煤气化技术中shell与GSP气化炉对比

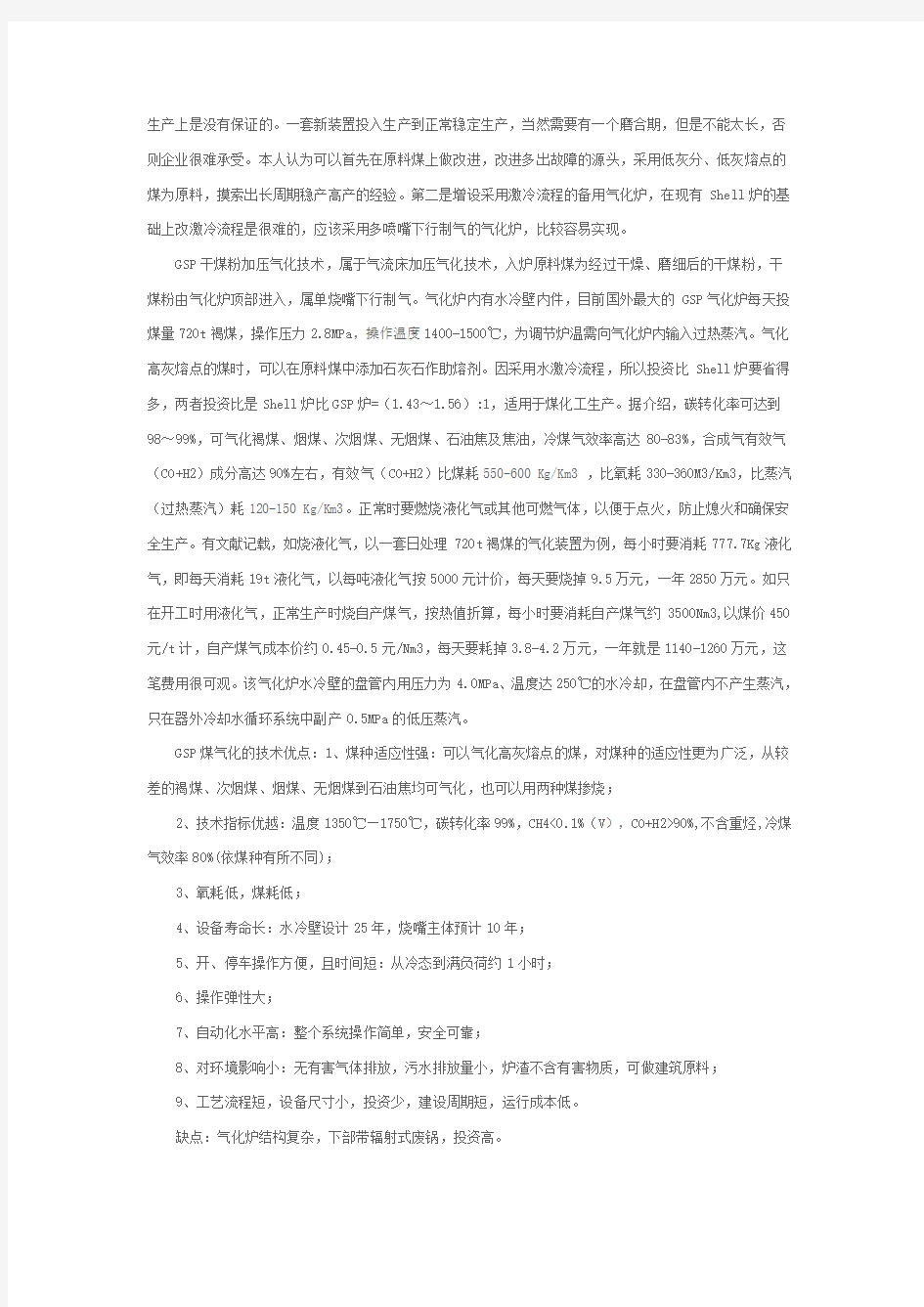
煤气化技术中shell与GSP气化炉对比
来源:编辑:阿勇发布时间:2013-04-03访问量:44次字体大小:大中小壳牌(Shell)干煤粉加压气化技术,属于气流床加压气化技术。可气化褐煤、烟煤、无烟煤、石油焦及高灰熔点的煤。入炉原料煤为经过干燥、磨细后的干煤粉。干煤粉由气化炉下部进入,属多烧嘴上行制气。目前国外最大的气化炉日处理2000t煤,气化压力为3.0MPa,国外只有一套用于商业化联合循环发电的业绩,尚无更高气化压力的业绩。这种气化炉是采用水冷壁,无耐火砖衬里。采用废热锅炉冷却回收煤气的显热,副产蒸汽,气化温度可以达到1400-1600℃,气化压力可达3.0-4.0MPa,可以气化高灰熔点的煤,但仍需在原料煤中添加石灰石作助熔剂。
该种炉型原设计是用于联合循环发电的,国内在本世纪初至今已签订技术引进合同的有19台气化炉装置,其最终产品有合成氨、甲醇,气化压力3.0-4.0MPa。其特点是干煤粉进料,用高压氮气气动输送入炉,对输煤粉系统的防爆要求严格;气化炉烧嘴为多喷嘴,有4个对称式布置,调节负荷比较灵活;为了防止高温气体排出时夹带的熔融态和粘结性飞灰在气化炉后的输气导管换热器、废热锅炉管壁粘结,采用将高温除灰后的部分300-350℃气体与部分水洗后的160-165℃气体混合,混合后的气体温度约200℃,用返回气循环压缩机加压送到气化炉顶部,将气化炉排出的合成气激冷至900℃后,再进入废热锅炉热量回收系统。返回气量很大,相当于气化装置产气量的80-85%,对返回气循环压缩机的操作条件十分苛刻,不但投资高,多耗动力,而且出故障的环节也多;出废热锅炉后的合成气,采用高温中压陶瓷过滤器,在高温下除去夹带的飞灰,陶瓷过滤器不但投资高,而且维修工作量大,维修费用高。废热锅炉维修工作量也大,故障也多,维修费用也高。据介绍碳转化率可达98-99%;可气化褐煤、烟煤、无烟煤、石油焦;冷煤气效率高达80-83%;合成气有效气(CO+H2)成分高达90%左右,有效气(CO+H2)比煤耗550-600Kg/Km3,比氧耗330-360M3/Km3(用河南新密煤时,比煤耗为709Kg/Km3。比氧耗为367.2Nm3/ Km3。所以在这里要说明一点,无论那一种煤气化技术,资料上介绍的比煤耗和比氧耗都是在特定条件下的数据,确切的数据,应该在煤试烧后方能获得,在做方案比较的时候可以用气化工艺计算的方法求得,要在同一个煤种的数据上作评价的依据。);比蒸汽耗120-150Kg/Km3;可副产蒸汽880-900Kg/Km3。
我国采用Shell干煤粉加压气化工艺的装置自2006年开始,陆续投料试生产的,已有好几家,但是至今尚未达到长周期稳定正常生产。主要的原因是系统流程长,设备结构复杂。当采用高灰分、高灰熔点的煤进行气化时。就会出现水冷壁能否均匀挂渣的问题、气化炉顶输气管和废热锅炉积灰问题、高温高压干法飞灰过滤器除尘效率和能力问题、每天产生的大量飞灰出路问题、激冷气压缩机故障多的问题、水洗冷却除尘的黑水系统故障问题。该工艺第一次用于化工(尤其是制合成氨、制甲醇、制氢),其除尘净化、长周期稳定正常生产的要求程度,远高于发电,用于发电尚有燃油(或天然气)发电可作为备用发电,而现在用于化工生产,一个大型企业只设1套设备结构复杂、控制系统要求高的煤气化装置,不设备用炉,
生产上是没有保证的。一套新装置投入生产到正常稳定生产,当然需要有一个磨合期,但是不能太长,否则企业很难承受。本人认为可以首先在原料煤上做改进,改进多出故障的源头,采用低灰分、低灰熔点的煤为原料,摸索出长周期稳产高产的经验。第二是增设采用激冷流程的备用气化炉,在现有Shell炉的基础上改激冷流程是很难的,应该采用多喷嘴下行制气的气化炉,比较容易实现。
GSP干煤粉加压气化技术,属于气流床加压气化技术,入炉原料煤为经过干燥、磨细后的干煤粉,干煤粉由气化炉顶部进入,属单烧嘴下行制气。气化炉内有水冷壁内件,目前国外最大的GSP气化炉每天投煤量720t褐煤,操作压力2.8MPa,操作温度1400-1500℃,为调节炉温需向气化炉内输入过热蒸汽。气化高灰熔点的煤时,可以在原料煤中添加石灰石作助熔剂。因采用水激冷流程,所以投资比Shell炉要省得多,两者投资比是Shell炉比GSP炉=(1.43~1.56):1,适用于煤化工生产。据介绍,碳转化率可达到98~99%,可气化褐煤、烟煤、次烟煤、无烟煤、石油焦及焦油,冷煤气效率高达80-83%,合成气有效气(CO+H2)成分高达90%左右,有效气(CO+H2)比煤耗550-600 Kg/Km3 ,比氧耗330-360M3/Km3,比蒸汽(过热蒸汽)耗120-150 Kg/Km3。正常时要燃烧液化气或其他可燃气体,以便于点火,防止熄火和确保安全生产。有文献记载,如烧液化气,以一套日处理720t褐煤的气化装置为例,每小时要消耗777.7Kg液化气,即每天消耗19t液化气,以每吨液化气按5000元计价,每天要烧掉9.5万元,一年2850万元。如只在开工时用液化气,正常生产时烧自产煤气,按热值折算,每小时要消耗自产煤气约3500Nm3,以煤价450元/t计,自产煤气成本价约0.45-0.5元/Nm3,每天要耗掉3.8-4.2万元,一年就是1140-1260万元,这笔费用很可观。该气化炉水冷壁的盘管内用压力为4.0MPa、温度达250℃的水冷却,在盘管内不产生蒸汽,只在器外冷却水循环系统中副产0.5MPa的低压蒸汽。
GSP煤气化的技术优点:1、煤种适应性强:可以气化高灰熔点的煤,对煤种的适应性更为广泛,从较差的褐煤、次烟煤、烟煤、无烟煤到石油焦均可气化,也可以用两种煤掺烧;
2、技术指标优越:温度1350℃—1750℃,碳转化率99%,CH4<0.1%(V),CO+H2>90%,不含重烃,冷煤气效率80%(依煤种有所不同);
3、氧耗低,煤耗低;
4、设备寿命长:水冷壁设计25年,烧嘴主体预计10年;
5、开、停车操作方便,且时间短:从冷态到满负荷约1小时;
6、操作弹性大;
7、自动化水平高:整个系统操作简单,安全可靠;
8、对环境影响小:无有害气体排放,污水排放量小,炉渣不含有害物质,可做建筑原料;
9、工艺流程短,设备尺寸小,投资少,建设周期短,运行成本低。
缺点:气化炉结构复杂,下部带辐射式废锅,投资高。
(来源:中国庆华集团王瑗整理)
壳牌煤气化技术简介
