矩形花键铣刀和圆孔拉刀说明书21
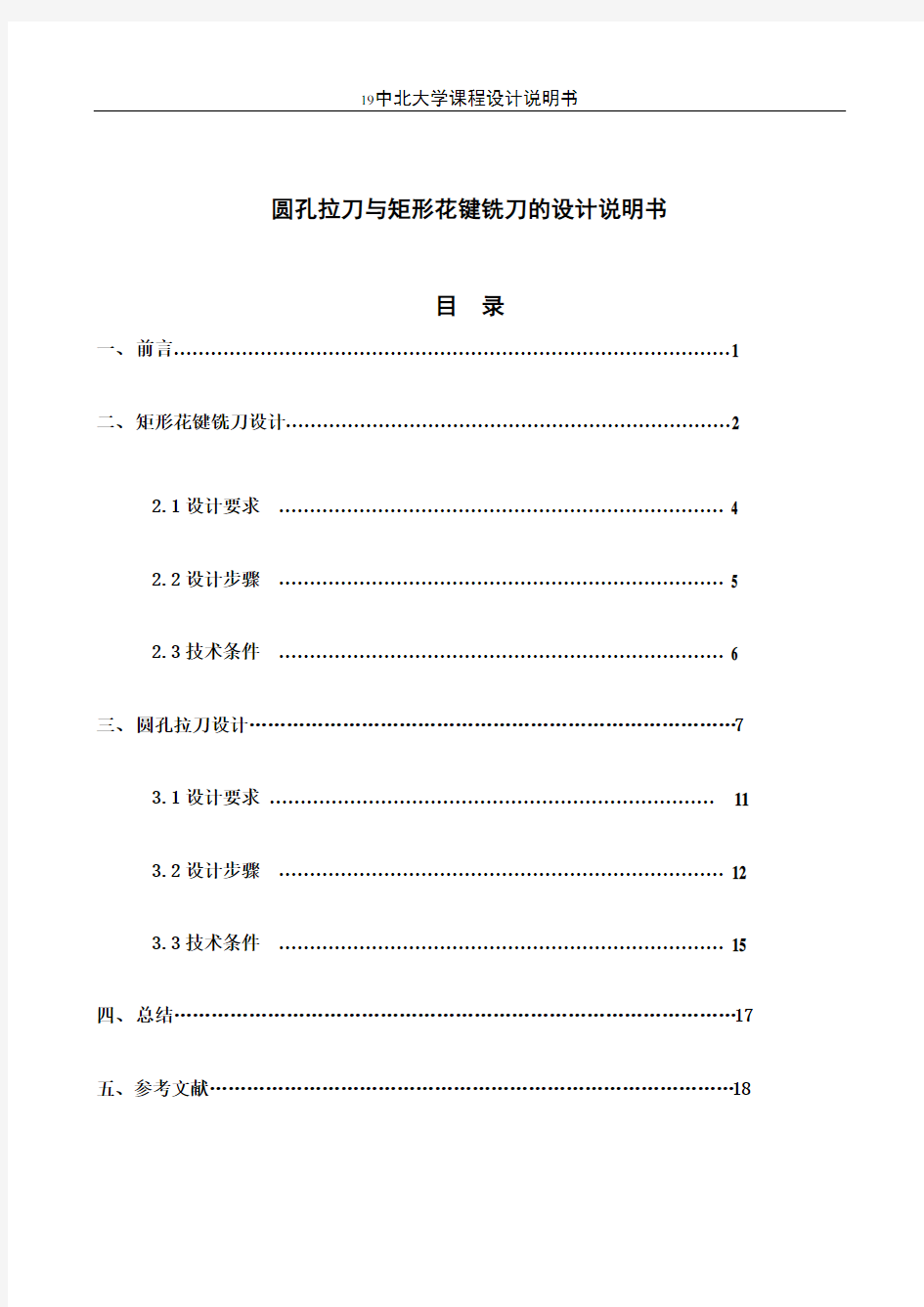
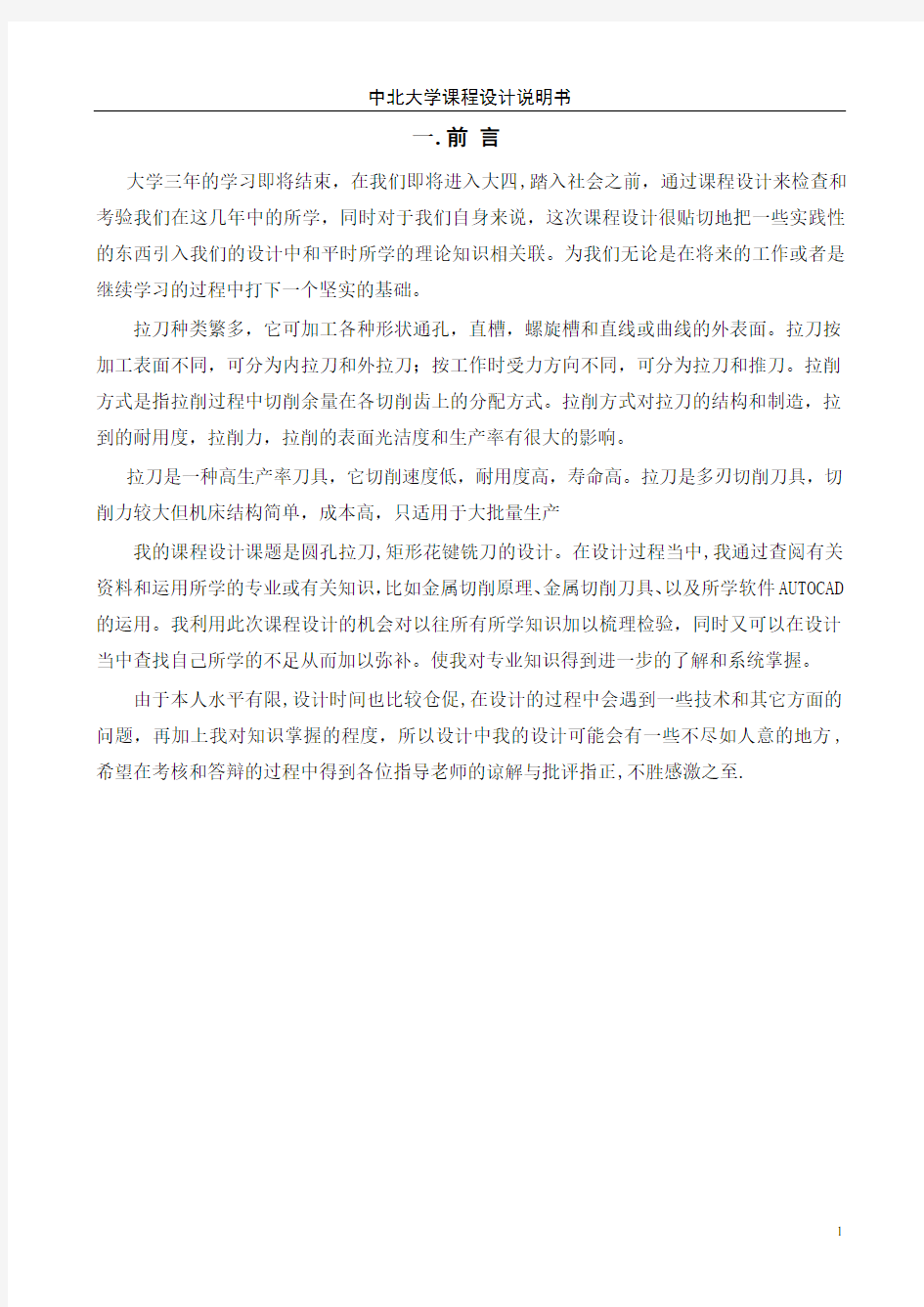
圆孔拉刀与矩形花键铣刀的设计说明书
目录
一、前言 (1)
二、矩形花键铣刀设计 (2)
2.1设计要求 (4)
2.2设计步骤 (5)
2.3技术条件 (6)
三、圆孔拉刀设计 (7)
3.1设计要求 (11)
3.2设计步骤 (12)
3.3技术条件 (15)
四、总结 (17)
五、参考文献 (18)
一.前言
大学三年的学习即将结束,在我们即将进入大四,踏入社会之前,通过课程设计来检查和考验我们在这几年中的所学,同时对于我们自身来说,这次课程设计很贴切地把一些实践性的东西引入我们的设计中和平时所学的理论知识相关联。为我们无论是在将来的工作或者是继续学习的过程中打下一个坚实的基础。
拉刀种类繁多,它可加工各种形状通孔,直槽,螺旋槽和直线或曲线的外表面。拉刀按加工表面不同,可分为内拉刀和外拉刀;按工作时受力方向不同,可分为拉刀和推刀。拉削方式是指拉削过程中切削余量在各切削齿上的分配方式。拉削方式对拉刀的结构和制造,拉到的耐用度,拉削力,拉削的表面光洁度和生产率有很大的影响。
拉刀是一种高生产率刀具,它切削速度低,耐用度高,寿命高。拉刀是多刃切削刀具,切削力较大但机床结构简单,成本高,只适用于大批量生产
我的课程设计课题是圆孔拉刀,矩形花键铣刀的设计。在设计过程当中,我通过查阅有关资料和运用所学的专业或有关知识,比如金属切削原理、金属切削刀具、以及所学软件AUTOCAD 的运用。我利用此次课程设计的机会对以往所有所学知识加以梳理检验,同时又可以在设计当中查找自己所学的不足从而加以弥补。使我对专业知识得到进一步的了解和系统掌握。
由于本人水平有限,设计时间也比较仓促,在设计的过程中会遇到一些技术和其它方面的问题,再加上我对知识掌握的程度,所以设计中我的设计可能会有一些不尽如人意的地方,希望在考核和答辩的过程中得到各位指导老师的谅解与批评指正,不胜感激之至.
1
2 二.矩形花键铣刀设计
(一)齿形的设计计算
1.前角为零时,工件法剖面截形就是铣刀的齿形。
2.前脚大于零时
铣刀有了前角以后,其刀齿在径向截面的齿形和前刀面上的齿形,就与工件法剖面的截形不同了。设γf为铣刀外圆处的纵向前角,当γf较大时,铣刀径向截面和前刀面上的齿形需进行修正计算。
下图所示的是工件齿形和铣刀齿形得关系,其中(b)为给定的工件齿形;(c)为铣刀径向截面应具有的齿形,即铲刀应具有的齿形;(d)为铣刀前刀面的齿形,即样板应具有的齿形。
(二)结构参数的选择及计算
1.铣刀齿形高度h
设被切工件成形部分高度为hw,则成形铣刀齿形高度应为:
h=hw+(1-2)mm
2.铣刀宽度B
设被切工件阔形宽度为Bw,则铣刀宽度B可取为稍大于B。
3.容屑槽底形式
铲齿成形铣刀容屑槽底形式通常有两种,即平地形式和中间有凸起或槽底倾斜的加强形式。在铲削深度较小和刀齿强度足够的情况下,应采用平底形式。在铣削深度较大时,宜采用加强形式。
4.铣刀的孔径d
铣刀的孔径d应根据铣削宽度和工作条件选取,可以按刚度,强度条件计算,也可根据
生产经验选取。
5.铣刀的外径do
对于平底形式的容屑槽,铣刀外径可按下面公式计算:do=d+2m+2H
式中:d-铣刀孔径
m-壁厚,一般取(0.3-0.5)d
H-全齿高
由于全齿高的计算又需依据外径do,因此,用上式直接计算铣刀外径是困难的,我国一些工厂采用下式估算铣刀外径:
do=(2-2.2)d+2.2h+(2-6)
根据上面公式的计算结果再取外径的推荐值。
6.铣刀的圆周齿数Zk
铲齿成形铣刀的圆周齿数Zk可按下式计算
Zk=Πdo/S
式中S为铣刀的圆周齿距,粗加工时,可取S=(1.8-2.4)H
精加工时,可取S=(1.3-1.8)H,式中H为容屑槽的高度。
但是在设计成形铣刀时,直接按公式计算圆周齿数是困难的,因为式中H尚未确定,而确定它时,又要反过来依据铣刀的圆周齿数。因而在设计时,可根据生产经验按铣刀外圆直径的大小预先选定圆周齿数,在设计计算出铣刀的其他结构参数后再反过来校验圆周齿数设计得是否合适。
7.铣刀的后角及铲削量K
设铲齿成形铣刀的顶刃径向后角为αf,一般取αf=10o-15o。相应的铲削量可按下式计算:K=tgαfΠdo/Zk,式中do为铣刀外径,Zk为圆周齿数。求出铲削量后,应按附录表40所列的铲床凸轮的升距选取相近的K值。
初步选定径向后角和计算出铲削量以后,需验算刀齿侧刃上一点x的主剖面后角αox,验算应选ψx最小处的x点,验算公式可按下面公式:
tgαox=tgα
sinψx
f
应使αox不小于2-3o。实际计算表明,当ψx<15时,常满足这宜要求,可采用增大顶刃后角,斜置工件,斜铲齿等方法增大侧刃后角。
对于精度要求高的成形铣刀,其齿背除铲齿外尚需进行铲磨。为使铲磨时又砂轮空刀,齿背后部应做出深铲部分。选择II型深铲形式,经计算选K=4,K2=0.7-0.8
3
4
8.容屑槽尺寸 (1)容屑槽底半径r
可按下式计算:r =Π[do-2(h+K)]/2AZ h
式中A 为系数,当铲齿凸轮空程角δ=60时,A =6,当δ=90时,A =4。对于需要铲磨齿背的成形铣刀,通常取δ=90o 计算出的r 应圆整刀0.5mm 。
(2)容屑槽间角θ:一般取20o -35o (3)容屑槽深度H :H =h +K+K 2+r 9.分屑槽尺寸
当铣刀宽度B<20时,切削刃上不需要作分屑槽。
