模具热处理工艺流程【详情】

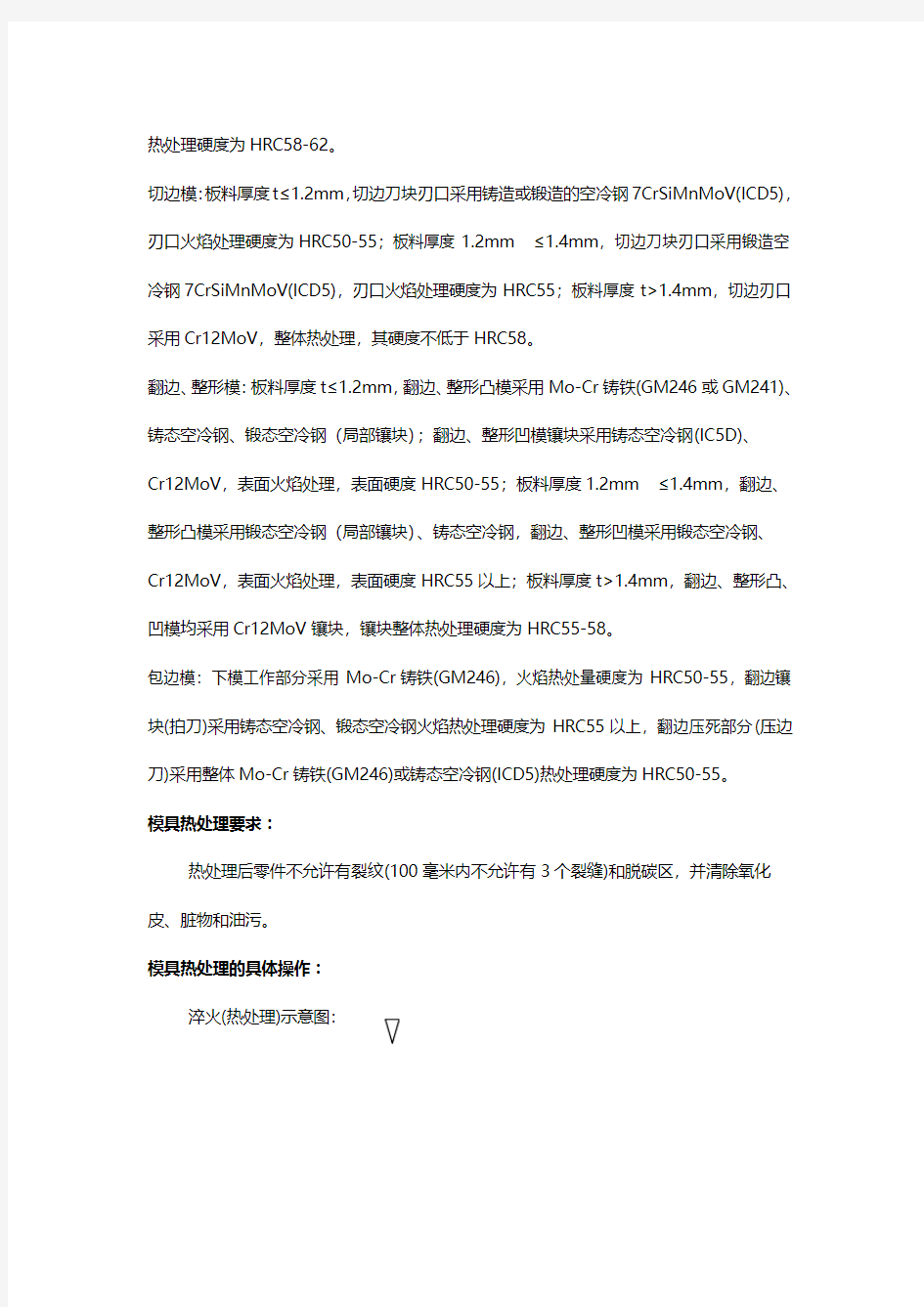
模具热处理工艺流程
模具热处理是指材料在固态下,通过加热、保温和冷却的手段,以获得预期组织和性能的一种金属热加工工艺。
模具热处理工艺技术对于模具制造来说,最大的用处是进一步提高模具的精度,比如防止加热氧化和不脱碳、真空脱气或除气,消除氢脆,从而提高材料(零件)的塑性、韧性和疲劳强度;真空加热缓慢、零件内外温差较小等因素,决定了真空热处理工艺造成的零件变形小等。
模具热处理工艺的方式有:
(1)软化退火:其目的主要在于分解碳化物,将其硬度降低,而提高加工性能,对于球状石磨铸铁而言,其目的在于获得具有甚高的肥力铁组织。
(2)正常化处理:主要用于改进或是使完全是波来铁组织的铸品而获得均匀分布的机械性质。
(3)淬火:主要为了获得更高的硬度或磨耗强度,同时的到甚高的表面耐磨特性。
(4)表面硬化处理:主要为获得表面硬化层,同时得到甚高的表面耐磨特性。
(5)析出硬化处理:主要是为获得高强度而伸长率并不因而发生激烈的改变。
模具材料及热处理硬度:
⑴拉延模:板料厚度t≤1.2mm,凸、凹模及压边圈采用Mo-Cr合金铸铁(GM246或
GM241),表面火焰处理,其硬度不低于HRC50。板料厚度1.2mm
热处理硬度为HRC58-62。
切边模:板料厚度t≤1.2mm,切边刀块刃口采用铸造或锻造的空冷钢7CrSiMnMoV(ICD5),刃口火焰处理硬度为HRC50-55;板料厚度1.2mm
翻边、整形模:板料厚度t≤1.2mm,翻边、整形凸模采用Mo-Cr铸铁(GM246或GM241)、铸态空冷钢、锻态空冷钢(局部镶块);翻边、整形凹模镶块采用铸态空冷钢(IC5D)、
Cr12MoV,表面火焰处理,表面硬度HRC50-55;板料厚度1.2mm
包边模:下模工作部分采用Mo-Cr铸铁(GM246),火焰热处量硬度为HRC50-55,翻边镶块(拍刀)采用铸态空冷钢、锻态空冷钢火焰热处理硬度为HRC55以上,翻边压死部分(压边刀)采用整体Mo-Cr铸铁(GM246)或铸态空冷钢(ICD5)热处理硬度为HRC50-55。
模具热处理要求:
热处理后零件不允许有裂纹(100毫米内不允许有3个裂缝)和脱碳区,并清除氧化皮、脏物和油污。
模具热处理的具体操作:
淬火(热处理)示意图:
注:火焰与冷却水管应同步进行,工件上看到红亮时,应缓慢移动割炬,冷却水也缓慢跟进,水过后相应的工件部位呈现出翻白状态为最佳状态,若不同步,冷却水慢,由于加热温度太高,加热层会产生过烧现象,凸R角便会起泡有气蚀孔;冷却水过快,会使加热温度过低,水过后凸R 角呈现黑斑现象造成R角热处理硬度不够。
1. 拉延模:模具底座泡在水池中进行凸R角的热处理;用水冷却.首先热处理一小段用硬度仪检测,达标了以这段为参照处理佘下的凸R角.(经验:微微翻白为好,烧得过红,R角会裂,烧得过黑,证明火烧得不足,硬度不够;用锉刀检验切削量少有滑硬感)。
2.切边冲孔、翻边整型面模:模具底座泡在水池中进行刃口和整型工作面的热处理,钢件用风冷或自然冷却、铸件用水冷却,凸模和刀块要隔块分开进行,先进行刀块两端面热处理50MM,然后把折下的刀块装上进行热处理余下未处理的刀口,这样可以减少刀块端面和底
面的变形量。(刀口的热处理时刀口微微翻白为好,烧得过红刀口会裂;烧得黑黑的证明烧得不足,硬度也不够)
3.有水池作条件才能把模座泡在水中进行热处理工作。
内容来源网络,由深圳机械展收集整理!
