过热器爆管原因
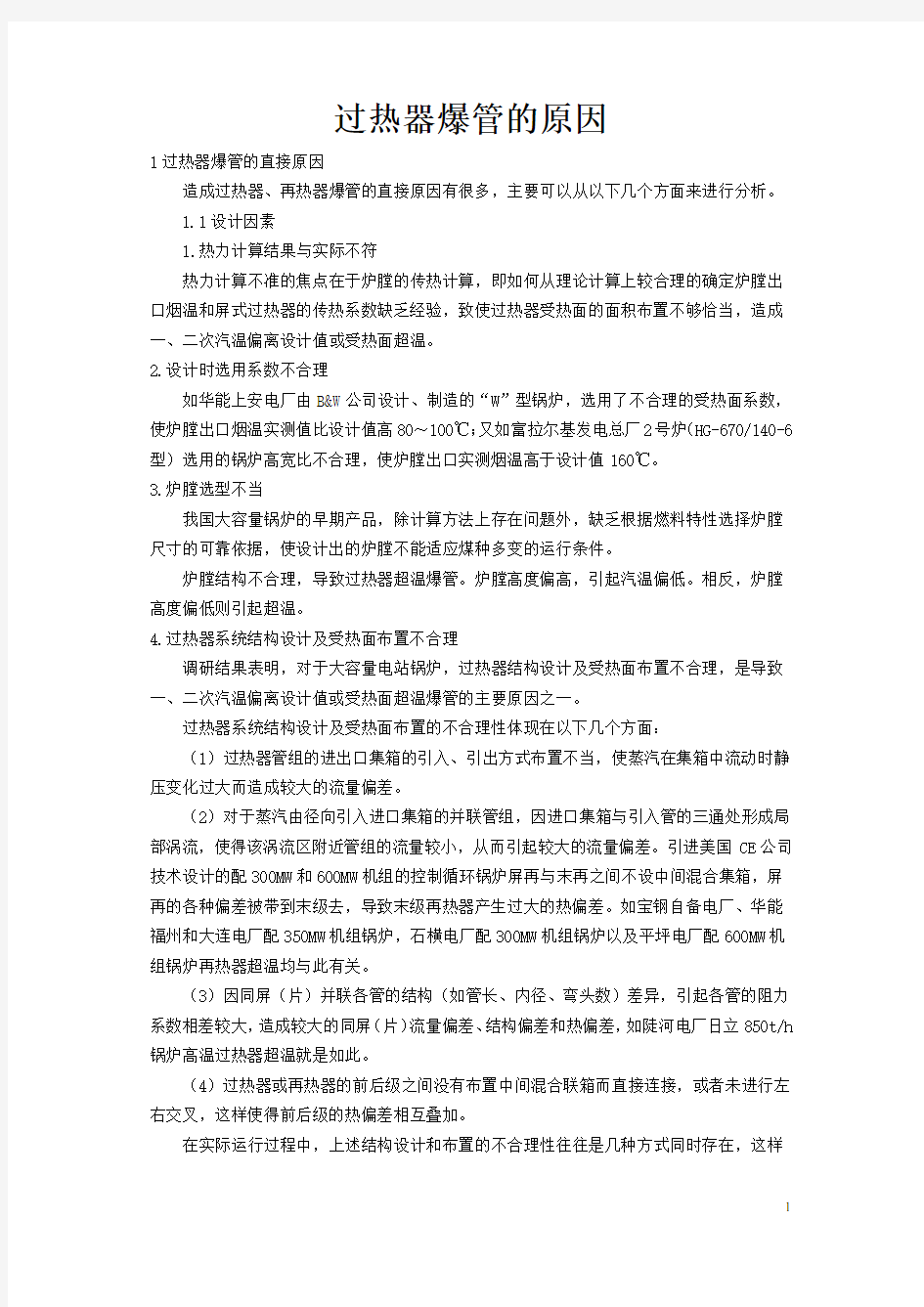
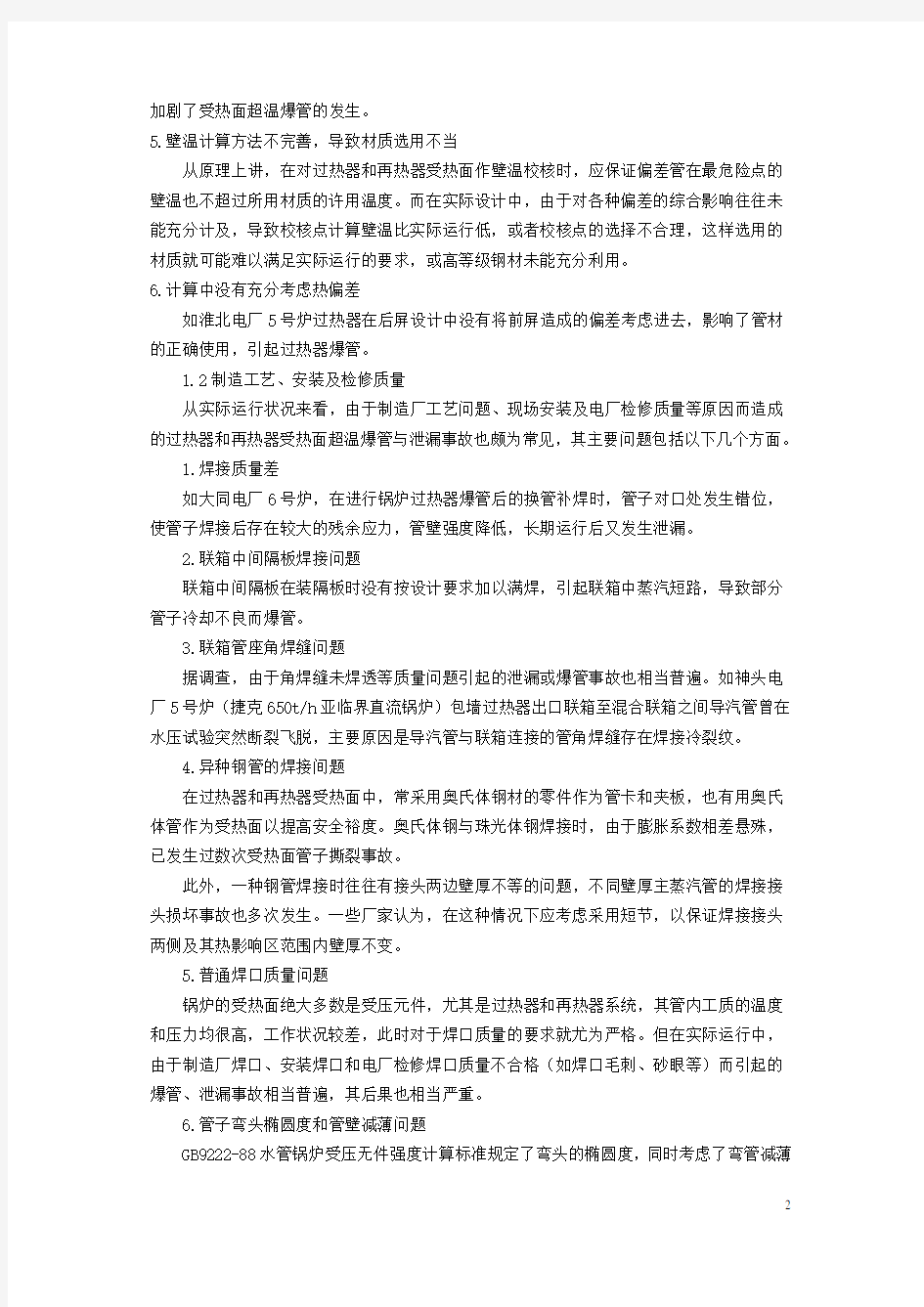
过热器爆管的原因
1过热器爆管的直接原因
造成过热器、再热器爆管的直接原因有很多,主要可以从以下几个方面来进行分析。
1.1设计因素
1.热力计算结果与实际不符
热力计算不准的焦点在于炉膛的传热计算,即如何从理论计算上较合理的确定炉膛出口烟温和屏式过热器的传热系数缺乏经验,致使过热器受热面的面积布置不够恰当,造成
一、二次汽温偏离设计值或受热面超温。
2.设计时选用系数不合理
如华能上安电厂由B&W公司设计、制造的“W”型锅炉,选用了不合理的受热面系数,使炉膛出口烟温实测值比设计值高80~100℃;又如富拉尔基发电总厂2号炉(HG-670/140-6型)选用的锅炉高宽比不合理,使炉膛出口实测烟温高于设计值160℃。
3.炉膛选型不当
我国大容量锅炉的早期产品,除计算方法上存在问题外,缺乏根据燃料特性选择炉膛尺寸的可靠依据,使设计出的炉膛不能适应煤种多变的运行条件。
炉膛结构不合理,导致过热器超温爆管。炉膛高度偏高,引起汽温偏低。相反,炉膛高度偏低则引起超温。
4.过热器系统结构设计及受热面布置不合理
调研结果表明,对于大容量电站锅炉,过热器结构设计及受热面布置不合理,是导致一、二次汽温偏离设计值或受热面超温爆管的主要原因之一。
过热器系统结构设计及受热面布置的不合理性体现在以下几个方面:
(1)过热器管组的进出口集箱的引入、引出方式布置不当,使蒸汽在集箱中流动时静压变化过大而造成较大的流量偏差。
(2)对于蒸汽由径向引入进口集箱的并联管组,因进口集箱与引入管的三通处形成局部涡流,使得该涡流区附近管组的流量较小,从而引起较大的流量偏差。引进美国CE公司技术设计的配300MW和600MW机组的控制循环锅炉屏再与末再之间不设中间混合集箱,屏再的各种偏差被带到末级去,导致末级再热器产生过大的热偏差。如宝钢自备电厂、华能福州和大连电厂配350MW机组锅炉,石横电厂配300MW机组锅炉以及平坪电厂配600MW机组锅炉再热器超温均与此有关。
(3)因同屏(片)并联各管的结构(如管长、内径、弯头数)差异,引起各管的阻力系数相差较大,造成较大的同屏(片)流量偏差、结构偏差和热偏差,如陡河电厂日立850t/h 锅炉高温过热器超温就是如此。
(4)过热器或再热器的前后级之间没有布置中间混合联箱而直接连接,或者未进行左右交叉,这样使得前后级的热偏差相互叠加。
在实际运行过程中,上述结构设计和布置的不合理性往往是几种方式同时存在,这样
加剧了受热面超温爆管的发生。
5.壁温计算方法不完善,导致材质选用不当
从原理上讲,在对过热器和再热器受热面作壁温校核时,应保证偏差管在最危险点的壁温也不超过所用材质的许用温度。而在实际设计中,由于对各种偏差的综合影响往往未能充分计及,导致校核点计算壁温比实际运行低,或者校核点的选择不合理,这样选用的材质就可能难以满足实际运行的要求,或高等级钢材未能充分利用。
6.计算中没有充分考虑热偏差
如淮北电厂5号炉过热器在后屏设计中没有将前屏造成的偏差考虑进去,影响了管材的正确使用,引起过热器爆管。
1.2制造工艺、安装及检修质量
从实际运行状况来看,由于制造厂工艺问题、现场安装及电厂检修质量等原因而造成的过热器和再热器受热面超温爆管与泄漏事故也颇为常见,其主要问题包括以下几个方面。
1.焊接质量差
如大同电厂6号炉,在进行锅炉过热器爆管后的换管补焊时,管子对口处发生错位,使管子焊接后存在较大的残余应力,管壁强度降低,长期运行后又发生泄漏。
2.联箱中间隔板焊接问题
联箱中间隔板在装隔板时没有按设计要求加以满焊,引起联箱中蒸汽短路,导致部分管子冷却不良而爆管。
3.联箱管座角焊缝问题
据调查,由于角焊缝未焊透等质量问题引起的泄漏或爆管事故也相当普遍。如神头电厂5号炉(捷克650t/h亚临界直流锅炉)包墙过热器出口联箱至混合联箱之间导汽管曾在水压试验突然断裂飞脱,主要原因是导汽管与联箱连接的管角焊缝存在焊接冷裂纹。
4.异种钢管的焊接间题
在过热器和再热器受热面中,常采用奥氏体钢材的零件作为管卡和夹板,也有用奥氏体管作为受热面以提高安全裕度。奥氏体钢与珠光体钢焊接时,由于膨胀系数相差悬殊,已发生过数次受热面管子撕裂事故。
此外,一种钢管焊接时往往有接头两边壁厚不等的问题,不同壁厚主蒸汽管的焊接接头损坏事故也多次发生。一些厂家认为,在这种情况下应考虑采用短节,以保证焊接接头两侧及其热影响区范围内壁厚不变。
5.普通焊口质量问题
锅炉的受热面绝大多数是受压元件,尤其是过热器和再热器系统,其管内工质的温度和压力均很高,工作状况较差,此时对于焊口质量的要求就尤为严格。但在实际运行中,由于制造厂焊口、安装焊口和电厂检修焊口质量不合格(如焊口毛刺、砂眼等)而引起的爆管、泄漏事故相当普遍,其后果也相当严重。
6.管子弯头椭圆度和管壁减薄问题
GB9222-88水管锅炉受压无件强度计算标准规定了弯头的椭圆度,同时考虑了弯管减薄
所需的附加厚度。该标准规定,对弯管半径R>4D的弯头,弯管椭圆度不大于8%。但实测数据往往大于此值,最大达21%,有相当一部分弯头的椭圆度在9%~12%之间。
另外,实测数据表明,有不少管子弯头的减薄量达23%~28%,小于直管的最小需要壁厚。因此,希望对弯管工艺加以适当的改进,以降低椭圆度和弯管减薄量,或者增加弯头的壁厚。
7.异物堵塞管路
锅炉在长期运行中,锈蚀量较大,但因管径小,无法彻底清除,管内锈蚀物沉积在管子底部水平段或弯头处,造成过热而爆管。在过热器的爆管事故中,由干管内存在制造、安装或检修遗留物引起的事故也占相当的比例。如长春热电二厂1号炉因管路堵塞造成短时超温爆管。
8.管材质量问题
钢材质量差。管子本身存在分层、夹渣等缺陷,运行时受温度和应力影响缺陷扩大而爆管。由于管材本身的质量不合格造成的爆破事故不像前述几个问题那么普遍,但在运行中也确实存在。
9.错用钢材
如靖远电厂4号炉的制造、维修过程中,应该用合金钢的高温过热器出口联箱管座错用碳钢,使碳钢管座长期过热爆破。为此,在制造厂制造加工和电厂检修时应注意严格检查管材的质量,加以避免。
10.安装质量问题
如扬州发电厂DG-670/140-8型固态排渣煤粉炉的包墙过热器未按照图纸要求施工,使管子排列、固定和膨胀间隙出现问题,从而导致爆管。这类问题在机组试运行期间更为多见。
1.3调温装置设计不合理或不能正常工作
为确保锅炉的安全、经济运行,除设计计算应力求准确外,汽温调节也是很重要的一环。大容量电站锅炉的汽温调节方式较多,在实际运行中,由于调温装置原因带来的问题也较多,据有关部门调查,配200MW机组的锅炉80%以上的再热蒸汽调温装置不能正常使用。
1.减温水系统设计不合理
某些锅炉在喷水减温系统设计中,往往用一只喷水调节阀来调节一级喷水的总量,然后将喷水分别左右两个回路。这时,当左右侧的燃烧工况或汽温有较大偏差时,就无法用调整左右侧喷水量来平衡两侧的汽温。
2.喷水减温器容量不合适
喷水式减温器一般设计喷水量约为锅炉额定蒸发量的3%~5%,但配200MW机组的锅炉由于其汽温偏离设计值问题比较突出,许多电厂均发现喷水减温器容量不够。如:邢台电厂、沙角A电厂和通辽电厂等都将原减温水管口放大,以满足调温需要;对再热蒸汽,由于大量喷水对机组运行的经济性影响较大,故设计时再热蒸汽的微量喷水一般都很小,或不用喷水。然而,在实际运行中,因再热器超温,有些电厂不得不用加大喷水量来解决。
3.喷水减温器调节阀调节性能问题
喷水减温器的喷水调节阀的调节性能也是影响减温系统调温效果的因素之一。调研结果表明,许多国产阀门的调节性能比较差,且漏流严重,这在一定程度上影响了机组的可靠性和经济性。
4.减温器发生故障
如巴陵石化公司动力厂5号炉,将减温器I级调节阀固定,用II级调节阀调节。因起主调作用的I级减温器减温水投入少,冷却屏式过热器、高温过热器的效果差,增加过热器超温的可能。
5.再热器调节受热面
所谓再热器调节受热面是指用改变通过的蒸汽量来改变再热蒸汽的吸热量,从而达到调节再热汽温的一种附加受热面。苏制Efl670 / 140型锅炉的再热汽温的调节就是利用这一装置实现的。但是由于运行时蒸汽的重量流速低于设计值,而锅炉负荷则高于设计值,因而马头电厂5, 6号炉都曾发生再热器调节受热面管子过热超温事故,后经减少调节受热面面积和流通截面积,才解决了过热问题。
6.挡板调温装置
采用烟气挡板调温装置的锅炉再热蒸汽温度问题要好于采用汽——汽热交换器的锅炉。挡板调温可改变烟气量的分配,较适合纯对流传热的再热蒸汽调温,但在烟气挡板的实际应用中也存在一些问题:
(1)挡板开启不太灵活,有的电厂出现锈死现象;
(2)再热器侧和过热器侧挡板开度较难匹配,挡板的最佳工作点也不易控制,运行人员操作不便,往往只要主蒸汽温度满足就不再调节。有些电厂还反映用调节挡板时,汽温变化滞后较为严重。
7.烟气再循环
