连铸连轧

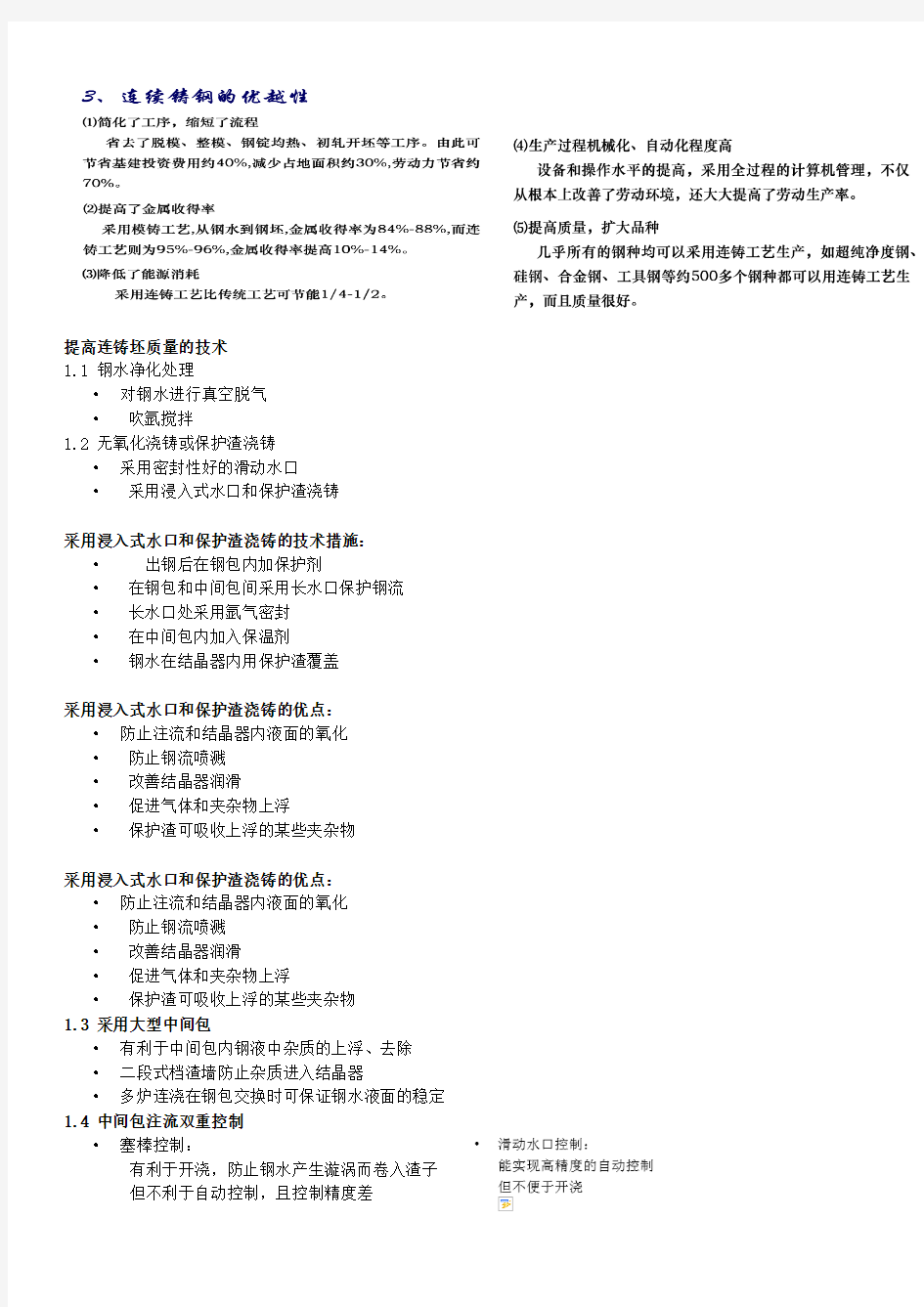
第一章
模铸与连铸的比较
?模铸:钢水→整模→浇铸→脱模→均热→初轧→成品轧制
?连铸:钢水→连铸→成品轧制
?液态铸轧:钢水→铸轧成品
模铸铸锭的凝固
?将炼成的钢水浇注到铸铁或砂型制成的钢锭模内,凝固后形成的锭子称为钢锭。钢锭经轧制或锻压成为钢
材后方能使用,所以钢锭是半成品。
?根据浇注方法的分为上注钢锭和下注钢锭。下注锭的表面质量优于上注锭。
?根据脱氧程度的不同又有沸腾钢钢锭、半镇静钢钢锭和镇静钢钢锭三种。沸腾钢是脱氧不完全的钢,镇静
钢是脱氧完全的钢,半镇静钢的脱氧程度介于前两者之间,接近于镇静钢。
钢锭的应用现状
?模铸锭与连铸坯相比,所占比例逐年减少,最终将减少到约占10%,其中合金钢和不锈钢将减少到20%,
工具钢和特殊钢将减少到40%。这是由于连铸坯可以多炉连浇、收得率高、不需初轧或开坯、能耗低,质量甚至优于模铸锭。
?但模铸镇静钢不可能完全被淘汰,因为锻造用钢、一些小批量生产的高级合金钢及VAR(真空电弧重熔)和
ESR(电渣精炼)用的坯料仍需用模铸镇静钢来生产。
钢锭的质量
?钢锭的质量有表面质量和内部质量之分。
?表面质量:结疤、裂纹、表皮的纯净度和致密度。
?内部质量:钢锭内部的纯净度、致密度、低倍非金属夹杂物数量和宏观偏析的程度。
?沸腾钢的表面质量好,但由于锭心偏析大,内部质量不如镇静钢。
连铸:使金属液由中间包经浸入式水口不断地通过水冷结晶器,凝成硬壳后从结晶器下方出口连续拉出,经喷水冷却,全部凝固后切成坯料的一种铸造工艺。
连铸的设备以弧形连铸机为例,主要有钢包支承装置、盛钢桶(钢包)、中间罐、结晶器(一次冷却装置)、结晶器振动装置、铸坯导向和二次冷却装置、引锭杆、拉坯矫直装置(拉矫机)、切割设备和铸坯运出装置(见辊道和横向移送设备)等
连铸的优点
变间断生产为连续生产,产量↑(连铸比,连浇炉数)
冷却强度大,铸造组织比较细密,偏析小
切头切尾率少,成才过程烧损和切损少,成材率提高8~12%
工艺过程缩短,生产周期短,能耗、运输成本降低,能耗降低30~60%(视是否热装、热送、直接轧制而定)
环保条件好,无整、脱模时的污染
便于自动化,提高技术水平
连铸的好处在于节能和提高金属收得率。
连铸的发展史
1、现代炼钢技术的发展(连铸技术的作用)
(1) 1947年-1974年:
技术特点:转炉、高炉的大型化;以模铸-初轧为核心,生产外延扩大。
(2) 1974年-1989年:
技术特点:全连铸工艺,以连铸机为核心。
(3) 1989年-现在:
提高连铸坯质量的技术
1.1 钢水净化处理
?对钢水进行真空脱气
?吹氩搅拌
1.2 无氧化浇铸或保护渣浇铸
?采用密封性好的滑动水口
?采用浸入式水口和保护渣浇铸
采用浸入式水口和保护渣浇铸的技术措施:
?出钢后在钢包内加保护剂
?在钢包和中间包间采用长水口保护钢流
?长水口处采用氩气密封
?在中间包内加入保温剂
?钢水在结晶器内用保护渣覆盖
采用浸入式水口和保护渣浇铸的优点:
?防止注流和结晶器内液面的氧化
?防止钢流喷溅
?改善结晶器润滑
?促进气体和夹杂物上浮
?保护渣可吸收上浮的某些夹杂物
采用浸入式水口和保护渣浇铸的优点:
?防止注流和结晶器内液面的氧化
?防止钢流喷溅
?改善结晶器润滑
?促进气体和夹杂物上浮
?保护渣可吸收上浮的某些夹杂物
1.3 采用大型中间包
?有利于中间包内钢液中杂质的上浮、去除
?二段式档渣墙防止杂质进入结晶器
?多炉连浇在钢包交换时可保证钢水液面的稳定1.4 中间包注流双重控制
?塞棒控制:
有利于开浇,防止钢水产生漩涡而卷入渣子
但不利于自动控制,且控制精度差
1.5 中间包重量自动控制
在铸造速度波动时,能保证结晶器液位的稳定
结晶器液位自动控制→浇钢的自动控制→铸坯质量的稳定
1.6 结晶器铜板双镀层
?双镀层铜板,既保证了板坯的表面质量,又延长了结晶器的使用寿命。
1.7 小辊密排及分节辊
?小辊密排以解决鼓肚问题
?分节辊以保证轧辊的刚度
1.8 最佳二次冷却控制
控制冷却方法:
?固定喷水法
?水表控制法
?参数控制法
?表面稳定控制法
1.9 采用电磁搅拌
?减小连铸坯内部的成分偏析和组织疏松
?扩大等轴晶带
?保证特殊钢材的质量,浇铸速度可以进一步提高
M-EMS: 结晶器电磁搅拌
S-EMS: 二冷区电磁搅拌
F-EMS: 凝固末端电磁搅拌
1.9 采用电磁搅拌
1. 净化弯月面处的熔体
2. 非金属夹杂物及气泡的离心化
3. 冲刷凝固前沿
4. 形成等轴晶
1.10 通过设置垂直段,有利于夹杂
物的上浮、去除,提高内部质量,
消除连铸坯裂纹
1.11 采用高温矫直、多点矫直等措施
减小矫直过程中的变形内力,避
免铸坯内裂的发生
1.12 压缩铸造,减少板坯内部缺陷
轻压下的作用:
?(1) 破碎“晶桥”
?(2) 补偿冷却收缩
?(3) 减小“鼓肚”量
1.13 板坯质量异常判定模型
?根据仪表电器提供的各种设备参数和工艺参数,对照相应的技术标准,对板坯的质量异常情况进行跟踪判定,实现控制的自动化。
1.14 快速硫印
?板坯质量的管理和检测技术
?快速检测板坯内部硫的分布,检查偏析和内裂
提高钢材质量的技术
2.1 采取适宜的轧制工艺制度
2.2 严格遵守加热、轧制及热处理工艺制度
2.3 合理设计轧辊孔型
2.4 利用轧制工序,消除或减小铸坯内部
疏松等缺陷。
连铸坯的保温技术
3.1 连铸坯的运送保温
固定保温罩、运输保温车以及绝热辊道等等
3.2 连铸坯在轧制过程中的保温
?防止或减小温降
?对连铸坯边角部分进行补偿加热
电磁感应加热、火焰加热法和保温罩加热法
?利用热卷曲箱将中间带坯卷成板卷,减少热量损失
连铸机型
①立式(空心管坯、大方坯)
②立弯式(异形坯、大板坯、大圆坯)
③弧形(薄板坯、圆坯、方坯)超低头(小方坯、小板坯)()
④水平式(拉线坯、无缝管坯小方坯)
不同形式铸机,厂房高度不同,液相钢水静压力不同,气体夹杂上浮不同,矫直应力不同,要根据钢种规格选取。
立式连铸机:立弯式连铸机:
弧形连铸机:
第二章:
钢铁冶金系统工程
1.工艺过程:矿石→选矿(磁选、浮选)→烧结(球团)→炼铁(高炉、非高炉)→炼钢(平炉、转炉)→
铸造(模铸、连铸)→轧制(热轧、冷轧)→成品(板、管、型、线)。
2.最终产品的组织性能要满足用户的各种需要。(强度、塑性、韧性、加工性能、特殊物理化学性能)。
3.最终性能取决于各工序的性能、组织、成份控制、具有遗传性、要求系列优化。
连铸钢水的准备
要想使连铸生产稳定高效地进行,并且保证铸坯质量,首先要准备好成分、温度、脱氧程度及纯净度都合格的钢水。
这里重点介绍钢水温度的要求。
另外,炼钢工序和连铸工序要紧密配合,步调一致。
温度合格:控制出钢温度、浇铸温度(考虑过程温降)。
浇铸温度:指钢水进入结晶器时的温度。也可以指中间包内的钢水温度.
