MatLab在机械零件可靠性设计中的应用
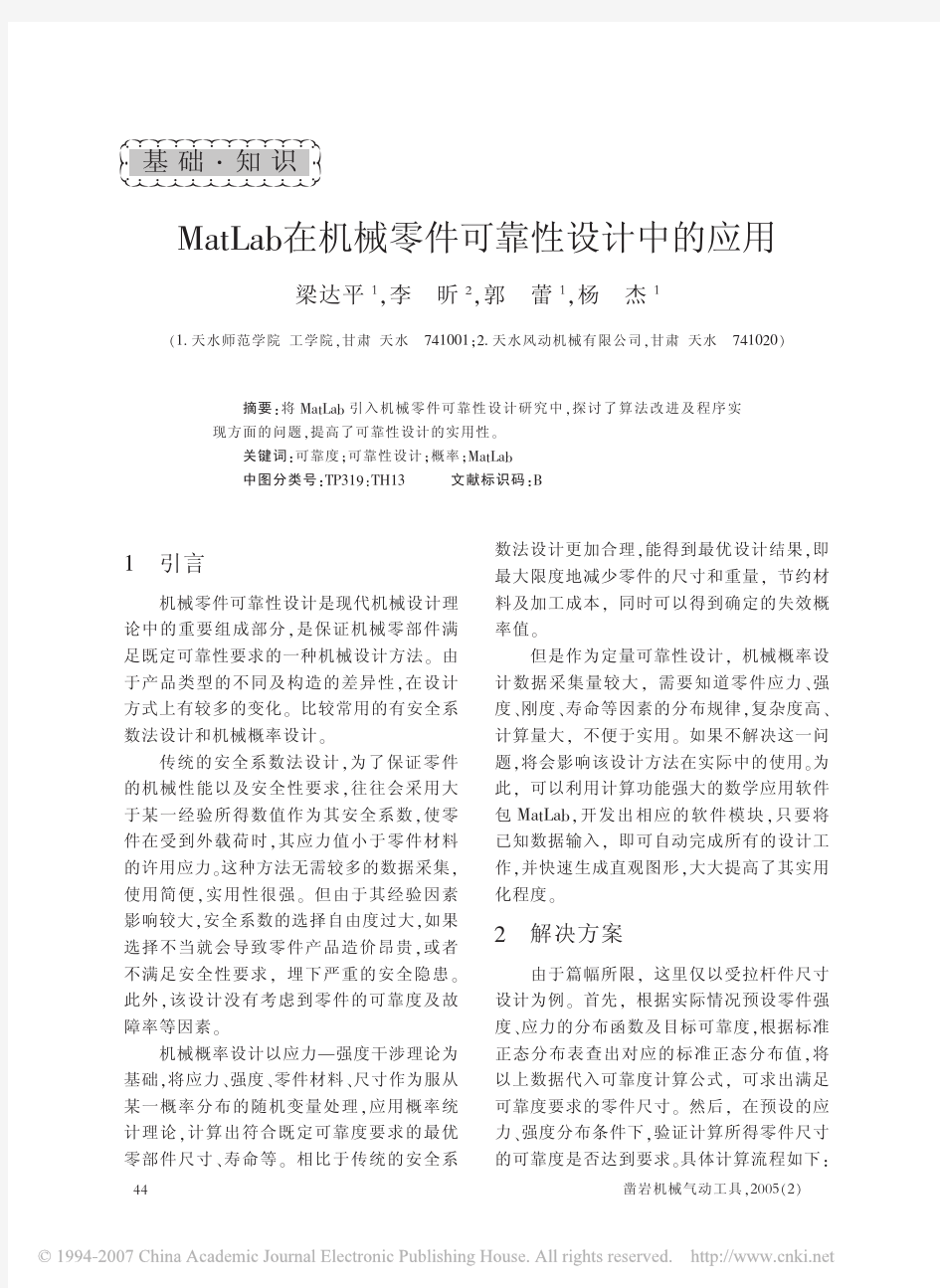

装配结构工艺性分析
一、分析研究产品的零件图样和装配图样 在编制零件机械加工工艺规程前,首先应研究零件的工作图样和产品装配图样,熟悉该产品的用途、性能及工作条件,明确该零件在产品中的位置和作用;了解并研究各 项技术条件制订的依据,找出其主要技术要求和技术关键,以便在拟订工艺规程时采用适当的措施加以保证。 工艺分析的目的,一是审查零件的结构形状及尺寸精度、相互位置精度、表面粗糙度、材料及热处理等的技术要求是否合理,是否便于加工和装配;二是通过工艺分析,对零件的工艺要求有进一步的了解,以便制订出合理的工艺规程。 如图3-8 所示的汽车钢板弹簧吊耳,使用时,钢板弹簧与吊耳两侧面是不接触的,所以吊耳内侧的粗糙度可由原来的设计要求R a3.2 μm 建议改为R a12.5 μ m. 。这样在铣削时可只用粗铣不用精铣,减少
铣削时间。 再如图3-9 所示的方头销,其头部要求淬火硬度55~60HRC ,所选用的材料为T 8A ,该零件上有一孔φ2H7 要求在装配时配作。由于零件长度只有15mm ,方头部长度仅有4mm ,如用T 8A 材料局部淬火,势必全长均被淬硬,配作时,φ 2H7 孔无法加工。若建议材料改用20Cr 进行渗碳淬火,便能解决问题。 二、结构工艺性分析 零件的结构工艺性是指所设计的零件在满足使用要求的前提下,制造的可行性和经济性。下面将从零件的机械加工和装配两个方面,对零件的结构工艺性进行分析。 (一)机械加工对零件结构的要求 1 .便于装夹零件的结构应便于加工时的定位和夹紧,装夹次数要少。图3 -10a 所示零件,拟用顶尖和鸡心夹头装夹,但该结构不便于装夹。若改为图b 结构,则可以方便地装置夹头。 2 .便于加工零件的结构应尽量采用标准化数值,以便使用标准化刀具和量具。同时还注意退刀和进刀,易于保证加工精度要求,减少加工面积及难加工表面等。表3-8b 所示为便于加工的零件结构示例。
机械零件结构工艺性分析与工艺路线的拟定
目录 一、零件结构工艺性分析2 1. 零件的技术要求2 2.确定堵头结合件的生产类型3 二、毛坯的选择4 1.选择毛坯4 2.确定毛坯的尺寸公差4 三、定位基准的选择6 1.精基准的选择6 2.粗基准的选择6 四、工艺路线的拟定7 1.各表面加工方法的选择7 2.加工阶段的划分8 3.加工顺序的安排8 4.具体技术方案的确定9 五、工序内容的拟定10 1.工序的尺寸和公差的确定10 2.机床、刀具、夹具及量具的选择12 3.切削用量的选择及工序时间计算12 六、设计心得35 七、参考文献36
一、零件结构工艺性分析 1.零件的技术要求 1.堵头结合件由喂入辊轴和堵头焊接在一起。其中喂入辊 轴:材料为45钢。堵头:材料为Q235-A。且焊缝不得有夹渣、气孔及裂纹等缺陷。 2.零件的技术要求表:
2. 确定堵头结合件的生产类型 根据设计题目年产量为10万件,因此该左堵头结合件的生产类型为大批量生产。
二、毛坯的选择 1.选择毛坯 由于该堵头结合件在工作过程中要承受冲击载荷,为增强其的强度和冲击韧度,堵头选用锻件,材料为Q235-A,因其为大批大量生产,故采用模锻。喂入辊轴由于尺寸落差不大选用棒料,材料为45钢。 2.确定毛坯的尺寸公差 喂入辊轴: 根据轴类零件采用精轧圆棒料时毛坯直径选择可通过零件的长度和最大半径之比查的毛坯直径 206 L8.24 == R25 查表得毛坯直径为:φ55 根据其长度和直径查得端面加工余量为2。故其长度为206+2+2=210mm
堵头: 1.公差等级: 由于堵头结合件用一般模锻工艺能够达到技术要求,确定该零件的公差等级为普通级。 2.重量: 锻件重量的估算按下列程序进行: 零件图基本尺寸-估计机械加工余量-绘制锻件图-估算锻件重量。并按此重量查表确定公差和机械加工余量 据粗略估计锻件质量: 11.6f Kg M = 3.形状复杂系数: 锻件外廓包容体重量按公式:2N d h 4 M π ρ= g g 计算 293 186.5101104 7.851021.65Kg N M π -= ?????= 形状复杂系数: f 11.6 0.5421.6M S M N === 故形状复杂系数为S2(一般)级。 4.锻件材质系数: 由于该堵头材料为Q235-A 所含碳元素的质量分数分别为C=0.14%—0.22%,小于0.65% 所含合金元素的质量分数分别为Si 0.3%≤、S 0.05%≤、P 0.045%≤故合金元素总的质量分数为0.3%0.05%0.045%0.395%3%++≤<%。故该锻件的材质系数为M1级。 5.锻件尺寸公差 根据锻件材质系数和形状复杂系数查得锻件尺寸公差为 ( 2.41.2+-) 。 6.锻件分模线形状: 根据该堵头的形装特点,选择零件轴向方向的对称平面为分模面,属于平直分模线。
网络可靠性设计
网络可靠性设计
目录 1.1 网络可靠性设计 (2) 1.1.1 网络解决方案可靠性的设计原则 (3) 1.1.2 网络可靠性的设计方法实例 (4) 1.1.3 网络可靠性设计总结 (9)
