失效模式分析
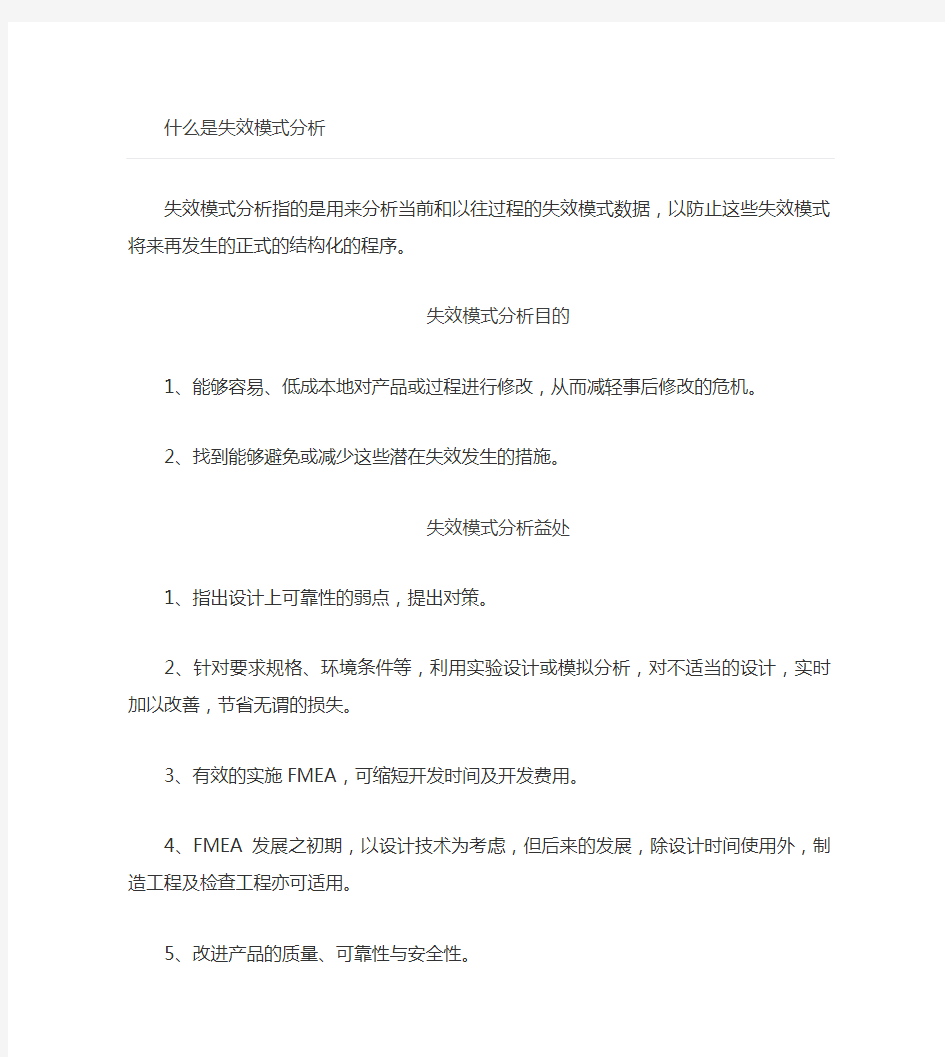

什么是失效模式分析
失效模式分析指的是用来分析当前和以往过程的失效模式数据,以防止这些失效模式将来再发生的正式的结构化的程序。
失效模式分析目的
1、能够容易、低成本地对产品或过程进行修改,从而减轻事后修改的危机。
2、找到能够避免或减少这些潜在失效发生的措施。
失效模式分析益处
1、指出设计上可靠性的弱点,提出对策。
2、针对要求规格、环境条件等,利用实验设计或模拟分析,对不适当的设计,实时加以改善,节省无谓的损失。
3、有效的实施FMEA,可缩短开发时间及开发费用。
4、FMEA发展之初期,以设计技术为考虑,但后来的发展,除设计时间使用外,制造工程及检查工程亦可适用。
5、改进产品的质量、可靠性与安全性。
失效模式分析的适用范围
失效模式分析对产品从设计完成之后,到首次样品的发展而后生产制造,到品管验收等阶段都可说皆有许多适用范围,基本上可以活用在3个阶段,兹说明如下:第一阶段设计阶段的失效模式分析
1.针对已设计的构想作为基础,逐项检讨系统的构造、机能上的问题点及预防策略。
2.对于零件的构造、机能上的问题点及预防策略的检讨。
3.对于数个零件组或零件组之间可能存在的问题点作检讨。
第二阶段试验计划订定阶段的失效模式分析
1.针对试验对象的选定及试验的目的、方法的检讨。
2.试验法有效的运用及新评价方法的检讨。
3.试验之后的追踪和有效性的持续运用。
第三阶段制程阶段的FMEA
1.制程设计阶段中,被预测为不良制程及预防策略的检讨。
2.制程设计阶段中,为了防止不良品发生,而必须加以管理之特性的选定,或管理重点之检讨。
3.有无订定期间追踪的效益。
除了上述所用的范围可以运用此一分析技巧外,使用者亦可自行运用在合适的地方。但是在运用上要注意到:
1.失效模式资讯情报。
如能在事前收集好对象产品、制程、机能等的相关资讯情报,对于分析有很大的帮助。在收集资料上要把握不要轻言放弃可能的因素,如果真的难以判断,就交由专案小组讨论确定。
2 .分析检讨人员足够
为防止分析时的偏差导致失之毫厘,差之千里的谬误并能收集思广益之功,一定的人数参与是必要的,至于多少人才算足够,当视分析对象的特征或公司能力而定。对这一点,固然在量上面要足够,质方面也要考量各个
层面的代表性,每个功能别组织要有,专业技术和管理人员都有则能更具周延性。
对于初次导入失效模式分析手法的企业而言,也许延聘外部顾问或指导者,进行人员训练、执行协助等是一项可行的做法。
3.开发时间整合
由于绝大部分进行此类分析的人员,都有既定的原本任务,一方面要能进行日常工作,另一方面要能顺遂分析工作,因此开发时间的妥善安排是非常重要的,可以专案性工作组织来进行失效模式分析可以获得更有利的分工。
同时,也要明示设计审查的检讨对象,界定谁有权利作最后定案的人。
4.结果加以追踪
任何专案工作都须订定追踪日期,比较好的作法是将追踪的作业也当成分析工作的一部分,并且在工作计划中也安排进去,当然,负责排定工作的人也要对追踪工作安排负责人,最好能对追踪情形定期提一份报告给公司执行长。
专案进度是检视失效模式分析成就多寡的重要指标,依照后续的实施步骤,建立一套模式化的分析流程。
PCB失效分析技术及部分案例
PCB失效分析技术及部分案例 作为各种元器件的载体与电路信号传输的枢纽,PCB已经成为电子信息产品的最为重要而关键的部分,其质量的好坏与可靠性水平决定了整机设备的质量与可靠性。但是由于成本以及技术的原因,PCB在生产和应用过程中出现了大量的失效问题。 对于这种失效问题,我们需要用到一些常用的失效分析技术,来使得PCB在制造的时候质量和可靠性水平得到一定的保证,本文总结了十大失效分析技术,供参考借鉴。 1.外观检查 外观检查就是目测或利用一些简单仪器,如立体显微镜、金相显微镜甚至放大镜等工具检查PCB的外观,寻找失效的部位和相关的物证,主要的作用就是失效定位和初步判断PCB 的失效模式。外观检查主要检查PCB的污染、腐蚀、爆板的位置、电路布线以及失效的规律性、如是批次的或是个别,是不是总是集中在某个区域等等。另外,有许多PCB的失效是在组装成PCBA后才发现,是不是组装工艺过程以及过程所用材料的影响导致的失效也需要仔细检查失效区域的特征。 