10.刀齿、刀体强度和砂轮干涉的校验
由以上所述可以看出,在确定铲齿成形铣刀的外径do ,齿数Zk ,铲削量K ,容屑槽深度H......等参数时,常常互相牵涉,难以直接确定某一参数。因此,需采取试算的方法,首先假设几个参数的数据,再根据他们确定其他一些参数。这样选定成形铣刀的各参数后,还需进行校验,检验铣刀结构是否紧凑,合理,刀体,刀齿强度是否足够。
HBS210 ;强度σb
内径 020.0041.026--=f D
键数 6=Z
5
键宽 040
.0098.06--=b
2.2设计步骤
⑴ 齿槽半角
=180/Z=180/6=30o
⑵ 齿顶圆弧中心半角 ψ=f D B /arcsin -? =?=?-?=-?7.163.133026
6
arcsin 30
⑶ 齿顶宽 47.77.16sin 26sin =?==?ψf a D B ⑷ 齿廓高度 4)2~1(2
26
30)2~1(=+-=
+=mm h h w ⑸ 铣刀宽度 1.12304247.72=???+=?+=tg tg h B B a ? 取B=13 ⑹ 铣刀齿顶圆弧半径 mm R f 132
26
==
⑺ 铣刀前角 ?=0f γ
⑻ 容屑槽形式 在铣削深度较小和刀齿强度足够的情况下,应采用平底式;在铣
削深度较大时,宜采用加强式。 故该容屑槽选择采用平底式。
⑼ 铣刀孔径 根据切削宽度B=13查表3-4,可得d=22mm
⑽ 铣刀外径 58542.2222)6~2(2.2)2.2~2(0=+?+?=++=mm h d d ⑾ 铣刀齿数 查表3-6 12=k Z
⑿ 铣刀后角 ?=12f α 1.030sin 12sin 0=??==tg k tg tg r f αα 故0α= ?6 可满足要求 ⒀ 铲削量 9.21212
58
=???=
=
tg tg Z d k f k
παπ
查附表—2 取k=3 f k =4.5 ⒁ 容屑槽半径 23.112
42)]
34(258[2)]
(2[0=??+-=
+-=
ππk
AZ k h d r 取r=2
⒂ 容屑槽间角 ?=25θ ⒃ 容屑槽深度 75.92
1
=+++
=r k k h H ⒄ 分屑槽尺寸 因为该铣刀宽度小于20,故切削刃上不需做分屑槽
6
⒅ 键槽尺寸和内孔空刀尺寸
查附录表1得 d=22,r=1.0,t=17.6,1't =24.1,h=4
查附录表3 1l =9
⒆ 校验 ①检验刀齿强度
齿根宽度C 25.8)
2(5.24
3
)2(00=-≈
?-≈
k
k
Z H d Z H d c π
8.084.075
.925.8>==H C 所以刀齿强度满足要求 ②检验刀体强度 81.82
20=--=d
H d m d m )5.0~3.0(≥ 所以刀体满足要求
