机电控制与可编程序控制器课程设计.doc
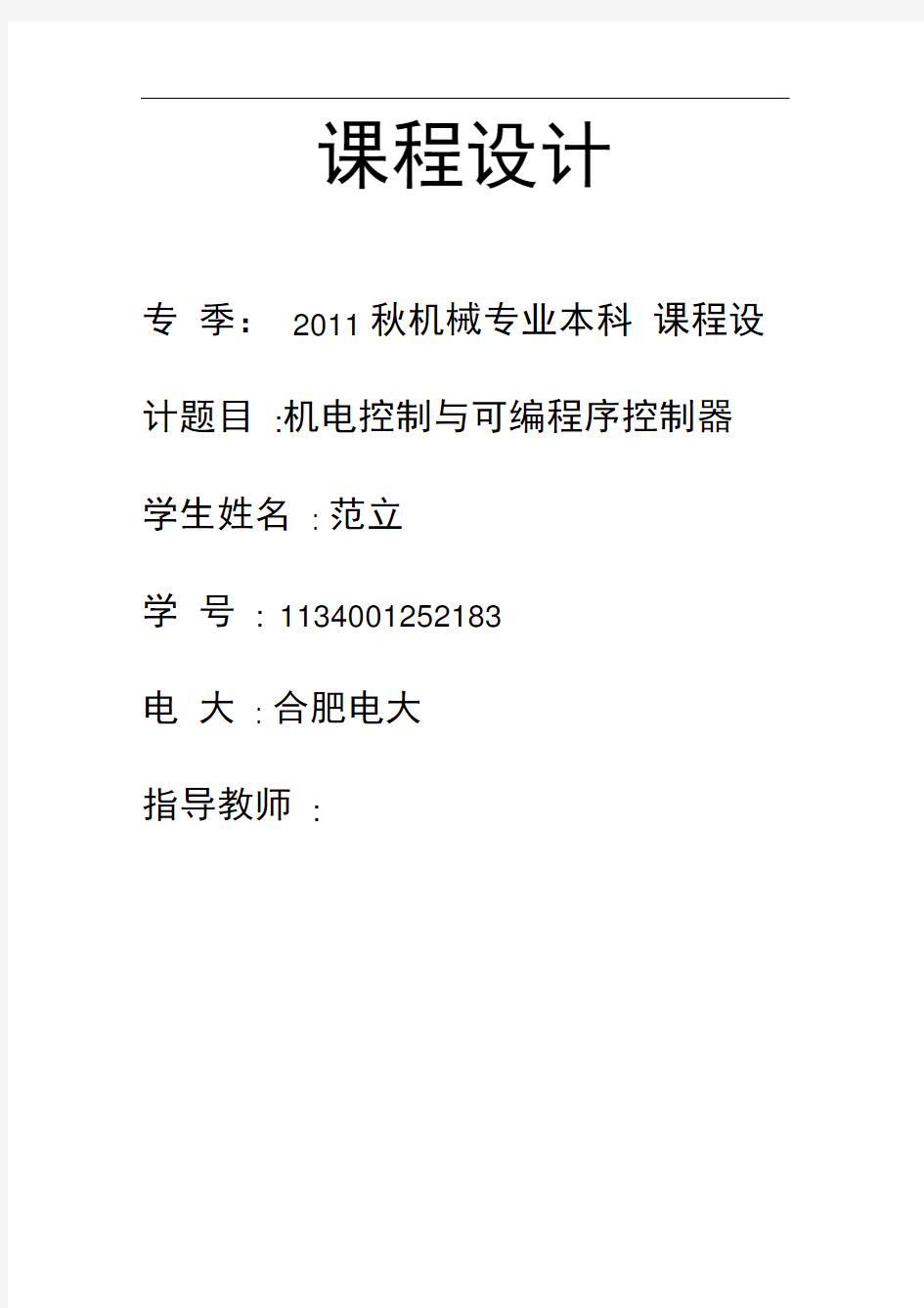
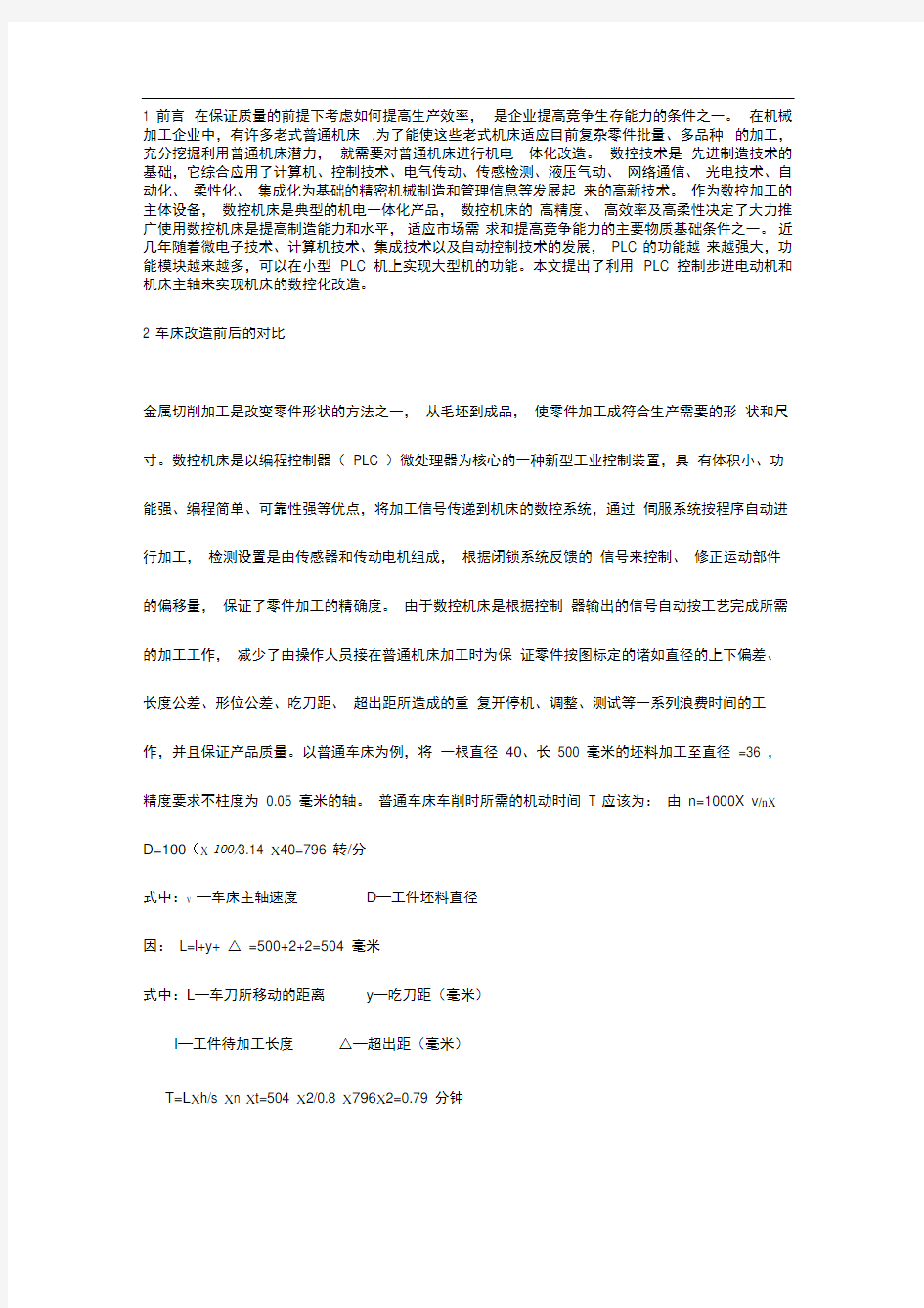
课程设计
专季:2011 秋机械专业本科课程设计题目:机电控制与可编程序控制器学生姓名: 范立
学号: 1134001252183
电大: 合肥电大
指导教师:
1 前言在保证质量的前提下考虑如何提高生产效率,是企业提高竞争生存能力的条件之一。在机械加工企业中,有许多老式普通机床,为了能使这些老式机床适应目前复杂零件批量、多品种的加工,充分挖掘利用普通机床潜力,就需要对普通机床进行机电一体化改造。数控技术是先进制造技术的基础,它综合应用了计算机、控制技术、电气传动、传感检测、液压气动、网络通信、光电技术、自动化、柔性化、集成化为基础的精密机械制造和管理信息等发展起来的高新技术。作为数控加工的主体设备,数控机床是典型的机电一体化产品,数控机床的高精度、高效率及高柔性决定了大力推广使用数控机床是提高制造能力和水平,适应市场需求和提高竞争能力的主要物质基础条件之一。近几年随着微电子技术、计算机技术、集成技术以及自动控制技术的发展,PLC 的功能越来越强大,功能模块越来越多,可以在小型PLC 机上实现大型机的功能。本文提出了利用PLC 控制步进电动机和机床主轴来实现机床的数控化改造。
2 车床改造前后的对比
金属切削加工是改变零件形状的方法之一,从毛坯到成品,使零件加工成符合生产需要的形状和尺
寸。数控机床是以编程控制器(PLC )微处理器为核心的一种新型工业控制装置,具有体积小、功
能强、编程简单、可靠性强等优点,将加工信号传递到机床的数控系统,通过伺服系统按程序自动进
行加工,检测设置是由传感器和传动电机组成,根据闭锁系统反馈的信号来控制、修正运动部件
的偏移量,保证了零件加工的精确度。由于数控机床是根据控制器输出的信号自动按工艺完成所需
的加工工作,减少了由操作人员接在普通机床加工时为保证零件按图标定的诸如直径的上下偏差、
长度公差、形位公差、吃刀距、超出距所造成的重复开停机、调整、测试等一系列浪费时间的工
作,并且保证产品质量。以普通车床为例,将一根直径40、长500 毫米的坯料加工至直径=36 ,
精度要求不柱度为0.05 毫米的轴。普通车床车削时所需的机动时间T 应该为:由n=1000X v/nX
D=100(X 100/3.14 X40=796 转/分
式中:v —车床主轴速度D—工件坯料直径
因:L=l+y+ △ =500+2+2=504 毫米
式中:L—车刀所移动的距离y—吃刀距(毫米)
I—工件待加工长度△—超出距(毫米)
T=L X h/s X n X t=504 X2/0.8 X796X2=0.79 分钟
式中:T—机动时间h —切削厚度
s —走刀量n —工件每分钟转数
t—切削深度
除以上能以轴、转速及走刀量等有据可依能算出的走刀时间外,其余的如为保证尺寸精度必须小心谨慎地给定进给量前的刀尖与工件表面的对刀,然后以拖板的刻度为参考小心进刀,试车一定长度后,停机检测(最多为两次),确信与图纸的要求相符后才进行车削,其中所需的时间只能按实际操作加上人为制定给出该项工作所耗费的工时,设定此所需的时间为0.
5分钟时,则普通车床的实际用时T应为:
T' =T+0.5=0.79+ 0.5=1.29 (分钟)
改装(PLC )后的车床,转由编程控制器(PLC )发出的信号完成所须的加工工序,由于车床的横向进给实现了自动化,程序应为:以车刀刀尖为基准点,控制车刀刀尖按指令给定的以主轴中心轴线为基准进到所需加工的轴的半径距离时,横向进给自锁,依照信号进行纵向切削工作,省去了由人工操作加工中所需的反复开停车及检测用时,因此,从以上的加工一根简单的$ 40X 500(毫米)的轴可以得出:如果改装后数控车床的转速、切削用量等和普
通车床相同,则数控机床所需的实际用时为
T〃=0.79分钟)。
普通车床与改装(PLC )可编程控制器后的车床的实际时间差为:
T'—T〃=1.29- 0.79=0.5(分钟)
由此可见改装(PLC )控制后车床的机动时比普通车床的用时省却了0.5分钟,工效将近提
高了一倍,对于批量生产的产品,不仅节省了大量的时间,还提高了控制系统的可靠性和准
确性,为企业提供了更可靠的自动化生产保障,提高了经济效益。
3以CW6140型普通车床为例,把继电控制改造为PLC控制
3.1改造分析
1)根据机床电气控制原理图(图1)的控制状态,选择合适的PLC机型;
2)列出PLC输入、输出I/O分配表(表1、表2);
3)画出PLC控制电路接线图(图2);
4)画出PLC梯形图(图3),并编制程序;
图1 CW6140型普通车床电气控制线路原理图
3.2电气控制线路分析
CW6140 型普通车床电气控制线路原理图如图1 所示。图中分主电路、控制电路和照明、信号电路。
3.2.1 电路分析
主电路中有两台电机,M1 为主轴电机,带动主轴旋转和刀架作进给运动;M2 为冷却泵。
三相交流电源通过转换开关QS1 引入,主轴电机M1 由接触器控制启动,热继电器FR1为主轴电机M1 的过载保护。
冷却泵电机M2由组合开关QS2控制启动和停止,热继电器FR2为它的过载保护。
3.2.2 控制电路分析
(1 )主轴电机的控制。当按SB2时,接触器KM i的线圈获得电动作,同时KM i的常开触
点闭合,KM3和KT得电,KM i和KM3主触点闭合时电机M i星形正转降压启动,当KT延时约3~5S 时,KT延时常闭触点断开使KM3失电,其星形接法主触点断开;KT延时常开
触点闭合使KM2得电,其主触点闭合,电机M i从星形转换为三角形运行。同理,按SB i 时,电机M i 反转(星形—三角形启动)。