2.X射线透视检查 对于某些不能通过外观检查到的部位以及PCB的通孔内部和其他内部缺陷,只好使用X 射线透视系统来检查。X光透视系统就是利用不同材料厚度或是不同材料密度对X光的吸湿或透过率的不同原理来成像。该技术更多地用来检查PCBA焊点内部的缺陷、通孔内部缺陷和高密度封装的BGA或CSP器件的缺陷焊点的定位。目前的工业X光透视设备的分辨率可以达到一个微米以下,并正由二维向三维成像的设备转变,甚至已经有五维(5D)的设备用于封装的检查,但是这种5D的X光透视系统非常贵重,很少在工业界有实际的应用。 3.切片分析 切片分析就是通过取样、镶嵌、切片、抛磨、腐蚀、观察等一系列手段和步骤获得PCB
新版FMEA-失效模式与影响分析实战训练(1)
新版FMEA-失效模式与影响分析实战训练 ●课程背景 德国汽车工业协会(VDA QMC)在德国柏林召开股东会议,并正式宣布新版AIAG-VDA FMEA标准发布!这是一个历史性时刻,历经了长时间汽车行业专家的反复研讨和修订,第一版的AIAG-VDA标准终于正式发布!本次培训将根据最新发布的AIAG-VDA FMEA 要求,系统地讲解新版FMEA的背景,重要变化点以及企业如何应对等,并对新的AIAG-VDA FMEA七步法进行详细讲解,帮助企业迅速掌握新版FMEA的使用。FMEA是1960 年代美国太空计划所发展出来的一套手法,为了预先发现产品或流程的任何潜在可能缺点,并依照其影响效应,进行评估与针对某些高风险系数之项目,预先采取相关的预防措施避免可能产生的损失与影响。近年来广为企业界做为内部预防改善与外部对供货商要求的工具,是从事产品设计及流(制)程规划相关人员不得不熟悉的一套运用工具。FMEA是系统化的工程设计辅助工具,主要利用表格方式协助进行工程分析,使其在工程设计时早期发现潜在缺陷及其影响程度,及早谋求解决之道,避免失效之发生或降低影响,提高系统之可靠度。因此尽早了解与推动失效分析技术,是业界进军国际市场必备的条件之一! ●培训对象 研发总监、经理、工程师;质量总监、质量经理、质量主管、质量工程师、质量技术员;技术总监、经理、工程师、技术员;产吕流程总监、经理、工程师、技术员;生产经理、生产主管以及所有工程师(PE,ME,QA,SQE等)。 ●培训时间 2-3天 ●课程收获 1.了解最新版FMEA的背景及主要变化点
2.理解和掌握新版FMEA的七步法 3.预先考虑正常的用户使用和制造过程中会出现的失效 4.有助于降低成本提升效益,预防不良品的发生 5.建立产品可靠度保证系统,具备整体的概念 6.认识失效的类型及其影响 7.熟悉并运用失效模式与效应分析手法预防产品设计与制程规划可能发生的不良现象 8.累积公司相关不良模式与效应处理之工程之知识库,不断改进产品可靠性 课程大纲 第一章FMEA的发展过程 一.了解FMEA 二.FMEA定义 三.FMEA的目的 四.什么时候用FMEA 五.新版FMEA的主要变化 1.七步法代替以前的“填表法” 2.全新的SOD评分标准 3.全新的措施优先级AP取代RPN 4.增加了优化措施的状态跟踪 5.监视及系统响应的补充FMEA(FMEA-MSR) 6.全新的表格等 第二章FMEA简介 一.FMEA的时间顺序 二.FMEA集体的努力 三.成功的FMEA小组 四.FMEA小组的守则 五.FMEA小组决定的标准/模式 第三章执行新版PFMEA和实例
FA失效分析案例集
FA失效分析案例集 案例1:大电流导致器件金属融化 某产品在测试现场频频出现损坏,经过对返修进行分析,发现大部分返修产品均是某接口器件失效,对器件进行解剖后,在金相显微镜下观察,发现器件是由于EOS导致内部铝线融化,导致器件失效,该EOS能量较大。进一步分析和该铝条相连的管脚电路应用,发现电路设计应用不当,没有采用保护电路,在用户现场带电插拔产生的电浪涌导致该器件失效。通过模拟试验再现了失效现象。 解决方法:强调该产品不支持带电插拔,建议客户在测试或使用的过程,需等电源关掉后,在进行插拔动作。 1.jpg
案例2: 客户反馈显示异常,显示暗淡,颜色异常,通过示波器查看波形,发现波形异常,通过一系列测试,判断IC 驱动损坏,通过EMMI 测试发现照片如下: 放大细节:
分析芯片内部电路,低压逻辑部分损坏。 分析原因:此IC的抗ESD能力 发现 COM SEG PIN在MM模式下,更容易被击穿。在HMB模式,小于+/-3K的 ESD均OK. 此IC现象是由于ESD损坏IC,导致IC出现短路所致。 具体解决方法: 生产,测试的注意,注意检查机台是否漏电,检查每位员工的ESD环是否OK.
下面简单谈谈在开发过程中的一些建议: 要想设计质量可靠性达到要求的产品,主要有以下几个步骤: 1, 明确产品的质量可靠性要求, 如是消费级还是电信级,最终的客户是谁,客户的需求是什么,使用的环境是什么,产品返修率指标是多少?等等。。。。,由此确定产品的质量可靠性要求,作为产品规格明确下来。 2, 在明确质量可靠性规格以后进行产品总体设计,这时最重要的是选择和使用质量可靠性符合产品规格要求的器件. 比如产品的使用环境比较恶劣,如使用在高海拔、强辐射地区,则需要对应的选择合适的器件。如果在应用环境中,选用的器件本身的质量可靠性无法满足要求,那么这个设计从一开始就注定是失败的。 3,在选好器件后,就要考虑在设计应用中避免各种可能的应力对器件的损伤, 如ESD防护设计、电浪涌防护设计、热设计、环境应力设计等,考虑到各种可能应力,并进行降额设计或者进行最坏情况分析。另外,还要进行信号完整性分析,EMC兼容设计等,来保证设计的产品的功能可靠性。在这一阶段,FMEA(失效模式影响分析)也是必不可少的步骤。 4, 在设计阶段还要考虑产品的可加工性. 如生产线的ESD、MSL控制水平是多少,如果生产线最多只能保证100V的ESD水平,那么ESD等级低于100V的器件就不
失效案例分析
工程材料失效分析 姓名:丁静 学号:201421803012
案例一乙烯裂解炉炉管破裂原因分析某石化公司化工一厂裂解车间CBL一Ⅲ型乙烯裂解炉于1998年9月投入运行,1 999年4月检查发现一根裂解炉管发生泄漏。为查明炉管泄漏原因,对失效炉管进行了综合分析。 CBL一Ⅲ型乙烯裂解炉炉管工作温度为1050~llOO℃,材质化学成分(质量分数)为0.35~0.60%C;1.0%~2.0%Si;1.O%~1.50%Mn;33%~38%Ni;23%~28%Cr及微量Nb.Ti.Zr等。宏观观察失效炉管表面可以看出,泄漏部位炉管内、外壁均有两个孔坑,两个孔坑在内、外表面相互对应,孔坑边缘金属略有凸起,呈火山口状。仔细观察发现,在内壁两个孔坑附近表面有一约3 mm xl mm凸棱,凸棱略高于附近炉管表面(图11-1、图11-2)。
化学成分分析结果表明,失效炉管化学成分符合厂家技术要求。金相检查结果表明,失效炉管显微组织基体为奥氏体,晶界分布有骨架状碳化物,晶内和晶界分布有一定数量的颗粒状碳化物(图11-3)。 能谱分析结果表明,这些颗粒状碳化物为Nb.Zr.Ti或Cr的
碳化物。晶界分布的骨架状碳化物系以铬为主的碳化物。首先,采用扫描电镜观察了泄漏部位炉管内、外表面的放大形貌,观察发现,所有孔坑均存在白亮色块状物。通常,不导电的非金属氧化物或金属氧化物在电子束作用下因积累电荷而呈白亮色。能谱分析结果表明,白亮色块状物含有很高的稀土铈。分析认为,白亮色块状物为稀土氧化物。在泄漏部位,分别在内壁凸棱和孔坑两处,垂直于内表面制备了炉管横截面金相试样。可以看出,不论是凸棱对应部位,还是炉管内、外表面两个孔坑之间,炉管横截面均分布有宏观深灰色金属夹杂物,夹杂物在内、外表面两个孔坑之间连续贯通(图11-4)。 在扫描电镜下进一步观察、分析结果表明,两个横截面深灰色区域同样是稀土铈的氧化物(图11-5)。采用微型拉伸试样,对失效炉管进行了1100℃短时高温拉伸试验,其结果如表11-1所示。可以看出,失效炉管1100℃高温短时拉伸性能低于厂家相关技术要求。
失效模式和效果分析
