关键元器件和材料的验证控制程序
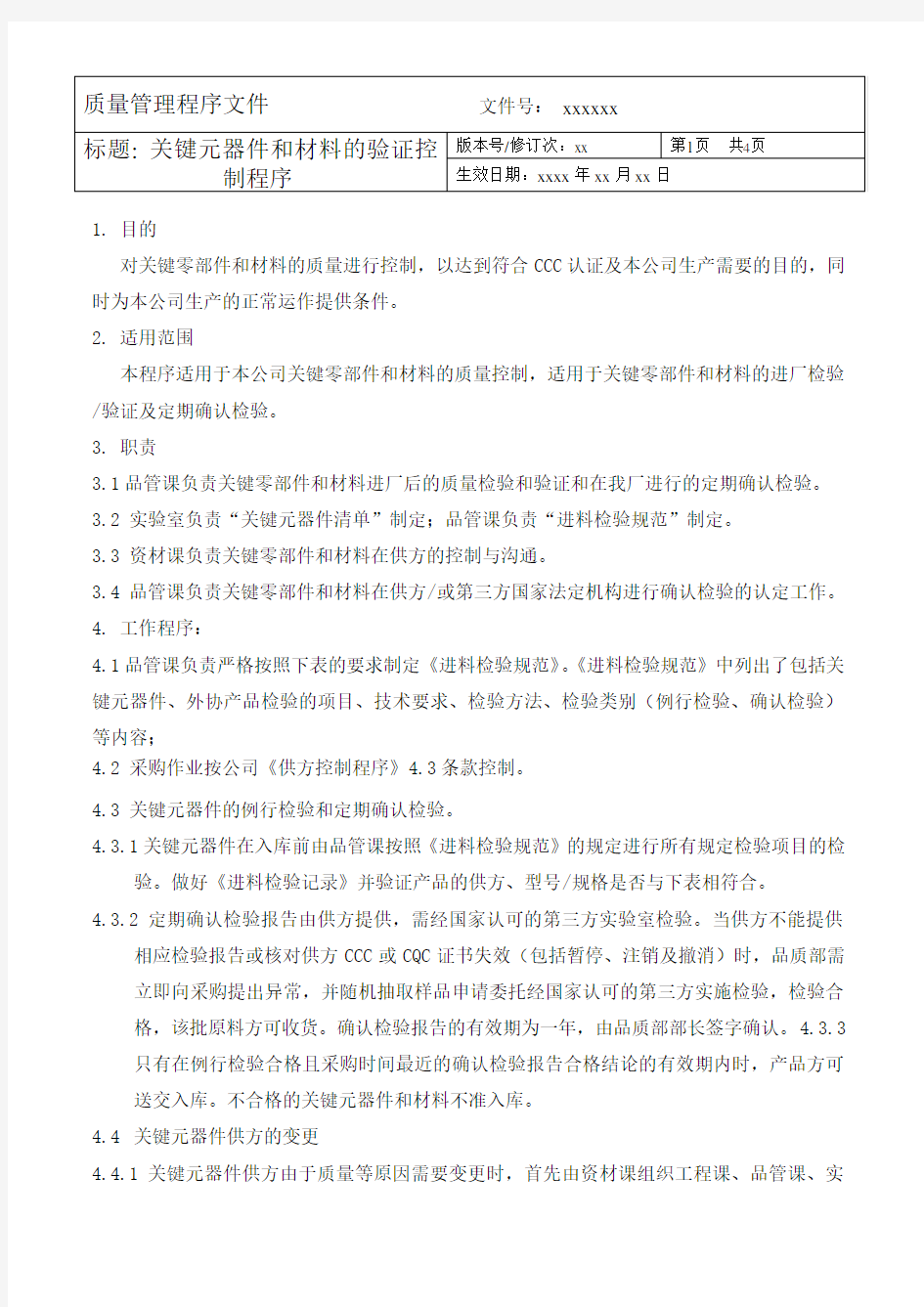
质量管理程序文件文件号:xxxxxx
标题:关键元器件和材料的验证控
制程序版本号/修订次:xx 第1页共4页生效日期:xxxx年xx月xx日
1. 目的
对关键零部件和材料的质量进行控制,以达到符合CCC认证及本公司生产需要的目的,同时为本公司生产的正常运作提供条件。
2.适用范围
本程序适用于本公司关键零部件和材料的质量控制,适用于关键零部件和材料的进厂检验/验证及定期确认检验。
3.职责
3.1品管课负责关键零部件和材料进厂后的质量检验和验证和在我厂进行的定期确认检验。
3.2 实验室负责“关键元器件清单”制定;品管课负责“进料检验规范”制定。
3.3 资材课负责关键零部件和材料在供方的控制与沟通。
3.4 品管课负责关键零部件和材料在供方/或第三方国家法定机构进行确认检验的认定工作。
4.工作程序:
4.1品管课负责严格按照下表的要求制定《进料检验规范》。《进料检验规范》中列出了包括关键元器件、外协产品检验的项目、技术要求、检验方法、检验类别(例行检验、确认检验)等内容;
4.2 采购作业按公司《供方控制程序》4.3条款控制。
4.3 关键元器件的例行检验和定期确认检验。
4.3.1关键元器件在入库前由品管课按照《进料检验规范》的规定进行所有规定检验项目的检
验。做好《进料检验记录》并验证产品的供方、型号/规格是否与下表相符合。
4.3.2 定期确认检验报告由供方提供,需经国家认可的第三方实验室检验。当供方不能提供
相应检验报告或核对供方CCC或CQC证书失效(包括暂停、注销及撤消)时,品质部需立即向采购提出异常,并随机抽取样品申请委托经国家认可的第三方实施检验,检验合格,该批原料方可收货。确认检验报告的有效期为一年,由品质部部长签字确认。4.3.3只有在例行检验合格且采购时间最近的确认检验报告合格结论的有效期内时,产品方可送交入库。不合格的关键元器件和材料不准入库。
4.4关键元器件供方的变更
4.4.1关键元器件供方由于质量等原因需要变更时,首先由资材课组织工程课、品管课、实
关键元器件和材料定期确认检验控制程序
质量体系文件 关键元器件和材料定期确认检验控制程序 发行部门:品质部 文件编号:YXD-QP-04 版本:A1 编制: 审核: 批准: 2010年01月22日发布 2010年02月01日实施
一、目的
对关键元器件和材料的检验/验证及定期确认检验,保证关键元器件的产品质量持续达到认证产品要求。 二、范围 本程序适用于认证产品的关键元器件和材料的检验/验证及定期确认检验。 三、职责 品质部:负责对关键元器件和材料的检验/验证及定期确认检验。 采购部:负责要求供应商及时对检验或验证中出现问题的关键元器件和材料进行处理。 四、程序 4.1关键元器件和材料的检验/验证 4.1.1对生产购进的关键元器件和材料,仓库保管员核对送货清单确认物料品名、规格、数量等无误、 包装无损后,置于待检区。 4.1.2检验员根据本公司检测能力,严格按照《进料检验规范》执行,在些标准中明确规定了检测频率、 抽样方法、检测项目、检测内容、检测方法、判断依据、使用的检测设备等。对于无检测能力的项 目,由供应商自行检验或验证,并提供相关的检测报告。对重要的关键元器件和材料,并且本身是 生产厂家的,本公司要求其提供产品的检验标准,若是中间商的则要求提供质量保证协议、每批产 品的检验记录、合格证明等文件。一般的关键元器件除本公司内部检验外,只需要求提供质量证明,并填写《IQC检验报告》。 仓库保管员根据合格记录或标识办理入库手续; 验证不合格时,检验员在物料上贴“不合格”标签,按《不合格品控制程序》进行处理。 采购及时跟进不合格品的处理. 4.1.3紧急放行 当生产急需来不及验证,在可追溯的前提下,由生产车间填写《紧急(例外)放行申请单入经生产负 责人批准后,一联留存,一联交品质部,一联交仓库。 仓库保管员根据批准的《IQC检验报告》按规定数量留取同批样品送检,其余由检验员在领料单上 注明“紧急放行”后放行;车间在其后生产记录上也应注明“紧急放行”。 在放行的同时,检验员应继续完成该批产品的检验:不合格时品质部负责对该批紧急放行产品进行 追踪处理。 4.2关键元器件和材料定期确认检验 4.2.1关键元器件材料定期确认的项目及频次见附表一、关键元器件和材料的定期确认要求。 4.2.3委托定期确认检验 定期确认检验由提供该关键元器件和材料的供应商来完成,若该供应商也无法完成,则委托
设计和开发控制程序文件
设计和开发控制程序 1 目的 对产品设计和开发全过程进行控制,确保设计能满足合同及顾客的要求,达到或超越国家/行业/企业标准规定的技术要求。 2 适用范围 本程序适用于新产品的设计和定型产品的改进活动。 3 职责 3.1 研发部负责编制并且监督执行产品设计开发计划,负责设计和开发全过程的组织、协调和管理工作,组织设计评审、设计验证、设计确认工作。负责处理车间生产制造过程中发生的产品设计问题,负责在外购件的采购发生困难时,协助采购部选择代用品。负责处理车间生产制造过程中发生与设计相关的工艺问题,负责试验组织实施工作。 3.2 总经理负责产品立项审批的批准,负责主持产品的定型鉴定并批准产品鉴定报告。3.3 制造生产部负责试制阶段的生产组织落实及计划进程的控制。 3.4 采购部负责试制过程中的配套采购。 4 工作程序 4.1 设计和开发策划 4.1.1 设计项目的来源
