Q)G13J-B-11-08压力管道检验通用规程
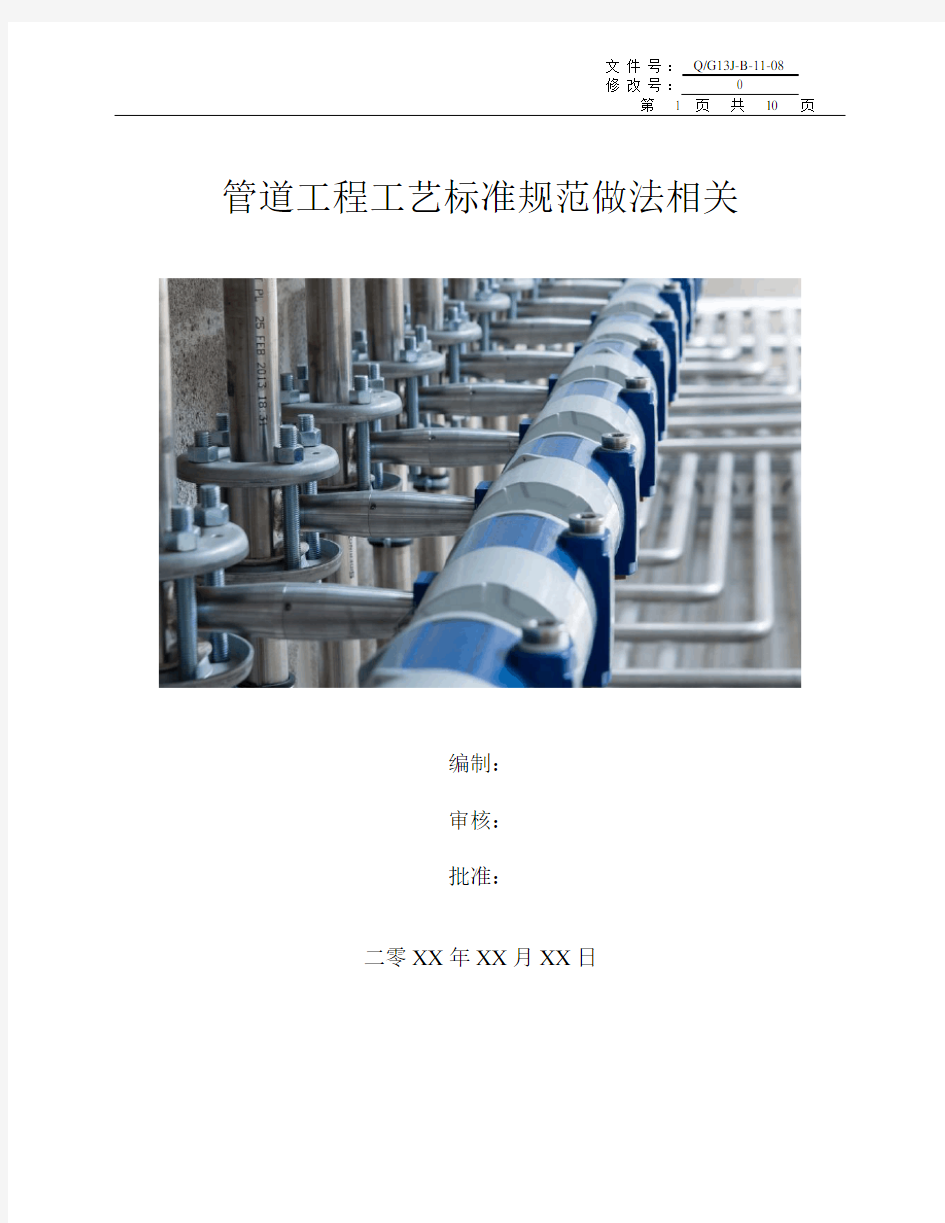

管道工程工艺标准规范做法相关
编制:
审核:
批准:
二零XX年XX月XX日
压力管道检验通用规程
编制日期
审查日期
批准日期
1总则
1.1本守则适用于GB50235-97、GB50236-98标准规定的碳钢、不锈钢管道检验。
1.2依据:
《压力管道安全管理与监察规定》
《工业金属管道工程施工及验收规范》(GB50235-97)
《现场设备、工业金属管道焊接工程施工及验收规范》(GB50236-98)
《低中压锅炉用无缝钢管》(GB3087-82)
《输送流体用无缝钢管》(GB/T8163-99)
《钢管的验收、包装、标志和质量证明书》(2102-88)
《碳钢焊条》(GB/T5117-1995)
《不锈钢焊条》(GB/T983-1995)
《化工设备、管道防腐蚀工程施工及验收规范》(HGJ229-83)
2 压力管道安装的检验分为二类
2.1材料质量检验;
2.2压力管道安装质量检验;
3 材料质量检验
3.1管道、管道组成件及管道支承件的检验
3.1.1管材、管件必须有制造厂的合格证明书,否则要补作所缺项目的检验,其指标要符合现行国家和部颁技术标准。
3.1.2管材、管件在入库及使用前应按要求核对其规格、材质、型号。
3.1.3管材、管件在使用前应进行外观检查,要求其表面○1无裂纹、缩孔、夹渣、折叠、重皮等缺陷;○2锈蚀或凹陷不超过壁厚负偏差、螺纹密封面良好,精度及粗糙度达到设计要求或制造标准;合金钢管及管件应有材质标记。
3.1.4合金钢管及管件在使用前均应用光谱分析或其它方法进行复查,并作标记。
3.1.5设计文件要求进行低温冲击韧性试验的材料,供货方应提供低温冲击韧性试验结果的文件,其指标不能低于设计文件的规定。
3.1.6设计文件要求进行晶间腐蚀试验的不锈钢管子及管件,供货方应提供晶间腐蚀试验结果的文件,其指标不能低于设计文件的要求。
3.2无缝钢管检验
根据公司的具体情况,如一般使用20#(GB3087、GB8163)无缝钢管。
3.2.1检查质量证明书、标识,质量证明书应由供方技术部门盖章,并应有如下内容:
○1供方名称或标记;○2需方名称、发货日期、合同号;○3产品标准号;○4钢的牌号;○5炉号、批号、交货状态、重量(或根数)和件数;○6品种名称、规格和质量等级;○7产品标准规定的各项检验结果;○8技术监督部门的印记,外径≥38mm的钢管的端部还应有标记,标记内容应包括钢的牌号、产品的规格、标准号、供方商标或印记。
3.2.2外径和壁厚允许偏差应符合表一要求。
3.2.3长度
1) 通常长度规定如下
热轧钢管3~12m
冷拔(轧)钢管 3~10.5m
2) 对于定尺长度和倍尺长度的钢管长度允许偏差如下:
GB3087:定尺长度应在通用长度范围内,长度允许偏差为+20mm
倍尺长度应在通用长度范围内,全长允许偏差为+20mm
GB8163:定尺长度应在通用范围内,长度允许偏差按如下规定:
长度≤6m 0~+10mm
长度<6m 0~+10mm
倍尺长度应在通用范围内,全长允许偏差为+20mm