(2)冷却泵电机的控制。旋合组合开关QS2使冷却泵电机M2启动运行。
(3)照明电路分析。控制变压器TC 的二次侧输出36V 电压,作为机床低压照灯电源, E L为机床的低压照明灯,由开关SA2控制。
3.3 PLC 及其程序设计
3.3.i PLC 选型和I/O 端口分配
根据以上机床主电路继电控制要求分析,系统共需开关量输入点 5 个,开关量输出点 4 个,考虑系统的经济性和技术指标,拟选用三菱公司的微型机FX2n —i6MR 机型,该机基本单
元有8 点输入,8 点输出,完全能满足控制要求。输入/输出信号地址分配如表i 和表2。
表1输入信号地址分配表
表2输出信号地址分配表
332 PLC控制电路接线图
为了保证安全,系统外部设置了急停控制电路,SB6为电源供给按钮,当系统出现故障时,
按下SB5,KM线圈失电,KM常开启点断开,PLC失去电源,机床停止工作。PLC控制电路接线如图2所示。
图2 PLC 控制电路接线图
333 PLC 程序设计:
当按SB 2时,X ooo 的常开触点闭合,Y ooo 、Y 003和T o 得电,接触器KM i 的线圈获得电动作, 同时KM i 和KM 4主触点闭合时电机 M i 星形正转降压启动,当 T0延时约3~5S 时,T0延
时常闭触点断开使 KM 4失电,其星形接法主触点断开;
T o 延时常开触点闭合使 KM 3得电,
其主触点闭合,电机 M i 从星形转换为三角形运行。同理,按
SB i 时,X ooi 的常开触点闭合,
接触器KM 2的线圈获得电动作,电机M i 反转(星形一三角形启动)。根据以上要求编制
P
LC 控制梯形图(图3)及由梯形图写出 PLC 控制指令程序。
X 塑0 J PLC+J
>
Xorn
j
Xoojj
COM
L
2
机电控制系统课程设计
JIANG SU UNIVERSITY 机电系统综合课程设计 ——模块化生产教学系统的PLC控制系统设计 学院:机械学院 班级:机械 (卓越14002) 姓名:张文飞 学号: 3140301171 指导教师:毛卫平 2017年 6月
目录 一: MPS系统的第4站PLC控制设计 (3) 1.1第四站组成及结构 (3) 1.2 气动回路图 (3) 1.3 PLC的I/O分配表,I/O接线图(1、3、6站电气线路图) (4) 1.4 顺序流程图&梯形图 (5) 1.5 触摸屏控制画面及说明,控制、信息软元件地址表 (10) 1.6 组态王控制画面及说明 (13) 二: MPS系统的两站联网PLC控制设计 (14) 2.1 PLC和PLC之间联网通信的顺序流程图(两站)&从站梯形图 (14) 2.2 通讯软元件地址表 (14) 三:调试过程中遇到的问题及解决方法 (18) 四:设计的收获和体会 (19) 五:参考文献 (20)
一:MPS系统的第4站PLC控制设计 1.1第四站组成及结构: 由吸盘机械手、上下摆臂部件、料仓换位部件、工件推出部件、真空发生器、开关电源、可编程序控制器、按钮、I/O接口板、通讯接口板、多种类型电磁阀及气缸组成,主要完成选择要安装工件的料仓,将工件从料仓中推出,将工件安装到位。 1.吸盘机械手臂机构:机械手臂、皮带传动结构真空吸嘴组成。由上下摆臂装置带动其旋转完成吸取小工件到放小工件完成组装流程的过程。 2.上下摆臂结构:由摆臂缸(直线缸)摆臂机械装置组成。将气缸直线运动转化为手臂旋转运动。带动手臂完成组装流程。 3.仓料换位机构:由机构端头换仓缸带动仓位装置实现换位(蓝、黑工件切换)。 4.推料机构:由推料缸与机械部件载料平台组成。在手臂离开时将工件推出完成上料。 5.真空发生器:当手臂在工件上方时,真空发生器通气吸盘吸气。 5.I/O接口板:将桌面上的输入与输出信号通过电缆C1与PLC的I/O相连。 6.控制面板:完成设备启动上电等操作。(具体在按钮上有标签说明)。
机电传动控制课程设计解析
学号:0121018700306 课程设计 题目组合机床加工过程PLC自动控制设计 学院物流学院 专业物流工程 班级行政1001班 姓名徐宏华 指导教师徐沪萍 2013 年 6 月29 日
课程设计任务书 学生姓名:徐宏华专业班级:物流行政1001班 指导教师:徐泸萍工作单位:物流学院 题目: 组合机床加工过程PLC自动控制设计 初始条件: 1.编程环境:Step7v5.5软件 2.PLC型号:西门子公司S7系列,S7-300 3.机电传动的相关资料指导书 4.仿真环境:S7-PLCSIM 要求完成的主要任务:(包括课程设计工作量及其技术要求,以及说明书撰写等具体要求) 液压滑台式组合机床在原位启动后,快速向前到设定的位置时转为慢速前进,到达攻丝进给位置时停止前进,转为攻螺纹主轴转动,丝锥能向前攻入,打到规定深度时,主轴快速制动。接着攻螺纹反转退出,回到原位时快速制动,同时滑台能快速退回原位,并在原位停止。 时间安排:十八周 指导教师签名:年月日 系主任(或责任教师)签名:年月日
本科生课程设计成绩评定表 指导教师签字: 年月日
