汽车离合器设计说明书
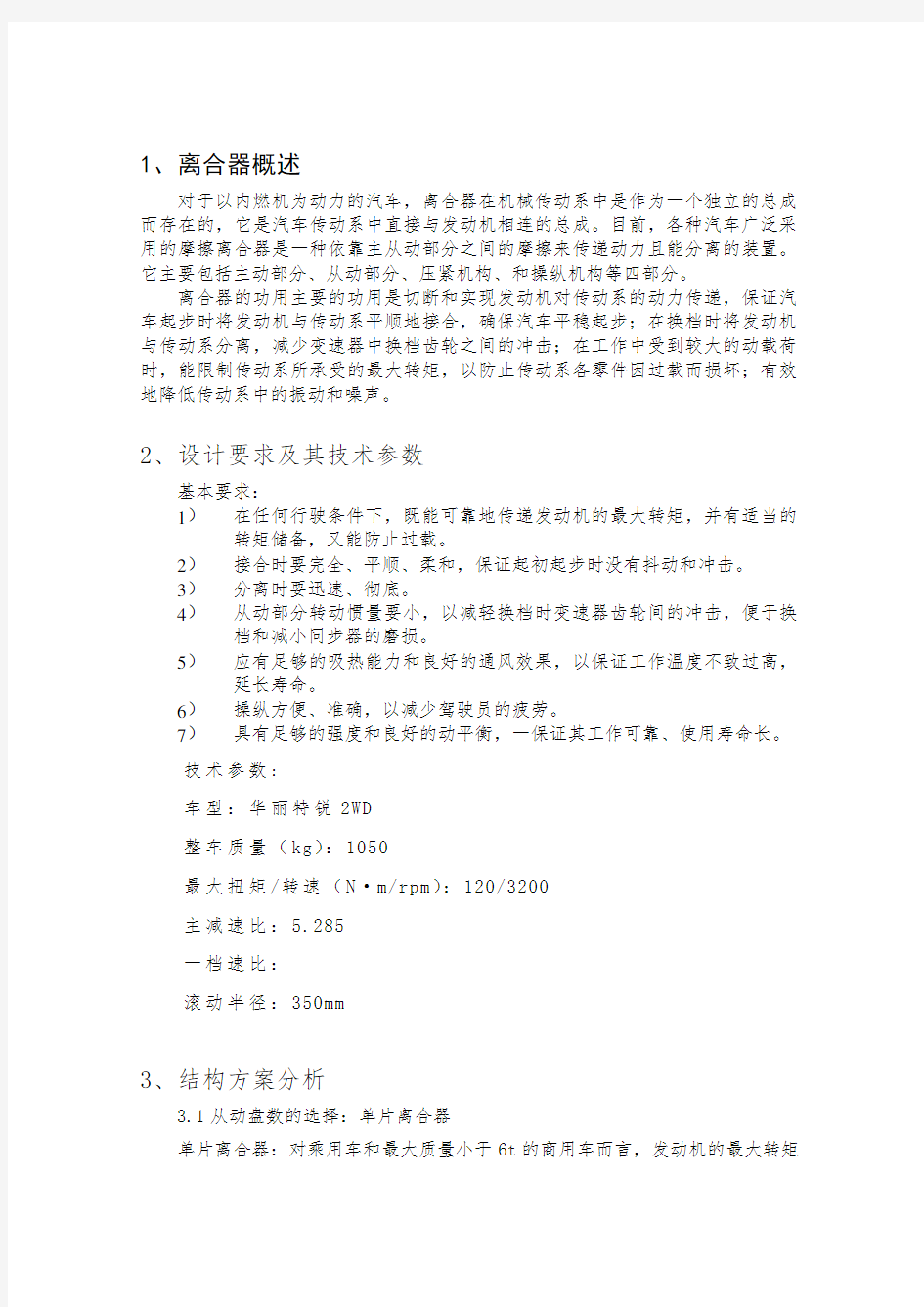

1、离合器概述
对于以内燃机为动力的汽车,离合器在机械传动系中是作为一个独立的总成而存在的,它是汽车传动系中直接与发动机相连的总成。目前,各种汽车广泛采用的摩擦离合器是一种依靠主从动部分之间的摩擦来传递动力且能分离的装置。它主要包括主动部分、从动部分、压紧机构、和操纵机构等四部分。
离合器的功用主要的功用是切断和实现发动机对传动系的动力传递,保证汽车起步时将发动机与传动系平顺地接合,确保汽车平稳起步;在换档时将发动机与传动系分离,减少变速器中换档齿轮之间的冲击;在工作中受到较大的动载荷时,能限制传动系所承受的最大转矩,以防止传动系各零件因过载而损坏;有效地降低传动系中的振动和噪声。
2、设计要求及其技术参数
基本要求:
1)在任何行驶条件下,既能可靠地传递发动机的最大转矩,并有适当的转矩储备,又能防止过载。
2)接合时要完全、平顺、柔和,保证起初起步时没有抖动和冲击。
3)分离时要迅速、彻底。
4)从动部分转动惯量要小,以减轻换档时变速器齿轮间的冲击,便于换档和减小同步器的磨损。
5)应有足够的吸热能力和良好的通风效果,以保证工作温度不致过高,延长寿命。
6)操纵方便、准确,以减少驾驶员的疲劳。
7)具有足够的强度和良好的动平衡,一保证其工作可靠、使用寿命长。
技术参数:
车型:华丽特锐2WD
整车质量(kg):1050
最大扭矩/转速(N·m/rpm):120/3200
主减速比:5.285
一档速比:
滚动半径:350mm
3、结构方案分析
3.1从动盘数的选择:单片离合器
单片离合器:对乘用车和最大质量小于6t的商用车而言,发动机的最大转矩
一般不大,在布置
尺寸容许条件下,离合器通常只设有一片从动盘。
单片离合器的结构简单,轴向尺寸紧凑,散热良好,维修调整方便,从动部分转动惯量小,在使用时能保证分离彻底,采用轴向有弹性的从动盘可保证结合平顺。
3.2压紧弹簧和布置形式的选择:拉式膜片弹簧离合器
膜片弹簧是一种由弹簧钢制成的具有特殊结构的碟形弹簧,主要由碟簧部分和分离指部分组成。
1. 膜片弹簧离合器与其他形式的离合器相比,有如下优点:
1) 具有较理想的非线性弹性特性。
2) 兼起压紧弹簧和分离杠杆的作用。
3) 高速旋转时,弹簧压紧力降低很少,性能较稳定。
4) 以整个圆周与压盘接触,使压力分布均匀,摩擦片接触良好,磨损均匀。
5) 通风散热良好,使用寿命长。
6) 膜片弹簧中心与离合器中心线重合,平衡性好。
2. 与推式相比,拉式膜片弹簧离合器具有许多优点:取消了中间支承各零件,并不用支承环或只用一个支承环,使其结构更简单、紧凑,零件数目更少,质量更小等。
3.3膜片弹簧的支撑形式
图3-1为拉式膜片弹簧的支承形式—单支承环形式,将膜片弹簧大端支承在离合器盖杀中的支承环上。
图3-1
4、离合器主要参数的选择
4.1后备系数β
后备系数β是离合器设计中的一个重要参数,它反映了离合器传递发动机最大转矩的可靠程度。在选择β时,应考虑摩擦片在使用中的磨损后离合器仍能可靠地传递发动机最大转矩、防止离合器滑磨时间过长、防止传动系过载以及操纵轻便等因素。乘用车β选择:1.20~1.75 ,本次设计取β = 1.2。
4.2摩擦因数f、摩擦面数Z和离合器间隙△t
