结构强度与振动试验报告

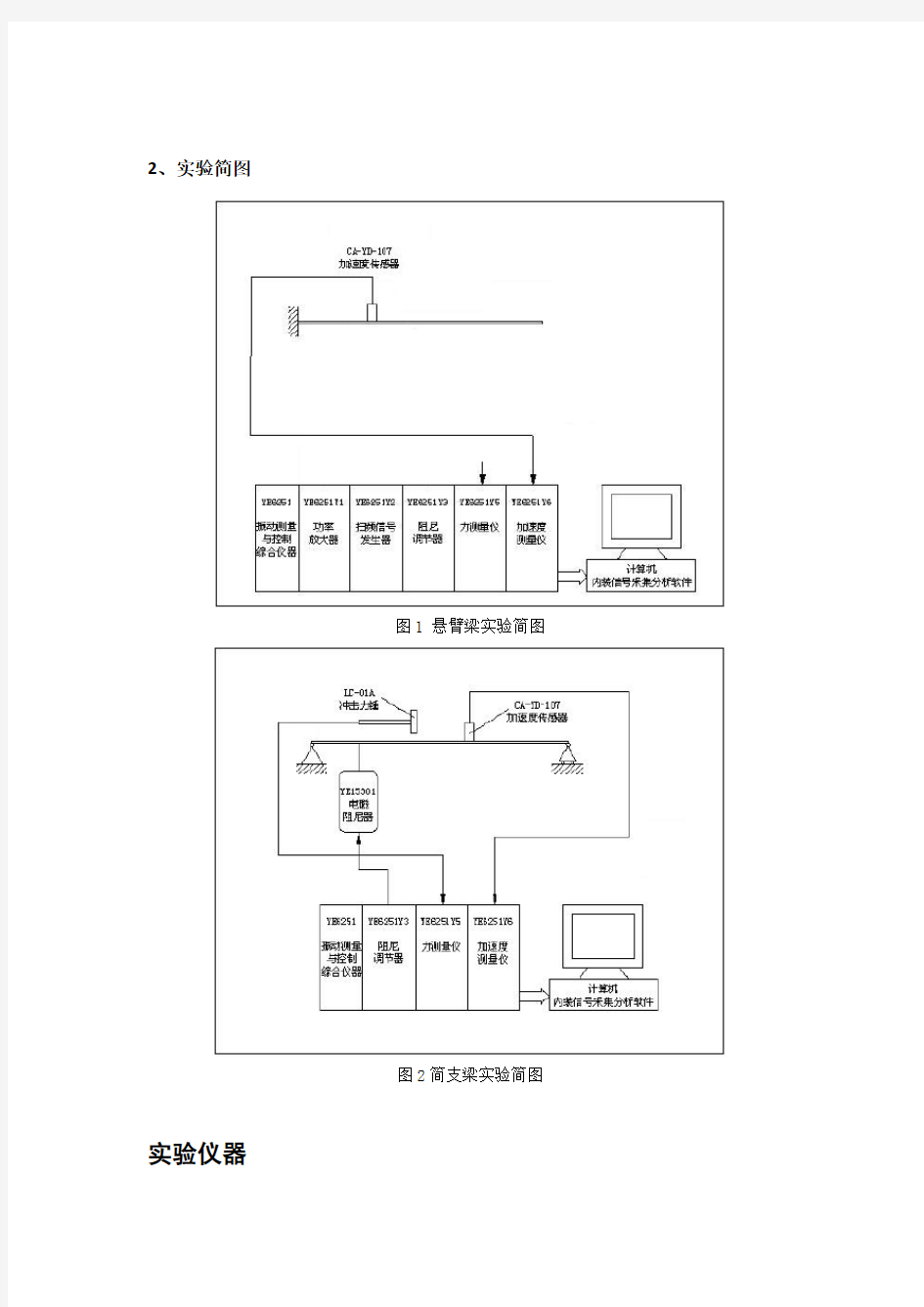
梁的振动实验报告
实验目的
改变梁的边界条件,对比分析不同边界条件,梁的振动特性(频率、振型等)。对比理论计算结果与实际测量结果。正确理解边界条件对振动特性的影响。
实验内容
对悬臂梁、简支梁进行振动特性对比,利用锤击法测量系统模态及阻尼比等。
实验原理
1、固有频率的测定
悬臂梁作为连续体的固有振动,其固有频率为:
()1,2,.......r r l r ωλ==其中, 其一、二、三、四阶时, 1.87514.69417.854810.9955.....r l λ=、
、、 简支梁的固有频率为:
()1,2,.......r r l r ωλ==其中 其一、二、三、四阶时, 4.73007.853210.995614.1372.....r l λ=、
、、 其中E 为材料的弹性模量,I 为梁截面的最小惯性矩,ρ为材料密度,A 为梁截面积,l 为梁的长度。
试件梁的结构尺寸:长L=610mm, 宽b=49mm, 厚度h=8.84mm. 材料参数: 45#钢,弹性模量E =210 (GPa), 密度ρ=7800 (Kg/m 3)
横截面积:A =4.33*10-4 (m 2),
截面惯性矩:J =3
12
bh =2.82*10-9(m 4)
则梁的各阶固有频率即可计算出。
2、实验简图
图1 悬臂梁实验简图
图2简支梁实验简图实验仪器
本次实验主要采用力锤、加速度传感器、YE6251数据采集仪、计算机等。图3和图4分别为悬臂梁和简支梁的实验装置图。图5为YE6251数据采集仪。
图3 悬臂梁实验装置图
图4 简支梁实验简图
图5 YE6251数据采集分析系统
实验步骤
1:"在教学装置选择"中,选择结构类型为"悬臂梁",如果选择等份数为17,将需要测量17个测点。
2:本试验可采用多点激励,单点响应的方式,如果是划分为17等份,请将拾振
点放在第5点。
3:请将力锤的锤头换成尼龙头,并将力通道的低通滤波器设置为1KHz,将拾振的加速度通道的低通滤波器设置为2KHz。
4:用力锤对第1点激振,对应的激励为f1,响应为1,平均3次,对应的数据为第1批数据,以此类推,测量完全部测点。
5:选择"教学装置模态分析和振型动画显示",调入测量数据进行分析。6:"在教学装置选择"中,选择结构类型为"简支梁",如果选择等份数为17,将需要测量17个测点。重复2—5的步骤,得到简支梁的试验数据和结果。