1.1网络可靠性设计 可靠性是指:设备在规定的条件下、在规定的时间内完成规定的功能的能力。对于网络系统的可靠性,除了耐久性外,还有容错性和可维护性方面的内容。 1)耐久性。是指设备运行的无故障性或寿命,专业名称叫MTBF(Mean Time Between Failure),即平均无故障时间,它是描述整个系统可靠性的重要指标。对于一个网络系统来说,MTBF是指整个网络的各组件(链路、节点)不间断无故障连续运行的平均时间。 2)容错性。专业名称叫MTTR(Mean Time to Repair),即系统平均恢复时间,是描述整个系统容错能力的指标。对于一个网络系统来说,MTTR是指当网络中的组件出现故障时,网络从故障状态恢复到正常状态所需的平均时间。 3)可维护性。在系统发生故障后,能够很快地定位问题并通过维护排除故障,这属于事后维护;根据系统告警提前发现问题(如CPU使用率过高,端口流量异常等),通过更换设备或调整网络结构来规避可能出现的故障,这属于预防维护。可维护性需要管理人员来实施,体现了管理的水平,也反映了系统可靠性的高低。
表示系统可靠性的公式为: MTBF / ( MTBF + MTTR ) * 100%。 从公式或以看出,提高MTBF或降低MTTR都可以提高网络可靠性。造成网络不可用的因素包括:设备软硬件故障、设备间链路故障、用户误操作、网络拥塞等。针对这些因素采取措施,使网络尽量不出故障,提高网络MTBF指标,从而提升整网的可靠性水平。 然而,网络中的故障总是不可避免的,所以设计和部署从故障中快速恢复的技术、缩小MTTR指标,同样是提升网络可靠性水平的手段。 在网络架构的设计中,充分保证整网运行的可靠性是基本原则之一。网络系统可靠性设计的核心思想则是,通过合理的组网结构设计和可靠性特性应用,保证网络系统具备有效备份、自动检测和快速恢复机制,同时关注不同类型网络的适应成本。 构建可靠的网络,需要从耐久性、容错性以及可维护性三个方面进行网络规划设计。而网络的规划设计是个系统工程,不同的设计方案的可靠性性效果不尽相同,这就需要以科学的方法进行设计,构建符合需要的可靠性网络。 1.1.1网络解决方案可靠性的设计原则 不同的网络,其可靠性的设计目标是不同的。网络解决方案的可靠性需要根据实际需求进行设计。高可靠性的网络不但涉及到网络架构、设备选型、协议选择、业务规划等技术层面的问题,还受用户现有网络状况、网络投资预算、用户管理水平等影响,因此在规划可靠性网络时需要因地制宜,综合考虑各方面的影响因素。
失效分析思路_张峥
理化检验-物理分册PTCA(PART:A PH YS.T EST.)2005年第41卷3专题讲座 失效分析思路 FAILURE ANA LYSIS M ETH ODOLOGY 张峥 (北京航空航天大学材料学院,北京100083) 中图分类号:T B303文献标识码:E文章编号:1001-4012(2005)03-0158-04 失效分析在生产建设中极其重要,失效分析的限期往往要求很短,分析结论要正确无误,改进措施要切实可行。导致零部件或系统失效的因素往往很多,加之零部件相互间的受力情况很复杂,如果再考虑外界条件的影响,这就使失效分析的任务更加繁重。此外,大多数失效分析的关键性试样十分有限,只容许一次取样、一次观察和测量。在分析程序上走错一步,可能导致整个分析的失败。由此可见,如果分析之前没有一条正确的分析思路,要能如期得出正确的结论几乎是不可能的。 有了正确的分析思路,才能制定正确的分析程序。大的事故需要很多分析人员按照分工同时进行,做到有条不紊,不走弯路,不浪费测试费用。所以从经济角度也要求有正确的分析思路。 1失效分析思路的内涵 世界上任何事物都是可以被认识的,没有不可以认识的东西,只存在尚未能够认识的东西,机械失效也不例外。实际上失效总有一个或长或短的变化发展过程,机械的失效过程实质上是材料的累积损伤过程,即材料发生物理的和化学的变化。而整个过程的演变是有条件的、有规律的,也就是说有原因的。因此,机械失效的客观规律性是整个失效分析的理论基础,也是失效分析思路的理论依据。 失效分析思路是指导失效分析全过程的思维路线,是在思想中以机械失效的规律(即宏观表象特征和微观过程机理)为理论依据,把通过调查、观察和实验获得的失效信息(失效对象、失效现象、失效环 收稿日期:2005-02-07 作者简介:张峥(1965-),男,教授,博士生导师。境统称为失效信息)分别加以考察,然后有机结合起来作为一个统一整体综合考察,以获取的客观事实为证据,全面应用推理的方法,来判断失效事件的失效模式,并推断失效原因。因此,失效分析思路在整个失效分析过程中一脉相承、前后呼应,自成思考体系,把失效分析的指导思路、推理方法、程序、步骤、技巧有机地融为一体,从而达到失效分析的根本目的。 在科学的分析思路指导下,才能制定出正确的分析程序;机械的失效往往是多种原因造成的,即一果多因,常常需要正确的失效分析思路的指导;对于复杂的机械失效,涉及面广,任务艰巨,更需要正确的失效分析思路,以最小代价来获取较科学合理的分析结论。总之,掌握并运用正确的分析思路,才可能对失效事件有本质的认识,减少失效分析工作中的盲目性、片面性和主观随意性,大大提高工作的效率和质量。因此,失效分析思路不仅是失效分析学科的重要组成部分,而且是失效分析的灵魂。 失效分析是从结果求原因的逆向认识失效本质的过程,结果和原因具有双重性,因此,失效分析可以从原因入手,也可以从结果入手,也可以从失效的某个过程入手,如/顺藤摸瓜0,即以失效过程中间状态的现象为原因,推断过程进一步发展的结果,直至过程的终点结果;/顺藤找根0,即以失效过程中间状态的现象为结果,推断该过程退一步的原因,直至过程起始状态的直接原因;/顺瓜摸藤0,即从过程中的终点结果出发,不断由过程的结果推断其原因;/顺根摸藤0,即从过程起始状态的原因出发,不断由过程的原因推断其结果。再如/顺瓜摸藤+顺藤找根0 /顺根摸藤+顺藤摸瓜0/顺藤摸瓜+顺藤找根0等。 # 158 #
零件的工艺性分析
