水泥厂立磨ATOX50_立磨系统的运行

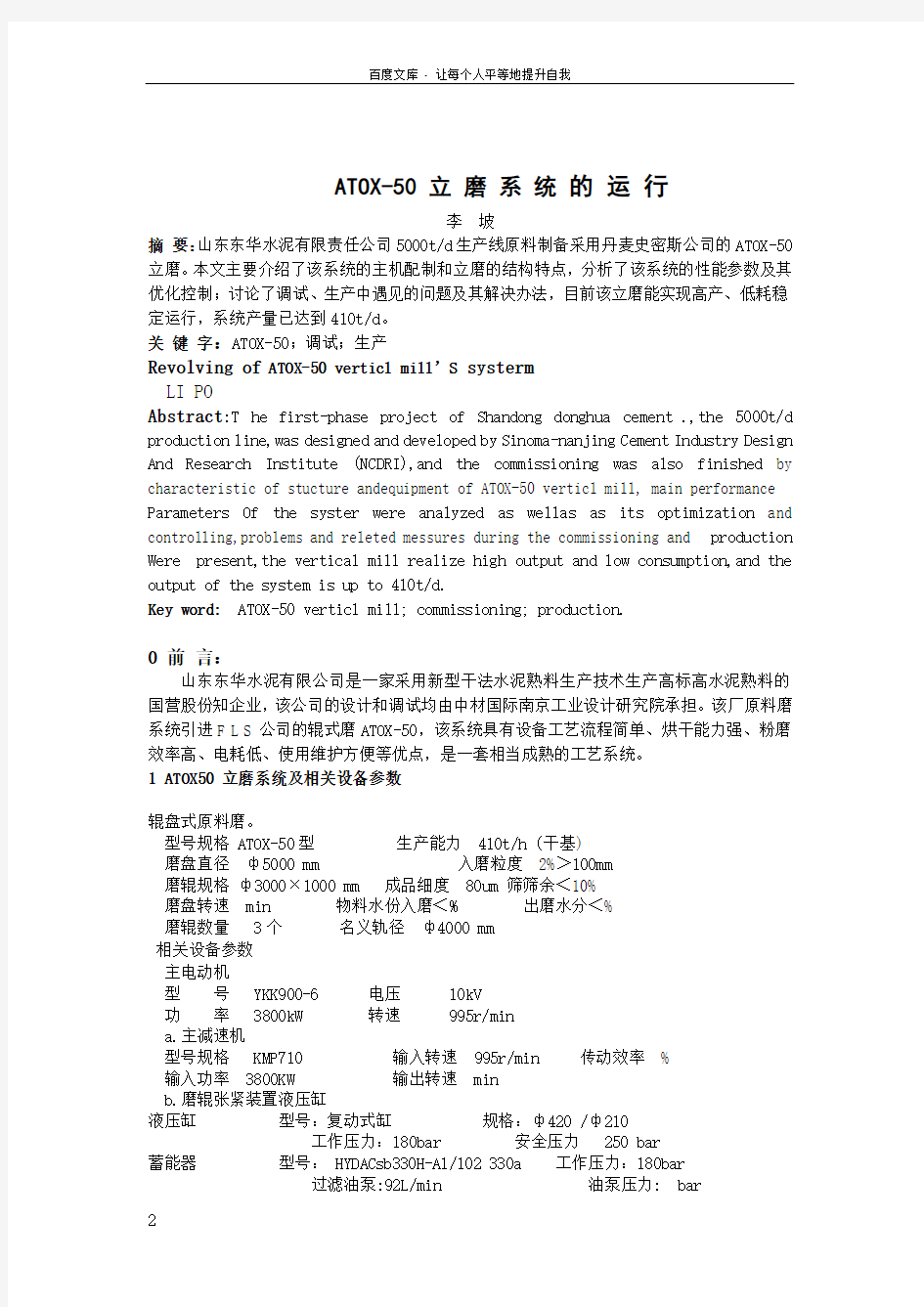
目录
0前言 (1)
1 ATOX-50 立磨系统及相关设备参数 (1)
辊盘式原料磨 (1)
相关设备参数 (2)
结构设计特点 (3)
工作原理 (3)
2运行中工艺参数控制及其调节 (3)
立磨系统的参数 (3)
磨内通风量 (3)
料层厚度 (4)
振动值 (4)
研磨压力 (5)
压差 (6)
磨机出口温度 (6)
产品细度 (7)
系统参数控制 (7)
控制要点 (8)
运行过程中的调节 (8)
立磨系统三大稀油站控制 (8)
主减速机稀油站 (8)
磨辊稀油站 (8)
液压系统 (9)
3调试与生产 (9)
调试 (9)
无负荷试车 (10)
负荷试车 (12)
开车顺序 (12)
停车 (12)
停车注意事项 (13)
故障停车 (13)
紧急停车 (13)
4 生产中常见的问题及解决措施 (13)
常见的问题及解决措施 (14)
磨机运行中异常情况分析及处理 (15)
5 结语 (15)
6 参考文献 (16)
7 致谢 (16)
ATOX-50 立磨系统的运行
李坡
摘要:山东东华水泥有限责任公司5000t/d生产线原料制备采用丹麦史密斯公司的ATOX-50立磨。本文主要介绍了该系统的主机配制和立磨的结构特点,分析了该系统的性能参数及其优化控制;讨论了调试、生产中遇见的问题及其解决办法,目前该立磨能实现高产、低耗稳定运行,系统产量已达到410t/d。
关键字:ATOX-50;调试;生产
Revolving of ATOX-50 verticl mill’S systerm
LI PO
Abstract:T he first-phase project of Shandong donghua cement .,the 5000t/d production line,was designed and developed by Sinoma-nanjing Cement Industry Design And Research Institute (NCDRI),and the commissioning was also finished by characteristic of stucture andequipment of ATOX-50 verticl mill, main performance Parameters Of the syster were analyzed as wellas as its optimization and controlling,problems and releted messures during the commissioning and production Were present,the vertical mill realize high-output and low-consumption,and the output of the system is up to 410t/d.
Key word: ATOX-50 verticl mill; commissioning; production.
0 前言:
山东东华水泥有限公司是一家采用新型干法水泥熟料生产技术生产高标高水泥熟料的国营股份知企业,该公司的设计和调试均由中材国际南京工业设计研究院承担。该厂原料磨系统引进F L S公司的辊式磨ATOX-50,该系统具有设备工艺流程简单、烘干能力强、粉磨效率高、电耗低、使用维护方便等优点,是一套相当成熟的工艺系统。
1 ATOX50 立磨系统及相关设备参数
辊盘式原料磨。
型号规格 ATOX-50型生产能力 410t/h (干基)
磨盘直径ф5000 mm 入磨粒度 2%>100mm
磨辊规格ф3000×1000 mm 成品细度 80um 筛筛余<10%
磨盘转速 min 物料水份入磨<% 出磨水分<%
磨辊数量 3个名义轨径ф4000 mm
相关设备参数
主电动机
型号 YKK900-6 电压 10kV
功率 3800kW 转速 995r/min
a.主减速机
型号规格 KMP710 输入转速 995r/min 传动效率 %
输入功率 3800KW 输出转速 min
b.磨辊张紧装置液压缸
液压缸型号:复动式缸规格:ф420 /ф210
工作压力:180bar 安全压力 250 bar
蓄能器型号: HYDACsb330H-A1/102 330a 工作压力:180bar
过滤油泵:92L/min 油泵压力: bar
油泵电机功率压力泵电机功率 37KW
冷却方式:水冷却冷却水压2-6 bar
冷却水用量h
c.磨辊润滑系统
油箱容积:1000L 润滑方式:循环油系统
冷却方式:水冷却冷却水压2-6 bar
冷却水用量h
d.回转锁风阀(4104)
规格:ф2000mm 允许物料通过量:769t/h 允许物料含水分:%
允许漏风量: 15700m3/h 压缩空气消耗量 min
压缩空气压力: 驱动电机功率 15KW
e.立磨喷水系统
正常喷水量:根据磨床的稳定程度。最大喷水量:21 m3/h
喷水量调节范围:0-21 m3/h 喷水压力:10bar
水泵电机型号:CR16-100 电机功率:11KW
控制阀电机型号:ST-53 电机功率:
f.磨机选粉机
型号:RAR-LV50 转子直径:ф5680mm 分离效率:85-90%
转子调速范围:45-90r/min 调速方式:变频调速
驱动电机功率:204KW 转速范围:1100-2600r/min
润滑油系统油泵电机功率:4KW
g.密封风机
型号:MPF-50 风量2200-4000 m3/h 风压: bar
电动机功率:
结构设计特点
3个磨辊有一个刚性的连接块连接在一起,每个磨辊的外端连接一根扭力杆,扭力杆通过橡胶缓冲装置中心固定在磨机壳体上。调整3根扭力杆的长度可以对磨辊进行精确定位,是3个磨辊的中心与磨盘中心相重合。每个磨辊的轴端均与一个双向液压缸相连,用以将磨辊压向磨盘,调节粉磨力,或者将磨辊抬起,脱离磨盘以利磨机空载启动
磨辊依靠本身的重力放置在磨盘上,只做上下运动,只受垂直方向力(不受轴向力),磨辊外套的磨损均匀。磨辊的直径比其他立磨大,对料层变化以及喂料大块(100~150mm),异物的适应强。磨辊为空心结构,质量小,刚性好,内部可装大型重载轴承,磨辊外套分层弧新形片状,可避免高硬度脆性合金材料,因残余应力热处理应力和热胀冷缩应力而引起开裂。磨辊采用稀油循环润滑,可对润滑油量油压和油温进行控制,润滑效果好确保磨辊轴承始终处于最佳润滑状态。润滑油采用在线过滤,确保不被污染。轴承腔双唇边油封,采用正压保护。
磨盘呈水平,磨辊为垂直状,粉末区为一平面,磨辊系统的重心在磨盘上只有垂直方向上的运动,所有的冲击力和压力都是垂直方向上的,易于处理。
三辊一体的磨辊悬浮系统和其他形式相比具有质量小,惯性小。所需动力小,运动平稳的优点,3个辊轴内端为刚性连接,但轴外端分别与液压缸相连,某一辊的运动相对另外两辊的影响很小,仅为2%。各辊的上下运动基本互不影响。
磨辊轴线与磨盘直径之间有一夹角使磨辊轴承只受圆周方向的力,无轴向推力,振动小,利于轴承负载和寿命。
采用双向液压缸启动前可将磨辊顶起,空载启动,不需辅助传动装置,待喂入一定物料料层厚度触及磨辊时液压缸向另一方向施压,逐渐转入粉末作业,磨机启动简单平稳。正常运行与到金属异物时,磨辊会自动抬起,保护设备。
工作原理
辊式磨与球磨相比在粉磨机理上有明显的区别,它是借助磨辊和磨盘的相对运动为碾磨装置来粉磨物料的机械。当物料处于立磨装置的作业区时,大块物料被压碎,细物料受压后形成一层料床,颗粒之间相互摩擦、剪切使棱角和边缘剥落而被粉碎,因此它属于料床粉磨。在粉磨的同时,通过风环进入磨内的热气体对含水份的物料进行烘干。它又属于风扫式磨,以一定速度上升的气体,将已被粉碎的物料经回转式选粉机选粉后,合格的细粉随气流排出磨外,而被分离的粗粉则重新回落到磨盘上进行再粉磨。物料的颗粒在此作往复运动,每分钟达到20~30次之多,因此,ATOX50型原料立磨的粉磨效率比较高。未经辊子粉碎或未被粉碎成小颗粒的物料,被磨盘甩到固定在磨机壳体的风环处,以高达60~70m/s以上速度通过风环的热气体将这部分物料吹回到磨盘上进行再粉磨。就这样物料被反复粉磨、烘干直至达到成品细度要求,随气体出磨,在旋风筒和系统的收尘装置中收集下来。
2运行中工艺参数控制及其调节
立磨系统的参数
磨内通风量:
辊式磨也是一种风扫磨,通风量要适当。风量不足,合格的生料不能及时带出,料层增厚,排渣量增多,设备负荷高,产量降低;风量过大,料层过薄,影响磨机稳定运转。
因此,磨机通风量一定与产量相匹配,不宜时大时小,应保持稳定。原则上,操作员选择的通风量,应以更有利于保持磨机负荷相对稳定为准,并力求振动最小,排渣料最少,产量最高,质量最好。在实际操作中,操作员根据风机转速、电流、压差、喂料量、进出口负压、温度等变量的趋势图,了解磨机运行情况,并结合磨机振动、排渣量、产品质量等进行调整,一般是通过调整循环风机的速度和挡板的开度以求达到最佳通风量。
正常情况下,整个工作稳定,各趋势图也显示平稳,一旦其中某个变量变化,很快就会影响其他变量的变化。此时,要及时做出相应调整,否则就可能出现磨机振停的情况。有些振停纯属疏忽或经验不足所致,如:减料时不减风,加料时不加风等,都可能引起压差异常变化,使磨机失控振停。
料层厚度:
立磨稳定运转的另一重要因素是料床稳定。料层稳定,风量、风压和喂料量才能稳定,否则就要通过调节风量和喂料量来维持料层厚度。若调节不及时就会引起震动加剧,电机负荷上升或系统跳停等问题。理论上讲,料层厚度应为磨辊直径的2%±20mm,该立磨磨辊直径为3000mm,因此60±20mm是适宜的料层厚度。这就要求操作员密切注意料层趋势的变化,尽量控制在最佳的范围内,以保证磨机稳定运转。此外,料层厚度还取决于原料粒度、易磨性、颗粒分布、含水量等。运转初期,为了找到最佳的料层厚度,得调试挡料圈的高度。而在挡料圈高度一定的条件下,稳定料层厚度的重要条件之一是喂料粒度及粒度级配合理。喂料平均粒径太小或细粉太多,料层将变薄;平均粒径太大或大块物料太多时料层将变厚,磨机负荷上升。可通过调节喷水量、研磨压力、循环风量和选粉机转速等参数来加以控制。振动值:
振动是辊式磨机工作中普遍存在的一个现象,合理的振动是允许的,但若振动过大,则会造成磨盘和磨辊以及衬板的机械损坏。所以在操作过程中应当严格将振动值控制在允许范围内(最好在s以下),磨机才能稳定运行。引起磨机振动的原因较多,归纳起来有以下几种:风量及风温的波动;研磨压力太高或太低;磨内有异物(如铁块);料层过薄或过厚;蓄能器压力过大或过小;刮料板磨损,积料多,风量分布不均;喂料量波动大。
在生产中控制磨机的振动可适当减料运行及减小研磨压力,同时根据料层厚度及出口温度调节喷水及循环风挡板、热风挡板来改善磨况,必要时,甚至可以通过提辊来避免振动过大,待磨况变好以后,再根据压差适当加料。
研磨压力:
ATOX-50立磨有三个磨辊,各配有一套蓄能器(见图一)。研磨压力是由液压系统产生的,液压系统有液压站和三个液压缸,每个液压缸都连有蓄能器,其作用是在研磨过程中起着液压气动吸振和缓冲机械负荷。
三个蓄能器的液压缸相连,当泵站工作时便可产生研压也可抬升磨辊,研磨压力的大小对磨的压力应该基本相等,否则会影响磨机的正常运行。三个磨辊通过辊轴及拉伸杆与各自机的性能影响较大,与产量有直接关系。研磨压力大,研磨作用增强,产量高;反之则产量低。但研磨压力也不宜过大,否则会增加主电机负荷,增加无用功,同时容易使磨机振动加剧,损坏磨机衬板及其它设备。在操作使用时,要保持研磨压力在设定范围内。在液压系统中设有安全保护的回油阀,当液压系统中压力超过设定压力7bar ,打开回油阀;当系统压力低于设定压力4bar 时,开起液压泵;当系统压力达设定值时,停泵。研磨压力还与蓄能器压力的大小有关,蓄能器压力太小或太大都起不到缓冲减振的作用,一般情况下研磨压力与蓄能器压力的关系如图二所示。
图二:氮气囊的充气压力与研磨压力使用范围的关系
N2
蓄能器
氮气囊
阀门
图一:蓄能器结构简图
204060
80100120
14016020
40
60
8010120
Pf/bar
P w /b a
A
B
氮气囊的充气压力
研磨压力
使用范围
压差:
压差是指风环处的压力损失,它也是立磨操作中最为重要的控制参数之一。
在磨机运行时,磨内负荷量的变化不仅从磨机电流、料层厚度、振动幅度等参数上反应出来,而且压差更能反映磨内状况。压差增大,磨内负荷加大;压差变小,说明磨内物料少,研磨层迅速减薄,磨内负荷下降。这两种情况,都会因料层不稳,使振动加剧,粉磨阻力增大,磨机输入功率增加,磨机电流也忽高忽低大幅摆动,直到磨机振停或振动稳定下来为止。操作上利用压差来作为控制磨内负荷量的变化,实现磨机稳定运行。
影响磨机压差的因素很多,如喂料量、系统风量、研磨压力、选粉机转速等。凡是影响磨机平稳运行的因素,几乎都可以在压差上反应出来。所以在磨机运行稳定前,这些变量都可能成为磨机操作的调整对象,操作员可根据实际情况作相应调整,直到工况稳定。然而,在磨机正常运行中,通常只采取调整喂料量来控制压差,一般不轻易改变研磨压力和选粉机转速两变量。研磨压力随产量要求预先设定好,而选粉机转速随产品细度而定。至于系统风量,也不是调节负荷的最佳变量,只有在特殊情况下,才调节风量,最终还需调整喂料,使磨机负荷恢复原稳定范围不影响产品质量。
磨机出口温度:
有效的控制出口温度,可以保持良好的烘干及粉磨作业条件,使产品达到规定的水分,该厂为保持生料水分在%以下,控制出口温度为90-95℃。影响磨机出口温度的因素通常有循环风、冷风、喷水量、热风、物料水分等,其中冷风量的变化有可能会使窑磨工况产生影响,一般很少采取调节冷风量的办法来调节出口温度,为了不影响窑系统,一般选择调节循环风挡板的开度来控制磨机出口温度。
磨机出口气体温度高低是衡量磨机运行状况的重要因素,过高过低都会引起磨机振动,通常在不影响质量的情况下,要控制出口温度基本稳定。当磨机运转到后期时,磨辊磨盘衬板磨损严重,出口温度稍微变化就会对磨有很大影响。例如,2003年十月份该厂ATOX-50立磨大修前,该磨已运转到后期,磨辊磨盘的衬板磨损非常严重,以致出现了很深的沟。在这种情况下,出口温度下降1oC料层就会变厚,压差增高,排泄量变大,磨机电流升高,然后振动加剧,出现类似球磨满磨的情况。此时应马上调节循环风,使出口温度很快恢复为原值,情况就会好转并稳定下来。所以作为立磨操作员应密切注意各参数的变化,尤其是出口
气体温度的变化,及时调节循环风,保证磨机稳定的运转。
当然,也可以采用磨内喷水的方法控制出口温度,但由于喷水量的变化会对所形成的稳定料床有影响,对料层厚度、磨机负荷的影响较大,所以不轻易采用调节喷水来控制温度。产品细度:
产品细度主要受选粉机转速影响,转速高,产品细;转速低,产品粗。调节细度主要靠手动改变选粉机转速来实现,但必须注意,增加或降低,只能逐步进行,每次增加或减少1%的设定值,调节过快,可能导致磨机振动加剧甚至振停。另外,磨内风量的大小对产品细度也有一定影响。
运行中参数的控制
a.生料磨系统操作稳定后,控制工艺参数如下:
生料磨进口温度: 160~260℃入磨粒度: 95%<80mm
生料磨出口温度: 90℃~95℃入磨水分: ≤%
生料磨进出口差压: 60mbar 生料细度: 80μm筛余≤%
生料旋风分离器差压: 生料水分: ≤%
废气收尘器进口温度: 90~150℃磨机能力: 300~400t/h 废气收尘器进出口差压: 小于200Pa
窑尾废气温度: 300~320℃
b.生料磨系统采用热风炉提供热气时,控制工艺参数如下:
生料磨进口温度: 160~220℃入磨粒度: 95%<80mm
生料磨出口温度: 90℃入磨水分: ≤%
磨机喂料量: 300~410t/h
主要设备控制点控制值报警值备注主电机绕组温度<85℃视外界温
度随调整出料温度<90℃
入磨温度≤300℃
研磨压力~120bar
入口压力大于-5mbar
磨机差压KPa 小于
磨辊油箱温度<58℃
张紧装置油位
主电机轴承温度<60℃
磨机震动<s
主减速机油箱温度<60℃
主减速机轴承温度<60℃
提升机电流
选粉机轴承温度℃<60℃
电流A 210
密封风机压力>30pa
电收尘器进口气体温度<150℃
压差Pa
出口压力Pa
高温风机风机轴承温度℃
风机出口压力KPa
a 入磨物料粒度、水分、硬度、易磨性。
b入磨物料按质控组下达的要求配比。
c磨机电流、选粉机电流。
d堆取料机堆料层数,均化效果。
e立磨出料温度,电机轴承的温度
f外循环系统的负荷。
运行过程中的调节
在刚开始开磨时,选粉机转速设定为85%,产量设定为240~300T/H,液压压力暂设定为100 ~120bar,系统风机风门设定为70~80~90~99%,调节冷风门及热风阀门保证入磨风温为160~220℃最大300℃. 当开磨时,由于启动输送组有时间滞后,一定要待物料入磨后(通过磨头监视器)并根据出磨风温适量调节磨内喷水系统,待磨进出口压差约35~45Kpa,可以降下磨辊,此时可能会出现振动,可以通过减小风量、微增加磨内喷水以稳定磨机,再逐步增加产量,不能骤然增加,可以20T为一个单位.同时要密切注意磨机的控制参数(电流、功率、料层厚度、磨机差压、振动值),当每加一次料,调节风量和选粉机转速,待稳定后,再次加料直到达产.
立磨系统三大稀油站控制
主减速机稀油站
1.加热器当减速机稀油站油箱温度>38℃时加热器断电;
当油箱温度<32℃加热器再次启动;
2.循环泵电机当油箱温度>20℃时,循环泵电机M01可以启动;
当油箱温度>20℃,推力瓦温度>20℃时,高压泵M02可以启动。
3.油泵接到停车命令时,延时60~180min后,油泵M01、M02将停止。
4.当推力瓦(D01~D12)的每一个瓦油压低于24bar将出现报警。
磨辊稀油站
1.当油箱油温>50℃时,可以开启M02~M07给、回油泵。
2.当油箱油温>60℃时,冷却水阀Y01打开;当油箱油温<57℃时,冷却水阀Y01关闭。
3.在设备运行中,当油箱油温<40℃时,润滑系统将停止运行。
4.若回油管中的真空压力太高持续600s则系统报警(油泵不停止)持续时间在1200s时则
油泵将停止运行.
5.当供油管油流量<70%时,油泵将停止运行.
6.当油箱温度>65℃时,将出现预报警; 油箱温度>67℃时, 油泵将停止运行.
7.当磨辊回油温度>65℃时,将出现预报警; 回油温度>68℃时, 油泵将停止运行.
8.当油箱油温>30℃时,循环泵M01可以启动;当油箱油温<28℃时,循环泵M01将停止运
行;
9.当回油压力<时,供油泵将以>70%供油量启动, 当回油压力>时供油泵将停止运行. 液压系统
1.当油箱油温>1℃时,可以启动循环油泵电机M01;当油箱油温<1℃时,循环油泵电机
M01不被认可启动;
2.当油箱油温>40℃时,加热器E01、E02停止; 当油箱油温<35℃时,加热器E01、E02自
动启动;
3.当油箱油温>17℃(20℃)时,高压泵M02可以启动;
4.当油箱油温>50℃时,电磁水阀Y04将开启冷却; 当油箱油温<47℃时,电磁水阀Y04将
关闭;
3调试与生产
调试
无负荷试车
(1)试车前的检查
a. 传动地脚螺栓是否紧固。
b. 安全运输设备是否已移走。
c. 下列螺栓联接是否用特定的扭力工具紧固。
d. 检查连接部位是否依照指导手册紧固;
e. 主要电机是否被正确紧固并正确安装(旋转方向检查是否正确);
f. 主要设备是否被紧固
g. 主要设备单元的冷却水供应是否安好并可投入使用。
h. 供油系统是否备妥(参考指导文件)
i. 可用冷却水质量是否可用并充足。
j. 报警装置是否正确安装。
k. 辊中的保护油是否被排干,轴承腔内是否被正确检查。
l. 辊中是否充满特定的润滑油。
m. 辊的保温套、轨道和耐磨(衬板)是否配套衬板间距是否调整好。
n. 辊中温度传感器是否校正并连接好。
o. 润滑管是否漏油。
p. N2缸是否充满N2。
q. 液压单元是否备妥。
r. 液压管是否漏油。
s. 所有检查门是否关闭。
t. 所有保护装置及报警信号是否正确对应。
u. 检查选粉机减速机油泵是否能正常工作。
v.检查选粉机立轴轴承润滑脂是否加到位。
w.检查选粉机静态叶片是否灵活可调,叶片方向是否正确。
(2)运转中的检查:
a. 检查各电机温度、温升是否正常,有无异振、异音;
b. 检查各泵、减速机温升是否正常,有无异常、异音;主减速机的振动情况;
c. 检查密封风机、液压系统、润滑系统、喷水系统工作状况,风压、油压、油温、水位等是否适当;
d. 选粉机转子有无磨擦,有无因转子不平稳而引起的异音和异振;
e. 检查各管路有无渗油、渗水现象,液压缸有无渗油;
f. 检查各地脚螺栓及连接螺栓有无松动或脱落;
g.检查主电机碳刷工作状况;
h. 空气密封管道、膨胀节有无损坏、漏气;
负荷试车
(1)负荷试车运转中的检查:
a. 检查各电机温度、温升是否正常,有无异振、异音;
b. 检查各泵、减速机温升是否正常,有无异常、异音;主减速机的振动情况;
c. 检查密封风机、液压系统、润滑系统、喷水系统工作状况,风压、油压、油温、水位等是否适当;
d. 选粉机转子有无磨擦,有无因转子不平稳而引起的异音和异振;
e. 检查各管路有无渗油、渗水现象,液压缸有无渗油;
f. 检查各地脚螺栓及连接螺栓有无松动或脱落;
g.检查主电机碳刷工作状况;
h. 空气密封管道、膨胀节有无损坏、漏气;
i.检查各仪表指示值,设备的工作状况,每半小时做一次记录,对每台电机的电流及温升状况都应有记录,对运行中出现的问题及时做好记录;
(2) 利用热风炉升温
●确认入磨热风挡板关闭,磨出口挡板全开,冷风挡板开至合理开度,通知
现场做好热风炉点火准备工作;
●按《热风炉操作规程》将热风炉投入运行;
●借助循环风挡板来控制磨入口负压,风温可用喷油量和冷风挡板来调节,
对磨机进行升温预热;
注:试运行时用热风炉热风开磨;开窑后用窑废气作为烘干热源时,可将磨负荷加至100%。
(3) 故障处理
a. 磨机磨料过程:当磨机出料出现过粗时,会出现磨机振动,这意味磨机减速机会出现危险,应立即抬起磨辊或停车处理,过粗原因是物料太少或磨机过载;
b. 喂料仓储料不足:一旦喂料仓储料不足,应立即停机,因为此时磨机继续向外输料,有空磨的危险,应向供料装置和磨机进料,否则会使料床变薄,发生振动导致磨机跳停;
c. 磨机粉磨时,料床储料不足会引起磨机震动,此时应调节磨机喂料量或者微调节磨内喷水,以稳定磨机工况。使其料层厚度不小于50mm
d. 窑尾电场跳停:当仪表显示粉尘过多时,必须减少磨机喂料量或停机;
(3) 系统停机后的检查
a. 石灰石取料机、辅料取料机各受力部件的磨损情况,有无脱焊/开裂;
b. 各部位联接螺栓和地脚螺栓有无松动、脱落;
c. 各润滑点润滑情况是否良好,管路密封是否正常,油位是否正常;
d. 检查各下料口磨损情况,有无脱焊、开裂、有无结皮、积料;
e. 检查磨内各磨损件的磨损情况和紧固情况,测量磨盘和磨辊衬板的磨损程度并做好记录,检查限位板螺栓松动情况,限位板有无裂纹;
f. 检查进风口积料情况及刮料板磨损情况;
g. 检查液压系统各元件的动作灵活性和补偿元件的紧固程度及各管的密封情况;
h. 检查密封风机压力,清洗风机过滤网;
i. 检查碾磨器各法兰盘及系统各膨胀节的松紧度;
j. 检查磨机风机及选粉机叶片是否有结疤和磨损;
k. 检查防雨设施是否完好;
m. 检查电收尘各振打装置是否完好;
n. 检查绝缘套管、轴瓦是否有裂纹,及各部的积灰情况,尤其是两极系统和气流分布板上的积灰。
o.检查蓄能器预加载压力有无损失,若损失应查明原因,予以补充。
p.打开磨门检查磨辊紧固套螺栓是否符合扭矩要求;磨辊密封处有无漏油现象;
q.检查主电机碳刷磨损及固定情况;
r.检查主电机轴承润滑情况,润滑站各管路有无渗漏,油箱油位是否正常;
s.各油站油、水过滤器清洗,密封风机过滤网清吹;
t.各地脚螺栓、连接螺栓有无松动、脱落;
u.检查喷水装置,防止漏水;
v.选粉机各叶片固定情况及磨损情况,轴承润滑及密封情况;
开车顺序
1 原料磨润滑系统及所有电机、风机的润滑系统
2 磨内密封系统
3 生料库顶收尘
4 生料入库输送系统
5 原料磨和磨尾收尘系统
6 选粉机及循环风系统
7 气流线路
8 立磨外循环系统
9 磨主驱动
10 原料入磨
停车
停车注意事项
a.停皮带机之前,必须把皮带上的物料走空。
b.停板式给料机之前,速度逐渐降低为零,才停机.
c.停磨机短时间之内,不要开磨门,以免骤然冷却,产生热应力变形.
d.停磨机短时间之内,不要停润滑系统和冷却水系统,防止损坏设备.
e.停喂料系统之前,将各皮带秤速度降为零.
f.停风机之前,先将风机速度逐渐降低,风门逐渐减小直到关闭.
g.注意磨机震动情况.
故障停车
在设备运行过程中,由于设备突然发生故障、电机过载跳闸、现场停车按钮误操作、临时断电等原因,系统中的全部或部分设备会连锁停车。另外,在紧急情况下,为了保证设备能顺利地再次启动,必须采取相应的措施:
a. 立即关掉与之相关的部分设备。
b. 为防止磨瓦、轴承等损伤,应尽快恢复稀油站组设备的运行。
c. 尽快查清原因,判断能否在短时间(30分钟)内处理完,以决定再次启动的时间,如果故障处理时间过长,应进行相应的操作。
紧急停机
当中控发现以下异常情况时,应按规定顺序停磨,通知岗位检查原因,排除故障。
a.各处联接螺栓发生松动、折断或脱落时;
b.磨机内机件脱落时;
c. 减速机润滑系统发生故障而引起轴承温度上升超过规定值时
d. 减速机发生异常振动及噪音时;
e. 电动机轴承温度超过其规定值时。
f. 如果磨机在动转中突然停电时,应立即将磨机及其附属设备的电机电源切断,以免来电时发生意外事故。注意:为保护磨主电机,主电机第二次启动距离主电机上次停车时间不得小于30分钟。
g. 如果出现任意一台配料秤断料10分钟以上。
h. 如果出现出磨输送设备堵塞而无法及时疏通时;如果出现设备跑、冒、滴、漏严重而无法临时处理时。
i. 如果有危及人身安全的事故出现时。
4生产中的问题及解决措施
常见的问题及解决措施
常见故障可能原因主要操作处理
A、磨机隆响振动1、起动前磨床上铺料不足
2、进磨物料粒度过粗;磨机供
料不足或过多;选粉机调整的
细度过细
3、窑尾高温风机故障而中断供
风;磨机风机故障而无法满足
1、立即停机,待加厚磨床上
物料量后重新启动
2、结合磨机工况下的其它参
数,及时采取相应的操作措
施,但情况严重时需考虑停
磨
3、停机检修
磨内通风与选粉出料的要求
B、磨机进出风口压差过大或过小1、喂料输送系统故障,供料过
多或过小;风量过低或不稳定;
选粉机调整细度过细或过粗
2、喷口风环阻塞或磨损严重
3、显示与仪表故障
1、结合磨机工况下的其它参
数,及时采取相应的操作措
施,同时还应加强生产监控
2、减少供料、加强监控,若
情况严重,需停机检修
3、尽快进行修理恢复。在此
期间,应密切监视其它工况
参数的变化和调控,并根据
工艺操作难易程度和对设备
安全性可能造成的影响程度
决定是否停磨。
C、磨辊张紧压力下降管路渗漏;压力安全溢流阀失
灵;油泵工作中断;压力开关
失常
对于完好设备,可起动油泵
重新开始工作,关泵后仍能
保压,否则,应停磨检修
D、磨辊密封风压下降管道漏风;密封风机故障;阀
门调节不当
检查设备,若风压略有降低
后仍能恒定,可不停机,如
果其恒定值已超过最低要
求,磨机将自动边锁停机。
E、磨机排渣量过多1、供料过多、磨机过载;磨机
通风量偏小,选粉机调整的细
度过细而使磨机过载
2、喷口风环面积过大或磨损严
重
1、减少供料、加强通风,适
当调整生料细度,并结合磨
机的其它工况下参数及时采
取其它相应的灵活措施
2、根据前项操作后,视排渣
量的变化,决定是否停机检
修和调整
F、换向阀频繁动作
1、金属探测仪频繁扳紧
2、换向阀本身的故障1、检查除铁器是否工作,若工作正常,再观察物料是否有其它金属物,若有剔除,若无金属物说明金属探测器误报警,联系相关人员处理。
2、通知相关人员检查处理,若处理不好停磨
G、磨机跳停1、振动大
2、密封风机跳停或压力低
3、选粉机跳停
4、生料输送设备跳停
5、液压泵或减速机油泵跳停
1、查看趋势图,看配料站下
料是否平稳,是否断料,堵
仓,以及看差压变化,同时
查看报警值,找出原因并处
理
2、现场检查密封风机及管
道,并清吹过滤阀
3、找出跳停原因并处理
4、找出跳停原因并处理
6、磨主电机绕组温度达140℃,电机轴承温度达65℃5、找出跳停原因并处理
6、查明温升原因,待温度下降再启动
磨机运行中异常情况分析及处理
振动跳停的原因
①喂料量过大或过小磨机运行中异常情况分析及处理
根据差压调整喂料量
②系统风量不足调整各挡板开度,增加系统风量
③研磨压力过高或过低重新设定张紧压力
④出磨温度骤然变化根据磨电流、料层厚度
变化及时调整喂料量
⑤磨内有异物或大块观察吐渣,加强入磨物料
除铁、金属杂质分离
⑥选粉机转速过高调整选粉机转速
⑦磨内料层波动大调整好喂料量、系统通风
⑧液压站三个N2囊预调整N2囊预加载压
加载压不平衡
⑨测振元件失灵重新校正或更换
差压高
①喂料量过大根据差压调整喂料量
②入磨物料易磨性差或粒度大根据物料特性调整喂料量
③研磨压力过低重新设定研磨压力
④系统通风不畅调整各档板开度,增强系统风量
⑤选粉机转速过高根据成品细度调整转速
⑥磨系统漏风量大加强系统密封,减少漏风量
吐渣多
①喂料量过大减少喂料量
②入磨物料粒度过大
③研磨压力过低增加研磨压力
④系统风量不足增加风量
⑤喷口环盖板损坏或磨损停机处理
细度过粗的原因
①风、料、选粉机转速不匹配调整比例使之匹配
②研磨能力低加大研磨压力或更换磨盘、磨辊衬板
③系统通风量大调整用风量
5 结语:
ATOX-50立磨在该厂使用已有一年多在短时间内即能够顺利实现达标,进入正常生产。现已能稳定操作达到设计产量400T/h取得了良好的经济效益,充分说明该立磨具有良好的使用性能,但是该磨不适于粉磨硬质和磨蚀性大的物料,衬板使用寿命较短维修较频繁,磨损件比球磨机的贵。但与其所取代的球蘑机,提升机、选粉机等设备的总维修量相比,乃显的维修简单、容易和工作量小,成为现代化水泥厂生料粉磨的首选设备之一。
6 参考文献:
1 李海涛主编。新型干法水泥生产技术与设备。北京:化学工业出版社, 2006
2 王仲春编著。水泥工业粉磨工艺技术。北京:中国建材工业出版社, 2000
3 邹莉,郭元东。 ATOX-50立磨操作浅谈。新世纪水泥导报, 1999
4 赵乃仁。辊式磨粉磨的运行机理及其选型原则的探讨。水泥工程, 2004 7致谢
在写本篇文章的过程中,得到了李海涛老师的悉心指导,有力帮助,使的该篇文章能够顺利完成,在此表示感谢.