基于MAXPAC闭式叶盘数控加工技术
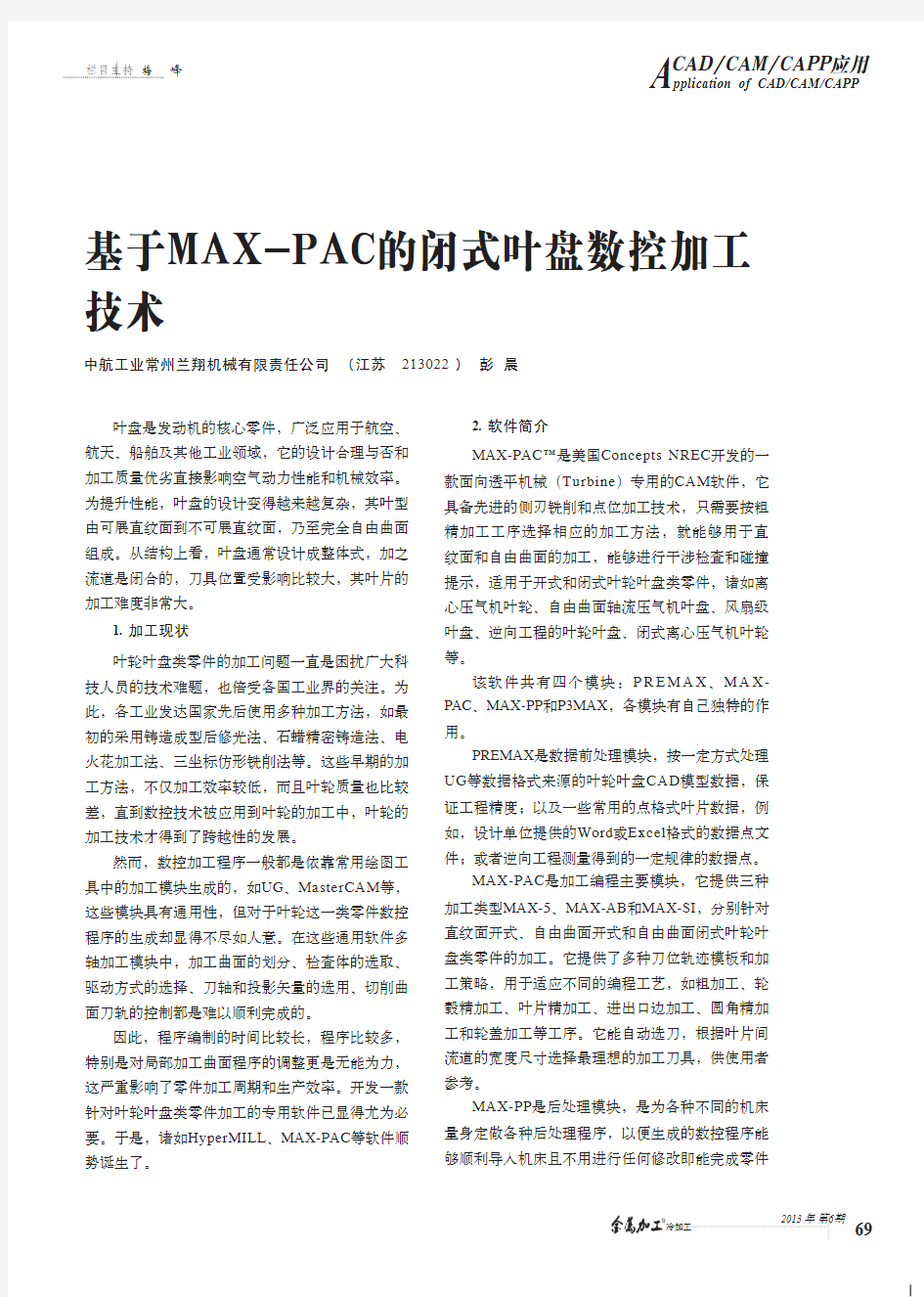

整体叶盘数控加工技术研究
第25卷第2期2004年3月航空学报 ACTA AERONAU TICA ET ASTRONAU TICA SIN ICA Vol 125No 12Mar 1 2004 文章编号:100026893(2004 022******* 整体叶盘数控加工技术研究 任军学, 张定华, 王增强, 刘维伟, 汪文虎 (西北工业大学现代设计与集成制造技术教育部重点实验室, 陕西西安710072 R esearch on the NC Machining T echnique of B lisk REN J un 2xue , ZHAN G Ding 2hua , WAN G Zeng 2qiang , L IU Wei 2wei , WAN Wen 2hu (The K ey Laboratory of Contemporary Design and Integrated Manufacturing , of China , Northwestern Polytechnical University , an , 摘要:。, 提出了一种整体, 、最佳刀轴方向的、加工变形处理和叶片与刀具减振技术等。给, 证明了所提方法的先进性和有效性。关键词:; 五坐标数控加工; 刀轴方向; 变形与振动控制中图分类 号:V261文献标识码:A Abstract :Blisk is a new integrated structure of blades and disk actually used in the aero 2engine of high thrust 2weight ratio. Based on the study of the state 2of 2the 2art of the Blisk manufacturing technology worldwide , a convenient manufacturing process and key technique of 52axis NC machining are proposed in this paper , Such novelties include analyses of blisk 2tunnel feature and partition of manufacturing area , determination of optimal orientation of cutter axis and its refinement , efficient rough 2cutting of the tunnel , high 2precision shaping , control of Blisk distortion and vibration
数控加工专业课程安排
数控加工专业课程安排
数控加工专业 课程安排符合学生全面发展及市场需求说明 随着全球经济一体化的发展趋势,大批境外企业的涌入,中国正在逐步变成“世界制造中心”。机械制造业传统的加工方式,已逐步被数控应用技术的加工方式所取代,从大批量的生产规模到单件小批的生产规模,数控加工均被广泛采用。由于数控技术迅速发展,相关数控技术的人才培养已成为各种层次学校的热点。我校也于2005年开办了数控加工专业,配备了师资力量,花巨资引进数控设备,建立了实验室、实习场所、绘图及模拟软件机房。为了提高学校教学质量,保证经过我们培养的技工学校学生能够适应市场需求,我们组织的相关教务负责人、招生就业合作处及专业教师进行市场调查,并将结果进行分析。分析结果说明我校数控加工专业课程设置、实习项目、主干课程较好的符合了学生全面发展及市场需求。说明如下: 一、原始调查资料 1、企业对我校数控专业的毕业生的评价简要概况 序号评价项目评价结果 1 企业对我校数控加工专业毕业生 的称职情况综合评价为17%优良,83%称职,0%不称职 2 企业对毕业生的职业道德的评价5%好,95%较好,0%一般,0%差 3 企业对毕业生专业业务知识的评 价 4.7%好,9 5.3%较好,0%一般,0%差4 企业对毕业生的基本素质的评价8.4%好,91.6%较好,0%一般,0%差
2、学生就业情况的调查简况1)就业岗位分布情况 操作编程维修工艺生产 管理 质量 检测 综合营销 行政 管理 其他 55.7% 13.4% 9.4% 8.0% 7.1% 4.5% 1.2% 1.7% 1.4% 5.5% 2)毕业生工作岗位上最有用的课程 机械加工工艺数控 编程 计算机 应用 数控 机床 构造 公差配 合 机械 制图 AUTOC AD Pro/e 切削 原理 与刀 具 机床 夹具 39.2% 53.1% 32.3% 31.5% 25.% 45.0% 32.3% 31.6% 5.5% 45.% 3、企业对学校技工学校数控专业毕业生的需求简况 1)“蓝领层”“蓝领层”是指在生产岗位上承担数控机床的具体操作及日常简单维护工作的技术工人,在企业数控技术岗位中占75%,是目前需求量最大的数控技术人才。 所需知识与能力结构:掌握数控机床结构的基本知识和机械加工与数控加工的工艺知识,具备数控机床的操作、日常维护和手工编程的能力,了解数控加工的自动编程。 2)、“灰领层”“灰领层”是指在生产岗位上承担数控编程的工艺人员和数控机床维护、维修人员,这类人员在企业数控技术岗位中占20%,其中数控编程工艺员占9%,数控机床维护、维修人员占11%。 所需知识与能力结构: 数控编程工艺员:掌握数控加工工艺专业知识和一定的模具制造基础知识,具备数控机床的操作、日常维护和手工编程的能力,能运用至少一种三维CAD/CAM软件进行三维造型和自动编程。