3.2.4钢管的弯曲度按下规定检查:
壁厚≤15mm 1.5mm/m
壁厚>15mm 2.0mm/m
对于外径大于或等于325mm热轧管,每米弯曲度不大于3mm
3.3
3.3.1弯头、异径管、法兰、三通、补偿器、阀门等各类管件的表面缺陷和尺寸偏差要符合现行国家及部颁标准。
3.3.2应按设计要求,查明核对所适用的公称通径和公称压力。
3.4下面列出部分重要管件的检验规定:
3.4.1法兰:材质、规格和尺寸偏差应符合国家标准,密封面要平整光洁,不得有毛刺及径向沟槽。凹凸面法兰应能自然嵌合,凸面的高度不得低于凹槽的深度。
3.4.2管件连接用螺栓及螺母:螺纹要完整,无伤痕、毛刺等缺陷,螺栓与螺母要配合良好,无松动或卡涩现象。螺栓拧固后,螺杆伸出螺母的长度要符合要求。
3.4.3垫片:管件所用各种垫片要符合下列要求:
1)石棉橡胶、橡胶、塑料等非金属垫片应质地柔软,无老化变质或分层现象。表面不应有折损、皱纹等缺陷。
2)金属垫片的加工尺寸、精度、粗糙度及硬度要符合要求,表面要无裂纹、毛刺、凹槽、径向划痕及锈斑等缺陷。
3)包金属及缠绕式垫片不能有径向划痕、松散、翘曲等缺陷。
3.4.4阀门
阀门的检验应符合下列规定:
1) 核对产品合格证、规格、型号是否符合订购货要求,内、外部检查应符合标准规定。
2) 合金钢阀门的内件材质应进行抽查,每批(同制造厂、同规格、同型号、同时到货,下同)抽查数量不得少于1个。
3) 下列管道的阀门,应逐个进行壳体压力试验和密封试验。不合格者,不得使用。a.输送有毒流体、可燃液体管道的阀门;b.输送设计压力>1MPa或设计压力≤1MPa且设计温度<-29℃或>186℃的非可燃液体、无毒流体管道的阀门。
4) 输送设计压力≤1MPa且设计温度为-29~186℃的非可燃液体、无毒流体管道的阀门,应从每批中批查10%,且不得少于1个,进行壳体压力试验和密封试验。当不合格时(有一个不合格,下同),应加倍抽查,仍不合格时,该批阀门不得使用。
5) 阀门的壳体试验压力为公称压力的1.5倍,试验时间不得少于5分钟,以壳体填料无渗漏为合格;密封试验以公称压力进行,以阀瓣密封面不漏为合格。
6) 带有蒸汽夹套的阀门,夹套部分应以1.5倍的蒸汽工作压力进行压力试验。
7) 试验合格的阀门,应及时排尽内部积水,并吹干。除需要脱脂的阀门外,密封面上应涂防锈油,关闭阀门,封闭出入口,做出明显的标识,并按规定的格式填写“阀门试验记录”。
3.4.5安全阀检验
安全阀应核对产品合格证、规格、型号,进行内、外部检查,合格后送当地计量部门校验,校验合格后方可安装。
3.4.6弯制弯头的检验
弯头的检验应符合下列规定:
3.4.6.1 弯曲半径应符合表二的规定:
3.4.6.2管子弯制后的质量应符合下列要求
1) 无裂纹、分层、过烧等缺陷;
2) 壁厚减薄率不得超过15%;
3) 椭圆率不得超过8%;
4) 弯曲角度a的偏差值按如下规定检验:
机械弯管不得超过±3mm/m,当直管长度大于3m时,其总偏差最大不得超过±10mm。
热煨弯管不得超过±5mm/m,当直管长度大于3m时,其总偏差最大不得超过±15mm。
4 管道焊接检验