通常一炉钢水需在中间包内测温3次,即开浇后5min、浇铸中期和浇铸结束前5min,而这3次温平均值被视为平均浇铸温度。
钢水的浇铸温度要求:(在一定范围内的合理温度)
◆在尽可能高的拉速下,保证铸坯出结晶器时形成足够厚度的坯壳,使连铸过程安全地进行下去;
◆在结晶器内,钢水将热量平稳的传导给铜板,使周边坯壳厚度能均匀的生长,保证铸坯表面质量。
钢水温度过高的危害:
①出结晶器坯壳薄,容易漏钢;
②耐火材料侵蚀加快,各项消耗增加,易导致铸流失控,降低浇铸安全性;
③增加非金属夹杂,影响板坯内在质量;
⑤铸坯柱状晶发达,枝晶晶粒大,钢质变差;
⑥中心偏析加重,易产生中心线裂纹;钢中气体夹杂物增加,铸坯易裂;
钢水温度过低的危害:
①浇铸困难,容易发生水口堵塞,浇铸中断;
②结晶器液面结壳,钢水粘度增加,连铸表面容易产生结疱、夹渣、裂纹等缺陷;
③气体夹杂物和非金属夹杂不易上浮,影响铸坯内在质量。
1.△T1 钢水从炼钢炉的出钢口流入钢包这个过程的温降
热量损失形式:钢流辐射热损失、对流热损失、钢包吸热。
影响因素:出钢时间、出钢温度及钢包的使用状况。
降低热量损失的措施:
①尽量降低出钢温度
②减少出钢时间
③维护好出钢口,使出钢过程中最大程度保持钢流的完整性
④钢包预热
⑤保持包底干净
2、△T
出完钢钢包内钢水到精炼开始前经过的运输和静置过程中产生的温降
2
热量损失形式:钢水上表面通过渣层的热损失、钢包包衬吸热。
影响因素:钢包的容量、包衬材质及温度,钢包的运输距离。
降低热量损失的措施:
①钢包烘烤、充分预热
②减少留置时间
③在钢包内加入合适的保温剂
3、△T3 钢包精炼过程的温降
热量损失取决于二次精炼的时间和方法。
4、△T4 钢包精炼结束钢水在静置和运往连铸平台的温降
热量损失形式:钢水上表面通过渣层的热
损失、钢包包衬吸热。
热量损失大小:钢包内衬吸热降低
加了保温剂,温降减小
5、△T5 钢水从钢包注入中间包过程中产生的温降
热量损失形式:辐射热损失、对流热损失、钢包吸热。
影响因素:钢流保护状况;中间包的容量、材质、
烘烤温度及保温措施
降低热量损失的措施:
①钢流需保护,采用长水口
②减少浇铸时间
③充分预热中间包内衬
④中间包钢液面添加保温剂
⑤提高连浇炉数
㈢钢水温度控制要点
1、出钢温度控制:
①提高终点温度命中率
②确保从出钢到二次精炼站,钢包钢水温度处于目标范围之内
2、充分发挥钢包精炼的温度与时间的协调作用
3、控制和减少从钢包到中间包的温度损失
采用长水口保护浇铸;钢包、中间包加保温剂
3、钢水在钢包中的温度控制
根据冶炼钢种严格控制出钢温度,使其在较窄的范围内变化;其次,要最大限度地减少从出钢、钢包中、钢包运送途中及进入中间包的整个过程中的温降。
实际生产中需采取在钢包内调整钢水温度的措施:
①钢包吹氩调温。
②加废钢调温。
③在钢包中加热钢水技术。
④钢水包的保温。
2.成份合格
基本成分:
C 来自铁水或增碳剂
Si 来自脱氧剂、铁合金
Mn 来自铁水、脱氧剂、铁合金
P 来自铁水、矿石
S 来自铁水中的焦炭、石灰
P 、S为有害元素,S引起热脆,P引起冷脆
炉外精炼
1.铁水预脱P、S
在铁水罐内和鱼雷罐车内喷CaSi,CaO、Mg 粉;
脱P希望温度较低,渣中FeO较高,有一定碱度[CaO/ SiO2];
脱S希望温度较高,碱度较高,温度较高,渣流动性好;
2.有真空的炉外精炼(可以脱气,有利于冶炼超低碳钢和高强钢)
3.有热源的炉外精炼
4.炉外精炼所起的作用
缩短冶炼周期,便于和连铸匹配(缓冲环节)
吹Ar搅拌,加快冶金反应,气体夹杂物上浮,均匀罐内温度
喷粉、吐丝、渣洗深脱硫(加大反应界面,提高脱硫效率)
微调成份,提高合金收得率
调节连铸温度
真空脱气、脱碳、脱氧
一、拉速定义:拉坯速度是以每分钟从结晶器拉出的铸坯长度来表示.拉坯速度应和钢液的浇注速度相一致。
二、拉速控制的意义:拉速控制合理,不但可以保证连铸生产的顺利进行,而且可以提高连铸生产能力,改善铸坯的质量.现代连铸追求高拉速.
三、拉速确定:
1、确定原则:确保铸坯出结晶器时的能承受钢水的静压力而不破裂,对于参数一定的结晶器,
拉速高时,坯壳薄;反之拉速低时则形成的坯壳厚。一般,拉速应确保出结晶器的坯壳厚度为8-15mm。
2、影响因素
A、机身长度的限制
B、拉坯力的限制
C、结晶器导热能力的限制
D、拉坯速度对铸坯质量的影响
E、钢水过热度的影响
F、钢种影响
铸坯冷却的控制
一、一冷确定:钢水在结晶器内的冷却即一冷,其冷却效果可以由通过结晶器壁传出的热流的大小来
度量。
1、一冷作用:一冷就是结晶器通水冷却。其作用是确保铸坯在结晶器内形成一定的初生坯壳。
2、一冷确定原则:一冷通水是根据经验确定,以在一定工艺条件下钢水在结晶器内能够形成足够的坯壳厚
度和确保结晶器安全运行为前提。
通常结晶器周边供水2L/mm.min。进出水温差不超过100C,出水温度控制在45-5000C为宜,水压控制在0.4-0.7Mpa.
1、二冷作用:二次冷却是指出结晶器的铸坯在连铸机二冷段进行的冷却过程.其目的是对带有液芯的铸坯实施喷水冷却,使其完全凝固,以达到在拉坯过程中均匀冷却.
2、二冷强度确定原则:二冷通常结合铸坯传热与铸坯冶金质量两个方面来考虑.铸坯刚离开结晶器,要采用大量水冷却以迅速增加坯壳厚度,随着铸坯在二冷区移动,坯壳厚度增加,喷水量逐渐降低.因此,二冷区可分若干冷却段,每个冷却段单独进行水量控制.同时考虑钢种对裂纹敏感性而有针对性的调整二冷喷水量.
3、二冷水量与水压:
对普碳钢低合金钢,冷却强度为:1.0-1.2L/Kg钢.
对中碳钢、高碳钢,冷却强度为:0.6-0.8L/Kg钢.
对热裂纹敏感性强的钢种,冷却强度为:0.4-0.6L/Kg钢.
水压为0.1-0.5MPa
连铸与冶炼能力、节奏的匹配
能力匹配。一般冶炼能力大于连铸能力15~20%保证连浇,轧钢能力大于连铸能力20%左右,提高热装热送率和连浇率。
提高连浇炉数
①冶炼、精炼、连铸周期的密切配合和生产组织
②防止漏钢技术
③提高自动开浇率(引流砂质量)
④快换中包和水口技术,提高中包水口寿命
⑤异钢种多炉连浇技术
⑥稳定的铸机状态和无缺陷铸坯生产技术
⑦计算机控制浇钢
⑧铸与轧的密切配合
连铸与模铸的比较
模铸:钢水→整模→浇铸→脱模→均热→初轧→成品轧制
连铸:钢水→连铸→成品轧制
液态铸轧:钢水→铸轧成品
连铸与模铸的分工
连铸的优点:
变间断生产为连续生产,产量↑(连铸比,连浇炉数)
冷却强度大,铸造组织比较细密,偏析小
切头切尾率少,成才过程烧损和切损少,成材率提高8~12%
工艺过程缩短,生产周期短,能耗、运输成本降低,能耗降低30~60%(视是否热装、热送、直接轧制而定)
环保条件好,无整、脱模时的污染
便于自动化,提高技术水平
连铸和模铸的分工:
某些特殊钢仍由模铸生产
特大特厚产品仍由模铸生产(连铸最大规格方坯450×450,400×600;板400×3200
连铸不能浇铸沸腾钢
小批量多品种材不适合连铸生产,连铸适合大批量品种比较单一产品的生产
可以连铸和初轧联合生产,各取所长
连铸机的构造和各部分功能
1.钢包回转台及钢包车
保证连续浇铸及换包
注中保温及称重
2.中间包
①储水池作用,保证换罐时注流和液面稳定
②分流作用(1~8流)要求各流均衡
③中间包冶金:
挡渣坝使气体夹杂上浮,过滤器去除Al2O3夹杂;
中间包容量和深度,保证包内存留时间在5min左右;
中间包内加热控温(等离子,电感加热)保证过热度;
中间包内喂丝,微调成份;
④中间包的升、降、对中
3.保护浇铸系统
①长水口、快换机械、Ar气保护自动开浇、下渣监测
②埋入水口、快换机械、吐出孔设计、埋入深度控制、渣线调整
③中包覆盖剂、结晶器保护渣、保护渣的三层结构
防止氧化、液面保温、吸附夹杂、润滑模型、调节热流、改善表面;
保护渣的性能:熔点、熔速、再结晶温度、粘度;
④滑动水口和塞棒
4.结晶器及结晶器振动装置
①结晶器的作用:是连铸机的心脏。
形成初生坯壳并保证其强度;
保证热流,快速凝固;
结晶器内钢水流动控制(电磁制动,埋入水口设计)液面波动小于5mm。
②结晶器的构造
整体式和组合式;
结晶器的长度和锥度 h=200~1200mm,i=0.6~1.0%;
③结晶器振动
频率和振幅;
振痕的产生和负滑脱;
正弦振动和非正弦振动;
5.二冷区及支撑辊(足辊、格栅、支撑辊)
①二冷区和液相穴
②凝固率系数及其应用
③比水量和冷却方式(水冷、雾冷、干冷)
④分节辊和二冷对中的要求,防止“鼓肚”
⑤热行和冷行的二冷水表
6.拉引矫直装置(拉坯、矫直送引锭杆)
①矫直应力和“压缩铸造”,带液芯矫直
②连续矫直和分布矫直
③拉速控制、拉速变化引起的系列反应
↑,液面波动↓,坯壳厚度↓,保护渣要求↑;
水调整,防止拉漏(漏钢预报);
7.切割装置
①飞剪及火焰切割
②定尺切割机械
③毛刺去除
8.引锭装置
①上装引锭杆和下装引锭杆
②防止拉漏措施和开浇策略
连铸坯的铸造组织
细晶竖壳带(大的过冷度及结晶器皆造成形核数量多)
柱状晶带(枝晶定向生长及枝晶偏析的生成)
中心等轴晶带(体积结晶、非均质形成)
小钢锭结构(中心偏析及疏松缩孔形成)
控制铸造组织的方法
低过热度浇铸
二冷控制
电磁搅拌。MES、EMS、FEMS、低频大电流产生洛仑兹力,起搅拌作用。
均匀粒度气体夹杂物上浮增加等轴晶加快传热凝固分散偏析连铸大方坯的液芯轧制特点
①液相穴末端轻压下和大压下
②液相穴位置动态跟踪
③用拉矫机改造成轧机
④用测量轧制压力反馈液芯率大小
⑤点压下和面压下,液芯轧制的变形特点
⑥极限压下率
⑦液芯部位重点压下
液芯轧制时控制铸坯的变形和应力状态
①鼓肚和凹陷
②物理变形区和非接触区
③液相穴挤出和连轧移动流量相等自适应
④应力状态控制
连铸坯的表面质量及其控制
表面纵裂纹产生的原因(面裂纹,角裂纹)
表面横裂纹产生的原因(角横裂,面横裂)
气泡和夹杂
应力和裂纹的关系
表面纵裂纹产生的原因及特征:
表面横裂纹产生的原因及特征:
铸坯边角部冷却过强是造成横裂纹的最重要外因,
钢种成分和钢中氮含量、酸溶铝含量过高则是内因;
连铸机设备状态变差等也会增加横裂纹发生几率.