烟气再循环是将省煤器后温度为250~350℃的一部分烟气,通过再循环风机送入炉膛,改变辐射受热面与对流受热面的吸热量比例,以调节汽温。
采用这种调温方式能够降低和均匀炉膛出口烟温,防止对流过热器结渣及减小热偏差,保护屏式过热器及高温对流过热器的安全。一般在锅炉低负荷时,从炉膛下部送入,起调温作用;在高负荷时,从炉膛上部送入,起保护高温对流受热面的作用。此外,还可利用烟气再循环降低炉膛的热负荷,防止管内沸腾传热恶化的发生,并能抑制烟气中NOx的形成,减轻对大气的污染。但是,由于这种方式需要增加工作于高烟温的再循环风机,要消耗一定的能量,且因目前再循环风机的防腐和防磨问题远未得到解决,因而限制了烟气再循环的应用。此外,采用烟气再循环后,对炉膛内烟气动力场及燃烧的影响究竟如何也有待于进一步研究。
因此,从原理上将烟气再循环是一种较理想的调温手段,对于大型电站锅炉的运行是十分有利的。但因种种原因,实际运行时极少有电厂采用。
8.火焰中心的调节
改变炉膛火焰中心位置可以增加或减少炉膛受热面的吸热量和改变炉膛出口烟气温度,因而可以调节过热器汽温和再热器汽温。但要在运行中控制炉膛出口烟温,必须组织好炉内空气动力场,根据锅炉负荷和燃料的变化,合理选择燃烧器的运行方式。按燃烧器形式的不同,改变火焰中心位置的方法一般分为两类:摆动式燃烧器和多层燃烧器。摆动式燃烧器多用于四角布置的锅炉中。在配300MW和600MW机组的锅炉中应用尤为普遍。试验表明,燃烧器喷嘴倾角的变化对再热器温和过热器温都有很大的影响,当采用多层燃烧器时,火焰位置改变可以通过停用一层燃烧器或调节上下一、二次风的配比来实现,如停用下排燃烧器可使火焰位置提高。遗憾的是,在实际运行时效果不甚理想。
1.4运行状况对过热器超温、爆管的影响
过热器调温装置的设计和布置固然对于过热器系统的可靠运行起着决定性的作用,但是,锅炉及其相关设备的运行状况也会对此造成很大的影响,而后者又往往受到众多因素的综合影响。因此,如何确保锅炉在理想工况下运行是一个有待深入研究的问题。
1.蒸汽品质不良,引起管内结垢严重,导致管壁过热爆管
如镇海发电厂6号炉(DG-670/140-8)曾因这类问题引起7次爆管。
2.炉内燃烧工况
随着锅炉容量的增大,炉内燃烧及气流情况对过热器和再热器系统的影响就相应增大。如果运行中炉内烟气动力场和温度场出现偏斜,则沿炉膛宽度和深度方向的烟温偏差就会增加,从而使水平烟道受热面沿高度和宽度方向以及尾部竖井受热面沿宽度和深度方向上的烟温和烟速偏差都相应增大;而运行中一次风率的提高,有可能造成燃烧延迟,炉膛出口烟温升高。如美国CE公司习惯采用,也是我国大容量锅炉中应用最广泛的四角布置切圆燃烧技术常常出现炉膛出口较大的烟温或烟速偏差,炉内烟气右旋时,右侧烟温高;左旋时左侧烟温高。有时,两侧的烟温偏差还相当大(石横电厂6号1025t/h炉最大时曾达250℃),因而引起较大的汽温偏差。
3.高压加热器投人率低
我国大容量机组的高压加热器投入率普遍较低,有的机组高加长期停运。对于200MW
机组,高压加热器投与不投影响给水温度80℃左右。计算及运行经验表明,给水温度每降低1℃,过热蒸汽温度上升0.4~0.5℃。因此,高加停运时,汽温将升高32~40℃。可见给水温度变化对蒸汽温度影响之大。
4.煤种的差异
我国大容量锅炉绝大部分处于非设计煤种下运行,主要表现在实际用煤与设计煤种不符、煤种多变和煤质下降等。燃烧煤种偏离设计煤种,使着火点延迟,火焰中心上移,当炉膛高度不足,过热器就会过热爆管。
燃料成分对汽温的影响是复杂的。一般说来,直接影响燃烧稳定性和经济性的主要因素是燃料的低位发热量和挥发份、水分等。此外,灰熔点及煤灰组份与炉膛结焦和受热面沾污的关系极为密切。当燃料热值提高时,由于理论燃烧温度和炉膛出口烟温升高,可能导致炉膛结焦,过热器和再热器超温。当灰份增加时,会使燃烧恶化,燃烧过程延迟,火
焰温度下降,一般,燃料中灰份越多,在实际运行中汽温下降幅度越大。另外,灰份增加,还会使受热面磨损和沾污加剧;挥发份增大时,燃烧过程加快,蒸发受热面的吸热量增加,因而汽温呈下降趋势。当水分增加时,如燃料量不变,则烟温降低,烟气体积增加,最终使汽温上升。据有关部门计算:水分增加1%,过热器出口蒸汽温度升高约1℃左右。
5.受热面沾污
国产大容量锅炉有的不装吹灰器(前期产品),或有吹灰器不能正常投用,往往造成炉膛和过热器受热面积灰,特别在燃用高灰份的燃料时,容易造成炉膛结焦,使过热器超温。对于汽温偏低的锅炉,如过热器积灰,将使汽温愈加偏低。因此,吹灰器能否正常投用,对锅炉安全和经济运行有一定影响。
6.磨损与腐蚀
锅炉燃料燃烧时产生的烟气中带有大量灰粒,灰粒随烟气冲刷受热面管子时,因灰粒的冲击和切削作用对受热面管子产生磨损,在燃用发热量低而灰分高的燃料时更为严重。当燃用含有一定量硫、钠和钾等化合物的燃料时,在550~700℃的金属管壁上还会发生高温腐蚀,当火焰冲刷水冷壁时也会发生;此外,当烟气中存在SO2和SO3且受热面壁温低于烟气露点时会发生受热面低温腐蚀。在过热器与再热器受热面中易发生的主要是高温腐蚀。
受热面管子磨损程度在同一烟道截面和同一管子圆周都是不同的。对于过热器和再热器系统出现磨损的常常是布置于尾部竖井的低温受热面。一般靠近竖井后墙处的蛇行管磨损严重,当设计烟速过高或由于结构设计不合理存在烟气走廊时,易导致局部区域的受热面管子的磨损。锅炉受热面的高温腐蚀发生于烟温大于700℃的区域内。当燃用K, Na, S 等成分含量较多的煤时,灰垢中K2S04和Na2S04;在含有SO2的烟气中会与管子表面氧化铁作用形成碱金属复合硫酸盐K2Fe(S04)及Na5Fe(S04)5,这种复合硫酸盐在550~710℃范围内熔化成液态,具有强烈腐蚀性,在壁温600~700℃ 时腐蚀最严重。据调查,导致受热面高温腐蚀的主要原因是炉内燃烧不良和烟气动力场不合理,控制管壁温度是减轻和防止过热器和再热器外部腐蚀的主要方法。因而,目前国内对高压、超高压和亚临界压力机组,锅炉过热蒸汽温度趋向于定为540℃,在设计布置过热器时,则尽量避免其蒸汽出口段布置于烟温过高处。
管间振动磨损。如耒阳电厂1号炉,固定件与过热器管屏间的连接焊缝烧裂,管屏发生振动,固定件与管屏内圈发生摩擦,使管壁磨损减薄,在内压力的作用下发生爆管。
管内壁积垢、外壁氧化。如洛河电厂2号炉管内壁结垢0.7mm,使过热器壁温升高20~30℃;外壁氧化皮1.0mm,又使管壁减薄,因此爆管频繁。
7.超期服役
如黄台2号炉过热器管己运行23万h以上,管材球化、氧化严重,已出现蠕变裂纹,如不及时更换,迟早会发生爆管。
8.运行管理
在实际运行中,由于运行人员误操作及检修时未按有关规定进行或未达到有关要求而
导致过热器或再热器受热面爆管的事故也时有发生。
运行调整不当。如浑江发电厂3号炉,过热器使用的材质基本都工作在材质允许的极限温度中,在运行工况发生变化时调整不当,发生瞬时超温爆管。
2过热器爆管的根本原因及对策
二十世纪八十年代初,美国电力研究院经过长期大量研究,把锅炉爆管机理分成六大类,共22种。在22种锅炉爆管机理中,有7种受到循环化学剂的影响,12种受到动力装置维护行为的影响。我国学者结合我国电站锅炉过热器爆管事故做了大量研究,把电站锅炉过热器爆管归纳为以下九种不同的机理。
2.1长期过热
1.失效机理
长期过热是指管壁温度长期处于设计温度以上而低于材料的下临界温度,超温幅度不大但时间较长,锅炉管子发生碳化物球化,管壁氧化减薄,持久强度下降,蠕变速度加快,使管径均匀胀粗,最后在管子的最薄弱部位导致脆裂的爆管现象。这样,管子的使用寿命便短于设计使用寿命。超温程度越高,寿命越短。在正常状态下,长期超温爆管主要发生在高温过热器的外圈和高温再热器的向火面。在不正常运行状态下,低温过热器、低温再热器的向火面均可能发生长期超温爆管。长时超温爆管根据工作应力水平可分为三种:高温蠕变型、应力氧化裂纹型、氧化减薄型。
2.产生失效的原因
(1)管内汽水流量分配不均;
(2)炉内局部热负荷偏高;
(3)管子内部结垢;
(4)异物堵塞管子;
(5)错用材料;
(6)最初设计不合理。
3.故障位置
(1)高温蠕变型和应力氧化裂纹型主要发生在高温过热器的外圈的向火面;在不正常的情况下,低温过热器也可能发生;
(2)氧化减薄型主要发生在再热器中。
4.爆口特征
长期过热爆管的破口形貌,具有蠕变断裂的一般特性。管子破口呈脆性断口特征。爆口粗糙,边缘为不平整的钝边,爆口处管壁厚度减薄不多。管壁发生蠕胀,管径胀粗情况与管子材料有关,碳钢管径胀粗较大。20号钢高压锅炉低温过热器管破裂,最大胀粗值达管径的15%,而12CrMoV钢高温过热器管破裂只有管径5%左右的胀粗。
(1)高温蠕变型
a.管子的蠕胀量明显超过金属监督的规定值,爆口边缘较钝;
b.爆口周围氧化皮有密集的纵向裂纹,内外壁氧化皮比短时超温爆管厚,超温程度越
低,时间越长,则氧化皮越厚和氧化皮的纵向裂纹分布的范围也越广;
