酸盐无氰电镀铜包铝镁合金线的生产工艺

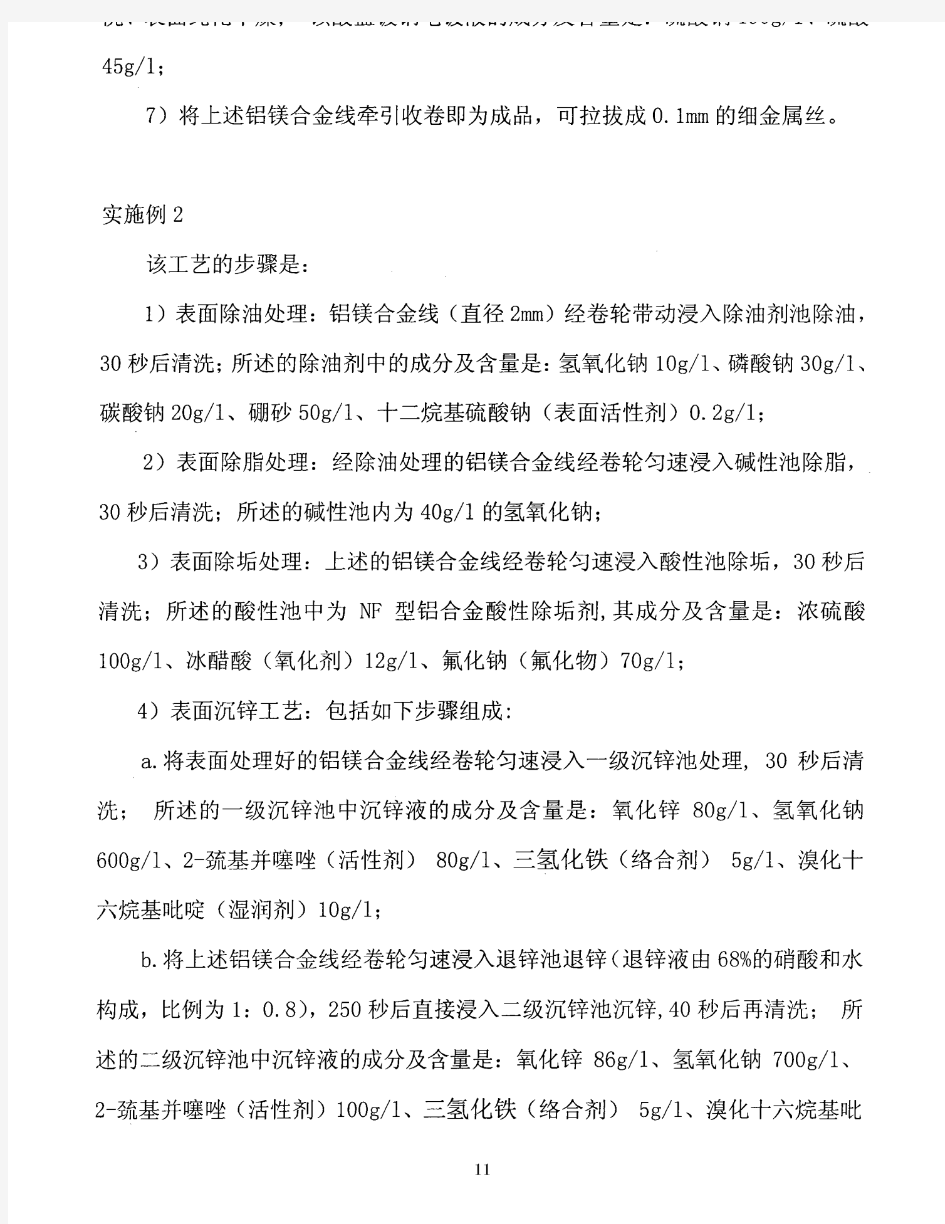
生产工艺流程图及说明
(1)电解 本项目电解铝生产采用熔盐电解法:其主要生产设备为预焙阳极电解槽,项目设计采用大面六点进电SY350型预焙阳极电解槽。铝电解生产所需的主要原材料为氧化铝、氟化铝和冰晶石,原料按工艺配料比例加入350KA 预焙阳极电解槽中,通入强大的直流电,在945-955℃温度下,将一定量砂状氧化铝及吸附了电解烟气中氟化物的载氟氧化铝原料溶解于电解质中,通过炭素材料电极导入直流电,使熔融状态的电解质中呈离子状态的冰晶石和氧化铝在两极上发生电化学反应,氧化铝不断分解还原出金属铝——在阴极(电解槽的底部)析出液态的金属铝。 电解槽中发生的电化学反应式如下: 2323497094032CO Al C O Al +?-+℃ ℃直流电 在阴极(电解槽的底部)析出液态的金属铝定期用真空抬包抽出送往铸造车间经混合炉除渣后由铸造机浇铸成铝锭。电解过程中析出的O 2同阳极炭素发生反应生成以CO 2为主的阳极气体,这些阳极气体与氟化盐水解产生的含氟废气、粉尘等含氟烟气经电解槽顶部的密闭集气罩收集后送到以Al 2O 3为吸附剂的干法净化系统处理,净化后烟气排入大气。被消耗的阳极定期进行更换,并将残极运回生产厂家进行回收处置。吸附了含氟气体的截氟氧化铝返回电解槽进行电解。 电解槽是在高温、强磁场条件下连续生产作业,项目设计采用大面六点进电SY350型预焙阳极电解槽,是目前我国较先进的生产设备。电解槽为6点下料,交叉工作,整个工艺过程均自动控制。电解槽阳极作业均由电解多功能机组完成。多功能机组的主要功能为更换阳极、吊运出铝抬包出铝、定期提升阳极母线、打壳加覆盖料等其它作业。 (2)氧化铝及氟化盐贮运供料系统 氧化铝及氟化盐贮运系统的主要任务是贮存由外购到厂的氧化铝和氟化盐 ,并按需要及时将其送到电解车间的电解槽上料箱内。
AZ31B 镁合金挤压工艺研究
AZ31B 镁合金挤压工艺研究 黄光胜, 汪凌云, 范永革金属成形工艺Vol. 20 №. 5 2002:11-14 镁及镁合金是所有金属结构材料中最轻的,其密度只有1. 74g/ cm3 ,是铝的2/ 3 ,比钢轻78. 1 %。与其它金属材料以及工程塑料相比,镁合金具有很高的比强度和比钢度。镁合金已被誉为21 世纪的金属,近年来在汽车、航空航天、电子工业领域获得了迅速的发展,而且发展前景越来越好[1 , 2 ] 。作为一种新兴金属材料,镁的现有使用状况远没有充分发挥镁合金材料的潜在优势, 镁合金在实际工业应用方面的发展远不及铝合金和钢铁工业,其规模只有铝业的1/ 50 ,钢铁工业的1/ 160[3 ] 。其主要原因是: (1) 作为工程材料,大多数的镁结构件都来自压铸这一种加工方式,限制了产品品种和类型; (2) 应用范围小,镁压铸件的80 %来自汽车工业,而且90 %又是室温使用的结构件,且主要局限于小体积零件。 由于镁的晶体结构为密排六方,塑性不及面心立方结构的铝,塑性成形能力差[4 ] ,因而镁合金在压铸成形领域优先得到重视和发展。变形镁合金与铸造镁合金相比,有更优良的综合力学性能,因此为了推动镁合金在航空、航天、汽车、摩托车等领域内的大量应用,发展我国的镁工业,必须大力开发变形镁合金及其生产工艺。对镁合金的挤压工艺进行了生产性试验研究。 1 实验方法及挤压参数的确定 1. 1 实验方法 试验合金为AZ31B ,其成分为表1。在油炉中熔炼,所用原料为Mg(1 级) ,Al (1 级) ,Zn (1 级) ,Al-10 %Mn 中间合金。熔炼过程中采用熔剂保护,石墨模铸造。棒材与型材铸锭尺寸为 <108mm ×250mm ,管材铸锭的尺寸为( <117mm/ <35mm) ×260mm。铸锭均匀化处理温度为400 ℃,保温时间为12h。铸锭均匀化处理后,车外皮,再挤压。 棒材与型材在1250t 卧式挤压机上成形,管材在600t 的立式挤压机上成形。挤压温度定为400 ℃,挤压筒和模具温度比挤压温度低,取380 ℃。为满足组织和力学性能要求,一般挤压比λ≥8 ,棒材的λ为10 ~25 ,管材、型材的λ为10 ~45。选择挤压速度为1 ~2. 5 m/ min。对铸锭和挤压出的棒材、管材、型材取样,在OLYMPUS 金相显微镜上进行微观组织观察。在WE2100 万能材料试验机上对棒材、管材、型材进行室温力学性能测试。 1. 2 挤压参数的确定 (1)挤压温度的确定。 挤压温度是挤压参数中最活跃的因素,它不但影响挤压过程的进行,还影响收得率、产品的质量以及力学性能等。从理论上考虑,应根据合金的相图、塑性图、和再结晶图[5 ] ,即挤压温度应低于合金的固相线高于再结晶温度,并且是塑性较好的温度,但实际上远比此复杂,尤其对镁合金而言,它易烧、易爆,需要格外注意。根据以上因素综合考虑,将镁合金的挤压温度定为300~450 ℃ [6 ] ,挤压筒、垫片、模具的温度一般比挤压温度低25 ℃,以补偿由于摩擦热、变形热而引起的温升。考虑到以上情况, 对AZ31B 而言, 取挤压温度为400 ℃。 (2)挤压速度的确定。 选择挤压速度的原则是,在保证制品不产生表面裂纹毛刺和扭拧、弯曲、波浪、间隙、扩(并) 口以及尺寸等重量问题的前提下,当挤压机能力允许时,速度越快越好。但挤压速度的确定同挤压温度一样,也十分复杂。挤压速度的大小受合金、状态、毛料、尺寸、挤压方法、挤压力、工具、制品复杂程度、挤压温度、模孔数量、润滑条件等的影响[7 ,8 ] 。因此综合考虑,AZ31B 的挤压速度定为1~2. 5m/ min。 (3)挤压比的确定。 为使镁合金在挤压过程中达到正常的加工效果,必须使断面减缩率保持在一定的范围内[6 ] 。试验的挤压比确定为:棒材的λ为10~25 ,管材、型材的λ为10~45 。 2 试验结果 2. 1 铸锭组织 铸锭的铸态组织如图1 ,基体为α固溶体,在基体上存在大量粗大枝晶, 少量的第二相