①公司内外反馈的信息 研发部根据公司内外反馈的信息,编制“项目开发建议书”,提出产品开发或技术改造的建议,报总经理批准。产品设计和开发活动应在公司战略目标指导下进行。 ②市场部的市场调查 市场部通过对市场调查结果的分析,提出“项目开发建议书”,报总经理批准后,连同有关资料移交研发中心。 ③合同评审的结果 有技术开发成份的合同或订单 ( 包括技术协议 ),必须由研发部组织相关部门进行评审。评审通过后,将“合同订单评审表”连同客户的有关资料移交采购部。 4.1.2 设计任务书的编制 《设计任务书》(亦称《项目手册》)应做如下明确规定: a) 产品的质量目标/ 指标及性能要求。 b) 确定活动的输出满足输入的要求,并处于受控状态。 c) 确定组织和技术上的接口。 d) 设计评审、设计验证、设计确认等设计过程的计划安排。 e) 控制产品研发过程的准则。 f) 特定的工作程序及相应的工艺技术文件。 g) 《设计任务书》的管理方法。 h) 特殊过程控制采用的必要检验和试验。 4.1.3 设计任务书的评审 研发部或项目组负责人组织包括设计、生产、质量部门人员对《设计任务书》进行评审。评审的内容包括:
关键元器件和原材料的控制程序
关键元器件和原材料的控制程序 1.目的 通过对本公司来料、过程和成品中的关键元器件和材料进行检验与验证,及时发现不合格品,防止不合格关键元器件和材料入库、发生及流出。 2.范围 适用于本公司来料、过程及成品中的关键元器件和材料的检验或验证。 3.职责与权限 3.1生产部员工负责在生产过程中的自检和互检。 3.2品质部负责对来料、过程及成品进行检验。 3.3技术部负责制定《关键元器件和材料清单》,根据国家相关规定有CCD光电转换主板、电源及电源线、电荷耦合器件以及外壳材料等关键元器件和材料。 4.定义 关键元器件和材料: 是指对产品的安全、环保、EMC和主要性能有较大影响 的元器件和材料。有时可能不仅限于认证实施规则中的 “关键零部件清单”。 5.工作程序 5.1 建立并保持关键件合格供应商名录。关键件应从经批准的合格供应商处购买,并保存关键件进货单,出入库单、台帐 5.1.1 对供应商提供的关键件的检验或验证进行控制,确保与采购控制要求一致,应保存相关的检验或验证记录。 5.1.2 选择合适的控制质量的方式,以确保入厂的关键件的质量特性持续满足认证要求,并保存相关的实施记录。合适的控制质量的方式可包括: a)获得强制性产品认证证书/可为整机强制性认证承认认证结果的自愿性认证证书,工厂应确保进货时证书的有效性。 b)每批进货检验,其检验项目和要求不得低于认证机构的规定。检验应由工厂实验室或工厂委托认可机构认可的外部实验室进行。 c)按照认证机构的要求进行关键件定期确认检验。 5.1.3 供应商或客户交货时,仓管员按送货单或订购单查验物料是否为关键元器件和材料,并查验物料的品名、规格、型号、数量等。初收无误后,把原物料整
过程的设计和开发控制程序
1.目的 对过程质量进行先期策划,做到早期识别,避免晚期更改,规范过程开发工作,确保持续稳定生产顾客满意产品。 2.适用范围 适用于对本公司产品的制造过程质量先期策划工作。 3.职责 3.1生技部负责过程开发的先期策划工作。 3.2生技部部长负责APQP的总体策划和监视,负责组织建立APQP小组。 3.3APQP小组成员及相关部门负责开发APQP策划输入评审验证工作。 4.工作程序 4.1APQP小组的成立与APQP工作进度计划的编制。 4.1.1与顾客初步达成产品生产协议后,总经理通知生技部部长,部长据此成立APQP小组。 4.1.2 APQP小组成员来自生技部、综合部、车间、以及顾客代表,必要时邀请顾客及供应商代表参加。 4.1.3通常情况下,APQP小组组长由生技部部长担任,遇到特殊情况时由总经理任命。APQP小组组长负责小组内成员的职责分工及工作安排,负责APQP全过程跟进和监督,负责组织APQP各阶段的组织、协调工作。 4.1.4 APQP小组组长组织编写APQP工作时间进度表,经APQP成员讨论通过,送总经理批准后下发有关部门实施。APQP工作时间进度表应随着APQP的进展适时进行修订。 4.2计划和项目的确定 4.2.1.本企业不进行产品设计,但要在2个工作周内对顾客提供的产品图纸和技术资料进行评审。 4.2.2.APQP小组对顾客提供的产品图和相关的产品符合性要求进行评审,填写《工程规范评审记录》,对评审中发现的问题,要及时与顾客联络解决。 4.2.3.评审时要确定需要进行试验及可靠性研究的项目(适用时)。
4.2.4必要时,生技部对顾客以往的投诉意见和建议进行收集分析,分析结果作为APQP 小组的参考资料。 4.2.5必要时,APQP小组应对顾客的业务计划进行研究,以识别顾客现在和未来最关注的事项。 4.2.6项目小组根据顾客要求和以往类似产品过程的设计、生产经验确定产品的质量目标、环保等要求,提出《初始材料清单》、《特殊特性清单》、《初始过程流程图》 4.2.7完成以上工作后APQP小组编写《产品保证计划》,其主要内容有: 1.产品过程要求。 2.可靠性和质量目标。 3.进度要求。 4.成本要求。 5.风险评估。 4.2.8计划和确定项目的总结 APQP小组在计划和确定项目阶段工作结束时,应召开APQP小组会议进行这一阶段工作的总结评审,评审时可要求有关管理人员参加,以获得其支持并协助解决有关未解决问题。 总结评审的结论应记录在《第一阶段评审表》中。 4.3样件制造 编制样件制造控制计划 生技部负责编制《样件控制计划》,对样件制造过程中尺寸测量和材料性能试验等进行描述。《样件控制计划》编写完成后,APQP小组用《控制计划检查表》对计划的完整性进行检查。 当顾客没有要求编制《样件控制计划》,本企业样件制造可使用与批量生产相同的设备、工装、材料和供方时,可以编制批量生产的《控制计划》。 4.3.1提出所需的新设施、设备和工装 生技部提出产品生产所需的新设施、设备和工装,编制《设备需求表》和《工装需求表》,保证样件试制和小批量生产前到位。 《设备需求表》和《工装需求表》由APQP小组有关人评审、总经理批准。