【CN109650924A】基于SiC纤维陶瓷基复合材料整体涡轮叶盘制备方法【专利】
(19)中华人民共和国国家知识产权局 (12)发明专利申请 (10)申请公布号 (43)申请公布日 (21)申请号 201910139569.9 (22)申请日 2019.02.26 (71)申请人 西北工业大学 地址 710072 陕西省西安市友谊西路127号 (72)发明人 刘持栋 刘小冲 刘永胜 董宁 孙肖坤 刘小瀛 陈博 成来飞 (74)专利代理机构 西北工业大学专利中心 61204 代理人 王鲜凯 (51)Int.Cl. C04B 35/80(2006.01) C04B 35/565(2006.01) C04B 35/571(2006.01) F01D 5/02(2006.01) F01D 5/28(2006.01) (54)发明名称 基于SiC纤维陶瓷基复合材料整体涡轮叶盘 制备方法 (57)摘要 本发明公开了一种基于SiC纤维陶瓷基复合 材料整体涡轮叶盘制备方法,用于解决现有整体 涡轮叶盘制备方法实用性差的技术问题。技术方 案是首先采用平面极坐标织造方法制备涡轮叶 盘预制体单元层,使得经向和纬向两个主应力方 向上有连续SiC纤维,然后采用Z向穿刺、缝合和 模压,完成预制体定型,再利用化学气相渗透法 在预制体的SiC纤维表面制备BN界面层,采用化 学气相渗透工艺对涡轮盘预制体预致密化,在多 轴数控机床上采用立方氮化硼或金刚石特种刀 具涡轮盘叶片进行加工,最后制备防氧化涂层。 由于预制体经向和纬向两个主应力方向上有连 续SiC纤维,提高了整体涡轮叶盘的承载性能,缩 短了整体涡轮叶盘的制备周期, 实用性好。权利要求书1页 说明书5页 附图1页CN 109650924 A 2019.04.19 C N 109650924 A
数控加工技术及设备
数控加工技术及设备 1 、CAM(计算机辅助制造)技术的历史与发展 计算几何理论的不断完善和数控技术的不断更新是CAM技术持续发展的物质基础,工业界对数控加工技术不断提出需求是CAM技术发展的原动力,CAM软件厂商之间的激烈竞争是CAM技术发展的催化剂。CAM技术从诞生到现在,可以划分为三个阶段: 1.1、加工质量稳定、加工精度高。 最早出现的CAM软件是50年代开发的平面编程系统,60年代发展到具有曲面编程能力的系统,80年代出现了具有图形交互的雕塑曲面编程能力的系统。在数控机床和数控技术出现以前,同一套图纸,在不同的加工车间,产品表面质量差异大,即使是同一个工人,加工相同的零件,其质量也不尽相同。当加工曲线、曲面以及精密孔时,对加工精度的要求就更加迫切了。有了数控机床,加工同一种零件,使用同一段数控代码,加工质量稳定。后来,发展了曲面造型技术,人们设计产品,不再仅仅满足产品的功能需求,开始追求产品的外观和更好的性能,大量使用复杂曲面进行产品设计。因此,产品的加工精度被提到首要地位。 1.2、加工效率高、产品更新换代快。 产品生产的趋势是多品种、小批量,制造业的目标是降低成本、提高质量、缩短制造周期。对制造业,尤其是对模具加工业来说,就是要在保证模具加工精度的前提下,充分利用数控机床的性能,提高加工效率,缩短加工时间,保证产品及时上市。为满足高效率的需求,出现了三轴、四轴、五轴甚至更多联动轴的机床。CAM技术也随之发展。各软件厂商纷纷推出多轴数控加工系统。近年来,绝大多数关于NC的文章都是围绕多轴刀具轨迹生成和干涉检查与修正展开讨论的。这是CAM技术发展的第二个阶段。
关于涡轮叶片尺寸稳定性的实验调查范文
关于涡轮叶片尺寸稳定性的实验调查 摘要:本文介绍的是涡轮叶片简易蜡模尺稳定性的实验研究。由于超级合金制作的涡轮叶片,具有严格的尺寸和形位公差。叶片由熔模铸造制作而成,包括压蜡、制壳、脱蜡、浇注及后处理完成。压蜡阶段的尺寸准确性如同后处理工序一样,对最终的叶片尺寸也有很大的影响。此项实验工作的重点是在射蜡阶段,调查过程参数及叶片形位要素对关键尺寸收缩造成的影响。为了降低分析和模具制造的复杂性,按照叶片形状设计了两种模型。一副模具上带有两个穴(形成两个蜡模)。选取射蜡温度和射蜡时间作为可变过程参数。结果会发现,对叶片的弯曲度和不规则的厚度的影响有明显的不同。射蜡时间比射蜡温度起了更加主要的影响。 1.介绍 燃气涡轮的作用是把热能转化为机械能。适用于很多工业领域,如泵,过滤,提纯,发电机及运输。燃气涡轮的一个关键组成部分就是叶片,包括可转动的叶片及静止叶片。叶片在困难运行条件下发挥作用,如高温,高机械压力,高热疲劳或腐蚀性环境等等。涡轮叶片尺寸及形位公差都很小,是由超级合金采用熔模铸造的方式生产出来的。此工序是用于生产高质量、形状复杂的产品。熔模铸造特别是用在,当产品用其他制作方式如锻造或是加工的方法生产时,不划算,不实用,或是不可行的情况。 熔模铸造主要工序包括压蜡、制壳、脱蜡、干燥、浇注及修磨。每一步都对最终产品尺寸有一定的影响,而压蜡和浇注是最主要的影响。 用于做模型的材料,必须有以下特点:底粘度、一定的固体强度,低混合、低收缩率、高稳定性、并且对于制壳用料有化学抗性、有可接合性并且对健康无害。而蜡恰恰具有了以上所有特性,于是被选为做模型的材料。 蜡模的最终尺寸,在射蜡阶段会受到以下因素影响:1)蜡料种类,2)形状,3)过程参数。 从另一方面来说,仅知道所选蜡料的线性(体)收缩率,是不足以预知尺寸的最终结果的。 产品形状和过程参数对最终尺寸具有相当的影响。 蜡与半结晶状热塑聚合物具有类似的性质。它们也有不一样的特点:1)低熔点(100摄氏度以下) 2)低热传导性。3)对高加热速率敏感。 压蜡包括以下几个阶段:1)把固体蜡放入一个用油来加工的容器里溶化。。2)把溶化的蜡传送到射蜡机的桶里。3)用射蜡机把蜡射入模具里。3)冷却蜡模。最后4)取出蜡模。(通常接下来的工序是校正工序)如果校正要求达到既定的尺寸,那或者增加生产周期或者使用更多的工装,无论是哪种方式,都会增加熔模铸造的总成本。图形1展示的是一个典型的射蜡机的简图。 过程参数对最终尺寸影响的程度,会由于叶片的复杂形状受到影响。因此,这就是要进行
