微晶玻璃 第四章
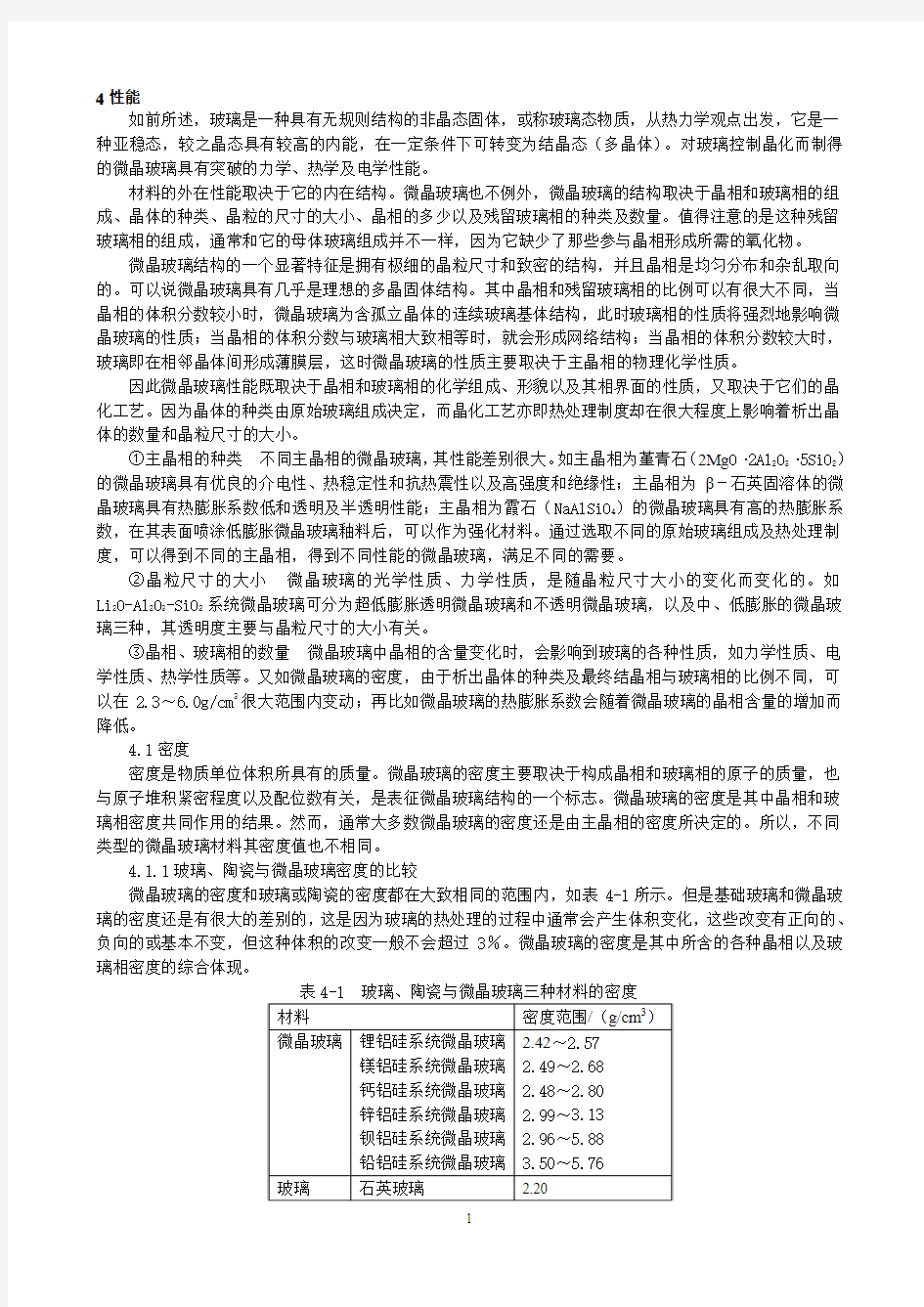

4性能
如前所述,玻璃是一种具有无规则结构的非晶态固体,或称玻璃态物质,从热力学观点出发,它是一种亚稳态,较之晶态具有较高的内能,在一定条件下可转变为结晶态(多晶体)。对玻璃控制晶化而制得的微晶玻璃具有突破的力学、热学及电学性能。
材料的外在性能取决于它的内在结构。微晶玻璃也不例外,微晶玻璃的结构取决于晶相和玻璃相的组成、晶体的种类、晶粒的尺寸的大小、晶相的多少以及残留玻璃相的种类及数量。值得注意的是这种残留玻璃相的组成,通常和它的母体玻璃组成并不一样,因为它缺少了那些参与晶相形成所需的氧化物。
微晶玻璃结构的一个显著特征是拥有极细的晶粒尺寸和致密的结构,并且晶相是均匀分布和杂乱取向的。可以说微晶玻璃具有几乎是理想的多晶固体结构。其中晶相和残留玻璃相的比例可以有很大不同,当晶相的体积分数较小时,微晶玻璃为含孤立晶体的连续玻璃基体结构,此时玻璃相的性质将强烈地影响微晶玻璃的性质;当晶相的体积分数与玻璃相大致相等时,就会形成网络结构;当晶相的体积分数较大时,玻璃即在相邻晶体间形成薄膜层,这时微晶玻璃的性质主要取决于主晶相的物理化学性质。
因此微晶玻璃性能既取决于晶相和玻璃相的化学组成、形貌以及其相界面的性质,又取决于它们的晶化工艺。因为晶体的种类由原始玻璃组成决定,而晶化工艺亦即热处理制度却在很大程度上影响着析出晶体的数量和晶粒尺寸的大小。
①主晶相的种类不同主晶相的微晶玻璃,其性能差别很大。如主晶相为堇青石(2Mg O·2Al2O3·5SiO2)的微晶玻璃具有优良的介电性、热稳定性和抗热震性以及高强度和绝缘性;主晶相为β-石英固溶体的微晶玻璃具有热膨胀系数低和透明及半透明性能;主晶相为霞石(NaAlSiO4)的微晶玻璃具有高的热膨胀系数,在其表面喷涂低膨胀微晶玻璃釉料后,可以作为强化材料。通过选取不同的原始玻璃组成及热处理制度,可以得到不同的主晶相,得到不同性能的微晶玻璃,满足不同的需要。
②晶粒尺寸的大小微晶玻璃的光学性质、力学性质,是随晶粒尺寸大小的变化而变化的。如Li2O-Al2O3-SiO2系统微晶玻璃可分为超低膨胀透明微晶玻璃和不透明微晶玻璃,以及中、低膨胀的微晶玻璃三种,其透明度主要与晶粒尺寸的大小有关。
③晶相、玻璃相的数量微晶玻璃中晶相的含量变化时,会影响到玻璃的各种性质,如力学性质、电学性质、热学性质等。又如微晶玻璃的密度,由于析出晶体的种类及最终结晶相与玻璃相的比例不同,可以在2.3~6.0g/cm3很大范围内变动;再比如微晶玻璃的热膨胀系数会随着微晶玻璃的晶相含量的增加而降低。
4.1密度
密度是物质单位体积所具有的质量。微晶玻璃的密度主要取决于构成晶相和玻璃相的原子的质量,也与原子堆积紧密程度以及配位数有关,是表征微晶玻璃结构的一个标志。微晶玻璃的密度是其中晶相和玻璃相密度共同作用的结果。然而,通常大多数微晶玻璃的密度还是由主晶相的密度所决定的。所以,不同类型的微晶玻璃材料其密度值也不相同。
4.1.1玻璃、陶瓷与微晶玻璃密度的比较
微晶玻璃的密度和玻璃或陶瓷的密度都在大致相同的范围内,如表4-1所示。但是基础玻璃和微晶玻璃的密度还是有很大的差别的,这是因为玻璃的热处理的过程中通常会产生体积变化,这些改变有正向的、负向的或基本不变,但这种体积的改变一般不会超过3%。微晶玻璃的密度是其中所含的各种晶相以及玻璃相密度的综合体现。
表4-1 玻璃、陶瓷与微晶玻璃三种材料的密度
注:微晶玻璃的晶核剂均为TiO2
4.1.2组成对密度变化的影响
由于从玻璃态转变为微晶玻璃时,其体积变化的程度通常较小,因此各种氧化物对微晶玻璃密度的影响和对普通玻璃的密度是相同的。这些氧化物如BaO或PbO能使玻璃具有高的密度,也同样使微晶玻璃获得高密度。在微晶玻璃中减少Al2O3或SiO2,增加MgO、CaO、ZnO、BaO、PbO的含量可以导致高的密度,而且BaO和PbO的影响最显著。
CaO-Al2O3-SiO2系统微晶玻璃中,随着CaO替代SiO2量的增加,微晶玻璃的密度明显增加。这是由于CaO含量提高,使得CaO与SiO2结合生成CaSiO3晶体的机会增加,且β-CaSiO3晶体的密度一般在2.90~3.20g/cm3之间,所以微晶玻璃试样的密度会随着CaO含量的增加而提高。
微晶玻璃的密度值一般来说取决于其总的化学组成,但是晶相及玻璃相的组成将决定具体微晶玻璃的密度。例如二氧化硅可以作为玻璃相中的一个组分,也可作为游离二氧化硅以方石英或石英的形成存在,也可以作为一种组分存在于复杂的硅酸盐晶体中。所有这些不同的存在形式对微晶玻璃密度的影响也不同。如石英的密度为2.65g/cm3,比方石英的密度2.32g/cm3高得多。因此,这两种晶体的相对含量的变化,对微晶玻璃的密度就会产生显著的影响。
4.1.3密度与玻璃热历史的关系
玻璃析晶是一个结构有序化的过程,因此玻璃在析晶后,其密度一般是增加的。玻璃晶化(包括微晶化)后,其密度的大小主要决定于析出晶体的类型。例如Li2O-Al2O3-SiO2系统微晶玻璃,在500℃前热处理,由于未发生晶化,其密度值不变。在530~700℃热处理5~24h,由于玻璃中析出偏硅酸锂晶体,使密度值从2.36g/cm3增加到2.38g/cm3;进一步提高热处理温度到800℃,密度值又升高到2.44g/cm3,比基础玻璃提高3.2%。这是因为玻璃相中生成了β-锂霞石固溶体。
G.Partridge曾明确指出,Li2O-Al2O3-SiO2系统低膨胀微晶玻璃在晶化过程中,前段密度的急剧上升是由于β-石英固溶体的析出所引起的,而后段密度的下降则是因为β-石英固溶体转变成了β-锂辉石固溶体,微晶玻璃密度与保温时间的关系如图4-1所示。
上述情况说明,微晶玻璃密度与析出的晶相、玻璃相种类和数量有着密切关系。所以根据各种热处理条件下密度的变化,可以通过控制热历史从而得到不同的晶相,以制取具有不同物理性质的微晶玻璃。
近年来有关密度测定在烧结法微晶玻璃板材生产中的应用,由何峰等得出CaO-Al2O3-SiO2系统微晶玻璃密度与晶化温度、玻璃颗粒度、晶化时间的关系曲线,分别如图4-2~图4-4所示。微晶玻璃的密度在1120℃前,随着晶化温度的提高而增大,在1120℃附近出现了极值点;而当晶化温度高于1120℃后,其密度有随着温度升高而下降的趋势,且在温度达到1150℃以后,密度下降幅度有所增加。由图4-3显示:随着玻璃颗粒度的增加,微晶玻璃试样的密度逐渐下降。图4-4中曲线反映出,在0.5~1.5h内,随晶化时间的增加,微晶玻璃的密度迅速增大;而当晶化保温时间大于2.0h以后,随晶化时间的延长,其密度增大,但变化非常缓慢。
4.2力学性质
4.2.1强度
在确定材料是否适于某一特定用途时,机械强度是其重要性能之一,也常常是主要的因素。材料的强度一般用抗压强度、抗折强度、抗弯强度和抗冲击强度等指标表示。在室温下,微晶玻璃和普通陶瓷及玻璃一样,都是脆性材料,这意味着它们不具有可延性和可塑性,在荷重造成破坏之前,呈现完全弹性的状态。和其他的脆性材料一样,它们具有较高的弹性,并以劈裂的形式断裂。
微晶玻璃之所以得到广泛应用,原因之一就是它的机械强度高,特别是抗弯强度高。但微晶玻璃存在
有易碎的玻璃相的组成,其机械强度在很大程度上,受到以下几个因素的影响:①结晶相的颗粒大小和体积分数;②界面的结合强度;③不同的弹性模量;④不同的热膨胀性能。
对于同一磨损条件下的微晶玻璃材料和基础玻璃来说,微晶玻璃的强度试验值要高于基础玻璃,这可以归纳为多因素的作用结果。建立在临界应力概念上的机械强度理论认为:微晶玻璃材料的强度很大程度
上来源于它的弹性模量(8×104~15×104MPa )大于玻璃的弹性模量(约6×104
MPa )。但是,实际上微晶玻璃与玻璃的强度比的倍数常常大于它们的弹性模量比的倍数,因此,另一合理的解释是微晶玻璃中的晶粒可以造成裂纹尖端的弯曲和可能的钝化,增加了破裂功,并且减缓甚至阻止了裂纹穿过晶相和玻璃相的界面,而在玻璃中则有一个不受阻碍的断裂路径。
微晶玻璃强度增加的原因主要是由于具有细晶、致密的微观结构。脆性材料中的裂纹通常带来缺陷,例如夹杂物(包裹体)、内部气孔或是微裂纹。机械强度将受到微晶玻璃的微观结构的影响。表4-2描述了几种典型的微晶玻璃材料在弯曲时晶体尺寸对强度的影响。
玻璃的机械强度,很大程度上可依靠由Griffith 推导的著名机械强度公式来进行解释。其机械强度ζ为:C
E ∏=
γ
σ2 (4-1) 式中 E ――弹性模量,MPa ; γ――断裂表面能;
C ――微裂纹的临界长度。
从式(4-1)可以看出来,玻璃强度的增加是依靠弹性模量E 或断裂表面能γ的增加或微裂纹的临界长度C 的减少来实现的。如果晶相在限制玻璃的微裂纹尺寸中起作用,当晶相具有比残余玻璃相低的热膨胀系数时,裂纹长度将受晶间距离λ的限制,机械强度ζ与λ的二次方根成反比:2
/1-'=λ
σK (4-2)
f f V V d /)1(-=λ
式中(4-2)中的K ′值由(2E υ/π)1/2
得出,d 为晶粒直径,V f 为晶相的体积分数。表4-2给出了组成及晶体尺寸对微晶玻璃抗弯强度的影响。
受到晶粒间应力的影响使得微裂纹得到扩张,这一现象是基于晶体和玻璃相不同的热膨胀系数,当结晶相的热膨胀系数比玻璃相的热膨胀系数小时,就会形成穿晶断裂;反之,则形成沿晶断裂。
4.2.1.1几种常见系统微晶玻璃的强度
表4-3列出了微晶玻璃和几种常见玻璃、陶瓷和石材等材料弹性模量。一般来说,微晶玻璃的机械强度比普通玻璃和陶瓷要高,这一点从杨氏模量上也可得到反映,表4-3所列的微晶玻璃及几种玻璃、陶瓷及石材的弹性模量数据可供比较。表4-4列出了几种常见系统微晶玻璃所采用的晶核剂以及主晶相和抗弯强度。从表4-4中可以看出,晶核剂对得到较高机械强度的重要性。例如,在Li 2O -SiO 2微晶玻璃组成中引入P 2O 5作为晶核剂就使其强度提高了6倍。在这些材料中,二硅酸锂是作为主晶相出现的,并且对Li 2O -ZnO -SiO 2系统的微晶玻璃也是如此,也能得到高强度。
表4-2 组成及晶体尺寸对微晶玻璃抗弯强度的影响
4
堇青石作为主晶相的MgO-Al2O3-SiO2系统的微晶玻璃也具有高的机械强度。其原因之一可能是由于结晶相和残余玻璃相的热膨胀系数相差很小。因此,微晶玻璃内的残余应力可能是比较低的。
Li2O-Al2O3-SiO2系统微晶玻璃具有很大的意义,因为采用该系统可制备具有低热膨胀系数和高抗热冲击性能的材料,不过,这种材料的机械强度一般比堇青石微晶玻璃的低。这种系统较低的机械强度可能是由于在微晶玻璃中存在显著的残余应力。因为β-锂辉石具有低的膨胀系数,在晶体周围的残余玻璃相中会造成周向张应力,即使这些应力不会造成微裂纹,却可能降低该系统微晶玻璃的整体强度。但是,如果没有形成具有很低热膨胀系数晶体的Li2O-Al2O3-SiO2系统微晶玻璃,则有可能获得较高的机械强度。这种
微晶玻璃的Al2O3含量较低,主晶相为二硅酸锂、石英或方石英。
当β-锂霞石作为主晶相存在时,会使微晶玻璃的整体强度大大降低,因为这种呈多晶相集合状的晶体具有大的负热膨胀系数,使β-锂霞石微晶玻璃表现显著的各向异性,其强度因而受到很大的影响。
4.2.1.2 玻璃组成的变化对强度的影响
微晶玻璃的结构及性能随着成分的变化而发生改变。实际上,玻璃成分是通过结构决定其性质的。如前所述,微晶玻璃不同于一般系统的玻璃,其结构中既存在玻璃相,亦存在有相当比例的晶相,玻璃相和晶相的结构和性质共同作用决定了微晶玻璃的性能。
例如,CaO-Al2O3-SiO2系统微晶玻璃的主晶相为β-硅灰石,晶相含量一般为30%~40%,最高含量的可达50%左右,通常该主晶相含量的增多,对微晶玻璃有提高T g、T f温度、降低热膨胀系数、增加密度和提高强度的作用;其玻璃相含量一般为60%~70%,其结构随着成分的变化而发生变化,导致对微晶玻璃性能的影响较为复杂,且结构随着成分的变化而发生变化,导致对微晶玻璃性能的影响较为复杂,且因为含量大而使其对性能的影响程度也很大。
