力矩转换

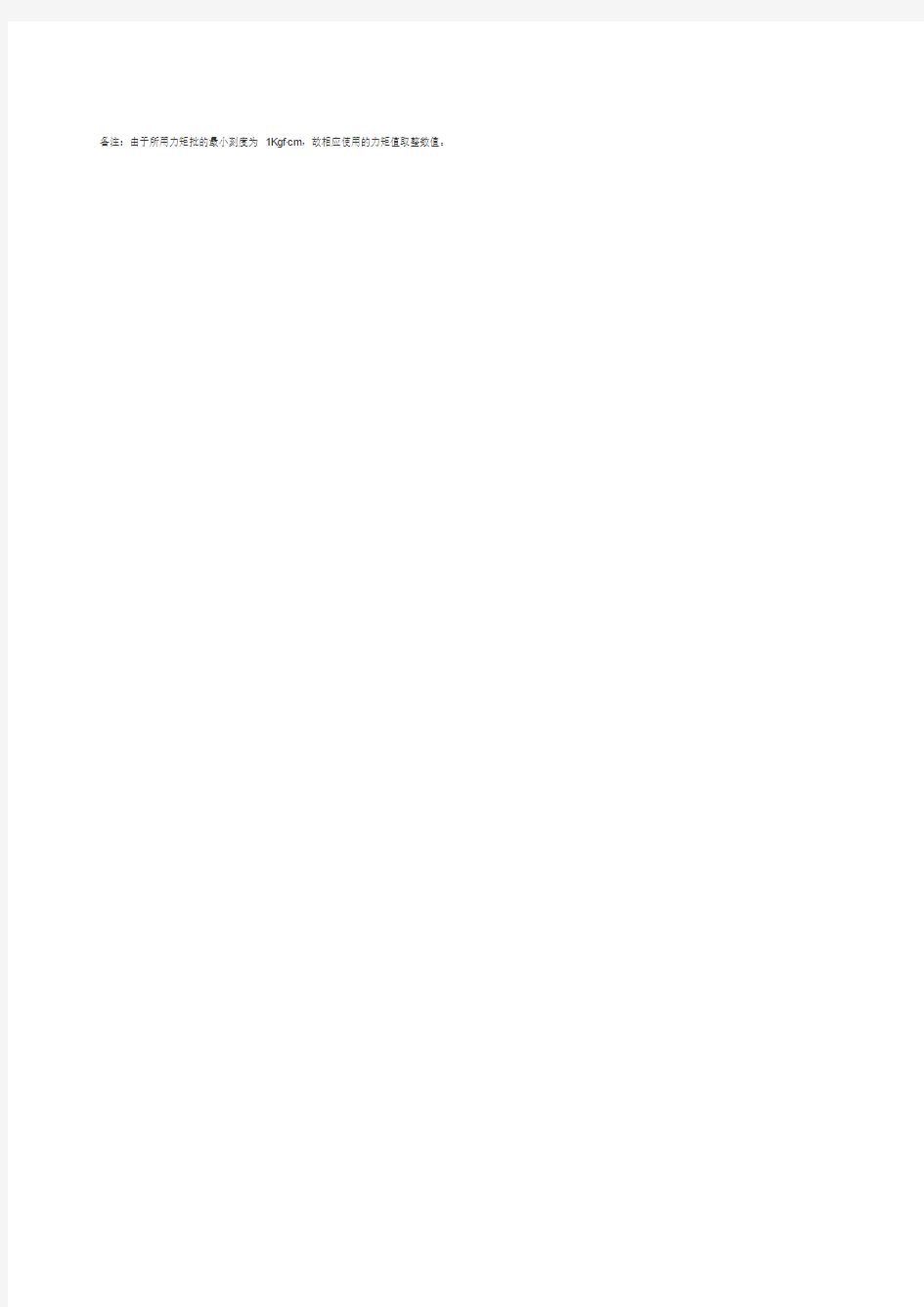
力矩单位换算对照表车间使用力
矩(Kgf·cm)
序号牛·米(N·m)千克力·米(Kgf·m)克力·厘米(gf·cm)千克力·厘米(Kgf·cm)
1 1 0.10197
2 10197.2 10.1972 10
2 0.1 0.0101972 1019.72 1.01972 1
3 0.2 0.020394
4 2039.44 2.03944 2
4 0.3 0.0305916 3059.16 3.05916 3
5 0.4 0.0407888 4078.88 4.07888 4
6 0.5 0.050986 5098.6 5.0986 5
7 0.6 0.0611832 6118.32 6.11832 6
8 0.7 0.0713804 7138.04 7.13804 7
9 0.8 0.0815776 8157.76 8.15776 8
10 0.9 0.0917748 9177.48 9.17748 9
11 1 0.101972 10197.2 10.1972 10
12 1.1 0.1121692 11216.92 11.21692 11
13 1.2 0.1223664 12236.64 12.23664 12
14 1.3 0.1325636 13256.36 13.25636 13
15 1.4 0.1427608 14276.08 14.27608 14
16 1.5 0.152958 15295.8 15.2958 15
17 1.6 0.1631552 8157.76 16.31552 16
18 1.7 0.1733524 17335.24 17.33524 17
19 1.8 0.1835496 18354.96 18.35496 18
20 1.9 0.1937468 19374.68 19.37468 19
21 2 0.203944 20394.4 20.3944 20
22 2.1 0.2141412 21414.12 21.41412 21
23 2.2 0.2243384 2243.384 22.43384 22
24 2.3 0.2345356 23453.56 23.45356 23
25 2.4 0.2447328 24473.28 24.47328 24
26 2.5 0.25493 25493 25.493 25
27 2.6 0.2651272 26512.72 26.51272 26
28 2.7 0.2753244 27532.44 27.53244 27
29 2.8 0.2855216 28552.16 28.55216 28
30 2.9 0.2957188 29571.88 29.57188 29
31 3 0.305916 30591.6 30.5916 30
备注:由于所用力矩批的最小刻度为1Kgf·cm,故相应使用的力矩值取整数值。
力矩计算
选择步进电机时,首先必须确保步进电机的输出功率大于负载所需的功率。选择动力步进电机时,应首先计算机械系统的负载转矩。电动机的转矩-频率特性可以满足机械负载并具有一定的裕度,以确保其可靠的运行。在实际工作过程中,各种频率的负载力矩必须在力矩-频率特性曲线的范围内。一般来说,静转矩Mjmax大的电动机具有大的负载转矩。 选择步进电机时,步进角应与机械系统匹配,以便获得机床所需的脉冲当量。在机械传动过程中,为了减小脉冲当量,一个可以改变丝杠的导程,另一个可以通过步进电机的细分驱动来实现。但是细分只能更改其分辨率,而不能更改其精度。精度取决于电机的固有特性。 在选择动力步进电机时,应估算机械负载的负载惯量和机床所需的启动频率,以使其与步进电机的惯量频率特性相匹配,并具有一定的余量,以便可以实现最高速度的连续工作频率。满足了机床快速运动的需求。 选择步进电机需要进行以下计算: (1)计算齿轮的减速比 根据所需的脉冲当量,齿轮减速比I计算如下: i =(φ.S)/(360.Δ)(1-1)
φ步进电机的步进角类型(o /脉冲) S ---螺距(mm) δ-(毫米/脉冲) (2)计算从工作台,螺杆和齿轮到电动机轴的惯量Jt。 Jt = J1 +(1 / i2)[(J2 + Js)+ W / g(S /2π)2](1-2) Jt的类型---转换为电动机轴上的惯性(Kg.cm.s2) J1,J2 ---齿轮惯性(Kg.cm.s2) 螺杆的JS惯性(Kg.cm.s2) W ---工作台重量(n) S ---螺距(cm) (3)计算电动机输出的总转矩m M = Ma + Mf + Mt(1-3) Ma =(Jm + Jt).n / T×1.02×10ˉ2(1-4) Ma ---电动机启动时的加速转矩(N.m) Jm,Jt ---电机本身的惯量和负载惯量(Kg.cm.s2) N ---电动机所需转速(r / min) T ---电机ACC时间(秒)
QC T 649汽车转向传动轴总成性能要求及试验方法