摩擦片的摩擦因数f取决于摩擦片所用的材料及其工作温度、单位压力和滑磨速度等因素。摩擦因数f的取值范围见下表。
表4-1 摩擦材料的摩擦因数f的取值范围
本次设计取f = 0.30 。
摩擦面数Z为离合器从动盘数的两倍,决定于离合器所需传递转矩的大小及其结构尺寸。本次设计取单片离合器 Z = 2 。
离合器间隙△t是指离合器处于正常结合状态、分离套筒被回位弹簧拉到后极限位置时,为保证摩擦片正常磨损过程中离合器仍能完全结合,在分离轴承和分离杠杆内端之间留有的间隙。该间隙△t一般为3~4mm 。本次设计取△t =3 mm 。
4.3单位压力p
单位压力p
决定了摩擦表面的耐磨性,对离合器工作性能和使用寿命有很大0
影响,选取时应考虑离合器的工作条件、发动机后备功率的大小、摩擦片尺寸、材料及其质量和后备系数等因素。p
取值范围见表4-2。
表4-2 摩擦片单位压力p 0的取值范围
p 0选择:0.10 MPa ≤ p 0 ≤ 1.50 MPa ,本次设计取 p 0 = 0.3MPa 。
4.4摩擦片外径D 、内径d 和厚度b
摩擦片外径是离合器的重要参数,它对离合器的轮廓尺寸、质量和使用寿命有决定性的影响。
D = 3
3
0)
1(12max c fZp T e -πβ ≈160 mm (2-1)
取D =198 mm
当摩擦片外径D 确定后,摩擦片内径d 可根据d/D 在0.53~0.70之间来确定。 取c = d/D = 0.7 ,d = 0.7D = 140 mm ,取d = 139mm
摩擦片厚度b 主要有3.2 mm 、3.5 mm 、4.0 mm 三种。取b = 3.5 mm 。 T c = βT emax = 1.2?120 = 143 N.m
5、离合器的设计与计算
5.1离合器基本参数的优化
设计离合器要确定离合器的性能参数和尺寸参数,这些参数的变化直接影响离合器的工作性能和结构尺寸。这些参数的确定在前面是采用先初选、后校核的方法。下面采用优化的方法来确定这些参数。
1)摩擦片外径D(mm)的选取应使最大圆周速度v
D
不超过65~70m/s,即
v
D =
60
π
n
emax
D?103- =
60
π
?3200?200?103- =38.28m/s ≤65~70m/s (2-2)
符合要求。
式中, v
D
为摩擦片最大圆周速度(m/s);n
emax
为发动机最高转速(r/min)。
2)摩擦片的内、外径比c应在0.53~0.70范围内,本次设计取c = 0.7 。
3)为了保证离合器可靠地传递发动机的转矩,并防止传动系过载,不同的车
型的β值应在一定范围内,最大范围为1.2~4.0 ,本次设计取β= 1.20 。
4)为了保证扭转减振器的安装,摩擦片内径d必须大于减振器弹簧位置直径
2R
约50mm,即 d > 2R
+ 50 mm
5)为降低离合器滑磨时的热负荷,防止摩擦片损伤,对于不同车型,单位压力
p
根据所用的摩擦材料在一定范围内选取,p
的最大范围为0.10~1.50 Mpa。
本次设计取p
= 0.3 MPa 。
6)为了减少汽车起步过程中离合器的滑磨,防止摩擦片表面温度过高而发生
烧伤,离合器每一次结合的单位摩擦面积滑磨功w应小于其许用值[w]。
汽车起步时离合器结合一次所产生的总滑磨功(J)为:
W =
1800
n2
e
2
π
(
2
g
2
2
r
a
i i
r
m
) = 6994.4(J) (2-4)
式中,m
a
为汽车总质量(kg);r
r
为轮胎滚动半径(m);i
g
为汽车起步时所用
变速器档位的传动比;i
为主减速器传动比;n
e
为发动机转速(r/min);乘用车n
e
取2000 r/min 。
w =
)
(
4
2
2d
D
Z
W
-
π
=
)
140
*
140
200
*
200
(*
2
*
14
.3
4.
6994
*
4
-
= 0.22 < [w] = 0.4
J/mm2 (2-5)
满足要求
5.2膜片弹簧的弹性特性曲线
5.3膜片弹簧基本参数的选择
1)比值H/h 和 h 的选择
为保证离合器压紧力变化不大和操纵轻便,汽车离合器用膜片弹簧的H/h 一般为1.5~2.0 ,板厚 h 为2~4 mm 。
取h = 2 mm ,H/h =1.7 ,即 H = 1.7h =3.4 mm 。
2)R/r比值和 R、r的选择
研究表明。R/r越大,弹簧材料利用率越低,弹簧越硬,弹性特性曲受直径误差的影响越大,且应力越高。根据结构布置和压紧力的要求。R/r一般为1.20~1.35 。为使摩擦片上的压力分布较均匀,拉式膜片弹簧的r值宜为大于或等于R
c
。即
R=摩擦片外径100
取R/r = 1.3 , r = R /1.3 = 77 mm 。
3)α的选择
膜片弹簧自由状态下圆锥角α与内截锥高度H关系密切,α一般在9°~15°范围内。
α = arctan H/(R-r) = 10°,符合要求。
4.)分离指数目n的选取
分离指数目n常取18,大尺寸膜片弹簧可取24,小尺寸膜片弹簧可取12 。
取分离之数目n =18 。
5)膜片弹簧小段内半径r
0及分离轴承作用半径r
f
的确定
r
0由离合器的结构决定,其最小值应大于变速器第一轴花键的外径。r
f
应大
于r
0。
I轴外径D>=2A
取r 0min >I 轴花键外径=40 由文献[4]得知花键尺寸 d=36 D=40 B=7
6)切槽宽度δ1、δ2及半径r e 的确定 δ1= 3.2~3.5 mm ,δ2= 9~10 mm ,r
e
的取值应满足r - r e ≥ δ2。
本次设计取δ1 = 3.2 mm ,δ2= 9 mm ,r
e
≤ r -δ2= 52.5 mm 。
7)压盘加载点半径R 1 和支承环加载点半径r 1 的确定
R 1=74 r 1=63 5.4 膜片弹簧的优化设计
膜片弹簧的优化设计就是要确定一组弹簧的基本参数,使其弹性特性满足离合器的使用性能要求,而且弹簧强度也满足设计要求,以达到最佳的综合效果。
1)为了满足离合器使用性能的要求,弹簧的H/h 与初始底锥角α≈H/(R-r)应在一定范围内,即
1.6 ≤ H/h = 1.7 ≤
2.2 9°≤α≈H/(R-r)=10°≤ 15°
2)弹簧各部分有关尺寸的比值应符合一定的范围,即
1.20 ≤ R/r=1.30 ≤ 1.35
3.5≤R / r 0= 80 / 32.6 =2.45 ≤5.0=2.4
3)为了使摩擦片上的压紧力分布比较均匀,拉式膜片弹簧的压盘加载点半径r 1应位于摩擦片的平均半径与外半径之间,即
(D+d)/4 ≤r 1=63 ≤ D/2