目录 摘要------------------------------------------------------------------------------------------------- 0第一章基本知识介绍 ------------------------------------------------------------------------ 1 1.1 设计的任务要求--------------------------------------------------------------------- 1 1.2 组合机床概述------------------------------------------------------------------------ 2 1.2.1 组合机床部件分类 --------------------------------------------------------- 2 1.2.2 组合机床的特点 ------------------------------------------------------------ 2 1.3 PLC控制系统 ----------------------------------------------------------------------- 3 1.3.1 PLC简介 --------------------------------------------------------------------- 3 1.3.2 PLC控制系统设计的基本原则 ------------------------------------------ 4 1.3.3 PLC控制系统的一般步骤 ------------------------------------------------ 4第二章总体方案选择和控制方式选择----------------------------------------------------- 6 2.1 总体方案选择------------------------------------------------------------------------ 6 2.2 控制方式的选择--------------------------------------------------------------------- 6第三章电路图的设计 -------------------------------------------------------------------------- 6 3.1 主电路的设计------------------------------------------------------------------------ 6 3.2 PLC的I/O地址分配--------------------------------------------------------------- 8第四章控制程序的设计 --------------------------------------------------------------------- 10 4.1 顺序功能图的设计---------------------------------------------------------------- 10 4.2 梯形图的设计---------------------------------------------------------------------- 11 4.3 语句表的设计---------------------------------------------------------------------- 15 第五章调试及结果分析 ------------------------------------------------------------------- 21 5.1 硬件组态---------------------------------------------------------------------------- 21 5.2 仿真结果分析---------------------------------------------------------------------- 21 感想----------------------------------------------------------------------------------------------- 25 参考资料书-------------------------------------------------------------------------------------- 26
微机原理与接口技术 课程设计
摘要 霓虹灯主要是通过8255A对LED亮灭状态的控制,和8254定时/计数器的定时功能实现霓虹灯闪烁控制系统,外设是红、绿、黄三种颜色的发光二极管,在程序自动控制下,按照不同规律闪烁同时由数码管显示相应的闪烁方式。 关键字: 8255A 8254 LED 数码管
一、设计的任务和要求 设计霓虹灯闪烁控制系统,是外设的红、绿、黄三种颜色的发光二极管,在开关的控制下或者在程序自动控制下,按照不同规律闪烁。 要求发光二极管的亮、灭变化有一定的规律;发光二极管变化规律要求有多种状态。 二、设计小组成员及分工 本次课设由冀任共同完成,在课设中遇到的问题四个人共同思考解决。 三、总体设计 1、8254用于定时:定时/计数器0与定时器/计数器1共同构成100ms的定时器,确定执行相邻闪烁方式的间隔时间。 2.8255A用于控制LED的状态和数码管显示:PA0接8254的输出,B口接数码管,显示对应的闪烁方式,C口输出控制LED的状态。 3、六种闪烁方式: 方式1:从左向右依次点亮8个LED灯,数码管显示1 方式2:从右向左依次点亮8个LED灯,数码管显示2 方式3:从左向右依次点亮4个的红灯、2个黄灯和2个绿灯,数码管显示3 方式4:从左向右两个两个的点亮8个LED灯,数码管显示4 方式5:从两边向中间依次点亮8个LED灯,数码管显示5 方式6:按红、绿、黄顺序点亮相同颜色的灯,数码管显示6 1、芯片介绍 (1)芯片8255A 8255A是具有3个8位并行I/O口3种工作方式的可编程并行接口芯片。8255共有40个引脚,采用双列直插式封装。