CaO-Al2O3-SiO2系统微晶玻璃中,晶相被连通的玻璃相所包裹,此时其抗折强度更大程度取决于玻璃相的性质。随着CaO含量的增加,玻璃相中CaO含量亦增加,积聚作用使网络结构紧密,玻璃相强度提高;但当CaO含量大30%时,由于晶体的析出量达到近50%,此时连通的玻璃相网络被晶相破坏,强度大幅度下降。随着Al2O3含量的增加,玻璃相中更多的〔AlO4〕,使断开的〔SiO4〕网络连接,网络紧密,微晶玻璃强度增大;当Al2O3含量增加到有部分〔AlO6〕存在时,填充网络空隙,亦使结构紧密。强度增加。随着B2O3含量的增加,B3+以〔BO4〕存在时,加入玻璃网络使断裂的〔SiO4〕连接,强度增加,当有过多的B3+存在时,结构疏松,使强度下降,因此其强度随着B2O3含量的变化有一个极大值。因为CaO-Al2O3-SiO2系统微晶玻璃主晶相β-硅灰石,且试样玻璃中ZnO含量变化,对玻璃析出β-硅灰石晶体影响不大。因此,随着ZnO含量的提高,微晶玻璃试样的抗折强度变化近似于直线,CaO-Al2O3-SiO2系统微晶玻璃抗折强度变化不大。
在Li2O-Al2O3-SiO2系统微晶玻璃中,用ZnO替代Al2O3时,研究表明:随着ZnO含量的增加,该系统微晶玻璃的弯曲强度显著加大。这是因为随着组成的变化,其晶相的类型和比例也发生了变化。当ZnO的含量小于Al2O3时,主晶相为富二氧化硅的β-锂辉石固溶体以及二硅酸锂;当ZnO的含量大于Al2O3时,其主晶相转变为石英和大量的二硅酸锂。因此,在这种材料中,将低热膨胀的晶体转换成高热膨胀的晶体时,其微晶玻璃的抗折强度得到了增强。
4.2.1.3热处理制度对强度的影响
热处理制度的变化在调整微晶玻璃的显微结构及晶相组成方面有重要意义,因此这是微晶玻璃材料强度的一个主要影响因素。热处理工艺的目的在于把玻璃转变为性能优越的微晶玻璃。通常情况下,要求微晶玻璃中的微晶体分布相对集中,并使它们紧密结合。应尽量避免出现晶粒异常长大的现象,少量微晶异常长大会影响到微晶玻璃的性质。这就意味着要对整个热处理的成核阶段进行仔细的控制。已经核化的玻璃需要进一步升温,以便使晶核生长,升温速度也要仔细控制,防止微晶玻璃在热处理过程中发生变形。因此,通过对基础玻璃成分的调整以及热处理工艺的优化,制备具有较高力学性能的微晶玻璃材料,就具有现实意义。
MgO-Al2O3-SiO2系统微晶玻璃具有非常广泛的组成,通过成分配比的调整和热处理工艺的选择,可以获得具有多种优良性能的材料。该系统中以堇青石为主晶相的微晶玻璃,具有优异的电学、热学性能、而且具有较高的力学性能。以TiO2作为晶核剂的堇青石微晶玻璃的晶化过程和力学性能已经进行了广泛的研究。赵永红等添加10%TiO2,并加入0~2%的复合澄清剂,玻璃配合料经仔细研磨、混合后加入高温预热的石英坩埚内,并于1500~1550℃熔制3h,随后浇铸在预热的铁板上,并立即于700℃退火2h,得到如图4-5所示的抗弯强度的变化曲线。由图4-5可以看出,在不同的温度下核化和晶化时,材料的抗弯强度变化均呈抛物线状,抗弯强度最高可达350MPa。在800℃和875℃核化的试样,其强度均低于850℃核化的试样。
造成这种现象的原因是:850℃核化时,该玻璃具有最佳的成核率,因为玻璃的成核速度与温度的关系也是一条具有单个峰值的曲线,而850℃接近于峰值温度。800℃核化的试样抗弯强度普遍较低,主要是因为此温度下,晶核的数量较少,晶体长大后更容易产生个别粗大的晶粒,而且所含晶相体积分数较小,
导致强度下降。
MgO-Al2O3-SiO2系统微晶玻璃抗弯强度随晶化温度的变化,可以结合玻璃的晶化过程进行分析。在1100℃热处理时,玻璃中主要有β-石英固溶体,晶体类型单一,晶体含量不高。当温度升高到1150℃,假蓝宝石晶体发展成为主晶相,晶体含量进一步增大,强度有一定的提高。温度进一步升高至1200℃,残余玻璃相已基本消失,晶相以α-堇青石和尖晶石为主体,并有少量β-石英固溶体的低膨胀系数,使材料具有合适的热膨胀系数和抗热冲击性,而具有高弹性模量和高硬度的均匀分布的细小尖晶石晶体,则起到均匀强化的作用。这时,微晶玻璃具有最佳的力学性能。在850℃核化时,其抗弯强度可稳定在340MPa 以上,可以替代一些工程陶瓷使用。1250℃晶化时,抗弯强度下降较快,这主要是由于高膨胀系数方石英相的析出,在材料内部产生很大的内应力,并导致热处理后材料中产生较大的微裂纹。
此外,较高温度晶化使部分晶粒异常长大,根据Griffith理论,当晶粒尺寸增加时,其中裂纹的尺寸也同时增大,由此造成抗弯强度的急剧下降。图4-6是玻璃在850℃核化时,分别于1200℃和1250℃晶化后的扫描电子显微镜(SEM)照片。图4-6(a)中,细小的尖晶石颗粒均匀分布于珊瑚状的α-堇青石和β-石英固熔体晶体相之间,晶粒尺寸均匀细小,大约为0.3~0.5μm之间,这样一种细晶致密结构使材料具有较高的抗弯强度。图4-6(b)中,晶体尺寸明显变大,部分合并呈条状,并在基体上产生了明显的微裂纹,这使材料的力学性能大大降低。
4.1.2.4表面状态对强度的影响
玻璃表面机械损坏通常认为会减小其强度,与玻璃相比,这一现象对微晶玻璃材料的影响要小得多。如表4-5所示,表面未受损坏的玻璃经过研磨后最高强度通常要减少为最初强度值的5%~15%。而微晶玻璃材料的强度则减少到50%~90%(这主要由微晶玻璃的类型决定,例如可加工微晶玻璃的抗弯强度在磨损后几乎没有变化)。这些结果说明,微晶玻璃对表面损伤的敏感性比玻璃的小得多。这是微晶玻璃具有较高强度的原因之一。
对于同样组成的微晶玻璃,在晶化热处理之前,对玻璃进行表面处理,在材料的最后强度方面产生了很好的影响。实验中,将一些玻璃棒在浓氢氟酸中侵蚀很短时间,另一些玻璃棒在球磨机中用80号金刚砂磨10min,其余的玻璃棒没有给予特殊的表面处理。将经过各种表面处理的试样进行强度测试,其结果列于表4-5中。为了方便,结果均以强度因数表示。所谓强度因数是指某一特定组试样的平均强度,对未经表面处理,也未经晶化处理的试样强度的比值。
从表4-5中可以得出:
⑴将未经热处理的玻璃在氢氟酸中侵蚀,其机械强度提高三倍以上(第3组和第1组相比);
⑵由侵蚀过的玻璃制备出的微晶玻璃强度,比未经侵蚀玻璃制得的微晶玻璃强度要高(第2组和第4组相比);
⑶在热处理前将玻璃研磨制得的微晶玻璃材料,比未经研磨玻璃制得的微晶玻璃强度要低(第2组和第5组相比)。
可见晶化前的表面机械损坏对晶化前除去玻璃表面的裂纹将会提高材料的强度。
微晶玻璃材料的强度还可以通过后续的表面强化处理方法得以提高。例如,采用离子交换法,可以使得研磨后的β-锂辉石固溶体微晶玻璃材料的强度值达到350MPa。霞石微晶玻璃材料经过离子交换后,其抗弯强度值大约可以达到1400MPa。
4.2.1.5微晶玻璃内应力与强度的关系
微晶玻璃中内应力的变化对其强度的影响很大。由于玻璃相和结晶相的热膨胀系数不同,在其界面处就会形成微应力。当晶相具有比残余玻璃相低的热膨胀系数时,则在靠近晶体周围的玻璃相中产生周向拉
应力和径向压应力。当晶相具有比残余玻璃相高的热膨胀系数时,所引起的应力的正负号也就相反。这样的应力分布通常导致材料强度的增加。因此,如果晶相在限制玻璃中的微裂纹尺寸方面起作用时,在前一种情况下,具有主轴沿径向排列的裂纹尺寸方面其作用时,在前一种情况下,具有主轴沿径向排列的裂纹可能更危险,而且裂纹长度将受到晶间距离,也就是λ的限制。对于第二种情形,由于存在高热膨胀系数的晶体,则沿周向排列的微裂纹就可能更危险。这种裂纹的长度,将和晶体直径d成正比,从而其强度将是d-1/2的函数,而不是λ-1/2的函数。
从上述讨论可以认为,含有低于基体玻璃热膨胀系数的晶体的微晶玻璃中,其界面应力将使微晶玻璃的强度的降低。虽然含有低膨胀晶相的微晶玻璃一般不像含有高热膨胀晶相的微晶玻璃具有那样高的机械强度,但是含有低膨胀晶相的微晶玻璃还是比它的原始玻璃的强度要大得多。
实用微晶玻璃可能含有热膨胀系数低于和高于残余玻璃相的两种或两种以上的复合晶相,这时微晶玻璃内应力与强度的关系就更为复杂。
程金树等以CaO-Al2O3-SiO2系统微晶玻璃为研究对象,利用X射线应力测试仪和相关软件以及其他现代测试手段,对玻璃组分,退火制度与微晶玻璃中的内应力和强度的关系进行了研究。通过实验,得到了以下几点结论。
⑴X射线衍射测试残余应力是非破坏性的检测方法,对于测试脆性和不透明材料的残余应力是最常用的方法。适合于微晶玻璃等脆性材料的残余应力的测试研究。测试的精确度可以通过选取高衍射角及延长衍射时间来实现。
⑵微晶玻璃中的残余应力由热梯度残余应力和热不匹配残余应力(CTE残余应力)组成,且热不匹配残余应力是微晶玻璃残余应力中的主要组成部分。
⑶当CaO含量增加时,微晶玻璃中β-硅灰石晶体的含量呈现上升趋势,而且β-硅灰石晶体的长径比逐渐减小,从开始的针状变为后来的短柱状。随CaO含量增加,微晶玻璃表面的残余应力先减小后增大。随CaO含量的增加,微晶玻璃的显微硬度逐渐增大,而抗折强度呈下降的趋势。综合考虑CaO含量对微晶玻璃残余应力、机械强度以及其他各方面的影响,在CAS系统微晶玻璃的实际生产中,CaO含量取16%~18%是较为合适的。
⑷Al2O3对CaO-Al2O3-SiO2系统微晶玻璃中β-硅灰石晶体的析出有抑制作用。微晶玻璃中β-硅灰石晶体的含量随Al2O3含量增加呈下降趋势,且β-硅灰石晶体的长径比逐渐增大,晶体形状由开始的短柱状变为后来的针状。随Al2O3含量增加,微晶玻璃表面的残余应力减小,抗折强度先增大后减小,微晶玻璃的显微硬度逐渐减小。综合考虑Al2O3含量对微晶玻璃残余应力、抗折强度、显微硬度以及其他各方面的影响,在CAS系统微晶玻璃的实际生产中,Al2O3含量取6%~8%是较为合适的。
4.2.2弹性与弹性模量
材料的弹性模量在确定它在变形时的行为方面是非常重要的。例如,当一种微晶玻璃由于温度应力的作用而产生变形时,弹性模量可决定所产生应力的大小。这种情况通常发生在材料突然加热或冷却情况下,此时低的弹性模量是可取的。同样,如果把一种为己功能玻璃与具有不同热膨胀系数的另一种材料(如一种金属或陶瓷等)进行焊接时,低弹性模量是有利的,因为对于一定的应变,其应力则较低。当然也有些情况可能希望高的弹性模量。这种情况常出现在玻璃纤维增强塑料中。
微晶玻璃材料的弹性性能包括杨氏模量E、刚性模量(扭变模量)G、体积弹性模量K和泊松比μ。对于各向同性的材料,这些常数有以下关系:G=E/2(1+μ) (4-3) K=E/3(1-2μ) (4-4)μ=E/2G-1 (4-5)
微晶玻璃的弹性模量比普通玻璃和某些普通陶瓷都高。但是它比烧结纯氧化物陶瓷的弹性模量低,如表4-6所示。玻璃的弹性模量E和它的化学组成具有近似加和的关系。多相陶瓷的弹性模量也是结晶相和玻璃相的各种性能的加和函数。微晶玻璃的弹性模量基本上取决于晶相的弹性常数。当然还必须考虑到,在玻璃相中能够促进高E值的氧化物的存在,特别是CaO、MgO和Al2O3对玻璃的弹性模量有显著的影响。
表4-6 微晶玻璃和其他材料的弹性模量
4.2.3硬度与耐磨性 4.2.3.1硬度
硬度是指材料抵抗其他较硬物体压入或刻划的能力,它是材料本身多种机械性能的综合指标。硬度并不是一种材料的基本物理特性,而是在不同程度上与测试方法有关的一系列物理性质的综合体现。
不同材料的硬度,测定方法不同。通常,矿物材料的硬度用刻划法测定;金属等材料的硬度用压入法测定。
刻划法是指一种材料对另一种材料的刻划能力。压入法是指一个荷重的锥体或球体(通常为钻石或钢球)在规定的条件下压入材料的深度。虽然其中任何一个方法都可用来区分材料的硬度等级,但硬度值却随着所用的方法不同而可能不一样。由于这个原因,必须尽可能选用尽量接近实际情况的硬度测定方法。
不同的测试条件也会得到不同的硬度值。刻痕硬度是通过莫氏硬度计来测定的。由刻划法测定的矿物硬度分为10级(莫氏硬度),其硬度递增的顺序为:滑石1;石膏2;方解石3;萤石4;磷灰石5;正长石6;石英7;黄玉8;刚玉9;金刚石10。通过刻划法测定玻璃的莫氏硬度,其值通常为5~7,微晶玻璃的莫氏硬度值大约为7~9。压痕硬度的测试方法较多,其中努氏硬度和钻石锥体硬度,虽然使用不同形状的压头,但都靠测量所造成的永久压痕的大小而定。努氏硬度是用荷载的质量数除以压痕的投影面积来表示;而钻石锥体硬度是用荷载的质量数除以接触面积表示。在洛氏硬度的测试中,用一个150kg 荷载的钻石球形锥体压头,在规定条件下压头压入试件的深度来表示其硬度。
当比较材料的压痕硬度时,必须规定测试时所用的荷载。努氏硬度通常(500g 荷载)用MPa 来表示。一些微晶玻璃的努氏硬度比铸铁还要大,可以达到1700~2900MPa ,而不锈钢的努氏硬度值在1450~1950MPa 之间。一些微晶玻璃和其他材料的努氏硬度值,如表4-7所示。