4)根据弹簧结构布置要求,R 1与R ,r f 与r 0之差应在一定范围内,即 1 ≤ R-R 1 = 6 ≤ 7 0 ≤ r f -r 0 = 1.4 ≤ 4
5)膜片弹簧的分离指起分离杠杆的作用,因此其杠杆比应在一定范围内选取,即
3.5 ≤
1
11r R r R f -- = 3.65 ≤ 9.0
6、主要零部件的结构设计
6.1扭转减振器的设计
6.1.1扭转减振器的概述
扭转减振器主要由弹性元件(减振弹簧或橡胶)和阻尼元件(阻尼片)等组成。弹性元件的主要作用是降低传动系的首段扭转刚度,从而降低传动系扭转系统的某阶(通常为三阶)固有频率,改变系统的固有振型,使之尽可能避开由发动机转矩主谐量激励引起的共振;阻尼元件的主要作用是有效地耗散振动能量。因此,扭转减振器具有如下功能:
1)降低发动机曲轴与传动系接合部分的扭转刚度,调谐传动系扭振固有频率。
2)增加传动系扭振阻尼,抑制扭转共振响应振幅,并衰减因冲击而产生的瞬态扭振。
3)控制动力传动系总成怠速时离合器与变速器轴系的扭振,消减变速器怠速噪声和主减速器与变速器的扭振及噪声。
4)缓和非稳定工况下传动系的扭转冲击载荷,改善离合器的接合平顺性。
减振器的扭转刚度k
?和阻尼摩擦元件间的阻尼摩擦转矩T
μ
是两个主要参
数,决定了减振器的减震效果。其设计参数还包括极限转矩T
j 、预紧转矩T
n
和极
限转角
j
?等。
6.1.2扭转减振器的设计
1)极限转矩T
j
极限转矩是指减振器在消除了限位销与从动盘毂缺口之间的间隙△
1
时所能传递的最大转矩,即限位销起作用时的转矩。它受限于减振弹簧的许用应力等因
素,与发动机最大转矩有关,一般可取 T
j = (1.5~2.0) T
emax
(2-6)
一般乘用车:系数取2.0 即 T
j = 2 T
emax
= 240N·m
2)扭转角刚度
K
?≤13T
j
=13×240=3120
3)阻尼摩擦转矩T
μ
由于减振器扭转刚度k ?受结构及发动机最大转矩的限制,不可能很低,故为了在发动机工作转速范围内最有效地消振,必须合理选择减振器阻尼装置的阻尼摩擦转矩T μ 。
一般可按下式初选:T μ=(0.06~0.17)T emax (2-7)
取T μ= 0.1T emax = 12N ·m
4)预紧转矩T n
减振弹簧在安装时都有一定的预紧。研究表明,T n 增加,共振频率将向减小频率的方向移动,这是有利的。但是T n 不应大于T μ ,否则在反向工作时,扭转减振器将提前停止工作,故取 T n = (0.05~0.15)T emax (2-8)
取T n = 0.1T emax =12N ·m 5)减振弹簧的位置半径R 0
R 0 的尺寸应尽可能大些,一般取 R 0 =(0.60~0.75)d/2 (2-10)
R 0 = 0.60d/2 = 37.5 mm
6)减振弹簧个数Z j Z j 参照表6-1选取。
表6-1 减振弹簧个数的选取
摩擦片外径D = 198mm ,选取Z j =4
7)减振弹簧总压力 F ∑
当限位销与从动盘毂之间的间隙1?或2?被消除,减震弹簧传递的转矩达到最大值T j 时,减震弹簧受到的压力F ∑为
F ∑ = T j /R 0 = 240000Nmm/37.5 = 6400 N (2-11)
8)极限转角j ?