大多数横裂发生在振动波纹的波谷深处。
一般认为,这种裂纹是铸坯矫直时产生抗张力造成的,当铸坯表面存在星状裂纹时,在矫直力作用下,以星状裂纹为缺口,扩展成横裂纹,如果裂纹在角部,就形成角部横裂。
另外,与宽面上的单维散热不同,在棱边上热量的散发是从宽面和窄面两个方向进行的。
棱边的温度明显地低
角部横裂还可能是铸机对中情况不好,使铸坯受到过分弯曲变形出现的。对于容易造成显微偏析的的高碳钢和高S、P钢,如果结晶器摩擦力稍有增加,也会造成坯壳横向撕裂。
防止横向裂纹的措施:
1)稳定结晶器液面。 2)减少振痕深度。 3)减少结晶器摩擦力。 4)采用合理的二次冷却。 5)支
撑辊的对中。6)降低钢中S、P、N、O等元素的含量,加入微量Ti、Zr、Ca等元素,抑制碳化物、氧化物、硫化物和氧化物在晶界上析出。7)结晶器锥度调整合适以及振动正常。
热应力裂纹
由热应力引起的星状细微裂纹,在有氧化铁皮覆盖时难于发现,酸洗或火焰清理后,就能用肉眼观测到,它往往是成组分布的细小晶间裂纹,或呈星状,或呈网状。
星状细微裂纹是由于局部过冷或过大的冷却间歇或局部再加热(例如在粘着氧化铁皮或渣子的下面)等原因产生的应力引起的。
正确的调节二冷区的喷水冷却,获得均匀的水雾分布,应根据拉速的变化调节二冷水量,可防止这种细微星状裂纹的产生。
热脆性裂纹
热脆性裂纹类似于细微星状裂纹,从放大的显微照片上可以清楚地看到在晶粒间有铜的渗入。这种裂纹是沿晶界开裂的。
它是由于高温坯壳与结晶器铜壁摩擦时,铜优先沿晶界扩散,从而降低了铸坯的高温强度而产生裂纹。其他物质如AlN、BN、Nb(CN)和硫化物在晶界的析出也会产生这种裂纹。
采用电镀铬或爆破镀镍的结晶器,有利于防止或减轻这类裂纹;采用合适的保护渣,在坯壳和结晶器之间形成一层均匀的熔融的保护渣薄膜,也有利于防止或减轻这类裂纹;其次,对足辊和扇形段0段正确对中,并加上弱而均匀的二次冷却,都是防止和减轻这类裂纹的有效措施。
皮下气泡
沿柱状晶方向伸长的,位于铸坯表面附近的空间叫气泡,空间细小而密集的叫针孔。按空洞的位置来分,露出表面的叫表面气孔,潜于皮下的叫皮下气泡。气泡会造成成品上的表面缺陷,深度较大时,危害较大。
皮下气泡一般仅在最先浇注的约1.5m长的范围内产生;钢中有较高的气体(如H2、O2)含量,在凝固过程
在浇注过程中注入结晶器的钢流被氧化,过早地往结晶器加保护渣,使之与钢水混和,用生锈的切屑或废钢块填入结晶器引锭头上、中间罐未烘烤干等都是气泡产生的原因。当这些气泡不能从钢中逸出时就会造成气泡缺陷。因此,降低钢水中主要气体如H2、02的含量,就可以减少气泡产生。
要想降低O 2含量,首先要采用强化脱氧措施。用Al在钢包中脱氧时,当铸坯中溶解Al含量>0.0015%时,就可以控制气泡的发生。
实践证明,在浇注过程中对钢流进行保护浇注,防止二次氧化,对减少气泡有明显的效果。
钢水中的H2是造成气泡的一个主要原因,H2进入钢水与大气中水蒸汽分压有密切关系。为减少钢水中的H2,在冶炼过程中应对入炉的原材料进行烘烤干燥;对钢水进行脱气处理。在浇注过程中防止H2浸入钢水,对钢流密封保护,采用保护渣浇注是行之有效的。
降低钢中气体含量、采用合适的结晶器保护渣,并让结晶器钢水上升到浸入式水口出口以上后才加入保护渣、用清洁切屑和废钢块放在结晶器内的引锭头上,中间罐衬和浸入式水口材质一定不能用含有放气的粘结材料。这些都是防止皮下气泡产生的有效措施。
表面夹渣
表面夹渣是指在铸坯表皮下2—10mm镶嵌有大块的渣子,
因而也称皮下夹渣。浇注成铸坯后,夹渣分布在铸坯表面,在无氧化铁皮覆盖,或经火焰清理后可以见到表面夹渣缺陷。从外观看,夹渣缺陷大而浅的属硅锰酸盐系;小而分散,深度在2-10㎜的属Al2O3系夹杂。
若不清除,会造成成品表面缺陷,增加制品的废品率。
表面夹渣对浇注操作和最终轧制成品都是有害的缺陷,在浇注时由于表面夹渣的导热性差,在有表面夹渣的部位,凝固速度减慢,坯壳变薄。容易造成漏钢事故,一般渣子的熔点高易形成表面夹渣。
敞开浇注时,由于二次氧化,结晶器液面有浮渣。浮渣的熔点、流动性,与铜液的浸润性都与浮渣的组成有直接关系。
对硅铝镇静钢来说,浮渣的组成与钢中的 Mn/Si有关;当Mn/Si低时,形成浮渣的熔点高,容易在弯月面处冷凝结壳,产生夹渣的几率较高;因此钢中的Mn/Si大于3为宜。对用铝脱氧的钢,铝线喂入数量也影响夹渣的性质,对钢液加铝量若大于200g/t时,浮渣中A12O3增多,熔点升高,致使铸坯表面夹渣猛增。
此外,可以加入能够软化和吸收浮渣的材料,改善浮渣的流动性,以减少铸坯的表面夹渣。
在用保护渣浇注时,表面夹渣缺陷主要是由于保护渣质量不好,容易形成坚硬渣壳,在结晶器液面波动情况下卷入铸坯表面所致。
水口出孔的形状、尺寸的变化、插入深度、吹Ar气量的多少、塞棒失控以及拉速突然变化等均会引起结晶器液面的波动,严重时导致夹渣;
就其夹渣的内容来看,有未熔的粉状保护渣,也有上浮未来得及被液渣吸收的Al2O3夹杂物,还有吸收溶解了的过量高熔点Al2O3等。
皮下夹渣深度小于2mm,铸坯在加热过程中可以消除;皮下夹杂深度在2—5mm时,热加工前铸坯必须进行表面精整。
消除铸坯表面夹渣应该采取的措施:
(1)要尽量减小结晶器液面波动,最好控制在小于5mm,保持液面稳定。
(2)浸入式水口插入深度应控制在(125±25)mm的最佳位置。
(3)浸入式水口出口的倾角要选择得当,以出口流股不致搅动弯月面渣层为原则。
(4)中间罐塞棒的吹Ar气量要控制合适,防止气泡上浮时,对钢渣界面强烈搅动和翻动。
(5)选用性能良好的保护渣,并且Al203原始含量应小于10%,同时控制一定厚度的液渣层。
此外采用钢包吹氩搅拌、中间罐净化、钢流保护等措施来减少浮渣数量也是很关键的手段。
振痕
在浇注过程中,结晶器振动以避免坯壳与结晶器之间粘结。结晶器上下运动的结果,造成铸坯4个表面上周期性的横纹痕迹.这些痕迹称为振痕。
振痕是坯壳被周期性的拉破又重新焊合的过程造成的。振痕的深度与钢中含碳量有很大关系,一般低碳钢振痕较深,而高碳铜振痕较浅。
当结晶器振动状况不佳,钢液面剧烈波动或保护渣选择不当时,会使振痕加深;并可能在振痕处潜伏横裂纹、夹渣和针孔等缺陷。
为了减少振痕深度,现在连铸机多采用小振幅、高振频的振动模式,同时减少结晶器液面波动和采用粘度较大的保护渣。
表面凹陷:1纵向凹陷
在板坯表面形成的纵向凹陷,它们可能延伸到整个铸坯长度,如果它们被中断,则在侧面位移点上再次开始,其深度可达40-50mm。
在方坯角部附近,平行于角部,有连续的或断续的纵向凹陷,其纵向凹陷通常是由于菱形变形所引起的。
是纵向裂纹的预裂口,通常伴生纵向裂纹,严重的会导致漏钢。
这种表面凹陷主要是由于结晶器壁的不良形状造成铸坯在结晶器中冷却不均匀。
在实际生产中常见的导致因素有:菱形变形伴生的缺陷;结晶器与二次冷却装置对弧不准;二次冷却局部过冷(特别是二次冷却装置的上部);拉矫辊上有金属异物粘附等。
由此造成坯壳不均匀增长,在结晶器出口处,坯壳厚度差达10-15mm,这种不均匀的坯壳厚度,使之产生横向应力,从而出现纵向凹陷。
在浇铸过程中发现有连续的纵向凹陷,首先应观察铸坯有无菱形变形。再检查二次冷却装置喷嘴(特别是二次冷却区上部)是否脱落,喷嘴是否离铸坯的距离太近等。
如果纵向凹陷是有规律的断续的则要检查拉矫辊上是否有冷钢。通常只要保证结晶器均匀冷却和结晶器出口处的均匀喷水冷却,就可预防这种表面纵向凹陷。
表面凹陷:2表面横向凹陷
窄的横向凹陷与浇注方向垂直,它们通常在有规则的间隔内发生,这些横向凹陷往往伴随着结疤和纵向裂纹发生。
凝壳与结晶器接触不良和摩擦阻力是产生横向凹陷的原因,在浇注过程中钢液过冷,靠液面处坯壳收缩离开结晶器壁,随后钢水又流入间隙后形成的。另外,操作中由于结晶器液面波动太大,保护渣渣壳随钢液卷入间隙中也形成这类表面横向凹陷。
局部的横向凹陷是由于操作不当所引起,连续的横向凹陷则与保护渣性状有关。
采用合适的结晶器保护渣来减少结晶器壁的冷却速度,降低结晶器出口处的冷却强度,适当提高拉速、保持正常而稳定的结晶器液面高度是预防这类缺陷产生的一些办法。
表面凹陷:3板坯窄面凹陷
窄面凹陷是窄面向里鼓肚,通常发生在结晶器中,或发生在结晶器下面。
造成这类缺陷主要是结晶器锥度太大,在结晶器下面的足辊区或第一个扇形段(0段)的窄面冷却太急。需要在维修时适当减少结晶器锥度,减缓足辊区或第一扇形段(0段)的冷却强度,就能有效防止窄面凹陷。
重皮
重皮缺陷在铸坯表面像叠加搭桥,以波形出现。重皮通常发生在铸坯中间,但也有发生在靠近边缘处的。
重皮缺陷通常与渣夹杂物一起产生,可达4—5mm深,严重的重皮叠层可在有明显波形的红热板坯上检测到。
重皮缺陷发生在结晶器中,由于浸入式水口深入钢液的深度不够,浸入式水口有缺陷,向结晶器供气大多,中间罐滑动水口开闭太急,都会造成结晶器液面产生不规则的剧烈波动,从而出现严重缺陷,因此,要特别注意浸入式水口的外形好坏、浸入深度和操作稳定性,以防止重皮缺陷产生。
结疤
在紧靠角部或窄面处,坯壳产生破裂,渗漏钢液,在铸坯表面形成结疤,这种缺陷总是与纵向裂纹相连。
在比较严重的情况下,铸坯可能在出结晶器后再次裂开。
产生这类缺陷的主要原因是铸坯窄面冷却不充分,或是结晶器锥度不合适,或是保护渣性能不良,影响冷却效果,或者是结晶器液面波动过大等原因造成的。
采用正确的结晶器锥度和成分合格、性能良好的保护渣,并采用结晶器液面自动控制,保持稳定的结晶器液面,有利于预防结疤缺陷的产生。
表面增碳和偏析
通常连铸坯表面和皮下区的化学成分是很均匀的,但有时也可能发现轻微的负偏析。另外,铸坯表面增碳也是一种偏析。
浇注用保护渣时,一般保护渣内含碳量为3—5%。其中大部分在熔化时已消耗掉,而少量残留的碳聚集在液态渣上面的界面内,形成富碳层,使接近弯月面处的固态渣固有碳的富集。当液面上升时,钢水与富碳
保护渣含碳量大于6%时,增碳现象更为严重。表面增碳层的厚度约为1—2mm。表面增碳对不锈钢非常有害,损害其耐腐蚀性能。
另一种表面偏析现象是在振痕底部富集合金元素如Si、Mn、Ni、Mo等。其含量多少及深度随负滑脱时间增加而加重,即随振痕深度加深而增加。
上述偏析和增碳可以用高频率小振幅的振动模式和保证结晶器液面稳定等措施来减轻。
连铸坯的表面质量及其控制
连铸坯表面质量的好坏决定了铸坯在热加工之前是否需要精整,也是影响金属收得率和成本的重要因素,还是铸坯热送和直接轧制的前提条件。
连铸坯表面缺陷形成的原因较为复杂,但总体来讲,主要是受结晶器内钢液凝固过程所控制。
铸坯的内部质量是指铸坯是否具有正确的凝固结构、偏析程度、内部裂纹、夹杂物含量及分布状况等。
凝固结构是铸坯的低倍组织,即钢液凝固过程中形成等轴晶和柱状晶的比例。铸坯的内部质量与二冷区的冷却及支撑系统密切相关。
液面波动小于5mm,防止卷渣和弯月面破裂
保护渣选择依钢种不同,采用不同的保护渣,开浇渣
提高钢纯净度的措施:
1、无渣出钢
2、选择合适的精炼处理方式