表4-7 微晶玻璃和其他材料的努氏硬度
4.2.3.2一般来说微晶玻璃的硬度和它的耐磨性有很好的相关性。因为硬度大的材料,其耐磨性越强。这个特性的实际意义是它可以影响材料在正常使用下的耐久性。因此材料的耐磨性在某种意义上可以看作是硬度的一种衡量。
耐磨性是指材料表面抵抗磨损的能力,常用磨损率(B )表示:A
m m B 2
1-=
(4-6) 式中m 1,m 2--试件被磨损前、后的质量,g ;
A ――试件受磨损的面积,cm 2
.
用标准情况下所测得的耐磨性来评价材料的硬度是非常有用的。例如,矿渣微晶玻璃得这种测试值就很高;还有一种Li 2O-ZnO-SiO 2系统微晶玻璃的耐磨性为某种不锈钢的10倍。
在考虑微晶玻璃部件相互接触、由于滑动或旋转而相互移动出现磨损的可能性时,其表现出的摩擦程度是重要的。由于这个原因,应该知道微晶玻璃接触面间的摩擦系数。表4-8中列出了不同类型的微晶玻璃在磨光面间测得静、动摩擦系数值。
表4-8 微晶玻璃的摩擦系数
4.3热学性质
4.3.1热膨胀系数和抗热冲击性能(抗热震性)
微晶玻璃以能制得很大范围的热膨胀系数而著称。一方面可以制得具有负的热膨胀系数材料,而另一方面又可以制得很高的正热膨胀系数的材料。在这两者之间还有一些热膨胀系数几乎等于零的微晶玻璃材料。更有实际意义的是微晶玻璃的热膨胀系数可以调整到和普通玻璃或普通陶瓷或某种金属或合金的热膨胀系数近似相仿。
对材料随着温度的变化而产生尺寸变化的研究是非常重要的。例如,如果要求一种微晶玻璃具有高的抗热冲击能力,则要求其热膨胀系数必须尽可能的低,以便把材料中由温度应力造成的应变降至最低。又例如要把微晶玻璃焊接到或者刚性连接到另一种材料上,如一种金属上时,则需要它们的热膨胀系数近似匹配,以防止这个接合件在加热或冷却时产生高应力。在大型光学镜头应用中,随着温度的变化,微晶玻璃尺寸的稳定性是非常重要的,此时需要制备一种热膨胀系数接近零的微晶玻璃材料。
4.3.1.1化学组成和晶体种类及含量对热膨胀性能的影响
微晶玻璃作为一种复合材料,其热膨胀系数是各相共同作用的结果。例如,相同化学组成(如Li2O-SiO2)的微晶玻璃,其热膨胀系数随着晶相和玻璃相含量的不同而不同。这可以通过测量得到验证,或在假设热膨胀系数是共同作用的前提条件下,通过计算得出来。如图4-7所示。
在那些对抗热震性或对热膨胀系数有较高要求的场合下,例如微晶玻璃与其他材料复合或微晶玻璃作为焊接料时,热膨胀系数的精确设定是非常重要的。
微晶玻璃热膨胀系数可以与原始玻璃大不相同。它主要取决于晶相的种类和微晶玻璃中各相的含量,这些可以通过热处理工艺灵活地得到控制。
微晶玻璃是由晶相和剩余玻璃相热膨胀系数相同是不太可能的。例如,在零膨胀微晶玻璃中,晶相是负向膨胀,而玻璃相为正向膨胀,因此两者之间的膨胀系数差别不是很大时,可以获得抗热冲击性良好的微晶玻璃。但是,微晶玻璃中的晶相和残余玻璃相的热膨胀系数经常是不相匹配的。这种热膨胀失配的影响,可能导致微晶玻璃中微应力的产生。在极端的情况下,就能够造成微裂纹,由于晶体的尺寸一般较小。使这种情况有所缓和,使局部应力限于允许的范围内。
尽管如此,在设计含有低膨胀晶相的微晶玻璃时,应避免选用倾向于富集在残余玻璃相中以及能提高其热膨胀系数的组分。因此一般应该避免用超过形成低膨胀锂铝硅酸盐晶体所需的过剩氧化锂,或是避免含量相当高由不参加晶相的其他碱金属氧化物的存在。
当具有很高的热膨胀系数的晶体形成时,也可能出现同样的同题。此时残余玻璃相几乎肯定具有比晶相低的热膨胀系数,根据以上设计微晶玻璃组成的原则,目的在于如何保证残余玻璃相的组成能够将热膨胀的不匹配降至最低限度。
虽然晶相的种类和含量多少是决定微晶玻璃热膨胀系数的主要因素,但也不应忽视残余玻璃相对热膨胀系数的影响。在某种情况下,残余玻璃相的热膨胀系数足以抵消所形成的晶相的影响,从而使微晶玻璃和其原始玻璃具有相近的热膨胀系数。计算微晶玻璃热膨胀系数α的方程式如式(4-7):
++
++=
2
2
21
1
12
2
221111ρρραρααF K F K F K F K (4-7)
式中α1,α2,…――复合材料中各相的热膨胀系数;
K 1,K 2,…――复合材料中各相的体积弹性模量; F 1,F 2,…――复合材料中各组分的质量分数。
如果泊松比都是相同的,则可用弹性模量代替体积弹性模量。当每个组分的压缩等同于总的压缩以及所有的微应力都是流体静力学的拉应力或压应力时这个方程式就假定为理想的行为。
已知晶相的体积分数及其物理性质,就能计算出微晶玻璃的热膨胀系数。困难的是要对残余玻璃相性质的变化作出恰当的估计。如果能根据电子显微镜或定量X 衍射分析较准确地知道晶相地体积分数,则可计算出残余玻璃相地组成。
表4-9列出了几种常见微晶玻璃材料中晶相的热膨胀系数。要使其中晶相的膨胀系数与剩余玻璃相的膨胀系数相同是不太可能的。例如,在零膨胀微晶玻璃中,晶相的膨胀系数大多时负的,而玻璃相为正向膨胀,因此两者间的膨胀系数差别不是很大时,可以获得抗热冲击性良好的微晶玻璃。
-7-1
由表4-9晶相的热膨胀系数的变化范围非常广泛。根据这种特性,可以通过设计微晶玻璃化学组成,控制其热处理制度,从而获得所需要的低膨胀或高膨胀系数的微晶玻璃材料。
如果一种晶相和另外一种晶相形成了固溶体,则微晶玻璃的热膨胀系数也随之发生变化。β-锂霞石和β-锂辉石可以形成一系列固溶体,其膨胀系数就处于这两相之间。当β-锂辉石中的Li 2O 、Al 2O 3及
SiO 2的摩尔比为1:1:4时,也能和SiO 2形成固溶体。纯β-锂辉石的热膨胀系数为9×10-7℃-1
(25~
100℃),其1:1:6的固溶体的热膨胀系数却为5×10-7℃-1
(25~100℃),其1:1:8的固溶体的热膨胀
系数为3×10-7℃-1(25~100℃),其1:1:10的固溶体的热膨胀系数则为5×10-7℃-1(25~100℃)。
从表4-9还可知,SiO2晶相热膨胀系数的大小与其测试温度范围紧密相关。因为,在特定温度时SiO2晶体会发生晶相发生转变,并伴随着热膨胀系数的变化。
当特定晶相的体积分数不同时,即使微晶玻璃含有相同的晶相,也可能具有不同的热膨胀系数。因此当设计具有特定热膨胀系数的微晶玻璃时,就不仅仅是改变晶体的类型,而且也要改变其比例,以获得所需要的性能。
在Li2O-ZnO-Al2O3-SiO2系统微晶玻璃中,用ZnO替换Al2O3,开始对膨胀系数只有较小的影响,但在ZnO的摩尔分数大约等于Al2O3时,膨胀系数急剧增加,当ZnO再增加时其膨胀曲线又变得较缓慢了(如图4-8所示)。其原因是该系统微晶玻璃中出现了晶相的变化。当ZnO比Al2O3少时,其主晶相为β-锂辉石与SiO2的固溶体;但当ZnO的含量超过Al2O3时,则由高膨胀的石英晶相取而代之。随着ZnO含量的继续增加,其热膨胀系数也持续增加。
图4-8说明了一个重要的问题,即当该系统微晶玻璃组成处与ZnO与Al2O3的物质的量比大约等于1区域时,其组成稍有变化,就会造成热膨胀系数发生剧烈改变。因此,从实际应用上看,这样的组成不适于制备可控热膨胀系数的微晶玻璃制品。而远离这个区域的任何组成都可制得可控膨胀系数的微晶玻璃材料。因此,玻璃组成的设计原则就是应避免因组成的微小波动就导致晶相的巨大变化,从而使其物理性质发生改变。
4.3.1.2热处理制度对热膨胀性能的影响
微晶玻璃的热膨胀性能可以受到热处理制度的显著影响,因为它能决定其中晶相的种类和含量。这一事实可由图4-9的曲线B和D加以明确的说明。这两种微晶玻璃都是从相同组成的原始玻璃制得,所以它们在化学成分上是相同的,不过一种是把热处理制度调整到使所有形成的晶体二氧化硅都为方石英(曲线B),而曲线D则使所有的二氧化硅都呈石英的状态。因此,改变热处理过程就可以从同一基础玻璃中制得含有不同比例的石英和方石英复合晶相的微晶玻璃。
改变热处理制度也可以使晶相的体积分数发生变化,其结果也将影响微晶玻璃的热膨胀系数。表4-10中反映的是热处理制度对Li2O-Al2O3-SiO2系统微晶玻璃的热膨胀系数的影响。由表4-10可知,随着热处理温度的升高,微晶玻璃的热膨胀系数增大。β-石英的晶体是由大量〔SiO4〕四面体连接而成的比较开放的六方螺旋结构,其膨胀系数为-5×10-7℃-1左右。当β-石英中的Si4+有规则地用Li+与Al3+取代时,便生成具有不同成分和性质的β-石英固溶体,此时,Al3+位于Si4+的格点位置,Li+填充于Al3+附近的构架空隙中使电性达到中和。其中比较稳定的是半数的Si4+被取代,即生成锂霞石晶体(Li2O·Al2O3·2SiO4)。
表4-10 不同热处理制度所对应微晶玻璃的热膨胀系数和晶相
旋所指的方向(c轴方向)膨胀系数是负值,其他方向都是正值。当微晶玻璃中晶粒尺寸很小时,其总膨胀值呈现负值。β-石英固溶体可以从含Li2O-Al2O3-SiO2组成的原始玻璃中经过适当热处理以微晶状态析出,其微晶玻璃含有β-石英固溶体和残余玻璃相近似相等的体积分数,前者的负膨胀和后者的正膨胀相抵消,就得到膨胀系数为零或接近于零的微晶玻璃。β-锂辉石(LAS4)是由LAS3中Li+与Al3+进一步取代Si4+而形成的。由于LAS3是由β-石英和β-锂霞石形成的固溶体,相对于LAS4而言,其晶粒细小,析晶密集,其热膨胀系数较低,因此含LAS3固溶体多的微晶玻璃,具有较低的热膨胀系数,如图4-10(a)所示,其热处理制度为:核化温度580℃,保温2h;晶化温度800℃,保温2h。图4-10,(b)样品的热处理制度为:核化温度580℃,保温2h;晶化温度910℃,保温2h。其主晶相为β-锂辉石。从图中可明显看出,β-锂辉石晶粒较大,结构疏松,因而呈现较高的热膨胀系数。
4.3.1.3抗热冲击性能(抗热震性)
抗热冲击性能是指一种材料能耐温度急变而不破坏的能力。通常根据材料急速冷却而不破裂的最大温度间隔加以说明。一般来说,材料耐急剧冷却比耐急剧加热更重要。因为前者造成材料断裂的可能性更大,但在特殊情况下也有必要了解材料耐急剧加热的能力。
抗热冲击试验必须在严格按标准规定的条件下进行,因为试样的形状可以显著影响材料的抗热冲击能力。此外,所用的冷却介质也很重要,因为它影响从试件表面带走热量的速度。常用抗热冲击试验方法是将具有各种已知温度的试样投入具有标准温度和流速的水浴中急冷。
急剧加热或冷却所产生的应力值高于材料在稳定状态下的应力,因为最初的温差只出现在表面层,突然加热使材料表面产生压应力,而突然冷却却使材料表面产生拉应力,材料抗拉断裂的可能性更大,而且一旦所产生的应力值超过材料的破坏应力,则材料就会发生破裂。
材料的表面应力可由式(4-8)计算:)]1(2/[υασ-?=T E (4-8)
式中 ζ――材料的表面应力(压应力或拉应力);
?T ――材料表面的温差; α――线热膨胀系数; υ――泊松比。
假设沿着试样高度方向存在一个均匀的温度差,显然材料的实际温差将取决于厚度及其热导率。 除了机械强度和弹性模量以外,热膨胀系数对于材料的抗热冲击性能也是一个重要的影响因素。在低的热膨胀系数下,微晶玻璃具有良好的抗热冲击性能和较大的强度。另外,由于玻璃相含量较少时,在晶粒之间存在较多的微气孔,这样材料在受热时,有一定的空间进行结构调整,在宏观性能上表现为热膨胀系数较低,因而抗热冲击性能较好。
从以上讨论可知,决定微晶玻璃抗热冲击的重要因素是它的弹性模量、热膨胀系数及机械强度。与普通玻璃及陶瓷相比,微晶玻璃具有更高的机械强度,因此,具有更好的抗热冲击性能。此外,微晶玻璃可以具有很低的热膨胀系数,使得其抗热冲击性能更为优异。以β-锂辉石、β-锂霞石或β-石英固溶体为
主晶相,具有热膨胀系数为5×10-7~10×10-7℃-1
的微晶玻璃可以从700℃左右的温度急冷到0℃的冰水中而不破裂。例如,规格为600mm ×600mm ×5mm 的微晶玻璃盘,以β-锂辉石为主晶相,热膨胀系数为3.3
×10-7℃-1
(25~700℃),就可以从700℃冷却到0℃而不破坏。高强度和第低的热膨胀系数以及较低的弹性模量使得微晶玻璃具有高的抗热冲击性,最大可高达1100℃。