本次设计j ? 取10°。
6.1.3扭转弹簧的设计
1)取弹簧钢丝直径d=3mm 2)弹簧指数比c=6 3)曲度系数K ’=1.25 4)弹簧中径Dm=18mm 5)外径D=Dm+d=21mm 6)弹簧总圈数n=i+1.5 7)工作负荷下变形f=P/K=30 8)n=i+1.5=4.7 9)△f=1.5
10)0H =(n-0.5)d+f+△f+0.2=99.211.H=0H -f=30
表6-2压簧的计算公式表
6.2从动盘总成的设计
6.2.1从动盘毂
从动盘毂是离合器中承受载荷最大的零件,它几乎承受由发动机传来的全部转矩。它一般采用齿侧对中的矩形花键安装在变速器的第一轴上,花键的迟钝可根据摩擦片的外径D与发动机的最大转矩T
由表3-1选取。
m ax
e
表6-2 从动盘毂花键的尺寸
本次设计D = 198mm ,T m ax e = 120 N ·m 故选择花键类型为: 6.2.2从动片的设计
从动盘对离合器工作性能影响很大,设计时应满足如下要求:
1)从动盘的转动惯量应尽可能小,以减小变速器换挡时轮齿间的冲击。 2) 从动盘应具有轴向弹性,使离合器结合平顺,便于起步,而且使摩擦面压力均匀,以减小磨损。
3)应安装扭转减振器,以避免传动系共振,并缓和冲击。 6.2.3摩擦片的设计 摩擦片应满足以下要求:
1)摩擦因数较高且稳定,工作温度、单位压力、滑磨速度的变化对其影响要
小
2)具有足够的机械强度与耐磨性
3)密度要小,以减少从动盘的转动惯量。
4)热稳定性要好
5)磨合性要好,不至刮伤飞轮和压盘表面
6.3离合器盖总成的设计
6.3.1离合器盖结构设计的要求:
1)应具有足够的刚度,否则影响离合器的工作特性,增大操纵时的分离行程,减小压盘升程,严重时使摩擦面不能彻底分离。
2)应与飞轮保持良好的对中,以免影响总成的平衡和正常的工作。
3)盖的膜片弹簧支承处应具有高的尺寸精度。
4)为了便于通风散热,防止摩擦表面温度过高,可在离合器盖上开较大的通风窗孔,或在盖上加设通风扇片等。
乘用车离合器盖一般用08、10钢等低碳钢板。
6.3.2压盘的设计
对压盘结构设计的要求:
1)压盘应具有较大的质量,以增大热容量,减小温,防止其产生裂纹和破碎,有时可设置各种形状的散热筋或鼓风筋,以帮助散热通风。中间压盘可铸出通风槽,也可以采用传热系数较大的铝合金压盘。
2)压盘应具有较大刚度,使压紧力在摩擦面上的压力分布均匀并减小受热后的翘曲变形,以免影响摩擦片的均匀压紧及与离合器的彻底分离,厚度约为15~25 mm 。
3)与飞轮应保持良好的对中,并要进行静平衡,压盘单件的平衡精度应不低于15~20 g·cm 。
4)压盘高度(从承压点到摩擦面的距离)公差要小。
压盘形状较复杂,要求传热性好,具有较高的摩擦因数,通常采用灰铸铁,一般采用HT200、HT250、HT300,硬度为170~227HBS。
6.4压盘的结构设计与选择