失效模式和效果分析(Failure Mode and Effect Analysis, FMEA)是一种用来确定潜在失效模式及其原因的分 析方法。具体来说,通过实行FMEA,可在产品设计或生产工艺真正实现之前发现产品的弱点,可在原形样机阶段或在大批量生产之前确定产品缺陷。FMEA最早是由美国国家宇航局(NASA)形成的一套分析模式,FMEA是一种实用的解决问题的方法,可适用于许多工程领域,目前世界许多汽车生产商和电子制造服务商(EMS)都已经采用这种模式进行设计和生产过程的管理和监控。 FMEA简介 FMEA有三种类型,分别是系统FMEA、设计FMEA和工艺FMEA,本文中主要讨论工艺FMEA。实施FMEA管理的具体步骤见图1。 确定产品需要涉及的技术、能够出现的问题,包括下述各个方面:需要设计的新系统、产品和工艺;对现有设计和工艺的改进;在新的应用中或新的环境下,对以前的设计和工艺的保留使用; 形成FMEA团队。理想的FMEA团队应包括设计、生产、组装、质量控制、可靠性、服务、采购、测试以及供货方等所有有关方面的代表。 记录FMEA的序号、日期和更改内容,保持FMEA始终是一个根据实际情况变化的实时现场记录,需要强调的是,FMEA文件必须包括创建和更新的日期。 创建工艺流程图。工艺流程图应按照事件的顺序和技术流程的要求而制定,实施FMEA需要工艺流程图,一般情况下工艺流程图不要轻易变动。 列出所有可能的失效模式、效果和原因、以及对于每一项操作的工艺控制手段: 1.对于工艺流程中的每一项工艺,应确定可能发生的失效模式,如就表面贴装工艺(SMT)而言,涉及的问题可能包括,基于工程经验的焊球控制、焊膏控制、使用的阻焊剂(solder mask)类型、元器件的焊盘图形设计等。 2.对于每一种失效模式,应列出一种或多种可能的失效影响,例如,焊球可能要影响到产品长期的可靠性,因此在可能的影响方面应该注明。 3.对于每一种失效模式,应列出一种或多种可能的失效原因,例如,影响焊球的可能因素包括焊盘图形设计、焊膏湿度过大以及焊膏量控制等。
失效分析案例
佳木斯大学 失效分析案例
失效分析案例 0 零件背景: 某?外径为?450 mm, 壁厚为 50mm 的GCrl5SiMn 钢轴承圈 ,在最终热处理后进?磨削加?时,批量产?沿径向由外表?迅速向内表?扩展的开裂,造成很大的经济损失。其?产?艺为轧制(1050~1150℃锻造) 球化退火→机械加?→淬?(840 ℃)?回?(170℃)→磨削等?序。 1.1化学成分分析 取一部分试样碎末,利用化学元素分析仪分析零件成分。 从上表看出,零件的化学成分符合标准要求。 1.2 硬度分析 在?相抛光?上,从裂纹源处开始沿轴向至壁厚中部每隔 3 mm 检测其硬度。 表 2 显?,裂纹边缘硬度与内部硬度基本?致,硬度均大于 60 HRC,符合标准要求;?明显脱碳软化现象。
1.3 断口宏观形貌 采?机械加压?法使套圈沿裂纹断开,?先对断?形貌??眼观察。 ?线切割从试样断?处切取?块含有裂纹源区?裂纹扩展区?压断区的断?试样。?酒精清洗后在丙酮中?超声波清洗 20 min 取出?燥,?扫描电镜观察该断?形貌 通过?眼观察发现,裂纹源位于轴承套圈外表?沟槽尖?处。试样两断?均为裂纹扩展形成,裂纹长?平直,由轴承套圈外表?沿径向向内表?扩展,初始裂纹最深处约为 15 mm,裂纹总长约 60mm。初始裂纹有褐?氧化条纹,继续向?扩展为灰?,裂纹表?光滑细腻呈瓷状,属典型的脆性断?特征。新断?呈银灰?,断?组织细密有?属光泽,说明晶粒很细?。
由图 2a 可见,断?平齐呈放射状特征,没有明显的塑性变形迹象,断?结构呈细瓷状,边缘?明显剪切唇,也?纤维状。 由图 2b 可见,断?形貌为韧窝?解理断?,呈混合断?特征。大部分属于沿晶脆性开裂,沿晶分离?平滑,?微观塑性变形特征,晶粒均匀细?,?过热特征。但发现有很长很深的?条穿晶带(如箭头所?),认为应该存在某种链条状脆性组织缺陷。 由图 3 可见,新压断?处形貌与起裂处大体相同 ,断?形貌仍为韧窝?解理断? ,混合断?特征不变。说明裂纹处与新压断?处的组织相同。另外均未发现有明显的非?属夹杂物和?孔等缺陷。
失效模式分析
什么是失效模式分析 失效模式分析指的是用来分析当前和以往过程的失效模式数据,以防止这些失效模式将来再发生的正式的结构化的程序。 失效模式分析目的 1、能够容易、低成本地对产品或过程进行修改,从而减轻事后修改的危机。 2、找到能够避免或减少这些潜在失效发生的措施。 失效模式分析益处 1、指出设计上可靠性的弱点,提出对策。 2、针对要求规格、环境条件等,利用实验设计或模拟分析,对不适当的设计,实时加以改善,节省无谓的损失。 3、有效的实施FMEA,可缩短开发时间及开发费用。 4、FMEA发展之初期,以设计技术为考虑,但后来的发展,除设计时间使用外,制造工程及检查工程亦可适用。