零件的工艺性分析 一、分析研究产品的零件图样和装配图样在编制零件机械加工工艺规程前,首先应研究零件的工作图样和产品装配图样,熟悉该产品的用途、性能及工作条件,明确该零件在产品中的位置和作用;了解并研究各项技术条件制订的依据,找出其主要技术要求和技术关键,以便在拟订工艺规程时采用适当的措施加以保证。工艺分析的目的,一是审查零件的结构形状及尺寸精度、相互位置精度、表面粗糙度、材料及热处理等的技术要求是否合理,是否便于加工和装配;二是通过工艺分析,对零件的工艺要求有进一步的了解,以便制订出合理的工艺规程。 如图3-8 所示的汽车钢板弹簧吊耳,使用时,钢板弹簧与吊耳两侧面是不接触的,所以吊耳内侧的粗糙度可由原来的设计要求R a3.2 μ m 建议改为R a12.5 μ m. 。这样在铣削时可只用粗铣不用精铣,减少铣削时间。 再如图3-9 所示的方头销,其头部要求淬火硬度55~60HRC ,所选用的材料为T 8A ,该零件上有一孔φ 2H7 要求在装配时配作。由于零件长度只有15mm ,方头部长度仅有4mm ,如用T 8A 材料局部淬火,势必全长均被淬硬,配作时,φ 2H7 孔无法加工。若建议材料改用20Cr
进行渗碳淬火,便能解决问题。 二、结构工艺性分析零件的结构工艺性是指所设 计的零件在满足使用要求的前提下,制造的可行性和经济性。下面将从零件的机械加工和装配两个方面,对零件的结构工艺性进行分析。(一)机械加工对零件结构的要求 1 .便于装夹零件的结构应便于加工时的定位和夹紧,装 夹次数要少。图3 -10a 所示零件,拟用顶尖和鸡心夹头装夹,但该结构不便于装夹。若改为图b 结构,则可以方便 地装置夹头。 2 .便于加工零件的结构应尽量采用标准化数值,以便使用标准化刀具和量具。同时还注意退刀和进刀,易于保证加工精度要求,减少加工面积及难加工表面等。表3-8b 所示为便于加工的零件结构示例。 3 .便于数控机床加工被加工零件的数控工艺性 问题涉及面很广,下面结合编程的可能性与方便性来作工艺性分析。 编程方便与否常常是衡量数控工艺性好坏的一个 指标。例如图3-11 所示某零件经过抽象的尺寸标注方法,若用APT 语言编写该零件的源程序,要用几何定义语句描
可靠性工程论文
学校代码:11517 学号:20121110**** 《可靠性工程技术》 课程论文 题目机械产品可靠性设计分析 学生姓名** 专业班级工业工程1242 学号201211104231 系(部)管理工程学院 指导教师(职称)***(教授) 完成时间 2015年5月19日 目录
机械产品可靠性设计分析 摘要................................................... I Abstract ................................................. I I 1可靠性设计的基本概念 (1) 1.1 可靠性设计的定义 (1) 2 可靠性设计的基本原理 (1) 3 可靠性设计的基本方法 (2) 3.1 产品可靠性设计采取的措施 (2) 4 应用实例:基于虚拟样机的机械产品可靠性设计分析 (3) 4.1 机械产品可靠性设计分析方法 (3) 4.2 基于概率虚拟样机的可靠性设计分析流程 (5) 4.3 基于可靠性的机械产品参数设计 (9) 5 结论 (10) 参考文献 (11)
机械产品可靠性设计分析 摘要 机械产品可靠性设计是解决机械可靠性设计的重大课题。本文研究的目的是在总结归纳工程经验的基础上,研究目前机械可靠性设计中突出的技术问题,为日后工作中遇到的机械产品可靠性设计进行分析,指导研究型号可靠性工作,提供实用方法和技术支持。本文研究的主要内容有对可靠性设计的基本概述,可靠性设计的基本原理和基本方法,可靠性分析的应用实例等几个方面。采用实例对机械可靠性问题进行研究,并将研究结果运用到可靠性工程中解决实际问题。 关键词:机械设计;可靠性;可靠性设计
机械零件的失效分析-学习领悟
机械零件的失效分析 失效:零件或部件失去应有的功效零件在工作过程中最终都要发生失效。所谓失效是指:①零件完全破坏,不能继续工作;②严重损伤,继续工作很不安全;③虽能安全工作,但已不能满意地起到预定的作用。只要发生上述三种情况中的任何一种,都认为零件已经失效。一般称呼失效大多是特指零件的早期失效,即未达到预期的效果或寿命,提前出现失效的过程。 失效分析:探讨零件失效的方式和原因,并提出相应的改进措施。根据失效分析的结果,改进对零件的设计、选材、加工和使用,提高零部件的使用寿命,避免恶性事故的发生,带来相应的经济效益和社会效益。 一、零件的失效形式 失效形式分3种基本类型:变形、断裂和表面损伤。 1、变形失效与选材(机件在正常工作过程中由于变形过大导致失效) ①弹性变形失效(由于发生过大的弹性变形而造成的零件失效) 弹性变形的大小取决于零件的几何尺寸及材料的弹性模量。金刚石与陶瓷的弹性模量最高,其次是难溶金属、钢铁,有色金属则较低,有机高分子材料的弹性模量最低。因此,作为结构件,从刚度及经济角度看,选择钢铁是比较合适。 ②塑性变形失效(零件由于发生过大的塑性变形而不能继续工作的失效) 塑性变形失效是零件中的工作应力超过材料的屈服迁都的结果。一般陶瓷材料的屈服强度很高,但脆性非常大,因此,不能用来制造高强度结构件。有机高分子材料的强度很低,最高强度的塑料也不超过铝合金。因此,目前用作高强度结构的主要材料还是钢铁。 2、断裂失效 ①塑性断裂 零件在受到外载荷作用时,某一截面上的应力超过了材料的屈服强度,产生很大的塑性变形后发生的断裂; ②脆性断裂 脆性断裂发生时,事先不产生明显的塑性变形,承受的工作应力通常远低于材料的屈服强度,所以又称为低应力脆断; ③疲劳断裂 在低于材料屈服强度的交变应力反复作用下发生的断裂称为疲劳断裂; ④蠕变断裂 在应力不变的情况下,变形量随时间的延长而增加,最后由于变形过大或断裂而导致的失效; 3、表面损伤 ①磨损失效 磨损主要是在机械力的作用下,相对运动的接触表面的材料以细屑形式逐渐磨耗,而使零件尺寸不断变小的一种失效方式。磨损可能是被硬质点切削下来,也可能是在大的压力下焊合撕开,所以材料表面的硬度愈高,抵抗磨损的能力愈强。 磨粒磨损:相对运动的零件表面间嵌入硬质颗粒而造成的磨损 粘着磨损:两个相对运动零件表面的微观凸起发生粘合而撕裂 ②表面疲劳(在交变接触应力作用下,使机件表面产生点蚀而发生磨损)