镁及镁合金板材的生产工艺流程
镁及镁合金板材的生产工艺流程(一) 镁及镁合金板材的生产工艺流程为: 1、熔炼与铸锭 熔炼包括熔化、合金化、精炼、晶粒细化、过滤等冶金和物理化学过程,通常在反射炉或坩埚炉内进行。镁及镁合金的熔点都在650℃左右,它们极易氧化且随温度的升高而加剧。当温度超过约850℃时,熔体的表面立即燃烧,故熔炼时必须用熔剂覆盖或以保护性气体保护。镁及镁合金在熔融和燃烧状态下遇水、含水(包括结晶水)物质和液态防火介质都可能导致剧烈爆炸,因此,在生产的全过程中注意安全是至关重要的。以隔离空气为主的覆盖熔剂和以提高熔体质量为主的精炼熔剂都是碱金属或碱土金属的氯化物和氟化物。除气(主要是氢)随熔剂精炼进行,也可向熔体中通入活性气体(如氯气)。对凝固时的晶粒粗大倾向,据合金的不同可采取控制熔体温度、向熔体加入微量元素进行变质处理等加以抑制,即晶粒细化(见铸锭晶粒的细化处理)。铸锭通常采用半连续铸锭法。除封闭式铸锭外,流槽和结晶器中裸露的金属,必须用s0:或SF。等气体保护。要科学地确定和控制各项铸造参数,以防止铸锭发生热裂,并降低冷隔深度和减少金属间化合物的形成和聚集。除镁一钇系合金外,铸锭的冷裂倾向小。 2、加热与热轧 铸锭在加热前必须铣面(见有色金属合金锭坯铣面),彻底去除冷隔和偏析物等表面缺陷;合金元素含量高和含锆、钇等的合金还要经均匀化处理(见有色金属合金锭坯均匀化)。铸锭加热时应避免直接热辐射和避免火焰同铝接触,以防局部过热、熔化或燃烧。根据合金的不同加热温度控制在370~510℃范围内。除含锂高的超轻合金有晶型转变外,余者皆为密排六方晶型,塑性差,但变形能力随加热温度的提高和晶粒尺寸的减小而提高,并比立方晶型的金属提高得更快。热轧的总变形量可以达到96%。严格控制终轧温度是保证热加工状态成品板材的力学性能并防止板坯及薄板产生裂纹的重要途径。晶粒粗大的铸锭和厚度较小的热轧成品,有的要进行二
车间生产工艺流程图
车间生产工艺流程图 实木车间 1.文件柜类:素板→大平砂→开毛料→贴面→精截→封边→钻孔→ 试装→半成品 2.茶几或沙发架: 锯材→干燥→截断→纵剖→压刨→划线→铣型→ 开榫头、榫槽→钻孔→手工组装→打磨→半成品 3.班台或会议桌: 素板(锯材)→大平砂(干燥)→开毛料(截断)→加厚 (纵剖)→精截(压刨)→加宽(胶贴)→贴面(热压)→ 铣型(精截)→手工组装(包括打磨、打腻子、封边、 钻孔)→试装→半成品 油漆车间 白坯→机磨(大平面)→手磨(小面、曲边)→擦色(打水灰、打底得宝、打腻子)→机磨(大平面)→手磨(小面、曲面)→PU(第1道底漆)→ 机磨(打平面)→手磨(小面、曲面)→PE(第2道底漆)→打磨(机磨、 手磨)→修补→修色→手磨→面漆→干燥→试装→包装 板式车间 1.开料→手工→封边→钻孔→镂铣、开槽→清洗→试装→包装 2.开料→力刨→涂胶→贴面→冷压→精截→手工→封边→钻孔 →镂铣、开槽→清洗、修边→试装→包装 沙发车间 裁皮、开棉→打底(电车)→粘棉→扪皮(组装)→检验→包装
转椅车间 裁布(皮)、开棉→车位、粘绵→扪皮→组装→检验→包装 屏风车间 开料(铝材)→喷胶→贴绵→扪布(打钉)→组装→试装→包装 五金车间 1.椅架类: 开料→弯管→钻孔、攻牙→焊接→打磨→抛光→喷涂 2.钢板类: 开料→冲板(圆孔、圆凸、方孔、方凸、小梅花、大梅花、 网孔、菱凸)→折弯→焊接→打磨→喷涂 3.台架类: 开料→冲弯→钻孔、攻牙→焊接→打磨→抛光→喷涂 4.电镀类: 开料→开皮→冲弯→焊接→打磨→精抛→电镀 总:开料(裁剪、剪板)→制造(冲床、弯管、钻孔、攻牙)→成型(焊接、打磨、抛光)→喷涂、电镀 喷涂车间 清洗→凉干→打磨→喷漆(喷粉)→电烤→包装
镁合金板材各向异性实验研究
本科毕业设计(论文) 镁合金板材各向异性实验研究 刘阳 燕山大学 2014年6月
本科毕业设计(论文) 镁合金板材各向异性实验研究 学院:机械工程学院 专业:轧钢 学生姓名:刘阳 学号:100101010371 指导教师:石宝东 答辩日期:2014/6/20
燕山大学毕业设计(论文)任务书
摘要 摘要 由于具有密度低、比强度和比刚度高等特点,镁合金板日益广泛地应用于交通、家电和通讯领域。由轧制而导致的镁合金晶体的取向特征以及镁合金晶体自身对称性较差的特点,镁合金经常表现出较强的各向异性行为。本论文以此为研究对象,试验确定了三种不同厚度镁合金板材的各向异性行为,通过试验数据研究了AZ31型镁合金板材在室温下的各向异性屈服行为,从而为使用量大、具有良好应用前景的镁合金的各向异性唯象模型提供了大量的实验研究数据。 基于对三种不同厚度AZ31镁合金板材的基本力学性能的研究发现:镁合金板材在不同方向上力学性能不同,所研究的板材的力学性能都表现出了各向异性特征。 进一步研究表明,现有的金属塑性强化模型不能满足工程上的要求,畸变强化理论有利于弥补现有强化模型的缺陷。此外,通过多向单轴拉伸实验,测定了AZ31镁合金板材的初始屈服面和等塑性功面,系统的分析了等塑性功面的演变规律。 关键词AZ31镁合金板;各向异性;拉伸力学性能;屈服面
