塑料注塑模设计说明书
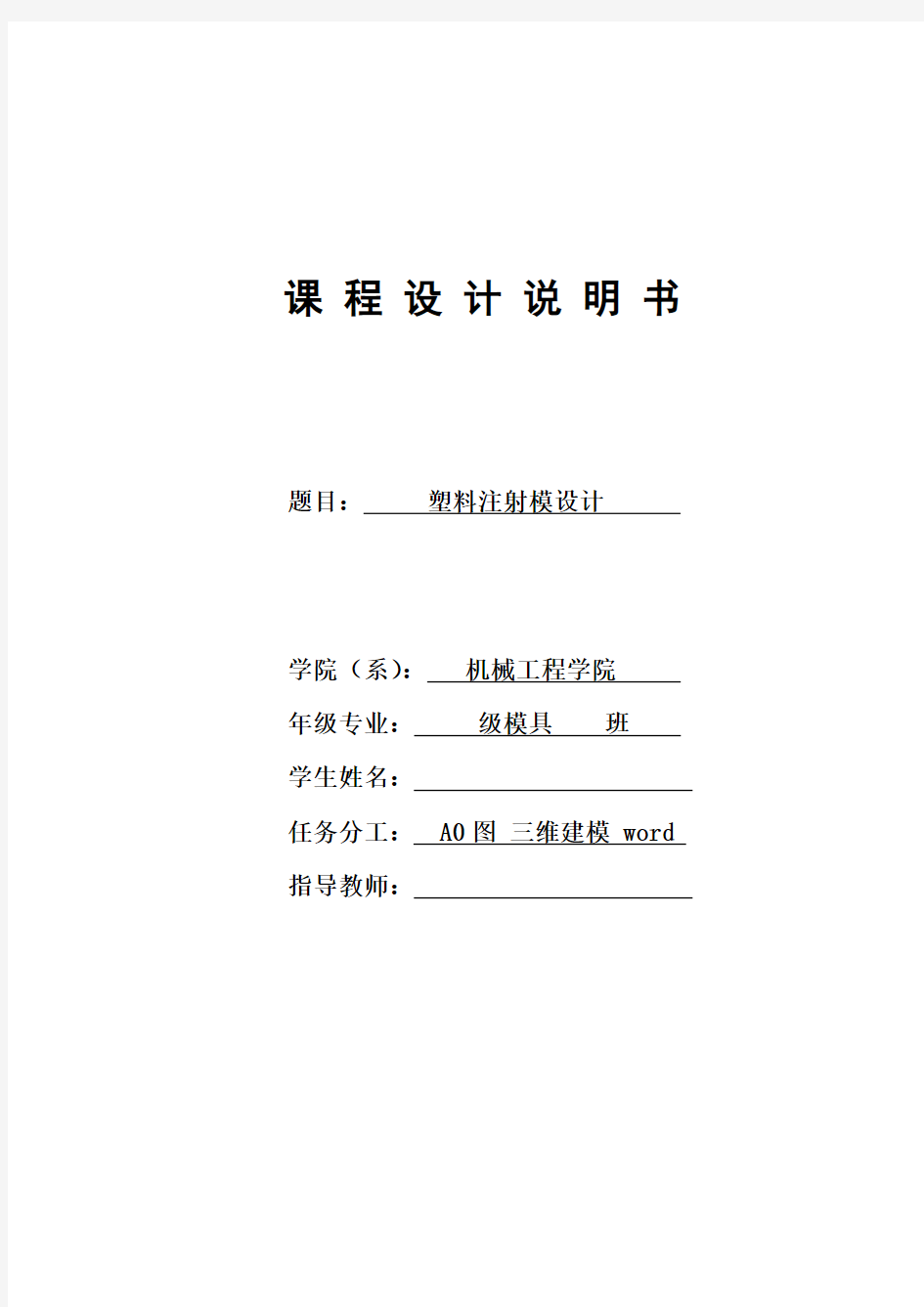

课程设计说明书题目:塑料注射模设计
学院(系):机械工程学院
年级专业:级模具班
学生姓名:
任务分工: A0图三维建模 word 指导教师:
目录
1 塑件分析 (4)
1.1 尺寸分析 (4)
1.1.1 外形尺寸 (4)
1.1.2 塑件圆角 (4)
1.1.3 脱模斜度 (4)
1.1.4 尺寸精度 (5)
1.2 成型性能分析 (5)
1.3 PC材料的成型工艺参数 (5)
2 拟定模具的结构形式 (6)
2.1 分型面位置的确定 (6)
2.2 型腔数量的确定 (7)
2.3 型腔排列形式的确定 (7)
3 注射机型号的确定和注射机相关参数的校核 (7)
3.1 注射机型号的确定 (7)
3.1.1 注射量的计算......................................... 8
3.1.2 浇注系统凝料体积的初步估算 (8)
3.1.3 选择注射机 (8)
3.2 注射机的相关参数的校核 (9)
3.2.1 注射压力校核 (9)
3.2.2 锁模力校核 (9)
4 浇注系统设计 (10)
4.1 主流道设计 (10)
4.2 分流道的设计 (11)
4.2.1 凝料体积 (12)
4.2.2 校核剪切速率 (12)
4.2.3分流道的表面粗糙度和脱模斜度 (13)
4.3 浇口的设计 (13)
4.3.1 浇口形式的选择 (14)
4.4 冷料穴的设计 (15)
5 成型零件的结构设计及计算 (15)
5.1 成型零件的结构设计 (15)
5.2 成型零件钢材选用 (16)
5.2.1 塑料模刚材的性能要求: (16)
5.2.2 凹模的技术要求: (16)
5.2.3 型芯的技术要求: (16)
5.3 成型零件工作尺寸的计算 (16)
5.3.1 型腔径向尺寸 (17)
5.3.2 型腔深度尺寸 (17)
5.3.3 型芯径向尺寸 (18)
5.3.4 型芯高度尺寸 (19)
5.4 成型零件尺寸及动模垫板厚度的计算 (19)
5.4.1 凹模侧壁厚度的计算 (19)
5.4.2 动模板厚度的计算 (19)
6 模架的确定 (19)
6.1 各模板尺寸的确定 (20)
6.2 模架各尺寸的校核 (21)
7 排气槽的设计 (21)
8 脱模推出机构的设计 (22)
8.1 推出方式的确定 (22)
8.2 脱模力的计算 (22)
9 加热系统的设计 (23)
10 冷却系统的设计 (23)
10.1 冷却介质 (23)
10.2 冷却系统的简单计算 (23)
10.3 凹模型腔与型芯冷却水道的设置 (25)
11 导向与定位机构的设计 (25)
12 总装图 (26)
13 参考文献
前言