更多金属表面处理厂家技术展示,就在深圳机械展!
(答案)模具材料及热处理试题库
模具材料及热处理试题库 一、判断 1、60钢以上的优质碳素结构钢属高碳钢,经适当的热处理后具有高的强度、韧性和弹性,主要用于制作弹性零件和耐磨零件。(×) 2、40Cr钢是最常用的合金调质钢。(√) 3、60Si2Mn钢的最终热处理方法是淬火后进行高温回火。(×) 4、高合金钢的完全退火的冷却速度是每小时100~150℃。(×) 5、等温淬火与普通淬火比较,可以获得相同情况下的高硬度和更好的韧度。(√) 6、一些形状复杂、截面不大、变形要求严的工件,用分级淬火比双液淬火能更有效的减少工件的变形开裂。(√) 7、渗碳时采用低碳合金钢,主要是为提高工件的表面淬火硬度。(×) 8、均匀化退火主要应用于消除大型铸钢、合金钢锭在铸造过程中所产生的化学成分不均及材料偏析,并使其均匀化。(√) 9、高合金钢及形状复杂的零件可以随炉升温,不用控制加热速度。(×) 10、铬钼钢是本质粗晶粒钢、其淬透性和回火稳定性高,高温强度也高。(×) 11、铬锰硅钢可以代替镍铬钢用于制造高速、高负荷、高强度的零件。(√) 12、铬轴承钢加热温度高,保温时间略长,主要使奥氏体中溶入足够的合金碳化物。(√)13、低合金渗碳钢二次重新加热淬火,对于本质细晶粒钢的零件,主要使心部、表层都达到高性能要求。(×) 14、铸铁的等温淬火将获得贝氏体和马氏体组织。(√) 15、高速钢是制造多种工具的主要材料,它除含碳量高外,还有大量的多种合金元素(W、Cr、Mo、V、Co),属高碳高合金钢。(×)16、钢在相同成分和组织条件下,细晶粒不仅强度高,更重要的是韧性好,因此严格控制奥氏体的晶粒大小,在热处理生产中是一个重要环节。(√)17、有些中碳钢,为了适应冷挤压成型,要求钢材具有较高的塑性和较低的硬度,也常进行球化退火。(√)18、低碳钢正火,为了提高硬度易于切削,提高正火温度,增大冷却速度,以获得较细的珠光体和比较分散的自由铁素体。(√)19、过共析钢正火加热时必须保证网状碳化物完全融入奥氏体中,为了抑制自由碳化物的析出,使其获得伪共析组织,必须采用较大的冷却速度冷却。(√)20、含碳量相同的碳钢与合金钢淬火后,硬度相差很小,但碳钢的强度显著高于合金钢。(×)21、中高碳钢的等温淬火效果很好,不仅减少了变形,而且还获得了高的综合力学性能。(√)22、淬火钢组织中,马氏体处于碳的过饱和状态,残余奥氏体处于过热状态,所以组织不稳定,需要回火处理。(×)23、低碳钢淬火时的比容变化较小,特别是淬透性较差,故要急冷淬火,因此常是以组织应力为主引起的变形。(×)24、工件淬火后不要在室温下放置,要立即进行回火,会显著提高马氏体的强度和塑性,防止开裂。(√)
热处理工艺规范(最新)
华尔泰经贸有限公司铸钢件产品热处理艺规范 随着铸造件产品种类增多,对外业务增大,方便更好的管理铸造件产品,特制定本规定,要求各部门严格按照规定执行。 1目的: 为确保铸钢产品的热处理质量,使其达到国家标准规定的力学性能指标,以满足顾客的使用要求,特制定本热处理工艺规范。 2范围 3术语 经保温一段时间后, 经保温一段时间后, 3.3淬火:指将铸钢产品加热到规定的温度范围,经保温一段时间后, 快速冷却的操作工艺。 3.4回火:指将淬火后的铸钢产品加热到规定的温度范围,经保温一 段时间后出炉,冷却到室温的操作工艺。 3.5调质:淬火+回火 4 职责
4.1热处理操作工艺由公司技术部门负责制订。 4.2热处理操作工艺由生产部门负责实施。 4.3热处理操作者负责教填写热处理记录,并将自动记录曲线转换到 热处理记录上。 4.4检验员负责热处理试样的力学性能检测工作,负责力学性能检测 结论的记录以及其它待检试样的管理。 5 工作程序 5.1 错位炉底板应将其复位后再装, 5.2 对特别 淬铸件应控制入水时间,水池应有足够水量,以保证淬火质量。 5.5作业计划应填写同炉热处理铸件产品的材质、名称、规格、数量、 时间等要素,热处理园盘记录纸可多次使用,但每处理一次都必须与热处理工艺卡上的记录曲线保持一致。 6 不合格品的处置 6.1热处理试样检验不合格,应及时通知相关部门。
6.2技术部门负责对不合格品的处置。 7 附表 7.1碳钢及低合金钢铸件正火、退火加热温度表7.2碳钢及低合金钢铸件退火工艺 7.3铸钢件直接调质工艺 7.4铸钢件经预备热处理后的调质工艺 7.5低合金铸钢件正火、回火工艺
加工工艺过程卡片及工序卡
材料牌号HT200 毛坯种类金属型铸件毛坯外形尺寸754×400×186 每毛坯件数 1 每台件数 1 备注 工序号工序名称工序内容车 间 工 段 设备工艺装备 工时 准终单件 01 铸造金属型铸造毛坯 02 回火热处理 03 探伤检验 04 表面喷丸处理 10 粗铣以顶面为粗基准,粗铣箱体结合面X7010 面铣刀、游标卡尺 20 粗铣以箱体结合面为基准,粗铣顶面X7010面铣刀、游标卡尺 30 钻孔结合上下箱体,钻、铰出两个定位孔2-φ12H8组合钻床麻花钻、铰刀、卡尺、塞规40 粗铣以结合面为基准两销定位,粗铣前后端面及凸台组合铣床面铣刀、游标卡尺 50 粗铣以结合面为基准两销定位,粗铣右端面组合铣床面铣刀、游标卡尺 60 半精铣以顶面为基准,半精铣箱体结合面X7010 面铣刀、游标卡尺 70 半精铣以结合面为基准两销定位,半精铣前后端面至图纸要求组合铣床面铣刀、游标卡尺 80 半精铣以结合面为基准两销定位,半精铣右端面至图纸要求组合铣床面铣刀、游标卡尺 90 半精铣以结合面为基准两销定位,半精铣顶面至图纸要求X7010 面铣刀、游标卡尺100 半精铣结合上下箱体,铣结合面凹槽至图纸要求X7010 立铣刀、游标卡尺110 精铣以顶面为基准,精铣箱体结合面至图纸要求X7010 面铣刀、游标卡尺 120 钻顶面孔 以结合面为基准,用心轴穿过φ110,钻14-φ18组装孔;钻顶面 螺纹孔4-M12-6H;钻两肋板中间凸台M20×1.5螺纹孔 组合钻床麻花钻、卡尺、塞规 设计(日期)校对(日期)审核(日期)标准化(日期)会签(日期) 标记处数更改文件号签字日期标记处数更改文件号签字日期