中华人民共和国汽车行业标准 汽车转向传动轴总成性能要求及试验方法QC/T 649-2000 1 范围 本标准规定了汽车转向传动轴总成的性能要求及试验方法。 本标准适用于汽车转向传动轴总成。 2 试验项目 2.1 总成间隙试验 2.2 转动力矩试验 2.3 滑动花键的滑动起动力试验 2.4 静扭强度试验 2.5 扭转疲劳寿命试验 3 试验样品 试验样品应按照规定程序批准的图样和技术文件制造,其材料、尺寸、热处理及装配状态应符合图样和技术文件规定。每项试验样品数量不少于3件。 4 损坏的判定 4.1 总成的零件表面出现可见裂纹。 4.2 总成运动不灵活,不能继续使用。 5 性能要求 5.1 总成间隙试验 5.1.1 对于滑动花键结构,总成包含1个万向节,总成的扭转角度不大于45'。 5.1.2 对于滑动花键结构,总成包含2个万向节,总成的扭转角度不大于1°。 5.1.3 对于无滑动花键结构,总成包含1个万向节,总成的扭转角度不大于15'。 5.2 转动力矩试验 转动力矩应符合设计要求。 5.3 滑动花键的滑动起动力试验 滑动起动力应符合设计要求。 5.4 静扭强度试验 施加转矩Mj进行静扭强度试验后,总成不允许损坏。 5.5 扭转疲劳寿命试验 施加正反方向的疲劳寿命试验转矩M,经3×105次循环试验后,总成不允许损坏。 6 试验条件 在各项试验项目中,应满足以下条件: 总成应按实际装车状态安装与固定。 7 试验方法 7.1 总成间隙试验 7.1.1 将总成与转向器联接的一端固定,从转向盘一端施加±3Nm的转矩,所施加的转矩也可以按设计要求确定。 7.1.2 测定总成的扭转角度。 7.1.3 测量误差不大于2%。 7.2 转动力矩试验 7.2.1 将转向柱管固定,从转向盘一侧驱动。 7.2.2 测出总成的转动力矩。 7.2.3 测量误差不大于2%。 7.3 滑动花键的滑动起动力试验
力矩控制通用技术标准(1)
力矩控制通用技术标准
前言 本标准根据环保动力公司的实际情况,结合国家及技术中心的产品技术要求,明确了力矩控制过程中的技术要求,工装、设备的使用规范 本标准由制造部工艺科提出、归口 本标准起草单位:制造部工艺科 本标准主要起草人:周陵 本标准所代替标准的历次版本的发布情况为:无
力矩控制通用技术标准 1 范围 本标准规定了发动机用螺纹直径4mm-20mm紧固件的力矩控制。 本标准适用于符合以下条件,以控制扭矩方式进行的紧固: —外螺纹件的机械性能符合GB/T 3098.1规定的8.8、10.9级; —内螺纹件的机械性能符合GB/T 3098.2或GB/T 3098.4,且具有充分发挥螺纹连接副承载能力的强度; —螺纹符合GB/T 196,螺纹精度不低于GB/T 197规定的6级; —内、外螺纹件的六角对边尺寸符合GB/T 3104规定的标准系列; —内、外螺纹件的表面为汽车工业通常采用的状态; —外螺纹件在紧固中受轴向拉伸载荷。 本标准不适用于外螺纹件在紧固中承受压缩力的紧定螺钉、由外螺纹件攻出螺纹的自攻螺钉及木螺钉。 当表面状态不同、支承面尺寸及形态与标准条件差异较大,以致预紧力不能满足要求以及对预紧力有特别要求时,应对紧固扭矩进行调整。 当产品对紧固扭矩有特殊要求时,根据产品要求调整控制要求。 2 引用标准 下列文件中的条款通过本标准的引用而成为本标准的条款。凡是注明日期的引用文件,其随后所有的修改单(不包括勘误的内容)或修订版均不适用于本标准,然而,鼓励根据本标准达成协议的各方研究是否可使用这些文件的最新版本。凡是不注日期的应用文件,其最新版本适用于本标准。 GB/T 196 普通螺纹基本尺寸(直径1mm-600mm) GB/T 197 普通螺纹公差与配合(直径1mm-355mm) GB/T 3098.1 紧固件机械性能螺栓、螺钉和螺柱 GB/T 3098.2 紧固件机械性能螺母 GB/T 3098.4 紧固件机械性能细牙螺母 GB/T 3104 紧固件机械性能六角产品的对边宽度 GB/T 16823.2 螺纹紧固件紧固通则
力矩计算
力矩计算 力矩:力和力臂的乘积叫做力对转动轴的力矩。 即:M=F*L 式中M是力F对转动轴O的力矩,凡是使物体产生反时针方向转动效果的,定为正力矩,反之为负力矩。 单位:在国际单位制中,力矩单位是牛顿*米,简称:牛*米,符号:N*m 力矩在物理学里是指作用力使物体绕着转动轴或支点转动的趋向。力矩的单位是牛顿-米。力矩希腊字母是tau。 力矩的概念,起源于阿基米德对杠杆的研究。转动力矩又称为转矩或扭矩。力矩能够使物体改变其旋转运动。推挤或拖拉涉及到作用力,而扭转则涉及到力矩。力矩等于径向矢量与作用力的叉积。 平衡条件: (1)有固定转动轴的物体的平衡是指物体静止,或绕转轴匀速转动; (2)有固定转动轴物体的平衡条件是合力矩为零,即∑Fx=0,也就是顺时针力矩之和等于逆时针力矩之和。 一般平衡条件:
合力为零,合力矩同时为零,即∑Fx=0,∑Fy=0,∑M=0。 力矩: (1)力臂(L):转动轴到力的作用线的垂直距离; (2)力矩(M):M=L×F,单位是牛*米; (3)力矩描述力对物体产生的转动效果; (4)力矩是矢量,中学里只考虑顺时针和逆时针两种方向。通常规定逆时针力矩为正,顺时针力矩为负。依照国际单位制,能量与功量的单位是焦耳,定义为1 牛顿-米。但是,焦耳不是力矩的单位。因为,能量是力点积距离的标量;而力矩是距离叉积力的伪矢量。当然,量纲相同并不仅是巧合;使1 牛顿-米的力矩,作用一全转,需要恰巧2*Pi 焦耳的能量。 当一个物体在静态平衡时,静作用力是零,对任何一点的净力矩也是零。关于二维空间,平衡的要求是: x,y方向合力均为0,且合力矩为0。
扭矩测试的几种方法对比与概念介绍.doc