首件检验控制程序
首件检验控制程序 首件检验控制程序 一、目的 为了保证产品生产质量,在产品量产前对影响产品质量 的因素和首件产品实物质量进行验证和确认,尽早发现生产过程中影响产品质量的因素,避免出现批量性质量问题。 二、范围适用所有新项目,新产品开发设计,供方提供产品
等的首件新产品验证,设计、工艺变更后的首件检验以及每日批量生产前首件验证。 2.1在新开发产品首次上线生产时的首件检验。 2.1.1 新产品的内部首检。 2.1.2 新产品交付顾客前的外部首件检验(顾客有要求现场验证的情况)。 2.1.3 供应商(外包、外购)提供的新产品首件检验。 2.2 因后续设计、工艺更改等变化导致先前首检失效的首件检验。 2.3 在批量生产过程中(每个生产班次开始加工的第一个工件,或加工过程中因换人、换料及换工装、调整机床等改变工序条件后加工的第一个工件)的首件检验。 三、定义 )即工Process First Article Inspection 3.1 P-FAI(序首检,是对工序的制程因素及其结果的验证。)即首件检验。是3.2 FAI (First Article Inspection 指按照技术文件的要求,对批量生产前的首个零(部或组)件进行全面的工序和成品检查、考核,以确定零部件是否满稳定的生产合格产品的能力。足技术要求,是否具备批量的、公司提供技术要求产品制造过程外包:(技术协议、3.3
图纸等)、必要时提供零部件(或原材料、半成品),要求供应商按技术要求进行相应工序加工的过程。 3.4外购:产品不是由组织(公司)设计的,通过选型向外界直接购买。 (四)职责 4.1营销部门(或新产品项目组) 4.1.1负责对客户提供技术资料、图纸等外来文件的审核、传递、归档。 4.1.2负责对客户所提供的图纸、验收准则等存在分歧的沟通协调处理。 4.1.3 负责提供产品的所有图纸、原材料清单、技术标准、关键零部件清单等检验准则,编制内部首件检验计划。4.1.4负责组织相关人员对供方提供的零部件新产品的首件验证及对产品制造过程外包的首件验证,对其它新产品的首样验证要求供方提供相关资料。 负责发起并组织顾客现场验证的首检工作(顾客 4.1.5 有要求的情况),并为迎接外部首检做工作安排,制定外部首检计划。 4.1.6参与并推动和促进首检工作。 负责跟踪产品交付后客户使用情况,整理和传递4.1.7 外部首检不合格项,并组织落实外部首检不合格项关闭。4.1.8
最新原材料进厂检验制度 (2)
原材料进厂检验管理 制度(2)
原材料进厂检验管理制度 第1章总则 第1条:目的为检查生产用原材料、辅料的质量是否符合企业的采购要求提供准则,确保来料质量合乎标准,严格控制不合格品流程,特制定本制度。 第2条:适用范围适用于所有进厂用于生产的原、辅材料和外协加工品的检验和试验。 第3条:定义来料检验又称进料检验,是工厂制止不合格物料进入生产环节的首要控制点。来料检验由质量管理部来料检验专员具体执行。 第4条:职责 (1)质量管理部负责进货的检验和试验工作。 (2)库房负责验收原材料的数量(重量)并检查包装情况。 (3)质量管理部制定《来料检验控制作业标准》。 第2章来料检验的规划 第5条:明确来料检测要项 (1)来料检验专员对来料进行检验之前,首先要清楚该批货物的质量检测要项,不明之处要向来料检验主管咨询,直到清楚明了为止。 (2)对于新来料,在明确该料的检测标准和方法之后,将之加入《来料检验控制作业标准》。第6条:影响来料检验方式、方法的因素 (1)来料对产品质量的影响程度。 (2)供应商质量控制能力及以往的信誉。 (3)该类货物以往经常出现的质量异常。
(4)来料对公司运营成本的影响。 (5)客户的要求。 第7条:确定来料检验的项目及方法 (1)外观检测。一般用目视、手感、限度样品进行验证。 (2)尺寸检测。一般用卡尺、千分尺等量具验证。 (3)结构检测。一般用拉力器、扭力器、压力器验证。 (4)特性检测。如电气的、物理的、化学的、机械的特性,一般采用检测仪器和特定方法来验证。 第8条:来料检验方式的选择(见抽检方案) (1)全检。适用于来料数量少、价值高、不允许有不合格品物料或工厂指定进行全检的物料。 (2)抽检。适用于平均数量较多,经常性使用的物料。(抽检比例待定) 第3章来料检验的程序 第9条:质量管理部制定《来料检验控制标准及规范程序》,由质量管理部经理批准后发放至检验人员执行。检验和试验的规范包括材料名称、检验项目、标准、方法、记录要求。 第10条:采购部根据到货日期、到货品种、规格、数量等,通知库房和质量管理部准备来验收和检验工作。 第11条:来料后,由库房人员检查来料的品种、规格、数量(重量)、包装情况,并及时通知质量管理部检验专员到现场检验。 第12条:来料专员接到检验通知后,到库房按《来料检验控制标准及规范程序》进行检验,并填写《产品进厂检验单》。相应的检验记录,和检验日报。
研发设计和开发控制程序
文件编号XG-YF/01 文件管理流程编制部门研发中心 版本/版次A/001 总页码22 版本编制日期编制记要备注 A/0新版编制 A/1 A/2 A/3 批准审核编制