整体叶盘数控加工技术研究
文章编号:1000-6893(2004)02-0205-04 整体叶盘数控加工技术研究 任军学,张定华,王增强,刘维伟,汪文虎 (西北工业大学现代设计与集成制造技术教育部重点实验室,陕西西安 710072) Research on the NC Machining Technigue of Blisk REN Jun-xue ,ZHANG Ding-hua ,WANG Zeng-giang ,LIU Wei-wei ,WANG Wen-hu (The Key Laboratory of Contemporary Design and Integrated Manufacturing Technoiogy ,Education Ministry of China , Northwestern Poiytechnicai University ,Xi*an 710072,China ) 摘 要:整体叶盘是高推比航空发动机采用的新结构。分析了国际同类整体叶盘制造技术,提出了一种整体 叶盘复合制造工艺方案及五坐标数控加工的关键技术,包括叶盘通道分析与加工区域划分、最佳刀轴方向的确定与光顺处理、通道的高效粗加工技术、型面的精确加工技术、加工变形处理和叶片与刀具减振技术等。给出了该研究成果在预研型号中的应用实例,证明了所提方法的先进性和有效性。关键词:整体叶盘;五坐标数控加工;刀轴方向;变形与振动控制中图分类号:V261 文献标识码:A Abstract :Biisk is a new integrated structure of biades and disk actuaiiy used in the aero-engine of high thrust-weight ratio.Based on the study of the state-of-the-art of the Biisk manufacturing technoiogy woridwide ,a convenient manufacturing pro-cess and key technigue of 5-axis NC machining are proposed in this paper ,Such noveities inciude anaiyses of biisk-tunnei feature and partition of manufacturing area ,determination of optimai orientation of cutter axis and its refinement ,efficient rough-cutting of the tunnei ,high-precision shaping ,controi of Biisk distortion and vibration reduction of cutter and biade.Preiiminary resuits of cutting test verify the vaiidity of the technigues mentioned above. Key words :biisk ;5-axis NC machining ;cutter axis orientation ;controi of distortion and vibration 近年来,国外航空发达国家在新型航空发动机结构设计中采用了称之为整体叶盘(biisk )的最新结构。与传统的叶片和轮盘装配结构相比,整体叶盘将叶片和轮盘设计成一个整体,省去了榫头、榫槽和锁紧装置,避免了榫头气流损失、减少了结构重量和零件数量;在气动布局上采用了宽弦、弯掠叶片和窄流道,从而提高了气动效率。由于整体叶盘使发动机结构大为简化,推重比和可靠性进一步提高,因而在新研制的第四代战斗机所配套的高推比发动机上得到了成功的应用。 1国内外整体叶盘制造技术现状 从目前所收集到的资料来看[1] ,国外采用的 整体叶盘结构形式主要有如图1所示的3种典型结构:(a )闭式结构———带箍整体叶盘;(b )开式结构———不带箍整体叶盘;(c )大小叶片转子结构———开式结构中大叶片间含有小叶片。 由于整体叶盘是高速旋转部件,既要达到减重和精确平衡要求,又要提高疲劳强度,因而其制 造技术难度特别大。整体叶盘毛坯一般采用钛合 图13种典型整体叶盘结构Fig.1 Three typicai structures of biisk 收稿日期:2003-06-17;修订日期:!!!!!!!!!!!!!!!!!!!!!!!!!!!!!!!!!!!!!!!!!!!!!!!!!!!!!!!!!!!!! 2003-12-15 第25卷第2期航空学报 Voi.25No.22004年3月ACTA AERONAUTICA ET ASTRONAUTICA SINICA Mar.2004
数控加工技术实训报告