D0--D7:三态双向数据线,与单片机数据总线连接,用来传送数据信息。 CS:片选信号线,低电平有效,表示芯片被选中。 RD:读出信号线,低电平有效,控制数据的读出。 WR:写入信号线,低电平有效,控制数据的写入。 Vcc:+5V电源。 PA0--PA7:A口输入/输出线。 PB0--PB7:B口输入/输出线。 PC0--PC7:C口输入/输出线。 RESET:复位信号线。 A1、A0:地址线,用来选择8255内部端口。 GND:地线。 三种工作状态: 1) 工作方式 0 :这是 8255A 中各端口的基本输入 / 输出方式。它只完成简单的并行输入 / 输出操作, CPU 可从指定端口输入信息,也可向指定端口输出信息,如果三个端口均处于工作方式 0 ,则可由工作方式控制字定义 16 种工作方式的组合。
《机电传动控制》课程设计任务书2016
《机电传动控制》课程设计任务书2016
课题1:专用镗孔机床的电气控制系统设计 (分别使用继电器接触器电路和PLC 实现控制) 1.机床概况 该设备用于大批量生产某零件的镗孔与铰孔加工工序。机床主运动采用动力头,由Y100L —6型(1.5kW-4A)三相异步电动机拖动,单向运转。该设备能进行镗孔加工,当更换刀具和改变进给速度时,又能进行铰孔加工(有镗孔与铰孔加工选择),加工动作流程如图2-1所示。 a 镗孔) b 铰孔) 图2-1 加工动作流程图 进给系统采用液压控制,为提高工效,进给速度分快进与工进两种且自动变换。液压系统中的液压泵拖动电机为Y801-2型(750W 、1.9A),由电磁阀(YVl ~YV4)控制进给速度,为作要求如表2-1所示。 表2-1 液压控制动作要求 为提高加工精度,主轴采用静压轴承,由Y801-2型电动机拖动高压液压泵产生静压油膜。 2.设计要求 1)主轴为单向运转,停车要求制动(采用能耗制 原位起动SQ3 原位起动SQ4
动)。 2)主轴电动机与静压电动机的联锁要求是:先开静压电动机,静压建立后(由油压继电器控制)才能起动主轴电动机,而停机时,要求先停主轴电动机,后停静压电动机。 3)主轴加工操作,采用两地控制。加工结束自动停止,手动快退至原位。 4)根据加工动作流程要求,设置镗孔加工及铰孔加工选择。 5)应有照明及工作状态显示。 6)有必要的电气保护和联锁。 7)PLC采用三菱FX2n。
课题2:千斤顶液压缸加工专用机床电气控制系统设计 (分别使用继电器接触器电路和PLC实现控制) 1.专用机床概况介绍本机为专用千斤顶液压缸两端面的加工,采用装在动力滑台上的左、右两个动力头同时进行切削。动力头的快进、工进及快退由液压油缸驱动。液压系统已用两位四通电磁阀控制,并用调整死挡铁方法实现位置控制,油泵电动机型号为Y80—4(0.55kW、1.6A)。 机床的工作程序是: 1)零件定位。人工将零件装入夹具后,定位油缸动作工件定位。 2)零件夹紧。零件定位后,延时15s,夹紧油缸动作使零件固定在夹具内。同时定位油缸退出以保证滑台入位。 3)滑台入位。滑台带动动力头一起快速进入加工位置。 4)加工零件。左右动力头进行两端面切削加工,动力头到达加工终点,即停止工进,延时30s后动力头停转,快速退回原位。 5)滑台复位,左右动力头退回原位后,滑台复位。 6)夹具松压。当滑台复位后夹具松开,取出零件。 以上液压缸各动作由电磁阀控制,电磁阀动作要求如表2-2所示。 2.设计要求 1)专用机床能半自动循环工作,又能对各个动作
电气控制与可编程控制器课程设计正文
电气控制与可编程控制 器课程设计正文 Company Document number:WUUT-WUUY-WBBGB-BWYTT-1982GT
课程设计任务书一、课程设计的目的 本课程的任务是使学生从实际工程应用出发,在理论和实践上掌握PLC的基本组成,工作原理,并通过设计典型的PLC控制系统,使学生对可编程序控器有一个完整的概念,并具有PLC控制系统研发的初步能力。 在课程设计中使学生掌握可编程序控器的基本组成,工作原理;掌握PLC编程语言;掌握传统的电气控制图;掌握可编程序控器自动控制系统硬件软件设计开发方法。 二、课程设计的开展方式 本课程为实践性环节,采用教师指导加学生自己动手设计的方式,包括以下两方面: 1.课程设计开始前,了解整个课程设计的目的、任务、步骤和方法; 2.课程设计任务主要由学生独立完成,教师负责指导。 三、课程设计的内容及时间安排 课程设计时间为2013年12月23日至 2013年 12月27 日1周,包括了解设计任务和实际动手设计及调试操作。具体内容及时间安排如下: 四、课程设计的考核办法 考核办法:根据平时表现、答辩情况及课程设计说明书按五级分优、良、中、及格、不及格评定成绩。 1.课程设计态度及遵守纪律情况; 2.查阅资料、阅读能力情况; 3.动手操作能力情况; 4.系统需求分析、程序设计思路; 5.梯形图(或语句表)编写情况;
6.课程设计说明书完成情况。 五、课程设计说明书的主要组成部分 1.课题名称及控制要求分析; 2.PLC的介绍及选型,电气原理图; 3.程序(包括注释)、框图、时序图、I/O接线图等; 4.有关的说明及调试小结等; 5.课程设计说明书,不少于15页; 6.电气原理图、系统框图、I/O接线图共三张A3图纸。 六、提交格式要求 1. 一律采用A4书写或打印,左侧装订。 2. 封面(应包含:课程设计题目、姓名、班级、学号) 3. 要求提交课程设计的电子文档和程序。 4. 具体格式见后面附表。 课题一装卸料小车PLC控制设计 (一)设计原始资料和控制要求 装卸料小车工作示意图 一辆小车在A,B两点之间运行,在A,B两点各设一个限位开关,如图所示,小车在A 点时(后限位开关受压动作),操作控制按钮可使小车向前行至料斗下碰到前限位开关,停止,装料后再返回A地将料卸下。小车要求有4种控制方式。 (1)手动控制方式, (2)单周期运行控制方式, (3)双周期运行控制方式, (4)自动循环运行控制方式。 1,手动控制方式
卧式镗床(T68)-机电传动控制课程设计任务书
沈阳航空航天大学 课程设计任务书 机电工程学院机械设计制造及自动化专业 班:学号:姓名: 一、课程设计课题某型号卧式镗床的电气控制系统设计 二、课程设计工作自至 三、课程设计技术说明和控制要求 1、设备机械部分运动说明 某型号卧式镗床主要有床身、前立柱、镗头架、工作台、后立柱和尾架等部分组成。其运动形式有三种:镗轴与花盘的旋转运动为主运动;进给运动包括镗轴的轴向进给、花盘上刀具的径向进给、镗头的垂直进给、工作台的纵向与横向进给;辅助运动为工作台的旋转、后立柱的水平移动、尾架的垂直移动及各部分的快速移动。 2、设备电气控制要求及技术参数 1)主运动与进给运动由同一台双速电动机M1拖动,各方向的快速运动由另一台电动机M2拖动 2)主轴旋转和进给都有较大的调速范围 3)要求M1能正反转,能正反向点动,并带有制动,各方向的进给都能快速移动,正反向都能短时点动 4)必要的保护环节、连锁环节、照明和信号电路 5)电动机的功率 M1:5.2KW M2:3KW
四、课程设计的主要内容 1、分析设备的电气控制要求,制定设计方案、绘制草图; 2、进行电路计算,选择元器件,并列出元器件目录表,绘制电气原理图(包 括主电路和控制电路); 3、通电调试、故障排除、任务验收,编写设计说明书 五、课程设计时间安排 六、主要参考资料 1、齐占庆. 机床控制技术. 北京: 机械工业出版社,1999 2、邓星中主编. 机电传动控制. 武汉:华中科技大学出版社,2001 3、齐占庆. 王振臣主编. 电器控制技术. 北京:机械工业出版社, 2002 4、陈远龄. 机床电气自动控制. 重庆:重庆大学出版社,1997 5、方承远.工厂电气控制技术. 北京: 机械工业出版社,2000 6、张万奎主编.机床电气控制技术.北京:中国林业出版社,北京大学出版社, 2006
机电控制系统课程设计
J I A N G S U U N I V E R S I T Y 机电系统综合课程设计 ——模块化生产教学系统的PLC控制系统设计 学院:机械学院 班级:机械 (卓越14002) 姓名:张文飞 学号: 指导教师:毛卫平 2017年 6月 目录 一: MPS系统的第4站PLC控制设计 (3) 1.1第四站组成及结构 (3) 1.2 气动回路图 (3) 1.3 PLC的I/O分配表,I/O接线图(1、3、6站电气线路图) (4) 1.4 顺序流程图&梯形图 (5) 1.5 触摸屏控制画面及说明,控制、信息软元件地址表 (10) 1.6 组态王控制画面及说明 (13) 二: MPS系统的两站联网PLC控制设计 (14) 2.1 PLC和PLC之间联网通信的顺序流程图(两站)&从站梯形图 (14) 2.2 通讯软元件地址表 (14) 三:调试过程中遇到的问题及解决方法 (18) 四:设计的收获和体会 (19)
五:参考文献 (20) 一:MPS系统的第4站PLC控制设计 1.1第四站组成及结构: 由吸盘机械手、上下摆臂部件、料仓换位部件、工件推出部件、真空发生器、开关电源、可编程序控制器、按钮、I/O接口板、通讯接口板、多种类型电磁阀及气缸组成,主要完成选择要安装工件的料仓,将工件从料仓中推出,将工件安装到位。 1.吸盘机械手臂机构:机械手臂、皮带传动结构真空吸嘴组成。由上下摆臂装置带动其旋转完成吸取小工件到放小工件完成组装流程的过程。 2.上下摆臂结构:由摆臂缸(直线缸)摆臂机械装置组成。将气缸直线运动转化为手臂旋转运动。带动手臂完成组装流程。 3.仓料换位机构:由机构端头换仓缸带动仓位装置实现换位(蓝、黑工件切换)。 4.推料机构:由推料缸与机械部件载料平台组成。在手臂离开时将工件推出完成上料。 5.真空发生器:当手臂在工件上方时,真空发生器通气吸盘吸气。 5.I/O接口板:将桌面上的输入与输出信号通过电缆C1与PLC的I/O相连。 6.控制面板:完成设备启动上电等操作。(具体在按钮上有标签说明)。 1.2气动回路图
机电传动控制课程设计
机电传动控制课程设计 一、目录 引言 2 设计说明相关内容 (一)、课程设计题目 3 (二)、设计目的及要求 3 (三)、设计内容 4 一、控制方案设计 4 二、线路设计 4 三、控制电路的设计 6 四、元件的选取 6 五、柜体设计 8 六、结束语 11 七、参考文献 12
二、引言 《机电传动控制》课程是机械制造及其自动化专业的一门必修专业基础课,它是机电一体化人才所需电知识结构的躯体。在学习《机电传动控制》这门课程的时候,我能够深刻的体会到其重要性。作为机械类专业本基础教材,本课程涵盖了经典控制理论的基本原理和基本知识,内容与机械类课程现代控制理论相衔接。本书所讲内容突出机电结合,电为机用。在保证基本内容的前提下,简化理论分析,加强反映了当前机电领域的新技术和新知识,加强实例的分析、设计,力求做到内容深入浅出、重点突出,以利于我们开拓思路、深化知识。《机电传动控制》是机械设计制造及其自动化专业系列的教材之一,可以作为机械类专业及与之相近专业的同学们学习和研究。本课程不仅在于它是一门系统理论基础课程,是我们掌握控制论的基础知识,解决机械工程中的控制问题,更重要的是通过呵护唯物辩证法的方法论的建明阐述,使我们学会用控制理论观点,系统论方法,分析、处理机械工程中遇到的难题,启迪和发展我们的思维,培养我们分析问题和解决问题的能力。 由于现代科学和计算机技术的迅速发展,控制理论应用于机械工程的重要性日益明显。将理论联系实际,展开设计的课程设计实践,可以激发我们对该课程的学习兴趣而且能够让我们初步掌握系统性能分析及系统设计的基本方法,为专业课学习和参加控制工程实践打下必要的基础。由此可见,本次课程设计势在必行!
