿真平台,希望通过这一过程达到对该软件的比较深入的了解。
一.GoBackN原理
二. 传统自动重传请求分成为三种,即停等式
(stop-and-wait)ARQ,回退n帧(go-back-n)ARQ,以及选择性重传(selective repeat)ARQ。后两种协议是滑动窗口技术与请求重发技术的结合,由于窗口尺寸开到足够大时,帧在线路上可以连续地流动,因此又称其为连续ARQ协议。三者的区别在于对于出错的数据报文的处理机制不同。三种ARQ协议中,复杂性递增,效率也递增。除了传统的ARQ,还有混合ARQ(Hybrid-ARQ)。
三.停等式ARQ
四. 在停等式ARQ中,数据报文发送完成之后,发送方等
待接收方的状态报告,如果状态报告报文发送成功,发送后续的数据报文,否则重传该报文。
五. 停等式ARQ,发送窗口和接收窗口大小均为1,发送方
每发送一帧之后就必须停下来等待接收方的确认返回,仅当接
收方确认正确接收后再继续发送下一帧。该方法所需要的缓冲存储空间最小,缺点是信道效率很低。
六.回退n帧的ARQ
七. 在回退n帧的ARQ中,当发送方接收到接收方的状态
报告指示报文出错后,发送方将重传过去的n个报文。
八. 回退N,发送窗口大于1,接收窗口等于1。允许发送
方可以连续发送信息帧,但是,一旦某帧发生错误,必须重新发送该帧及其后的n帧。这种方式提高了信道的利用率,但允许已发送有待于确认的帧越多,可能要退回来重发的帧也越多。
九.选择性重传ARQ
十. 在选择性重传ARQ中,当发送方接收到接收方的状态
报告指示报文出错,发送方只发送传送发生错误的报文。
十一. 选择重传协议,发送窗口和接收窗口都大于1。发送方仅重新传输发生错误的帧,并缓存错误帧之后发送的帧。与回退N相比,减少了出错帧之后正确的帧都要重传的开销。
十二.混合ARQ
十三.在混合ARQ中,数据报文传送到接收方之后,即使出错也不会被丢弃。接收方指示发送方重传出错报文的部分或者
全部信息,将再次收到的报文信息与上次收到的报文信息进行合并,以恢复报文信息。
当接收方收到一个乱序帧时,将会请求发送方重新传输从该乱序帧开始的后面N个帧。例如,发送方发送完8号帧后,发现接收方在接收2号帧时出错,这时发送方将会重传2到8号帧。基本原理图如下:
二.仿真设计思路
1.在该仿真中,我将先从最里层的PROCESS状态机开始实现。
初步设想为发送方和接收方两个PROCESS,实现发送方到接
收方的单向传输。下面将分别进行讨论。
2.发送方主要实现两个功能:发送和重传。
3.接收方主要实现两个功能:接收处理和发送反馈信息。
4.状态机设计时需要考虑的问题
5.发送端的Process状态机主要包含5个状态:init、idle、
send_data、re_transfer和ip_arrival。
6.接收端的Process状态机主要包括4个状态:init、idle、
receive_data、send_ack。
7.发送端需要着重考虑的问题有:如何控制多长时间发送一个包、
发送条件需要包括哪些因素、重传时候的判断机制、定时器的
设置等。
8.接收方需要着重考虑的问题有:如何判断该数据是否为正确接
收的数据、移动接收窗口的设置、定时器的设置等。
发送端:
1.发送窗口设置。发送窗口用来对发送端流量进行控制。而发送窗口的大小表示在没有收到对方确认信息的情况下,发送端最多能够发送的数据帧的个数。本仿真中将采用3bit来对发送序号进行编码。因此,将发送窗口大小设置为7。
2.发送方将维护1个队列:发送窗口队列。发送方的协议处理模块在收到上层传输过来的数据后,会将其插入到发送窗口队列中。根据定时中断控制其向接收端的发送。
3.发送方的发送超时定时器。发送方对于从发送窗口发送出去的数据都会启动一个发送超时定时器,当规定时间内还未收到接收方的确认信息,则对该数据进行超时重传。
接收方:
1.接收窗口设置。接收窗口是为了控制可以接受哪些帧而不可以接受哪些帧。在本仿真中,由于采用的连续ARQ协议,接收窗口大小设置为1.