3、采用无氧化浇注技术
4、充分发挥中间罐冶金净化器的作用
5、选用优质耐火材料
6、充分发挥结晶器的作用
7、采用电磁搅拌技术,控制注流运动
包晶钢成分控制
包晶钢 C 0.12~0.17%,最易裂;
Mn/Si>3,可得脱氧产物;
Mn/S>40,减少S的有害作用生成MnS;
S<0.025%,S+P<0.05%,防裂纹;
钢中As、Pb、Sn等总量<0.01%;钢中酸溶Al 0.01~0.02%,完全脱氧;
连铸坯的内部质量及其控制
拉速控制
应力控制
1.拉坯应力
2.鼓肚应力
3.变形应力
4.热应力
5.组织应力(相变应力)
6.矫直应力
7.连铸过程中的脆性曲线
8.零强度温度和零韧性温度
铸坯的的内部裂纹
板坯内部裂纹包括从皮下到接近铸坯中心的裂纹,这些裂纹在凝固过程产生,也叫凝固裂纹。
按其产生的原因有热应力裂纹、弯曲矫直裂纹、菱形变形造成的角部裂纹、压力裂纹,鼓肚裂纹等。
凝固裂纹发生在1200℃以上的高温脆化区,即在固液两相区范围内;
当凝固界面上有拉伸应力作用时,引起一次树枝晶或等轴晶的晶界开裂,随之浓化的钢水填充到这些开裂的缝隙中。因此这种裂纹都伴有偏析存在。
在铸坯断面硫印图上显示出浓厚的偏析线,从此意义上,内部裂纹也可称做“偏析条纹”。
这种宏观偏析不能通过热加工消除,在最终产品中会遗留条纹状缺陷,对机械性能,尤其是横向性能有影
1、减少铸坯内部裂纹的措施
(1)采用压缩浇铸技术,或者应用多点矫直技术
(2)二冷区采用合适夹辊辊距,支撑辊准确对弧
(3)二冷水分配适当,保持铸坯表面温度均匀
(4)取合适的拉辊压下量,最好采用液压控制机构
2、夹杂物的控制
从炼钢→精炼→连铸生产洁净钢,主要控制对策是:
(1) 控制炼钢炉下渣量
挡渣法(偏心炉底出钢、气动法、挡渣球);
扒渣法:目标是钢包渣层厚<50mm,下渣2kg/t。
(2) 钢包渣氧化性控制
出钢渣中高(FeO+MnO)是渣子氧势量度。
(FeO+MnO)↑板坯T[O]↑
(3)钢包精炼渣成分控制
不管采用何种精炼方法(如RH、LF、VD),合理搅拌强度和合理精炼渣组成是获得洁净钢水的基础合适的钢包渣成分:
CaO/ Al2O3=1.5~1.8,CaO/ SiO2=8~13,(FeO+MnO)<5%。
高碱度、低熔点、低氧化铁、富CaO钙铝酸盐的精炼渣,能有效吸收大颗粒夹杂物,降低总氧。
(4)保护浇注
?钢水保护是防止钢水再污染生产洁净钢重要操作。
?保护浇注好坏判断指标:
-Δ[N]=[N]钢包-[N]中包
-Δ[Al]S=[Al]钢包-[Al]中包
?保护方法:
-中包密封充Ar
-钢包→中间包长水口;Δ[N]=1.5ppm甚至为零
-中间包→结晶器浸入式水口
(5)中间包控流装置
●中间包不是简单的过渡容器,而是一个冶金反应容器,作为钢水进入结晶器之前进一步
净化钢水
●中间包促进夹杂物上浮其方法:
1)增加钢水在中间包平均停留时间t:
t=w/(a×b×ρ×v)
中间包向大容量深熔池方向发展。
2)改变钢水在中间包流动路径和方向,促进
夹杂物上浮。
(6)中间包覆盖剂
中间包是钢水去除夹杂物理想场所。钢水面上覆盖剂要有效吸收夹杂物。
●碳化稻壳;
●中性渣:(CaO/SiO2=0.9~1.0);
●碱性渣:(CaO+MgO/SiO2≥3);
●双层渣。
渣中(SiO2)增加,钢水中T[O]增加。生产洁净钢应用碱性复盖剂。
(7)碱性包衬
钢水与中间包长期接触,钢水与包衬的热力学性能必须是稳定的,这是生产洁净钢的一个重要条件。
包衬材质中SiO2增加,铸坯中总氧T[O]是增加,因此生产洁净钢应用碱性包衬。
对低碳Al -K钢,中间包衬用Mg-Ca质涂料(Al2O3→0),包衬反应层中Al2O3可达21%,说明能有效吸
(8)钢种微细夹杂物去除
●大颗粒夹杂(>50μm)去除,采用中间包控流技术;
●小颗粒夹杂(<50μm)去除:
-中间包钙质过滤器
-中间包电磁旋转
(9)防止浇注过程下渣和卷渣
—加入示踪剂追踪铸坯中夹杂物来源;
—结晶器渣中示踪剂变化;
—铸坯中夹杂物来源,初步估算外来夹杂物占41.6%,二次氧化占 39%,脱氧产物为20%
(10)防止Ar气泡吸附夹杂物
对Al-K钢,采用浸入式水口吹Ar防止水口堵塞,但吹Ar会造成水口堵塞物破碎进入铸坯,大颗粒Al2O3轧制延伸会形成表面成条状缺陷
<1mm Ar气泡上浮困难,它是Al2O3和渣粒的聚合地,当气泡尺寸>200μm易在冷轧板表面形成条状缺陷。
为解决水口堵塞问题,可采用:
-钙处理改善钢水可浇性
-钙质水口
-无C质水口
目前还是广泛采用吹Ar来防止堵塞。生产洁净钢总的原则是:钢水进入结晶器之前尽可能排除Al2O3。
3、连铸坯形状缺陷及控制
1)鼓肚变形
带液心的铸坯在运行过程中,于两支撑辊之间,高温坯壳中钢液静压力作用下,发生鼓胀成凸面的现象,称之为鼓肚变形。板坯宽面中心凸起的厚度与边缘厚度之差叫鼓肚量,用以衡量铸坯彭肚变形程度。减少鼓肚应采取措施:
◆降低连铸机的高度
◆二冷区采用小辊距密排列;铸机从上到下
辊距应由密到疏布置;
◆支撑辊要严格对中
◆加大二冷区冷却强度。
◆防止支撑辊的变形,板坯的支撑辊最好选
用多节辊。
2)菱形变形
菱形变形也叫脱方。是大、小方坯的缺陷。是指铸坯的一对角小于90°,另一对角大于90°;两对角线长度之差称为脱方量。
应对菱变的措施:
◆选用合适锥度的结晶器
◆结晶器最好用软水冷却
◆保持结晶器内腔正方形,以使凝固坯壳为
规规正正的形状
◆结晶器以下的600mm距离要严格对弧;并确保二冷区的均匀冷却。
◆控制好钢液成分。
3)圆铸坯变形
圆坯变形成椭圆形或不规则多边形。圆坯直径越大,变成随圆的倾向越严重。形成椭圆变形的原因有: 1)圆形结晶器内腔变形;
2)二冷区冷却不均匀;
3)连铸机下部对弧不准;
4)拉矫辊的夹紧力调整不当,过分压下。
中间包冶金的最新技术
◆ H型中间包
◆离心流中间包
◆中间包吹氩
◆去夹杂的陶瓷过滤器
◆电磁流控制
(一)中间包钢液温度测定
1、中间包钢液温度的点测
用快速测温头及数字显示二次仪测量温度。
2、中间包钢液温度的连续测定
铸机台数和轧机能力的关系、加热炉的配置
直送保温辊道及边角复热器
缓冷保温坑
加热炉的分工
热履历及其影响
相变的影响。A→P+F,P+F→A
第二相析出的影响AlN,Nb(CN),Ti(CN),V(CN)
第五节薄板坏连铸连轧的思路
减小细化铸造组织可以减少压缩比,省略粗轧机组
断面减小可以利用高拉速保证产量
连铸—连轧可以改变热应力,改变成品性能,生产新钢种 缩短工艺流程可以生产更薄产品,以热代冷
第三章:薄板坯连铸连轧工艺
典型的薄板坯连铸连轧工艺流程由炼钢(电炉或转炉)—炉外精炼—薄板坯连铸—连铸坯加热—热连轧等五个单元工序组成。
连铸-连轧可有两种主要形式:
?连铸-热装轧制(CC-HCR)
?连铸-直接轧制(CC-DR)
连铸-连轧技术的优点:
?大幅度的节约能源,能耗降低85%左右
?进一步提高成材率,减少烧损和切损
?提高钢材表面质量
?减少钢坯加热及运输等各项设备,使生产流程简化
薄板坏连铸连轧的思路:
?减小细化铸造组织可以减少压缩比,省略粗轧机组
?断面减小可以利用高拉速保证产量
?连铸—连轧可以改变热应力,改变成品性能,生产新钢种
?缩短工艺流程可以生产更薄产品,以热代冷
典型的薄板坯连铸连轧工艺
? ASP 工艺
? 1 CSP 工艺
? 2 ISP 工艺
? 3 FTSRQ 工艺
? 4 CONROLL 工艺
? 5 QSP 工艺
? 6 TSP 工艺
? 7 CPR 工艺
传统热连轧生产线
采用传统的工艺流程布局,即建设大的板坯库作为连铸工序与连轧工序之间的缓冲区,使用200mm以上厚度的连铸坯,按照传统模式组织生产。代表工程如:鞍钢1780,宝钢2050,武钢2250。
连铸连轧生产线
采用连铸-连轧工艺,简称CC-CR(Continuous Casting-Continuous Rolling)是一种热轧前铸坯无相变的生产工艺,通过铸坯在高温下直接装炉轧制或直接轧制,实现从炼钢、连铸到轧钢有节奏的均衡连续化生产。
ASP
中薄板坯连铸连轧生产(Angang Strip Production 简称ASP),实现CC-CR的工艺目标。采用厚度为100mm 、135mm、150mm、170mm近终断面铸坯;开发多机多流合流直装的铸机、轧机连接专利技术;应用步进式加热炉作为连接缓冲,实现全部直接热装的CC-CR技术。目前世界上采用该工艺的中薄板坯连铸连轧生产线有3条,分别为鞍钢ASP1700,鞍钢ASP2150,济钢ASP1700。
ASP工艺最显著特点就是,连铸连轧生产线为短流程布置,采用介于薄板坯与常规轧机板坯之间的中等厚度板坯,实现中等厚度板坯连铸与常规轧制直接相连的技术集成,它集常规轧制和CSP薄板坯连铸连轧的优点,一方面具有铸坯直轧与直接热装、高效节能的突出特点,同时又具有生产组织灵活,产品覆盖面广的特点。具有短流程、节能低耗、生产组织灵活、产能大、投资少等诸多优点。
1、CSP工艺技术(Compact Strip Production)
CSP工艺也称紧凑式热带生产工艺。CSP生产工艺流程一般为:电炉或转炉炼钢→钢包精炼炉→薄板坯连铸机→剪切机→辊底式隧道加热炉→粗轧机(或没有)→均热炉(或没有)→事故剪→高压水除鳞机→小立辊轧机(或没有)→精轧机→输出辊道和层流冷却→卷取机。
CSP特点
①漏斗式结晶器和偏水口
②二冷区头段的液芯轻压下,由60~70→40~50
③隧道式加热炉
④6~7架精轧机组及控轧控冷的应用
⑤无头或半无头轧制
a.产量高
b.成材率高
c.辊耗低;
d.轧制稳定性高
e.生产以热代冷产品;
CSP的工艺技术特征
?该工艺连铸机采用漏斗型结晶器 ,铸出厚度为 50mm 的连铸坯 , 经加热炉后直接送入精轧机组 , 轧成规定厚度的带卷。CSP 工艺生产稳定 ,运行可靠 ,产品质量好。
?其工艺流程:薄板坯连铸机→均热→剪切机→除鳞机→精轧机组→层流冷却→地下卷取机。
?与传统工艺相比,CSP 生产线的总压缩比和各道次的压下量有较大的不同,从而导致轧制力、摩擦状态和内部组织的显著差异。
ISP工艺技术(Inline Strip Production)
? ISP工艺也称在线热带钢生产工艺。ISP生产线的工艺流程一般为:电炉或转炉炼钢→钢包精炼→连铸机→大压下量初轧机→剪切机→感应加热炉→克日莫那炉→热卷箱→高压水除鳞机→精轧机→输出辊道和层流冷却→卷取机。
ISP特点
①平行板式结晶器及落水口
②液芯铸轧60→40
③三机架大压下40→15
④感应加热器和热卷箱
⑤四机架精轧及控冷
⑥生产线短
连铸连轧
