840D螺距补偿
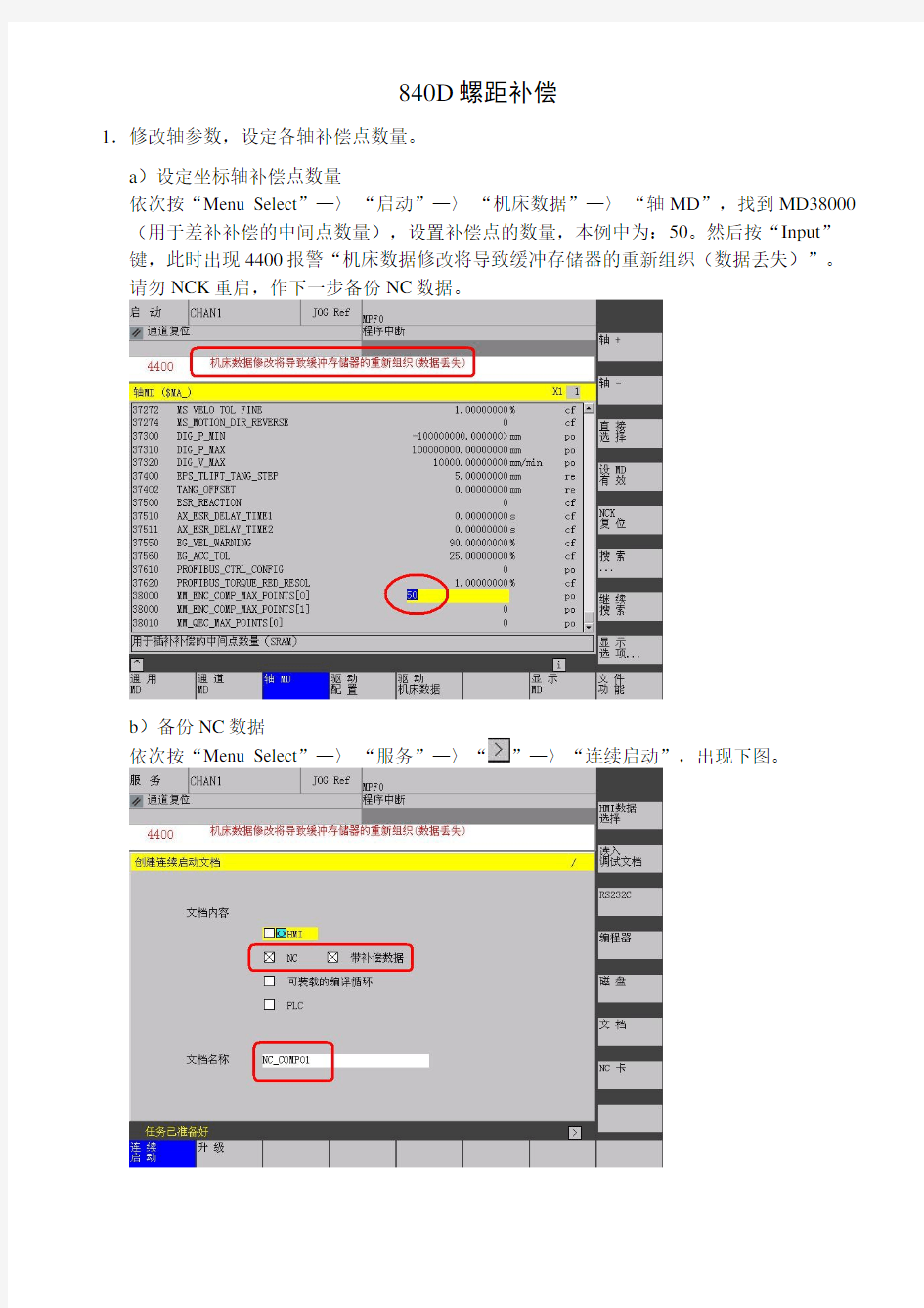

840D螺距补偿
1.修改轴参数,设定各轴补偿点数量。
a)设定坐标轴补偿点数量
依次按“Menu Select”—〉“启动”—〉“机床数据”—〉“轴MD”,找到MD38000(用于差补补偿的中间点数量),设置补偿点的数量,本例中为:50。然后按“Input”
键,此时出现4400报警“机床数据修改将导致缓冲存储器的重新组织(数据丢失)”。
请勿NCK重启,作下一步备份NC数据。
b)备份NC数据
依次按“Menu Select”—〉“服务”—〉“”—〉“连续启动”,出现下图。
在文档内容中选择“NC”和“带补偿数据”;输入文件名称,一定要按“Input”键,否则文件名无效。本例中为:NC_COMP01;按“文档”键,开始创建连续启动文档,如下图所示。
c)恢复数据
待连续启动文档创建好后,按“读入调试文档”键。
选择刚才创建的连续启动文档NC_COMP01,按“启动”键,并点击“是”加以确认。此后系统会重启几次。
2.导出补偿数据,生成ARC文件或MPF程序(参见补充说明)
因为补偿文件不能直接修改,只能输出成ARC文件。下面以给轴1添加螺补为例说明。
依次按“Menu Select”—〉“服务”—〉“数据选择”,选择“NC-生效-数据”,按“确认”键。
在数据输出窗口的树形图中选择“NC-生效-数据”—〉“测量系统误差补偿”—〉“测量系统错误补偿—轴1”,按“文档”键。
出现下图。输入文档名,本例中为:AX1_EEC。选择文档格式,必须为:带CR+LF穿孔带,否则无法编辑。按启动键。
3.输入补偿数据,编辑ARC文件。
PCU50可直接编辑ARC文件。PCU20可将ARC文件通过RS232传出,使用文本编辑器编辑。也可制作补偿程序,见第7条的补偿说明。
PCU50操作如下:
在树形图中选择“文档”—〉“AX1_EEC”,按“Input”键打开文件。
补偿文件结构如下:
$AA_ENC_COMP[0, 0, AX1]=0.5 对应于最小位置上的误差值
$AA_ENC_COMP[0, 1, AX1]=0.2 对应于最小位置+1个间隔位置上的误差值
$AA_ENC_COMP[0, 2, AX1]=-0.5 对应于最小位置+2个间隔位置上的误差值
… …
$AA_ENC_COMP[0, 48, AX1]=0 对应于最小位置+48个间隔位置上的误差值
$AA_ENC_COMP[0, 49, AX1]=0 对应于最小位置+49个间隔位置上的误差值
$AA_ENC_COMP_STEP[0, AX1]=10 测量间隔(毫米)
$AA_ENC_COMP_MIN[0, AX1]=0 最小位置(绝对)
$AA_ENC_COMP_MAX[0, AX1]=100 最大位置(绝对)
$AA_ENC_COMP_IS_MODULO[0, AX1]=0 用于旋转轴
修改文件后,保存并关闭编辑器。
4.补偿数据ARC文件导入NC系统。
设定MD32700=0,并且按“设MD有效”按钮,使参数生效,这样ARC文件才能写入补偿文件。
依次按“Menu Select”—〉“服务”—〉“”—〉“连续启动”—〉“读入调试文档”,选择修改好的AX1_EEC文件,按“启动”按钮。
设定MD32700=1,并且按“设MD有效”按钮,返参考点,补偿值生效。
返回参考点,出现回参考点标志。
6.确定补偿值生效。
此时螺补已生效,可在诊断界面中看到当前点的补偿值。
依次按“Menu Select”—〉“诊断”—〉“服务显示”—〉“轴调整”,观察“绝对补偿值测量系统1”的值会随当前点变化。
7.补充说明:
将“测量系统错误补偿—轴1”ARC文件通过RS232C接口传到电脑中,编辑补偿文件头和文件尾,将补偿文件改为加工程序格式。见下面例子:
%_N_BUCHANG_MPF
; $PATH=/_N_MPF_DIR
$AA_ENC_COMP[0, 0, AX1]=0.5
$AA_ENC_COMP[0, 1, AX1]=0.2
$AA_ENC_COMP[0, 2, AX1]=-0.5
...
$AA_ENC_COMP_STEP[0, AX1]=10
$AA_ENC_COMP_MIN[0, AX1]=0
$AA_ENC_COMP_MAX[0, AX1]=100
$AA_ENC_COMP_IS_MODULO[0, AX1]=0
M02
将修改过的文件传回系统中,这时在加工程序目录中可以看到名为“BUCHANG”的加工程序,打开加工程序,按“执行”键,待系统进入自动方式后按机床控制面板上的“NC 启动”按钮,执行加工程序后补偿值即存入系统中。
数控车床丝杠螺距误差的补偿
项目数控车床丝杠螺距误差的补偿 一、工作任务及目标 1.本项目的学习任务 (1)学习数控车床丝杠螺距误差的测量和计算方法; (2)学习数控车床螺距误差参数的设置方法。 2.通过此项目的学习要达到以下目标 (1)了解螺距误差补偿的必要性; (2)掌握螺距误差补偿的测量和计算方法; (3)能够正确设置螺距误差参数。 二、相关知识 滚珠丝杠螺母机构 数控机床进给传动装置一般是由电机通过联轴器带动滚珠丝杆旋转,由滚珠丝杆螺母机构将回转运动转换为直线运动。 1、滚珠丝杠螺母机构的结构 滚珠丝杠螺母机构的工作原理见图1;在丝杠1 和螺母 4 上各加工有圆弧形螺旋槽,将它们套装起来变成螺旋形滚道,在滚道内装满滚珠2。当丝杠相对螺母旋转时,丝杠的旋转面经滚珠推动螺母轴向移动,同时滚珠沿螺旋形滚道滚动,使丝杠和螺母之间的滑动摩擦转变为滚珠与丝杠、螺母之间的滚动摩擦。螺母螺旋槽的两端用回珠管 3 连接起来,使滚珠能够从一端重新回到另一端,构成一个闭合的循环回路。
2、进给传动误差 螺距误差:丝杠导程的实际值与理论值的偏差。例如PⅢ级滚珠丝杠副的螺距公差为0.012mm/300mm。 反向间隙:即丝杠和螺母无相对转动时丝杠和螺母之间的最大窜动。由于螺母 结构本身的游隙以及其受轴向载荷后的弹性变形,滚珠丝杠螺母机构存在轴向间隙,该轴向间隙在丝杠反向转动时表现为丝杠转动α角,而螺母未移动,则形成了反向间隙。为了保证丝杠和螺母之间的灵活运动,必须有一定的反向间隙。但反向间隙过大将严重影响机床精度。因此数控机床进给系统所使用的滚珠丝杠副必须有可靠的轴向间隙调节机构。 图2为常用的双螺母螺纹调隙式结构,它 用平键限制了螺母在螺母座内的转动,调整时只要扮动圆螺母就能将滚珠螺母沿轴 向移动一定距离,在将反向间隙减小到规定的范围后,将其锁紧。
立式加工中心机床的螺距误差补偿(精)
立式加工中心机床的螺距误差补偿 随着我国制造业的飞速发展,数控机床制造技术也在不断地发展,同时对数控机床的各项性能提出了越来越高的要求。机床的定位精度便成为了衡量机床性能的一项重要指标。机械结构当中不可避免的摩擦、间隙,以及装配误差成为了制约机床定位精度的主要因素。由此,数控系统的制造商开发出了螺距误差补偿功能,借此以消除或者削弱以上因素对机床定位精度的影响,从而达到更好的加工效果。发那科与西门子两大公司在这个领域表现得尤为出色,以下将对这两种数控系统的螺距误差补偿方法进行详细介绍。 1.发那科数控系统机床的误差补偿(以FANUC 0i-MD为例) 1.1基本概念 1.1.1补偿点的指定 各轴的补偿点的指定,可通过夹着参考点的补偿点编号指定(+)侧、(-)侧来进行。机械的行程超过(+)侧、(-)侧所指定的范围时,有关超出的范围,不进行螺距误差补偿(补偿量全都成为0)。 1.1.2补偿点号 补偿点数,在螺距误差设定画面上提供有共计1024 点,从0 到1023。通过参数将该编号任意分配给各轴。 另外,螺距误差设定画面中,在最靠近负侧的补偿号前,显示该轴的名称。 1.1.3补偿点的间隔 螺距误差补偿的补偿点为等间隔,在参数中为每个轴设定该间隔。 螺距误差补偿点的间隔有最小值限制,通过下式确定。 螺距误差补偿点间隔的最小值=最大进给速度(快速移动速度)÷7500 1.2相关参数 (1)1851 每个轴的反向间隙补偿量。 (2)1852 每个轴的快速移动时的反向间隙补偿量。 (3)3620 每个轴的参考点的螺距误差补偿点号。 (4)3621 每个轴的最靠近负侧的螺距误差补偿点号。 (5)3622 每个轴的最靠近正侧的螺距误差补偿点号。 (6)3623 每个轴的螺距误差补偿倍率。 (7)3624 每个轴的螺距误差补偿点间隔。 注:以上参数中3620,3621,3622,3624修改后需要切断电源并重新上电才生效,其余参数修改后复位即可生效。 1.3操作方法(以X轴行程为850mm的丝杠为例,全长采集20个数据) 1.3.1连接激光干涉仪 1.3.2设置参数
西门子840D系统下的螺距补偿和垂度补偿的综合运用
西门子840D系统下的螺距补偿和垂度补偿 的综合运用 李培志 (武汉华中自控技术发展有限公司,武汉430062) 摘要:结合西门子840D系统介绍了两种为提高机床定位精度的补偿方法------螺距补偿和垂度补偿。以及在机械几何精度不理想情况下的两种方法的综合运用。 关键词:螺距补偿垂度补偿位置精度检测 由于机械电子技术的飞速发展,数控机床作为一种高精度、高效率、稳定性强的自动化加工设备,越来越多的受到大家的关注。数控系统的定位精度是影响其高精度性能的一个重要因素,而利用西门子840D数控系统自带的螺距补偿和垂度补偿功能可以极大的降低机床的定位误差,提高机床的定位精度。本文就此介绍了这两种方法在实际中的具体使用。 补偿一般在机床几何精度调整完成后进行,这样可以尽量减少几何精度对定位精度的影响。一般情况下,螺距补偿可以运用在所有的直线进给轴以及旋转轴中,垂度补偿多运用在镗床的主轴箱滑枕或镗杆与立柱间的交叉补偿。1.螺距补偿 840D数控系统的螺距补偿功能是一种绝对型补偿方法,螺距补偿是按轴进行的。我们设定补偿起始点位置a,补偿终止点位置b,补偿间隔距离c,那么需要插补的中间点的个数n,其中n=1+(b-a)/c。 具体操作步骤如下: 1)设置轴数据MD38000 MM_ENC_COMP_MAX_POINTS[t] =n,修改此参数后会引起 NCK内存的重新分配。所以修改后要在服务菜单下对NC做一次备份。(t=所补偿轴的轴号) 2)对系统做一次NCK复位后会出现“M4400” 报警,提示轴参数丢失,此时将 1)步骤下的NC备份Load进NC系统。 3)在Nc-Active-Data菜单下Copy出“C EC_DATA”到一个新建立的备份文档目 录*.MDN中。 4)在新的目录下找到并打开补偿文件表格,根据测量人员测量的数据把相应的 补偿点直接在表格中更改。保存并关闭编辑器。 5)设定轴参数MD32700 ENC_COMP_ENABLE=0,将修改后的补偿表格 Load进NC
西门子840D数控系统螺距误差补偿知识
西门子840D数控系统螺距误差补偿 西门子840D数控系统不同于以前曾广泛应用的810T/M和840C等老数控系统,它并没有提供专门的双向螺距误差补偿功能,通过对840D系统中的下垂补偿功能的分析研究,找到了一种方法,成功的解决了进行双向螺距误差补偿的问题。 关键词:数控系统下垂补偿功能双向螺距误差补偿 由于机床丝杠在制造、安装和调整等方面的误差,以及磨损等原因,造成机械正反向传动误差的不一致,导致零件加工精度误差不稳定。因此也必须定期对机床坐标精度进行补偿,必要时要做双向坐标补偿,以达到坐标正反向运动误差的一致性。 一、西门子840D数控系统的补偿功能 西门子840D数控系统提供了多种补偿功能,供机床精度调整时选用。这些功能有: 1、温度补偿。 2、反向间隙补偿。 3、插补补偿,分为: (1) 螺距误差和测量系统误差补偿。 (2)下垂补偿(横梁下垂和工作台倾斜的多维交叉误差补偿)。 4、动态前馈控制(又称跟随误差补偿)。包括:速度前馈控制和扭矩前馈控制。
5、象限误差补偿(又称摩擦力补偿)。分为:常规(静态) 象限误差补偿和神经网络(动态)象限误差补偿。 6、漂移补偿。 7、电子重量平衡补偿。 在西门子840D功能说明样本和资料中所列的众多补偿功能中,都没有指出该系统具有双向螺距误差补偿功能。但是在下垂补偿功能描述中却指出,下垂补偿功能具有方向性。这样,如果下垂误差补偿功能,在基准轴和补偿轴定义为同一根轴时,就可能对该轴进行双向丝杠螺距误差补偿,由此提供了一个双向螺距误差补偿的依据。 二、840D下垂补偿功能的原理 1、下垂误差产生的原因: 由于镗铣头的重量或镗杆自身的重量,造成相关轴的位置相对于移动部件产生倾斜,也就是说,一个轴(基准轴)由于自身的重量造成下垂,相对于另一个轴(补偿轴)的绝对位置产生了变化。 2、840D下垂补偿功能参数的分析: 西门子840D数控系统的补偿功能,其补偿数据不是用机床数据描述,而是以参数变量,通过零件程序形式或通用启动文件(_INI文件) 形式来表达。描述如下: (1) $AN_CEC[t,N]:插补点N的补偿值,即基准轴的每个插补点对应于补偿轴的补偿值变量参数。 (2) $AN_CEC_INPUT_AXIS[t]:定义基准轴的名称。 (3) $AN_CEC_OUTPUT_AXIS[t]:定义对应补偿值的轴名称。 (4) $AN_CEC_STEP[t]:基准轴两插补点之间的距离。 (5) $AN_CEC_MIN[t]:基准轴补偿起始位置: (6) $AN_CEC_MAX[t]: 基准轴补偿终止位置 (7) $AN_CEC_DIRECTION[t]:定义基准轴补偿方向。其中:
反向间隙的补偿
.反向间隙的补偿 首先要求机械安装完成后的反向间隙必须保证在一定范围内。反向间隙在不同速度下切换方向时的数值不同,所以反向间隙补偿时对进给和快速移动分开进行补偿,传统习惯上只是设定前者,这是不科学的。以FANUC Oi系统为例,说明如下: 参数:P1851:各轴进给时的反向间隙补偿值。 没定值:按切削进给(一般取500~1000mm/min)时检测的反向间隙值设定(用激光干涉仪测量)。 参数:P1852.各轴快速时的反向间隙补偿值。 设定值:按快速(例如10000mm/min)时检测的反向间隙值设定(用激光干涉仪测量)。 参数:P1800#4 RBK。 设定值:此位参数设定为1,则切削和快速的反向间隙可以分别生效。 2.螺距误差的补偿 数控系统一般每轴设置最大可达128点的螺距误差补偿点数。必要时,可对某轴进行补偿,一般习惯是按50mm或100mm的间隔进行补偿,为了提高精度,建议用5mm或10mm的间隔进行补偿,效果更好。 3.补偿计数器的设定 全闭环控制时,通常设定补偿计数器,以FANUCOi系统为例,说明如下:参数:P2010#5 HBBL反向问隙补偿值加到误差计数器中。 设定值:设定为0,表示为半闭环方式(标准设定)。 参数:P2010#4 HBPE螺距误差补偿值加到误差计数器中。 设定值:设定为0,表示为全闭环方式(标准设定)。 4.提高增益设定 在无振动的前提下,尽量提高位置环增益P1825,速度环增益P2043、P2045及负载惯量比P2021等参数。 游隙是滚动轴承能否正常工作的一个重要因素轴承的刚性,是指轴承产生单位变形所需力之大滚动轴承是一种精密的机械支承元件,轴承用户滚动轴承是一种精密的机械支承元件,轴承用户越南没有前段半导体晶圆厂,为了建立自有IC
840D螺距补偿步骤
1.螺距补偿 →Service →Manage Date →NC-active –date →Meas.-system-error-comp. →选择将要补偿的轴。 →Copy →光标到LIECHTI →Insert →打开补偿表 →输入补偿值 如X轴的补偿: CHANDATA(1) $AA_ENC_COMP[1,0,AX1]=0 $AA_ENC_COMP[1,1,AX1]=-0.00 $AA_ENC_COMP[1,2,AX1]=-0.001 $AA_ENC_COMP[1,3,AX1]=-0.003 $AA_ENC_COMP[1,4,AX1]=-0.004 $AA_ENC_COMP[1,5,AX1]=-0.007 $AA_ENC_COMP[1,6,AX1]=-0.009 $AA_ENC_COMP[1,7,AX1]=-0.011 $AA_ENC_COMP[1,8,AX1]=-0.012 $AA_ENC_COMP[1,9,AX1]=-0.014 $AA_ENC_COMP[1,10,AX1]=-0.017 $AA_ENC_COMP[1,11,AX1]=-0.016 $AA_ENC_COMP[1,12,AX1]=-0.018 $AA_ENC_COMP[1,13,AX1]=-0.019 $AA_ENC_COMP[1,14,AX1]=-0.023 $AA_ENC_COMP[1,15,AX1]=-0.026 $AA_ENC_COMP[1,16,AX1]=-0.028 $AA_ENC_COMP[1,17,AX1]=-0.029 $AA_ENC_COMP[1,18,AX1]=-0.029 $AA_ENC_COMP[1,19,AX1]=-0.032 $AA_ENC_COMP[1,20,AX1]=-0.034 $AA_ENC_COMP[1,21,AX1]=-0.037 $AA_ENC_COMP[1,22,AX1]=-0.037 $AA_ENC_COMP[1,23,AX1]=-0.039 $AA_ENC_COMP[1,24,AX1]=-0.042 $AA_ENC_COMP[1,25,AX1]=-0.046 $AA_ENC_COMP[1,26,AX1]=-0.049 . $AA_ENC_COMP_STEP[1,AX1]=56 $AA_ENC_COMP_MIN[1,AX1]=-171 $AA_ENC_COMP_MAX[1,AX1]=1285
西门子与fanuc螺距补偿
数控设备调试与维护 ----数控系统参数调整 一、实验的性质与任务 数控机床的性能在很大程度上是由系统软件的运行性能决定,在系统中对参数设置不同的值可以改变系统的运行状态。为了使数控机床运行良好,在数控机床生产过程中、生产完成以后都会根据机床以及系统的配置和测试性能对系统参数进行调试。通过该实验期望通过该实验对数控系统及其调试有更为深刻的了解。 二、实验的目的和要求 在完成实验过程中,熟悉数控系统参数手册的使用方法,了解数控系统的参数构成及其种类。通过完成参数调整实验的过程,以及观测参数调整完成后系统以及机床的运行性能,了解系统参数的变化对机床的影响。对学生的要求是: 1、养成安全、认真、踏实、严谨、一丝不苟的工作作风。 2、熟悉查阅数控系统参数手册的方法; 3、了解系统参数的体系架构; 4、掌握在数控系统中查找、修改参数的方法; 6、掌握方法; 7、撰写符合实验过程、内容的实验报告; 8、现场操作指导教师要求的实验内容; 三、预备知识 数控系统的参数体系是比较繁杂,参数种类比较多,我们在调整参数前必须对各系统参数有较为详细的了解。系统参数种类繁多,涉及到对系统的各个方面的调整。 在数控机床中,不管是那一种系统,参数按其不同功能土要有以下几种: 1.系统参数 这些参数一般由机床开发部制造商根据用户的选择进行设置,并有较高级别的密码保护,其中的参数设置对机床的功能有一定的限制,他其中的内容一般不容许用户修改。 2.用户参数 这是供用户在使用设备时自行设置的参数,内容以设备加工时所需要的各种要求为主,可随时根据用户使用的情况进行调整,如设置合理可提高设备的效率和加工精度。 2.通信参数 用以数据的输入/输出(i/o)转送。 3.PLC参数 设置PLC中容许用户修改的定时、计时、计数,刀具号及开通PLC中的一些控制功能。4.机械参数 有些也包括在用户参数内,主要以机床行程规格,原点位置,位置的测量方式,伺服轴、主轴调整,丝杆螺距、间隙补偿方面为主,特别是伺服,主轴控制参数,设置不当设备就不能正常工作并且造成机床精度达不到要求,甚至于机床不能使用。各种不同类型的数控系统,参数的分类方法不一定相同,有些虽不明显地进行分类,但总包含着以上的内容。正常情况下,数控机床的参数厂方一般已按要求调整设置,使用中,因操作不当误改,机床使用较长时间后部分机械的磨损,断电或电路板损坏引起参数丢失,电气参数的改变等因素都会造成
间隙补偿和螺距补偿
丝杠补偿一般指丝杠的螺距误差补偿. 间隙补偿包括所有传动链中的间隙(包括丝杆螺母付)的补偿. 由于丝杆螺距的不均匀性,传动链正,反向运动的间隙,都会直接影响数控精度,有些通改进运动付的结构,例如采用滚珠丝杆,使之正反向间隙得以消除,但螺距误差是避免不了的.所以必须进行补偿,以求较高的精度.同样,齿轮啮合需要间隙才能正常运行,这种累计间隙误差也需要通过补偿,才能提高 控制精度. 丝杆(丝杠)反向间隙又称丝杠背隙、丝杠间隙、丝杠失动量 在数控机床的进给传动链中.齿轮传动、滚珠丝杠:螺母副等均存在反向间隙,这种厦向间隙的存在会造成机床丁作台反向运动时,伺服电动机空转而工作台实际不运动。对于采用半闭环伺服系统的数控机球.反向问隙的存在会影响到机床的定位精度和重复定位精度,从而影响到产品的加工精度这就需要数挫系统提供反向间隙补偿功能,以便在加工过程中自动补偿一些有规律的误差,提高加工零件的精度。并且随着数控机床使用时删的增长,反向间隙还会因磨损造成的运动副间隙的增大而逐渐增加,因此需定期对数控机床各坐标轴的反向问隙进行测定和补偿。 1.反向间隙补偿过程 在数控系统无补偿的条件下,于机床测量行程范围内,在靠近行程的中点及两端的三个位置上分别进行多次测量,用千分表或百分表测量m各日标点位置P的平均反向间隙B.以所得平均值中的最大值为反向隙值B,并输人到数控系统反向间 隙补偿参数中。 CNC系统在控制坐标轴反向运动时,自动先让该标轴反向运动,然后再按指令进行运动.即数控系统会控制伺服电动机多走一段距离,这段距离等等于反向间隙值 B.从而补偿反向间隙。 需要指出的是这种方法只适合于半闭环数控系统.对于全闭环数控系统则不能采 取以上补偿办法。 2.反向间隙补偿方法 可使用激光干涉仪和百分表/千分表 百分表/千分表方法: 用手脉发生器移动相关轴,(将手脉倍率定为1×100的挡位,即每变化一步,电机进给0.1mm),配合百分表观察相关轴的运动情况。在单向运动精度保持正常后作为起始点的正向运动,手脉每变化一步,机床该轴运动的实际距离 d=d1=d2=d3…=0.1mm,说明电机运行良好,定位精度良好。而返回机床实际运动位移的变化上,可以分为四个阶段:①机床运动距离d1>d=0.1mm(斜率大于
FANUC0系统和三菱系统补偿方法和步骤
光动LICS-100激光多普勒激光干涉仪线性补偿方法及其步骤 1.Faunc0系统 测量前将原有反向间隙和螺距补偿都消去. ⑴反向间隙补偿 进入轴规格参数 将反向间隙〈B〉值填入相对应的轴的补偿地址: 进入反向间隙补偿地址backlash:输入对应轴的补偿值即可。(备注两端反向间隙,故补偿的 有两个数值) ⑵螺距误差补偿 通用:螺距补偿需要设置的参数有螺距补偿方式,补偿轴,参考点,补偿区间(即最负点和 最正点),补偿倍率,补偿节距。六大要素。 ① Faunc0系统只支持增量补偿,所以一开始无需要设置补偿方式 ②设置参考点在参数地址的[3620]处(Faunc系统的补偿点共计为0—1124个点,为 XYZ 轴所共用,所以我们可以为XYZ三个轴设定相应的有效区间,正常我们可设置0-100 号码,为X轴使用;100-200为Y轴使用;200以后为Z使用。所以对应轴的参考点地 址根据需要设置为相应区间的任意点)如图A-1所示。 图 A-1 ③设置相对应的补偿区间 地址3621和 3622 3621为设置补偿区间内的最负点 3622为设置补偿区间内的最正点 即例如:测量范围为-450---0则3621设置的补偿地址即为-450的补偿地址;3622则为0的 补偿地址。 附加:3620---3622的区间设置方法 例:测量Z轴由-450测量到0,节距为 25mm
Z轴补偿区间我们假设为200以后,假设参考点为309。 则3620处填 309 3621最负处的地址为参考点-(测量长度/节距)+1=309-18+1=292即3621处填写 292 3621最正处填写参考点地址+1的地址数,即310。 这样参考点和补偿地址都设置好了。如图 A-2 图 A-2 ④3623 为倍率。Faunc 系统相对补偿参数限制为0——±7,所以倍率为 1 的情况下,如误 差中有很多的+7或者-7的话说明实际补偿误差可能大于这个数值,(例如:误差可能大于± 7,比如误差有8,10,-9那它也只能显示到7,7,-7,)那这个时候我们就要改倍率为2。 数值才会比较精确。 ④ 3624为设置测量时候实际的节距 例测量-450——0,每段测量25mm,则3624处设置为25000(大部分数控机床的设置单位基数为0.001mm如图 A-3
13、螺距误差补偿及反向间隙补偿
螺距误差补偿及反向间隙补偿 根据下表设置螺距误差补偿相关参数: 参数号参数位设定值设置说明 3620 X Z 100 200 每个轴的参考点的螺 距误差补偿点号 3621 X Z 负方向最远的补偿位置号根据下面的公式进行计算: 参考点的补偿位置号—(负方向的机床行程/补偿位置间隔)+ 1 100-(1000/50)+1=81 所以负方向补偿位置号设置为81 3622 X Z 正方向的最远补偿位置号根据下面的公式进行计算: 参考点的补偿位置号+(正方向的机床行程/补偿位置间隔)+ 1 100+(0/50)+1=101 所以参考点正方向补偿位置号为101. 3624 补偿点间隔输入格式 为无小数点输入格 式,由于X轴为直径 值编程,所以X轴补 偿点间隔应为实际补 偿点间隔的2倍,应 设置为100000,为 100mm. 参数号参数位设定值设置说明 1800 #4(RBK) 是否分别进行切削进 给/快速移动反向间 隙补偿 0: 不进行。 1: 进行。 1851 X Z 每个轴的反向间隙补偿量,设置后,回零
生效 1852 X Z 每个轴的快速移动时的反向间隙补偿量,回零生效 由于FANUC系统螺距误差补偿采用增量式的补偿方式,所以在进行螺距误差补偿时,需根据补偿数据进行补偿数据的设定个。 下表为螺距误差补偿表 由于每个补偿点的最大补偿值只能到7,在上表中可以看到,在-400mm测量位置处出现了一次22的值,此点是所有补偿点误差的最大值,所以补偿倍率按此点进行计算,而且考虑其它点的误差值,将补偿倍率设置为3倍。 补偿倍率设置为3倍,所有的补偿值都放大了三倍,所以在补偿数据处看到的是计算值的1/3,如果测量人员给出的是补偿值,那么补偿数据就按上图中的数据进行输入,如果给出的
840D系统补偿功能汇总
840D系统补偿功能汇总 数控机床的的几何精度,定位精度一方面受到机械加工母机的精度限制,另一方面更受到机床的材料和机械安装工艺的限制,往往不能够达到设计精度要求。而要在以上诸多方面来提高数控机床的几何精度,定位精度需要投入大量的人力物力。在机械很难提高精度的情况下,通过数控电气补偿能够使数控机床达到设计精度。 一、反向间隙补偿 机床反向间隙误差是指由于机床传动链中机械间隙的存在,机床执行件在运动过程中,从正向运动变为反向运动时,执行件的运动量与目标值存在的误差,最后反映为叠加至工件上的加工精度。 机床反向间隙是机床传动链中各传动单元的间隙综合,如电机与联轴器的间隙,齿轮箱中齿轮间隙,齿轮与齿条间隙,滚珠丝杠螺母副与机床运动部件贴合面的间隙等等。 反向间隙直接影响到数控机床的定位精度和重复定位精度。在半闭环下,由伺服电机编码器作为位置环反馈信号。机械间隙无法由编码器检测到,在机械调整到最佳状态下需要进行反向间隙补偿。在全闭环下,直线轴一般采用光栅尺作为位置环反馈信号,旋转轴一般采用外接编码器或圆光栅作为位置环反馈信号。由于是直接检测运动部件的实际位移,理论上讲全闭环下无反向间隙。但是由于光栅尺或圆光栅本身精度的限制和安装工艺的限制等等,使得全闭环下也具有“反向间隙”,这在激光干涉仪下能很明显看出来,一般在0.01mm
左右。 西门子840D数控系统反向间隙补偿的方法如下: 测得反向间隙值后在轴机床数据输入反向差值,单位为mm。 MD32450 BACKLASH [0] MD32450 BACKLASH [1] 其中[0]为半闭环,[1]为全闭环。输入后按下Reset键,回参考点后补偿生效。可以在诊断→服务显示→轴调整→绝对补偿值测量系统中看到补偿效果。 反向间隙补偿能够在较大程度上提高数控机床的定位精度、重复定位精度,但是它的值是固定的,不能适用于机床的整个行程,这就需要另一种电气补偿手段,螺距误差补偿。两者结合能使数控机床达到较高的定位精度和重复定位精度。 二、螺距误差补偿 重型数控机床的传动机构,一般为滚珠丝杠传动或齿轮齿条传动。受到制造精度的影响丝杠上的螺距和齿条齿轮的齿距都有微小的误差,对于半闭环数控机床,这将直接影响其定位精度与重复定位精度。而对于全闭环,由于受到光栅尺自身的精度,光栅尺安装的直线度、挠度的影响也会产生“螺距误差”。 西门子840D数控系统螺距误差补偿原理如下图所示:
840D螺距补偿
840D螺距补偿 1.修改轴参数,设定各轴补偿点数量。 a)设定坐标轴补偿点数量 依次按“Menu Select”—〉“启动”—〉“机床数据”—〉“轴MD”,找到MD38000(用于差补补偿的中间点数量),设置补偿点的数量,本例中为:50。然后按“Input” 键,此时出现4400报警“机床数据修改将导致缓冲存储器的重新组织(数据丢失)”。 请勿NCK重启,作下一步备份NC数据。 b)备份NC数据 依次按“Menu Select”—〉“服务”—〉“”—〉“连续启动”,出现下图。