主流煤气化技术及市场情况系列展示(之五) 壳牌煤气化技术 技术拥有单位:壳牌全球解决方案国际私有有限公司 壳牌是世界知名的国际能源公司之一。壳牌煤气化技术可以处理石油焦、无烟煤、烟煤、褐煤和生物质。气化炉的操作压力一般在,气化温度一般在1400~1700摄氏度。在此温度压力下,碳转化率一般会超过99%,冷煤气效率一般在80~83%。对于废热回收流程,合成气的大部分显热可由合成气冷却器回收用来生产高压或中压蒸汽;如配合采用低水气比催化剂的变化工艺,在变换单元消耗少量蒸汽即可保证变换深度要求,剩余大量蒸汽可送入全厂蒸汽管网,获得可观的经济效益。 目前,壳牌全球解决方案国际私有有限公司负责壳牌气化技术的技术许可,工艺设计以及技术支持。2007年壳牌成立了北京煤气化技术中心,2012年初,壳牌更是将其全球气化业务总部也从荷兰移师中国,这充分体现了壳牌对中国现代煤化工蓬勃发展的重视,同时壳牌也能更好地利用其全球气化技术能力,贴近市场,为中国客户提供更加快捷周到的技术支持。目前,在北京的壳牌煤气化技术团队可提供从研发、工程设计、培训、现场技术支持以及生产操作和管理的全方位技术支持和服务。 一、整体配套工艺 根据不同的煤质特性以及用户企业的不同生产需求和规划,壳牌开发了下面3种不同炉型: 壳牌废锅流程是当前工业应用经验最丰富的干粉气化技术。它的效率和工艺指标的先进性已经得到了验证和认可,而且在线率也在不断创造新的世界纪录,大部分客户已实现满负荷、长周期、安全、稳定运转。如果业主比较关注热效率,全厂能效和环保效益的话,采用壳牌废锅流程并配合已成功应用的低水气比变换技术应该是最合适稳妥的方案。 壳牌上行水激冷流程特别适合处理有积垢倾向的煤种;适合大型项目,此外投资低,可靠性高。对于比较关注在线率和低投资的业主,采用壳牌上行水激冷流程应该是最合适稳妥的方案。
四种煤气化技术及其应用
四种煤气化技术及其应用 李琼玖,钟贻烈,廖宗富,漆长席,周述志,赵月兴 (成都益盛环境工程科技公司,四川成都610012) 摘要:介绍了4种煤气化工艺技术,包括壳牌工艺、德士古水煤浆气化工艺、恩德工艺、灰熔聚流化床气化工艺,对其技术特点、工艺流程、主要设备及应用实例进行了详细阐述,并对4种工艺进行了对比。 关键词:煤气化;壳牌工艺;德士古;恩德工艺;灰熔聚工艺;煤气炉 中图分类号:TQ546文献标识码:A文章编号:1003-3467(2008)03-0004-04 Four Coal Gasification Technologi es and Their Applicati on L I Q iong-ji u,ZHONG Y i-lie,LIAO Zong-fu, QI Chang-xi,ZHOU Shu-zhi,ZHAO Yue-xing (Chengdu Y i s heng Envir on m ent Eng i n eering Techo logy C o.Ltd,Chengdu610012,China) Abst ract:Four coal gasificati o n technologies,inc l u d i n g Shell techno logy,Texaco coa l-w ater sl u rry gasif-i cati o n,Enticknap pr ocess,ash agg l o m erati o n fl u i d ized bed gasification technology are intr oduced,and the technical features,technolog ical process,m ai n equipm ent and app lication exa m p le o f the four techno l o g i e s are descri b ed in detai.l K ey w ords:coal gasification;She ll techno logy;Texaco;Enticknap process;ash agglo m erati o n tech-nology;gas stove 1壳牌粉煤气化制取甲醇合成气 1.1壳牌工艺技术的特点 壳牌煤气化过程(SCGP工艺)是在高温加压下进行的,是目前世界上最为先进的第FG代煤气化工艺之一。按进料方式,壳牌煤气化属气流床气化,煤粉、氧气及蒸汽在加压条件下并流进入气化炉内,在极为短暂的时间内完成升温、挥发分脱除、裂解、燃烧及转化等一系列物理和化学过程。一般认为,由于气化炉内温度很高,在有氧存在的条件下,碳、挥发分及部分反应产物(H2、CO等)以发生燃烧反应为主;在氧气消耗殆尽之后发生碳的各种转化反应,过程进入到气化反应阶段,最终形成以CO、H2为主要成分的煤气离开气化炉。 壳牌粉煤气化的技术特点:1干煤粉进料,加压氮气输送,连续性好,气化操作稳定。气化温度高,煤种适应性广,从无烟煤、烟煤、褐煤到石油焦均可气化,对煤的活性几乎没有要求,对煤的灰熔点范围比其它气化工艺更宽。对于高灰分、高水分、含硫量高的煤种同样适应。o气化温度约1400~1700e,碳转化率高达99%以上,产品气体相对洁净,不含重烃,甲烷含量极低,煤气中有效气体(CO+H2)高达90%以上。?氧耗低,与水煤浆气化相比,氧气消耗低,因而与之配套的空分装置投资可减少。?单炉生产能力大,目前已投入运转的单炉气化压力为3MPa,日处理煤量已达2000t。?气化炉采用水冷壁结构,无耐火砖衬里,维护量少,气化炉内无转动部件,运转周期长,无需备炉。?热效率高,煤中约83%的热能转化在合成气中,约15%的热能被回收为高压或中压蒸汽,总的热效率为98%左右。?气化炉高温排出的熔渣经激冷后成玻璃状颗粒,性质稳定,对环境几乎没有影响。气化污水中含氰化合物少,容易处理,必要时可做到零排放,对环境保护十分有利。à壳牌公司专利气化烧嘴可根据需要选择,气化压力2.5~4.0M Pa,设计保证寿命为8000h,荷兰De m ko lec电厂使用的烧嘴在近4年 收稿日期:2007-10-13 作者简介:李琼玖(1930-),男,教授级高级工程师、研究员,长期从事化工设计、建设、生产工程技术工作,主编5合成氨与碳一化学6、5醇醚燃料与化工产品链工程技术6专著,发表论文百余篇,电话:(028)86782889。
壳牌煤气化