几种微晶玻璃与钠钙硅普通玻璃的热冲击性能的比较,如表4-11所示。试验是把各种温度的棒状试样投入到20℃的水中急冷。用急冷的棒状试样进行机械强度测试。因热冲击而造成的明显微裂纹使材料的强度降低,从表中可以看出热膨胀系数在决定微晶玻璃的抗热冲击性方面使重要的影响因素。
表4-11 微晶玻璃与钠钙硅酸盐玻璃的热冲击性能比较
4.3.2比热容和热导率
材料的比热容是指单位质量的物质温升1K 或温降1K 所吸收或放出的热量,用符号c (J ·kg -1·K -1)
来表示。dt
dQ m C ?=
1 (4-9) 式中 m ――物体的质量;
dQ ――吸收或放出的热量; dt ――升高或降低的温度。
微晶玻璃材料的比热容几乎不随成分的改变而改变;从20~400℃温度间的平均比热容为1000J ·kg -1
·K
-1。与玻璃和陶瓷的比热容相比,并没有太大的差别,且随着温度的升高而增大。
微晶玻璃材料被用作热导体或是绝缘体时,热导率就成为一个很重要的参数。相对玻璃而言,微晶玻璃有较高的热导率,但比纯氧化物陶瓷的热导率小得多。表4-12给出了几种材料的热导率。
表4-12 几种材料的热导率单位:W·m-1·K-1
4.3.3热稳定性和机械应力变形
在实际应用中,微晶玻璃受热而不发生变形的温度值是非常重要的一个参数。要想在高温下使用微晶玻璃材料,就必须要了解它们能承受多高的温度而不发生变形。微晶玻璃中的结晶相和残余玻璃相的种类和含量影响着这种变形,因为当晶相呈现相当高的熔化温度时,则玻璃相就对材料的热稳定性产生决定性的影响。因此,通过限制玻璃相的含量来提高玻璃的抗热震性能是十分有效的。荷重软化温度可以通过热膨胀仪测定膨胀软化点来确定。通常,这种变形时的温度是由材料加热的速率和机械应力的类型及大小决定的。
变形随着温度的升高而增大,这方面的数据和理论对于材料的实用性是非常重要的。变形的程度可以通过对不同的机械应力进行测量来获得。微晶玻璃材料的变形速率常常由玻璃相的黏性流动决定。
图4-11给出了Li2O-SiO2微晶玻璃在不同温度下荷载形变速率。图4-12给出了在实际应用中不同微晶玻璃材料的温度和变形量的曲线图。所用微晶玻璃的相关性质及其晶化温度和主晶相如表4-13所示。
注:Li2O-Al2O3-SiO2系统的实验组分有两种,即图4-12中B1和B2。
4.4电学性质
4.4.1电阻率
微晶玻璃具有很高的电阻系数,因此一直可用作绝缘材料。一般来说,微晶玻璃与普通陶瓷和陶瓷相比,是良好的电绝缘材料。如即使在700℃高温下,Li2O-Al2O3-SiO2系统微晶玻璃的电阻率也很高。玻璃和陶瓷的电导率依赖于自身所含的几种不同类型的可迁移的离子,其中主要是碱金属离子,随着碱金属离子含量的增加其电导率也跟着增加。对于微晶玻璃来说,碱金属离子也是其电阻率的主要影响因素。离子的迁移能力决定于离子所在的结构。
玻璃析晶时,在晶相中结合了碱金属氧化物,因此降低了微晶玻璃的电导率。例如,在700℃温度下,Li2O-ZnO-SiO2系统微晶玻璃材料单位面积内的表面电阻率是107.3Ω·m,而原始玻璃的表面电阻率为102.4Ω·m。因此,一般情况下,微晶玻璃具有比原始玻璃高得多的电阻率。虽然有些玻璃、陶瓷以及微晶玻璃的导电涉及到电子或空穴的迁移过程,因而可被作为半导体材料,但是大多数微晶玻璃是离子导体,本节主要讨论这样的导电过程。
表4-142232232
电阻率的比较。随着温度的增加,电阻率降低,而电导率则正好相反。ZnO-Al2O3-SiO2系统微晶玻璃在掺入B2O3、BaO、CaO后,除了具有高的电阻率,还呈现几乎和硅相同的热膨胀系数,32×10-7~39×10-7℃-1(20~500℃)。因此,它们可以与硅片一起被用来制备半导体材料。
4.4.1.1热处理温度对电阻率的影响
在热处理过程中,对Na2O-Al2O3-SiO2系统微晶玻璃电阻率影响的研究中,测得霞石微晶玻璃试样的电阻率随热除颗粒温度变化的规律如图4-13和图4-14所示。从图4-13可以看出,霞石微晶玻璃试样的电阻率在T1=700℃左右热处理时,存在一个极大值区间。这是因为,核化温度低于700℃时,生成的霞石晶核数量不足,经晶体长大后,试样的结晶比例较低,电阻率较小;而晶核形成温度超过700℃左右时,则生成过多、过密的霞石晶核,致使晶化热处理后,晶相密集,在外电场的作用下,晶格振动频率加快,Na+迁移时,两势垒间距减小,电阻率下降。图4-14的曲线说明,维持晶核生成温度T1为700℃不变,晶体长大的温度T2从850℃变化到880℃,霞石微晶玻璃试样的电阻率也在860℃热处理时存在一最大值区间。究其原因,主要是晶体长大程度以及晶体粒径的影响。T2低于860℃时,晶体长大不充分,晶粒过于细小,试样的最终晶相含量低,电阻率降低;而温度高于860℃时,晶粒生长过大,晶粒间的架桥作用使试样程度变差,Na+迁移的阻力减小,电阻率也降低。
4.4.1.2热处理时间与电阻率的关系
由于微晶玻璃热处理时间的长短直接影响试样微晶化程度,因而也与试样的电阻率有关。保持核化、晶化热处理的温度不变,分别为T1=700℃和T2=860℃,同时保证热处理过程中升温速率不变,改变两段式热处理温度(T1和T2)下的保温时间,分别得到图4-15和图4-16所示的热处理时间η1和η2与霞石微晶玻璃电阻率的关系。
在核化温度T1下,试样的保温时间η1较小时,显然晶核生成的数量不够,而η1较大则又生成过于密集的晶核,这都不利于第二段热处理时晶体长大,故试样的电阻率都较小(如图4-15所示)。同样,在晶化温度T2下,保温时间η2较小时,晶核没有充分长大,试样的析晶比例低;而η2过长则由于晶体尺寸过大,破坏了试样结构的有序性,使材料的导电性反而增加,电阻率下降(如图4-16所示)。
4.4.2介电常数、介电损耗和介电强度
4.4.2.1介电常数
介电常数是指在介电材料中和在真空中建起的两个电场的电能比率。许多微晶玻璃在室温下的介电常数处于5~6之间,且这些数量不太受测试时频率的影响。在低频下,介电常数随温度(150℃以前)的升高而缓慢加大;在高频下,温度升高到400~500℃,介电常数几乎没有受到影响。
如果材料用作高频绝缘体,则要求材料具有低的介电常数和低的介电损耗(功率因数),且其介电常数随温度的升高变化越小越好。
在低频下,介电常数的加大,是和离子的迁移率以及晶体的缺陷迁移率的增加有关;并且在高温下,直流电导作用也增强了;这两者共同作用造成介电常数急剧增加。
对于大多数的微晶玻璃材料来说,晶相和残余玻璃相的介电常数值是非常接近的。所以玻璃相的体积分数对微晶玻璃材料的介电常数值影响很小。如果微晶玻璃所含的晶相具有高的介电常数,例如钛酸钡,那么玻璃相的体积分数将影响最终的介电常数值。因此,可以通过减少残余玻璃相的体积分数来获得具有高介电常数的微晶玻璃材料。
以堇青石(2MgO·2Al2O3·5SiO2)为主晶相的微晶玻璃为例。其耐热性高及电绝缘性好,高频损耗小。但这种微晶玻璃在高频(>1GHz)下的介电常数却较低(ε=5.0~5.5)。从图4-17中可知,主晶相α-堇青石(MAS)和镁铝钛酸盐(MAT)的比例量影响材料的介电常数。随镁铝钛酸盐相对比例的增加,材料的
介电常数呈上升的趋势。众所周知,α-堇青石具有较低的介电常数,而富钛的晶相如钛酸镁、钛酸铝等介电常数均大于α-堇青石。在具有多晶相组成的微晶玻璃中,其介电常数取决于各晶相的介电常数和它们所占的体积百分数。所以,其介电常数增加的原因是因为具有较高介电常数的晶相(MAT)含量的增加。
另外,样品在同一温度、保温不同时间下,进行热处理,观察晶粒发育状况与介电性能的关系。保温不同时间微晶玻璃样品的SEM照片见图4-18,从图4-18中可看出保温时间短的样品中晶粒较小,晶粒之间孔隙较多〔如图4-18(a)所示〕;保温时间较长的样品晶粒较大,晶粒之间孔隙较少〔如图(b)所示〕。在介电性能方面,保温时间长的样品介电常数略高于保温时间短的样品。
4.4.2.2介电损耗
如果在电介质中建立起一个电场,则在此材料中就储存了电能,当去掉电场后,电能完全回复。但是通常只有部分能量可以恢复,失掉的那部分电能就表现为热。所以在一个交流电场中,绝缘材料就出现了电能损耗。电能的不能恢复部分和可恢复部分的比率,用介电损耗角正切(tanδ)来表示。介电损耗是和材料的电容率或介电常数ε相关的,并且介电损耗因数是介电常数和介电损耗角正切的乘积,即ε·tanδ。如果绝缘材料用于高频绝缘,则低的介电损耗是最重要得。为此tanδ和ε都不应该随着温度的变化而发生明显变化。
介电损耗包括电导损耗、离子迁移损耗、变形和振动损耗等。在频率低于1MHz时,电导和离子迁移损耗就显得很重要;而在频率大约为10MHz左右时,其他两种形式的损耗占主要地位。电导损耗和离子迁移损耗主要决定于碱金属离子的浓度和迁移能力。据此推测,在低的频率下,碱金属离子在残余玻璃相中有很高的活动性,在晶相中这种离子则对介电损耗的影响较小。
因此,玻璃中易活动的离子是造成中范围内介电损耗的主要原因。介电损耗依金属离子的迁移率顺序而加大:Rb+→K+→Na+→Li+。
介电损耗也受到占据玻璃网络结构间隙位置的其他调整阳离子的影响,像钡和铅这样的半径较大的离子,能有效地减少玻璃的介电损耗,因为它们可以阻碍碱金属离子的迁移。微晶玻璃的情况比玻璃更为复杂,难以准确说明结晶相和残余玻璃相的确切作用。但单晶的介电损耗小,因此可以认为玻璃相是造成微晶玻璃中介电损耗的主要原因,所以要达到低的介电损耗,残余玻璃相的含量应尽可能少,并且其组成还必须进行控制,使其中碱金属离子的量减少。微晶玻璃的介电损耗和玻璃的一样,除了化学组成外,也和测试时的频率及温度有关。通常是随着温度的提高介电损耗加大。
当碱金属离子结合到晶相中时,其功率因数随着玻璃的晶化而显著减少。锂铝硅酸盐微晶玻璃中,主晶相为二硅酸锂,锂离子被结合到这个晶体中,使其迁移率减少,从而降低了该材料的介电损耗。如果易活动的碱金属离子(如Na+)没有参与晶相组成,而是富集在残余玻璃相中,就会使微晶玻璃具有高的介电损耗。
表4-15列出了几种类型微晶玻璃和其他材料在1MHz及20℃的介电常数及介电损耗的比较。从中可以看出,在所用的测试频率下,微晶玻璃的损耗因数和低损耗陶瓷相比是有利的。含有碱金属离子微晶玻璃的介电损耗,对频率有显著的依赖性。由于锂离子的活动性,所有微晶玻璃材料在低频时都具有较高的介电损耗。但含铅的微晶玻璃在非常广的频率范围内表现出低的介电损耗,其原因是因为玻璃相中存在不易活动的铅离子。
表4-15 材料在1MHz及20℃时的介电常数和介电损耗
注:介电损耗因数=介电损耗角正切×介电常数。
值得注意的是介电损耗因数随着频率的变化主要是功率因数的变化,而介电常数与频率的关系不大。
微晶玻璃的显微结构,特别是晶相的平均尺寸及体积分数对介电损耗影响方面的研究结果表明,晶体
尺寸对介电损耗的影响不大。但晶相种类不同,介电损耗差别很大。如含有大量β-锂辉石的微晶玻璃具有较高的介电损耗,而在频率为1MHz时,β-锂辉石的损耗角正切值却比β-锂辉石的大9倍,说明含有β-锂辉石的微晶玻璃具有更高的介电损耗。如前所述,晶相的体积分数对介电损耗来说是一个重要因素,因为它决定了残余玻璃相的数量和组成。
虽然微晶玻璃的介电损耗机理通常和离子的迁移有关,但在特殊情况下,其他过程也是很重要的。如含20%TiO2的微晶玻璃,其未晶化玻璃在频率为1MHz时损耗角正切值小于20×10-4,而晶化后的微晶玻璃具有极高的损耗角正切角,约为3000×10-4。其原因是微晶玻璃中的钛酸盐晶体的缺氧所引起的非化学计量形式的半导性。另外钛酸盐晶体与三价离子结合后,会使其导电性能减弱。如在其中引入很少量的氧化铬或氧化铁,其损耗正切值会大大减少。因此微晶玻璃有可能形成非化学计量晶体时,就必须仔细控制原始玻璃的氧化状态。
4.4.2.3介电强度
如果绝缘材料承受较大的电压差,则这种材料可能会因击穿而被破坏。这种破坏几率是控制高压绝缘体设计的重要因素。当微晶玻璃材料用于高电压时,例如,用作高电压的绝缘体和电容器,其介电的击穿强度就显得很重要。和普通陶瓷相比,微晶玻璃材料具有很高的介电击穿强度,这是因为微晶玻璃具有非常均匀的细晶致密结构。