2.3矩形花键铣刀的技术条件
1. 光洁度(按GB1031-68)
(1)刀齿前刀面,内孔表面、端面及铲磨铣刀的齿背表面--不低于7 (2)铲齿铣刀的齿背面--不低于6 (3)其余部分--不低于4 2. 尺寸公差:
表4
表5
表6
铣刀材料一般用高速钢,热处理后硬度应为HRC63-66。在铣刀的工作部分,不得有脱碳层和软点。
7
8
三.拉刀设计
拉刀是一种高生产率的刀具,可以用来加工各种形状的通孔、直槽、螺旋槽以及直线或
曲线外表面,广泛的用于大量和成批生产中。
拉刀的种类如图(1)
用于拉削的成形刀具。刀具表面上有多排刀齿,各排刀齿的尺寸和形状从切入端至切出端依次增加和变化。当拉刀作拉削运动时,每个刀齿就从工件上切下一定厚度的金属,最终得到所要求的尺寸和形状。拉刀常用于成批和大量生产中加工圆孔、花键孔、键槽、平面和成形表面等, 生产率很高。拉刀按加工表面部位的不同,分为内拉刀和外拉刀;按工作时受力方式的不同,分为拉刀和推刀。推刀常用于校准热处理后的型孔。
拉刀的种类虽多,但结构组成都类似。如普通圆孔拉刀的结构组成为:柄部,用以夹持拉刀和传递动力;颈部,起连接作用;过渡锥,将拉刀前导部引入工件;前导部,起引导作用,防止拉刀歪斜;切削齿,完成切削工作,由粗切齿和精切齿组成;校准齿,起修光和校准作用,并作为精切齿的后备齿;后导部,用于支承工件,防止刀齿切离前因工件下垂而损坏加工表面和刀齿;后托柄,承托拉刀。
拉刀的结构和刀齿形状与拉削方式有关。拉削方式通常分为分层拉削和分块拉削两类。前者又分成形式和渐成式;后者又分轮切式和综合轮切式。成形式拉刀各刀齿的廓形均与被加工表面的最终形状相似;渐成式拉刀的刀齿形状与工件形状不同,工件的形状是由各刀齿依次切削后逐渐形成。轮切式拉刀由多组刀齿组成,每组有几个直径相同的刀齿分别切去一层
金属中的一段,各组刀齿轮换切去各层金属。综合轮切式拉刀的粗切齿采用轮切式,精切齿采用成形式。轮切式拉刀切削厚度较分层拉削的拉刀大得多,具有较高的生产率,但制造较难。
拉刀常用高速钢整体制造,也可做成组合式。硬质合金拉刀一般为组合式,因生产率高、寿命长,在汽车工业中常用于加工缸体和轴承盖等零件,但硬质合金拉刀制造困难。
(一)选定刀具类型和材料的依据
1选择刀具类型:
对每种工件进行工艺设计和工艺装备设计时,必须考虑选用合适的刀具类型。事实上,对同一个工件,常可用多种不同的刀具加工出来。
采用的刀具类型不同将对加工生产率和精度有重要影响。总结更多的高生产率刀具可以看出,增加刀具同时参加切削的刀刃长度能有效的提高其生产效率。例如,用花键拉刀加工花键孔时,同时参加切削的刀刃长度l=B×n×Zi,其中B为键宽,n为键数,Zi为在拉削长度内同时参加切削的齿数。若用插刀同时参加切削的刀刃长度比插刀大得多,因而生产率也高得多。
