催化反应动力学报告
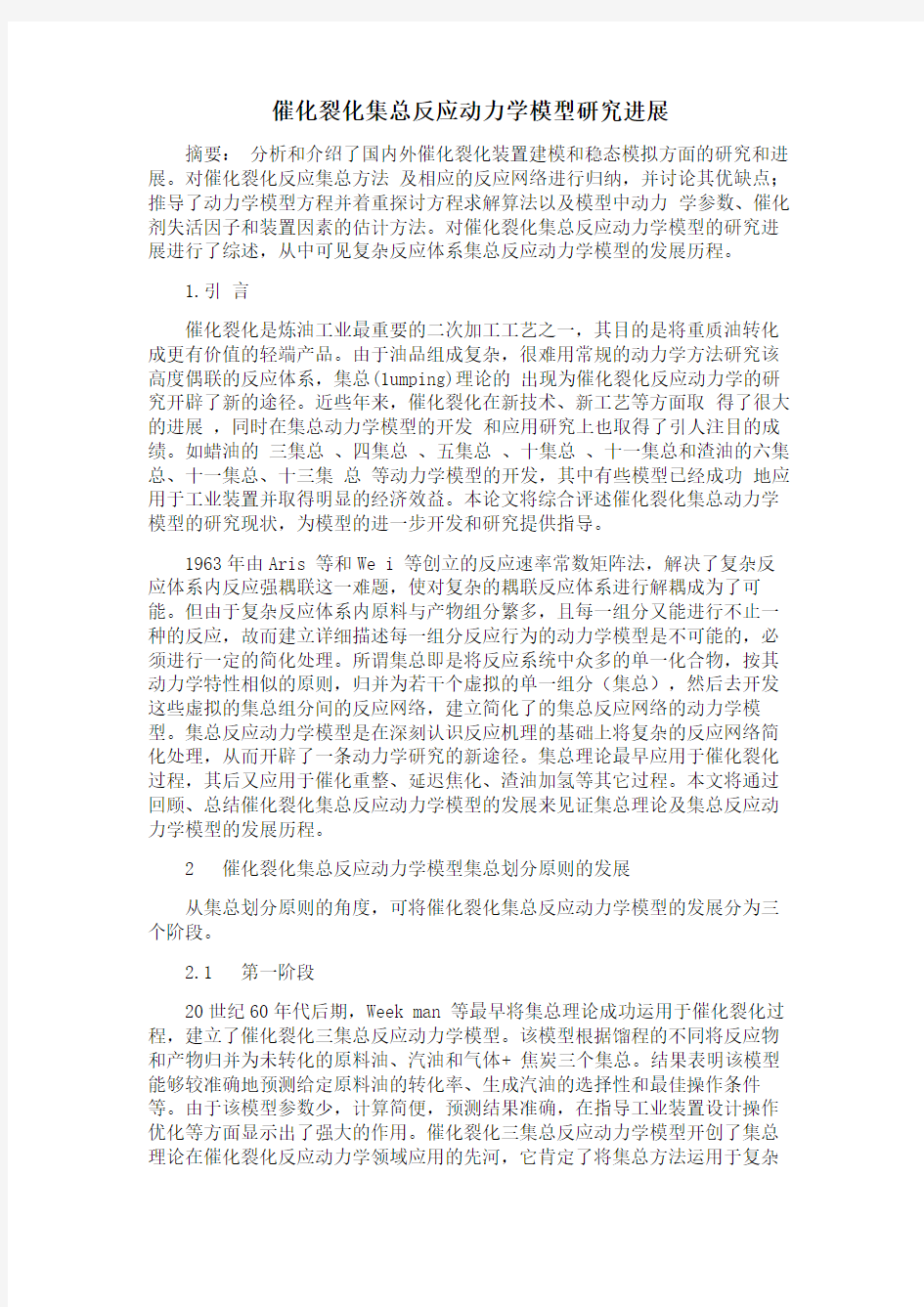

催化裂化集总反应动力学模型研究进展
摘要:分析和介绍了国内外催化裂化装置建模和稳态模拟方面的研究和进展。对催化裂化反应集总方法及相应的反应网络进行归纳,并讨论其优缺点;推导了动力学模型方程并着重探讨方程求解算法以及模型中动力学参数、催化剂失活因子和装置因素的估计方法。对催化裂化集总反应动力学模型的研究进展进行了综述,从中可见复杂反应体系集总反应动力学模型的发展历程。
1.引言
催化裂化是炼油工业最重要的二次加工工艺之一,其目的是将重质油转化成更有价值的轻端产品。由于油品组成复杂,很难用常规的动力学方法研究该高度偶联的反应体系,集总(1umping)理论的出现为催化裂化反应动力学的研究开辟了新的途径。近些年来,催化裂化在新技术、新工艺等方面取得了很大的进展,同时在集总动力学模型的开发和应用研究上也取得了引人注目的成绩。如蜡油的三集总、四集总、五集总、十集总、十一集总和渣油的六集总、十一集总、十三集总等动力学模型的开发,其中有些模型已经成功地应用于工业装置并取得明显的经济效益。本论文将综合评述催化裂化集总动力学模型的研究现状,为模型的进一步开发和研究提供指导。
1963年由Aris 等和We i 等创立的反应速率常数矩阵法,解决了复杂反应体系内反应强耦联这一难题,使对复杂的耦联反应体系进行解耦成为了可能。但由于复杂反应体系内原料与产物组分繁多,且每一组分又能进行不止一种的反应,故而建立详细描述每一组分反应行为的动力学模型是不可能的,必须进行一定的简化处理。所谓集总即是将反应系统中众多的单一化合物,按其动力学特性相似的原则,归并为若干个虚拟的单一组分(集总),然后去开发这些虚拟的集总组分间的反应网络,建立简化了的集总反应网络的动力学模型。集总反应动力学模型是在深刻认识反应机理的基础上将复杂的反应网络简化处理,从而开辟了一条动力学研究的新途径。集总理论最早应用于催化裂化过程,其后又应用于催化重整、延迟焦化、渣油加氢等其它过程。本文将通过回顾、总结催化裂化集总反应动力学模型的发展来见证集总理论及集总反应动力学模型的发展历程。
2 催化裂化集总反应动力学模型集总划分原则的发展
从集总划分原则的角度,可将催化裂化集总反应动力学模型的发展分为三个阶段。
2.1 第一阶段
20世纪60年代后期,Week man 等最早将集总理论成功运用于催化裂化过程,建立了催化裂化三集总反应动力学模型。该模型根据馏程的不同将反应物和产物归并为未转化的原料油、汽油和气体+ 焦炭三个集总。结果表明该模型能够较准确地预测给定原料油的转化率、生成汽油的选择性和最佳操作条件等。由于该模型参数少,计算简便,预测结果准确,在指导工业装置设计操作优化等方面显示出了强大的作用。催化裂化三集总反应动力学模型开创了集总理论在催化裂化反应动力学领域应用的先河,它肯定了将集总方法运用于复杂
反应体系反应动力学研究的可行性,为后来的催化裂化集总反应动力学模型研究开发奠定了坚实的基础。尽管在工业应用中该模型也暴露出了它的局限性,即由于模型将进料全部归并为一个集总,因此当进料组成发生变化时,模型就不能适应装置进料组成的变化,而该局限性恰恰为催化裂化集总反应动力学模型以后的发展指出了方向:即要适应原料组成的变化,须要将原料进一步细分。
之后各国研究者提出的四集总、五集总都是遵循了三集总反应动力学模型按馏程划分集总的思想,他们将产物中气体+ 焦炭分开集总以便分别预测气体和焦炭的产率。Hagelberg等将五集总中汽油集总划分为烷烃、烯烃、环烷烃和芳烃,建立了八集总。Takatsuka等为使催化裂化集总动力学模型能适用于渣油原料,建立了渣油催化裂化六集总反应动力学模型,即按馏程将原料油分割为减压渣油(>538 ℃)和蜡油(343~538 ℃)两个集总;而将产物划分为4 个集总:柴油(221~343 ℃)、汽油(C 5 约221 ℃)、裂化气(≤
C4)和焦炭。上述这些模型将产物分别集总,可预测较为细致的产品信息,但在原料集总划分上与三集总模型基本相同,可认为是三集总模型的延续,并没有弥补模型不能适应原料组成变化这一不足。
2.2 第二阶段
20 世纪 70 年代,Week man 等在催化裂化三集总动力学模型的基础上,针对催化裂化三集总动力学模型的缺点,采用馏程- 烃族- 结构族组成划分集总组分的方法,对原料油集总进行了细化,开发了催化裂化十集总反应动力学模型。该模型首先按馏程将原料油和产物分成重燃料油(HFO )、轻燃料油(LFO )、汽油(G)和焦炭+ 气体(C)4 部分,然后再按烃族和结构族组成将 HFO 和LFO 分别划分为烷烃(P)、环烷烃(N)、芳环上的碳原子(C)和芳环上的取代基(A)4 个集总。实践证明,该模型可在较宽的反应条件范围内,既对各种组成的催化裂化进料成功预测其原料油转化率、汽油选择性、轻燃料油产率、轻质产品分布,还考虑了碱氮中毒、重芳烃吸附等对催化剂活性的影响,使模型预测更为准确。催化裂化十集总反应动力学模型根据馏分的烃族和结构族组成不同将轻、重燃料油进一步细分为八个集总,尤其是将芳烃中的芳环与芳环上的取代基团分别集总的创举,使催化裂化十集总反应动力学模型从根本上解决了模型受原料组成变化限制的问题而得到了广泛的应用,并表现出良好的外推性,也使催化裂化集总动力学模型的发展上了一个新的台阶。