绝缘材料的介电击穿有两种方式,第一为本征介电击穿,起源于电子;第二为热击穿,由于电导引起局部过热的结果。这种局部导电增加到一定程度时,就会产生介电击穿。实际上很难区分这两种作用,而且即使是使用精密的测试方法,其所得的数值也未必能达到材料的实际强度。除此之外,所测得的实验数据还取决于测试条件,诸如电极的尺寸与形状、承受电应力的材料厚度、施加电压的速度以及施加电压的延续时间等都可能影响所测得的数值。如果击穿强度是在交流电下测定的,那么频率还会对其产生显著的影响,因为在高频下对应低的击穿强度。因此,必须规定测试条件,以及必须使用标准试样。表4-16给出了在50MHz及20℃时的介质击穿强度。
4.4.3铁电性和铁磁性
目前已能从经过适当热处理的原始玻璃中析出铁电相,从而制得具有高介电常数、低功率因数、高介电强度及良好的绝缘性能的微晶玻璃。其晶相主要是钙钛矿型,它的通用分子式为ABO3。A离子选自周期表中的Ⅰ~Ⅲ族,B离子选自Ⅱ~Ⅴ族。
钛酸盐、铌酸盐和锆酸盐以及钽酸盐、铣酸盐等晶相就是这类重要的铁电化合物。这些铁电化合物中的氧化物组分不能形成玻璃,因此其组成中必须含有能形成玻璃的氧化物,以便能进行后期的控制晶化热处理。但形成玻璃的氧化物应尽可能少,以避免稀释铁电相。
表4-17中列出了含有铁电相微晶玻璃的性能,图4-19为钛酸钡微晶玻璃的晶粒尺寸及温度对其介电常数的影响。从图中可以看出,该铁电微晶玻璃与一般微晶玻璃不同,其介电常数随着晶粒尺寸的增大而增加,并且在晶粒尺寸为0.2μm时其介电常数-温度曲线上的波峰没有了,该峰为铁电-反铁电的转变处。铁电相的体积分数也是影响介电常数的一个重要因素,其体积分数为60%~80%时,微晶玻璃的介电常数约为纯晶体介电常数的1/3~1/2.
表4-17 含有铁电相微晶玻璃的性能
形成鲜明的对比。这些晶体的铁电性能使其产生双折射或散射现象,使得这种材料在电信领域中的光转换器件或滤波器方面是非常有用的,对于具有很高的信息记录密度的光存储计算机来说也是如此。
如果玻璃组成中包含过渡金属或稀土氧化物,那么这些系统就会产生具有磁性的铁氧体晶相、石榴石或磁铁铅矿晶相。如果这种材料有一个窄的微晶尺寸分布曲线,那么磁化所需要的能量几乎和所有的晶体相同;由于这种微晶玻璃具有高的电阻率,所以可以应用在高频技术上。这种情况可以通过在玻璃基体中析出结晶相来实现,当然也限制了磁性相的大量产生。如果磁性晶体粒子的尺寸减小到临界值以下,那么,磁性将不再产生,而这种现象对于制备强磁性材料是很有用的。
4.5化学性能
微晶玻璃的化学稳定性和耐久性受结晶相组成的影响,也受到残余玻璃相的组分和数量以及两相形貌的影响。碱金属离子在晶相中比在残余玻璃相中稳定。因此,当微晶玻璃材料与水接触时,碱金属离子在水的作用下很快从玻璃相中迁移出来。为了使微晶玻璃材料具有良好的化学稳定性,就必须使残余玻璃相中不含有大量的碱金属氧化物。
图4-20为Na2O-BaO-SiO2系统微晶玻璃相图。图中点划线是表示亚稳液相从高硅分离的分界线,残余玻璃相的化学组成受到热处理特别是受到原始玻璃组成的影响。在Na2O-BaO-SiO2系统中,改变原始玻璃组成会影响到微晶玻璃材料的化学稳定性,从热处理过程中,晶相BaO·2SiO2依赖于原始组成就可以体现出来。如果初始组成A选择亚稳的不混溶区,热处理过程首先伴随着分相,即形成组成B和C两种液相。BaO·2SiO2结晶仅发生在含硅低的液相B中。当剩余玻璃相组成开始向D移动时,在亚稳不混溶区外,这种析晶可发生在富含硅的玻璃相C中,在剩余玻璃相中,D能向富含SiO2的E点移动。此时虽然剩余玻璃相中相对含SiO2较高,仍然可以保证最终结晶产物具有良好的化学稳定性。然而当初始组成选择F点时,在析晶结束后,BaO·2SiO2晶相总量达到50%,则由二硅酸钠(Na2O·2SiO2)形成的剩余玻璃相就可以在水中发生溶解。多相产物因此分解成很细的BaO·2SiO2粉末。初始组成G的重要意义在于BaO·2SiO2晶体的分解,结果使剩余玻璃相组成点向玻璃形成系统的边界移动,因此剩余玻璃相不再形成而逐渐发生结晶,这已通过实验得到证明。分解相主要由二硅酸钠结晶构成,它可以在空气中受潮发生反应,因此该产物在空气中是很不稳定的。
总的来说,大部分的微晶玻璃材料表现出足够高的化学稳定性。典型的例子是以β-石英固溶体为主晶相的微晶玻璃的化学稳定性与硼硅酸盐玻璃的化学稳定性相当。
4.6光学性能
玻璃最重要的光学性能是透射和辐射能力。而有相当一部分微晶玻璃材料是不透明或具有花岗岩、大理石花纹(白色或彩色),但也有一部分微晶玻璃具有半透明、透明或是透过红外辐射的特性。光线通过透明微晶玻璃时,主要受到其晶体尺寸的影响。如果晶体尺寸小于可见光波长(λ<0.4μm),微晶玻璃材料就是透明的。其他影响光线通过的因素是光学非均匀性,以及在玻璃相和晶相之间不同的折射率。即使晶体尺寸大于光的波长,假若折射率很小甚至接近于零,且在单晶体相中的双折射率也很小时,材料也可以透明。
透明微晶玻璃已在多种系统中制备出来,其中最重要的有以β-石英固溶体为主晶相的(Li2O,MgO)-Al2O3-SiO2系统、以莫来石为晶体的Al2O3-SiO2系统、以尖晶石(MgO·Al2O3,ZnO·Al2O3)为主晶相的(MgO,ZnO)-Al2O3-SiO2系统。透明微晶玻璃材料包括Kokubo和Tashiro提出的以钛酸铅为晶相的铁电物质具有很高的介电常数,从而具有电光学性能。当通电时,这种材料可以旋转偏振面,从而让极化的光束通过。
近年来以BaCO3、H3BO3为原料,经高温熔融及控制热处理,获得了BaO-B2O3透明微晶玻璃。在玻璃表面得到了含有单一β-BaB2O4(BBO)晶体结构的析晶薄膜层,薄膜表面均匀,单膜厚度约为2μm,晶粒平均约为0.2μm,且晶粒沿α轴方向优先生长。析晶优先从玻璃表面开始向内部进行,形成晶化层-玻璃-晶化层的三元“夹心”结构,该微晶玻璃具有良好的光学性能。
透明微晶玻璃、黑色微晶玻璃、耐高温微晶玻璃
透明微晶玻璃、黑色微晶玻璃、耐高温微晶玻璃 耐高温玻璃——透明微晶玻璃、黑色微晶玻璃(英文名Glass Ceramic,也称玻璃陶瓷) 材料提供:国产微晶玻璃,常规最大尺寸350*450*4mm,也可以选择进口微晶玻璃,常规最大尺寸1954*1100,2100*1266,厚度4\5。 透明微晶玻璃介绍: 由于其极低的热膨胀度,透明微晶玻璃不会受高温(760℃)的影响,也不受显著温度变化或温度差异的影响,且十分优越的耐热冲击性能。另外,透明微晶玻璃具有良好的热辐射,特别是短波红外辐射透过性。而正是在为火炉燃烧过程中释放的强烈热辐射为我们带了舒适暖意。 因此,微晶玻璃特别知合应用在既有高热能又需要良好透光性的场合,作为室内加热装置(如壁炉和火炉)的观察窗。 图 1 透明微晶玻璃 150 999 63668
产品应用: ?室内加热/取暖器的视窗面板(燃油/燃气室内取暖器/炉、传 统燃料的室内取暖器/炉) ?红外辐射加热/取暖器的面板 ?加热电暖炉的盖板玻璃 ?反光杯和高性能泛光照明灯的盖板 ?红外烘干器的盖板 ?投影仪的保护盖片 ?隔紫外线护罩 ?烤肉/烧烤设备的面板 ?大功率泛光灯和反射器上耐高温的面板 加工:①切割、②倒角、③钻孔、④丝印、⑤镀膜 黑色微晶玻璃面板说明: 由特殊微晶玻璃制成,该材料的最大特点是:可耐高达750℃的急剧升温。微晶玻璃面板非常环保,不含砷、锑等有毒重金属。它的主要原料是石英,这种原料在自然界取之不尽、用之不竭。 黑色微晶玻璃灶具面板非常坚固、耐受冲击,经久耐用。灶具面板横向热传导低,靠近烹调区的地方温度相对较低,热量会直接传导至烹饪锅具。 图 2 黑色微晶玻璃 150 999 63668
商用电磁炉为什么要用微晶玻璃
商用电磁炉为什么要用微晶玻璃 目前大部分的商用电磁炉,都需要用到微晶玻璃,微晶玻璃对于商用电磁炉又有什么特别作用呢? 微晶玻璃又称微晶玉石或陶瓷玻璃。主要应用在商用电磁炉,大功率电磁炉等产品上面。是综合玻璃,它的学名叫做玻璃陶瓷。将加有晶核剂的特定组合的玻璃,在有控条件(一定温度)下进行晶化处理,成为具有微晶体和玻璃相均匀分布的复合材料。 微晶玻璃和我们常见的玻璃看起来大不相同。它具有玻璃和陶瓷的双重特性,普通玻璃内部的原子排列是没有规则的,这也是玻璃易碎的原因之一。而微晶玻璃象陶瓷一样,由晶体组成,也就是说,它的原子排列是有规律的。所以说,微晶玻璃比陶瓷的亮度高,比玻璃韧性强。 商用电磁灶面板采用微晶玻璃的主要原因是:微晶玻璃性能机械强度高,绝缘性能优良,介电损耗少,介电常数稳定,热膨胀系数可在很大范围调节,耐化学腐蚀,耐磨,热稳定性好,使用温度高。平面微晶玻璃目前广泛应用到商用电磁炉上,凹面微晶玻璃即是指形状呈凹型,类似锅的现状的微晶玻璃。该微晶玻璃板主要用途目前以大功率商用电磁炉上用为主。 随着煤气,物价的上升,饮食行业的成本骤增,以及人们对无明火烹饪的理解,商用炉灶用户的增加。凹型微晶玻璃需求也会相应增加。常用厚度12~20mm 商用炉灶采用的平面微晶玻璃板常规尺寸为:250×250mm、300×300mm、350×350mm、450×450mm、500×500mm、600×600mm等。商用电磁炉采用的凹面微晶玻璃常规尺寸为:直径200mm、直径300mm、直径400mm、直径500mm等。 微晶玻璃原来有这么大的不同,您知道了吗?对于商用电磁炉产品上面有任何疑问,您可以在沁鑫商用电磁炉官网咨询: 沁鑫官网:https://www.360docs.net/doc/8f11434823.html, 阿里巴巴官网:https://https://www.360docs.net/doc/8f11434823.html,
微晶玻璃
微晶玻璃 摘要:本文介绍了微晶玻璃与普通玻璃和陶瓷的区别,通过分析组成将其分类。 同时描述了微晶玻璃的制备,性质,应用,浅析其发展趋势。 关键词:微晶玻璃组成制备性能应用 Abstract:This paper introduces the difference between microcrystalline glass and common glass and ceramics. Through the analysis of composition classified microcrystalline glass. At the same time, also describe microcrystalline glass’s preparation, property and application. Analysisthe trend of its development. Keywords: Microcrystalline glass preparation property application trend 1 前言 微晶玻璃又称微晶玉石或陶瓷玻璃,是综合玻璃,是一种外国刚刚开发的新型的建筑材料,它的学名叫做玻璃水晶。微晶玻璃和我们常见的玻璃看起来大不相同。它具有玻璃和陶瓷的双重特性,普通玻璃内部的原子排列是没有规则的,这也是玻璃易碎的原因之一。而微晶玻璃象陶瓷一样,由晶体组成,也就是说,它的原子排列是有规律的。所以,微晶玻璃比陶瓷的亮度高,比玻璃韧性强。但晶玻璃既不同于陶瓷,也不同于玻璃。微晶玻璃与陶瓷的不同之处是:玻璃微晶化过程中的晶相是从单一均匀玻璃相或已产生相分离的区域,通过成核和晶体生长而产生的致密材料;而陶瓷材料中的晶相,除了通过固相反应出现的重结晶或新晶相以外,大部分是在制备陶瓷时通过组分直接引入的[1]。微晶玻璃与玻璃的不同之处在于微晶玻璃是微晶体(尺寸为0.1~0.5μm)和残余玻璃组成的复相材料;而玻璃则是非晶态或无定形体。另外微晶玻璃可以是透明的或呈各种花纹和颜色的非透明体,而玻璃一般是各种颜色、透光率各异的透明体。 2分类及其组成 目前,问世的微晶玻璃种类繁多,分类方法也有所不同。通常按微晶化原理分为光敏微晶玻璃和热敏微晶玻璃;按基础玻璃的组成分为硅酸盐系统、铝硅酸盐系统、硼硅酸盐系统、硼酸盐和磷酸盐系统;按所用原料分为技术微晶玻璃(用一般的玻璃原料)和矿渣微晶玻璃(用工矿业废渣等为原料);按外观分为透明微晶玻璃和不透明微晶玻璃;按性能又可分为耐高温、耐腐蚀、耐热冲击、高强度、低膨胀、零膨胀、低介电损耗、易机械加工以及易化学蚀刻等微晶玻璃以及压电微晶玻璃、生物微晶玻璃等 晶玻璃的组成在很大程度上决定其结构和性能。按照化学组成微晶玻璃主要分为四类:硅酸盐微晶玻璃,铝硅酸盐微晶玻璃,氟硅酸盐微晶玻璃,磷酸盐微晶玻璃。 2.1 硅酸盐微晶玻璃 简单硅酸盐微晶玻璃主要由碱金属和碱土金属的硅酸盐晶相组成,这些晶相的性能也决定了微晶玻璃的性能。研究最早的光敏微晶玻璃和矿渣微晶玻璃属于 这类微晶玻璃。光敏微晶玻璃中析出的主要晶相为二硅酸锂(Li 2Si 2 O 5 ),这种晶 体具有沿某些晶面或晶格方向生长而成的树枝状形貌,实质上是一种骨架结构。