c.在爆口周围的较大范围内存在着蠕变空洞和微裂纹;
d.向火侧管子表面已完全球化;
e.弯头处的组织可能发生再结晶;
f.向火侧和背火侧的碳化物球化程度差别较大,一般向火侧的碳化物己完全球化。
(2)应力氧化裂纹型
a.管子的蠕胀量接近或低于金属监督的规定值,爆口边缘较钝,呈典型的厚唇状;
b.靠近爆口的向火侧外壁氧化层上存在着多条纵向裂纹,分布范围可达整个向火侧。内外壁氧化皮比短时超温爆管时的氧化皮厚;
c.纵向应力氧化裂纹从外壁向内壁扩展,裂纹尖端可能有少量空洞;
d.向火侧和背火侧均发生严重球化现象,并且管材的强度和硬度下降;
e.管子内壁和外壁的氧化皮发生分层;
f.燃烧产物中的S、Cl、Mn、Ca等元素在外壁氧化层沉积和富集。
(3)氧化减薄型
a.管子向火侧、背火侧的内外壁均产生厚度可达1.0~1.5mm的氧化皮;
b.管壁严重减薄,仅为原壁厚的1/3~l/8 ;
c.内、外壁氧化皮均分层,为均匀氧化。内壁氧化皮的内层呈环状条纹;
d.向火侧组织己经完全球化,背火侧组织球化严重,并且强度和硬度下降;
e.燃烧产物中的S、Cl、 Mn、Ca等元素在外壁氧化层沉积和富集,促进外壁氧化。
5.防止措施
对高温蠕变型可通过改进受热面、使介质流量分配合理;改善炉内燃烧、防止燃烧中心偏高;进行化学清洗,去除异物、沉积物等方法预防。对应力氧化裂纹型因管子寿命已接近设计寿命,可将损坏的管子予以更换。对氧化减薄型应完善过热器的保护措施。
2.2短期过热
1.失效机理
短期过热是指当管壁温度超过材料的下临界温度时,材料强度明显下降,在内压力作用下,发生胀粗和爆管现象。
2.产生失效的原因
(1)过热器管内工质的流量分配不均匀,在流量较小的管子内,工质对管壁的冷却能力较差,使管壁温度升高,造成管壁超温;
(2)炉内局部热负荷过高(或燃烧中心偏离),使附近管壁温度超过设计的允许值;
(3)过热器管子内部严重结垢,造成管壁温度超温;
(4)异物堵塞管子,使过热器管得不到有效的冷却;
(5)错用钢材。错用低级钢材也会造成短期过热,随着温度升高,低级钢材的许用应力迅速降低,强度不足而使管子爆破;
(6)管子内壁的氧化垢剥落而使下弯头处堵塞;
(7)在低负荷运行时,投入减温水不当,喷入过量,造成管内水塞,从而引起局部过热;
(8)炉内烟气温度失常。
3.故障位置
常发生在过热器的向火面直接和火焰接触及直接受辐射热的受热面管子上。
4.爆口形状
(1)爆口塑性变形大,管径有明显胀粗,管壁减薄呈刀刃状;
(2)一般情况下爆口较大,呈喇叭状;
(3)爆口呈典型的薄唇形爆破;
(4)爆口的微观为韧窝(断口由许多凹坑构成);
(5)爆口周围管子材料的硬度显著升高;
(6)爆口周围内、外壁氧化皮的厚度,取决于短时超温爆管前长时超温的程度,长时超温程度越严重,氧化皮越厚。
5.防止措施
预防短期过热的方法有改进受热面,使介质流量分配合理;稳定运行工况,改善炉内燃烧,防止燃烧中心偏离;进行化学清洗;去除异物、沉积物;防止错用钢材:发现错用及时采取措施。
2.3磨损
1.失效机理
包括飞灰磨损、落渣磨损、吹灰磨损和煤粒磨损。以飞灰磨损为例进行分析。飞灰磨损是指飞灰中夹带Si02, Fe03, Al2O3等硬颗粒高速冲刷管子表面,使管壁减薄爆管。
2.产生失效的原因
(1)燃煤锅炉飞灰中夹带硬颗粒;
(2)烟速过高或管子的局部烟气速度过高(如积灰时烟气通道变小,提高了烟气流动速度;
(3)烟气含灰浓度分布不均,局部灰浓度过高。
3.故障位置
常发生在过热器烟气入口处的弯头、出列管子和横向节距不均匀的管子上。
4.爆口特征
(1)断口处管壁减薄,呈刀刃状;
(2)磨损表面平滑,呈灰色;
(3)金相组织不变化,管径一般不胀粗。
5.防止措施
通常采用减少飞灰撞击管子的数量、速度或增加管子的抗磨性来防止飞灰磨损,如:通过加屏等方法改变流动方向和速度场;加设装炉内除尘装置;杜绝局部烟速过高;在易磨损管子表面加装防磨盖板。还应选用适于煤种的炉型、改善煤粉细度、调整好燃烧、保
证燃烧完全。
2.4腐蚀疲劳(或汽侧的氧腐蚀)
1.失效机理
腐蚀疲劳主要是因为水的化学性质所引起的,水中氧含量和pH值是影响腐蚀疲劳的主要因素。管内的介质由于氧的去极化作用,发生电化学反应,在管内的钝化膜破裂处发生点蚀形成腐蚀介质,在腐蚀介质和循环应力(包括启停和振动引起的内应力)的共同作用下造成腐蚀疲劳爆管。
2.产生失效的原因
(1)弯头的应力集中,促使点蚀产生;
(2)弯头处受到热冲击,使弯头内壁中性区产生疲劳裂纹;
(3)下弯头在停炉时积水;
(4)管内介质中含有少量碱或游离的二氧化碳;
(5)装置启动及化学清洗次数过多。
3.故障位置
常发生在水侧,然后扩展到外表面。过热器的管弯头内壁产生点状或坑状腐蚀,主要在停炉时产生腐蚀疲劳。
4.爆口特征
(1)在过热器的管内壁产生点状或坑状腐蚀,典型的腐蚀形状为贝壳状;
(2)运行时腐蚀疲劳的产物为黑色磁性氧化铁,与金属结合牢固;停炉时,腐蚀疲劳的产物为砖红色氧化铁;
(3)点状和坑状腐蚀区的金属组织不发生变化;
(4)腐蚀坑沿管轴方向发展,裂纹是横断面开裂,相对宽而钝,裂缝处有氧化皮。
5.防止措施
防止氧腐蚀应注意停炉保护;新炉起用时,应进行化学清洗,去除铁锈和脏物,在内壁形成一层均匀的保护膜;运行中使水质符合标准,适当减小PH值或增加锅炉中氯化物和硫酸盐的含量。
2.5应力腐蚀裂纹
1.失效机理
这是指在介质含氯离子和高温条件下,由于静态拉应力或残余应力作用产生的管子破裂现象。
2.产生失效的原因
(1)介质中含氯离子、高温环境和受高拉应力,这是产生应力腐蚀裂纹的三个基本条件;
(2)在湿空气的作用下,也会造成应力腐蚀裂纹;
(3)启动和停炉时,可能有含氯和氧的水团进入钢管;
(4)加工和焊接引起的残余应力引起的热应力。
3.故障位置
常发生在过热器的高温区管和取样管。
4.爆口特征
(1)爆口为脆性形貌,一般为穿晶应力腐蚀断口;
(2)爆口上可能会有腐蚀介质和腐蚀产物;
(3)裂纹具有树枝状的分叉特点,裂纹从蚀处产生,裂源较多。
5.防止措施
防止应力腐蚀裂纹应注意去除管子的残余应力;加强安装期的保护,注意停炉时的防腐;防止凝汽器泄漏,降低蒸汽中的氯离子和氧的含量。
2.6热疲劳
1.失效机理
热疲劳是指炉管因锅炉启停引起的热应力、汽膜的反复出现和消失引起的热应力和由振动引起的交变应力作用而发生的疲劳损坏。
2.产生失效的原因
(1)烟气中的S、Na、V、Cl等物质促进腐蚀疲劳损坏;
(2)炉膛使用水吹灰,管壁温度急剧变化,产生热冲击;
(3)超温导致管材的疲劳强度严重下降;
(4)按基本负荷设计的机组改变为调峰运行。
3.故障位置
常发生在过热器高热流区域的管子外表面。
4.防止措施
防止热疲劳产生的措施有改变交变应力集中区域的部件结构;改变运行参数以减少压力和温度梯度的变化幅度;设计时应考虑间歇运行造成的热胀冷缩;避免运行时机械振动;调整管屏间的流量分配,减少热偏差和相邻管壁的温度;适当提高吹灰介质的温度,降低热冲击。
2.7高温腐蚀
1.失效机理
V2O5和Na2S04等低熔点化合物破坏管子外表面的氧化保护层,与金属部件相互作用,在界面上生成新的松散结构的氧化物,使管壁减薄,导致爆管。
2.产生失效的原因
(1)燃料中含有V、Na和S等低熔点化合物;
(2)局部烟温过高,腐蚀性的低熔点化合物粘附在金属表面,导致高温腐蚀;
(3)腐蚀区内的覆盖物、烟气中的还原性气体和烟气的直接冲刷,将促进高温腐蚀的产生。
3.故障位置
高温腐蚀常发生在过热器及吊挂和定位零件的向火侧外表面。
4爆口特征
(l)裂纹萌生于管子外壁,断口为脆性厚唇式;
(2)沿纵向开裂,在相当于时钟面10点和2点处有浅沟槽腐蚀坑,呈鼠啃状;
(3)外壁有明显减薄,但不均匀,无明显胀粗;
(4)外壁有氧化垢,呈鳄鱼皮花样,垢中含黄色、白色、褐色产物,垢较疏松,为熔融状沉积物,最内层氧化物为硬而脆的黑灰色。
5.防止措施
防止高温腐蚀的方法有控制局部烟温,防止低熔点腐蚀性化合物贴附在金属表面上;使烟气流程合理,尽量减少热偏差;在燃煤锅炉中加入CaSO4和MgSO4等附加剂;易发生高温腐蚀的区域采用表面防护层或设置挡板;除去管子表面的附着物。
2.8异种金属焊接
1.失效机理及原因
焊接接头处因两种金属的蠕变强度不匹配,以及焊缝界面附近的碳近移,使异种金属焊接界面断裂失效。其中,两种金属的蠕变强度相差极大是异种金属焊接早期失效的主要原因。
2.故障位置
常发生在过热器出口两种金属的焊接接头处,当焊缝的蠕变强度相当于其中一种金属的蠕变强度时,断裂发生在另一种金属的焊缝界面上。
3.防止措施
稳定运行是减少异种金属焊接失效最关键的因素;当两种金属焊接时,在其中加入具有中间蠕变强度的过渡段,使焊缝界面两侧蠕变强度差值明显减少;在过渡段的两侧选用性质不同的焊条,使其分别与两种金属的性质相匹配。
2.9质量控制失误