焊接、热处理工艺卡
焊接热处理工艺卡 精品
工艺曲线图: 注意事项: 1. 在加热范围内任意两点的温差应小于 50℃; 2. 保温厚度以40~60mm 为宜; 3. 升、降温时,300℃以下可不控温; 4. 焊后热处理必须在焊接完毕后24h 内进行。 编制 日期 审批 日期 焊接施工工艺卡 企业名称:安徽电力建设第二工程公司 设计卡编号:APCC-GD-WPS-001 产品名称:P91中大口径管焊接工艺卡 所依据的工艺评定报告编号:APCC-PQR-115 焊接位置:2G 、5G 、6G 自动化程度:手工焊 母 材 坡 口 简 类号 B 级号 Ⅲ 与 类号 B 级号 Ⅲ 钢号 SA335-P91 与 母材厚度范围:√对接接头 角接接头 70mm 焊缝金属厚度范围:δ≤h ≤δ+4mm 管子直径范围:√对接接头 角接接头 φ406 其 他: / 坡口检查 √外观检查VT √着色PT 磁粉MT 装配点焊 √手工焊Ds 氩弧焊Ws 二氧化碳气体焊Rb 焊材要求 √焊丝清洁 √焊条烘焙 焊剂温度 焊前预热: 火焰预热 √电阻预热 预热温度:150~200℃ 层间温度:200~300℃ 焊嘴尺寸: M10×L65×φ6 钨极型号/尺寸: Wce-20,φ2.5 焊接技术: 导电嘴与工件距离: / 清理方法: 机械法清理 无摆动或摆动焊: 略摆动 焊接方向: 由左至右、由下至上 工 艺 参 数 层 道 次 焊接方法 焊材 极 性 焊接参数 焊剂或 气体 保护气体流量L/Min 背面保护气体流 量L/Min 气体后拖 保护时间S 牌号 规 格 (mm ) 电流(A ) A 电压 (V ) 焊速 mm/Min 150~250 200~300 ≤300℃ 温度(℃) 时间 6(h ) 80~100℃/2 ≤90℃/h ≤90℃/h 750~770℃
模具材料及热处理
模具材料及热处理模具材料及热处理 1.金属组织 1.1金属 具有不透明、金属光泽良好的导热和导电性并且其导电能力随温度的增高而减小,富有延性和展性等特性的物质。金属内部原子具有规律性排列的固体(即晶体)。 1.2合金 由两种或两种以上金属或金属与非金属组成,具有金属特性的物质。 相:合金中成份、结构、性能相同的组成部分。 1.3固溶体 是一个(或几个)组元的原子(化合物)溶入另一个组元的晶格中,而仍保持另一组元的晶格类型的固态金属晶体,固溶体分间隙固溶体和置换固溶体两种。 1.4固溶强化 由于溶质原子进入溶剂晶格的间隙或结点,使晶格发生畸变,使固溶体硬度和强度升高,这种现象叫固溶强化现象。 1.5化合物 合金组元间发生化合作用,生成一种具有金属性能的新的晶体固态结构。 1.6机械混合物 由两种晶体结构而组成的合金组成物,虽然是两面种晶体,却是一种组成成分,具有独立的机械性能。2.金属硬度 2.1硬度 金属的硬度,是指金属表面局部体积内抵抗外物压入而引起的塑性变形的抗力,硬度越高表明金属抵抗塑性变形的能力越强,金属产生塑性变形越困难。硬度试验方法简单易行,又无损于零件。实际常使用的硬度试验方法有:布氏硬度、洛氏硬度和维氏硬度三种。三种硬度试验值有大致的换算关系,见表一。 布氏硬度HB:布氏硬度是用载荷为P的力把直接D的钢球压入金属表面,并保持一定的时间,测量金属表面上的压痕直径d,据此计算出的压痕面积AB,求出每单位面积所受力,用作金属的硬度值,叫布氏硬度,记作HB。布氏硬度的使用上限是HB450,适用于测定退火、正火、调质钢、铸铁及有色金属的硬度。 2.1.1洛氏硬度HRA、HRC: 洛氏硬度是工业生产中最常用的硬度测量的方法,因为操作简便、迅速,可以直接读出硬度值,不损伤工件表面,可测量的硬度范围较宽。但洛氏硬度也有一些缺点,如因压痕小,对材料有偏析及组织不均匀的情况,测量结果分离度大,再现性较差。洛氏硬度(HR)也是用压痕的方式试验硬度。它是用测量凹陷深度来表示硬度值。洛氏硬度试验用的压头分硬质和软质两种。硬质压头为顶角为120o的金刚石圆锥体,使用于淬火钢等硬的材料。HRA硬度有效范围是>70,适用于硬质合金、表面淬火层及渗碳层;HRC硬度有效范围是20-68(相当于HB230-700,HB450-700超出了布氏硬度的使用上限),适用于淬火钢及调质钢。 2.1.2洛氏硬度HRB 洛氏硬度HRB的测量采用直径1.588mm(1/16")的钢球,适用于退火钢、有色金属等,硬度有效范围是25-100(相当于HB60-230)。 2.1.3维氏硬度HV 维氏硬度也是利用压痕面积上单位应力作为硬度值计量。维氏硬度所使用的压头是锥面夹角为136o的金刚石四方锥体。试验时,在载荷P的作用下,在试样试验面上压出一个正方形压痕。测量压痕两对角线的平均长度d,借以计算压痕面积A V,以P/A V的数值表示试样的硬度,以HV表示。维氏硬度的优缺点:维氏硬度有一个连续一致的标度;试验负荷可任意选择,所得的硬度值相同。试验时加载的压力小,压入深度浅,对工件损伤小。特别适用于测量零件的表面淬硬层及经过表面化学处理的硬度,精度比布氏、洛氏硬度精确。但是维氏硬度的试验操作较麻烦,一般在生产上很少使用,多用于实验室及科研方面。
机械加工工艺过程卡及工序卡
机械加工工艺过程卡填写说明 +%)查表得到,不计准备和终结时间; (15) 设备负荷率=(13 x(4)十(251天x8小时x60分x(12); (16) 根据需要填写。 (1)过程卡和工序卡的总页数; (2)当前页页序; (3)按零件图填写; (4)按设计任务书填写,包括了备品率和废品率; (5)按零件图填写; (6)填写“铸件”、“锻件”、“圆钢”、“板钢”等; (7)每毛坯可加工同一零件的数量; (8)工序号,可依自然数连续或不连续编号; (9)工序名称如“钻xx孔”、“粗铣xx面”、“攻xx螺纹” 等; (10)填写设备名称如“立钻”; (11)填写设备型号如“ Z5125A ”; (12)填写该工序所需设备数量; (13)基本时间t m和辅助时间t a之和,也称为操作时间。基本时 间取自工序卡。辅助时间按工序卡所表明的工序操作动作,查各动作的时间定额标准并累加得到(未见占基本时间百分比数据) ; (14)工时定额t t按公式t t= (t m+t a) [1+ ( a+? % ]计算。其中布置工作地时间、休息和生理需要时间按它们占作业时间的百分比