实验数据记录和整理
图6 悬臂梁的传递函数幅值和相位
图7 悬臂梁的固有振型、频率和阻尼比
图8 简支梁的传递函数幅值和相位
图9 简支梁的固有振型、频率和阻尼比
单自由度系统的动力吸振实验
实验目的
通过对单自由度系统施加动力吸振器,减小其振动量,观察实验现象,灵活掌握动力减振实验方法。
实验内容
基于二自由度反共振原理设计动力吸振的基本理论,测试单自由度系统的固有频率,了解动力吸振器设计过程,采用动力吸振器后单自由度系统的减振效果。实验对象和装置
实验步骤
1、将系统安装成单自由度无阻尼系统。
2、将激振器对准单自由度系统,将信号源设置为输出正弦信号。
3、在固有频率附近调节信号源的频率,观察输出幅值为最大时的频率为单自由度系统的共振频率,同时记下加速度的幅度。
4、将吸振块安装于第二个质量块上,用电涡流传感器对准此质量块,打开一个FFT视图,并调节附加质量块杆的长度使其与上面的单自由度系统的固有频率一致(本次实验无法调节一致,按照最接近的频率进行实验)。
5、将吸振块安装于第一个质量块上,打开信号源让其对第一质量块激振,这时记录下加速度的幅度。
实验数据记录和整理
调节信号发生器输出为25mA,连续调节激振器的频率,由振幅图像可知频率在41.8Hz附近时振幅达到最大值,振幅随时间的变化图像如图1所示。系统加上吸振器之后,在激振器频率为41.8Hz时,得到振幅随时间变化的图像如图2所示。
图1 频率为41.8Hz时振幅随时间的变化图像
图2 加上激振器之后振幅随时间的变化图像
实验分析
单自由度系统在固有频率下发生共振,产生较大的响应幅值。接入吸振器后,系统成为二自由度振动系统,在原固有频率正弦激励信号下,可以发现原系统的振动幅值大大减小,达到吸振目的。理论上,当吸振器的固有频率和单自由度系统的固有频率相等时,原系统振幅为零。
转子临界转速测量实验
实验目的
1.观察转子在亚临界、临界及超临界的工作情况。
2.计算转子的理论临界转速,并与实测值作比较
3.分析研究在实验中产生的各种物理现象,了解影响转子临界转速的各种因素。
4.熟悉实验设备及其操作方法;熟悉软件应用。
实验原理
转速测量:本实验系统采用的是光电转速传感器,在转轴上贴有反光条,转轴每转动一周光电转速传感器感应一个脉冲。此脉冲就是键相位,反光条所在的位置就是振动相位零角度对应的实际位置。同时,转速脉冲信号输入测量系统的转速输入通道用于转速测量。转速的测量可以通过计数器测量单位时间内键相位脉冲的个数得到(计数法),可以测量2个键相位脉冲之间的时间T得到(测周期法)。