管道焊接应按《工业金属管道工程施工及验收规范》(GB50235-97)
《现场设备、工业金属管道焊接工程施工验收规范》(GB50236-98)规定执行。
4.1焊接前检查
4.1.1焊接母材及焊接材料的检查:
1) 焊接母材应符合设计文件及现行相应国家标准的要求。
2 )焊接材料应符合设计文件及现行相应国家标准的要求,质量证明书、合格证、标志齐全。施焊用的电焊条应确认无变质方可使用。施工现场的焊接材料贮存场所及烘干、去污设施应符合规定,并建立
保管、烘干、清洗、发放制度。
4.1.2道组成件组对时,结构尺寸应符合设计文件的规定,坡口形式和尺寸应符合设计文件、焊接工艺指导书或国家标准的规定。坡口表面不得有夹层、裂纹、加工损伤、毛刺及火焰切割熔渣等缺陷。对坡口及其内外表面进行清理后的检查应符合下表三的规定。
4.1.3
4.2
4.2.1定位焊缝焊完后,应清除渣皮进行检查,对发现的缺陷应去除后方可进行焊接。
4.2.2对焊接线能量有规定的焊缝,施焊时应测量电弧电压、焊接电流及焊接速度并应记录,焊接线能量应符合焊接工艺指导书的规定。
4.2.3当对焊缝层次有明确规定时,应检查焊接层数,其层次数及每层厚度应符合焊接工艺指导书的规定。多层焊每层焊完后,应立即清理并进行检查,发现缺陷消除后方可进行下一层的焊接。
4.2.4焊接双面焊件时应清理并检查焊缝根部的背面,消除缺陷后方可施焊背面焊缝。
4.3焊接后检查
4.3.1 焊缝外观检查:除焊接工艺指导书有特殊要求的焊缝外,焊缝应在焊完后立即去除渣皮、飞溅物,清理干净焊缝表面,然后对焊缝外部质量检查。焊缝外观质量应符合下列规定:
1) 设计文件规定焊缝系数为1的焊缝或规定进行100%射线检测的焊缝,其焊缝外观质量不得低于下
表五(焊缝质量分级标准)规定的II级。
2) 设计文件规定进行局部射线检测或超声波检测的焊缝,其外观质量不得低于下表中的III级。
3) 不要求进行无损检测的焊缝,其外观质量不得低于下表中的IV级。
4.3.2对接焊缝内部质量检查
1 )设计文件等要求进行100%射线检测的管道焊缝应进行100%射线检测,其质量不得低于II级,输送剧毒流体的管道必须进行。
2) 输送设计压力小于或等于1MPa且设计温度小于400℃的非可燃液体管道、无毒流体管道的焊缝,可不进行射线检测。
3) 其它管道应进行抽样射线检测,抽检比例不得低于5%,其质量不得低III级。抽检比例和质量等级应符合设计文件的要求。
4) 对不要求进行内部质量检验的焊缝,质检人员应对全部焊缝进行外观检验。
5) 对焊缝射线检测质量等级的划分见《现场设备、工业管道焊接工程施工及验收规范》。
5 管道安装检查
5.1管道安装前检查:
5.1.1与管道有关的土建工程检验合格,满足管道安装要求,并已办理交接手续。
5.1.2与管道连接的机械已安装合格,固定完毕。
5.1.3管道组成件及管道支承件已检验合格。
5.1.4管子、管件、阀门等内部已清理干净,无杂物。对管内有特殊要求的管道,其质量经检验符合设计文件的规定。
5.1.5在管道安装前必须完成的脱脂、内部防腐、衬里等有关工序已完成,并经检验合格。
5.2管道预制检查
自由管段和封闭管段的选择应合理,封闭管段应按现场实测后的安装长度加工。