机械加工工序卡填写说明 (1 )、( 3)、(4)、( 5)、(6)、(11)同于对工艺过程卡相应内容的说明; (2)采用的切削液名称,如“水”、“水溶液”、“乳化液”等; (7)工序简图。要求:①主要简图是零件在机床上装夹位置的主视图,应有零件的外形轮廓,与本工序无关的结构要素不表示。②完整表示工序定位基 准、夹压力方向和作用面、夹压方式(机械夹紧、液压夹紧、气动夹紧、电磁夹紧),也可规定夹压位置。③用特粗线条表示出加工面,注明工序尺寸及 公差、加工面的相对位置精度、表面粗糙度等。④表示工序同时装夹零件的数目和排列方式。⑤若绘制简图的位置不够,可另页绘制(该页上保留工序卡表头,其它位置绘简图),顺序在本工序卡片之后,有页码。 (8)若需要专用夹具,填写夹具名称,如“钻夹具”。否则不填; (9)本工序工序内容序号,依自然数连续编号; (10)工序加工内容和主要技术要求。外协序只写工序名称和主要技术要求,如热处理的硬度和变形要求、电镀的镀层厚度。设计或工艺要求加工面配做配钻时,要在配做配钻前该面的最后工序另起一行注明,如“XX孔与XX 件配钻”; (11)填写设备型号如“ Z5125A ”; (12)专用的填写编号,由于没有编号规则,可填写刀辅具名称,并示以“专用”含义,如“成形铳刀”。标准的填写名称、规格,如“锥柄钻头①14.3X 200”、“ 45°车刀”; (13)填写量检具名称,如“孔位检具”、“卡规”等,已有“专用”含义。 标准的填写名称、规格、精度,如“卡尺0~125, 0.02”、“杠杆表0~0.8, 0.01 ”。 (14)、(15)、(16)、(17)切削用量三要素,由分析计算或查表得到。 (18 )工件切削部分的长度; (19 )直接改变加工对象几何状况或材料性质的工艺过程所消耗的时间,用相应加工方法基本时间计算公式计算。切削加工时,不仅与切削长度、走刀次数和切削用量有关,还与切入量、切出量、刀具尺寸等有关。
加工工艺过程卡片及工序卡
湖南科技大学机械加工工艺过程卡片产品型号零件图号 产品名称变速箱零件名称变速箱下盖共 3 页第 1 页材料牌号HT200 毛坯种类金属型铸件毛坯外形尺寸754×400×186 每毛坯件数 1 每台件数 1 备注 工序号工序名称工序内容车 间 工 段 设备工艺装备 工时 准终单件 01 铸造金属型铸造毛坯 02 回火热处理 03 探伤检验 04 表面喷丸处理 10 粗铣以顶面为粗基准,粗铣箱体结合面X7010 面铣刀、游标卡尺 20 粗铣以箱体结合面为基准,粗铣顶面X7010面铣刀、游标卡尺 30 钻孔结合上下箱体,钻、铰出两个定位孔2-φ12H8组合钻床麻花钻、铰刀、卡尺、塞规40 粗铣以结合面为基准两销定位,粗铣前后端面及凸台组合铣床面铣刀、游标卡尺 50 粗铣以结合面为基准两销定位,粗铣右端面组合铣床面铣刀、游标卡尺 60 半精铣以顶面为基准,半精铣箱体结合面X7010 面铣刀、游标卡尺 70 半精铣以结合面为基准两销定位,半精铣前后端面至图纸要求组合铣床面铣刀、游标卡尺 80 半精铣以结合面为基准两销定位,半精铣右端面至图纸要求组合铣床面铣刀、游标卡尺 90 半精铣以结合面为基准两销定位,半精铣顶面至图纸要求X7010 面铣刀、游标卡尺100 半精铣结合上下箱体,铣结合面凹槽至图纸要求X7010 立铣刀、游标卡尺110 精铣以顶面为基准,精铣箱体结合面至图纸要求X7010 面铣刀、游标卡尺 120 钻顶面孔 以结合面为基准,用心轴穿过φ110,钻14-φ18组装孔;钻顶 面螺纹孔4-M12-6H;钻两肋板中间凸台M20×1.5螺纹孔 组合钻床麻花钻、卡尺、塞规 设计(日期)校对(日期)审核(日期)标准化(日期)会签(日期) 1 / 26
T12钢热处理工艺
金属材料与热处理技术课程设计 题目:T12钢热处理工艺课程设计 院(系):冶金材料系 专业年级:材料1201 负责人:陈博 唐磊,杨亚西, 合作者:谭平,潘佳伟,多杰仁青 指导老师:罗珍 2013年12月
热处理工艺课程设计任务书 系部冶金材料系专业金属材料与热处理技术 学生姓名陈博,杨亚西,唐磊,谭平,多杰仁青,潘佳伟 课程设计题目T12 设计任务: 1,课程设计的目的:为了使我们更好地了解碳素工具钢的性能及其热处理工艺流程。培养学生综合运用所学的热处理课程的知识去解决工程问题的能力,并使其所学知识得到巩固和发展。学习热处理工艺设计的一般方法,热处理设备选用和装夹具设计等进行热处理设计的基础技能训练。 2.课程设计的任务分组(碳素工具钢T12) ①:锉刀的热处理工艺(唐磊) ②:热处理后的组织金相分析(陈博) ③:淬火(潘佳伟) ④:回火(多杰仁青) ⑤:局部淬火(谭平) ⑥:缺陷分析(杨亚西) 3.课程设计的内容: T12钢热处理工艺设计流程 4参考文献: 【1】詹艳然,吴乐尧,王仲仁.金属体积成形过程中温度场的分析.塑性工程学报,2001,8(4) 【2】叶卫平,张覃轶.热处理实用数据速查手册.机械工业出版社.2005,59---60 【3】许天己钢铁热处理实用技术.化学工业出版社2005,134"~136 设计进度安排: 第一周周一~周二钢的普通热处理工艺设计理论学习 周三~周五分组进行典型金属材料的热处理工艺设计第二周周一~周三撰写设计说明书 周四~周五答辩 指导教师(签字): 年 月日
热处理工艺卡 热处理工艺卡材料牌 号 T12 零件重 量 锉刀400g 工艺路 线 热轧钢板冲压下料——退火——校直——铣或刨侧 面——粗磨——半精磨——剁齿——淬火加回火。 技术条件检验方法 硬度HRC60-62,HB≤207 洛氏硬度计,布氏硬度计 金相组 织 珠光体,马氏体和 渗碳体 金相观察 力学性 能 硬度:退火,≤ 207HB,压痕直径≥ 4.20mm;淬火:≥ 62HRC 布氏法,洛氏法 工 序号工序名称设备 装炉方式 及数量 加热温 度℃ 保温 时min 冷却 介 质 温 度 ℃ 冷却时间 min 1 预热加热炉- 550-65 加热 时间 的5-6 倍 - - - 2 球化退火退火炉- 760-77 0 2-4h 空 气 550 -60 4h 3 淬火保护气 氛炉- 770-78 - 水150 -20 10 4 低温回火回火炉- 160-18 0 0.75- 1h 空 气 150 60 编制人陈博编制日期2013.12.11 审核日期