数控加工技术实训报告 Company number:【WTUT-WT88Y-W8BBGB-BWYTT-19998】
数控加工技术实训报告 班级:机械1111 学号: 姓名:倪浩然 专业:机械设计制造及其自动化 指导老师:殷振 时间过得真快,为期15天的数控加工技术实训就结束了。在老师个耐心讲解和鼓励下,我从总体上达到了实习预期的目标和要求。这次总实习给了我一次全面的、系统的实践锻炼的机会,巩固了所学的理论知识,增强了我的实际操作能力。在这次实训中,我从中懂得理论与实际的结合的重要性。也让我学到了很多书本之外的知识,让我受益匪浅。 实训的第一天我怀着激动的心情来到了实验楼。第一天我们的任务就是对数控机床进行熟悉。一共有四台机床:华中数控机床、北一数控铣床、沈一数控车床、沈一加工中心。经过老师的讲解和指导书的介绍我们初步了解:数控机床的类型、基本结构及工作原理;加工特点和应用;数控系统的的基本操作;还有就是对数控机床的外观和结构建立感性认识。老师向我们介绍了数控车床的操作面板上主要按钮的功能,还向我们演示了加工程序的输入、编辑、初步认识数控车床加工程序。同时还现场动手演示了“回零”、“点动”、“步进”等操作……下面我就数控机床的数控机床的组成、特点及分类进行详细的说明: 1、数控机床的组成:现代数控机床都是CNC机床,一般由数控系统和机床本体组成,主要有如下几部分组成。
1)CNC装置:计算机数控装置(即CNC装置)是CNC系统的核心,有微处理器(CPU)、存储器、各I/O接口及外围逻辑电路等构成。 2)数控面板:数控面板是数控系统的控制面板,主要有显示器和键盘组成。通过键盘和显示器实现系统管理和对数控程序及有关数据进行输入和编辑修改。3)可编程逻辑控制器PLC:PLC是一种以微处理器为基础的通用型自动控制装置,用于完成数控机床的各种逻辑运算和顺序控制。例如:主轴的启停、刀具的更换、冷却液的开关等辅助动作。 4)机床操作面板:一般数控机床均布置一个机床操作面板,用于在手动方式下对机床进行一些必要的操作,以及在自动方式下对机床的运行进行必要的干预。上面布置各种所需的按钮和开关。 5)伺服系统:伺服系统分为进给伺服系统和主轴伺服系统。进给伺服系统主要有进给伺服系统单元和伺服惊电机组成,用于完成刀架和工作台的各项运动;主轴伺服系统用于数控机床的主轴驱动,一般由恒转调速和恒功率调速。为满足某些加工要求,还要求主轴和进给驱动能同步控制。 6)机床本体:机床本体的设计与制造,首先应满足数控加工的需求,具有刚度大、精度高、能适应自动运行等特点,由于一般均采用无级调速技术,使得机床进给运动和主传动的变速机构被大大简化甚至取消,未满足高精度的传动要求,还采用滚珠丝杆、滚动导轨等高精度传动件。未提高生产率和满足自动加工的要求,还采用自动刀架及能自动更换工件的自动夹具等。 2、数控机床的特点:由于数控机床是计算机自动控制同精密机床两者之间的相互结合,使得它具有高效率、高精度、高柔性等特点。
涡轮叶片
涡轮叶片的作用、结构特点 和发展趋势 涡轮叶片一般指涡轮工作叶片和导向叶片。工作叶片的外型结构由叶身、缘板、过渡段、榫齿等组成,内型结构包括横向肋、纵向肋、找流柱和积叠轴。导向叶片由外缘板、叶身和内缘板构成。 涡轮是处于燃烧室后面的一个高温部件,燃烧室中产生的高温高压燃气首先经过燃气导向叶片,此时会被整流并通过在收敛管道中将部分压力能转化为动能而加速,最后被赋予一定的角度以更有效地冲击涡轮工作叶片。 涡轮叶片处于温度最高、应力最复杂、环境最恶劣的部位,被誉为“王冠上的明珠”。在涡轮发动机中叶片无论是压气机叶片还是涡轮叶片,它们的数量最多,而发动机就是依靠这众多的叶片完成对气体的压缩和膨胀,以及以最高的效率产生强大的动力来推动飞机前进的工作。涡轮叶片是一种特殊的零件,它的数量多,形状复杂,要求高,加工难度大,而且是故障多发的零件,一直以来各发动机厂的生产的关键。 目前航空发动机涡轮叶片都采用空心结构。就是在涡轮叶片上设计了很多细小的管道,可以使高压冷空气通过这些管道流经高温叶片,起到强制冷却作用,以提高涡轮的耐热性能。 为了提高航空发动机中燃气涡轮的效率,增加航空发动机推重比,就必须提高发动机燃烧室出口燃气温度也即涡轮前的进口温度。也就必须提高涡轮叶片(导叶+动叶)的高温性能。为此,人们在涡轮叶片设计、高温材料的研制、冷却方法研究及表面涂层等方面作了大量的工作。 在涡轮材料方面,近期的发展方向是:定向共晶合金、超单晶合金、机械合金化高温合金,远期的是人工纤维增强高温合金、定向再结晶氧化物弥散强化合金以及新的能承受高温度的材料如金属间化合物及复合材料,碳-碳复合材料,陶瓷和陶瓷基复合材料。未来的发动机将大量采用非金属材料。 在制造工艺和结构上,现在国外在探索更高性能水平的单晶对开和扩散连接的叶片和多孔层板叶片制造技术,这种加工技术可使涡轮进口温度进一步提高。由小孔加工发展的铸造冷却技术使得在涡轮叶片上铸造出0.25mm的气膜孔成为可能,单晶精密铸造、真空扩散焊和优良的表面防护及处理等工艺技术的发展保证了涡轮叶片经过设计越来越精细。 随着快速成型技术在精密铸造领域的应用发展,可以用快速成型制造的原型替代蜡型,在其表面上涂挂耐火材料,然后焙烧,使原型材料烧蚀气化后得到铸壳,用于金属零件的烧
数控加工工艺毕业设计论文
日照职业技术学院毕业设计(论文) 数控加工工艺 姓名 : 付卫超 院部:机电工程学院 专业:数控设备应用与维护 指导教师:张华忠 班级: 11级数控设备应用与维护二班 2014年05月