在文档内容中选择“NC”和“带补偿数据”;输入文件名称,一定要按“Input”键,否则文件名无效。本例中为:NC_COMP01;按“文档”键,开始创建连续启动文档,如下图所示。 c)恢复数据 待连续启动文档创建好后,按“读入调试文档”键。
选择刚才创建的连续启动文档NC_COMP01,按“启动”键,并点击“是”加以确认。此后系统会重启几次。 2.导出补偿数据,生成ARC文件或MPF程序(参见补充说明) 因为补偿文件不能直接修改,只能输出成ARC文件。下面以给轴1添加螺补为例说明。 依次按“Menu Select”—〉“服务”—〉“数据选择”,选择“NC-生效-数据”,按“确认”键。
在数据输出窗口的树形图中选择“NC-生效-数据”—〉“测量系统误差补偿”—〉“测量系统错误补偿—轴1”,按“文档”键。 出现下图。输入文档名,本例中为:AX1_EEC。选择文档格式,必须为:带CR+LF穿孔带,否则无法编辑。按启动键。
3.输入补偿数据,编辑ARC文件。 PCU50可直接编辑ARC文件。PCU20可将ARC文件通过RS232传出,使用文本编辑器编辑。也可制作补偿程序,见第7条的补偿说明。 PCU50操作如下: 在树形图中选择“文档”—〉“AX1_EEC”,按“Input”键打开文件。 补偿文件结构如下: $AA_ENC_COMP[0, 0, AX1]=0.5 对应于最小位置上的误差值 $AA_ENC_COMP[0, 1, AX1]=0.2 对应于最小位置+1个间隔位置上的误差值 $AA_ENC_COMP[0, 2, AX1]=-0.5 对应于最小位置+2个间隔位置上的误差值 … … $AA_ENC_COMP[0, 48, AX1]=0 对应于最小位置+48个间隔位置上的误差值 $AA_ENC_COMP[0, 49, AX1]=0 对应于最小位置+49个间隔位置上的误差值 $AA_ENC_COMP_STEP[0, AX1]=10 测量间隔(毫米) $AA_ENC_COMP_MIN[0, AX1]=0 最小位置(绝对) $AA_ENC_COMP_MAX[0, AX1]=100 最大位置(绝对) $AA_ENC_COMP_IS_MODULO[0, AX1]=0 用于旋转轴 修改文件后,保存并关闭编辑器。 4.补偿数据ARC文件导入NC系统。 设定MD32700=0,并且按“设MD有效”按钮,使参数生效,这样ARC文件才能写入补偿文件。 依次按“Menu Select”—〉“服务”—〉“”—〉“连续启动”—〉“读入调试文档”,选择修改好的AX1_EEC文件,按“启动”按钮。
螺距误差补偿
螺距误差补偿 螺补有关的参数: MD32450MA_BACKLASH[ ] (轴反向间隙补偿) MD32700MA_ENC_COMP_ENABLE[ ] = 0 可以写补偿值 = 1 补偿文件写保护MD38000MA_MM_ENC_COMP_MAX_POINTA[ ](轴螺补补偿点数) 螺补的步骤(以X轴为例): 1参数MD38000,按照X轴的全行程以及步长必须小于150mm的规则确定要补偿的点数(最好是一次确定并更改所有需要螺补轴的补偿点数)。更改完此参数后会出现一个报警4000,此时不要做NCK Reset,此时应该做NC备份。备份完后作POWER ON。 2在“Programe”(程序)中“Workpiece Programe(工件程序)”拷入各个轴的螺补程序LBX,LBY,LBZ等。 3在Service(服务)中找寻Data selection,在打开的界面中选择NC_active_data,回到data manage(数据管理)中打开NC_active_data,会出现meas.system_error_comp目录,再打开此目录会出现几个子目录:meas.system_error_comp_axis1(axis2,Axis3,axis4,……),点击axis1,按copy出现一个面板,将axis1复制到LB中,回到“workpiece(工件)”的LB 中,将出现AX1—EEC程序,此程序就是X轴的数据补偿程序。其他轴同理。 4在对机床进行螺补之前,应先走一遍所测轴全程,确定所测轴的全程间隙,如果过大需要调整光栅钢带的长度,使得所测轴全程激光测得的数与显示屏显示的数相差范围在0.02mm以下。 5设置MD32700= 0,将X轴以LBX的程序运行一遍(注意要设置好LBX里的步长,全长等数据),将激光测试出的各个点的误差及反向间隙数据采集下来。把各个点的误差数据以及程序的步长,最大和最小点一次写入AX1—EEC程序(注意不要改变数据的正负号),将反向间隙写入MD32450。 6在auto方式下选择AX1—EEC程序,并执行此程序。将MD32700设置为1,按“MD 参数生效”,作一次复位,使补偿值生效。再执行LBX程序,再检验X轴精度是否合格。 7如果精度检验不合格,可能有以下几种情况: ⑴定位精度不合格。需要分析一下激光曲线,具体看是否有地方出现较大拐点等, 要检查钢带外壳的直线度并调整,最好控制在0.05mm以内,重复E,F步骤, 再次补偿。 ⑵重复精度不合格。这个问题就比较复杂,对于螺补数据几乎不可能,因为它完 全来源于机械的安装,只能寄希望于机械的安装精度合格了。也许唯一能解点
ACS螺距补偿手册
Dynamic Error Compensation Application Note August2014 Document Revision:1.0