机械设计习题及答案
机械设计习题及答案 第一篇总论 第一章绪论 一.分析与思考题 1-1 机器的基本组成要素是什么? 1-2 什么是零件?什么是构件?什么是部件?试各举三个实例。 1-3 什么是通用零件?什么是专用零件?试各举三个实例。 第二章机械设计总论 一.选择题 2-1 机械设计课程研究的内容只限于_______。 (1) 专用零件的部件 (2) 在高速,高压,环境温度过高或过低等特殊条件下工作的以及尺寸特大或特小的通用零件和部件 (3) 在普通工作条件下工作的一般参数的通用零件和部件 (4) 标准化的零件和部件 2-2 下列8种机械零件:涡轮的叶片,飞机的螺旋桨,往复式内燃机的曲轴,拖拉机发动机的气门弹簧,起重机的起重吊钩,火车车轮,自行车的链条,纺织机的纱锭。其中有_____是专用零件。 (1) 3种 (2) 4种 (3) 5种 (4) 6种 2-3变应力特性可用σmax,σmin,σm, σa, r 等五个参数中的任意_____来描述。 (1) 一个 (2) 两个 (3) 三个 (4) 四个 2-4 零件的工作安全系数为____。 (1) 零件的极限应力比许用应力 (2) 零件的极限应力比零件的工作应力 (3) 零件的工作应力比许用应力 (4) 零件的工作应力比零件的极限应力 2-5 在进行疲劳强度计算时,其极限应力应为材料的____。 (1) 屈服点 (2) 疲劳极限 (3) 强度极限 (4) 弹性极限 二.分析与思考题 2-1 一台完整2-3 机械零件主要有哪些失效形式?常用的计算准则主要有哪些? 2-2 机械零件主要有哪些失效形式?常用的计算准则主要有哪些? 2-3 什么是零件的强度要求?强度条件是如何表示的?如何提高零件的强度? 2-4 什么是零件的刚度要求?刚度条件是如何表示的?提高零件刚度的措施有哪些? 2-5 机械零件设计中选择材料的原则是什么? 2-6 指出下列材料的种类,并说明代号中符号及数字的含义:HTl50,ZG230-450,2-7 机械的现代设计方法与传统设计方法有哪些主要区别? 第三章机械零件的强度 一.选择题 3-1 零件的截面形状一定,如绝对尺寸(横截面尺寸)增大,疲劳强度将随之_____。 (1) 增高 (2) 不变 (3) 降低 3-2 零件的形状,尺寸,结构相同时,磨削加工的零件与精车加工相比,其疲劳强度______。 (1) 较高 (2) 较低 (3) 相同
典型零件的机械加工工艺分析
第4章典型零件的机械加工工艺分析 本章要点 本章介绍典型零件的机械加工工艺规程制订过程及分析,主要内容如下: 1.介绍机械加工工艺规程制订的原则与步骤。 2.以轴类、箱体类、拨动杆零件为例,分析零件机械加工工艺规程制订的全过程。 本章要求:通过典型零件机械加工工艺规程制订的分析,能够掌握机械加工工艺规程制订的原则和方法,能制订给定零件的机械加工工艺规程。 §4.1 机械加工工艺规程的制订原则与步骤§4.1.1机械加工工艺规程的制订原则 机械加工工艺规程的制订原则是优质、高产、低成本,即在保证产品质量前提下,能尽量提高劳动生产率和降低成本。在制订工艺规程时应注意以下问题: 1.技术上的先进性 在制订机械加工工艺规程时,应在充分利用本企业现有生产条件的基础上,尽可能采用国内、外先进工艺技术和经验,并保证良好的劳动条件。 2.经济上的合理性 在规定的生产纲领和生产批量下,可能会出现几种能保证零件技术要求的工艺方案,此时应通过核算或相互对比,一般要求工艺成本最低。充分利用现有生产条件,少花钱、多办事。 3.有良好的劳动条件 在制订工艺方案上要注意采取机械化或自动化的措施,尽量减轻工人的劳动强度,保障生产安全、创造良好、文明的劳动条件。 由于工艺规程是直接指导生产和操作的重要技术文件,所以工艺规程还应正确、完整、统一和清晰。所用术语、符号、计量单位、编号都要符合相应标准。必须可靠地保证零件图上技术要求的实现。在制订机械加工工艺规程时,如果发现零件图某一技术要求规定得不适当,只能向有关部门提出建议,不得擅自修改零件图或不按零件图去做。 §4.1.2 制订机械加工工艺规程的内容和步骤 1.计算零件年生产纲领,确定生产类型。 2.对零件进行工艺分析 在对零件的加工工艺规程进行制订之前,应首先对零件进行工艺分析。其主要内容包括: (1)分析零件的作用及零件图上的技术要求。 (2)分析零件主要加工表面的尺寸、形状及位置精度、表面粗糙度以及设计基准等; (3)分析零件的材质、热处理及机械加工的工艺性。
《机械零件可靠性设计》教学大纲