Araujo-Monroy等则更为细致地建立了 15集总:首先按馏程将反应物产物划分为柴油、轻循环油(LCO )、汽油、LPG 、干气、焦炭,然后根据烃族-结构族组成将每个集总再细分为烷烃(P)、烯烃(O)、环烷烃(N)、芳烃(A)。具体为柴油(P、N、A)、LCO (P、O、N、A)、汽油(P、O、N、A)、LPG (P、O)。
我国的催化裂化集总反应动力学研究始于20世纪80 年代,虽然起步较晚,但基于催化裂化在我国炼油工业的重要地位,催化裂化反应动力学的研究也受到广泛重视,并很快出现了适合我国催化裂化工艺特点的集总反应动力学模型。如翁惠新等开发的催化裂化十一集总反应动力学模型就是一个典型代表。该模型在国外催化裂化十集总反应动力学模型的基础上,结合我国催化裂
化大回炼比等特点,将重燃料油中的芳环组分(C Ah)划分为单、双环芳环集总(SCAh)和多环芳环集总(PCAh),首次建立了适合我国炼油工艺国情的催化裂化十一集总反应动力学模型。此后刘之定等又在催化裂化十一集总反应动力学模型的基础上,将原来气体+焦炭(C )集总分为气体(G )、焦炭(C )两个集总,建立了催化裂化十二集总反应动力学模型。
催化裂化十一集总反应动力学模型在我国不少炼厂得到了应用,并在指导优化提高轻质油收率等方面取得了很好的效益,但由于该模型按烃族和结构族组成划分,需要的分析手段和仪器非常规分析手段,我国的一般炼厂难以做到,这在一定程度上限制了模型的工业应用,而随着催化裂化原料的日趋重质化和劣质化,原料分析的矛盾愈为突出。
于是,根据上述问题,任杰等提出了一种新的集总划分方法:馏程-结构族划分法,即从重油催化裂化原料特点出发,将原料按馏程分为 3 个馏分:轻燃料油(LFO )、重燃料油(HFO )和渣油馏分(RFO );每个馏分又按结构族组成分成烷基碳、环烷碳和芳香碳 3 个集总,再加上汽油集总和气体+焦炭集总建立了重油催化裂化十一集总反应动力学模型。由于该模型完全按馏程- 结构族组成划分集总,不需要质谱分析,只需对常规的物理性质进行测定并通过一些关联式计算即可得到集总组分的性质,分析方法的简单可行大大提高了模型的实用性。
此后,为适应催化裂化原料日趋重质化和劣质化的需要,邓先梁等在上述重油催化裂化十一集总反应动力学模型的基础上将原料油中的胶质、沥青质中的芳环基团单独集总,并将裂化气和焦炭分别集总,提出了适用于渣油催化裂化的十三集总反应动力学模型。孙铁栋等提出将原料油中的直链烷烃和环烷烃合并为一个集总,以减少集总数目,使模型得到简化。一系列的研究结果表明集总的划分不仅要依据动力学特性相似的原则,同时还需考虑集总组分的易测定性和满足应用的需要,此时的催化裂化集总反应动力学模型的研究正日趋成熟。
2.3 第三阶段
在经历了通过增加集总数目来提高模型适用性和预测性的阶段后,为了使模型更加完善,国外学者把目光聚焦在可影响催化裂化反应的因素上。如在20 世纪 90 年代建立的动力学模型当中,催化剂失活函数一般认为是对催化裂化所有反应类型具有同样效应的单一函数。但事实上,催化剂失活对每种反应类型的影响是不同的,Bollas 等对此提出了一个具有选择性的催化剂失活函数,这种选择性以进料性质和产品性质等为导向和依据。Nevicato 等认为导致催化剂失活的直接原因并不是催化剂停留时间,而是催化剂上附着的焦炭,因此他提出了以催化剂含焦量为变量的催化剂失活函数。此后不少学者在其建立的模型当中都运用该催化剂失活函数。
20世纪90 年代后,催化裂化工艺技术面临了原料劣质化、产品清洁化和多样化的挑战,促使新的催化裂化工艺及技术不断涌现。催化裂化集总反应动力学模型的研究为满足应用的需要也取得了长足的进步,我国作为催化裂化大国,在这方面表现尤为突出。