随着数控技术的不断发展和应用领域的扩大,数控加工技术对国计民生的一些重要行业(IT、汽车、轻工、医疗等)的发展起着越来越重要的作用,因为效率和质量是先进制造技术的主体。高速、高精加工技术可极大提高效率,提高产品的质量和档次,缩短生产周期和提高市场竞争能力。而对于数控加工,无论是手工编程还是自动编程,在编程前都要对所加工的零件进行工艺分析,拟定加工方案,选择合适的刀具,确定切屑用量,对一些工艺问题(如对刀点、加工路线等)也需要做一些处理,并在加工过程掌握控制精度的方法,才能加工出合格的产品。 本文根据数控机床的特点。针对具体的零件,进行了工艺方案的分析,工装方案的确定,刀具和切屑用量的选择,确定加工顺序和加工路线,数控加工程序编制。通过整个工艺的过程的制定,充分体现了数控设备在保证加工精度、加工效率、简化工序等方面的优势。 关键词工艺分析加工方案进给路线控制尺寸
第1章前言-----------------------------------第2页第2章工艺方案的分析-------------------------第3页 2.1 零件图-------------------------------第3页 2.2 零件图分析---------------------------第3页 2.3 零件技术要求分析---------------------第3页 2.4 确定加工方法-------------------------第3页 2.5 确定加工方案-------------------------第4页第3章工件的装夹-----------------------------第5页 3.1 定位基准的选择-----------------------第5页 3.2 定位基准选择的原则-------------------第5页 3.3 确定零件的定位基准-------------------第5页 3.4 装夹方式的选择-----------------------第5页 3.5 数控车床常用的装夹方式---------------第5页 3.6 确定合理装夹方式---------------------第5页第4章刀具及切削用量-------------------------第6页 4.1 选择数控刀具的原则-------------------第6页 4.2 选择数控车削刀具---------------------第6页 4.3 设置刀点和换刀点---------------------第6页 4.4 确定切削用量-------------------------第7页第5章轴类零件的加工-------------------------第8页 5.1 轴类零件加工工艺分析-----------------第8页 5.2 轴类零件加工工艺---------------------第11页 5.3 加工坐标系设置-----------------------第13页 5.4 保证加工精度方法---------------------第14页 参考文献 ---------------------------------第15页
《数控加工技术》模拟考题
《数控加工技术》模拟考题 (闭卷考) 一、选择题(5*4分=20分) 1.闭环控制系统的位置检测装置装在______ A数控装置中 B 机床移动部件上C伺服电动机轴上 D 传动丝杠上 2.FMS是指_____ A 自动化工厂 B 计算机数控系统 C 柔性制造系统 D 数控加工中心 3.在数控机床的闭环控制系统中,其检测环节具有两个作用,一个是检测出被测信号的大小,另一个作用是把被测信号转换成可与______进行比较的物理量,从而构成反馈通道。A偏差信号B脉冲信号 C 指令信号D反馈信号 4.加工中心是在数控铣镗床或数控铣床的基础上增加_____装置改型设置成的。 A 刀库与自动换刀 B 自动换刀 C 刀库 D 伺服 5.数控系统所规定的最小设定单位是______ A 数控机床的运动精度 B 机床的加工精度; C 脉冲当量 D 数控机床的传动精度 参考解答:BCCAC 二、填充题(5*4分=20分) 1.按数控系统的控制方式分类,数控机床分为________,__________,__________。2.数控机床的精度主要包括______,_______,_______。 3.机床工作时会产生哪两种形式的振动_______,_______。 4.未来数控机床发展趋势主要表现在哪三个方面_______,_______,_______。 5.数控系统常用的两种插补功能是_______和_______。 参考解答: 1、开环控制数控机床、半闭环控制数控机床、闭环控制数控机床。 2、加工精度、定位精度、重复定位精度 3、强迫振动与自激振动 4、数控技术,数控系统,驱动系统 5、直线插补和圆弧插补 三、简答与计算(共60分)(每题分5、10、15分/题不等) 1.简述数控机床的特点与主要组成部分。 2.数控机床按照轨迹控制方式和伺服控制方式可以分为几类? 3.用逐点比较法插补如图所示对于第一象限圆弧AB,起点A(4,0),终点B(0,4),并给出简要步骤。 4.…………。 5.…………。 6.…………。
涡轮叶片精铸全过程