工艺原理 壳牌煤气化过程是在高温、加压条件下进行的,煤粉、氧气及少量蒸汽在加压条件下并流进入气化炉内,在极为短暂的时间内完成升温、挥发分脱除、裂解、燃烧及转化等一系列物理和化学过程。由于气化炉内温度很高,在有氧条件下,碳、挥发分及部分反应产物(H2和CO 等)以发生燃烧反应为主,在氧气消耗殆尽之后发生碳的各种转化反应,即气化反应阶段,最终形成以CO和H2为主要成分的煤气离开气化炉。 工艺流程 目前,壳牌煤气化装置从示范装置到大型工业化装置均采用废锅流程,激冷流程的壳牌煤气化工艺很快会推向市场。 原料煤经破碎由运输设施送至磨煤机,在磨煤机内将原料煤磨成煤粉(90%<100μm)并干燥,煤粉经常压煤粉仓、加压煤粉仓及给料仓,由高压氮气或二氧化碳气将煤粉送至气化炉煤烧嘴。来自空分的高压氧气经预热后与中压过热蒸汽混合后导入煤烧嘴。煤粉、氧气及蒸汽在气化炉高温加压条件下发生碳的氧化及各种转化反应。气化炉顶部约1500℃的高温煤气经除尘冷却后的冷煤气激冷至900 ℃左右进入合成气冷却器。经合成气冷却器回收热量副产高压、中压饱和蒸汽或过热蒸汽后的煤气进入干式除尘及湿法洗涤系统,处理后的煤气中含尘量小于1 mg/m3送后续工序。 湿洗系统排出的废水大部分经冷却后循环使用,小部分废水经闪蒸、沉降及汽提处理后送污水处理装置进一步处理。闪蒸汽及汽提气可作为燃料或送火炬燃烧后放空。 在气化炉内气化产生的高温熔渣,自流进入气化炉下部的渣池进行激冷,高温熔渣经激冷后形成数毫米大小的玻璃体,可作为建筑材料或用于路基。 技术特点 (1)煤种适应性广 对煤种适应性强,从褐煤、次烟煤、烟煤到无烟煤、石油焦均可使用,也可将2种煤掺混使用。对煤的灰熔点适应范围比其他气化工艺更宽,即使是较高灰分、水分、硫含量的煤种也能使用。 (2)单系列生产能力大 目前已投人生产运行的煤气化装置单台气化炉投煤量达到2000 t/d 以上。
煤气化技术的现状及发展趋势分析
煤气化技术是现代煤化工的基础,是通过煤直接液化制取油品或在高温下气化制得合成气,再以合成气为原料制取甲醇、合成油、天然气等一级产品及以甲醇为原料制得乙烯、丙烯等二级化工产品的核心技术。作为煤化工产业链中的“龙头”装置,煤气化装置具有投入大、可靠性要求高、对整个产业链经济效益影响大等特点。目前国内外气化技术众多,各种技术都有其特点和特定的适用场合,它们的工业化应用程度及可靠性不同,选择与煤种及下游产品相适宜的煤气化工艺技术是煤化工产业发展中的重要决策。 工业上以煤为原料生产合成气的历史已有百余年。根据发展进程分析,煤气化技术可分为三代。第一代气化技术为固定床、移动床气化技术,多以块煤和小颗粒煤为原料制取合成气,装置规模、原料、能耗及环保的局限性较大;第二代气化技术是现阶段最具有代表性的改进型流化床和气流床技术,其特征是连续进料及高温液态排渣;第三代气化技术尚处于小试或中试阶段,如煤的催化气化、煤的加氢气化、煤的地下气化、煤的等离子体气化、煤的太阳能气化和煤的核能余热气化等。 本文综述了近年来国内外煤气化技术开发及应用的进展情况,论述了固定床、流化床、气流床及煤催化气化等煤气化技术的现状及发展趋势。 1.国内外煤气化技术的发展现状 在世界能源储量中,煤炭约占79%,石油与天然气约占12%。煤炭利用技术的研究和开发是能源战略的重要内容之一。世界煤化工的发展经历了起步阶段、发展阶段、停滞阶段和复兴阶段。20世纪初,煤炭炼焦工业的兴起标志着世界煤化工发展的起步。此后世界煤化工迅速发展,直到20世纪中叶,煤一直是世界有机化学工业的主要原料。随着石油化学工业的兴起与发展,煤在化工原料中所占的比例不断下降并逐渐被石油和天然气替代,世界煤化工技术及产业的发展一度停滞。直到20世纪70年代末,由于石油价格大幅攀升,影响了世界石油化学工业的发展,同时煤化工在煤气化、煤液化等方面取得了显著的进展。特别是20世纪90年代后,世界石油价格长期在高位运行,且呈现不断上升趋势,这就更加促进了煤化工技术的发展,煤化工重新受到了人们的重视。 中国的煤气化工艺由老式的UGI炉块煤间歇气化迅速向世界最先进的粉煤加压气化工艺过渡,同时国内自主创新的新型煤气化技术也得到快速发展。据初步统计,采用国内外先进大型洁净煤气化技术已投产和正在建设的装置有80多套,50%以上的煤气化装置已投产运行,其中采用水煤浆气化技术的装置包括GE煤气化27套(已投产16套),四喷嘴33套(已投产13套),分级气化、多元料浆气化等多套;采用干煤粉气化技术的装置包括Shell煤气化18套(已投产11套)、GSP2套,还有正在工业化示范的LurgiBGL技术、航天粉煤加压气化(HT-L)技术、单喷嘴干粉气化技术和两段式干煤粉加压气化(TPRI)技术等。
煤气化技术
煤气化技术 国外气化炉发展现状 1、GE-德士古(Texaco)气化炉 Texaco气化炉是最成熟的第二代喷流床气化炉,它是由美国德士古石油公司下属的德士古开发公司(Texaco Development Corporation)研发的。第一套日处理15吨煤的中试装置于1948年在美国洛杉矶建成,并于1958年在美国摩根城建立了日处理100吨煤的原型装置,以东部煤为原料,操作压力为2.8MPa,合成气用于生产氨。但由于缺乏竞争力,被迫停止运行。石油危机之后,Texaco 气化炉得到了快速发展,尤其是美国15t/d和德国150t/d的实验装置做了大量的试验,解决了水煤浆制造、高温气体热回收、燃料喷嘴及煤种适应性的系列难题。并且于1983年和1984年分别成功应用于Eastman化工厂和Cool Water IGCC示范电站。目前,Texaco气化炉是国际上最成熟、商业化装置最多的第二代气化炉。美国的伊斯曼2台,日本宇部4台及德国SAR的1台都在运行。除此之外尚有美国Tampa电站一台2400t/d煤的气化炉示范装置。2004年5月,GE能源公司收购了Texaco气化炉业务。 自从上世纪80年代初,Texaco气化炉开始大规模应用,最初主要应用于化工领域,特别是用于F-T合成和生产化工产品。进入上世纪90年代之后,更多的应用于电力生产行业。这主要是因为20世纪90年代以来,IGCC和以IGCC 为核心的多联产系统的迅速发展。在Texaco气化炉被GE能源收购之后,这一趋势会更加明显。 Texaco气化炉进入我国比较早,从20世纪80年代就开始陆续在我国化工行业应用,且有较多业绩。自1993、1996年鲁南化肥厂、陕西渭河化肥厂Texaco 水煤浆气化工业装置分别投运以来,Texaco气化炉在我国陆续投产。Texaco气化炉在我国的国产化进程发展也较快,华东理工大学在开发“多喷嘴对置式水煤浆气化炉”方面,就借鉴了Texaco的运行经验。据我们的统计,截止2006年底,中国共有28台Texaco气化炉建成投运;另外有12台在建,预计2010年之前投运。这些气化炉除了早期有17台以石油焦为气化原料以外,其他气化炉,包括在建的12台都是以煤炭为原料。目前这些气化炉主要用于化工品的生产,尤其