质量控制失误是指在制造、安装、运行中由于外界失误的因素所造成的损坏。质量控制失误的原因有:维修损伤;化学清理损伤;管材缺陷(管材金属不合格或错用管材);焊接缺陷等。加强电厂运行、检修及各种制度的管理是防止质量控制失误出现的有效手段。3结论
造成大型电站锅炉过热器爆管的原因很多,只有对过热器爆管的直接原因和根本原因进行综合分析,才能从根本上解决锅炉爆管问题,有效地防止锅炉过热器爆管事故的发生。
锅炉过热器爆管原因分析及对策(正式)
编订:__________________ 审核:__________________ 单位:__________________ 锅炉过热器爆管原因分析及对策(正式) Deploy The Objectives, Requirements And Methods To Make The Personnel In The Organization Operate According To The Established Standards And Reach The Expected Level. Word格式 / 完整 / 可编辑
文件编号:KG-AO-8363-82 锅炉过热器爆管原因分析及对策(正 式) 使用备注:本文档可用在日常工作场景,通过对目的、要求、方式、方法、进度等进行具体的部署,从而使得组织内人员按照既定标准、规范的要求进行操作,使日常工作或活动达到预期的水平。下载后就可自由编辑。 摘要:锅炉承压部件的安全运行对整个电厂的安全至关重要。文章结合微水电厂实际,分析了过热器爆管泄漏的机理、原因及实际采取的一些对策,以求对锅炉过热器设备的完好运行有所裨益。 关键词:锅炉过热器爆管电网 1 前言 据统计,河北省南部电网锅炉各种事故约占发电厂事故的63.2%,而承压部件泄漏事故又占锅炉事故的86.7%。因此迫切需要大幅度降低锅炉临修次数。下面结合微水电厂实际,分析过热器爆管泄漏的机理、原因及采取的一些对策。 微水发电厂锅炉型号为HG-220/100-4,露天布置,固态排渣煤粉炉,四角切圆燃烧,过热器由辐
射式炉顶过热器、半辐射屏式过热器、对流过热器和包墙管4部分组成。减温水采用给水直接喷入,分两级减温。炉顶管、包墙管和第二级过热器管用?38×4.5的20号碳钢管组成。第一级过热器和屏过热器用?42×5的12Cr1 MoV钢管组成。 2 过热器爆管的主要原因 2.1 超温、过热和错用钢材 2.2 珠光体球化及碳化物聚集 针对12Cr1 MoV钢分析,试验表明当12Cr1 MoV 钢严重球化到5级时,钢的室温强度极限下降约11kg /mm2。微水发电厂1993年4月过热器爆管的统计资料表明:因局部长期过热,珠光体耐热钢已达到了5级球化现象,而它的塑性水平仍然比较高。发生球化现象以后,钢的蠕变极限和持久强度下降。通过580℃下对12Cr1 MoV钢的持久爆管试验,可以看出到了球化4级的钢管,其持久强度降低1/3。影响珠光体耐热钢发生球化的因素主要有温度、时间、应力和钢材的化学成份等。在钢中掺入“V”这种强碳化物元素,
浅析垃圾焚烧炉过热器腐蚀原因及解决措施(最新版)
浅析垃圾焚烧炉过热器腐蚀原因及解决措施(最新版) Safety work has only a starting point and no end. Only the leadership can really pay attention to it, measures are implemented, and assessments are in place. ( 安全管理 ) 单位:______________________ 姓名:______________________ 日期:______________________ 编号:AQ-SN-0148
浅析垃圾焚烧炉过热器腐蚀原因及解决措 施(最新版) 摘要:垃圾焚烧发电是实现城市垃圾无害化、减量化和资源化处理的一种有效方法,目前正得到大力的推广。焚烧发电具有工艺简单,运行可靠,垃圾处理速度快,处理量大。但是由于垃圾成份相当复杂,用于焚烧垃圾的焚烧炉存在非常严重的磨损、腐蚀现象,在腐蚀现象中以高温过热器管的腐蚀问题最为严重。本文主要就这个问题展开讨论并提出预防措施。 关键词:垃圾焚烧炉;高温过热器管腐蚀;措施 一、垃圾焚烧发电工艺原理垃圾焚烧发电是将垃圾放在焚烧炉中进行燃烧,释放出热能,余热回收加热给水变成蒸汽,蒸汽在汽轮机中推动汽轮发电机旋转做功,将蒸汽的热能转化为电能,释放热能后的烟气经净化系统处理后排放,从而将垃圾由“废物”变为
可利用的“资源”。随着各种炉型技术的实践应用广泛开展,炉排式垃圾焚烧炉以适应性强,处理比较彻底的优势正成为目前国内垃圾焚烧的主流工艺。随着技术的不断的提高和发展,我国焚烧炉的垃圾处理容量也不断的提高,从初期的150t/d提高到现在的750t/d,规模日趋增大。 二、垃圾焚烧发电的特点一般来说,垃圾经焚烧处理后残余的固体废物约占20%(炉渣约占15%,飞灰约占5%),考虑炉渣的综合利用因素,减量化效果更为显著。这相比于垃圾填埋处理要永久性占用土地来说节约了大量的土地资源。垃圾中的可燃物在焚烧中基本上变为了可利用的热能。根据城市发展程度及地理位置、生活习惯不同,垃圾的热值有所不同,一般用于焚烧的垃圾要求低位热值大于4180KJ/Kg,垃圾发电量一般在250kwh/t以上(随热值的提高而增加)。另外,由于垃圾焚烧后的尾气经过了严格的净化处理,因此对环境的污染被控制到了最低。因此,垃圾焚烧处理的特点是处理量大、减量效果好、无害化彻底,且有热能回收作用,是真正实现垃圾处理的“无害化、资源化、减量化”的技术手段。因此,对
锅炉过热器爆管原因分析及对策
锅炉过热器爆管原因分 析及对策 集团企业公司编码:(LL3698-KKI1269-TM2483-LUI12689-ITT289-
锅炉过热器爆管原因分析及对策摘要:锅炉承压部件的安全运行对整个电厂的安全至关重要。文章结合微水电厂实际,分析了过热器爆管泄漏的机理、原因及实际采取的一些对策,以求对锅炉过热器设备的完好运行有所裨益。 关键词:锅炉过热器爆管电网 1 前言 据统计,河北省南部电网锅炉各种事故约占发电厂事故的63.2%,而承压部件泄漏事故又占锅炉事故的86.7%。因此迫切需要大幅度降低锅炉临修次数。下面结合微水电厂实际,分析过热器爆管泄漏的机理、原因及采取的一些对策。 微水发电厂锅炉型号为HG-220/100-4,露天布置,固态排渣煤粉炉,四角切圆燃烧,过热器由辐射式炉顶过热器、半辐射屏式过热器、对流过热器和包墙管4部分组成。减温水采用给水直接喷入,分两级减温。炉顶管、包墙管和第二级过热器管用38×4.5的20号碳钢管组成。第一级过热器和屏过热器用42×5的12Cr1MoV钢管组成。 2 过热器爆管的主要原因 2.1 超温、过热和错用钢材 2.2 珠光体球化及碳化物聚集
针对12Cr1MoV钢分析,试验表明当12Cr1MoV钢严重球化到5级时,钢的室温强度极限下降约11kg/mm2。微水发电厂1993年4月过热器爆管的统计资料表明:因局部长期过热,珠光体耐热钢已达到了5级球化现象,而它的塑性水平仍然比较高。发生球化现象以后,钢的蠕变极限和持久强度下降。通过580℃下对12Cr1MoV钢的持久爆管试验,可以看出到了球化4级的钢管,其持久强度降低1/3。影响珠光体耐热钢发生球化的因素主要有温度、时间、应力和钢材的化学成份等。在钢中掺入“V”这种强碳化物元素,可以阻碍珠光体的球化过程,只要能形成稳定的碳化物,则球化过程减速。 通过对12Cr1MoV管试验发现,温度在540℃时,随着运行时间的增加,钢的工作温度下蠕变极限和持久强度也相应降低。随着运行温度的提高、时间的延长、应力的变化都会加速合金元素的固溶体和碳化物间的重新分配现象。 2.3 焊接质量 钢材焊接质量也是影响安全的重要因素之一。焊接的缺陷一般指焊接接头裂纹未熔合、根部未焊透、气孔、夹渣、咬边,焊缝外形尺寸不合格以及焊接接头的金属组织异常等现象。 2.4 金属在高温下的氧化和腐蚀
蒸汽过热器管断裂失效分析
蒸汽过热器管断裂失效分析 王印培陈进 (华东理工大学化机所上海200237) 摘要:某奥氏体不锈钢制蒸汽过热器管在加碱煮炉过程中发生断裂。采用力学性能测定宏微观检验及能谱分析,对该断裂管进行了分析研究。结果表明,蒸汽过热管断裂失效是由碱脆造成的。 主题词:碱脆;不锈钢;失效分析 1 概述 某炼油厂新建制氢装置的转化炉蒸汽过热器管在中压汽包加碱煮炉过程中多处发生断裂。蒸汽过热器管外径Φ89mm,壁厚6.5mm,材料为1Cr19Ni9奥氏体不锈钢。经现场检查,断裂均发生于与集汽管相连的蒸汽过热器的弯管上,裂纹大多位于焊接热影响区,为环向裂纹,在裂口周围管外有结碱。典型的裂纹宏观形貌见图1和图2。 图1 蒸汽过热器直管段裂纹宏观形貌图2 蒸汽过热器弯头裂纹宏观形貌