振动传感器:旋转机械的振动测量有多种传感器,其中电涡流传感器为非接触式,用于直接测量旋转轴的振动位移。
振动测量模块可以给电涡流振动位移传感器提供工作电源、对反馈的振动信号进行测量、分析。
等角度数据采集:不同于一般数据采集系统的是旋转机械的振动数据采集必须保证等角度,即:在转子的每个转动周期T内采集Kph 个数据,称之为等角度采样或称整周期采样。
轴心轨迹:旋转机械振动实验的一个突出特点。在旋转轴的水平、
垂直两个方向分别安装两只互相垂直的位移传感器,两路信号分别输入示波器的X、Y轴,可以合成显示转轴轴心的运转轨迹。实验中采用软件中的重采样时间波形,即可看到转子轴心轨迹。
实验步骤
1.测量参数设置
分析模式:瞬态
阶次上限:64X
阶次分辨率:0.125X
转速控制:通过转速控制数据采集的进行
起始转速:1000rpm
结束转速:6000rpm(应大于临界转速)
转速间隔:50rpm
显示阶次:1X (显示工频振动)
2、调出Bode 图的相频曲线
首先建立显示Bode 图的幅频曲线窗口,在Bode 图窗口中点击鼠标右键,选择“图形属性”弹出右边的对话框。进入“坐标”,在右下“Y轴”选项下拉菜单中选择“相频”
3、显示转速
由主菜单“显示”中选择“转速显示”,调出转速显示框,显示框大小、位置可调整。
4、测试
由主菜单“控制”中选择“启动采样”,进入数据采集。
5、记录每次测量的结果,撰写实验报告。
实验数据记录和整理
图1为临界转速是的数据图,转速为4016r/min。图2为各个转速下的db 图。
图1
图2
有关材料数据及理论公式
1.
无盘有重轴的临界转速轴cr ω
ρ
πωA EJ l 2
2
=
轴cr 式中:J —截面的惯性矩,464
d J π
=
,其中d=0.0095m 为转轴的直径;
l 为跨度,l=0.24m ;E —弹性模量,210GPa ;ρ—转子材料密度:
7800kg/3
m ;A —转轴的截面积,2d A π=
4,2m
2. 单盘无重轴的临界转速盘cr ω
盘
盘m c
=
cr ω 式中:c —装盘处的刚性系数,3
l
48EJ c =,2
m N ;其中E 、J 、l 同前式 盘m --盘的质量,0.8kg 3.
单盘均质轴转子的临界转速cr ω
2cr 2cr 2cr
1
1
1
盘
轴
ω
ω
ω
+
=
cr cr n ωπ
30
=
式中:cr n --理论计算临界转速,rpm 。
经计算可得,临界转速为5536r/min
实验分析
经试验得出的临界转速为4016r/min,而经过理论计算得出的临界转速为5536r/min,两者有较大的差距,但仍在可接受的范围内,实验仪器和外界的干扰对试验的影响较大。
材料疲劳实验
实验目的
通过材料试验机对某一材料进行疲劳动强度测试,观察实验现象,掌握动强度实验中试件设计和试验设计的过程。
实验内容
对某一材料(金属或复合材料)进行疲劳实验的试件设计,说明试件设计的力学原理,对不同的试验设计方法(如力、位移、应变控制下的加载方式)进行分析,对实验现象和实验结果进行分析。
实验观摩
本次观摩的实验为疲劳裂纹预制实验,掌握金属材料的裂纹扩展抗力,即断裂韧度。只要满足小范围屈服和平面应变条件,断裂韧度就不再与试样或结构的几何尺寸形状有关,而仅为材料的常数。它表征材料所固有的平面应变裂纹扩展抗力。由于它代表了实际结构中最常见和最危险的裂纹顶端约束情况,所以平面应变断裂韧度在安全设计中有重要地位。
实验过程
开机程序:
1、打开总电源,打开UPS电源。
2、打开冷却水电源,并设置冷却方式为“自动”,
3、打开MTS控制器。
4、打开计算机,点击“开始”,打开“Station Manager”。选择适合的站并打开,设置各种参数。
5、打开硬件油源开关,按“Reset”键复位。
6、点击计算机程序中的“reset”,复位软件,打开软件油源,可以听到油源被开启的声音。
7、调节安装架位置,安装试件及其各种附属装置。
8、检查各种试验参数和试验件安装无误后,开始运行试验程序。
进行试验:
1、将软件中的“Manual Controls”中的“Control Mode”设置为“Displacement”
位移模式,见图1。
2、输入最高幅值2.5kN,最低幅值0.5kN的正弦拉力,记录循载次数,观察应变值的变化趋势。
3、当应变曲线变化基本恒定时,如图2,卸下试件,做微观裂纹检查和分析,见图3。
关机程序:
1、关闭软件上的油源,保存各种试验数据,依次关闭子程序和主程序,关闭主机及其显示器电源。
2、关闭MTS控制器。
3、关闭硬件油源,关闭UPS电源。
4、将冷却水运行方式设置为“停止”,关闭冷却水电源。
5、关闭总电源。
图1:软件界面
图2:应变曲线
图3:微观检查
对金属材料来说,即使在平面应变条件下,裂纹开始扩展(启裂)并一定试样就会立即失稳断裂。这是因为在裂纹前端存在塑性区。裂纹扩展要产生塑性变形,会导致材料加工硬化,必须要增大外载,裂纹才会继续扩展。这种扩展叫稳态扩展,或慢扩展。但当载荷继续增加达到某一临界点后,即使载荷不再增加,裂纹也能自动向前扩展直到断裂。
试样设计
现根据GBT228.1-2010《金属材料拉伸试验》设计一个圆形横截面比例试样,比例系数取65.5=k 。设计其平行长度的原始直径为mm d 100=,试样采用机加工成型,平行长度和夹持头部过渡弧半径mm d r 5.775.00=≥,这里取mm r 10=。原始标距mm d L 50500==,平行长度mm d L L c 552/00=+≥,这里取mm L c 60=。试样采用圆柱形夹持头部,端面直径为mm d 150=,实验时采用楔形夹头夹持试样,试样总长度mm d L L c t 10040=+>,这里取mm L t 105=。根据上述试样设计尺寸,利用AutoCAD 绘图软件画出试样如图4。
图4