对辊式红枣分级机的设计教案资料
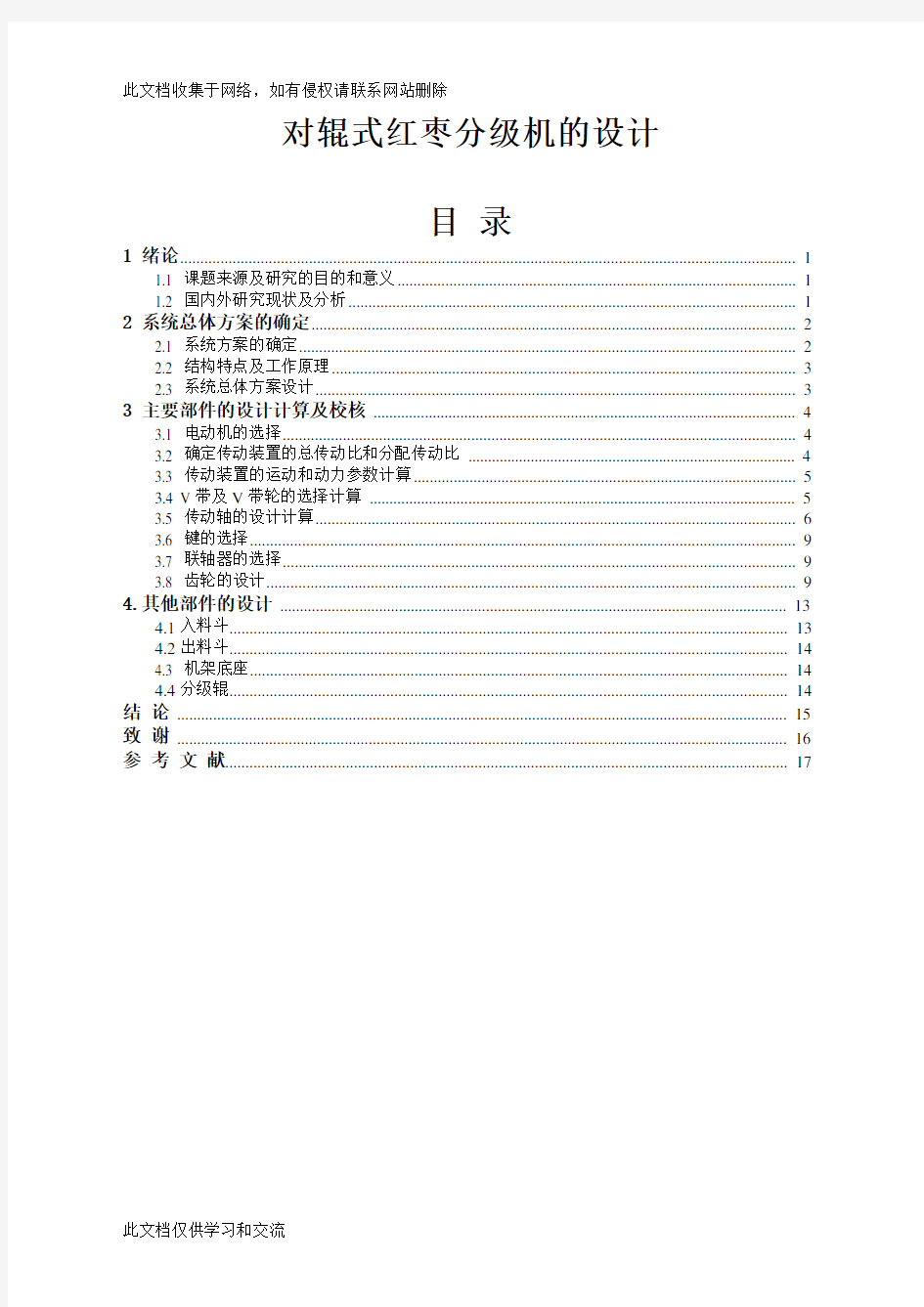

对辊式红枣分级机的设计
目录
1 绪论 (1)
1.1 课题来源及研究的目的和意义 (1)
1.2 国内外研究现状及分析 (1)
2 系统总体方案的确定 (2)
2.1 系统方案的确定 (2)
2.2 结构特点及工作原理 (3)
2.3 系统总体方案设计 (3)
3 主要部件的设计计算及校核 (4)
3.1 电动机的选择 (4)
3.2 确定传动装置的总传动比和分配传动比 (4)
3.3 传动装置的运动和动力参数计算 (5)
3.4 V带及V带轮的选择计算 (5)
3.5 传动轴的设计计算 (6)
3.6 键的选择 (9)
3.7 联轴器的选择 (9)
3.8 齿轮的设计 (9)
4.其他部件的设计 (13)
4.1入料斗 (13)
4.2出料斗 (14)
4.3 机架底座 (14)
4.4分级辊 (14)
结论 (15)
致谢 (16)
参考文献 (17)
1 绪论
1.1 课题来源及研究的目的和意义
红枣,又名大枣。自古以来就被列为“五果”(桃、李、梅、杏、枣)之一,历史悠久。大枣最突出的特点是维生素含量高。在国外的一项临床研究显示:连续吃大枣的病人,健康恢复比单纯吃维生素药剂快3倍以上。因此,大枣就有了“天然维生素丸”的美誉。红枣为温带作物,适应性强。红枣素有“铁杆庄稼”之称,具有耐旱、耐涝的特性,是发展节水型林果业的首选良种.近些年红枣价格年年攀升,红枣产业在新疆一些地区有了较快的发展,对带动地区经济增长,尤其在带动农牧民增收上起到了重要作用。由于某些原因,没有上传完整的毕业设计(完整的应包括毕业设计说明书、相关图纸CAD/PROE、中英文文献及翻译等),此文档也稍微删除了一部分内容(目录及某些关键内容)如需要的朋友,请联系我的叩扣:二二壹五八玖一壹五一,数万篇现成设计及另有的高端团队绝对可满足您的需要.
新疆南疆地区是世界上最适宜种植优质红枣的区域,是国家农业部确认的国家级绿色食品基地.南疆地区光照时间长,每年4-10月累计日照时数达2027.1小时,平均每天的日照时数达到10小时以上,且光照度强,十分有利于红枣果实生长;该地区8-10月平均日较差在17.5—18.2℃,最大日较差可达27.8℃,特别有利于枣果可溶固形物和糖分积累,这也是造就南疆地区红枣品质极优的根本原因。
“十一五”期间,随着新疆产业结构的调整,红枣种植面积大不断扩大。截至2009年底,新疆红枣种植面积达481.08万亩,约占全国的21.38%;产量26.32万吨,约占全国的8.63 %。红枣种植主要分布在南疆的阿克苏、喀什、和田、巴州等地。新疆红枣栽培历史悠久,建国后,特别是60-80年代引进品种42个,加之古、近代的引入,共计49个品种。目前从各地州规模发展的主栽品种构成来看:绝大多数为干、鲜两类的灰枣、骏枣及赞皇红枣等品种。红枣种植模式主要有枣农间作和成片建园两种方式,间作模式有枣树+小麦、枣树+豆类、枣树+棉花、枣树+蔬菜、枣树+西(甜)瓜。成片建园的枣树株行距多以2 x 3米或1.5 x 4米,每亩110株较为普遍。
由于新疆独特的区位优势,新疆红枣品质受到追捧,国内外出现热销新疆红枣的态势,红枣龙头加工企业纷纷向新疆集中,红枣形成了产销两旺。目前,红枣主要以制干初加工销售,红枣加工企业将半干红枣经过筛选、分级、哄干、包装后销售。
其中,红枣分级是红枣制干过程中的一个重要环节,红枣分级质量的好坏,尺寸的大小直接影响红枣的经济效益。
1.2 国内外研究现状及分析
国外公司较早开始对水果自动分级技术进行研究并将研究成果产品化,意大利、日本和美国是果品分级分选设备研究的倡导者,目前来看,欧洲果品分级分选设备的研究集中在果品分级生产线的研制;美国和亚洲的日本、韩国则是着重研究尖端的分级分选技术,比如核磁共振成像分级、内部品质检测分级,如成熟度分级等。我国对智能化程度较高的果品分选机的研制尚处于起步阶段,对水果品质检测及自动分级研究时间不长,国内目前能生产的水果分级设备基本还限于机械分级阶段,主要进行大小、重量的分级,自动分级设备基本还处于实验室研发阶段。我国水果质量检测中使用的水果品质自动检测生产线多为进口设备,由于引进设备操作较为复杂,设备成本较高,且这种进口设备是针对大农场生产所设计的,在我国小农户生产方式的农产品的检测中并不实用。
目前国内主要的红枣分级机构有以下几种:一是差速带式红枣分级机。差速带式红枣分级机,由差速带式红枣分级机构组成,包括机架、电机、喂料斗及其传动装置,其特征在于机架上至少设有两级的差速带式红枣分级装置,机架下方的电动机输出轴上设有传动轴,传动轴的前后两端均设有锥形齿轮,与其相啮合的锥形齿轮轴上均设有皮带轮,且前端的皮带轮直径比尾端的皮带轮直径大,两个皮带轮通过皮带分别与机架上方的两个直径相同的皮带轮相接,轴上间隔均布有与方轴连为一体的、和不连为一体的两种轴套,前后两个轴上的两种轴套相错而设,前后两个轴套间设有分级皮带,每根分级皮带的下方设有击打装置。与现有技术相比,本实用新型具有结构简单、操作方便、无卡枣现象、红枣破损率低的优点。缺点是效率低,分级不均,造价较高。二是重叠式筛笼红枣分级机。该红枣分级机,解决现有红枣分级机分级效果差、破损率较高以及结构复杂等问题,包括箱体,箱体一侧设有进料口,箱体内贯穿设置转动轴,转动轴上至少固定有两个互相套接且一端面呈阶梯状分布的筛笼,筛笼另一端面与环形圆板固定,筛笼上各筛条之间的间隙尺寸由内向外逐渐减小,其中内层筛笼一端与进料口相通,另一端与设置在箱体另一侧的一级出料口相通,每个筛
笼下方均设有出料口。本实用新型将多个筛笼呈重叠式且端面呈阶梯状安装,整体结构简单、造价低、效率高,可一次将红枣分成多个等级,分级均匀,在设备中的行程较短,在实际使用中效果显著,可广泛用于红枣产地的规模化加工。缺点是有卡枣现象,破损率较大。
针对上述两种红枣分级机存在的问题,课题提出一种对辊式红枣分级机,该机械可连续做业,各将红枣按企业要求分成多个级别。
2 系统总体方案的确定
2.1 系统方案的确定
辊式分级机主要有以下辊带式和对辊式。辊带式尺寸分级一般由分级滚轴和输送带组成。根据分级滚轴直径是否变化又可以分为等径辊带式尺寸分级机和变径辊带式尺寸分级,如下图:
图2-1 等径辊带式分级机原理图
1.输送带主带轮
2.待分级物料
3.分级隔板
对辊式尺寸分级机分级间隙的改变一般靠对辊之间的空间位置变化来来改变分级间隙分为以
下几种:
按对辊之间的相对角度变化分级:
a) b)
图2-2 按对辊角度变化分级原理图
1.待分物料
2.分级辊
按对辊之间的相对高度变化分级:
图2-3 按对辊相对高度变化分级原理图
1.定辊
2.浮动辊
3.待分物料
由于对辊式分级的结构简单,分级范围较广,对枣子的破坏比较小,所以本次设计采用对辊式分级,按照对辊之间的角度相对变化来分级。 2.2 结构特点及工作原理 2.2.1 结构特点
本设计吸收了当前的设计优势,主要由原动机、传动系、工作系、机架系四部分构成。原动机采用电动机带动,传动系选择V 带传动,齿轮传动,工作系由滚筒和刀片组成,其中工作系由圆形锥辊和卡位铁皮组成,机架系由底座、架身、进料斗、出料斗组成。此外采用全损耗系统用油进行润滑,橡胶密封。主运动轴、轴承、键、联轴器都采用标准件,易于更换。 2.2.2 工作原理
电动机运转,通过联轴器将动力传到V 带轮,通过V 带轮将发动机转速降低,经过减速的动力通过V 带将动力传到主运动轴,带动锥辊开始工作。在确认机器启动运转平稳后开始喂料,喂料要及时均匀,要观察入料口,如有堵塞及时清除。 工作原理简图(总体方案图)
图2-4 对辊式红枣分级机方案图
1—入料斗,2—辊子1,3—辊子2,4—齿轮,5—V 带,6—机架,
7—电动机,8—联轴器,9—出料斗
2.3 系统总体方案设计
组成:传动装置由电机、减速器、工作机组成。
确定传动方案:考虑到电机转速高,传动功率大,在工作中要承受轻微冲击等实际要求,故采用一级斜齿轮减速器,初步确定传动系统总体方案如图2。选择带传动和一级圆柱斜齿轮减速器。 传动装置的总效率a η:
83314.096.098.097.097.047654321=???==ηηηηηηηηα;
1η为联轴器的效率,2η为高速轴齿轮的效率, 3η为高速轴承的效率,4η为第二对轴承的效率,
5η为第三对轴承的效率,6 η为第四对轴承的效率,7η为V 带的效率(齿轮为9级精度,油脂润滑。因是薄壁防护罩,采用半开式效率计算)。
3 主要部件的设计计算及校核
3.1 电动机的选择
电动机所需工作功率为: kw P P w d 6.38331.0/3000/===αη
--w P 工作装置的功率;a η—总效率;
执行机构的转速n 为100~200r/min
经查表按推荐的传动比合理范围,带传动的传动比5~20=i ,圆柱齿轮减速器传动比
8~21=i ,则总传动比合理范围为40~4=αi ,电动机转速的可选范围为
m in /)8000~400()200~100()40~4(r n i n d =?=?=α。
根据容量和转速,由设计手册查出的电动机型号,因此有以下三种传动比选择方案,如下
表3-1 电动机型号
方案
电动机型号 额定功率
kw
同步转速
min r
满载转速
min r
电动机质量kg
参考价格 传动装置传动比 1 Y-112M -2 4 3000 2890 45 5.00 22.40 2 Y112M -4 4 1500 1440 43 3.48 20.42 3
Y132M 1-6
4
1000
960
73
2.22
13.61
下面的表格就是电动机的技术参数、性能以及外形尺寸的数据:
表3-2 电动机外形尺寸
图3-1 电动机主要外形安装尺寸
3.2 确定传动装置的总传动比和分配传动比 3.2.1 总传动比
中心高
外型尺寸
L ×(AC/2+AD )×HD
底脚安装尺寸A ×B 地脚螺栓孔直径K
轴伸尺寸D ×
E
装键部位尺寸
F ×GD
112
38×265×190
190×140
12
28×60
8
由选定的电动机转速m n 和工作装置主动轴转速w n ,可得传动装置总传动比为
15100/1500/===w m a n n i 。
3.2.2分配传动装置传动比
i i i a ?=0
式中10,i i 分别为带传动和减速器的传动比。
为使带传动外廓尺寸不致过大,初步取31=i ,则减速器传动比为53/15/1===i i i a 3.3 传动装置的运动和动力参数计算 3.3.1 各轴转速 min /15000r n =
m in /5003/1500/001r i n n === m in /1005/500/02r i n n === 3.3.2 各轴的输出功率kw P d 6.3=
kw p P d 42.398.097.06.3311=??=??=ηη
kw p P 02.396.097.098.097.042.3754212=????=????=ηηηη
3.3.3 因电动机轴的输出转矩m N n P T m d d ?=?
==92.221500
6
.395509550所以: m N i T T d ?=???=???=36.6598.097.0392.224201ηη m N i T T ?=???=???=3.30496.097.0536.6575112ηη
运动和动力参数结果如下表:
表3-3 运动和动力参数表
3.4 V 带及V 带轮的选择计算 3.
4.1 V 带的选择
因为小带轮(主动轮)的转速为500转/分,输出功率为3.42千瓦,根据设计要求,经查《机械设计基础》得到小带轮初选的基准直径为140mm 。初步确定选普通V 带B 型,基准长度d L 为1800mm 。
实际工作时,应对V 带的基本额定功率0
p 值加以修正。修正后既得实际工作条件下V 带所能传递
的功率,称为许用功率[
p ]:[
p ]=(
0p +0p ?)?k L
k
式中:
0p
?-功率增量。 ?k -包角修正系数。
L k -带长修正系数。
经查表02.00=?p ;95.0=?k ;95.0=L k 。
[]42.363.395.095.0)02.04(0>=??+=p 符合要求。 所以小带轮的基准直径因选择140mm 。 根数的确定
设P 为传动的额定功率(Km ),A K 为工作情况,则计算功率为:P K p A c =; 式中:A K --工作情况系数,查表得1.5。则:13.542.35.1=?=c p 轴 名 功率P/ KW 输出
转矩T /Nm 输出
转速r/min 电动机轴 1轴 2轴
3.6 3.42 3.02
22.92 65.36 304.3
1500 500 100
V 带的根数由式:[]()L
c
o c K K P p p p z ??+==
00p 计算确定,带入数据计算得41.1=z ;确定为两根。
3.4.2 带轮的设计计算
1)大小带轮直径的确定
由3.4.1可知小V 带轮的直径1d 为140mm ,设大带轮为2d ,由经验公式:
12id d =
带入数据计算得:
mm d 42014032=?= 由《机械设计基础》表13-9取mm d 4002= 2)中心距的确定
初步选定中心距:取0a =650mm ,符合)(2)(7.021021d d a d d +<<+,得带长:
()o
o a d d d d a L 4)(2
22
122
10-+
++
=π
()
o
o a d d d d a L 4)(2
22
12210-+
++
=π
()mm 2174650
4140400)400140(2
65022
=?-+
++
?=π
经查《机械设计基础》表8-2得B 型带基准长度d L =2240mm 。再由2
o d L L a a -+=计算实
际中心距: mm L L a a o d 7162
2174
224065020=-+=-+
= 综上所述,可以确定V 带选用普通V 带A 型,mm L d 2240=,中心距为716mm ;大带轮直径为400mm ,小带轮直径为140mm 。由于mm d 4002≥,所以采用轮辐式,小带轮可采用孔板
式。
3.5 传动轴的设计计算
3.5.1 主运动轴(从动轴)的设计
1)求主运动轴上的功率0P ,转速0n ,转矩0T 。
由上述可知kw P 02.3=,min /100r n =,m N T ?=3.304 2)求作用在从带轮上的力
已知低速带轮的基准圆直径为mm d 4002= 而初步知道:
圆周力:N d T F t 1521104002
.304223
2=??==
- 径向力:N F F o
o
n 6.57759
.16cos 20tan 1521cos tan =?===βατγ 轴向力:N F F t a 2.453298.01521tan =?==β
3)初步确定主运动轴的最小直径
先按课本初步估算轴的最小直径,选取轴的材料为45钢,调质处理,根据《机械设计基础》的公式14-2:
3
min n P C d c
≥
式中:C —由轴的材料和承载情况确定的常数; P —传递的功率; n —轴的转速。 带入数据:
mm n P C d c 5.23100
02.313533
min =?=≥ 轴的最小直径取24mm ,显然是安装在轴承上的直径,为了使所选的轴与轴承吻合,故需同时选
取轴承的型号。
4)根据轴向定位的要求确定轴的各段直径和长度 初步设计主运动轴(从动轴)如图:
图3-2 轴简图
1)如上图,ab 段为螺纹,用以安装橡胶辊,bc 段安装轴承,cd 段安装齿轮,ef 段安装另一轴承,fg 安装带轮,在左侧应钻螺纹孔,起轴向固定作。
2)初步选择滚动轴承 因轴承同时受有径向力和轴向力的作用,但轴向力相对较小,故选用单列深沟球轴承。参照工作要求并根据mm d ef 24=,由轴承产品目录中初步选取0基本游隙组标准精度级的单列深沟球轴承6005型,如表:
表3-4 轴承参数表
d
D B 2d
2D
轴承代号 17 35 10 19.4 32.6 6003 20 42 12 25 37 6004 25 47 12 30 42 6005 30
55
13 36
49
6006
3.5.2 主运动轴各轴段长度直径的确定
对于选取的单向深沟球轴承其尺寸为的mm mm mm B D d 124225??=??,故直径
mm
d mm mmd mmd mmd ef mmd d ab bc cd d
e fg 354050754525======
长度
mm l
fg
70=,mm l ef 50=,mm l de 10=,mm l cd 90=,mm l bc 40=mm l ab 120=考虑到
实际工作情况,将轴的总长380mm 。 3.5.3 求主动轴上载荷及校核
首先根据结构图作出轴的计算简图, 确定顶轴承的支点位置时,查《机械设计手册》得对于6005型的深沟球轴承,做为简支梁的轴的支承跨距.
由上述可知,圆周力:N F t 1521=,径向力:N F r 6.577=,轴向力:N F 2.435=α
mm L 175= mm K 125=
1)求垂直面的支承反力(图3-3 b )
N L d
cd F a L r F F v 10.211175
2602.45321756.577221=?-?=-=
N F v F r F v 5.36610.2116.57712=-=-= 2)求水平面的支承反力(图3-3c ) N N F F F t H H 5.7602
1521221===
= 3)F 力在支点产生的反力(图3-3d )
N N L K F F F 507175
125
7101=?=?=
N N F F F F F
1217)507710(12=+=+=
外力F 作用方向与带传动的布置有关,在尚未确定具体布置前,可按最不利情况考虑。 4)绘垂直面的弯矩图(3-3图b ) m N m N L F M V v ?=??=?=02.322175.05.36622α m N m N L F M V V
?=??=?=37.182
175.010.21121'
α
5)绘水平面的弯矩图(图3-3c)
m N m N L F M H aH ?=??=?
=5.662
175
.05.76021 6)F 力产生的弯矩图(图3-3d )
m N m N K F M F ?=??=?=5.177125.07102 截面F 产生的弯矩图为: N m N L F M F aF 9.482
193.050721=??=?
= 7)求合成弯矩图(图3-3e )
考虑到最不利的情况,把M aF 与2
2
aH av M M +直接相加。
m N m N M M M M aF aH aV a ?=?++=++=7.1229.4802.325.662222
m N m N M M M M aF aH aV a
?=?++=++=91.859.485.6675.18)()(2222''
m N M M F ?==5.17722
8)求轴传递的转矩(图3-3f )
m N d
cd F T t ?=?
=?=84.802
06.015212
9)求危险截面的当量弯矩(图3-3g )
从图可见,a-a 截面最危险,其当量弯矩为 ()22T M M a e α+=
取折合系数α=0.6,代入上式得
m N M e ?=?+=μ159)84.806.0(7.12222
10) 计算危险截面处轴的直径
轴材料为45号钢,调质处理,由表14—1查得σB =650 MP a ,由
表14-3查的许用应力[]b 1-σ=60 MP a ,则
[]
mm N M d b e
?=??=
≥
-8.2960
1.0101591.03
3
13
σ
考虑到键槽对轴的削弱,将d 值加大10%,故 8.322.291.1=?=d
粗取轴径为35,合适,安全。
3.6 键的选择
键主要用来实现轴和轴上零件之间的周向固定以传递转矩。键是标准件,分为平键、半圆键、契键和切向键。本设计采用A 型平键连接,它的两侧是工作面,上表面与轮毂槽底之间留有间隙。 3.6.1 键的强度校核
1)选择键联接的类型和尺寸
一般9精度的尺寸的齿轮没有定心精度要求,用平键比较好。 查《机械设计课程设计手册》表4-2取: 键宽 80=b 键高70=h 键长220=L 141=b 91=h 501=L
其中键O 安装在从动带轮上,键1齿轮轴上。 2)校核键联接的强度
查得 []MPa P 110=σ=110
工作长度 148-22000==-=b L l
3614-50111==-=b L l
3)键与轮毂键槽的接触高度
5.35.00==h K 5.45.01==h K
由公式得 []P 3
0003
098.317
822107.1921020
σσ<=????=?=h l d T p
[]P p d l h T σσ<=????=?=148
5014107.1921023
3333
13
两者都合适 取键标记为:
键0:8?22AGB/T1096-1979
3.7 联轴器的选择
本设计的联轴器的选择主要包括了两个联轴器的选择,第一个是电动机轴与箱体的输入主轴的联结,根据文献12中的表12-23Y 系列电动机的外型尺寸,本设计所选用的电动机的型号为Y112M-4,可知电动机的输出主轴的外伸部分的长度E 和直径D 分别是50和35。根据《机械设计手册》表8-2凸缘联轴器,最后确定电动机与箱体的输入轴间的联轴器选择为GYH3型。 3.8 齿轮的设计
已知载荷变化不大,传动比为:5=i 小齿轮转速为m in /5001r n = 传动功率kw P I 42.3=
3.8.1 决定传动形式,齿轮上的转矩,选择小齿轮的齿数 1)决定传动形式
5=i ,选择一级直齿圆柱齿轮传动。