蒸汽过热器与中压汽包相连通,管外被转化炉炉气加热,管内为过热蒸汽。转化炉投入运行前先烘炉并对中压汽包进行加碱煮炉,煮炉碱液按每立方米各加入NaOH,Na2PO44kg的要求配制,并保证65%~75% 液位。经采样分析炉水碱度达到不小于45mg?L要求。烘炉与煮炉先后结束后(10d),转化炉对流段入口温度保持在525℃,中压汽包仍保压运行。运行一天后发现蒸汽过热器泄漏蒸汽,漏点不断扩大,迫使转化炉降温停炉。根据现场操作记录,在煮炉过程中,蒸汽过热器的蒸汽温度在200℃以上的时间达78h,其中300℃以上的达60h。 2 化学成分分析与铁素体含量测定 对蒸汽过热器直管、弯头和焊缝金属的化学成分进行分析,结果见表1。由表可见,蒸汽过热器直管与弯头的化学成分符合GB13296-1991对1Cr19Ni9钢的要求。 采用铁素体含量测定仪对蒸汽过热器中已开裂的直管、弯头及其焊缝处的铁素体含量进行测定,结果直管的铁素体含量平均为1.5%(共8点),最高为1.84%;弯头的铁素体含量平均为0.35%(共8点),最高为0.38%;焊缝处铁素体含量平均为319%,最高为6.47%。可见,蒸汽过热器管铁素体含量正常。 3 蒸汽过热器管内壁渗透液检验 为检验过热器管焊缝以外其它部位是否有裂纹,将过热器直管(部分)及弯头沿对称轴切开,进行内壁渗透液检验。结果显示,除了已穿透的裂纹及部分分叉外,未发现其它裂纹。 4 力学性能测试 力学性能试样均为两种状态,即过热器管的使用态和重新固溶热处理状态。重新固溶热处理工艺为1050℃水冷。 4.1 拉伸性能 按GB6397-1986标准,在过热器直管段取样,试样为矩形截面全厚度试样。拉伸试验按GB228-1987标准进行。试验温度为室温。试样数量为使用态和重新固溶态各两根。试验结果见表2。
过热器爆管的根本原因及对策
过热器爆管的根本原因及对策 二十世纪八十年代初,美国电力研究院经过长期大量研究,把锅炉爆管机理分成六大类,共22种。在22种锅炉爆管机理中,有7种受到循环化学剂的影响,12种受到动力装置维护行为的影响。我国学者结合我国电站锅炉过热器爆管事故做了大量研究,把电站锅炉过热器爆管归纳为以下九种不同的机理。 1、长期过热 1.1失效机理 长期过热是指管壁温度长期处于设计温度以上而低于材料的下临界温度,超温幅度不大但时间较长,锅炉管子发生碳化物球化,管壁氧化减薄,持久强度下降,蠕变速度加快,使管径均匀胀粗,最后在管子的最薄弱部位导致脆裂的爆管现象。这样,管子的使用寿命便短于设计使用寿命。超温程度越高,寿命越短。在正常状态下,长期超温爆管主要发生在高温过热器的外圈和高温再热器的向火面。在不正常运行状态下,低温过热器、低温再热器的向火面均可能发生长期超温爆管。长时超温爆管根据工作应力水平可分为三种:高温蠕变型、应力氧化裂纹型、氧化减薄型。 1.2产生失效的原因 (1)管内汽水流量分配不均; (2)炉内局部热负荷偏高; (3)管子内部结垢; (4)异物堵塞管子; (5)错用材料; (6)最初设计不合理。 1.3故障位置 (1)高温蠕变型和应力氧化裂纹型主要发生在高温过热器的外圈的向火面;在不正常的情况下,低温过热器也可能发生; (2)氧化减薄型主要发生在再热器中。 1.4爆口特征 长期过热爆管的破口形貌,具有蠕变断裂的一般特性。管子破口呈脆性断口特征。爆口粗糙,边缘为不平整的钝边,爆口处管壁厚度减薄不多。管壁发生蠕胀,管
径胀粗情况与管子材料有关,碳钢管径胀粗较大。20号钢高压锅炉低温过热器管破裂,最大胀粗值达管径的15%,而12CrMoV钢高温过热器管破裂只有管径5%左右的胀粗。 (1)高温蠕变型 a.管子的蠕胀量明显超过金属监督的规定值,爆口边缘较钝; b.爆口周围氧化皮有密集的纵向裂纹,内外壁氧化皮比短时超温爆管厚,超温程度越低,时间越长,则氧化皮越厚和氧化皮的纵向裂纹分布的范围也越广; c.在爆口周围的较大范围内存在着蠕变空洞和微裂纹; d.向火侧管子表面已完全球化; e.弯头处的组织可能发生再结晶; f.向火侧和背火侧的碳化物球化程度差别较大,一般向火侧的碳化物己完全球化。 (2)应力氧化裂纹型 a.管子的蠕胀量接近或低于金属监督的规定值,爆口边缘较钝,呈典型的厚唇状; b.靠近爆口的向火侧外壁氧化层上存在着多条纵向裂纹,分布范围可达整个向火侧。内外壁氧化皮比短时超温爆管时的氧化皮厚; c.纵向应力氧化裂纹从外壁向内壁扩展,裂纹尖端可能有少量空洞; d.向火侧和背火侧均发生严重球化现象,并且管材的强度和硬度下降; e.管子内壁和外壁的氧化皮发生分层; f.燃烧产物中的S、Cl、Mn、Ca等元素在外壁氧化层沉积和富集。 (3)氧化减薄型 a.管子向火侧、背火侧的内外壁均产生厚度可达1.0~1.5mm的氧化皮; b.管壁严重减薄,仅为原壁厚的1/3~l/8 ; c.内、外壁氧化皮均分层,为均匀氧化。内壁氧化皮的内层呈环状条纹; d.向火侧组织己经完全球化,背火侧组织球化严重,并且强度和硬度下降; e.燃烧产物中的S、Cl、Mn、Ca等元素在外壁氧化层沉积和富集,促进外壁氧化。
锅炉爆管典型事故案例及分析
锅炉典型事故案例及分析 第一节锅炉承压部件泄露或爆破事故大型火力发电机组的非停事故大部分是由锅炉引起的。随着锅炉机组容量增大,“四管”爆泄事故呈现增多趋势,严重影响锅炉的安全性,对机组运行的经济性影响也很大。有的电厂因过热器、再热器管壁长期超温爆管,不得不降低汽温5~10℃运行;而主汽温度和再热汽温度每降低10℃,机组的供电煤耗将增加0.7~1.1g/kWh;主蒸汽压力每降低1MPa,将影响供电煤耗2g/kWh。为了防止锅炉承压部件爆泄事故,必须严格执行《实施细则》中关于防止承压部件爆泄的措施及相关规程制度。 一.锅炉承压部件泄露或爆破的现象及原因 (一)“四管”爆泄的现象 水冷壁、过热器、再热器、省煤器在承受压力条件下破损,称为爆管。 受热面泄露时,炉膛或烟道内有爆破或泄露声,烟气温度降低、两侧烟温偏差增大,排烟温度降低,引风机出力增大,炉膛负压指示偏正。 省煤器泄露时,在省煤器灰斗中可以看到湿灰甚至灰水渗出,给水流量不正常地大于蒸汽流量,泄露侧空预器热风温度降低;过热器
和再热器泄露时蒸汽压力下降,蒸汽温度不稳定,泄露处由明显泄露声;水冷壁爆破时,炉膛内发出强烈响声,炉膛向外冒烟、冒火和冒汽,燃烧不稳定甚至发生锅炉灭火,锅炉炉膛出口温度降低,主汽压、主汽温下降较快,给水量大量增加。 受热面炉管泄露后,发现或停炉不及时往往会冲刷其他管段,造成事故扩大。 (二)锅炉爆管原因 (1)锅炉运行中操作不当,炉管受热或冷却不均匀,产生较大的应力。 1)冷炉进水时,水温或上水速度不符合规定;启动时,升温升压 或升负荷速度过快;停炉时冷却过快。 2)机组在启停或变工况运行时,工作压力周期性变化导致机械应 力周期性变化;同时,高温蒸汽管道和部件由于温度交变产生热应力,两者共同作用造成承压部件发生疲劳破坏。 (2)运行中汽温超限,使管子过热,蠕变速度加快 1)超温与过热。超温是指金属超过额定温度运行。超温分为长期 超温和短期超温,长期超温和短期超温是一个相对概念,没有严格时间限定。超温是指运行而言,过热是针对爆管而言。过热可分为长期过热和短期过热两大类,长期过热爆管是指金属在应力和超温温度的长期作用下导致爆破,其温度水平要比短期过热的水平低很多,通常不超过钢的临界点温度。短期过热爆管是指,在短期内由于管子温度升高在应力作用下爆破,其
弯头错用钢材长期过热爆管
弯头错用钢材长期过热爆 管 Revised by Hanlin on 10 January 2021
弯头错用钢材,长期过热爆管【简述】2009年12月11日,某电厂1号机因主蒸汽变侧至启动疏水扩容器的疏水管弯头错用钢材,管道长期过热,材质老化,运行中弯头背弧面发生爆破,机组停运。 【事故经过】事故前工况:1号机组带功率333MW运行,主汽压力 17.70MPa,给水流量941t/h,蒸汽流量969t/h,其他参数无异常。 2009年12月11日05时53分,运行人员听到汽轮机房突然传来一声巨响和持续的蒸汽泄漏声,经派人现场检查发现1号机附近有大量蒸汽喷出,人员无法进入现场详细检查,立即对1号机组进行降压、降负荷。06时17分,经中调同意,1号发电机解列。07时01分,检查发现1号机主蒸汽变侧至启动疏水扩容器的疏水管上往下第3个弯头背弧面发生爆破。机组停运后,立即组织安排抢修工作。14日12时10分,抢修工作结束。14日21时58分,机组恢复运行。 【事故原因】 爆口位置为弯头背弧面,形状为梭形,长约240mm,最宽约70mm;边缘最薄处厚8.4mm,无明显减薄,脱落的破片窄而长(长约225mm×宽约 30mm),从爆口宏观分析看,为过热爆管。经材质光谱半定量分析,爆口
弯头无Cr、Mo、V合金元素,为碳钢材料。根据《火力发电厂金属材料选用导则》(DL/T715-2000),碳钢材料的钢号应用范围在壁温≤425℃的蒸汽管道、集箱,而该段主蒸汽管道疏水的介质温度在540℃。从以上分析可知,由于爆管弯头错用钢材,存在长期过热现象,导致材质老化,直至出现蠕变裂纹后爆破,是造成此次事故的直接原因。 【防范措施】 1.在新机组基建安装阶段,要加强监督管理和过程控制,坚决杜绝建设安装工作的随意性,杜绝错用钢材事件的重复发生。要严格高压焊接工艺管理,严格按照规程使用焊工代号钢印,建立完善责任追究机制。同时要同步建立机、炉外管道的台帐,确保资料台帐与机组同步移交生产。 2.严格按照金属技术监督规程和集团公司机炉外管管理有关要求,成立工作小组,从完善基础资料、台帐入手,认真开展普查工作,认真排查每一段管材、管件,确保材质、规格符合设计要求,并确保台帐帐实相符。 3.在对机、炉外管道清查过程中,对底数不清而又没有检修机会的机组,要按照《防止电力生产重大事故二十五项重点要求实施导则》防止人身伤亡事故的有关要求,在高温疏放水管道周围设置警戒围栏,悬挂
锅炉过热器爆管原因及对策
锅炉过热器爆管原因及对策 前言 随着我国电力工业建设的迅猛发展,各种类型的大容量火力发电机组不断涌现,锅炉结构及运行更加趋于复杂,不可避免地导致并联各管内的流量与吸热量发生差异。当工作在恶劣条件下的承压受热部件的工作条件与设计工况偏离时,就容易造成锅炉爆管。 事实上,当爆管发生时常采用所谓快速维修的方法,如喷涂或衬垫焊接来修复,一段时间后又再爆管。爆管在同一根管子、同一种材料或锅炉的同一区域的相同断面上反复发生,这一现象说明锅炉爆管的根本问题还未被解决。因此,了解过热器爆管事故的直接原因和根本原因,搞清管子失效的机理,并提出预防措施,减少过热器爆管的发生是当前的首要问题。 1过热器爆管的直接原因 造成过热器、再热器爆管的直接原因有很多,主要可以从以下几个方面来进行分析。 1.1设计因素 1.热力计算结果与实际不符 热力计算不准的焦点在于炉膛的传热计算,即如何从理论计算上较合理的确定炉膛出口烟温和屏式过热器的传热系数缺乏经验,致使过热器受热面的面积布置不够恰当,造成一、二次汽温偏离设计值或受热面超温。 2.设计时选用系数不合理 如华能上安电厂由B&W公司设计、制造的“W”型锅炉,选用了不合理的受热面系数,使炉膛出口烟温实测值比设计值高80~100℃;又如富拉尔基发电总厂2号炉(HG-670/140-6型)选用的锅炉高宽比不合理,使炉膛出口实测烟温高于设计值160℃。 3.炉膛选型不当 我国大容量锅炉的早期产品,除计算方法上存在问题外,缺乏根据燃料特性选择炉膛尺寸的可靠依据,使设计出的炉膛不能适应煤种多变的运行条件。 炉膛结构不合理,导致过热器超温爆管。炉膛高度偏高,引起汽温偏低。相反,炉膛高度偏低则引起超温。 4.过热器系统结构设计及受热面布置不合理 调研结果表明,对于大容量电站锅炉,过热器结构设计及受热面布置不合理,是导致一、二次汽温偏离设计值或受热面超温爆管的主要原因之一。 过热器系统结构设计及受热面布置的不合理性体现在以下几个方面: (1)过热器管组的进出口集箱的引入、引出方式布置不当,使蒸汽在集箱中流动时静压变化过大而造成较大的流量偏差。 (2)对于蒸汽由径向引入进口集箱的并联管组,因进口集箱与引入管的三通处形成局部涡流,使得该涡流区附近管组的流量较小,从而引起较大的流量偏差。引进美国CE公司技术设计的配300MW和600MW机组的控制循环锅炉屏再与末再之间不设中间混合集箱,屏再的各种偏差被带到末级去,导致末级再热器产生过大的热偏差。如宝钢自备电厂、华能福州和大连电厂配350MW机组锅炉,石横电厂配300MW机组锅炉以及平坪电厂配600MW机组锅炉再热器超温均与此有关。 (3)因同屏(片)并联各管的结构(如管长、内径、弯头数)差异,引起各管的阻力系数相差较大,造成较大的同屏(片)流量偏差、结构偏差和热偏差,如陡河电厂日立850t/h锅炉高温过热器超温就是如此。 (4)过热器或再热器的前后级之间没有布置中间混合联箱而直接连接,或者未进行左右交叉,这样使得前后级的热偏差相互叠加。 在实际运行过程中,上述结构设计和布置的不合理性往往是几种方式同时存在,这样加剧了
锅炉受热面高温腐蚀原因分析及防范措施
锅炉受热面高温腐蚀原因分析及防范措施 Cause Analysis and Protective Measues to High-temperature Corrosion On Heating Surface of Boiler 张翠青 (内蒙古达拉特发电厂,内蒙古达拉特 014000) [摘要]达拉特发电厂B&WB-1025/18.44-M型锅炉在九八及九九年#1、#2炉大修期间,检查发现两台炉A、B两侧水冷壁烟气侧、屏式过热器迎火侧、高温过热器迎火侧存在大面积腐蚀,根据腐蚀部位、形态和产物进行分析,锅炉受热面的腐蚀属于高温腐蚀,其原因主要与炉膛结构、煤、灰、烟气特性及运行调整有关,并提出了防范调整措施。 [关键词] 锅炉受热面;高温腐蚀;机理原因分析;防范措施
达拉特发电厂#1~#4炉是北京B&WB公司设计制造的B&WB-1025/18.4-M型亚临界自然循环固态排渣煤粉炉。锅炉采用前后墙对冲燃烧方式。设计煤种为东胜、神木地区长焰煤。在九八及九九年#1、#2炉大修期间,检查发现两台炉A、B两侧水冷壁烟气侧、屏式过热器迎火侧、高温过热器迎火侧存在大面积腐蚀,两台炉腐蚀的产物、形状及部位相似。腐蚀区域水冷壁在标高16~38米之间及屏式过热器、高温过热器沿管排高度,腐蚀深度在0.4~1.0mm之间,最深处达1.7mm,腐蚀面积达500平方米左右。腐蚀给机组安全运行带来严重隐患。 1.腐蚀机理原因 1.1锅炉炉膛结构 锅炉炉膛结构设计参数见下表: 高40%多,同时上排燃烧器至屏过下边缘高度值比推荐范围的下限还低1.8米,这就导致燃烧器布置过于集中、燃烧器区域局部热负荷偏大、该区域内燃烧温度过高,实测炉膛温度达1370~1430℃。燃烧温度偏高直接导致水冷壁管壁温度过高,理论计算该区域水冷壁表面温度为452℃。大量的试验研究表明当水冷壁管壁温度大于400℃以后,就会产生明显的高温腐蚀。 1.2 煤、灰、烟气因素 蒙达公司实际燃煤是东胜、神木煤田的长焰煤和不粘结煤的混煤。:燃煤中碱性氧化物含量较高,灰中钠、钾盐类含量高,平均值达3.85%,含硫量偏高。 1.3 运行调整不当 为了分析运行调整因素对腐蚀的影响,在A、B侧水冷壁标高20、25、28米处安装了三排烟气取样点,每排三个,共18个。分析烟气成分后发现,燃用含硫量高的煤种时,由于燃烧配风调整不合理,省煤器后氧量偏大(实侧值 气体,加剧了高温腐蚀的产生与发展。 4.35%),导致燃烧过程中生成大量的SO 2 2.腐蚀类型 所取垢样中,硫酸酐及三氧化二铁的含量最高,具有融盐型腐蚀的特征,属于融盐型高温腐蚀。从近表层腐蚀产物的分析结果看,S和Fe元素含量最高,具有硫化物型腐蚀特征,说明存在较严重的硫化物型腐蚀。因此,达拉特发电厂的锅炉高温腐蚀是以融盐型腐蚀为主并有硫化物腐蚀的复合型腐蚀。 3.防止受热面高温腐蚀的措施 2.1.采用低氧燃烧技术组 由于供给锅炉燃烧室空气量的减少,因此燃烧后烟气体积减小,排烟温度下 的百分数和过量空气百分数之间降,锅炉效率提高。燃油和煤中的硫转化为SO 3 的转化明显下降。的关系是,随着过量空气百分数的降低,燃料中的硫转化为SO 3
分隔屏过热器爆管分析及处理
分隔屏过热器爆管分析及处理 翟德双 (田集发电厂232098) 摘要:分析田集发电厂1号锅炉分隔屏过热器超温爆管的原因,介绍所采取的针对性运行调整措施及实施结果。关键词:超临界;直流锅炉;分隔屏过热器;爆管;原因分析 1 概述 田集发电厂一期工程装有2台600MW超临界燃煤机组,2台机组分别于2007年7月26日和10月15日投产。该机组锅炉为超临界压力螺旋管圈直流炉,炉膛四角布置直流式喷燃器,配置6台中速磨煤机直吹式制粉系统,锅炉采用等离子方式点火(四角A层布置),启动系统采用容量为30%BMCR的不带循环泵的内置式启动系统,汽轮机设高低压两级串联旁路系统,旁路容量为35%BMCR。 2 锅炉爆管经过 2007年5月30日,机组首次整套启动,顺利进行锅炉点火、汽机冲转、发电机并网,机组带10%初始负荷4小时进行暖机,机组与系统解列后,做汽轮机超速试验,做汽机主汽门及调速汽门严密性试验。 2007年5月31日,机组再次启动,6月1日1时53分发电机并网,逐渐加负荷,14时22分向调度申请机组加负荷,进行锅炉安全门校验, 17时30分左右,锅炉转干态运行,发现机组补给水量异常,各系统进行全面检查,未发现明显异常情况,在对给水和疏放水系统进行全面检查和隔离后,机组补给水量有所下降,于是按计划带负荷进行锅炉安全门校验,23时20分发现捞渣机卡涩现象,发现内部有疑似受热面钢管。即向调度申请停炉,当时机组负荷330MW,分离器压力22MPa,过热器出口温度正常,给水量860~920t,燃煤量178t。确定锅炉爆管,经调度同意,于6月2日1时42分锅炉停炉。 3 爆管检查及分析 3.1 爆管情况检查和试验 (1)停炉后进入炉膛检查发现分隔屏过热器爆管断裂,部分管屏及定位管变形严重。 (2)光谱分析检查:分隔屏管进口段材质为T12,出口段材质为T23,下部外三圈为T91,T91与T12间用T23短管过渡,通过对现场管光谱分析检查,材质与设计图纸相符。 (3)硬度检查:对爆管管子和现场管子进行硬度检查,T91管子HB基本在170左右,T23管子HB基本在140~150左右,T12管子HB基本在120~130左右,参考ASTM SA213标准,T12 114
过热器爆管原因
过热器爆管的原因 1过热器爆管的直接原因 造成过热器、再热器爆管的直接原因有很多,主要可以从以下几个方面来进行分析。 1.1设计因素 1.热力计算结果与实际不符 热力计算不准的焦点在于炉膛的传热计算,即如何从理论计算上较合理的确定炉膛出口烟温和屏式过热器的传热系数缺乏经验,致使过热器受热面的面积布置不够恰当,造成 一、二次汽温偏离设计值或受热面超温。 2.设计时选用系数不合理 如华能上安电厂由B&W公司设计、制造的“W”型锅炉,选用了不合理的受热面系数,使炉膛出口烟温实测值比设计值高80~100℃;又如富拉尔基发电总厂2号炉(HG-670/140-6型)选用的锅炉高宽比不合理,使炉膛出口实测烟温高于设计值160℃。 3.炉膛选型不当 我国大容量锅炉的早期产品,除计算方法上存在问题外,缺乏根据燃料特性选择炉膛尺寸的可靠依据,使设计出的炉膛不能适应煤种多变的运行条件。 炉膛结构不合理,导致过热器超温爆管。炉膛高度偏高,引起汽温偏低。相反,炉膛高度偏低则引起超温。 4.过热器系统结构设计及受热面布置不合理 调研结果表明,对于大容量电站锅炉,过热器结构设计及受热面布置不合理,是导致一、二次汽温偏离设计值或受热面超温爆管的主要原因之一。 过热器系统结构设计及受热面布置的不合理性体现在以下几个方面: (1)过热器管组的进出口集箱的引入、引出方式布置不当,使蒸汽在集箱中流动时静压变化过大而造成较大的流量偏差。 (2)对于蒸汽由径向引入进口集箱的并联管组,因进口集箱与引入管的三通处形成局部涡流,使得该涡流区附近管组的流量较小,从而引起较大的流量偏差。引进美国CE公司技术设计的配300MW和600MW机组的控制循环锅炉屏再与末再之间不设中间混合集箱,屏再的各种偏差被带到末级去,导致末级再热器产生过大的热偏差。如宝钢自备电厂、华能福州和大连电厂配350MW机组锅炉,石横电厂配300MW机组锅炉以及平坪电厂配600MW机组锅炉再热器超温均与此有关。 (3)因同屏(片)并联各管的结构(如管长、内径、弯头数)差异,引起各管的阻力系数相差较大,造成较大的同屏(片)流量偏差、结构偏差和热偏差,如陡河电厂日立850t/h 锅炉高温过热器超温就是如此。 (4)过热器或再热器的前后级之间没有布置中间混合联箱而直接连接,或者未进行左右交叉,这样使得前后级的热偏差相互叠加。 在实际运行过程中,上述结构设计和布置的不合理性往往是几种方式同时存在,这样
浅析垃圾焚烧炉过热器腐蚀原因及解决措施(新编版)
( 安全论文 ) 单位:_________________________ 姓名:_________________________ 日期:_________________________ 精品文档 / Word文档 / 文字可改 浅析垃圾焚烧炉过热器腐蚀原因及解决措施(新编版) Safety is inseparable from production and efficiency. Only when safety is good can we ensure better production. Pay attention to safety at all times.
浅析垃圾焚烧炉过热器腐蚀原因及解决措 施(新编版) 摘要:垃圾焚烧发电是实现城市垃圾无害化、减量化和资源化处理的一种有效方法,目前正得到大力的推广。焚烧发电具有工艺简单,运行可靠,垃圾处理速度快,处理量大。但是由于垃圾成份相当复杂,用于焚烧垃圾的焚烧炉存在非常严重的磨损、腐蚀现象,在腐蚀现象中以高温过热器管的腐蚀问题最为严重。本文主要就这个问题展开讨论并提出预防措施。 关键词:垃圾焚烧炉;高温过热器管腐蚀;措施 一、垃圾焚烧发电工艺原理垃圾焚烧发电是将垃圾放在焚烧炉中进行燃烧,释放出热能,余热回收加热给水变成蒸汽,蒸汽在汽轮机中推动汽轮发电机旋转做功,将蒸汽的热能转化为电能,释放热能后的烟气经净化系统处理后排放,从而将垃圾由“废物”变为
可利用的“资源”。随着各种炉型技术的实践应用广泛开展,炉排式垃圾焚烧炉以适应性强,处理比较彻底的优势正成为目前国内垃圾焚烧的主流工艺。随着技术的不断的提高和发展,我国焚烧炉的垃圾处理容量也不断的提高,从初期的150t/d提高到现在的750t/d,规模日趋增大。 二、垃圾焚烧发电的特点一般来说,垃圾经焚烧处理后残余的固体废物约占20%(炉渣约占15%,飞灰约占5%),考虑炉渣的综合利用因素,减量化效果更为显著。这相比于垃圾填埋处理要永久性占用土地来说节约了大量的土地资源。垃圾中的可燃物在焚烧中基本上变为了可利用的热能。根据城市发展程度及地理位置、生活习惯不同,垃圾的热值有所不同,一般用于焚烧的垃圾要求低位热值大于4180KJ/Kg,垃圾发电量一般在250kwh/t以上(随热值的提高而增加)。另外,由于垃圾焚烧后的尾气经过了严格的净化处理,因此对环境的污染被控制到了最低。因此,垃圾焚烧处理的特点是处理量大、减量效果好、无害化彻底,且有热能回收作用,是真正实现垃圾处理的“无害化、资源化、减量化”的技术手段。因此,对
火电厂超温爆管实例分析
超温爆管实例分析 锅炉承压部件的安全运行对整个电厂的安全至关重要。文章结合微水电厂实际,分析了过热器爆管泄漏的机理、原因及实际采取的一些对策,以求对锅炉过热器设备的完好运行有所裨益。 1 前言 据统计,河北省南部电网锅炉各种事故约占发电厂事故的63.2%,而承压部件泄漏事故又占锅炉事故的86.7%。因此迫切需要大幅度降低锅炉临修次数。下面结合微水电厂实际,分析过热器爆管泄漏的机理、原因及采取的一些对策。 微水发电厂锅炉型号为HG-220/100-4,露天布置,固态排渣煤粉炉,四角切圆燃烧,过热器由辐射式炉顶过热器、半辐射屏式过热器、对流过热器和包墙管4部分组成。减温水采用给水直接喷入,分两级减温。炉顶管、包墙管和第二级过热器管用φ38×4.5的20号碳钢管组成。第一级过热器和屏过热器用φ42×5的12Cr1 MoV钢管组成。 2 过热器爆管的主要原因 2.1 超温、过热和错用钢材 2.2 珠光体球化及碳化物聚集 针对12Cr1 MoV钢分析,试验表明当12Cr1 MoV钢严重球化到5级时,钢的室温强度极限下降约11kg/mm2。微水发电厂1993年4月过热器爆管的统计资料表明:因局部长期过热,珠光体耐热钢已达到了5级球化现象,而它的塑性水平仍然比较高。发生球化现象以后,钢的蠕变极限和持久强度下降。通过580℃下对12Cr1 MoV钢的持久爆管试验,可以看出到了球化4级的钢管,其持久强度降低1/3。影响珠光体耐热钢发生球化的因素主要有温度、时间、应力和钢材的化学成份等。在钢中掺入“V”这种强碳化物元素,可以阻碍珠光体的球化过程,只要能形成稳定的碳化物,则球化过程减速。 通过对12Cr1 MoV管试验发现,温度在540℃时,随着运行时间的增加,钢的工作温度下蠕变极限和持久强度也相应降低。随着运行温度的提高、时间的延长、应力的变化都会加速合金元素的固溶体和碳化物间的重新分配现象。 2.3 焊接质量
锅炉爆管知识
锅炉爆管知识 如何根据爆口特征判断爆管原因 四管爆漏的种类和定义 四管爆漏是指锅炉热交换面中的水冷壁、过热器、再热器和省煤器四种受热面管由于过热、腐蚀、磨损等各种原因发生破裂、泄漏, 导致炉管失效, 甚至引起锅炉事故停机。 根据其产生的原因不同, 可以按表1 分类。 爆口特征判断法是现场确定爆管原因的重要手段。 爆口特征主要是指: (1)爆口位置:位于何种受热面的具体部位是向火侧还是背火侧。 (2)爆口形状 1)断口面是否垂直于轴向;
2)爆口边缘有无明显变薄情况,是锐边还是钝边; 3)爆口内壁有无积垢,外壁氧化情况,爆口附近宏观裂纹; 4)爆口附近内外壁有无明显的腐蚀坑; 5)爆口附近内外壁上的裂纹走向。 (3)爆口附近的金相:包括相的组成、数量、形态、大小和分布 ,以及各类金相裂纹( 性质、大小、形态、走向及其与显微组织的关系等), 显微孔洞的大小和分布,珠光体球化程度和石墨化程度 , 脱碳、过烧、过热等。 过热爆管 过热可分短期过热和长期过热两大类。 长期过热 长期过热爆管通常爆口不大 , 破口断面粗糙而不平整 ,管壁减薄不多 ,破口边缘是钝边 , 并不锋利 , 破口附近有众多的平行于破口的管子轴向裂纹。 由于长期在高温下运行 , 爆口附近往往有较厚的黑色氧化 皮。从蠕变原理上来说 , 破口应为塑性断裂 ,但蠕变爆管往往伴有应力腐蚀 , 这使爆口表现出脆性断裂的特征。 当管子过热时 , 管子会以加快了的蠕变速度发生管径胀粗 ,通常在爆口的金相图中可以看到明显的蠕变晶间裂纹 ,伴随有严重的球化现象。