5、改进产品的质量、可靠性与安全性。 失效模式分析的适用范围 失效模式分析对产品从设计完成之后,到首次样品的发展而后生产制造,到品管验收等阶段都可说皆有许多适用范围,基本上可以活用在3个阶段,兹说明如下:第一阶段设计阶段的失效模式分析 1.针对已设计的构想作为基础,逐项检讨系统的构造、机能上的问题点及预防策略。 2.对于零件的构造、机能上的问题点及预防策略的检讨。 3.对于数个零件组或零件组之间可能存在的问题点作检讨。 第二阶段试验计划订定阶段的失效模式分析 1.针对试验对象的选定及试验的目的、方法的检讨。 2.试验法有效的运用及新评价方法的检讨。 3.试验之后的追踪和有效性的持续运用。 第三阶段制程阶段的FMEA
1.制程设计阶段中,被预测为不良制程及预防策略的检讨。 2.制程设计阶段中,为了防止不良品发生,而必须加以管理之特性的选定,或管理重点之检讨。 3.有无订定期间追踪的效益。 除了上述所用的范围可以运用此一分析技巧外,使用者亦可自行运用在合适的地方。但是在运用上要注意到: 1.失效模式资讯情报。 如能在事前收集好对象产品、制程、机能等的相关资讯情报,对于分析有很大的帮助。在收集资料上要把握不要轻言放弃可能的因素,如果真的难以判断,就交由专案小组讨论确定。 2 .分析检讨人员足够 为防止分析时的偏差导致失之毫厘,差之千里的谬误并能收集思广益之功,一定的人数参与是必要的,至于多少人才算足够,当视分析对象的特征或公司能力而定。对这一点,固然在量上面要足够,质方面也要考量各个
潜在的失效模式及后果分析FAME
潜在的失效模式及后果分析FAME 潜在的失效模式及后果分析 Potential Failure Mode and Effects Analysis FMEA 第三版
潜在的失效模式及后果分析POTENTIAL FAILURE MODE AND EFFECTS ANALYSIS (FMEA) 参考手册
概要 概述: 本手册介绍了失效模式及后果分析(FMEA)这一专题,给出了应用FMEA技术的通用指南。 什么是FMEA: FMEA可以描述为一组系统化的活动,其目的是:(a)认可并评价产品/过程中的潜在失效以及失效的后果;(b)确定能够消除或减少潜在失效发生机会的措施;(c)将全部过程形成文件。FMEA是对确定设计或过程必须做那些事情才能使顾客满意这一过程的补充。 所有的FMEA都关注设计,无论是产品设计或者是过程设计。 手册格式:
本参考文件介绍了两种类型的FMEA:设计FMEA和过程FMEA。 采用QS-9000或其等效的公司的供应商应使用本手册。FMEA小组可以使用手册中给出的指南,但要以对于给定情况最有效的方式使用。 FMEA的实施: 由于一般的工业倾向是尽可能持续改进产品和过程的质量,所以将FMEA作为专门的技术应用以识别并帮助最大程度地减少潜在的隐患一直是非常重要的。对车辆召回的研究结果表明,FMEA项目的全面实施可能会防止很多召回事件的发生。 成功实施FMEA项目的最重要因素之一是时间性。其含义是指“事件发生前”的措施,而不是“事实出现后”的演练。为实现最大价值,FMEA必须在产品或过程失效模式被纳入到产品或过程之前进行。事先化时间很好地完成FMEA分析,能够最容易、低成本地对产品或过程进行更改,从而最大程度地降低后期更改的危机。FMEA能够减少或消除实施可能会带来更大隐患的预防/纠正性更改的机会。应在所有的FMEA小组间提倡交流和协作。
失效分析案例举例
失效分析案例举例
案例1 油井套管腐蚀 0、背景介绍: 1、套管腐蚀形貌 2、腐蚀产物XRD分析 3、油套管材质的金相和非金属夹杂分析 4、管壁SRB分析检测 5、腐蚀试验 6、结论
背景介绍:中原油田全油田有100多口井套管 腐蚀穿孔,30多口井报废,200多口井套管待修。油井套管的最大穿孔速度为0.48mm年。 1套管腐蚀形貌 对现场取出损坏的套管进行解剖分析。套管内壁分布腐蚀坑,管内壁腐蚀面平稳,腐蚀沿管轴纵向延伸呈马蹄形,其横断面为上宽下窄的梯形深谷状,管壁穿孔处周边锐利,界面清晰。从总体上看,套管内壁都附着黑色粘性油污,无明显腐蚀产物堆积,主要表现为坑蚀穿孔,并有一定的流体冲刷作用。