Dynamic Error Compensation Release Date:August2014 Copyright ?ACS Motion Control Ltd.2014.All rights reserved. Changes are periodically made to the information in this document.Changes are published as release notes and later incorporated into revisions of this document. No part of this document may be reproduced in any form without prior written permission from ACS Motion Control. Trademarks ACS Motion Control,SPiiPlus,PEG,MARK,ServoBoost,MotionBoost,NetworkBoost and NanoPWN are trademarks of ACS Motion Control Ltd. Windows and Visual Basic are trademarks of Microsoft Corporation. EtherCAT is registered trademark and patented technology,licensed by Beckhoff Automation GmbH,Germany. Any other companies and product names mentioned herein may be the trademarks of their respective owners. https://www.360docs.net/doc/5f16725072.html, support@https://www.360docs.net/doc/5f16725072.html, sales@https://www.360docs.net/doc/5f16725072.html, Notice The information in this document is deemed to be correct at the time of publishing.ACS Motion Control reserves the right to change specifications without notice.ACS Motion Control is not responsible for incidental,consequential,or special damages of any kind in connection with using this document. Revision History Date Revision Description August201401First release
采用间隙误差补偿与螺距误差补偿改善机床最终数控精度_刘西京
采用间隙误差补偿与螺距误差补偿 改善机床最终数控精度 刘西京 (陕西东风昌河车桥股份有限公司,陕西铜川 727000) 摘 要:采用间隙误差补偿与螺距误差补偿的方法,改善机床最终数控精度并介绍了具体应用过程。关键词:间隙误差补偿;螺距误差补偿;机床最终数控精度 中图分类号:TH161+.4 文献标识码:B 文章编号:1007-4414(2001)03-0006-02 加工中心机床是集钻,镗,铣加工功能为一体,具有自动换刀装置的数控设备,各项精度要求十分严 格,特别是对坐标轴定位精度与重复定位精度的要求非常高,如TH6350型机床,对三坐标定位精度的要求是每300mm 长上允差为+0.01mm ,全行程上允差不超过0.04mm ,而对此三坐标重复定位精度的要求不超过+0.005mm 。采用FANUC -OMC 系统可快速定位,伺服电机经联轴节带动滚珠丝杠转动,可获得10m /min 速度,定位精度高,机床进给振动小,低速无爬行,具有较高的稳定性。 影响机床坐标定位与重复定位精度的因素有螺距误差与间隙误差,对于刚性的丝杠系统来说,螺距误差来自丝杠本身制造精度引起的螺距不等。对于同一方向定位的各定位点来说,由于不存在间隙误差的影响,因此它们之间的定位误差可以很好的反映螺距误差。反向间隙误差则来自丝杠与丝杠副之间,轴承与轴承座之间的空隙。丝杠向其相反方向运动时,此空隙会造成一段空运转,这时丝杠转动,但工作台不动,此种情况下产生的误差称为反向间隙误差,此反向定位误差值即被认为是该点的间隙误差。 传动部件与运动部件具有一定的弹性,完全刚性的物质是理想化的。因此在外力的作用下会发生弹性形变,运行中的丝杠受弹性形变影响很大,它所造成的误差是其与反向间隙的总和,与丝杠受力有关,运动过程中阻力大的地方弹性间隙也大,如丝杠定位不好,导轨变形不均匀或压板配合不紧凑,都会导致在运动全程上丝杠受力不均匀,导致弹性间隙在全程上分布变化大,使精度受影响。 所以当机床定位精度与重复定位精度不好时,可以在消除机械上的因素之后采用螺距误差补偿和间隙误差补偿的方式改善机床精度,由于加工中心采用 高科技的数控系统来驱动电机带动机床运动,系统本身具有的功能可以进行自动补偿。 如前所述,由于丝杠存在着反向间隙误差,因此在其运动换向时利用数控系统让电机多转几转,以带动丝杠多走一个补偿值来弥补丝杠反向时间隙产生的一段空程,因此我们可以用读数显微镜—刻度尺法进行间隙补偿,用读数显微镜进行观测刻线,并通过显微镜中的游标记录下该刻线的位置。由于相邻两刻线的间距是0.1mm ,故当刻线尺沿与尺平行的方向移动整数毫米后,另一条刻线将移动到和被记录下的刻线的同一位置上。如果运动有误差,则可以通过读数显微镜测出。读数值和误差方向之间的关系与显微镜的放置方法有关,可以通过以下方法判断:由于显微镜成倒像,故此机床运动方向。显微镜读数分辨率为1μm 即0.001mm ,游标卡尺每格之间距离为0.1mm 。图1(a )表示游标卡尺和读数显微镜都在中间位置,测量点0mm 处定位偏差读数应看显微镜刻度盘值即50,图1(b )表示测量点150mm 处定位偏差值相对0mm 处少走了一端距离例如15,此时转动显微镜刻度盘将游标卡尺刻线与显微镜中线重合,这时150mm 处定位偏差值的数值应为转动显微镜刻度盘后读数值即50-15=35,图1(c )表示测量点300m m 处定位偏差值相对0mm 处多走了一端距离例如15, 此时转动显微镜刻度盘将游标卡尺刻线与显微镜中线重合,这时300mm 处定位偏差值的数值应为转动显微镜刻度盘后读数值即50+15=65,下面介绍差值超过0.1mm 时显微镜的读数方法,如图2(假设游标卡尺和显微镜刻度盘读数都在中间位置) 用这种方法无法测量1mm 以上的误差,另外安装刻线尺显微镜必须保证:①运动方向和刻线尺平行。②显微镜光路与刻线尺垂直。③游标轴线与刻 · 6· 收稿日期:2001-02-05 作者简介:刘西京(1965-),男,工程师,1989年毕业于陕西机械学院工业电气自动化专业,长期从事数控机床维修与改造工作。
FANUC数控系统螺距误差补偿功能.