为满足石油化工高速发展对乙烯、丙烯等低碳烯烃需求的急剧增长,中国石油北京石油化工科学研究院开发了一系列以重油直接生产轻质烯烃的FCC 新技术,如催化裂解(DCC)、催化热裂解(CPP )、重油接触裂解(HCC)等所谓催化裂化家族工艺。为指导优化这些新工艺,研究者们相继开发了一系列相应的集总反应动力学模型。如对于DCC工艺,许友好等考虑到汽油和烯烃为该工艺的主要产品,把汽油和包含气体烯烃的液化气各作为一个集总,再加上VGO和焦炭+ 干气两个集总,建立了馏分油催化裂解四集总反应动力学模型。Meng针对重油催化裂解工艺,建立了包含重油、汽油+ 柴油、LPG 、干气、焦炭的催化裂解五集总。后考虑到烯烃和烷烃的二次裂化性质的不同,将LPG 和干气中烯烃和烷烃分别集总,建立了催化裂解七集总,后将重油划分为芳烃和非芳烃建立催化裂解八集总以扩展模型适应性。Liu 等将七集总中汽油+ 柴油分开集总提出催化裂解八集总。对于CPP 工艺,李丽等为更细致地研究裂解气体的反应行为,将反应体系分为 1 个原料集总和 6 个产品集总:汽柴油、丙烯+丁烯、丙烷+丁烷、乙烯、小分子烷烃和焦炭,建立了重油催化裂解七集总反应动力学模型。对于 HCC工艺,王国良等首先按馏程将原料和产物划分为重油、柴油、汽油、裂化气和焦炭,然后按结构族组成将重油和柴油分别划分为烷烃、环烷烃和芳烃,将裂化气再细分为氢气、甲烷、乙烯、乙烷、丙烯、丙烷、丁烯和丁烷。由于乙炔、硫化氢、二氧化碳含量很低,在模型的建立过程中没有考虑,从而建立了重油接触裂解十六集总反应动力学模型。
灵活多效催化裂化工艺(FDFCC)是由洛阳石化工程公司开发的旨在降低汽油烯烃含量、提高催化裂化装置柴汽比、同时副产丙烯的催化裂化新工艺。吴飞跃针对该工艺开发了 FDFCC集总反应动力学模型。他根据工艺由重油提升管和汽油提升管两根提升管串联而成的特点,分别建立了重油催化裂化集总反应动力学模型和汽油催化改质集总反应动力学模型两个子模型,然后通过粗汽油组分的物料平衡将两个子模型有机地结合起来,构成了FDFCC集总反应动力学模型。结果表明,除油浆的相对误差较大外,其它集总组分的模型计算值和工业实测值之间相对误差基本上均在5%以内,可为工业装置提供优化指导。
两段提升管(TSRFCC )技术是由中国石油大学开发的,其目的在于提高汽、柴油的收率。刘熠斌等针对该工艺开发了相应的集总反应动力学模型。该模型包含第一段提升管反应动力学模型和第二段提升管反应动力学模型,然后通过循环油的物料衡算将二个子模型联系起来,构成最终的TSRFCC 集总反应动力学模型。该模型集总数少,计算简便,能够对两段不同转化率分配和不同目的产物产率进行较准确预测。
随着原油资源的匮乏和劣质化程度的加剧,在全球尤其在我国出现了不少以催化裂化为核心的组合工艺,以适应处理高硫、高金属、高残炭等性质低劣重油的需要。常见的有渣油加氢-催化裂化组合工艺、延迟焦化- 催化裂化组合工艺、溶剂脱沥青-催化裂化组合工艺等。组合工艺因能耗低,灵活强等优点而得到很快发展,同时也促进了与之相适应的集总反应动力学模型的研究。许先焜针对渣油加氢- 催化裂化组合工艺开发了渣油加氢- 催化裂化组合工艺动力学模型。该模型由渣油加氢处理动力学模型和加氢渣油催化裂化动力学模型两部分组成。通过加氢渣油和重循环油的物料平衡将两个装置的动力学模型有机结合。验证结果表明,该模型能较准确预测主要目的产品的产率,具有良好的
预测性和外推性。曹新怀针对重油催化裂化-芳烃抽提组合工艺从联合整体角度出发建立了重油催化裂化-芳烃抽提组合工艺模型。工业验证表明,该模型具有良好的预测性和外推性。新工艺、新技术的不断涌现成为了集总动力学模型发展的动力,相信随着组合工艺的发展,与之相应的组合工艺集总动力学模型种类将越来越多、内容将越来越丰富。
3 催化裂化集总反应动力学模型建模过程的发展
一个成功的集总动力学模型的建立,合理的集总划分是关键,但简单可靠的数据来源、快捷正确的参数估计等建模过程中必不可少的辅助步骤也是建模成功的保障,而随着催化裂化集总动力学模型的不断发展,这些方面也愈来愈成熟和完善。
3.1 数据来源的多渠道
在集总划分后,依据反应机理建立集总间的反应网络,而此集总反应网络中的各动力学参数通常是通过实验测定和参数估计相结合获得的。集总反应网络尽管相对于实际反应体系来说已作了大量的简化,但因本身反应系统的复杂性及为满足应用的需要,集总反应网络仍有一定数量的动力学参数。求取这些参数通过不同反应条件下的实验获得,为此需搭建专门的实验装置,进行一系列的微反实验。但由于模型参数求取的数据是通过实验室反应器获得,因此当模型用于工业装置时还必须考虑工业反应器与实验室反应器间的偏差,通常采用设置装置因数等办法予以解决。但随着集总划分愈来愈细,模型参数愈来愈多,实验工作量也就愈来愈大,实验结果用于工业装置的矛盾也就愈来愈突出。
尽管自催化裂化三集总反应动力学模型问世起,传统的集总反应动力学模型参数就一直来源于实验数据,但随着集总反应动力学模型研究的深入,研究者们开始把目光转向工业实测数据,于是出现了如吴飞跃、许先焜等直接采用工业标定数据或平稳操作数据建立集总反应动力学模型的例子。在这些模型的建立中,不但实验工作量大大减少,而且模型更贴近工业实际,针对性强,在工业应用中取得了很好的效果。目前己有愈来愈多的研究者部分或全部采用工业实测数据代替实验数据来进行集总反应动力学模型的研究。