几种常用煤气化技术的优缺点
几种煤气化技术介绍 煤气化技术发展迅猛,种类很多,目前在国内应用的主要有:传统的固定床间歇式煤气化、德士古水煤浆气化、多元料浆加压气化、四喷嘴对置式水煤浆气化、壳牌粉煤气化、GSP气化、航天炉煤气化、灰熔聚流化床煤气化、恩德炉煤气化等等,下别分别加以介绍。 一 Texaco水煤浆加压气化技术 德士古水煤浆加压气化技术1983年投入商业运行后,发展迅速,目前在山东鲁南、上海三联供、安徽淮南、山西渭河等厂家共计13台设备成功运行,在合成氨和甲醇领域有成功的使用经验。 Texaco水煤浆气化过程包括煤浆制备、煤浆气化、灰水处理等工序:将煤、石灰石(助熔剂)、添加剂和NaOH称量后加入到磨煤机中,与一定量的水混合后磨成一定粒度的水煤浆;煤浆同高压给料泵与空分装置来的氧气一起进入气化炉,在1300~1400℃下送入气化炉工艺喷嘴洗涤器进入碳化塔,冷却除尘后进入CO变换工序,一部分灰水返回碳洗塔作洗涤水,经泵进入气化炉,另一部分灰水作废水处理。 其优点如下: (1)适用于加压下(中、高压)气化,成功的工业化气化压力一般在4.0MPa 和6.5Mpa。在较高气化压力下,可以降低合成气压缩能耗。 (2)气化炉进料稳定,由于气化炉的进料由可以调速的高压煤浆泵输送,所以煤浆的流量和压力容易得到保证。便于气化炉的负荷调节,使装置具有较大的操作弹性。 (3)工艺技术成熟可靠,设备国产化率高。同等生产规模,装置投资少。 该技术的缺点是: (1)由于气化炉采用的是热壁,为延长耐火衬里的使用寿命,煤的灰熔点尽可能的低,通常要求不大于1300℃。对于灰熔点较高的煤,为了降低煤的灰熔点,必须添加一定量的助熔剂,这样就降低了煤浆的有效浓度,增加了煤耗和氧耗,降低了生产的经济效益。而且,煤种的选择面也受到了限制,不能实现原料采购本地化。 (2)烧嘴的使用寿命短,停车更换烧嘴频繁(一般45~60天更换一次),为稳定后工序生产必须设置备用炉。无形中就增加了建设投资。 (3)一般一年至一年半更换一次炉内耐火砖。 二多喷嘴对置式水煤浆加压气化技术 该技术由华东理工大学洁净煤技术研究所于遵宏教授带领的科研团队,经过20多年的研究,和兖矿集团有限公司合作,成功开发的具有完全自主知识产权、国际首创的多喷嘴对置式水煤浆气化技术,并成功地实现了产业化,拥有近20项发明专利和实用新型专利。目前在山东德州和鲁南均有工业化装置成功运行。
壳牌气化炉的现场组焊技术
石油化工建设10. 03 图1气化炉整体模型 1气化炉概况 近年来,随着煤化工的兴起,煤液化技术、煤制甲醇、油改煤在国内大批推进,其中壳牌气化炉(以下简称:气化炉)是采用最多的设备之一,如神华煤制油、中原大化50万t 甲醇装置、大唐多伦168万t 甲醇46万t 煤基烯烃均采用壳牌专利技术。壳牌气化炉一律为专利设备整体引进,并由外商进行总体设计,其壳体部分大致分由两个国家制造:西班牙、印度L &T 公司;内件部分由荷兰SEG 公司设计,分别由西班牙和L &T 公司制造;其结构形式为膜式水冷壁结构。1.1气化炉总体介绍 气化炉主要由壳体和内件组成。其中壳体分为反应器(Re-actor )+激(急)冷管(Quench Pipe )(位号:V1301),合成气冷却器(Syngas Cooler )+气体返回室(Gas Return Chamber )(位号:V1302),输气管(Transfer Duct )(位号:V1303)。内件分为渣池(位号:V1401)、激冷管中压蒸汽发生器(位号:E1301)、输气管中压蒸汽发生器(位号:E1302)、合成气冷却器中压蒸汽发生器(位号:E1303)、气化炉反应器中压蒸汽发生器(位号:E1320)以及气体返回室内的立管(主管)和斜管(支管)等七部分。1.2设备材料及设备规格 气化炉整体重量约1300t 。壳体主要材质为SA387GR11CL2;在反应器段、合成气冷却器段有一部分材质为复合材料SA387GR11CL2+NO8825;最大壁厚285mm ;壳体最大内径Φ4630mm ;需要现场组对焊缝处的壁厚为65~90mm ;整体长段50.2m 。气化炉整体模型如图1所示。1.3设备分段(以2000t 炉子为例) 为了满足设备内陆道路运输及组焊吊装要求,在初步设计期间,技术方案的讨论必须有制造厂商参加,他们必须充分考虑 管口方位、外壳外部尺寸等因素,并按照以下尺寸和重量极限进 行设计分段: (1)组件高度最高5.1m ;(2 )组件宽度最大7m ;(3)组件长度最长25.00m ;(4)组件重量 最大150t 。 具体的设备分段情况列表如表1、表2所示:(注大唐3000t 炉子分段的几何尺寸及重量略大些) 壳牌气化炉的现场组焊技术 ■肖晓磊 中国化学工程第十一建设公司河南开封 475002 摘 要通过与壳牌公司技术交流,借鉴国外压力容器组焊的先进经验,在国内中石化油改煤工程投料调试的经验基础上, 结合大型气化炉组焊技术的工程实例,阐述一项成熟的气化炉现场组焊技术。本文着重于描述施工程序(组装流程) 、组对与焊接、内件安装。对于无损检测、消除应力热处理、液压试验、衬里等仅做一般性介绍。关键词壳牌技术气化炉现场组对 焊接 中图分类号TG44 文献标识码B 文章编号1672-9323(2010)03-0035-08 35
SCGP(壳牌)煤气化工艺
SCGP(壳牌)煤气化工艺 1、SCGP(壳牌)煤气化技术简介。 1.1工艺原理。 SCGP壳牌煤气化过程是在高温、加压条件下进行的,煤粉、氧气及少量蒸汽在加压条件下并流进入气化炉内,在极为短暂的时间内完成升温、挥发分脱除、裂解、燃烧及转化等一系列物理和化学过程。由于气化炉内温度很高,在有氧存在的条件下,碳、挥发分及部分反应产物(H2和CO等)以发生燃烧反应为主,在氧气消耗殆尽之后发生碳的各种转化反应,即过程进入到气化反应阶段,最终形成以CO和H2为主要成分的煤气离开气化炉。典型的SCGP煤气成分见表1。 1.2工艺流程。 目前,壳牌煤气化装置采用废锅流程,废锅流程的壳牌煤气化工艺简略流程见图1。 原料煤经破碎由运输设施送至磨煤机,在磨煤机内将原料煤磨成煤粉(90%<100μm)并干燥,煤粉经常压煤粉仓、加压煤粉仓及给料仓,由高压氮气或二氧化碳气将煤粉送至气化炉煤烧嘴。来自空分的高压氧气经预热后与中压过热蒸