随着中国当前的经济形势的日趋好转,在“实现中华民族的伟大复兴”口号的倡引下,中国的制造业也日趋蓬勃发展;而模具技术已成为衡量一个国家制造业水平的重要标志之一,模具工业能促进工业产品生产的发展和质量提高,并能获得极大的经济效益,因而引起了各国的高度重视和赞赏。在日本,模具被誉为“进入富裕的原动力”,德国则冠之为“金属加工业的帝王”,在罗马尼亚则更为直接:“模具就是黄金”。可见模具工业在国民经济中重要地位。我国对模具工业的发展也十分重视,早在1989年3月颁布的《关于当前国家产业政策要点的决定》中,就把模具技术的发展作为机械行业的首要任务。
近年来,塑料模具的产量和水平发展十分迅速,高效率、自动化、大型、长寿命、精密模具在模具产量中所战比例越来越大。注塑成型模具就是将塑料先加在注塑机的加热料筒内,塑料受热熔化后,在注塑机的螺杆或活塞的推动下,经过喷嘴和模具的浇注系统进入模具型腔内,塑料在其中固化成型。
本次课程设计的主要任务是注塑模具的设计。也就是设计一副注塑模具来生产塑件产品,以实现自动化提高产量。针对塑件的具体结构,通过此次设计,使我对单分型面侧浇口模具的设计有了较深的认识。同时,在设计过程中,通过查阅大量资料、手册、标准、期刊等,结合教材上的知识也对注塑模具的组成结构(成型零部件、浇注系统、导向部分、推出机构、排气系统、模温调节系统)有了系统的认识,拓宽了视野,丰富了知识,为将来独立完成模具设计积累了一定的经验。
摘要:注射模进行了实体及工艺分析,并按照其要求选定材料,分析材料的特性及工艺参数。选择了注射机的类型并对其进行了校核。对成型零部件进行了结构设计和工作尺寸以及动模垫板厚度的计算。最后,完成了模具装配图和三维立体图。
1塑件分析
1.1尺寸分析
1.1.1外形尺寸
塑件的壁厚应使各部分均匀,避免太薄,否则会应引起收缩不均匀使塑件变形或产生气泡,凹陷等成型问题。塑件壁厚一般在1~6mm之间。而最常用的数值是2~3mm。大型塑件的壁厚也有比6mm更大的,这都随塑料类型及塑件的大小而定。壁厚还与流程有密切相关。本塑件的壁厚均匀,为2mm。又由于塑件外形尺寸不大,塑件熔体流程不太长,适合于注射成型。如图所示。
材料:PC
1.1.2塑件圆角
在塑件设计过程中,为了避免应力集中,提高塑件强度,改善塑件的流动情况及便于脱模,在塑件的各面或内部连接处,应采用圆弧过渡。另外,塑件上的圆角对于模具制造和机械加工及提高模具强度,也是有利的。本塑件中未注圆角为R1-R2。
1.1.3脱模斜度
为保证塑件很好的脱模,塑件应有一定的脱模斜度,最小脱模斜度与
塑料性能、收缩率的大小、塑件的几何形状有关。材料质脆、硬的,脱模斜度要求大。本塑件内表面外表面都有脱模斜度,参考表2-10选择该塑件型芯和凸模的统一脱模斜度为1°。
1.1.4尺寸精度
依据材料类型查表2-3,得出塑件各尺寸为MT3。
1.2成型性能分析
该塑件所用材料为聚碳酸酯(PC)
1.无定型塑料,热稳定性好,成形温度范围宽,超过330C才呈现严重分解,分解时产生无毒.无腐蚀性气体。
2.吸湿性小,但水敏性强,含水量不得超过0.2%,加工前必须干燥处理,否则会出现银丝、气泡及强度显著下降现象。
3.流动性差,溢边值为0.06mm左右,流动性对温度变化敏感,冷却速度快。
4.成形收缩率小,如成形条件适当,塑件尺寸可控制在一定公差范围内,塑件精度高。
5.可能发生应力开裂,易产生应力集中,应严格控制成形条件,而喷嘴应加热,喷嘴宜用敞开式延伸喷嘴。
6.粘度高,但对剪切作用敏感。浇注系统宜设冷料穴。进料口附近有残余应力,必要时可采用调节时进料口,模温一般取70C~120C为宜,应注意顶出均匀,模具应用耐磨钢,并淬火。
7.料筒温度对控制塑料质量是一个重要因素,料温低时会造成缺料,表面无光泽,温度高时易溢边,出现银丝暗条,塑件变色有泡。注射压力宜高不宜低。
8.模温对塑件质量影响很大,薄壁塑件宜取80C~100C,厚壁塑件宜取80C~120C;模温低则收缩率.伸长率.冲击韧性打,抗弯.抗压.抗拉强度低。模温超过120C则塑件冷却变慢,易变形粘模,脱模困难,成型周期长。
9.成性收缩率为0.6%。
1.3PC材料的成型工艺参数
工艺参数规格工艺参数规格
干燥温度(℃):110-120
成型时间(s)
注射时间1-5 时间(h): >24 高压时间20-90
料筒温度(℃)后段210-240 冷却时间20-90 中段230-280 总周期50-130 前段240-285 螺杆转速(r/min) 25-40
喷嘴温度(℃) 240-250
后处理方法红外线灯烘箱
模具温度(℃) 70-110 温度(℃) 70 注射压力
(Mpa)
70-130 时间(h) 1
注射机类型螺杆式喷嘴结构直通式
2拟定模具的结构形式
2.1分型面位置的确定
塑料在模具型腔凝固形成塑件,为了将塑件取出来,必须将模具型腔打开,也就是必须将模具分成两部分,即定模和动模两大部分。定模和动模相接触的面称分型面。通常有以下原则:
(1)分型面的选择有利于脱模:分型面应取在塑件尺寸的最大处。而且应使塑件流在动模部分,由于推出机构通常设置在动模的一侧,将型芯设置在动模部分,塑件冷却收缩后包紧型芯,使塑件留在动模,这样有利脱模。如果塑件的壁厚较大,内孔较小或者有嵌件时,为了使塑件留在动模,一般应将凹模也设在动模一侧。拔模斜度小或塑件较高时,为了便于脱模,可将分型面选在塑件中间的部位,但此塑件外形有分型的痕迹。
(2)分型面的选择应有利于保证塑件的外观质量和精度要求。
(3)分型面的选择应有利于成型零件的加工制造。
(4)分型面应有利于侧向抽芯,但是此模具无须侧向抽芯,此点可以不必考虑。
不论塑件的结构如何以及采用何种设计方法,都必须首先确定分型面,因为模具结构很大程度上取决于分型面的选择。在选择分型面时,根据分型面的选择原则,考虑不影响塑件的外观质量、便于清除毛刺及飞边、有利于排除模具型腔内的气体、分模后塑件留在动模一侧及便于取出塑件等因素,通过对塑件结构形式的分析,分型面应选在端面截面积最大且有利于开模取出塑料的底平面上,如图所示。
2.2型腔数量的确定
该塑件可采用一模多腔的结构形式。同时,考虑到塑件尺寸、模具结构尺寸的大小关系,以及制造费用和各种成本等费用,初步定为一模两腔的结构形式。