涡轮叶片精铸全过程及其影响因素 无余量熔模精密铸造目前为涡轮叶片制造的最佳手段。其工艺流程主要包括型芯模具的设计与制造、压制型芯、蜡模模具的设计与制造、装配注蜡、涂浆制壳、干燥型壳、脱蜡、烧结、浇注金属、脱壳脱芯、激光打孔等环节。 模具的设计定型:1、精铸模具型腔体设计,首先建立叶片零件模型,包括叶身、缘板、榫头伸根的内型特征,以此构建叶身实体。此后进行叶片的多态模型转化,由叶片零件模型转化到型腔体模型。2、型腔优化及精铸仿真,根据铸件的收缩原理采用反变形优化工艺方法对型腔进行放型最终得到模具型腔。3、精铸模具结构设计与制造,确定核心包络块并设计叶片精铸模具模架,再由模具标准件经机械加工、表面处理、装配、检测、修模到定型。模具结构的合理性和尺寸精度对于熔模精铸件十分重要。设计制造高质量的内外型模具即精铸模具就成为精密熔模铸造技术的关键。 陶瓷型芯的制造:在叶片蜡型压制之前是需制作设计陶瓷型芯模具,并压制合格陶瓷型芯。陶瓷型芯的制备包括浆料的配制、型芯压制、型芯素肧的修理、烧结、强化及其过程质量控制与检验等。决定浆料性能的因素有陶瓷粉料的成分与颗粒形状、增塑剂的成分和性质、粉料和增塑剂的比例等。陶瓷型芯的质量很大程度上取决于素胚的压制质量,压制压力、锁模压力、浆料温度、保压时间等是影响陶瓷型芯压制质量的主要原因。 蜡模的制造工艺:合格的蜡型是制备精密铸件的前提,压制蜡型时,将陶芯放入蜡型模具中,并依靠定位元件对其定位。生产中大多采用压力把糊状模料压入压型的方法制造熔模。压制蜡基模料时,分型剂可为机油、松节油等;分型剂层越薄越好,使熔模能更好地复制压型的表面,提高熔模的表面光洁度。模料压制温度、压注压力、保压时间、压型温度、和模力、分型剂种类及其用量,以及制模和存放熔模的环境都会影响蜡模的质量。 熔模铸型的制造工艺:首先是熔模的组装,把形成铸件的熔模和形成浇冒口系统的熔模组合在一起,主要采用焊接法,用薄片状的烙铁,将熔模的连接部位熔化,使熔模焊在一起。后再经过若干次涂料、挂砂,干燥硬化,密封加固,脱蜡,焙烧最终制成型壳。型壳的性能与质量取决于面层与加固层材料的性能、相应涂挂工艺和过程控制。
整体叶盘精密电解加工工艺
埃马克电化学公司关于整体叶盘精密电解加工 工艺综述面向未来的技术 EMAG ECM GmbH- A PECM Cost-Saving Approach to Blisk Manufacturing EMAG ECM GmbH, 2012 Abstract 摘要 整体叶盘的出现是为了满足市场的需求,与传统转子叶片和轮盘分离的装配式叶盘相比,由于减少了传统连接中的榫头,榫槽等装配零件,叶轮边缘负载降低,重量减轻 高达30%,同时由于避免了榫头气流损失也即减少动力消耗,从而也提高气动效率并 显著提高功率,有助于减少燃油消耗和废气排放。追溯其发展历史最初应用到高压压 气机以及商用压气机末端上。是现代燃气涡轮发动机中最具创新和挑战的零部件。 The emergence of BLISK(Bladed integrated Disk) is in order to meet the market demand calls, comparing with conventional separable assembled rotor blades and disk counterparts, due to the reduction in the conventional connector assembly parts of the disk lugs, blade root groove, etc.; the rim load lower. The essential advantages are that they reduce weight up to 30% as well as reduce aerodynamic losses by avoiding disk lugs air leakage flows, thus improve aerodynamic efficiency and the power output, specially it enables reduce in fuel consumption and exhaust gas volume emissions. Retracing the history of Blisk development, it’s application initially used in high-pressure compressors and commercial compressors. It is the most innovative and challenging components of modern gas turbine engine. 图1: 整体叶盘模拟图 Fig. 1: CAD Blisk
数控加工技术专业培养目标
数控加工技术专业培养目标 一、职业岗位分析 随着科学技术和经济的不断发展,数控机床正以其高速度、高效率、高精度的优势逐步代替普通机床,成为制造业的主力。因此,社会对数控加工技术方面的高级专门人才的需求也越来越迫切。数控加工技术专业就是为适应这种情况而设立的。本专业主要是培养学生掌握金属切削加工的基本理论知识和工艺规程的编制方法,夹具的设计方法,数控设备的使用、维护和维修,能熟练使用数控机床和其他数控设备进行产品加工的高等应用性专门人才。 数控加工技术专业的就业岗位: 1、在工业企业中的数控车间或班组中,进行手工和计算机编制数控加工程序,能熟练的 进行产品加工并能解决加工中出现的问题; 2、在工业企业中的机加工车间从事工艺方面的技术工作,能进行零件加工工艺规程的编 制和常用工装设计; 3、数控机床(数控车床、数控铣床、加工中心和其它数控设备)的操作、使用、维护及 维修; 4、技术部门、车间、班组及其它基层和中层的管理工作等。 二、培养目标与专业要求 1.培养目标本专业培养德、智、体全面发展,牢固掌握必要的文化科学基础知识和数控机床加工技术方面的专业知识,有较强实践能力,具有爱岗敬业,踏实肯干,勇于创新,与人合作的良好品德,能适应社会主义市场经济需要的实用型高级人才。毕业生具有数控机床加工的工艺工装设计和编程能力,能熟练地操作数控机床进行产品加工,能够进行数控机床的安装、调试、维护与维修,也可以从事车间生产与技术管理工作。 2.专业基本要求 (1)掌握工程技术所必需的基础学科理论知识; (2)掌握本专业所必需的计算机基础知识和较强的计算机应用能力; (3)掌握机械工程基础知识,掌握机械加工工艺、工艺准备的基本知识; (4)掌握数控机床的工作原理与结构、数控机床编程的基本知识,能够进行中等复杂程