2.接收方将维护1个队列:接收窗口队列。当接收方接收到从发送方传输过来的数据后,会将其插入到接收窗口队列中去。并对其接收状态进行确认。如果为正确接收,则将其从接收窗口中删除,并且移动接收窗口,定时发送确认信息。如果为错误接收,则就诶收窗口不移动。
3.接收方只对正确接收的数据进行确认。同时采用累积的确认方式:一段时间后,对该时间之前接收窗口内所有正确接收的数据包进行一次性确认,只发送该确认包给接收端。
仿真图如下:
曲柄连杆机构运动学仿真
课程设计任务书
目录 1 绪论 (1) 1.1CATIA V5软件介绍 (1) 1.2ADAMS软件介绍 (1) 1.3S IM D ESIGNER软件介绍 (2) 1.4本次课程设计的主要内容及目的 (2) 2 曲柄连杆机构的建模 (3) 2.1活塞的建模 (3) 2.2活塞销的建模 (5) 2.3连杆的建模 (5) 2.4曲轴的建模 (6) 2.5汽缸体的建模 (8) 3 曲柄连杆机构的装配 (10) 3.1将各部件导入CATIA装配模块并利用约束命令确定位置关系 (10) 4 曲柄连杆机构导入ADAMS (14) 4.1曲柄连杆机构各个零部件之间运动副分析 (14) 4.2曲柄连杆机构各个零部件之间运动副建立 (14) 4.3曲柄连杆机构导入ADAMS (16) 5 曲柄连杆机构的运动学分析 (17) 结束语 (21) 参考文献 (22)
1 绪论 1.1 CATIA V5软件介绍 CATIA V5(Computer-graphics Aided Three-dimensional Interactive Application)是法国Dassault公司于1975年开发的一套完整的3D CAD/CAM/CAE一体化软件。它的内容涵盖了产品概念设计、工业设计、三维建模、分析计算、动态模拟与仿真、工程图的生成、生产加工成产品的全过程,其中还包括了大量的电缆和管道布线、各种模具设计与分析、人机交换等实用模块。CATIA V5不但能保证企业内部设计部门之间的协同设计功能而且还可以提供企业整个集成的设计流程和端对端的解决方案。CATIA V5大量应用于航空航天、汽车及摩托车行业、机械、电子、家电与3C产业、NC加工等领域。 由于其功能的强大而完美,CATIA V5已经成为三维CAD/CAM领域的一面旗帜和争相遵从的标准,特别是在航空航天、汽车及摩托车领域。法国的幻影2000系列战斗机就是使用CATIA V5进行设计的一个典范;波音777客机则使用CATIA V5实现了无图纸设计。另外,CATIA V5还用于制造米其林轮胎、伊莱克斯电冰箱和洗衣机、3M公司的粘合剂等。CATIA V5不仅给用户提供了详细的解决方案,而且具有先进的开发性、集成性及灵活性。 CATIA V5的主要功能有:三维几何图形设计、二维工程蓝图绘制、复杂空间曲面设计与验证、三维计算机辅助加工制造、加工轨迹模拟、机构设计及运动分析、标准零件管理。 1.2 ADAMS软件介绍 ADAMS即机械系统动力学自动分析(Automatic Dynamic Analysis of Mechanical Systems),该软件是美国MDI公司(Mechanical Dynamics Inc.)开发的虚拟样机分析软件。目前,ADAMS己经被全世界各行各业的数百家主要制造商采用。根据1999年机械系统动态仿真分析软件国际市场份额的统计资料,ADAMS软件销售总额近八千万美元、占据了51%的份额。 ADAMS软件使用交互式图形环境和零件库、约束库、力库,创建完全参数化的机械系统几何模型,其求解器采用多刚体系统动力学理论中的拉格郎日方程方法,建立系统动力学方程,对虚拟机械系统进行静力学、运动学和动力学分析,输出位移、速度、加速度和反作用力曲线。ADAMS软件的仿真可用于预测机械系统的性能、运动范围、
基于Workbench仿真的内燃机曲柄连杆机构动力学分析
基于Workbench的仿真内燃机曲柄连 杆机构动力学分析 (机械与动力工程学院南京 211816) 摘要:本文以S195 内燃机为例,对单缸内燃机的曲柄连杆机构简化模型 进行了有限元分析。根据力学分析结果和强度要求设计内燃机曲柄连杆机构结构,并应用UG软件建立该机构三维数字化虚拟装配模型,结合有限元理论及其分析软件ANSYS Workbench,模拟分析了曲柄连杆机构装配体动力学分析,结果表明,数字化模型结合装配体有限元分析,可解决曲柄连杆机构结构强度评价问题,有助于缩短汽油机开发周期和减少成本。 关键词:曲柄连杆,有限元分析,Workbench,动力学仿真。 Dynamic analysis of the crank connecting rod mechanism based on Workbench simulation (Nanjing Technology of University, mechanical and power engineering, Yin Zhenhua, Nanjing, 211816) Abstract Based on the S195 diesel engine as an example, the crank connecting rod mechanism of single cylinder diesel engine was analyzed in finite element analysis. According to the mechanical analysis results and strength requirements, the structure of the engine crank connecting rod mechanism is designed, and the 3D digital virtual assembly model of the mechanism is established. Combined with the finite element theory and the analysis software ANSYS Workbench. The results show that the numerical model combined with the finite element analysis can solve the problem of structural strength evaluation of the crank link mechanism, which helps to shorten the development cycle and reduce the cost. Key words: crank connecting rod, finite element analysis, Workbench, dynamic simulation.