汽混合后导入煤烧嘴。煤粉、氧气及蒸汽在气化炉高温加压条件下发生碳的氧化及各种转化反应。气化炉顶部约1500℃的高温煤气经除尘冷却后的冷煤气激冷至900℃左右进入合成气冷却器。经合成气冷却器回收热量后的煤气进入干式除尘及湿法洗涤系统,处理后的煤气中含尘量小于1mg/m3送后续工序。 湿洗系统排出的废水大部分经冷却后循环使用,小部分废水经闪蒸、沉降及汽提处理后送污水处理装置进一步处理。闪蒸汽及汽提气可作为燃料或送火炬燃烧后放空。 在气化炉内气化产生的高温熔渣,自流进入气化炉下部的渣池进行激冷,高温熔渣经激冷后形成数毫米大小的玻璃体,可作为建筑材料或用于路基。 1.3技术特点。 1.3.1煤种适应性广。 SCGP工艺对煤种适应性强,从褐煤、次烟煤、烟煤到无烟煤、石油焦均可使用,也可将2种煤掺混使用。对煤的灰熔点适应范围比其他气化工艺更宽,即使是较高灰分、水分、硫含量的煤种也能使用。 1.3.2单系列生产能力大。 煤气化装置单台气化炉投煤量达到2000t/d以上,生产能力更高的的煤气化装置也正在建设中。 1.3.3碳转化率高。 由于气化温度高,一般在1400~1600℃,碳转化率可高达99%以上。 1.3.4产品气体质量好。 产品气体洁净,煤气中甲烷含量极少,不含重烃,CO+H2体积分数达到90%以上。 1.3.5气化氧耗低。 与水煤浆气化工艺相比,氧耗低15%~25%,可降低配套空分装置投资和运行费用。 1.3.6热效率高。
Shell煤气化工艺的评述和改进意见
Shell煤气化工艺的综述及流程改进 意见 戴进美 (湖南工学院材料与化学工程系应用化工专业0901班) 摘要:叙述了Shell煤气化技术的发展过程,介绍了Shell煤气化工艺和主要设备的特 点,回顾国内的装置建设情况,坦言一些存在的问题,并提出Shell工艺的改进意见:在为中国设计的制氢气、氨和甲醇化工装置中,将废锅流程改为激冷流程,町以明显降低投资,加快建设周期,提高开车速度,降低运行成本。 关键词:Shell 煤气化工艺废锅流程激冷流程 编者按:虽然Shell煤气化工艺是目前世界上较为先进的第二代煤气化工艺之 一,但是这种工艺不是十全十美的国内引进该枝术应用于氢、氨、醇生产的过程中将面临着很多困难,认识上有很多不足。本文作者结合多年的工程实践经验,坦言Shell煤气化工艺存在的一些问题,并提出Shell工艺的改进意见.可供业界同行参考。 Shell煤气化过程是目前世界上较为先进的第二代煤气化工艺之一。按学术上的分类,She[1煤气化属气流床气化。煤粉、氧气及少量水蒸气在加压条件下并流进入气化炉内,在极为短暂的时间内完成升温、挥发分脱除、裂解、燃烧及转化等一系列物理和化学过程,气化产物为以氢气和一氧化碳为主的合成气,二氧化碳的含量很少。 1 Shell煤气化技术的发展历程 自20世纪50年代起,壳牌公司就参与了气化技术的开发。当时,该公司开发r以油为原料的壳牌气化技术(SGP),至今已有150多套SGP没施得到技术转让。在积累油气化经验后,1972年开始在该公司的阿姆斯特丹研究院(KSLA)进行煤气化技术研究。1976年,煤气化工艺(SCGP)已达到一定水平并建立一座处理煤量为6t/d的试验厂,利用该装置一共试验了30多个不同的煤种。 1978年,在汉堡附近的哈尔堡炼油厂建设一座处理煤量为150t/d的工厂,公司利用这座装置进行了一系列成功的试验,至1983年该装置停止运转为止,累计运行了6l00h,其中包括超过1 000h的连续运转,顺利完成了工艺开发和过程优化的任务。 在汉堡中试装置成功运行的基础上,1987年,壳牌公司在美同休斯顿附近的DeerPark 石化巾心建设了一座规模较大的上厂,这庠命名为SCGP l的示范进煤量为每天250t高硫煤或每天400t高湿度、高灰褐煤,共积累了15000h的操作经验。SCGP1试验了约18种原料,
壳牌煤气化问题
1、Shell煤气化技术开车问题分析 Shell粉煤加压气化工艺是荷兰壳牌公司开发的一种先进的煤气化技术,国内进口了十多套,其中三套(分别在岳阳,安庆、枝江)干煤粉气化炉,近一段时间开车。三套干煤粉气化炉刚开车时,出现了严重的问题(按供应商提供操作条件操作):Shell每台气化炉有点火烧嘴一个,开工烧嘴2个,煤粉喷嘴4个。在气化炉投料运行前需要对气化炉进行烘炉,烘炉是用两个开工烧嘴时进行的,用点火烧嘴对开工烧嘴进行点火。点火顺序:点火烧嘴—开工烧嘴—煤粉烧嘴;首先点着点火烧嘴,之后开工烧嘴投料,给气化炉升温和升压,当温度和压力达到了工艺要求的工况时,煤粉烧嘴进行化工投料,至此,气化炉进入化工运行阶段。岳阳,安庆,枝江三家使用Shell气化炉的企业在对点火烧嘴进行开车时都出现了同样的问题:点火不到10秒钟就将其点火烧嘴烧坏;该点火烧嘴的内喷头材质是铜,外壳为不锈钢incolly-800材料。燃料油从内喷头12个圆孔喷出,与氧气在内喷头与外壳之间的空隙混合,然后自12个槽型孔喷出,喷出之后进行燃烧。中心通冷却水,对点火烧嘴进行冷却。在点火烧嘴点火10秒钟后,点火烧嘴的外壳就如同气割一样被切割开了,严重损坏了。 问题①点火烧嘴易损坏,最短时间不大于10秒钟,最多使用不到二十次,厂家是否有改进的措施? ②点火烧嘴造价高昂、更换频繁,从技术上能否提高设备寿命? ③点火烧嘴是否实现了国产化?造价、寿命如何?。
2、SHELL气化炉、GE废锅气化炉和GE水冷激气化炉 ①气化炉运行负荷是否能够达到100%?,目前是多少? ②连续运行时间是多少?目前有没有突破两个月? ③维修项目有哪些?维修时间能否缩短?成本如何? 3、煤气化工艺中循环使用的洗涤灰水如何处理效果最佳? 4、壳牌煤气化工艺流程中的合成气反吹系统的反吹介质能否用洗涤后的粗合成气改为高温高压氮气?是否满足下游装置的工艺要求?对比节省工程投资是多少? 5、壳牌粉煤气化是一种先进成熟的洁净煤气技术,该技术的关键设备是由气化炉、输气管和合成冷却器三大件组成,其中气化炉又是核心,如何将气化炉、输气管和合成气冷却器等设备进行安全可靠合理的配置,实现高转化效率,长周期运行,节省投资? 6、废锅造价高,现在是否有降低造价的措施?尤其采用上行废锅形式,煤气激冷、余热回收、去除渣尘使这套系统变得庞大、复杂、昂贵;为了清除渣尘,采用庞大的陶瓷过滤装置,需要定期脉冲反吹。能否采用下行水激冷工艺设备? 7、气化炉高温排出的熔渣经激冷后成玻璃状颗粒,性质稳定,能否综合利用? 8、合成气中的粉尘含量的标准是多少?检测措施是什么?如果合成气粉尘超标将直接影响合成气的质量,对下游工艺流程有什么影响?