2腐蚀产物XRD分析 取套管内壁物质,洗去油污,再用丙酮清洗吹干,进行X—射线 衍射分析。套管内壁腐蚀产物中主要有FeCO 3和CaCO 夹杂有NaCl和硫酸亚铁等。腐蚀产物的主要成份为碳酸盐,显示出套管、油管腐蚀与CO 2 腐蚀有关。 3油套管材质的金相和非金属夹杂分析 采用电子探针分析仪进行钢基、夹杂物定性、定量和元素面分析。套管钢的纵截面夹杂物形貌及面分析发现, 大量细小球形 暗灰色颗粒为Al 2O 3 , 短条状为MnS。材质中夹杂物以Al 2O 3 和MnS为主, 少量Al 2 O 3 、TiO2存在。整个材料裂口 面上夹杂物多且分散较均匀,夹杂物以Al 2O 3 、MnS为主 散均匀,加速了钢材的腐蚀。同时经电子探针元素定量分析表明随着向腐蚀坑底的深入,表层元素中氧、硫、氯、钙、镁含量在逐步增大。说明生成的腐蚀产物有铁氧化物、硫化铁、碳酸钙、碳酸镁等,并随腐蚀深入呈增加趋势。
FMEA失效模式及影响分析及其应用
FMEA失效模式及影响分析及其应用 课程背景: 在企业管理、客户服务、产品开发过程中,是“亡羊补牢”,等出现问题再想办法补救呢,还是“防患于未然”,先预测风险并实施控制的方法呢?答案是显而易见的。 有人会说,不出问题,我怎么知道存在什么问题呢?也有人说,我也想“先知先觉”,但我又不能未卜先知,我怎么知道产品投放市场后回出现什么问题呢? ·风险到底是什么,我们该如何来防范它?? ·客户投诉的问题五花八门,理不出头绪,我该怎么进行分析呢?? ·有没有一种系统的工具可以帮助我们对可能出现的问题予以关注呢? ·老是出现类似的问题为什么一直得不到有效的解决?…… 如果您也也有类似的困惑,并且您还没有找到好的方法来解决这些问题,敬请关注《FMEA(失效模式及影响分析)及其应用》 本课程将详细讲解FMEA(Failure Mode and Effect Analysis)失效模式和影响分析这一系统化的预见失效、避免失效的重复出现、降低风险的方法,这一方法最先运用于阿波罗登月计划中,现在被广泛运用于汽车工业中。这一结构化的方法通过对失效(缺陷)的严重性、发生频率和检出性的评分,对风险进行优先排序,并在此基础上对高风险进行控制。是一种有效的预警和降低风险的分析工具。 本课程中您还将现场对照您身边发生的实例,进行FMEA的练习,让您在现实生活中可以学以致用! 同时,本课程还将同你分享企业实施中指南、经验和成功案例,使您在您的企业中推广时事半功倍!培训目标: ·帮助理解失效模式及后果分析在生产过程和质量体系中的应用 ·确定针对不同产品特性而使用FMEA的适用的标准 ·帮助企业建立有效的、及时的和充分的FMEA控制体系 课程大纲: 新版FMEA 概述 ·FMEA的定义、范围和好处 ·FMEA的种类: 系统FMEA, 设计FMEA, 设计FMEA ·原因和效果基本关系 ·FMEA的模式和产品实现流程 ·FMEA开发过程中的关联 ·FMEA开发组织和小组作用 ·高层管理在FMEA过程的作用(新版) 设计FMEA ·DFMEA的基本模式 ·DFMEA的信息流 ·DFMEA的目的 ·前期策划:客户和产品要求的确定 ·产品功能表 ·分析途径 设计FMEA (续) ·界限图(Boundary Diagram) ·接触矩阵图 (Interface Matrix) ·白噪声图(参数图) (P-Diagram) ·DFMEA内部的动态链接(新版) ·DFMEA输入和输出 ·设计矩阵 ·开发DFMEA: 功能、失效模式、后果分析、潜在原因、因果分析工具、设计控制、SOD评分(新版) ·多方位的风险分析(新版强调)
设计失效模式分析DFMEA