燕山大学本科生毕业设计(论文) Abstract Due to their good properties,such as low density,high specific strength and high specific stiffness , magnesium alloy sheets are widely applied in transportation , household appliance, communication and many other fields.Because of the orientations of magnesium alloy crystals by rolling and less symmetrical characteristics,magnesium alloys often show strong anisotropy behavior.In this paper, as a research object,Testing to determine the anisotropic behavior of three different thicknesses of magnesium alloy sheet,Through experimental data to study the anisotropic yield behavior of AZ31 magnesium alloy sheet type at room temperature,Anisotropic phenomenological model for the use of magnesium alloy so large,with good prospects of a large number of experimental studies provide data. Based on the basic mechanical properties of three different thicknesses AZ31 magnesium alloy sheet study found: magnesium alloy sheet in different directions different mechanical properties, the mechanical properties of the sheet are studied showed anisotropy. Further study showed that the existing metal plastic hardening model can not meet the requirements for building works,to compensate the distortion in favor of strengthening the existing theoretical models to strengthen the theoretical defects.In addition,multi-directional uniaxial tensile test and biaxial loading experiments,we measured the yield surface systems and functions such as shaping the surface of AZ31 magnesium alloy sheet, which systematically analyzes the evolution of the yield surface. Keywords AZ31 magnesium alloy plate anisotropy ; Anisotropy ;tensile mechanical properties ;yield surface;
服装生产工艺流程图汇总
服装生产工艺流程图 ┌——┐┌——┐┌———┐┌——┐┌——┐┌——┐┌——┐ │验布│→│裁剪│→│印绣花│→│缝制│→│整烫│→│检验│→│包装│ └——┘└——┘└———┘└——┘└——┘└——┘└——┘ 服装生产的工艺流程大全 (一)面辅料进厂检验 面料进厂后要进行数量清点以及外观和内在质量的检验,符合生产要求的才能投产使用。在批量生产前首先要进行技术准备,包括工艺单、样板的制定和样衣制作,样衣经客户确认后方能进入下一道生产流程。面料经过裁剪、缝制制成半成品,有些梭织物制成半成品后,根据特殊工艺要求,须进行后整理加工,例如成衣水洗、成衣砂洗、扭皱效果加工等等,最后通过锁眼钉扣辅助工序以及整烫工序,再经检验合格后包装入库。 (二)面料检验的目的和要求 把好面料质量关是控制成品质量重要的一环。通过对进厂面料的检验和测定可有效地提高服装的正品率。 面料检验包括外观质量和内在质量两大方面。外观上主要检验面料是否存在破损、污迹、织造疵点、色差等等问题。经砂洗的面料还应注意是否存在砂道、死褶印、披裂等砂洗疵点。影响外观的疵点在检验中均需用标记注出,在剪裁时避开使用。 面料的内在质量主要包括缩水率、色牢度和克重(姆米、盎司)三项内容。在进行检验取样时,应剪取不同生产厂家生产的、不同品种、不同颜色具有代表性的样品进行测试,以确保数据的准确度。 