壳牌气化炉用煤分析
煤气化近期用煤分析 一、近期用煤及调整情况 1、煤气化双炉在2017年2月7日及以前用煤主要为: 白羊墅贫瘦煤:东川蒙煤:瑞丰蒙煤=23%:14%:63%。 2、受配煤后煤质波动较大影响在2月8日开始双炉上煤按1:1加配了(汽运阳泉贫瘦煤:瑞丰蒙煤=20%:80%),因此煤气化上煤调整为: (白羊墅贫瘦煤:东川蒙煤:瑞丰蒙煤=23%:14%:63%):(汽运阳泉贫瘦煤:瑞丰蒙煤=20%:80%)=1:1。 3、因近期煤气化消耗较高,为排除相关煤粉指标(如CaO、热值等)对气化炉消耗的影响,自2月14日起煤气化上煤1#炉没变,2#炉改为: 阳泉贫瘦煤:东川大砭窑混蒙煤:大砭窑蒙煤=24%:40%:36% 4、1#炉因前一种煤用完,自2月18日起煤气化1#炉上煤改为: 阳泉贫瘦煤:瑞丰蒙煤:东川蒙煤=18%:64%:18% 二、煤质分析 1、灰分 根据下图1、2#炉用煤灰分可以看出(主要看中采),本月上旬灰分波动较大,上煤时调整为1:1后灰分趋于稳定;2#炉换煤后灰分较同期1#炉要稳定。
2、低位热值 从下图可以看出,双炉低位发热量变化同灰分变化相同,双炉上旬波动较大,中采热值在5700左右;中旬经过两次换煤后双炉热值都有所提高在5800左右。
3、硅铝比 从下图可以看出,本月上煤2月7日调整后硅铝比略有下降,从2.1降到2.0左右;2月14日2#炉第二次调整后从2.0涨到2.2左右;2月18日1#炉调整后硅铝比有所上涨。
4、CaO变化 从下图可以看出本月上旬双炉中采CaO含量基本在6%左右,但波动较大,经双炉上煤调整后波动有所好转;2#炉14日换煤后稳定在6%-7%;1#炉18日换煤后有上涨趋势(受数据较少只供参考)。
煤气化技术方案比较及选择
煤气化技术方案比较及选择 何正兆,宫经德,郑振安,汪寿建(五环科技股份有限公司,湖北武汉 430079) 2005-09-16 1 煤气化技术概述 以煤为原料生产合成气,国内过去常用常压固定层气化炉。该工艺虽然技术成熟可靠,设备全部国产化,投资较省,但能耗高、煤质要求高,需用无烟块煤或焦炭,资源利用率低,而且是常压操作,生产强度小,操作时“三废”排放量大,对环境污染比较严重,显然与国外煤气化技术相比,存在较大差距。 多年以前,国内研究部门也曾开发过以粉煤为原料的K-T炉和熔渣炉,并在常压固定层气化炉中采用富氧连续气化的工艺,以及近年开发的恩德粉煤气化炉和灰熔聚气化炉等,因种种原因这些技术尚未达到大型工业化装置推广的程度。 早在20世纪初煤气化技术在国外已实现工业化,50年代后因天然气、石油大量开发,煤气化技术发展一度停止不前。 20世纪70年代,国际上出现能源危机,发达国家出于对石油天然气供应紧张的担忧,纷纷把煤气化技术作为替代能源技术重新提到议事日程,并加快了对煤气化新工艺的研究。近二十年来,国外很多公司为了提高燃煤电厂热效率,减少对环境的污染,对煤气化联合循环发电技术进行了大量的开发研究工作,促进了煤气化技术的发展。 目前已成功开发了对煤种适应性广、气化压力高、生产能力大、气化效率高、对环境污染少的新一代煤气化工艺。其中具有代表性的有荷兰壳牌(SHELL)公司的干煤粉气化工艺、美国GE公司的水煤浆气化工艺[原称德士古(TEXACO)水煤浆气化工艺]、美国DYNEGY 公司的DESTEC气化工艺、德国KRUPP UHDE公司的PRENFLO工艺(加压K-T法)及德国鲁奇(LURGI)工艺。其中DESTEC气化工艺与GE 工艺相近,但其业绩及经验不如GE;PRENFLO工艺的工艺指标较好,但目前仅有一套示范装置,生产操作经验较少;鲁奇(LURGI)工艺虽然工业装置较多,生产操作经验也比较丰富,但由于煤气中CH4含量高,有效成分(CO+H2)含量低,且煤气中焦油及酚含量高,污水处理复杂,不宜用来生产合成氨和甲醇的原料气。 目前国际上技术比较成熟、工艺指标比较先进、业绩较多的主要是SHELL 公司干煤粉气化工艺和GE的水煤浆气化工艺,两者均为加压纯氧气流床液态排渣的气化工艺。SHELL公司在渣油气化技术取得工业化成功经验的基础上,于1972年开始从事煤气化技术的研究。1978年第一套中试装置在德国汉堡建成并投入运行;1987年在美国休斯敦附近建成的日投煤量250~400t的示范装置投产;日投煤量2000t 的大型气化装置于1993年在荷兰的Buggenum建成投产(Demkolec电厂),用于联合循环发电,该气化装置为单系列操作,装置的开工率在95%以上。生产实践证明,SHELL煤气化工艺是先进成熟可靠的。目前该技术在国内推广比较迅速。 GE(TEXACO)公司很早就开发了以天然气和重油为原料生产合成气技术,20世纪70年代的石油危机促进其寻找替代能源和洁净的煤气化技术,经多年研究以后,推出了水煤浆气化工艺。该工艺技术自引进中国以来已有山东鲁南、上海焦化、陕西渭河、安徽淮化四套装置投运,最长的已有10年生产操作经验。基本运行良好,显示了水煤浆气化的先进性,但使用该项技术所建的生产装置,要达到长周期满负荷运行,尚较困难,特别是对煤种的选择性限制了其发展。 2 SHELL和GE两种煤气化技术的主要特点 SHELL煤气化工艺与GE水煤浆气化工艺,是当前先进而又成熟的两种煤气化技术,已成功地在工业上应用多年。两种气化工艺对比分析如下。 2.1 原料的适应性 SHELL煤气化是洁净的煤气化工艺,可以使用褐煤、次烟煤、烟煤、无烟煤等煤种以及石油焦为原料,也可使用两种煤掺合的混煤。并可气化高灰分(5.7%~24.5%,最高35%)、高水分(4.5%~30.7%)和高硫分的劣质煤。对于原料煤和燃料煤价差较大的地区有可能使其
浅析 SHELL 煤气化技术