1.目的: 对设计和开发过程进行有效管理、控制,以确保产品的特性和实现过程符合设计要求。 2.范围: 2.1适用于新产品开发的过程管理。 2.2适用于对现有产品进行技术改造的管理。 3.职责: 3.1 研发中心负责新产品开发过程中的小试、工艺设计与工程实施、中试以及试生产的组织、策划和控制。 3.2 销售部负责市场信息的收集、市场调研、产品销售。 3.3技术部负责检测新产品的各种性能指标,以及产品的的检测工作。 3.4分析部负责建立开发过程中原材料的检测方法、中间控制;负责原材料、中间控制的检测工作。 3.5仓库负责原料进货的点收、入库保管和发放。 3.6采购部负责按工厂的采购计划联系供应商保质保量供应生产所需要的原辅料,负责来货品质不良的信息传递给供应商,并跟踪其快退换处理,确保生产正常运作。 4工作程序 4.1 新产品开发项目的策划 4.1.1项目的来源 4.1.1.1销售部通过多种渠道广泛收集市场信息,分析市场的需求,并将相关资料传递到研发中心;研发中心通过参加相关会议、专业人士的技术交流等获取市场信息;负责收集技术资料并对这些信息进行综合分析 4.1.1.2根据市场信息公司决策层确定开发研究项目,并以会议纪要、通知或XG-YF-001《新产品开发信息单》等形式发放到研发中心。 4.2新产品开发项目计划的评审 由总工组织有关人员对研发中心编制的《新产品开发信息单》进行会议评审,评审结果以会议纪要等形式传递到研发中心。 4.3新产品开发项目的输入、输出、评审、验证和确认
iso包装验证控制程序
包装验证控制程序 1、目的 对无菌医疗器械产品生产的包装过程进行有效控制,确保经环氧乙烷灭菌产品的包装有效性。 2、范围 本程序规定了无菌医疗器械产品包装工艺过程验证的管理职责、工作程序、内容和要求。 本程序适用于环氧乙烷灭菌产品包装的控制,以及包装验证方案、报告的编制。 3、职责 3.1生产部负责成品包装过程的控制。 3.2生产车间负责成品的包装工作。 3.3技术部负责成品包装验证方案的编制。 3.4质检部负责成品包装的检查验证,并形成包装验证报告。 4、控制程序 4.1包装材料确定的原则 4.1.1包装材料应清洁完整,具有良好的密封加工性能。 4.1.2标签印刷应清晰可见无污染及其它制造缺陷。 4.2包装材料与灭菌过程的适合性。 4.2.1在灭菌过程中,应保证环氧乙烷能穿透包装材料。并在灭菌后对环氧乙烷灭菌剂能有 效的解析。 4.2.2经环氧乙烷灭菌后,其包装材料及包装标签与使用的灭菌过程的适应性无不利影响。 4.3包装材料的毒性。 在使用过程中,包装材料不得释放出对人体健康产生危害的有毒性物质。 4.4包装材料的生物兼容性。 经密封包装后的产品其表面与包装材料充分接触并经过环氧乙烷灭菌后,按照EN30993—X要求确定其细胞毒性、过敏性、溶血性和皮内刺激性。 4.5包装材料的无菌性保持。
需经环氧乙烷的产品经包装热压封口后应保持其封口处的完整性和不透气性,并应确保整个密封包装的不透气性和阻菌性。 4.6包装材料贮藏和运输的适宜性。 在指定的运输和贮藏条件下,经灭菌后包装材料的保存期应与产品相一致,确保包装材料的耐老化性能。 4.7包装材料(单包装袋)应在10万级洁净区内制造。 4.8包装封口过程的操作方法按《包装操作规程》进行。 4.9包装材料的有效性验证按《灭菌包装》EN868-1:1997进行。 4.1O在完成了所有的包装项目验证以后,应形成包装验证报告,所有的包装验证记录报告由技术部归档保存。 5、相关文件 5.1产品监视和测量控制程序YH/QP-20 5.2灭菌包装EN868-1 5.3医疗器械生物学评估EN30993-X 6、文件记录 6.1包装验证报告QP15-01。
CCC关键元器件检验验证控制程序
CCC关键元器件检验验证控制程序 1.目的 通过对本公司来料、过程和成品中的关键元器件和材料进行检验与验证,及时发现不合格品,防止不合格关键元器件和材料入库、发生及流出。 2.范围 适用于本公司来料、过程及成品中的关键元器件和材料的检验或验证。 3.职责与权限 3.1生产部员工负责在生产过程中的自检和互检。 3.2品质部负责对来料、过程及成品进行检验。 3.3工程部负责制定《关键元器件和材料清单》。 4.定义 关键元器件和材料: 是指对产品的安全、环保、EMC和主要性能有较大影 响的元器件和材料。有时可能不仅限于认证实施规则 中的“关键零部件清单”。 5.工作程序 5.1建立并保持关键件合格供应商名录。关键件应从经批准的合格供应商处购买。并保存关键件进货单,出入库单、台帐 5.1.1对供应商提供的关键件的检验或验证进行控制,确保与采购控制要求一致,应保存相关的检验或验证记录。 5.1.2选择合适的控制质量的方式,以确保入厂的关键件的质量特性持续
满足认证要求,并保存相关的实施记录。合适的控制质量的方式可包括: a)获得强制性产品认证证书/可为整机强制性认证承认认证结果的自愿性认证证书,工厂应确保进货时证书的有效性。 b)每批进货检验,其检验项目和要求不得低于认证机构的规定。检验应由工厂实验室或工厂委托认可机构认可的外部实验室进行。 c)按照认证机构的要求进行关键件定期确认检验。 5.1.3供应商或客户交货时,仓管员按送货单或订购单查验物料是否为关键 元器件和材料,并查验物料的品名、规格、型号、数量等。初收无误 后,把原物料整齐排放于关键元器件和材料待检区域,通知IQC进行来 料检验。 5.1.4 品质部IQC按公司来料检验标准及指导书的检验方式和内容进行检 验,并将检验结果如实填写在《来料检查报告》中。 5.1.5对公司无法检验的材料,要求供应商提供检验报告,由IQC依检验标 准进行确认。IQC检验完毕,将《来料检查报告》(注明是关键元器件 或材料)交主管审核做出合格或不合格判定,作为验收判定。 5.1.6IQC依检验结果,对物料做合格或不合格的标识,检验合格的来料由仓 管员办理入库手续。 5.1.7经检验之不合格品,IQC人员应填写《品质异常处理报告》经经理确认 后通知采购部,具体按《不合格品控制程序》实施。 5.1.8来料急需生产而来不及作检验时,由生产部提出申请,经总经理批准可 紧急放行,但生产过程中必须进行检验,并按规定对来料作好标识、记