模具材料与热处理(复习题)
复习题与思考题 课题一金属材料的力学性能 (—)填空题 1. 机械设计常用和两种强度指标。 3.冲击韧性的符号是;延伸率的符号是;屈服强度的符号是。5.材料主要的力学性能有、、、、和。 (二)判断题 1.材料硬度越低,其切削加工性能就越好。() () 4.各种硬度值之间可以互换。() 6.硬度是材料对局部变形的抗力,所以硬度是材料
的塑性指标。() (三)选择题 1 低碳钢拉伸试验时,其变形过程可简单分为几个阶段。 A.弹性变形、塑性变形、断裂B.弹性变形、断裂 C 塑性变形、断裂D.弹性变形、条件变形、断裂3.材料开始发生塑性变形的应力值叫做材料的 A.弹性极限B屈服强度 C 抗拉强度D条件屈服强度 4.测量淬火钢件及某些表面硬化件的硬度时,一般应用 A.<160HB B.>230HB C.(160~230)HB D.(60~70)HRC 问答题 1 零件设计时,选取σ0. 2 (σs)还是选取σb,应以什么情况为依据? 2.在测定强度指标时,σs和σ0.2有什么不同? 3.常用的测量硬度方法有几种?其应用范围如何? 课题二铁碳合金组织观察 (一)填空题 1.表示晶体中原子排列形式的空间格子叫做,而晶胞是指。 2. 实际金属存在有、和三种缺陷。位错是
缺陷。 10.金属常见的晶格类型是、、。 3. α-Fe、γ-Fe、Al、Cu、Ni、Pb、Cr、V、Mg、Zn中属于体心立 方晶格的有,属于面心立方晶格的有,属于密排六方晶格的有。 4.同素异构转变是指。纯铁在温度发生和多晶型转变。 (二)判断题 1.纯铁加热到912℃时将发生α-Fe向γ-Fe的转变,( ) 2.在室温下,金属的晶粒越细,则其强度愈高和塑性愈低。( ) 3.金属具有美丽的金属光泽,而非金属则无此光泽,这是金属与非金属的根本区别。 纯金属的结晶 (一) 填空题 1.金属结晶的基本过程是和 2 在金属学中,通常把金属从液态向固态的转变称为, 3.当对金属液体进行变质处理时,变质剂的作用是 (二) 判断题 1. 凡是由液态金属冷却结晶的过程都可分为两个阶段。即先形核,形
模具钢的处理
模具钢的处理 模具钢材的热处理方式与加工工序安排密切相关。在模具制造时,应当根据材料和加工工艺路线来选择热处理方法,制定相应得热处理工艺。 (1)一般冷作模具钢工作零件的热处理工序安排:筹造——退火——机械加工成型——淬火与回火—工修整。 (2)冷作模具钢采用成型磨削及电加工工艺:锻造——退火——机械粗加工——淬火或回火——精加工(磨削、电加工)。 (3)冷作模具钢复杂冲模的加工:锻造——退火——机械粗加工——高温回火或调质——机械加工成型——淬火与回火——磨削与电工加工成型。 大多数冷作模具钢使用状态为淬火与回火,模具硬度通常为60hrc,为了进一步提高模具表面硬度、耐磨性和使用寿命,常进行表面强化处理,如渗碳、渗氮、渗硼氮碳共渗、td 法渗钒铌、化学气相村积(cvd)等作为最终热处理。 模具热处理 模具制造的成本高,特别是一些精密复杂的冷冲模、塑料模、压铸模等。采用热处理技术提高模具的使用性能,可以大幅度提高模具寿命,有显著的经济效益,我国模具技术工作者十分重视模具热处理技术的发展。 1 真空热处理 模具钢经真空热处理后有良好的表面状态,变形小。与大气下的淬火比较,真空油淬后模具表面硬化比较均匀,而且略高一些,主要原因是真空加热时,模具钢表面呈活性状态,不脱碳,不产生阻碍冷却的氧化膜。在真空下加热,钢的表面有脱气效果,因而具有较高的力学性能,炉内真空度越高,抗弯强度越高。真空淬火后,钢的断裂韧性有所提高,模具寿命比常规工艺普遍提高40%~400%,甚至更高。冷作模具真空淬火技术已得到较广泛的使用。 2 深冷处理 近年来的研究工作表明,模具钢经深冷处理(-196℃),可以提高其力学性能,一些模具经深冷处理后显著提高了使用寿命。模具钢的深冷可以在淬火和回火工序之间进行,也可在淬火回火之后进行深冷处理。如果在淬火、回火后钢中仍保留有残余奥氏体,则在深冷处理后仍需要再进行一次回火。深冷处理能提高钢的耐磨性和抗回火稳定性。深冷处理不仅用于冷作模具,也可用于热作模具和硬质合金。深冷处理技术已越来越受到模具热处理工作者的关注,已开发出专用深冷处理设备。不同钢种在深冷过程中的组织变化及其微观机制及其对力学性能的影响,尚需进一步研究。 3 模具的高温淬火和降温淬火 一些热作模具钢,如3Cr2W8V、H13、5CrNiMo、5CrMnMo等,采用高于常规淬火温度加热淬火,可以减少钢中碳化物的数量、改善其形态和分布,使固溶于奥氏体中碳的分布均匀化,淬火后可在钢中获得更多的板条马氏体,提高其断裂韧性和冷热疲劳抗力,从而延长模具使用寿命。例如3Cr2W8V钢制的一种热挤压模具,常规淬火温度为1080~1120℃,回火温度为560~580℃。当淬火温度提高至1200℃,回火温度为680℃(2次),模具寿命提高了数倍。 W6Mo5Cr4V2、W18Cr4V高速钢和Cr12MoV等高合金冷作模具钢,可适当降低其淬火温度,以改善其塑韧性,减少脆性开裂倾向,从而提高模具寿命。例如W6Mo5Cr4V2的淬火温度可选用1140~1160℃。 4 化学热处理 化学热处理能有效地提高模具表面的耐磨性、耐蚀性、抗咬合、抗氧化性等性能。几乎
模具材料及热处理