·270·2016年7月 第8卷技术论坛工程技术 浅析SHELL煤气化技术 赵 野 神华鄂尔多斯煤制油分公司,内蒙古 鄂尔多斯 017209 摘 要:随着国内近年掀起的煤化工热潮,Shell煤气化工艺以其高效、安全和环保的特点,成为很多企业的首选工艺之一。本文介绍了Shell煤气化的工艺原理、特点,煤种的选择,气化炉炉温偏高和偏低的参数变化和影响,气化炉温度监测,煤烧嘴与烧嘴罩损坏泄漏的一般原因及影响,以及对Shell煤气化未来的展望。 关键词:壳牌煤气化;气化炉的特点;煤种;炉温;烧嘴罩 中图分类号:TQ546 文献标识码:A 文章编号:1671-5586(2016)64-0270-02 1 引言 能源和环境是人类赖以生存与发展的基础,然而当今世界正面临着能源短缺、环境污染和温室效应等诸多问题,如何实现人类社会、经济与环境的协调可持续发展,已经引起国际社会的普遍关注。人类必须在化石能源濒临枯竭和生存环境濒临崩溃之前,完成替代能源和相关技术的开发。我国是能源消耗大国,而且煤多油少气贫,那么煤转气转油将是未来发展的趋势,它将带动经济的发展,也是国家能源战略储备的一部分。壳牌煤气化技术的出现为洁净能源的开发指明方向,产品具有节能降耗,应用广泛的特点。以下是结合自己在工作中的实践和对壳牌煤气化的所知进行分析探讨。 2 SHELL煤气化的原理和特点 2.1 SHELL煤气化的工艺原理 Shell煤气化技术是目前世界上较为先进的第二代粉煤气化技术之一,气化过程也是在高温加压下进行的。其进料方式是将碎煤磨成0.1mm以下、水分2%以下的细粉,高压氮气通过特殊的喷嘴将粉煤送进炉膛,与被蒸汽稀释的氧气在气化炉内高温高压下气化形成合成气(CO+H2>90%)、飞灰和熔渣[1]。该技术工艺流程较简单,原煤经碎煤后送至磨煤机,磨成的细粉被热惰性气体干燥,由高压氮气将干煤粉送入气化炉,另外高压氧气和中压过热蒸汽混合后也由喷嘴喷入炉内。炉口约1400~1600℃的高温合成气离开气化炉顶部,与来自洗涤和除灰系统混合后200℃的合成气混合,被激冷到900℃后进入合成气冷却段冷却到340℃,然后再进入干式除灰系统和湿洗除灰系统。大部分熔渣被渣水激冷破碎成粒径平均接近1mm的玻璃球体。 2.2 SHELL煤气化的特点 第一,干粉进料,气化效率高。原料煤所含能量之中,大约80~83%以合成气形式回收,另外14%~16%以蒸汽形式回收,总的热效率可达98%左右。 第二,气化操作温度高。气化温度约在1400~1600℃,在高的气化温度下碳转化率高达99%,有效气体成份含量高,产品气体相对洁净,不含重烃,甲烷含量很低,煤气品质好[2]。 第三,氧耗低。与湿法进料水煤浆气化相比,氧气消耗低(15%~25%),原料制备系统简单,进料灵活,与之配套的空分装置投资可相对减少。 第四,加压操作,单炉生产能力大。目前已投入的单炉日处理煤量达到2000吨。 第五,气化炉结构较简单,内部为膜式水冷壁,无任何耐火砖,烧嘴寿命长,所以气化炉坚固耐用,操作可靠[3]。 第六,生产调幅能力强,连续运转周期长。采用对称式多烧嘴,混合效果好,提高了气化操作的可靠性和生产调幅能力。气化煤烧嘴设计保证寿命8000h。 第七,煤种适应性广。 第八,环保性能好。 3 SHELL煤气化工艺对煤种的选择 尽管壳牌煤气化炉适应的煤种很广,但也不是万能的,从技术经济的角度考虑对煤种还是有一定的要求。煤种特性对煤气化炉和相关的设备设计及操作密切相关。壳牌煤气化着重从水分、灰分、煤粉粒度、挥发份、反应活性、总硫、 灰熔点及灰组成来具体选择适合自己的煤。 4 SHELL煤气化炉温度 4.1 气化炉温度监测 气化炉蒸汽产量可以用来作为气化炉温度监测的主要参数,与此同时要对其渣型进行比对,保证对炉温进行正确判断,从而对气化温度进行调节,也可通过CO2和CH4量的变化对炉温进行监控。 气化炉蒸汽产量自动控制用于灰熔点和灰分正常波动时校正气化温度[4]。 图1 炉温偏高渣型 图2 炉温偏低渣型 4.2 气化炉温度波动 在气化炉操作过程中,炉温偏高,合成气中CO2含量升高、CH4含量降低、汽包小室副产蒸汽升高,煤粉燃烧后产生的煤渣成黄褐色晶体,针状物多(见图1所示),燃烧充分,渣的流动性强,炉壁不易挂渣,保温效果差,极易烧坏气化炉膜式水冷壁、烧嘴头以及烧嘴罩,降低了它们的使用寿命。 炉温过高煤粉燃烧后,液态熔渣还容易被合成气带到气化炉冷却段十字吊架处,随着温度的降低,熔渣容易凝固在换热器上,时间长了,换热器的前后压差将增大,SGC入口温度也会升高,气化炉压力增大,激冷气量明显下降,饱和蒸汽经过换热器时的换热效果差,过热蒸汽的温度将受到影响。如果SGC出口温度也升高,说明换热器堵的不是很厉害;反之,说明堵的很严重了。 炉温偏低,合成气中CO2含量降低、CH4含量升高、汽包小室副产蒸汽降低,煤粉燃烧后产生的煤渣成黑色小颗粒状(见图2所示),燃烧很不充分,渣的流动性差,炉壁挂渣较厚,传热效果差,下渣口很容易堵渣,给生产造成影响。 5 SHELL煤气化炉烧嘴罩的损坏泄漏 在气化炉运行过程中,导致烧嘴罩损坏泄漏的原因很多,也是诸多壳牌煤气化人多年要攻克的瓶颈,下面谈谈个人对此问题的理解,仅供参考。 5.1 烧嘴罩泄漏的直接原因 局部超温导致的烧蚀。制造烧嘴罩的材料为13CrMo4-5钢,其金相组织为铁素体/珠光体。烧嘴罩泄漏部位的金相组织为马氏体。金相学理论表明:超过840℃的高温可以导致铁素体/珠光体转变为马氏体,而马氏体恰好不耐高温。 5.2 烧嘴罩泄漏的根本原因 (1))粉煤烧嘴火苗长度偏低,低于设计值。导致粉煤烧嘴火苗的高温外焰(2500-3000℃)接近烧嘴罩。 (2))炉温整体偏高但波动很大。炉温过高时,渣的流动性变得非常好。因为烧嘴位置的原因,合成气和渣在炉膛内形成环流。此种情况在下渣口下方同样存在。渣的流动性太好,会有部分渣被气流带到渣裙和热裙的位置,并附着在 (下转第273 页)
几种煤气化炉炉型的比较
气化工艺各有千秋 1.常压固定床间歇式无烟煤(或焦炭)气化技术 目前我国氮肥产业主要采用的煤气化技术之一,其特点是采用常压固定床空气、蒸汽间歇制气,要求原料为准25~75mm的块状无烟煤或焦炭,进厂原料利用率低,单耗高、操作繁杂、单炉发气量低、吹风放空气对大气污染严重,属于将逐步淘汰的工艺。 2.常压固定床无烟煤(或焦炭)富氧连续气化技术 其特点是采用富氧为气化剂、连续气化、原料可采用?准8~10mm粒度的无烟煤或焦炭,提高了进厂原料利用率,对大气无污染、设备维修工作量小、维修费用低,适合用于有无烟煤的地方,对已有常压固定层间歇式气化技术进行改进。 3.鲁奇固定床煤加压气化技术 主要用于气化褐煤、不粘结性或弱粘结性的煤,要求原料煤热稳定性高、化学活性好、灰熔点高、机械强度高、不粘结性或弱粘结性,适用于生产城市煤气和燃料气。其产生的煤气中焦油、碳氢化合物含量约1%左右,甲烷含量约10%左右。焦油分离、含酚污水处理复杂,不推荐用以生产合成气。 4.灰熔聚煤气化技术 中国科学院山西煤炭化学研究所技术。其特点是煤种适应性宽,属流化床气化炉,煤灰不发生熔融,而只是使灰渣熔聚成球状或块状灰渣排出。可以气化褐煤、低化学活性的烟煤
和无烟煤、石油焦,投资比较少,生产成本低。缺点是操作压力偏低,对环境污染及飞灰堆存和综合利用问题有待进一步解决。此技术适合于中小型氮肥厂利用就地或就近的煤炭资源改变原料路线。 5.恩德粉煤气化技术 属于改进后的温克勒沸腾床煤气化炉,适用于气化褐煤和长焰煤,要求原料煤不粘结或弱粘结性,灰分<25%~30%,灰熔点高、低温化学活性好。在国内已建和在建的装置共有13套22台气化炉,已投产的有16台。属流化床气化炉,床层中部温度1000~1050℃。目前最大的气化炉产气量为4万m3/h半水煤气。缺点是气化压力为常压,单炉气化能力低,产品气中CH4含量高达1.5%~2.0%,飞灰量大、对环境污染及飞灰堆存和综合利用问题有待解决。此技术适合于就近有褐煤的中小型氮肥厂改变原料路线。 6.GE水煤浆加压气化技术 属气流床加压气化技术,原料煤运输、制浆、泵送入炉系统比干粉煤加压气化简单,安全可靠、投资省。单炉生产能力大,目前国际上最大的气化炉投煤量为2000t/d,国内已投产的气化炉能力最大为1000t/d。设计中的气化炉能力最大为1600t/d。对原料煤适应性较广,气煤、烟煤、次烟煤、无烟煤、高硫煤及低灰熔点的劣质煤、石油焦等均能用作气化原料。但要求原料煤含灰量较低、还原性气氛下的灰熔点低于1300℃,灰渣粘温特性好。气化系统不需要外供过热蒸汽及输送气化用原料煤的N2或CO2。气化系统总热效率高达94%~96%,高于Shell干粉煤气化热效率(91%~93%)和GSP干粉煤气化热效率(88%~92%)。气化炉结构简单,为耐火砖衬里,制造方便、造价低。煤气除尘简单,无需价格昂贵的高温高压飞灰过滤器,投资省。国外已建成投产6套装置15台气化炉;国内已建成投
壳牌煤气化装置(SCGP)操作规程精品完整版
壳牌煤气化装置(SCGP)操作规程 1、煤气化装置各岗位的岗位职责 1.1 磨煤岗位 本岗位的职责是将电厂燃料车间送来的碎煤贮存在碎煤仓V-1101A/B中,石灰石贮存在V-1102A/B中,两者混合配比加入到中速磨A-1101A/B中,〉在微负压和惰性气体条件下被磨粉干燥,干燥所需的热量由热风炉F-1101A/B中燃烧合成气或柴油提供,出来的煤粉要求直径范围0.005mm〈 D〈0.09mm,煤粉被输送到袋滤器S-1103A/B,之后送往低压粉仓V-1201A/B。 1.2 现场岗位 本岗位的主要职责是做好现场巡查工作,,做好开车前后设备的运行、调试,让每件现场设备具备一次开车成功能力;在开车期间,协助中控岗位做好设备的运行监护,准确无误的做好数据记录,并对未运行设备进行维护、保养,使设备随时处于可备用状态。(现场设备包括压缩机,汽包,破渣机,火炬系统,各种高低压泵等)。 1.3 分析岗位 本岗位的职责是对煤气化工艺所需各种原料进行及时准确的分析,对正常生产中的气体,液体,固体进行取样分析,并把分析结果及时反馈给中控岗位,以协助中控岗位控制好整个煤气化装置的运行。 1.4 中控岗位 本岗位的职责是维持磨煤系统(U-1100),煤给料系统(U-1200),气化系统(U-1300),除渣系统(U-1400),干法除尘系统(U-1500),湿法除尘系统(U-1600).初级水处理系统(U-1700)及公共系统(U-3000至3600)的正常运行,并协调与电厂燃料车间,氨厂净化车间,空分车间的生产关系。 磨煤系统(U-1100)的职责是与现场磨煤岗位的协调,将合格的粉煤送往煤给料系统。 煤给料系统(U-1200)由2套完全相同的锁斗加压系统组成,本系统的职责是将磨煤送来的粉煤经煤锁斗加压,再送往气化炉的四个煤烧嘴。 气化系统(U-1300)的职责是将加压后的粉煤以及氧蒸汽混合物通过2对相对的煤烧嘴送入气化炉,使粉煤和氧蒸汽混合物在一定条件发生反应,同时控制好炉内的温度,压力,出口合成气的温度及气化炉内的渣层厚度.并将产生的中压饱和蒸汽导入管网。 除渣系统(U-1400)的职责是将气化炉口流出的液态渣冷却,粒化并排至渣收集槽T-1401,然后捞渣机及渣输送带送往渣场. 干法除尘系统(U-1500)的职责是除去来自合成气中的干灰(通过过滤器和锁斗系统),同时将飞灰中的有毒微量气气提,然后将飞灰输送到筒仓,或送至磨煤系统。 湿法洗涤系统(U-1600)的职责是将经过干法除尘后的热合成气在湿洗塔里洗涤激冷,以脱除粗合成气中所含的氯化氢,氢氟酸和微量固体.最后将合格的合成气送往净化车间。 初级水处理系统(U-1700)的职责是将除渣系统,湿洗系统及其它装置送来的废水,进行初级处理、回收、再利用。 公共系统包括氮气系统(U-3000),燃料和火炬系统(U-3100),冷却水系统(U-3200),工艺水系统(U-3300),蒸汽/冷凝液系统(U-3400),酸碱系统(U-3600)。该系统为各单元提供服务,满足各单元对氮气,各种用水,蒸汽,酸碱等需要。 2、煤气化装置各岗位的岗位管辖范围 2.1 U-1100 磨煤与干燥系统 A-1101A/B 磨煤机2台