薄板坯连铸连轧之产品质量控制 王庆 (安徽工业大学) 摘要介绍了国外关于薄板坯连铸连轧生产中影响产品质量各种因素的研究成果, 对于一些主要的影响原理进行了简单的探讨,并且介绍了薄板坯来连铸连轧工艺产品的质量优势和工艺优势,使人们对采用薄板坯连铸连轧技术生产质量合格产品主要方面有一定基本了解。 关键词薄板坯连铸连轧质量 薄板坯连铸连轧在国际上是新出现的技术, 这些技术在正常生产中可满足用户需要, 但为达到现代工业对于板带钢质量的苛刻要求, 在生产控制方面要注意一些问题, 本文介绍了国外的一些经验。 1 薄板坯连铸连轧技术工艺流程与产品质量 现在拥有薄板坯连铸连轧技术的外国公司主要有4家, 其典型工艺布置各不相同。工艺布置的不同对质量性能是有影响的。 1.1 西马克的CSP技术 西马克CSP技术设备相对简单, 流程通畅, 易于掌握, 但是由于其采用50mm的板坯, 对薄规格产品道次变形量过大, 轧机负荷大; 对厚规格的产品压缩比过小, 对提高质量不利, 了产品范围的扩大和质量的提高。 1.2 德马克的ISP技术 德国德马克ISP技术连铸75mm板坯, 液芯压下至60m , 2架大压下轧机轧制到20mm, 进感应炉和无芯卷取箱炉均热, 4架精轧机轧制为成品。德马克方案的技术含量较高, 液芯压下大压下轧机、感应加热等都有特色, 但是新技术多带来的问题就是设备复杂,对管理水平和水平要求高。另外, 板坯出连铸机后进大压下轧机前, 板坯温度一般已不均匀, 工艺设计此有一除鳞设备, 但是板坯此时除鳞, 温度下降不利于轧制, 不除鳞则影响表面质量, 在生产一矛盾始终未得到解决。大压下轧机与连铸机连接在一起, 中间无缓冲设备, 而轧机换辊需要停机进行, 势必影响铸机的工作。 1.3奥钢联的CONROLL技术 奥钢联只在美国MANSFIELD的ARMCO利用原有的旧轧机改造了一条使CONROLL铸机的生产线。该生产线浇铸75~125mm的板坯, 奥钢联技术的特点是全部使用成熟技术。近年人们认为,连铸薄板坯从质量与经济性方面考虑, 并非越薄越好, 而是有一个经济厚度, 这一厚度为90~100mm左右。因为这个厚度离传统的板坯厚度较近, 可以借用长期积累的丰富经验与技术; 板坯较厚压缩比大, 从而可提高产品质量; 板坯断面积大可采用较低的拉速, 降低了结晶器磨损, 减少了拉漏几率; 在卷重相同的情况下板坯定尺短, 输送辊道、加热炉长度较短, 节省了投资, 平板结晶器的加工、修复也相对容易, 有色金属消耗低。 1.4 达涅利的FTSR技术 达涅利为加拿大的ALGOMA钢铁公司建设薄板坯连铸连轧线已投产, 该生产线使用达涅利的凸透镜型结晶器, 铸造60~80mm的薄板坯, 出结晶器进行液芯压下到50~70mm然后进入辊底式隧道炉均热, 由一台粗轧机轧制到25~35mm , 再进行均热(辊底式隧道炉) ,最后进入6机架精轧机组。达涅利技术生产的钢种范围较广, 包括包晶钢在内均可生产。在提高质量方面考虑也比较全面, 增加了边部感应加热和粗轧后的二次加热。为得到更好的表面质量, 达涅利的生产线有三次除鳞, 分别在连铸机出口、粗轧机入口和精轧机入口, 这对于提高表面质量无疑是有利的。达涅利设计的除鳞机为旋转的形式, 这对于提高表面质量和减少
连铸连轧法生产铜杆---图
连铸连轧法生产铜杆 一、连铸连轧铜杆生产工艺过程: 电解铜加料机竖炉上流槽保温炉下流槽浇堡 铸造机夹送辊剪切机坯锭预处理设备轧机清洗冷却管道涂蜡成圈机包装机成品运输 二、连铸连轧铜杆生产线 当前世界各国采用的铜杆连续生产线新工艺主要有:意大利的Properzi系统(缩称CCR系统),美国的SouthWire系统(缩称SCR系统)、联邦德国的Krupp/Hazelett系统(缩称Contirod系统)、以及将法国的SECIM系统。这些系统在原理上基本相同,工艺上也大同小异,其差异主要是在铸机和轧机的形式和结构上。 CCR系统沿用铝连铸连轧的双轮铸机和三角轧机形式连铸连轧铜杆。最初铜铸锭截面1300mm2,现在最大可达2300mm2,理论能力18t/h,轧制孔型系“三角——圆”系统。当锭子截面太大时,原轧机前面加两平一立辊机架,采用箱式孔型开坯,箱孔型道次减缩率在40%左右。 SCR系统是在CCR的基础上改进而成的如图2-35,铸机由双轮改为五轮(一大四小),轧机则改为平一立辊式连轧机,孔型改为箱—椭—圆系统。头上两道箱式孔型同样起开坯作用。SCR五轮铸机可铸铜锭截面6845 mm2,理论能力2518t/h。 图2-35 1——提升机及加料台2——熔化炉3——保温炉4——液压剪5——铸锭整形器6——飞剪7——酸洗8——卷取装置9——精轧机组10——粗轧机组11——连铸机 Contirod系统工艺和生产规模基本上和SCR一样,只是铸机改用了“无轮双钢带式”即Hazelett式。 SECIM系统(图2-36),采用四轮式连铸机,(一大三小),最大铸锭截面4050mm2,11机架,孔型前三道为箱—扁—圆系统。生产铜杆φ7~16mm,重量达到5t,生产能力30 t/h。
连铸连轧知识点
连铸连轧部分知识点 1、连铸生产工艺对连铸设备的要求: 1)必须适合高温钢水由液态变成液固态,又变成固态的全过程; 2)必须具有高度的抗高温,抗疲劳强度的性能和足够的强度; 3)必须具有较高的制造和安装精度,易于维修和快速更换,充分冷却和良好的润滑等。 2、连铸流运行轨迹将连铸机分为哪几种?简述每种机型的特点? 1)立式连铸机、立弯式连铸机、弧形连铸机、椭圆形连铸机和水平连铸机。2)A、立式连铸机:此铸机坯壳冷却均匀,且不受弯曲矫直作用,故不宜产生内部和表面裂纹,有利于夹杂物上浮,但其设备高度大,操作不方便,投资费用高,设备维护及事故处理难,铸坯断面和定长及拉速受限,并且铸坯因钢水静压力大,板坯股肚变形较突出。 B、立弯式连铸机:铸机的中间包,结晶器,导辊,引锭杆沿垂线分布。拉矫机切割机沿水平布置,浇注和冷却凝固在垂直方向上完成,完全凝固后被顶弯90°,进入弯曲段,在水平方向出坯,它的铸机高度比立式下降,运输方便,可适合较长定尺的要求,但由于增加了一次弯曲和矫直,一造成裂纹。 C、弧形连铸机:分为单点矫直弧形连铸机,多点矫直弧形连铸机,直结晶器弧形连铸机。a)单点矫直弧形连铸机:优点:高度比立式、立弯式低,故设备重量轻,投资费用低,安装和维修方便,钢水对铸坯的静压力小,可减少因股肚造成的内列和偏析,有利于提高拉速改善铸坯质量。缺点:钢水凝固过程中,非金属夹杂物有向弧内聚焦的倾向,一造成铸坯内部杂物分布不均匀。b)多点矫直弧形连铸机:优点:固液界面变形率降低铸坯带液芯矫直时,不产生内部裂纹,有利于提高拉速。 c)直结晶器弧形连铸机优点:具有立式的优点,有利于大型夹杂物的上浮及钢中夹杂物的平均分布,比立弯式高度更高,建设费用低。缺点:铸坯外弧侧坯壳受拉伸,两相区易造成裂纹缺陷,设备结构复杂,检修,维修难度大。 D、椭圆形连铸机:其优点是高度较弧形大大减小,钢水静压力低,铸坯股肚量小,内部裂纹中心偏析得到改善,投资节约20%----30%(比弧形)。但结晶器内钢水中的夹杂物几乎无上浮机会,故对钢水要求严格。 E、水平连铸机:其优点是设备高度最低,钢水物二次氧化,铸坯质量得到改善,不受弯曲及矫直作用,有利于防止裂纹,设备维护简单,事故处理方便,但中间包和结晶器连接处的分离较贵,结晶器和铸坯间润滑困难,拉坯时结晶器不振动,适合小坯量,多种浇注,200mm以下方坯,圆坯,特殊钢。 3、连铸连轧的定义:由连铸机生产出来的高温无缺陷坯,不需要清理和再加热(但需经过短时均热和保温处理)而直接轧制成材,这样把“铸”“轧”直接连成一条生产线的工艺流程就称为连铸连轧。 4、连铸和连轧紧凑联结的方法:连铸坯热装、直接轧制。连铸坯热装工艺是指连铸机生产的钢坯不经过冷却,在热状态下卷入加热炉加热,然后进行轧制的方法。连铸坯直接轧制工艺是指铸机出来的高温铸坯不再经过加热或只对边棱进行轻度的补充加热就直接送往轧机轧制成材。 5、连铸连轧的优点:1)简化生产工艺流程,生产周期短; 2)占地面积少; 3)固定资产投资少; 4)金属的收得率高; 5)钢材性能好; 6)能耗少; 7)工厂定员大幅降低; 8)劳动条件好,易于实现自动化。 6、提高拉坯速度的限制因素:1)拉坯力的限制; 2)铸坯断面影响; 3)铸坯厚度影响; 4)结晶器导热能力的限制; 5)速度对铸质的影响; 6)钢水过热度的影响;7)钢种的影响。 7、二冷区包括:足辊段、支撑导向段和扇形段。 二冷区冷却方式:1)干式冷却;2)水喷雾冷却;3)水—气喷雾冷却(效果最好)。 8、倒锥度:为了减少气隙,加速钢水的传热和坯壳生长,通常结晶器的下口断面比上口断面小。倒锥度过小会导致坯壳过早脱离铜壁产生气隙,降低冷却效果,或使结晶器的坯壳厚度不够产生拉漏事故;倒锥度过大容易导致坯壳与结晶器铜壁之间的挤压力过大从而加速铜壁的磨损。 9、结晶器满足要求:1)结构简单重量轻;2)良好的导热性和水冷条件; 3)应做上下往复运动并加润滑剂; 4)结晶器有足够的刚度,以免影响铸坯质量。 10、结晶器震动方式:同步式、负滑脱式、正弦振动式 11、结晶器调宽方法:1)停机变宽; 2)平移变宽; 3)转动加平移变宽(最具代表性)。
连铸结晶器液面自动加渣控制系统简介
连铸结晶器液面自动加渣控制系统简介
连铸结晶器液面自动加渣控制系统简介 一、概述 连铸机浇筑时结晶器加保护渣是连铸生产中最重要的工作,保护渣在连铸生产中起着极为重要的作用,如防止二次氧化、润滑及吸附杂质等。连铸工艺要求保护渣在浇铸过程中形成熔融层、烧结层及粉渣层等三层结构,以便更好的发挥作用。少加勤加是添加保护渣的一条重要原则。 二、现场现状 目前连铸机上采用的加渣方式大都还是人工方式,每个工人管理着一流或两流,需时刻观察着结晶口的状态,需要加时就用随便的推上一堆,心情好或领导在时加的还均匀些,领导不在那就看自己的心情了,心情好负责些,心情不好那就随便了。况且连铸机旁的环境比较恶劣,工人的劳动强度很大,要求工人长时间的高质量的完成加渣工作也有难度。因此人工添加保护渣受操作者因素的影响较大,很难保证添加的稳定性,容易产生卷渣和液面波动,从而产生夹杂、振痕加深等缺陷。针对这种情况,我公司最新研发了一套连铸结晶器液面自动加渣控制系统,可以代替工人进行自动加渣而基本无需工人干预。 三、系统简介 我公司新研发的连铸结晶器液面自动加渣控制系统,包括工控机、控制执行单元、现场控制报警单元、加料仓、气动单元、结晶器渣液面温度检测装置、渣料喷头、料位计、专用软件组成。
连铸结晶器液面自动加渣控制系统是一套闭环自动控制系统,它以工控机为核心,通过专用软件来自动控制各个组成部分自动工作,在基本参数设置完成后,由工控机来根据连铸机结晶器内渣液面的实际情况进行参数调整,无需再人工干预调整而能保证结晶器内渣液面的均匀和稳定。 系统的工作过程由工控机实时不停的读取结晶器内渣液面的表面温度,如果渣液面的表面温度超过设定的加料温度,则工控机控制执行单元让加料仓下料,同时打开气动单元,保护渣在下料管内被送料气体经渣料喷头均匀吹送到结晶器内,然后再测结晶器内渣液面的表面温度,如果渣液面的表面温度仍然超过设定的加料温度,则工控机重复上面的加料过程,如果测量到结晶器内渣液面的表面温度低于设定的加料温度则停止加料和关闭气动单元。 在现场设有工人控制箱,可以控制任意一流加料系统的启动和停止。当出现故障时控制箱会发出声光报警,并指示灯提示哪一流出现问题。 系统实现框图如下: 图1系统框图 加 料 下料控制单 渣料 工控 干燥 渣层 料显示 报