由于长期在高温下运行 ,在裂纹发展的同时 , 也发生裂纹内部的氧化 , 结果在裂纹内壁上生成了氧化层 , 尤其是粗大的蠕变裂纹处 ,其氧化层更为明显。 短期过热 短期过热是由于管子在严重超温的情况下力学性能严重下降 ,管子在压力的作用下发生塑性变形以至爆破。短期过热爆管按过热程度的高低又可分为: (1)瞬时过热爆管 , 温度在 Ac3 以上; (2)短期直接过热爆管; (3)小鼓包爆管。 瞬时过热爆管破口处呈喇叭状 , 管子严重减薄胀粗 ,边缘锋 利 , 为韧性断裂 , 外表呈蓝黑色氧化组织。破口的内壁由于管内汽水混合物急剧冲出 , 因此显得十分光洁 ,管子胀粗严重。管子外壁一般呈蓝黑色;破口附近没有众多平行于破口的轴向裂纹 , 破口处的组织为羽毛状贝氏体组织。 短时直接过热爆管的爆口很大 , 外形上呈不规则菱形 ,显微组织碳化物球化 , 破口边较锋利 , 破口附近有一定的胀粗并且在离破口较远处管子也有不同程度的胀粗。破口组织为铁素体加块状珠光体 , 珠光体已有一定程度的球化。 小鼓包爆管是局部过热爆破 , 未爆破部位胀粗不明显 ,破口处有明显的小鼓包 , 破口也较锐利、光滑。破口组织为铁素体加块状珠光体 , 珠光体已有一定程度的球化 ,晶界上也有渗碳体球。
过热器高温腐蚀机理分析-赵梦瑾
过热器高温腐蚀机理分析 赵梦瑾 摘要:介绍了锅炉过热器高温硫腐蚀和水蒸汽氧化腐蚀的过程机理,分析导致腐蚀不断进行的主要因素,并提出防治措施,促进锅炉安全经济运行。 1 前言 过热器用于回收烟气中的热量,提高锅炉效率。炉膛出口烟气温度比较高,为1000~1100℃,经过过热器后温度降至700~800℃。过热器在锅炉受压部件中承受的温度最高。高温硫腐蚀和水蒸汽氧化腐蚀是过热器管两种主要腐蚀形式,其中外壁高温硫腐蚀已受到较多关注。近年来由水蒸气氧化腐蚀而引发爆管以及剥落下来的坚硬氧化皮微粒造成的汽轮机固体颗粒侵蚀的事故日益突出,水蒸汽氧化腐蚀问题也越来越引起重视。 2 高温硫腐蚀 2.1 机理 高温积灰所生成的内灰层含有较多的碱金属,这些碱金属与飞灰中的铁铝等成分以及烟气中通过松散外灰层扩散进来的氧化硫进行较长时间的化学作用便生成碱金属的硫酸盐等复合物,复合硫酸盐附着在管壁上,对管子金属进行氧化腐蚀。在腐蚀发生过程中,从机理上讲主要会有如下几种反应发生[1]: (1)在燃烧过程中,FeS2及有机硫化物与氧发生反应; 4FeS2 +11O2→2Fe2O3+8SO2 RS(有机硫化物)+ O2→SO2 2SO2+ O2→2SO3 (2)在高温条件下,煤中钠和钾被氧化成Na2O和K2O; (3)Na2O和K2O与烟气中或沉积在管壁上的SO3发生反应生成碱性硫酸盐; Na2O+ SO3→Na2SO4 K2O+ SO3→K2SO4 (4)碱性硫酸盐、氧化铁与SO3反应形成复合硫酸盐; 3Na2SO4+Fe2O3+ 3SO3→2Na3Fe(SO4)3 3K2SO4+Fe2O3+ 3SO3→2K3Fe(SO4)3 (5)在高温条件下,处于熔融状态的复合硫酸盐与管子金属发生下列反应。 4Na3Fe(SO4)3 +12Fe→3FeS+ 3Fe3O4 +2Fe2O3 +6Na2SO4+ 3SO2 4K3Fe(SO4)3 +12Fe→3FeS+ 3Fe3O4 +2Fe2O3 +6K2SO4+ 3SO2 这些复合硫酸盐在550~750℃范围内以熔化状态贴附在管壁上,并随着烟气的流动而被带走,造成管壁表面粗糙,而后面新生成的硫酸盐就越易在这些粗糙表面优先附着,又会重复上述的腐蚀反应。这是一个恶性循环过程,周而复始,随着腐蚀的进行,管壁就会被逐渐蚕食。当被侵蚀的金
锅炉过热器爆管原因分析及对策(通用版)
Enhance the initiative and predictability of work safety, take precautions, and comprehensively solve the problems of work safety. (安全管理) 单位:___________________ 姓名:___________________ 日期:___________________ 锅炉过热器爆管原因分析及对策 (通用版)
锅炉过热器爆管原因分析及对策(通用版)导语:根据时代发展的要求,转变观念,开拓创新,统筹规划,增强对安全生产工作的主动性和预见性,做到未雨绸缪,综合解决安全生产问题。文档可用作电子存档或实体印刷,使用时请详细阅读条款。 摘要:锅炉承压部件的安全运行对整个电厂的安全至关重要。文章结合微水电厂实际,分析了过热器爆管泄漏的机理、原因及实际采取的一些对策,以求对锅炉过热器设备的完好运行有所裨益。 关键词:锅炉过热器爆管电网 1前言 据统计,河北省南部电网锅炉各种事故约占发电厂事故的63.2%,而承压部件泄漏事故又占锅炉事故的86.7%。因此迫切需要大幅度降低锅炉临修次数。下面结合微水电厂实际,分析过热器爆管泄漏的机理、原因及采取的一些对策。 微水发电厂锅炉型号为HG-220/100-4,露天布置,固态排渣煤粉炉,四角切圆燃烧,过热器由辐射式炉顶过热器、半辐射屏式过热器、对流过热器和包墙管4部分组成。减温水采用给水直接喷入,分两级减温。炉顶管、包墙管和第二级过热器管用?38×4.5的20号碳钢管组成。第一级过热器和屏过热器用?42×5的12Cr1MoV钢管组成。
循环流化床锅炉屏式过热器爆管原因分析及处理
第6期 2009年11月 中 氮 肥 M 2Sized N itr ogenous Fertilizer Pr ogress No 16Nov .2009 循环流化床锅炉屏式过热器爆管原因分析及处理 谭 伟,吴小刚 (兖矿国泰化工有限公司,山东滕州 277527) [中图分类号]TK 22916+ 6 [文献标识码]B [文章编号]1004-9932(2009)06-0047-03 [收稿日期]2009204214 [作者简介]谭 伟(1980—),男,湖北宜城人,助理工 程师。 1 情况简介 我公司2# HG 2130/9182LY M20型循环流化床 锅炉于2005年5月点火试运行。2007年屏式过热器下部同一位置发生了6次爆管事故。现场勘查发现:锅炉管外径涨粗,同一管屏<42mm ×5mm 锅炉管涨粗后外径达44~49mm 不等,这是长期过热进而高温蠕变的显著特性;管壁没有明显减薄,爆管处破口呈厚唇状(如图1),破口断裂面粗糙、不平整;破口附近有众多平行于破口的轴向裂纹;管外壁氧化皮较厚,较脆,易剥落。对该锅炉管取样送山东大学材料学院进行金相分析,结果显示金属组织完全球化。按照DL438—2000《火力发电厂金属技术监督规程》817规定:合金钢锅炉管外径蠕变变形大于215%时应及时更换。该屏式过热器已于2008年 3月大修时全部更换,大修后的2# 锅炉已运行近24000h,负荷100t/h 左右,运行情况较好 。 图1 爆管处形状 2 锅炉屏式过热器超温爆管原因分析 HG 2130/9182LY M20型循环流化床锅炉炉膛 内部悬挂布置4片屏式过热器,每屏装有22根 锅炉管,规格为<42mm ×5mm ,材料为12Cr1Mo VG,管屏间距1200mm ,下集箱标高 +20960mm ,上集箱标高+36410mm 。设计蒸 汽进口温度为400℃,出口温度为485℃。炉膛风帽处标高+4500mm ,炉膛高度28500mm 。 根据锅炉原始开车及近3a 运行、改造记录分析,屏式过热器爆管原因主要有以下几点。211 减温水量不够,导致屏式过热器超温 该锅炉共设计2级混合式喷水减温器,屏式过热器在低温过热器和高温过热器之间。设计一级减温水管规格为<28mm ×3mm ,减温水量为413t/h,温度由425℃减至400℃;二级减温水管规格为<28mm ×3mm ,减温水量为214t/h,温度由485℃减至468℃。但锅炉在负荷大于80t/h 运行中,该减温水量不够,屏式过热器进口温度为420℃,出口温度为510℃,均超设计温度,导致屏式过热器管壁长期超温。这是屏式过热器超温爆管的主要原因。212 汽轮机高压加热器未投运,给水温度达不到设计值 该锅炉于2005年5月试运行,锅炉产蒸汽主要作为空分系统透平压缩机动力源和全厂蒸汽管网使用。由于蒸汽量不够,配套汽轮机于2005年11月试运行后一直低负荷运行(12MW 左右,额定负荷50MW ),无法投运汽轮机抽汽系统。锅炉给水未经高压加热器加热,给水温度设计值为215℃,但实际给水温度仅158℃,比设计温度低57℃。在锅炉运行前期,锅炉须在较高负荷状态下运行以满足后系统化工试开车用蒸汽需求。锅炉加负荷时,必然加大风量及燃料量,提高密相燃烧区域,相应就提高了火焰中心,强化了炉内燃烧,炉膛沸下温度达950℃,屏式过热器受到的热辐射增强;同时锅炉排烟量增大,尾部烟道对流换热量增大,也造成汽温升