同时对进厂的辅料也要进行检验,例如松紧带缩水率,粘合衬粘合牢度,拉链顺滑程度等等,对不能符合要求的辅料不予投产使用。 (三)技术准备的主要内容 在批量生产前,首先要由技术人员做好大生产前的技术准备工作。技术准备包括工艺单、样板的制定和样衣的制作三个内容。技术准备是确保批量生产顺利进行以及最终成品符合客户要求的重要手段。 工艺单是服装加工中的指导性文件,它对服装的规格、缝制、整烫、包装等都提出了详细的要求,对服装辅料搭配、缝迹密度等细节问题也加以明确。服装加工中的各道工序都应严格参照工艺单的要求进行。 样板制作要求尺寸准确,规格齐全。相关部位轮廓线准确吻合。样板上应标明服装款号、部位、规格、丝绺方向及质量要求,并在有关拼接处加盖样板复合章。 在完成工艺单和样板制定工作后,可进行小批量样衣的生产,针对客户和工艺的要求及时修正不符点,并对工艺难点进行攻关,以便大批量流水作业顺利进行。样衣经过客户确认签字后成为重要的检验依据之一。 (四)裁剪工艺要求 裁剪前要先根据样板绘制出排料图,“完整、合理、节约”是排料的基本原则。在裁剪工序中主要工艺要求如下:(1)拖料时点清数量,注意避开疵点。(2)对于不同批染色或砂洗的面料要分批裁剪,防止同件服装上出现色差现象。对于一匹面料中存在色差现象的要进行色差排料。(3)排料时注意面料的丝绺顺直以及衣片的丝缕方向是否符合工艺要求,对于起绒面料(例如丝绒、天鹅绒、灯芯绒等)不可倒顺排料,否则会影响服装颜色的深浅。(4)对于条格纹的面料,拖料时要注意各层中条格对准并定位,以保证服装上条格的连贯和对称。(5)裁剪要求下刀准确,线条顺直流畅。铺型不得过厚,面料上下层不偏刀。(6)根据样板对位记号剪切刀口。(7)采用锥孔标记时应注意不要影响成衣的外观。裁剪后要进行清点
生产工艺流程示意图和工艺说明
AHF生产工艺流程示意图和工艺说明 干燥的萤石粉经螺旋机进入斗式提升机、卸入萤石粉储仓,再由储仓定时加入萤石计量斗,经电子秤,变频调节螺旋输送机将萤石粉定量送入反应器。 来自硫酸储槽的98%硫酸经电磁流量计、调节阀调节流量送至H2SO4吸收塔吸收尾气中的HF,而后进入洗涤塔洗涤反应气体夹带的粉尘及其夹带的重组分,然后进入混酸槽。发烟硫酸经电磁流量计、调节阀调节流量与98%硫酸配比计量后一并送至混酸槽。在混酸槽中经过混合,使SO3与98%硫酸中的水分及副反应水分充分反应,达到进料酸中水含量为零,而后进入反应器。进入反应器的萤石和硫酸严格控制配比,在加热的条件下氟化钙和硫酸进行反应。反应所需热量由通过转炉夹套的烟道气提供。烟道气来自燃烧炉由煤气燃烧产生。煤气发生炉产生的煤气经管道输送至燃烧炉。离开回转反应炉夹套的烟道气经烟道气循环风机大部分循环回燃烧炉,少量烟道气经烟囱排空。反应系统为微负压操作,炉渣干法处理。 反应生成的粗氟化氢气体,首先进入洗涤塔除去水分、硫酸和粉尘。洗涤塔出来的气体经粗冷器将其大部分水分、硫酸冷凝回洗涤塔。粗冷后的气体经HF水冷、一级冷凝器和二级冷凝器将大部分HF 冷凝,冷凝液流入粗氟化氢中间储槽;未凝气为SO2、CO2、SiF4、惰性气体及少量HF进入H2SO4吸收塔,用硫酸吸收大部分HF后进入尾气处理系统。粗HF凝液自粗HF中间储槽定量进入精馏塔,塔底为重组分物料,返回洗涤酸循环系统,塔顶HF经冷凝后进入脱气塔,从脱气塔底部得到无水氟化氢经成品冷却器冷却后进入AHF检验槽,分
析合格后进入AHF 储槽,后送至充装工序灌装槽车或钢瓶出售。从脱气塔顶排出的低沸物和部分未凝HF 气一起进入H 2SO 4吸收塔,在此大部分HF 被硫酸吸收。工艺尾气经水洗、碱洗后,除去尾气中的SiF 4及微量HF ,生成氟硅酸,废气经洗涤处理后达标排放。生产装置采用DCS 集散控制系统。 其化学反应过程如下: CaF 2+H 2SO 4?→? 2HF ↑+CaSO 4 (1) SiO 2+4HF ?→? SiF 4+2H 2O (2) SiF 4+2HF ?→ ?H 2SiF 6 (3) CaCO 3+H 2SO 4 ?→ ?CaSO 4+H 2O +CO 2 (4) ·生产采取的工艺技术主要包括7个生产装置 萤石干燥单元 萤石给料计量单元 酸给料计量单元 反应单元 精制单元 尾气回收单元 石膏处理单元 附:生产工艺流程示意图 ↓ ↓
镁合金材料工艺
镁合金发展 针对陕北的跨越式发展目标,提出了建设府谷、神木镁产业基地,推进榆林能源基地资源深度转化,拉长产业链条,加大财政引导资金投入力度,组建省级镁业企业集团,集中力量开展技术攻关,重点发展六种镁合金,加强镁业人才建设 镁锂合金材料是当今世界上最轻的金属结构材料,属于国际上列入高度保密的技术。今年年底,中国将在西安阎良国家航空高技术产业基地实现这种金属结构材料的规模化生产,用于航空、航天、能源等多个领域。 据西安交通大学材料专家柴东朗教授介绍,镁锂合金材料具有低密度、高塑性等特点,是当今世界上最轻的金属结构材料,可部分替代目前应用于航空、航天领域的铝材及其他铝合金材料,具有广泛的应用前景。中国对镁锂合金材料研究已有一段时间,但是大多数处于实验室阶段,直到2010年西安交通大学与西安四方超轻材料有限公司合作在西安阎良国家航空高技术产业基地建成了中国第一条镁锂合金生产线。 经过两年来的进一步研发,目前西安四方超轻材料有限公司已在镁锂合金的冶炼工艺、质量控制、表面处理、机械加工等方面取得了突破性成果,为产品的推广应用创造了良好条件。 根据规划,到今年年底,西安四方超轻材料有限公司镁锂合金超轻材料项目将实现规模化生产,预计可年产100吨镁锂合金超轻材料。 我国镁深加工能力很薄弱。虽然早在50年代后期镁压铸业就已经起步,先后有若干厂家生产林业用机械和工具、风动工具等镁合金压铸件。到了90年代初,在汽车工业、电子工业发展的带动下,国内的镁压铸业有了较大的发展。为3C等产品配套的镁合金压铸件厂主要云集在华南和江、浙地区,尤以珠江三角洲一带最为突出。这一地区受到香港、台湾两地资金的投入、技术的支撑、市场的开拓以及管理的介入等全方位的拉动,发展速度令人关注。 积极稳妥地发展镁产业实现镁合金产业化是一项涉及面广、技术集成度高的大型系统工程。近10多年来,在世界范围内相继建立的一大批镁合金压铸工