3.2 参数估计方法的发展
无论是从实验室还是工业装置获得基础数据后,均须对模型参数进行优化确定。参数估计是获得可靠模型参数的重要环节,于是随着反应动力学模型的全面发展,各种行之有效的参数估计方法应运而生,如Guass-Newton 法、Marquadt 法、单纯形法、Powell 法、共轭梯度法、变尺度法(B-F-G-S)等。这些方法各有特点,通常从收敛性、稳定性、可靠性、有效性、适用性、易用性、移植性、强健性等方面进行详细的研究分析、比较权衡之后,按需选用。
催化裂化反应网络中一般有几十个动力学参数,如果逐一测定各反应的速率常数,不仅实验工作量大,而且由于反应网络中有的集总组分(如芳环及芳环上的取代基团)不可能单独存在,故难以完全实行,必须借助于参数估计。而为确保所估参数的可靠性,同时估计的参数数目又不能太多,于是常常根据
反应机理将反应网络划分成几个子网络,采取分步实验及分步参数估计直到最后确定全部模型参数,但这样一来,必然使实验工作量成倍增加。新型的参数估计方法的选用大大提高了多参数估计的可靠性,既减少了测定速率常数的实验工作量,又不失参数估计的准确性,使建模过程更快捷、高效、准确,如邹劲松对比了各种优化算法的优缺点后,选用 Fletcher 开关算法依据实验室数据进行了参数优化。在催化裂化集总反应动力学模型的建立过程中,打破了常规的分步测定法,提出了一种新的参数估计方法——一步法。实验证明,一步法估计动力学参数不但是可靠的,且该法避免了分步实验和参数估计过程中的误差累积,故最终拟合结果略优于分步法。
近年来由于参数估计方法的快速发展,如吴飞跃研究中,尽管反应速率常数多达一百多个,但都能顺利得到解决。快捷可靠的参数估计方法使动力学模型的研究更上了一层楼,既缩短了模型开发周期,又提高了模型的可靠性。
3.3 辅助模型的开发
催化裂化集总反应动力学模型不可能面面俱到,由上介绍可知集总反应动力学模型建立过程的严密性和复杂性,不可能将己建模型随意改动,但为了满足不同的用户使用的需要,研究者们须不断拓宽催化裂化集总反应动力学模型的适用范围,提高模型的适应性和灵活性,这方面的进展主要有两大方面:一方面是对模型本身的完善,如We ek ma n等所建的催化裂化十集总动力学模型考虑到若加工重质原料,可在模型方程中引入碱氮中毒、重芳烃吸附项等予以解决。另一方面是开发与主模型配合使用的辅助模型,这方面的实例较多。如:
为满足催化裂化产品结构随市场需求的变化,汽油与柴油的馏程范围常会变动,为了避免按新的馏程标准重新划分集总、建立模型、测定参数等一系列繁冗的实验工作,Liu 等建立了汽柴油切割点变化与柴油收率的关联模型——馏程修正模型,作为所建催化裂化集总反应动力学模型的补充,可在不改变所建动力学模型的情况下,简便正确地满足馏程范围变化的需要。
为解决渣油原料的结构族组成数据需用核磁共振波谱(NMR)等大型仪器而一般炼厂又不具备的矛盾,沙颖逊等在FCCU 反-再系统模拟优化软件中开发了一组可由重质原料油的常规物性数据求出其结构族组成数据的关联式,称之为原料结构性质模型;江洪波根据国内外发表的大量数据,利用一些经典算法建立了族组成和结构族组成的关联方程等。此类辅助模型的建立,使得用户只需测定原料油常规分析数据即可得到其结构族性质数据,具有很大的实用价值。
在早期开发的催化裂化集总反应动力学模型中,都将气体和焦炭作为一个集总考虑,随着石油化工原料需求量的骤增,炼厂对催化裂化各种轻端产品的产率和组分分布开始重视。为不增加模型的复杂性,沙颖逊等在FCCU 反-再系统模拟优化软件中嵌入了焦炭产率模型和裂化气产率模型,用以预测焦炭生成量和裂化气产率。江洪波对轻端产品分布与反应条件及催化裂化产物分布之间的相互关系进行了回归分析,得到了轻端产品中各个组分浓度的关联模型。这些辅助模型与催化裂化集总反应动力学模型的结合使用,拓宽了集总模型的应
用功能和适用范围,大大提高了模型的实用性和灵活性,成为了集总反应动力学模型发展中的重要组成部分。
4 结语
催化裂化集总反应动力学模型经过近半个世纪的发展,在模型的开发和应用上都取得了令人瞩目的成就。随着催化裂化新技术新工艺的不断涌现,如今的集总划分越来越合理,参数估计方法更为先进多样,辅助模型更加丰富易用,集总模型越来越完善,适应性更强,应用范围更广,并在推动催化裂化新技术新工艺的发展中起到了良好的作用。集总反应动力学模型的成熟,为更高层次的复杂反应体系反应动力学模型——分子尺度反应动力学模型的研究奠定了良好的基础。
多相催化反应基础
多相催化反应基础
催化反应循环
以CO催化氧化反应 为例,催化反应过 程的分子水平描述 如图1.5所示。
CO+O2→CO2
催化反应过程基本步骤
?
?
第一步,反应分子扩散过程:反应分子从气相扩散到金属(活性 组分)表面,这里,反应分子基本上以吸附分子形态存在 分子表面扩散与解离过程:,反应分子可能发生表面扩散,并解离 成吸附态原子。以CO催化氧化为例,由于O2的键能(500kJ/mol) 比CO的键能(1076kJ/mol)低,O2分子易于解离成Oa。 表面反应过程: CO+Oa →CO2 通常表面反应过程是催化反应的 速度控制步骤(rate-determining step) 反应产物脱附过程: 吸附在催化剂表面的反应产物(CO2)的表面结 合能被打破,并从表面脱附出来 产物分子扩散过程:产物分子从催化剂表面脱附后扩散到气相, 然后随反应气离开反应器
?
?
?
气相扩散过程是催化反应中复杂性问题
扩散控制的判断与消除
?
?
?
催化反应过程中涉及的扩散包括 外扩散与内扩散 外扩散阻力来自气固边界层的滞 流层,气流方向的线速度直接影 响滞流层的厚度。当流体线速度 达到足够高时,外扩散的影响可 以消除(为什么?) 内扩散阻力来自催化剂颗粒孔隙 内径和长度(内通道几何尺 度),所以,催化剂颗粒大小将 直接影响分子内扩散过程。通过 改变催化剂颗粒度大小对反应速 率影响的实验,可以判断反应区 内是否存在内扩散的影响
问题1:为什么要消除扩散影 响?改变线速度是否就可以达到 预定效果? 问题2:说明内扩散效应对催化 反应的利与弊。
催化反应动力学
催化反应动力学研究小报告 催化反应大致可以分为三大类: (1)均相催化:催化剂与反应物处于同一相种,均为气相或均为液相; (2)复相催化:催化剂与反应物处于不同相中,如Fe 对合成氨的催化作用; (3)生物催化:即酶催化,如制酒过程中的发酵作用。酶是蛋白质或核酸分子组成,而分子很大,因此它既不属于均相也不属于复相,而是兼备二者的某些特性。本文将对这三种催化反应的反应动力学进行具体文献分析。 1.均相催化反应动力学研究 在均相催化反应中,催化剂和反应物同处于液相或者气相。其机理为首先反应物和催化剂生成不稳定的中间化合物,然后中间化合物又分解生成产物,使催化剂再生。 陈荣悌[1]等人以H g C I 2为催化剂时乙炔氢氯化制氯乙烯均相反应的动力学。 反应方程如下: 设速率方程为: 因为在一次实验中, 催化剂浓度是不变的, 而且当〔H +〕、〔Cl -〕均远大于〔C H ≡C H 〕时, 则速率方程可写成: 第一步:确定反应对乙炔的级数 当反应为一级或假一级反应时,可推导出如下公式: 本反应以)ln(P P -∞对t 线性回归, 其相关系数在0.99 以上。表明反应对乙炔为一级。 第二步:消除扩散影响的实验
为了消除扩散的影响,作者作了改变搅拌速度对速率常数影响的实验。当转速在1 3 85 转/ 分以上时,k′′值趋于稳定, 即扩散影响基本消除。全部实验中皆控制搅拌速度在1 3 8 5 转/分以上进行。 第三步:确定反应对催化剂H g CI2的级数 改变H g CI 2的浓度, 分别求出k′′值, 以l g k′′对lg〔H g C I2〕线性回归, 相关系数R =0 . 9 9 6 , 斜率为1 . 0 4 6 , 即m为1, 说明反应对催化剂H g C I2为一级。 第四步:确定反应对C l-的级数 在盐酸浓度为5.37 M 的基础上分别加入H C I O 4,使〔H C I〕+ 〔H C IO4〕= 6.2 7M 和7.16M , 并与单纯的〔H C I〕= 6.2 7M 和7.1 6M 的实验相比较发现当〔C l -〕足够大时( 因为生成H g C I2需足够的C l-) , 反应对C I-零级。 第五步:确定反应对H +的级数 由于反应对Cl-为零级, 因此可以通过改变盐酸浓度来确定反应对H+ 的级数以lgk′′对lg 〔H + 〕线性回归, 相关系数R = 0 .98 1 , 斜率为3 .07, 即n=3 , 说明反应对H+为三级。 第六步:求反应的表观活化能 在相同的条件下, 改变温度进行实验, 分别求出k′′值。以lnk′′对l/ T 线性回归, 相关系数R =0 . 9 9 7, 斜率为-6 8 21 , 从斜率求出表观活化能E =1 3 . 6千卡/ 摩尔。 最后该反应速率方程为: 2.复相催化反应动力学研究 复相催化主要是用固体酸催化气相反应或者液相反应。催化作用是通过表面来实现的,目前理论都不能完善解释其中机理,但活性中心的性质的解释是各种理论的共同点。 祁喜旺[2]等人采用经巯基乙胺改性的大孔磺酸型离子交换树脂作催化剂,在60-80℃, 原料酚/酮( mol比)为4:1-12:1的范围内研究了由苯酚与丙酮合成双酚A的催化反应动力学。 反应方程为:
催化反应动力学数据测定
实验三气固相苯加氢催化反应实验 一.实验目的 1.了解苯加氢的实验原理和方法。 2.了解气固相加氢设备的使用方法和结构。 3.掌握加压的操作方法。 4.通过实验进一步考察流量、温度对苯加氢整套反应的影响。 二.实验原理 环己烷是生产聚酰胺类纤维的主要中间体之一,高纯度的环己烷可由苯加氢制得。 苯加氢是典型的有机催化反应,无论在理论研究还是在工业生产上,都具有十分重要的意义。工业上常采用的苯加氢生产环己烷的方法主要有气相法和液相法两种。气相法的优点是催化剂与产品分离容易,所需反应压力也较低,但设备多而大,费用比液相大。液相法的优点是反应温度易于控制,不足之处是所需压力比较高,转化率较低。 反应主要方程式如下: 苯加氢制环己烷的反应是一个放热的、体积减小的可逆反应,因此,低温和高压对该反应是有利的。所以,苯加氢制环己烷的反应温度不宜过高,但也不能太低,否则反应分子不能很好地活化,进而导致反应速率缓慢。如果催化剂活性较好,选择性可达95%以上。
本实验选择在加压固定床中进行催化反应,催化剂采用r-Al 2O 3 载Ni 或Cu 。 原料:苯,氢气,氮气(吹扫用),环己烷 三、流程示意图与面板布置图 1、流程示意图 V -截止阀,S -三通转换阀,T C I -控温,T I -测温,P I -测压 气体钢瓶, 过滤器, 稳压阀 , 干燥器, 质量流量计,止逆阀缓冲器, 预热器, 预热炉, 反应炉, 反应器 , 冷却 器 气 液分离器背压阀, 取样器,湿式流量计, 加料泵
2、面板布置图
四.实验步骤 1、装填20ml催化剂 打开反应加热炉,卸下反应器的上下盖法兰的连接口接头,从炉内取出反应器(拆卸时先将热电偶插件拔出)。在设备外部将上下法兰压紧螺栓松开,旋转推出,若反应器内上部有玻璃棉,用带有倒钩的不锈钢丝将它取出,并倒出催化剂,再取出反应器下部的玻璃棉,最后用镊子夹住沾有丙酮的脱脂棉擦拭一下,同样擦拭反应器内部,用吸耳球吹干。这时要注意,反应器内有测温套管,不能将它碰歪。若感到不方便,可将下法兰也卸下来,这样就很好清洗了。装填催化剂时要先将下法兰装好,后装好支撑架测好位置,装玻璃棉,倒入催化剂,最后再装入玻璃棉。上好上法兰,拧紧螺栓放回反应炉内支撑好,再次连接出入口接头,插入热电偶(其底端位置应根据装在反应器内催化剂的高度而定。催化剂的加入量以实验的要求而定,单位的取舍是根据空速单位而定,由此选择称量重量还是测量体积。装催化剂要通过小漏斗装入反应器。装填时要轻轻震动反应器使催化剂均匀分布,催化剂上部再放入少许玻璃棉。 注意:安装反应器和上开启炉子一定要轻轻操作,拧紧接头时要用力适当不能过力,以免损坏接口螺纹。 2、系统试漏 <1>确定操作压力,关闭尾气出口阀门、背压阀。
催化反应动力学报告
催化裂化集总反应动力学模型研究进展 摘要:分析和介绍了国内外催化裂化装置建模和稳态模拟方面的研究和进展。对催化裂化反应集总方法及相应的反应网络进行归纳,并讨论其优缺点;推导了动力学模型方程并着重探讨方程求解算法以及模型中动力学参数、催化剂失活因子和装置因素的估计方法。对催化裂化集总反应动力学模型的研究进展进行了综述,从中可见复杂反应体系集总反应动力学模型的发展历程。 1.引言 催化裂化是炼油工业最重要的二次加工工艺之一,其目的是将重质油转化成更有价值的轻端产品。由于油品组成复杂,很难用常规的动力学方法研究该高度偶联的反应体系,集总(1umping)理论的出现为催化裂化反应动力学的研究开辟了新的途径。近些年来,催化裂化在新技术、新工艺等方面取得了很大的进展,同时在集总动力学模型的开发和应用研究上也取得了引人注目的成绩。如蜡油的三集总、四集总、五集总、十集总、十一集总和渣油的六集总、十一集总、十三集总等动力学模型的开发,其中有些模型已经成功地应用于工业装置并取得明显的经济效益。本论文将综合评述催化裂化集总动力学模型的研究现状,为模型的进一步开发和研究提供指导。 1963年由Aris 等和We i 等创立的反应速率常数矩阵法,解决了复杂反应体系内反应强耦联这一难题,使对复杂的耦联反应体系进行解耦成为了可能。但由于复杂反应体系内原料与产物组分繁多,且每一组分又能进行不止一种的反应,故而建立详细描述每一组分反应行为的动力学模型是不可能的,必须进行一定的简化处理。所谓集总即是将反应系统中众多的单一化合物,按其动力学特性相似的原则,归并为若干个虚拟的单一组分(集总),然后去开发这些虚拟的集总组分间的反应网络,建立简化了的集总反应网络的动力学模型。集总反应动力学模型是在深刻认识反应机理的基础上将复杂的反应网络简化处理,从而开辟了一条动力学研究的新途径。集总理论最早应用于催化裂化过程,其后又应用于催化重整、延迟焦化、渣油加氢等其它过程。本文将通过回顾、总结催化裂化集总反应动力学模型的发展来见证集总理论及集总反应动力学模型的发展历程。 2 催化裂化集总反应动力学模型集总划分原则的发展 从集总划分原则的角度,可将催化裂化集总反应动力学模型的发展分为三个阶段。 2.1 第一阶段 20世纪60年代后期,Week man 等最早将集总理论成功运用于催化裂化过程,建立了催化裂化三集总反应动力学模型。该模型根据馏程的不同将反应物和产物归并为未转化的原料油、汽油和气体+ 焦炭三个集总。结果表明该模型能够较准确地预测给定原料油的转化率、生成汽油的选择性和最佳操作条件等。由于该模型参数少,计算简便,预测结果准确,在指导工业装置设计操作优化等方面显示出了强大的作用。催化裂化三集总反应动力学模型开创了集总理论在催化裂化反应动力学领域应用的先河,它肯定了将集总方法运用于复杂
化工动力学
1、CO在钯催化剂上的抵押氧化动力学 从该反应速率方程式中可以看出, 反应速率与TiO2表面吸附的O浓度和Pt 表面吸附的CO浓度呈正比
2、合成氨催化反应动力学 氨合成为气固相催化反应,它的宏观动力学过程包括以下几个步骤。 ①氮氢气体从气流主体扩散到催化剂颗粒的外表面----外扩散②反应物从外表面向催化剂的孔道内部扩散----内扩散 ③反应物被催化剂吸附----吸附④在催化剂内部孔道内组成的内表面上进行催化反应----化学反应⑤产物从催化剂表面脱附----脱附⑥产物从催化剂内表面扩散到外表面----内扩散⑦产物从外表面扩散到气流主体----外扩散 氮、氢气在催化剂表面反应机理,可表示为: N2(g)+催化剂—→2N(催化剂) H2(g)+催化剂—→2H(催化剂) N(催化剂) + H(催化剂) —→NH(催化剂) NH(催化剂) + H(催化剂) —→NH2(催化剂) NH2(催化剂) + H(催化剂) —→NH3(催化剂) NH3(催化剂)—→NH3(g) + 催化剂 实验结果证明,N2活性吸附是最慢的一步,即为表面反应过程的控制步骤。 对整个气固相催化反应过程,是表面反应控制还是扩散控制,取决于实际操作条件。低温时可能是动力学控制,高温时可能是内扩散控制; 大颗粒的催化剂内扩散路径长,小颗粒的路径短,所以在同样温度下大颗粒可能是内扩散控制,小颗粒可能是化学动力学控制。 1、温度 变换反应是放热反应,存在反应最佳温度。从热力学上看,T↑,Kp↓;但从动力学因素看,T↑,Kp ↑。使变换率最大的温度为最佳温度, 2.压力 从速度方程可看出,提高压力可使正反应速度增加大于逆反应速度增加,所以一般选择较高压力。同时必须在较高压力下才有可观的速度。 3、甲烷蒸汽转化反应动力学
催化反应的热力学和动力学
第三章 催化反应的热力学和动力学 一、催化反应的热力学热力学 化学和酶催化反应和普通化学反应一样,都是受反应物转化为产物过程中的能量变化控制的。因此要涉及到化学热力学、统计学的概念。下面对催化反应热力学作简要介绍。 1.热力学第一定律(又称为能量守恒与转化定律) 实际上是能量守恒和转化定律的说明。能量有各种形式,能够从一种形式转化为另一种形式,从一个物体传递给另一个物体,但在转化和传递中,能量的总量保持不变。如果反应开始时体系的总能量是U 1,终了时增加到U 2,那么,体系的能量变化U ?为: U ?=U 2-U 1 (3-1) 如果体系从环境接受的能量是热,那么,体系还可以膨胀作功,所以体系的能量变化U ?必须同时反映出体系吸收的热`和膨胀所作的功。体系能量的这种变化还可以表示为: U ?=Q -W (3-2) Q 是体系吸收的热能,体系吸热Q 为正值,体系放热(或体系的热量受到损失)Q 为负值;W 是体系所作的功,当体系对环境作功时,W 值是正的,当环境对体系作功时,W 值是负的。体系能量变化U ?仅和始态及终态有关,和转换过程中所取得途径无关,是状态函数。 大多数化学和酶催化反应都在常压下进行,在这一条件下操作的体系,从环境吸收热量时将伴随体积的增加,换言之,体系将完成功。在常压p ,体积增加所作的功为: ??==V p pdV W (3-3) 这里,△V 是体系体积的变化值(即终态和始态时体积的差值)。因此,这时在常压下,体系只作体积功时,热力学一律的表达式为: U ?=V p Q p ?- (3-4) 对在常压下操作的封闭体系,H Q p ?=,△H 是体系热函的变化。因此,对常压下操作的体系:热力学一律的表达式为:V p U H ?+?=? (3-5) △U 和p △V 对描述许多化学反应十分重要。但对发生在水溶液中的反应有其特殊性,因为水溶液中的反应没有明显的体积变化,p △H 接近于零。△H ≈△U ,所以对在水溶液中进行的任何反应,可以用热函的变化△H 来描述总能量的变化,而这个量△H 是可以测定的。
多相催化反应