机电控制技术课程设计
《机电控制技术》课程设计指导书 第一节、课程设计的目的及要求 《机电控制技术》课程是高等院校机械电子工程专业比修一门专业基础课,可编程序控制器应用技术、单片机应用技术是机电控制技术的重要组成部分,也是工程技术人员用以实现各种控制功能的常规方法。结合《机电控制技术》这门课程,开设本课程设计,其目的是加强实践环节,让学生通过对从生产实践中精心提炼出来的具有典型意义课题进行系统设计、编程、调试,使得学生对如何设计和开发一个PLC或单片机应用系统有一定的感性认识,同时可培养和提高学生解决工程问题的能力,启发学生的创造性思维,从而改变以往学生遇到面宽一点、复杂程度大一点的机电结合型测控系统课题,就一筹莫展而不能进入角色的局面,并为他们以后的实际工作打下基础。通过本课程设计,要求学生能综合运用本课程的基础知识,进行融汇贯通的独立思考,在规定的时间内完成指定的设计任务。 第二节、汽车连杆半精镗专用机床PLC控制系统的设计 1、设计任务 设计一汽车连杆半精镗专用机床PLC控制系统,并用编程器调试、开发该系统的硬件和软件。 2、控制系统设计要求 汽车连杆半精镗专用机床由以下几个部分组成:左滑台、右滑台、左动力头、右动力头、工件定位夹具及液压站。图2为机床的大致轮廓。机床的左、右滑台动作及工件的定位夹紧都由液压提供动力。 左动力头 右 动 力 头定位夹具 左滑台右滑台 图2 机床轮廓 M 汽车连杆的加工工艺过程要求一面两销定位,同时装卡两件,两件同时加工。机床在原始状态,两件人工认销,认销完成后,首先同时按SB7、SB8启动循环,然后同时按SB1、SB2按钮,将工件夹紧(继电器YV5、YV7、YV9得电)。夹紧力到后(夹紧压力继电器SP0得电),进行拔销(YV11继电器得电)。拔销到位后SQ2继电器得电发出指示信号。接着右动力头在右滑台带动下快进(继电器YV1得电),同时右主轴启动(接触器KM1得电),右滑台快进一段距离,碰到工件后,液压系统内压力升高,(右滑台压力继电器SP1发出得电信号后),右滑台通过液压行程调速自动转为工进,同时镗工件的两个大孔和两个小孔,镗完孔到终点,碰到右滑台终点行程开关SQ3时,右滑台后退(继电器YV2得电)。右滑台碰到原位行程开关SQ4时,右主轴停止(KM1断电),同时左滑台带动左动力头快进(继电器YV3带动),与此同时,左主轴启动(左主轴接触器KM2得电)。当左滑台快进一段距离碰到加工工件后,液压系统压力升高(左滑台压力继电器SP2得电),左滑台通过液压行程阀自动调整为工进,加工左边的孔,碰到左滑台终点行程开关SQ5后,左滑台快退(继电器YV4得电)。左滑台退回原位,
机电传动控制
1. 引言 1.1 课程设计的目的: 电气控制系统是由各种低压电器和PLC 控制器按一定要求组成的控制系统。通过机电传动系统课程设计,进一步掌握各种低压电器和PLC 的结构原理、选用及使用;正确处理使用中出现的各种问题;了解器件和系统之间的关系;培养正确的设计思想、理论联系实际的工作作风、分析问题和解决问题的能力、运用标准与规范的能力、实事求是的科学态度和勇于探索的创新精神。 1.2 课程设计的内容及要实现的目标: 如图所示: 图1. 模型图 主要内容包括: 1. 设计出硬件系统的结构图、接线图、时序图等; 2. 系统有启动、停止功能; 3. 运用功能指令进行PLC 控制程序设计,并有主程序、子程序和中断程序; 4. 程序结构与控制功能自行设计; 5. 进行系统调试,实现机械手臂搬运加工流程的控制要求。 要实现的目标: 有两部机械对工作物进行加工,对象由输送带A 送到加工位置,然后由机械手将加工物送至工作台1的位置进行第一次加工,当第一步骤加工完成后,机械手臂将工作物夹
起送至工作台2进行第二步加工:当第二步骤加工完成后,机械手臂将工作物放到输送带B送走,然后由7段数码管显示加工完成的数量。 15 左移 ST4 14 上升 YA3 ST1 图2. 机械手工艺流程图 机械手工作前应位于原点,不同的位置分别装有行程开关。ST1为下限为开关,ST2为上限位开关,ST3为右极限位开关,ST3为左限位开关。 机械手的上、下、左、右移动以及工件的夹紧,均由电磁阀驱动气缸来实现。电磁阀YA1通电,机械手下降;电磁阀YA2通电,夹紧工件;电磁阀YA3通电,机械手上升;电磁阀YA4通电,电磁阀右移;电磁阀YA5通电,机械手左移。
机电传动控制课程设计报告
机电传动控制课程设计报 告 The Standardization Office was revised on the afternoon of December 13, 2020
引言 作为通用工业控制计算机,30年来,可编程控制器从无到有,实现了工业控制领域接线逻辑到存储逻辑的飞跃;其功能从弱到强,实现了逻辑控制到数字控制的进步;其应用领域从小到大,实现了单体设备简单控制到胜任运动控制、过程控制、及集散控制等各种任务的跨越。今天的可编程控制器正在成为工业控制领域的主流控制设备,在世界各地发挥着越来越大的作用。个人计算机(简称PC)发展起来后,为了方便,也为了反映可编程控制器的功能特点,可编程序控制器定名为Programmable Logic Controller(PLC),现在,仍常常将PLC简称PC。 可编程控制器的定义可编程控制器,简称PLC,是指以计算机技术为基础的新型工业控制装置。在1987年国际电工委员会颁布的PLC标准草案中对PLC做了如下定义:“PLC是一种专门为在工业环境下应用而设计的数字运算操作的电子装置。它采用可以编制程序的存储器,用来在其内部存储执行逻辑运算、顺序运算、计时、计数和算术运算等操作的指令,并能通过数字式或模拟式的输入和输出,控制各种类型的机械或生产过程。PLC及其有关的外围设备都应该按易于与工业控制系统形成一个整体,易于扩展其功能的原则而设计。 PLC具有通用性强、使用方便、适应面广、可靠性高、抗干扰能力强、编程简单等特点。PLC在工业自动化控制特别是顺序控制中的地位,在可预见的将来,是无法取代的。
1 PLC控制系统设计 PLC控制系统设计的基本原则 任何一种控制系统都是为了实现被控对象的工艺要求,以提高生产效率和产品质量。因此,在设计PLC控制系统时,应遵循以下基本原则: 1.最大限度地满足被控对象的控制要求 2.C控制系统安全可靠 3. 力求简单、经济、使用及维修方便 4. 适应发展的需要 PLC机型选择 随着PLC的推广普及,PLC产品的种类和型号越来越多,功能日趋完善。从美国,日本、德国等国家引进的PLC产品及国内厂商组装或自行开发的PLC 产品已有几十个系列。上百种型号。其结构形式、性能、容量、指令系统,编程方法、价格等各有不同,适用的场合也各有侧重。因此,合理选择PLC产品,对于提高PLC控制系统的技术经济指标起着重要作用。一般来说,各个厂家生产的产品在可靠性上都是过关的,机型的选择主要是指在功能上如何满足自己需要,而不浪费机器容量。PLC的选择主要包括机型选择,容量选择,输入输出模块选择、电源模块选择等几个方面。 1、可编程控制器控制系统I/O点数估算 I/O点数是衡量可编程控制器规模大小的重要指标。根据被控对象的输入信号与输出信号的总点数,选择相应规模的可编程控制器并留有10%~15%的I/O 裕量。估算出被控对象上I/O点数后,就可选择点数相当的可编程控制器。如果是为了单机自动化或机电一体化产品,可选用小型机,如果控制系统较大,输入输出点数较多,被控制设备分散,就可选用大、中型可编程控制器。 2、内存估计 用户程序所需内存容量要受到下面几个因素的影响:内存利用率;开关量输入输出点数;模拟量输入输出点数。 (1)内存利用率用户编的程序通过编程器键入主机内,最后是以机器语言的形式存放在内存中,同样的程序,不同厂家的产品,在把程序变成机器语言存放时所需要的内存数不同,我们把一个程序段中的接点数与存放该程序段所代表的机器语言所需的内存字数的比值称为内存利用率。高的利用率给用