《机械零件可靠性设计》教学大纲 课程名称:机械零件可靠性设计面向专业:农机化、机师、汽运 课程代码:大纲执笔人:吕钊钦 总学分:2 大纲审定人:王会明 1、课程的教学目的、性质、地位和任务 随着科学技术的飞速发展,可靠性技术已被广泛地应用于各个行业。可靠性设计作为一门边缘科学受到重视在国外已有40多年的历史了,在航天、航空、机械、电子技术中的应用得到了很大发展。可靠性设计、优化设计、有限元分析和计算机辅助设计构成了现代化机械设计的新方法。机械设备是由许多零件组成的,要提高设备的可靠性,必须先提高零件的可靠性。本课程的基本任务是掌握汽车可靠性设计理论,根据要求将零件的可靠度设计到产品中,保证产品的使用可靠性、实现产品寿命的可预测性,从而达到低成本、高效益之目的。 2、课程教学的基本要求 《机械零件可靠性设计》具有较强的理论性。要求掌握产品可靠性的评价尺度,威布尔分布、正态分布、对数正态分布等可靠性工程常用的几种概率分布;学会应力、强度分布的确定方法;熟练掌握应力、强度分布干涉理论及可靠度计算;了解可靠性试验与分析方法,学会轴、螺栓、键连接、齿轮传动等机械零件的可靠性设计。 3、课程教学大纲及学时分配(36学时) 第一章:绪论(2学时) 第一节概述 第二节可靠性定义及评价指标 一、可靠性定义 二、可靠性尺度(特征量) 1 可靠度R(t) 2 失效率l(t) 3 平均寿命(平均无故障工作时间)MTBF 4 维修度M(t) 5 有效度 6 可靠寿命三、零件传统设计法与可靠性设计法的比较 内容要点是可靠性发展史、重要性和任务;可靠性定义及其评价指标。重点是可靠性定义及其评价指标、零件传统设计法与可靠性设计法的比较。 教学方法:采用多媒体教学。通过理论学习、习题等教学环节的相互配合,突出重点、难点。 思考题:1、可靠性定义及评价指标有哪些? 2、比较零件传统设计法与可靠性设计法的不同点。 第二章:可靠性的数学基础(2学时) 第一节:随机变量 一离散型随机变量
第7章_机械制造工艺基础考试复习题教学提纲
第7章_机械制造工艺基础考试复习题
第7章练习题 一、是非题 1、零件的切削加工工艺性反映的是零件切削加工的难易程度。(√) 2、零件的结构工艺性是衡量零件结构设计优劣的指标之一。(√) 3、在单件小批生产中一般采用机械加工艺过程卡片指导生产。(√) 4、定位基准属于工艺设计过程中所使用的一种基准,因此属于设计基准。 (×) 5、粗基准是粗加工所使用的基准,精基准是精加工所使用的基准。(×) 6、经济精度指的是在正常工艺条件下,某种加工方法所能够达到的精度。 (√) 7、加工顺序的安排仅指安排切削加工的顺序。(×) 8、单件小批生产中倾向于采用工序集中的原则。(√) 9、退火等热处理工序一般安排在半精加工之后、精加工之前进行。(×) 10、箱体类零件的精基准及定位方式一般采用一面两销。(√) 11、热处理前已加工好的中心孔,热处理后必须研磨,以保证定位精度。(√) 12、粗基准是粗加工所使用的基准,精基准是精加工所使用的基准。(×) 13、变速箱体上的Φ50H7Ra0.8μm轴承孔,采用下列方案:钻—扩—粗磨—精磨。(×) 14、在多品种小批量生产中,一般倾向于使用工序分散的原则。(×) 15、有色金属的精加工适合车削和铣削而不适合磨削。(√) 二、选择题 1、下面关于零件结构工艺性论述不正确的是( D ) A.零件结构工艺性具有合理性 B 零件结构工艺性具有综合性 C:零件结构工艺性具有相对性 D零件结构工艺性具有正确性 2、零件加工时,粗基准一般选择(A) A 工件的毛坯面 B工件的已加工表面 C 工件的过渡表面 D工件的待加工表面 3、下面对粗基准论述正确的是(C) A 粗基准是第一道工序所使用的基准 B粗基准一般只能使用一次 C 粗基准一定是零件上的不加工表面 D粗基准是一种定位基准 4、自为基准是以加工面本身为基准,多用于精加工或光整加工工序,这是由于(C) A 符合基准重合原则 B符合基准统一原则 C 保证加工面的余量小而均匀 D保证加工面的形状和位置精度 5、工艺设计的原始资料中不包括(D) A零件图及必要的装配图 B零件生产纲领 C工厂的生产条件 D机械加工工艺规程 6、下面(C )包括工序简图。 A机械加工工艺过程卡片 B机械加工工艺卡片
机械零部件可靠性设计方法研究
机械零部件可靠性设计方法研究 作者:常秀旺宋晓艳 来源:《汽车世界·车辆工程技术(中)》2019年第07期 摘要:随着经济的发展以及科技的进步,人们对于机械产品的要求也越来越高。所以机械产品在满足功能性和多样性的同时,更需要满足可靠性的要求,所以本文针对机械产品的可靠性设计方面加以阐述分析。 关键词:机械零件;可靠性;设计 1 机械零部件的可靠性概述 零部件在机械设备中起到负载、部件联动、动力传输的重要作用,在设备长时间工作状态下,零部件易发生是失效现象,令机械设备产生故障。当零部件发生损毁现象时,例如老化、堵塞、松脱等,将增加联动部件的运行压力,提升零部件故障检测的难度。此外,机械设备加工工艺、工作原理存在差异性,在零部件基准参数方面难以进行统一,只有少部分密封件、阀门、泵体等零部件实现通用化、标准化。为此,在对零部件的可靠性进行设计时,零部件的荷载分布能力、材料强度等则应作为主要突破点。 2 可靠性设计方法 可靠性优化设计主要采用的方法有鲁棒设计法和降额设计法。 2.1 鲁棒设计法 鲁棒设计法,是由日本的机械设计师田口玄一首次提出,以统计分析为基础,主要是根据产品的不可用性为用户产生的损失来评判设计的可靠性。其中的损失指的是流失的可用性与合格可用性的比值,流失的可用性越大则可靠性越差,即产品合格性越差,说明产品质量不合格。因此,降低流失可用性是关键因素,也是提升产品质量的重点,可以通过严格审核产品设计、加强生产材料质量检验,优化生产加工工艺、强化产品调试试验等提升产品可靠性。 任何一种机械产品都具有不同程度的敏感性,这是因为,机械产品设计功能的实现受到制造因素、使用环境因素以及使用年限等因素的影响。产品在制造过程中如温度等可变因素有很多,使用过程中环境中的粉尘、烟雾、高温等可变因素也很多,由于产品使用的时间变长,产品的结构会发生变化,某些参数可能会发生改变,系统不可避免地会老化,以上种种因素都会使得产品变得敏感,这种设计方法正是以降低这种敏感性为主要目的。 2.2 降额设计