学习心得 一、催化剂在在工业生产中的应用 工业生产中采用催化剂生产或加工产品已有百余年历史,化工生产中典范 的催化剂应当是铁基合成氨催化剂,也是历史很久、研究得最多、用量最大的 一个催化剂。其中氧化铝是公认的结构型助催化剂,还加入钾等一些电子型助 催化剂,氯、硫、磷等是催化剂永久性毒物,氧、二氧化碳、一氧化碳、水汽 等是催化剂暂时性毒物。钢铁零件表面固体渗碳是一个古老的生产工艺,估计 也有百年历史,为了加快渗碳速度、缩短生产时间以及提高渗碳层质量,渗碳 剂中必须加入催化剂(又称助渗剂)。常用的催化剂是碳酸钡等碱土和碱金属 碳酸盐,S、Cl等是过程的阻滞剂(又称反应毒物)。与固体渗碳工艺密切相 关的碳气化反应(CO2+C=2CO)是一个非常重要的工业反应,由于涉及能源、冶 金和化工工业,因此有关这个反应的热力学、动力学、反应机理、催化剂与毒 物等同样进行了大量研究。 二、什么是单相催化反应和多相催化反应? 单相催化,又称均相催化,其中反应物质与催化剂都处于同一相中。 多相催化反应是气态或液态反应物与固态催化剂在两相界面上进行的催化反应。其历程至少包括反应物在催化剂表面上的化学吸附,吸附中间物的转化(表面反应)和产物脱附三个连续步骤。阐明一个多相催化反应的历程,需揭 示有关催化剂的活性部位和表面吸附中间物的结构和性质;吸附与催化反应 的关系(如吸附分子之间反应或吸附分子与气相分子反应);催化剂表面活性 部位如何在催化循环中获得再生以使催化反应能连续进行等。一般是通过多 相催化反应的动力学与催化剂的物理化学分析以获得对其历程的了解。 实际上,多相催化主要由于化学吸附,且催化剂表面只有一小部分能起催 化作用,这部分称活性中心 ....。反应物只有被吸附在活性中心上,才能变形并活化,从而加速反应。化学吸附带有化学键性质,故一种催化剂只能催化某些特 定的反应,这就是催化剂选择性的原因。一般说,粒子越细或表面积越大,表 面缺陷越多,其催化活性越好。多相催化剂可连续进行催化;与产物易于分离,使用温度范围很宽,故许多工业反应都采用多相催化,或将均相催化剂负载于 多孔的聚合物或无机载体上,如将酶负载于若干不溶性载体上,获得固定化酶,应用极广。 三、多相催化反应的步骤 1.反应物由气体向催化剂的外表面扩散(外扩散); 2.反应物由外表面向内表面扩散(内扩散); 3.反应物吸附在表面上;
多相催化
多相催化 多相催化反应是气态或液态反应物与固态催化剂在两相界面上进行的催化反应。其历程至少包括反应物在催化剂表面上的化学吸附,吸附中间物的转化(表面反应)和产物脱附三个连续步骤。阐明一个多相催化反应的历程,需揭示有关催化剂的活性部位和表面吸附中间物的结构和性质;吸附与催化反应的关系(如吸附分子之间反应或吸附分子与气相分子反应);催化剂表面活性部位如何在催化循环中获得再生以使催化反应能连续进行等。一般是通过多相催化反应的动力学与催化剂的物理化学分析以获得对其历程的了解和应用,下面就让我来阐述具体的影响过程。 吸附质分子与固体表面原子(或分子)发生电子的转移、交换或共有,形成吸附化学键的吸附。由于固体表面存在不均匀力场,表面上的原子往往还有剩余的成键能力,当气体分子碰撞到固体表面上时便与表面原子间发生电子的交换、转移或共有,形成吸附化学键的吸附作用。 化学吸附的主要特点是:仅发生单分子层吸附;吸附热与化学反应热相当;有选择性;大多为不可逆吸附;吸附层能在较高温度下保持稳定等。化学吸附又可分为需要活化能的活化吸附和不需活化能的非活化吸附,前者吸附速度较慢,后者则较快。
化学吸附是多相催化反应的重要步骤。研究化学吸附对了解多相催化反应机理,实现催化反应工业化有重要意义。 吸附特点与物理吸附相比,化学吸附主要有以下特点:①吸附所涉及的力与化学键力相当,比范德华力强得多。②吸附热近似等于反应热。③吸附是单分子层的。因此可用朗缪尔等温式描述,有时也可用弗罗因德利希公式描述。捷姆金吸附等温式只适用于化学吸附:V/Vm=1/a·㏑CoP。式中V是平衡压力为p时的吸附体积;Vm是单层饱和吸附体积;a和c0是常数。④有选择性。⑤对温度和压力具有不可逆性。另外,化学吸附还常常需要活化能。确定一种吸附是否是化学吸附,主要根据吸附热和不可逆性。 吸附机理 可分3种情况:①气体分子失去电子成为正离子,固体得到电子,结果是正离子被吸附在带负电的固体表面上。②固体失去电子而气体分子得到电子,结果是负离子被吸附在带正电的固体表面上。③气体与固体共有电子成共价键或配位键。例如气体在金属表面上的吸附就往往是由于气体分子的电子与金属原子的d 电子形成共价键,或气体分子提供一对电子与金属原子成配位键而吸附的。 在复相催化中的作用及其研究 在复相催化中,多数属于固体表面催化气相反应,它与固体表面吸附紧密相关。在这类催化反应中,至少有一种反应物是被固体表面化学吸附的,而且这种吸附是催化过程的关键步骤。在固体表面的吸附层中,气体分子的密度要比气相中高得多,但是催化剂加速反应一般并不是表面浓度增大的结果,而主要是因为被吸附分子、离子或基团具有高的反应活性。气体分子在固体表面化学吸附时可能引