SolidWorks的曲柄连杆机构动力学仿真研究
基于SolidWorks的曲柄连杆机构动力学仿真研究 发表时间:2012-2-28 作者: 陈敏*刘晓叙来源: 万方数据 关键字: 发动机运动学动力学仿真 本文用SolidWorks软件建立了一个简化的单缸发动机模型,用COSMOS Motion对该模型进行了发动机运动学和动力学仿真,对运动学仿真的结果进行了验证。 设计往复活塞式发动机时,要进行发动机的运动学和动力学计算,发动机的运动学是计算发动机活塞的位移、速度和加速度。动力学计算主要包括主要运动件的载荷,为零件的强度计算提供依据。在过去的设计中,发动机的运动学和动力学引算一般是采用计算机编程的方式进行。 SolidWorks是目前应用较为广泛的三维设计软件,COSMOS Motion是以ADAMS软件的技术为内核的机构运动学和动力学仿真软件,是SolidWorks的一个插件,与SolidWorks可以进行无缝对接。我们运用该软件,对一个简化的单缸发动机模型进行了运动学与动力学仿真,其结果对往复活塞式发动机的运动学和动力学设计计算有参考意义,现将研究情况介绍如下: 1 发动机模型的基本情况 为了研究的需要,建立了一个简化的单缸发动机模型,主要的结构参数为:缸径125mm,行程160mm,连杆大、小头孔中心距210mm,λ=0.381。发动机的活塞、活塞销、连杆和曲轴用SolidWorks进行三维实体造型设计,然后进行装配,发动机装配后效果及坐标系见图1。 图1 发动机模型 2 发动机的运动学仿真 由于是对一个特定的模型作定量的运动学和动力学仿真,所以,从简单起见,在仿真参数中,将曲轴的转速设为60r/min,即1r/s。在COSMOS Motion中运行仿真后,可以得到活塞运行的位移、速度和加速度,见图2、图3、图4。
汽车曲柄连杆机构设计
摘要 本文以捷达EA113汽油机的相关参数作为参考,对四缸汽油机的曲柄连杆机构的主要零部件进行了结构设计计算,并对曲柄连杆机构进行了有关运动学和动力学的理论分析与计算机仿真分析。 首先,以运动学和动力学的理论知识为依据,对曲柄连杆机构的运动规律以及在运动中的受力等问题进行详尽的分析,并得到了精确的分析结果。其次分别对活塞组、连杆组以及曲轴进行详细的结构设计,并进行了结构强度和刚度的校核。再次,应用三维CAD软件:Pro/Engineer建立了曲柄连杆机构各零部件的几何模型,在此工作的基础上,利用Pro/E软件的装配功能,将曲柄连杆机构的各组成零件装配成活塞组件、连杆组件和曲轴组件,然后利用Pro/E软件的机构分析模块(Pro/Mechanism),建立曲柄连杆机构的多刚体动力学模型,进行运动学分析和动力学分析模拟,研究了在不考虑外力作用并使曲轴保持匀速转动的情况下,活塞和连杆的运动规律以及曲柄连杆机构的运动包络。仿真结果的分析表明,仿真结果与发动机的实际工作状况基本一致,文章介绍的仿真方法为曲柄连杆机构的选型、优化设计提供了一种新思路。 关键词:发动机;曲柄连杆机构;受力分析;仿真建模;运动分析;Pro/E
ABSTRACT This article refers to by the Jeeta EA113 gasoline engine’s related parameter achievement, it has carried on the structural design compution for main parts of the crank link mechanism in the gasoline engine with four cylinders, and has carried on theoretical analysis and simulation analysis in computer in kinematics and dynamics for the crank link mechanism. First, motion laws and stress in movement about the crank link mechanism are analyzed in detail and the precise analysis results are obtained. Next separately to the piston group, the linkage as well as the crank carries on the detailed structural design, and has carried on the structural strength and the rigidity examination. Once more, applys three-dimensional CAD software Pro/Engineer establishing the geometry models of all kinds of parts in the crank link mechanism, then useing the Pro/E software assembling function assembles the components of crank link into the piston module, the connecting rod module and the crank module, then using Pro/E software mechanism analysis module (Pro/Mechanism), establishes the multi-rigid dynamics model of the crank link, and carries on the kinematics analysis and the dynamics