验证和确认控制程序9
HACCP验证和确认控制程序 1 目的 通过对CCP点、HACCP计划、PRP(S)前提方案、HACCP系统的验证,以确保HACCP计划实施和HACCP系统运行达到预期目标。 2范围 本程序适用于对CCP点的验证、PRP(S)前提方案、HACCP计划的验证、HACCP系统的验证。3职责 3.1食品安全小组组长负责主持验证工作; 3.2食品安全小组成员参加验证,负责具体的验证工作。 3.3责任部门负责对不符合项采取纠正措施。 4工作程序 4.1HACCP验证包括:HACCP计划的验证、CCP的验证、PRP(S)前提方案、HACCP系统的验证他等等。验证活动应确认: a)危害分析的输入持续更新。 b)操作性前提方案和HACCP计划中的要素得以实施且有效。 c)已实施基础设施和维护方案。 d)危害水平低于确定的可接受水平。 e)组织要求的其他程序得以实施且有效。 f)内部审核结果。 4.2验证的方法: a)相关记录的复查。 b)针对性的取样和检测(如在OPRP中把供方的证明作为监控的对象时,供方的证明是否 可信,需要通过针对性的取样检测来验证;当关建限值设定在设备操作中时,可抽查产品以确保设备设定的操作参数适于生产安全的产品。 c)监控设备的校准。 d)对终产品的微生物检测。
e)内部审核。 4.3 HACCP计划验证 HACCP计划在制定后,食品安全小组组长应主持对HACCP计划进行验证,证实HACCP计划是否能有效的控制了食品中的安全危害。当出现下列情况时,也应对HACCP计划进行验证: a) 改变食品或加工工艺时; b) 验证数据出现相反的结果,重复出现偏差; c) 有关危害和控制手段的新信息出现; d) 生产中观察到异常情况出现。 4.4 CCP的验证 HACCP计划在制定实施后,应对CCP进行验证,验证可以在HACCP计划验证时进行,也可以在对HACCP系统进行验证时进行。CCP的验证应从以下几个方面进行: a) 检查监控记录,这些记录是否能表明达到策划的要求; b) 监控设备的校正; c) 有针对性的取样检测; d) 验证对CCPS的控制是否达到原预期的目的。 4.5 PRP(S)的验证 PRP(S)在制定实施后,应对PRP(S)进行验证,验证可以单独进行,也可以在对HACCP系统进行验证时进行。验证方法可以进行现场核查、记录检查、有针对性的取样检测如对食品接触面消毒效果的微生物验证等。 4.6 HACCP系统的验证 a) HACCP系统验证主要采用审核的方法进行,可以与内部审核合二为一,验证主要是检查食品说明和生产流程的准确性、系统运行的有效性。 b) HACCP系统验证由食品安全小组组长主持,食品安全小组成员参加。每年至少进行二次验证(可以在包含卫生质量体系内部审核中,也可以单独进行),当出现以下情况时,则应考虑增加验证的次数。 1) 系统发生故障时;食品、加工工艺发生显著变化时 2) 当公司内外环境发生重大变化,如食品、加工工艺发生显著变化时; 3) 关键控制点出现重大质量事故时;
原材料、零部件入库检验办法
原材料、零部件入库检验办法 1.目的: 为检查生产用原材料、辅料及零部件的质量是否符合企业的采购要求提供准则,确保来料质量合乎标准,严格控制不合格品流程,特制定本制度。 2.适用范围: 适用于所有进厂用于生产的原、辅材料和外协加工品的检验和试验。 3.定义: 来料检验又称进料检验,是工厂制止不合格物料进入生产环节的首要控制点。来料检验由质量管理部来料检验专员具体执行。 4.职责: 4.1 质检部负责进货的检验和试验工作; 4.2 库房负责验收原材料的数量(重量)并检查包装情况; 4.3 采购部、技术部负责制定《来料检验控制规定》。 5. 来料检验注意事项: 5.1来料检验专员对来料进行检验之前,首先要清楚该批货物的质量检测要项,不明之处 要向来料检验主管咨询,直到清楚明了为止; 5.2 对于新来料,在明确该料的检测标准和方法之后,将之加入《来料检验控制作业标准》。 5.3 来料检验时的考虑因素; 5.3.1 来料对产品质量的影响程度; 5.3.2 供应商质量控制能力及以往的信誉; 5.3.3 该类货物以往经常出现的质量异常; 5.3.4 来料对公司运营成本的影响; 5.3.5 客户的要求。 6.来料检验方法: 6.1 外观检测:一般用目视、手感、限度样品进行验证;
6.2 尺寸检测:一般用卡尺、千分尺等量具验证; 6.3 结构检测:一般用拉力器、扭力器、压力器验证; 6.4特性检测:如电气的、物理的、化学的、机械的特性,一般采用检测仪器和特定方法来 验证。 7.来料检验方式的选择: 7.1 全检: 适用于来料数量少、价值高、不允许有不合格品物料或工厂指定进行全检的物料。 7.2 抽检: 对于原材料、外协件的入库验收不进行抽样检验,均进行全数验收;外购件、零部件的抽样数量为入库量的30%,另外,入库量在10以内(包括10)则进行全数验收,当入库量超过10,但是按30%算出的抽样量不达到10的,则按10的抽样量进行抽样验收。 7.3检查方法及检查条件 原材料、外协件、外购件、零部件入库验收的检查条件(即前提)是供货商所出具的供货清单上所列物品与我公司的订货清单所列物品一致;具体的检查方法是:按照订货清单所列物品名称、规格型号检查物品是否相符,再检查物品的出厂合格证所列规格型号与实物是否一致,最后按照物品的出厂合格证或说明书上所列的技术数据进行相关检验 8. 来料检验的程序: 8.1采购部制定《来料检验控制规定》,由采购部经理批准后发放至检验人员执行。检验和 试验的规范包括材料名称、检验项目、标准、方法、记录要求。 8.2采购部根据到货日期、到货品种、规格、数量等,通知库房和质量管理部准备来验收 和检验工作。 8.3来料后,由库房人员检查来料的品种、规格、数量(重量)、包装情况,并及时通知质 量管理部检验专员到现场检验。 8.4 来料专员接到检验通知后,到库房按《来料检验控制标准及规范程序》进行检验,并 填写《产品进厂检验单》。相应的检验记录,和检验日报。 8.5 检验完毕后,对合格的来料贴上合格标识,通知库房人员办理入库手续。 8.6 如果是生产急需的来料,在来不及检验和试验时,须按《紧急放行控制制度》中规定 的程序执行。 8.7 检测中不合格的来料应根据《不合格品控制程序》的规定进行处置,不合格的来料不
设计和开发控制程序.pdf
1目的 对设计和开发过程进行有效的策划、控制,提高设计和开发的质量,确保产品满足 顾客需求和期望及有关法律、法规的要求。 2适用范围 适用于本公司新产品设计、开发全过程,包括引进产品的转化、定型产品及生产 过程中的技术改进等。 3职责 技术部: 负责编制项目建议书,制定设计和开发的策划,实施设计和开发计划过程的 输入、输出、评审、验证、确认和更改阶段的控制。 质量管理部: 负责产品性能的检测,参加设计开发的评审、验证与确认等控制活动。 市场部: 采购员负责外购、外协件的采购和业务联系。 董事长: 负责批准项目建议书。 管理者代表: 批准设计和开发相关技术文件资料和试产报告所提出的必要的资料。 4程序 设计开发的策划 4.1.1根据公司发展战略、市场信息分析结果由管理层策划设计开发项目。技术部根据 设计开发的策划,编制《项目建议书》。项目建议书应包括: a) 设计和开发项目目标的描述(对产品的构思概念,产品的用途,开发产品的原因。) b) 顾客和市场对该产品的需求情况(对市场的需求做研究评估,产品在市场中的 价值地位。) 4.1.2《项目建议书》由技术部负责人审核,报董事长批准立项。 4.1.3对于具体设计工作,根据新产品开发建议书,技术部负责人组织有关部门进行评 审,并在评审通过后组织编制“产品设计任务书”,“产品设计开发任务书”的内容 包括: a) 明确方案设计、技术统计、工作室设计、样品试制、小试、产品定型各阶段的 划分和要求; b) 明确各设计阶段人员的分工和设计人员的职责权限、进度要求、成立试制小 组; c) 明确各设计阶段的接口、传递和评审的要求,过程中的信息必须写成文件,为 采购、制造、检验等活动提供技术依据; d) 适用于设计和开发控制的质量管理体系文件、程序和形成的记录描述; e) 对产品设计过程中的风险分析,包括设计过程中采取的措施;
确认验证验证结果的评价与分析控制程序.pdf
标题: 确认、验证、验证结果的评价与分析控制程序版号:A/0 分发日期:页码:分发编号: 1 目的 通过确认,证实各控制措施或控制措施的组合能使相应的食品安全危害达到预期的控制水 平;通过验证,证明各控制措施或控制措施的组合确实达到了预期的控制水平。 2 适用范围 适用二对控制措施组合进行确认;适用于对食品安全管理体系进行验证。 3 职责 3.1 食品安全小组负责对OPRP和HACCP计划进行确认;负责对OPRP和HACCP计划进行验证。负责对PRP进行验证。 3.2 品管部食品安全小组成员负责CCP的验证;负责最终产品的检验。 3.3 食品安全小组组长负责组织进行食品安全管理体系的内部审核;负责组织对验证结果进行评价和分析。 4 工程程序 4.1 控制措施组合的确认 4.1.1 OPRP的确认 4.1.1.1 确认的时机 ①在OPRP实施之前。 ②在下列情况下,根据需要,对OPRP做必要的修改,在修改后的OPRP实施之前,要对其进行确认: a. 原料的改变; b. 产品或加工的改变; c. 复查时发现数据不符或相反; d. 重复出现同样的偏差; e. 有关危害或控制手段的新信息(原来依据的信息来源发生变化); f. 生产中观察到异常情况; g. 出现新的销售或消费方式。 4.1.1.2 确认的内容 确认的内容见表COP12-01“OPRP确认记录表”。 4.1.1.3 确认的实施 食品安全小组用“OPRP确认记录表”对OPRP进行确认,确认的结果记录在“OPRP确认记录表”的相关栏目中。 4.1.1.4 确认结果的处理 当确认结果表明OPRP不能对相应的食品安全危害进行预期的控制时,应对OPRP进行修改、重新评价和确认。 4.1.2 HACCP计划的确认 4.1.2.1 确认的时机 ①在HACCP计划实施之前。 ②在下列情况下,应对危害分析的输入进行必要的更新,重新进行必要的危害分析,并对 HACCP计划进行必要的修改,在修改后的HACCP计划实话之前,要对其进行确认: 编制/日期:张三2006/5/1 审核/日期:李四2006/5/1 批准/日期:王二2006/5/1
关键元器件和原材料的控制程序
精心整理关键元器件和原材料的控制程序 1.目的 通过对本公司来料、过程和成品中的关键元器件和材料进行检验与验证,及时发现不合格品,防止不合格关键元器件和材料入库、发生及流出。 2.范围 适用于本公司来料、过程及成品中的关键元器件和材料的检验或验证。 3.职责与权限 3.1生产部员工负责在生产过程中的自检和互检。 3.2品质部负责对来料、过程及成品进行检验。 3.3技术部负责制定《关键元器件和材料清单》,根据国家相关规定有CCD光电转换主板、电源及电源线、电荷耦合器件以及外壳材料等关键元器件和材料。 4.定义 关键元器件和材料:是指对产品的安全、环保、EMC和主要性能有较大影响的元器件和材料。有时 可能不仅限于认证实施规则中的“关键零部件清单”。 5.工作程序 5.1建立并保持关键件合格供应商名录。关键件应从经批准的合格供应商处购买,并保存关键件进货单,出入库单、台帐 5.1.1对供应商提供的关键件的检验或验证进行控制,确保与采购控制要求一致,应保存相关的检验或验证记录。 5.1.2选择合适的控制质量的方式,以确保入厂的关键件的质量特性持续满足认证要求,并保存相关的实施记录。合适的控制质量的方式可包括: a)获得强制性产品认证证书/可为整机强制性认证承认认证结果的自愿性认证证书,工厂应确保进货时证书的有效性。 b)每批进货检验,其检验项目和要求不得低于认证机构的规定。检验应由工厂实验室或工厂委托认可机构认可的外部实验室进行。 c)按照认证机构的要求进行关键件定期确认检验。 5.1.3供应商或客户交货时,仓管员按送货单或订购单查验物料是否为关键元器件和材料,并查验物料的品名、规格、型号、数量等。初收无误后,把原物料整齐排放于关键元器件和材料待检区域,通知IQC进行来料检验。
设计评审、验证、确认控制程序
设计评审、验证、确认控制程序 文件管理号:BQ040 版本号:第二版 分发号: *********************** * * 设计评审、验证、确认控制程序 * * * * *********************** 编制审核批准 泰尔茂医疗产品(杭州)有限公司 文件管理号:BQ040 生产技术课设计评审、验证、确认控制程序 版本号:第二版 〈目录〉〈页码〉 第 1 条 (目的) P2/23 第 2 条 (适用范围) P2/23 第 3 条 (相关部门职责) P2/23 第 4 条 (设计评审) P2/23,4/23 1( 开发计划评审 P2/23 2( 设计输入评审 P3/23 3( 试制样品设计评审 P3/23 4( 最终样品设计评审 P4/23 第 5 条 (设计验证) P4/23 第 6 条 (设计确认) P5/23 第 7 条 (相关文件) P5/23 第 8 条 (质量记录表单) P6/23 附1. 「开发计划评审报告」 P7/23,9/23 附2. 「设计输入评审报告」 P10/23,12/23
附3. 「试制样品设计评审报告」 P13/23,15/23 附4. 「最终样品设计评审报告」 P16/23,18/23 附5. 「设计验证报告」 P19/23,20/23 附6. 「设计确认报告」 P21/23,22/23 第 9 条 (更改履历) P23/23 泰尔茂医疗产品(杭州)有限公司 (P1/23) 文件管理号:BQ040 生产技术课设计评审、验证、确认控制程序 版本号:第二版 第 1 条 (目的) 对产品设计开发阶段的设计评审、验证、确认作出规定,以确保设计开发的产品的 安全性和有效性。 第 2 条 (适用范围) 适用于新产品和有重大变更型号规格变更品的设计评审、验证、确认活动的控制。 第 3 条 (相关部门职责) 1(商品策划委员会:以生产技术课设计管理负责人为主,各部门技术负责人参加, 在设计开发的适当阶段以会议形式负责产品的设计评审(包括开发计划评审)、设计验证、设计确认。 2(设计管理负责人:为技术部生产技术课设计开发总负责,主持商品策划委员会的 工作。 3(运营会议:公司运营会议负责产品开发计划的批准及设计确认后的批准事宜。
关键元器件和原材料的控制程序
关键元器件和原材料的 控制程序 标准化管理部编码-[99968T-6889628-J68568-1689N]
关键元器件和原材料的控制程序 1.目的 通过对本公司来料、过程和成品中的关键元器件和材料进行检验与验证,及时发现不合格品,防止不合格关键元器件和材料入库、发生及流出。 2.范围 适用于本公司来料、过程及成品中的关键元器件和材料的检验或验证。3.职责与权限 3.1生产部员工负责在生产过程中的自检和互检。 3.2品质部负责对来料、过程及成品进行检验。 3.3技术部负责制定《关键元器件和材料清单》,根据国家相关规定有CCD光电转换主板、电源及电源线、电荷耦合器件以及外壳材料等关键元器件和材料。 4.定义 关键元器件和材料: 是指对产品的安全、环保、EMC和主要性能有较大影 响的元器件和材料。有时可能不仅限于认证实施规则 中的“关键零部件清单”。 5.工作程序 5.1 建立并保持关键件合格供应商名录。关键件应从经批准的合格供应商处购买,并保存关键件进货单,出入库单、台帐 5.1.1 对供应商提供的关键件的检验或验证进行控制,确保与采购控制要求一致,应保存相关的检验或验证记录。 5.1.2 选择合适的控制质量的方式,以确保入厂的关键件的质量特性持续满足认证要求,并保存相关的实施记录。合适的控制质量的方式可包括: a)获得强制性产品认证证书/可为整机强制性认证承认认证结果的自愿性认证证书,工厂应确保进货时证书的有效性。 b)每批进货检验,其检验项目和要求不得低于认证机构的规定。检验应由工厂实验室或工厂委托认可机构认可的外部实验室进行。 c)按照认证机构的要求进行关键件定期确认检验。
设计和开发控制程序
.