序方法名称 号 拧紧法(增拧一 法) 标记法(划线二 法) 三松开法紧固件扭矩测试方法(拆车) 具体方法优点缺点备注 扭力扳手平稳用力逐渐增加力矩操作简1、存在二次紧固静态扭矩,该方法(切忌冲击),当螺母或螺栓刚开 单,但必的可能;用于残余扭矩的 须熟练2、对螺栓何时开测试,适用于装配始产生微小转动时它的瞬时扭矩值 有经验始启动很难确定,现场拧紧质量的最大(因要克服静摩擦力),继续存在主观因素;检测 转动,扭矩值就会回落到短暂的稳3、螺栓启动的时 定状态,这时的扭矩值即为检查所候,实际扭矩值应 得的扭矩。该是大约安装时 候的扭矩值,所以 测试值一般偏大。 检验前先在被检螺栓或螺母头部与技术水相对方法一更精动态扭矩,设计人被连接体上划一道线,确认相互的平不高,确员从设计角度给原始位置。然后将螺栓或螺母松开操作较出的扭矩即为动些,在用扭矩扳手将螺栓或螺母拧繁琐,不态扭矩,故拆车时紧到原始位置(划线处要线对准),适宜有建议采用该方法 这时的最大扭矩值再乘以0.9 ~ 1.1 防松功 所得的值即为检查所得的扭矩。能的紧 固件 用扭矩扳手慢慢地向被检螺栓或螺操作简扭矩偏小 母施加扭矩,使其松开,读取开始单,但必 转动时的瞬时扭矩值,并根据试验须熟练 和经验乘以一个系数: 1.1~ 1.2 即为有经验 检验扭矩值。 残余扭矩值是再继续拧紧螺栓/ 螺母时旋紧一个小角度测得的最小扭矩值。 起动扭矩不能作为残余扭矩。 动态扭矩:当紧固件再被固定的过程中测量得到的最大峰值。扭力扳手和动力工具都可以施加动态扭矩,动态扭矩不能在紧固件被紧固完之后测量。动态扭矩加载时进行在线测量得到的扭矩值。 静态扭矩:在一个紧固件被固定好之后,将其在拧紧方向上继续旋转的瞬时所需 要的扭矩。加载后对扭矩进行测量。 检测扭矩:与静态扭矩相同 动态与静态两种扭矩的监控与使用何种工具无任何关系,但是在确认扭矩时却非常有用。动态扭矩和静态扭矩的测量结果可能并不相同。静态扭矩会随着时间的推移而衰减,被紧固件为非金属时尤为明显;而且影响静态扭矩的因素较多,与
弯管力矩计算公式
第二节管材弯曲 一、材弯曲变形及最小弯曲半径 二、管材截面形状畸变及其防止 三、弯曲力矩的计算 管材弯曲工艺是随着汽车、摩托车、自行车、石油化工等行业的兴起而发展起来的,管材弯曲常用的方法按弯曲方式可分为绕弯、推弯、压弯和滚弯;按弯曲加热与否可分为冷弯和热弯;按弯曲时有无填料(或芯棒)又可分为有芯弯管和无芯弯管。 图6 —19、图6 —20、图6 —21和图6 —22分别为绕弯、推弯、压弯及滚弯装置的模具示意图
图6-19 在弯管机上有芯弯管 1—压块2—芯棒3—夹持块4—弯曲模胎5—防皱块6—管坯
图6-20 型模式冷推弯管装置 图6 — 21 V 形管件压弯模 1 —压柱2—导向套3 —管坯4—弯曲型模 1 —凸模 2—管坯 3—摆动凹模
图6 —22 三辊弯管原理 1 —轴2、4、6—辊轮3—主动轴5—钢管 一、材弯曲变形及最小弯曲半径Q 管材弯曲时,变形区的外侧材料受切向拉伸而伸长,内侧材料受到切向压缩而缩短,由于切向应
力及应变沿着管材断面的分布是连续的,可设想为与板材弯曲相似,外侧的拉伸区过渡到内侧的压缩区,在其交界处存在着中性层,为简化分析和计算,通常认为中性层与管材断面的中心层重合,它在断面中的位置可用曲率半径表示(图6 —23)。 管材的弯曲变形程度,取决于相对弯曲半径只。和相对厚度t D( R为管材断面中心层曲率半径,D为管材外径,t为管材壁厚)的数值大小,RD和tD值越小,表示弯曲变形程度越大(即RD和tD过小),弯曲中性层的外侧管壁会产生过度变薄,甚至导致破裂;最内侧管壁将增厚,甚至失稳起皱。同时,随着变形程度的增加,断面畸变(扁化)也愈加严重。因此,为保证管材的成形质量,必须控制变形程度在许可的范围内。管材弯曲的允许变形程度,称为弯曲成形极限。管材的弯曲成形极限不仅取决于材料的力学性能及弯曲方法,而且还应考虑管件的使用要求。 对于一般用途的弯曲件,只要求管材弯曲变形区外侧断面上离中性层最远的位置所产生的最大伸长应变max不致超过材料塑性所允许的极限值作为定义成形极限的条件。即以管件弯曲变形区外侧的外表层保证不裂的情况下,能弯成零件的内侧的极限弯曲半径r min,作为管件弯曲的成形极限。r min与材料力学性能、管件结构尺寸、弯曲加工方法等因素有关。
力矩转矩扭矩的定义
扭矩是使物体发生转动的力。发动机的扭矩就是指发动机从曲轴端输出的力矩。在功率固定的条件下它与发动机转速成反比关系,转速越快扭矩越小,反之越大,它反映了汽车在一定范围内的负载能力。 膇螈蒁螄膇羀蝿扭矩在物理学中就是力矩的大小,等于力和力臂的乘积,国际单位是牛米Nm,此外还可以看见kgm、lb-ft这样的扭矩单位,由于G=mg,当g=9.8的时候,1kg的重量为9.8N, 所以1kgm=9.8Nm,而磅尺lb-ft则是英制的扭矩单位,1lb=0.4536kg;1ft=0.3048m,可以算出1lb-ft=0.13826kgm。在人们日常表达里,扭矩常常被称为扭力(在物理学中这是2个不同的概念)。例如:8代Civic 1.8的扭矩为173.5Nm@4300rpm,表示引擎在4300转/分时的输出扭矩为173.5Nm,那173.5N的力量怎么能使1吨多的汽车跑起来呢?其实引擎发出的扭矩要经过放大(代价就是同时将转速降低)这就要靠变速箱、终传和轮胎了。引擎释放出的扭力先经过变速箱作“可调”的扭矩放大(或在超比挡时缩小)再传到终传(尾牙)里作进一步的放大(同时转速进一步降低),最后通过轮胎将驱动力释放出来。如某车的1挡齿比(齿轮的齿数比,本质就是齿轮的半径比)是3,尾牙为4,轮胎半径为0.3米,原扭矩是200Nm的话,最后在轮轴的扭力就变成200×3×4=2400Nm(设传动效率为100%)在除以轮胎半径0.3米后,轮胎与地面摩擦的部分就有2400Nm/0.3m=8000N,即800公斤力的驱动力,这就足以驱动汽车了。 薀蚁薅芇薇罿膄若论及机械效率,每经过一个齿轮传输,都会产生一次动力损耗,手动变速箱的机械效率约在95%左右,自动变速箱较惨,约剩88%左右,而传动轴的万向节效率约为 98%。