航天发动机涡轮叶片主要冷却方式综述
航天发动机涡轮叶片主要冷却方式综述 航天发动机是为航空器提供飞行所需动力的发动机。有3种类型:①活塞式航空发动机。早期在飞机或直升机上应用的航空发动机,用于带动螺旋桨或旋翼。大型活塞式航空发动机的功率可达2500千瓦。后来为功率大、高速性能好的燃气涡轮发动机所取代。但小功率的活塞式航空发动机仍广泛地用于轻型飞机、直升机及超轻型飞机。②燃气涡轮发动机。应用最广。包括涡轮喷气发动机、涡轮风扇发动机、涡轮螺旋桨发动机和涡轮轴发动机,都具有压气机、燃烧室和燃气涡轮。涡轮螺旋桨发动机主要用于时速小于800千米的飞机;涡轮轴发动机主要用作直升机的动力;涡轮风扇发动机主要用于速度更高的飞机;涡轮喷气发动机主要用于超声速飞机。③冲压发动机。特点是无压气机和燃气涡轮,进入燃烧室的空气利用高速飞行时的冲压作用增压。它构造简单、推力大,特别适用于高速高空飞行。由于不能自行起动和低速下性能欠佳,限制了应用范围,仅用在导弹和空中发射的靶弹上。 参考发动机工作原理,我们知道,在燃烧室产生温度极高的气体,通过涡轮叶片把内能转化成机械能,所以涡轮叶片承受着很大的温度。我们知道,温度过高会对涡轮叶片的性能和寿命都有不利的影响,尽管现在的高温材料已经取得了很大的成就,但是相对于从燃烧室出来的气体的温度,还远远不够。于是,我们必须采取其他的措施来使冷却发动机的涡轮叶片。 目前应用最广的冷却方式主要有一下几种: 一:对流冷却。靠液体或气体的流动来传热的方式叫对流。根据冷却介质的不同,分为水冷系统和风冷系统。这是一种最简单的冷却方式,冷却剂流过受热零件壁面,靠对流传热将热量带走,如对着受热壁面喷射冷却剂以提高对流冷却的效果。对流冷却广泛用于发动机的各种受热零、组件。航天发动机的涡轮叶片采用空气对流冷却,可使叶片温度降低200~250°C。如果流过冷却套的推进剂由喷管末端一周小孔直接排出,排放射流也能产生一部分推力。 二:冲击冷却。冷气通过细小的冲击孔,以很高的速度冲击到叶片内壁面,对内壁面进行有效的冷却。冲击冷却比一般对流冷却效果高出好几倍,由于它这种特殊的方式,大多用来冷却受热最严重而冷却条件又差的领域。[1]三:气膜冷却。在壁面附近沿一定方向向主流喷人冷气,这股冷气在主流的压力和摩擦力作用下向下游弯曲。粘附在壁面附近,形成温度较低的冷气膜,将壁面同高温燃气隔离,并带走部分高温燃气或明亮火焰对壁面的辐射热量,从而对壁面起到良好的保护作用,这种冷却方式就是气膜冷却。最初有关气膜冷却的研究是Wieghardt为解决机翼的防冻所做的二维槽缝热气喷射,航空燃气轮机出现后,人们发现可以喷射冷气对高温部件进行冷却,这种技术首先被用于燃烧室中。到七十年代,气膜冷却开始被运用到涡轮叶片上。由于涡轮前温度的不断升高,对叶片的冷却也日益关键,气膜冷却的研究很快展开,成为涡轮叶片外表面的重要冷却技术。通常影响气膜冷却效果的因素有:①气膜孔的几何参数,比如气膜孔的喷射角度、孔径的大小、孔长与孔径的比、孔的间距、孔排数亦即孔出口的形状;②孔的气动参数,比如主流速度、吹风比、冷气流与主流的动量比、主流湍流度、气膜孔前边界层发展情况、压力梯度等。该冷却技术的效果可达
先进航空发动机用高温钛合金双性能整体叶盘的制造
34航空制造技术·2019年第62卷第19期先进航空发动机用高温钛合金 双性能整体叶盘的制造 蔡建明1,李 娟1,田 丰2,叶俊青2 (1. 中国航发北京航空材料研究院,北京 100095; 2. 贵州安大航空锻造有限责任公司,安顺 561005) [摘要] 钛合金整体叶盘是先进航空发动机压气机系统的典型轻质高效结构。整体叶盘零件工作时,叶片和盘承受不同的热力条件,采用“双性能”代替传统的“均质”设计,是提高压气机转子减重效果及满足愈加严苛且多变的温度和载荷工作条件使用的有效措施。对比分析了两种“梯度热处理”工艺,即分区控温梯度热处理工艺和局部包覆控时梯度热处理工艺制备钛合金双性能整体叶盘的可行性,评估了叶片、盘及过渡区的显微组织控制能力。试验结果表明:两种工艺均能在钛合金整体叶盘的叶片与盘之间的过渡区形成稳定可控的温度梯度,得到双重组织,即叶片为双态组织,盘为细小的片层组织,过渡区位置和尺寸可控,显微组织呈渐变特征。可根据整体叶盘锻件的外形特点和组织性能要求,选用适合的制备工艺及相应的工艺参数。 关键词: 钛合金双性能整体叶盘;分区控温梯度热处理;局部包覆控时梯度热处理 DOI:10.16080/j.issn1671–833x.2019.19.034 同使用性能情况下,通过以钛代镍,可实现约40%的减重效果[3],且钛合金转子相对降低了对压气机轴的载荷作用,从而可以提高发动机的推重比和使用可靠性。与传统榫齿连接结构相比,采用整体叶盘结构可以显著提高发动机的部件减重效果,提高压气机空气增压效率和气动稳定性,并可避免榫齿连接结构因叶片榫头与盘榫槽接触区域发生微动磨损引发疲劳失效的风险。