模具材料及热处理 1.金属组织 1.1金属 具有不透明、金属光泽良好的导热和导电性并且其导电能力随温度的增高而减小,富有延性和展性等特性的物质。金属内部原子具有规律性排列的固体(即晶体)。 1.2合金 由两种或两种以上金属或金属与非金属组成,具有金属特性的物质。 相:合金中成份、结构、性能相同的组成部分。 1.3固溶体 是一个(或几个)组元的原子(化合物)溶入另一个组元的晶格中,而仍保持另一组元的晶格类型的固态金属晶体,固溶体分间隙固溶体和置换固溶体两种。 1.4固溶强化 由于溶质原子进入溶剂晶格的间隙或结点,使晶格发生畸变,使固溶体硬度和强度升高,这种现象叫固溶强化现象。 1.5化合物 合金组元间发生化合作用,生成一种具有金属性能的新的晶体固态结构。 1.6机械混合物 由两种晶体结构而组成的合金组成物,虽然是两面种晶体,却是一种组成成分,具有独立的机械性能。 2.金属硬度 2.1硬度 金属的硬度,是指金属表面局部体积内抵抗外物压入而引起的塑性变形的抗力,硬度越高表明金属抵抗塑性变形的能力越强,金属产生塑性变形越困难。硬度试验方法简单易行,又无损于零件。实际常使用的硬度试验方法有:布氏硬度、洛氏硬度和维氏硬度三种。三种硬度试验值有大致的换算关系,见表一。布氏硬度HB:布氏硬度是用载荷为P的力把直接D的钢球压入金属表面,并保持一定的时间,测量金属表面上的压痕直径d,据此计算出的压痕面积AB,求出每单位面积所受力,用作金属的硬度值,叫布氏硬度,记作HB。布氏硬度的使用上限是HB450,适用于测定退火、正火、调质钢、铸铁及有色金属的硬度。 2.1.1洛氏硬度HRA、HRC: 洛氏硬度是工业生产中最常用的硬度测量的方法,因为操作简便、迅速,可以直接读出硬度值,不损伤工件表面,可测量的硬度范围较宽。但洛氏硬度也有一些缺点,如因压痕小,对材料有偏析及组织不均匀的情况,测量结果分离度大,再现性较差。洛氏硬度(HR)也是用压痕的方式试验硬度。它是用测量凹陷深度来表示硬度值。洛氏硬度试验用的压头分硬质和软质两种。硬质压头为顶角为120o的金刚石圆锥体,使用于淬火钢等硬的材料。HRA硬度有效范围是>70,适用于硬质合金、表面淬火层及渗碳层;HRC硬度有效范围是20-68(相当于HB230-700,HB450-700超出了布氏硬度的使用上限),适用于淬火钢及调质钢。2.1.2洛氏硬度HRB 洛氏硬度HRB的测量采用直径1.588mm(1/16")的钢球,适用于退火钢、有色金属等,硬度有效范围是25-100(相当于HB60-230)。 2.1.3维氏硬度HV 维氏硬度也是利用压痕面积上单位应力作为硬度值计量。维氏硬度所使用的压头是锥面夹角为136o的金刚石四方锥体。试验时,在载荷P的作用下,在试样试验面上压出一个正方形压痕。测量压痕两对角线的平均长度d,借以计算压痕面积AV,以P/AV的数值表示试样的硬度,以HV表示。维氏硬度的优缺点:维氏硬度有一个连续一致的标度;试验负荷可任意选择,所得的硬度值相同。试验时加载的压力小,压入深度浅,对工件损伤小。特别适用于测量零件的表面淬硬层及经过表面化学处理的硬度,精度比布氏、洛氏硬度精确。但是维氏硬度的试验操作较麻烦,一般在生产上很少使用,多用于实验室及科研方面。 2.1.4硬度值对照表:
42CrMo热处理生产工艺卡
42CrMo热处理生产工艺卡 一、钢管规格、钢级、工艺、订单号及执行标准 219*23 42CrMo 淬火+回火 rzg-0517 XTG-RZ-C-067-2014 单支交货长度5300mm 二、生产工艺流程 生产准备→淬火炉→淬火机→回火炉→定径机→冷床→矫直机→冷床→标记→取样。三、热处理生产工艺 控制参数 一、淬火炉 淬火炉加热段温度℃880±14℃ 淬火炉均热段温度℃870±14℃ 布料方式连续布料 步进时间97秒(加热时间80分钟) 二、淬火机床 淬火方式外淋水关闭,采用内喷浸入式 浸入水量开启3台水泵 内喷水量开启2台水泵(1台低频 1台工频) 淬火时间(48s)45秒(淬后管温50-70度) 喷嘴规格D160mm 拖轮转速40rpm 翻料延时5s 浸入延时8s 淬火高度250mm 三、回火炉 回火炉加热段温度℃565±7℃ 回火炉均热段温度℃560±7℃ 回火炉保温段温度℃560±7℃ 布料方式连续布料 步进时间97秒(加热时间121分钟) 注意事项: 1、淬火炉和回火炉各区炉温按中限控制,特别注意回火温度实时调整,保证炉温均匀一致。 2、淬火后钢管内外表温控制在50-70℃,测试管温全长一致性。 3、淬火后钢管应及时回火,严禁淬水后停留时间超过15分钟。 4、调快定径机后冷床速度,保证矫直前钢管温度≥400℃,钢管矫后冷床来回转动。 5、取样前平头50mm,每批截取220mm管环试样,委托拉伸、化学成分、冲击(纵向、常温、U口)、交货硬度、晶粒度、非金属夹杂。每批取2个试样,取样位置为不同的支头尾。 6、取样时应注意交货长度要求,严禁取短尺事故发生。 编制:审阅:批准:
模具材料与热处理论文
冲压模具材料的分类及强化处理技术 [摘要] :随着现代制造技术的不断进步,尤其是汽车、电子、航空工业的快速发展,越来越多的产品要求模具在高温、高速条件下工作且具有高的耐磨性、抗氧化性等,在一定程度上给模具制造业带来了挑战。文章从常用冲压模具材料的种类、冲压模具材料的合理选择对热处理的影响、冲压模具表面处理技术等方面出发,对常用冲压模具材料的分类及处理技术进行相应分析。 [关键词] :冲压模具材料;热处理;表面处理;模具材料性能 模具作为工业生产的重要工艺设备,在其实际应用过程中,具有生产效率高、材料利用率高、制件精度高、复杂程度高等优势,这些是其它加工制造技术无法比拟的。模具生产技术已经广泛应用在汽车、电子、机械、仪表、家电、航空等行业中。在很长一段时间内,模具作为重要工艺设备极大的促进了生产的发展,但是随着模具种类的不断增多,形状越来越复杂,加工工艺越来越困难,再加上热处理技术的限制,模具技术的发展速度逐渐缓慢,并出现各种质量问题。在这种情况下,有必要对模具材料的种类进行分析并选取合适的模具材料以及对应的处理技术,确保模具质量。 1 常见冲压模具材料的种类及性能 1.1 常见冲压模具材料种类 常见冲压模具材料主要包括碳素工具钢、低合金工具钢、高碳高