整体而言,汽车的驱动力可由下列公式计算:扭矩×变速箱齿比×最终齿轮比×机械效率/轮胎半径 袁肃蒆荿莃蚂莇补充一点: 袅蚆袇薃蒄薆膈为什么引擎的功率能由扭矩计算出来呢? 螆虿螃肂螆羀肁功率P=功W/时间t,功W=力F×距离s;所以,P=F×s/t=F×速度v 蒀袂袃袆蒇膀蒃这里的v是线速度,而在引擎里,曲轴的线速度=曲轴的角速度ω×曲轴半径r,代入上式得:功率P=力F×半径r×角速度ω ;而力F×半径r=扭矩 肂蚅肆艿莀芄羆得出:功率P=扭矩×角速度ω 所以引擎的功率能从扭矩和转速中算出来角速度的单位是弧度/秒,在弧度制中一个π代表180度 莅蕿蚀薄莅袀节发动机扭矩 蒁衿莆蒅莈蒂羅概述 芃袃蚅腿薁蒂薅扭矩是使物体发生转动的力。发动机的扭矩就是指发动机从曲轴端输出的力矩。在功率固定的条件下它与发动机转速成反比关系,转速越快扭矩越小,反之越大,它反映了汽车在一定范围内的负载能力。 蚅袄螇螁芄螅羈在某些场合能真正反映出汽车的“本色”,例如启动时或在山区行驶时,扭矩越高汽车运行的反应便越好。以同类型发动机轿车做比较,扭矩输出愈大承载量愈大,加速性能愈好,爬坡力愈强,换挡次数愈少,
位置 速度 转矩3种控制方式介绍
1从原理上理解3种控制方式 一般伺服都有三种控制方式:速度控制方式,转矩控制方式,位置控制方式。之所以有这三中控制方式,是因为伺服一般为三个环控制。所谓三环就是3个闭环负反馈PID调节系统。由伺服系统的三个控制回路来实现。 第1环是电流环,它是最内环。此环完全在伺服驱动器内部进行,通过霍尔装置检测驱动器给电机的各相的输出电流,负反馈给电流的设定进行PID调节,从而达到输出电流尽量接近等于设定电流,电流环就是控制电机转矩的,所以在转矩模式下驱动器的运算最小,动态响应最快。 第2环是速度环,它是次外环,通过检测的电机编码器的信号来进行负反馈PID调节,它的环内PID输出直接就是电流环的设定,所以速度环控制时就包含了速度环和电流环,换句话说任何模式都必须使用电流环,电流环是控制的根本,在速度和位置控制的同时系统实际也在进行电流(转矩)的控制以达到对速度和位置的相应控制。 第3环是位置环,它是最外环,可以在驱动器和电机编码器间构建也可以在外部控制器和电机编码器或最终负载间构建,要根据实际情况来定。由于位置控制环内部输出就是速度环的设定,位置控制模式下系统进行了所有3个环的运算,此时的系统运算量最大,动态响应速度也最慢。 2从使用上理解3种控制方式 1、转矩控制:转矩控制方式是通过外部模拟量的输入或直接的地址的赋值来设定 电机轴对外的输出转矩的大小,具体表现为例如10V对应5Nm的话,当外部 模拟量设定为5V时电机轴输出为2.5Nm:如果电机轴负载低于2.5Nm时电机正 转,外部负载等于2.5Nm时电机不转,大于2.5Nm时电机反转(通常在有重力 负载情况下产生)。可以通过即时的改变模拟量的设定来改变设定的力矩大小, 也可通过通讯方式改变对应的地址的数值来实现。应用主要在对材质的受力有 严格要求的缠绕和放卷的装置中,例如饶线装置或拉光纤设备,转矩的设定要
电机力矩计算
电机扭矩计算 电机力矩的定义:垂直方向的力*到旋转中心的距离 1、电动机有一个共同的公式: P=M*N/9550 P为功率,M为电机力矩(也称扭矩),N为电机转速,当M 和N都为额定值时,电机的功率也是额定功率,额定是指电机能够长期工作的极限值 2、瞬态扭矩是指电机在负载变化、速度变化时出现的过渡值,和额定没有关系,具体说,这个值可以超过额定扭矩,如果此时电机速度为额定时,电机可能会出现功率过载,这个过载只能持续很短的时间,这个时间取决于电机设计。 3、变频器的功率一般要大于等于三相异步电动机,但这还不够,还需要变频器输出的额定电流和过载电流都要大于等于电机所需的额定值或最大值,以保证电机能出足够的力矩(额定和瞬态力矩),否则可能出现变频器无法带动电机和负载的情况。 步进电机是一种能将数字输入脉冲转换成旋转或直线增量运动的电磁执行元件。每输入一个脉冲电机转轴步进一个步距角增量。电机总的回转角与输入脉冲数成正比例,相应的转速取决于输入脉冲频率。
步进电机是机电一体化产品中关键部件之一,通常被用作定位控制和定速控制。步进电机惯量低、定位精度高、无累积误差、控制简单等特点。广泛应用于机电一体化产品中,如:数控机床、包装机械、计算机外围设备、复印机、传真机等。选择步进电机时,首先要保证步进电机的输出功率大于负载所需的功率。而在选用功率步进电机时,首先要计算机械系统的负载转矩,电机的矩频特性能满足机械负载并有一定的余量保证其运行可靠。在实际工作过程中,各种频率下的负载力矩必须在矩频特性曲线的范围内。一般地说最大静力矩Mjmax大的电机,负载力矩大。 选择步进电机时,应使步距角和机械系统匹配,这样可以得到机床所需的脉冲当量。在机械传动过程中为了使得有更小的脉冲当量,一是可以改变丝杆的导程,二是可以通过步进电机的细分驱动来完成。但细分只能改变其分辨率,不改变其精度。精度是由电机的固有特性所决定。 选择功率步进电机时,应当估算机械负载的负载惯量和机床要求的启动频率,使之与步进电机的惯性频率特性相匹配还有一定的余量,使之最高速连续工作频率能满足机床快速移动的需要。 选择步进电机需要进行以下计算: (1)计算齿轮的减速比 根据所要求脉冲当量,齿轮减速比i计算如下:
扭矩测量方法