航空发动机压气机整体叶盘工作时,叶片和盘承受的温度条件和应力条件有着显著差异,相对而言,叶片工作温度高、应力小、振动频率大,主要承受离心拉应力和高频振动应力的综合作用,且有受到外物冲击的可能,因此应重点考虑叶片的拉伸强度、高周疲劳和抗外物冲击性能;盘承受高的 先进航空发动机高推重比、高增压比、高涡轮前温度及低油耗目标的实现,除了采用先进的结构设计和精准的强度计算外,还强烈依赖于轻质耐热钛合金材料及高效轻量整体叶盘结构的综合应用。传统钛合金受航空发动机压气机转子部件高温、高压、高速工作状态引起的蠕变、保载疲劳、氧化、钛火等因素的制约,长时工作温度不能超过600℃[1–2],典型的600℃高温钛合金有英国IMI834及我国Ti60等。与国内其他常用航空钛合金如TC11、TA19、TC17相比,Ti60钛合金在500℃以上有显著的蠕变性能优势,适用于高压压气机后段的整体叶盘、机匣等部件。在 400~600℃温度区间,与GH4169镍 基高温合金相比,Ti60钛合金的比 强度和比疲劳强度有优势,在获得相蔡建明 工学博士,高级工程师,主要从事 航空发动机用高性能高温钛合金的科 研工作。在国内外学术期刊上发表论 文30余篇。
数控加工技术专业个人求职简历
数控加工技术专业个人求职简历 数控加工技术专业个人求职简历数控加工技术专业个人求职简历姓名:王xx性别:男学历:大专工作年龄:4年出生年月:1984-5民族:汉族籍贯:xxxx登记时间:2010-2-2317:27:10 最高学历:大专毕业学校:xx市职业技术学院所学专业:数控加工技术掌握外语:英语政治面貌:群众登记时间:2010-2-2317:27:10 教育经历: 2003年9月至2006年6月xx市职业技术学院数控加工技术 2000年9月至2003年6月xx市小越中学 工作年龄:4年能力与专长:喜欢学习新事物,动手能力强,善于交际,能融入群体和睦相处,具备一定的管理能力,能熟练运用企业ERP系统,woRD和EXCEL等软件,且有较强的上进心,对事对物严于律己,拥有驾驶执照。工作经历: 2006年3月至2007年3月台湾建德工业集团xx荣德机械有限公司NC技师大型数控加工设备售后维修及管理 2007年6月至2010年2月东莞市亚力通电子科技有限公司市场部业务特助全程负责全国oE订单的接洽、跟进以及售后管理,与客户建立好关系,及时满足客户的售后需求,全国各地出差等个人简介:本人之前在学校学习机械类专业,从事售后维修及管理,后从事全国oE订单的业务管理,计划,生产以及售后管理。具体为:从产品的设计开发至样品跟踪确认,到正式订单下达后的物料控制,
再到产线的管控和及时出货,最终的货款跟催等全程服务。 希望工作类型壹:市场专员/助理希望工资待遇:面议希望工作类型:全职希望工作地点:xx县意向提交时间:2010/2/23 其它工作要求:我的自荐书:本人能吃苦耐劳,敬业爱岗,好进心强,学习能力强,愿与贵司一起打造美好未来希望工作类型贰:市场经理希望工资待遇:面议希望工作类型:全职希望工作地点:xx县意向提交时间:2010/2/23 其它工作要求:我的自荐书:本人能吃苦耐劳,敬业爱岗,好进心强,学习能力强,愿与贵司一起打造美好未来希望工作类型叁:销售经理希望工资待遇:面议希望工作类型:全职希望工作地点:xx县意向提交时间:2010/2/23 其它工作要求:我的自荐书:本人能吃苦耐劳,敬业爱岗,好进心强,学习能力强,愿与贵司一起打造美好未来
涡轮叶片的材料和制造工艺
涡轮叶片的材料和制造工艺 涡轮叶片是航空发动机的关键件,其承受温度的能力是评价发动机性能和决定发动机寿命上的重要因素,为了使涡轮叶片获得高耐温能力,应从两方面进行考虑:铸造工艺和叶片材料。 涡轮叶片的工作环境极其恶劣,一方面叶片的工作温度很高,对于航机的涡轮进口温度最高已达1950℃,因此要求叶片材料在高温下应具有较高的持久强度和蠕变强度,足够的韧性,良好的抗热疲劳和机械疲劳性能,以及较高的抗高温氧化和抗热腐蚀能力。另一方面,由于叶片承受温度的不均匀性,使其存在很高的热应力,并且燃机在变工况时将承受很大的热冲击,所以要求叶片拥有耐热冲击能力。随着大推力、高效率、长寿命的涡轮发动机的发展,需要不断提高涡轮进口燃气温度,为适应这一要求,无论叶片结构还是叶片材料都应不断改进以提高其耐高温能力。 无余量熔模精密铸造目前为涡轮叶片制造的最佳手段。其工艺流程主要包括型芯模具的设计与制造、压制型芯、蜡模模具的设计与制造、装配注蜡、涂浆制壳、干燥型壳、脱蜡、烧结、浇注金属、脱壳脱芯、激光打孔等环节。 模具的设计定型:1、精铸模具型腔体设计,首先建立叶片零件模型,包括叶身、缘板、榫头伸根的内型特征,以此构建叶身实体。此后进行叶片的多态模型转化,由叶片零件模型转化到型腔体模型。2、型腔优化及精铸仿真,根据铸件的收缩原理采用反变形优化工艺方法对型腔进行放型最终得到模具型腔。3、精铸模具结构设计与制造,确定核心包络块并设计叶片精铸模具模架,再由模具标准件经机械加工、表面处理、装配、检测、修模到定型。模具结构的合理性和尺寸精度对于熔模精铸件十分重要。设计制造高质量的内外型模具即精铸模具就成为精密熔模铸造技术的关键。 陶瓷型芯的制造:在叶片蜡型压制之前是需制作设计陶瓷型芯模具,并压制合格陶瓷型芯。陶瓷型芯的制备包括浆料的配制、型芯压制、型芯素肧的修理、烧结、强化及其过程质量控制与检验等。决定浆料性能的因素有陶瓷粉料的成分与颗粒形状、增塑剂的成分和性质、粉料和增塑剂的比例等。陶瓷型芯的质量很大程度上取决于素胚的压制质量,压制压力、锁模压力、浆料温度、保压时间等是影响陶瓷型芯压制质量的主要原因。 蜡模的制造工艺:合格的蜡型是制备精密铸件的前提,压制蜡型时,将陶芯放入蜡型模具中,并依靠定位元件对其定位。生产中大多采用压力把糊状模料压入压型的方法制造熔模。