2正确选择刀具材料:
刀具材料选择得是否恰当对刀具的生产率有重要的影响。因为硬质合金比高速钢及其他工具钢生产率高得多,因此,在能采用硬质合金、的情况下应尽力采用。由于目前硬质合金的性能还有许多缺陷,如脆性大,极难加工等,使他在许多刀具上应用还很困难,因而,目前许多复杂刀具还主要应用高速钢制造。
拉刀结构复杂,造价昂贵,因此要求采用耐磨的刀具材料,以提高其耐用度;考虑到还应有良好的工艺性能,根据《刀具课程设计指导书》表29,选择高速工具钢,其应用范围用于各种刀具,特别是形状较复杂的刀具。根据表30,选择W18Cr4V。
(二)刀具结构及各部分功用
1拉刀的结构
9
10
图1
表1
代号名称功用
1 柄部夹持拉刀,传递动力
2 颈部
连接柄部和后面各部,其直径与柄部相同或略小,拉刀材
料及规格等标记一般打在颈部。
3 过度锥颈部到前导部的过渡部分,使拉刀容易进入工件孔中。
4 前导部起引导拉刀切削部进入工件的作用,
5 切削部担负切削工作,包括粗切齿、过渡齿及精切齿。
6 校准部
起刮光、校准作用,提高工件表面光洁度及精度,并作为
切削部的后备部。
7 后导部
保持拉刀与工件的最后相对位置,防止在拉刀即将离开工
件时因工件下垂而损坏工件已加工表面及刀齿。
8 尾部
支持拉刀使之不下垂,多用于较大较长的拉刀,也用于安
装压力环。
2 切削方式:采用分层拉削方式中的同廓式拉削方式
拉刀刀齿结构:表2
名称功用
11
3圆孔拉刀 3.1设计要求
b =400Mpa ;
孔的直径: a D =021
.00
25 3.2设计步骤 ⑴拉床及其他条件
选取拉床型号:L6120型,工作状况:良好的旧拉床。 采用10%的极压乳化液。
12 设计时应考虑:预制孔加工方式,标准麻花钻钻削,拉削变形量,拉削后孔收缩,收缩量(在直径上)为0.01。 ⑵刀具材料及热处理硬度的选择
参考附录表5选V C W r 418高速钢按整体式制造拉刀。热处理要求见图。 ⑶拉削方式的选择
综合式拉刀较短,适于拉削碳钢和低合金钢,拉削精度和表面质量并不低于其它拉削方式,且拉刀耐用度较高。因此,选用综合式拉削。 ⑷刀齿几何参数的选择
按表4-2、表4-3选择,?=100γ ?=501γ ?+?=1'3020α 1.01≤a b ⑸校准齿直径的确定
分别以脚标o 、w 、m 、c 、g 、j 和x 依次表示拉刀、预制孔、拉削孔、粗切齿、过渡齿、精切齿和校准齿。
dox=dmmax+δ=25.021+0.01=25.031mm
式中 δ:拉削变形(收缩量),δ=0.01 mm 。 ⑹拉削余量的确定
计算拉削余量(按表4-1)为
A ′=0.005dm+(0.1~0.2) l
=(0.005 25+0.15