扭矩测量的方法原理 引言:扭矩是工厂场地上大多数设备的重要被测量对象之一。测量扭矩常常被误解,这就可能导致对测量系统的过度设计或设计不足。本文介绍多种用于扭矩测量的技术和折衷方法。 扭矩可以分为两大类,静态扭矩或动态扭矩。用于测量扭矩的方法可以被进一步分为两类,反扭矩和联机扭矩测量。被测扭矩的类型以及现有各类传感器,对所测的数据精度及测量的成本有重要影响。 在讨论静态和动态扭矩的比较中,最容易入手的是首先了解静力和动力的差异。简而言之,动力包括加速度,而静力则没有。 动力和加速度之间的联系被描述为牛顿第二定律:F=ma(力等于物质质量乘以加速度)。以汽车自身物质(质量)把车停下所需要的力就是动力,因为汽车必须被减速。由刹车卡钳施加以停止汽车的力就是静力,因为所涉及的刹车垫没有加速度。 扭矩只是旋转力或通过一定距离产生的力。根据前面的讨论,它被认为是静力,如果它没有角加速度的话。时钟弹簧施加的扭矩就是静态扭矩,因为没有旋转,因而也就没有角加速度。当汽车以匀速在高速公路上巡航的时候,通过汽车传动轴传输的扭矩就是一个旋转静态扭矩的例子,因为即使存在旋转,以匀速行驶也没有加速度。 汽车引擎产生的扭矩有静态和动态扭矩,取决于测量的部位。如果在机轴中测量扭矩,当汽缸每一次燃烧且活塞旋转机轴的时候,就有大的动态扭矩波动。 如果在传动轴测量扭矩,那几乎就是静态扭矩,因为调速轮和传动系统要阻尼引擎产生的动态扭矩。用曲柄提升车窗所需要的扭矩就是静态扭矩的例子,尽管涉及到旋转加速度,因为曲柄的加速和旋转惯性很小,与车窗运动有关的摩擦力相比,所产生的动态扭矩(扭矩=旋转惯性*旋转加速度)可以忽略不计。 最后一个例子描述了一个事实,大多测量应用都在某种程度上涉及静态和动态扭矩。如果动态扭矩是整个扭矩的主要组成部分或是感兴趣的扭矩,那么,要特别考虑何时对其作出最佳的测量。 反扭矩与联机扭矩的比较 通过在扭矩支撑零件之间插入一种扭矩传感器,可以做联机扭矩测量,非常类似于在套筒和套筒扳手之间插入延长杆。旋转套筒所需要的扭矩直接由套筒延长杆支撑。该方法容许扭矩传感器被放置在尽可能与感兴趣的扭矩靠近的地方,并避免可能出现的测量误差,如寄生扭矩(轴承等等)、无关负载和具有大的旋转惯性 的零件(会阻尼动态扭矩)。
转矩控制、矢量控制
转矩控制、矢量控制和VF 控制解析 1. 变转矩就是负载转矩随电机转速增大而增大,是非线性变化的,如风机水泵 恒转矩就是负载转矩不随电机转速增大而增大,一般是相对于恒功率控制而言。如皮带运输机提升机等机械负载 2. VF 控制就是变频器输出频率与输出电压比值为恒定值或正比。例 如:50HZ时输出电压为380V,25HZ时输出电压为190V即恒磁通控制;转矩不可控,系统只是一个以转速物理量做闭环的单闭环控制系统,他只能控制电机的转速 根据电机原理可知,三相异步电机定子每相电动势的有效 值:E仁4.44f1N1①m 式中:E1--定子每相由气隙磁通感应的电动势的有效值,V ;f1 --定子频率,Hz;N 1 ——定子每相绕组有效匝数;①m-每极磁通量由式中可以看出,①m的值由E1/f1决定,但由于E1 难以直接控制,所以在电动势较高时,可忽略定子漏阻抗压降,而用定子相电压U1代替。那么要保证①m不变,只要U1/f1 始终为一定值即可。这是基频以下调时速的基本情况,为恒压频比(恒磁通)控制方式,属于恒转矩调速。 基准频率为恒转矩调速区的最高频率,基准频率所对应的电压为即为基准电压,是恒转矩调速区的最高电压,在基频以下调速时,电压会随频率而变化,但两者的比值不变。在基频以上调速时,频率从基频向上可以
调至上限频率值,但是由于电机定子不能超过电机额定电压,因此电压不再随频率变化,而保持基准电压值不变,这时电机主磁通必须随频率升高而减弱,转矩相应减小,功率基本保持不变,属于恒功率调速区。 3. 矢量控制,把输出电流分励磁和转矩电流并分别控制,转矩可控,系统是一个以转矩做内环,转速做外环的双闭环控制系统。它既可以控制电机的转速,也可以控制电机的扭矩。 矢量控制时的速度控制(ASR )通过操作转矩指令,使得速度指令和速度检出值(PG 的反馈或速度推定值)的偏差值为0。带PG 的V/f 控制时的速度控制通过操作输出频率,使得速度指令和速度检出值(PG 的反馈或速度推定值)的偏差值为0。 矢量控制原理是模仿直流电动机的控制原理, 根据异步电动机的动态数学模型,利用一系列坐标变换把定子电流矢量分解为励磁分量和转矩分量,对电机的转矩电流分量和励磁分量分别进行控制,在转子磁场定向后实现磁场和转矩的解耦,从而达到控制异步电动机转矩的目的,使异步电机得到接近他励直流电机的控制性能。 具体做法是将异步电动机的定子电流矢量分解为产生磁场的电流分量(励磁电流)和产生转矩的电流分量(转矩电流)分别加以控制,并同时控制两分量间的幅值和相位,即控制定子电流矢量,所以称这种控制方式称为矢量控制方式。 矢量控制分有速度传感器矢量控制和无速度传感器矢量控制两种, 前者精度高后者精度低。矢量控制系统的无速度传感器运行方式,首先必须解决电机转速和转子磁链位置角的在线辨识问题。常用的方法有基于检测定子
盘点电机扭矩的测量方法有哪些