薄板坯连铸连轧
薄板坯连铸连轧 薄板坯连铸连轧技术是 20 世纪 80 年代末世界钢铁工业发展的一项重大技术 , 它的开发成功是近终形浇铸技术的重大突破。按类型可分为CSP、ISP、FTSR、和CONROLL技术,但就不同类型的生产线来看,以CSP建设得最多[3]。 CSP(Compact Strip Production)即紧凑式板带生产工艺,是由德国施罗曼.西马克(SMS)公司研究开发的薄板坯连铸连扎技术,世界上第一条CSP生产线,于1989年在美国NUCOR公司的CRAWFORDSVILLE厂建成,投产后,取得满意的生产效果和良好的经济效益,因而得到广泛应用。目前,有38台CSP连铸机在内的24条CSP生产线广泛分布在北美、南美、欧洲、亚洲、非洲等世界各地,生产能力达到3900万吨/年[4,5]。 图1.1为CSP生产线示意图,工艺流程为:电炉(AD或DC)→钢包精炼炉→薄板坯连铸机→均热保温→热连轧机→层流冷却→地下卷取。该工艺设备结构简单,操作稳定,产量高。具有流程短、生产简便且稳定,产品质量好、成本低、有很强的市场竞争力等一系列突出优点。 图1.1 CSP工艺生产线 1-中间包;2-结晶器;3-切断剪;4-均热炉;5-事故剪;6-除鳞机;7-精轧机; 8-1号层流却;9-飞剪;10-生产薄规格的旋转式卷取机;11-2号层流冷却; 12-生产厚规格的常规卷取机 薄板坯连铸连轧工艺流程特点: (1) 整个工艺流程是由炼钢(电炉或转炉) -炉外精炼- 薄板坯连铸- 物流的时间节奏与温度衔接- 热连轧5 个单元工序组成, 将原来的炼钢厂和热轧厂紧凑地压缩, 有机地组合在一起。 (2) 在整个工序流程中, 炼钢炉、薄板坯连铸机和热连轧机都是刚性较强的工艺装置, 为了稳定地连续浇铸和轧制, 需匹配好各段物流。例如, 对于宽度1350~1600 mm的薄板坯, 若平均拉速为415 m/ min , 则转炉容量应在100 t以上。
连铸连轧
1、连铸流运行轨迹将连铸机分为哪几种?简述每种机型的特点? 1)立式连铸机、立弯式连铸机、弧形连铸机、椭圆形连铸机和水平连铸机。 2)A、立式连铸机:优点:铸机坯壳冷却均匀,且不受弯曲矫直作用,故不宜产生内部和表面裂纹,有利于夹杂物上浮;缺点:其设备高度大,操作不方便,投资费用高,设备维护及事故处理难,铸坯断面和定长及拉速受限,并且铸坯因钢水静压力大,板坯股肚变形较突出。 B、椭圆形连铸机:优点:是高度较弧形大大减小,钢水静压力低,铸坯股肚量小,内部裂纹中心偏析得到改善,投资节约20%----30%(比弧形)。缺点:结晶器内钢水中的夹杂物几乎无上浮机会,故对钢水要求严格。 C、水平连铸机:优点:是设备高度最低,钢水物二次氧化,铸坯质量得到改善,不受弯曲及矫直作用,有利于防止裂纹,设备维护简单,事故处理方便;缺点:中间包和结晶器连接处的分离较贵,结晶器和铸坯间润滑困难,拉坯时结晶器不振动,适合小坯量,多种浇注,200mm 以下方坯,圆坯,特殊钢。 D、弧形连铸机:分为单点矫直弧形连铸机,多点矫直弧形连铸机,直结晶器弧形连铸机。a)单点矫直弧形连铸机:优点:高度比立式、立弯式低,故设备重量轻,投资费用低,安装和维修方便,钢水对铸坯的静压力小,可减少因股肚造成的内列和偏析,有利于提高拉速改善铸坯质量。缺点:钢水凝固过程中,非金属夹杂物有向弧内聚焦的倾向,一造成铸坯内部杂物分布不均匀。 b)多点矫直弧形连铸机:优点:固液界面变形率降低铸坯带液芯矫直时,不产生内部裂纹,有利于提高拉速。 c)直结晶器弧形连铸机优点:具有立式的优点,有利于大型夹杂物的上浮及钢中夹杂物的平均分布,比立弯式高度更高,建设费用低。缺点:铸坯外弧侧坯壳受拉伸,两相区易造成裂纹缺陷,设备结构复杂,检修,维修难度大。 2、连铸生产工艺对连铸设备的要求: 1)必须适合高温钢水由液态变成液固态,又变成固态的全过程; 2)必须具有高度的抗高温,抗疲劳强度的性能和足够的强度; 3)必须具有较高的制造和安装精度,易于维修和快速更换,充分冷却和良好的润滑等。 3、连铸连轧的定义:由连铸机生产出来的高温无缺陷坯,不需要清理和再加热(但需进过短时均热和保温处理)而直接轧制成材,这样把“铸”“轧”直接连成一条生产线的工艺流程就称为连铸连轧。 4、连铸和连轧紧凑联结的方法:连铸坯热装、连铸坯直接轧制。 连铸坯热装工艺是指连铸机生产的钢坯不经过冷却,在热状态下卷入加热炉加热,然后进行轧制的方法。 连铸坯直接轧制工艺是指铸机出来的高温铸坯不再经过加热或只对边棱进行轻度的补充加热就直接送往轧机轧制成材。 5、连铸连轧的优点:1)简化生产工艺流程,生产周期短;2)占地面积少; 3)固定资产投资少;4)金属的收得率高;5)钢材性能好;6)能耗少; 7)工厂定员大幅降低;8)劳动条件好,易于实现自动化。 6、提高拉坯速度的限制因素:1)拉坯力的限制;2)铸坯断面影响;3)铸坯厚度影响;4)结晶器导热能力的限制;5)速度对铸质的影响;6)钢水过热度的影响;7)钢种的影响。 7、二次区包括:足辊段、支撑导向段和扇形段。 二冷区冷却方式:1)干式冷却;2)水喷雾冷却;3)水—气喷雾冷却(效果最好)。 二冷区作用:1)带液心的铸坯从结晶器中拉出后,需喷水或喷气水直接冷却,使铸坯快速凝固,以进入拉铸区; 2)对未完成凝固的铸坯起支撑、导向作用,防止铸坯的变形; 3)在上引锭杆时对锭杆起支撑、导向作用; 4)直弧形连铸机,二冷区第一段把直坯弯成弧形坯。 8、结晶器的主要参数:⑴长度;⑵倒锥度(最重要);⑶结晶器断面。 倒锥度:为了减少气隙,加速钢水的传热和坯壳生长,通常结晶器的下口断面比上口断面
连铸连轧
连铸连轧
————————————————————————————————作者: ————————————————————————————————日期:
1、连铸流运行轨迹将连铸机分为哪几种?简述每种机型的特点? 1)立式连铸机、立弯式连铸机、弧形连铸机、椭圆形连铸机和水平连铸机。 2)A、立式连铸机:优点:铸机坯壳冷却均匀,且不受弯曲矫直作用,故不宜产生内部和表面裂纹,有利于夹杂物上浮;缺点:其设备高度大,操作不方便,投资费用高,设备维护及事故处理难,铸坯断面和定长及拉速受限,并且铸坯因钢水静压力大,板坯股肚变形较突出。 B、椭圆形连铸机:优点:是高度较弧形大大减小,钢水静压力低,铸坯股肚量小,内部裂纹中心偏析得到改善,投资节约20%----30%(比弧形)。缺点:结晶器内钢水中的夹杂物几乎无上浮机会,故对钢水要求严格。 C、水平连铸机:优点:是设备高度最低,钢水物二次氧化,铸坯质量得到改善,不受弯曲及矫直作用,有利于防止裂纹,设备维护简单,事故处理方便;缺点:中间包和结晶器连接处的分离较贵,结晶器和铸坯间润滑困难,拉坯时结晶器不振动,适合小坯量,多种浇注,200mm以下方坯,圆坯,特殊钢。 D、弧形连铸机:分为单点矫直弧形连铸机,多点矫直弧形连铸机,直结晶器弧形连铸机。 a)单点矫直弧形连铸机:优点:高度比立式、立弯式低,故设备重量轻,投资费用低,安装和维修方便,钢水对铸坯的静压力小,可减少因股肚造成的内列和偏析,有利于提高拉速改善铸坯质量。缺点:钢水凝固过程中,非金属夹杂物有向弧内聚焦的倾向,一造成铸坯内部杂物分布不均匀。 b)多点矫直弧形连铸机:优点:固液界面变形率降低铸坯带液芯矫直时,不产生内部裂纹,有利于提高拉速。 c)直结晶器弧形连铸机优点:具有立式的优点,有利于大型夹杂物的上浮及钢中夹杂物的平均分布,比立弯式高度更高,建设费用低。缺点:铸坯外弧侧坯壳受拉伸,两相区易造成裂纹缺陷,设备结构复杂,检修,维修难度大。 2、连铸生产工艺对连铸设备的要求: 1)必须适合高温钢水由液态变成液固态,又变成固态的全过程; 2)必须具有高度的抗高温,抗疲劳强度的性能和足够的强度; 3)必须具有较高的制造和安装精度,易于维修和快速更换,充分冷却和良好的润滑等。 3、连铸连轧的定义:由连铸机生产出来的高温无缺陷坯,不需要清理和再加热(但需进过短时均热和保温处理)而直接轧制成材,这样把“铸”“轧”直接连成一条生产线的工艺流程就称为连铸连轧。 4、连铸和连轧紧凑联结的方法:连铸坯热装、连铸坯直接轧制。 连铸坯热装工艺是指连铸机生产的钢坯不经过冷却,在热状态下卷入加热炉加热,然后进行轧制的方法。 连铸坯直接轧制工艺是指铸机出来的高温铸坯不再经过加热或只对边棱进行轻度的补充加热就直接送往轧机轧制成材。 5、连铸连轧的优点:1)简化生产工艺流程,生产周期短; 2)占地面积少; 3)固定资产投资少;4)金属的收得率高; 5)钢材性能好;6)能耗少; 7)工厂定员大幅降低;8)劳动条件好,易于实现自动化。 6、提高拉坯速度的限制因素:1)拉坯力的限制;2)铸坯断面影响; 3)铸坯厚度影响; 4)结晶器导热能力的限制;5)速度对铸质的影响;6)钢水过热度的影响;7)钢种的影响。7、二次区包括:足辊段、支撑导向段和扇形段。 二冷区冷却方式:1)干式冷却;2)水喷雾冷却;3)水—气喷雾冷却(效果最好)。 二冷区作用:1)带液心的铸坯从结晶器中拉出后,需喷水或喷气水直接冷却,使铸坯快速凝固,以进入拉铸区; 2)对未完成凝固的铸坯起支撑、导向作用,防止铸坯的变形; 3)在上引锭杆时对锭杆起支撑、导向作用; 4)直弧形连铸机,二冷区第一段把直坯弯成弧形坯。 8、结晶器的主要参数:⑴长度;⑵倒锥度(最重要);⑶结晶器断面。 倒锥度:为了减少气隙,加速钢水的传热和坯壳生长,通常结晶器的下口断面比上口断面小。倒锥度过小会导致坯壳过早脱离铜壁产生气隙,降低冷却效果,或使结晶器的坯壳厚度不够产生拉漏事故;倒锥度过大容易导致坯壳与结晶器铜壁之间的挤压力过大从而加速
连铸结晶器液面自动加渣控制系统简介样本
连铸结晶器液面自动加渣控制系统简介 一、概述 连铸机浇筑时结晶器加保护渣是连铸生产中最重要的工作, 保护渣在连铸生产中起着极为重要的作用, 如防止二次氧化、润滑及吸附杂质等。连铸工艺要求保护渣在浇铸过程中形成熔融层、烧结层及粉渣层等三层结构, 以便更好的发挥作用。少加勤加是添加保护渣的一条重要原则。 二、现场现状 当前连铸机上采用的加渣方式大都还是人工方式, 每个工人管理着一流或两流, 需时刻观察着结晶口的状态, 需要加时就用随便的推上一堆, 心情好或领导在时加的还均匀些, 领导不在那就看自己的心情了, 心情好负责些, 心情不好那就随便了。况且连铸机旁的环境比较恶劣, 工人的劳动强度很大, 要求工人长时间的高质量的完成加渣工作也有难度。因此人工添加保护渣受操作者因素的影响较大, 很难保证添加的稳定性, 容易产生卷渣和液面波动, 从而产生夹杂、振痕加深等缺陷。针对这种情况, 我公司最新研发了一套连铸结晶器液面自动加渣控制系统, 能够代替工人进行自动加渣而基本无需工人干预。 三、系统简介 我公司新研发的连铸结晶器液面自动加渣控制系统, 包括工控机、控制执行单元、现场控制报警单元、加料仓、气动单元、结晶器渣液面温度检测装置、渣料喷头、料位计、专用软件组