FANUC数控系统螺距误差补偿功能数控机床的直线轴精度表现在轴进给上主要由三项精度:反向间隙、定位精度和重复定位精度,其中反向间隙、重复定位精度可以通过机械装置的调整来实现,而定位精度在很大程度上取决于直线轴传动链中滚珠丝杠的螺距制造精度。在数控机床生产制造及加工应用中,在调整好机床反向间隙、重复定位精度后,要减小定位误差,用数控系统的螺距误差螺距补偿功能是最节约成本且直接有效的方法。 FANUC数控系统已广泛应用在数控机床上,其螺距误差补偿功能有一定的典型性。螺距补偿原理是将机械参考点返回后的位置作为螺距补偿原点,CNC系统以设定在螺距误差补偿参数中的螺距补偿量和CNC移动指令,综合控制伺服轴的移动量,补偿丝杠的螺距误差。 1 螺距误差补偿前的准备工作回参考点后,编程控制需要螺距误差补偿的轴,从参考点或机床机械位置某一点间歇移动若干个等距检测点,用激光干涉仪等检测计量仪器检测出各点的定位误差。检测点数量可根据机床的工作长度自设。 2 设定螺距误差补偿参数 打开参数开关在MDI方式下设置参数PWE=1,系统出现1000报警,同时按CAN和RESET键清除报警。 ⑴参考点的螺距误差补偿点号码参数X轴参数No.1000Z轴参数No.2000 ⑵螺距误差补偿倍率参数参数No.0011的PML1,PML2。.PML2 PML1 倍率( 0 0 31,0 1 32, 1 0 34,1 1 38)设定的螺距补偿值,乘上该倍率,即为输出值. ⑶螺距误差补偿点间隔X轴参数No.756Z轴参数No.757螺距误差补偿点为等间隔,设定范围从0到999999999。一般设定单位是0.001毫米。⑷螺距补偿点数目各轴从0到127共128个螺距补偿点 ⑸螺距补偿量及螺距补偿点的号X轴参数No.(1001+螺距补偿点号)Z轴参数No.(2001+螺距补偿点号)每个螺距补偿点螺距补偿量的范围为(-7)~(+7)乘以螺距补偿倍率。负侧最远补偿点的号=原点补偿点-(负侧的机床长/补偿点间隔)+1正侧最远补偿点的号=原点补偿点+(正侧的机床长/补偿点间隔) 3设定好螺距补偿参数后,在MDI方式下,设置参数PWE=0,关闭参数写状态。机床断电后重新启动,回参考点,螺距补偿生效。再检测定位精度,没达到要求的补偿点可反复修改补偿量,直至达到要求。 4 应用举例 数控车床的参考点一般设在机械正限位不到处,参考点与正限位之间的范围在加工工件时很少用到,下面以一台数控车床的Z轴丝杠精度检测结果,阐述螺距误差补偿如何应用。 编程后运行,检测Z轴移动点,每点来回检测
螺距误差测定及补偿 电子教材
螺距误差测定及补偿 任务内容 螺距误差补偿原理 VDF850加工中心螺距误差补偿 数控机床以其高效高精度,正在机械制造企业中广泛应用。目前数控机床的传动机构一般采用传动精度较高的滚珠丝杠,滚珠丝杠在生产制造时由于加工设备的精度和加工条件的变化,丝杠和螺母之间存在着误差,如螺距的轴向误差、螺纹滚道的形状误差、直径误差等。滚珠丝杠在数控机床上进行装配时,由于采用双支撑结构,使丝杠工作载荷较大时轴向尺寸发生变化造成其螺距误差增大。滚珠丝杠产生的传动误差在全闭环数控机床中由于检测原件(如光栅尺)检测的是机床运动部件的实际位移,将不会对机床加工精度造成影响;而对于工厂中大量使用的半闭环数控机床而言,丝杠、齿形带等机械传动造成的误差不在反馈原件检测范围内,因此若不对此类误差进行适当修正和补偿,势必影响数控机床的定位精度,造成加工质量的不稳定。要得到高的运动精度和良好的加工质量,必须采用螺距误差补偿功能,精确测量出丝杠不同位置的误差值,利用数控系统对螺距误差进行自动补偿与修正[1]。另外,数控机床经过长期使用,由于丝杠磨损,运动精度也会下降。采用该功能定期检测与补偿,可以延长数控机床的使用寿命,保证加工精度。 一、螺距误差补偿原理 螺距误差补偿的基本原理是在某进给轴上利用高精度位置检测仪器所测良出的位置(可作为理论位置用)与机床实际运动位置进行比较,计算出该轴全行程上的误差曲线,并将不同位置的误差值输入数控系统中。机床在经过补偿的轴上运动时,数控系统会根据该位置的补偿数据,自动对该轴的不同位置进行误差补偿,从而减小或消除该轴该位置的定位误差。 螺距误差补偿分单向和双向补偿两种,单向补偿为补偿轴正反向移动时采用相同的数据补偿;而双向补偿为进给轴正反移动时采用不同的数据进行补偿。由于数控机床丝杠装配时有多种反向间隙消减措施,而且大部分数控机床除了能够进行螺距误差补偿外,还可以进行反向间隙补偿,所以通常仅采用单向螺距误差补偿。 进行螺距误差补偿时应该注意的几个问题: (1)螺距误差补偿仅对定位精度进行补偿,而对重复定位精度无法补偿,而且对于重复定位精度较低的运动轴,由于无法准确确定某点位置误差,因此螺距误差补偿将不会起到预期目的。 (2)进给轴上螺距误差值是以机床坐标系为参照确定其测量位置的,机床坐标原点不能丢失,否则所测量的误差值将失去意义。因此对于使用绝对脉冲编码器的伺服系统,一定要保证编码器电池的供电,否则会因为电池亏电而丢失参考点,从而丢失机床坐标原点。重新建立参考点后的机床一定要重新进行螺距误差补偿。
如何通过反向间隙补偿、螺距补偿提升机床精度
【二】如何通过反向间隙补偿、螺距补偿提升机床精度 数控机床设备生产效率的好坏与精度有很大的关系,因此企业在购买或研发数控机床时都十分看重这一点。然而,绝大部分的新机床在刚出厂时,精度都不够标准,或者后期使用过程中出现机械磨合磨损的现象,所以调校数控机床的精度对日后生产工作的开展是非常关键的。 一、反向间隙补偿 在数控机床上,由于各坐标轴进给传动链上驱动部件的反向死区、各机械运动传动副的反向间隙等误差的存在,造成各坐标轴在由正向运动转为反向运动时形成反向偏差,通常也称反向间隙或失动量。对于采用半闭环伺服系统的数控机床,反向偏差的存在就会影响到机床的定位精度和重复定位精度,从而影响产品的加工精度。同时,随着设备投入运行时间的增长,反向偏差还会随因磨损造成运动副间隙的逐渐增大而增加,因此需要定期对机床各坐标轴的反向偏差进行测定和补偿。 【反向间隙的测定】 反向偏差的测定方法:在所测量坐标轴的行程内,预先向正向或反向移动一个距离并以此停止位置为基准,再在同一方向给予一定移动指令值,使之移动一段距离,然后再往相反方向移动相同的距离,
测量停止位置与基准位置之差。在靠近行程的中点及两端的三个位置分别进行多次测定(一般为七次),求出各个位置上的平均值,以所得平均值中的最大值为反向偏差测量值。在测量时一定要先移动一段距离,否则不能得到正确的反向偏差值。 测量直线运动轴的反向偏差时,测量工具通常采有千分表或百分表,若条件允许,可使用双频激光干涉仪进行测量。当采用千分表或百分表进行测量时,需要注意的是表座和表杆不要伸出过高过长,因为测量时由于悬臂较长,表座易受力移动,造成计数不准,补偿值也就不真实了。若采用编程法实现测量,则能使测量过程变得更便捷更精确。 例如,在三坐标立式机床上测量X轴的反向偏差,可先将表压住主轴的圆柱表面,然后运行如下程序进行测量: N10G91G01X50F1000;工作台右移 N20X-50;工作台左移,消除传动间隙 N30G04X5;暂停以便观察 N40Z50;Z轴抬高让开 N50X-50:工作台左移 N60X50:工作台右移复位 N70Z-50:Z轴复位 N80G04X5:暂停以便观察 N90M99; 需要注意的是,在工作台不同的运行速度下所测出的结果会有所