盘点电机扭矩的测量方法有哪些 扭矩是电机试验中一个重要的参数,尤其是在电机效率评测中扭矩更是一个不可或缺的被测量,扭矩测量的准确性直接关系到电机效率的评测的正确性。目前使用的扭矩测量方法按照测量原理可分为平衡力法、传递法和能量转换法。 一、平衡力法处于匀速工作状态的传动机械构件,其主轴和机体上一定同时存在一对扭矩T 和T,并且二者大小相等、方向相反。通过测量机体上的T来测量主轴上T 的方法称为平衡力法。设F 为力臂上的作用力,L 为力臂长度,则T=LF。通过测量作用力F和力臂L即可得出T和T。平衡力法的优点是不存在传递扭矩信号的问题,力臂上的作用力F容易测得;缺点是测量范围仅局限为匀速工作状态,无法完成动态扭矩的测量。二、传递法传递法利用传递扭矩时弹性元件的物理参数会发生某种程度的变化。利用这种变化与扭矩的对应关系来测量扭矩。按照不同的物理参数,可将传递法进一步划分为磁弹性式、应变式、振弦式、光电式等,目前传递法在扭矩测量领域应用最为广泛。 图1 传递法分类 1.光电式扭矩测量法 将开孔数完全相同的两片圆盘形光栅固定在转轴上,并将光电元件和固定光源分别固定在光栅两侧,转轴无扭矩作用时两片光栅的明暗条纹错开,完全遮挡光路,无光线照到光敏元件上不输出电信号;有扭矩作用时两个圆盘形光栅的截面产生相对转角,明暗条纹部分重合,部分光线透过光栅照到光敏元件上,输出电信号。扭矩值越大扭转角越大,照到光敏元件上的光线强度越大,输出电信号也就越大,通过测量输出的电信号能够测得外加扭矩的大小。 图2 光电式扭矩测量原理 该方法的优点是响应速度快,能实现扭矩的实时监测;其缺点是结构复杂、静标困难、可靠性较差、抗干扰能力差,测量精度受温度变化的影响较大。该方法不适用于刚启动和低
力矩控制器原理与接线
力矩控制器 一.概述 力矩控制器为代替三相自耦变压器,而专门设计的一种先进的全电子化控制装置,能工作在电阻、电感性负载。此控制器广泛应用于五金机械塑料、电线、电缆、绳网、印刷、造纸、纺织、印染、化疑纤、橡绞、电影胶皮等各种机械、机电行业。 与三相自藕调压器相比较,本控制器由于采用了电子调节,无触点磨损,电压调节平衡,起动性能好,本控制器具有体积小、重量轻、效率高、发热小、节约能源(经测定平均节能17%以上),使用寿命长、安装、维修方便。 二.技术参数 1.输入电压:三相交流电压 380V±10% 2.输出电压:三相交流电压 0-380V 3.额定电流:标称电流(面板上标称的电流) 4.输出电压可以无极调节,从而使电机实现无极调速 5、频率50~60HZ。 三.工作环境 1、环境温度:-25℃~+55℃。 2、空气相对湿度:≤85%(20℃±5℃)。 3、无显著冲击震动。 四.工作原理 三相调压器调速控制器主回路采用进口双向可控硅,改变可控硅的开放角大小,就能使电机或其它负载的工作电压从0至380V连续可调,也就实现了平衡地调压调速过程,以满足不同生产的工艺要求。 在可控硅控制电路中采用了先进的集成电路,加入了电
流回馈, 构成一个循环控制系统。既提高了力矩电机的机械性硬度,又改善性能,同时还提高了力矩电机的超载能力,扩大了力矩电机的使用范围。为了使调速过程尽快进入稳定状态,在控制回路中还加入了电压回馈以提高控制器的技术性能。 五.使用方法 1. 接线说明:请严格按以下接线示意图接线:D1、D2、D3三点为 控制器的输出端,接力矩电机;A 、B 、C 、为输入端接三相380V 电源。 N 为零线接口,接零线。 2.旋钮旋至零位。 3.总电源。(指示灯亮) 4.控制开关,调节调速电位器旋钮,使电机达到你所需的速度。 5. 电位器为精密长寿电位器。 六.注意事项 1.严禁输出短路。 2.严禁使用中,负载电流超过过面板标称电流值。 3、严禁零线N 接入电机星点. 4、若控制器出现问题务必请专业人员检修,以免使故障范围扩大. 六.接线图 A B C D1D2D3A B C 输入 380V 输出 0~380V V 1 U1 W1 W2V 2U2力矩电机 A B C D1D2D3 A B C 输入 380V 输出 0~380V V 1 U1 W1 W2V 2U2力矩电机 N
力矩计算
解:1) 求支座反力 2) 用截面依次在1-1,2-2 截面处截开,取左段为研究对象; 图(b): P Q F F -= 11 Q 1 M c ) (b 1 用截面法计算如图所示外伸梁1-1,2-2, 截面上的内力,其中: pa F M 21= C (a ) 解得: )(4 5↑= p Ay F F ) (4 1↓= p By F F 校核: 4 14 5=-- = -+=∑P P P P By Ay y F F F F F F F ∑=0 B M 23=?--?a F M a F Ay p ∑=0 A M 2=?+-?a F M a F By P ∑=0 y F 1=--Q P F F ∑=-0 1 1M 1=+M F pa pa F M -=1
2.悬臂梁AB,在自由端受集中力偶M 作用,试绘出此梁的剪力图和弯矩图 解:1)列剪力方程和弯矩方程 ? 将坐标 x 的原点取在A 端,由直接法可得 M 3.作剪力图和弯矩图 FQ 2 2 Q F Ay ) (c (a) A F ∑=0 y F 2=--Q P Ay F F F P Q F F 4 12= ∑=-0 2 2M 2=+M F pa pa F M -=2A m x M L x Q =≤≤)(,0
FQ(x)= Fp左=FAY=bFp /L (0 转矩是旋转机械的重要参数之一。转矩的测试方法,按其基本原理可以分为三种:传递法(扭轴法)、平衡力(反力)法及能量转换法。 传递法是根据弹性元件在传递转矩时所产生的变形、应力或应变来测试转矩的方法(因为常用的弹性元件是扭轴,所以又称扭轴法)。变化的参数可以是变形、应力或应变等,使用的弹性元件是扭轴,等截面圆柱形扭轴的应变可按下式计算: 它所产生的应变可以引起贴在表面的电阻应变片阻值的变化而形成应变型转矩传感器。电机主轴旋转时,将转矩传递到扭轴上,扭轴上所产生的应变,通过转矩传感器的电阻应变片转换成相应的电信号,该信号通过处理后送显示器显示转矩数值。这种传感器使用方便,精度高,易于集成。 平衡力法是通过外加己知的与被测转矩方向相反的转矩,当传动轴静止或匀速转动时,外加转矩与被测转矩相等。这种方法简单,但必须通过另外一种方法测量外加的转矩或力及力臂,这样会对测量引入一定的累计误差。 能量转换法则是一种间接测量方法,根据对应于转矩大小而变化的其他能量参数来测试转矩的方法,是通过利用能量守恒的原理间接测量转矩,不易实现。这三种转矩测试方法的原理示意图,分别如图7.8(a),(b),(c)所示。本节对这三种转矩测试方法分别进行讨论。 一、传递法测试转矩 传递法所用转矩传感器是多种多样的,例如: (1)变形型转矩传感器,反映机械、液压、气动、电阻、电容、电感、光学、光电等参数的变化。 (2)应力型转矩传感器,反映材料磁阻变化或透光材料的双折射现象(磁弹或光弹转矩传感器)。 (3)应变型转矩传感器,反映轴的应变引起电阻应变片的电阻变化。 转矩测试仪因所用传感器不同而有较大差别,为此,分别举例讨论如下: 1.相位转矩测量仪(采用变形型转矩传感器) 近年来,随着电子测试技术的迅速发展,信号的相位测试方法也日趋完善。利用相位测试原理制成的相位转矩测试仪,也得到广泛应用。特别是数字显示相位转矩测试仪,由于具有读数直观,信号可远传,不易受干扰,测试准确度高,测试结果便于自动记录或输入计算机进行数据处理等优点,在现代科学实验工作中的应用日益广泛。 (1)转矩与相位差。相位转矩测试仪一般由产生信号的转矩传感器和检测信号相位差的测量电路两部分组成,如图7.9(a)所示。 1、系统构成:变频器控制电机,电机接蜗轮蜗杆升降机; 2、两组系统举升约最大250kg负载,举升形成300mm; 3、蜗轮蜗杆升降机丝杆的升降速度最大200mm/min; 4、启停时平稳,加减速距离50mm,加减速时间5s; 小弟咨询的电机为4极异步电机550w和750w两种,550w扭矩3.75N.M,750w扭矩5N.M,请大侠们指点,如何选择电机的扭矩。 一、重物转动惯量:JW = F * (PB/2/3.14)^2 (kg.cm^2) 二、丝杆转动惯量: JB = MB * (DB^2)/8 (kg.cm^2) 三、折算到电机轴上的转动惯量:JL = (JW + JB)/R^2 (kg.cm^2) JL/(R^2) <=3JD 验算减速比 Jω = F.v (N.m) F.v = F.r (N.m) 其中:PB丝杆螺距;DB丝杆直径;R减速比;v速度; 计算时要考虑传动效率与单位换算比如转动惯量单位(kg.cm^2)换算成(kg.m^2) 感谢各位的回复,虽然1楼大侠给出了详细的公式,但是小弟有两处还略有不懂。 1、小弟需要计算电机的扭矩,最终确定电机的型号; 2、JD是什么参数; 3、Jω=F.V=F.r中ω.V.r分别表示什么参数; 4、蜗轮蜗杆升降机选择SWL2.5的 小弟新人,请不吝赐教哦!!现在把结构简图发出来,方便大家分析问题,越详细越喜欢的哦!!想问的重点是这套系统选择550w、3.75N.M扭矩的电机可以吗? JD 电机转动惯量 扭矩T=Jω = F.v J 折算的转动惯量ω 角速度ω=2πn/60 n转速v 速度你这个系统中还要折算减速箱的转动惯量; 此系统550W电机足够了。 考虑传动效率:丝杆0.8,蜗箱0.8 T = F.PB/2π/R/η = 200*9.8*6/6280/24/0.8/0.8 = 0.12N.m (1)助力转矩的计算 汽车的转向阻力矩为: P G T w 3 13μ= (1) 式中1G ----前轴载荷; μ----轮胎和路面的摩擦因数,一般取0.7; P ----轮胎气压。 此时,需要转向盘提供的转矩为: +=ηω0i T T w h (2) 式中0ωi ——为转向系角传动比; +η——转向系正效率,对齿轮齿条式转向器,+η一般在70%~85%[27],这 里取+η=0.8。 根据推荐值,转向盘操纵力不应大于30~50N,在10N 以下则转向很轻便,因此作用在转向盘上的转矩为 2 00h h h D F T ?= (3) 式中0h F ——作用在转向盘上的力,这里取0h F =30N ; h D ——转向盘直径; 所以作用在转向轴上的最大助力转矩max a T 为: 0max h h a T T T -==00h w T i T -+ηω (2)电动机参数的选择和计算 这里采用永磁直流电动机,转向轴驱动的结构形式,考虑到电动机的转速过大,需要减速增矩,故电动机的输出转矩经减速机构后再驱动转向轴。因此电动机的额定输出转矩为 G T T a e max = (4) 式中G 为减速机构的减速比。 转向盘(即转向轴)的转动速度一般取h n =1.2r/s=72r/min,为了使电动机在转向盘转速较快的时候能够跟得上,所需电动机的最大额定转速为 G n n h e ?= (5) 由式(4)和(5)可得到电动机的额定功率 9549 e e e n T P ?= 计算得到LC 车型的电机额定功率为117.7W<125W ,EK 车型115.7W<125W 。 而扭转则涉及到力矩。 根据国际单位制,力矩的单位是牛顿米。本物理量非能量,因此不能以焦耳(J)作单位; 力矩的表示符号是希腊字母,或。 力矩与三个物理量有关:施加的作用力、从转轴到施力点的位移矢量、两个矢量之间的夹角。力矩以矢量方程表示为 。 力矩的大小为 。 力矩的概念,起源于阿基米德对杠杆的研究。 力矩的定义:力矩等于作用于杠杆的作用力乘以支点到力的垂直距离。假设作用力施加于位置为的粒子。选择原点为参考点,力矩以方程定义为 。 力矩大小为 ; 其中,是两个矢量与之间的夹角。 力矩大小也可以表示为 ; 其中,是作用力对于的垂直分量。 任何与粒子的位置矢量平行的作用力不会产生力矩。 从叉积的性质,可以推论,力矩垂直于位置矢量和作用力。力矩的 方向与旋转轴平行,由右手定则决定。 使1牛顿米的力矩,作用1 全转,需要恰巧焦耳的能量: 。 其中,是能量,是移动的角度,单位是弧度。 力矩有大小方向是矢量,与动量等道理一样,只是一个力学名称。 角动量在物理学中是与物体到原点的位移和动量相关的物理量,在经典力学中表示为到原点的位移和动量的叉积,通常写做。角动量是矢量。 其中,表示质点到原点的位移,表示角动量。表示动量。而又可写为: 其中表示杆状系统的转动惯量,ω是角速度矢量。 在不受非零合外力矩作用时,角动量是守恒的。需要注意的是,由于成立的 条件不同,角动量是否守恒与动量是否守恒没有直接的联系。 角动量在量子力学中与角度是一对共轭物理量。 需要特别说明的是:动量, 也就是说动量的方向和速度的方向一致. 角动量守恒定律是指系统所受合外力矩为零时系统的角动量保持不 变。当方程式右边力矩为零时,可知角动量不随时间变化。 需要搞懂有心力也就是向心力的作用不能产生力矩。 第26卷第8期2009年8月 机 电 工 程 Mechanical &Electrical Engineering Magazine Vol .26No .8 Aug .2009 收稿日期:2008-12-08 作者简介:李 保(1981-),男,河南新乡人,主要从事机电一体化设备程序设计、嵌入式系统开发等方面的研究.E 2mail:libao1982@https://www.360docs.net/doc/8e10549524.html, 基于伺服电机转矩模式的动态力矩测试系统 李 保,王长华,倪森祥 (浙江省机电设计研究院有限公司,浙江杭州310003) 摘 要:为测试阻尼稳速展开机构的稳速能力和带负载特性,采用了基于CANopen 协议的力矩传感器 及工作于转矩模式下的交流伺服电动机,由工控机及可编程序控制器(P LC )调节转矩大小,实现了对展开机构角度2输出力矩曲线和展开机械2转速曲线的动态测试。试验结果表明,该系统能够对阻尼稳速展开机构特性进行高精度地评测。关键词:交流伺服电机;负载特性;转矩中图分类号:TP383.4 文献标识码:A 文章编号:1001-4551(2009)08-0079-04 D ynam i c m o m en t testi n g syste m ba sed on AC servo m otor torque con trol m ode L IBao,WANG Chang 2hua,N I Sen 2xiang (Zhejiang Institute of M echanical &Electrical Engineering Co .L td .,Hangzhou 310003,China ) Abstract:A i m ing at testing fixed 2s peed and driving l oad character of fixed 2s peed da mp ing t o expand machine,t orque transducer based on C ANopen p r ot ocol and AC servo mot or operated at t orque contr ol mode were used,the AC servo mot or mode s witch and l oad were contr olled by PC and P LC .Charts of expanding angle 2out put with t orque and expanding angle 2s peed were tested with high p recisi on .The test results indicate that the syste m can comparatively p recise evaluate the character of fixed 2s peed da mp ing t o expand machine . Key words:AC servo mot or;l oad character;t orque 0 引 言 应某航天研究所要求设计一个在不同环境条件下,能够对阻尼稳速展开机构各项性能指标测试的仪器。测试仪能自动收拢机构和释放机构,同时测试仪还能使机构加设定的负载力矩展开。因此,系统需要有收拢机构时的驱动源和机构展开时的负载源。由于交流伺服 电机[1] 具有体积小、重量轻、大转矩输出、低惯量和良好的控制性能等优点,同时有些交流伺服电动机具有多种工作模式,因此在该动态力矩测试系统中,驱动源和负载源的主要部件都采用了交流伺服电机。 基于此,本研究主要介绍基于伺服电机转矩模式的动态力矩测试系统。 1 力矩测试和控制系统 整个测控系统分为伺服电动机控制部分和力矩角 度测量部分,其中各种传感器测量信号通过US B [2] 接入工控机,整个力矩测控系统如图1所示 。 图1 力矩测控系统结构图 本系统中的P LC 选取三菱公司FX 1N 型,具有晶体管输出并带高速脉冲输出端。电动机选择三菱公司MR 2J3系列交流伺服电机和配套的MR 2J32350A 伺服放 大器 [3] 。交流伺服电动机输出功率为3.5k W ,它具有 位置、速度控制模式和转矩控制模式。伺服放大器具有多个电隔离的开关量输入/输出口和脉冲量输入/输出转矩的测试
电机扭矩计算
转向力计算
力矩与角动量的关系
基于伺服电机转矩模式的动态力矩测试系统