成。 连铸结晶器液面自动加渣控制系统是一套闭环自动控制系统, 它以工控机为核心, 经过专用软件来自动控制各个组成部分自动工作, 在基本参数设置完成后, 由工控机来根据连铸机结晶器内渣液面的实际情况进行参数调整, 无需再人工干预调整而能保证结晶器内渣液面的均匀和稳定。 系统的工作过程由工控机实时不停的读取结晶器内渣液面的表面温度, 如果渣液面的表面温度超过设定的加料温度, 则工控机控制执行单元让加料仓下料, 同时打开气动单元, 保护渣在下料管内被送料气体经渣料喷头均匀吹送到结晶器内, 然后再测结晶器内渣液面的表面温度, 如果渣液面的表面温度依然超过设定的加料温度, 则工控机重复上面的加料过程, 如果测量到结晶器内渣液面的表面温度低于设定的加料温度则停止加料和关闭气动单元。 在现场设有工人控制箱, 能够控制任意一流加料系统的启动和停止。当出现故障时控制箱会发出声光报警, 并指示灯提示哪一流出现问题。 系统实现框图如下:
薄板坯连铸连轧
薄板坯连铸连轧是生产热轧板卷的一项结构紧凑的短流程工艺,是继氧气转炉炼钢及连续铸钢之后,又一重大的钢铁产业的技术革命。薄板坯连铸连轧是将传统的炼钢厂和热轧厂紧凑地压缩并流畅地结合在一起。随着在大产业生产中的不断完善、不断发展,该工艺的节能和高效的特点突现出来,充分显示出该工艺的先进性、公道性和科学性,也给企业带来了巨大的经济效益。 薄板坯连铸连轧技术因众多的单位参与研究开发,已形成了各具特色的薄板坯连铸连轧生产工艺,如CSP、ISP、FTSR、CONROLL、TSP、QSP等。其中推广应用最多的是CSP工艺。各种薄板坯连铸连轧技术各具特色,同时又相互影响、相互渗透,并在不断地发展和完善。 一、三种薄板坯连铸连轧技术的各自现状: 1.1 CSP CSP是由德国西马克公司开发的世界上最早投入工业化生产的薄板坯连铸连轧技术,自1989年在纽柯公司建成第一条生产线以来,随着技术的不断改进,该生产线不断发展完善,现已进入成熟阶段。 CSP技术的主要特点是:(1)采用立弯式铸机,漏斗型直结晶器,刚性引锭杆,浸入式水口,连铸用保护渣,电磁制动闸,液芯压下技术,结晶器液压振动,衔接段采用辊底式均热炉,高压水除鳞,第一架前加立辊轧机,轧辊轴向移动,轧辊热凸度控制,板形和平整度控制,平移二辊轧机等。(2)可生产0.8mm或更薄的碳钢、超低碳钢。(3)生产钢种包括:低碳钢、高碳钢、高强度钢、高合金钢及超低碳钢。 1.2 ISP ISP是由德马克公司最早开发的,1992年1月在意大利阿尔维迪公司克雷莫纳厂建成投产,设计能力为50万吨/a。它是目前最短的薄板坯连铸连轧生产线,主要技术特点是:(1)采用直弧型铸机,小漏斗型结晶器,薄片状浸入式水口,连铸用保护渣,液芯压下和固相铸轧技术,感应加热后接克雷莫纳炉(也可用辊底式炉),电磁制动闸,大压下量初轧机+带卷开卷+精轧机,轧辊轴向移动,轧辊热凸度控制,板形和平整度控制,平移式二辊轧机。(2)生产线布置紧凑,不使用长的均热炉,总长度180m左右。从钢水至成卷仅需30min,充分显示其高效性。(3)二次冷却采用气雾或空冷,有助于生产较薄断面且表面质量要求高的产品。(4)整个工艺流程热量损失较小,能耗少。(5)可生产1.0mm或更薄的产品。1.3 FTSR FTSR是由意大利达涅利公司开发出的一种薄板坯连铸连轧工艺,有的也称FTSC。该技术具有相当的灵活性,能浇铸范围较宽的钢种。可提供表面和内部质量、力学性能、化学成分均匀的汽车工业用板。主要技术特点是:(1)采用直弧型铸机, H2结晶器,结晶器液压振动,三点除鳞,浸入式水口,连铸用保护渣,动态软压下(分多段,每段可单独),熔池自动控制,独立的冷却系统,辊底式均热炉,全液压宽度自动控制轧机,精轧机全液压的AGC,机架间强力控制系统,热凸度控
各种连铸连轧生产线的比较
各种连铸连轧生产线的比较 一、基本概述 裸电线是电线电缆不可缺少的部分,除了光缆以外,几乎所有的电线电缆都需要导体、需要裸线,而且相当数量的一部分产品就以裸电线的形式出现,例如钢芯铝绞线。粗略概算,包括导体部分在内的裸电线的总产值,约占电线电缆总产值的三分之一,它有着举足轻重的作用。 裸电线、电线电缆导体,其材料主要是铜、铜合金、铝、铝合金,以及其它有色和稀有金属材料。 在工农业总的用铜量中,电线电缆行业用铜量占有很高的比重。九十年代初期,全国电线电缆行业的用铜量约近30万吨,而今年估计用铜量为80余万吨,约增加近二倍的用铜量,价格却从最高每吨3万元至现在每吨1.5万元,下跌约50%,因此一些在缺铜时采用铝作代用品的电线电缆产品又恢复采用铜,如布电线、电车线等,使铜的用量日增。铜作为电线电缆最主要的导电材料,又逐步向不同的用途延伸,如用作电车线的高强度、高耐磨的铜合金线应运而生;使用高纯度、高精度的铜线为通信电缆等提供优质导电材料;特细铜线、超细铜线更为新型的电子仪器设备、通信设备、办公自动化设备等提供更为优良的产品,用铜量的增加便是理所当然的。 每年几十万吨铜需要加工,从电解铜板、加工成杆、线或异型材,需要约万台套以上的杆材、线材和异型材的生产设备,这是十分庞大的设备群体。 铜杆生产中最主要四种方法的设备,我国都应有尽有。拥有2台套浸涂法设备和至少700余台套的上引法机组用于生产无氧铜杆,保守估计,设备年生产能力在180万吨至200万吨;从德国、美国、意大利引进的铜铸轧机组超过10
台套,加上国产的连铸连轧机组,光亮铜杆的生产能力至少为50万吨至60万吨;至于原有常用的横列式轧机轧制黑铜杆,加上用水平连铸法制作型材的坯料,其年生产能力不低于30万吨至50万吨。也就是说,我国拥有的生产设备中,无氧、低氧铜杆的年生产能力在220万吨至250万吨左右。加上黑铜杆生产能力,将超过300万吨。由于乡镇企业的大量出现,一些简易的生产铜杆的方法,也就无法在此估计之中。80万吨的需要量和250万吨无氧、低氧铜装机能力之间,存在着很大的距离,因此相当大的部分设备就不得不处于减产或停产状态,以700 余台套上引法机组为例,估计约1/3至1/4的机组由于各种原因而处于停产状态,而1/2的机组的产量尚未达到原设计的生产能力,但即使如此,由上引法机组生产的铜材,仍占有我国铜杆用量的半璧江山,起着重要的作用。 我国铜线拉线机约在万台左右,至少有一半是由电工机械厂制造的,少量由国外引进,这二部分设备的性能都较优,特别至九十年代中后期,国产大、中、小拉采用连续退火的水平,已与国外设备逐步靠近,差距大大缩小了。然而在乡镇企业中仍有土拉线机,这些机器能耗高、劳动强度高、效率低、粗糙,难以加工质优的产品,这部分设备数量估计约为总数的一半,需要给予彻底改造或弃之不用。 裸电线中大量采用铝,例如:铝绞线及钢芯铝绞线。九十年代初期,用铝量每年尚不超过20万吨,以后随着经济的增长逐年增加,由于以前国家在电力系统的政策上是重发电轻送电,使送电的增长赶不上发电的增长速度。近年来开始的城市电网和农村电网改造,使送电的增长速度急剧加快,兼之九十年代开始建设的大型电站,像二滩电站、黄河小浪底电站和长江三峡电站,将相继逐步建成,送电便成为电站建设以后的重中之重,送电工程建设步入本世纪以来最辉煌、
连铸自动化
攀钢1#板坯连铸机的自动化系统改造实践 2009-4-29 9:13:00 来源:中国自动化网浏览:50 网友评论条点击查看 一、引言 攀钢1#板坯连铸机于1993年10月18日一次热负荷试车成功。1996年实现高效化改造,2003年年产板坯210万吨,大大超过原设计100万吨的能力。原自动化控制系统采用贝利-N90集散控制系统,原过程计算机系统采用的是TJ2236小型计算机,控制系统的设备已淘汰,有的元件也日趋老化,系统故障增多,控制系统备件已无法准备。因此,对现有的基础自动化控制系统和过程计算机控制系统进行了改造。 二、自动化控制系统的构建 攀钢1#板坯连铸机自动化系统改造拟采用两级控制系统,即由基础自动化系统(L1)及过程控制计算机系统(L2)组成。基础自动化网络系统采用光纤环形以太网,过程计算系统的网络采用星型连接,两条以太网独立配置,以解决网络数据的畅通。自动化系统配置如图1所示。 1. 基础自动化系统构成 基础自动化(L1)级配置11套西门子S7-400PLC系统,其中新增7套PLC(包括1套平台控制的公共PLC,2套流道控制的流PLC,2套冷却控制的冷却PLC,1套出坯控制的出坯PLC),且大量采用分布式远程I/O站,各分布式I/O站与控制器间以现场总线连接;利旧4套(包括2套
拉矫机控制PLC和2套框架控制PLC)。HMI系统配置两台服务器,互为热备方式。设置5个操作员站、1个工程师站。 ⑴公共PLC系统的配置 公共PLC配备了主站、2路PROFIBUS-DP网络以及4个远程I/O站。其中,一路DP网络连接浇铸平台大包操作的1个远程I/O站,另一路DP网络连接电气室和公共水系统的3个远程I/O 站。 ⑵流PLC系统的配置 流PLC配备了主站、2路PROFIBUS-DP网络以、11个远程I/O站以及PROFIBUS-DP网络中继器2台。其中,一路DP网络连接浇铸平台上的1个远程I/O站,另一路DP网络连接切割PLC 室、电气室、切割室、现场液压阀台、现场操作箱的10个远程I/O站。由于第2路PROFIBUS-DP 网络线路较长,在线路中配置了PROFIBUS-DP网络中继器,对信号进行放大。 ⑶冷却PLC系统的配置 冷却PLC配备了主站、2路PROFIBUS-DP网络以及5个远程I/O站。其中,一路DP网络连接结晶器水的1个远程I/O站,另一路DP网络连接二冷水、二冷气控制的4个远程I/O站。 ⑷出坯PLC系统的配置 出坯PLC配备了主站、1路PROFIBUS-DP网络以及6个远程I/O站。其中,电气室3个远程I/O站、切割室2个远程I/O站、出坯室1个远程I/O站。 ⑸网络系统的配置 L1网络是自动化系统的关键环节,采用了光纤环形以太网。网络系统连接11套PLC系统、2台L1监控服务器、2台L2服务器、5个L1操作员站以及1个L1工程师站。 ⑹操作监控系统的配置 操作监控系统配置2台L1监控服务器以及5个L1操作员站,两台服务器,互为热备方式。 2. 过程计算机系统L2的构成 过程控制计算机系统在结构上采用三层应用结构,第一层为前端客户表现层,即系统的HMI,主要完成L2系统与用户的人机界面交互,第二层为中间应用服务层,主要完成应用系统的业务逻辑处理;第三层为后台数据库层,完成生产数据的历史存储。L2级系统在L1级系统的支撑下,对连铸生产过程进行优化控制、管理。 ⑴L2服务器系统 L2服务器系统包括1台数据库服务器和1台用服务器。由1台PC服务器担当数据库服务器,由1台PC服务器担当应用服务器。在服务器中配置Windows 2003 Server操作系统和Oracle 数据库管理系统。服务器位于计算机机房。服务器通过高速以太网与各PC客户机相连接,实现数据共享,提高了系统的灵活性和可靠性。网络拓扑结构为星型,采用100Mbps快速以太交换网技术构建系统网络,通讯协议采用TCP/IP。 ⑵技术工作站 配置技术工作站TWS(Technology Work Station)1台。位于计算机室,与二级应用服务器交换数据,主要用于模型开发及模型仿真程序,可选择配置较好的专用工作站。 ⑶工艺师工作站