机电控制技术课程设计报告书
机电控制技术课程设计报告书 1.1任务描述 本系统结构与工作原理如上图所示,纺织品由五个电动机带动辊子与橡胶辊的摩擦带动左向右传动。要求设计该系统的控制部分。本控制部分采用西门子S7-224PLC(继电器型)控制5个三相变频电机,实现纺织布料在该系统中自左向右的同步传动。 1.2 控制任务和要求 (1)确定本系统所需要的电气元件,并说明元件型号; (2)变频电机的转速范围0~1500r/min; (3)按下启动按钮,布料按一个初始速度自左向右运行; (4)一直按下升速按钮,布料运行速度持续上升(上升到上限不在上升);一直按降速按钮,布料运行速度持续下降(下降到下限不在下降); (5)按停止按钮,系统停止运行; 2 控制方案的选择 交流电机按品种分同步电机、异步电机两大类。 同步电机转子的转速n s与旋转磁场的转速相同,称为同步转速。n s与所接交流电的频率 (f)、电机的磁极对数(P)之间有严
格的关系 n s=f/P 在中国,电源频率为50HZ,所以三相交流电机中一对磁极电机的同步转速为3000转/分,三相交流电机中两对磁极电机的同步转速为1500转/分,以此类推。异步电机转子的转速总是低于或高于其旋转磁场的转速,异步之名由此而来。异步电机转子转速与旋转磁场转速之差(称为转差)通常在10%以内。 转差率 S=n0-n/n0(n0为同步转速,n为空载转速) 由此可知,交流电机(不管是同步电机还是异步电机)的转速都受电源频率的制约。因此,交流电机的调速比较困难,最好的办法是改变电源的频率。 本系统结构与工作原理如上系统联动控制图所示,纺织品由五个电动机带动辊子与橡胶辊的摩擦带动左向右传动。首先可以看出该系统属于同步开环控制,在布的同步传动中必须保证布在传动过程中始终被拉直,因此要求后一个电动机的转速比前一个电动机的转速高,但转速差不宜过大,否则会影响布的质量甚至会拉断布。由上述控制要求可知,本系统要求五个电机实现同步升速和同步降速,而且在升速和降速的过程中保持各个电机之间存在一个速度差,从而使绕过辊子的布保持一定的张力。如果在运行过程中出现紧急情况,可以实现紧急停车,从而把损害减小到最少。 为了实现上述功能,达到控制要求,经分析可知,选择变频调速的开环交流调速系统。理由如下: (1)提供的电源为工频50HZ的三相四线制的线电压为380V
电气控制课程设计
第一章水泵控制原理 1.1 供水系统的要求及控制线路的组成 1.1.1供水系统对水泵的要求 1.在高位水箱中设置水位信号器,由水位信号器控制水泵的自动运行。当高位水箱水位达到低水位时,生活水泵启动向高位水箱注水;当水箱中水位升至高水位时,自动关闭水泵。 2.为了保障供水的可靠性,生活水泵分为工作泵和备用泵;当工作泵发生故障时,备用泵应能自动投入(简称备泵自投)。 3.应有水泵电动机运行指示及自动、手动控制的切换装置、备用泵自动投入控制指示。 1.1.2控制线路的组成 该供水系统设置地下水池和高位水箱,地下水池设于大厦底层,高位水箱设于大厦顶层。水泵供水控制系统原理图如下图所示,图1-1为水泵电动机主电路、电源为交流380/220V;图1-2为控制电路,由水位信号控制回路、1#~2#电动机控制回路组成,控制电压分别为交流220v,直流380v.
1-1 生活水泵的电气控制主电路
1-2生活水泵的电气控制的控制电路
1.2小功率生活水泵的电气控制线路的工作原理分析 SA是万能转换开关(LW5系列),万能转换开关的操作手柄一般是多档位的,触点数量也较多。其触点的闭合或断开在电路中是采用展开图来表示,即操作手柄的位置用虚线表示,虚线上的黑圆点表示操作手柄转到此位置时,该对触点闭合;如无黑圆点,表示该对触点断开。转换开关触点闭合表如下表所示,用“×”表示触头闭合,无此标记表示触头断开。 转换开关触点闭合表 触点编号1号泵用 2号泵备 Z145° 手动S 0° 2号泵用 1号泵备 Z245° 1-2× 3-4× 5-6× 7-8× 9-10× 11-12× 13-14× 15-16× 1.2.1自动控制 将转换开关SA转至“Z1”位,其触点5-6、9-10、15-16接通,其它触头断开,控制过程如下。 1.正常工作时的控制 若高位水箱为低水位,干簧式水位信号器接点SL1闭合,回路1–3–5–2接通,水位继电器KA1线圈得电并自锁,其动合触头闭合,1–7点接通,109-107点接通,209–207点接通,则回路101–109–107–104–102接通,使接触器KM1线圈得电,KM1主触头闭合,使1号泵电动机M1启动运转。当高位水箱中的水位到达高水位时,水位信号器SL2动断触点断开,KA1线圈失电,其动合触头恢复断开,109-107点断开,KM1线圈失电,KM1主触头断开,使1号泵电动机M1脱离电源停止工作。 2.备用泵自动投入控制 在故障状态下,即使高位水箱的低水位信号发出,水位继电器KA1线圈得电,其动合触头闭合,但如果KM1机械卡住触头不动作,或电动机M1运行中保护电器动作导致电动机停车,KM1的动断触头复位闭合,9–11点接通,所以回路1–7–9–11–13–2接通,警铃HA发出事故音响信号,同时时间继电器KT线圈得电,经预先整定的时间延时后,备用继电器KA2线圈通电,其动合触头211–207接通,故回路201–211–207–204–202接通,使KM2线圈通电,其主触头闭合,备用2号泵M2自动投入。 由于线路对称性,当万能转换开关SA手柄转至“Z2”位时,M2为工作泵,M1为备用泵,其工作原理与SA位于“Z1”档类似。
《机电传动控制》期末考试重点总结
第三章、直流电机 1、机械传动系统负载特性:恒转矩型(反抗性恒转矩负载、位能性恒转矩负载)、离心式通风机型、直线型、恒功率型负载特性。 2、要加快电动机系统过渡过程,应设法减小系统飞轮转矩和增加动态转矩。 3、他励直流电动机 (1)、为什么直流电动机不能直接启动?直流电动机启动方法: 电动机启动之前,n=0,E=0,Ra很小。电动机直接并入电网并施加额定电压时,启动电流Ist=Un/Ra,为额定电流的10-20倍。①在换向过程中,产生危险的电火花,甚至烧坏整流子。 ②过大的电枢电流产生过大的电动应力,可能引起绕组的损坏。③产生与启动电流成正比的启动转矩,在机械系统和传动机构中产生过大的动态转矩冲击,使机械传动部件损坏。④对电网供电电动机来说,过大的启动电流将使保护装置动作,从而切断电源,使生产机械停止工作,或引起电网电压下降,影响其它负载正常运行。 启动方法:①降压启动②在电枢回路中串接外加电阻启动。 问:为什么要逐级切除启动电阻?如果切除太快,会带来什么后果? 如果启动电阻一下全部切除,在切除瞬间,由于机械惯性作用使电动机转速不能突变,再次瞬间转速维持不变。机械特性会转移到其他特性曲线上,此时冲击电流很大。如果切除太快,会有可能烧坏电动机。 (2)、调速:①改变电枢电路串接电阻Rad、(空载转速不变,随着电阻增加,转速降落增大,特性变软) ②改变电枢供电电压U、(空载转速随电压减小而减小,转速降落不变,特性硬度不变,恒转矩调速)③改变电动机主磁通φ(理想空载转速随磁通改变而改变,转速降落随磁通改变而改变,特性变软,恒功率调速) (3)、制动:反馈制动、反接制动(电源反接,倒拉反接制动)、能耗制动 4、问:一台直流电动机拖动一台卷扬机构,在重物匀速上升时将电枢电源反接,电动机经历了几种运行状态?①正向电动状态,由a到b特性曲线转变②反接制动状态,n降低,到达c点转速为零③反向电动状态,c→f,转速n逐渐反向增加④稳定平衡状态,到达f 平衡点,转速n不再变化 5、单相异步电动机采用定容分相式和罩极式法进行启动 第四章、交流电机 1、三相异步电动机 (1)、启动特性:启动电流大、启动转矩小。 启动方法:①直接启动、②电阻或电抗器降压启动、③Y-△降压启动、④自耦变压器降压启动、⑤软启动器------绕线异步电动机:逐级切除启动电阻法、频敏变阻器启动法。(2)、调速方法:①变极对数调速、②变转差率调速(调压调速、转子电路串接电阻调速)③变频调速(变压变频调速、恒压弱磁调速) (3)、制动方法:反馈制动、反接制动(电源反接,倒拉制动)、能耗制动 2、单相异步电动机启动:电容分相式异步电动机、罩极式单相异步电动机 3、同步电动机启动方法:异步启动法 4、三相异步电动机带动一定的负载运行时,若电源电压降低了,此时电动机的转矩、电流及转速有无变化?如何变化? 若电源电压降低, 电动机的转矩减小, 电流也减小. 转速不变. 5、结合交流异步电动机的机械特性分析,在负载转矩不变的情况下,当电源电压降低很多
机电传动控制课程设计报告
引言 作为通用工业控制计算机,30年来,可编程控制器从无到有,实现了工业控 制领域接线逻辑到存储逻辑得飞跃;其功能从弱到强,实现了逻辑控制到数字控制得进步;其应用领域从小到大,实现了单体设备简单控制到胜任运动控制、过程控制、及集散控制等各种任务得跨越。今天得可编程控制器正在成为工业控制领域得主流控制设备,在世界各地发挥着越来越大得作用。个人计算机(简称PC)发展起来后,为了方便,也为了反映可编程控制器得功能特点,可编程序控制器定名为Programmable Logic Controller(PLC),现在,仍常常将PLC简称PC、?可编程控制器得定义可编程控制器,简称PLC,就是指以计算机技术为基础得新型工业控制装置。在1987年国际电工委员会颁布得PLC标准草案中对PLC做了如下定义:“PLC就是一种专门为在工业环境下应用而设计得数字运算操作得电子装置。它采用可以编制程序得存储器,用来在其内部存储执行逻辑运算、顺序运算、计时、计数与算术运算等操作得指令,并能通过数字式或模拟式得输入与输出,控制各种类型得机械或生产过程。PLC及其有关得外围设备都应该按易于与工业控制系统形成一个整体,易于扩展其功能得原则而设 计、 PLC具有通用性强、使用方便、适应面广、可靠性高、抗干扰能力强、编程简单等特点。PLC在工业自动化控制特别就是顺序控制中得地位,在可预见得将来,就是无法取代得、 1 PLC控制系统设计 1。1PLC控制系统设计得基本原则 任何一种控制系统都就是为了实现被控对象得工艺要求,以提高生产效率与产品质量。因此,在设计PLC控制系统时,应遵循以下基本原则: 1.最大限度地满足被控对象得控制要求 2.C控制系统安全可靠 3、力求简单、经济、使用及维修方便 4、适应发展得需要 1.2 PLC机型选择 随着PLC得推广普及,PLC产品得种类与型号越来越多,功能日趋完善。从美国,日本、德国等国家引进得PLC产品及国内厂商组装或自行开发得
机电传动控制-课程设计任务书
机电传动控制 课程设计任务书(配套教材:《机电传动控制》;适用专业:机械设计制造及自动化) 指导教师:陶兆胜
10 20 30 40 30 60 70 80 $0 SECT* 课题一:十字路口交通信号灯 PLC 控制系统设计和调试 1. 控制要求: 系统工作受开关控制,起动开关 ON 则系统工作;起动开关 OFF 则系统停止工作。 东西方向左转弯绿灯两个,南北方向左转弯绿灯两个。 3. 控制规律: 1)高峰时段按时序图二(见附图)运行, 正常时段按时序图三(见附图)运行,晚上时段按提示警告 方式运行,规律为: 东、南、西、北四个黄灯全部闪亮, 其余灯全部熄灭,黄灯闪亮按亮0.4秒,暗0.6 秒的规律反复循环。 2)高峰时段、 正常时段及晚上时段的时序分配按时序图一运行 (见附图)。 0 1 2 3 4 5 6 7 8 9 10 11 12 13 14 15 16 17 18 19 20 21 22 23 24 小时, 时序圏二+ 00004 00001 L ——汕 G —SN+ 00000 R —SN+J 00005 L —E 阳 00006 G —EW 00007 ¥—E 阳2. 控制对象: 东 西方向红灯两个 东 西方向黄灯两个 东西方向绿灯两个 南北方向红灯两个, 南北方向黄灯两个, 南北方向绿灯两个,
时序图三 00004 R-E忙 ||| 00001 L——SN<-' _ im 00002 G—SM 00003 丫—SNa 00008 R—SN3 00005 L—EW*- 00006 G—EW 00007 Y—EWk 10 20 30 40 50 60 70 80 90 SEO1
机电传动控制课程设计
目录 1.设计题目及要求 (2) 2.可编程控制技术介绍 (2) 3.I/O电器接口图 (5) 4.流程图 (6) 5.控制系统梯形图 (7) 6.总结 (10) 参考目录 (10) 布料车控制系统程序设计 1.设计题目及要求: 布料车的工作行程按“进二退一”的方式往返行使于四个光电开关之间,使得物料在传送带上分布更加合理。布料车由三相交流异步电机驱动。 布料车可以实现单周期、连续两种种方操作式。 1.1单周期循环控制要求: 按下单周期循环控制按钮SB1,布料车由起始位置,即光电开关SQ1处,向右运行到光电开关SQ3处,然后向左回到光电开关SQ2处;再向右运动到行程开关SQ4处,再向左运动到光电开关SQ2处,然后向右运动到光电开关SQ3处,最后向左回到开始位置,光电开关SQ1处停止,完成单周期循环控制过程。 1.2连续循环控制要求: 按下连续循环控制按钮SB2,布料车将反复执行单周期循环控制过程,
按下停止按钮SB3后,布料车运行到开始位置,即光电开关SQ1处停止。要求循环50次后终止循环,发出声光简短报警,按停止按钮终止报警。 工艺流程图如下: 2可编程控制技术介绍 2.1 PLC的定义及特点 2.1.1 PLC的定义 可编程序控制器是一种数字运算操作的电子系统,专为在工业环境下应用而设计,它采用可编程序的存储器,用来在其内部存储执行逻辑运算、顺序控制、定时、计数和算术运算等操作命令,并通过数字式、模拟式的输入和输出,控制各种类型的机械或生产过程。可编程序控制器及其有关的外部设备,都应按易于与工业控制系统联成一个整体,易于扩充其功能的原则而设计。 2.1.2 PLC的特点 PLC是综合继电器接触器控制的优点及计算机灵活、方便的优点而设计制造和发展的,这就使PLC具有许多其他控制器所无法相比的特点。 (1)可靠性高,抗干扰能力强 (2)通用性强,使用方便 (3)采用模块化结构,使系统组合灵活方便 (4)编程语言简单、易学,便于掌握 (5)系统设计周期短 (6)对生产工艺改变适应性强 (7)安装简单、调试方便、维护工作量小 2.2 PLC的基本组成及工作原理 2.2.1 PLC的基本组成