2.3型腔排列形式的确定
多型腔模具尽可能采用平衡式排列布置,且要力求紧凑,并与浇口开设的部位对称。由于该设计选择的是一模两腔,型腔平衡布置在型腔板两侧,以方便浇口排列和模具的平衡。
3注射机型号的确定和注射机相关参数的校核
3.1注射机型号的确定
3.1.1 注射量的计算
塑件体积: 3塑
cm 92.15=V 塑件质量: g 104.19g 2.192.15m 塑塑=?==V ρ 式中,ρ取1.2g/cm3。
3.1.2 浇注系统凝料体积的初步估算
浇注系统的凝料在设计之前是不能确定准确的数值,但是可以根据经验按照塑件体积的0.2~1倍来估算。由于本次采取流道简单并且较短,因此浇注系统的凝料按塑件体积的0.5倍来估算,故一次注入模具型腔塑料熔体的总体积(即浇注系统的凝料和2个塑件体积之和)为
()33塑总cm 76.47cm 25.192.1525.01=??=?+=V V
3.1.3 选择注射机
根据第二步计算得出一次注入模具型腔的塑料总质量3塑cm 76.47=V ,
则有3cm 23.687.0/76.47==V 。根据以上的计算,初步选定公称注射量为3104cm ,注射机型号为XS-ZY-125,其主要技术参数见下表: 理论注射容/3cm 104
模板最大行程/mm 300 螺杆柱塞直径/mm 30
最大模板厚度/mm 300 注射压力/MPa 150
最小模板厚度/mm 200 注射行程/mm 160
合模形式 液压—机械 注射时间/s 1.8
定位圈尺寸/mm 100 螺杆转/-1min r 10-104
喷嘴球半径/mm 12 锁模力/kN
900 喷嘴孔半径/mm 4
3.2 注射机的相关参数的校核
3.2.1 注射压力校核
查表可知,所需注射压力为70~130MPa ,这里取
0=100p MPa ,该注射机的公称注射压力
=150p MPa 公,注射压力安全系数1=1.25~1.4k ,这里取1=1.3k ,则: 10=1.3100=130k p p ?公<,所以,注射机注射压力合格。
3.2.2 锁模力校核
塑件在分型面上的投影面积塑A ,则2塑mm 74.2640=A
浇注系统在分型面上的投影面积浇A ,即流道凝料(包括浇口)在分型面上的投影面积浇A 的数值,可以按照多型腔模的统计分析来确定。浇A 是每个塑件在分型面上的投影面积塑A 的0.2~0.5倍。由于本例流道设计简单,分流道相对较长,因此流道凝料投影面积可以适当取小一些。这里取塑浇A A *5.0=。
塑件和浇注系统在分型面上总的投影面积A 总,则
()22浇塑总mm 7922mm 26415.12n =??=+=A A A
模具型腔内的胀型力F 胀,则
KN
N A F 66.237307922p 模总胀=?== 式中,模p 是型腔的平均计算压力值,模p 是模具型腔内的压力,通
常取注射压力的20%~40%,大致范围为25~40MPa 。对于粘度较大的精度较高的塑料制品应取较大值。
模p 应取30MPa 。