针对设计和开发过程进行有效控制,确保设计和开发的产品能够满足客户要求和有关标准及法律法规。 2.范围 适用于本公司所有产品设计和开发的全过程,包括产品的技术提升和结构改良。 3.权责 3.1 销售部门:负责对市场调查分析、收集客户反馈的信息进行综合评估填写市场调查分析报告,根据综合信息 转换为《设计开发任务书》输出;参与新产品设计开发的评审工作。负责对新产品上市前的培训资 料、宣传资料等平面设计初步策划。 3.2 研发部: 1、负责参与新产品设想讨论会,议会期间就参会人员提出的新产品功能、性能、结构方面进行可 行性评估,并填写《新产品开发可行性分析报告》会签存档; 2、研发部参与或组织召开新产品立项会,根据《新产品开发可行性分析报告》确定新产品项目小 组成员;研发主管编制《项目流程检查表》,利于项目工程师对项目工作的清晰执行,利于研 发主管对项目进度的管控,研发部定期进行项目流程检查; 3、研发主管制定并输出项目预算表,包括但不限于对产品成本、研发人员工时成本、模具成本、 ID设计成本、检测认证费用、试产工时成本、质量成本等等;项目预算表由研发主导制定,总 经办协助完善,经总经理审批,输出给到财务部,参考附件《设计开发预算管理表》; 4、项目工程师按照《新产品立项书》制定《设计开发任务书》、《新产品开发计划书》;设计开发任 务书需要销售部门确认; 5、按《设计开发任务书》的要求进行新产品的设计与开发;负责输出设计开发文件,为生产和品 质管理提供依据,如:零件设计图纸、装配图、爆炸图、产品规格书、电路图、使用说明书、 BOM表,并保证文件使用的有效性; 6、负责协调工程部对新产品开发过程中试产、量试的治具及工装制作,生产工艺流程、作业指导 书的编制,工程部PE工程师应协助项目工程师处理技术工艺、问题点分析、工艺完善; 7、当新产品量试后符合移交条件时,由项目工程师申请召开产品移交会议并移交。 3.3工程部: 1、对已经移交的老产品负责生产维护和改良,有效工时的核算已达到产能提升的目的; 2、对新产品负责试产、量试的治具及工装制作,生产工艺流程、作业指导书的编制,协助项目工程 师处理技术工艺、问题点分析、工艺; 3、对老产品更换新供应商的评估和来样确认、安排试产。并根据《工程变更管理程序》完善变更 资料; 4、老产品型号升级或派生由总经办按照研发流程,组织并下发《新产品立项书》。 3.4生产部:负责组织新产品量试、量产,对生产现场操作员进行技能培训,确保生产过程中产品质量的稳定, 对生产现场进行管理。 3.5品质部:负责开发过程中新产品零部件的检验与评价,以及新产品的型式试验、验证,编制产品零件部件的 检验规范;负责试产、量产过程中来料检验、制程检验、成品检验、型式试验。 3.6 项目工程师C部:负责依研发部发出的《试产/量试通知单》安排试产计划及物料统筹,知会相关部门具体试产日期。 3.7 采购部:负责依试产BOM表、《样品打样单》采购开发产品的新材料、物料,同时进行新供应商的开发及打样, 并洽谈物料周期及提供样品的有效证书,保证研发/工程部工作所需。 3.8 财务部:参与新产品立项会,审核项目预算表,制定研发项目明细帐,分类统计研发支出科目,项目经费开 支与研发过程同步,定期对经费开支进行检查,力求经费执行专款专用,及时对经费支出异常反馈给 研发部门;项目研发阶段完成后,给出研发预算与决算对比,结果汇报总经理,并反馈给研发团队; 4.定义
11检验和试验控制程序
1目的O b j e c t i v e 对原材料、协配件、半成品、成品进行检验和试验,防止不合格的原材料、协配件非预期使用,不合格半成品转序,不合格成品出厂。 This is to inspect and test the raw material, components, semi-finished and finished products to avoid the nonconforming raw materials and components from unexpected usage, to avoid the defective semi-finished product from flowing into the next process and to avoid the defective finished product from releasing out of the factory. 2 适用范围Applicable Scope 适用于本公司的原材料、协配件、半成品、成品的检验和试验控制。 This is applicable to the control over the inspection and test of the raw materials, components, semi-finished and finished products of the company. 3 职责Responsibility 3.1 质量部负责原材料、协配件、半成品、成品的入库检验和验证的归口管理。 The Quality Department is responsible for the incoming inspection and test of the raw material, components, semi-finished and finished products. 3.2 技术工程部负责制订和发放原材料、协配件、半成品、成品的图样、检验规程及相关接收标准。 The Engineering Department is responsible to formulate and release the drawings, inspection procedures and relevant receiving standards applicable to the raw materials, components, semi-finished and finished products. 4 工作程序Work Procedures 4.1 检验和试验前的准备Preparation Prior to the Inspection and Test 4.1.1 由质量部根据《控制计划》和检验指导书,在开始检验工作之前,复查是否已经对每项重要检 验项目的方式和方法做出规定,其内容包括:检验方法、检验工具及精度、抽样方法、评定方法、记录方法,注明可能需要提供的质量保证书/自检报告、要求和验证方式。 Prior to inspection, the Quality Department shall refer to the “Control Plan” and Inspection Instruction, checking if the inspection way and method for each important item have been regulated, including: inspection approach, inspection tools and their precision, sampling method, assessment approach and recording method, as well as the remarks on necessary quality warranty/self-inspection report, requirements and verification way.