25 ) mm =0.875 mm
按GB6137-85<<锥柄长麻花钻>>第1系列取Φ24.00 mm 的钻头。这样,实际拉削量为
A= dox –dmmin=25.031 - 24 = 1.031 mm ⑺齿升量的确定
按表4-4,选取粗切齿齿升量af =0.05mm 。 ⑻ 容屑槽的确定
① 计算齿距
按表4-7,粗切齿与过渡齿齿距为P =1.3l =1.325=6.5mm,当P ≤10mm 时,精切齿和校准齿齿距为P j =P x =(0.6~0.8)P=5.2mm
② 选取拉刀容屑槽
查表4-8,选曲线齿背型,粗切齿和过渡齿取深槽,h=3mm :精切齿和校准齿取基本槽,h=2.5mm 。
③校验容屑条件
13
查表4-10得容屑系数k =3.0,则
h ′=1.13l af k )2(=1.13 2505.025.2???mm=2.5mm
显然,h ′<=h ,容屑条件校验合格。
④校验同时工作齿数
照表4-7计算(l/p )=30/7=4, z emin =4,z emax =5。满足3≤z e ≤8的校验条件,校验合格。 ⑼ 分屑槽参数的确定
拉刀粗切齿与过度齿采用弧形分屑槽,精切齿(最后一个精切齿除外)采用三角形分屑槽。弧形槽按表4-12设计,当min 0d =24.00mm ,槽数n k =8,槽宽
a=min 0d sin90o /n k -(0.3~0.7)=24 sin90o /8-(0.3~0.7)=4.18mm
切屑宽度 a w =2d omin sin90o
/n k -a=2×24×sin90o
/8-4.18=5.18mm 因a w >a ,可使拉削表面质量较好,前后刀齿重叠拉削而无空隙。
三角形槽按表4-11设计,d 。=25mm, 槽数 N=(1/7~1/6)πd 。=13, 槽宽b=1~1.2mm,深h ′=0.4~0.5mm,槽形角w ≥90o 。
前后刀齿的分屑槽应在圆周方向错开半个槽距,交错排列。 ⑽拉刀前柄的选择
按表4-17,选用Ⅱ型—A 无周向定位面的圆柱形前柄,取d 1=23mm,卡爪处底径d 2=19mm,其他见拉刀的cad 图。
拉刀无需设后柄。 ⑾拉刀强度与拉床载荷的校验
按表4-20、表4-21和表4-22计算最大拉削力。根据综合式拉削特点,切削厚度a c =2a f 。: Fmax= F z ′∑a w Z emax k 0 k 1 k 2 k 3 k 4×10ˉ
3
=242×30π/2×5×1.27×1.15×1.13×1.0×1.0×10-3KN=94.1KN
拉刀最小断面为前柄卡爪底部,其面积为 Armin =πd 22/4=π 192/4mm 2=283.5mm 2 危险截面部位的拉应力为 σ=F max /A rmin =94.1/283.5GPa=0.33GPa
按表4-25,高速钢圆拉刀许用应力[б]=0.35GPa,显然,σ<[σ],拉刀强度校验合格。 按表4-23、表4-24和已知L6120型良好状态旧拉床,可算出拉床允许拉力 F r k=200 0.8KN=160KN
显然,Fmax ⑿拉刀齿数和每齿直径尺寸的确定 按本章一、3.齿升量中所述,取过度齿与精切齿齿升量递减为:0.03、0.025、0.020、 0.015、0.01、0.01mm,共切除余量 A g+ j A=2(0.03+0.025+0.020+0.015+0.01+0.01)mm=0.22mm 其中,前2齿齿升量大于1/2a f,可属过渡齿;后4齿齿升量较小,属精切齿。 粗切齿齿数按下式计算后取整为 z c=[A-(A g+ j A)]/2a f+1=(1.031-0.22)/2 0.05+1=9 粗切齿、过渡齿、精切齿共切除余量 [(9-1)×2×0.05+0.22]mm=1.02mm 剩下(1.031-1.02)mm=0.01mm的余量未切除,需增设一个精切齿切到要求的尺寸。 按表4-14,取校准齿7个,其直径尺寸d ox已在前面计算确定了。 这样,拉刀总齿数为 z o +z g +z j +z x =9+2+5+7=23 图4-1中按齿号列出了各齿直径尺寸及其公差。 14 15 ⒀ 拉刀其他部分的确定 按表4-19: 前柄 l 1=90mm d 1=23f8mm 颈部 l 2=m+B s +A-l 3≈120mm d 2=d 1-0.5mm=22.5mm (取m=15, B s =75, A=35) 过渡锥l 3=15mm 前导部 l 4=40mm d 4=d wmin =24f7mm 后导部7l =25mm d 7=d mmin =25mm 拉刀前柄端面至第1刀齿的距离 L 1′=l 1′+m+B s ′+A+l 4=(90+15+75+35+40)mm=255mm ⒁ 拉刀总长的确定和效验效验 粗切齿与过度齿长 l 5=10×(9+2)=110mm 精切齿与效准齿长 l 6=10×(5+7)=120mm 拉刀总长 L=L ′+l 5+l 6+7l =510mm 按表4-26允许拉刀总长为24d o =24×25mm=600mm,显然,拉刀短得多,所以长度合格。 3.3制定拉刀技术条件 1、拉刀材料:W6Mo5Gr4V2 2、拉刀热处理硬度:刀齿及后导部:63~66 HRC ;前导部:6066 HRC ;前柄:45~58 HRC 。 3、拉刀表面不能有裂纹、碰伤、锈迹等影响使用性能的缺陷。 4、拉刀切削刃应锋利,不得有毛刺、崩刃和磨削烧伤。 5、拉刀容屑槽的连接应圆滑,不允许有台阶,一般应磨光槽底。 