连铸连轧杆工艺技术操作规程
山东平阴铝厂企业标准 QJ/PL03.4-2001 连铸连轧杆工艺技术 操作规程 2001—10—01发布2001—11—01实施 山东平阴铝厂
说明: 1.本规程由山东平阴铝厂科技处提出,由科技处组织起草. 2. 编制:邹永华、叶俊 审核:黄建芳 批准:谷吉存 参加讨论人员::黄建芳、沈其民、杨飞侠、王显锋、边红、 邹永华、赵凯
目录 一生产工艺流程图 (1) 二熔炼工艺技术操作规程 (1) 三浇铸工艺技术操作规程 (3) 四轧制工艺技术操作规程 (4) 五收杆工艺技术操作规程 (5) 六清炉工艺技术操作规程 (6) 七烘炉工艺制度 (6) 八检查、包装 (6) 附:连铸连轧杆生产工艺卡片
一、生产工艺流程图 铝杆 二熔炼工艺技术操作规程 1 新保温炉的使用 ①保温炉投入使用前,按烘炉工艺制度进行烘炉,待炉膛温度升到800℃以上时进行洗炉。 ②洗炉应用A199.70以上品位铝水,灌铝水占炉子容积的1/2,用大耙伸进熔体中充分搅拌,然后将铝水放出,如此再清洗一次。
按连铸连轧杆生产工艺技术要求进行配料。 3 装炉 ①一般固体炉料要在灌炉前加入。若为调整铝液温度或化学成份,需要加入固体炉料。固体炉料在加入之前,要在炉门预热,待干燥后再用大耙或钎子推入炉内。禁止向炉内扔甩固体炉料以免铝水溅到电热体上或者溅出伤人。 ②灌炉前要扒干净敞口包表面的浮渣,小心倒入炉内,要倒干净敞口包内的铝水。 ③装炉前要停电,加完炉料后,根据情况确定是否送电与关闭炉门。 ④将装入的铝水、固体炉料重量记入连铸连轧杆生产工艺卡片。 4 取样 ①取样温度720~740℃,当铝水温度高出这个温度时,要通过添加固体炉料来调整铝水温度,取样前铝水温度夏天720~730℃,冬天730~740℃。 ②取样部位:熔体中间部位。 ③取样前,必须充分搅拌,搅拌时间不少于5分钟。搅拌时,作到铝液“起波不起浪”。 ④搅拌后,立即取样进行分析,鉴定化学成分是否符合要求,取样前,取样勺要预热。 ⑤当成分不符合要求时,应采用加中间合金或稀释的方法重新配料,再进行二次取样分析。 ⑥将加入的中间合金的重量计入连铸连轧杆生产工艺卡片。 5 精炼 ①精炼之前温度720~740℃。 ②精炼所用保温砖必须预热,并且在四氯化碳中浸泡30分钟以上。 ③精炼器装入保温砖之前,先在炉门口予热。 ④精炼时,精炼器应在整个熔池内缓慢移动,沿整个熔池均匀精炼,时间不少于15分钟。 ⑤精炼剂用量0.5千克/吨铝。 ⑥将精剂量的用量计入卡片。
连铸连轧
第一章 模铸与连铸的比较 ?模铸:钢水→整模→浇铸→脱模→均热→初轧→成品轧制 ?连铸:钢水→连铸→成品轧制 ?液态铸轧:钢水→铸轧成品 模铸铸锭的凝固 ?将炼成的钢水浇注到铸铁或砂型制成的钢锭模内,凝固后形成的锭子称为钢锭。钢锭经轧制或锻压成为钢 材后方能使用,所以钢锭是半成品。 ?根据浇注方法的分为上注钢锭和下注钢锭。下注锭的表面质量优于上注锭。 ?根据脱氧程度的不同又有沸腾钢钢锭、半镇静钢钢锭和镇静钢钢锭三种。沸腾钢是脱氧不完全的钢,镇静 钢是脱氧完全的钢,半镇静钢的脱氧程度介于前两者之间,接近于镇静钢。 钢锭的应用现状 ?模铸锭与连铸坯相比,所占比例逐年减少,最终将减少到约占10%,其中合金钢和不锈钢将减少到20%, 工具钢和特殊钢将减少到40%。这是由于连铸坯可以多炉连浇、收得率高、不需初轧或开坯、能耗低,质量甚至优于模铸锭。 ?但模铸镇静钢不可能完全被淘汰,因为锻造用钢、一些小批量生产的高级合金钢及VAR(真空电弧重熔)和 ESR(电渣精炼)用的坯料仍需用模铸镇静钢来生产。 钢锭的质量 ?钢锭的质量有表面质量和内部质量之分。 ?表面质量:结疤、裂纹、表皮的纯净度和致密度。 ?内部质量:钢锭内部的纯净度、致密度、低倍非金属夹杂物数量和宏观偏析的程度。 ?沸腾钢的表面质量好,但由于锭心偏析大,内部质量不如镇静钢。 连铸:使金属液由中间包经浸入式水口不断地通过水冷结晶器,凝成硬壳后从结晶器下方出口连续拉出,经喷水冷却,全部凝固后切成坯料的一种铸造工艺。 连铸的设备以弧形连铸机为例,主要有钢包支承装置、盛钢桶(钢包)、中间罐、结晶器(一次冷却装置)、结晶器振动装置、铸坯导向和二次冷却装置、引锭杆、拉坯矫直装置(拉矫机)、切割设备和铸坯运出装置(见辊道和横向移送设备)等 连铸的优点 变间断生产为连续生产,产量↑(连铸比,连浇炉数) 冷却强度大,铸造组织比较细密,偏析小 切头切尾率少,成才过程烧损和切损少,成材率提高8~12% 工艺过程缩短,生产周期短,能耗、运输成本降低,能耗降低30~60%(视是否热装、热送、直接轧制而定) 环保条件好,无整、脱模时的污染 便于自动化,提高技术水平 连铸的好处在于节能和提高金属收得率。 连铸的发展史 1、现代炼钢技术的发展(连铸技术的作用) (1) 1947年-1974年: 技术特点:转炉、高炉的大型化;以模铸-初轧为核心,生产外延扩大。 (2) 1974年-1989年: 技术特点:全连铸工艺,以连铸机为核心。 (3) 1989年-现在:
薄板坯连铸连轧技术
薄板坯连铸连轧技术 薄板坯连铸连轧是20世纪80年代末开发成功的新技术。自1989年美国纽柯克拉兹维莱钢厂世界第一套薄板坯连铸连轧CSP生产线投产以来,该项技术发展很快,至今已建成和在建的薄板坯连铸连轧生产线(含中厚板坯连铸连轧)已近30条,生产能力达4000万吨以上,占热轧带钢总产量的11%。薄板坯连铸连轧技术除SMS开发的CSP外还有DEMAG的QSP、DANIELI的FTSR和V AI的CONROL 等5种类型。 实践证明,它们具有三高(装备水平高、自动化水平高、劳动生产效率高)、三少(流程短工序少、布置紧凑占地少、环保好污染少)和三低(能耗低、投资低、成本低)等优点。和传统工艺相比,薄板坯连铸连轧工艺还具有如下特点: ⑴由于板坯厚度较薄,它在结晶器内冷却强度大,柱状晶短,铸态组织晶粒细化。 ⑵直接轧制,取消了α—δ相变温度区的中间冷却,热轧变形在粗大奥氏体组织上直接进行,避免合金元素在板坯冷却过程中析出,而使成品组织得到弥散硬化和获得更精细、更均匀的金相组织。 ⑶均热工艺、辊底炉式均热炉保证了板坯在轧制过程中头尾温度的均匀和稳定,而使带钢全长的力学性能和厚度公差均匀一致。 ⑷强力高压水除鳞,保证带钢的表面质量。 ⑸高精度动态液压压下厚度自动控制(HAGC)、板形和平直度自动控制(PCFC)、精确的宽度和温度自动控制使带钢的几何尺寸
精度达到最高水平。 ⑹较高的轧制温度、进精轧机的开轧温度一般控制在1100~1150℃,比常规轧机进精轧高100~150℃。因此,即使精轧机架数少,也能更易轧制超薄热轧带钢。 ⑺由于薄板坯连铸连轧机生产线的小时产量主要取决于连铸机的拉速和板坯宽度,因此轧制薄规格带钢不会像传统轧机那样受到很大影响。 薄板坯连铸连轧机的上述特点使其在产品质量和薄规格轧制上具有较大优势。
铝杆连铸连轧机简单说明
UL+Z-1800/10+255/12型铝杆连铸连轧生产线机械说明一、机组用途及组成 本设备采用连铸连轧法工艺生产电工铝杆,生产的杆径为¢10mm。原材料为普铝锭或废铝线。 本生产线由溶化炉(竖炉)、五轮式整体连铸机、油剪机、喂料装置、连轧机、润滑系统、冷却系统、滑动无油收杆装置等组成。 (其中炉子为外购配套或用户自备) 二、技术规范 (一)主要技术参数 导电铝杆直径:¢10mm 生产能力: 2.5-4.8t/h 设备总尺寸:36.05×7.2×4.2m 设备总重量:55t (二)各组成部分技术参数: 1、五轮式连铸机(四面冷却) 1)、结晶轮直径¢1800mm 2)、结晶轮截面积 1800mm2 3)、铸锭面积 1800mm2 4)、浇铸速度 8-15m/min(电动机转速 500-1000rpm) 5)、结晶轮转速 1.66-3.3r/min 6)、电动机型号 Z4-112/4-2 5.5K 1000r/min 7)、冷却水压 0.35-0.6Mpa 8)、冷却水量 100t/h (内冷 40t/h;外冷 40t/h;侧冷 20t/h) 9)、浇堡升降电机 Y901-2 1.1KW 2840r/min 10)、钢带压紧气缸 10A-2CDD125B100-Y 11)、钢带张紧气缸 10A-2CDD250B100-Y 2、油剪 3、连轧机 1)、形式 2+10(2架两辊;10架三辊Y型) 2)、出杆直径¢10 3)、机架数 12架 4)、轧辊名义尺寸¢255mm 5)、相邻机架传动比 1:1.25 6)、终轧速度 V=7.2m/s 7)、产量 2.5-4.8t/h 8)、轧制中心高 900mm 9)、主电机型号功率 Z4-315-22 225kw 680r/min 10)、齿轮箱润滑油箱 3m3 11)、乳化液 65m3 4、喂料装置
连铸连轧综述
薄板坯连铸连轧综述 1.前言 连铸连轧技术作为钢铁生产工业近年来最重要的技术进步之一,具有节约能源、流程短、设备少、成材率高、生产成本低、产品质量好、品种开发潜力大等突出优点[1~5]。而在薄板坯在生产过程中应用该技术时获得的组织晶粒细小、二次枝晶间距小、偏析程度低,应用该技术进行生产优势更加明显[6]。因此,全世界各大钢铁生产企业纷纷引进投建薄板坯连铸连轧生产线。近些年来,随着薄板坯连铸连轧技术日益成熟和广泛,使人们认识到原来的薄板坯连铸连轧技术仍有许多不足之处,开始进行技术的再开发和提高,使技术更臻于成熟和完善。2.薄板坯连铸连轧技术简介 2.1连铸连轧技术 连铸连轧全称连续铸造连续轧制,是将液态金属连续通过水冷结晶器凝固后直接进入轧机进行塑性变形的工艺方法。传统生产工艺是用熔炼炉将炼好的钢液铸成铸锭,经过保温、锻造制成锻坯,之后再通过均热炉加热到高温并保温一段时间后才进行热轧。这一过程需要多次加热保温,既浪费了能源,也使生产周期过长。而连铸连轧技术则是把熔炼好的液态钢倒入连铸机中轧制出钢坯(称为连铸坯),然后不经冷却,在均热炉中保温一定时间后直接进入热连轧机组中轧制成型的钢铁轧制工艺。这种工艺巧妙地把铸造和轧制两种工艺结合起来,相比于传统的先铸造出钢坯后经加热炉加热再进行轧制的工艺具有简化工艺、改善劳动条件、增加金属收得率、节约能源、提高连铸坯质量、便于实现机械化和自动化的优点[1~5]。 2.2薄板坯连铸连轧 连铸坯在轧制之前依据板坯厚度可以分为厚板坯连铸、中厚板坯连铸和薄板坯连铸。随着连铸坯厚度的减小,板坯中部的冷却速度增大。冷却速度增大之后,铸坯中部的晶粒变得细小、缺陷减少、偏析减轻、二次枝晶的间距也随之减小。