analysis simulation, and it studies the piston and the connecting rod movement rule as well as crank link motion gear movement envelopment. The analysis of simulation results shows that those simulation results are meet to true working state of engine. It also shows that the simulation method introduced here can offer a new efficient and convenient way for the mechanism choosing and optimized design of crank-connecting rod mechanism in engine. Key words: Engine;Crankshaft-Connecting Rod Mechanism;Analysis of Force;Modeling of Simulation;Movement Analysis;Pro/E
发动机曲柄连杆机构动力学运动规律仿真研究
发动机曲柄连杆机构动力学运动规律仿真研究 Dynamics simulation analysis of engine crank connecting rod mechanism 黄硕 东风商用车有限公司发动机厂 湖北省十堰市 442001 摘 要:本文从动力学角度研究了曲柄连杆机构的工作原理,,建立简易曲柄连杆机构的三维实体模型,利用机械系统动力学仿真分析软件HyperWorks,对dCi11发动机曲柄连杆机构进行仿真;并基于模态综合分析法研究柔性体的力学性能,对连杆进行了动态特性分析,得出连杆在自由模态情况下的模态振型;然后对该曲柄连杆机构进行运动学和动力学分析,得到连杆在一个工作循环过程中应力变化规律,从而确定了连杆的受力边界条件以及危险工况分析,为连杆优化设计和强度校核提供了依据,并为进一步分析和研究曲柄连杆机构特性提供了参考。 关键词:曲柄连杆机构 多体系统动力学 模态分析 结构优化 HyperWorks Abstract: This paper has studied the crank works from dynamics perspective. the mechanical system dynamics simulation software HyperWorks has simulated the crank of engine of car;And based on a comprehensive analysis of modal,Studied flexible body the mechanical properties and conducted a dynamic characteristics analysis to the connecting rod.Rod in the case of free modal shape has been came out.Then the crank has done kinematic and dynamic analysis, the connecting rod determined the linkage of the force boundary condition sin a work cycle variation of stress, and dangerous working conditions analysis, link optimization and strength check provides the basis for further analysis and study crank feature provides a reference. Keywords:Crank and Connecting Rod Mechanism, Multi-Body Dynamics, Model Analysis, Structural optimization, HyperWorks 1 课题研究意义 目前,随着工程技术的发展在研究曲柄连杆机构的运动学和动力学分析方法很多,而且已经较完善和成熟。其中机构运动学分析是研究两个或两个以上物体间的相对运动即位移、速度和加速度随时间变化的关系,动力学则是研究产生运动的力。通过对机构运动学和动力学分析,我们可以清楚了解曲柄连杆机构工作的运动性能、运动规律等,从而可以更好地对机构进行性能分析和产品设计。但是过去由于手段的原因,大部分复杂的机构运动尽管能够给出解析式,却难以计算出供工程使用的计算结果,不得不用粗糙的图解法求得数据。随着计算机的发展,通过计算机辅助设计、校核和计算的系统,可以更直观清晰地了解曲柄连杆机构在运行过程中的受力状态,便于进行精确计算,并绘制受力分析曲线图,对进一步研究内燃机的平衡与振动等均有较为实用的应用价值。
汽车曲柄连杆机构毕业设计说明书
本科毕业设计(论文)通过答辩 优秀论文设计,答辩无忧,值得下载!摘要 本文以捷达EA113汽油机的相关参数作为参考,对四缸汽油机的曲柄连杆机构的主要零部件进行了结构设计计算,并对曲柄连杆机构进行了有关运动学和动力学的理论分析与计算机仿真分析。 首先,以运动学和动力学的理论知识为依据,对曲柄连杆机构的运动规律以及在运动中的受力等问题进行详尽的分析,并得到了精确的分析结果。其次分别对活塞组、连杆组以及曲轴进行详细的结构设计,并进行了结构强度和刚度的校核。再次,应用三维CAD软件:Pro/Engineer建立了曲柄连杆机构各零部件的几何模型,在此工作的基础上,利用Pro/E软件的装配功能,将曲柄连杆机构的各组成零件装配成活塞组件、连杆组件和曲轴组件,然后利用Pro/E软件的机构分析模块(Pro/Mechanism),建立曲柄连杆机构的多刚体动力学模型,进行运动学分析和动力学分析模拟,研究了在不考虑外力作用并使曲轴保持匀速转动的情况下,活塞和连杆的运动规律以及曲柄连杆机构的运动包络。仿真结果的分析表明,仿真结果与发动机的实际工作状况基本一致,文章介绍的仿真方法为曲柄连杆机构的选型、优化设计提供了一种新思路。 关键词:发动机;曲柄连杆机构;受力分析;仿真建模;运动分析;Pro/E
本科毕业设计(论文)通过答辩 优秀论文设计,答辩无忧,值得下载!ABSTRACT This article refers to by the Jeeta EA113 gasoline engine’s related parameter achievement, it has carried on the structural design compution for main parts of the crank link mechanism in the gasoline engine with four cylinders, and has carried on theoretical analysis and simulation analysis in computer in kinematics and dynamics for the crank link mechanism. First, motion laws and stress in movement about the crank link mechanism are analyzed in detail and the precise analysis results are obtained. Next separately to the piston group, the linkage as well as the crank carries on the detailed structural design, and has carried on the structural strength and the rigidity examination. Once more, applys three-dimensional CAD software Pro/Engineer establishing the geometry models of all kinds of parts in the crank link mechanism, then useing the Pro/E software assembling function assembles the components of crank link into the piston module, the connecting rod module and the crank module, then using Pro/E software mechanism analysis module (Pro/Mechanism), establishes the multi-rigid dynamics model of the crank link, and carries on the kinematics analysis and the dynamics analysis simulation, and it studies the piston and the connecting rod movement rule as well as crank link motion gear movement envelopment. The analysis of simulation results shows that those simulation results are meet to true working state of engine. It also shows that the simulation method introduced here can offer a new efficient and convenient way for the mechanism choosing and optimized design of crank-connecting rod mechanism in engine. Key words: Engine;Crankshaft-Connecting Rod Mechanism;Analysis of Force;Modeling of Simulation;Movement Analysis;Pro/E
一种气动发动机曲柄连杆机构的仿真性能研究
一种气动发动机曲柄连杆机构的仿真性能研究 气动发动机是以高压空气作为“燃料”,来提供动力。由于高压空气能力密度较低,且气动发动机的能量利用率低,因此,改善其能量利用率,提高其机械效率至关重要。曲柄连杆机构是发动机动力传输的核心机构,对发动机的整体工作及汽车的动力传递起到至关重要的作用。通过研究一种新型气动发动机的曲柄连杆机构,利用MATLAB/Simulink对其运动特性进行仿真分析,分析其对气动发动机性能的影响,研究结果为今后进一步提高气动发动机的效率提供了指导方向。 标签:曲轴;连杆;气动发动机;运动学仿真;发动机性能 0引言 气动发动机以压缩空气作为工质,将高压空气直接输入气缸膨胀以推动活塞做功,实现了将高压空气的压力能转化为转动形式的机械能输出。与传统内燃机相比,气动发动机的做功原理比较简单,通过气体膨胀推动活塞做功,进而对外输出功率,实现了无燃烧、零污染物,是真正意义上的绿色动力汽车。气动发动机具有突出的特点和很好的应用前景,但其能量利用效率低是最为突出的和最需要迫切解决的问题。 曲柄连杆机构是发动机实现工作循环,完成能量转换的关键部件,它将活塞的周期往复运动转变为曲轴的旋转运动,从而对外输出转矩,为汽车提供行驶所需的动力,对发动机的可靠性、动力性影响很大。一直以来,以曲柄连杆机构为基础的往复活塞式发动机的研究及进展对汽车行业乃至整个工业的发展起着较大的推动作用。当活塞在作往复运动时,其速度和加速度的数值及变化规律对曲柄连杆机构以及内燃机整体的工作有很大影响,研究曲柄连杆机构运动学的主要任务实际上就是研究活塞的运动规律。为了进一步提高循环热效率和燃烧效率以及机械效率,优化内燃机的性能,众多国内外的专家学者都对传统往复式活塞所用的曲柄连杆机构(图1)进行改进,试图通过对内燃机曲柄连杆机构的改进提高其性能。笔者对一种新的双连杆往复机构进行仿真研究,这种曲柄连杆机构的结构特点,使得其在运动过程中,活塞在上止点附近停留时间较长。本文对应用这种机构的气动发动机建立了数学模型,利用Matlab/simulink进行仿真,并与传统往复活塞式曲柄连杆机构进行对比,得出仿真结果。此外,对这种新型曲柄连杆机构的活塞运动规律以及有可能对气功发动机工作过程产生的影响作了简要分析。 1.1传统曲柄连杆机构数学模型及求解 根据图1所示,设OB=R为曲拐中心到曲轴旋转中心的距离(即曲柄),AB=L 为连杆长度,λ=R/L。活塞在上止点时(A1位置)曲轴转角为0,活塞在下止点时(A2位置)曲轴转角为180°。由此可推导出活塞的位移为:
往复式割刀曲柄连杆机构的运动特性仿真
往复式割刀曲柄连杆机构的运动特性仿真 设计说明书 1 绪论 大力发展农业机械化是我国现代农业发展的必要条件,只有实现农业机械化,才能真正提高农 民收入,人民的生活水平才能得以改善。切割器是各种收割机械的重要工作部件。目前,各种收割 机械普遍采用的切割器有往复式和回转式两种。往复式割刀副较宽,并且工作效率高,可获得较好 的采摘质量,割茬平齐,且不会产生割碎作物的现象。其缺点是工作惯性力大,割台震动和噪音都 很大,广泛应用于谷物收获。回转式切割器用于收获牧草、青饲料、粗秆作物等,少数谷物也使用 这种切割器。回转式切割器的切割速度高,惯性力容易平衡,震动较小,割刀的结构比较简单。但 受回转直径的限制,不能用于宽幅切割,割刀的寿命较短,维修费很高。 当前,收获机上使用的切割器以往复式最多,而且制造技术趋于完善,只是在局部有所改进, 但其惯性力不平衡仍是主要问题。. 国内收割机起步较晚,早期以模仿及从苏联,美国及加拿大等国家进口为主。很多连接或支撑 部件没有经过详细的计算,二十根据发达国家已造好的收割机的尺寸设计制造的,使得收割机体积 庞大,质量偏大。大型收割机是非常复杂的机械装备,大型收割机的使用对土地的平整和规模有更 高的要求,华北平原,三江平原等重要的小麦,水稻产区很早就使用联合收割机进行生产。相对大 型收割机,小型收割机的设计更随意,现在国内很多院校都开始尝试针对设计制造小型收割机。这 些院校设计适合本地土地环境和生产力的小型收割机,这种收割机价格低,维修简单,使用方便, 适合各种地形,保养要求低,适合小农户规模的生产。 往复式割刀驱动机构,其作用是将源动力的旋转转换为割刀所需的直线往复式运动。目前,国 内的收割机采用的往复式机构种类众多。大致上可以归纳为曲柄连杆机构和摆环机构两类。 传统的往复式手工费器大都采用单边驱动,惯性力很难平衡,日本久保田麦稻联合收割机将刀 杆分成两段, 采用两个曲柄连杆机构双边驱动, 两段刃杆的运动方向总是相反, 可部分抵消惯性力。 由于南方水田深泥脚,水稻收获是切割器易被泥土卡住,因此久保田收割机将刀杆加宽,在其底部 挖了排泥孔,割刀在运动时可将进入切割器间隙的泥土及时排出。此外,这种机型还加装了割刀自 动润滑系统, 可将润滑油自动滴到刀杆上, 随动刀的运动而进入摩擦间隙, 以免手工加油发生危险。 1.1 切割器的要求 切割器是收获机械的重要部件之一, 它的功用是将田间的作物切断, 切割器应该满足一下要求: 1)切割质量好:割茬整齐,不漏割,不重割,不堵刀,切割损失小; 2)切割省力,功率消耗少,振动小; 3)通用性好,结构简单,调整方便。 切割器按照其运动方式可分为往复式和回转式两种,经过多年的研究,其技术已较为成熟,基 本可以满足上述需要,但也存在许多问题。 1.2 影响切割质量的因素 切割质量与切割器的特性、茎秆的物理性能、切割器与茎秆的相对位置以及切割的速度和方向 都有密切的关系。 1)切割器的机构
基于ug的发动机曲轴连杆机构的虚拟设计与运动仿真
基于U G 的发动机曲轴连杆机构的 虚拟设计与运动仿真 Engine Crank and Link Mechanism Virtual Design and Motion Animation B ased on UG 韦尧兵 聂文忠 (兰州理工大学机电学院,兰州 730050) 摘 要:三维模型虚拟设计是机械设计的必然趋势。该文简述了三维设计软件U G NX110的强大功能,并且结合发动机曲柄连杆机构实现了模型的虚拟设计、虚拟装配及三维动态仿真。 关键词:虚拟设计 虚拟装配 三维动态仿真 Abstract :Three -dimentional model virtual design is the tendency of mechanic design.The paper simply state its powerful function of U G NX110with three dimentional design soft ,and realize model virtual design 、virtual assembly and three -dimentional dynamic animation combined with engine crank and link mechanism. K ey w ords :virtual design virtual assembly three -dimentional dynamic animation 作者简介:韦尧兵 1965年生,兰州理工大学机电工程学院副教授、硕士,甘肃省“555”创新人才工程人选。研究方向 为裂纹技术及其装备和CAD/CAM ,发表论文23篇,获省部级科技进步三等奖1项,厅局级科技进步二等奖1项。 聂文忠 1971年生,兰州理工大学机电学院在读研究生。 0 引言 虚拟技术是近年来随着计算机辅助设计技术发展起来的一种新型技术。随着计算机辅助技术的发展,传统的以AutoCad 为代表的二维设计越来越不能满足工业生产、设计的需求。它不仅开发时间长,而且功能单一,设计过程中不能够及时地发现设计中存在的问题。本文简要介绍了美国U GS 公司开发的U G 软件及其在虚拟设计中的应用。 1 UG 软件简介 Unigraphics (简称U G )软件是美国U GS 公司的五大主要产品(U G ,Parasolid ,iMAN ,Solid Edge ,Product Vision )之一。U G 软件起源于美国 麦道飞机公司,并于1991年并入美国通用汽车公司EDS (电子资讯系统有限公司),因此,该软件汇集了美国航空工业及汽车工业的专业经验[1]。 U G 是一个高度集成的CAD/CAM/CAE 软件系统,可应用于整个产品的开发过程,包括产品的建模、分析和加工。 U G 不仅具有强实体造型、曲面造型、虚拟装配和产生工程图等设计功能,而且在设计过程中可进行有限元分析、机构运动分析、动力学分析和仿真模拟等,提高了产品设计的可靠性。同时,可用建立的三维模型直接生成数控代码,用于产品的加工,其后处理程序能够支持多种类型的数控机床。另外它所提供的二次开发语言U G/Open 64机电一体化 Mechatronics 2005年第1期
汽车四缸汽油机的曲柄连杆机构设计
本科毕业设计(论文)通过答辩 I 摘 要 本文以捷达EA113汽油机的相关参数作为参考,对四缸汽油机的曲柄连杆机构的主要零部件进行了结构设计计算,并对曲柄连杆机构进行了有关运动学和动力学的理论分析与计算机仿真分析。 首先,以运动学和动力学的理论知识为依据,对曲柄连杆机构的运动规律以及在运动中的受力等问题进行详尽的分析,并得到了精确的分析结果。其次分别对活塞组、连杆组以及曲轴进行详细的结构设计,并进行了结构强度和刚度的校核。再次,应用三维CAD 软件:Pro/Engineer 建立了曲柄连杆机构各零部件的几何模型,在此工作的基础上,利用Pro/E 软件的装配功能,将曲柄连杆机构的各组成零件装配成活塞组件、连杆组件和曲轴组件,然后利用Pro/E 软件的机构分析模块(Pro/Mechanism),建立曲柄连杆机构的多刚体动力学模型,进行运动学分析和动力学分析模拟,研究了在不考虑外力作用并使曲轴保持匀速转动的情况下,活塞和连杆的运动规律以及曲柄连杆机构的运动包络。仿真结果的分析表明,仿真结果与发动机的实际工作状况基本一致,文章介绍的仿真方法为曲柄连杆机构的选型、优化设计提供了一种新思路。 关键词:发动机;曲柄连杆机构;受力分析;仿真建模;运动分析; Pro/E
本科毕业设计(论文)通过答辩 ABSTRACT This article refers to by the Jeeta EA113 gasoline engine’s related parameter achievement, it has carried on the structural design compution for main parts of the crank link mechanism in the gasoline engine with four cylinders, and has carried on theoretical analysis and simulation analysis in computer in kinematics and dynamics for the crank link mechanism. First, motion laws and stress in movement about the crank link mechanism are analyzed in detail and the precise analysis results are obtained. Next separately to the piston group, the linkage as well as the crank carries on the detailed structural design, and has carried on the structural strength and the rigidity examination. Once more, applys three-dimensional CAD software Pro/Engineer establishing the geometry models of all kinds of parts in the crank link mechanism, then useing the Pro/E software assembling function assembles the components of crank link into the piston module, the connecting rod module and the crank module, then using Pro/E software mechanism analysis module (Pro/Mechanism), establishes the multi-rigid dynamics model of the crank link, and carries on the kinematics analysis and the dynamics analysis simulation, and it studies the piston and the connecting rod movement rule as well as crank link motion gear movement envelopment. The analysis of simulation results shows that those simulation results are meet to true working state of engine. It also shows that the simulation method introduced here can offer a new efficient and convenient way for the mechanism choosing and optimized design of crank-connecting rod mechanism in engine. Key words: Engine;Crankshaft-Connecting Rod Mechanism;Analysis of Force;Modeling of Simulation;Movement Analysis;Pro/E II
曲柄滑块机构的运动学matlab仿真
代码实例 [anim_zzy1.m] function f=anim_zzy1(K,ki) % anim_zzy1.m 演示红色小球沿一条封闭螺线运动的实时动画% 仅演示实时动画的调用格式为anim_zzy1(K) % 既演示实时动画又拍摄照片的调用格式为f=anim_zzy1(K,ki)% K 红球运动的循环数(不小于1 ) % ki指定拍摄照片的瞬间,取1 到1034 间的任意整数。 % f 存储拍摄的照片数据,可用image(f.cdata) 观察照片。 % 产生封闭的运动轨线 t1=(0:1000)/1000*10*pi;x1=cos(t1);y1=sin(t1);z1=-t1; t2=(0:10)/10;x2=x1(end)*(1-t2);y2=y1(end)*(1-t2);z2=z1(end)*ones(size(x2)); t3=t2;z3=(1-t3)*z1(end);x3=zeros(size(z3));y3=x3; t4=t2;x4=t4;y4=zeros(size(x4));z4=y4; x=[x1 x2 x3 x4];y=[y1 y2 y3 y4];z=[z1 z2 z3 z4]; plot3(x,y,z, 'b' ), axis off % 绘制曲线% 定义" 线" 色、" 点" 型(点)、点的大小(40 )、擦除方式(xor) h=line( 'Color' ,[1 0 0], 'Marker' , '.' , 'MarkerSize' ,40, 'EraseMode' , 'xor' );% 使小球运动 n=length(x);i=1;j=1; while 1 % 无穷循环 set(h, 'xdata' ,x(i), 'ydata' ,y(i), 'zdata' ,z(i)); % 小球位置 drawnow; % 刷新屏幕<21> pause(0.0005) % 控制球速<22> i=i+1; ifnargin==2 &nargou t==1 % 仅当输入宗量为2 、输出宗量为1 时,才拍摄照片 if (i==ki&j==1);f=getframe(gcf); end % 拍摄i=ki时的照片<25> end if i>n i=1;j=j+1; if j>K; break ; end end end (2)在指令窗中运行以下指令,就可看到实时动画图形。 f=anim_zzy1(2,450); (3)显示拍摄的照片 image(f.cdata),axis off %曲柄连杆机构充气球动画演示程序 hf=figure('name','打气筒吹气球');set(hf,'color','g');axis([-10,10,-4,4]);hold onaxis off; %除掉坐标 xa0=-2.5;%活塞左顶点坐标xa1=-1.8;%活塞右顶点坐标xb0=-2;%连杆左顶点坐标xb1=5;%连杆右顶点坐标 x3=5.6;%转轮坐标y3=0;%转轮坐标x4=xb1;%设置连杆头的初始位置横坐标 y4=0;%设置连杆头的初始位置纵坐标 x5=xa1;y5=0;x6=x3;%设置连轴初始横坐标 y6=0;%设置连轴初始纵坐标 a=0.7;b=0.7;c=0.7; a1=line([xa0;xa1],[0;0],'color','m','linestyle','-','linewidth',20); %设置活塞 a8=line([-2.7;2.3],[0.3;0.3],'color','b','linestyle','-','linewidth',5);%设置打气筒 a9=line([-2.6;2.3],[-0.3;-0.3],'color','b','linestyle','-','linewidth',5);%设置打气筒 a10=line([-2.6;-2.6],[-0.1;-0.37],'color','b','linestyle','-','linewidth',5);%设置打气筒 a11=line([2.0;2.0],[0.1;0.37],'color','b','linewidth',5);%设置打气筒 a12=line([2.0;2.0],[-0.1;-0.37],'color','b','linewidth',5);%设置打气筒