微晶石各项指标
微晶石是新型的装饰建筑材料,其中复合微晶石称为微晶玻璃复合板材,是将一层3—5mm的微晶玻璃复合在陶瓷玻化石的表面,经二次烧结后完全融为一体的高科技产品。微晶石厚度在13—18mm,光泽度大于95。 特点 质感 微晶石是在与花岗岩形成条件类似的高温下,经烧结晶化而成的材料。在外观质感方面,其抛光板的表面光洁度远高于石材(光度可达90-120光泽度单位),更重要的特点是,其特殊的微晶结构,使得光线无论从任何角度射入,经过精细微晶微粒的漫反射,都能将光线均匀分布到任何角度(而不再是像镜面那样仅仅是集中在反射角度),使板材形成柔和的玉质感,比天然石材更为晶莹柔润,使建筑更加流光溢彩。 性能 比天然石更具理化优势:微晶石是在与花岗岩形成条件相似的高温状态下,通过特殊的工艺烧结而成,质地均匀,密度大、硬度高,抗压、抗弯、耐冲击等性能优于天然石材,经久耐磨,不易受损,更没有天然石材常见的细碎裂纹。 质地 板面光泽晶莹柔和:微晶石既有特殊的微晶结构,又有特殊的玻璃基质结构,质地细腻,板面晶莹亮丽,对于射入光线能产生扩散漫反射效果,使人感觉柔美和谐。 色彩 微晶石的制作工艺,可以根据使用需要生产出丰富多彩的色调系列(尤以水晶白、米黄、浅灰白麻四个色系最为时尚、流行),同时,又能弥补天然石材色差大的缺陷,产品广泛用于宾馆、写字楼、车站机场等内外装饰,更适宜家庭的高级装修,如墙面、地面、饰板、家具、台盆面板等。 耐酸碱度 微晶石作为化学性能稳定的无机质晶化材料,又包含玻璃基质结构,其耐酸碱度、抗腐蚀性能都甚于天然石材,尤其是耐候性更为突出,经受长期风吹日晒也不会褪光,更不会降低强度。
卓越的抗污染性,方便清洁维护 微晶石的吸水率极低,几乎为零,多种污秽浆泥、染色溶液不易侵入渗透,依附于表面的污物也很容易清除擦净,特别方便于建筑物的清洁维护。 异性 微晶石可用加热方法,制成顾客所需的各种弧形、曲面板,具有工艺简单、成本低的优点,避免了弧形石材加工大量切削、研磨、耗时、耗料、浪费资源等弊端。 不含放射 微晶石的制作已经人为的剔除了任何含辐射性的元素,不含像天然石材那样可能出现对人体的放射伤害,是现代最为安全的绿色环保型材料。 缺点 1、微晶石表面晶玉层莫氏硬度为5-6级,强度低于抛光砖的莫氏硬度6-7级。 2、微晶石表面光泽度高,可以达到90%,如果遇划痕会很容易显现出来。 3、微晶石表面有一定数量的针孔,遇到脏东西很容易显现。 鉴别 透明度 透明玻璃的光学性能就是具有透明的性质。企业正是利用它的这一性质,才将透明玻璃陶瓷印花砖复合板产品印制的精美艺术花纹得到充分的展现,并增加了这种花纹的立体感和光亮度。 微晶玻璃,除极个别的主微晶相极小品种外,其光学性质都是半透明到不透明的。这是微晶玻璃与玻璃之间最大的外观差异。 纹样 透明玻璃陶瓷印花砖复合板所呈现的艺术纹样是靠丝网印刷、胶辊印刷、喷墨打印等现代印刷工艺在陶瓷砖上实现的。表层覆盖的透明玻璃只是加强了这些花纹的立体和光亮的视觉效果,起到了画龙点睛或锦上添花的作用。这种产品的艺术装饰性主要靠印花的艺术纹样与色彩来提升,即需要在制版、色彩的选择、印刷设备等方面下功夫。从建筑陶瓷业界的技术水平与生产能力来说,研制和生产这种产品的技术门槛相对还是比较低的,技术含量也相对不高的。印花陶瓷砖几乎所有陶瓷厂都可以实现生产。
纳米相玻璃陶瓷
J. Am. Ceram. Soc. 82[1]5-16,1999 纳米相玻璃陶瓷 George H.beall and Linda R. Pinckney Corning Incorporated, Corning, New York 在将来,玻璃陶瓷主要利用它的内部性能,特别是对信息的传输,显示,存储等专业性能来进行应用的。玻璃陶瓷的显微结构是由许多均匀分布的尺寸小于100纳米的晶体所组成,它可以进行许多可行的新型的应用,也可使许多现有的产品具有特殊的性能。这篇文章主要讨论两种类型的纳米晶玻璃陶瓷:透明的微晶玻璃和可用于精密工程表面的硬的高模量的微晶玻璃。透明的微晶玻璃是从铝酸盐玻璃中形成的,这种玻璃能够有效的进行结晶形核,并缓慢长大。其中主要的晶体相包括具有低热膨胀行为的?相石英固溶体,高硬度及弹性模量的尖晶石和具有独特的荧旋光性的莫来石。 I.绪论 玻璃陶瓷技术是以玻璃的可控形核与结晶为基础的。虽然玻璃陶瓷物体可以通过玻璃整体的内部形核或者经由玻璃原料烧结和结晶来制取,但是由内部形核而可能所具有的显微结构的类型范围要宽广的多。一些玻璃成分可以自发形核,但是通常来说,原料中都需要加入某种特定的形核剂来促使分离和内部形核。这些形核剂均匀的溶入玻璃当中,在二次加热中以精确的比例来使得相分离。这种分散相在结构上的特征就是与母体玻璃不相容,因而在高于玻璃退火点30—100℃的温度下加热时,细小的晶核就可以沉淀出来。这些晶粒可以作为初始晶体相再次形核时的形核点。此外,晶化过程可以在分离相自身内部进行,也可以从分离体的表面开始。 形核之后,可进行多次的高温热处理来促使初始相的晶化并形成所需要的微观结构.此时晶核将继续长大,直到碰触到相邻晶粒为止,从而形成一个大的结晶体,并有少量的剩余玻璃,这些剩余玻璃也可能作为结晶成分而被消耗掉。某些玻璃陶瓷的微观结构可专门设计成这样,即在有连续剩余相玻璃存在的基体中均匀分布着不相互接触的小晶体。 玻璃陶瓷相对于传统的粉末制备陶瓷来说具有许多优点。除了在玻璃态便于成型外,玻璃陶瓷还具有均匀的显微结构,而且对于同质的初始玻璃,其性能可再现。此外,玻璃陶瓷的物理性能可在一个很大的范围内变化。例如热膨胀系数(CETs),可从-75×10(-7)/℃到+200×10(-7)/℃。而玻璃或陶瓷都很难有这么大的变化范围。许多玻璃陶瓷主要都因其热膨胀几乎为零而具有商业价值。而若将其高的机械强度与零孔隙度结合起来,则从建筑材料到餐具到骨头移植等,均可使玻璃陶瓷得到广泛应用。在玻璃陶瓷可形成的众多微观结构中,那些晶体尺寸小于100nm且均匀分布的微晶结构可使现有的产品具有某些特殊的性能,同时还可开发许多可行的新的应用。这种显微结构在学术上即被称为“纳米晶”。 这篇文章主要着重于两种类型的纳米晶玻璃:透明微晶玻璃和具有可精密加工表面的硬的高模量的微晶玻璃。前者拥有大量的消费者及技术方面的应用。而后者则主要用于磁存储盘底层和要求具有光洁表面,耐化学腐蚀的高温环境下。 II.透明微晶玻璃 透明微晶玻璃通常具有两种特性:;一是具有纳米晶,二是比透明玻璃的热稳定性要好,一般都高于常用温度800℃。多数商用透明微晶玻璃都是利用其比较好的热学性能,特别是极低的热膨胀和高的热稳定性,热震抗性。以填充锂?相石英晶体为基础的零或近零膨胀材料可用于高精密光学仪器,比如望远镜镜片,炉顶盖,烹饪用具,煤气炉口,炉门和其他技术设备。 另一种透明微晶玻璃的热膨胀特性与硅非常相近。这种材料通常都是以分布着尖晶石和
微晶玻璃 第一章
1 绪论 1.1 微晶玻璃的定义 1.1.1 定义及特性 微晶玻璃(glass-ceramic)又称玻璃陶瓷,是将特定组成的基础玻璃,在加热过程中通过控制晶化而制得的一类含有大量微晶相及玻璃相的多晶固体材料。 玻璃是一种非晶态固体,从热力学观点看,它是一种亚稳态,较之晶态具有较高的内能,在一定的条件下,可转变为结晶态。从动力学观点看,玻璃熔体在冷却过程中,黏度的快速增加抑制了晶核的形成和长大,使其难以转变为晶态。微晶玻璃就是人们充分利用玻璃在热力学上的有利条件而获得的新材料。 微晶玻璃既不同于陶瓷,也不同于玻璃。微晶玻璃与陶瓷的不同之处是:玻璃微晶化过程中的晶相是从单一均匀玻璃相或已产生相分离的区域,通过成核和晶体生长而产生的致密材料;而陶瓷材料中的晶相,除了通过固相反应出现的重结晶或新晶相以外,大部分是在制备陶瓷时通过组分直接引入的。微晶玻璃与玻璃的不同之处在于微晶玻璃是微晶体(尺寸为0.1~0.5μm)和残余玻璃组成的复相材料;而玻璃则是非晶态或无定形体。另外微晶玻璃可以是透明的或呈各种花纹和颜色的非透明体,而玻璃一般是各种颜色、透光率各异的透明体。 尽管微晶玻璃的结构、性能及生产方法与玻璃和陶瓷都有一定的区别,但是微晶玻璃既有玻璃的基本性能,又具有陶瓷的多相特征,集中了玻璃和陶瓷的特点,成为一类独特的新型材料。 微晶玻璃具有很多优异的性能,其性能指标往往优于同类玻璃和陶瓷。如热膨胀系数可在很大范围内调整(甚至可以制得零膨胀甚至是负膨胀的微晶玻璃);机械强度高;硬度大,耐磨性能好;具有良好的化学稳定性和热稳定性,能适应恶劣的使用环境;软化温度高,即使在高温环境下也能保持较高的机械强度;电绝缘性能优良,介电损耗小、介电常数稳定;与相同力学性能的金属材料相比,其密度小但质地致密,不透水、不透气等。并且微晶玻璃还可以通过组成的设计来获取特殊的光学、电学、磁学、热学和生物等功能,从而可作为各种技术材料、结构材料或其他特殊材料而获得广泛的应用。 微晶玻璃的性能主要决定于微晶相的种类、晶粒尺寸和数量、残余玻璃相的性质和数量。以上诸因素,又取决于原始玻璃的组成及热处理制度。热处理制度不但决定微晶体的尺寸和数量,而且在某些系统中导致主晶相的变化,从而使材料性能发生显著变化。另外,晶核剂的使用是否适当,对玻璃的微晶化也起着关键作用。微晶玻璃的原始组成不同,其主晶相的种类不同,如硅灰石、β-石英、β-锂辉石、氟金云母、尖晶石等。因此通过调整基础玻璃成分和工艺制度,就可以制得各种符合性能要求的微晶玻璃。 1.1.2 微晶玻璃的种类 目前,问世的微晶玻璃种类繁多,分类方法也有所不同。通常按微晶化原理分为光敏微晶玻璃和热敏微晶玻璃;按基础玻璃的组成分为硅酸盐系统、铝硅酸盐系统、硼硅酸盐系统、硼酸盐和磷酸盐系统;按所用原料分为技术微晶玻璃(用一般的玻璃原料)和矿渣微晶玻璃(用工矿业废渣等为原料);按外观分为透明微晶玻璃和不透明微晶玻璃;按性能又可分为耐高温、耐腐蚀、耐热冲击、高强度、低膨胀、零膨胀、低介电损耗、易机械加工以及易化学蚀刻等微晶玻璃以及压电微晶玻璃、生物微晶玻璃等。表1-1列出了常用微晶玻璃的基础组成、主晶相及其主要特性。 表1-1常用微晶玻璃的组成、主晶相及主要特性
电磁炉微晶玻璃面板市场分析要点
近年来,随着电磁炉市场的发展,微晶玻璃面板供求也较为紧俏,但是从2006年开始,由于多方面原因,电磁炉微晶玻璃面板的开始供大于求,从而也导致了2007年上半年电磁炉微晶玻璃面板价格暴跌。未来,电磁炉微晶玻璃面板市场又将如何呢? 市场需求及供应状况 从2000年开始,电磁炉市场以每年70%以上的市场增长率高速增长,从刚开始的100余万台猛增到了2005年的近4000万台。中怡康统计资料显示,2005年电磁炉市场零售量增长55.85%,市场零售额增长51.67%。当时,电磁炉市场被业界一致看好,预测在2006年市场容量将接近6000万台。 在电磁炉市场高速发展的同时,上游原材料特别是微晶玻璃面板也处于供不应求的状态。2004年和2005年,中国微晶玻璃面板行业有限的产能遇到电磁炉井喷式的市场增长,供应十分紧张,特别是到了每年9月份的市场旺季,购买微晶玻璃,甚至一板难求。当时,微晶玻璃面板市场出现了专业的“倒板户”,而且经济效益十分可观。 出于整个电磁炉行业的乐观估计,微晶玻璃行业开始了大规模的产能扩张。据不完全统计,2006年,中国微晶玻璃企业已经超过10家,窑炉数量37个,不算其他正在上马的企业,仅37个窑炉的年产能就超过1亿片。 “在2006年9月电磁炉的旺季前,大多数电磁炉企业对市场充满期待,制订了宏大的发展规划,同时为防止货源不足,还采购了大量的原材料,大量囤积微晶玻璃面板。”浙江湖州岱兴电器制品有限公司一位产品经理回忆一年前的场景时说。 但是,预期火爆的电磁炉市场却没有如期而至。2006年10月,重新审视市场后的电磁炉企业开始减少或者停止采购微晶玻璃面板,有的小电磁炉企业为了防止资金链断裂,开始低价抛售之前储备的原材料。于是,从2006年底到2007年上半年,在供应量加大、市场需求速度减缓、低价抛售、竞争激烈等多方面因素的影响下,电磁炉微晶玻璃面板的供求形势发生逆转。图1显示了2004年至今电磁炉用微晶玻璃面板的价格走势,与2006年10月相比,如今每片微晶玻璃面板每片的价格都有大幅度下降。 广东东莞市金业电子科技有限公司生活电器部项目经理邱明勇介绍说,随着微晶玻璃面板价格在2007年上半年降到最低点,一些小型或者新进入的面板行业的企业开始退出这个市场。 “经历了一次洗牌以后,微晶玻璃面板企业也开始理性对待市场。一些企业开始关停部分生产线,力求让整个行业供求得到平衡。”邱明勇称,2007年下半年微晶玻璃面板的单价开始止跌回升,上涨到20元左右。同时,曾经困扰微晶玻璃面板生产企业的原材料问题也得到了缓解,也减轻了微晶玻璃面板企业的经营压力。据了解,生产微晶玻璃的主要原材料之一碳酸锂曾经出现断货,令微晶玻璃面板企业颇为苦恼。作为电池材料、特种玻璃、陶瓷添加剂及各种锂化合物原料,碳酸锂需求量大,中国本地产能有限,需要从智利和澳大利亚等国进口。供不应求的形势使碳酸锂的价格节节攀升,2004年每吨为3万元,2006年1 月涨到每吨4万元,5月更是达到每吨6万元。不仅是价格上涨,而且供应严重不足,不少
微晶玻璃简述
微晶玻璃简要概述 刘帅聪 (无机非金属材料工程1301班,湖南工学院材料与化学工程学院 湖南衡阳 421002) 摘要 微晶玻璃是通过基础玻璃或其它材料在加热过程中进行控制晶化而得到的一种中含有大量微晶体和玻璃体的复合固体材料。由于其机械强度高、热膨胀性可调、抗热震性好、耐化学腐蚀、介电损耗低、电绝缘性好等优越的综合性能,已在许多领域得到广泛的应用。 关键词微晶玻璃特点制备工艺应用发展 Brief Introduction of Glass - Ceramics Shuai Cong Liu (Inorganic Nonmetallic Materials Engineering1301class,Hunan Institute of TechnologyDepartment of Material and Chemical Engineering Hunan Hengyang 421002) Abstract: Crystalline glass is a composite solid material containing a large amount of microcrystals and vitreous bodies obtained by controlling crystallization during the heating process by the base glass or other materials. Because of its high mechanical strength, adjustable thermal expansion, good thermal shock resistance, chemical resistance, low dielectric loss, good electrical insulation properties such as superior performance, has been widely used in many fields. Key words: glass - ceramics, characteristics, preparation technology, application development
微晶玻璃特性表
一、什么是微晶玻璃 微晶玻璃(CRYSTOE and NEOPARIES)又称微晶玉石或陶瓷玻璃。是综合玻璃、石材技术发展起来的一种新型建材。因其可用矿石、工业尾矿、冶金矿渣、粉煤灰、煤矸石等作为主要生产原料,且生产过程中无污染,产品本身无放射性污染,故又被称为环保产品或绿色材料。 微晶玻璃集中了玻璃、陶瓷及天然石材的三重优点,优於天石材和陶瓷,可用於建筑幕墙及室内高档装饰,还可做机械上的结构材料,电子、电工上的绝缘材料,大规模集成电路的底板材料、微波炉耐热列器皿、化工与防腐材料和矿山耐磨材料等等。是具有发展前途的21世纪的新型材料。 二、微晶玻璃的组成 把加有晶核剂或不加晶核剂的特定组成的玻璃,在有控条件下进行晶化热处理,使原单一的玻璃相形成了有微晶相和玻璃相均匀分布的复合材料。微晶玻璃和普通玻璃区别是:前者部分是晶体,后者全是非晶体。微晶玻璃表面可呈现天然石条纹和颜色的不透明体,而玻璃则是各种颜色、不同程序的透明体。 微晶玻璃的综合性能主要决定三大因素:原始组成的成份、微晶体的尺寸和数量、残余玻璃相的性质和数量。 后两种因素是由微晶玻璃晶化热处理技术决定。微晶玻璃的原始组成不同,其晶相的种类也不同,例如有β硅灰石、β石英、氟金云母、二硅酸锂等,各种晶相赋予微晶玻璃的不同性能,在上述晶相中,β硅灰石晶相具有建筑微晶玻璃所需性能,为此常选用CaO-Al2O3-SiO2系统为建筑微晶玻璃原始组成系统,其一般成分如表一所示。 表一:CaO-Al2O3-SiO2微晶玻璃组成 颜色\组成SiO2 Al2O3 B2O3 CaO ZnO BaO Na2O K2O Fe2O3 Sb2O3 白色59.0 7.0 1.0 17.0 6.5 4.0 3.0 2.0 0.5 黑色59.0 6.0 0.5 13.0 6.0 4.0 3.0 2.0 6.0 0.5 上述玻璃成份在晶化热处理后所析出的主晶相是:β——硅灰石(β——CaO、SiO2)。 三、建筑微晶玻璃性能 建筑用微晶玻璃装饰面板材与天然大理石、花岗岩性能列表二(见下页)。 材料微晶玻璃大理石花岗岩 特性 机械性能抗弯强度①(Mpa) 40~50 5.7~15 8~15 抗压强度(Mpa) 341.3 67~100 100~200 抗冲击强度(Pa) 2452 2059 1961
玻璃材料论文
微晶玻璃的制备与应用 【摘要】玻璃陶瓷(glass-ceramics)又称微晶玻璃。是综合玻璃,玻璃陶瓷和我们常见的玻璃看起来大不相同。它具有玻璃和陶瓷的双重特性,普通玻璃内部的原子排列是没有规则的,这也是玻璃易碎的原因之一。而玻璃陶瓷像陶瓷一样,由晶体组成,也就是说,它的原子排列是有规律的。所以,玻璃陶瓷比陶瓷的亮度高,比玻璃韧性强。 【关键字】玻璃陶瓷;可切削玻璃陶瓷;分相;结晶化;晶核剂 微晶玻璃是将加有晶核剂的特定组合的玻璃,在有控条件(一定温度)下进行晶化热处理,成为具有微晶体和玻璃相均匀分布的复合材料。微晶玻璃由玻璃相与结晶相组成。两者的分布状况随其比例而变化:当玻璃相占的比例大时,玻璃相为连续的基体,晶相孤立地均匀地分布在其中;当玻璃相较少时,玻璃相分散在晶体网架之间,呈连续网状;当玻璃相数量很低,则玻璃相以薄膜状态分布在晶体之间。这种结构也决定了其机械强度高,绝缘性能优良,介电损耗少,介电常数稳定,热膨胀系数可在很大范围调节,耐化学腐蚀,耐磨,热稳定性好,使用温度高的良好性能。 微晶玻璃集中了玻璃、陶瓷及天然石材的三重优点,优于天石材和陶瓷,可用于建筑幕墙及室内高档装饰,还可做机械上的结构材料,电子、电工上的绝缘材料,大规模集成电路的底板材料、微波炉耐热列器皿、化工与防腐材料和矿山耐磨材料等等。是具有发展前途的21世纪的新型材料。 1制备方法 微晶玻璃的制备方法根据其所用原材料的种类、特性、对材料的性能要求而变化,主要的有熔融法、烧结法、溶胶—凝胶法、二次成型工艺、强韧化技术等。 1.1熔融法 熔融后急冷,退火后在经一定的热处理制度进行成核和晶化以获得晶粒细小、含量多、结构均匀的微晶玻璃制品。热处理制度的确定是微晶玻璃生产的关键技术。作为初步的近似估计,最佳成核温度介于Tg 和比它高50℃的温度之间。晶化温度上限应低于主晶相在一个适当的时间内重熔的温度。通常是25℃~50℃。 常用的晶核剂有TiO2,P2O5,ZrO2,CaO,CaF2,Cr2O3、硫化物、氟化物。晶核剂的选择与基础玻璃化学组成有关,也与期望析出的晶相种类有关。Stooky指出,良好的晶核剂应具备如下性能:(1)在玻璃熔融成形温度下,应具有良好的溶解性,在热处理时应具有较小的溶解性,并能降低成核的活化能。(2) 晶核剂质点扩散的活化能要尽量小,使之在玻璃中易与扩散。(3) 晶核剂组分和初晶相之间的界面张力愈小,它们之间的晶格参数之差愈小(σ<±15%),成核愈容易。复合晶核剂可以起到比单一晶核剂更好核化效果,它主要是起到双碱效应。 熔融法制备微晶玻璃可采用任何一种玻璃的成形方法,如:压制、浇注、吹制、拉制,便于生产形状复杂的制品和机械化生产,但也存在一些问题有待于解决:(1) 熔制温度过高,通常都在1400~1600℃,能耗大。(2) 热处理制度在现实生产中难于控制操纵。(3) 晶化温度高,时间长,现实生产中难于实现。 1.2烧结法 烧结法制备微晶玻璃材料的基本工艺为将一定组分的配合料,投入到玻璃熔窑当中,在高温下使配合料熔化、澄清、均化、冷却,然后,将合格的玻璃液导入冷水中,使其水淬成
微晶玻璃的制备
微晶玻璃的制备 一、文献综述 1、微晶玻璃的概念 微晶玻璃又叫微晶玉石或瓷玻璃,是综合玻璃,学名叫做玻璃水晶。 微晶玻璃和我们常见的玻璃看起来大不相同。它具有玻璃和瓷的双重特性,普通玻璃部的原子排列是没有规则的,这也是玻璃易碎的原因之一。而微晶玻璃象瓷一样,由晶体组成,也就是说,它的原子排列是有规律的。 所以,微晶玻璃比瓷的亮度高,比玻璃韧性强。但微晶玻璃不同于瓷和玻璃。 微晶玻璃与瓷的不同之处是:玻璃微晶化过程中的晶相是从单一均匀玻璃相或已产生相分离的区域,通过成核和晶体生长而产生的致密材料; 而瓷材料中的晶相,除了通过固相反应出现的重结晶或新晶相以外,大部分是在制备瓷时通过组分直接引入的。微晶玻璃与玻璃的不同之处在于微晶玻璃是微晶体(尺寸为0.1~0.5μm)和残余玻璃组成的复相材料;而玻璃则是非晶态或无定形体。 另外微晶玻璃可以是透明的或呈各种花纹和颜色的非透明体,而玻璃一般是各种颜色、透光率各异的透明体。 2、微晶玻璃的分类 (1)通常按微晶化原理分为光敏微晶玻璃和热敏微晶玻璃; (2)按基础玻璃的组成分为硅酸盐系统、铝硅酸盐系统、硼硅酸盐系统、硼酸盐和磷酸盐系统; (3)按所用原料分为技术微晶玻璃(用一般的玻璃原料)和矿渣微晶玻璃(用工矿业废渣等为原料); (4)按外观分为透明微晶玻璃和不透明微晶玻璃; (5)按性能又可分为耐高温、耐腐蚀、耐热冲击、高强度、低膨胀、零膨胀、低介电损耗、易机械加工以及易化学蚀刻等微晶玻璃以及压电微晶玻璃、生物微晶玻璃等 (6)晶玻璃的组成在很大程度上决定其结构和性能。按照化学组成微晶玻璃主要分为四类:硅酸盐微晶玻璃,铝硅酸盐微晶玻璃,氟硅酸盐微晶玻璃,磷酸盐微晶玻璃。 3、微晶玻璃的制备方法 微晶玻璃的制备方法根据其所用原材料的种类、特性、对材料的性能要求而变化,主要的有熔融法、烧结法、溶胶—凝胶法、二次成型工艺、强韧化技术等。 3.1、熔融法(整体析晶法) 熔融后急冷,退火后在经一定的热处理制度进行成核和晶化以获得晶粒细小、含量多、结构均匀的微晶玻璃制品。热处理制度的确定是微晶玻璃生产的关
微晶玻璃花岗岩石材装饰板介绍
微晶玻璃花岗岩石材装饰板介绍 微晶玻璃花岗岩装饰板是目前际上开始流行的高级建筑装饰材料,较天然花岗岩石材更能进行灵活设计,而且装饰效果更佳。是21世纪的绿色建材,是内、外墙及地面的理想装饰材料。 微晶玻璃花岗岩是应用受控晶化新技术生产的新型装饰材料,其结构致密、高强、耐磨、耐蚀,在外观上纹理清晰、色彩鲜艳、无色差、不褪色。是天然花岗岩石材最理想的替代产品,与天然花岗岩比,具有以下优点。 (1)色泽可根据要求生产各种色彩、色调和混合色的各种装饰材料,颜色有白、绿、灰、黄、红、蓝、黑等,而且装饰效果更佳。 (2)材质微晶玻璃花岗岩装饰板的成分与天然花岗岩相同,均属硅酸盐质,在材料内部结构中,生长有硅灰石的主晶相,所以耐磨、耐蚀、强度上均优于天然花岗岩石材。 (3)环保微晶玻璃花岗岩板材无任何类型的放射性物质,符合环保要求,有益人体。 (4)规格可生产各种厚度、尺寸的平板,,弧形板。另外还可生产30多种混合色和多种规格异型微晶玻璃花岗岩装饰板。是机场、银行、地铁、宾馆、酒楼、别墅及居室的首选理想装饰材料。 一、绪言
优质花岗岩饰面材料具有优异的硬度和耐磨性、并具优美的外观花纹,一直是人们首选的建筑饰面材料。然而,天然花岗岩因:(1)含有一定量地放射性元素---氡,长期接触会对人身体造成一定伤害,国外一些发达国家及国内很多大城市都已明令禁止有放射性地天然石材用于室内装饰。(2)内部组成与结构的原因,机械强度和化学稳定性较差,造成抗风化能力和耐久性较差。(3)一些优质石材蕴藏量有限,价格昂贵。(4)天然石材的颜色花纹变化较大,整体装饰效果较差等本身固有的原因。市场迫切需要开发天然石材代用品。特别是近几年人们环境保护意识的增强,人们更加迫切地需要不含放射性物质的天然石材替代品。近二十年来,各科研单位及生产企业纷纷研制开发了许多种仿大理石、花岗岩产品,如:无机胶凝和有机胶结的“仿大理石”,陶瓷仿大理石釉面砖和渗花砖,等等。所有这些虽然有一些具有大理石或花岗岩的花纹,但质感和性能却远远不及天然石材。 本世纪六十年代后期,微晶玻璃的研究取得突破性进展,各种具优异性能的微晶玻璃制品开始工业化生产,一些国家的科学家开始研究开发微晶玻璃饰面材料,如前苏联开发成功地“矿渣微晶玻璃”、捷克斯洛伐克以玄武岩作原料生产地“人造玄武岩”和美国开发成功地“人造蛋白石”等等。所有这些制品其理化性能都远优于天然石材,但没有天然石材那漂亮的外观花纹。很难作为天然石材的理想替代品。 到了七十年代,日本电器硝子株式会社的科学家率先突破技术难关,研制出了具天然大理石外观、且性能远优于天然石材的“结晶化玻璃大理石”,并于 1974年开始工业化生产,商品名为“新型玻璃大理石(Neoparies)”。 我们于1982年开始研究“结晶化玻璃大理石”,次年就研究成功了具花岗岩外观的“微晶玻璃花岗岩”,但在进行工业化试生产过程中,因气泡和变形缺陷无法解决,成品率极低,技术推广和产品商品化就此搁浅了。 直到1994年南方某厂投资近亿元人民币建成了年产40万平米的生产线,他们经过近半年试生产,也同样遇到了气泡问题无法解决而造成成品率极低,委托我们帮助解决;为此我们对过去的技术资料进行了认真分析讨论,认为气泡的来源主要有以下三点: 1.玻璃融化不完全,残存有未排除之气泡,在二次烧结过程中膨胀形成。 2.玻璃料水淬及淬碎料处理过程中混入的吸附水及杂质所为。 3.由于热传递温度梯度的存在,烧结过程中板材表面先受热熔融,将气体封 接在板材中,随着温度地升高,玻璃料黏度的降低,气泡浮向表面造成 缺陷。 在后来我们借助高温显微镜证实气泡也确实是由上述第二、三点原因造成地,遂产生了这样一个设想:如果我们研究这样一种添加剂即或者具有吸收气体的作用或者具较小黏度和表面张力能在烧结过程中使气泡顺利排出。问题不就解决了吗? 1994年我们成立专门地技术开发课题小组,集中对以下技术课题深入地研究开发并取得了突破性进展: 1.研制出了微晶玻璃花岗岩消泡剂,基本彻底地解决了气泡问题。
微晶玻璃
. 1 绪论 1.1 微晶玻璃的定义 1.1.1 定义及特性 微晶玻璃(glass-ceramic)又称玻璃陶瓷,是将特定组成的基础玻璃,在加热过程中通过控制晶化而制得的一类含有大量微晶相及玻璃相的多晶固体材料。 玻璃是一种非晶态固体,从热力学观点看,它是一种亚稳态,较之晶态具有较高的内能,在一定的条件下,可转变为结晶态。从动力学观点看,玻璃熔体在冷却过程中,黏度的快速增加抑制了晶核的形成和长大,使其难以转变为晶态。微晶玻璃就是人们充分利用玻璃在热力学上的有利条件而获得的新材料。 微晶玻璃既不同于陶瓷,也不同于玻璃。微晶玻璃与陶瓷的不同之处是:玻璃微晶化过程中的晶相是从单一均匀玻璃相或已产生相分离的区域,通过成核和晶体生长而产生的致密材料;而陶瓷材料中的晶相,除了通过固相反应出现的重结晶或新晶相以外,大部分是在制备陶瓷时通过组分直接引入的。微晶玻璃与玻璃的不同之处在于微晶玻璃是微晶体(尺寸为0.1~0.5μm)和残余玻璃组成的复相材料;而玻璃则是非晶态或无定形体。另外微晶玻璃可以是透明的或呈各种花纹和颜色的非透明体,而玻璃一般是各种颜色、透光率各异的透明体。 尽管微晶玻璃的结构、性能及生产方法与玻璃和陶瓷都有一定的区别,但是微晶玻璃既有玻璃的基本性能,又具有陶瓷的多相特征,集中了玻璃和陶瓷的特点,成为一类独特的新型材料。 微晶玻璃具有很多优异的性能,其性能指标往往优于同类玻璃和陶瓷。如热膨胀系数可在很大范围内调整(甚至可以制得零膨胀甚至是负膨胀的微晶玻璃);机械强度高;硬度大,耐磨性能好;具有良好的化学稳定性和热稳定性,能适应恶劣的使用环境;软化温度高,即使在高温环境下也能保持较高的机械强度;电绝缘性能优良,介电损耗小、介电常数稳定;与相同力学性能的金属材料相比,其密度小但质地致密,不透水、不透气等。并且微晶玻璃还可以通过组成的设计来获取特殊的光学、电学、磁学、热学和生物等功能,从而可作为各种技术材料、结构材料或其他特殊材料而获得广泛的应用。 微晶玻璃的性能主要决定于微晶相的种类、晶粒尺寸和数量、残余玻璃相的性质和数量。以上诸因素,又取决于原始玻璃的组成及热处理制度。热处理制度不但决定微晶体的尺寸和数量,而且在某些系统中导致主晶相的变化,从而使材料性能发生显著变化。另外,晶核剂的使用是否适当,对玻璃的微晶化也起着关键作用。微晶玻璃的原始组成不同,其主晶相的种类不同,如硅灰石、β-石英、β-锂辉石、氟金云母、尖晶石等。因此通过调整基础玻璃成分和工艺制度,就可以制得各种符合性能要求的微晶玻璃。 1.1.2 微晶玻璃的种类 目前,问世的微晶玻璃种类繁多,分类方法也有所不同。通常按微晶化原理分为光敏微晶玻璃和热敏微晶玻璃;按基础玻璃的组成分为硅酸盐系统、铝硅酸盐系统、硼硅酸盐系统、硼酸盐和磷酸盐系统;按所用原料分为技术微晶玻璃(用一般的玻璃原料)和矿渣微晶玻璃(用工矿业废渣等为原料);按外观分为透明微晶玻璃和不透明微晶玻璃;按性能又可分为耐高温、耐腐蚀、耐热冲击、高强度、低膨胀、零膨胀、低介电损耗、易机械加工以及易化学蚀刻等微晶玻璃以及压电微晶玻璃、生物微晶玻璃等。表1-1列出了常用微晶玻璃的基础组成、主晶相及其主要特性。表1-1常用微晶玻璃的组成、主晶相及主要特性
微晶玻璃面板规格说明书(英文版)
Product description Product Name: Black Transparent Electromagnetic Oven panel Guangdong Kedi Glass-ceramic Industrial Co., Ltd. 1 Scope of Application This manual applies to black transparent glass ceramics panel. 2 Reference Standard Guangdong Province Industry Standard, Q/PKT 02-2007 Broad Black Transparent Glass-ceramic Plate. 3 Material Black transparent glass ceramics are used to meet the special requirements of electromagnetic oven Standard features which are to be described respectively, fit the RoHS rules. 3.1 Characteristics of glass ceramics 3.1.1 Maximum Service Temperature: The original color of the plate will change at the temperature of 780 ℃. 3.1.2 Temperature of Thermal Shock
黑色微晶玻璃规格书(中英对照)
产品说明书 Product description 产品名称:黑色透明电磁炉面板 Product Name: Black Transparent Electromagnetic Oven panel 广东科迪微晶玻璃实业有限公司 Guangdong Kedi Glass-ceramic Industrial Co., Ltd. 1适用范围 1 Scope of Application 本说明书适用于黑色透明微晶玻璃板材。 This manual applies to black transparent glass ceramics panel. 2 引用标准 2 Reference Standard 广东省行业标准,Q/PKT 02-2007,大板黑色透明微晶玻璃板材。 Guangdong Province Industry Standard, Q/PKT 02-2007 Broad Black Transparent Glass-ceramic Plate. 3 材质 3 Material 黑色透明微晶玻璃,满足电磁炉灶的特殊要求; Black transparent glass ceramics are used to meet the special requirements of electromagnetic oven 标准特性将分别说明,同时适合RoHS规定。 Standard features which are to be described respectively, fit the RoHS rules. 3.1 微晶玻璃的特性 3.1 Characteristics of glass ceramics 3.1.1 最高安全使用温度: 3.1.1 Maximum Service Temperature: 780℃,初期使用板材颜色将发生变化。 The original color of the plate will change at the temperature of 780 ℃. 3.1.2 热冲击温度:
微晶玻璃及微晶玻璃幕墙
微晶玻璃及微晶玻璃幕墙 一、什么是微晶玻璃 微晶玻璃(CRYSTOE and NEOPARIES)又称微晶玉石或陶瓷玻璃。是综合玻璃、石材技术发展起来的一种新型建材。因其可用矿石、工业尾矿、冶金矿渣、粉煤灰、煤矸石等作为主要生产原料,且生产过程中无污染,产品本身无放射性污染,故又被称为环保产品或绿色材料。 微晶玻璃集中了玻璃、陶瓷及天然石材的三重优点,优於天石材和陶瓷,可用於建筑幕墙及室内高档装饰,还可做机械上的结构材料,电子、电工上的绝缘材料,大规模集成电路的底板材料、微波炉耐热列器皿、化工与防腐材料和矿山耐磨材料等等。是具有发展前途的21世纪的新型材料。 二、微晶玻璃的组成 把加有晶核剂或不加晶核剂的特定组成的玻璃,在有控条件下进行晶化热处理,使原单一的玻璃相形成了有微晶相和玻璃相均匀分布的复合材料。微晶玻璃和普通玻璃区别是:前者部分是晶体,后者全是非晶体。微晶玻璃表面可呈现天然石条纹和颜色的不透明体,而玻璃则是各种颜色、不同程序的透明体。 微晶玻璃的综合性能主要决定三大因素:原始组成的成份、微晶体的尺寸和数量、残余玻璃相的性质和数量。 后两种因素是由微晶玻璃晶化热处理技术决定。微晶玻璃的原始组成不同,其晶相的种类也不同,例如有β硅灰石、β石英、氟金云母、二硅酸锂等,各种晶相赋予微晶玻璃的不同性能,在上述晶相中,β硅灰石晶相具有建筑微晶玻璃所需性能,为此常选用CaO-Al2O3-SiO2系统为建筑微晶玻璃原始组成系统,其一般成分如表一所示。
表一: CaO-Al2O3-SiO2微晶玻璃组成 颜色\组成SiO2 Al2O3 B2O3 CaO ZnO BaO Na2O K2O Fe2O3 Sb2O3 白色59.0 7.0 1.0 17.0 6.5 4.0 3.0 2.0 0.5 黑色59.0 6.0 0.5 13.0 6.0 4.0 3.0 2.0 6.0 0.5 上述玻璃成份在晶化热处理后所析出的主晶相是:β——硅灰石(β——CaO、SiO2)。 三、建筑微晶玻璃性能 建筑用微晶玻璃装饰面板材与天然大理石、花岗岩性能列表二(见下页)。 材料微晶玻璃大理石花岗岩 特性 机械性能抗弯强度①(Mpa) 40~50 5.7~15 8~15 抗压强度(Mpa) 341.3 67~100 100~200 抗冲击强度(Pa) 2452 2059 1961 弹性模量(×104MPa) 5 2.7~8.2 4.2~6.0 莫氏硬度6,5 3~5 ~5.5 维氏硬度(100g)600 130 130~570 比重2.7 2.7 2.7 化学性能耐酸性②(1%H2SO4)0.08 10.0 0.10 耐碱性②(1%NaOH) 0.05 0.30 0.10 耐海水性③(mg/cm2) 0.08 0.19 0.17 吸水率④(%)0 0.3 0.35 抗冻性(%)⑤0.028 0.23 0.25