1. 目的 确定与产品相关的设计过程潜在的失效模式,确定设计过程中失效的起因,确定减少失效发生或找出失效条件的过程控制变量并编制潜在失效模式分级表,为采取预防措施提供对策。 2. 适用围 本程序适用于新产品设计、产品设计变更时的样品试验阶段的FMEA分析。 3.职责 3.1项目组:负责设计潜在失效模式和后果分析的工作主导,DFMEA的制定; 3.2 APQP跨功能小组:负责设计失效模式和后果分析(DFMEA)结果的评估; 3.3各职能部门:负责各失效模式和后果分析相关工作配合和对策的实施; 3.4 管理者代表:负责设计失效模式和后果分析(DFMEA)结果的批准。 4.定义 4.1 DFMEA:设计潜在失效模式和后果分析(Design Failure Mode and Effecting Analysis)是指设计人员采用的一门分析技术,在最大围保证充分考虑失效模式及其后果、起因和机理,DFMEA以最严密的形式总结了设计技术人员进行产品设计时的指导思想。 4.2 APQP小组:由总经理指定的公司部从事新产品设计和更改的跨功能组织。 4.3严重度(S):是潜在失效模式对下序组件、子系统、系统或顾客影响后果的严重程度的评价指标。
4.4频度(O):是指某一特定的具体的失效起因/机理发生的可能性/频率。 4.5探测度(D):DFMEA是指在零部件、子系统或系统投产之前,现行过程控制方法找出失效起因/机理(设计薄弱部份)的能力的评价指标,PFMEA是指在零部件离开制造工序或装配工位之前,现行过程方法找出失效起因/机理(过程薄弱部份)的可能性的评价指标。 5.流程图:设计失效模式和后果分析(DFMEA)流程图参见(附件一)。 6.作业程序和容 6.1实施DFMEA的时机 6.1.1在设计阶段图面设计之前项目组负责主导DFMEA小组实施DFMEA ,并且在产品图样完成之前全部完成。 6.2 DFMEA小组的构成 6.2.1DFMEA小组成员由项目组根据项目需要从APQP小组成员中选择组成。 6.3 设计失效模式和后果分析(DFMEA)的实施 6.3.1 DFMEA小组应收集相关文件,列出设计意图,将产品要求文件、产品制造/装配要求等确定的顾客需求综合起来。 6.3.2设计FMEA从所要分析各零部件的关系框图开始,分析各零件之间的主要关系,确定分析的逻辑顺序。 6.3.3由项目组主导DFMEA小组相关人员根据设计任务书的设计要求和预期的工艺流程,
董斌—模具失效分析完整版
董斌—模具失效分析 Document serial number【NL89WT-NY98YT-NC8CB-NNUUT-NUT108】
模具失效分析 目录 1引言模具失效 2模具失效形式案例分析及其改进 模具磨损失效 模具断裂失效 模具塑性变形失效 3总结 4参考文献 1引言模具失效 冲压模具是冲压生产中必不可少的工艺装备,是技术密集型产品。冲压件的质量、生产效率以及生产成本等,与模具设计和制造有直接关系。模具设计与制造技术水平的高低,是衡量一个国家产品制造水平高低的重要标志之一,在很大程度上决定着产品的质量、效益和新产品的开发能力。 生产中的冲压模具经过一定时间使用后,由于种种原因不能再冲出合格的产品,同时又不能修复的现象称为冲压模具的失效。由于冲压模具类型、结构、模具材料、工作条件的不同,所以冲压模失效的原因也各不相同。 一般为塑性变形、磨损、断裂或开裂、金属疲劳及腐蚀等等。 模具的失效也可分为: 正常失效和早期失效
模具模具在工作中,与成形坯料接触,并受到相互作用力产生一定的相对运动造成磨损。当磨损使模具的尺寸、精度、表面质量等发生变化而不能冲出合格的产品时,称为磨损失效,磨损失效是模具的主要失效形式,为冲模的正常失效形式,不可避免。 按磨损机理,模具磨损可分为磨粒磨损、黏着磨损、疲劳磨损、腐蚀磨损。 ①磨粒磨损硬质颗粒存在于坯料与模具接触表面之间,或坯料表面的硬突出物,刮擦模具表面引起材料脱落的现象称为磨粒磨损。 ②黏着磨损坯料与模具表面相对运动,由于表面凹凸不平,黏着部分发生剪切断裂,使模具表面材料转移或脱落的现象称为黏着磨损。 ③疲劳磨损坯料与模具表面相对运动,在循环应力的作用下,使表面材料疲劳脱落的现象称为疲劳磨损。 ④腐蚀磨损在摩擦过程中,模具表面与周围介质发生化学或电化学反应,引起表层材料脱落的现象称为腐蚀磨损。 在模具与坯料相对运动过程中,实际磨损情况非常复杂。工作中可能出现多种磨损形式,它们相互促进,最后以一种磨损形式失效。 冲裁模的工作条件 冲裁模具主要用于各种板料的冲切。从冲裁工艺分析中我们已经得知,板料的冲裁过程可以分为三个阶段: 弹性变形阶段
潜在失效模式及后果分析程序
