公差尺寸英寸和毫米的互换算

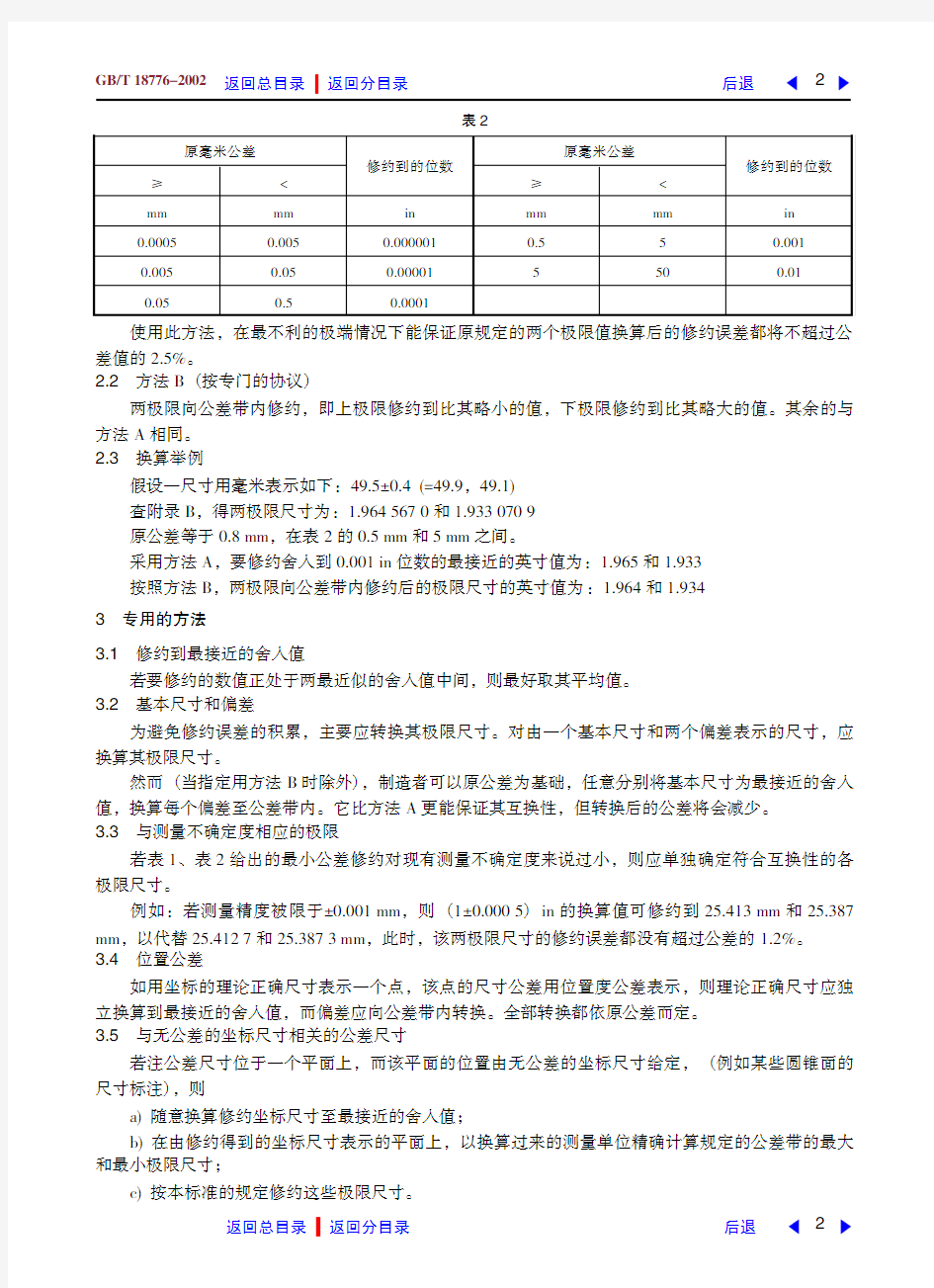
中国第一重型机械集团公司标准
公差尺寸英寸和毫米的互换算
GB/T 18776-2002
中国第一重型机械集团公司2008-12-01批准
2008-12-31实施
本标准规定了英寸和毫米间相互换算的方法,以保证互换算后规定公差的互换性。1英寸换算为毫米
1.1方法A (一般规则)
a)对每个英寸尺寸,仅考虑其最大和最小两个极限。
b)用换算式1in=25.4mm 准确地将两对应的极限值换算为毫米(可查附录A )。c)按原英寸公差(即英寸的两个极限之差)将换算结果修约为如表1所列的最接近的舍入值。使用此方法,在最不利的极端情况下能保证原规定的两个极限值换算后的修约误差都将不超过公差值的2%。1.2方法B (按专门的协议)
两极限向公差带内修约,即上极限修约到比其略小的值,下极限修约到比其略大的值。其余的与方法A 相同。
表1
原英寸公差修约到的位数
原英寸公差修约到的位数
≥<
≥<
in
in
mm
in
in
mm 0.000010.00010.000010.010.10.01
0.00010.0010.00010.11
0.1
0.0010.01
0.001
1.3换算举例
假设某一尺寸用英寸表达如下:1.950±0.016(=1.966,1.934)查附录A ,得两极限尺寸为:49.9364和49.1236
原公差等于0.032in ,在表1的0.01in 和0.1in 之间。
采用方法A ,要修约舍入到
0.01
mm 位数的最接近的毫米值为:49.94和49.12按照方法B ,两极限向公差带内修约后的极限尺寸的毫米值为:49.93和49.132毫米换算为英寸
2.1方法A (一般规则)
a)对每个毫米尺寸,仅考虑其最大和最小两个极限。
b)用换算式1mm=1/25.4in 准确地将两对应的极限值换算为英寸(可查附录B )。c)按原毫米公差(即毫米的两极限之差)将换算结果修约为如表2所列的最接近的舍入值。1
后退
返回分目录返回总目录
表2
原毫米公差
修约到的位数
原毫米公差
修约到的位数≥<≥<
mm mm in mm mm in
0.00050.0050.0000010.550.001
0.0050.050.000015500.01
0.050.50.0001
使用此方法,在最不利的极端情况下能保证原规定的两个极限值换算后的修约误差都将不超过公差值的2.5%。
2.2方法B(按专门的协议)
两极限向公差带内修约,即上极限修约到比其略小的值,下极限修约到比其略大的值。其余的与方法A相同。
2.3换算举例
假设一尺寸用毫米表示如下:49.5±0.4(=49.9,49.1)
查附录B,得两极限尺寸为:1.9645670和1.9330709
原公差等于0.8mm,在表2的0.5mm和5mm之间。
采用方法A,要修约舍入到0.001in位数的最接近的英寸值为:1.965和1.933
按照方法B,两极限向公差带内修约后的极限尺寸的英寸值为:1.964和1.934
3专用的方法
3.1修约到最接近的舍入值
若要修约的数值正处于两最近似的舍入值中间,则最好取其平均值。
3.2基本尺寸和偏差
为避免修约误差的积累,主要应转换其极限尺寸。对由一个基本尺寸和两个偏差表示的尺寸,应换算其极限尺寸。
然而(当指定用方法B时除外),制造者可以原公差为基础,任意分别将基本尺寸为最接近的舍入值,换算每个偏差至公差带内。它比方法A更能保证其互换性,但转换后的公差将会减少。
3.3与测量不确定度相应的极限
若表1、表2给出的最小公差修约对现有测量不确定度来说过小,则应单独确定符合互换性的各极限尺寸。
例如:若测量精度被限于±0.001mm,则(1±0.0005)in的换算值可修约到25.413mm和25.387 mm,以代替25.4127和25.3873mm,此时,该两极限尺寸的修约误差都没有超过公差的1.2%。3.4位置公差
如用坐标的理论正确尺寸表示一个点,该点的尺寸公差用位置度公差表示,则理论正确尺寸应独立换算到最接近的舍入值,而偏差应向公差带内转换。全部转换都依原公差而定。
3.5与无公差的坐标尺寸相关的公差尺寸
若注公差尺寸位于一个平面上,而该平面的位置由无公差的坐标尺寸给定,(例如某些圆锥面的尺寸标注),则
a)随意换算修约坐标尺寸至最接近的舍入值;
b)在由修约得到的坐标尺寸表示的平面上,以换算过来的测量单位精确计算规定的公差带的最大和最小极限尺寸;
c)按本标准的规定修约极限尺寸。
表A.1
in
mm
in
mm
1/641/323/641/165/643/327/641/8
9/645/3211/643/1613/647/3215/641/417/649/3219/645/1621/6411/3223/643/825/6413/3227/647/1629/6415/3231/641/20.0156250.0312500.0468750.0625000.078125
D .0937500.1093750.1250000.1406250.1562500.1718750.1875000.2031250.2187500.2343750.2500000.2656250.2812500.2968750.3125000.3281250.3437500.3593750.375000
.3906250.4062500.4218750.4375000.4531250.4687500.4843750.5000000.3968750.7937501.1906251.5875001.9843752.3812502.7781253.1750003.5718753.9687504.3656254.7625005.1593755.5562505.9531256.3500006.7468757.1437507.5406257.9375008.3343758.7312509.1281259.5250009.921875
10.31875010.71562511.11250011.50937511.90625012.30312512.70000033/6417/3235/649/16
37/6419/3239/645/841/6421/3243/6411/1645/6423/3247/643/449/6425/3251/6413/1653/6427/3255/647/857/6429/3259/6415/166l/6431/3263/6410.5156250.581250
0.5488750.562500
0.5781250.5937500.609375
0.6250000.640625
0.6562500.6718750.6875000.7031250.7187500.734375
0.7600000.765625
0.7812500.7968750.8125000.8281250.8437500.859375
0.8750000.890625
0.9062500.9218750.9375000.9531250.9687500.984375
1.000000
13.09687513.49375013.89062514.28750014.68437515.08125015.47812515.87500016.27187516.66875017.06562517.46250017.85937518.25625018.65312519.05000019.44687519.84375020.24062520.63750021.03437521.43125021.82812522.22500022.62187523.01875023.41562523.81250024.20937524.60625025.00312525.400000
例如:假定锥度为0.05的某一圆锥体,在由无公差的位置尺寸0.93in 表示的坐标面上的直径为(1±0.002)in 。由于圆锥的锥度,公差带的极限尺寸取决于坐标面的位置。因此,如把尺寸0.93in=23.622mm 修约为23.6mm ,比修约前减少了0.022mm 当把两原极限尺寸精确地换算为毫米时,在修约前应用0.022mm ×0.05=0.0011mm 进行适当的修正。
附录A (规范性附录)英寸到毫米的换算表
A.1分数英寸
表A.2
表A.3in mm in
mm
in
mm
in
mm
1234567891011121314151617181920212223242525.450.876.2
101.6127.0152.4177.8203.2228.6254.0279.4304.8330.2355.6381.0406.4431.8457.2482.6508.0533.4558.8584.2609.6635.026272829303132333435363738394041424344454647484950
660.4685.8711.2736.6762.0787.4812.8838.2863.6889.0914.4939.8965.2990.6
1016.01041.41066.81092.21117.61143.01168.41193.81219.21244.61270.0
51
525354555657585960616263646566676869707172737475
1295.41320.81346.21371.61397.01422.41447.81473.21498.61524.01549.41574.81600.21625.61651.01676.41701.81727.21752.61778.01803.41828.81854.21879.61905.0
76777879808l
8283848586878889909192939495969798991001930.4
1955.81981.2
2006.62032.02057.42082.82108.22133.62159.02184.42209.82235.2
2260.6
2286.02311.4
2336.82362.22387.6
2413.02438.42463.82489.22514.6
2540.0in
mm
in
mm
in
mm
0.0010.0020.0030.0040.0050.0060.02540.05080.07620.10160.12700.1524
0.0070.0080.0090.010.020.03
0.17780.20320.22860.2540.5080.7620.70.80.917.7820.3222.86in
mm
in
mm
0.040.050.060.070.080.091.0161.2701.524
1.778
2.032
2.286
0.10.20.3
0.40.50.62.545.087.6210.1612.7015.24A.2小数英寸和整数英寸
表B.1
mm
in
mm
in
mm in
0.0010.0020.0030.0040.0050.0060.00003940.00007870.00011810.00015750.00019690.0002362
0.0070.0080.0090.010.020.030.00027560.00031500.00035430.00039370.00078740.00118110.70.80.9
0.02755910.03149610.0354331
mm
in
mm in
0.040.050.060.070.080.090.0015748
0.0019685
0.0023622
0.0027559
0.0031496
0.0035433
0.1
0.20.30.4
0.50.60.0039370
0.0078740
0.01181100.0157480
0.01968500.0236220表B.2
mm in mm in mm in
mm in
12345678910
1112131415161718192021222324250.03937010.07874020.11181020.15748030.19685040.23622050.27559060.31496060.35433070.39370080.43307090.47844090.51181100.55118110.59053120.62902130.66929130.70866140.74803150.78740160.82677170.86614170.90551180.94488190.9842520
26272829303132333435363738394041424344454647484950
1.02362201.06299211.10236221.14173231.18110241.22047241.25984251.29921261.33858271.37795281.41732281.45669291.49606301.53543311.57480311.61417321.65354331.69291341.73228341.77165351.81102361.85039371.88976381.92913391.9685039
51525354555657585960616263646566676869707172737475
2.00787402.0472441
2.0866142
2.12598422.16535432.2047244
2.24409452.28346462.32283462.36220472.40157482.44094492.48031502.51968502.55905512.59842522.63779532.6771654
2.7165354
2.75590552.7952756
2.83464572.87401572.9133858
2.9527559767778798081828384858687888990919293949596979899
1002.99212603.03149613.07086613.11023623.14960633.18897643.22834653.26771653.30708663.34645673.38582683.42519683.46456693.50393703.54330713.58267723.62204723.66141733.70078743.74015753.77952763.81889763.85826773.89763783.9370079
附录B (规范性附录)毫米到英寸的换算表
工序尺寸及其公差的确定与加工余量大小
工序尺寸及其公差的确定与加工余量大小
工序尺寸及其公差的确定与加工余量大小,工序尺寸标注方法及定位基准的选择和变换有密切的关系。下面阐述几种常见情况的工序尺寸及其公差的确定方法。 (一)从同一基准对同一表面多次加工时工序尺寸及公差的确定 属于这种情况的有内外圆柱面和某些平面加工,计算时只需考虑各工序的余量和该种加工方法所能达到的经济精度,其计算顺序是从最后一道工序开始向前推算,计算步骤为: 1 .确定各工序余量和毛坯总余量。 2 .确定各工序尺寸公差及表面粗糙度。 最终工序尺寸公差等于设计公差,表面粗糙度为设计表面粗糙度。其它工序公差和表面粗糙度按此工序加工方法的经济精度和经济粗糙度确定。 3 .求工序基本尺寸。
从零件图的设计尺寸开始,一直往前推算到毛坯尺寸,某工序基本尺寸等于后道工序基本尺寸加上或减去后道工序余量。 4 .标注工序尺寸公差。 最后一道工序按设计尺寸公差标注,其余工序尺寸按“单向入体”原则标注。 例如,某法兰盘零件上有一个孔,孔径为 ,表面粗糙度值为R a0.8 μ m (图3-83 ),毛坯为铸钢件,需淬火处理。其工艺路线如表3-19 所示。 解题步骤如下:
( 1 )根据各工序的加工性质,查表得它们的工序余量(见表3-19 中的第 2 列)。 ( 2 )确定各工序的尺寸公差及表面粗糙度。由各工序的加工性质查有关经济加工精度和经济粗糙度(见表3-19 中的第 3 列)。 ( 3 )根据查得的余量计算各工序尺寸(见表3-19 中的第四列)。 ( 4 )确定各工序尺寸的上下偏差。按“单向入体”原则,对于孔,基本尺寸值为公差带的下偏差,上偏差取正值;对于毛坯尺寸偏差应取双向对称偏差(见表3-19 中的第 5 列)。
工艺尺寸链计算的基本公式
工艺尺寸链计算的基本公式 来源:作者:发布时间:2007-08-03 工艺尺寸链的计算方法有两种:极值法和概率法。目前生产中多采用极值法计算,下面仅介绍极值法计算的基本公式,概率法将在装配尺寸链中介绍。 图3-82 为尺寸链中各种尺寸和偏差的关系,表3-18 列出了尺寸链计算中所用的符号。 1 .封闭环基本尺寸 式中n ——增环数目;
m ——组成环数目。 2 .封闭环的中间偏差 式中Δ0——封闭环中间偏差; ——第i 组成增环的中间偏差; ——第i 组成减环的中间偏差。 中间偏差是指上偏差与下偏差的平均值:3 .封闭环公差 4 .封闭环极限偏差 上偏差 下偏差
5 .封闭环极限尺寸 最大极限尺寸A 0max=A 0+ES 0 (3-27 ) 最小极限尺寸A 0min=A 0+EI 0 (3-28 ) 6 .组成环平均公差 7 .组成环极限偏差 上偏差 下偏差 8 .组成环极限尺寸 最大极限尺寸A imax=A i+ES I (3-32 )最小极限尺寸A imin=A i+EI I (3-33 )工序尺寸及公差的确定方法及示例
工序尺寸及其公差的确定与加 工余量大小,工序尺寸标注方法及定位基准的选择和变换有密切的关系。下面阐述几种常见情况的工序尺寸及其公差的确定方法。 (一)从同一基准对同一表面多次加工时工序尺寸及公差的确定 属于这种情况的有内外圆柱面和某些平面加工,计算时只需考虑各工序的余量和该种加工方法所能达到的经济精度,其计算顺序是从最后一道工序开始向前推算,计算步骤为: 1 .确定各工序余量和毛坯总余量。 2 .确定各工序尺寸公差及表面粗糙度。 最终工序尺寸公差等于设计公差,表面粗糙度为设计表面粗糙度。其它工序公差和表面粗糙度按此工序加工方法的经济精度和经济粗糙度确定。 3 .求工序基本尺寸。 从零件图的设计尺寸开始,一直往前推算到毛坯尺寸,某工序基本尺寸等于后道工序基本尺寸加上或减去后道工序余量。 4 .标注工序尺寸公差。 最后一道工序按设计尺寸公差标注,其余工序尺寸按“单向入体”原则标注。 例如,某法兰盘零件上有一个孔,孔径为,表面粗糙度值为R a0.8 μ m (图3-83 ),毛坯为铸钢件,需淬火处理。其工艺路线如表3-19 所示。
工序尺寸及其公差的确定
安徽工程科技学院教师备课教案 本章节讲稿共5 页教案第1 页备课时间:05年6月15 日教师签名:
第七章工艺规程设计 四、加工余量、工序尺寸及其公差的确定 1.加工余量的确定 对于柱面为双边余量;对于平面为单边余量。 加工总余量(毛坯余量):毛坯尺寸与零件图上的设计尺寸之差。 工序余量:相邻两工序尺寸之差。分为: ①工序基本余量Z=±(上工序基本尺寸L a-本工序基本尺寸 L b) 外表面取+;内表面取- 外表面:内表面: ②最小工序余量Z min=L amin-L bmax Z min=L bmin-L amax ③最大工序余量Z max=L amax-L bmin Z max=L bmax-L amin ④工序余量公差T z=Z max-Z min =上工序尺寸公差Ta+本工序尺寸公差Tb 工序尺寸公差的标注,按入体原则:即实体最小化,图7-9 毛坯尺寸公差,双向标注,图7-10 1)确定工序余量的原则和应考虑的因素 ①在确保加工质量的前提下,工序余量尽可能小。 ②上工序的R a及缺陷层D a图7-11和表7-2 ③T a和形位误差ρa ④本工序定位、夹紧误差误差εb 2)确定加工余量的方法 ①公式计算法,比较准确,但数据难得,用于大批量生产; 式7-5、7-6 p173 ②经验估计法,余量一般偏大,用于单件小批生产; ③查表修正法,将生产实践和试验积累的大量数据列成表格, 使用时直接查找,应根据实际情况修正。 2.工序尺寸及其公差的确定 工件某表面需多道工序加工时, 工序尺寸:各工序应保证的加工尺寸。 工序尺寸公差:工序尺寸允许的变动范围。 1)工艺基准与设计基准重合时 首先确定各工序余量,再从最后一道工序开始向前推算各工序基本尺寸,直到毛坯基本尺寸。例见表7-3 各工序尺寸公差按经济精度确定。 2)工艺基准与设计基准不重合时 需按工艺尺寸链原理分析计算。
谈零件工序尺寸公差的零值和负值
《装备制造技术》2012年第11期 在生产中,编制零件工艺规程,一般都要涉及工艺尺寸链的计算,特别是遇到零件的工序基准和定位基准(或测量基准)不重合时,计算工序尺寸的公差就会经常出现零值或负值问题。近几年,经过工科教学课程体系改革,相关课程内容合并、压缩和简化,涉及这一部分的知识,在教材中已经不再阐述或仅简单提示一下。当前,由于大学生接触生产实际时间有限,对工序尺寸公差的零值或负值的后果不够清晰以及对解决方法的不了解。为此,笔者根据多年的教学经验,从培养工科大学生应用型的人才出发,认为《机械制造技术》课程的课堂教学可以适当安排一定课时来讲解工序尺寸公差的零值或负值问题。 1尺寸公差零值或负值的概念 零件尺寸公差是指允许尺寸的变动量。公差等于最大极限尺寸与最小极限之代数差的绝对值,也等于上偏差与下偏差的代数差的绝对值。在计算尺寸链时,工序尺寸的公差值,首先必须是正的,其次公差要有一定范围,公差数值的大小取决产品的性能和使用要求。 在工序尺寸的计算中,当工序基准和定位基准重合时,零件的工序尺寸一般无需计算,也不会出现尺寸公差零值或负值。当工序基准和定位基准不重合时,工序尺寸的计算有可能会出现公差零值或负值。由于尺寸公差的零值和负值会造成零件无法加工,生产中碰到此类问题的一般三种解决方法。 (1)等公差值法 按等公差值方法重新分配封闭环的公差,即: 各组成环公差=封闭环公差/(n-1) 这种方法在计算上比较方便,但从加工工艺上看不够合理,只宜有选择地使用。 (2)等公差级法 按等公差级方法分配封闭环的公差,即各组成环的公差根据其基本尺寸的大小按比例分配,或是按照公差表中的尺寸分段及某一公差等级来规定组成环的公差,使各组成环的公差满足以下条件:封闭环公差=各组成环公差之和 最后进行适当调整。这种方法从工艺上讲比较合理。 (3)经验法 各组成环的公差可以凭工程技术人员的经验,按照具体情况来分配。 前二种方法都有优点和不足,而经验法对大学生还谈不上。为此,在教学中可以结合生产实际介绍一种既方便又比较合理的方法,即先用等公差值分配公差,再根据尺寸大小适当调整来求解工序尺寸和公差。 2计算实例 对工序尺寸公差零值和负值的问题,在教学中,还可以通过实例提高学生的认识。 2.1应用实例 采用调整法铣削,图1所示为阶梯轴的槽面。试标注以大端端面轴向定位时的铣槽工序尺寸及其公差。 谈零件工序尺寸公差的零值和负值 樊琳 (苏州大学机电工程学院,江苏苏州215021) 摘要:生产中解决零件加工工序尺寸公差零值或负值问题的计算方法有三种。针对这三种工序尺寸计算方法在实际应用中暴露出的一些不足,介绍一种简便的工序尺寸计算方法,并通过实例验证其计算结果准确可行。 关健词:工序尺寸;公差;零值;负值 中图分类号:G642.3文献标识码:B文章编号:1672-545X(2012)11-0143-02 收稿日期:2012-08-03 作者简介:樊琳(1954—),男,副教授,硕士生导师,主要研究方向机械制造技术。 143
尺寸链及公差叠加分析
课程培训目标: ?能够计算装配零件的最小和最大壁厚、间隙、或干涉, ?能够创建几何公差或正负公差的尺寸链,分析公差叠加结果, ?能够创建、分析复杂的公差叠加分析工具,包含几何公差,名义尺寸,实效条件尺寸,和正负公差, ?能够分析通用装配条件的公差叠加分析, ?能够分析浮动紧固件的公差叠加分析,如何定义螺栓,轴类,或孔类公差, ?能够分析固定紧固件的公差叠加分析,如何定义螺栓,间隙孔,槽,凸缘,和整体尺寸的公差,以及螺纹孔的投影公差, ?能够计算在不同的基准方案下的最大,最小间隙, ?掌握一套逻辑的,系统的,数量化的公差分析方法, 课程包含主要内容: 课程参与者能够解决实际工作中面对的从简单到复杂的装配体的公差叠加分析。培训中以理论讲授和实践练习相结合来分析尺寸公差和几何公差的叠加分析,比较分析不同的基准设置情况下的输出结果。 培训大纲: ?尺寸链分析的起点 ?创建正负尺寸链 ?如何计算,如何确定影响贡献公差叠加结果的尺寸因素 ?如何分析:最差条件法Wost Case ?哪些几何公差影响公差叠加结果? ?均值分析:Mean ?边界计算:GD&T,MMC,LMC和RFS材料条件修正情况下, ?等边正负公差转换 2.复杂装配体的正负尺寸公差叠加分析 ?计算方法 ?尺寸链分析工具制作 ?分析工具的应用 ?最大、最小间隙的分析结果输出 ?合格率的计算 ?Cpk与公差叠加分析 ?统计公差的分析及计算 ?6Sigma公差设计方法
3.公差叠加的2D分析法–水平方向公差叠加和竖直方向的公差叠加分析?尺寸链分析的起点 ?创建正负尺寸链 ?最小、最大间隙的分析结果输出 4.装配体的公差叠加分析 ?装配体中零件间的尺寸链如何建立 ?不同的尺寸布局方案的公差叠加分析 ?尺寸公差定义的装配体中公差叠加分析复杂性 ?最小,最大间隙结果输出 ?公差的优化 ?合格率的计算 ?与几何公差的比较 5.浮动螺栓装配分析 ?几何公差控制的实效边界和补偿公差 ?内边界,外边界,均值边界 ?公差叠加分析中直径到半径的转化方法 ?轮廓度的叠加分析分解方法 ?基准浮动因素 ?几何公差浮动因素 ?复杂装配体的几何公差尺寸链建立方法 ?分析的标准化模板, 6.固定螺丝装配分析 ?计算装配体的最大、最小间隙 ?投影公差的因素 ?正向设计固定螺栓装配总成 ?逆向设计固定螺栓装配总成 ?对于孔类、槽类、凸缘和轴类装配体的分析 ?确定所有的几何公差因素 ?独立特征和阵列特征的不同分析方法 7.几何公差复杂装配体实例分析 ?对零件进行GD&T定义 ?装配设计方案 ?螺纹特征
线性尺寸链公差分析
線性尺寸鏈公差分析. 程序設計用于(1D)線性尺寸鏈公差分析。程序解決以下問題: 1公差分析,使用算術法"WC"(最差條件worst case)綜合和最優化尺寸鏈,也可以使用統計學計算"RSS"(Root Sum Squares)。 2溫度變化引起的尺寸鏈變形分析。 3使用"6 Sigma"的方法拓展尺寸鏈統計分析。 4選擇裝配的尺寸鏈公差分析,包含組裝零件數的最優化。 所有完成的任務允許在額定公差值內運行,包括尺寸鏈的設計和最優化。 計算中包含了ANSI, ISO, DIN以及其他的專業文獻的數據,方法,算法和信息。標准參考表:ANSI B4.1, ISO 286, ISO 2768, DIN 7186 計算的控制,結構及語法。 計算的控制與語法可以在此鏈接中找到相關信息"計算的控制,結構與語法". 項目信息。 “項目信息”章節的目的,使用和控制可以在"項目信息"文檔裏找到. 理論-原理。 一個線性尺寸鏈是由一組獨立平行的尺寸形成的封閉環。他們可以是一個零件的相互位置尺寸(Fig.A)或是組裝單元中各個零件尺寸(Fig. B). 一個尺寸鏈由分開的部分零件(輸入尺寸)和一個封閉零件(結果尺寸)組成。部分零件(A,B,C...)可以是圖面中的直接尺寸或者是按照先前的加工工藝,組裝方式。所給尺寸中的封閉零件(Z)表現爲加工工藝或組裝尺寸的結果,結果綜合了部分零件的加工尺寸,組裝間隙或零件的幹涉。結果尺寸的大小,公差和極限直接取決于部分尺寸的大小和公差,取決于部分零件的變化對封閉零件變化的作用大小,在尺寸鏈中分爲兩類零件: - 增加零件- 部分零件,該零件的增加導致封閉零件的尺寸增加 - 減少零件- 部分零件,封閉零件尺寸隨著該零件的尺寸增加而減小 在解決尺寸鏈公差關系的時候,會出現兩類問題: 5公差分析- 直接任務,控制 使用所有已知極限偏差的部分零件,封閉零件的極限偏差被設置。直接任務在計算中是明確的同時通常用于在給定圖面下檢查零件的組裝與加工。 6公差合成- 間接任務,設計
机械制造工艺学习题计算
二、计算题 1. 图所示某齿轮机构,已知A1=300-0.06mm,A2=50-0.06mm,A3=38 +0.16 +0.10 mm, A4=30-O.O5mm,试计算齿轮右端面与档圈左端面的向端在面的轴向间隙A0的变动范围。 根据公式A0=A3-A1-A2-A4=38-30-5-3=0 ES0=ES3-(EI1+EI2+EI4)= (0.16+0.06+0.04+0.05)mm=+0.31mm EI0=EI3-(ES1+ES2+ES4)=(0.10-0-0-0)mm=+0.10mm 故轴向间隙A0的变化范围为0.10~0.31mm。 A3 A2A1 A0 A4 2.如图所示,A、 工出。本工序中,以E面为测量基准加工D面,得尺寸10±0.1,并要求保证设计尺寸10±0.4、35±0.2,现在要求计算前工序加工所得到的两个工序尺寸L1、L2的尺寸及偏差,以满足两个设计尺寸的要求。 L1的尺寸链如图所示。 35为封闭环,L1为增环,10为减环。可求得:L1=45± 0.1 L2的尺寸链如图所示。 10为封闭环,20、L2为减环,35为增环。可求得:L2=5±0.1
3.如图所示零件,按图样注出的尺寸A 1和A 3加工时不易测量,现改为按尺寸A 1和A 3加工,为了保证原设计要求,试计算A 2的基本尺寸和偏差。 据题意,按尺寸A1、A2加工,则A3必须为封闭环,A2则为工序尺寸。 A2 A3=10A1=500 -0.060 -0.36 1 023否合理? 根据公式校核 N=A1-A2-A3=150-75-75=0 ESN=ES1-EI2-EI3=0.016-2×-0.06 mm=+0.136mm EIN=EI1-ES2-ES3=0-2×-0.02 mm=+0.04mm 故 N 范围为 0.040.136mm 在装配精度要求范围 0.10.2mm 以内故合理。 5. 如图轴套零件在车床上已加工好外圆、内孔及各表面,现需在铣床上以端面A 定位,铣出表面C 保证尺寸20-0.2mm ,试计算铣此缺口时的工序尺寸。(10分) 已知:A2=40+0.05 A3=65±0.05 A ∑=20-0.2 求A (1) 尺寸链图(2分) (2) 判断封闭环A ∑=20-0.2(2分) (3)上下偏差与基本尺寸计算(2分) A Σ=A+ A2―A3 A =45 BsA Σ= BsA+BsA2-BxA3 BsA=-0.1 BxA Σ= BxA+BxA2-BsA3 BxA=-0.15 (4)入体尺寸标注:44.9-0.05(2分) (5)校核δ∑= δ+δ2+δ3 = 0.2(2分)
工序尺寸及公差计算
确定加工余量,工序尺寸及公差 根据上述加工工艺,查各种表面加工余量表分别确定各种加工表面的加工余量,工序尺寸及公差,如下表所示。 表1:外圆柱面Φ85加工余量计算 工序名称 工序间余量/mm 工序 工序基本尺寸/mm 标注工序尺寸公差 /mm 经济精度 表面粗糙度Ra/μm 磨削 0.5 IT6 0.8 φ85 0.012 0.03485--? 半精车 1.6 IT9 3.2 φ85.5 0.0120.09985.5--? 粗车 4.1 IT11 12.5 Φ87.1 0.0120.23287.1--? 毛坯 φ91 0.91.891+-? 表2:外圆柱面Φ36加工余量计算 工序名称 工序间余量/mm 工序 工序基本尺寸/mm 标注工序尺寸公差 /mm 经济精度 表面粗糙度Ra/μm 精磨 0.15 IT6 0.4 φ36 0.009 0.02536--? 粗磨 0.25 IT7 0.8 φ36.15 0.0090.03436.15--? 半精车 1.4 IT8 3.2 φ36.4 0.0090.04836.4--? 粗车 2.2 IT11 12.5 φ37.8 0.0090.16937.8--? 毛坯 φ42 0.41.242+-? 表3:圆柱面Φ28加工余量计算 工序名称 工序间余量/mm 工序 工序基本尺寸/mm 标注工序尺寸公差 /mm 经济精度 表面粗糙度Ra/μm 磨削 0.4 IT6 0.8 φ28 00.01328-? 半精车 1.5 IT8 3.2 φ28.4 00.03328.4-? 粗车 12.1 IT11 12.5 φ29.9 00.1329.9-?
第五节 工序尺寸及其公差的确定
第五节 工序尺寸及其公差的确定 工序尺寸是加工过程中各个工序应保证的加工尺寸,其公差即工序尺寸公差。正确地确定工序尺寸及其公差,是制订工艺规程的重要工作之一。 零件的加工过程,是毛坯通过切削加工逐步向成品过渡的过程。在这个过程中,各工序的工序尺寸及工序余量在不断地变化,其中一些工序尺寸在零件图纸上往往不标出或不存在,需要在制定工艺过程时予以确定。而这些不断变化的工序尺寸之间又存在着一定的联系,需要用工艺尺寸链原理去分析它们的内在联系,掌握它们的变化规律。运用尺寸链理论去揭示这些尺寸之间的联系,是合理确定工序尺寸及其公差的基础。 一、工艺尺寸链的基本概念 (一)尺寸链的定义 下面先就图5—17所示零件在加工和测量中有关尺寸的关系,来建立工艺尺寸链的定义。 图 图 图5—17 a )所示为一定位套,0A 与1A 为图样已标注的尺寸。当按零件图进行加工时,尺寸0A 不便直接测量。如欲通过易于测量的尺寸2A 进行加工,以间接保证尺寸0A 的要求,则首先需要分析尺寸1A 、2A 和0A 之间的内在关系,然后据此计算出尺寸2A 的数值。又如图5—18 a )所示零件,当加工表面C 时,为使夹具结构简单和工件定位稳定可靠,若选择表面A 为定位基准,并按调整法根据对刀尺寸2A 加工表面C ,以间接保证尺寸0A 的精度要求,则同样需要首先分析尺寸1A 、2A 和0A 之间的内在关系,然后据此计算出对刀尺寸2A 的数值。 我们将互相关联的尺寸(1A 、2A 和0A )以一定顺序首尾相接排列成一封闭的尺寸组,称为零件的工艺尺寸链。图5—17 b )和图5-18 b )所示,即为反映尺寸1A 、2A 、0A 三者关系的工艺尺寸链简图。由上述两例可以看出,在零件的加工过程中,为了加工和测量的方便,有时需要进行一些工艺尺寸的计算。利用工艺尺寸链就可以方便地对工艺尺寸进行分析计算。 (二)尺寸链的组成 1. 环 是指列入尺寸链中的每一个尺寸。例如,图5-17(b )中的1A 、2A 和0A 都称为尺寸链
工序尺寸及公差
工序尺寸及公差 1、尺寸链的定义 尺寸链在零件加工或机器装配过程中,相互联系并按一定顺序排列的封闭尺寸组合。 工艺尺寸链在机械加工过程中,由同一个零件有关工序尺寸组成 的尺寸链。 装配尺寸链在机器设计及装配过程中,由有关零件设计尺寸所组 成的尺寸链。 图示工件如先以A面定位加工C面,得尺寸A1然后再以A面定位用调整法加工台阶面B,得尺寸A2,要求保证B面与C面间尺寸A0;A1、A2和A0这三个尺寸构成了一个封闭尺寸组,就成了一个尺寸链。 2、工艺尺寸链的组成 尺寸链的环可分为封闭环和组成环。 尺寸链的环:组成尺寸链的每一个尺寸。
(1)封闭环:在加工过程中间接获得的尺寸,称为封闭环。在图b所示尺寸链中,A0是间接得到的尺寸,它就是图b所示尺寸链的封闭环。 (2)组成环:在加工过程中直接获得的尺寸,称为组成环。尺寸链中A1与A2都是通过加工直接得到的尺寸,A1、A2都是尺寸链的组成环。 增环:在尺寸链中,其余各环不变,当该环增大,使封闭环也相应增大的组成环减环:在尺寸链中,其余各环不变,当该环增大,使封闭环相应地减小的组成环,建立尺寸链时,首先应确定哪一个尺寸是间接获得的尺寸,并把它定为封闭环。再从封闭环一端起,依次画出有关直接得到的尺寸作为组成环,直到尺寸的终端回到封闭环的另一端,形成一个封闭的尺寸链图。 在分析、计算尺寸链时,正确地判断封闭环以及增环、减环是十分重要的。通常先给封闭环任定一个方向画上箭头,然后沿此方向环绕尺寸链依次给每一组成环画出箭头,凡是组成环尺寸箭头方向与封闭环箭头方向相反的,均为增环;相同的则为减环。 3、尺寸链的分类 (1)按尺寸链在空间分布的位置关系,可分为线性尺寸链、平面尺寸链和空间尺寸链。 1)线性尺寸链:尺寸链中各环位于同一平面内且彼此平行。 2)平面尺寸链:尺寸链中各环位于同一平面或彼此平行的平面内,各环之间可以不平行。 3)空间尺寸链:尺寸链中各环不在同一平面或彼此平行的平面内。 (2)按尺寸链的应用范围,可分为工艺尺寸链和装配尺寸链。 1)工艺尺寸链:在加工过程中,工件上各相关的工艺尺寸所组成的尺寸链。
工序尺寸及公差的确定
工序尺寸是指某一工序加工应达到的尺寸,其公差即为工序尺寸公差,各工序的加工余量确定后,即可确定工序尺寸及公差。 零件从毛坯逐步加工至成品的过程中,无论在一个工序内,还是在各个工序间,也不论是加工表面本身,还是各表面之间,他们的尺寸都在变化,并存在相应的内在联系。运用尺寸链的知识去分析这些关系,是合理确定工序尺寸及其公差的基础。 一、工艺尺寸链的概念及计算公式 (一)工艺尺寸链的概念 1 .尺寸链的定义 在机器装配或零件加工过程中,由相互连接的尺寸形成的封闭尺寸组,称为尺寸链。如图 3-78 所示,用零件的表面 1 定位加工表面 2 得尺寸 A1 ,再加工表面 3 ,得尺寸 A2 ,自然形成 A0 ,于是 A1 — A2 — A0 连接成了一个封闭的尺寸组(图 3-78b ),形成尺寸链。 在机械加工过程中,同一工件的各有关尺寸组成的尺寸链称为工艺尺寸链。 2 .工艺尺寸链的特征 ( 1 )尺寸链有一个自然形成的尺寸与若干个直接得到的尺寸所组成。 图 3-78 中,尺寸
A1 、 A2 是直接得到的 尺寸,而 A0 是自然形成 的。其中自然形成的尺寸 大小和精度受直接得到 的尺寸大小和精度的影 响。并且自然形成的尺寸 精度必然低于任何一个 直接得到的尺寸的精度。 ( 2 )尺寸链一定 是封闭的且各尺寸按一 定的顺序首尾相接。 3 .尺寸链的组成 组成尺寸链的各个尺寸称为尺寸链的环。图 3-78 中 A 1 、 A 2 、A 0 都是尺寸链的环,它们可以分为: ( 1 )封闭环在加工(或测量)过程中最后自然形成的环称为封闭环,如图 3-78 中的 A 0 。每个尺寸链必须有且仅能有一个封闭环,用 A 0 来表示。 ( 2 )组成环在加工(或测量)过程中直接得到的环称为组成环。尺寸链中除了封闭环外,都是组成环。按其对封闭环的影响,组成环可分为增环和减环。
尺寸链的计算、各工序尺寸及公差计算
尺寸链的计算、各工序尺寸及公差计算 例2-3 如图所示的零件要求φ10mm 孔的中心与槽的对称中心相距100±0 .2mm ,各平面及槽均已加工,钻φ10mm 孔时以侧面K 定位,试确定钻孔时的工序尺寸A 及其偏差。 作业1 如左图所示。零件各平面及孔均已加工,求以侧面F 定位加工槽宽12的工序尺寸A 及其偏差。(定位基准与设计基准不重合) 作业2 如右图所示零件,其外表镀铬直径为 ,镀层双边厚度为0.08-0.03mm,表面的 加工顺序为车—磨—镀铬,试计算磨削时的工序尺寸A 。 例2-4如图所示零件顶端已加工完毕,加工内孔底面K 时,要保证尺寸20mm ,因该尺寸不便直接测量,试标出测量尺寸A 。(测量基准与设计基准不重合) 例2-5如图所示,一轴套零件,孔径为 mm 的表面要求渗氮,精加工后要求单边渗 氮层深度为 ,该表面的加工顺序:磨内孔—渗氮(单边t 1/2) —精磨内孔至尺 寸 ,并保证单边渗氮层的深度为 。试求精磨前渗氮层深度。 (工序基准是尚需继续加工的表面) 例2-6 图为一零件内孔的简图,其加工顺序为精镗内孔—加工(插或拉)键槽,保证尺寸A —淬火—磨内孔到设计尺寸同时间接保证键深尺寸46mm 。 045.030-φ04.00150+φ2.003.0+04.00150+φ2.003.0+
例题:如图所示的零件图的有关工艺过程如下。 ①车外圆至尺寸A1(IT9),如图b所示,留磨量z=0.6mm。 ②铣轴端小平台,工序尺寸为A2,如图c所示。 ③磨外圆,保证工序尺寸A3=28 (IT7).试确定各工序尺寸及其偏差。 例2-1某型芯的直径为Φ50 ,尺寸精度IT5,表面粗糙度Ra要求为0.04μm。加工的工艺路线为:粗车--半精车—高频淬火—粗磨—精磨—研磨。用查表法确定毛坯尺寸、各工序尺寸及其公差。【列表】 例2-2需加工φ28孔。孔表面粗糙度为Ra0.8μm,淬火硬度为58~62HRC,加工顺序为钻孔——半精车——精车——热处理——磨孔。确定毛坯尺寸、各工序尺寸及其公差。【列表】
机械加工余量和锻件尺寸公差的确定
机械加工余量和锻件尺寸公差的确定 (一)主要参数及影响因素 1.锻件重量(G1) 根据锻件图的尺寸计算锻件的重量。对于杆部不参与变形(不锻棒料部分)的平锻件重量只计算镦锻部分(见图2a)。若不锻棒料部分的长度与其直径之比小于2时,可看作一个完整的锻件来计算其重量(见图2b)。若平锻件的两端分两次镦锻时,前一道镦锻成形部分连同不锻棒料杆部部分,视为第二道镦锻部分的不锻棒料部分(见图2c)。 2.锻件形状复杂系数(S) 锻件形状复杂系数为锻件重量(G1)与相应的锻件外廓包容体重量(G2)的比值。即: S= 图2 镦锻件重量计算特点 a)一头一长杆;b)一头一短杆;c)二头一杆; A 镦锻部分; B 不锻棒料部分; C 第一道成形 圆形锻件的外廓包容体重量(见图3): 式中:ρ—密度(7.85/cm3) 图3 圆形锻件的外廓包容体 非圆形锻件外廓包容体重量(见图4): 图4 非圆形锻件外廓包容体 锻件形状复杂系数分为四级: 简单:S1>0.63~1 一般:S2>0.32~0.63 较复杂:S3>0.16~0.32 复杂:S4≤0.16 特例:当锻件为薄形圆盘或法兰件(见图5a),其圆盘厚度和直径之比L/d≤0.2时,取形状复杂系数S4。 当L1/d1≤0.2或L2/d2>4时(见图5b),采用形状复杂系数S4。 当冲孔深度大于直径的1.5倍时,形状复杂系数提高一级。 图5 锻件形状复杂特例 3.锻件的材质系数 锻件的材质系数分为二级: M1:钢的含碳量小于0.65%的碳钢,或合金元素总含量小于3.0%的合金钢。 M2:钢的含碳量大于或等于0.65%的碳钢,或合金元素总含量大于或等于3.0%的合金钢。 4.零件的机械加工精度 零件表面粗糙度低于R a1.6,机械加工余量从余量表查得;粗糙度高于R a1.6,加工余量要适当加大;对扁薄截面或在锻件相邻部位截面变化较大的零件(如图6),在长度L范围内应适当加大局部的余量。 图6 应局部增大余量的零件 5.加热条件 采用煤气或油炉加热钢坯时,机械加工余量和公差从余量表和公差表查得;当采用煤加热钢坯,或经二火进行加热时,适当增大加工余量和公差。 6.其他条件
加工余量及工序尺寸和公差的确定
加工余量及工序尺寸和公差的确定 一、加工余量的确定 (一)加工余量的概念 加工总余量:毛坯经机械加工而达到零件图的设计尺寸,毛坯尺寸与零件图的设计尺寸之差,即从被加工表面上切除的金属层总厚度。 工序余量:相邻两工序的尺寸差,即在某一工序所切除的金属层厚度。 某个表面的加工余量。与加工该表面各工序余量之间有下列的关系: (8-1) 式中——加工该表面的工序数; ——加工总余量; ——各工序余量。 工序余量又可以分为单边余量和双边余量。 单边余量:若相邻两工序的工序尺寸之差等于被加工表面任一位置上在该工序切除的金属层厚度。 双边余量:若加工回转表面时,在一个方向的金属层被切除时,对称方向上的金属层也等量地同时被切除掉,使相邻两工序的工序尺寸之差等于被加工表面任一位置上在该工序内切除的金属层厚度的两倍。 如图8-11所示。 图8-4-1 单边余量和双边余量 基本余量、最大加工余量和最小加工余量
a) b) 图8-4-2 基本余量、最大余量和最小余量 加工余量变化的公差等于上道工序的工序尺寸公差与本工序的工序尺寸公差之和。即 (8-2) 各个加工余量与相应加工尺寸的关系如图8-4-3所示。 图8-4-3 加工余量与相应加工尺寸 (二)影响加工余量的因素 1.上道工序加工表面(或毛坯表面)的表面质量包括表面粗糙度高度和表面缺陷层深度; 2.上道工序的尺寸公差 3.上道工序的位置误差 4.本工序的安装误差 (三)确定加工余量的方法 1. 计算法此法是根据一定的资料,对影响加工余量的各项因素进行分析计算,然后综合考虑计算出来的,
多用于大批大量生产,计算公式如下: 对双边余量: (8-3) 对单边余量: (8-4) 一般取 2. 查表法以工厂的实际生产经验及工艺实践积累的有关加工余量的资料数据为基础,结合具体加工方法进行适当修正而得到加工余量的方法。 3. 经验法根据工艺人员的经验来确定加工余量的方法。 二、工序尺寸和公差的确定 一般情况下,加工某表面的最终工序的尺寸及公差可直接按零件图的要求来确定。中间各工序的工序尺寸则可根据零件图的尺寸,加上或减去工序的加工余量而得到。采用由后向前推的方法,由零件图的尺寸,一直推算到毛坯尺寸。 例:加工轴时的各工序尺寸之间的关系。 图8-4-4 工序尺寸的计算 其中为零件的基本尺寸,为毛坯基本尺寸。由图8-4-4可见,对于外表面,本工序的尺寸加上本工序的余量即为前工序的尺寸。 由上可得出,各工序尺寸可由最终尺寸及余量推出。在计算时应注意区分内、外表面,同时注意单边、双边余量的问题。 中间工序尺寸的公差可根据加工方法的加工经济精度来选取,正确地选定工序公差有着 重要的意义。 工序尺寸及公差确定好以后,在工序单上标注时,按“入体原则”进行标注。 即对于外表面尺寸,注成负偏差,对于内表面尺寸,往成正偏差。
工序尺寸及其公差的确定与加工余量大小
工序尺寸及其公差的确定与加工余量大小,工序尺寸标注方法及定位基准的选择和变换有密切的关系。下面阐述几种常见情况的工序尺寸及其公差的确定方法。 (一)从同一基准对同一表面多次加工时工序尺寸及公差的确定 属于这种情况的有内外圆柱面和某些平面加工,计算时只需考虑各工序的余量和该种加工方法所能达到的经济精度,其计算顺序是从最后一道工序开始向前推算,计算步骤为: 1 .确定各工序余量和毛坯总余量。 2 .确定各工序尺寸公差及表面粗糙度。 最终工序尺寸公差等于设计公差,表面粗糙度为设计表面粗糙度。其它工序公差和表面粗糙度按此工序加工方法的经济精度和经济粗糙度确定。 3 .求工序基本尺寸。 从零件图的设计尺寸开始,一直往前推算到毛坯尺寸,某工序基本尺寸等于后道工序基本尺寸加上或减去后道工序余量。 4 .标注工序尺寸公差。 最后一道工序按设计尺寸公差标注,其余工序尺寸按“单向入体”原则标注。
例如,某法兰盘零件上有一个孔,孔径为,表面粗糙度值为R a0.8 μ m (图3-83 ),毛坯为铸钢件,需淬火处理。其工艺路线如表3-19 所示。 解题步骤如下: (1 )根据各工序的加工性质,查表得它们的工序余量(见表3-19 中的第2 列)。 (2 )确定各工序的尺寸公差及表面粗糙度。由各工序的加工性质查有关经济加工精 度和经济粗糙度(见表3-19 中的第3 列)。 (3 )根据查得的余量计算各工序尺寸(见表3-19 中的第四列)。 (4 )确定各工序尺寸的上下偏差。按“单向入体”原则,对于孔,基本尺寸值为公差带的下偏差,上偏差取正值;对于毛坯尺寸偏差应取双向对称偏差(见表3-19 中的第5 列)。