镁合金板材轧制技术
镁合金板材轧制技术 变形镁合金板材在电子、通讯、交通、航空航天等领域有着十分广泛的应用前景,但目前镁合金板材的应用仍然受到很大的限制,其产量及用量远不及钢铁及铝、铜等有色金属。制约镁合金板材发展的因素主要有两个:大部分的镁合金室温塑性变形能力较差,且轧制板材中存在严重的各向异性;镁合金板材制备工艺不够成熟,力学性能尚需进一步提高。 镁合金板材一般采用轧制的方法生产,因此了解镁合金轧制工艺流程、阐明轧制过程中组织性能的变化规律,对促进镁合金板材的轧制技术的发展是十分必要的。 1 镁合金轧制工艺流程 镁合金板材的轧制设备与铝合金相似,根据生产规模2、3或4辊轧机。镁合金轧制时所用的坯料可以是铸坯、挤压坯或锻坯。锭坯在轧制前需进行铣面,以除掉表面缺陷。塑性加工性能较好的镁合金如镁-锰(Mn<2.5%)和镁-锌-锆合金可直接用铸锭进行轧制,但铸锭轧制前一般应在高温下进行长时间的均匀化处理。对含铝量较高的镁-铝-锌系镁合金,用常规方法生产的铸锭轧制性能较差,因此常采用挤压坯进行轧制。镁合金轧制工艺流程如下:原料→熔炼→铸造→扁锭→锯切→铣面→一次加热→一次热轧→二次加热→二次热轧→剪切→三次加热→三次热轧→冷轧→酸洗→精轧→成品剪切→退火→涂漆→固化处理→检查→包装→运输。 1.1扁锭铸造 镁合金铸锭可用铁模铸造,也可用半连续或连续工艺铸造。铁模铸造时,铸锭厚度一般不大于60mm。而半连续或连续铸造时,铸锭厚度可达300mm以上,长度则可通过铸造井内安装的同步锯切设备锯切成所需尺寸。通常镁合金的注定尺寸为:(127~305)mm×(406~1041)mm×(914~2032)mm,宽度与厚度之比应控制在4.0左右为宜。铸锭的质量主要取决于冷却速度、金属凝固时结晶的方向性、熔体补给情况、铸造压力及铸造温度等工艺参数。 1.2铸锭加热 镁合金铸锭特别是含铝量较高的合金铸锭,在轧制前需要进行均匀化处理,以减小或消除成分偏析、提高铸锭的塑性成形能力。均匀化处理的温度范围为
镁合金板材轧制
5.4镁合金板材轧制变形镁合金板材在电子、通汛、交通、航空航天等领域有着卜分J‘泛的血用前景,但目前镁合金板材的应用仍然受到很大限制.其产量和用量均远不及钢铁及铝.铜等有色金属。制约镁合金板材发展的因素主要有两个:①大部分镁合金的室温塑性变形能力较差,且轧制板材中存在严重的各向异性;②镁合金板材制备工艺不够成熟,力学性能尚需进一步提高。镁合金板材一般采用轧制方法生产.因此了解镁合金轧制工艺流程、阐明轧制过程中组织性能的变化规律,对促进镁合金板材轧制技术的发展是十分必要的,5.4.1镁合金轧制工艺流程·i””\,.镁合金板材的生产工艺流程如图5—76所示。轧制设备与铝合金相似,根据乍产规模可采用2,3或4辊轧机(批量较小时可采用2辊轧机,大批量生产时则常用3辊或4辊轧机)。镁合金轧制用的坯料可以是铸坯、挤压坯或锻坯,锭坯在轧制前需进行铣面,以除掉表面缺陷。塑性加工性能较好的镁合金如镁—锰(Mn<2.5%)和镁—锌—锆合金可直接用铸锭进行轧制,但铸锭轧制前一般应在高温下进行长时间的均匀化处理。对含铝量较高的镁—铝—锌系镁合金,用常规方法生产的铸锭轧制性能较差,因此常采用挤压坯进行轧制。际tl堉焯铸造扁锭锯切铣面。图。令。图。令。抖。图次bU热二次0U 热—二次热轧啊训-:次加热次坤轧寸轧酞f;《枯轧6《川,蓟川退火汁漆闹/t:处煅检古包装运输图5~76镁合金板材轧制工艺流程·:239 陈振华主编.变形镁合金.化学工业出版社,2005年06月. 常用的镁合金为密排六方晶格结构,塑性加工性能较差,因此不能像铝合金、铜合金等立方晶格结构金属那样以很大的道次变形率(可达50%一60%)进行轧制。镁合金在室温附近轧制时,一般应将道次变形率控制在10%一15%左右。道次变形率过大时易发生严重的裂边,甚至表面开裂而使轧制过程无法继续进行。在再结晶温度以上轧制时,镁合金的塑性因棱柱面及锥面等潜在滑移系的启动而大幅度提高,因而大部分镁合金板材生产均采用热轧的方式,且在热轧过程中应进行反复加热。在Mg—以合金中,当锂含量为5%一10%(质量)时可形成。十p相(密排六方与体心立方的混合相),因此塑性加工性能变好;当合金中锂含量大于11%(质量)时,全部转化为体心立方相,可使镁合金轧制性能得到大幅度改善。5.4.1.1
设备生产制造工艺流程图
设备生产制造工艺流程图 主要部件制造要求和生产工艺见生产流程图: 1)箱形主梁工艺流程图 原材料预处理划线下料清理 材质单与喷涂划划数半剪清割坡 钢材上炉丸富出出控自除渣口 号批号一除锌拱外自动焊等打 一对应油底度形动气切区打磨 锈线线气割 割 校正对接拼焊无损探伤装配焊接清理 达度埋超X 确垂内工清焊到要弧声光保直部电除渣平求自波拍隔度先焊内杂直动片板用接腔物 焊手 检验装配点焊四条主缝焊接清理校正 内焊装成用Φ清磨修修振腔缝配箱埋HJ431 除光正正动检质下形弧直焊焊拱旁消验量盖主自流渣疤度弯除板梁动反应 焊接力自检打钢印专检待装配 操专质 作检量 者,控 代填制 号写表