零件的结构工艺性分析
零件的结构工艺性分析 零件的结构工艺性是指在满足使用性能的前提下,是否能以较高的生产率和最低的成本方便地加工出来的特性。为了多快好省地把所设计的零件加工出来,就必须对零件的结构工艺性进行详细的分析。主要考虑如下几方面。 (1) 有利于达到所要求的加工质量 ①合理确定零件的加工精度与表面质量 加工精度若定得过高会增加工序,增加制造成本,过低会影响机器的使用性能,故必须根据零件在整个机器中的作用和工作条件合理地确定,尽可能使零件加工方 便制造成本低。 ②保证位置精度的可能性 为保证零件的位置精度,最好使零件能在一次安装中加工 出所有相关表面,这样就能依靠机床本身的精度来达到所要求 的位置精度。如图4-6(a)所示的结构,不能保证φ80㎜与内孔φ 60㎜的同轴度。如改成图(b)所示的结构,就能在一次安装中加 工出外圆与内孔,保证二者的同轴度。 (2) 有利于减少加工劳动量 ①尽量减少不必要的加工面积(a) (b) 减少加工面积不仅可减少机械加工的劳动量,图4-6 有利于保证位置精度的工艺结构 而且还可以减少刀具的损耗,提高装配质量。图(a) 错误(b) 正确 4-7(b)中的轴承座减少了底面的加工面积,降低了修配的工作量,保证配合面的接触。图4-8(b)中减少了精加工的面积,又避免了深孔加工。 (a) (b) (a) (b) 图4-7 减少轴承座底面加工面积图4-8 避免深孔加工的方法 (a) 错误(b) 正确(a) 错误(b) 正确 ②尽量避免或简化内表面的加工 因为外表面的加工要比内表面加工方便经济,又便于测量。因此,在零件设计时应力求避免在零件内腔进行加工。如图4-9所示箱体,将图(a)的结构改成图(b)所示的结构,这样不仅加工方便而且还有利于装配。再如图4-10所示,将图(a)中件2上的内沟槽a加工,改成图(b)中件1的外沟槽加工,这样加工与测量就都很方便。 (3) 有利于提高劳动生产率 ①零件的有关尺寸应力求一致,并能用标准刀具加工。如图4-11(b)中改为退刀槽尺寸一致,则减少了刀具的种类,节省了换刀时间。如图4-12(b)采用凸台高度等高,则减少了加工过程中刀具的调整。如图4-13(b)的结构,能采用标准钻头钻孔,从而方便了加工。 ②减少零件的安装次数零件的加工表面应尽量分布在同一方向,或互相平行或互相垂直的表面上;次要表面应尽可能与主要表面分布在同一方向上,以便在加工主要表面时,
失效分析的任务
失效分析的任务、方法及其展望 摘要:概述了失效与失效分析的概念,以及失效分析的意义、作用和任务;以防止失效为出发点,论述了失效分析的工作思路、程序和辩证方法;展望了失效分析的未来。 关键词:失效分析;失效分析反馈;失效预测预防 美国《金属手册》认为,机械产品的零件或部件处于下列三种状态之一时,就可定义为失效:①当它完全不能工作时;②仍然可以工作,但已不能令人满意地实现预期的功能时;③受到严重损伤不能可靠而安全地继续使用,必须立即从产品或装备拆下来进行修理或更换时。 机械产品及零部件常见的失效类型包括变形失效、损伤失效和断裂失效三大类。 机械产品及零部件的失效是一个由损伤(裂纹)萌生、扩展(积累)直至破坏的发展过程。不同失效类型其发展过程不同,过程的各个阶段发展速度也不相同。例如疲劳断裂过程一般较长,发展速度较慢,而解理断裂失效过程则很短,速度很快,等等。 机械产品及零部件在整个使用寿命期内失效发生的规律可用“寿命特性曲线”来说明,即用失效率(λ)———单位时间内发生失效的比率来描述失效的发展过程。那么在不进行预防性维修的情况下,失效率(λ)与其工作时间(t)之间具有图1所示的典型失效曲线,俗称“浴盆曲线”。按照“浴盆曲线”的形状,即按照机械产品使用的过程,可将失效分为三类。 图1 失效率浴盆曲线 (1)早期失效是在使用初期,由于设计和制造上的缺陷而诱发的失效。因为使用初期,容易暴露上述缺陷而导致失效,因此失效率往往较高,但随着使用时间的延长,其失效率则很快下降。假若在产品出厂前即进行旨在剔除这类缺陷的过程,则在产品正式使用时,便可使失效率大体保持恒定值。
(2)随机失效在理想的情况下,产品或装备发生损伤或老化之前,应是无“失效”的。但是由于环境的偶然变化、操作时的人为差错或者由于管理不善,仍可能产生随机失效或称偶然失效。偶然失效率是随机分布的,其很低而且基本上是恒定的。这一时期是产品最佳工作时间。偶然失效率(λ)的倒数即为失效的平均时间。 (3)耗损失效又称损伤累积失效。经过随机失效期后,产品中的零部件已到了寿命后期,于是失效开始急剧增加,这种失效叫做耗损失效或损伤累积失效。如果在进入耗损失效期之前进行必要的预防维修,它的失效率仍可保持在随机失效率附近,从而延长产品的随机失效期。 1 失效分析的意义与任务 1.1 失效分析及其意义 按一定的思路和方法判断失效性质、分析失效原因、研究失效事故处理方法和预防措施的技术活动及管理活动,统称失效分析。 失效分析预测预防是使失败转化为成功的科学,是产品或装备安全可靠运行的保证,是提高产品质量的重要途径,是科学技术进步的强有力杠杆,是许多重大法律、法规及技术标准制定的依据。它着眼于整个失效的系统工程分析。其意义和作用在于: (1)失效分析可减少和预防产品或装备同类失效现象重复发生,从而减少经济损失或提高产品质量。 (2)失效是产品质量控制网发生偏差的反映,失效分析是可靠性工程的重要基础技术工作,是产品全面质量管理 中的重要组成部分和关键技术环节。 (3)失效分析可为技术开发、技术改造、科学技术进步提供信息、方向、途径和方法。 (4)失效分析可为裁决事故责任、侦破犯罪案例、开展技术保险业务、修改和制订产品质量标准等提供可靠的科学技术依据。 (5)失效分析可为各级领导进行宏观经济和技术决策提供重要的科学的信息来源。 1.2 失效分析的任务 失效分析预测预防的总任务就是不断降低产品或装备的失效率,提高可靠性,防止重大失效事故的发生,促进经 济高速持续稳定发展。从系统工程的观点来看,失效分析的具体任务可归纳为:①失效性质的判断;②失效原因的分析; ③采取措施,提高材料或产品的失效抗力。 近代材料科学和工程力学对破断、腐蚀、磨损及其复合型(或混合型)的失效类型和失效机理做了相当深入的研究,积累了大量的统计资料,为失效类型的判断、失效机理及失效原因的解释奠定了基础。发展中的可靠性工程及完整性与适用性评价是预测、预防和控制失效的技术工作和管理工作的基础。可靠性工程是运用系统工程的思想和方法,权衡经济利弊,研究将设备(系统)的失效率降到可接受程度的措施。完整性和适用性评价则是研究结构或构件中原有缺欠和使用中新产生的或扩展缺陷对可靠性的影响,判断结构的完整性及是否适合于继续使用,或是按预测的剩余寿命监控使用,或是降级使用,或是返修或报废的定量评价。
各类零件机械设计图集锦
各类零件机械设计图集锦! 1.轴套类零件 这类零件一般有轴、衬套等零件,在视图表达时,只要画出一个基本视图再加上适当的断面图和尺寸标注,就可以把它的主要形状特征以及局部结构表达出来了。为了便于加工时看图,轴线一般按水平放置进行投影,最好选择轴线为侧垂线的位置。 在标注轴套类零件的尺寸时,常以它的轴线作为径向尺寸基准。由此注出图中所示的Ф14 、Ф11(见A-A断面)等。这样就把设计上的要求和加工时的工艺基准(轴类零件在车床上加工时,两端用顶针顶住轴的中心孔)统一起来了。而长度方向的基准常选用重要的端面、接触面(轴肩)或加工面等。 如图中所示的表面粗糙度为Ra6.3的右轴肩,被选为长度方向的主要尺寸基准,由此注出13、28、1.5和26.5等尺寸;再以右轴端为长度方向的辅助基,从而标注出轴的总长96。
2.盘盖类零件 这类零件的基本形状是扁平的盘状,一般有端盖、阀盖、齿轮等零件,它们的主要结构大体上有回转体,通常还带有各种形状的凸缘、均布的圆孔和肋等局部结构。在视图选择时,一般选择过对称面或回转轴线的剖视图作主视图,同时还需增加适当的其它视图(如左视图、右视图或俯视图)把零件的外形和均布结构表达出来。如图中所示就增加了一个左视图,以表达带圆角的方形凸缘和四个均布的通孔。 在标注盘盖类零件的尺寸时,通常选用通过轴孔的轴线作为径向尺寸基准,长度方向的主要尺寸基准常选用重要的端面。 3.叉架类零件 这类零件一般有拨叉、连杆、支座等零件。由于它们的加工位置多变,在选择主视图时,主要考虑工作位置和形状特征。对其它视图的选择,常常需要两个或两个以上的基本视图,并且还要用适当的局部视图、断面图等表达方法来表达零件的局部结构。踏脚座零件图中所示视图选择表达方案精练、清晰对于表达轴承和肋的宽度来说,右视图是没有必要的,而对于T字形肋,采用剖面比较合适。
机械可靠性设计
机械可靠性设计 LG GROUP system office room 【LGA16H-LGYY-LGUA8Q8-LGA162】
机械可靠性设计概述 专业:机械设计制造及其自动化 班级:机制(2)班 组员: 黄佳辉 芦朝晖
摘要 可靠性就是产品在规定的时间和规定的条件下完成规定功能的能力,无论任何产品或是零件能否在复杂多变的环境下发挥其应有的功能是至关重要的,目前几乎所以的机器在设计制造的过程中都必须考虑其可靠性,可靠性设计已经变得越来越重要,怎样合理的采用科学的可靠性设计方法使机器能够在要求的工作环境下不会失效损坏是设计中必须考虑的重要问题,只有这样才能提高和稳定产品的可靠性。 关键词:可靠性发展趋势设计方法意义原理 正文 机械可靠性设计的目的就是确保其设计的机械零件能够在规定的工作时间,规定的条件下完成规定的功能。机械产品是在综合学科交叉作用下的高新技术的衍生物, 其主要功效就是实现产品运行过程中的安全性、可靠性[1] 。一个产品如果无法保证其 运作的稳定性,将会极大的威胁到人生安全,而且稳定性也是对产品质量的一种保证。 一机械可靠性设计研究发展状况 国内主要的可靠性研究机构有中国赛宝实验室(CEPREI,工业和信息化部电子第五 研究所)、摩尔实验室(MORLAB)等。中国赛宝实验室是中国唯一专业进行电子产品质量与可靠性研究的权威机构。可靠性研究分析中心(RAC)是中国赛宝实验室的核心技术部门,是按国际标准ISO17025管理和运行的实验室,主要开展电子产品失效分析、破坏性物理分析、电子制造技术服务、电子产品污染控制技术项目等。 经过多年的建设和发展,分析中心在电子材料、元器件、封装、组装和电子辅料的质量与可靠性方面,具有完善的检测、分析和试验能力;开展有毒有害物质(RoHS)、环境评估与监测、ODS替代技术检测等方面的技术服务,是目前国内最先进、综合技术能力最强的电子制造技术支持实验室和环保检测实验室。 摩尔实验室中的可靠性实验室主要实验为:气候环境实验、机械环境实验、高温可靠性实验。环境试验室拥有一批国际、国内着名的专业环境试验设备制造商生产的气候环境试验设备;设备技术先进、性能稳定、功能齐全,可编程控制,自动绘制试验曲线;可按IEC、ISO等国际标准和国家标准(GB)、行业标准、企业标准,以及客户的要求进行高温、低温、恒温恒湿、交变湿热、温度变化、温度/湿度组合循环、低气压等气候环境试验。环境试验室还拥有面积40余平方米的具有国内领先水平的大型淋雨试验室,配备了可编程控制、不锈钢材料的垂直淋雨、摆管淋雨、花洒淋雨、防
可靠性论文