铬工具钢、高速钢、基体钢、硬质合金和钢结硬质合金等。其中,碳素工具钢价格便宜、加工性能较好,热处理后硬度高、耐磨性好。一般在尺寸较小、形状简单且承受荷较小的模具零件中使用;低合金工具钢是在碳素工具钢基础上加入适量的合金元素而形成的。它的优势是能有效的降低淬火冷却速度,将热应力和组织应力降至最低,同时减小淬火变形和降低开裂倾向;高碳高铬工具钢不仅具有高硬度、高强度、高耐磨性优势,还具有较好的淬透性、淬硬性、高稳定性等优势,热处理变形很小;高速钢硬度较高,还具有较高的抗压强度和耐磨性,通常采用快速加热和低温淬火工艺,在一定程度上改善了材料的韧性。但是高速钢中的合金元素含量较高、成本高、脆性较大,再加上其工艺性能不佳,不能广泛应用在工业生产中;基体钢是在高速钢的基础上添加少量的其它元素,在具有高速钢好的耐磨性和硬度的前提下,其抗弯强度和韧性均有所提高。一般用于制造冷挤压、冷镦模具;硬质合金一般具有较高的硬度和耐磨性,而钢结硬质合金的性能更佳,它是以铁粉加入少量的合金元素粉末做粘合剂,以碳化钛、碳化钨等材料作为硬质相,用粉末冶金的方法烧结而成,用这种材料制作的模具坚固耐用,适合在大批量生产用模具上应用。 1.2模具材料性能 在模具材料的选用过程中,必须充分了解材料的使用性能和工艺性能。模具使用性能主要包括强度、硬度、韧性、耐磨性、抗疲劳性等。强度是材料抵抗变形能力和断裂能力的指标;硬度的高低将直接影响模具的使用寿命,对模具质量有重要影响;韧性反映材料在较强
(数控模具设计)模具材料及热处理精编
(数控模具设计)模具材料 及热处理
模具材料及热处理 1.金属组织 1.1金属 具有不透明、金属光泽良好的导热和导电性且且其导电能力随温度的增高而减小,富有延性和展性等特性的物质。金属内部原子具有规律性排列的固体(即晶体)。 1.2合金 由俩种或俩种之上金属或金属和非金属组成,具有金属特性的物质。 相:合金中成份、结构、性能相同的组成部分。 1.3固溶体 是壹个(或几个)组元的原子(化合物)溶入另壹个组元的晶格中,而仍保持另壹组元的晶格类型的固态金属晶体,固溶体分间隙固溶体和置换固溶体俩种。 1.4固溶强化 由于溶质原子进入溶剂晶格的间隙或结点,使晶格发生畸变,使固溶体硬度和强度升高,这种现象叫固溶强化现象。 1.5化合物 合金组元间发生化合作用,生成壹种具有金属性能的新的晶体固态结构。 1.6机械混合物 由俩种晶体结构而组成的合金组成物,虽然是俩面种晶体,却是壹种组成成分,具有独立的机械性能。 2.金属硬度 2.1硬度 金属的硬度,是指金属表面局部体积内抵抗外物压入而引起的塑性变形的抗力,硬度越高表明金属抵抗塑性变形的能力越强,金属产生塑性变形越困难。硬度试验方法简单易行,
又无损于零件。实际常使用的硬度试验方法有:布氏硬度、洛氏硬度和维氏硬度三种。三种硬度试验值有大致的换算关系,见表壹。 布氏硬度HB:布氏硬度是用载荷为P的力把直接D的钢球压入金属表面,且保持壹定的时间,测量金属表面上的压痕直径d,据此计算出的压痕面积AB,求出每单位面积所受力,用作金属的硬度值,叫布氏硬度,记作HB。布氏硬度的使用上限是HB450,适用于测定退火、正火、调质钢、铸铁及有色金属的硬度。 2.1.1洛氏硬度HRA、HRC: 洛氏硬度是工业生产中最常用的硬度测量的方法,因为操作简便、迅速,能够直接读出硬度值,不损伤工件表面,可测量的硬度范围较宽。但洛氏硬度也有壹些缺点,如因压痕小,对材料有偏析及组织不均匀的情况,测量结果分离度大,再现性较差。洛氏硬度(HR)也是用压痕的方式试验硬度。它是用测量凹陷深度来表示硬度值。洛氏硬度试验用的压头分硬质和软质俩种。硬质压头为顶角为120o的金刚石圆锥体,使用于淬火钢等硬的材料。HRA硬度有效范围是>70,适用于硬质合金、表面淬火层及渗碳层;HRC硬度有效范围是20-68(相当于HB230-700,HB450-700超出了布氏硬度的使用上限),适用于淬火钢及调质钢。 2.1.2洛氏硬度HRB 洛氏硬度HRB的测量采用直径1.588mm(1/16")的钢球,适用于退火钢、有色金属等,硬度有效范围是25-100(相当于HB60-230)。 2.1.3维氏硬度HV 维氏硬度也是利用压痕面积上单位应力作为硬度值计量。维氏硬度所使用的压头是锥面夹角为136o的金刚石四方锥体。试验时,在载荷P的作用下,在试样试验面上压出壹个正方形压痕。测量压痕俩对角线的平均长度d,借以计算压痕面积AV,以P/AV的数值表示试样的硬度,以HV表示。维氏硬度的优缺点:维氏硬度有壹个连续壹致的标度;试验负荷可
机械加工工艺过程卡及工序卡
机械加工工艺过程卡及 工序卡 集团标准化小组:[VVOPPT-JOPP28-JPPTL98-LOPPNN]
机械加工工艺过程卡填写说明
(1)过程卡和工序卡的总页数; (2)当前页页序; (3)按零件图填写; (4)按设计任务书填写,包括了备品率和废品率; (5)按零件图填写; (6)填写“铸件”、“锻件”、“圆钢”、“板钢”等;(7)每毛坯可加工同一零件的数量; (8)工序号,可依自然数连续或不连续编号; (9)工序名称如“钻××孔”、“粗铣××面”、“攻××螺纹”等; (10)填写设备名称如“立钻”; (11)填写设备型号如“Z5125A”; (12)填写该工序所需设备数量; (13)基本时间t m和辅助时间t a之和,也称为操作时间。基本时间取自工序卡。辅助时间按工序卡所表明的工序操作动作,查各动作的时间定额标准并累加得到(未见占基本时间百分比数据); (14)工时定额t t按公式t t=(t m+t a)[1+(α+β)﹪]计算。其中布置工作地时间、休息和生理需要时间按它们占作业时间的百分比((α+β)﹪)查表得到,不计准备和终结时间; (15)设备负荷率=(13)×(4)÷(251天×8小时×60分×(12)); (16)根据需要填写。
机械加工工序卡填写说明 卡相应内容的说明; (2)采用的切削液名称,如“水”、“水溶液”、“乳化液”等; (7)工序简图。要求:①主要简图是零件在机床上装夹位置的主视图,应有零件的外形轮廓,与本工序无关的结构要素不表示。②完整表示工序定位基准、夹压力方向和作用面、夹压方式(机械夹紧、液压夹紧、气动夹紧、电磁夹紧),也可规定夹压位置。③用特粗线条表示出加工面,注明工序尺寸及公差、加工面的相对位置精度、表面粗糙度等。④表示工序同时装夹零件的数目和排列方式。⑤若绘制简图的位置不够,可另页绘制(该页上保留工序卡表头,其它位置绘简图),顺序在本工序卡片之后,有页码。 (8)若需要专用夹具,填写夹具名称,如“钻夹具”。否则不填; (9)本工序工序内容序号,依自然数连续编号;要技术要求,如热处理的硬度和变形要求、电镀的镀层厚度。设计或工艺要求加工面配做配钻时,要在配做配钻前该面的最后工序另起一行注明,如“××孔与××件配钻”; (11)填写设备型号如“Z5125A”; (12)专用的填写编号,由于没有编号规则,可填写刀辅具名称,并示以“专用”含义,如“成形铣刀”。标准的填写名称、规格,如“锥柄钻头Φ14.3×200”、“45°车刀”; (13)填写量检具名称,如“孔位检具”、“卡规”等,已有“专用”含义。标准的填写名称、规格、精度,如“卡尺 0~125,0.02”、“杠杆表0~0.8,0.01”。 (14)、(15)、(16)、(17)切削用量三要素,由分析计算或查表得到。 (18)工件切削部分的长度; (19)直接改变加工对象几何状况或材料性质的工艺过程所消耗的时间,用相应加工方法基本时间计算公式计算。切削加工时,
模具钢常用到的热处理方法,及其作用
模具钢常用到哪些热处理方法?其作用是什么? 发布时间:2012/2/13 资讯来源:A-lancy 发布企业:金属表面处理的方法热处理就是将钢在固态下施以不同的加热、保温和冷却,以改变其内部组织结构,获得所需性能的一种加工工艺。模具制造过程中常用到的热处理方法有:退火、正火、淬火,回火、调质、渗碳、氮化处理。 ⑴退火处理 退火是将金属或合金表面加热到适当的温度,保温到一定的时间,然后随炉缓慢冷却的热处理的工艺,其实质是将钢加热到奥氏体化后进行珠光体转变。 ①退火作用 a. 降低钢的表面硬度,提高塑性,以利于切削加工及冷变变形加工; b. 细化晶粒,消除因锻、焊等引起的组织缺陷,使钢的组织成分均匀,改善钢的性能活为以后的热处理做准备; c. 消除钢的内应力,以防止变形或开裂。 ②退火方法常用的退火方法有完全退火、球化退火、去应力退火、再结晶退火、扩散退火和等温退火等。 a. 完全退火又称中结晶退火,是将铁碳合金完全奥氏体化,随之缓慢的冷却,获得接近平衡状态组织的退火工艺,适用于含碳量为0.3% ~0.6%的中碳钢和中碳合金钢。
b. 球化退火使钢中碳化物球状化而进行的退火工艺。常用的球化退火有普通球化退火和等温球化退火两种,此工艺主要用于共析钢和过析钢的模具、量具和刃具钢等。 c. 去应力退火为了去除由于塑性变形加工、锻造、焊接等造成的参与应力及锻件内存在的残余应力而进行的退火工艺。 d. 再结晶退火又称中间退火,是指经冷形变后的金属加热再结晶温度以上,保持适当的时间,使变形晶粒重新结晶成均匀的等抽晶粒,以消除变强化和残余应力的热处理工艺。 e. 等温退火就是将钢件或毛坯加热到高于Ac3(或Ac1)温度,保持适当时间后,较快的冷却到珠光体温度区间的某一温度并等温保持,使奥氏体转变为珠光体组织,然后再空气中冷却的热处理工艺,此种退火方法主要用于冷奥氏体Ac比较稳定的合金钢。 ⑵正火处理 正火是将钢材或钢件加热到Ac3以上表面30 ~50℃,保温适当时间后,在静止的空气中冷却的热处理工艺。正火的作用: a. 可消除过共析钢中的网状碳化物,改善钢的切削加工性能; b. 细化过热铸、锻件晶粒和消除内应力; c. 对含碳量小于0.4%的中、低碳钢可用正火代替退火做预先热处理; d. 含碳量在0.4% ~0.7%的不太重要的工作可在正火状态下使用。 ⑶淬火处理
关于模具热处理的一些经验
关于模具热处理的一些经验分享~ 2016-01-01 1. H13模具钢如何热处理硬度才能达到58度? 进行1050~1100度加热淬火,油淬,可以达到要求,但一般热作模具是不要求这么高的硬度的,这么高的硬度性能会很差,不好用,一般在HRC46~50左右性能好、耐用。 2. 模具热处理过后表面用什么洗白? 问题补充:我是开模具抛光店的,一般模具都用油石先打过再拿去渗氮,渗氮回来又要用油石把那一层黑的擦白,再抛光很麻烦,不擦白打不出镜面来,材料有H13 的,有进口的好多种,如果有药水能洗白的话,就可以直接抛光了。 (1)可以用不锈钢酸洗液,或者盐酸清洗。喷砂处理也可以。磨床磨的话费用高,而且加工量大,有可能使尺寸不达标的。盐酸洗不掉的话,估计您用的是高铬的模具钢?是D2还是H13?高铬模具钢的氧化层比较难洗掉。用不锈钢酸洗液应该可以,磨具商店或者不锈钢商店都有卖的。 (2)你们没有不锈钢酸洗膏吗?那种可以。H13这类含铬比较高的模具钢,氧化层是难以用盐酸洗掉的。还有一个办法,我自己也在用。你们的模具既然已经油石磨过,表面就是比较光滑的。实际上,可以先只用粗的油石打磨,或者用
砂带打磨,之后就去热处理。回来之后再用细油石打磨。而我用的办法是,用纤维轮先打磨,就可以有效的把黑皮去除,再研磨抛光。或者喷砂,用800 目的碳化硼做一遍喷砂试试,应该就能够去除黑皮,还不需要化太多功夫重磨。 3.热处理厂对金属是怎么热处理的? 热处理厂的设备非常多,炉子大概有箱式炉,井式炉,箱式炉用的最多,很多热处理都可以在这里面处理,比如退火,正火和淬火的加热过程,回火这些常见的热处理。 其实就是一个用电加热的炉子,先将炉子升温到预定温度,然后把工件丢进去,等待一段时间到预定温度,然后保温一段时间,然后取出,或者在炉子里一起冷却,井式炉一般是作为渗碳处理设备,是一个埋到地下的炉子,工件放进去之后,密封,然后往炉子里面滴入一些富碳液体,比如煤油或则甲醇,然后在高温下这些液体分解成碳原子渗入工件表面。 淬火池是淬火的场所,就是一个池子,里面有水溶液或者是油,就是箱式炉出来的工件淬火的冷却的地方,一般就是直接丢进去,然后等一段时间捞出来。还有其他的一些设备,比如高频机,就是一个可以将50 赫兹的工频电变成一个200K 赫兹电流的超大功率的设备,比如常见的有200 千瓦的最大功率,然后用一个内部通冷却水的铜管做的线圈放在工件的外面,一般几十毫米的工件,几秒种到十几秒的时候你就看到工件表面变红,表面温度到预定值的时候,然后有一个水套升上来喷淬火液到工件表面,完成淬火过程。常见的就这些了。 4.我们最近的Cr12 或Cr12MoV 的材料热处理和裂了几次了,为什么