2)小车架工艺流和 原材料预处理划线下料清理 材质单与喷涂划划数半剪清割坡 钢材上炉丸富出出控自除渣口 号批号一除锌拱外自动焊等打 一对应油底度形动气切区磨 锈线线气割 校正对接拼焊无损探伤装配焊接清理 达度埋超X 确垂内工清焊 到要弧声光保直部电除渣 平求自波拍隔度先焊内杂 直动片板用接腔物 焊手 检验装配点焊主缝焊接清理校正 内焊清磨修修振应腔缝除光正正动力检质焊焊拱旁消验量渣疤度弯除 自检划线整体加工清理 A表A表 行车行车 适用适用 自检打钢印专检待装配 操专质
作检量 者,控 代填制 号写表 3)车轮组装配工艺流程图 清洗检测润滑装配 煤清轮确尺轴部 油洗孔认寸承位 或轴等各及等加 洗承部种公工润 涤,位规差作滑 剂轴格剂 自检打钢印专检待装配 操 作 者 代 号 4)小车装配工艺流程图 准备清洗检测润滑 场按领煤清轴确尺轴加最注 地技取于油洗及认寸承油后油 清术各或轴孔各及内减 理文件洗承等件公、速件涤齿部规差齿箱 剂轮位格面内 装配自检空载运行检测标识入库 螺手起行噪 钉工升走音 松盘机机震 紧动构构动
镁铝合金表面处理工艺大全
镁铝合金表面处理工艺 大全 集团标准化工作小组 #Q8QGGQT-GX8G08Q8-GNQGJ8-MHHGN#
铝表面处理工艺一、选材 铝合金6061:镁铝6061-T651是6系合金的主要合金,是经热处理预拉伸工艺的高品质铝合金产品;镁铝6061具有加工性能极佳、良好的抗腐蚀性、韧性高及加工后不变形、上色膜容易、氧化效果极佳等优良特点。主要用途:广泛应用于要求有一定强度和抗蚀性高的各种工业结构件,如制造卡车、塔式建筑、船舶、电车、铁道车辆。 6061典型用途:代表用途包括航天固定装置、电器固定装置、通讯领域,也广泛应用于自动化机械零件、精密加工、模具制造、电子及精密仪器、SMT、PC板焊锡载具等等。 电镀是在表面添加一层金属保护层。阳极氧化是把表面一层人为按要求用电化学进行氧化,用这层氧化层作保护层。铝不好电镀,但氧化铝很硬(可作磨料),化学性能又特好(不会再氧化,不受酸腐蚀),比一般金属还好,还可以染成各种颜色。所以铝件一般用阳极氧化。 二、工艺类型、效果图、厂家调研 氧化工艺 喷砂可以使丝印时,印料和承印物的结合更加牢固。均匀适当的喷砂处理,基本上可以克服铝材表面常见的缺陷。详见附录 、喷涂工艺 1、表面处理工艺:机壳漆
机壳漆金属感极好,耐醇性佳,可复涂PU或UV光油。玩具油漆重金属含量符合国际安全标准。包括CPSC含铅量标准、美国测试标准ASTMF 963、欧洲标准 EN71、EN1122。 2、表面处理工艺:变色龙 随不同角度而变化出不同颜色。是一种多角度幻变特殊涂料,使你的商品价值提高,创造出无懈可击的超卓外观效果。 3、表面处理工艺:电镀银涂料 电镀银漆是一款无毒仿电镀效果油漆,适用ABS、PC、金属工件,具有极佳的仿电镀效果和优异的耐醇性。 4、表面处理工艺:橡胶漆 适用范围:ABS、PC、PS、PP、PA以及五金工件。 产品特点:本产品为单组份油漆,质感如同软性橡胶,富有弹性,手感柔和,具有防污、防溶剂等功能。这种油漆干燥后可得涂丝印。重金属含量符合国际安全标准。包括CPSC含铅量标准、美国测试标准ASTMF 963、欧洲标准EN71、EN1122。5、表面处理工艺:导电漆 适用于各种 PS 及 ABS 塑料制品;导电导磁、对外界电磁波、磁力线都能起到屏蔽作用;在电气功能上达到以塑料代替金属的目的。电阻值可根据客人要求调试。重金属含量符合国际安全标准,包括 CPSC 含铅量标准、美国测试标准 ASTMF-963 、欧洲标准 EN71 、EN1122。 6、表面处理工艺:UV油
镁及镁合金板材的生产工艺流程(一)
镁及镁合金板材的生产工艺流程(一) 镁及镁合金板材的生产工艺流程为: 1、熔炼与铸锭 熔炼包括熔化、合金化、精炼、晶粒细化、过滤等冶金和物理化学过程,通常在反射炉或坩埚炉内进行。镁及镁合金的熔点都在650℃左右,它们极易氧化且随温度的升高而加剧。当温度超过约850℃时,熔体的表面立即燃烧,故熔炼时必须用熔剂覆盖或以保护性气体保护。镁及镁合金在熔融和燃烧状态下遇水、含水(包括结晶水)物质和液态防火介质都可能导致剧烈爆炸,因此,在生产的全过程中注意安全是至关重要的。以隔离空气为主的覆盖熔剂和以提高熔体质量为主的精炼熔剂都是碱金属或碱土金属的氯化物和氟化物。除气(主要是氢)随熔剂精炼进行,也可向熔体中通入活性气体(如氯气)。对凝固时的晶粒粗大倾向,据合金的不同可采取控制熔体温度、向熔体加入微量元素进行变质处理等加以抑制,即晶粒细化(见铸锭晶粒的细化处理)。铸锭通常采用半连续铸锭法。除封闭式铸锭外,流槽和结晶器中裸露的金属,必须用s0:或SF。等气体保护。要科学地确定和控制各项铸造参数,以防止铸锭发生热裂,并降低冷隔深度和减少金属间化合物的形成和聚集。除镁一钇系合金外,铸锭的冷裂倾向小。 2、加热与热轧 铸锭在加热前必须铣面(见有色金属合金锭坯铣面),彻底去除冷隔和偏析物等表面缺陷;合金元素含量高和含锆、钇等的合金还要经均匀化处理(见有色金属合金锭坯均匀化)。铸锭加热时应避免直接热辐射和避免火焰同铝接触,以防局部过热、熔化或燃烧。根据合金的不同加热温度控制在370~510℃范围内。除含锂高的超轻合金有晶型转变外,余者皆为密排六方晶型,塑性差,但变形能力随加热温度的提高和晶粒尺寸的减小而提高,并比立方晶型的金属提高得更快。热轧的总变形量可以达到96%。严格控制终轧温度是保证热加工状态成品板材的力学性能并防止板坯及薄板产生裂纹的重要途径。晶粒粗大的铸锭和厚度较小的热轧成品,有的要进行二次加热和热轧。热轧要求轧辊保持良好的温度条件。轧辊温度的高低和分布状况能影响轧制的成败。工艺润滑(见塑性加工工艺润滑)不可采用通常的水溶性乳化液,为防止金属粘辊和控制辊型(见辊型控制),可向辊面喷射少量多碳原子的单烷烃水溶液。热轧最小的终了厚度为6~10mm。 3、温轧 温轧又可分为温粗轧和温精轧。温轧要反复进行多次,两次温轧之间应对坯料进行中间加热,加热温度要高于再结晶退火温度。温粗轧的终轧温度一般不低于250℃,总变形量可达65%。随着坯料或成品厚度的减小,加热温度和随后的终轧温度可相应降低。每次温轧的总变形量视合金的不同控制在26%~65%的范围内。轧辊的温度条件也是进行有效轧制的重要保障。因此,充分利用坯料和轧辊的温度条件是十分重要的。工艺润滑可用分子量较小的单烷烃水溶液,也可用煤油等。厚度较薄(如0.5mm)的低成分镁合金还可进行叠轧(见叠轧薄板生产)。为提高板材的表面质量,温粗轧之后,对坯料应进行一次较彻底的清理,最有效的方法是在硝酸溶液中浸洗。
镁合金焊接
镁合金焊接技术研究 2010年02月25日 0 前言 近10年来,由于受到能源节约以及环境保护的巨大推动,镁合金及其焊接技术的发展比任何时期都快,从焊接方法、焊接材料到焊接设备等方面都不断有新的突破,为镁合金焊接生产向优质、高效、低成本的方向发展提供了前所未有的良好条件,并大大促进了镁合金的产业化进程。 镁合金由于其自身的物理化学特点,导致其焊接有很大困难,满意的焊接质量不易获得。镁合金的结晶温度区大,易于产生热裂纹;镁的沸点低,温度进一步升高后,其蒸气压比在相同温度下的铝合金要高4-5倍,因而焊接时温度一旦过高,镁会气化,产生爆炸形成飞溅;镁对氧的亲和力大,其氧化物密度较大,而容易形成夹杂;镁在接近熔化温度时,能与空气中的氮强烈化合生成脆性的镁的氮化物,显著降低接头力学性能;因此,实现镁合金优质焊接是比较困难的,在焊接时容易产生裂纹、气孔、飞溅等缺陷。但是由于工业的迫切需要,许多科学工作者做出了很大的努力,并取得了一些重要成果。 本文介绍大连理工大学近年来开展的镁合金同种及其与异质材料的焊接研究工作,并展望了镁合金焊接技术在镁合金新型结构件产品上的应用。 1 激光焊接技术 1.1同种镁合金的激光焊接 激光焊接作为一种先进的连接技术,具有速度快、线能量低、焊后变形小、接头强度高等优点,得到了人们极大的关注。采用脉冲YAG激光对AZ31B变形镁合金进行对接焊,结果表明,镁合金激光焊焊缝变形小,成型美观,无裂纹等表面缺陷、背面熔透均匀,如图1所示。焊接接头热影响区不明显,无晶粒长大现象;焊缝区由细小的等轴晶组成,如图2所示。在本试验条件下,接头的抗拉强度可达母材的95%以上,实现了镁合金的良好连接。研究表明,激光焊接对焊接工艺参数要求严格,同时镁合金激光焊接过程中易出现裂纹、气孔、热影响区脆化和激光能量吸收率低等系列问题。 图1 激光焊焊缝表面形貌图2 镁合金激光焊接接头组织 1.2镁合金与铝合金的激光焊接 镁铝异种金属可以通过真空扩散焊、爆炸焊、搅拌摩擦焊等方法实现一定程度的连接,但其结合强度并不理想。造成这种结果的主要原因是两种材料焊接时在熔池内部形成了高硬度高脆性的金属间化合物。 SiC颗粒在铸造领域常常与镁、铝合金结合形成复合材料,可以细化材料的微观组织并且全面地提高机械性能;其在表面熔覆的工艺中也经常得到应用。针对SiC的性质及其在镁、铝复合材料中应
镁和镁合金的焊接工艺要点
毕业设计(论文)、 题目镁和镁合金的焊接工艺 专业焊接技术及自动化 班级学号11G51218 姓名刘东洵 指导教师赵丽玲 2014 年06 月06 日
目录 1 绪论 (4) 2 课题的背景 (5) 3 材料介绍 (6) 4 激光焊接技术 (7) 1)同种镁合金的激光焊接 (7) 2)镁合金与铝合金的激光焊接 (7) 5 等离子弧焊技术 (8) 1)同种镁合金的变极性等离子弧焊 (8) 2)镁合金的变极性等离子弧缝焊 (9) 6 低能耗激光诱导增强电弧复合焊接技术 (9) 1)同种镁合金板材的焊接 (9) 2)同种镁合金薄板的焊接 (10) 3)异种镁合金板材的焊接 (10) 4)镁合金与钢异种金属的焊接 (11) 7活性焊接技术 (12) 1) 镁合金活性焊接 (12) 2)镁合金活性焊丝填丝焊接 (12) 8 熔化胶接焊焊接技术 (13) 1) 镁合金等离子弧胶接焊 (14)
2) 镁合金与铝合金的激光胶接焊 (14) 9 镁合金与铝合金的扩散焊接技术 (15) 10 镁合金焊接接头电弧喷涂防护技术 (16) 11 镁合金焊接技术的应用及展望 (17) 12 结论 (18) 13 参考文献 (19) 14 致谢 (20)
1. 绪论 近10年来,由于受到能源节约以及环境保护的巨大推动,镁合金及其焊接技术的发展比任何时期都快,从焊接方法、焊接材料到焊接设备等方面都不断有新的突破,为镁合金焊接生产向优质、高效、低成本的方向发展提供了前所未有的良好条件,并大大促进了镁合金的产业化进程。 镁合金由于其自身的物理化学特点,导致其焊接有很大困难,满意的焊接质量不易获得。镁合金的结晶温度区大,易于产生热裂纹;镁的沸点低,温度进一步升高后,其蒸气压比在相同温度下的铝合金要高4-5倍,因而焊接时温度一旦过高,镁会气化,产生爆炸形成飞溅;镁对氧的亲和力大,其氧化物密度较大,而容易形成夹杂;镁在接近熔化温度时,能与空气中的氮强烈化合生成脆性的镁的氮化物,显著降低接头力学性能;因此,实现镁合金优质焊接是比较困难的,在焊接时容易产生裂纹、气孔、飞溅等缺陷。但是由于工业的迫切需要,许多科学工作者做出了很大的努力,并取得了一些重要成果。
生产工艺流程及产排污点位示意图知识讲解
1、 4000t/a α-羟基环己基甲酰苯项目 1.1化学方程式 COOH PCl 3 COCl 3 3 H 3PO 3 AlCl O HCl COCl HCl COCl H 2O COOH O HCl Cl 2 O Cl NaCl O Cl O OH 副反应: O HCl Cl 2 O Cl
NaOH NaCl O Cl O OH H 2O COOH NaOH COONa 1.2 生产工艺流程 (1) 项目生产工艺流程及污染物产生点位见图1.2-1。
备注:Gn-废气污染物、Wn-水污染物、Sn-固体废物。 图1.2-1 项目生产工艺流程及污染物产生点位图 (2)工艺过程简述: a、酰氯化
将一定量的环己甲酸及三氯化磷加入酰氯化釜,蒸汽加热至70℃,常压下进行酰氯化反应,反应结束后过滤,中间产品环己酰氯进库。副产品亚磷酸出售。 b、合成 将一定量的三氯化铝和苯加入合成釜,滴加环己酰氯,冷冻盐水控制温度20℃左右进行反应,反应过程中产生的氯化氢气体经水吸收生成副产品盐酸(未吸收含氯气、HCl废气G2-1去废气处理装置)。反应结束后合成液去水解釜。(本条件下生产的产品的规格为99.5%) c、水解、酸洗向水解釜中加入一定量水,保持温度40℃进行水解,水解结束后,下层废水去碱式氯化铝工段。再向釜中加入水和盐酸,升温至55℃进行酸洗,下层的废水去碱式氯化铝工段,上层去脱溶釜。 d、脱溶 蒸汽加热至110℃,常压下进行脱溶,脱出的苯去苯中间罐回用(含苯不凝废气G2-2去废气处理装置),剩余物去氯化釜。 e、氯化 向氯化釜中缓慢通入氯气,用循环水将釜温冷却至45℃进行氯化反应。反应过程中产生的氯化氢气体经水吸收后生成副产品盐酸。反应结束后,氯化液去碱解釜。 f、碱解 碱解釜中加入一定量的氢氧化钠溶液和水,蒸汽加热至65℃进行碱解。结束后,分层,下层废水W2-1去厂污水预处理设施。上层有机层去精馏釜。 g、精馏 将精馏釜用导热油加热至190℃、-0.1KPa下精馏,α-羟基环己基甲酰苯粗品去结晶釜(含α-羟基环己基甲酰苯不凝废气G2-3去废气处理装置)。 h、结晶
镁铝合金表面处理工艺大全
铝表面处理工艺 一、选材 1.1铝合金6061:镁铝6061-T651是6系合金的主要合金,是经热处理预拉伸工艺的高品质铝合金产品;镁铝6061具有加工性能极佳、良好的抗腐蚀性、韧性高及加工后不变形、上色膜容易、氧化效果极佳等优良特点。主要用途:广泛应用于要求有一定强度和抗蚀性高的各种工业结构件,如制造卡车、塔式建筑、船舶、电车、铁道车辆。 6061典型用途:代表用途包括航天固定装置、电器固定装置、通讯领域,也广泛应用于自动化机械零件、精密加工、模具制造、电子及精密仪器、SMT、PC板焊锡载具等等。 1.2电镀是在表面添加一层金属保护层。阳极氧化是把表面一层人为按要求用电化学进行氧化,用这层氧化层作保护层。铝不好电镀,但氧化铝很硬(可作磨料),化学性能又特好(不会再氧化,不受酸腐蚀),比一般金属还好,还可以染成各种颜色。所以铝件一般用阳极氧化。
二、工艺类型、效果图、厂家调研 2.1氧化工艺
喷砂可以使丝印时,印料和承印物的结合更加牢固。均匀适当的喷砂处理,基本上可以克服铝材表面常见的缺陷。详见附录
2.2、喷涂工艺
1、表面处理工艺:机壳漆 机壳漆金属感极好,耐醇性佳,可复涂PU或UV光油。玩具油漆重金属含量符合国际安全标准。包括CPSC含铅量标准、美国测试标准ASTMF 963、欧洲标准EN71、EN1122。 2、表面处理工艺:变色龙 随不同角度而变化出不同颜色。是一种多角度幻变特殊涂料,使你的商品价值提高,创造出无懈可击的超卓外观效果。 3、表面处理工艺:电镀银涂料 电镀银漆是一款无毒仿电镀效果油漆,适用ABS、PC、金属工件,具有极佳的仿电镀效果和优异的耐醇性。 4、表面处理工艺:橡胶漆 适用范围:ABS、PC、PS、PP、PA以及五金工件。 产品特点:本产品为单组份油漆,质感如同软性橡胶,富有弹性,手感柔和,具有防污、防溶剂等功能。这种油漆干燥后可得涂丝印。重金属含量符合国际安全标准。包括CPSC含铅量标准、美国测试标准ASTMF 963、欧洲标准EN71、EN1122。 5、表面处理工艺:导电漆 适用于各种PS 及ABS 塑料制品;导电导磁、对外界电磁波、磁力线都能起到屏蔽作用;在电气功能上达到以塑料代替金属的目的。电阻值可根据客人要求调试。重金属含量符合国际安全标准,包括CPSC 含铅量标准、美国测试标准ASTMF-963 、欧洲标准EN71 、EN1122。 6、表面处理工艺:UV油 高性能UV固化光油,类似钢琴漆。 7、表面处理工艺:珠光粉-ZG001 珠光颜料广泛应用于化妆品、塑料、印刷油墨及汽车涂料等行业。珠光颜料的主要类型有:天然鱼鳞珠光颜料、氯氧化铋结晶珠光颜料、云母涂覆珠光颜料。 8、表面处理工艺:夜光漆 夜光粉是一种能在黑暗中发光的粉末添加剂;它可以与任何一种透明涂层或外涂层混和使用,效果更显著,晚上发光时间长达8小时! 2.3、印刷工艺