机械可靠性设计 1.机械可靠性技术的发展历程 可靠性技术的研究开始于20世纪20年代,在结构工程设计中的应用始于20世纪柏年代。可靠性技术最早应用在二战末期德国V一Ⅱ火箭的诱导装置上。德国火箭研究机构参加人之一R.Lusser首先提出了利用概率乘积法则,把一个系统的可靠度看成该系统的子系统可靠度的乘积。自从1946年Freuenthal在国际上发表“结构的安全度”一文以来,可靠性问题扦始引起学术界和工程界的普遍关注与重视。 从已有的资料了解到国内外机械产品可靠性研究状况如下: 美国的可靠性研究起步较早,在机械产品可靠性理论方面,一亚利桑那大学 D.Kececioglu教授为首。主要研究机械零件的可靠性概率设计方法。在机械故障预防和检测方面,以机械故障预防小组(MFPG)为代表对设计、诊断、监测、故障等进行研究,在可靠性数据的收集和分析方面取得了很大的进步,并且编制了一些可靠性设计手册和指南、可靠性数据手册。 日本的可靠性设计是从美国引进的,以民用产品为主,强调实用化,日本科技联盟是其全国可靠性技术的推广机构。在可靠性工程应用方面,比较重视可靠性试验、故障诊断和寿命预测技术的研究与应用,以及产品失效分析、现场使用数据的收集和反馈。 原苏联对机械可靠性的研究十分重视,并有其独到之处。其可靠性技术应用主要靠国家标准推动,发布了一系列可靠性标准。他们认为可靠性技术的主要内容是预测,即在产品设计和样机试验阶段,预测和评估在规定的条件下的使用可靠性,研究各项指标随时间变化的过程。他们认为可靠性研究的方向主要有两个:一是可靠性数学统计方法和使用信息的统计处理技术,以及保证复杂系统可靠性的技术。二是适于机械制造行业,包括无力故障学机械零件的耐磨、耐热、耐蚀等设计方法以及保证可靠性的工艺的方法研究。 英国国家可靠性分析中心(NCRS)成立了机械可靠性研究小组,汇编出版了《机械系统可靠性》一书。从失效模式、使用环境、故障性质、筛选效果、实验难度、维修方式和数据积累等7个方面阐明了机械可靠性应用的重点,提出了几种机械系统可靠性的评估方法,并强调重视数据积累。 我国对机械产品可靠性研究起步较晚,20世纪80年代才得到较快发展,机械行业相继成立了可靠性研究的相关协会,各有关院所和高校也开展了机械产品可靠性研究,制定了一批可靠性标准,取得了较大的成果。但总的看来,理论研究多,实际应用少,与西方国家差距大,有些成果尚不能完整地成熟地应用在不同的机械系统中 2.广义可靠性的研究现状
机械零件失效分析
第一章 失效:产品丧失其规定功能的现象。 常见失效形式:有变形、断裂、损伤失效。 失效分析:研究机械装备的失效诊断、失效预测和失效预防的理论、技术、方法及其工程应用的一门学科。(综合性、实用性) 引起失效的因素是复杂的,归纳为两个方面: 材料因素:内因,包括材料品质及加工工艺方面的各种因素; 环境因素:外因,包括受载条件、时间、温度及环境介质等因素。 产品的失效都是在材料或零件的强度(韧性)与应力因素和环境条件不相适应的条件下发生的。失效总是从产品对服役条件最不适应的环节开始的,而且失效产品或零件的残骸上必然会保留有失效过程的信息。 产品的可靠度: 产品在规定的条件下和规定的时间内满意地完成规定功能的概率。 四个含义:即功能、时间、使用条件和满意地完成规定功能的概率。 第二章 按失效的宏观特征作为一级失效形式分类,分为变形失效、断裂失效和表面损伤失效。机械零件失效原因概述 1.服役条件---受力状况(载荷类型、载荷性质、应力状态)和环境(介质和温度) 2.材料因素 3.设计和工艺因素 4.使用和维修 α越大,应力状态越软,易引起塑性变形 硬性应力状态:α<1 α越小,应力状态越硬,易引起脆性断裂
第三章 P25+P69 常见失效形式(11种):过量弹性变形失效、屈服失效(塑性变形失效)、塑性断裂失效、脆性断裂失效、疲劳断裂失效、腐蚀失效、应力腐蚀失效、氢脆失效、腐蚀疲劳失效、磨损失效、蠕变失效。 脆性断裂失效:构件在断裂前没有发生或很少发生宏观可见的塑性变形的断裂形式。断裂应力低于材料屈服强度,因此称为低应力脆断。工作条件: 高速、高压、高温和低温导致材料的服役条件越来越苛刻。 低温脆性断裂主要发生于体心立方和密排六方金属材料中,这些材料称为低温脆性材料,低碳钢是其典型代表。 脆性断裂特征: (1)断裂部位在宏观上几乎看不出或者完全没有塑性变形,碎块断口可以拼合复原。 (2)起裂部位常在变截面处即应力集中部位,或者存在表面缺陷或内部缺陷处。 (3)形成平断口,断口平面与主应力方向垂直。 (4)断口呈细瓷状,较光亮,对着光线转动,可看到闪光刻面,无剪切唇。 (5)断裂常发生于低温条件下,或受冲击载荷作用时。 (6)断裂过程瞬间完成,无预兆。 金属机件或构件在变动应力和应变长期作用下,由于累积损伤而引起的断裂现象称为疲劳。疲劳断裂特点 ⑴疲劳断裂是低应力循环延时断裂,即具有寿命的断裂。 ⑵疲劳断裂是突然断裂,即脆性断裂。断裂前没有明显的征兆,疲劳是一种潜在的突发性断裂。 ⑶对缺陷(缺口、裂纹及组织缺陷)十分敏感。 典型疲劳断口具有三个形貌不同的区域:疲劳源、疲劳裂纹扩展区、瞬时断裂区。 疲劳裂纹有贝纹线,贝纹线是以疲劳源为圆心的一簇同心圆弧;间距不同,近源者密,远源者疏。贝纹线的宽窄不同。与过载程度、材质有关,过载大、韧性差的线粗而不明显。贝纹线和疲劳辉纹的区别: ◆形成原因不同。 贝纹线是交变应力的频率、幅度变化或载荷停歇等原因造成的。 疲劳辉纹是一次交变应力循环使裂纹尖端塑性钝化形成的。 ◆二者可以同时出现,也可以不同时出现。 有时在宏观断口上看不到贝纹线; 在电子显微镜下也不一定看到疲劳辉纹。 氢脆失效的类型及特征 1.白点:又称发裂,是由于钢中存在的过量的氢造成的。