自由管段和封闭管段的加工尺寸允许偏差应符合下表六的规定。
5.3钢制管道安装检查
5.3.1管道安装时,应检查法兰密封面及密封垫片,不得有影响密封性能的划痕、斑点等。大直径垫片需要拼接时,应采用斜口搭接或迷宫式拼接,不得平口对接。软垫片的周边应整齐,垫片尺寸应与法兰密封面相符,允许偏差应符合下表七的规定。
。
5.3.2管子对口:管子对口时应在距接口200mm处测量平直度。当管子公称直径小于100mm时,允许偏差1mm;当管子公称直径大于等于100mm时,允许偏差为2mm。全长允许偏差均不得大于10mm。
5.3.3弯管制作质量的检查
1) 不得有裂纹(目测或依据设计文件规定);
2) 不得存在过烧、分层等缺陷;
3) 不宜有皱纹;
4) 弯管任一截面上的最大外径与最小外径差,不得超过制作弯管前管子的外径的8%。
5) Π形弯管平面度允许偏差△应符合下表八的规定。
5.3.4管道安装的允许偏差应按下表九的规定进行检查:
5.3.5连接机械的管道安装质量检查
1) 连接机械的管道,其固定焊口应远离机器。
2) 管道与机器连接前,应在自由状态下,检查法兰的平行度和同轴度,允许偏差应符合下表十的规定。
3) 管道系统与机器最终连接时,应在联轴节上架设百分表测量机器位移。当转速大于6000r/min时,位移值应小于0.02mm;当转速小于6000r/min时,位移值应小于0.05mm。
5.3.6补偿器安装检查
1) 检查补偿器的安装是否合理,应符合设计文件及相应国家标准、规范的要求。
2) 检查补偿器的固定支架、导向支架、滑动支架的安装是否合理,应符合设计文件及国家现行相应标准、规范的要求。
3) Π形或Ω形补偿器应按设计文件规定进行预拉伸或压缩,允许偏差为±10mm。
5.3.7阀门安装质量的检查
阀门安装质量的检查应按《工业金属管道工程施工及验收规范》及本公司《工业管道安装通用工艺规程》、《阀门试压通用工艺规程》的规定执行。
5.3.8管道支、吊架安装质量的检查按《工业金属管道工程施工及验收规范》及本公司《工业管道安装通用工艺规程》的规定执行。
6管道系统安装完成后的质量检验
1) 综合检查管道系统安装的合理性,应符合设计文件的要求及相应国家标准、规范的要求。
2) 按设计文件或国家标准、规范的要求进行焊缝外观检查及无损照相检测。
3) 在以上检查均合格后,对管道系统按设计文件要求或按国家标准、规范的要求进行压力试验,以检
查管道系统各连接部位的工程质量。
4) 管道系统的压力试验应按设计文件、图纸的规定及《工业金属管道工程施工及验收规范》(GB50235-97)的规定进行,同时应遵守本公司《管道强度、严密性试验通用工艺守则》的规定。
7管道系统的清洗和吹扫质量的检验
管道系统的清洗和吹扫质量的检查应符合《工业金属管道工程施工及验收规范》(GB50235-97)及本公司《压力管道吹扫与清洗通用工艺守则》的规定。
8管道防腐工程质量的检验
管道防腐工程质量的检查应符合《工业金属管道工程施工及验收规范》(GB50235-97)及国家现行标准《工业设备、管道防腐蚀工程施工及验收规范》及本公司《压力管道防腐通用工艺守则》的规定。