6、拉刀各部分的径向圆跳动应在同一个方向。 7.拉刀各部分的表面粗糙度: 刀齿前面Ra0.8μm后导部表面Ra0.8μm 刀齿后面Ra0.8μm柄部表面Ra1.6μm 刃带表面Ra0.4μm颈部表面Ra6.4μm 前导部表面Ra0.8μm过渡锥表面Ra1.6μm 8.拉刀外径在全长上的径向跳动不超过0.06mm。 9、花键齿等分累计误差0.015mm. 16 总结 课程设计作为工科院校大学生的必修环节,不仅是巩固大学生大学所学知识的重要环节,而且也是在检验毕业生综合应用知识的能力、自学能力、独立操作能力和培养创新能力,是大学生参加工作前的一次实践性锻炼。 大学三年的学习即将结束,在我们即将进入大四,踏入社会之前,通过课程设计来检查和考验我们在这几年的所学的知识,同时对于我们自身来说,这次课程设计很贴切地把一些实践性的东西引入我们的设计中和平时所学的理论知识相关联。为我们无论是在将来的工作或者是继续学习的过程中打下一个坚实的基础。 通过这一学期的学习和对有关资料的查阅,我运用所学的专业知识和从与专业相关联的课程为出发点,设计了刀具零件的工艺、编制了刀具零件的加工程序,并复习了所学软件AUTOCAD、PRO/E的运用,同时学习了其他一些相关软件的应用。在设计思想中尽可能体现了我所学的、掌握和了解的知识。 我从这次课程设计中获益匪浅,在以后的工作中,肯定会遇到许多困难,但回想起这设计经历的时候,我就萌发出那种和困难做斗争的勇气。 当然由于设计经验的不足,在设计过程中难免有不足和缺点,但是我绝得得到教训也算是一种收获吧。 一周的课程设计很快就结束了。虽然结果仍不是令人很满意,但是设计的过程让我学到了不少东西:首先学会了主动去检索文献、资料,而且清楚了刀具的很多构造,弥补了课堂上所学知识的不足;其次通过绘图,使自己更加熟练了AutoCAD软件的各种功能。这些都为我以后的学习、工作奠定了坚实的基础。 虽然在设计过程中遇到了不少的困难,但是都在指导老师的耐心指点和同学的共同探讨下克服了。由于时间比较仓促,再加能力有限,设计中肯定存在一些缺陷与不足,望老师在审阅过程中批评指正。 再次感谢老师的指导! 17 四.参考文献 1. 机械工程手册(金属切削刀具) 1980年机械工业出版社 2.金属切削刀具设计 1962年机械工业出版社 3.铣刀,拉刀生产图册 1977年技术标准出版社 4.金属切削手册上海市科学技术交流站 1974年上海人民出版社 5.乐兑谦主编金属切削刀具北京 1993年机械工业出版社 6.刘华明主编金属切削刀具课程设计指导资料 1986年机械工业出版社 7.刀具课程设计指导 1985年机械工业出版社 8.许先绪主编非标准刀具设计手册 1985年机械工业出版社 9. 徐嘉元主编机械加工工艺基础 1990年机械工业出版社18