1. 评价在制造过程中潜在的失效模式,分析其后果,评估其风险,从而预先采取措施,消除 或减少失效发生的机会,有效地提高产品质量和可靠性,达到顾客扌两丿意。 2. 适用范围: 适用于新的或更改后的产品/过程的策划阶段,对产品的零部件及各个过程的潜在失效模式及后果进行分析的活动。 3. 定义: 3.1 FMEA:过程潜在失效模式和后果分析,主要是由负责制造的工程师/多方论 证小组采用的一种分析技术,用来保证在可能的范围内已充分地考虑到并指明潜在失效模 式及其相关的起因或机理。 4. 职责 4.1开发部职责: 4.1.1由负责过程设计、制造、装配、售后服务、质量等方面的专家成立多方论证小组,负责 计算风险顺序数RPN 4.1.2多方论证小组职责: 4.121负责收集与FMEAS关数据资料。 4.1.2.2负责进行FMEA分析、评审、效果跟踪和确认。 4.1.3开发部负责对FMEA勺输出整理归档。 5. 作业流程 5.1开展FMEA勺时机FMEA旨在及早识别出潜在的失效,因此FMEA应在以下情况下开 展: 5.1.1在产品、过程设计概念形成,设计方案初步确定时开始FMEA 5.1.2在产品、过程设计的各个重要阶段,对FMEAJ行评审、修改; 5.1.3在如产品、过程设计文件完成之后完成FMEAC作; 5.1.4在进行产品、过程设计修改时对FMEAS行重新评审和修改。 5.2 FMEA活动的实施 5.2.2多方论证小组根据过程流程图、特殊特性清单、产品技术要求、过程特性参数、制造和 装配的要求等和现有的FMEA&料对过程潜在失效模式及后果进行分析。 5.3按下列要求填写FMEA表格:
失效模式分析说明
1.0目的: 为使整个品质系统标准化、设计/生产过程文件规范化,以确保各单位能正确有效地填写“FMEA”且能及时更新. 2.0权责: FMEA表由生产工程部发行并示范,制程FMEA表由生产工程部填写并更新. 3.0定义: FMEA: 失效模式及效应分析. PFMEA: 制程失效模式及效应分析 4.0 制程FMEA表单之填写方法: (1)FMEA编号 填入FMEA文件编号,以便查询. (2) 项目(料号) 填入所分析的系统、子系统或零件的过程名称、编号。 (3) 制程责任 填入整车厂(OEM)、部门和小组,如果知道,还应包括供方的名称。 (4) 编制者\审核者 填入负责FMEA准备工作的工程师的姓名、电话和所在公司的名称及审核者的姓名 (5)类型 填入将使用和/或正被分析过程影响的预期的产品类型(如果已知的话) (6)关键日期 填入初次FMEA预定完成的日期,该日期不应超过计划开始生产的日期。 (7)FMEA日期 填入编制FMEA原始稿的日期及最新修订的日期,最新版本。 (8)核心小组 列出被授权确定和/或执行任务的责任部门和个人姓名(建议所有参加人员的姓名、部门、电话、地址等都应记录在一张分发表上)。 (9)编号 填入PFMEA所分析的项目的编号. (10) 制程说明/制程目的 简单描述被分析的过程或工序(如车、钻、攻丝、焊接、装配)。尽可能简单地说明该过程或工序的目的。 如果过程包括许多具有不同潜在失效模式的工序(例如装配),那么可以将这些工序作为过程列出。 (11)潜在失效模式 所谓潜在失效模式是指过程可能发生的不满足过程要求和/或设计意图的形式,是对某具体工序不符合要求的描述。它可能是引起下一道(下游)工序的潜在失效模式的起因,也可能是上一道(上游)工序潜在失效的后果。但是,在FMEA准备中,应假定提供的零件/材料是合格的。根据零件、子系统、系统或过程特定的工序,列出每一个潜在失效模式。前提是假设这种失效可能发生,但不一定必然发生。过程工程师/小组应能提出并回答下列问题: *过程/零件怎么不能满足规范? *假设不考虑工程规范,顾客(最终使用者、后续工序)对类似零件的索赔情况的研究作为出发点。此外,对设计目的的了解也很必要。典型的失效模式可能是但不限于下列情况: 弯曲、粘合、毛刺、转运损坏、断裂、变形、脏污、安装调节器试不当、接地、开路、短路、工具磨损等 (12)潜在失效后果 潜在失效后果是指失效模式对顾客的影响。在这里,顾客可以是下一道工序、后续工序或工位、代理商、和/工车主。当评价潜在失效后果时,这些因素都必须考虑。 应依据顾客可能注意到的经历的情况来描述失效的后果。对最终使用者来说失效的后果一律用产品或系统的性能来描述,例如: